ZF presents ‘ultra-compact’ e-drive for passenger cars
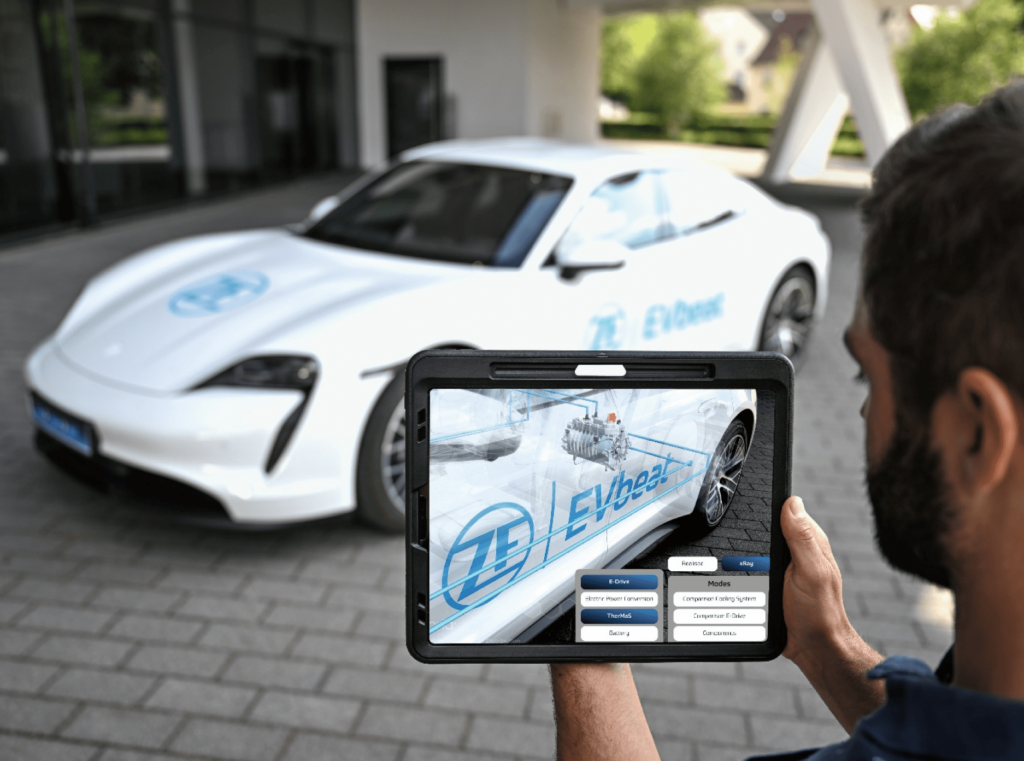
(Images courtesy of ZF)
ZF has unveiled its electric concept vehicle, the EVbeat, in which the components of an e-driveline have been optimised and combined into a holistic system. These include an ultra-compact 74 kg driveline with a torque density of 70 Nm/kg, holistic thermal management and cloud-networked driveline software. At temperatures around freezing point, the range in real-world operation increases by up to a third compared with current technology.
The EVbeat is based on a Porsche Taycan, and takes technology from ZF and other market players as a benchmark.
The electric motor works without heavy rare earth elements, and the thermal management system uses propane rather than a fluorine-based refrigerant. The EVbeat has a maximum torque of 5200 Nm available at the rear axle, and continuous and peak power of 206 and 275 kW respectively.
The EVSys800 modular 800 V driveline consists of SiC power electronics, the electric motor and a reduction gearbox. In terms of dimensions, the drive saves 50 mm in width thanks to the compact reduction gearbox and the ZF-patented ‘Braided Winding’ technology of the motor.
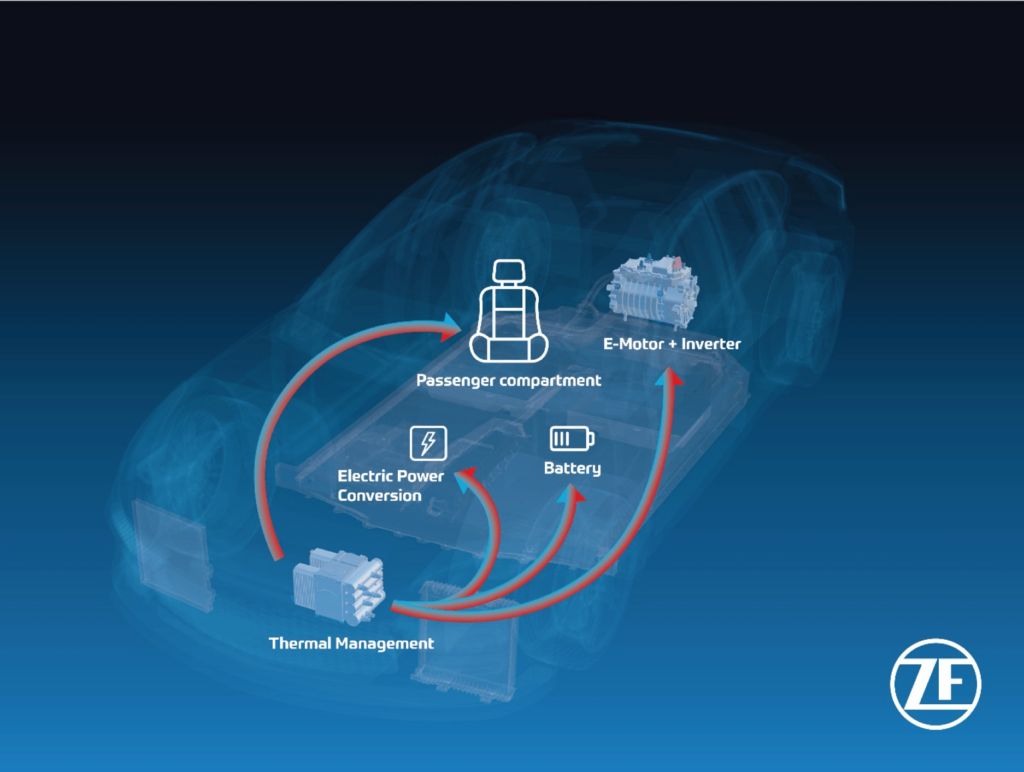
With a total weight of 74 kg, the EVSys800, normalised to the same output as the latest ZF 800 V series drive, is about 40 kg or one-third lighter.
For cooling, ZF allows oil to flow directly around the copper rods. In addition, the use of heavy rare earth elements can be dispensed with, and the electric motor can be produced more sustainably.
The Braided Winding technology saves a total of 10% installation space. The winding head alone is up to 50% smaller than with conventional approaches. This saves around 10% in copper.
A new, coaxial reduction gearbox transmits the drive forces of the electric motor via two planetary gear sets. Compared with conventional offset concepts, in which the input and output shafts are not on the same axis, ZF says the coaxial solution reduces weight and installation space requirements without compromising on efficiency, noise and vibration.
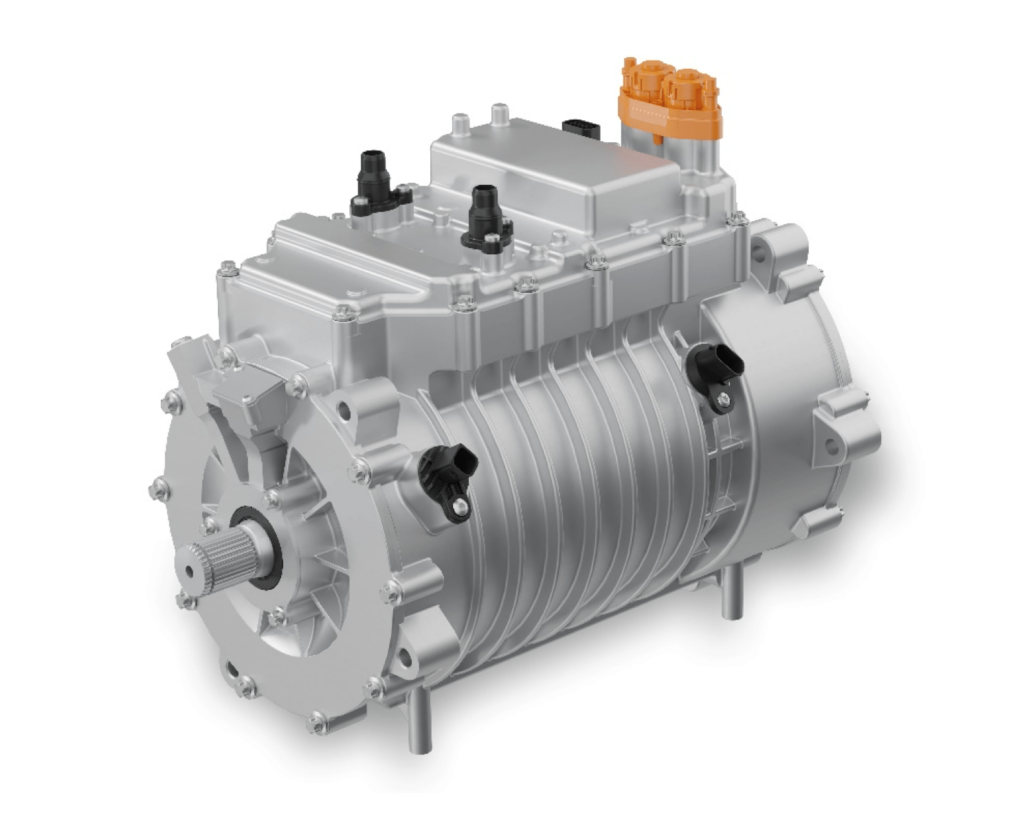
The first central thermal management system (TherMaS) developed by ZF for electric vehicles is integrated into the EVbeat. TherMaS uses a central unit and intelligent software to control all the thermal processes for the driveline and passenger compartment.
An 800 V heat pump for the propane coolant also requires much less energy. Although only half the previous refrigerant is used, the cooling capacity increases by a factor of two compared with refrigerants commonly used today.
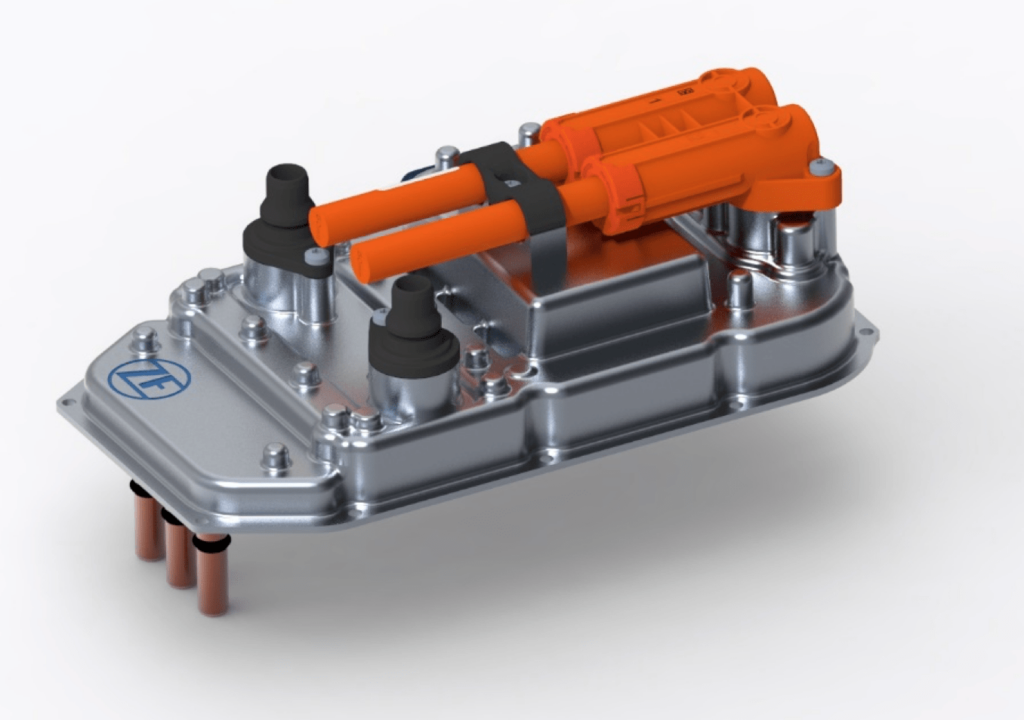
If required, the central refrigerant circuit serves two separately controllable cooling circuits in which frost-protected water flows as usual. The first is designed for the comparatively high temperatures of the electric motor, while the second regulates the temperature of the power and charging electronics. The control software regulates the cooling capacity.
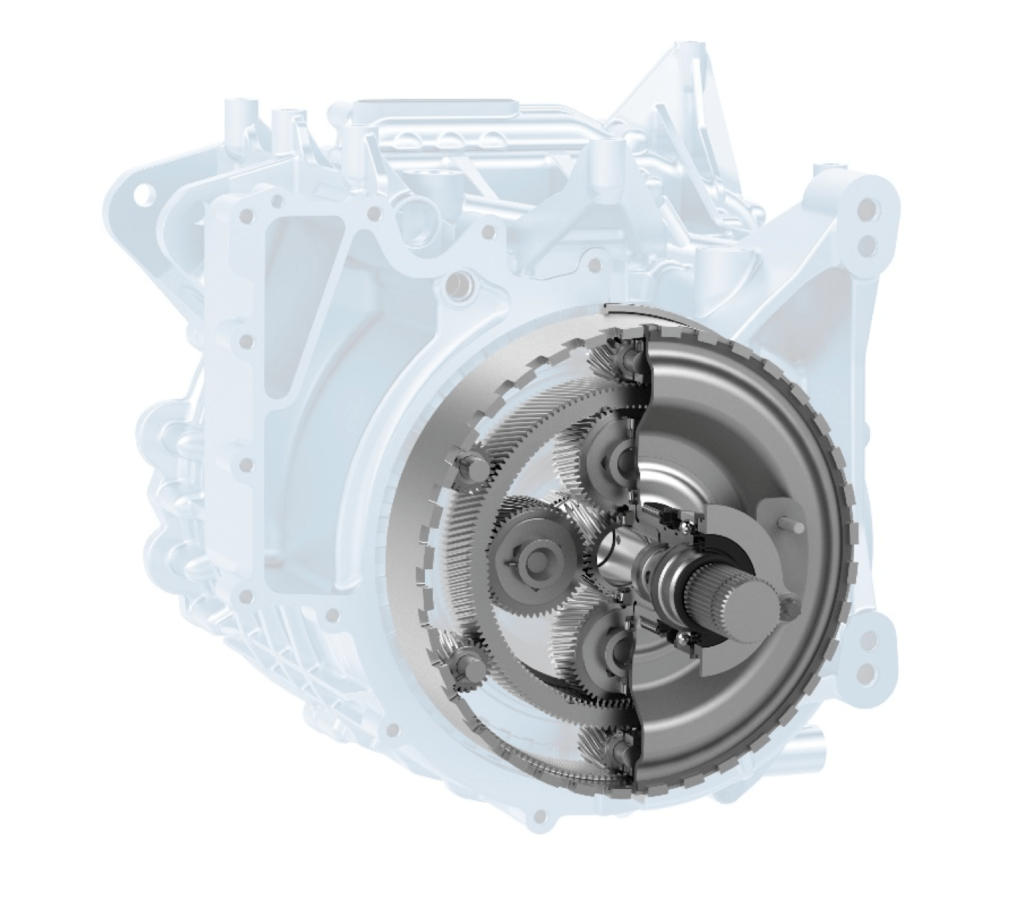
This overall thermal management boosts the range of the EVbeat by up to a third in demanding winter operation.
ZF has also developed its own powertrain software that networks all the vehicle systems with each other and establishes a connection to the ZF cloud.
It can anticipate the optimum thermal operating points from the individual driving profiles and prepare the system accordingly. It can also anticipate the probability of individual driving profiles through an AI-based cloud service.
The first technologies of the new ZF driveline will be available from 2026.
ONLINE PARTNERS
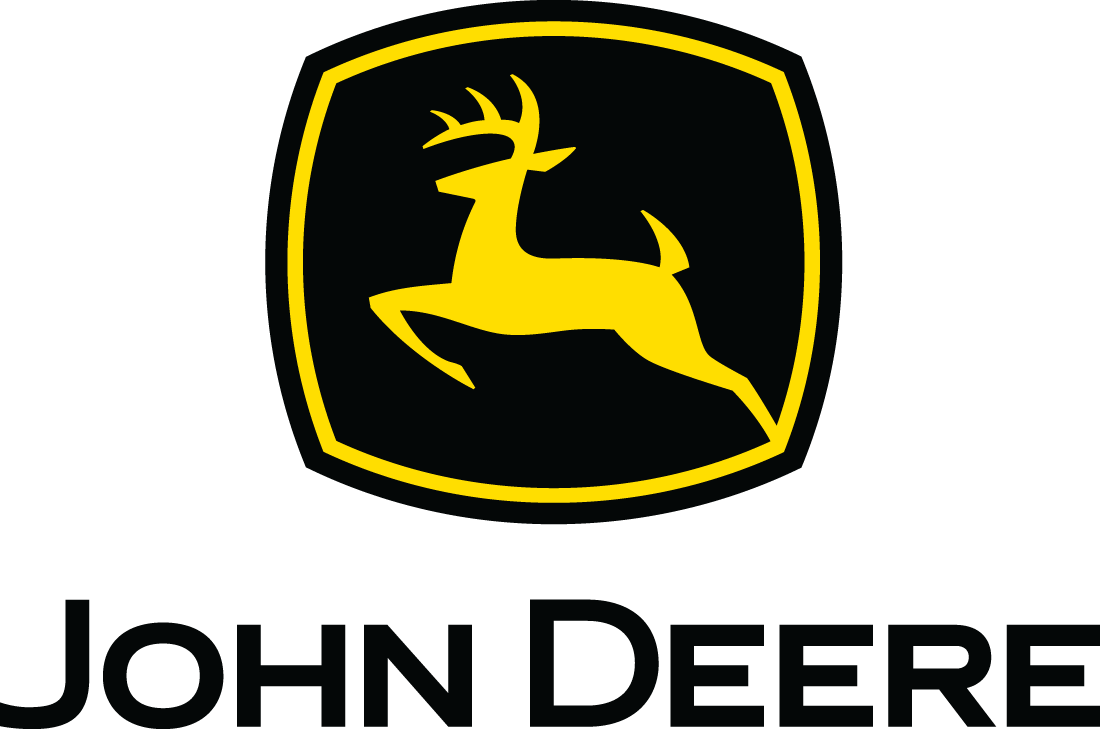
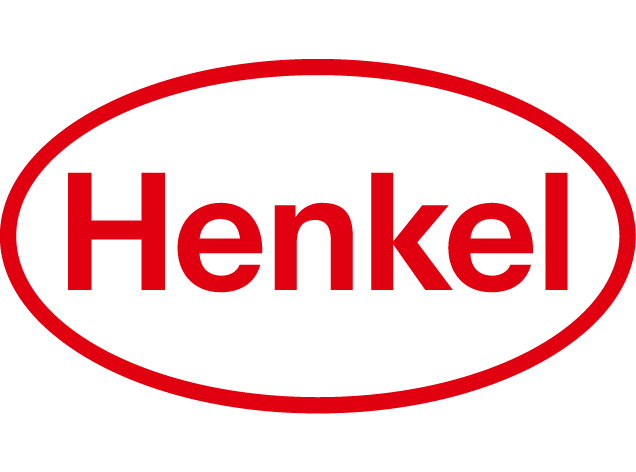
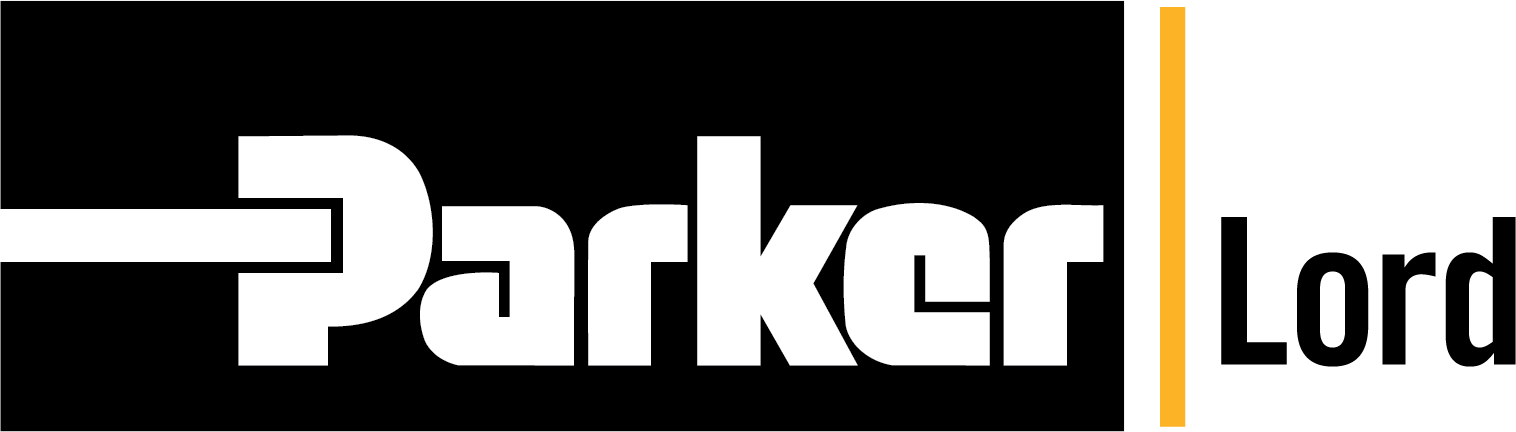
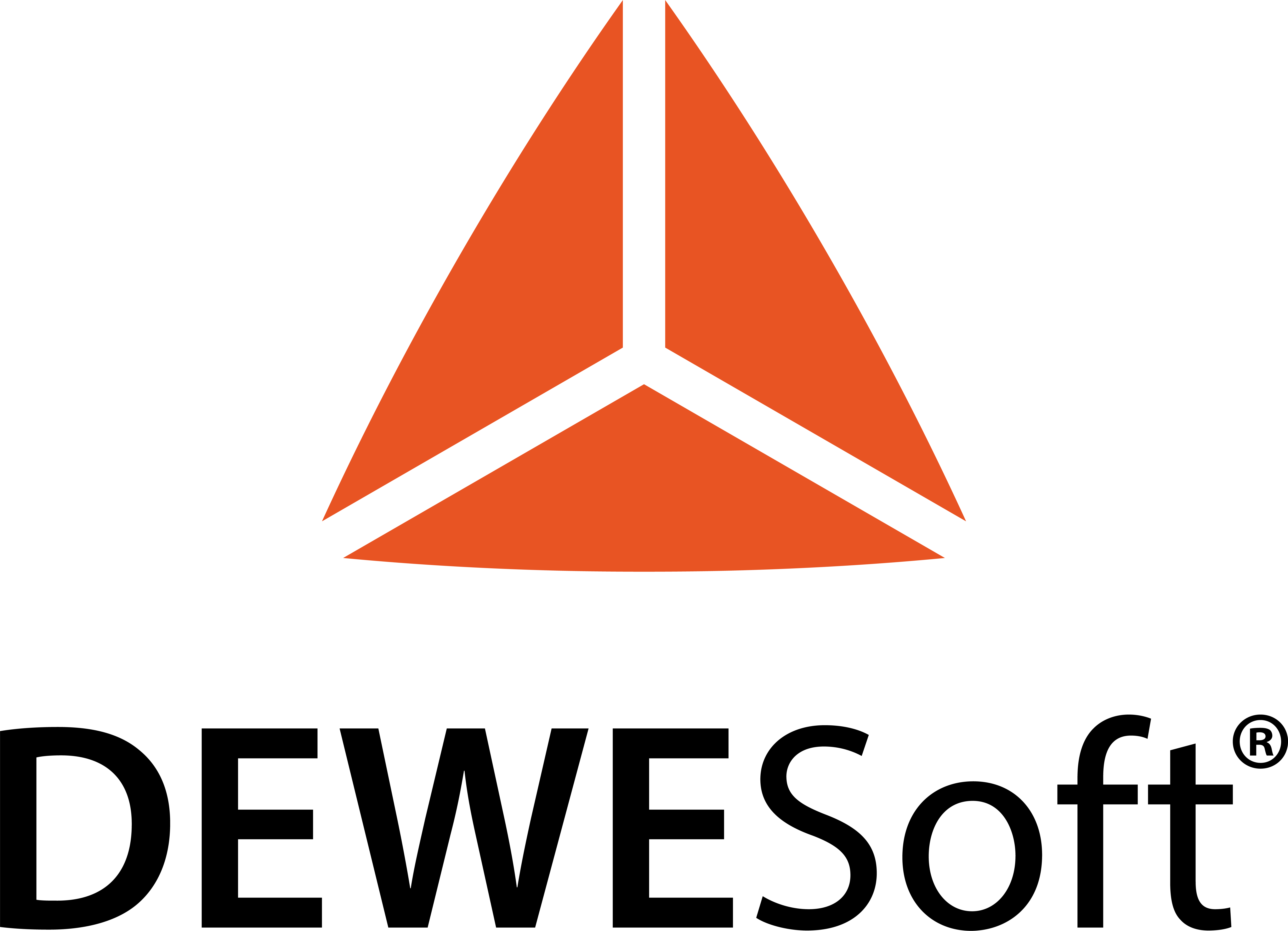
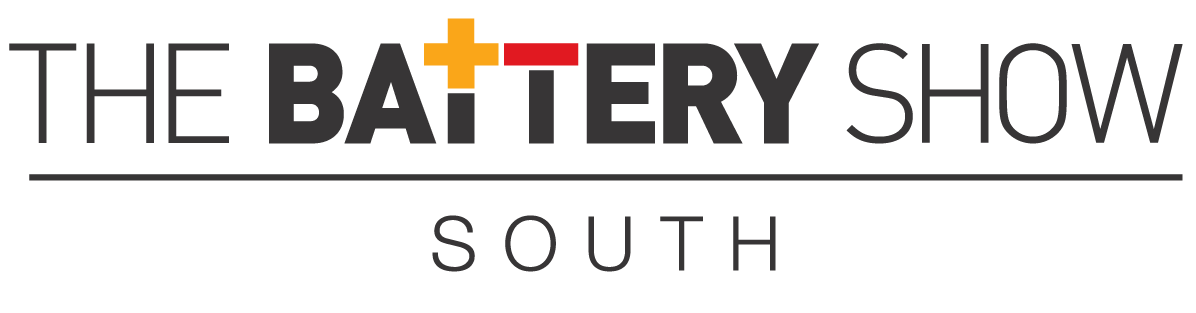
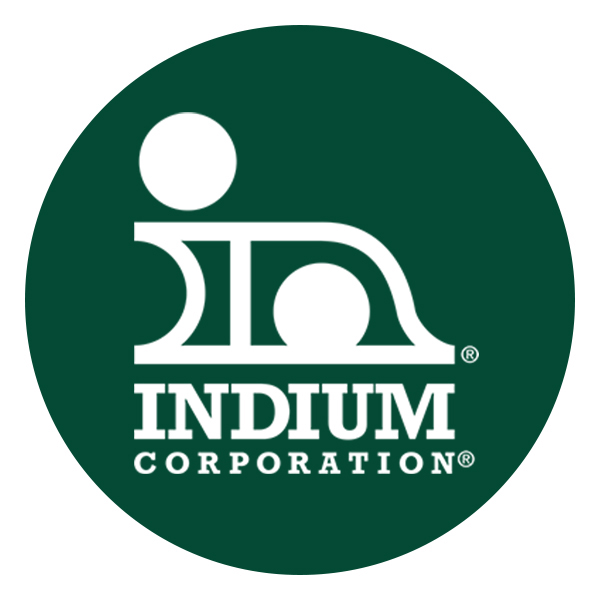
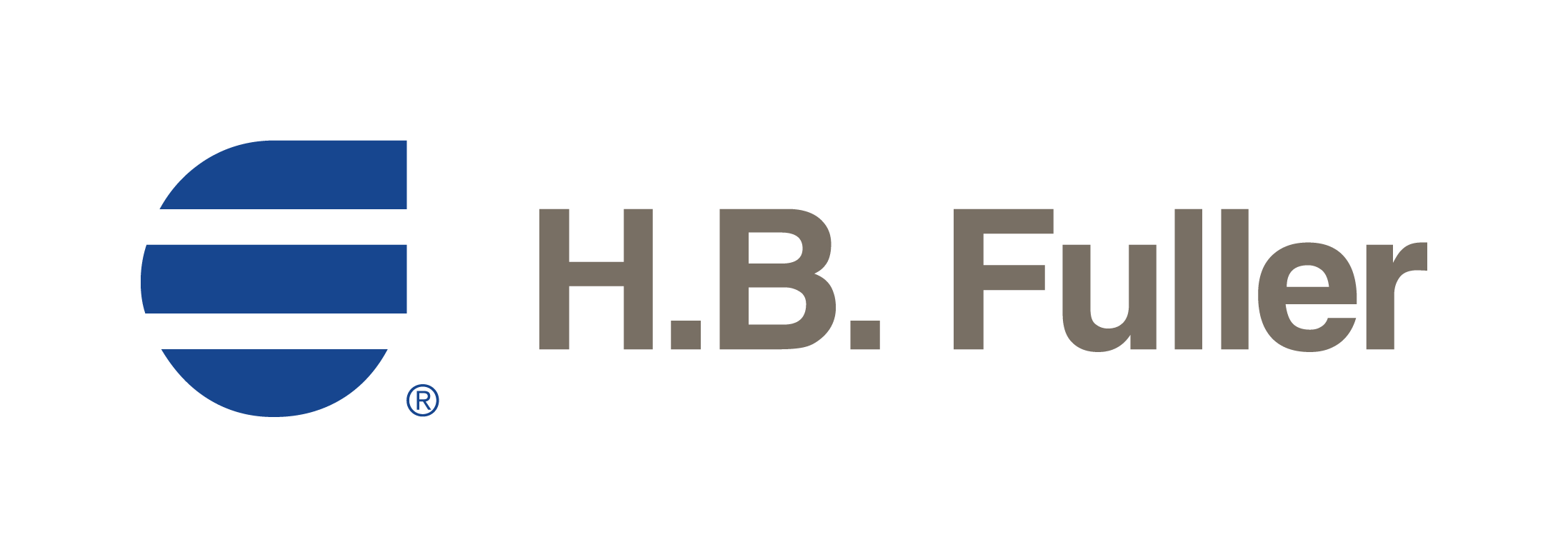