Protecting electric ships with rapid DC switching
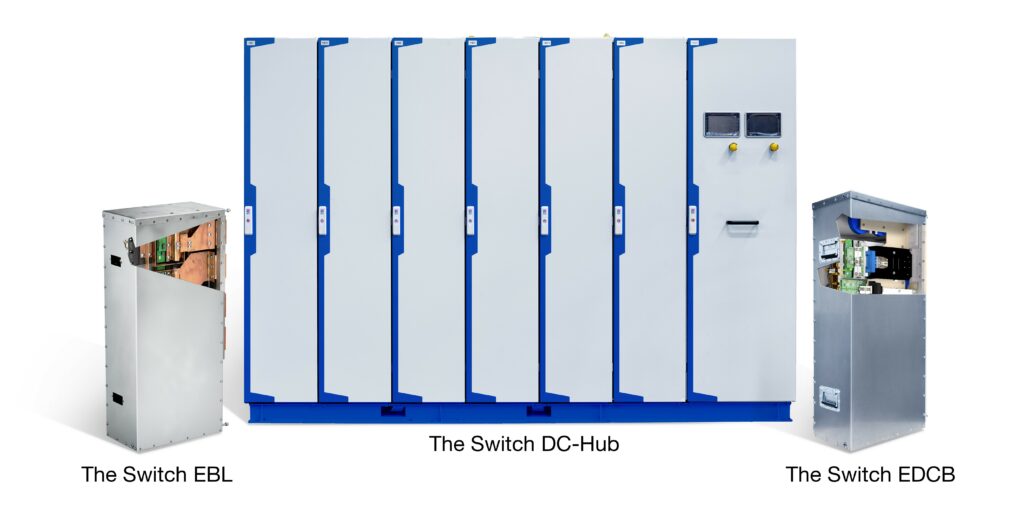
(Images courtesy of Yaskawa Environmental Energy/The Switch)
Potentially critical faults in the high-power DC powertrains increasingly found in ships, particularly ferries, must be isolated as quickly as possible to minimise damage and allow the rest of the system to continue operating as normal (writes Peter Donaldson).
Key to this is the application of solid-state power electronics in the form of switches based on IGBTs, which stop the flow of current into a fault within 10 µs – orders of magnitude faster than conventional fuses that typically take milliseconds to blow. These components are at the heart of the Electronic Direct Current Breaker (EDCB) and the Electronic Bus Link (EBL) devices developed by Yaskawa Environmental Energy/The Switch.
Both components are part of The Switch’s DC-Hub offering for multi-megawatt power systems. EDCBs are integrated into inverter modules within the DC-Hubs to detect and disconnect critical faults selectively.
The EBL is used to connect multiple hubs in a vessel’s DC distribution system, and enables ultra-rapid splitting of onboard grids to isolate any DC-Hub or connection cable with a fault without affecting healthy systems, which provides extra redundancy. Such rapid disconnection is important, because it minimises the amount of energy going into the fault.
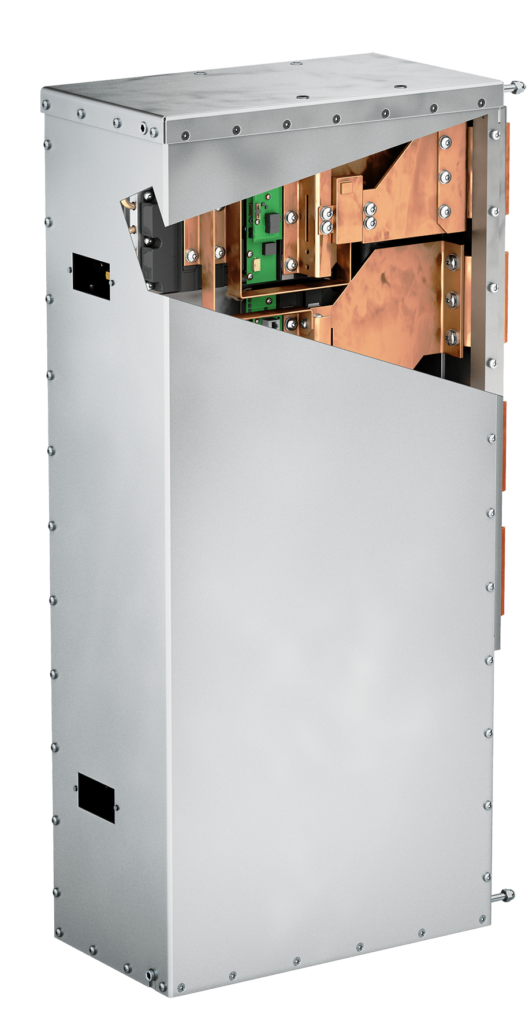
As technical solutions manager Asbjorn Halsebakke explains, “If you have a short-circuit, that is a standing fault, for a long time, and a lot of energy will go into it and cause a lot of damage by melting copper and creating a lot of soot, so you want to disconnect it before the energy going into it is too high. Maybe the most important thing is that if you disconnect quickly, other systems will not be affected by that fault.
“If you are using fuses or breakers – which is quite common in AC systems but is not a good solution in DC systems – it will be some time before a fuse blows or breaker opens. That means the voltage on everything will go down and some equipment will stop, such as motors, navigation systems and lighting, and anything can happen to a ship that’s drifting in the dark, say.”
Rapid disconnection of large DC currents can be difficult, because they don’t cross zero amps as AC currents do twice per cycle. “A DC current just continues, so you need to use other means of disconnecting it,” Halsebakke says.
“IGBT technology in our frequency converters is used for switching large DC currents on and off, and it is what we use in the EDCB and the EBL to replace fuses and breakers, and make something that works much better in a DC system.”
In addition to their switching capabilities, the EDCB and the EBL modules have sensitive fault-detection circuits, which rely on measuring amperage and rate of change of amperage, Halsebakke explains. “That helps to detect faults faster, because while a normal heavy load will draw a large current it does not change very fast, but if it is a fault, the current rises very, very fast,” he says.
The move to DC electrical distribution is being driven by the need for efficiency in systems that rely heavily on large batteries. Complex switchboards serving multiple AC loads require the extensive use of inverters and converters, and every stage of conversion involves energy losses, he explains.
With a number of successful pilot programmes behind it, the company reports that it is close to finalising its new-generation single-drive and DC-Hub package. It was successfully piloted on Hagland Shipping’s 4699 tons deadweight general cargo ship the Hagland Captain (built 2012), which was converted to battery hybrid propulsion in 2021.
ONLINE PARTNERS
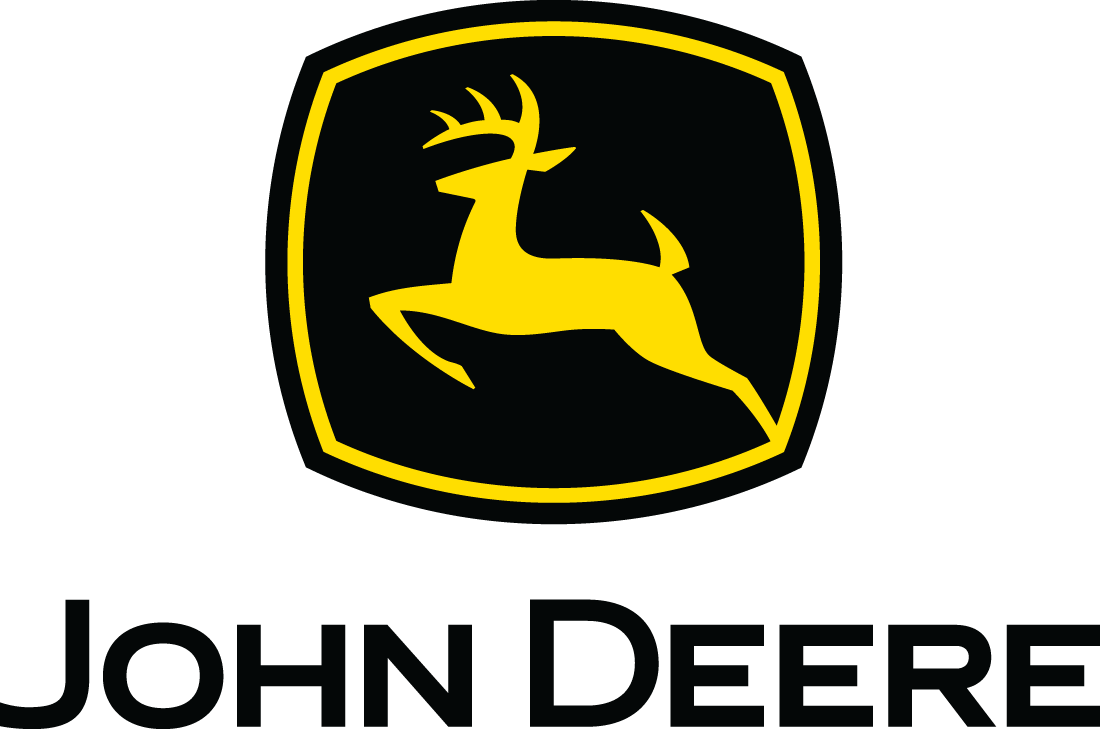
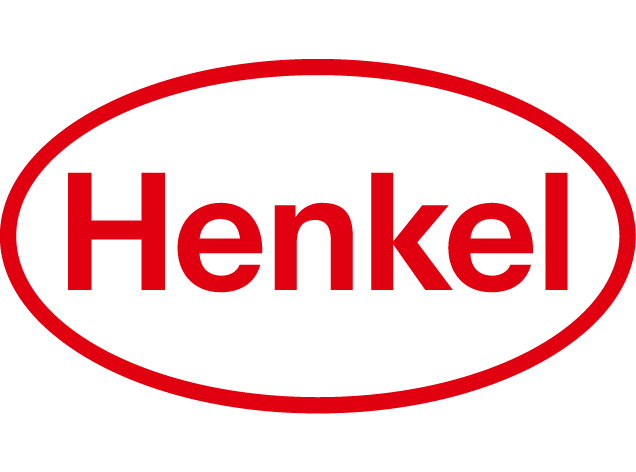
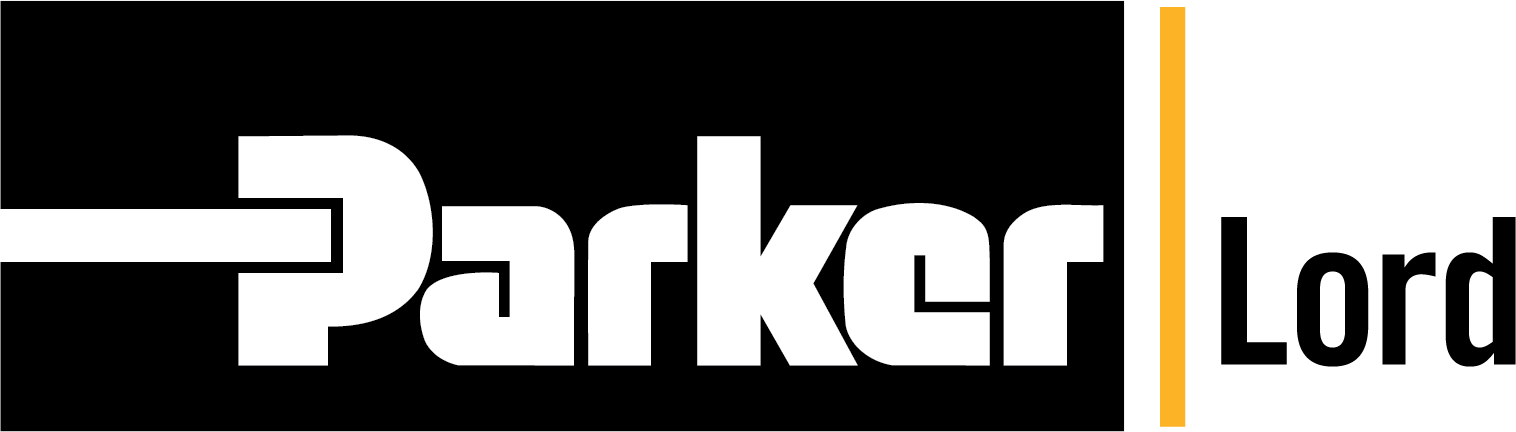
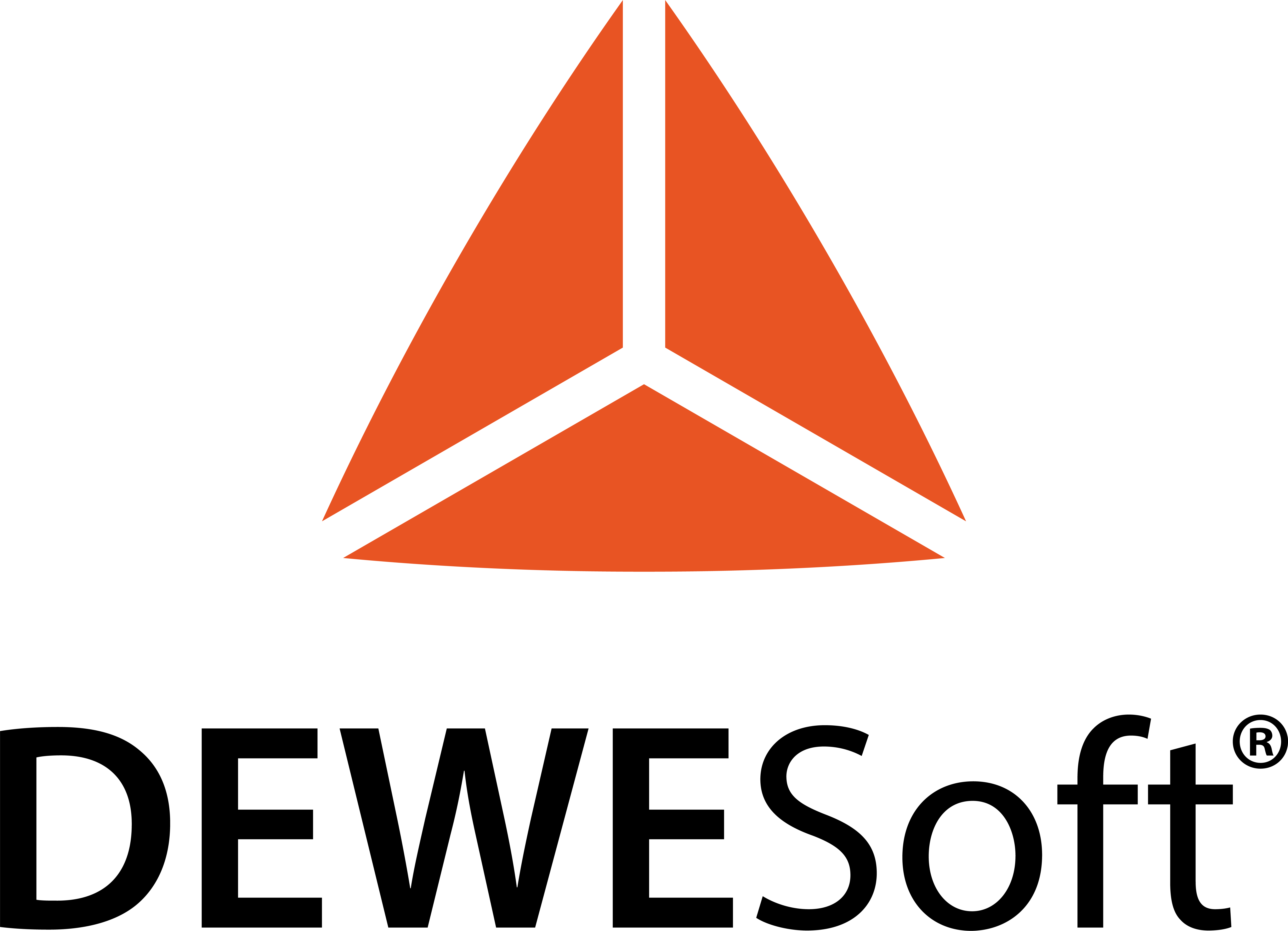
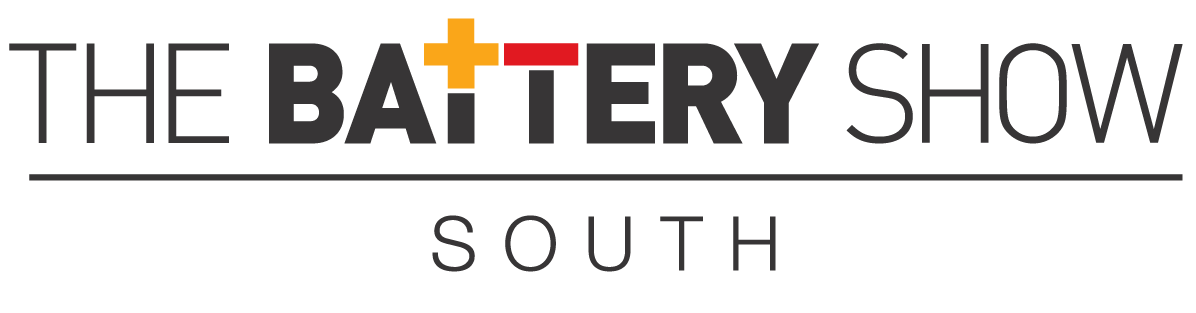
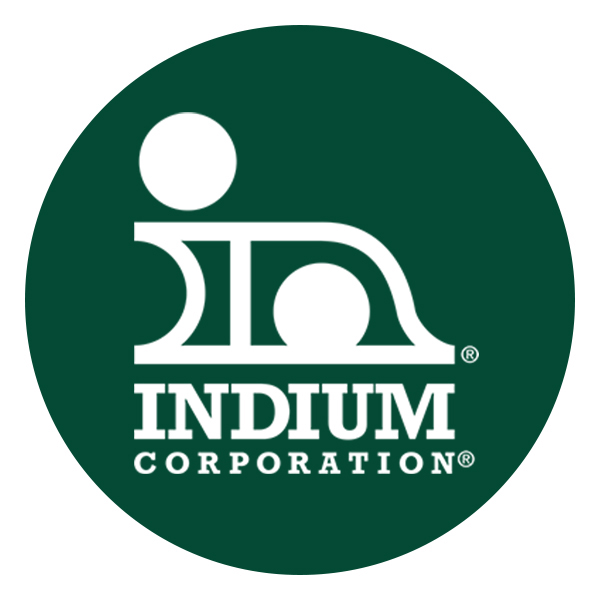
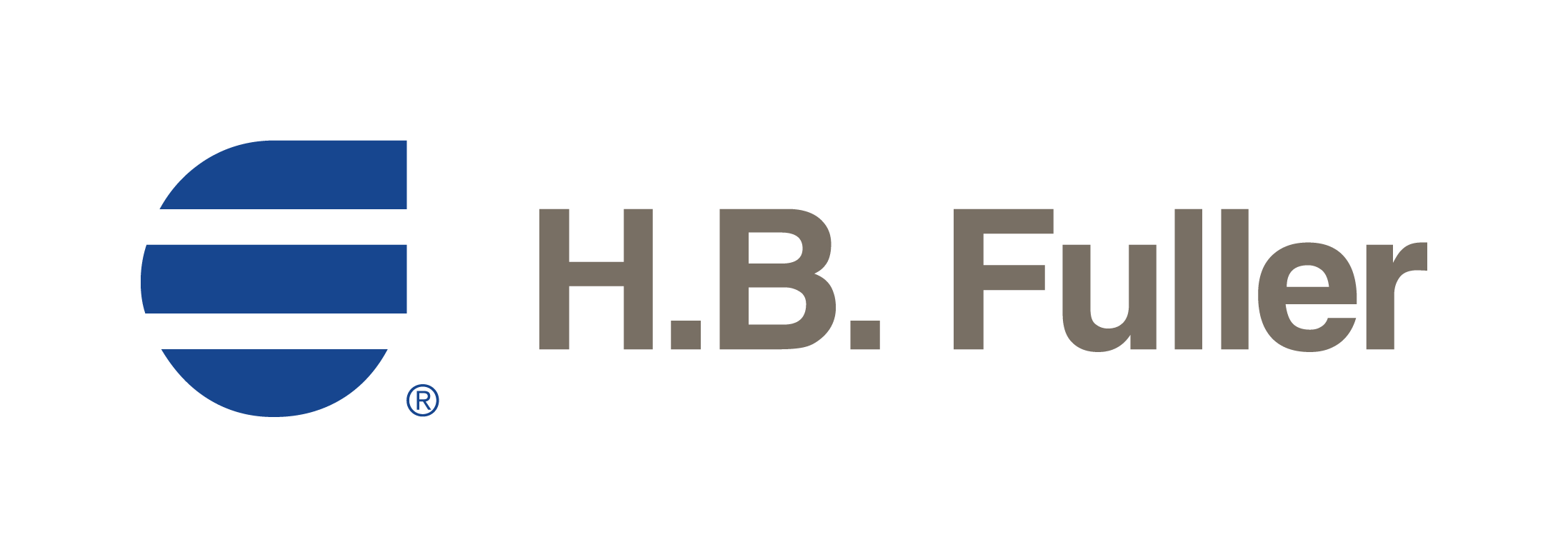