WAE EVR
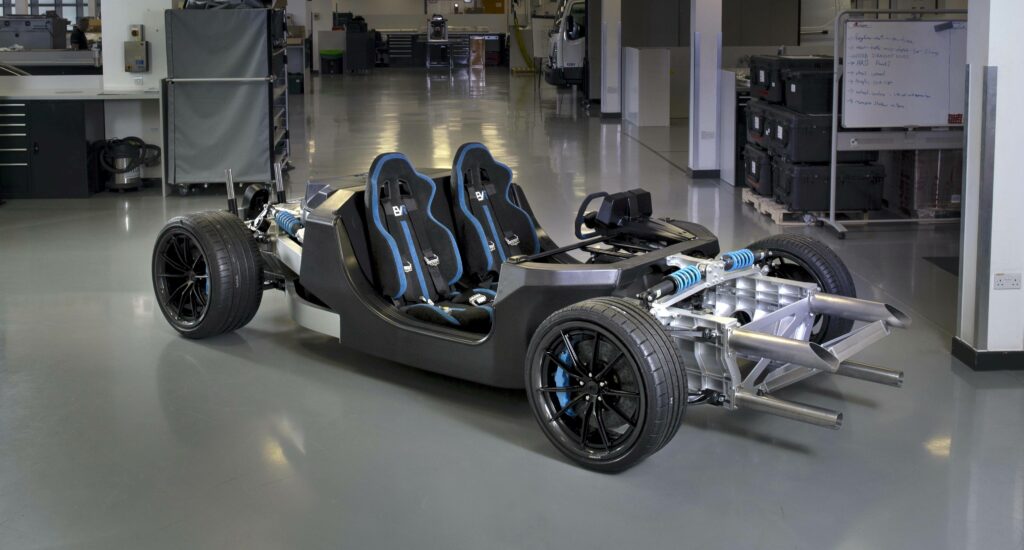
(Images courtesy of WAE)
All on board
Rory Jackson looks at this motorsport specialist’s latest skateboard for high-performance roadcars
Developing a new EV on a pre-existing skateboard-type platform offers benefits in terms of the associated times and costs of development cycles. As previously discussed in this publication, altering the wheelbase of a typical car or truck design by 12-15 cm can entail making so many modifications to the transmission, suspension, and centre of gravity (CoG) that a completely new vehicle design becomes necessary, sending the cost of the project into the billions and extending its lead time to 5-10 years.
The skateboard approach enables a chassis to be modularly tuned for the loading, propulsion and maintenance requirements of the end-user, leading to a far quicker and less expensive process than in conventional automotive r&d. This decoupling of the body from the chassis also allows production runs to right-sized, and for bodywork to be assembled in small regional factories close to their customer markets.
Despite all these benefits, however, skateboard platforms have not yet found widespread take-up among existing large automotive OEMs, many of whom have elected to stick with their usual (and arguably less efficient) ways of designing and engineering their EVs.
But as global EV industry observers will have noticed, a new wave of small-to-medium sized automotive companies is emerging, which means hundreds of new EV manufacturers who are willing to adopt new approaches to automotive design in a way that traditional OEMs are not. Many of them are therefore eager to partner with the right skateboard designer.
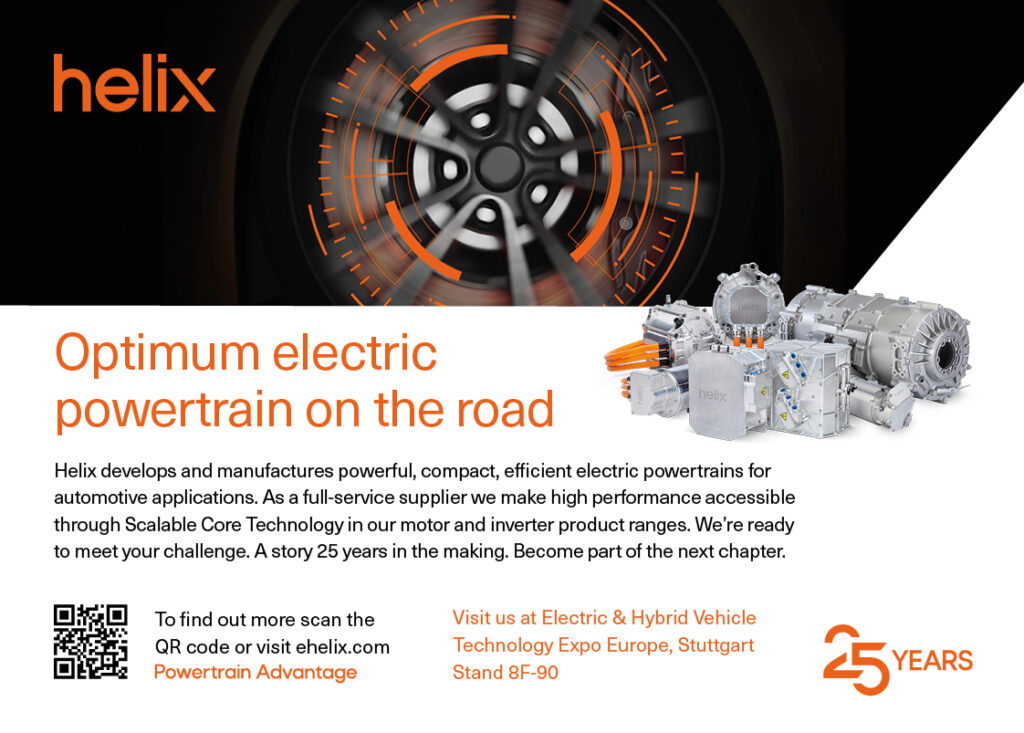
WAE (formerly known as Williams Advanced Engineering, though now not legally permitted to use the Williams name) is a case in point. Drawing on its experience in Formula E, Extreme E and so on, it has been showcasing passenger car platforms for several years, starting with the unveiling of the FW-EVX skateboard in late 2017.
The FW-EVX was designed as a lightweight, durable and scalable system intended for integration with conventional passenger car designs. It features a novel carbon composite chassis, with each cell in its lithium-ion battery being wrapped in carbon fibre boxes, as well as WAE’s patented Racetrak carbon fibre wishbone suspension.
In addition to the EVX and related projects, WAE has also worked on a number of two-seater sportscars over the past several years, including the C-X75 HEV from Jaguar and the all-electric Nissan Bladeglider proof of concept.
“Those kinds of projects and EV configurations led us to talking with a lot of prospective customers in the smaller, more of a start-up domain, who were looking to start manufacturing an original EV design, and in particular to bring a low-volume electrified ‘halo’ platform to life,” says Paul McNamara, technical director at WAE. The term ‘halo’ in this instance refers typically to limited-edition showstopper vehicles that some manufacturers will unveil to grab the attention of the automotive media and enthusiasts.
“The problem that all of them find is that the development costs of producing that initial EV are highly uneconomical, particularly for a low-volume product,” McNamara says. “Knowing that, along with our background in high-performance motorsport, we felt we could put something together that would serve this new generation of start-up OEMs, as a practical way for them to start on their low-volume sports EVs.”
From that came the EVR, a highly modular skateboard EV platform optimised for headline-grabbing electric supercars. The system was unveiled to the public for the first time at LCV-Cenex at Millbrook in 2022.
In its baseline configuration it features an 85 kWh battery that can be DC fast-charged from empty to full SoC in just under 20 minutes, and provides a range of just over 450 km between charges. Also, its powertrain is engineered for a maximum power output of 1650 kW, enough to enable a top speed of just over 400 kph and acceleration from 0-100 kph in just shy of 2 seconds. All this is contained within a platform weighing just under 1800 kg.
By developing and offering the EVR, WAE sees itself as providing the chassis and powertrain engineering in a base that has the flexibility to meet the body parameters of different start-ups. As a result, out of the 3 years typically required to develop a new low-volume EV, at least a year should be cut from start-ups’ r&d time and associated costs by building their halo on top of the EVR instead of developing their own chassis and powertrain in-house.
“Of course, the EVR also works as a platform for us to put different things on,” McNamara comments. “For instance, we have multiple powertrain solutions in mind but we’ll focus on discussing the powertrain configuration and subsystems we had on show at LCV.
At LCV, we talked about doing hydrogen-based propulsion systems, among other things, and the skateboard works as an r&d platform for developing and maturing a wide range of power technologies we will offer in the future.”
By using this approach, WAE hopes to offer its customers not a blank sheet in its EVR but rather a ‘menu’ of options across energy, power, and control technologies it has validated first-hand.
Development background
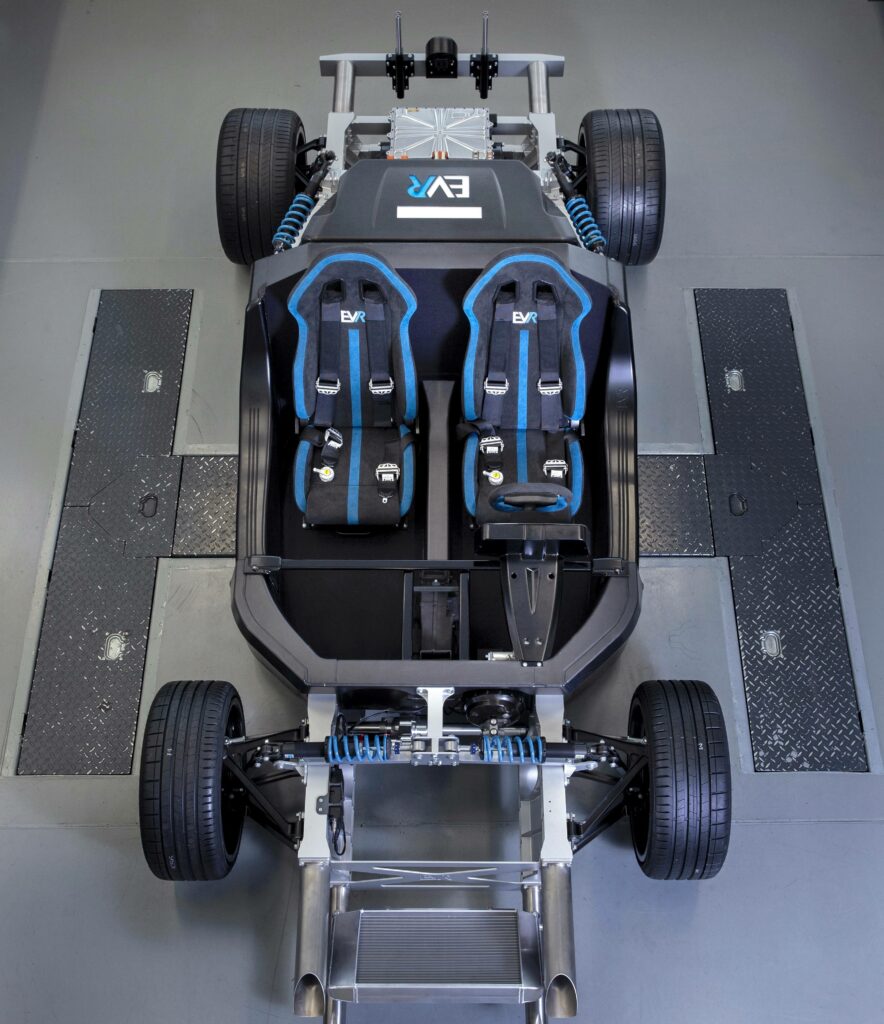
The EVR project was given the go-ahead in January 2021. McNamara says however that WAE had been looking at the general concept of a modular skateboard for limited-edition electric sportscars for a few years beforehand. Over the 5-6 months prior to January 2021 it was agreed that the concept was worth pursuing, the decision coming in time for the company’s annual budgeting plans in December 2020 to include funding for the project’s r&d.
“By that point, we had produced five or six clear and measurable car concepts, some digitally, some in physical form. One of them made it to the market as the EVX, and we learned a lot of useful learnings along the way from contributing to projects such as the Lotus Evija,” McNamara explains.
“Even though WAE is perhaps best known for its battery and powertrain technologies, we also have a vehicle design and production capability. We have a chassis team with skills in brakes, suspension and so on, and an aero team for active aerodynamics research, so we’ve always got some kind of vehicle activity on the go. So taking on the EVR as a project didn’t pose any particular change of direction for us.”
Naturally, developing the EVX (and its updated version, the EVX-2, produced in partnership with Italdesign) also yielded important lessons in the engineering of skateboard platforms. It showed WAE’s engineers that tuning a pre-existing skateboard platform to suit end-users’ high-level requirements, rather than designing a conventional chassis from a blank sheet to fit a list of lower-level specs, gave them far more freedom to innovate and experiment with battery technologies, materials, aerodynamics and other in-house specialisms in order to reduce weight and enhance efficiency.
Chris McCaw, technical lead for the EVR, recounts, “Development was very much an iterative process. We started with some initial targets for the platform, for instance the energy and capabilities of the battery pack, but over the course of the following 18 months we found that many customers wanted to build EVs on top of or around the EVR that they could then sell as products.”
McCaw cites the Deus Vayanne as the prime example of what those customers hope to achieve. It is a new EV hypercar that is due to be built using the EVR platform, with Italdesign also announced as a key partner in this project.
“Those discussions informed us more closely on some key ways to alter the base capabilities of the skateboard, particularly with regard to some slight boosts to the powertrain,” McCaw says. “And even though we didn’t start implementing those changes until maybe 6-12 months into development, the flexibility inherent in skateboards enabled us to mix in those changes without any setbacks.
“New electric motors, battery cells and other technologies are being launched almost every six months, so being able to adopt new solutions during the development process was something we’d anticipated from the outset. Compared to the powertrain specifications we’d initially targeted, we’ve since added maybe another 5-10% of power, energy and acceleration to what we thought it would be capable of.”
Although McCaw now has trouble numbering how many distinct iterations the skateboard went through, as different sections of the vehicle would evolve at different stages, he notes that they used at least five to eight different powertrain configurations – three of which did not even exist when the project began.
Similarly, he comments that drive-by-wire systems have only started reaching a level of maturity ideal for use in production cars in the past couple of years, whereas previously they might have been deemed sufficient only for technology demonstrators. They are therefore another subsystem that has been adopted into and iterated on the EVR in an ad-hoc manner.
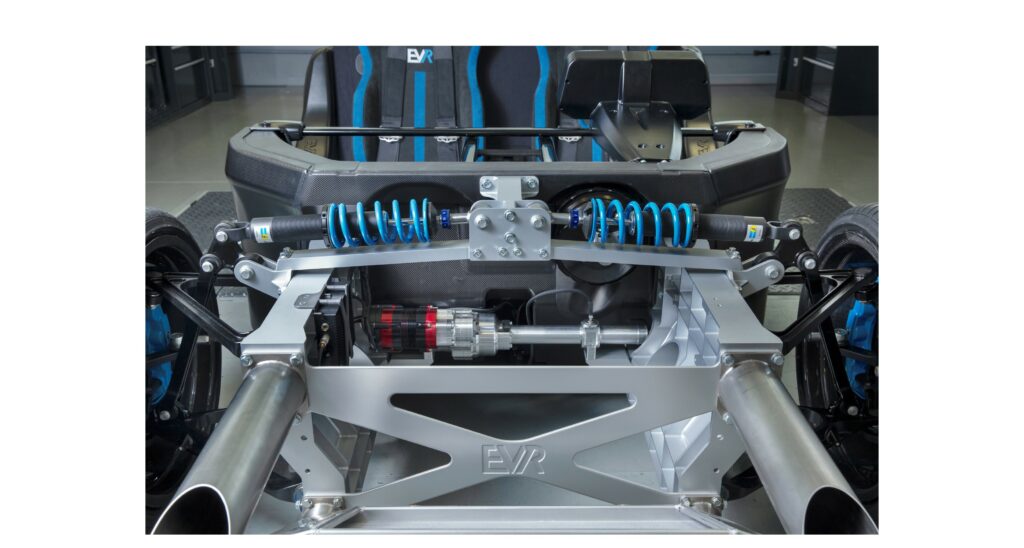
Structural and subsystem overview
The basis of the EVR is a wheelbase and track design that can be scaled to an end-user’s particular vehicle, and the main differentiator between the EVR and the EVX is that the former features a very low seating point for the driver and the passenger next to them.
“Many other platforms start with this idea of a tray of battery packs at the bottom of the platform, and a flat free-form space above that you can do with as you like, but that inherently pushes the driver up by at least 150 mm, maybe 200 mm typically, before you’ve even started designing the cabin,” McCaw explains.
For the EVR, the driver’s position had to be kept as low to the floor as possible: this is expected of supercar designs owing to the need to keep their CoGs low for good handling. Given how common this is across different sportscar models, WAE determined that it would be a common requirement of the EVR’s architecture.
Asking supercar customers to accept the replacement of an IC engine powertrain with an all-electric one is already a considerable request; asking them to then also accept the fundamental change in cabin placement and feel that would come from not having a low floor position for the driver could be asking too much of sportscar enthusiasts.
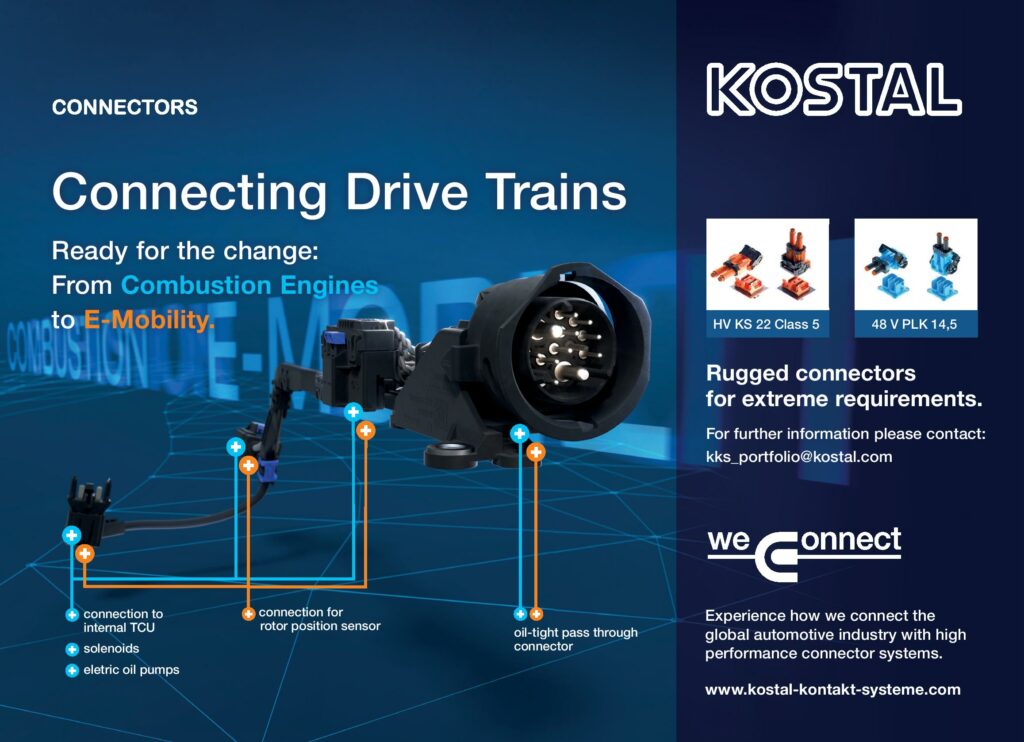
“The EVR is meant to be a basis of common components and a chassis that collectively works for some of the most demanding electric powertrain and vehicle driving profiles, and very early in development we did a lot of studies to benchmark what was on the market in comparable vehicles,” McNamara says. “We extrapolated from that how high-end automotive designs and engineering would be likely to evolve over the coming years, in order to create an architecture that would still work as a template for limited-edition electric sportscar designs coming out upwards of 5-6 years into the future.”
Around the time of those studies, electric sportscars such as the Pininfarina Battista, the Rimac C2 and the Lotus Evija were attracting interest, and compared with hybrid EV hypercars such as the Aston Martin Valkyrie and the Mercedes AMG One it affirmed WAE’s determination to go the all-electric route with the standard-issue EVR rather than offering a hybrid-electric configuration as the baseline (although a hybrid powertrain can be designed and installed on request).
As a result, the EVR has two seats with a low position, and 85 kWh of battery packs are installed behind the driver. Further back are the motors and inverters for driving the rear wheels in a single cylindrical housing. The Battista, C2 and Evija also provided benchmarks of the key performance parameters the EVR’s powertrain would need to have, particularly in terms of power output and acceleration.
“Beyond that, we’ve made certain design considerations that allow us to either take the conventional approach of a solid steering column passing through the bulkhead, and a conventional brake booster with pushrod passing through, or to go with the by-wire approach,” McCaw says.
“As we said earlier, drive-by-wire only started reaching production-level maturity in the past 2 years as far as we’ve seen, and some of our customers want to push the boundaries of technology and use innovative subsystems. But there are also others that want something more traditional; some have suggested they want hydraulic steering because they think the feel of that is above and beyond anything else that can be delivered right now.
“So, we’ve made sure that either conventional or by-wire systems for steering and braking can be integrated into the EVR without needing to redesign the whole front architecture of the vehicle.”
Carbon structure
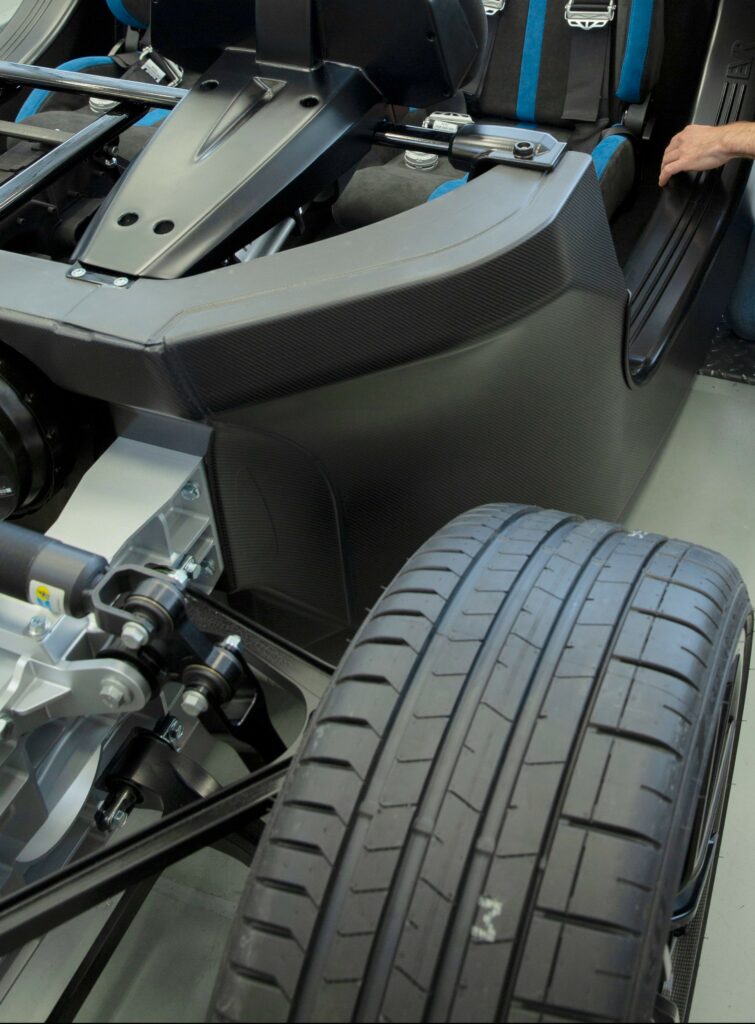
When it came to developing the structure of the EVR, WAE was initially tempted to build the skateboard around a carbon monocoque, as is typical for many of the aforementioned sports EVs. Depending on the model, they might also incorporate the suspension mounts and engine bay, for example.
Instead, however, the EVR’s structure is typically composed of 12 pre-formed carbon fibre modules, which are then bonded together separately using proprietary adhesives to form the complete tub.
“The advantage with that approach is that if a customer wants say a slightly different door seal design, maybe to suit their preferred egress route into the vehicle, then rather than having to start again and redesign the tub, we can just take that one piece where the doors mount, retool it, redesign it, put it back in, and then run an analysis to confirm that it works structurally,” McCaw says.
“We’ve engaged with a Tier 1 supplier [their name protected by NDA] specifically for their skill set in bonding together multiple different carbon modules. And in addition to considering the weave content of the carbon fibre and the lay-up analysis that goes with that, what’s becoming more prevalent is looking towards the end-of-life stage of the carbon fibre, and how we or our customers can make this a greener product beyond just electrification.”
To that end, WAE is investigating opportunities for the use of natural fibre composites or recycled carbon fibre, and is eyeing the possibility of initially doing so in parts of the EVR (or other vehicles in the future) that are not structurally critical, for instance using chopped-strand SMC (sheet moulding compound) in some of the panel work.
It is also researching the availability of more sustainable resins such as bio-resins, as well as easier recovery of the material’s fibre constituents by looking to use thermoplastic resins in applications that can be melted or otherwise separated from the carbon fibres to enable them to be recollected at end of life.
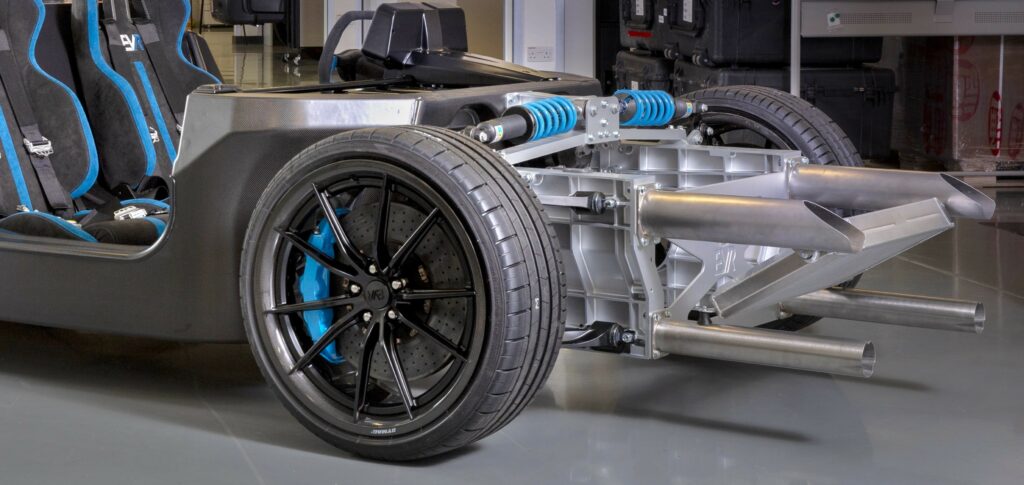
Metal components
“The carbon tub is cut off at the belt line, just at the bottom of the A-pillars and B-pillars, and from there we’ve opted to go with a metallic upper structure,” McCaw says.
“There’s a metallic roll cage, which allows us a certain flexibility regarding door closures, both for when customers want something conventional like a gull-wing design or something different, like a dihedral design. The hinge location and where the door seal runs is of course fairly flexible since we haven’t tooled it into the fundamental carbon moulding of the structure.”
The front and rear structures (forward and aft of the central composite tub) are also metallic, again to allow redesigns, ordering or cutting of new structural architectures, particularly for new wheelbase and track concepts, without needing to resort to the expense of new moulds for the carbon. It also means that new side parts such as metal castings can be easily added.
McCaw says, “It’s always interesting with multi-material structures like this, when you’re coupling metals with composites and trying to get them to work. Because, for instance, they typically have different rates of thermal expansion and contraction, and they can suffer galvanic corrosion as carbon reacts electrolytically to certain metals. Those kinds of problems need to be considered with every simulation, every iteration – we can’t just bolt a metal front end onto a carbon tub and hope for the best.
“First, the tub needs metallic inserts that we bolt through to. Then, on top of that, those metal parts need to be either coated in glass before they’ve been bonded onto the carbon, or if they’re aluminium parts then we need to add an appropriate coating to change the electrical differential between the carbon and metallic parts.”
Most of the metal parts are indeed aluminium for high strength-to-weight, although a significant proportion is also made from steels, particularly high-strength steels, as they can offer advantages such as better predictability and hence control of how structures will deform and collapse in response to impacts.
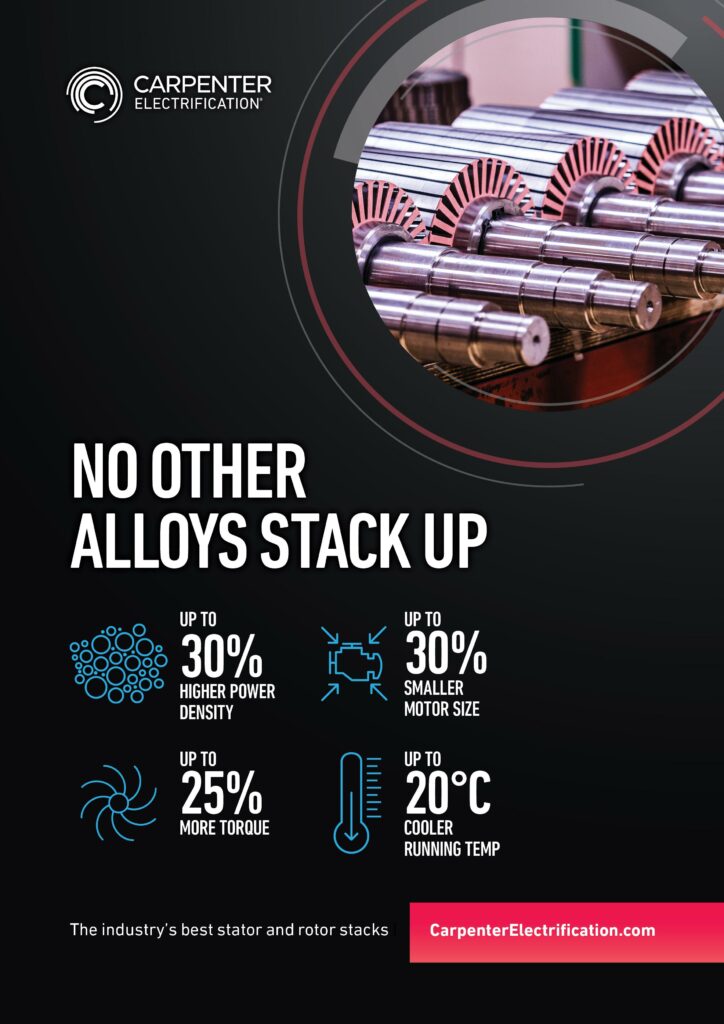
The metallic crash tube structures extending from the front of the chassis are likely to be application-specific, and developed in the final stages of each EVR platform’s customisation, when the customer is expected to finalise and install their own bodywork around the skateboard.
At that point, WAE will carry out detailed crash analyses through simulated and physical crash tests to see not just how the crash tubes crumple but also what contribution the body makes to the deformations. This can then inform steps for re-engineering, for example by identifying where strength and resilience might be removed from the crush structure or the underlying platform, in order to take out as much weight as possible while still maintaining levels of performance and safety for the customer.
“And outside of the carbon and metal parts discussed so far, the chassis components themselves can be anything, from quite conventional coil-over dampers to an active air suspension,” McCaw says.
“One thing we’ve tried to do at the rear, which is quite unique from a chassis suspension perspective, is to orient the dampers down the side of the vehicle rather than vertically or across the car, again just to give us that flexibility of extra powertrain or battery pack space at the rear. Initially we thought we’d just put more packs there, but we’ve since shown variations of the EVR where we’ve got our hydrogen range extender integrated, so we’ve installed hydrogen fuel tanks where traditionally a cross-over suspension architecture would go.”
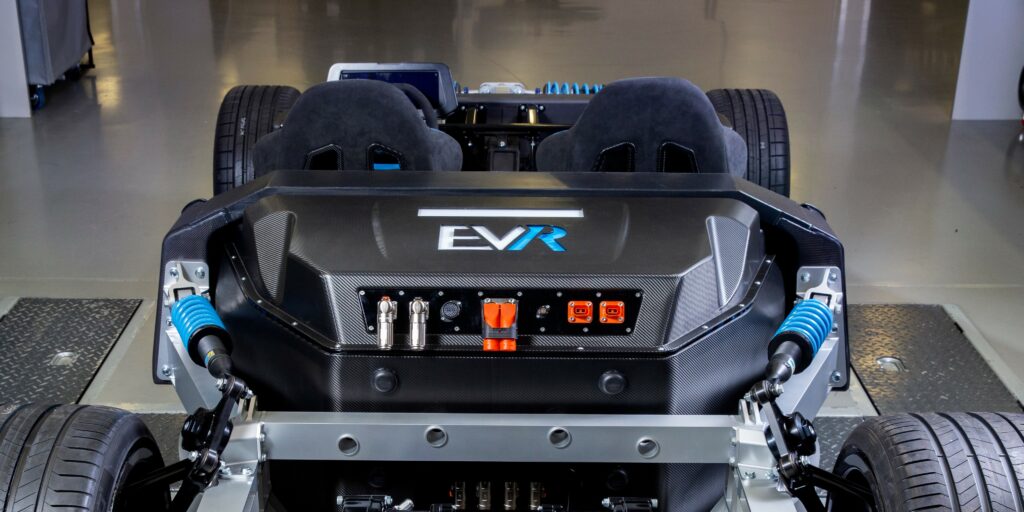
Wheels
Like the crash tubes, the wheels vary between versions of the EVR.
For instance, the skateboard has been displayed with carbon rim wheels, for their aesthetic qualities. “We know we’re going to be selling these cars at six-figure prices and above, so the styling and perceived value of these products becomes important from a design perspective,” McCaw says.
“However, some drivers will want to take their sports EVs out to tracks, and they’ll want the rolling mass to be as light as possible. Some magnesium wheels also offer good weight efficiency.”
In addition to wheel and rim materials, the size of the wheel is also likely to vary, with a major consideration during development having been the size of the smallest wheel that WAE would be willing to offer on the EVR. Track-focused hypercar drivers for instance will probably not care for the 21-23 in rims that auto stylists insist on pushing; they will more often opt for smaller wheels, which then places constraints on the braking package, especially with regard to the discs at the front.
“Obviously, at this level of technology, CCM-R (carbon ceramic material brakes produced originally for the racing market) discs with six-pot calipers are what’s expected, and that will mean that going anywhere below 19 in wheels will become very challenging,” McCaw says.
Pack-to-body battery
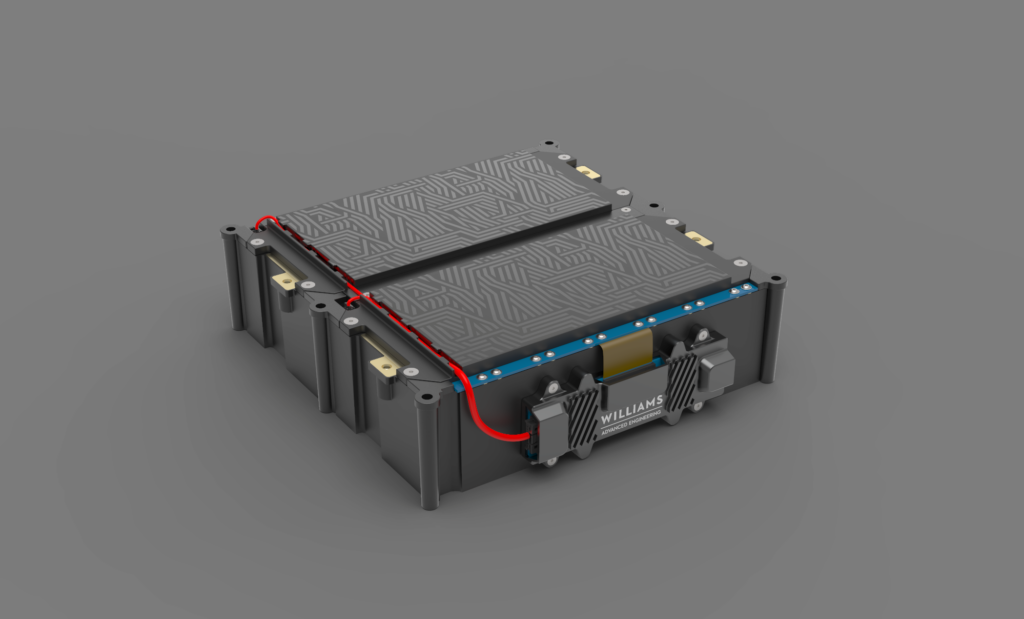
The EVR’s battery pack is built around 21700 lithium-ion cylindrical cells, as well as a module design supplied by Hyperbat that WAE has tested and validated in-house. “It’s a semi-structural module carrier inside the pack, with a composite housing around the pack, and that all creates a very rigid structure for the battery which ties into the composite tub and the rear metal structure,” McCaw says.
“By using the pack as a semi-structural member – or in a ‘pack-to-body’ configuration as we call it sometimes – we avoid the weight of a dedicated metallic pack housing.”
WAE also anticipates that using 21700 cylindrical cells will help it avoid major changes to its manufacturing and integration lines in the future, given that this form factor is widely expected to remain a standard for many years to come. The exact cathode and anode chemistries remain undisclosed, although WAE describes the cell as a new one supplied by an organisation with whom the company collaborates.
“We provide them with forecasts of what the EV market is likely to want within the next few years, and in return they can supply us with unique cell chemistries that are still in the development stages, and not yet necessarily a COTS system available to others,” McCaw says.
“When faced with the trade-off between energy and power in cells, we’ve tended towards a chemistry that can deliver a consistently high rate of power, and that’s best for their life cycle given how they will be used. Our motorsport background made us to look into certain pouch-type cells that have a very high power output, but they don’t have the life cycles and durability that a road-oriented vehicle like the EVR does.”
Various cell types were therefore evaluated against expected drive cycles, with WAE’s vehicle dynamics team simulating how they would perform within known power cycles (such as fast laps around the Nurburgring race track), then cycling the cells through those simulated routines in test rigs to directly observe the rates at which their capacities degraded after, say, 1000 simulated laps of the Nurburgring.
“Energy and range can’t be ignored of course,” McCaw says. “Plenty of drivers will want to drive for a couple of hours per day, so 80-90 kWh was ideal to ensure the kinds of 400-500 km between charges we anticipated.”
The BMS has been optimised through pack simulations and digital twinning to determine how the lives of the cells can be maximised through balancing of voltages, currents, temperatures and other parameters. Predictive analytics are embedded into the system to reprofile its charging, discharging and balancing behaviours after 10-20% of the cells’ expected lifetime, in order to improve the longevity of the overall pack against the usage characteristics up to that point.
The pack is designed to a nominal 800 V (ranging from around 900 V at a high SoC down to roughly 550 V at low SoCs) to match charging infrastructure and how WAE sees recharging stations evolving. A COTS onboard charger is installed at the back, although many users are in fact expected to decline the mass and complexity of AC-DC onboard chargers and opt for fast DC charging instead, or to use a comparatively lighter 400-800 V DC-DC for slower DC charging stations, as many EVs in future are expected to integrate this type of converter as standard.
“In fact, at present the modules are assembled together in what we call a split-pack architecture, which allows us to cut this 800 V pack in half when we’re charging, so it becomes two 400 V packs linked in parallel,” McCaw explains.
“That allows us to charge at 400 V without even needing a 400-800 V DC-DC. That’s going to be a critical battery r&d route for us, because there’s an industry-wide problem of compatibility between charging stations.
“It’s not like IC-engined cars, where you know every petrol nozzle is going to fit; there needs to be compatibility and communication between the vehicle and the charger, and making that possible on a global scale is something OEMs are struggling with. Fortunately, some test facilities in Europe are now installing what are effectively banks of charging stations from all the suppliers they can, so that when big OEMs or smaller teams like ours turn up, there’s something like 15-20 different chargers for us to test compatibility with.”
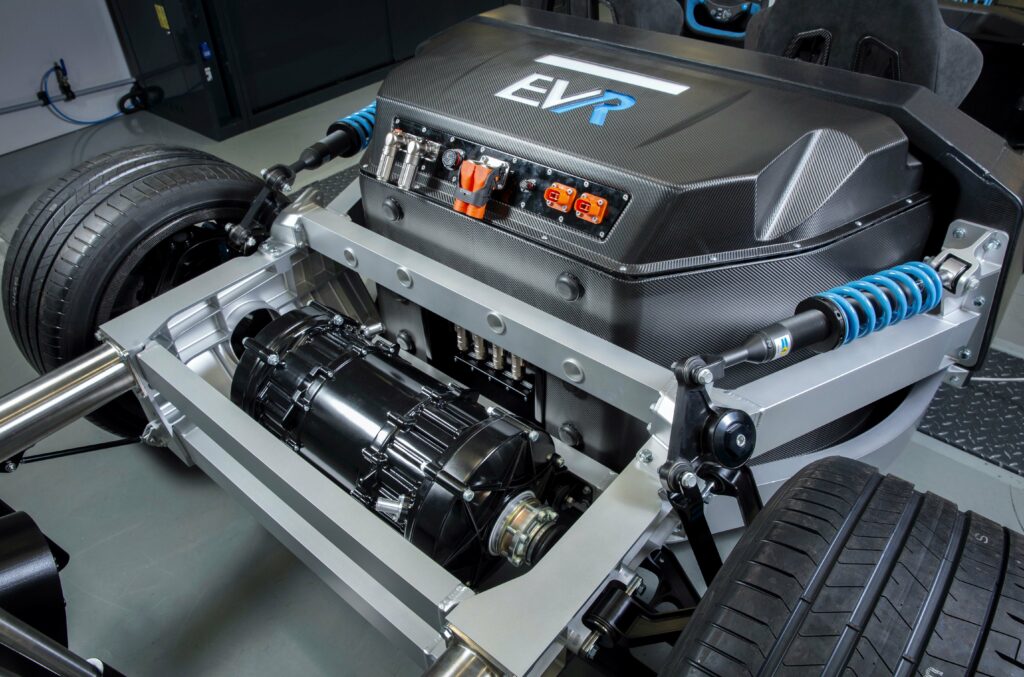
Battery thermal management
A standard water-glycol system is used to cool the EVR’s packs, rather than immersion cooling or the dielectrics that would entail. Although WAE has plenty of experience in immersion cooling, it opted for this more tried and tested thermal management approach that had been validated with the battery module’s design.
Modules are installed back-to-back to allow sharing of cooling plates between them, as is increasingly common in the EV world, although WAE also installs a system of valves throughout the plates and passages to change the direction and routes the coolant takes.
The system also allows coolant pressure to be concentrated at different levels of the pack and modules, so that the BMS can reroute and focus cooling as necessary.
For final heat exchange, radiators are likely to be installed at locations chosen for their aesthetics and aerodynamics as much as thermal efficiency. A front radiator has been shown on display versions of the EVR, but as it and other EVs typically no longer integrate a frontal IC engine, this is entirely a style point and not at all necessary.
“Rather than sticking a radiator at the front and having coolant hoses running the length of the EV back to the battery pack and powertrain, it would perhaps make more sense to have multiple smaller radiators dotted around the rear of the vehicle, potentially taking air from underneath the car and from the wheel arches, saving weight and avoiding potential failure points by using very short coolant lines,” McCaw says.
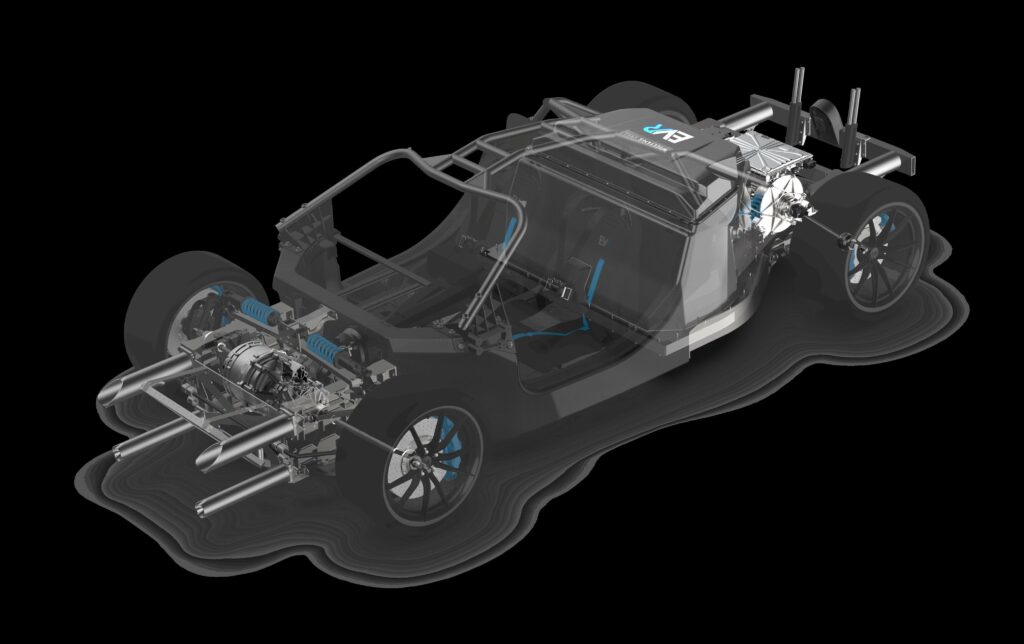
Integrated powertrain
“As I said, we’ve gone through maybe eight different powertrain configurations, and to do that we approached a considerable number of powertrain suppliers who were offering different things,” he continues. “We’ve looked at several set-ups that had separate motors and inverters, and evaluated the packaging implications of that type of integration, and we have also investigated fully integrated motor-inverter solutions.”
At the time of writing, the powertrain on the baseline EVR was a fully integrated package with two inverters and two motors – one pairing for each rear-wheel drive. This gives fully independent torque vectoring to both the rear-left and rear-right wheels, although WAE is happy to integrate all-wheel drive on request thanks to the space available in the front of the chassis.
DC power passes from the battery to the large, cylindrical enclosure on the back of the vehicle, and within that housing the three-phase current is able to run from the inverters to the motors via busbars, without the need for cabling (and hence without any of the weight, copper losses or potential points of failure that these could represent).
“It also saves us the complexity and weight of all the additional HV connectors that separate inverter-motor installations need,” McCaw says. “Right now, with the standard EVR, there are four silver connectors coming out of the back of the battery pack, which enable a DC supply from either side of the battery pack – two from the left and two from the right.”
Directly behind the battery connectors are the two inverters, seated back-to-back inside the central part of the powertrain cylinder. They are recognisable as the very smooth middle section, whereas the ribbed sections on either side house the motors.
Outboard of these sections are the epicyclic transmissions that form the final part of the powertrain and output the final torque and speed for the wheels. WAE describes these as single-speed systems, heavily influenced by work on previous hypercar programmes, with the epicyclic layout having been chosen to suit the package constraints of the vehicle.
“We are developing a novel two-speed concept, but can’t share any details about it at this stage due to IP,” McCaw adds.
Like the battery, the inverter is also an 800 V system; 800 V has been the power supply target across the board in order to eliminate the need for DC-DCs that would take up additional volume and weight as well as leading to minute losses regardless of conversion efficiency.
“At the moment, the inverter runs using silicon carbide [SiC] transistors, but we are also working with other suppliers that are using GaN [gallium nitride] solutions in power distribution boards, and as we see technology moving forwards in the next few years, we see the price point of GaN really starting to shift,” McCaw says. “That’s likely to stem from the increasing availability of materials and parts and falling production costs, but for now the SiCs are a must-have.”
Although there is a debate between proponents of SiC and those of GaN, for WAE there are three key parameters that help inform its ultimate decision as to which it will primarily offer with the EVR – availability, cost and the architectures of the inverter systems that can be achieved using the chosen transistors.
McCaw explains, “Each architecture can have slight differences in critical variables such as where losses are coming from. Inverter suppliers are doing a lot of work at the moment on issues such as how to stack their switches, and having multiple different switch levels of GaN systems on top of each other, to give smoother, more sinusoidal waves for the motor.
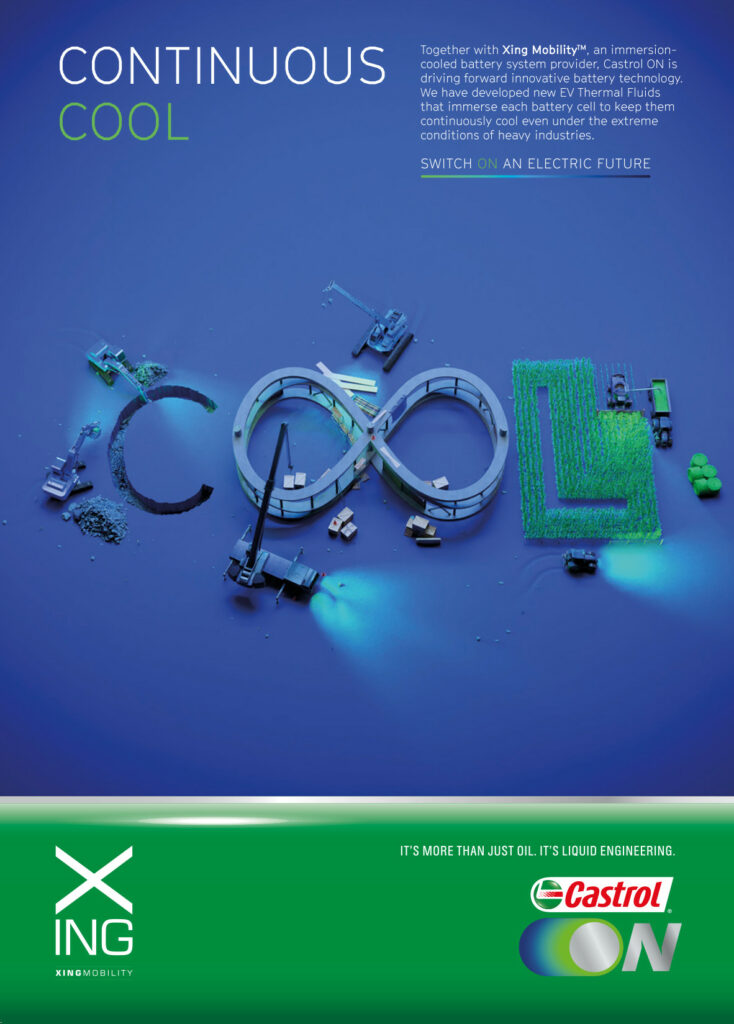
“That leads to lower hysteresis losses in the motor and in turn higher thermal efficiency. It all starts to add up when you look at the efficiency of components, and when we look at the market we see inverters that can now run at 98-99% efficiency and motors at 96%. But getting that last 1% is incredibly difficult, so we’re willing to try out new and relatively less mature technologies if it means we could offer that.”
While WAE declines to disclose the precise topology of the SiCs used in the inverter, it says the cylindrical housing has posed a considerable technical challenge to make it a fully integrated and simplified part of the powertrain that can be handled, installed and removed easily.
“The rear suspension architecture is designed to have the springs running up and down the sides of the vehicle, rather than across the top, and in the show car at LCV we installed an onboard charger in that top space,” McCaw notes.
“That was a rectangular package, and with it we essentially showcased that two or four conventional, rectangularly enclosed inverters could be packaged across that space at the back, with the motors then seated underneath. So we have quite a few in-house design templates already with different approaches towards the kinds of powertrain sub-components or architectures that integrators might want.”
WAE is similarly agnostic regarding the EVR’s motors, so the platform is capable of using induction motors and switched reluctance motors for example; at the time of writing, the two baseline motors were permanent magnet AC machines. They are radial flux designs with their rotors running internally to their external stators, and integrate what McCaw describes as “the latest high-end, neodymium-type rare earth magnets, in order to deliver enough power in a compact package”.
The company notes however that a growing number of its customers want to use alternatives to rare earth magnets, be it for sustainability or resilience in supply chains. As a result, it has designed the back of the EVR with packaging space for potentially larger motors built using less power-dense magnetic materials but which can still achieve levels of power appropriate for sportscars.
As with the battery packs, WAE has sought to stick with tried-and-tested water-glycol cooling for the powertrain, and it intends to stipulate to suppliers that these systems must be packaged in a manner that shares common cooling channels between all the different systems and sections, even if the motors, inverters and gearboxes come different suppliers.
“And because of the software integration in the powertrain, we can effectively ask the inverter manufacturer to supply a ‘dumb’ system where we just request a desired level of torque, and they design it to the necessary current for that,” McCaw explains.
“We then use our own algorithms to establish how the motors and epicyclics need to behave in order to optimise the torque output and vectoring for different performance targets. That can be for safety reasons, handling and dynamics, or to make it understeer. Having a range of drive modes is pretty common for production EVs now, so we’ve made sure to cover that for our customers.”
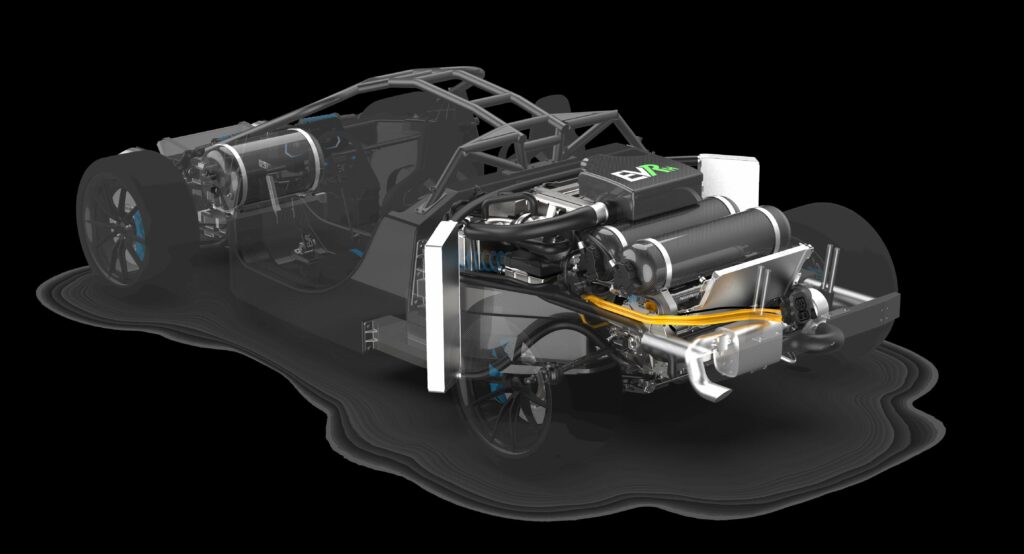
Future plans
WAE sees three main configurations being offered for the EVR.
The rear-wheel drive is the smallest and lightest arrangement, as it leaves the most space and freedom for redesigning different sections of the EVR or adding components such as supplementary battery packs or range extenders. It is the powertrain most often showcased by WAE and is something of a de facto baseline.
“The package we have at the rear could be moved to the forward wheels for front-wheel drive, but because of weight transfer during hard accelerations, we’ve found it doesn’t actually deliver all the torque down to the ground, so at the very least it would make sense to downsize the motors for a front-drive version, with maybe 66-75% of the torque and power of the RWD, and that would then allow opportunities to take out weight,” McCaw explains.
“That’s essentially how we would do frontal motors for a 4WD configuration for across-the-board torque vectoring, which is the second powertrain option we’ll offer.”
Third is a single central drive motor at the front (along with the RWD) installed either through a limited-slip differential or potentially a clutch-pack torque vectoring differential. That would reduce weight, cost and complexity at the front compared with the 4WD approach, while still essentially delivering a 4WD solution, albeit possibly without all-wheel torque vectoring, depending on the exact differential installed.
“The torque vectoring you’d get from just a single axle actually delivers 80% of the benefit you’d get from all-wheel torque vectoring, particularly in normal track driving conditions,” McCaw notes.
“The all-wheel torque vectoring really comes into its own in adverse conditions, such as wet or icy weather or if there’s loose gravel on the road. But if you think about the kinds of integrators who will build upon the EVR, and how their type of customer will probably use those cars, it’ll be a bit like the Ferrari FXX – the three-motor configuration will probably be the optimal choice.”
Although there is already a lot of flexibility in the powertrain configurations that WAE can implement on the EVR, McCaw notes that in-wheel motors do not make much sense for the skateboard. “We’ve looked into in-wheel motors for the EVX, but for the power, torque and speed we want on the EVR, we need inboard motors; there just isn’t an in-wheel motor yet that can deliver those targets.
“And in-wheel systems rely on having quite a large seal around the outside of their hub motor to stop the ingress of the water, grit and other road detritus they’d otherwise be very exposed to. The large surface contact area between the seal and the rim going around it becomes critical at that point, and the larger the diameter of the wheel, the larger and more hazardous the differential of speed at the seal interface.”
As mentioned, WAE has also begun researching and showcasing range extenders based on hydrogen (with the company planning to use green rather than blue or grey hydrogen). A fuel cell is currently in development in-house to allow WAE’s engineers to explore future routes towards sustainable, long-range electric driving.
Specifications
WAE EVR
Skateboard-type platform
All-electric
Rear wheel drive
Battery energy: 85 kWh
Maximum power output: 1650 kW
Maximum range between charges: about 450 km
Maximum speed: about 400 kph
Mass: about 1800 kg
ONLINE PARTNERS
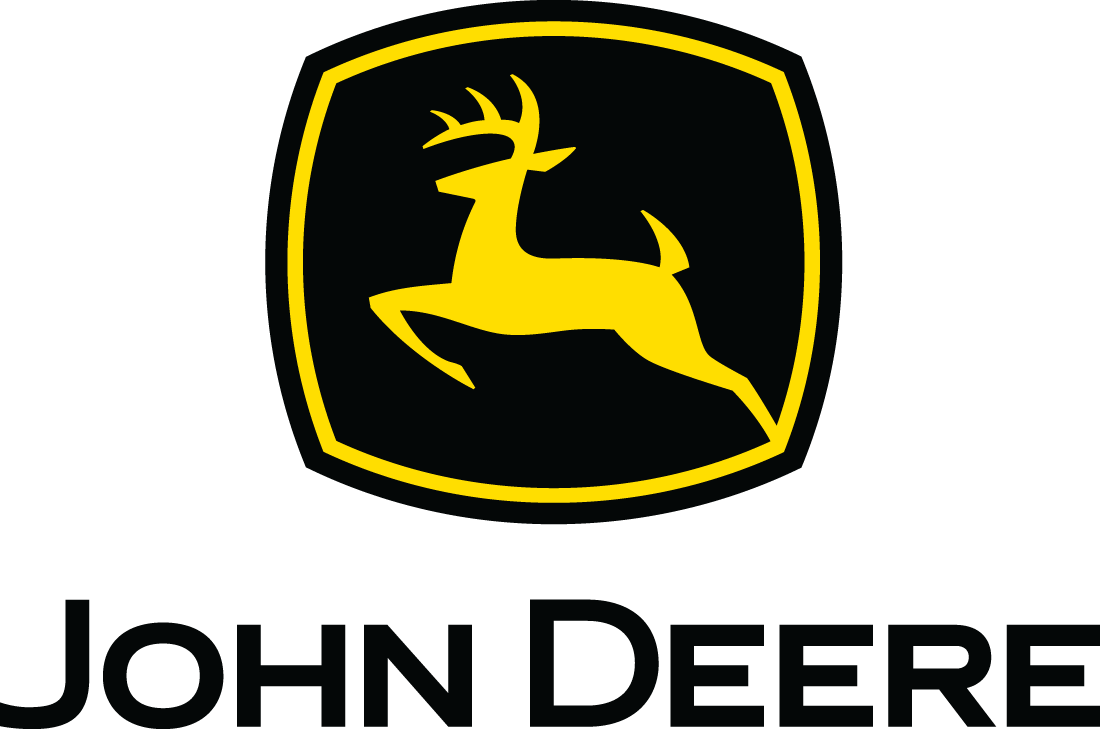
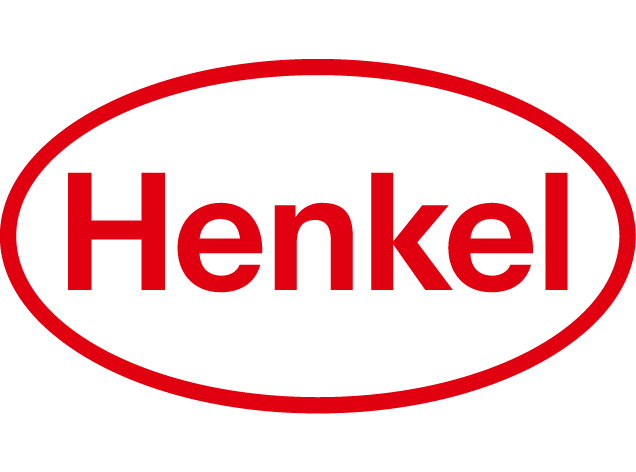
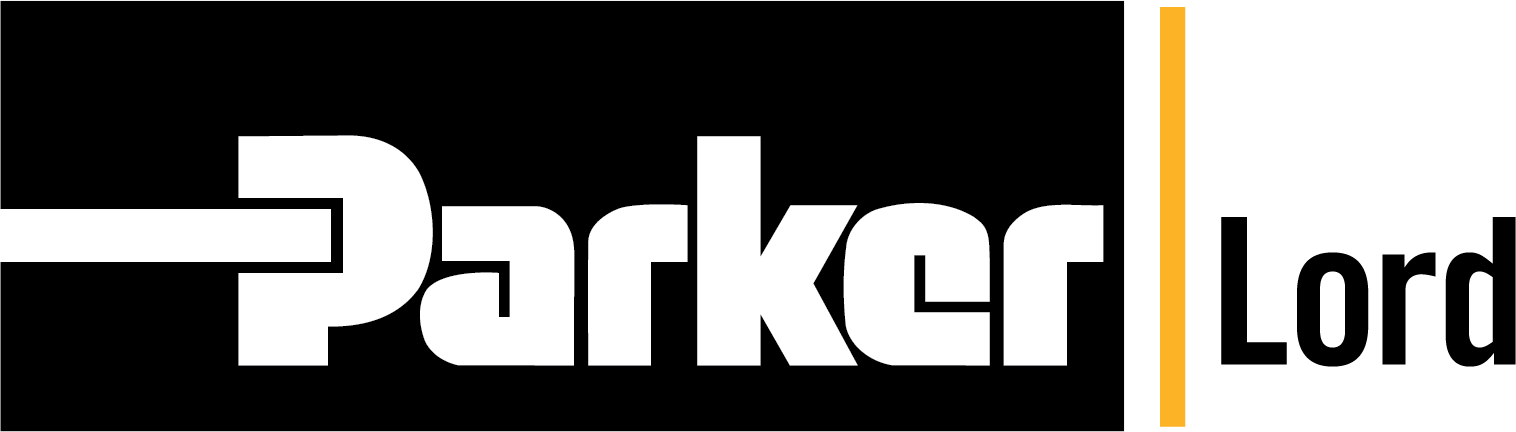
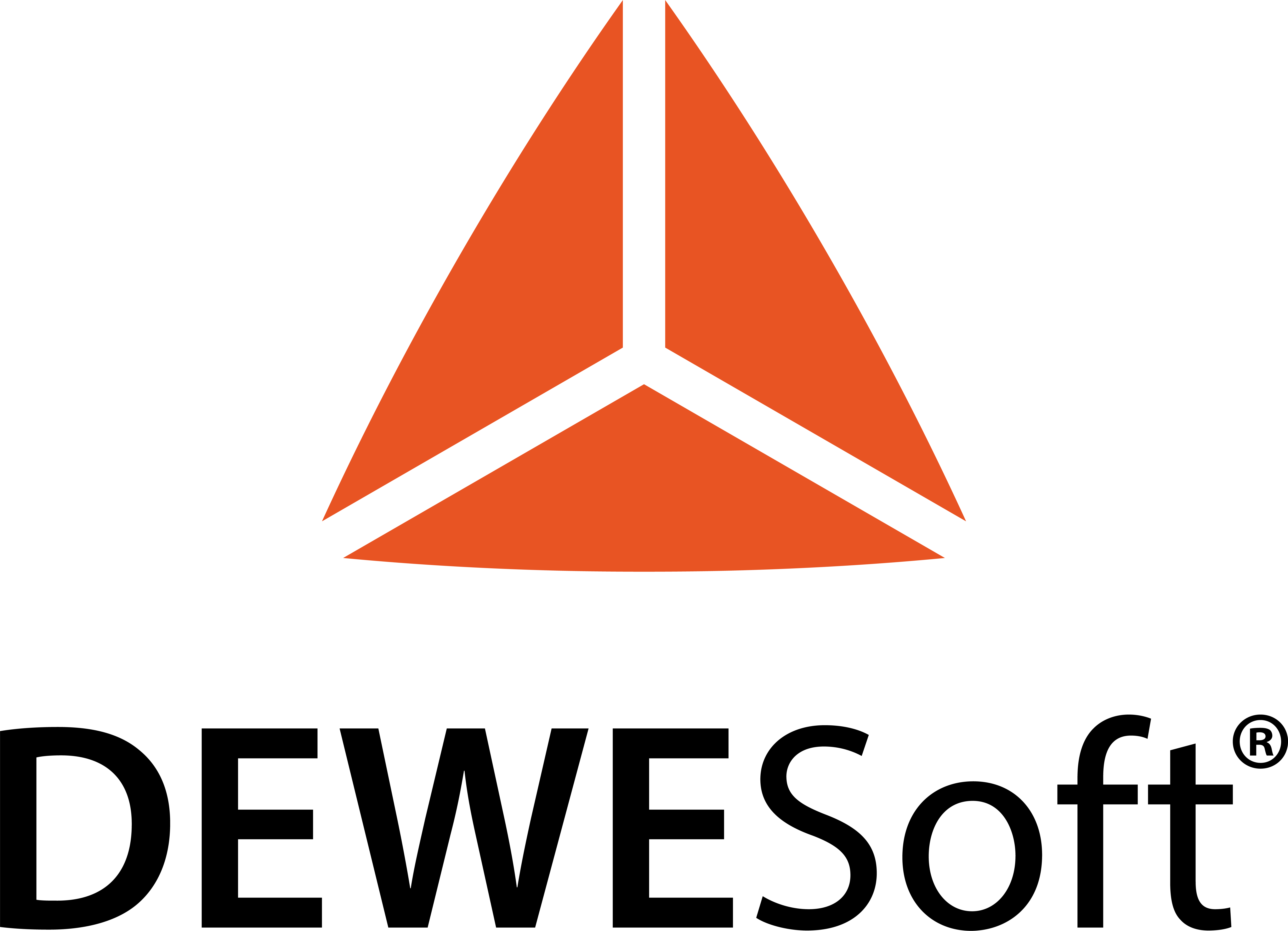
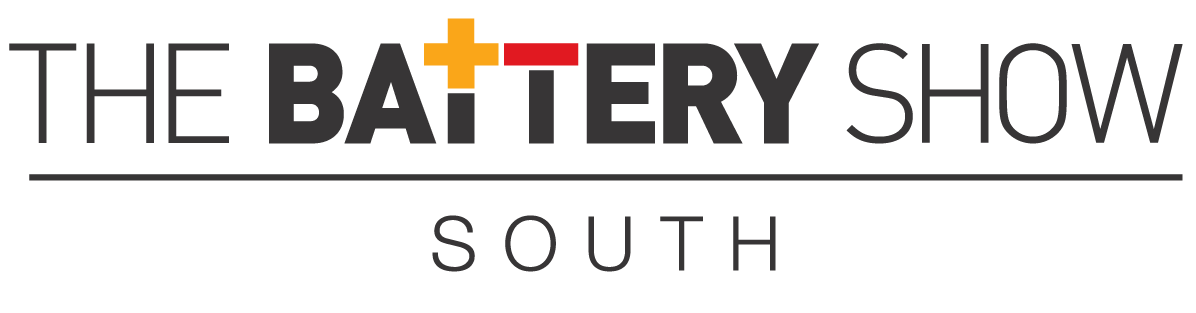
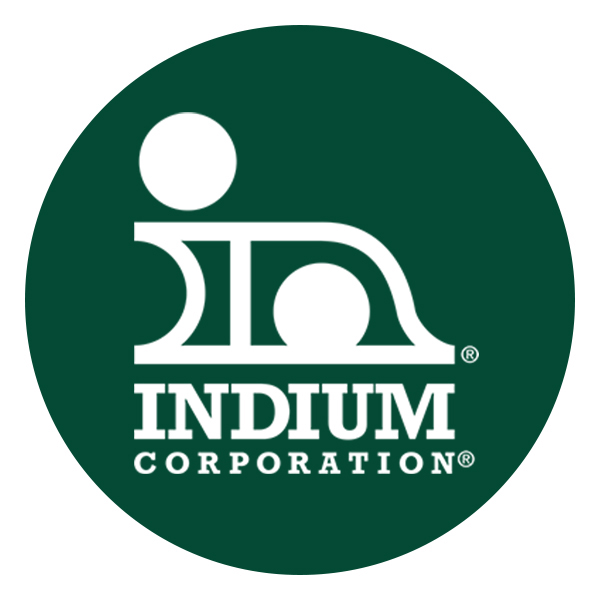
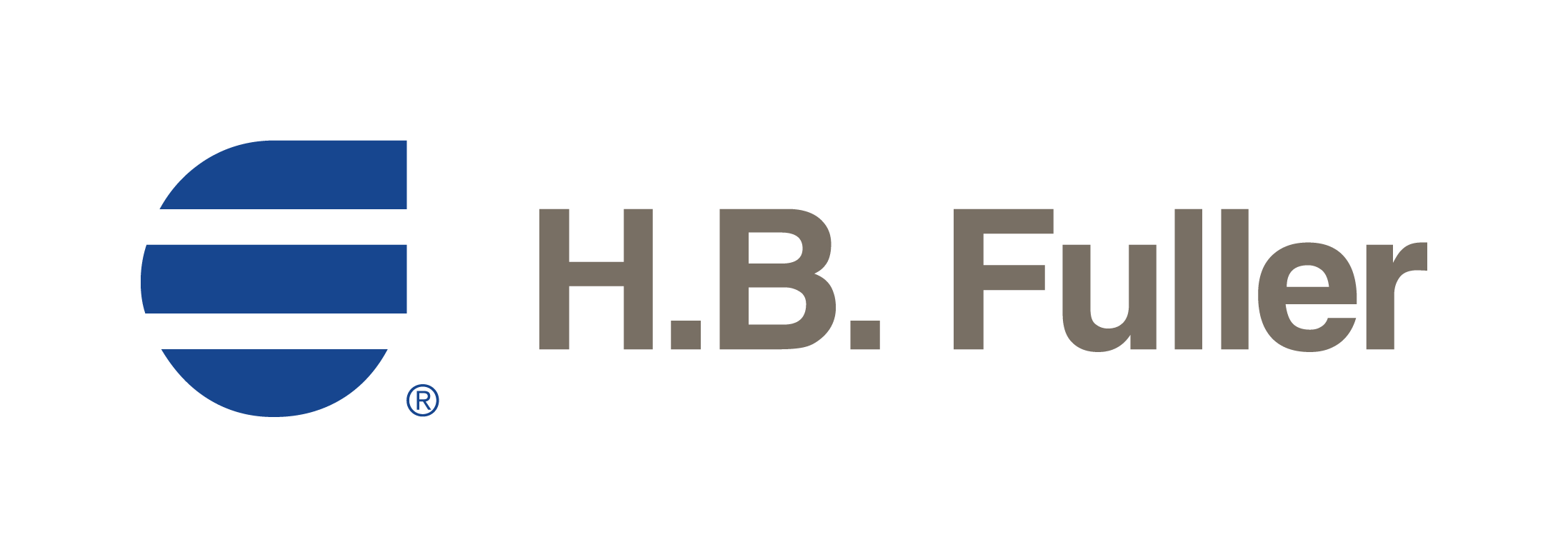