vRbikes vR3
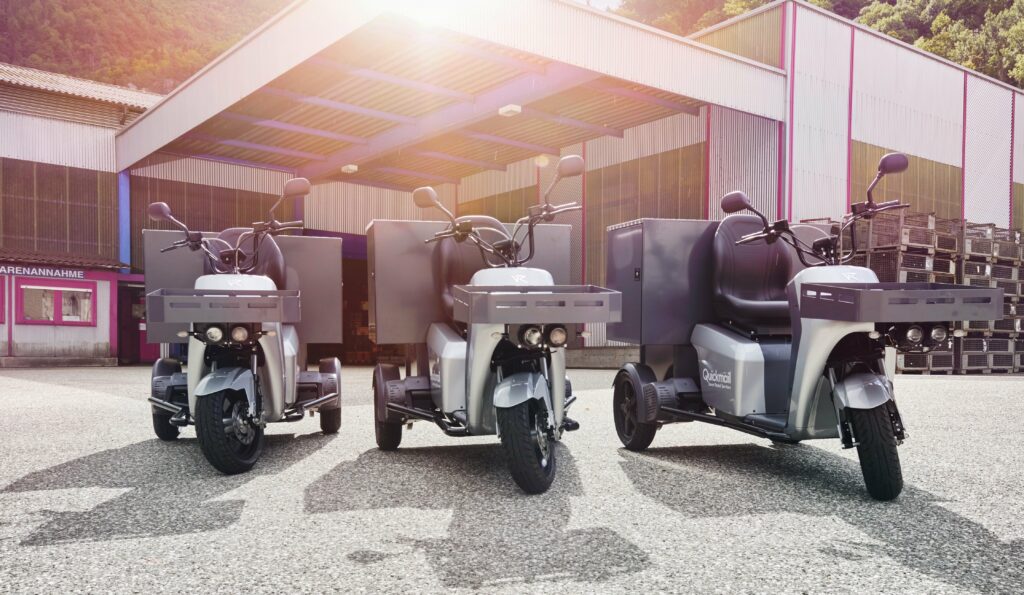
(All photos courtesy of vRbikes)
Rory Jackson looks at how this three-wheeler has been designed to carry as much cargo as possible in the smallest footprint possible.
Given that an electric powertrain brings with it lower maintenance times and costs compared with ICE powertrains, so more and more EV developers are looking to ‘right-size’ their vehicles into smaller and more compact architectures, for ease of use and nimble handling in commercial operations.
The vR3, from Swiss company vRbikes, is a key example of this trend. The three-wheeled EV has been designed to provide a platform for maximising cargo-carrying and delivery capacity relative to its size and weight, while running on a carefully balanced all-electric powertrain.
The standard version of the tricycle has a kerb weight of 225 kg, while up to 90 kg can be stored in the customisable carrier bay behind the seat. At the same time, up to 200 kg can be hauled in a trailer, which attaches behind the vR3 using universal connection points. Two more such connectors are installed in front of the handlebars for carrying up to 30 kg.
“If you’re driving without a trailer towed behind, you can still carry a little more than 90 kg in the main cargo hold without experiencing significant losses in performance,” says Gilles Clerc, head of technology and development at vRbikes. “While we can’t recommend doing that, it’s still not a ‘hard’ weight limit, so drivers can be a little flexible with how much they deliver at a time.”
With air-cooled lithium-ion battery packs and synchronous electric motors driving its two rear wheels (which have 33 cm aluminium rims and tubeless tyres), the vR3 is capable of speeds of up to 45 kph and a nominal range between charges of up to 130 km.
“On top of all the standard specifications we give out publicly, we have built or are currently designing various customised versions of the vR3, which have different suspensions, performance and cargo capacities and locations, among other things,” Clerc adds.
The vR3’s origins and development
The company was founded in 2012, with its founders initially aiming to design and manufacture electric two wheeled vehicles such as scooters and e-motorcycles. However, its research soon found that the market for electric two-wheelers was already sufficiently supplied – and possibly saturated – so it looked instead at last-mile delivery vehicles.
“We first started developing the vR3 in 2014,” Clerc recounts. “The idea was to manufacture a vehicle with as much cargo volume as possible, by freeing up the space between the back wheels.”
The first prototype was produced in early 2015, which was also the year that vRbikes started the certification process for the vehicle.
“It is now fully certified as an L2e vehicle, as per EU regulations on vehicle definitions,” Clerc says. “Between 2015 and 2020, we iterated and refi ned the design, and gradually found better suppliers, motors and controllers. In the course of development we also produced a custom BMS through a partnership with battery company Dencell, so all in all we can say the vR3 is definitely a finished product.”
And indeed, vR3s are now in service with a number of organisations throughout many of Switzerland’s cantons, including construction supplies deliverer Materiaux Sabag, postal courier Quickmail, and catering and food delivery company Yoojis.
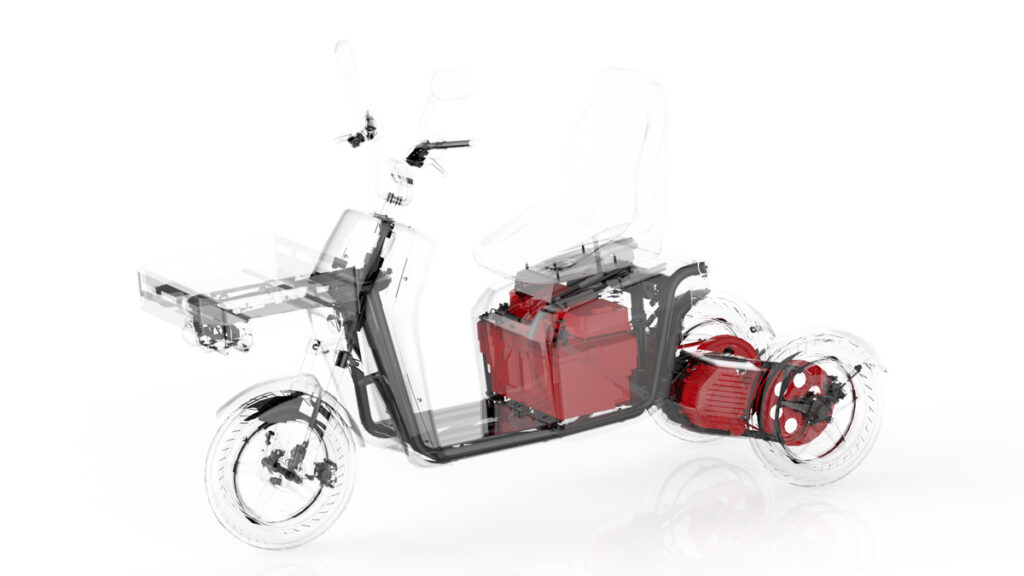
The company’s battery packs are made from NCA cells for endurance, regenerative use and low price-to-capacity ratio
Battery
The lithium-ion cells for the vR3’s battery are from Samsung, while the pack was designed and assembled in partnership with Dencell, which is based in Switzerland. The chosen cell chemistry is NCA (lithium nickel cobalt aluminium oxide), the same as that used by Tesla, Clerc remarks, because of its low ratio of price to capacity compared with other battery chemistries the company had looked at, including LFP and NMC.
“They also last longer than many other chemistries, provided end-users don’t routinely discharge the battery pack below 40 V,” he adds. “If end users constantly run the battery from 100% down to 0%, they will get maybe 500 cycles out of it, but by limiting their consumption in this way, it will last for 1300 cycles before its maximum capacity is reduced to 80%.”
The standard vR3 battery pack has two ‘cell pack’ modules connected in series, and in each module there are typically three or four cells connected in parallel. Overall, that equates to between 100 and 160 Ah of battery capacity, around 12 kWh of energy storage and about 6 hours for a full charge.
A 230 V charging input port is installed usually above the motor on the tricycle’s right-hand side. The company also has 150 V onboard chargers where necessary to account for differences in national regulations on EV charging.
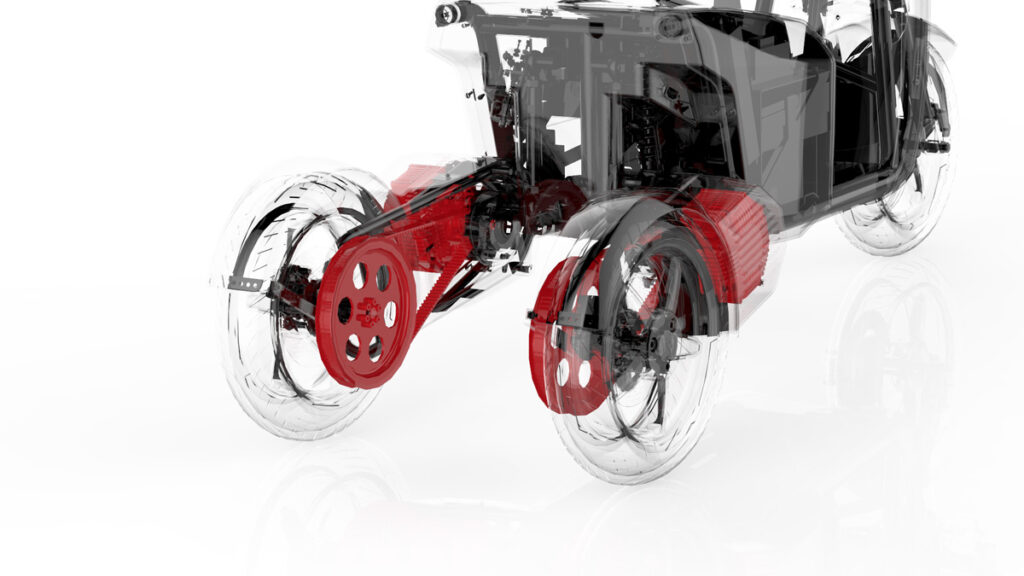
he vR3’s transmission system uses belts and gears with a 5:1 reduction ratio, which means at start-up the electric motors’ 42 Nm of torque translates to 450 NM at the wheels
“The first iteration of our specialised BMS was made around two years ago,” Clerc recalls. “Rather than using one off the shelf, we customised one because we wanted a system that was more modular than anything widely available.
“Essentially we wanted a software platform that would enable us to quickly change the number of cell strings and modules connected to the vehicle, so that we and end-users could quickly reconfigure the battery pack and the vehicle according to what work has to be carried out, or how many packs are available at a given time.”
As a result, each vRbikes cell module has its own BMS control unit. Up to eight of them can be connected in parallel (with CAN bus being the company’s chosen interfacing protocol between modules, and I2C between cells) depending on the range each vR3 needs on a given day without having to stop to recharge.
At time of writing, the BMS had recently been given a firmware update (transmitted via wi-fi to the vR3s already built and in use across Switzerland) which has improved how the battery packs operate. This includes more information on the CAN bus link between the cells and the main BMS unit for more accurate and better informed diagnostics.
Rather than using cooling fans, the pack is designed to be cooled by the ambient air that flows through its compartment. Given that the initial markets for the vR3 are in central, northern and western Europe, this has proven to be sufficient in tests and trial adoptions. However, the company plans to install more active battery cooling systems, such as air fans or liquid circuits, for customers in hotter climates such as North Africa or Australia.
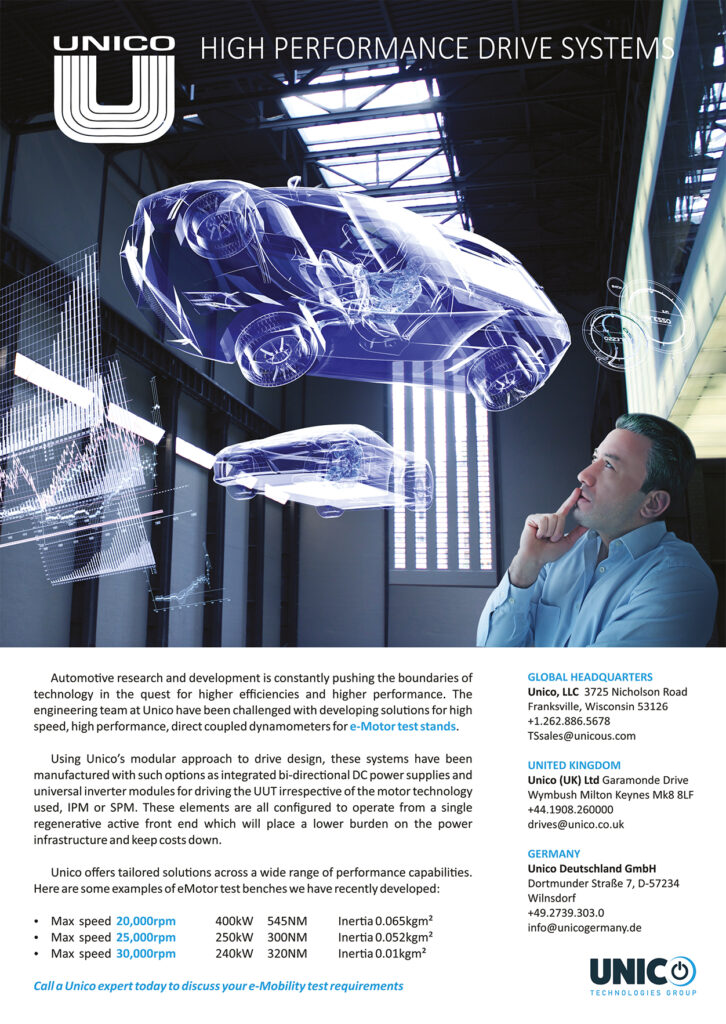
“While the two main BMSs from the two standard battery modules communicate with each other via CAN bus, we or the end-user can also view the cell- and pack-level information on temperatures, voltages, humidity, state of charge and so on remotely, using a telematics system and 3G data link in the vehicle,” Clerc adds.
“The operating company can then check that everything with the delivery driver is OK, or if the vehicle is having – or is about to have – problems that mean sending out a technician. It also gives more information for long term maintenance: for example, the end-user can see how many hours or kilowatt-hours the BMS has spent since its last reboot or inspection.
“Alternatively, if a critical operating parameter falls below a certain level or rises above a dangerous figure, the BMS can be programmed to send an SMS to the driver or fleet manager to alert them to take the appropriate safety countermeasures.”
Powertrain
As a consequence of having an open space for cargo between the wheels (with no differential or other gear train between them), the vR3 is designed with a twin rear-wheel motor drivetrain – one motor per wheel.
Each motor-wheel pair is built on a swing arm that connects to the chassis’ rear beneath the seat. Each swing arm consists broadly of a housing at the front with a fender and wheel assembly integrated behind.
Inside each housing is an inverter, one for controlling each motor. For electronic speed management, the two inverters communicate with each other via CAN bus in a master-slave arrangement, to ensure they both consistently supply the correct power for the forward speed or steering required.
This ensures that when turning left, for example, the right wheel spins faster than the left. Meanwhile, the forward wheel banks left or right based on the operator’s hold on the handlebars, as in a conventional motorcycle, all the while keeping the vR3 upright and level and, by extension, the cargo stable.
Each motor inverter is a Gen4 size 2 unit from UK company Sevcon (now a subsidiary of BorgWarner). These measure 187 x 151 x 71 mm to fi t into the limited spaces of the vR3’s swing-arm housings, in an IP66-rated enclosure for protection from rain or similar.
“The motors are at the front of the gear train, and are far more exposed than the inverters, with more space for reducing heat build-up in the motors’ fairings than is in the inverters’ housings,” Clerc says. “Air-cooling is therefore enough to keep the motors at a safe operating temperature, but the inverters need a bit of help, so we install a heatsink on each inverter.”
With the batteries supplying DC power to the inverters, the Sevcon Gen4s step the power to a nominal 48 V AC input for either motor (for a nominal current of 90 A). The inverters can supply a peak phase current of up to 275 A for 2 minutes, or a continuous phase current of 110 A for up to an hour.
In each swing arm is a toothed belt and- gear assembly that connects a small gear on each motor’s output shaft to a much larger gear mounted on each wheel to reduce the motor’s speed down to a more feasible rpm for the wheels. The reduction ratio is 5:1.
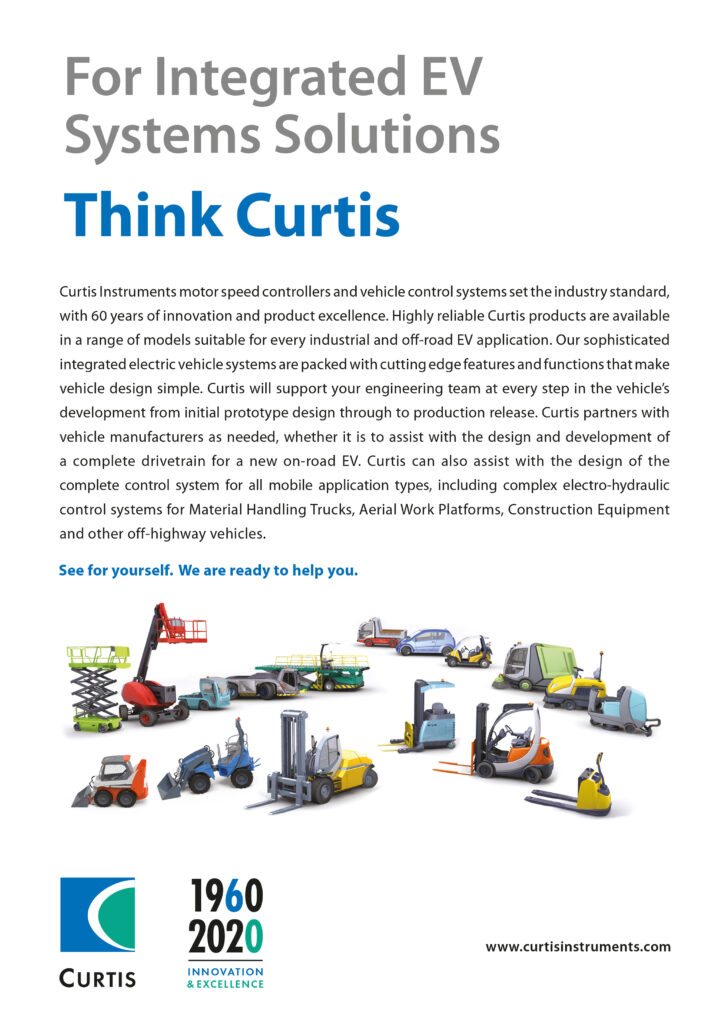
However, the company can (and has) customised that for some customers, particularly those who wanted to carry slightly more than the standard payload weight. In this case, the wheel gears are enlarged to increase the reduction ratio, converting more of the motor speed into torque for the wheels.
Also, the wheels can be extended further outwards from the chassis if the increased payload weight needs extra space. Alternatively, the reduction ratio can be decreased if an end-user wants to drive faster (without breaching the certification speed limit) and does not need to carry so much weight around.
“Going in, we had a good idea of what we wanted from the motors, based on the limitations of our battery-carrying capacity,” Clerc says. “We wanted 48 V machines, minimal current draw, and something as small and light as possible to fit the spaces inside the swing arms.”
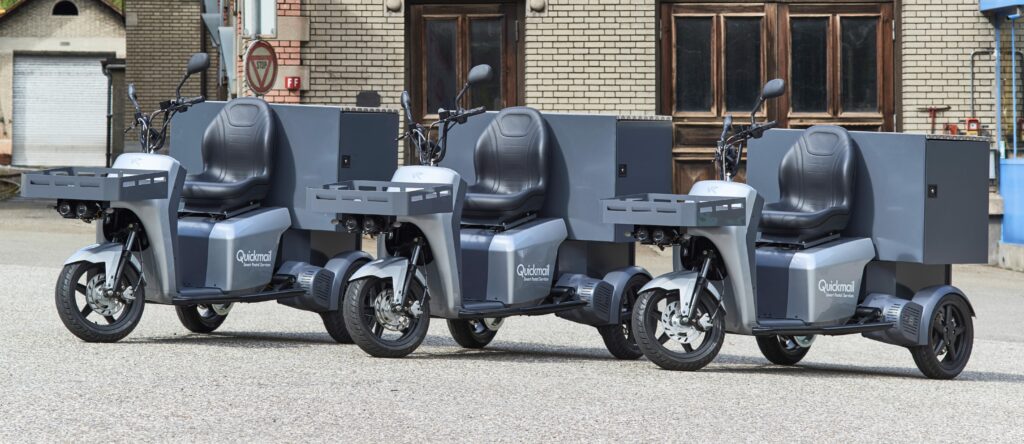
The motors are permanent magnet AC (PMAC) products from Kolektor, with some slight changes to the motors’ housing geometries to make them fit better in the vR3’s chassis. Each motor has 10 pole pairs, weighs 8.23 kg and is rated to supply up to 4 kW of power. To meet the safety requirements for certification, however, the control software prevents their collective power output from exceeding 4 kW.
Therefore, at the vehicle’s aforementioned top speed of 45 kph, each motor produces 2 kW. For this driving speed and power, the motors turn at around 2500 rpm, producing 15 Nm of torque.
At start-up, the motors produce up to 42 Nm of torque (typically around 40 Nm) and draw a current of about 250 A. With the previously mentioned reduction ratio, the transmission system increases the collective starting torque for the wheels to 450 Nm, which is a critical factor for ensuring that up to 90 kg can be carried in the rear while up to 200 kg is being pulled in a trailer behind.
“Because it’s a PMAC motor, we have sin/cos motor position encoders installed inside the motor, for position data, feedback and control,” Clerc says. “For further health monitoring and diagnostics, we also integrate temperature sensors into the motors. That information is also displayed on the driver’s HUD, so they’ll know beforehand if they’re starting to run the motors too hot.
“We could of course run the motors faster and make more output torque for the wheels, but the vR3 is certified as an L2e vehicle. We might produce a future version that’s certified to L5e, which would allow it to exceed 45 kph, but we would have to change the powertrain and drivetrain, including the designs of the motors and inverters, in order to meet the regulatory engineering requirements of this certification.”
Brakes
For stopping ahead of traffic lights or signs of trouble on the road, standard 220 mm hydraulic brake discs from J Juan Brake Systems are integrated inside each wheel. A combined braking system is also installed, to enable the driver to engage a single handle on their controls to activate all three wheel brakes. Also, their opposite handle will brake just the front wheel, for a slower, gentler halt.
In addition to having an input connector for use at charging stations, the powertrain has been designed as a bidirectional system for regenerative braking. In the standard design, once the vR3 has been accelerated close to its 45 kph limit, the driver can release the throttle, and the residual turning of the wheels drives the motors.
These then act as generators to produce an AC voltage that is sent through the inverters. They convert that input voltage to a DC output, replenishing a small amount of battery energy.
“The vR3 is driven using a dynamic of alternating between acceleration and deceleration, so by clutching the throttle, then releasing it, the battery is discharging, then recharging, over and over, all the time,” Clerc comments.
“That’s another reason we use NCA battery cells – they’re very good for taking small, repeated discharges and recharges without suffering increased build-ups of heat or dendrites.”
Clerc also notes that the degree of speed reduction achievable through regenerative braking can be increased or decreased according to the application. Rather than integrating a friction braking system, vRbikes uses power resistors (which wear down more slowly and decelerate AC motors faster than friction brakes) to help dissipate some of the kinetic energy of the wheels as heat.
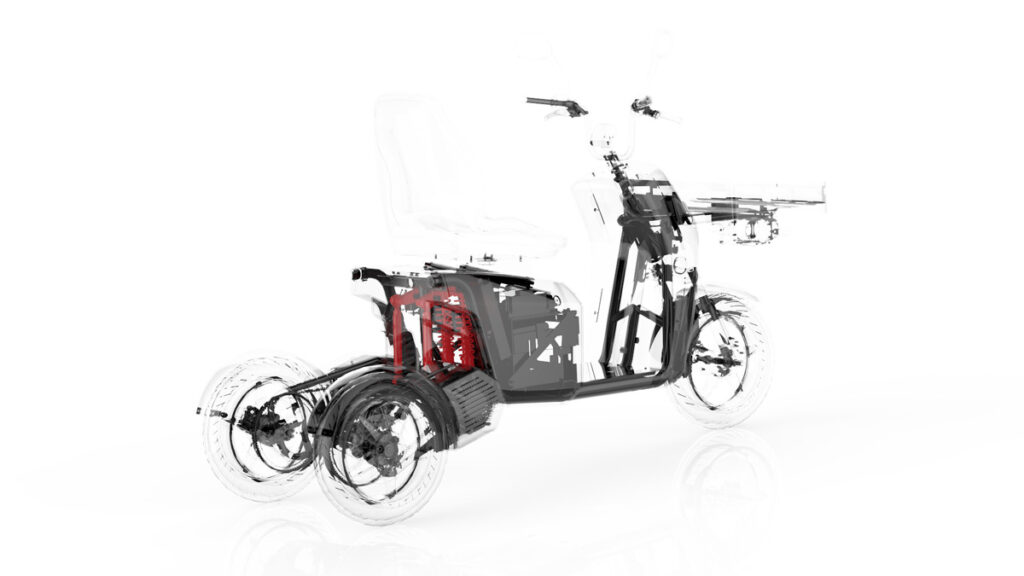
The tricycle’s dampers connect to its rear suspension struts, which then connect to the swing arms and drivetrains
“If we turn it up to maximum, the vR3 will automatically grind almost to a halt when the driver takes their foot off the pedal,” he says. “That sounds like it could be a problem, but for some of our clients, such as the postal services, they like to stop very quickly so they can jump out to make a delivery.”
Depending on the application and how the regenerative braking is confi- gured, vRbikes estimates that 25- 50% of the total battery energy can be replenished over the course of a 6-hour operation. That could potentially extend operations between stationary charging stops by 1.5 to 3 hours.
“If a user drives down, say, a 45º incline, the vR3 will not stop by itself if it has no resistor; it will continue freewheeling until the driver engages one of the braking handles,” Clerc says. “But with the speed and voltage that the wheels would generate through the motors and inverters, the tricycle could theoretically recapture 50-60% of the amount of energy it would have taken to drive up that incline in the first place.”
Structural design
As mentioned, cargo on the vR3 is carried in the container or rack between its rear wheels, which can be customised to fit the kinds of boxes, bags, or tools the end-user is likely to be driving around.
“In order to have this space between the two rear wheels, we needed to move the dampers forward a bit compared with how we’d envisioned them on our two-wheeler designs from 2012,” Clerc recounts. “The dampers are not connected directly to the swing arms from the drivetrain; the rear suspension struts are built using perpendicular rods that connects to the rear strut.”
Rather than having a suspension strut At the front wheel a telescopic fork is installed, which has been customised in-house using different dampers. Both selections were made to improve the driver’s comfort during driving.
Between the wheels, the chassis hub is made from a series of steel tube struts and some aluminium chassis parts that evenly distribute the loading from the cargo across the vehicle, even when it is concentrated in the rear basket or trailer. The choice of steel for the structural tubes was made for its greater strength relative to aluminium, as well as reducing the overall manufacturing cost.
Operator display and maintenance systems
A 200 W DC-DC converter switches the battery’s 48 V DC supply down to a 12 V AC output for powering the driver’s information display panel, as well as USB ports for charging their mobile devices. Another such converter is used for delivering 12 V to the vehicle’s indicators and other lights.
The display panel conveys a wide range of critical information to the driver. This includes alerts for when the vR3 is plugged in and charging, when it is in reverse and approaching a wall (via an ultrasonic sensor at the back), and if the batteries, motors or inverters are performing outside their usual envelopes – for example, if over currents, over voltages, excess humidity or any other potentially harmful issue is detected.
Running information can be set to show performance dials, such as speedometers and torque outputs at each wheel, in addition to battery charge and other values.
And of course, between operations and at regular intervals, data collected from the many health monitoring systems throughout the powertrain can be aggregated, analysed and evaluated against each other to determine if part replacements or overhauls are needed.
Conclusion
VRbikes continues to analyse, modify and experiment with its vR3 designs and systems, and is certified for distributing it throughout Europe and beyond. The mileage its technology accrues, along with the experience being amassed by its design engineers and data analysts, can be expected to feed back into further advances in the years ahead.
Some key suppliers
Battery packs: Dencell
BMS: Dencell
Motor/generators: Kolektor
Inverters: Sevcon
Brake discs: J Juan Brake Systems
ONLINE PARTNERS
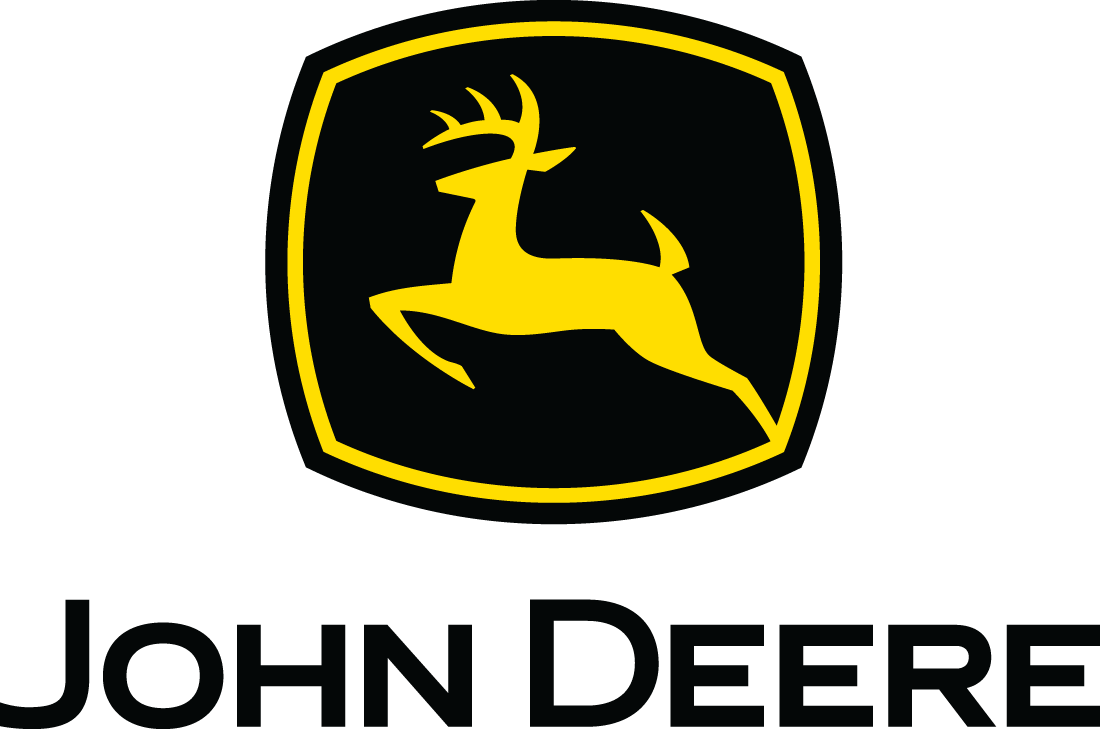
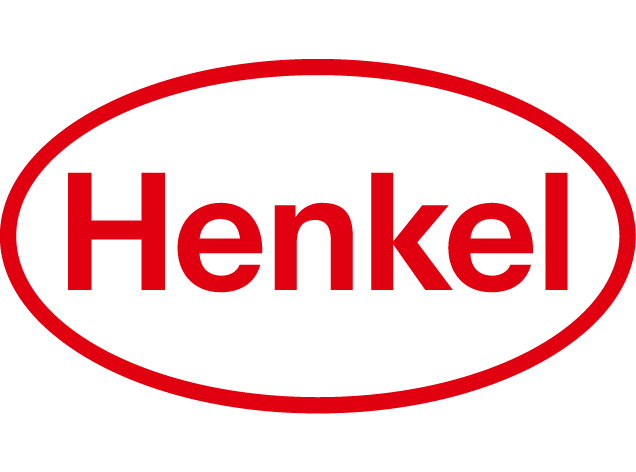
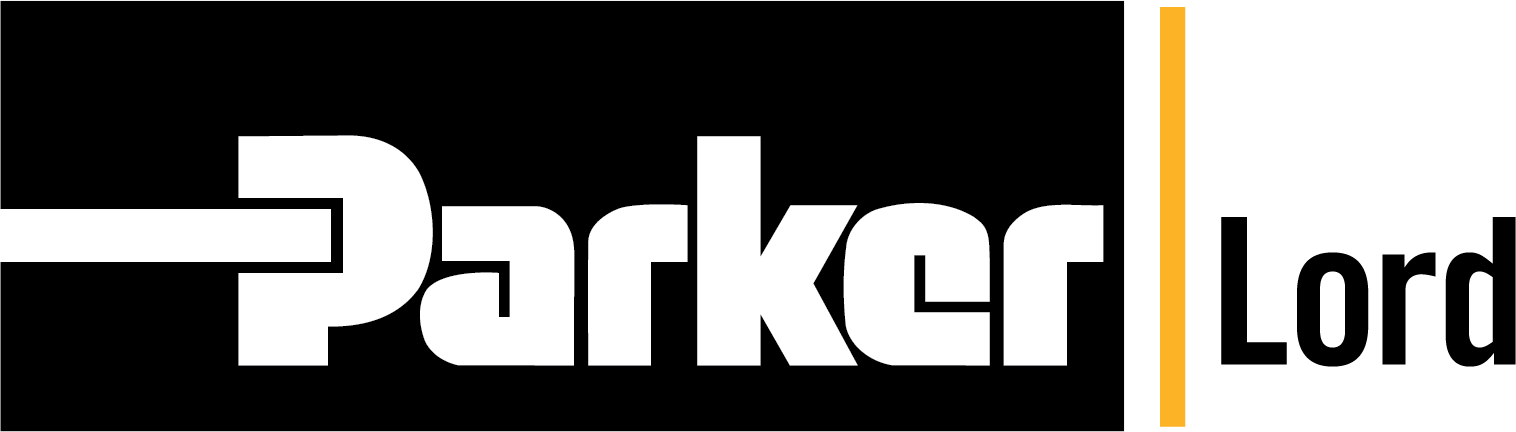
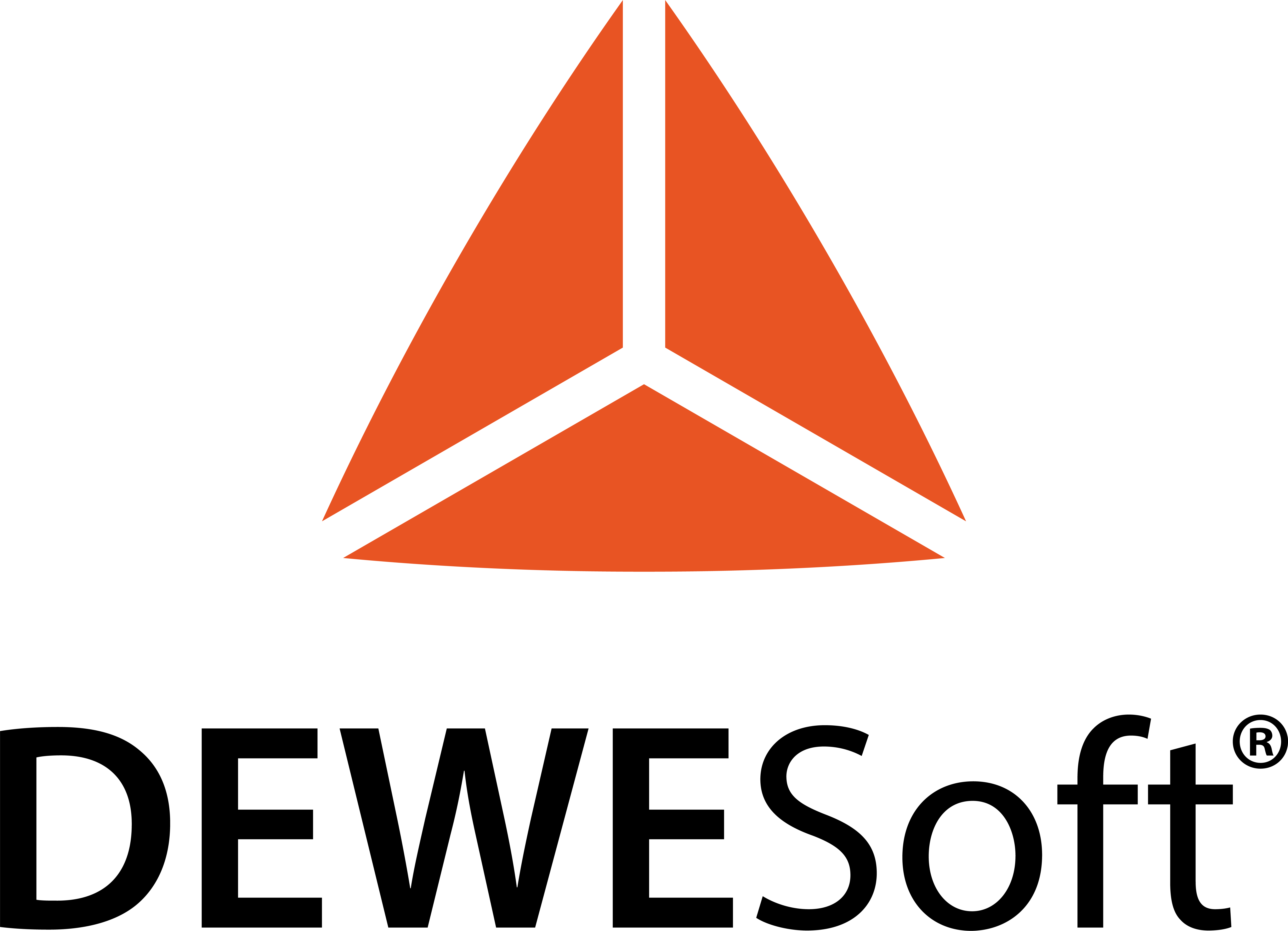
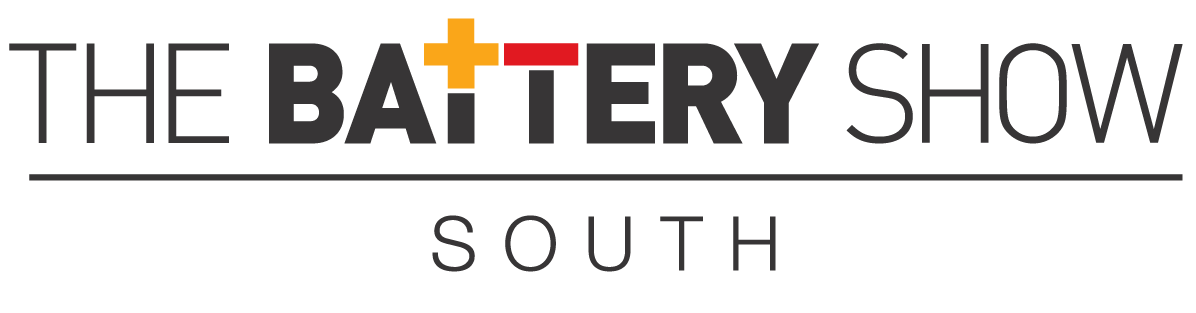
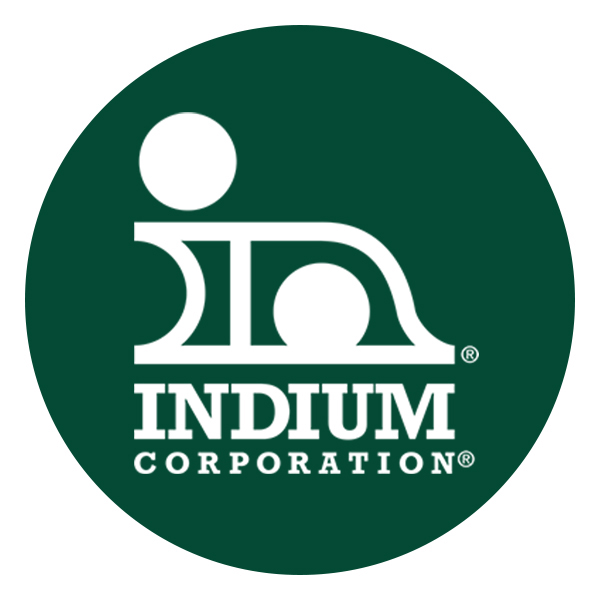

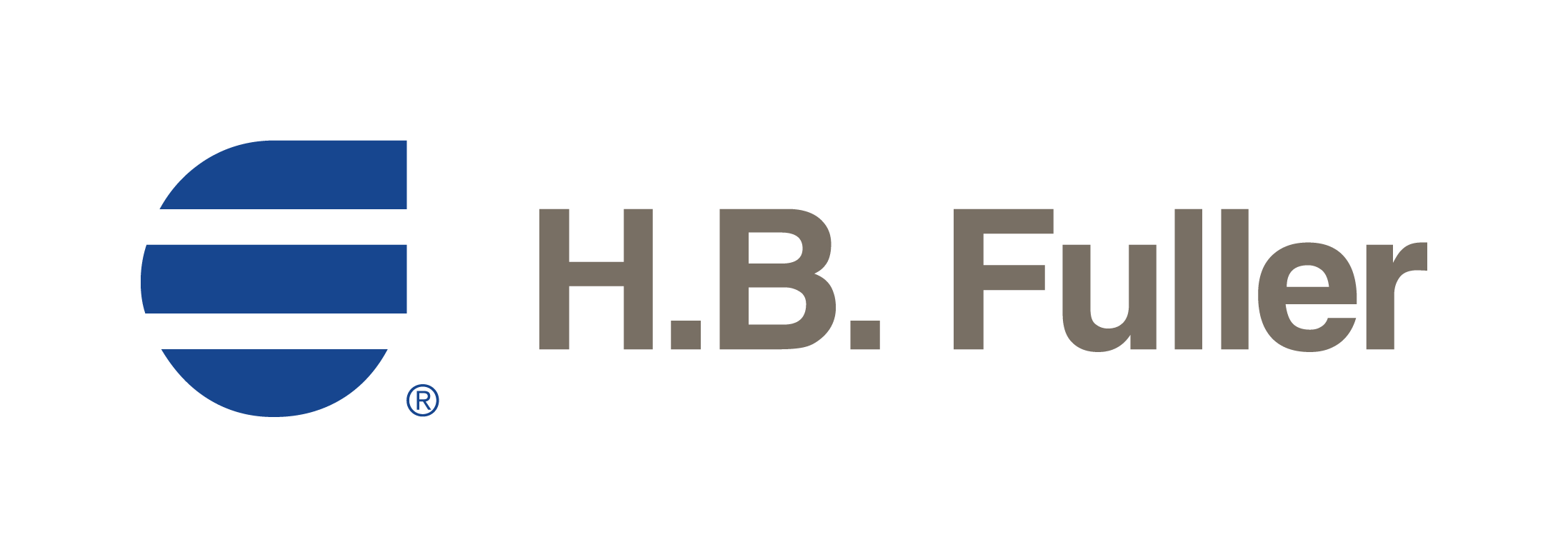
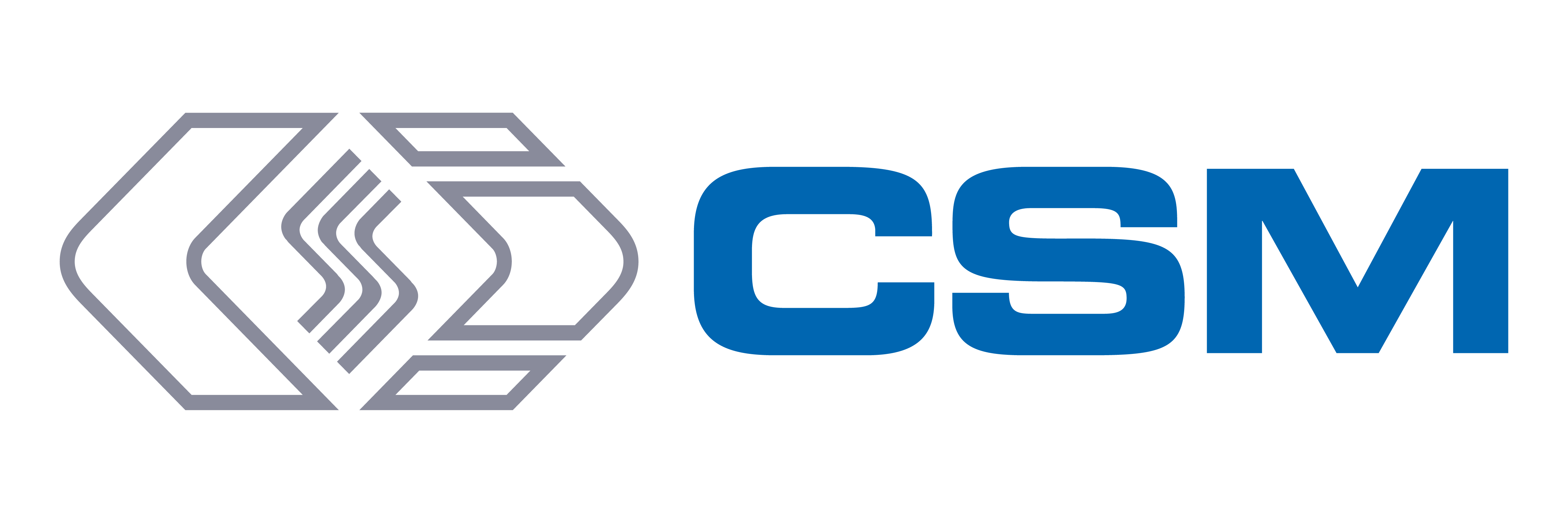
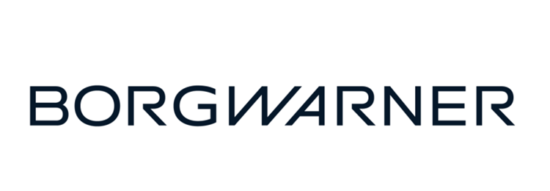