Volabo ISCAD motor
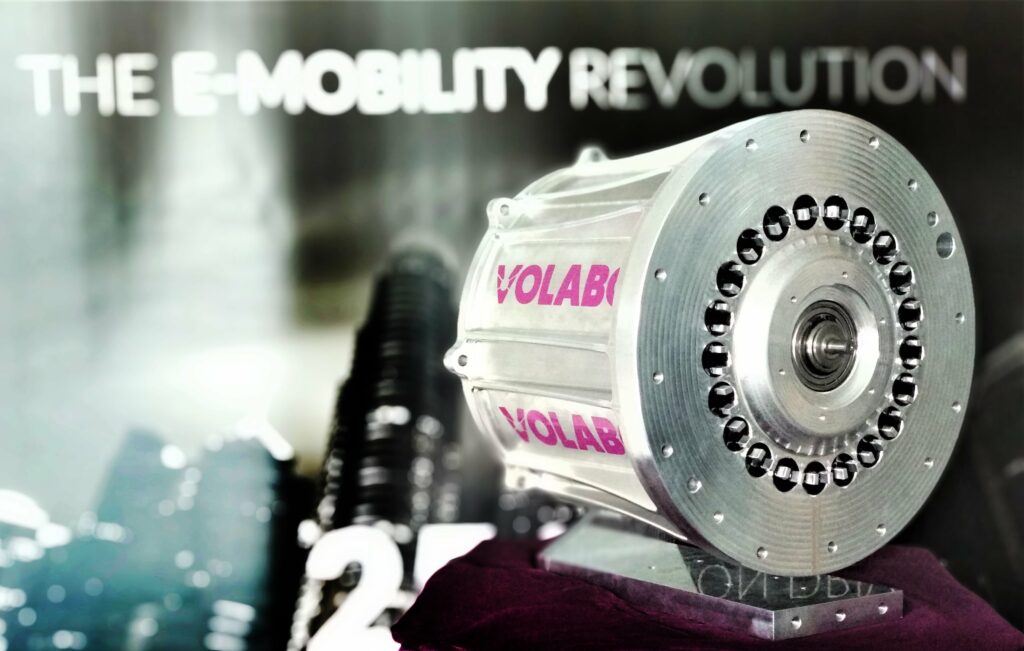
When less is more
Lawrence Butcher talks to two of Volabo’s founders about their concept for a traction motor that runs off a mere 48 V.
It is generally accepted that in order to use an electric traction motor in a vehicle, where a relatively high power output is required, a high voltage power supply is needed. Most production EVs run in the 400 V range, while some manufacturers (notably Porsche) are migrating to 800 V systems. With such voltage levels though comes the need for comprehensive electrical safety systems on a vehicle, to minimise the risk of an operator coming into contact with a live high-voltage circuit.
While it may appear that this is the accepted status quo, Volabo, a startup company based near Munich in Germany, is hoping to break the mould with an innovative traction motor design that needs only 48 V, yet is capable of power outputs of up to 300 kW.
The ISCAD concept
The potential benefits of a 48 V traction motor are evident. Removing highvoltage cabling and the need for complex failsafe systems would reduce costs for manufacturers while allowing greater flexibility in servicing vehicles. There are of course some downsides, not least the need for conductors with large cross-sections to handle high currents, but the team at Volabo has addressed these issues.
Its motor concept centres on a completely new approach to the construction of the stator for an induction motor. In a conventional motor, the stator consists of multiple copper windings arranged in the slot gaps of the stator, but Volabo’s uses a ‘cage’ of solid conductors around the internal perimeter of the stator. Hence the name ISCAD, which stands for Intelligent Stator Cage Drive.
The idea for the ISCAD system did not stem from a desire to create a 48 V motor, it was the result of an investigation into creating a simpler and cheaper alternative to permanent magnet synchronous machines, which are the choice at the moment for anyone wanting a motor with high power density.
The solution, which sought to overcome the disadvantages of approaches such as the use of distributed windings or hairpin windings in a stator, just happened to be one that lent itself to low-voltage operation.
The initial concept for the ISCAD was inherently suited to low-voltage operation thanks to the removal of the copper coils – made up as they are of many individual conductors – from the stator.
“The replacement of the coils with aluminium bars, with a common shortcircuit, meant that automatically there were low induced voltages within the system,” explains Adrian Patzak, one of Volabo’s founders. “Thus the rest of the components in the system have to be designed for low voltage and high current.”
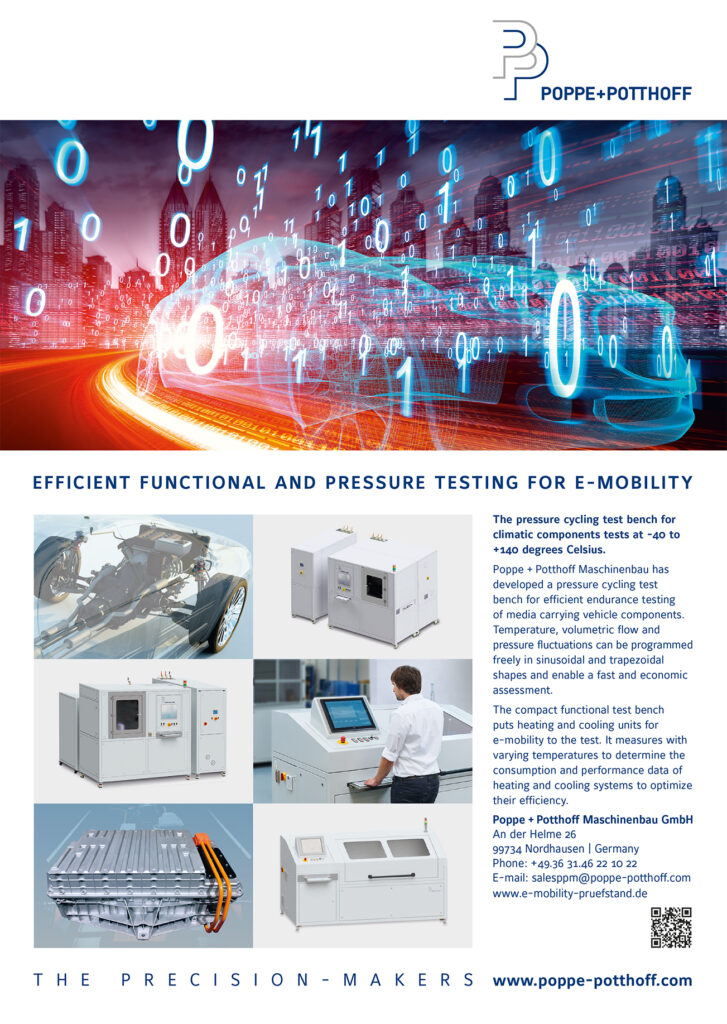
Concurrent with the development of the idea for a stator cage design was the concept that each bar in the cage could be driven by a dedicated current, forming the intelligent element of the ISCAD.
“That means you have individual control of the current in every bar of the motor,” says Patzak. “And by doing that you can generate completely new degrees of freedom with the magnetic fields within the motor.
“You can change the numbers of poles, or even drive several rotating fields with different magnetic pole numbers at the same time. That makes it possible to shift from one pair pole number to another [changing the characteristic of the motor] without any torque gap.”
This capability to shift operating modes ‘on the fly’ means that a key disadvantage of many electric motors – a fixed best-efficiency range – can be overcome. “The motor can be mapped in different areas, high speed or high torque, and you can choose the best pole configuration to optimise efficiency,” observes Patzak.
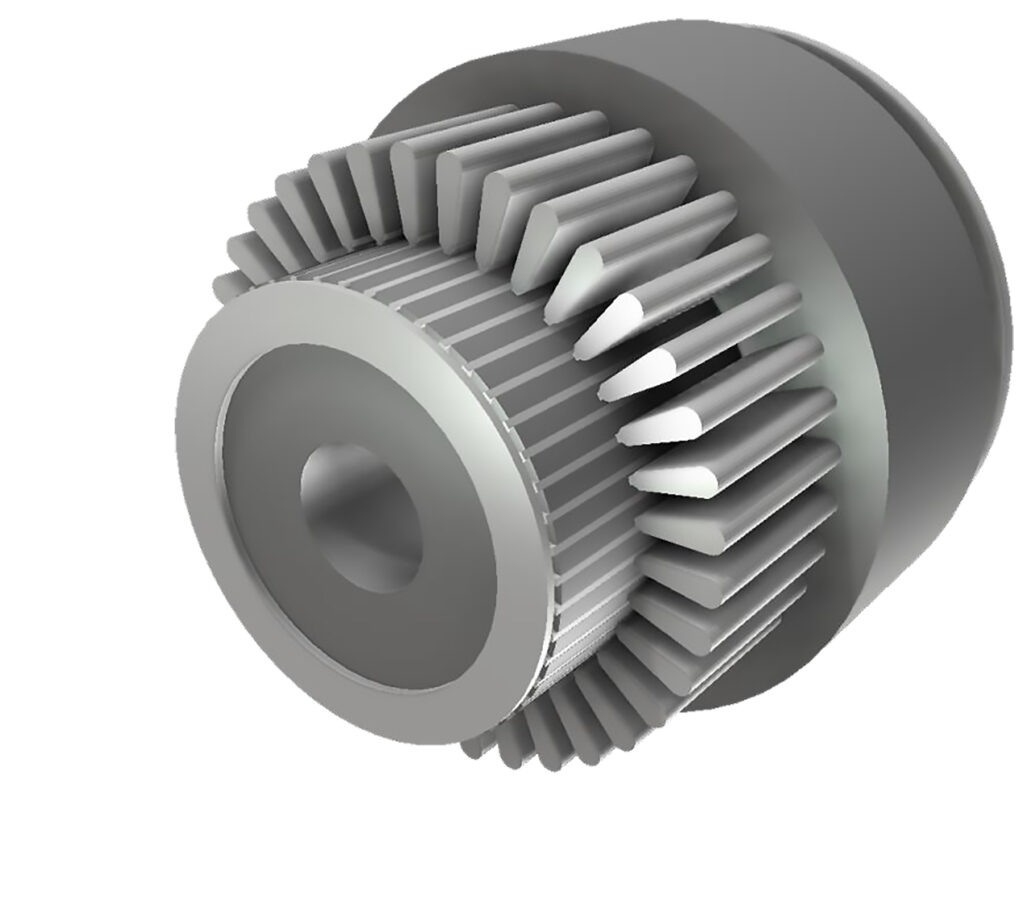
It is in effect a virtual electronic gearbox, allowing for high torque at low rpm (using a high number of poles) through to high-speed use with a low number of poles.
Architecture
The basic layout of the stator cage can be seen on page 36, with the aluminium ‘windings’ inserted into a casing of iron laminates, in much the same way as the coils in a regular motor stator. Attached to one end of the axial assembly is a connector ring, which replaces the end windings in a normal motor stator.
Looking at this set-up, one advantage over copper windings is immediately visible – the much higher fill factor (the density of the windings within each slot).
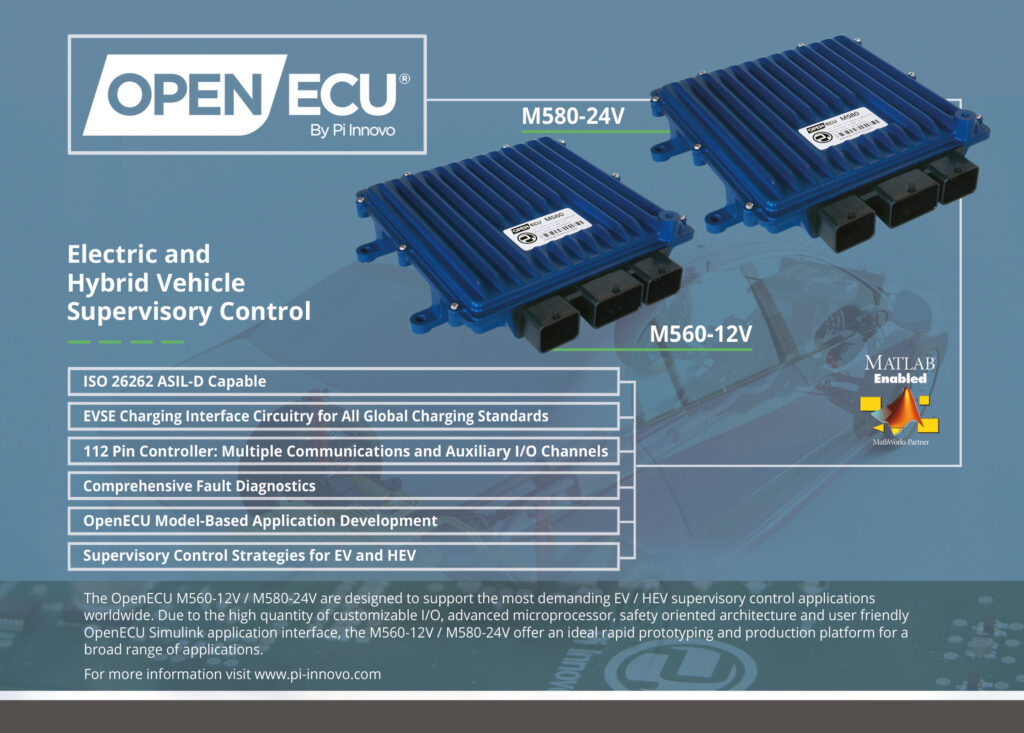
Aluminium was chosen for its low cost, while maintaining good conductivity and light weight. “For phase current transmission, you obviously need a good conductor, and copper would be the standard choice,” explains Patzak. However, he adds, “We have the advantage over copper coils though, in that we can use almost 100% of the space in the slots.”
In general, in motors with conventional windings, only 4550% fill factor is achieved. There are technologies that can increase this up to 90% using rectangular-section copper wire “but they always have disadvantages and are expensive,” says Patzak.
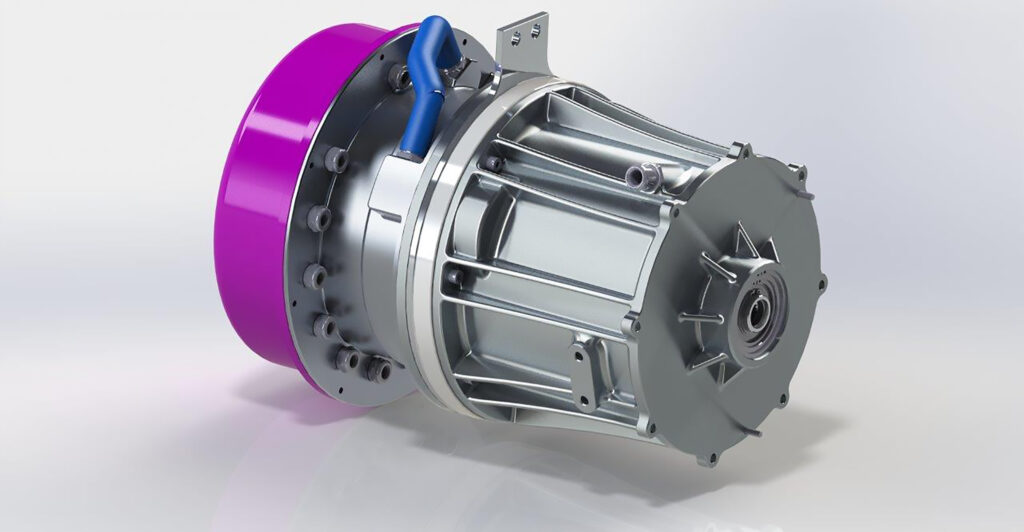
While aluminium is not as effective a conductor as copper, the fact that the bars can be formed to perfectly fit the stator slots means that, comparatively, it still provides better performance than the best wire-wound coils, coupled with a much-reduced weight.
As the bars in the stator play no structural role, the team at Volabo opted for pure aluminium rather than an alloy, to gain the best possible conductivity.
“Usually, if you use an induction rotor for a regular motor [which has a similar structure to the stator cage], you would use die-cast aluminium, which tends to contain silicon to improve the structural properties at high rotation speeds. With the stator, you don’t need this so we can use pure aluminium, to maximise conductivity,” says Patzak.
He notes however that although an insulation layer is still needed between the bars and the iron laminates, a fill factor of over 90% is still achieved. “The high filling factor compensates for the lower conductivity, is much lighter and importantly, much cheaper,” points out Patzak.
“It is the structure and the material that makes our design very low-cost. Producing the coils inside an electric motor is usually one of the most expensive processes in the overall cost of a motor, and we eliminate the need for that.”
The precise thickness of the insulating layer for the stator bars depends on the specific application the ISCAD is to be used in. Although the headline figure for the Volabo system is 48 V, the company has built motors that operate at higher voltages, even if they are still low-voltage in motor terms.
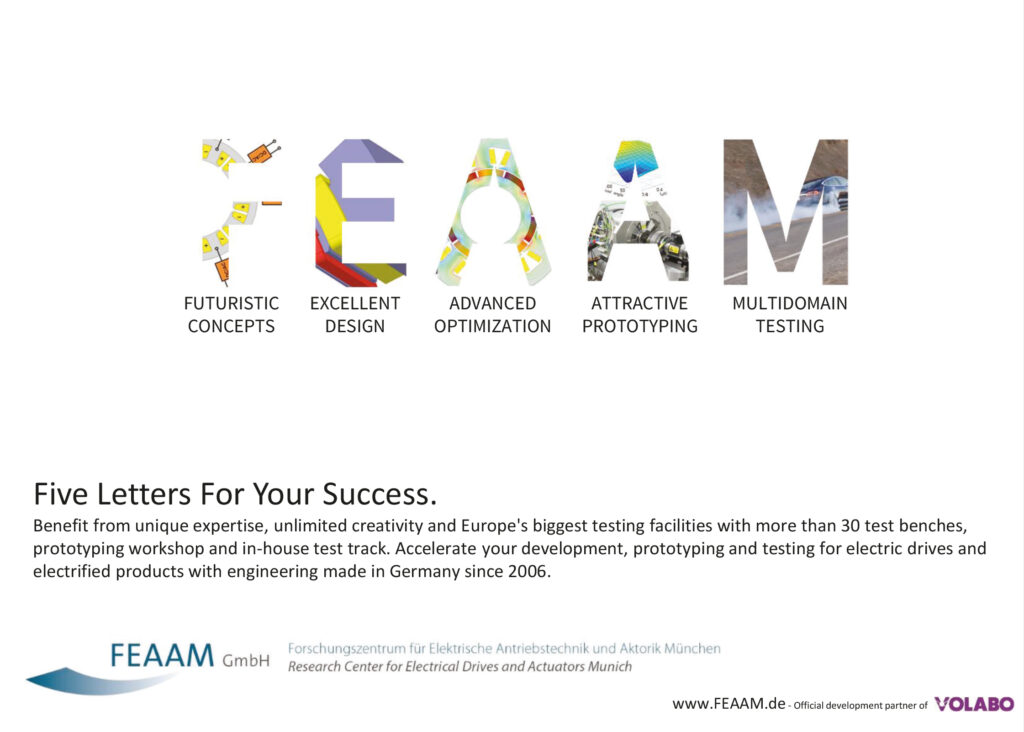
Despite these low voltages, the insulation layer is thicker than might be expected. “Normally our systems operate at below 60 V, but for certification purposes the resistance needs to be able to provide insulation for 500 V plus two times the rated voltage of the system.
“In our case that means around 600 V in total. That means we cannot use super-thin insulation, but if you consider that with high-voltage systems [400 V and up], they have to run this test at nearly 2000 V.”
To minimise the insulation thickness while still keeping costs reasonable, Volabo has been investigating different types of insulation materials, including resin and polymer systems, which would allow for an insulation layer of between 10 and 20 µm. However, Patzak explains that for economical manufacturing, an insulation layer of 100-200 µm will probably be used (the very thin insulation methods being more expensive to apply). “It is a tradeoff between technical feasibility and production costs,” he says.
“Most of the aspects of motor production are not changed [from a conventional motor]. You have the new type of stator, and there we have some challenges with how best to produce the cage at low cost, and how to achieve the insulation. We have some projects underway to find the best ways to massproduce this, but it will definitely be cheaper than copper windings.”
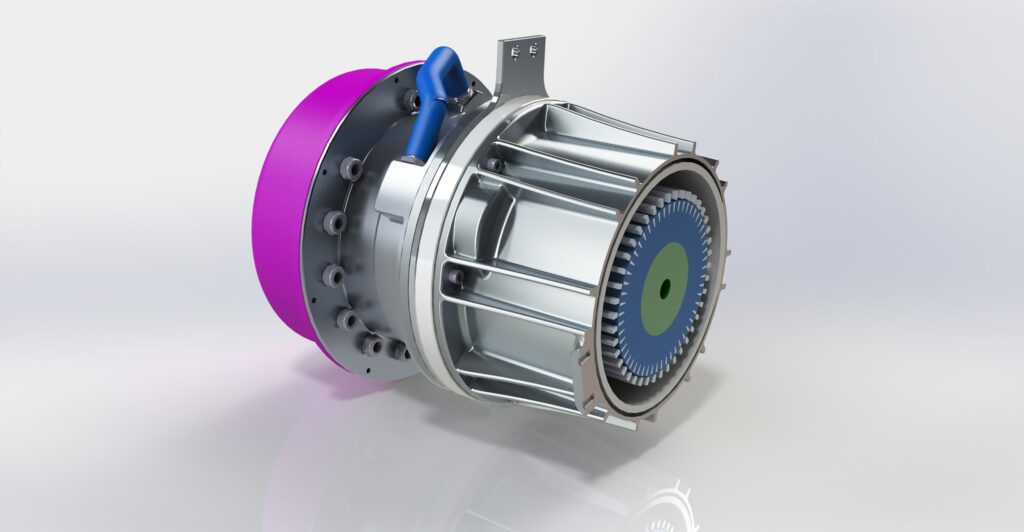
One potential method for the massproduction of the cage would be the use of pre-made bars, which would be coated in insulation and then inserted into the stator stack. The connector ring would then be attached to the end. The individual bars could be cast, or Patzak suggests that forging could also be used to produce the entire cage structure in one go. “For different applications, it might make sense to choose different production processes,” he says.
The rotor in the ISCAD motor is relatively conventional. Patzak recalls, “We considered using some off-theshelf rotors, which are already on the market and are not expensive. However, they are not suitable for very high speeds, maybe a maximum of 3000 rpm for industrial applications, whereas our motors run up 11,00012,000 rpm or higher. That means we have to design the rotor to match.”
While the ISCAD has a bespoke rotor design, Patzak points out that this step would have been necessary for any conventional induction motor running at high speeds. The high motor speed also meant using precision bearings suitable for highrpm operation, as well as having to ensure the casing (which carries the bearing supports) is stiff enough to ensure rigidity.
An upshot of having to design its own rotor is that Volabo could fully exploit the electrical characteristics of the ISCAD system. “The rotor is optimised to run with multiple poles,” says Patzak. While unwilling to divulge too much detail of the rotor design, he did reveal that the rotor uses a squirrel cage-type design, with conductor bars set in iron laminates.
“The number of bars [in the rotor] has to be carefully selected depending on the number in the stator, as there is an interaction between them,” he says. “Because we have the pole-changing capability, you have to make sure the rotor will work with every combination.”
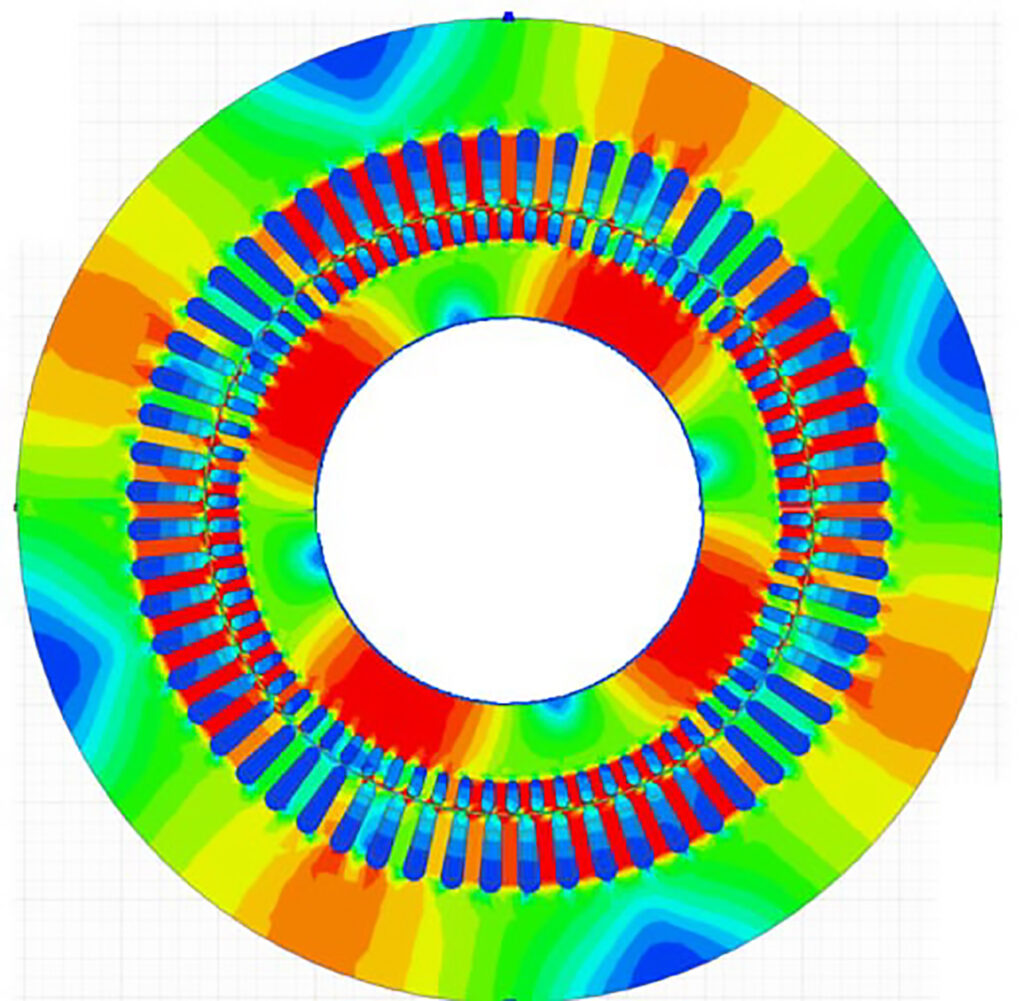
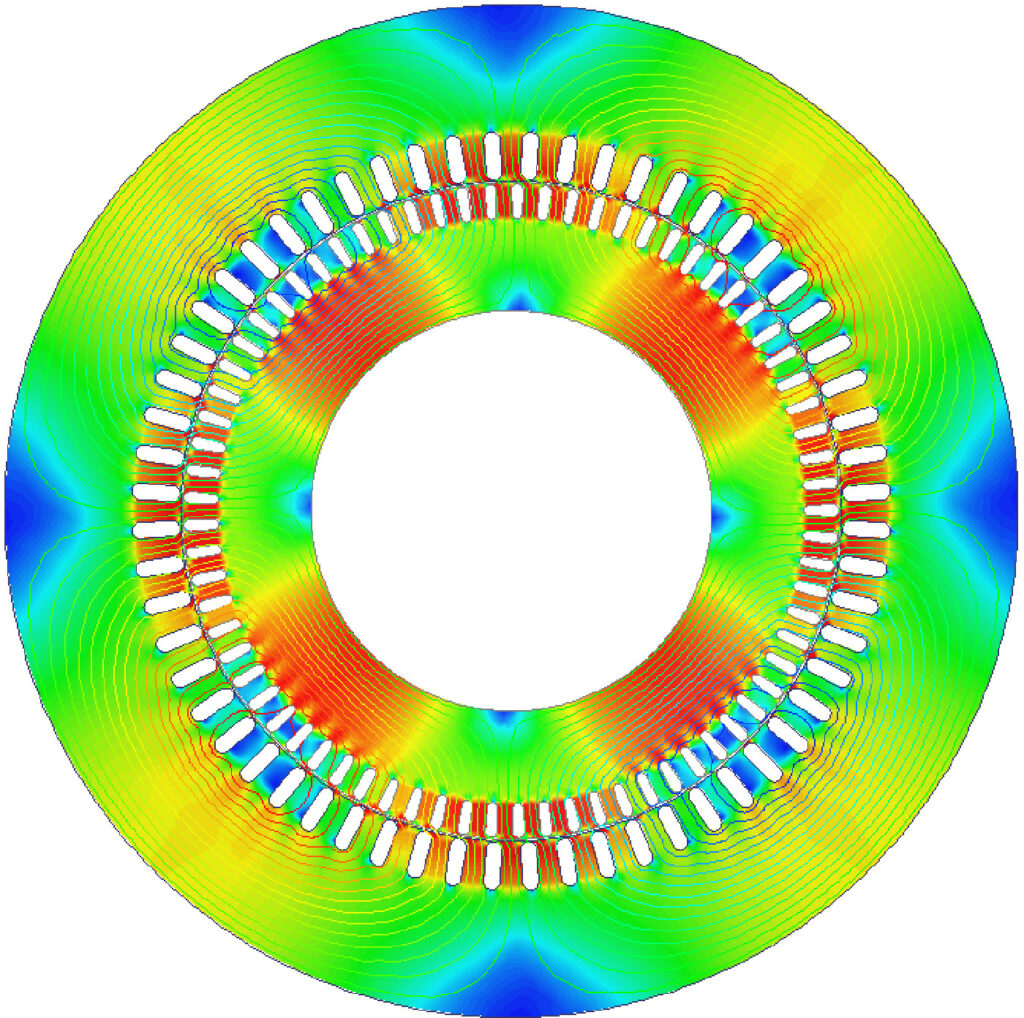
Control
Key to the entire ISCAD concept is the ability to control the current flow through each conductor bar in the stator cage.
Unsurprisingly, the design of the control system, both in terms of hardware and the control software, has been an area of considerable research at Volabo. From a hardware perspective, in simple terms, a single half-bridge inverter is used per stator bar, with Volabo using silicon MOSFETs rather than IGBTs.
The MOSFETs are commercially available units, selected for their lowresistance qualities. Florian Bachheibl one of Volabo’s other founders, notes, “We only use components that are available on the market, but we use custom packaging of the components for our application.
“The biggest and most important advantage of MOSFETs for us is that they have much lower losses. If you look at all the work being done with SiC [silicon carbide], it is to get the benefits of MOSFETs at high voltages. We are able to have the high power with normal silicon MOSFETs,” he explains.
Another benefit of MOSFETs is that they are far cheaper than IGBTs. Bachheibl says, “Even though we have a higher part count [than a conventional motor] because each phase has a MOSFET, we are still comparable on cost for normal power electronics.”
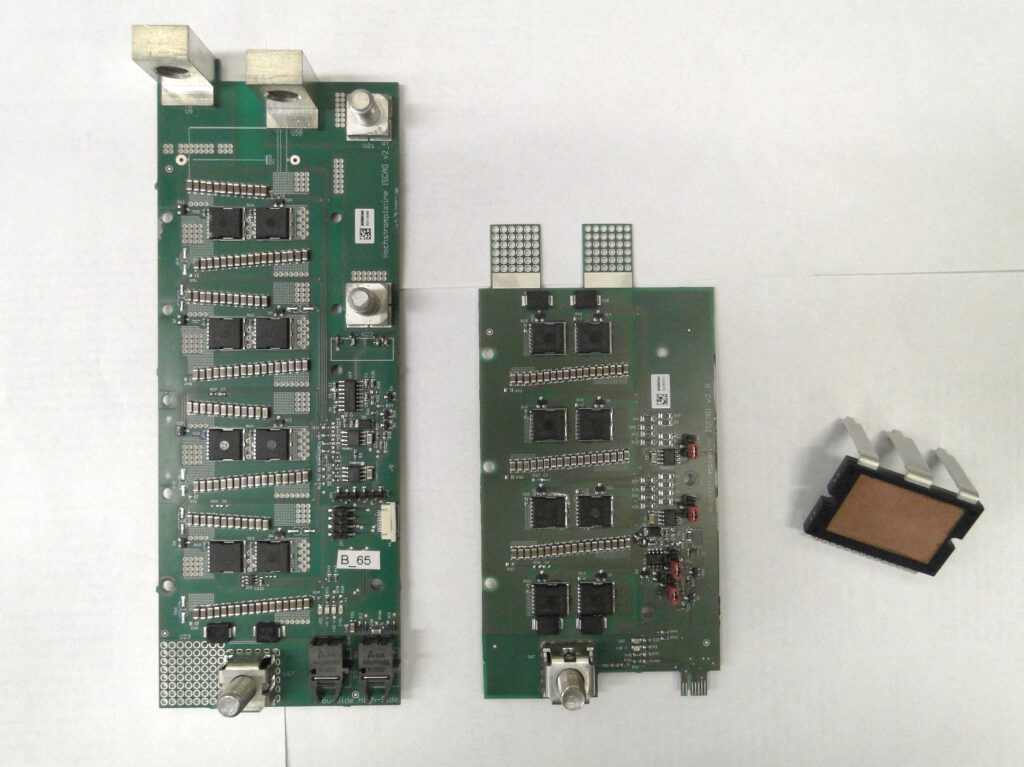
A further benefit is the higher switching frequency of the MOSFETs (compared to IGBTs) which puts their operation outside the audible spectrum for the human ear.
While the current seen by each MOSFET is not huge it is still substantial, so reducing resistance is important, a task made easier thanks to the low operating voltage.
“If you reduce the blocking voltage for a silicon device, you can increase the doping on it and reduce the resistance,” says Patzak. “So for a given cross-section of silicon device, the current capability increases at lower voltages. With devices working at 48 V, you can drive large currents because of the higher doping.”
On the subject of current draw, although a motor rated at 300 kW and running at 48 V will have a current draw of more than 6000 A, it is not in fact the level of current seen by the MOSFETs in the power electronics module.
“Each bar represents a single phase on the motor, so there is a very high number of phases compared to a regular motor, the number in the ISCAD depending on the number of bars.” Patzak explains. “Each phase can therefore be seen as a parallel path for the current, which means we are splitting the very high current and distributing it over a lot of paths, so the current is moderate for each path.”
Working on the basis of the motor having 42 phases, the MOSFETs on a 300 kW motor would only have to handle around 300 A, while on the 100 kW prototype discussed here, it is about 200 A in continuous operation.
The use of an individual controller for each phase of the motor creates the scope for a previously unheard-of level of control of the motor’s operation. “We have a lot more possibilities for control compared to a three-phase drive,” says Patzak. “We can use control methods to increase the efficiency, for example by increasing the number of poles.
“And that is just a basic step. We can also do much more in areas such as tuning the switching of the MOSFETs to reduce the capacitor current inside the inverter.”
Elaborating on the benefits of this latter step, he says, “Besides the silicon used in the power electronics, the capacitor is, I think, the second most expensive part. Using what I would call smart switching, we can reduce the number of capacitors in the system.
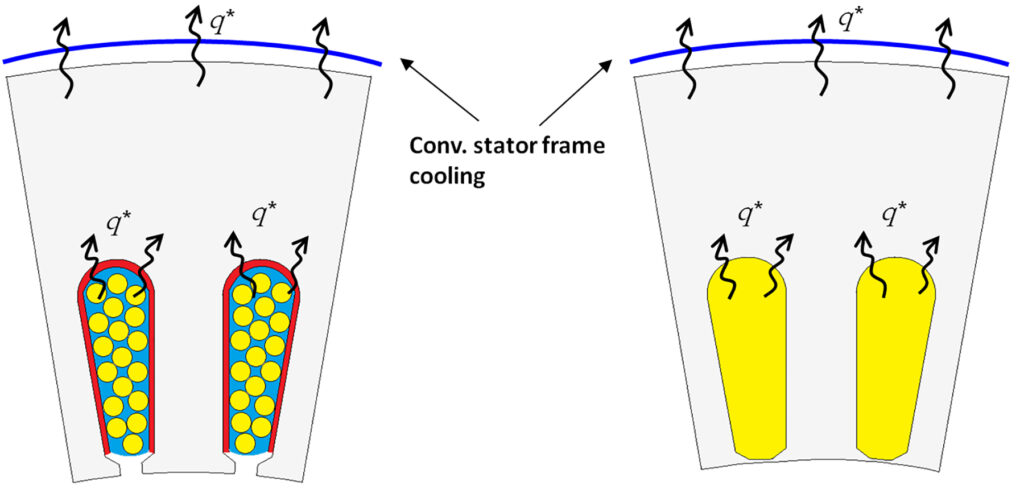
“This is still an area of research, but we have found ways to do it to a significant degree. There are many possibilities, through the software control, to increase reliability or reduce cost.”
Another goal of the ISCAD design team is to create a motor with a fully integrated power electronics module, mounted directly on the stator ring. Removing the need for a standalone electronics module would significantly aid vehicle packaging.
“The advantages of being able to integrate the electronics and create a compact package are considerable. It allows for very short paths for the high currents, and we can reduce cost and complexity by having a higher level of integration,” remarks Patzak.
Cooling
Thermal management in any electric drive system is an important design consideration. Depending on the application, the ISCAD motor’s cooling system can be tailored to suit the needs of a customer. “We have a high-voltage reference system, and we design the cooling system for our motor to ensure it has the same space envelope and cooling requirements,” says Patzak.
The most likely cooling method that would be used in a mass-produced unit is a water jacket around the stator core (as is used on the prototype), but the team has also looked at the potential for active air-cooling. “That would be viable for applications where there is more space available, or those with a low power output,” says Patzak.
The company is also investigating the potential to take advantage of the architecture of the stator cage in order to deploy more sophisticated cooling methods, such as oil cooling of both the rotor and the stator. With the lack of windings in the stator, it is more straightforward to integrate cooling channels into the stator body.
Patzak also highlights that using a connector ring, rather than end windings, opens up new cooling possibilities. “We have investigated connecting cooling channels to the connector ring,” he says.
“Cooling conventional motors is a big issue, as you can only use a water jacket on the outside of the coils. So if heat is generated by the current, the heat has to be conducted through resin in the slots, through the insulation, then into the laminate stack and then finally into the water jacket.
“Attaching a cooling channel at the connector ring it makes it possible to reduce the heat path from the bars, because we do not have to go through so many layers.” Volabo has produced prototype motors with this type of cooling, which have proved successful.
The use of bars rather than windings in the stator also provides a better thermal path from the bars to the laminates, as there is a much greater surface area in contact with the stator laminates. Thus, even a conventional water jacket can operate more efficiently than on a conventional motor.
Parallel approach
Although the main innovation from Volabo is the ISCAD, it has to be viewed as part of an overall powertrain system. As such, the design team has also followed the concept of parallel energy paths from the battery through to the motor.
“There is a high DC current between the battery and the power electronics,” notes Patzak. “But even here, we can use two, four or even more cables. With that approach, we can use conventional cables with conventional connectors.”
By ‘conventional’, Patzak is not referring to the type of high-voltage connectors found in most EVs but far simpler screw contacts, which are acceptable on a 48 V system. “They have been used for many years but cannot be used with high voltages. On those systems, you have to have plugin connectors, with isolation.”
While using readily available cables is cost-effective, Volabo has also looked at developing dedicated cables for the ISCAD system. For example, it has investigated cables with a coaxial design of the positive and negative poles.
“By using such cables, we can compensate for induced electromagnetic fields perfectly, because the sum of currents in the inside and outside conductor is zero,” says Patzak.
Patzak admits though that the high current draw of the motor, in relation to the transmission of power from the battery to the power electronics, remains a design bottleneck. Even when wired in parallel, thick (and thus heavy) cables with around 10 times the conductor area are needed.
Weight is of course not the only challenge: thicker cables are harder to manipulate in a vehicle’s structure. However, Patzak says this should not be a problem in many installations.
“We always need high current, which limits the applications that are feasible for our technology. So we have focused on compact applications, where the distance between battery and motor is short,” he says.
Fortunately, taking the example of a small passenger car with a centrally mounted battery and a motor drive at either the front or rear axle, the cable runs needed are unlikely to be more than 1 m. If the architecture of a vehicle was designed specifically for a 48 V drive, that could be further reduced.
Even over a short run, a copper cable would still be a heavy (and expensive) production, so Volabo has turned its attention to aluminium cabling, which is already used in some high-power EV applications. For example, many teams in Formula One have used aluminium cables on their hybrid systems to benefit from the weight reduction.
“Using aluminium, we can really keep materials costs and conductor mass low,” Patzak points out. He also notes that some modern IC-engined cars, particularly those with large diesel engines and rear-mounted batteries, already accommodate cables to accept more than 1000 A for the starter motors.
As a 48 V system does not need to be galvanically isolated, this further reduces the cost of installation and also opens up the possibility of creating structural conductors, whereby sections of a vehicle’s chassis are used for transmitting current. Patzak cites the example of the protective cell required to prevent objects penetrating the battery.
“These are often made from aluminium, and we could use this structure as a conductor, which is an exciting possibility,” he says. “That does not mean it makes sense to use everything as a conductor, not least because of electromagnetic interference, but it introduces some new degrees of design freedom.
“Using some smart design, you could reduce the impact of the need for current conduction.”
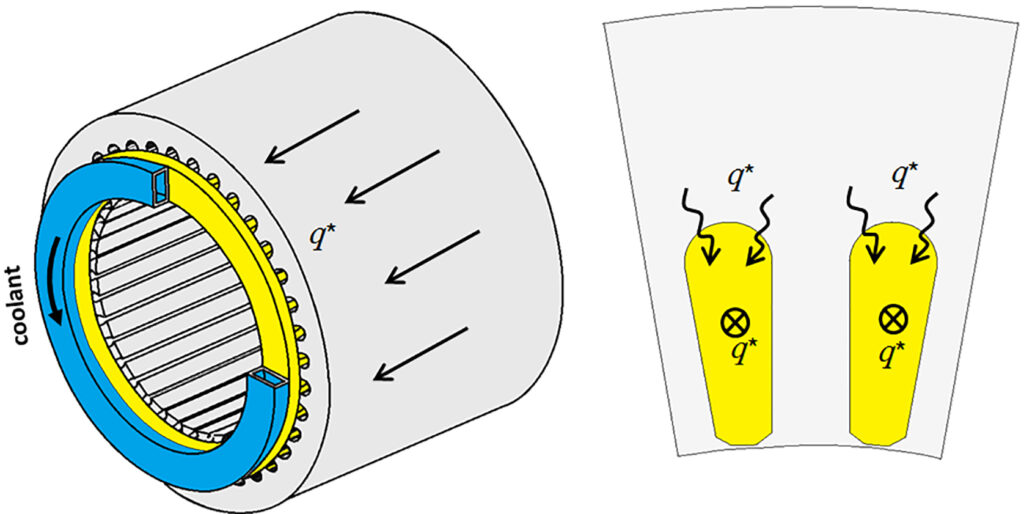
Power provision
The use of 48 V also means having to use a different design of battery system, although the basic components are the same as for a high-voltage system. “We can use any type of battery cell, or in fact any type of electricity source,”says Patzak. “It is the configuration of the cells in the battery that is different.”
A modern 400 V system will usually use blocks of 96 cylindrical (18650 type, for example) lithium-ion cells arranged in series, to generate the 400 V. In the case of systems running higher voltages (such as Porsche, at 800 V) nearly 200 cells will be used in series.
Looking at the batteries developed for use with the ISCAD, these have only 12-16 cells in series in each pack to produce the 48 V. Having such a small number of cells in series makes battery management relatively straightforward.
The load on each cell is the same whether it is a high- or low-voltage system, but the interconnection of the cells is different, with the ISCAD using lots of parallel connections.
Having many parallel connections and a small number of series connections makes the battery very fault-tolerant – if a cell drops out, only the output of 12 cells is lost, rather than 96. Based on the battery pack for its 300 kW system, the performance impact of a cell going bad in the battery would be “less than 0.2%” according to Patzak.
A high tolerance of faults is also a feature of the motor design. “The motor’s design enables it to handle the loss of multiple phases [if a bar or its individual controller were to fail],” explains Bachheibl. Even if several phases were lost, the motor could still operate at 85-90% of its torque output.
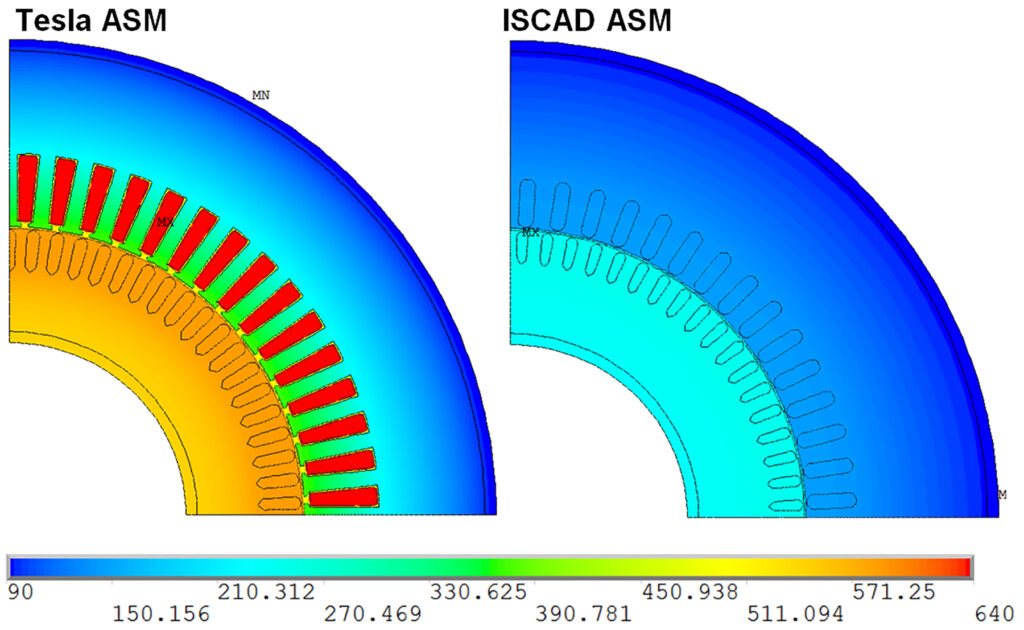
This ability to have continued operation, even with a level of component failure, makes the ISCAD system a particularly interesting proposition for future e-mobility sectors, where the default failure mode cannot be a total system shutdown.
As noted earlier, aviation is one such market where this would be beneficial, with Bachheibl also highlighting autonomous vehicles. “The usage time of these vehicles [such as autonomous cars] will be much higher, and vehicles will be more like industrial assets. If the vehicle has to be repaired or maintained, that means a loss of earnings. With the ISCAD, maintenance intervals could be much longer.”
The team at Volabo are realistic about the limitations of their systems, with Bachheibl identifying the challenge presented by fast-charging a 48 V battery. “Fast-charger networks operate at 400 V DC, which is the standard that has seen widespread adoption,” he notes.
For a 48 V system to be compatible with the established charging grid, it would need an onboard adapter. “We already have a prototype for a DC-DC converter; it is not space-age technology,” says Bachheibl. “For example, fuel cell cars tend to have a DC-DC converter to raise the fuel cell voltage to the drive voltage. We would do the reverse.”
On the subject of fuel cells, he points out that a 48 V system would be far more suited to the needs of a fuel cell drive than a high-voltage one.
Progress
The Volabo ISCAD concept is still very much at the prototype stage, but the company’s first test vehicle installed with a motor ran in August 2018. Work on the initial prototype motors began early in the development process.
Bachheibl says, “We had the first motor running a year after the first idea for the ISCAD. That prototype was unable to produce much power, but it was capable of changing pole pairs, which is one of the key things.”
That was in 2015, and by 2016 the group had produced a functioning motor producing more than 90 kW continuous and 150 kW peak power.
Bachheibl describes these early prototypes as “chunky” but by mid2017, what could be classed as the current generation of motors had been built, with the power electronics integrated into the motor, and suitable for installation into a vehicle.
“Prototyping has been essential for us because we are doing something new, and things can always happen [in reality] that simulations don’t predict,” he says. “We learned a lot from those.”
Construction design and manufacturing planning of the mechanical elements of the prototypes was handled by IGEL, a company local to Volabo (which does not have in-house manufacturing capabilities). “They did a great job of manufacturing the housings, and all our components were made by companies local to Munich,” says Bachheibl.
The mechanical design of the prototypes was shared between Volabo and IGEL, with Volabo handling the active parts of the motor (including the rotor) while IGEL worked on the construction of the motor housing, with a brief to create something that lent itself to easy manufacture.
IGEL also handled aspects such as bearing analysis, an important factor for a high-speed motor. On that point, a less obvious advantage of a 48 V system is that electrical erosion of the bearings is less of an issue than in high-voltage systems, thanks to the low operating voltage.
The performance of the prototype motors has been impressive, despite the focus being on cost-effective production rather than outright performance. “Compared to other induction motors, we have a higher power and torque density,” says Patzak. “But we will still usually be below permanent magnet machines, because we still have to generate the excitation of the rotor through the stator.”
However, he also points out, “In some applications we can design our motor to fit in the same space envelope as a reference permanent magnet motor, because we have a very compact stator design with nearly no end windings.”
The ISCAD approach also has clear benefits outside the automotive area. “The low-voltage approach has huge merit in the off-highway sector,” Bachheibl says.
“On the one hand, you have a very robust system; on the other you have one that can be repaired and serviced in the field by people who don’t have specialist high-voltage training.”
Whether the ISCAD will see widespread adoption remains to be seen, but the concept is certainly an intriguing one. With the team at Volabo pushing ahead with further prototyping work, while also forging connections with industry partners and beginning in-vehicle testing, the company is certainly determined to change the industry mindset on the capabilities and potential of lowvoltage systems.
Some key suppliers
Rotors: Wieland
Laminations: LCD LaserCut/Waelzholz/ Cogent
Bearings: SKF
Insulation materials: Kaltenbach
Coolant: BASF
Connectors: Würth
IGBTs: Infineon
MOSFETs: OnSemi
PCBs: Multi-CB
PCBs: Karré Elektronik
Simulation and design software: Ansys Maxwell/Simplorer/Icepak/ Matlab/Simulink/Tesis/CADFEM
Test systems: Universitaet der Bundeswehr Muenchen
Construction design: IGEL
Anatomy of ISCAD Generation 3
The Volabo ISCAD Generation 3 is an asynchronous induction motor, using a stator cage instead of windings. The stator is made up of 0.35 mm thick electrical steel, laser-cut laminations, with slots to accept the solid stator bars. The 42 pure aluminium stator bars fit within the stator slots and are coated in an insulating material. Encompassing one end of the bars is a solid shortcircuit ring, also made from aluminium. Attached to the opposite of this ring is a power electronics module, incorporating 84 silicon MOSFETs, two per bar. The stator is housed in a machined aluminium alloy housing that incorporates a cooling jacket to carry water/glycol. The coolant inlet is at the rear of the motor, where the connector ring and control electronics are housed; the exit is at the front of the motor (where the drive take-off is). The motor housing has a number of bracing ribs to ensure rigidity. The drive end of the motor housing and the outer casing are one piece, while the rear of the motor is a removable section, attached with eight fasteners equally spaced around the perimeter of the casing. The casing offers support for two, high-precision ball bearings for the rotor shaft. The rotor is a squirrel cage design, also using aluminium conductors. Rotational speed is about 12,000 rpm. The current prototype motor produces a maximum of 110 kW with a continuous output of 50 kW. Overall weight is 70 kg, including the power electronics; the total length is 460 mm and the diameter is 300 mm. The number of poles can be varied from two to eight.
ISCAD Generation 3 Specification
Motor designation/model number: ISCAD Generation 3
Motor type: Intelligent Stator Cage Drive (ISCAD) synchronous motor
Operating voltage: 48 V rated
Power output: 110 maximum/ 50 kW rated
Number of phases: 42
Number of poles: two to eight
Motor weight: 70 kg
Motor length: 460 mm
Motor diameter: 300 mm
Casing: aluminium
Stator: electrical steel
Winding type: aluminium bars – stator cage
Cooling system: water jacket
Power electronics: MOSFETs
Semiconductor material: silicon
Background to Volabo
The ISCAD concept, and Volabo as a company, stem from the University of the Federal Armed Forces in Munich, where the key team members were studying under the chair of electrical drives and actuators. Both Florian Bachheibl and Adrian Patzak were research assistants for the senior researcher, Prof Dieter Gerling. His senior scientist, Dr Gurakuq Dajaku, had the initial idea for the ISCAD concept while Patzak and Bachheibl worked on the feasibility of integrating such a motor into a vehicle, dealing with power electronics and battery/ cabling respectively. “At first we were just fascinated by the technology, and the more we looked into it, the more we were convinced that it was worth pursuing,” recalls Bachheibl. It was after the first prototype was produced that the decision was made to form Volabo, which came into being in July 2016. Patzak says it is valuable having a university environment as an incubator for innovations such as the ISCAD. “In a company, people would just immediately say, ‘No, that concept does not make sense.’ We did the research and found out that it does make sense.” Since the founding of the company, initially with six staff, Volabo has won a number of awards for innovation. As of July 2018, it employed 20 people.
ONLINE PARTNERS
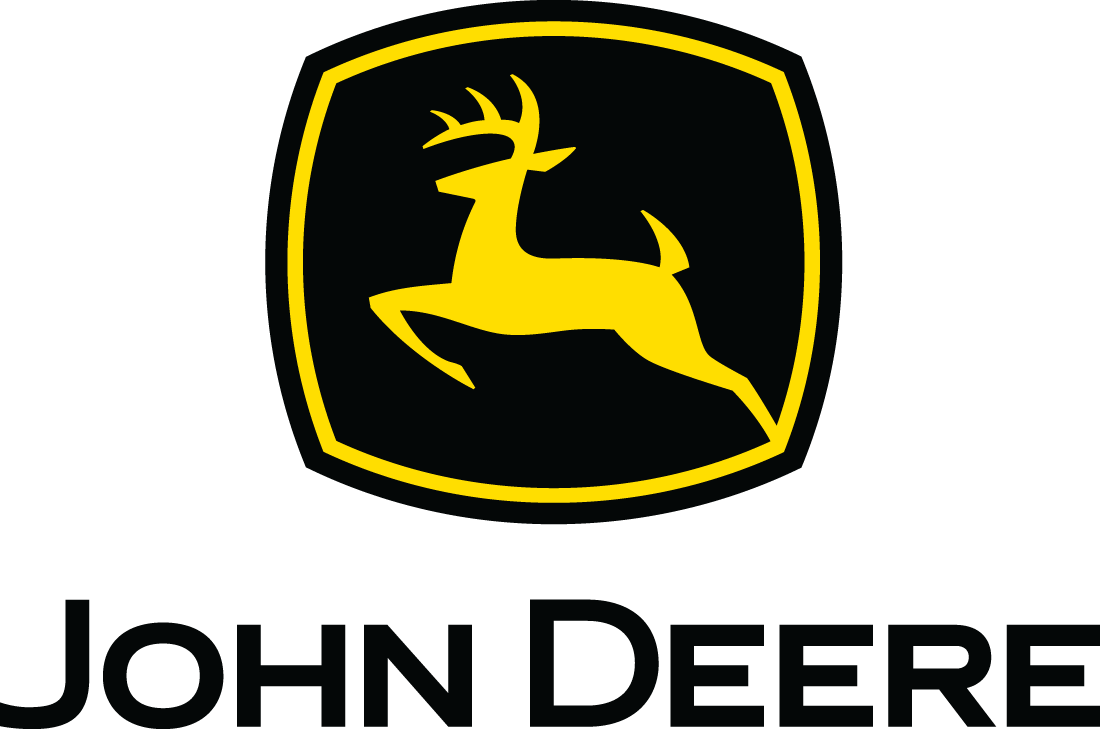
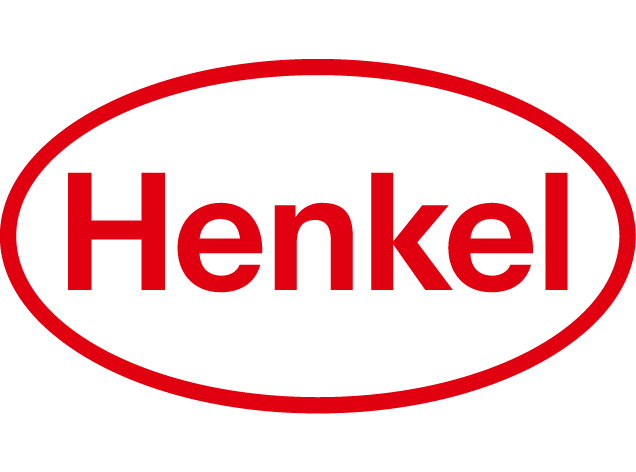
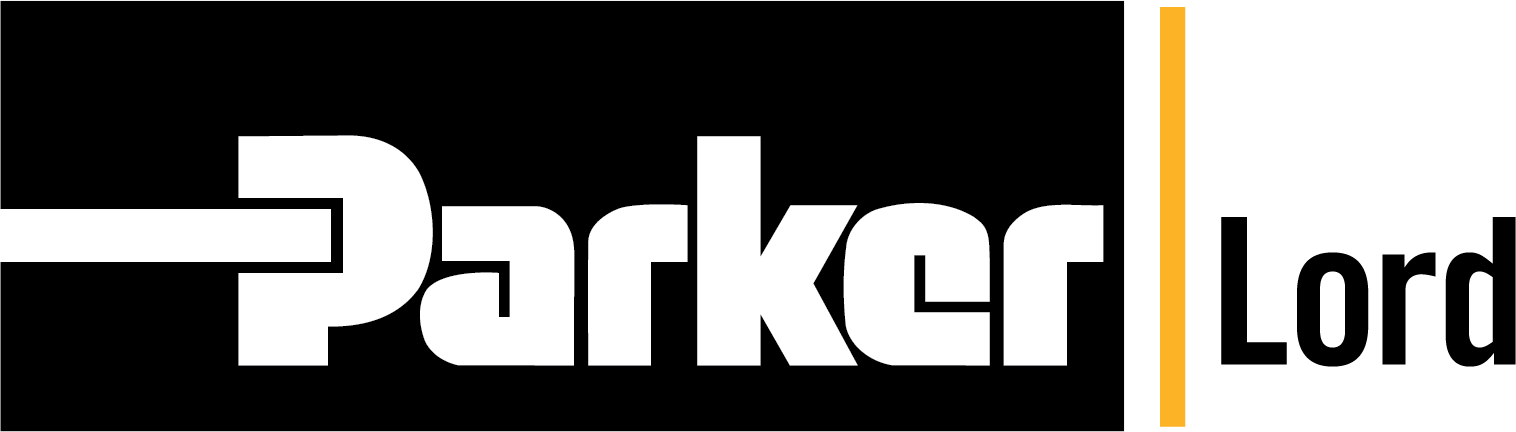
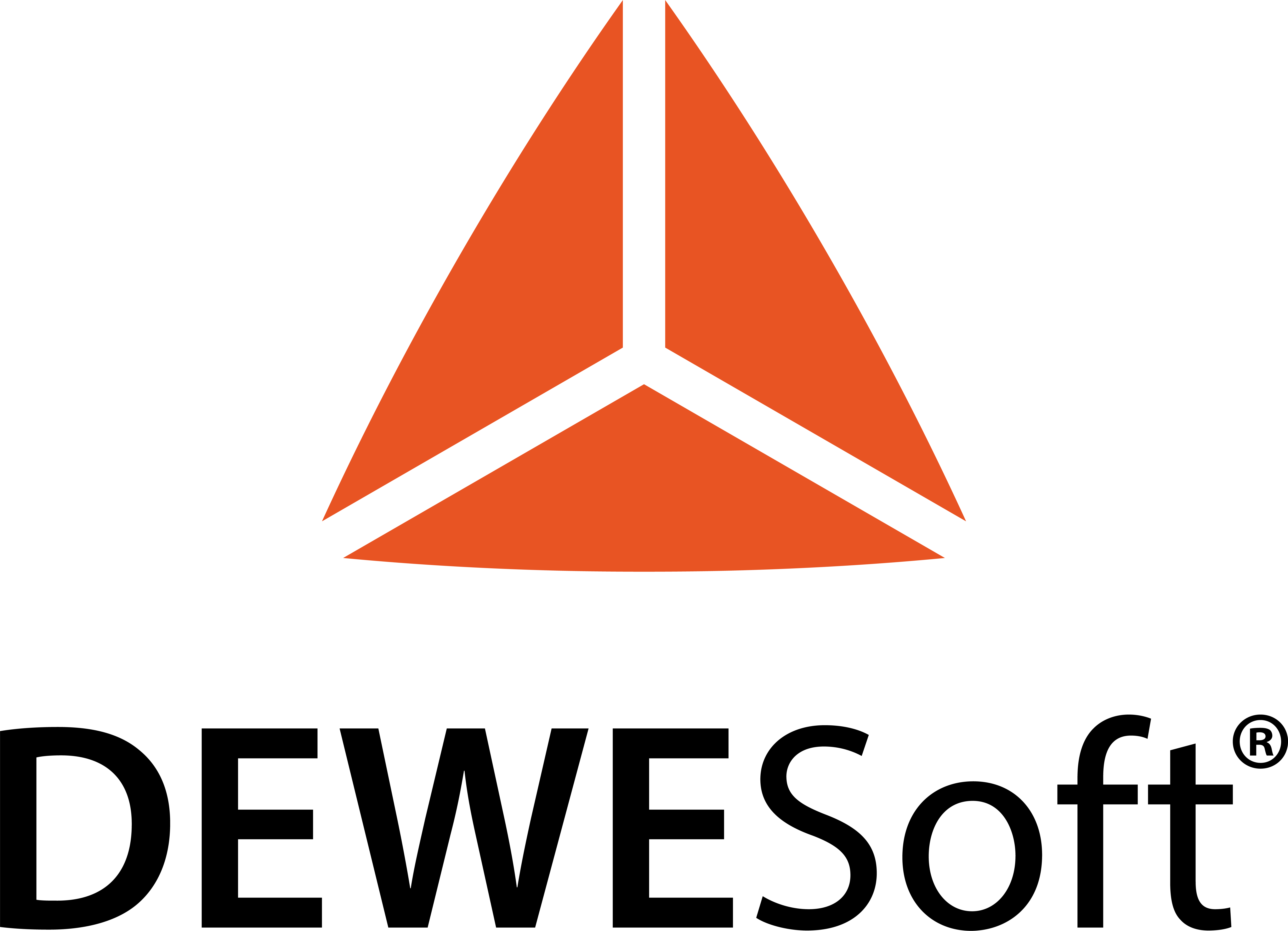
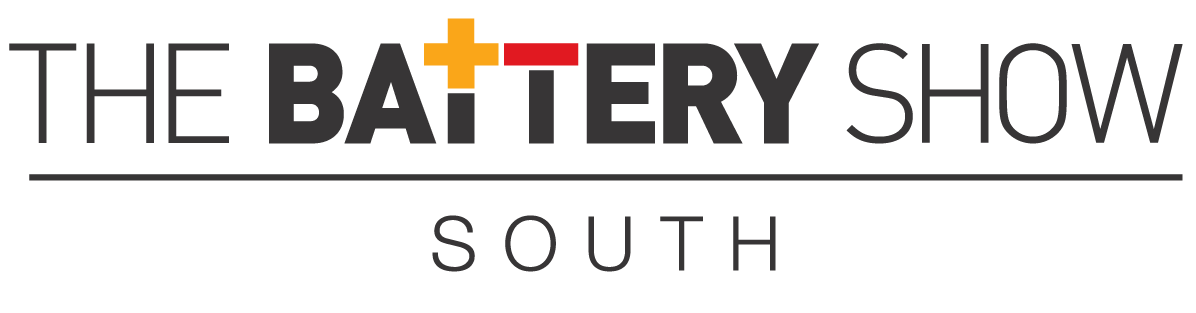
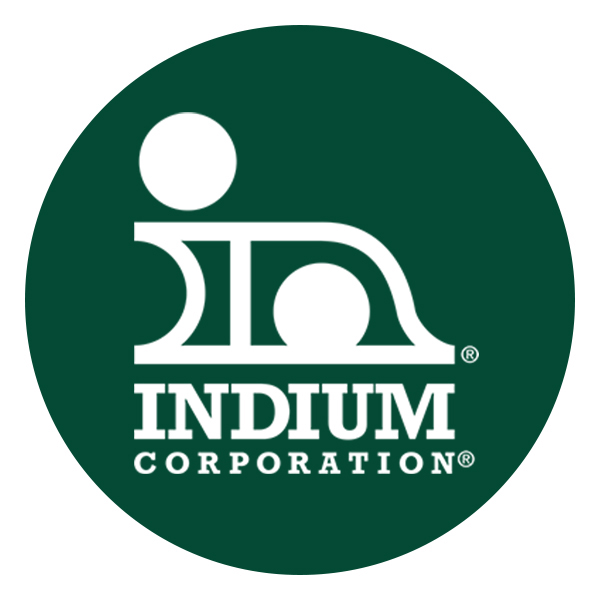
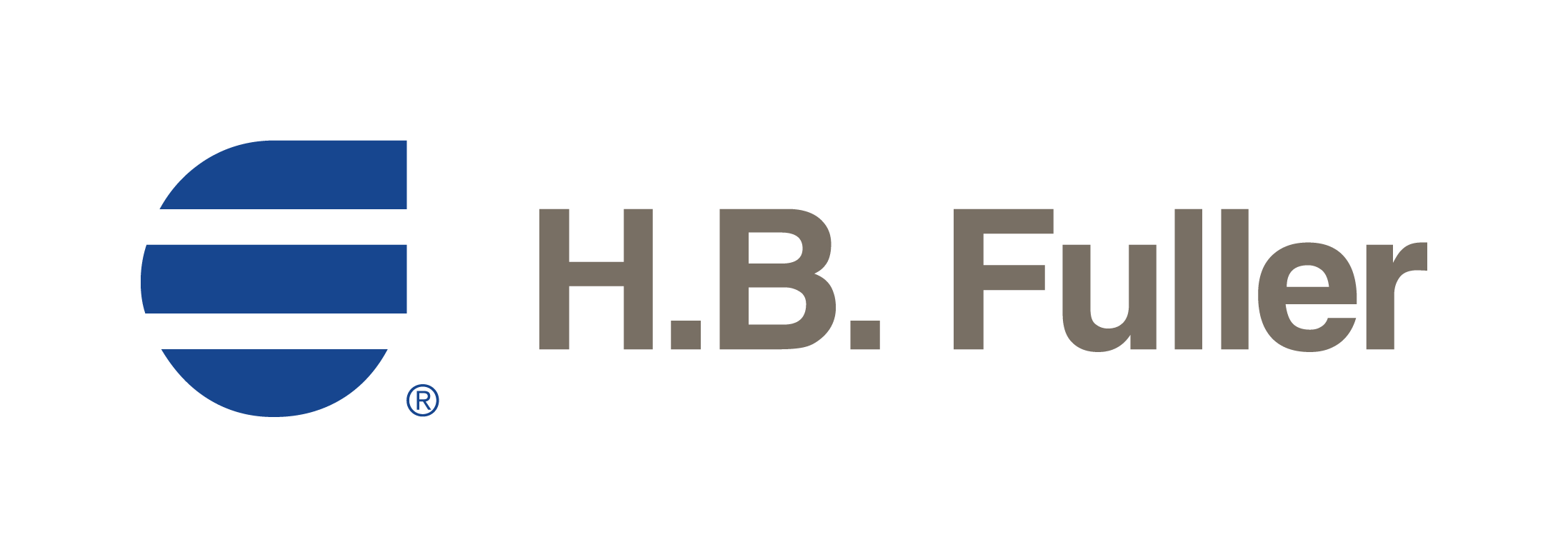