Parallel processing saves energy
As EVs become more sophisticated to appeal to potential buyers, manufacturers will have to pay close attention to both the power consumption and heat dissipation of sensors and their associated computers if they are to squeeze maximum range from the battery, which will require more parallelisation (writes Peter Donaldson).
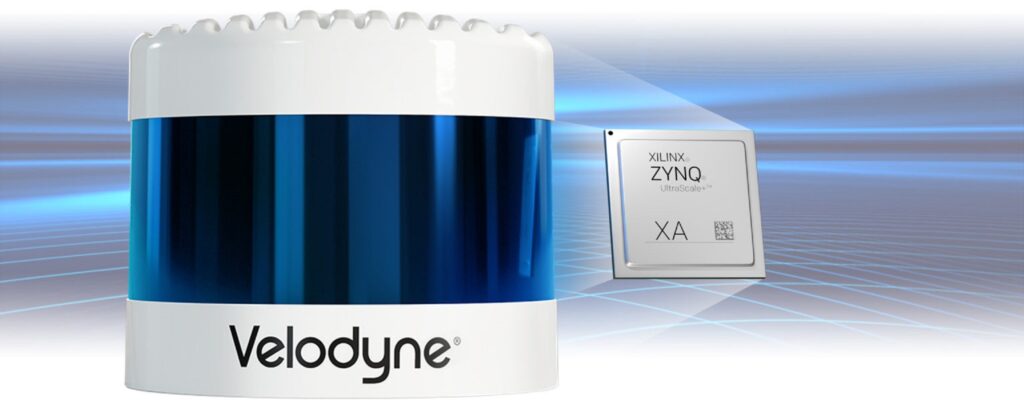
(Images courtesy of Velodyne)
Among the most important of these sensor technologies is Lidar, which is used to create a 3D picture around the vehicle that concentrates on all the moving objects in its environment that could represent collision hazards. This picture must be continuously updated in real time, a task that requires a lot of processing power physically close to the sensor to minimise latency, while at the same time allowing for regular upgrades of in-service sensors as algorithms improve.
This combination of needs makes hardware-based programmable logic devices such as field programmable gate arrays (FPGAs) important for the development of such sensors, as they add more channels in pursuit of higher resolution, for example.
As Willard Tu, senior director of automotive at Xilinx, explains, “Programmable logic gets a bad reputation for needing higher levels of energy, but that’s not really true when you look at it at a system level.” Although FPGAs have more static power leakage than comparable devices, Tu argues that the parallelisation of the signal chain that they enable at low processor clock rates more than compensates for that.
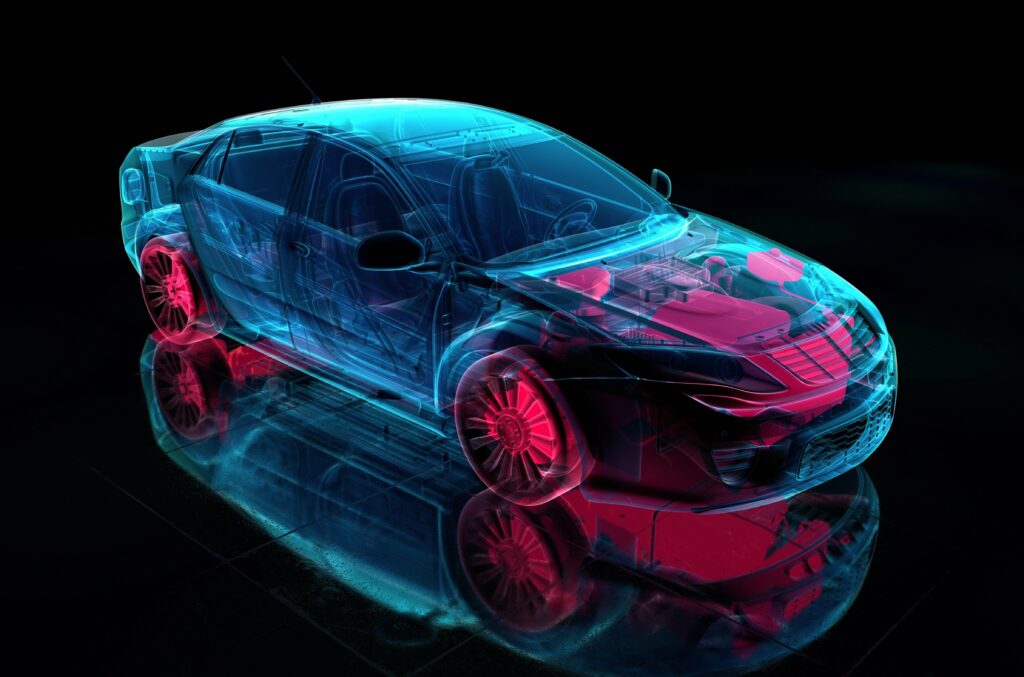
“For example, if you are going from 16 to 32 to 64 channels, to achieve ultra-low latency you are going to have to parallelise your data paths, and for that you can use programmable logic,” he says, contrasting that with solutions based on graphics processing units (GPUs), digital signal processors and CPUs.
“If you are using just GPU- or CPU-centric solutions, the only way you can get more performance is to clock them at a higher frequency, because ultimately they all rely on serial pipelines,” he says. “Instead of clocking at, for example, 1 GHz, maybe I’m clocking at 800 MHz, so that ultimately the silicon will dissipate less power. When you realise what you can do with parallelisation through programmable logic, that becomes an energy-saving moment.”
Xilinx has supplied its MPSoC device family to Velodyne Lidar for its Vella advanced driver assistance system. In addition to the programmable logic, the MPSoC has a processing subsystem with quad-core ARM Cortex processors including an A53 and dual R5s, plus an as yet unused MALI GPU.
Jim Barnhart, chief operating officer at Velodyne Lidar, notes that because Velodyne’s Lidars run relatively cool, it allows vehicle systems designers more freedom to place the sensors in positions that enable the best use to be made of their performance without having to worry about heat dissipation needs and therefore cooling.
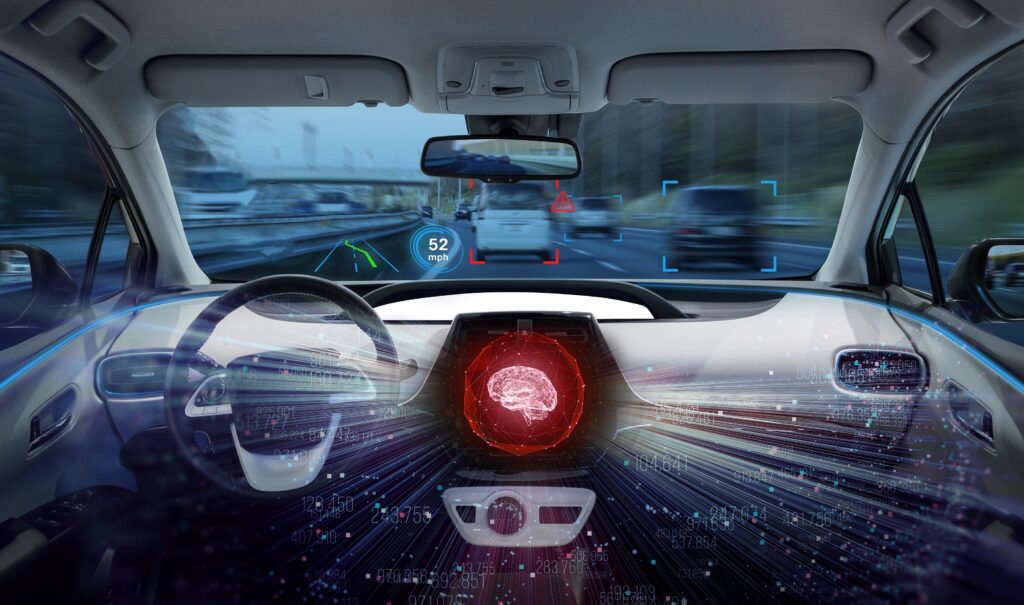
In turn, he adds, that allows more efficient overall use of the vehicle battery. In one case involving a snow plough, the extra waste heat output of a competitor’s Lidar was deemed a benefit because it kept ice at bay!
As Lidars and their algorithms mature, however, Barnhart says the extra efficiency of ASICs become more attractive and their fixed logic less of a problem. “We are investing in ASIC-based capabilities for the future, as we shrink the form factor on some of the products, especially on the solid-state laser side,” he says.
ONLINE PARTNERS
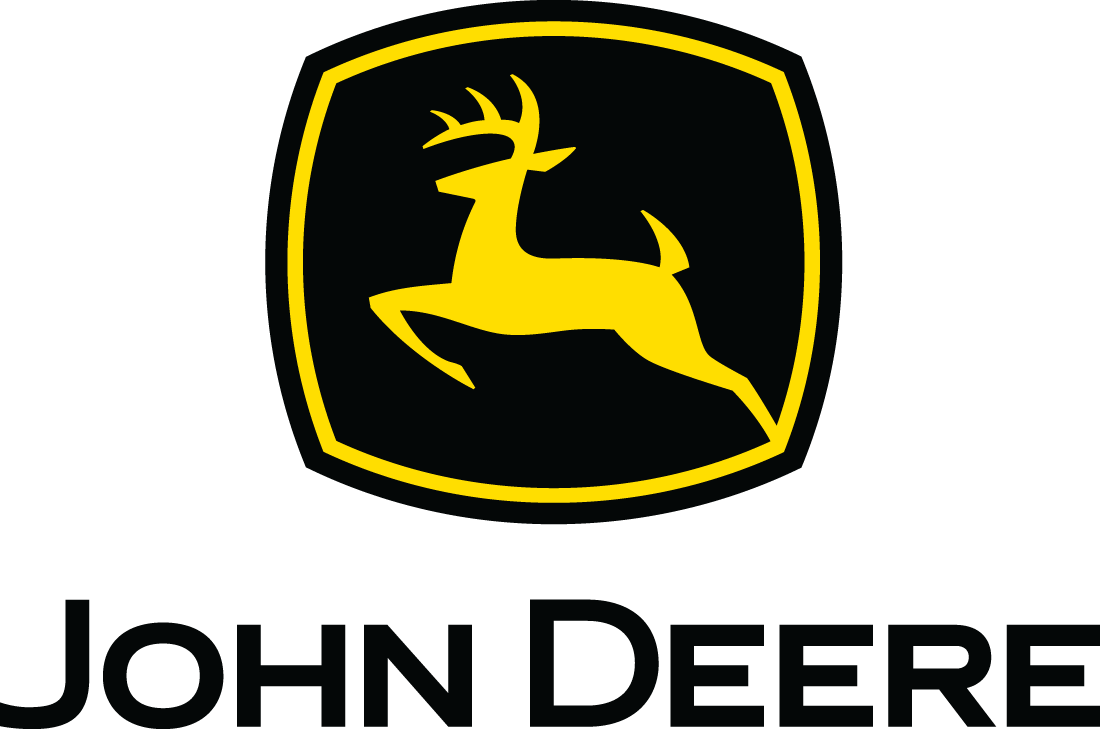
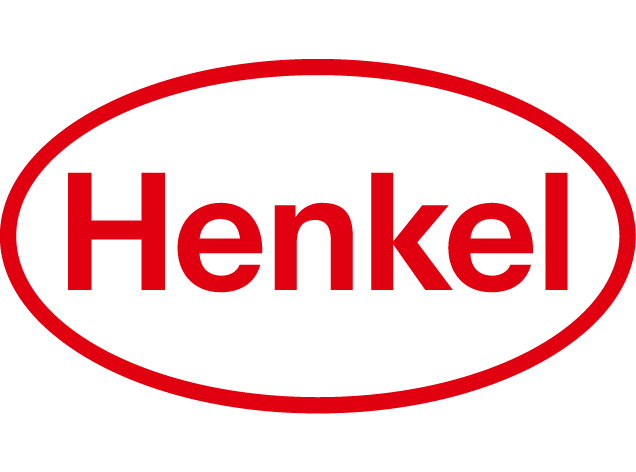
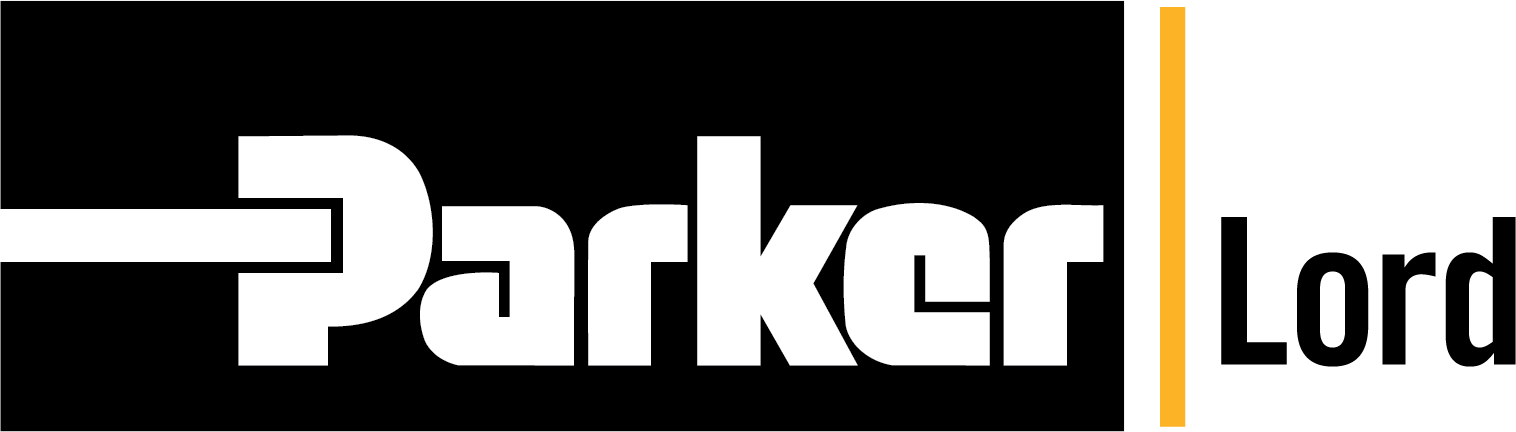
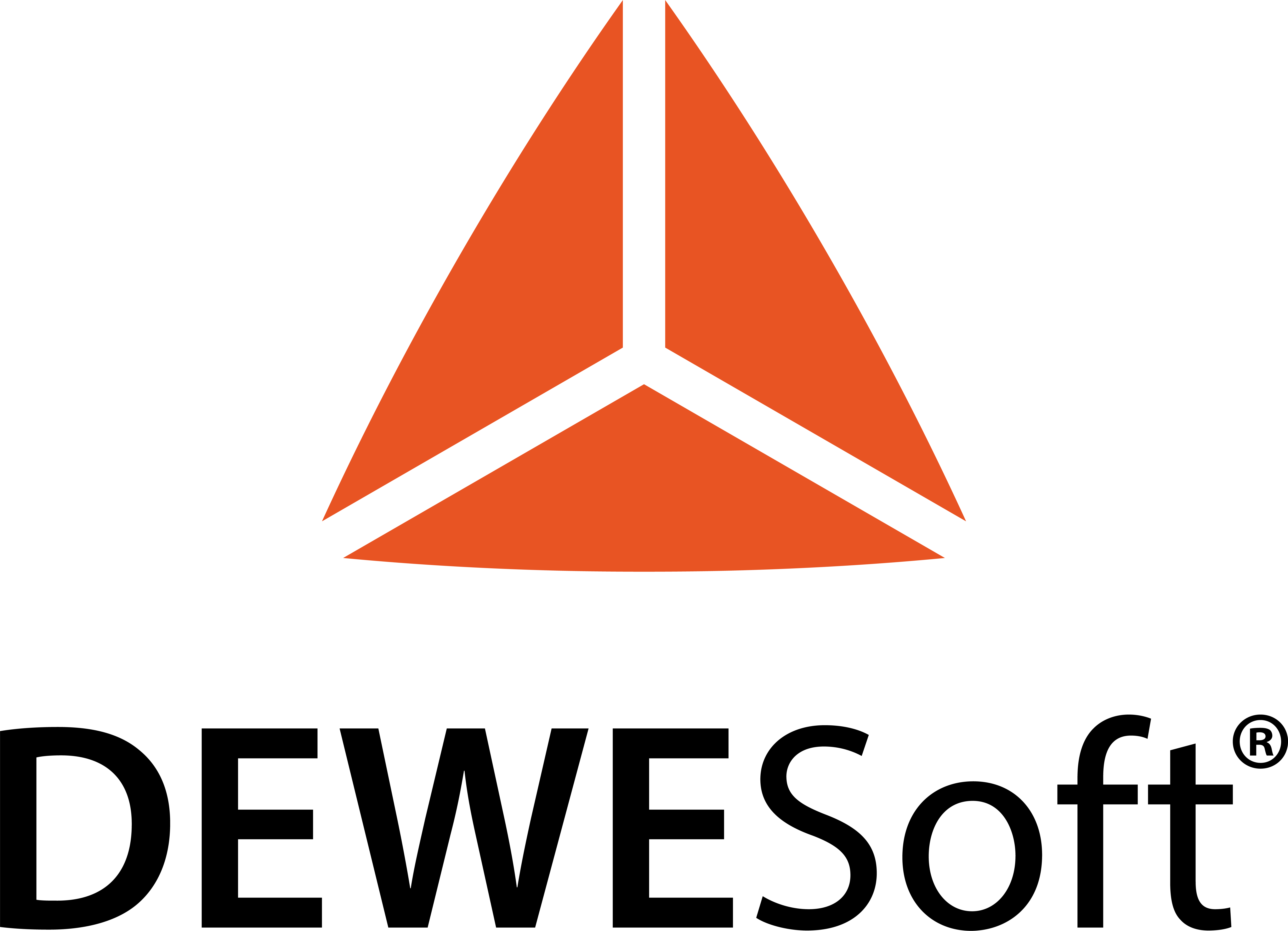
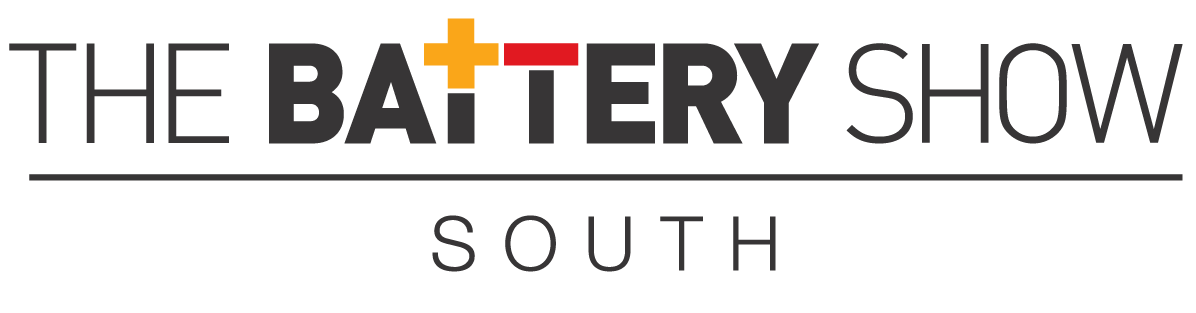
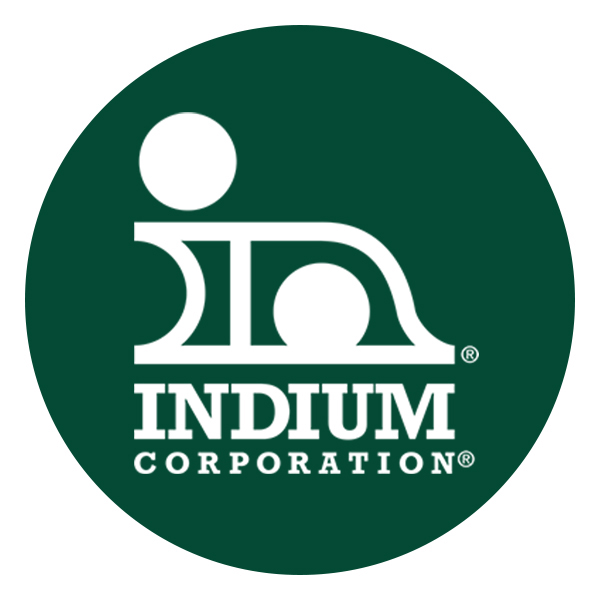
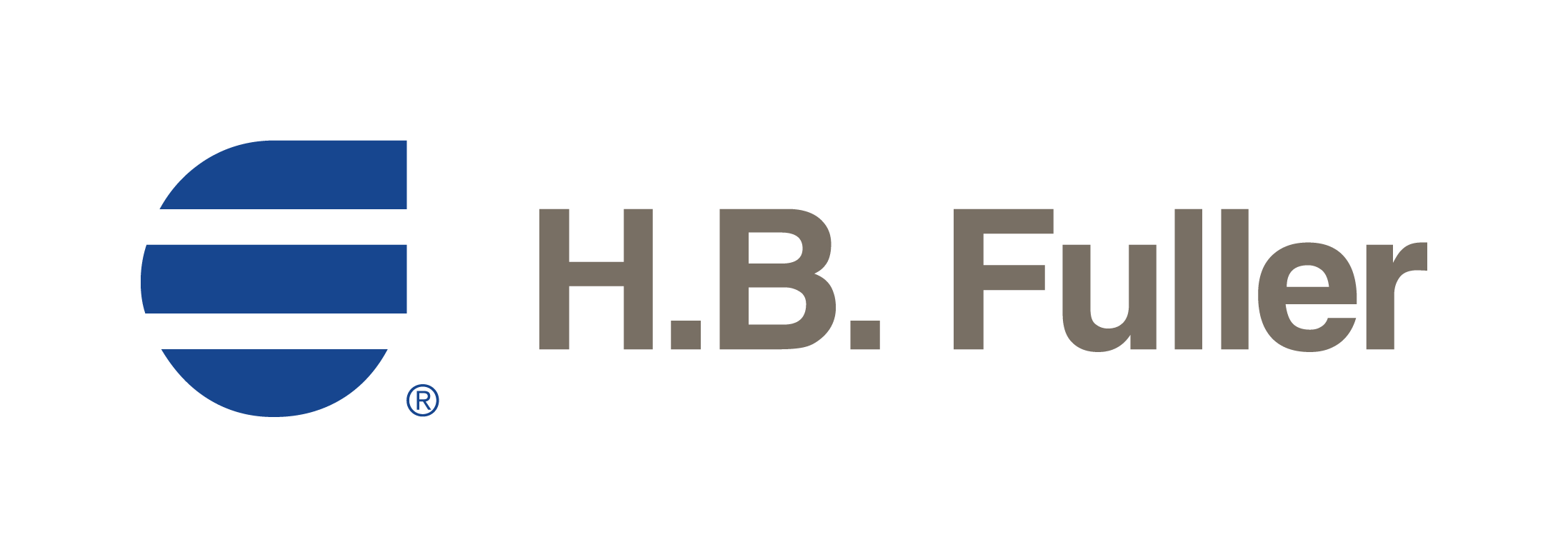