Hybrid approach to safe transport
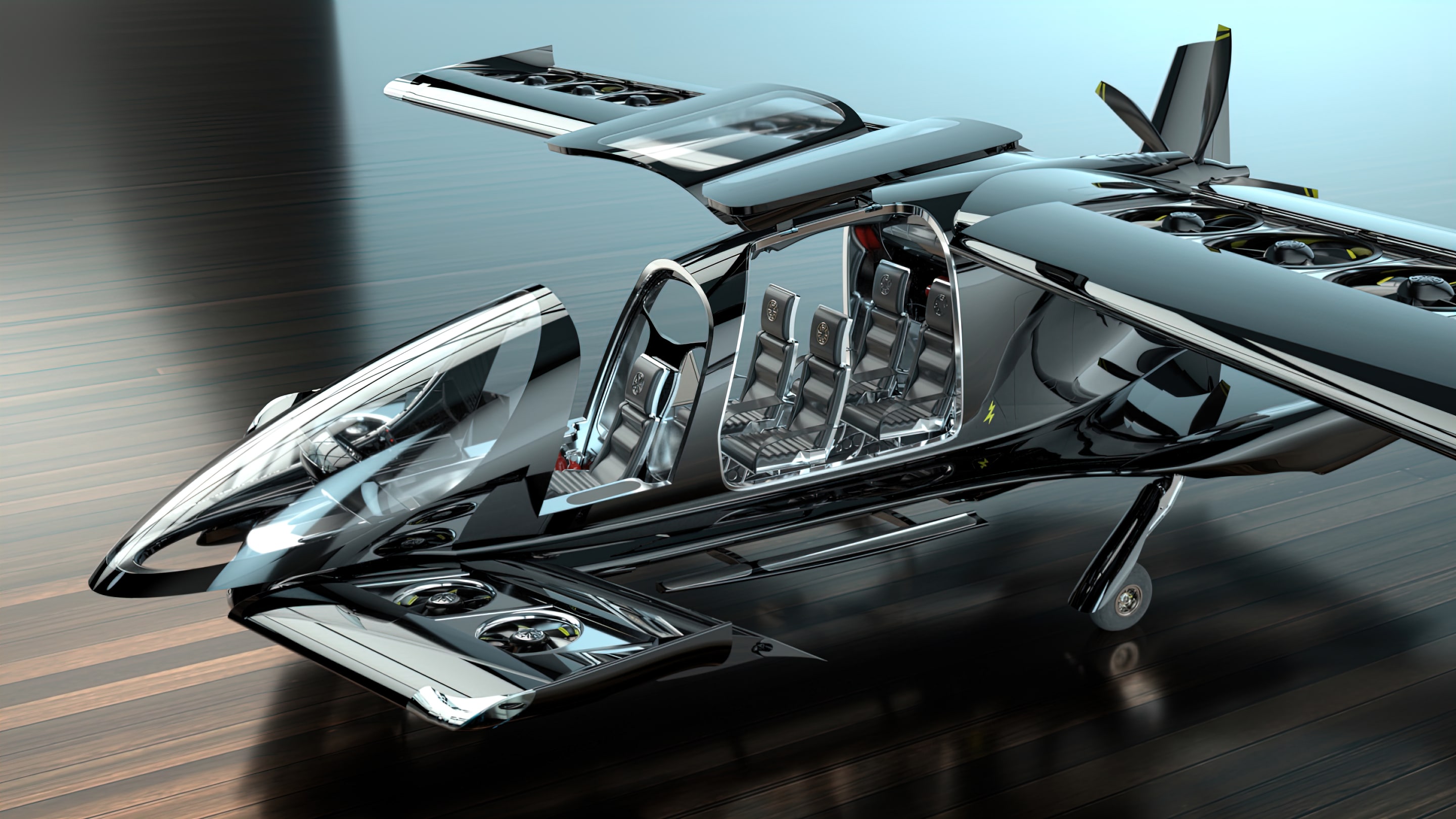
Horizon Aircraft has developed a hybrid electric vertical take-off (eVTOL) aircraft with safety at the heart of its design (writes Nick Flaherty).
The Cavorite x5 eVTOL fan-in-wing platform is designed with a redundant gas/electric powertrain to enable safety certification for carrying up to five people. The high-wing canard design has six motors in each wing and two each in the front canards.
“This is fundamentally different from other eVTOL aircraft,” said Brandon Robinson, CEO of Horizon Aircraft. “Our design started as a normal aircraft and we were looking to get it in and out of smaller areas. Then we looked at the most efficient way to fly. It has to return to a normal configuration for 99% of the time. Quadcopters can carry a lot vertically but spend a lot of the mission [in horizontal flight] paying for that vertical capability.”
The forward propulsion comes from a conventional V8 gasoline engine from General Motors that generates 700 bhp. This runs through a 2:1 reduction drive to an electric motor on the same shaft as the propeller. That decouples the engine and the electric motor and can be used to recharge a bank of batteries that are used to power the motors that provide the vertical lift.
The propeller runs at 1900 rpm from the IC engine running at 3800 rpm for peak efficiency. However, a redundant electric motor would have to run at 1900 rpm to get the aircraft to safety in the event of the failure of the main engine. Instead the vertical fans are used to extend the glide to get the aircraft to safety. This also provides stall protection.
The fans in the wings are individual units with their own battery and controllers, which means shorter cables than having a wiring harness throughout the aircraft. The batteries can be smaller than a straight VTOL design, with an energy density of 150 Wh/kg as they are designed to be used with the forward propulsion to provide lift straight after the aircraft leaves the ground.
“We are currently designing the packs for the wings with lithium-ion cells, nothing too fancy, to give high discharge rates and rugged operation. Because the design is hybrid, lithium-sulphur is too fragile, and the cycle life is too low for us.”
That also fits with the operational concept, where there is another mechanism to recharge the cells on the ground. “The idea is that by the time you get to the destination you have recharged the cells from the IC engine for the most part. In a normal mission the batteries would be recharged for the landing phase, and then there would be a 20-30 minute turnaround time to charge the batteries on the ground,” Robinson said.
Placing the fans in the wings means short ducted fans have to be used, so there are potential structural issues. Normal ducts tend to deform and have tip clearance issues.
“One of the interesting things is that the array of fans give more combined thrust than the sum of six fans, but this is not reflected in the CFD modelling,” Robinson said.
“It’s also much more efficient, operating at an ideal point and using battery power to increase the efficiency. Once the batteries get better we will go
ONLINE PARTNERS
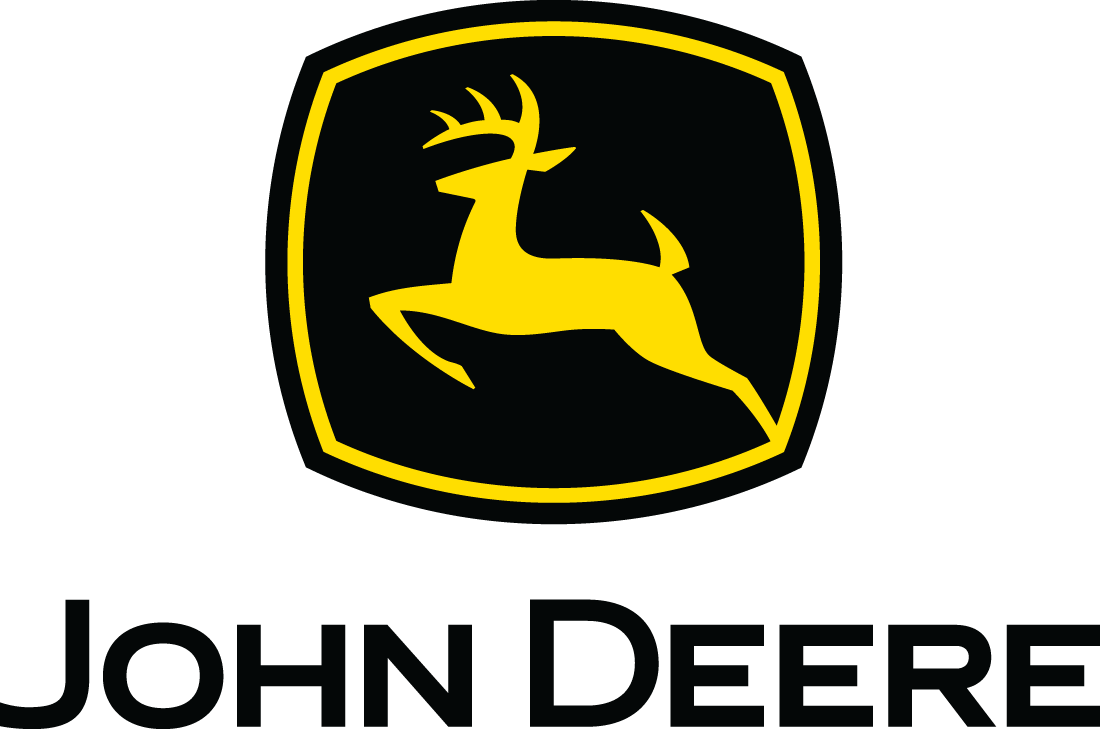
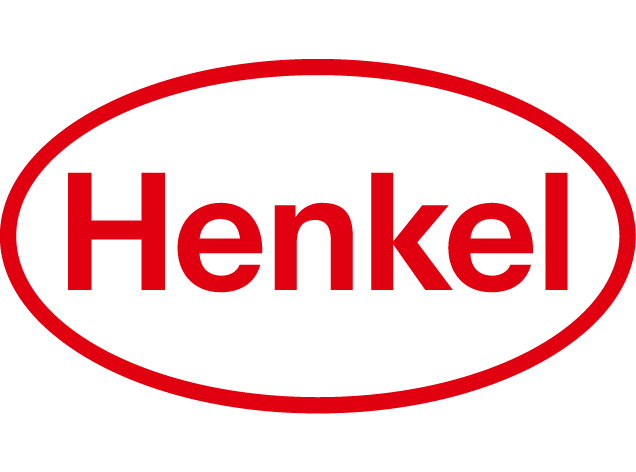
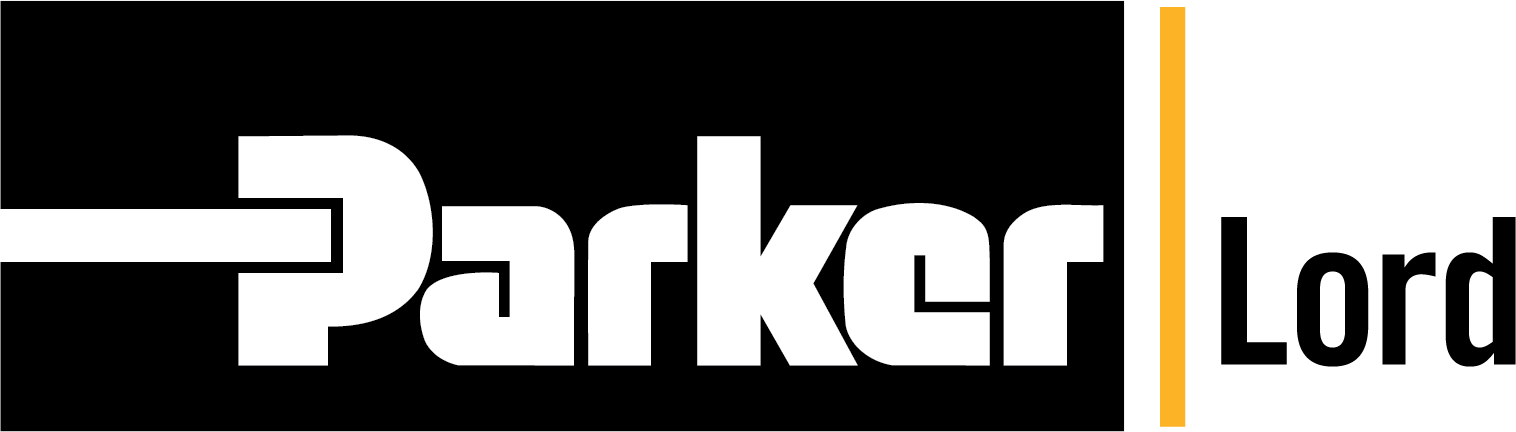
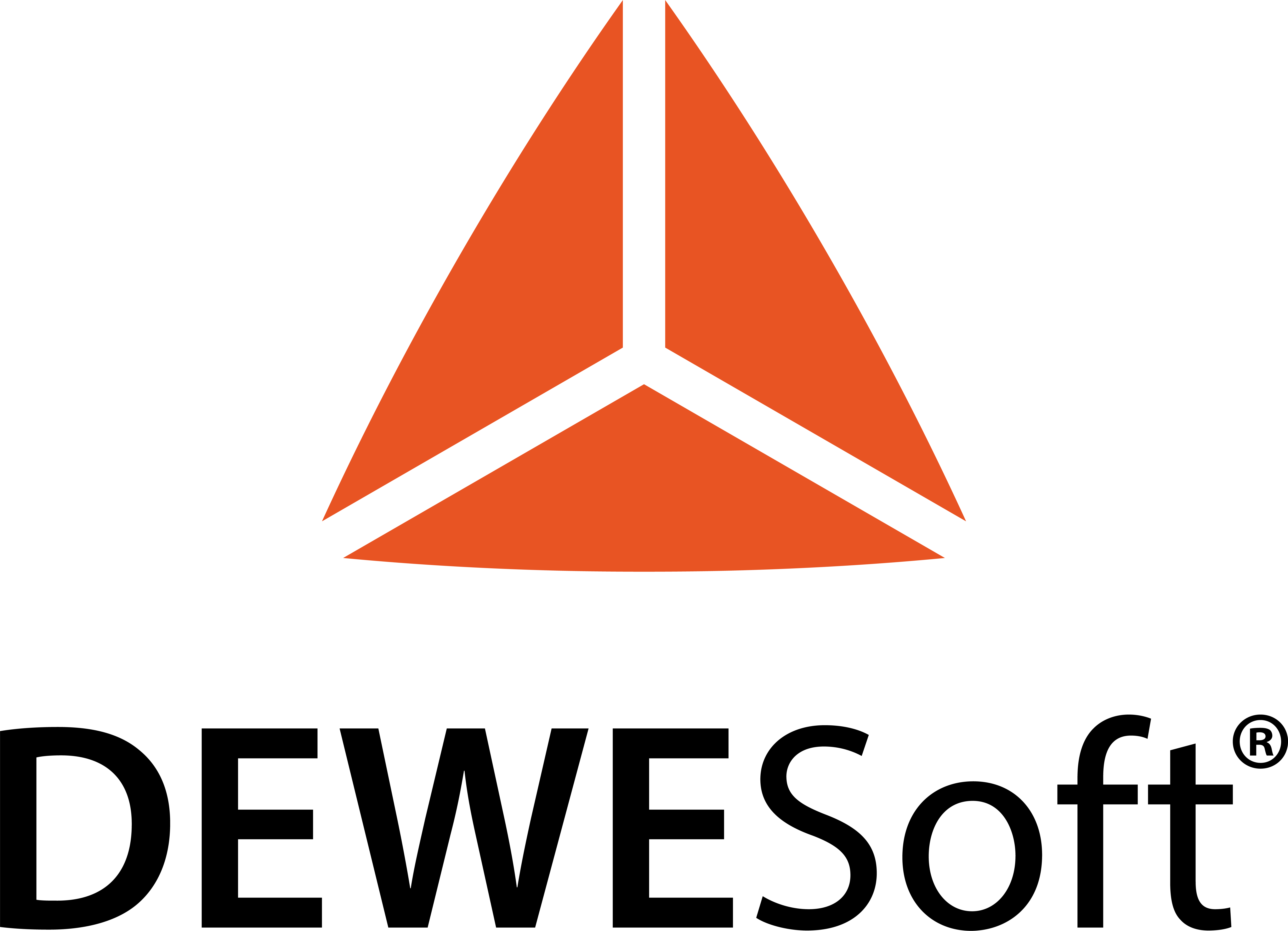
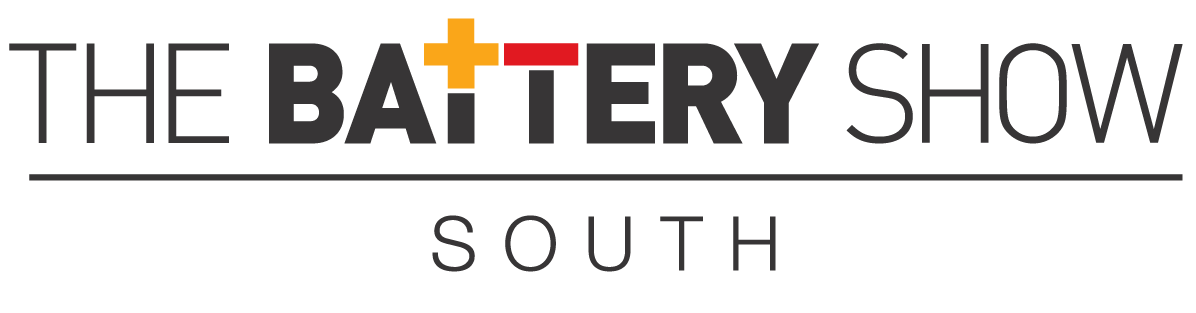
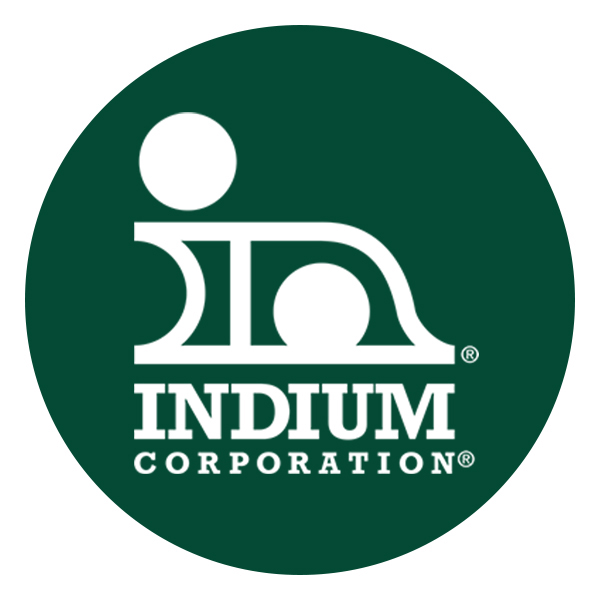
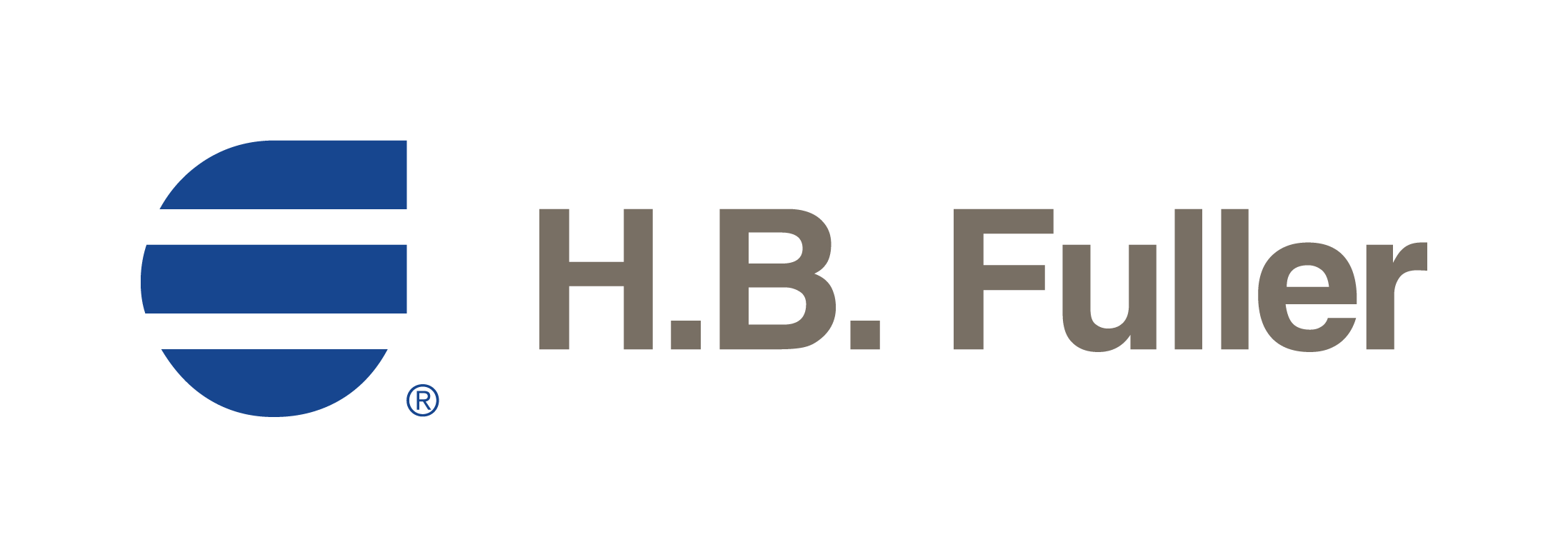