Test system reduces SWaP needs
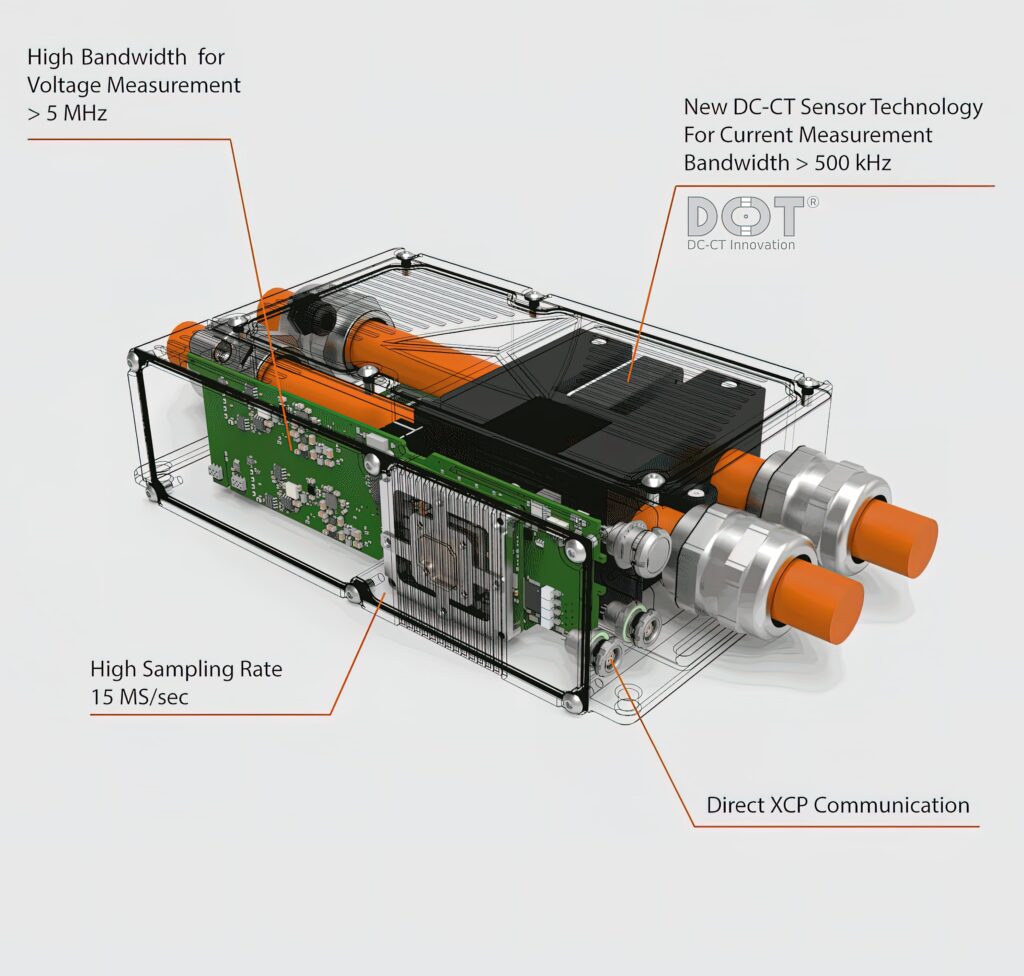
Dewesoft has developed an new integrated 2000 A and 2000 V sensing system for automotive testing (writes Nick Flaherty).
The Sirius XHS-PWR integrates a new current sensor architecture with the DewesoftX software, XCP, or OPC/UA on PoE Gigabit Ethernet with PTPv2 time synchronisation, including high-end data acquisition of 15 MS/s at 16 bits, 1 MS/s at 24 bits, and real time decimation filters for lower alias free sample rates.
The system provides a 1000 A calibrated range with 2000 A peak current sensing up to 2000 V through isolated current sensing technology with a core diameter of 5 cm.
The Platise Flux Sensor DC-CT technology in the sensor has a 500 kHz wide bandwidth with a flatness of less than 0.2 dB within 200 kHz and an accuracy of 0.01%.
The motive for developing a new current sensing technology was to use the best possible properties of a gapless magnetic core and a single-core closed-loop transducer to reduce size and weight, cost and standby power.
The Platise Flux combines a single high-permeability core and a zero-flux closed-loop null-method measurement principle. The DC-CT transducer can be seen as an AC current transformer (CT), where primary and secondary (also named compensation) windings couple the transformer for AC signals down to a few Hertz. As with other closed-loop technologies, the PFS continuously measures residual magnetic flux in the core resulting from the difference between the primary and secondary currents.
The output of the sensor is proportional to the magnetic flux in the core. It drives feedback control circuitry to adjust the compensation current to restore the optimal zero-flux balance in the core. The compensation current therefore perfectly mirrors the primary current, scaled for the number of primary versus secondary turns.
The shielded DC-CT transformer has an outer diameter of 50 mm and provides common-mode rejection of about 64 µA/V at 100 kHz. The transformer itself defines the most important accuracy properties of a transducer, such as hysteresis and thus maximum offset, with typical values of within ±50 mA and typical linearity of 50 ppm.
Transducer secondary current is sensed on a low-ohmic precision burden resistor by a programmable gain amplifier, driving a hybrid analogue-to-digital converter. The total DC-CT current sensing accuracy is thus a sum of the errors from the DC-CT core, the amplifiers, a voltage reference and the hybrid ADC.
Models include single-phase and dual-line configurations. Differential high-voltage sensing ranges up to 2000 V with 5 MHz at -3 dB of flat bandwidth. Current sensing ranges include configurations from 250 to 1000 A, and 2000 A peak current measurement.
ONLINE PARTNERS
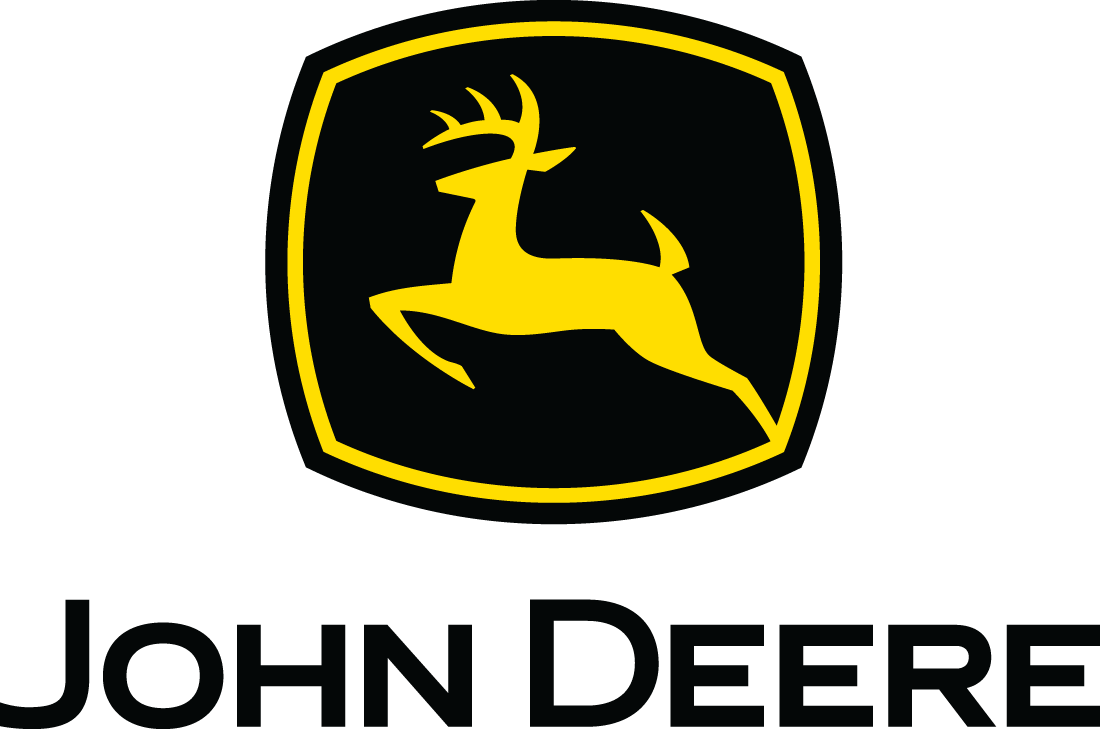
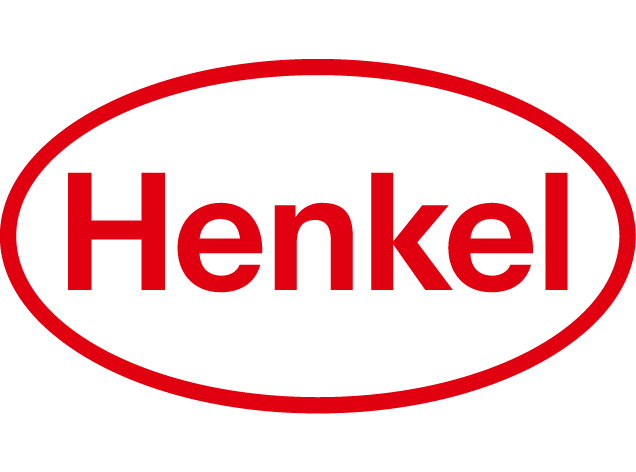
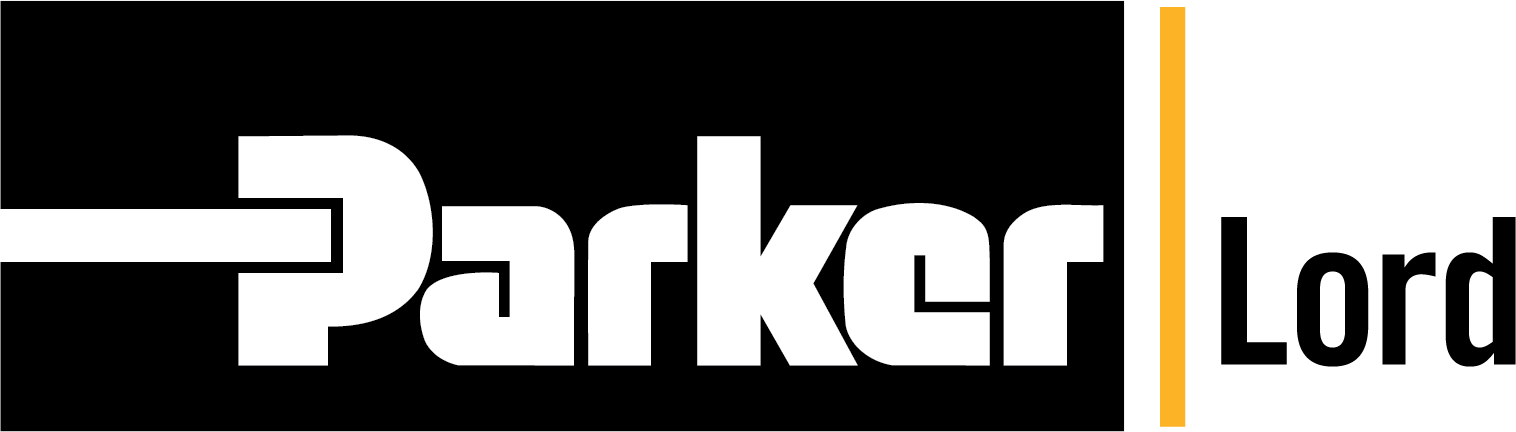
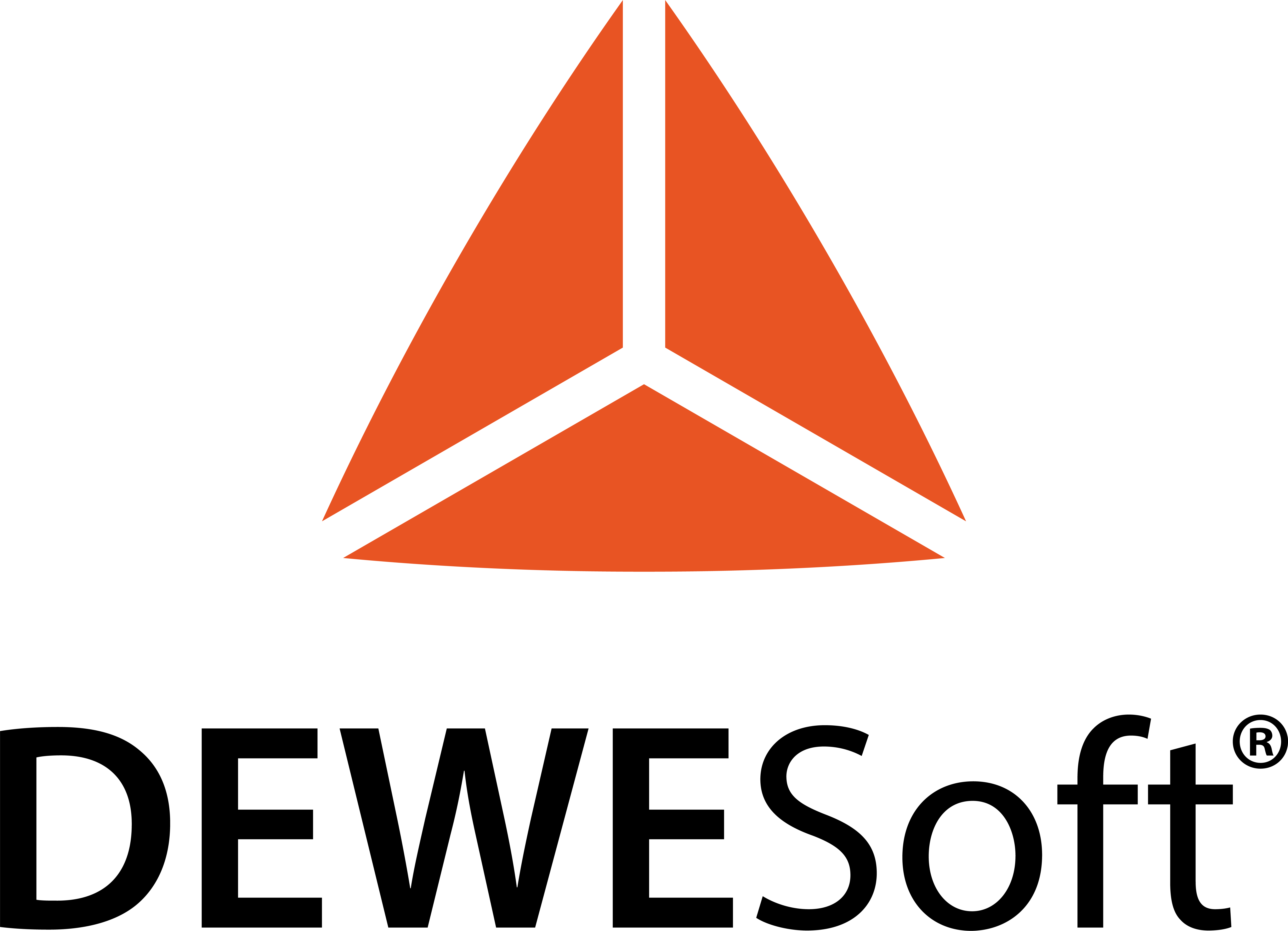
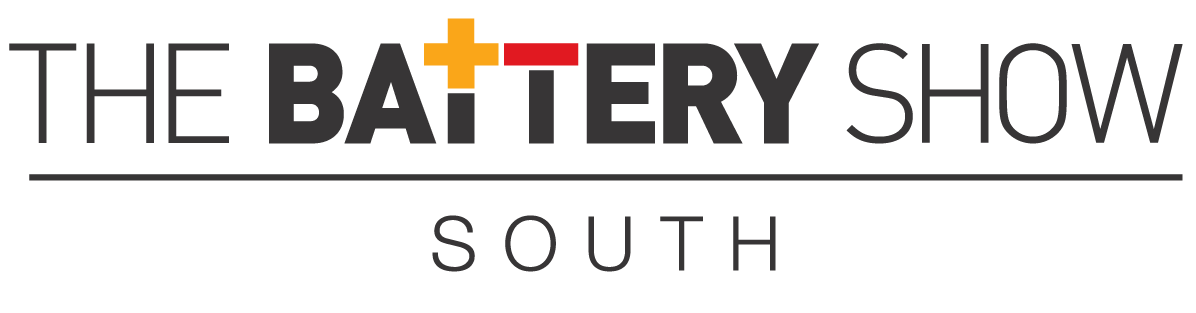
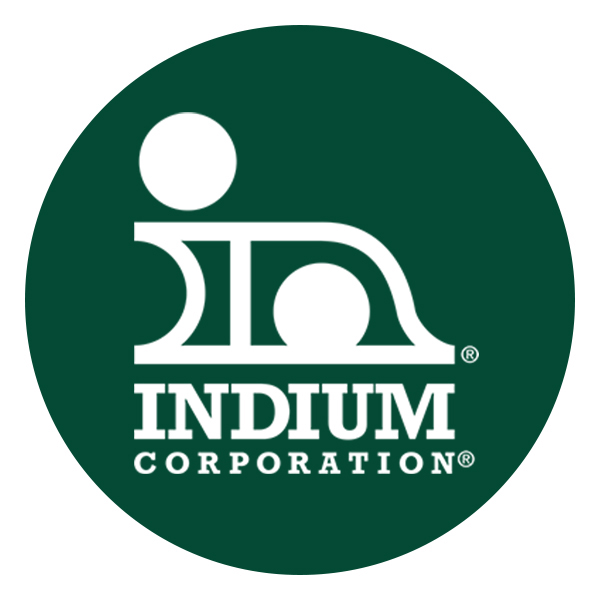
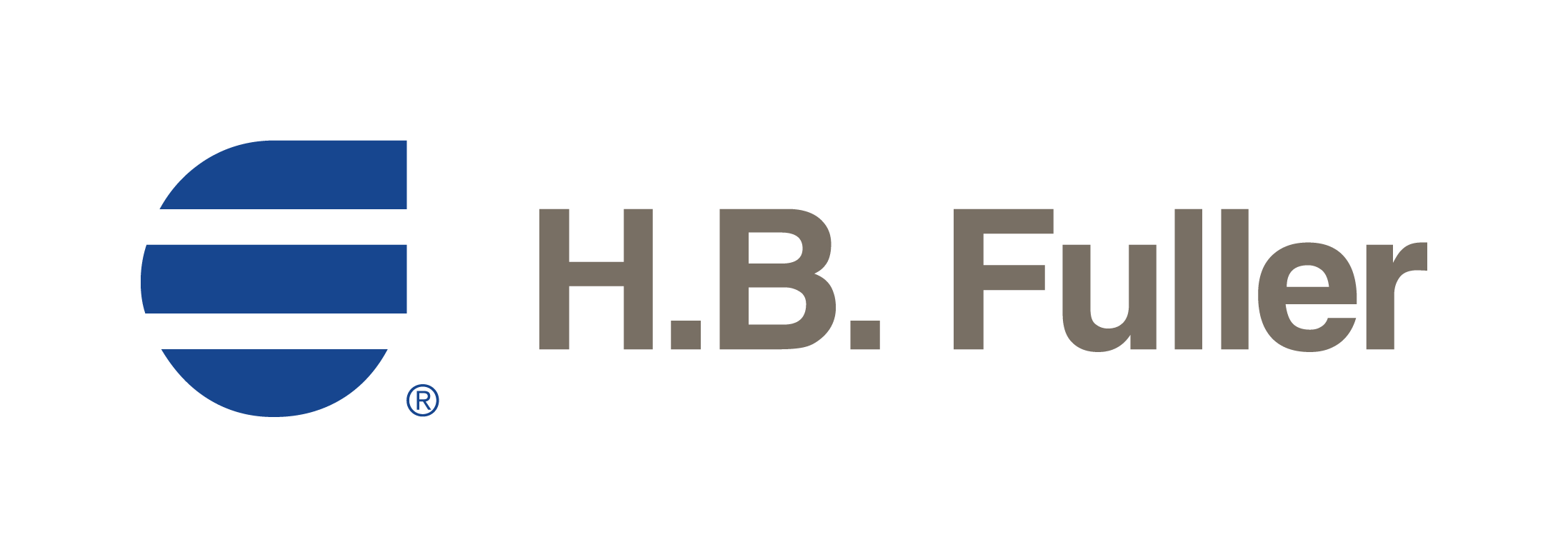