Battery Show North America 2019
The latest battery cooling, management, monitoring and other related technologies were exhibited at this show. Rory Jackson has some highlights.
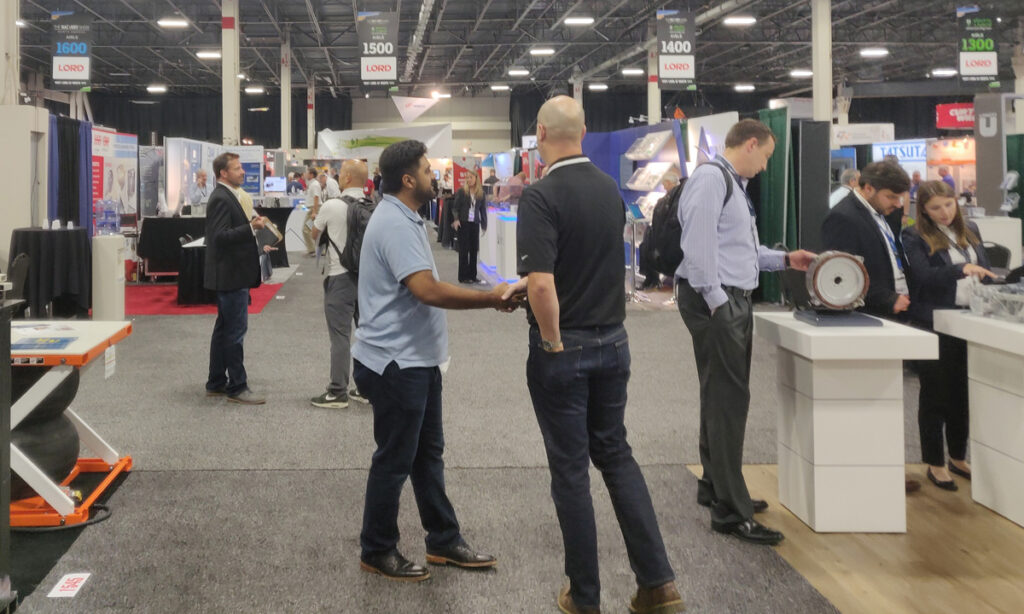
Doing a power of good
Every year, the Suburban Collection Showplace in Novi, Michigan, plays host to The Battery Show North America (co-located with Electric & Hybrid Tech Expo North America). With more than 650 exhibitors and 8500 professionals in attendance, EME attended the show for the second time to uncover the latest technologies and components being unveiled for electric powertrains.
Donaldson attended the expo to unveil a new dual-stage battery vent designed to help ensure proper mitigation in case of a thermal runaway event inside a battery pack.
“The first stage in battery venting is having a porous membrane through which air and other gases are allowed to move in and out of the battery enclosure,” explained Jacob Sanders. “This equalises the pressures inside and outside the pack, given changes in altitude and temperature as the vehicle travels through different locations and environments, while also preventing liquid ingress.
“By keeping liquids out but ensuring that gases can move in and out, our proprietary Tetratex expanded PTFE (or ePTFE) membrane enables the pack to be made lighter and prolongs the life of the battery, particularly by reducing the stress on the gaskets and other seals.”
However, when thermal runaway events occur and gases start being given off at high rates, they often cannot pass through the pores in conventional battery vents’ membranes quickly enough, which can cause pressure to build up inside.
Under these conditions, the second stage of the Donaldson vent begins. The ePTFE membrane is designed to burst open at 300 ±50 millibar, so that the pressure inside the battery pack is rapidly eased to allow the gases out.
“After talking in depth with pack manufacturers about what they wanted, we moved quickly into calculating for specific project objectives, such as making sure the vent was closed to water pressures up to 2.7 bar,” Sanders said. “We then did experiments and automotive-standard tests to identify and validate the dimensions we needed for our target ‘bursting range’.”
The vent measures 47 x 10 mm, and can be housed with IP67 or IP68 protection. The system’s membrane is welded into the housing, the latter being designed with a quarter-turn bayonet interface to allow manual installation onto sheet metal battery housings, and an O-ring seal for water and air tightness at the installation point.
NetPower showcased its latest onboard DC-DC converters for stepping down battery voltages of 400-800 V down to 14 and 28 V, for powering vehicle electronics and cabin systems in commercial EVs.
“Most DC-DC converters in the EV market have basically adopted the same approach used in rack-mount power converters,” said Dr Yimin Jiang. “Those types are easily replaceable, so they generally aren’t designed for reliability to the level that board-mount DC-DC power modules are.
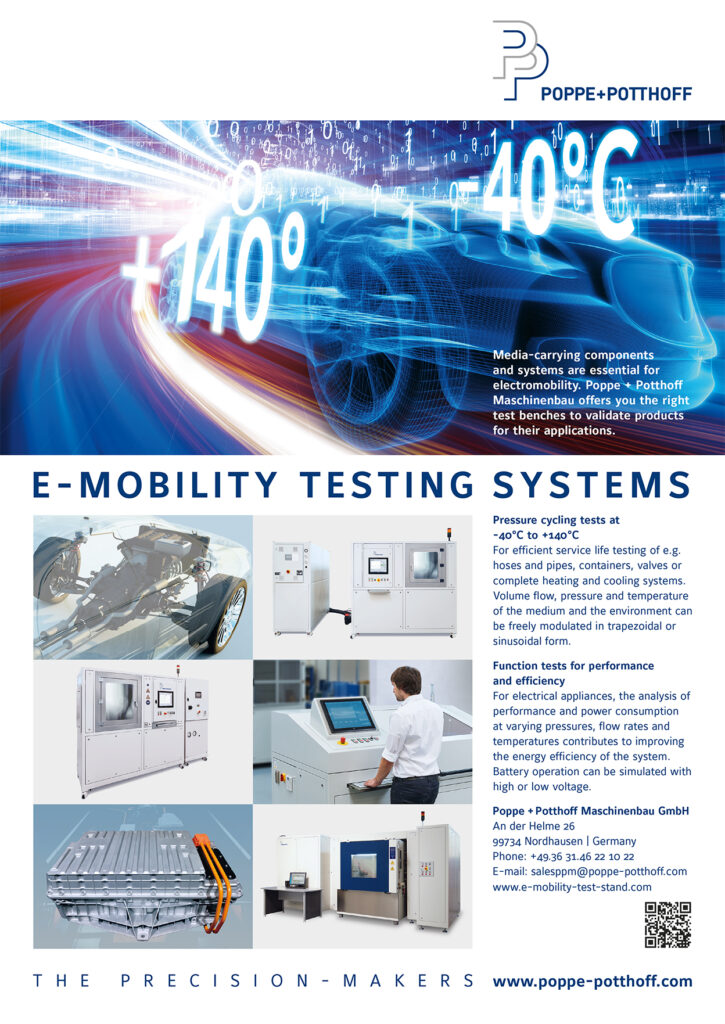
“Often the least reliable component in a power converter is its magnetics. Rack-mount converters use discrete magnetics for their transformer and inductors, and they often have hand-wound windings – a significant bottleneck when it comes to optimising the converter’s reliability.
“We use planar magnetics, in which the windings are built into the PCB, and with the planar magnetic cores simply snapped onto the PCB, you generate simple and reliable magnetic components relative to most of the other offerings at the moment.”
NetPower’s CD13K0-14BL converter has an input voltage range of 400- 800 V, a power rating of 3 kW, and outputs 14 V up to a maximum efficiency of 95%, using liquid cooling for thermal management. The CD13K0- 28BL of the same series outputs 28 V.
“We’ve sought to balance power conversion efficiency, small form factors and thermal performance in our converters, which are the main competing factors,” said Dr Jiang.
“Producing our converters with the board-mounted technologies allowed us to minimise their physical footprint and maximise their reliability.”
Also on display at the show was NetPower’s integrated EV onboard charger (OBC) and DC-DC converter. This OBC/DC-DC combo unit takes an input voltage of between 85 and 265 V AC to deliver 6.6 kW of power to the main onboard battery at voltages between 200 and 420 V DC, as well as 2 kW to the DC-DC output junction at 14 V. It weighs 8 kg and measures 454 x 291 x 83 mm in an IP67-rated enclosure.
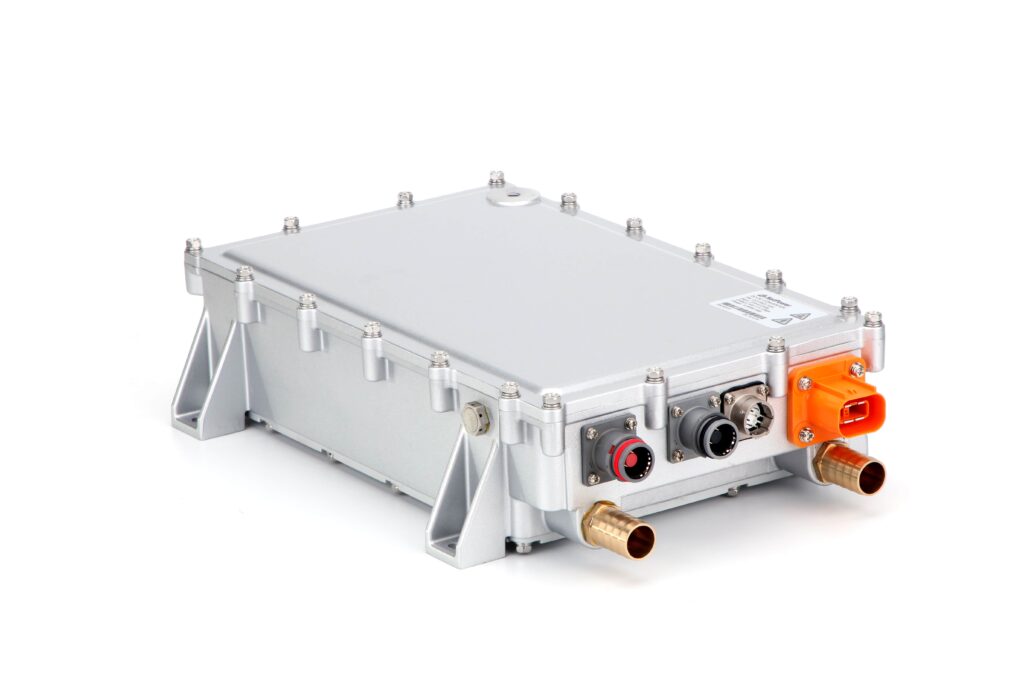
Bloomy Controls showcased its Battery Simulator 1200 product, which is designed primarily for testing battery management systems (BMSs). “It simulates lithium-ion, or indeed any cell chemistry, and contains 12 individually programmable 0-5 V DC cells that sink and source current similar to real battery cells,” said Peter Blume.
“It’s much safer, faster and more resource-efficient than using real cells to validate a new BMS, because each cell has an individually programmable current limit, so you can limit the current to up to 500 mA per cell as opposed to testing with a full-power battery pack. And with a battery cell simulator, you can test extreme conditions without the actual real-world dangers of a battery cell exploding in your laboratory.”
“In terms of speed, you can program for a SoC or edge condition instantly, just by commanding the voltage levels using a PC or controller by Ethernet or CAN link, and simulate various scenarios. Each cell has a four-terminal wiring interface, providing two sense lines for detecting voltages and compensating for drops across the lead wires.”
Each cells is isolated to 1000 V channel-to-channel and channel-toground. That enables many cells from multiple simulator instruments to be connected in series, to simulate as many as 200 cells at a time from a single control interface – for example, to test a BMS being developed for a large battery pack.
“In addition, you can simulate temperature using the analogue outputs, which would emulate thermistor voltages,” Blume added. “The system is FCC- and CE-certified for use in North America, the EU and much of Asia.
“A typical lithium-ion cell is 3.3-3.7 V nominally, and a common use case for testing is to simulate edge conditions and faults such as overvoltage, undercurrent or broken wires.
“Our 5 V DC range allows us to simulate swings in voltage and current outside the nominal lithium-ion values. That functionality can also simulate out-of-balance conditions, enabling developers to test cell-balancing capabilities, with bidirectional current flow between the cells.”
LiCAP was exhibiting an electrochemical double-layer capacitor (EDLC) model that provides 3000 F of storage potential at 2.7 V DC, with a storage capacity of 3.04 Wh.
“This model also uses a cylindrical cell, unlike most supercapacitors [or ultracapacitors] on the market that use pouch cells,” explained Roy Sueda. “The electrode material inside the capacitor is machine-wound in a ‘jelly roll’ design, similar to a cylindrical lithium-ion cell but much larger, and then inserted into the housing and welded and sealed in-place. This approach was much more fitting for the cylindrical form factor we wanted to go with than a pouch cell would’ve been.”
The production process also uses an ‘activated dry electrode’ process instead of a wet slurry process in manufacturing. Here, LiCAP applies activated carbon to the base electrode material without needing a liquid or other substance as a binding agent. This also makes large, energyintensive drying ovens (for curing the electrode) unnecessary, which reduces manufacturing times by removing one of the lengthier steps.
Sueda added, “It also produces a more robust electrode: most electrodes manufactured via a wet slurry process are very fragile. If you vibrate them or subject them to a moderate shock after or even during production, it’s very easy to destroy them. So the dry process gives ours a longer lifespan than most supercapacitors out there.”
The ultracapacitor is 142.2 mm in length and 61 mm in diameter while weighing 520 g. It has been tested to 1 million cycles between its rated voltage and half its rated voltage at 25 C with constant current, which resulted in under a 20% loss in capacity.
Lithium Power showcased its new ruggedised smart batteries, which are designed for various EVs as well as military-grade robotic vehicles.
“The LPI-4875 was originally developed as a direct drop-in replacement for lead-acid batteries in forklifts; our BMS is designed in such a way that it mimics the charging and discharging characteristics of lead-acid packs,” said Stan Chan. “That means end-users can keep their original controllers and chargers without having to change any of their ancillary battery systems or infrastructure.
“Lead-acid chargers have a markedly different charge curve to lithium-ion chargers. We can accommodate that curve – and those of many other chemistries – to enable compatibility and drop-in replacements across a range of pack types in various existing battery chemistry platforms.”
The battery packs can be connected in parallel, with some users having connected up to 10 modules in parallel at once, self-balancing via a single power cable, with no comms between the batteries.
The company can design-in comms links if requested though, in order to track and log battery performance stats, giving the ability to pull up to 60 parameters of information, including SoC, state of health, operating temperatures and so on.
“All of that information can be critical for troubleshooting and fine-tuning the solution,” Chan said.
“We can use our LEDs to display simple error messages, or a CAN bus or SM bus to interface with the batteries and collect more extensive and in-depth information, in a simplified interface to minimise micromanagement.”
Lithium Power typically manufactures its custom battery packs to safety certifi cations such as UL, IEC, and UN standards.
NeoGraf Solutions has unveiled its newest thermal management solution, its SpreaderShield cooling fins. These thermal spreaders are made from flexible graphite, and are designed for battery pack manufacturers to help with the problem of managing thermal distribution and heat routing through their packs.
“Current thermal solutions are typically aluminium plates or a bulky, complex, liquid-cooling system,” Bret Trimmer explained. “As a material, aluminium is moderately thermally conductive, but it is also very thick and dense. That drives up the overall size and weight of the battery.
“Our graphite cooling fi ns give the same heat-spreading performance as aluminium, but at only half the thickness and a third of the weight. This assists with two of the major EV design problems, which are the weight and physical footprint of the battery pack.”
SpreaderShield undergoes faster rates of thermal distribution across its surface than aluminium. Battery cells, especially prismatic and pouch cells, perform better and last longer with a uniform temperature distribution across their surfaces.
“SpreaderShield for EV batteries is an all-natural graphite product, Trimmer said. “The material is engineered to have high thermal conductivity in the x and y planes, exceeding that of copper.
“We’re in the 400-600 W/m·K range in the x and y directions; the throughthickness conductivity is 4 W/m·K. This performance comes from the sheetstructure of graphite’s atomic graphene layers. Aluminium spreads at about 180 W/m·K in every direction, which unfortunately enables hotspots to go right through its thickness, affecting the adjacent cells.”
Dorman Products exhibited a range of its re-manufactured HEV battery products, which are aimed at improving the reliability and longevity of hybrid powertrain energy storage packs.
Alex Litvinchuk explained, “What typically happens is that one or two cells in a HEV battery pack will fail, making them little more than scrap to the HEV owner. We take those batteries, ‘remanufacture’ them and make them available to end-users at a fraction of the price of a new battery pack just off a production line, but with exactly the same warranty.
“At the moment, we work largely with nickel metal hydride chemistry cells, because they are the battery types that are going out of warranty across the market.”
The company uses a range of battery test systems (from its partnership with Maccor) to grade each battery module, with very strict (but undisclosed) internal tolerances and guidelines for matching cells and components to their modules.
In addition to testing for cell balancing, Dorman applies sealing to every module to minimise the risk of leakages, and runs performance and emissions tests on its assembled modules using a vehicle dynamometer.
“Across batteries doing similar kinds of work we try to find common failure modes,” Litvinchuk said. “For example, there tends to be some corrosion on the busbars, so we often replace them and install special inhibitors that reduce future corrosion. That enables us to collect a lot of new real-world data on how these batteries fail – data that couldn’t have been predicted by simulation software.
“We manufacture one battery at a time, on an assembly line, which enables us to ship more than 500 battery packs per month. We also incorporate all the necessary electronics, sensors and control modules to ensure our endusers receive these batteries as turnkey solutions.”
TE Connectivity unveiled the HV-20T, a new high-voltage, 20 ton force terminator press designed for crimping terminals and ferrules onto wires for HV cable applications.
“Whether it’s a ferrule crimp, a traditional F-crimp, or a closed-barrel crimp, the press will crimp wires up to 120 mm2 ,” said Cameron Hayden. “Its main feature is that it has CQM – crimp quality monitoring – technology, which helps to detect whether a crimp is good or bad.
“That is based on the force of the crimp, which is detected by sensors in the framework of the press and gauges how far the pressure is from the expected value for a good crimp. If there’s not enough force, or too much, then the press has encountered the wrong level of resistance from the terminal or wire. Also, the CQM can detect up to 7% of missing strands.”
The HV-20T also includes an optional particle vacuum, for cleaning the crimping area and preventing the presence of chips or loose particles that could create arcing issues and field failures in the crimped cables. The cycle time of the press can be controlled, and ranges from 1.8 to 8.3 s per crimp; so far, the fastest recorded total time for loading a wire with a terminal and performing a crimp is just under 12 s.
The press can operate on a 200 or 400 V power supply, consumes 3 kW during normal operations, and weighs 390 kg (or 392 kg if the particle vacuum is selected).
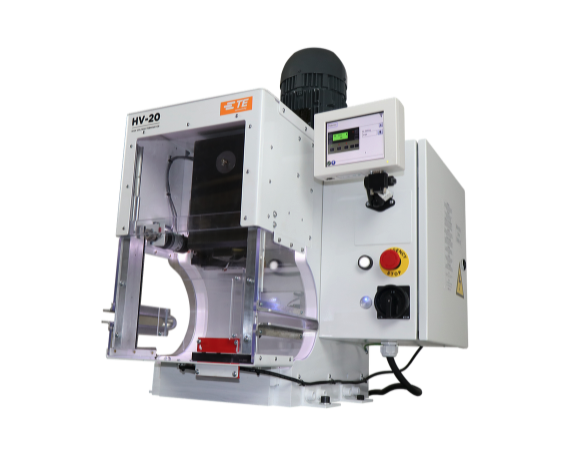
Paraclete Energy attended the expo to showcase its SM-Silicon/3590 anode material, which it offers as an enhancement to (or replacement for) graphite anodes.
“The best-performing graphite has a capacity of around 350 mAh/g, whereas our SM-Silicon/3590 has nearly the full 3590 mAh theoretical capacity of elemental silicon,” explained Brian Byars. “It can be mixed with graphite in any desired percentage to obtain the capacity needed for a given application, since it has a TAP density very similar to graphite – 0.8 g/cm3 for SM-Silicon/3590, compared with 1.1 g/cm3 for graphite.
“This is unlike oxidised silicon [SiOx], which has a TAP density of about 0.08 g/cm3 , so SiOx therefore takes up nearly 10 times more volume with inactive oxide. That can have adverse effects on batteries when mixed with graphite.
“Our first-cycle efficiency is 85-94%, which is also superior to SiOx, at 65- 70%. Because SM-Silicon/3590’s capacity is up to six times that of SiOx, a customer can use much less to achieve the same goals, saving money and space.”
The SM-Silicon/3590 solution also has an artificial SEI (solid electrolyte interphase), which acts as a 3-5 nm surface modifier, allowing the silicon to expand and contract within the SEI without being exposed to the battery’s electrolyte.
While SiOx can fail at around the 50th cycle, or with a hard carbon shell at around the 150th cycle, Paraclete’s artificial SEI architecture prevents this in the SM-Silicon/3590, enabling it to last beyond 1000 cycles for many applications.
With the SEI, SM-Silicon/3590 also eliminates the problem of hydrogen offgassing, which can lead to expansion of pouch cells with SiOx and possibly bursting. Because SM-Silicon/3590 does not off-gas, its pouch cells experience 98% less volumetric expansion.
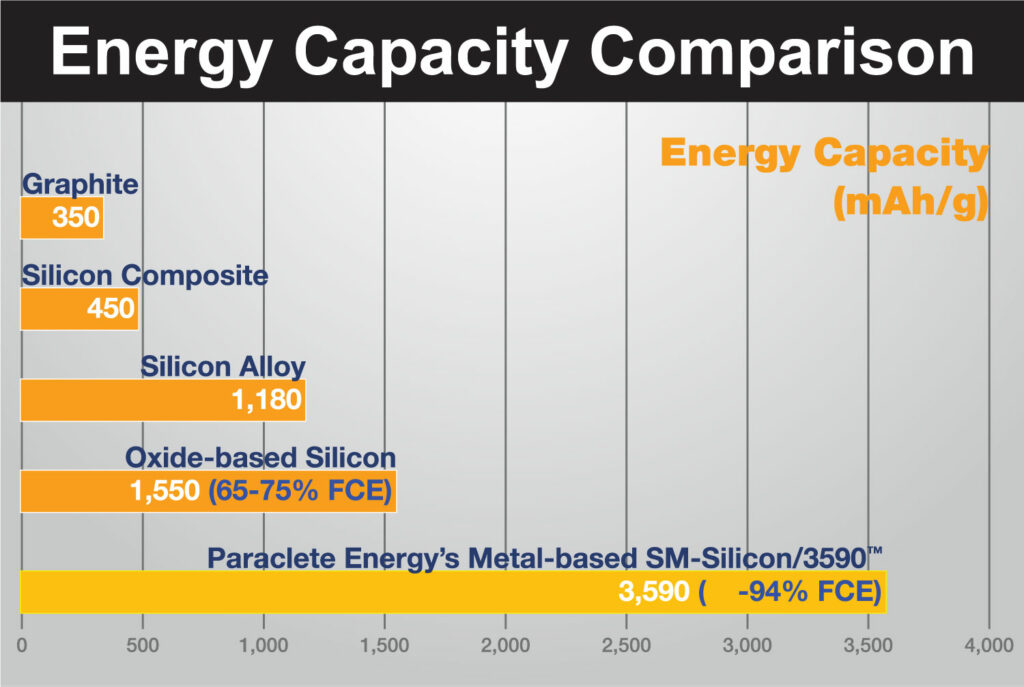
Aspen Systems had on display a range of liquid cooling, direct refrigerant cooling and air cooling solutions developed for thermal management projects in EVs, HEVs and charging infrastructures.
“In the American Solar Challenge – for EVs powered by the sun – the regulations were changed to where the vehicles had to maintain a temperature below about 45 C in the battery pack,” said Jim Burnett.
“We supplied a team from Principia University with a chiller system to keep their batteries in safe operating conditions, comply with the regulations and improve the energy efficiency of the batteries, to make the most of the solar panels’ recharge without heat losses.”
Aspen also showcased a 550 W cooling system designed for comms electronics in the backs of defence and government services vehicles, to enable rack-mounted electronics designed for large, heavily-air-conditioned rooms to function in the cramped quarters of relatively small vehicles. Since then, it has also designed a larger, 1.8 kW version of the same system.
Aspen also designs and supplies direct refrigerant systems, piping a liquid coolant through an aluminium cold plate so that EV or electronics manufacturers can mount batteries either directly onto the cold plate or other components. Systems as large as multiple square-metre cold plates have been developed for projects on cooling vehicles’ batteries and phased-array antennas.
The core technology of most of Aspen’s thermal management systems is its proprietary compressor, which to Burnett’s knowledge is the smallest production compressor in existence.
The compressor was first developed by the company for a project aimed at cooling dismounted soldiers. Aspen has since re-purposed the technology for cooling batteries, electronics, lasers, medical devices and other EV powertrain components.
Burnett explained, “Most cooling systems need a 10 lb compressor that’s about the size of a football; ours is smaller than a baseball though, and has the same capacity as the larger systems.
“We get all the displacement and refrigerant fl ow we need from our highrpm variable speed BLDC motor in the compressor series, which pushes a high volume of refrigerant through the heat exchangers. The compressor comes in 12, 24 or 48 V DC versions at the same size, and can run off of AC or DC power depending on end-user requirements.”
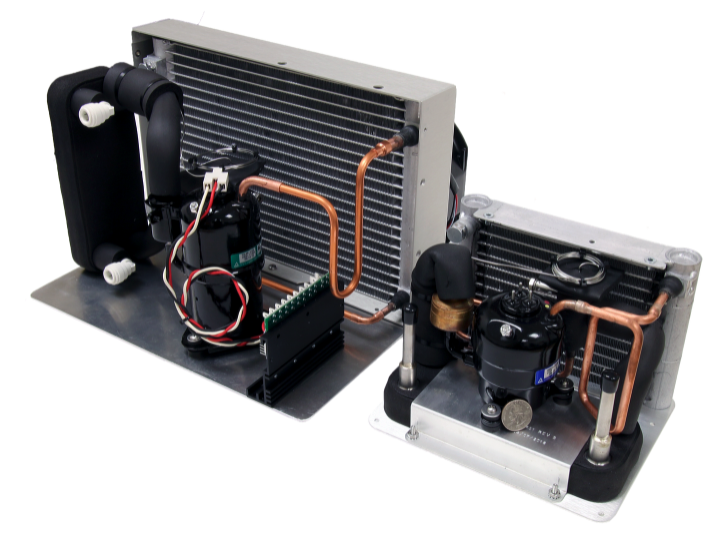
Chroma ATE attended the show to exhibit its two newest systems for testing and developing EV energy storage solutions.
The first is the Model 17011 battery cell charge and discharge test system, which has been developed for researching, developing and qualitymanaging lithium-ion batteries as well as lithium-ion capacitors and electrical double-layer capacitors.
As such, the test system encompasses a series of different machines – two designed for linear circuits (one-way from a battery to its load source) and three that integrate bidirectional AC-DC converters for testing regenerative circuits for energy recycling efficiency, current response speed and other critical factors for regenerative charging.
Jason Lin told us, “The two linear circuit test systems are available as a 10 V, 6 A version or a 6 V, 30 A version, with up to 64 channels for testing and measuring different cells at once.” The testers can measure cell voltages accurate to ±0.015% and currents to a 0.02% margin of error.
The test systems can operate over up to 48 channels at once, measuring voltages accurate to 0.02% and currents to 0.05%.
The software and hardware have been designed to simulate the dynamic waveforms typical of battery charging and discharging cycles, and can log up to 720,000 data points per channel. The time interval between measurements has been reduced to 10 ms.
The company also showcased its 87001 Battery Cell Simulator, designed to provide programmable and close-precision bidirectional DC power. It can be used in place of lithium-ion batteries to provide a safe testing environment for developing BMSs for EVs and battery modules.
“It includes a special function for testing the balancing capability of BMSs. The battery industry is moving towards two forms of BMS balancing: active and passive,” explained Rocky Chang from Chroma. “And the Chroma 87001 can examine the current balance of a BMS for both techniques.”
Eaton attended the show to launch its newest EDLC modules, the XLR-51 and the XLR-16.
“The XLR-51 is a 51.3 V rated, 188 F supercapacitor, and it’s been certifi ed to UN-ECE’s regulations 10 and 100,” Nick Stone said.
“The latter of those is an environmental stress certifi cation, involving crush and fire resistance tests, and withstanding those to ensure it can be integrated safely into electric powertrains for commercial transport that use regenerative braking through frequent stopping and starting.”
The XLR-51 weighs 14.7 kg, and has the same physical footprint as the company’s previous XLR-48 supercapacitor module (421 x 196 x 177 mm). It also integrates the same number of cells – 18 in series – with the same shunt-balancing technology to ensure the cells age at the same desired rate.
However, the XLR-51 uses Eaton’s new XL60 cells, rated at 2.85 V each (compared with the 2.7 V cells in the XLR-48) to achieve a 5.5% increase in voltage rating for the same size. It can store up to 68.7 Wh, and deliver power at up to 131.6 kW,
A temperature thermistor is installed in the XLR-51 to provide constant temperature readings, as well as an overvoltage circuit to detect when one cell needs to be discharged to balance it with the others.
Meanwhile, the XLR-16 supercapacitor module integrates six XL-60 cells in series to provide 16.2 V at a capacitance of 500 F. It incorporates the same protection sensors as the larger XLR-51, and is designed for smaller commercial EVs, which capture less energy while braking.
The XLR-16 measures 416.2 x 175.9 x 67.2 mm and weighs 5.7 kg. It can store up to 18.2 Wh and output power at a maximum rate of 38.6 kW.
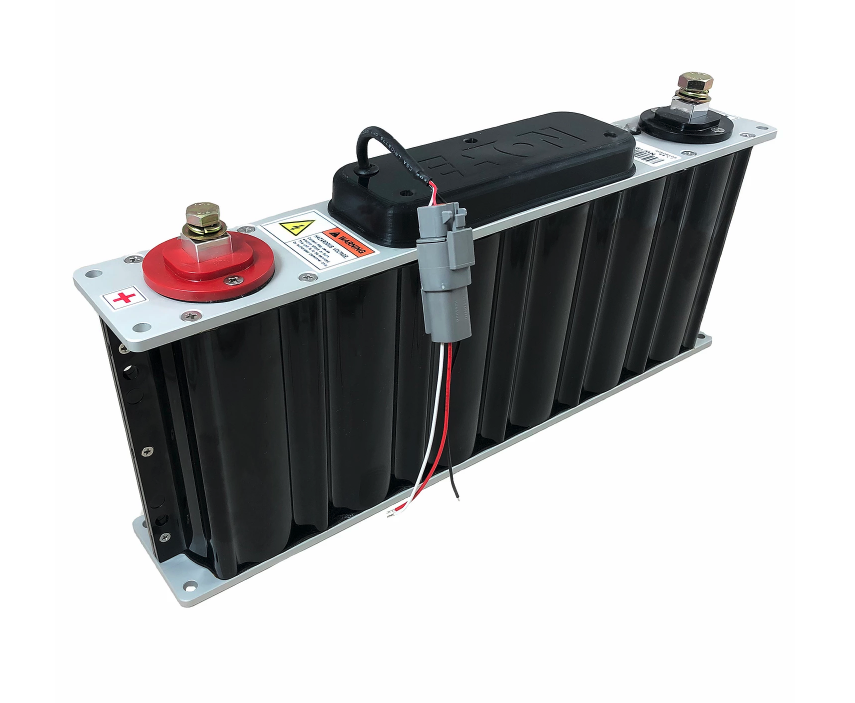
Aavid, the thermal division of Boyd Corporation, displayed its new HybridPACK double-side cooling solution, which was developed as a compact heat dissipation system for an Infineon Technologies inverter module for hybrid and electric vehicles.
“After prototyping and performance testing of the thermal and mechanical requirements of the project, to validate our analysis of the liquid cooling system, we opted for an integrated brazed assembly, made from multiple components joined at high temperature,” Jerome Toth said.
“Using a sheet of 3003 aluminium clad with 4000-series aluminium as filler, the material melts at around 1100 F [595 C]. Five components go into the furnace but only one comes out.”
The resulting cold plate has two heat transfer fi n sets, one on top and one on the bottom, to provide thermal management on both sides. Eight mechanical fixing points are included to secure the plates to each other using rivets or screws.
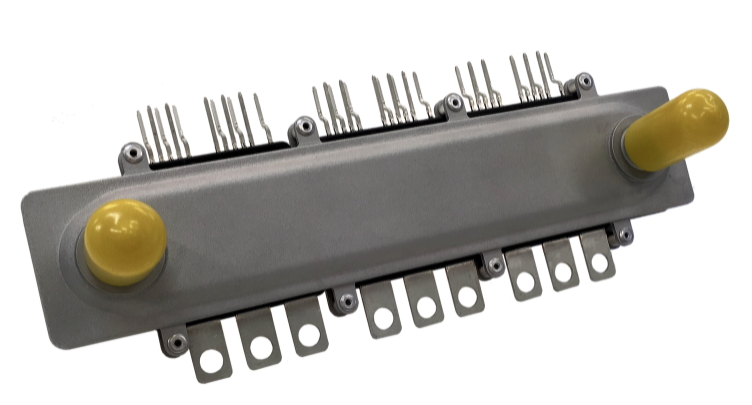
“From an economic perspective, we wanted to optimise the solution by putting what we call a ‘u-fl ow’ cold plate into it. The phase-change material used in it was also selected to provide protection against shock, vibration and other hazards in the automotive environment,” Toth said.
ONLINE PARTNERS
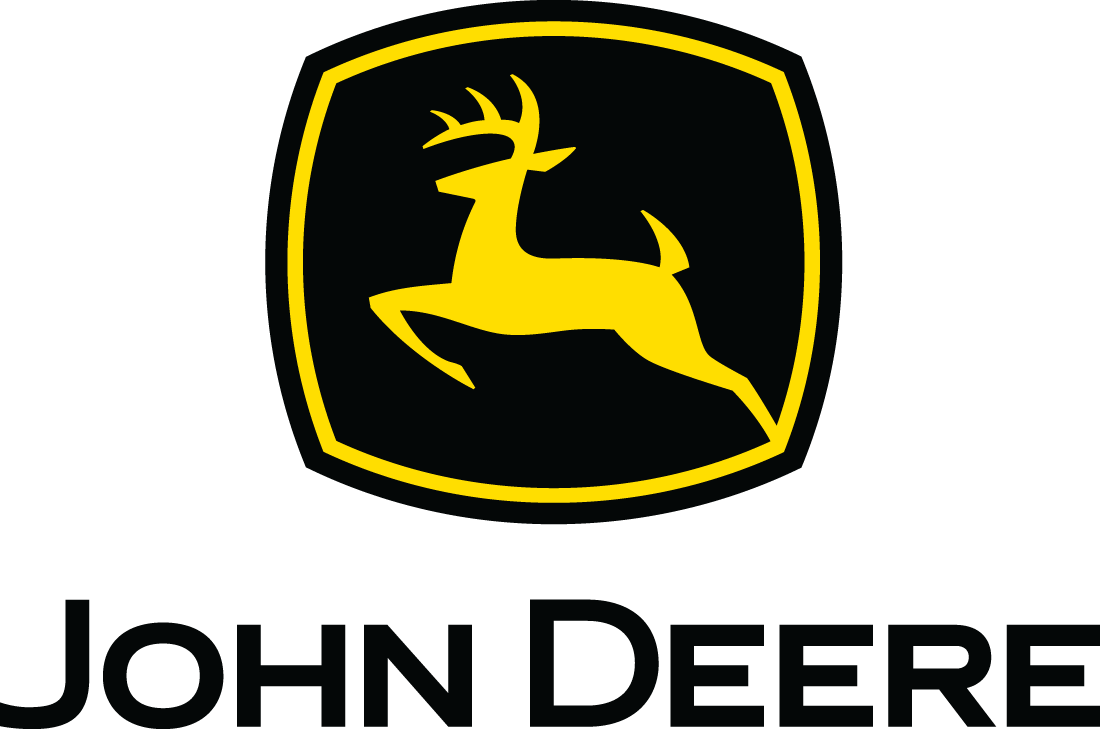
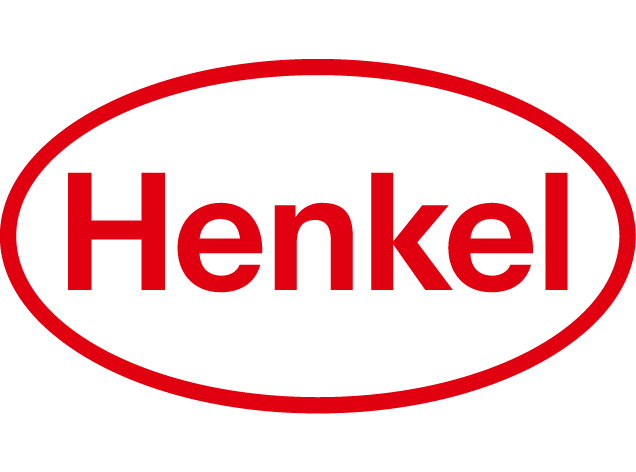
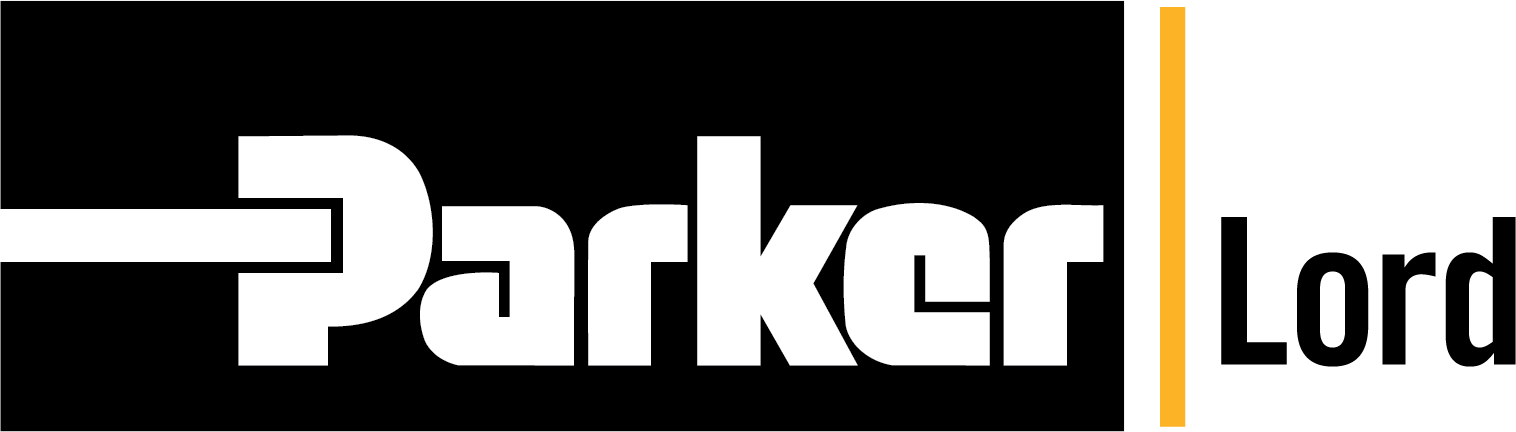
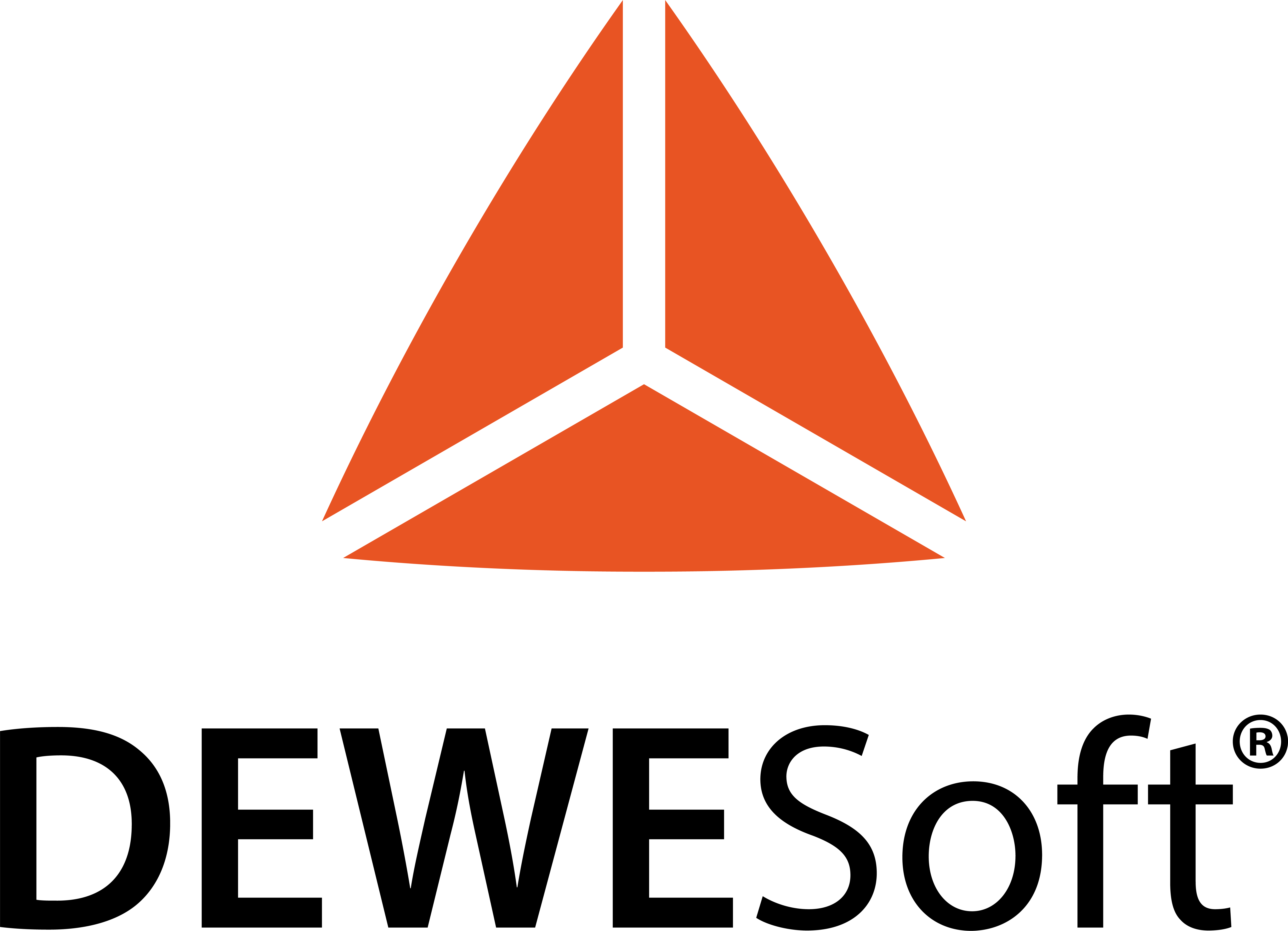
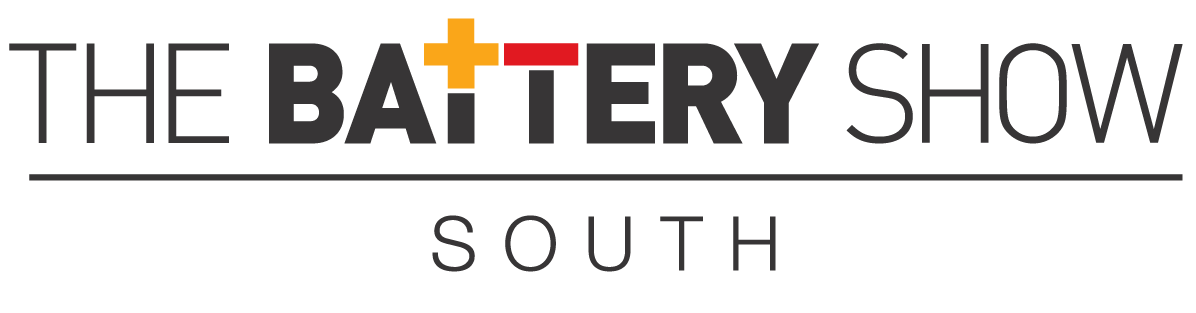
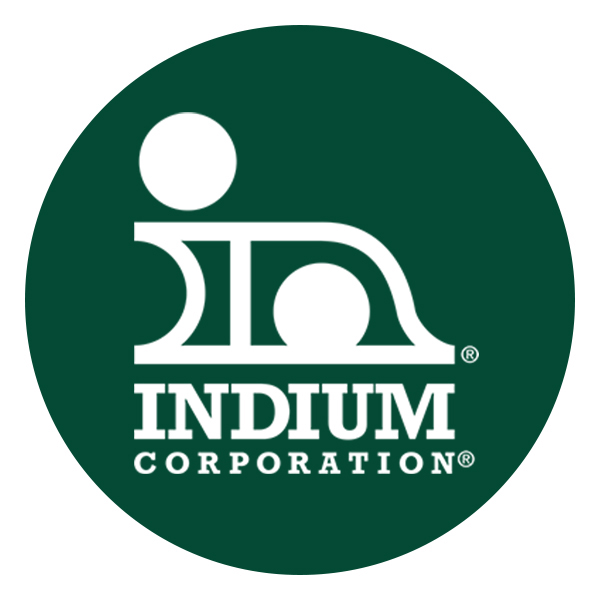
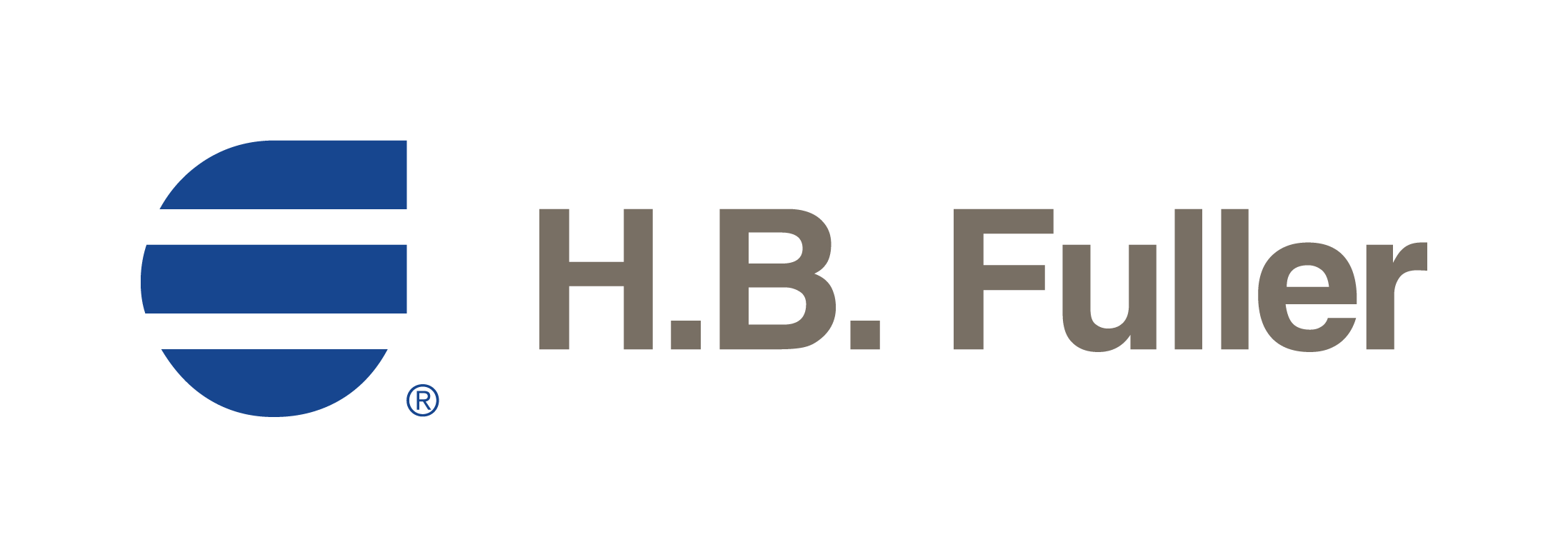