Improving the accuracy of EV chargers
The technology behind EV charging is becoming increasingly complex, and as infrastructure manufacturers push the boundaries to develop next-generation solutions that deliver power faster and more efficiently, one of the crucial areas of focus is the method of power metering.
Inaccurate measurements can cost millions in lost revenue for charging providers. As EV adoption increases and more companies enter the market, the ability to achieve highly accurate power calculations, resulting in more reliable billing, while meeting local design requirements will become a key differentiator.
Myriad options
There are many different charging solutions on the market, ranging from the compact, lower-cost, singular-module AC units that are most suitable for domestic EVs to the larger, more expensive stacked-module DC chargers, which provide faster charging times and speeds of more than 360 kW for public charging stations.
Likewise, various metering solutions are available to suit different requirements. These include simple, integrated system-on-a-chip (SoC) products, application-specific standard products (ASSP) and discrete designs that pair a precision analogue-to-digital converter (ADC) with an external microcontroller.
All of these are designed to monitor power usage during charging to enable service providers to bill for all the energy used at the end of the session. However, some measure more accurately than others.
Accuracy and control
Errol Leon, system engineering & marketing manager for smart meter and EV charging systems at Texas Instruments, explains: “Some approaches provide more accurate control and flexibility over different types of power calculations, but it depends on the design requirements. Both SoC and ASSP are more fixed methods that require less firmware development, but they do not allow the same level of customisation as a discrete approach.”
The ADC-based discrete designs measure current and voltage from three phases, with measurements taken either from a current transformer or a shunt sensor.
Leon continues: “The current transformer and shunt-sensor approaches are both accurate, and the decision to use one or the other is more about overall solution size and cost, and how you want to measure AC or DC current.
Cost differences
“Current transformers are typically more expensive because the design requires shielding to make it less susceptible to magnetic tampering. They also allow for galvanic isolation, but you are limited to only measuring AC current.
“The shunt solution is smaller and naturally less susceptible to magnetic tampering. However, this approach requires data and power isolation for multi-phase meters. Shunts can measure AC or DC current, but you will need to add isolation and account for thermals, depending on the magnitude of the current,” Leon adds.
ADC must be highly accurate to meet strict standards such as the American National Standards Institute (ANSI) C12 Class 0.5 or Class 0.2 meters.
A high signal-to-noise ratio, low noise and a low gain error are also factors when determining whether a particular ADC is suitable for a metering application. If you decide to use a current transformer as the sensor, the meter will require a high-accuracy, multichannel, precision ADC.
Trio of ADCs
Texas Instruments has developed three new ADCs to suit all requirements. The ADS131M08 is a 24-bit ADC, designed for AC metering, with a current transformer sensor and an integrated phase delay that helps exceed ANSI C12 metering standards.
The AMC131M03 is a 24-bit isolated ADC for AC or DC metering with a shunt sensor, and it has integrated data and power isolation, and a high standard of radiated emissions performance. It provides high accuracy measurements through its signal-to-noise ratio and low gain error, while maintaining 7070-VPEAK reinforced isolation with 5000-VRMS isolation for one minute. Finally, the ADS131B04-Q1 works with a shunt sensor but is solely for DC chargers, with tighter offset error and drift specifications.
Poised for precision
As the requirements for AC and DC chargers increase, precision ADCs are likely to be increasingly favoured to enable accurate energy calculations and provide the flexibility required to build infrastructures for environmentally sustainable transport.
Leon concludes: “At the end of the day, our goal is to make flexible, accurate and reliable parts to enable our customers to innovate in areas such as EV charging and smart meters.”
Click here to read the latest issue of E-Mobility Engineering.
ONLINE PARTNERS
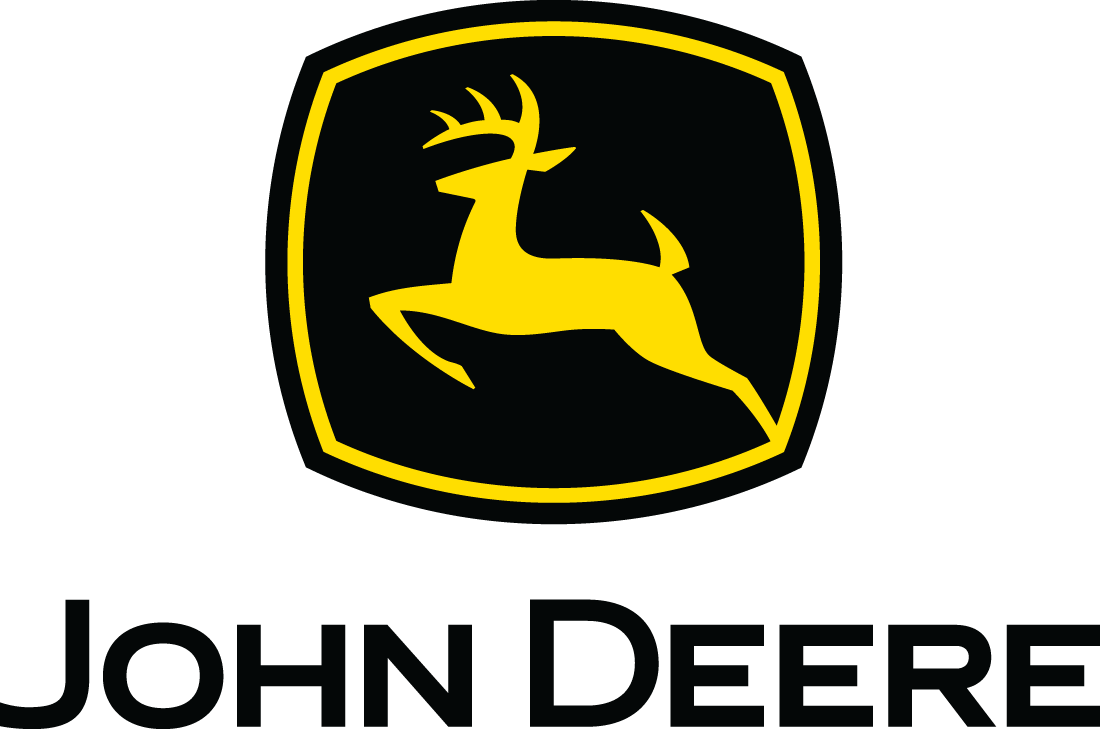
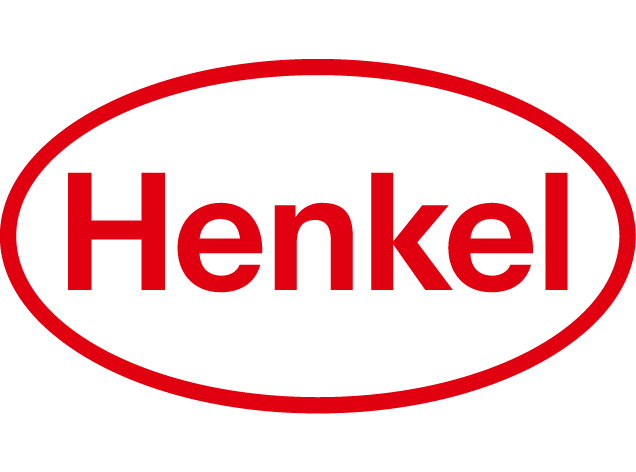
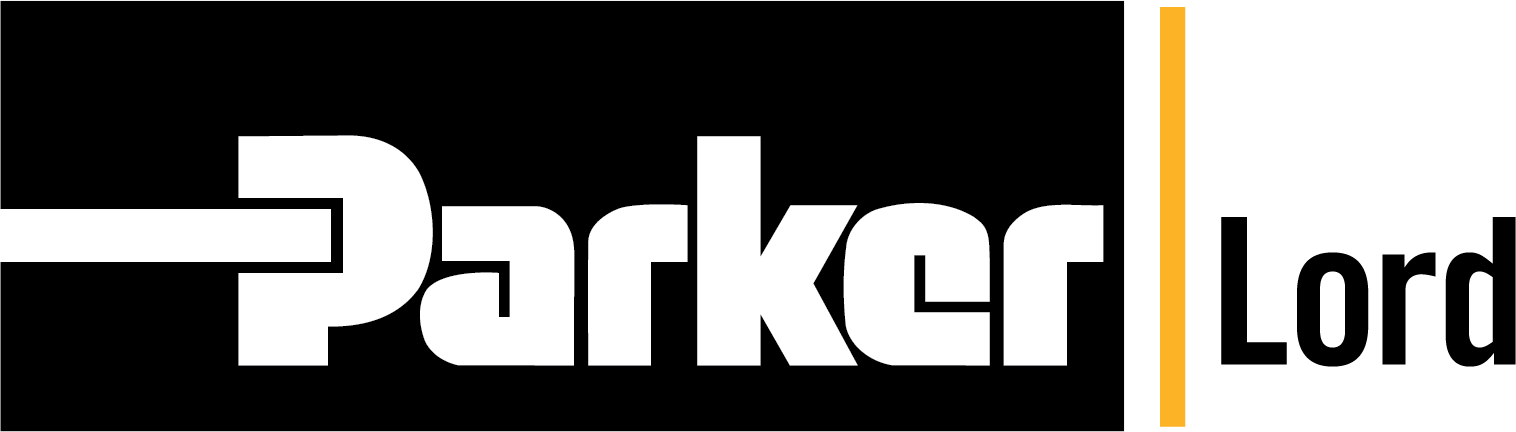
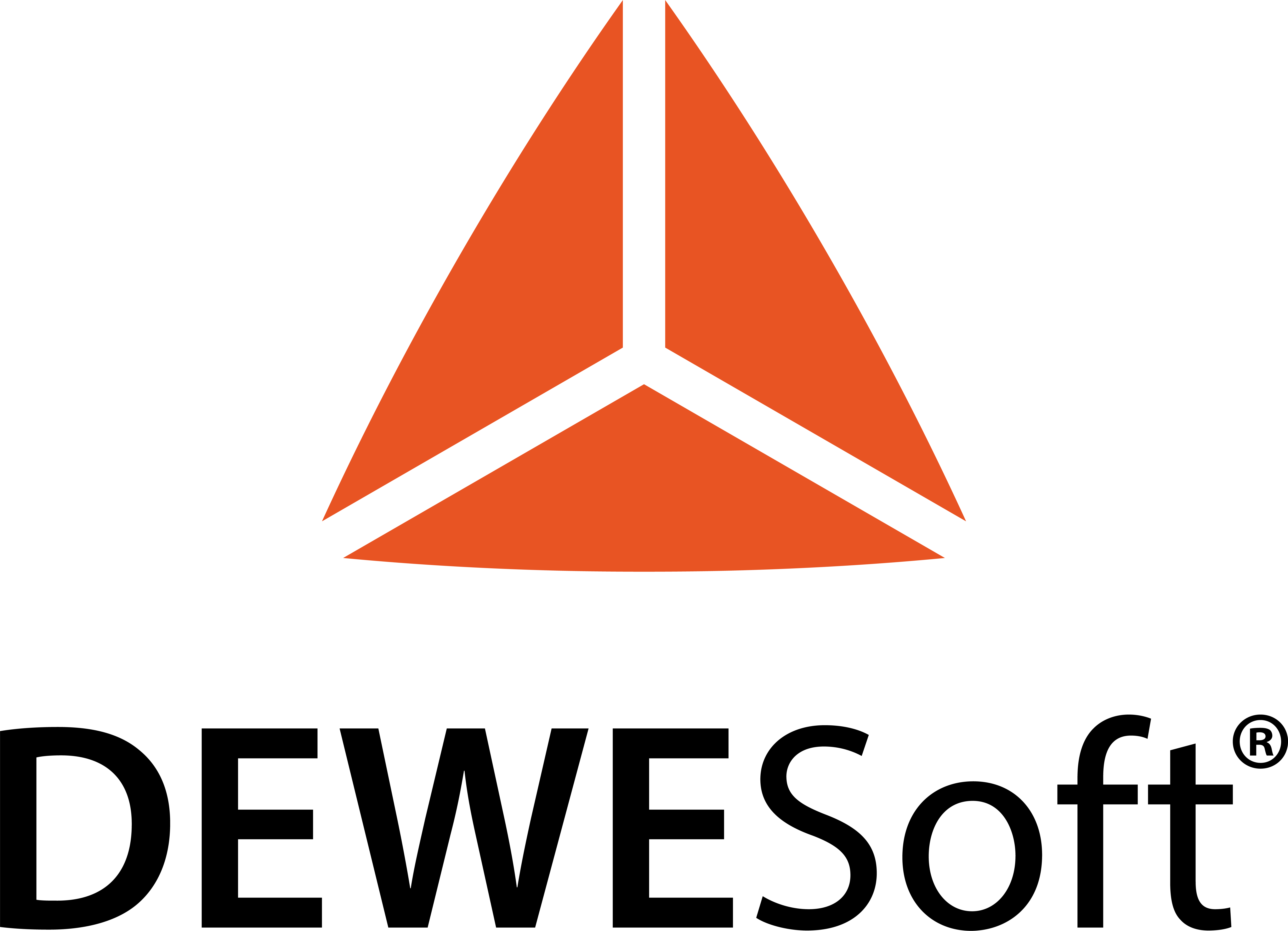
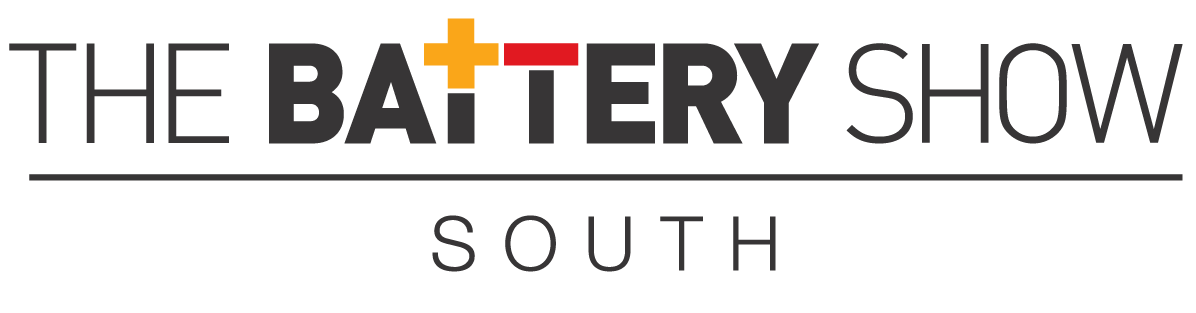
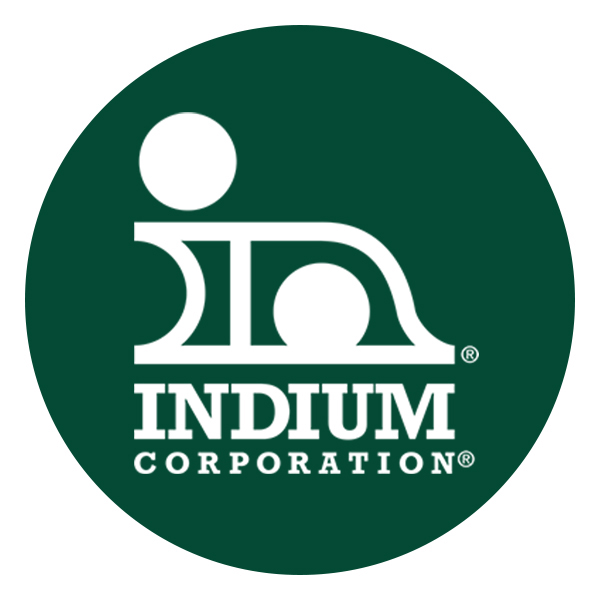
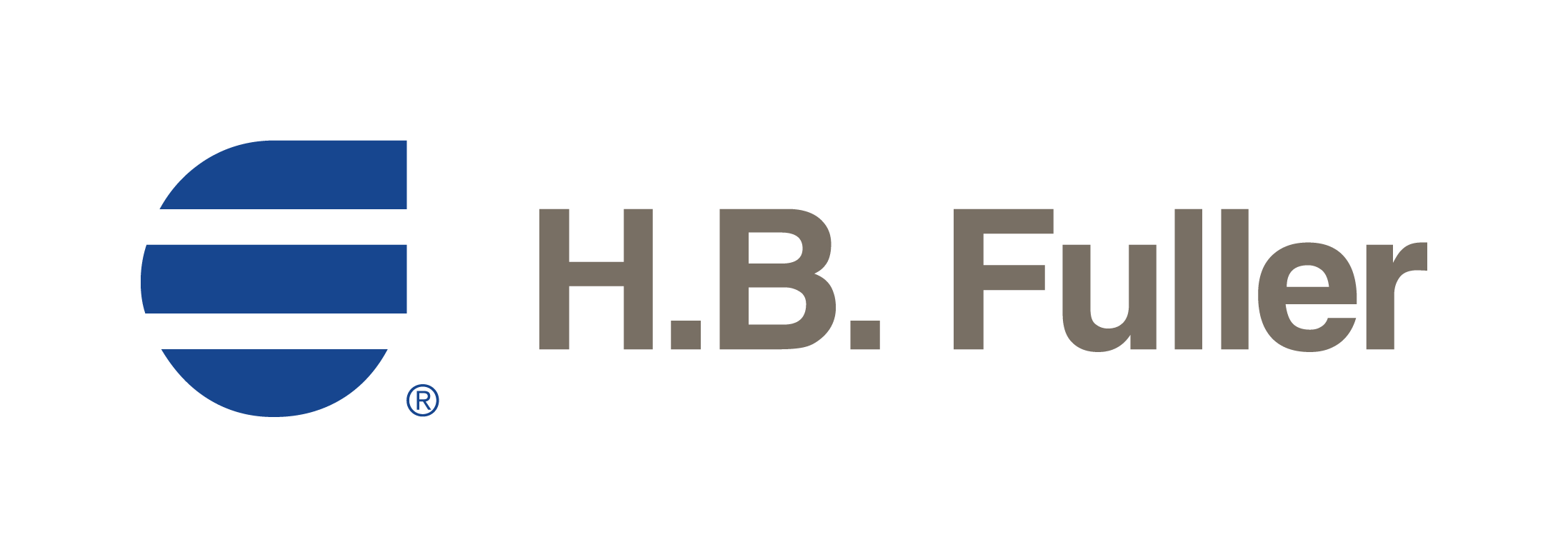