Technical Services discusses benefits of high-voltage thermal management
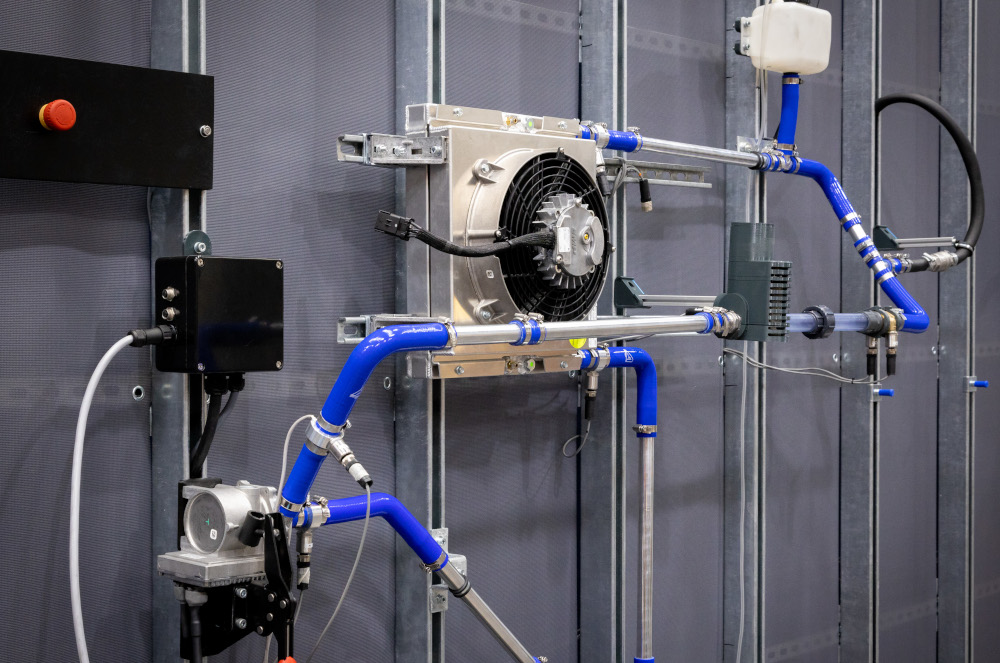
There are big, system-level energy savings to be made in thermal management by switching high-power components such as pumps and fans to higher voltages (writes Peter Donaldson).
Technical Services should know. It is the UK-based European technical partner of US electric pump and fan manufacturer EMP, handling application engineering for OEMs. Its sales and engineering director Andrew McMahon says, “Traditionally, coolant pumps have been on 12 and 24 V circuits, but as flow rates increase, so does their amperage, meaning that multiple large and expensive DC-DC converters and heavy gauge cables are needed.
“The current draw when you have multiple fans on a system, particularly in fuel cell applications, is really quite overwhelming. With a 24 V architecture, 300-plus A and multiple DC-DC converters are not uncommon.”
As with powertrains, the shift to HV enables these systems to run at high power with low current draw. That gives a huge efficiency increase for the system as a whole by reducing the number of DC-DC converters (and associated cooling) – with a commensurate reduction in conversion losses – and thinner cabling.
Initial HV applications will typically be in hydrogen fuel cell-powered buses, trucks, power generation and in battery cooling for last-mile delivery and long-haul trucks. The components to support these applications are now becoming available.
McMahon says, “The high-voltage pumps are now a reality, initially for the top end of a product range in terms of flow and pressure. Likewise, the fans are available in high voltages in diameters from 15 to 31 in.
“That really helps with the coolant loops that are rejecting heat to ambient air, yet there is more to be done on the whole vehicle architecture to move more components to high voltage.”
He emphasises that the process will not be one of simply replacing components with HV equivalents on a one-to-one basis, but will involve, for example, one large, powerful HV component replacing several smaller low-voltage ones.
“Then, with improved system architecture, using valves and plate heat exchangers allows you to achieve the thermal management you need with fewer, more intelligent components,” he says.
There will also be a significant degree of functional integration. “Separate cooling loops will interact with one another to scavenge heat from one loop to reject it into another [waste heat recovery] or other system-level architectural choices to put all the heat into a high-temperature loop and ultimately reject it through a single heat exchanger.”
Technical Services partners with customers to get the right flow, pressure and heat rejection from a cooling system, testing, validating and delivering parts for production EV and hybrid applications, McMahon explains.
One tool the company uses in this process is its latest in-house test rig at its facility in Cleckheaton, England.
“We have customer-specific elements in there so that we can demonstrate and visualise flow and cavitation issues, pressure and flow distribution around a circuit, and the pros and cons of one layout over another,” McMahon notes. “That is useful from a technical communication perspective and also in providing empirical data on a component and system level to feed into customers’ 1D modelling for more accurate simulation.”
ONLINE PARTNERS
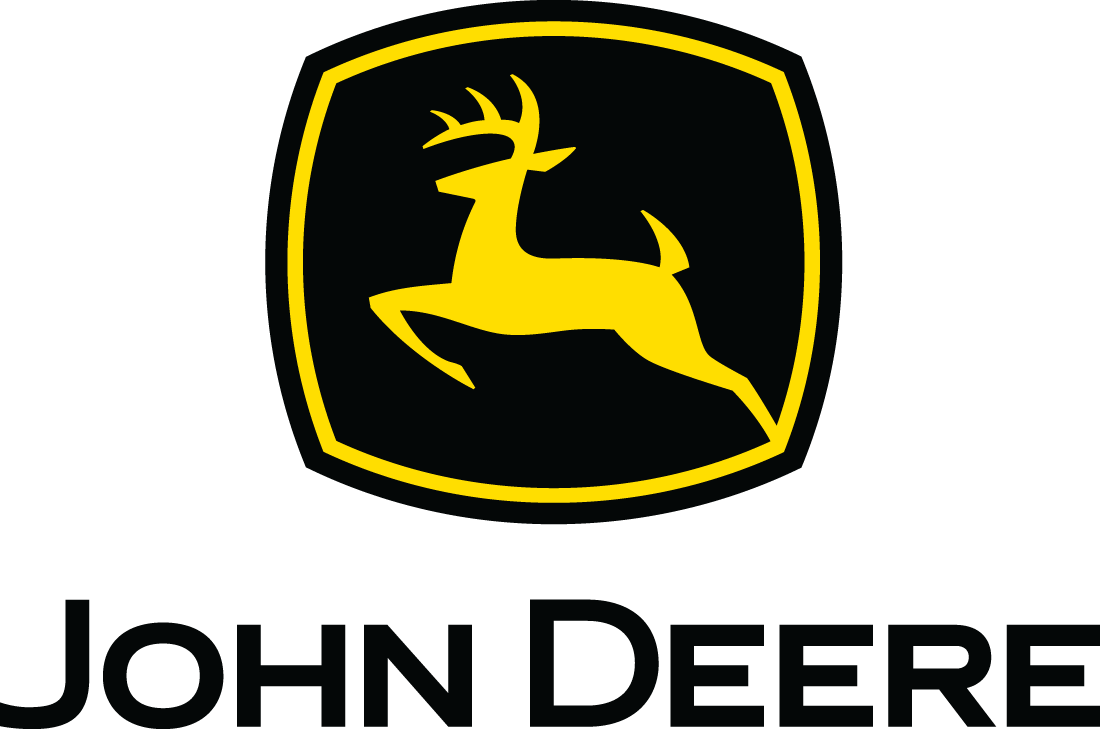
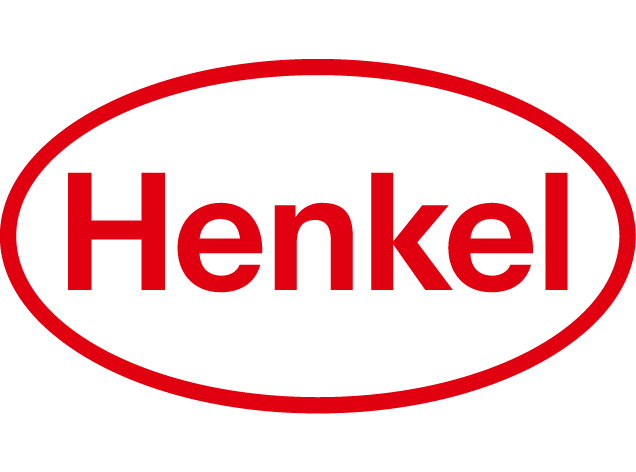
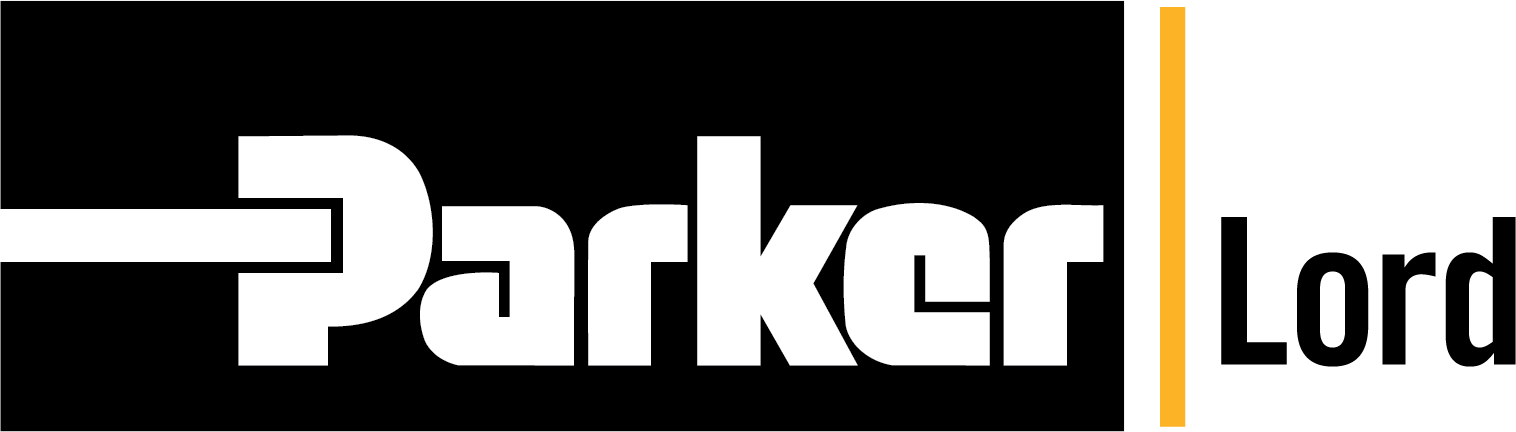
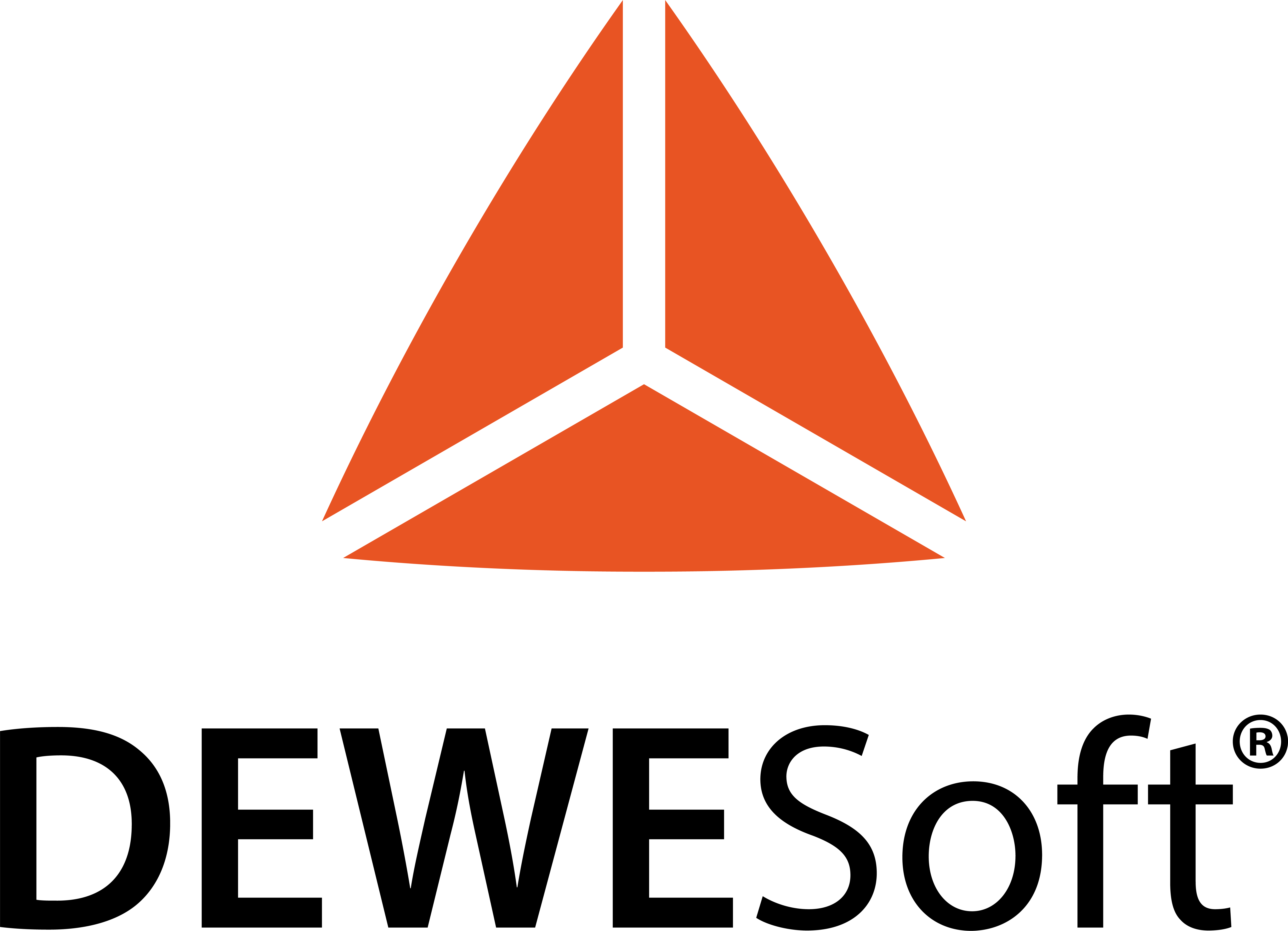
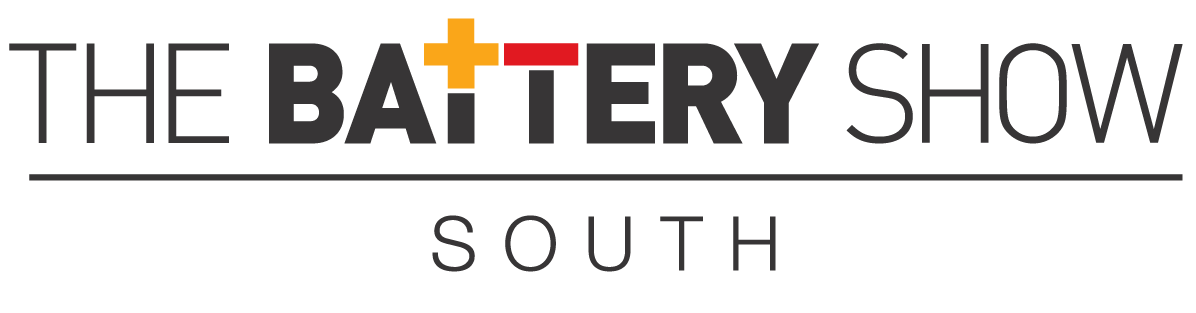
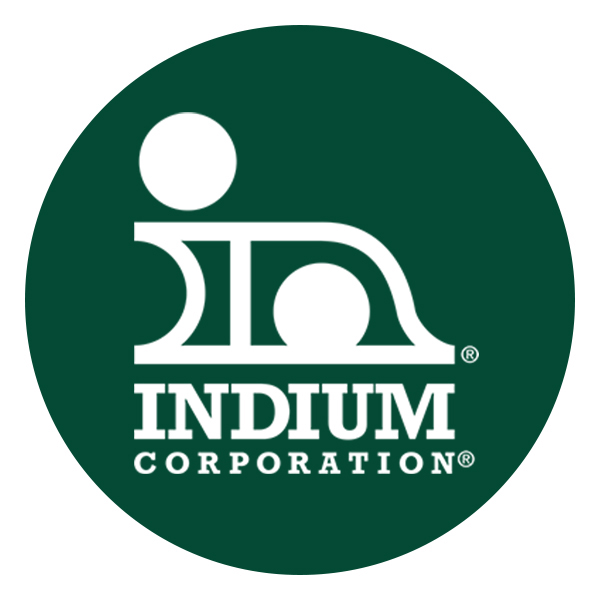
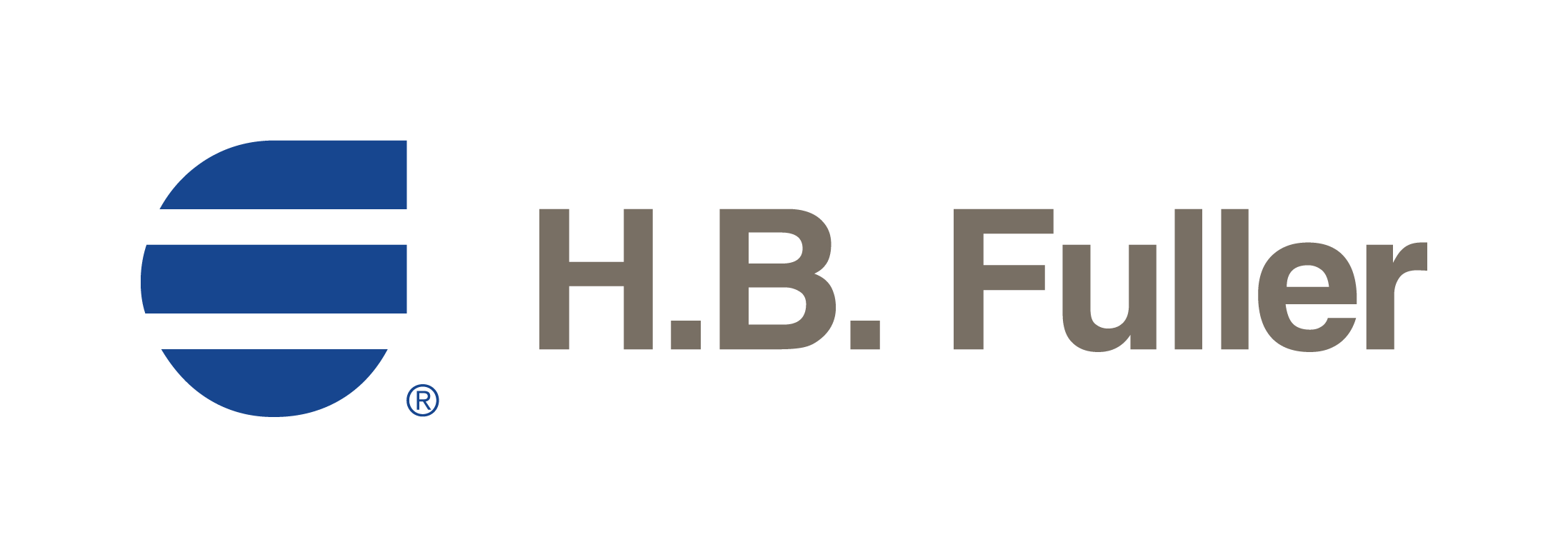