Tackling battery welding challenges with new beam-shaping techniques
A new beam-shaping welding technology has been developed by Cailabs with the aim of significantly improving accuracy and efficiency in the construction of electric mobility parts. This is key to the construction of the battery assembly and is often important for other parts of the vehicle, such as motor hairpins or battery cases.
Manufacturers typically use copper or aluminium conductors to optimise the efficiency of electrical conduction, but these are challenging materials to weld due to their high reflectivity and high heat conductivity, with particularly significant difficulties faced with Al5xxx and Al6xxx series metals.
The weld is a weak point in connectivity, and it is essential to limit welding pores, which are formed by gas entrapment during the solidification of the molten weld metal, as these can cause increased resistance and reduce battery capacity, and therefore vehicle range. It is also important to limit weld spatters as these can lead to accident-inducing short circuits.
Traditional welding with an unshaped beam achieves very low absorption, and therefore difficult weld initiation, when carried out on these metals, while the high heat conductivity of the materials can also lead to an instability. As a result, it is extremely difficult to achieve the required quality, especially with regard to the pores.
Key improvements
Several beam-shaping welding technologies have been introduced, but Cailabs’ solution promises several key improvements compared with other approaches. Most notably, an extended depth of field means the beam remains well-shaped for a long distance along its propagation, making it possible to relax many of the alignment constraints usually required.
The technology turns what is traditionally a challenging process into one that is far more forgiving. It uses fibre lasers, which can be either mono-mode or of several modes, ranging from 15µm to 100µm fibres, with high power management up to 24 kW and reduced focus shift, which helps to fasten the process and keep it stable.
This is compatible with all laser brands, and with small and large field scanners, and it also offers variable beam shapes and dimensions, add-ons and a customisable footprint.
Test results
Tests on real e-mobility parts, including busbars and hairpins, have been carried out using a Raycus 6 kW fibre laser and a Precitec ScanMaster system.
The process has been proven to deliver a 1.5 times larger process window, reducing optimisation time and increasing reproducibility; a four times greater depth of field, which reduces preparation time and lowers scrap rate; better performance at lower speeds; stable capillary length over the whole welding time; and near-complete elimination of visible pores and ejected material. All of this enables both slow and deep, and high-speed and low-penetration welding, which is particularly challenging with other technologies. The developers say this results in a far higher quality and more robust process, with reduced preparation and scrap rate, and ultimately, reduction.
Click here to read the latest issue of E-Mobility Engineering.
ONLINE PARTNERS
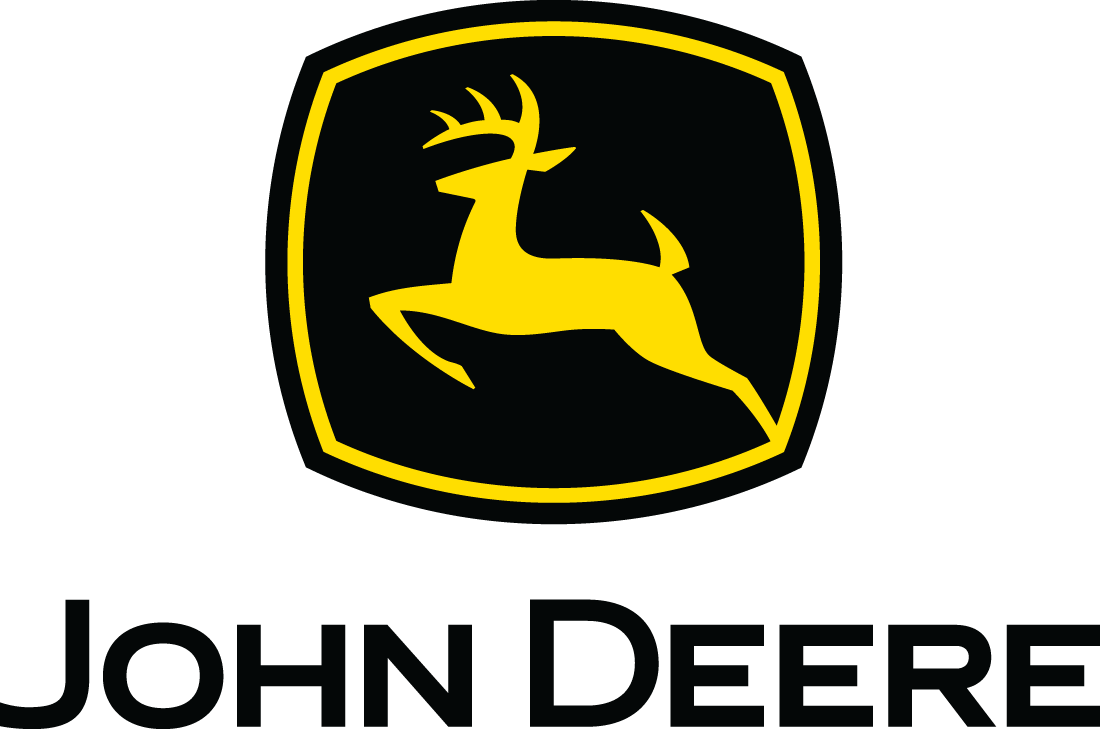
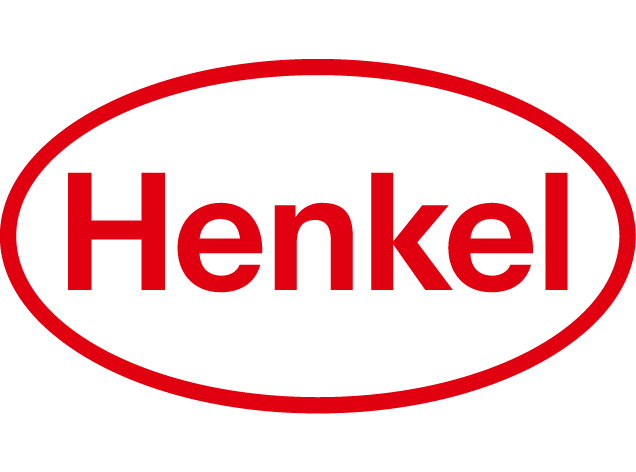
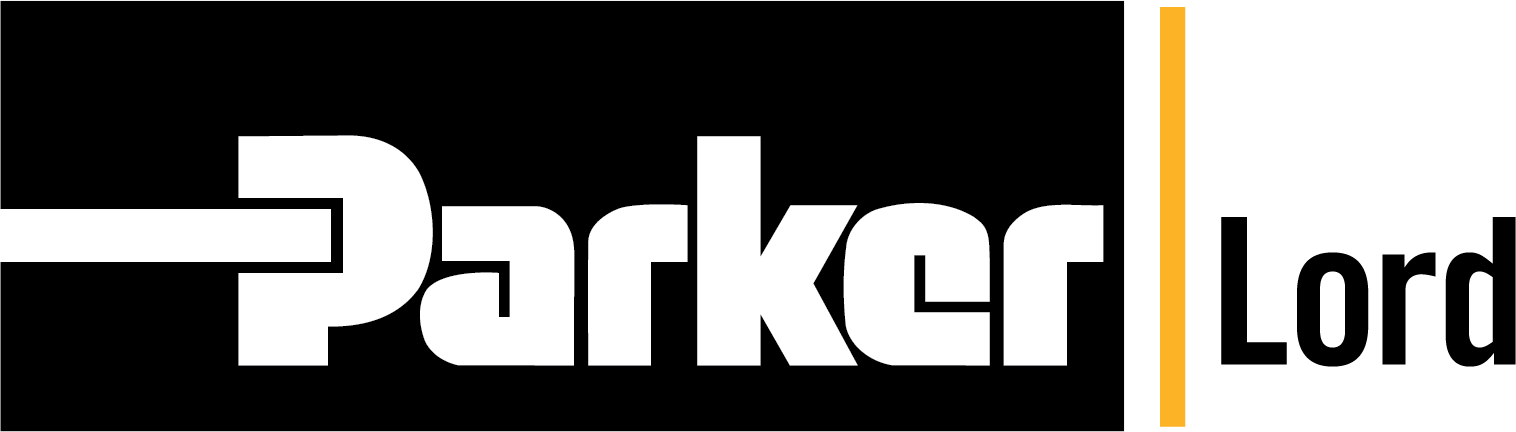
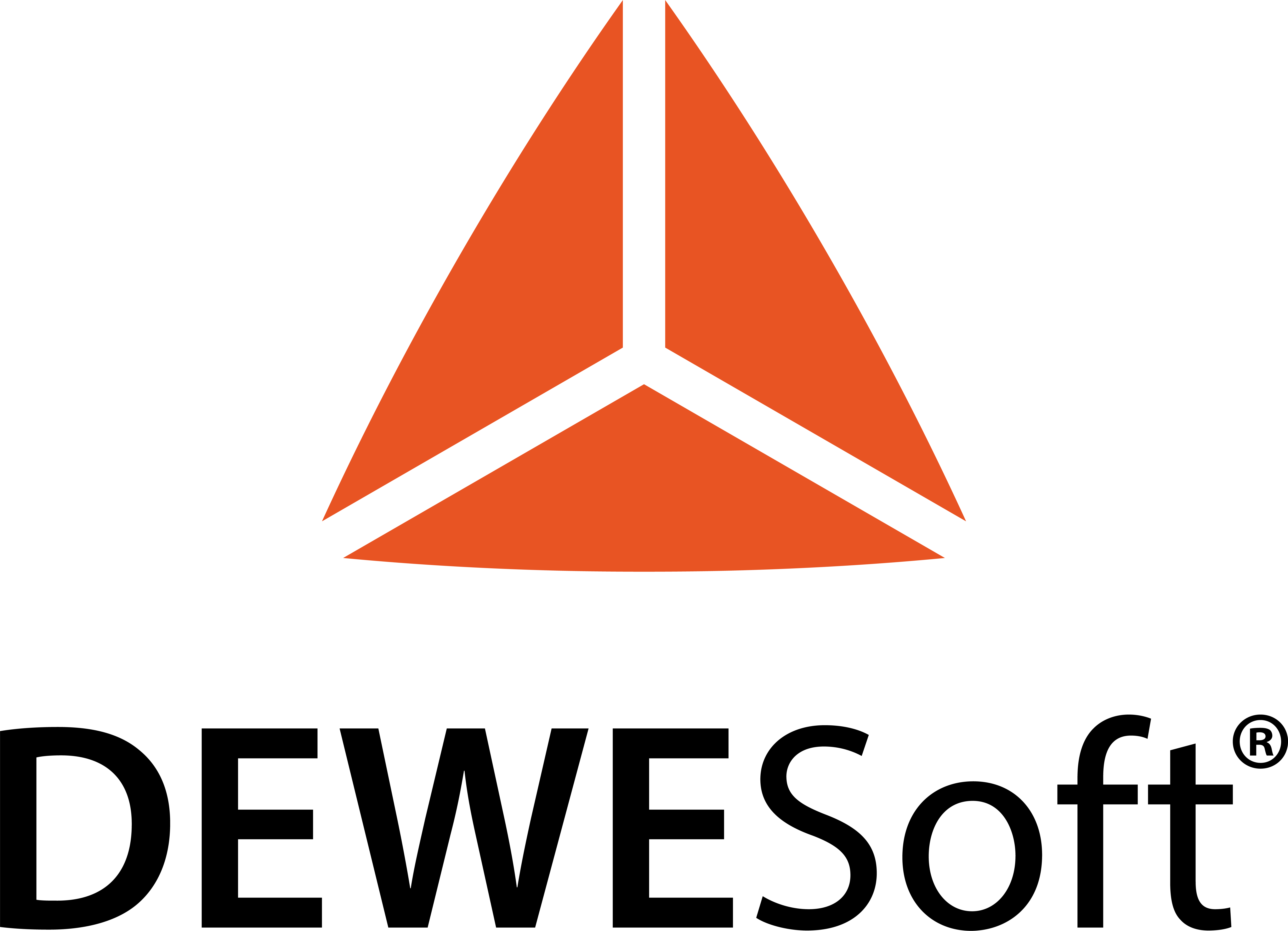
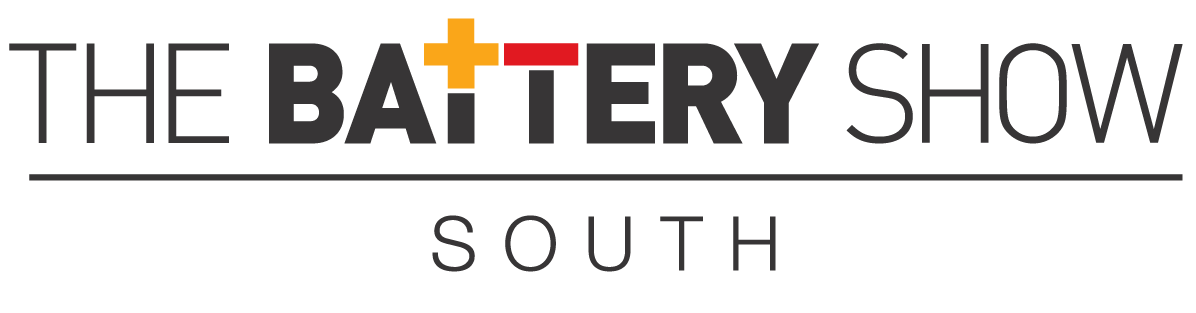
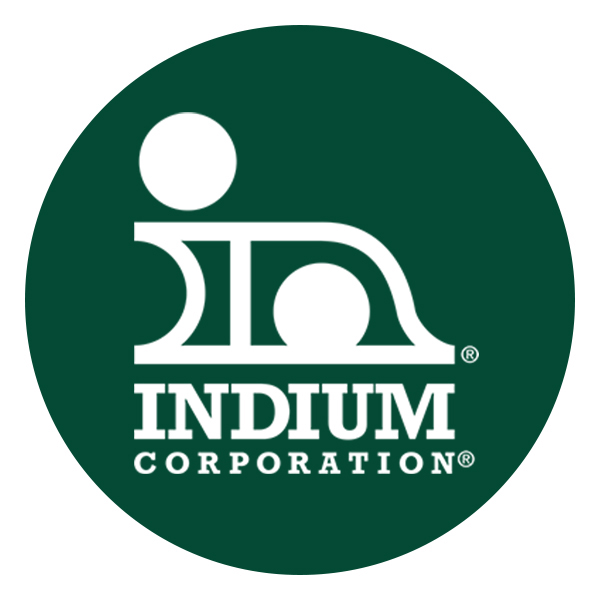
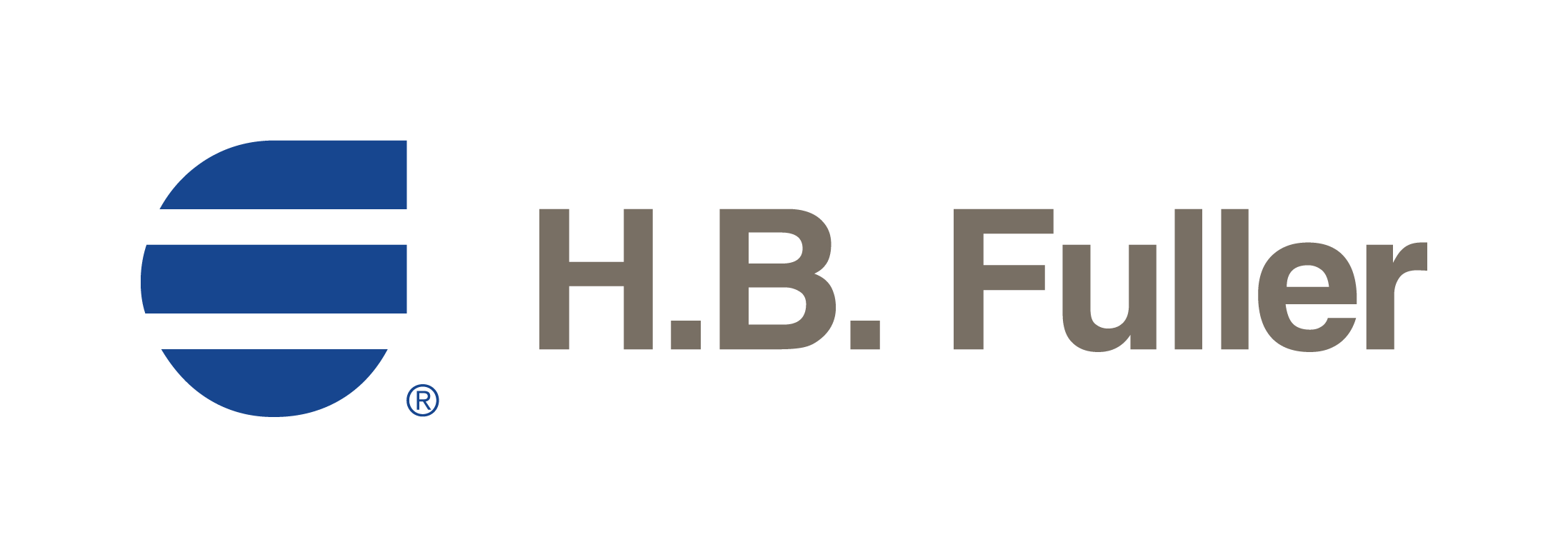