Supercapacitor applications
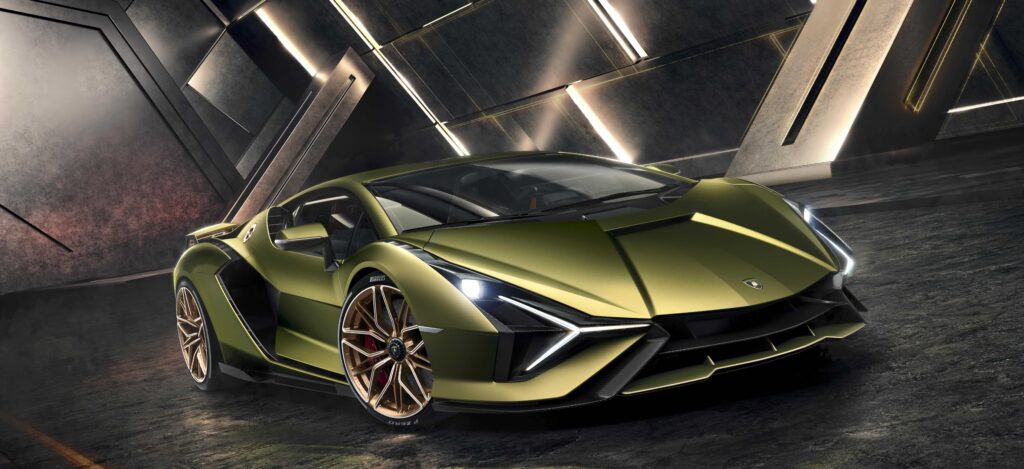
(Courtesy of Lamborghini)
Perfect partners
Supercapacitors and batteries make an ideal team, reports Peter Donaldson, who reports on how they are used in EVs
Although batteries and supercapacitors both store electrical energy, they do so in very different ways that bestow them with complementary characteristics. In a nutshell, batteries store energy chemically and offer high energy density (measured in Wh/litre) while supercapacitors store energy in electric fields and offer high power density, measured in kW/litre.
That means supercapacitors can absorb and deliver a lot of power in short bursts, which is very useful in many EV applications but is something that batteries don’t do very well, and for which they suffer when forced into applications that require it. Supercapacitors are therefore a battery’s best friend, as one supplier puts it.
Illustrating this relationship, they are teamed up increasingly with batteries as load smoothing, ‘shock absorbing’ devices that give the batteries easier lives and allow them to focus on what they do best, which is absorb and deliver large amounts of energy at relatively low rates.
This perhaps becomes clearest when considered in terms of charge rates. Where a state-of-the art EV’s lithium-ion battery might accept a full charge in less than an hour, an equivalent supercapacitor could be fully charged in less than 10 seconds, assuming a sufficiently powerful charger could be found.
Supercapacitors also typically discharge over time frames measured in seconds, while EV batteries discharge at rates that depend on how the vehicle is driven, often delivering modest amounts of power over several hours. Supercapacitors are much longer lived than batteries as well, withstanding orders of magnitude more charge-discharge cycles and greater extremes of temperature, so they can generally be expected to last at least as long as the host vehicle.
Supercapacitor principles
Sometimes referred to as ultracapacitors, supercapacitors are called that simply because they have far higher capacitance than ordinary capacitors. In an ordinary capacitor, the insulating layer is either air or a plastic film, while the electrodes can be rigid plates or flexible films coated with conductive materials such as carbon.
As the capacitor is charged, electrons leave one electrode, where a positive charge builds up, and collect on the other, building a negative charge. The two opposing charges are kept apart by the insulator, creating the electric field that stores the energy. Connecting the positive and negative electrodes in an electric circuit allows current to flow, discharging the device.
A 1 Farad (symbol F) capacitor holding a charge of 1 Coulomb (C) has a potential difference of 1 V between its electrodes, and takes 1 second to charge to 1 V when given a 1 A current. A Coulomb can be thought of as an astronomical number of electrons, and because all electrons carry a negative electric charge and therefore repel each other, forcing them together on one conductor by charging the capacitor is rather like compressing a spring.
Ordinary capacitors are rated in small fractions of a Farad, while supercapacitors are available in ratings of thousands of Farads.
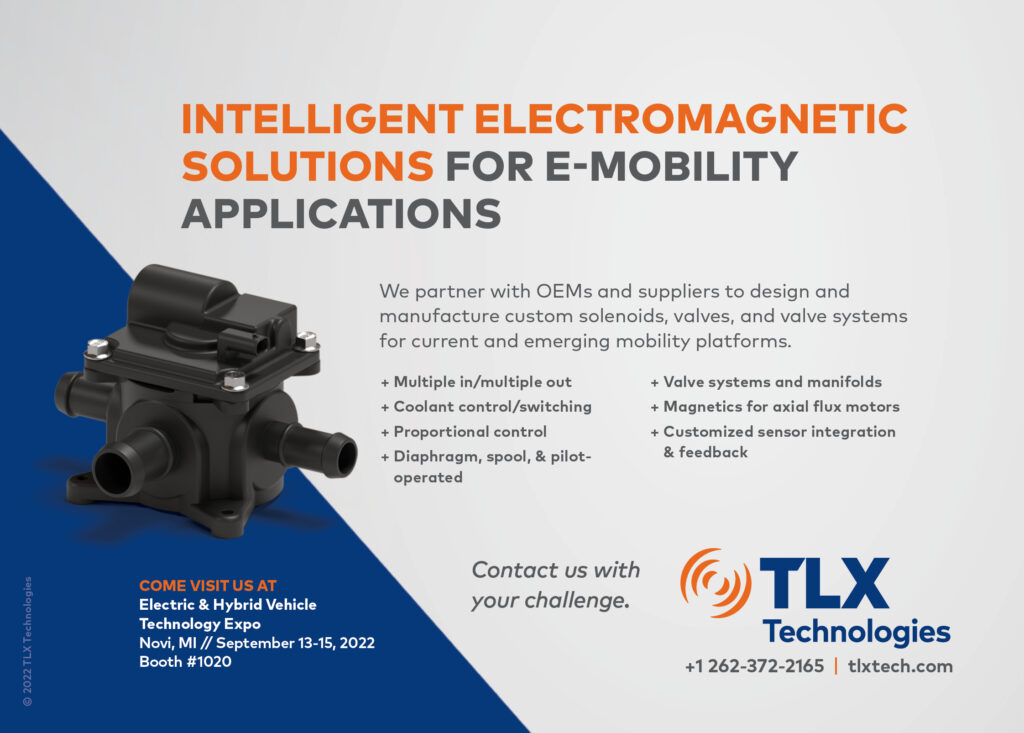
As with battery cells, supercapacitors come in a range of form factors, including cylindrical, prismatic and pouch types.
The term ‘supercapacitor’ refers to the electric double-layer capacitor (EDLC). Other devices – including pseudocapacitors, which store energy electrochemically in a manner akin to that of batteries, and hybrids that store energy both electrochemically and electrostatically – are under development, but this article will focus on EDLCs.
In an EDLC, the two electrodes are coated with porous activated carbon, separated by an insulating layer and immersed in a liquid electrolyte consisting of positive and negative ions in a solvent. The ions collect on each plate during charging, and two layers of charge form on each electrode. That is because supercapacitors also store energy in the electric field formed between two oppositely charged particles, and the electrolyte contains an equal number of uniformly dispersed positive and negative ions.
This is where the ‘double layer’ term comes from. The very large surface area of its electrodes, and the small distance between the ions’ charge and the surface charge gives EDLCs their very large capacitance values.
Powertrains and beyond
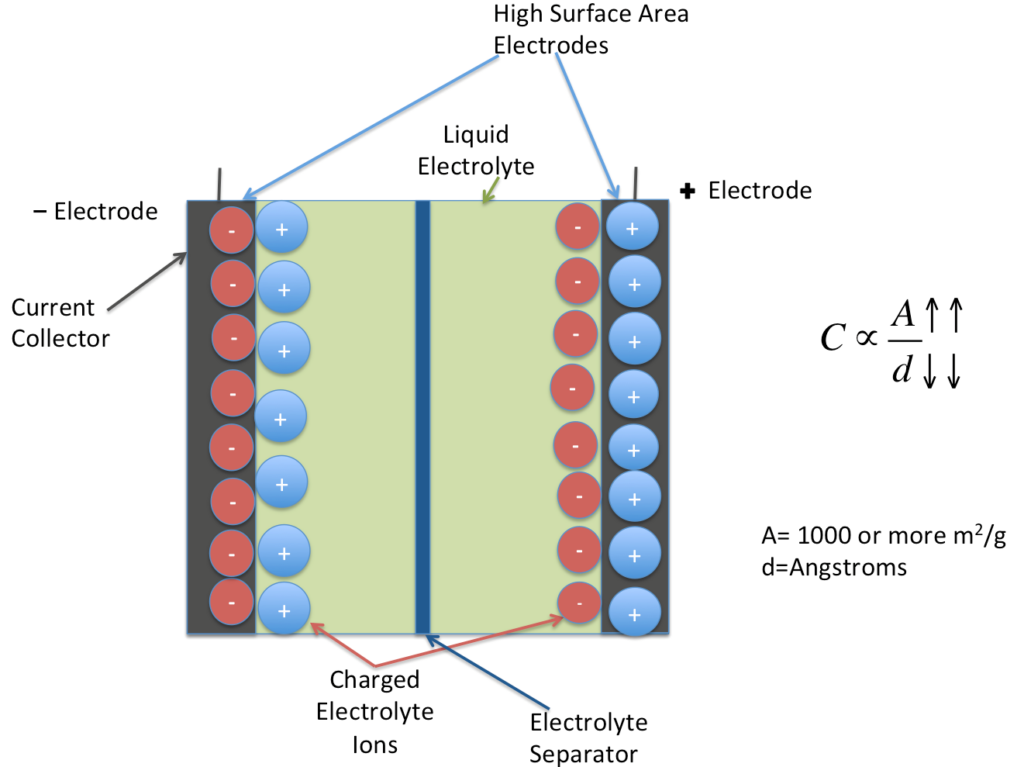
(Courtesy of Stanford University)
In automotive powertrains, supercapacitor applications include stabilising electrical system output in IC-engined and hybrid vehicles, engine downsizing and emissions reduction, energy capture from regenerative braking and in acceleration-boosting applications. They can also be found protecting batteries and even fuel cells from peak loads.
Away from the powertrain, safety-critical electrical accessories such as power steering, braking and Advanced Driver Assist Systems and technologies need back-up power. Supercapacitors can provide vital seconds of power to enable the driver to guide the vehicle to a safe place to stop in case of a battery failure, for example.
Another non-powertrain application in which supercapacitors have found a niche is in suspensions. “Our supercapacitors are used in active suspension systems, where they provide the power required and have the lifecycles to last the lifetime of the vehicle,” says Dr Sebastian Pohlmann, vice-president of automotive and business development at Skeleton Technologies. “In this application, they provide much better lifetime compared to batteries, a smaller form factor and, most important, the ability to work at -40 Celsius.”
The technology is also finding its way into IC-engined vehicles, including hybrids, in support of lead-acid batteries.
Another supplier, Ioxus, provides starting modules based on supercapacitors that come packaged with power electronics for commercial trucks, off-road equipment, military vehicles and motor sports. “The main application is engine starting, increasing the reliability of start-up and enabling idle reduction efforts such as stop/start and engine-off allowance,” says Chad Hall, Ioxus’ senior VP, sales and operations.
Skeleton provides a similar product, its SkelStart ultracapacitor module, for the same segments.
Ioxus’ uSTART v5, for example, is a 24 Wh, 12 V supercapacitor bank that provides 700 Cold Cranking Amps, which as its name suggests is a rating used to define a battery’s ability to crank an engine in low temperatures. Fitting a truck with a uSTART module usually allows one or more 12 V batteries to be removed, although it is designed to work with at least one such battery connected in parallel.
If the 12 V batteries are in a low state of charge, the uSTART goes into jump-start mode, initiating the sequence by pulling energy from the battery into the supercapacitors that, when fully charged, provide the power to start the engine. This reduces the maintenance costs associated with low-voltage conditions.
The uSTART also stabilises the voltage throughout the 12 V electrical system, which improves the reliability and lengthens the service life of components such as starter motors, relays and powertrain control modules, says the company.
“In EVs, the main application for ultracapacitors would be range extension through efficient brake energy regeneration, with peak power handled by the capacitors, allowing the battery to be sized and used for maintaining speed,” Hall says.
Skeleton’s Dr Pohlmann points out that among the supercapacitor applications in passenger cars is Mazda’s iELOOP start-stop micro-hybrid system.
Offered in the IC-engined Mazda cars, iELOOP continuously recovers kinetic energy as the vehicle decelerates, according to Mazda. It does this with a variable voltage alternator that charges a supercapacitor, which powers the vehicle’s 12 V electrical equipment and accessories, offloading the battery. The alternator varies its output voltage between 12 V and 25 V in response to the capacitor’s voltage, which is related to its state of charge.
The system switches the alternator off when the driver presses the accelerator, leaving the supercapacitor to power the electrical system so that less engine power is needed to achieve the level of acceleration that the driver demands, reducing fuel consumption.
Get the lead out
EVs also have numerous electrical loads that run on automotive industry standard 12 V supplies, and many rely on lead-acid batteries rather than a DC-DC converter that takes power from the main high-voltage battery. Battery EVs also rely on a low-voltage supply to close the contactors to bring the main battery on line, so an independent 12 V supply is likely to remain important for the foreseeable future.
Pollution from dangerous operations to recycle lead from vehicle batteries is attracting international attention and is expected to provoke new legislation, so replacing lead-acid batteries in these applications is firmly on the agenda, and supercapacitors/ultracapacitors look set to play an important role.
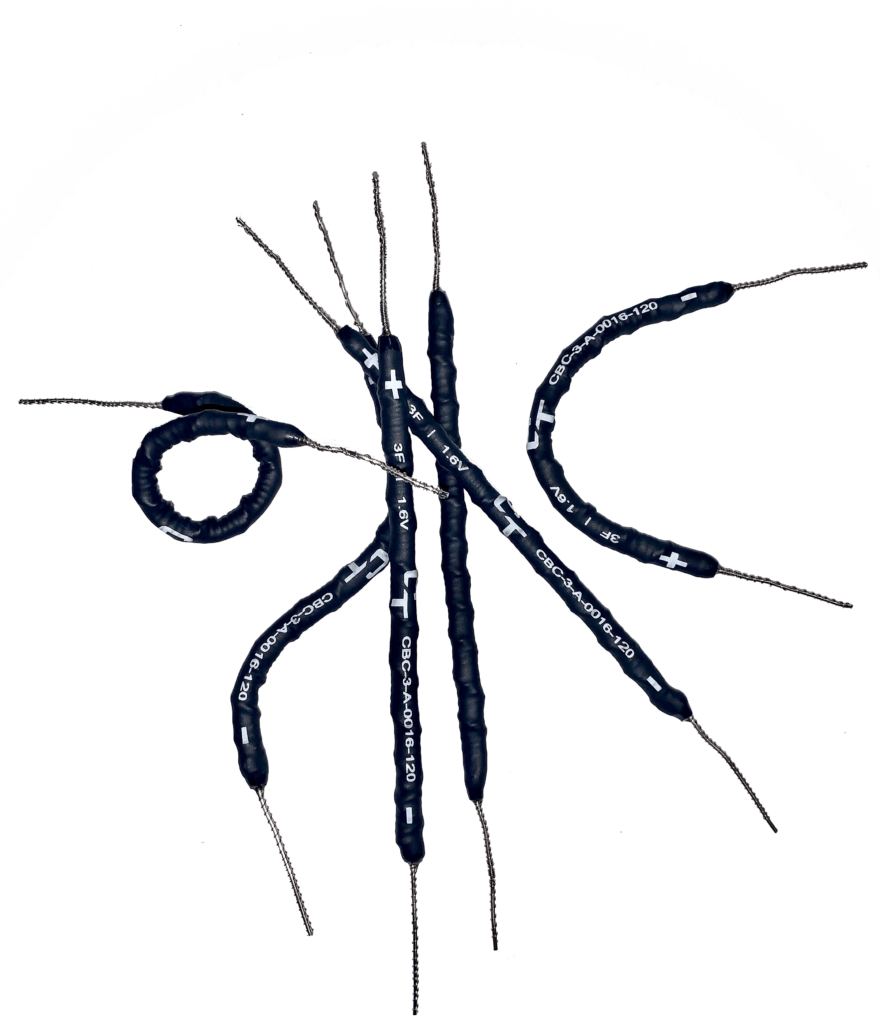
(Courtesy of Capacitech)
“The advanced research team at our Maxwell Technologies subsidiary is working with industry partners to take an ultracapacitor, either in a module or in a bigger system, and combine it with a non-lead-acid battery technology,” says Gordon Schenk, CEO of UCAP Power.
As far as other battery chemistries are concerned, particularly lithium-ion, supercapacitors look set to continue in their supporting role. “Battery-supercapacitor hybrid energy storage systems are the way of the future,” says Capacitech’s CEO Joe Sleppy. “The challenge is finding the physical space to add supercapacitors into a design.”
Cable-format supercapacitors
This is where the company’s cable-based capacitors (CBCs) come in, he adds. Where traditional capacitors use parallel plate electrodes (even if they are on films rolled into a cylinder), CBCs have two concentric electrodes. This long, thin and flexible form factor allows them to fit into vehicle wiring harnesses rather than battery casings or electronics enclosures.
“Our CBCs offer engineers placement advantages over traditional supercapacitors, helping them to improve design and performance with fewer trade-offs,” Sleppy says.
“The goal is to integrate supercapacitors into the wiring infrastructure of the vehicle to complement batteries. For smaller vehicles such as electric scooters, this placement advantage helps enable features such as regenerative braking systems.”
In EVs and e-mobility in general, supercapacitors will be used in low-voltage applications, particularly in support of vehicle electronics on 12 V ‘board net’ subsystems, according to Dr Pohlmann. “They provide unique advantages such as low-temperature performance, very high power and very robust design, as required for redundancy when you have more autonomous and safety-critical systems such as braking and steering on the 12V board net.”
Hybrid option
He adds that supercapacitors’ applications will widen into more propulsion-related areas as technology improves, with Skeleton’s contributions to this being its second-generation Curved Graphene supercapacitors and the SuperBattery hybrid energy storage system. While Skeleton’s Gen 2 supercapacitors, such as the SkelCap SCX5000 offer a specific energy of 11.1 Wh/kg, the SuperBattery offers 65 Wh/kg.
Dr Pohlmann says SuperBattery technology offers new capabilities for high-voltage hybrids and fuel cell vehicles. “They provide the power required for fast acceleration and the energy to support the fuel cell during longer periods of uphill travel or for warm-up purposes. Here we’re talking about periods of between 10 seconds and 5 minutes of use,” he explains.
“In these applications, SuperBatteries are preferable to high-power lithium-ion batteries, because they provide higher safety as well as better low-temperature performance and better efficiency, especially at high C-rates.
“However, we don’t see SuperBatteries rivalling batteries, but rather as a complementary technology. Batteries are not ideal for some applications, such as high-voltage hybrids, for which they lack power density, but SuperBatteries can help there.”
One of the major contributors to a supercapacitor’s high power density compared with batteries is its low resistance. This is usually expressed as the equivalent series resistance (ESR), which is the internal resistance that appears in series with the device’s capacitance, and Skeleton argues that ESR is the factor with the single strongest impact on system efficiency and working temperature.
In turn, these determine the proportion of the energy stored in the supercapacitor that can be retrieved under real-world conditions. Further, the operating temperature is the strongest predictor of how long the device will last in service. Through innovations in materials, construction and electrode manufacturing, Skeleton says it has been able to reduce the ESR significantly.
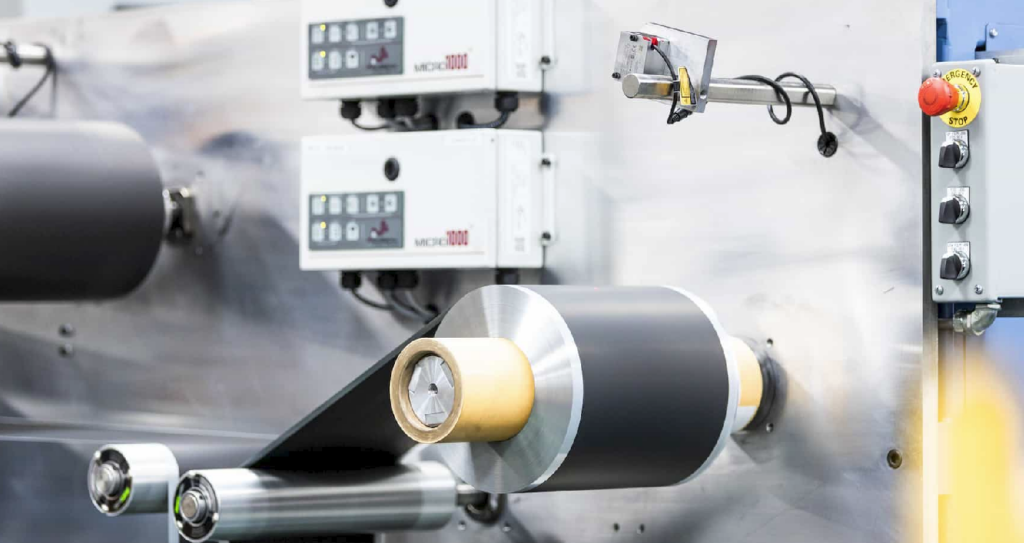
(Courtesy of LiCAP Technologies)
Ragone plots with W/kg on the horizontal axis and Wh/kg on the vertical axis allow the specific energy and specific power of devices with different capacitance ratings to be compared directly at different discharge rates, and consequently at different power levels.
For example, at a modest power output – indicated by complete discharge over 10 seconds – a 300 F Skeleton supercapacitor achieves 5.3 Wh/kg, while a commercial standard 310 F device with a higher ESR manages only 3.3 Wh/kg. The difference is even more marked as the discharge rates and power levels increase, and the device with higher resistance sees its specific energy drop sharply, while that of the lower resistance Skeleton device falls in a much gentler curve.
Chad Hall emphasises that supercapacitors have much longer service lives than batteries, which he points out is because they don’t rely on chemical reactions. “Every time you charge or discharge a battery, a chemical reaction takes place, using up some of the electro-active materials,” he explains. “How fast you charge/discharge, the temperature, and how old the battery is, can all have a major impact on how much damage is done to that battery for that cycle, and each cycle shortens the battery’s life.”
That is why supercapacitors are so good for protecting batteries in high-power applications and improving performance at the same time. “Applications that require high energy/power in and out, such as acceleration and brake energy regeneration, are ideal for a capacitor,” Hall adds. “You can capture about 55% more energy with an ultracap during regen than with a lithium-ion battery – and do it a million times.”
The impact on battery life can be substantial, as Jason McMillen, director of engineering at LiCAP Technologies, points out. “As an example, we are supporting major rail customers to replace batteries for emergency back-up track switching,” he says. “The switching is power-intensive but short in duration. That triples the life of the main lead-acid battery.”
Dr Pohlmann notes that most of the operational examples of supercapacitors paired with batteries these days are in industrial settings rather than e-mobility, but he does expect the combination to play an important role in the automotive sector, again mostly in low-voltage applications.
“If you combine a lithium-ion battery technology such as LFP with supercapacitors, you fix a big disadvantage of batteries – poor low-temperature performance,” he says. “That means you can reduce the size of the batteries, and at the same time add redundancy into the system.”
He does not expect the combination to be used on a large scale in high-voltage applications, however. “Not every EV will have supercapacitors and batteries paired, but the combination is relevant to high-performance vehicles,” he says.
While all vehicles could benefit from battery-supercapacitor hybrid energy storage systems, those used for last-mile deliveries where there is a lot of starting and stopping stand to benefit the most, argues Sleppy. “That is especially true in applications where space is limited, and the battery operates at high C-rates when accelerating or going up a hill,” he says.
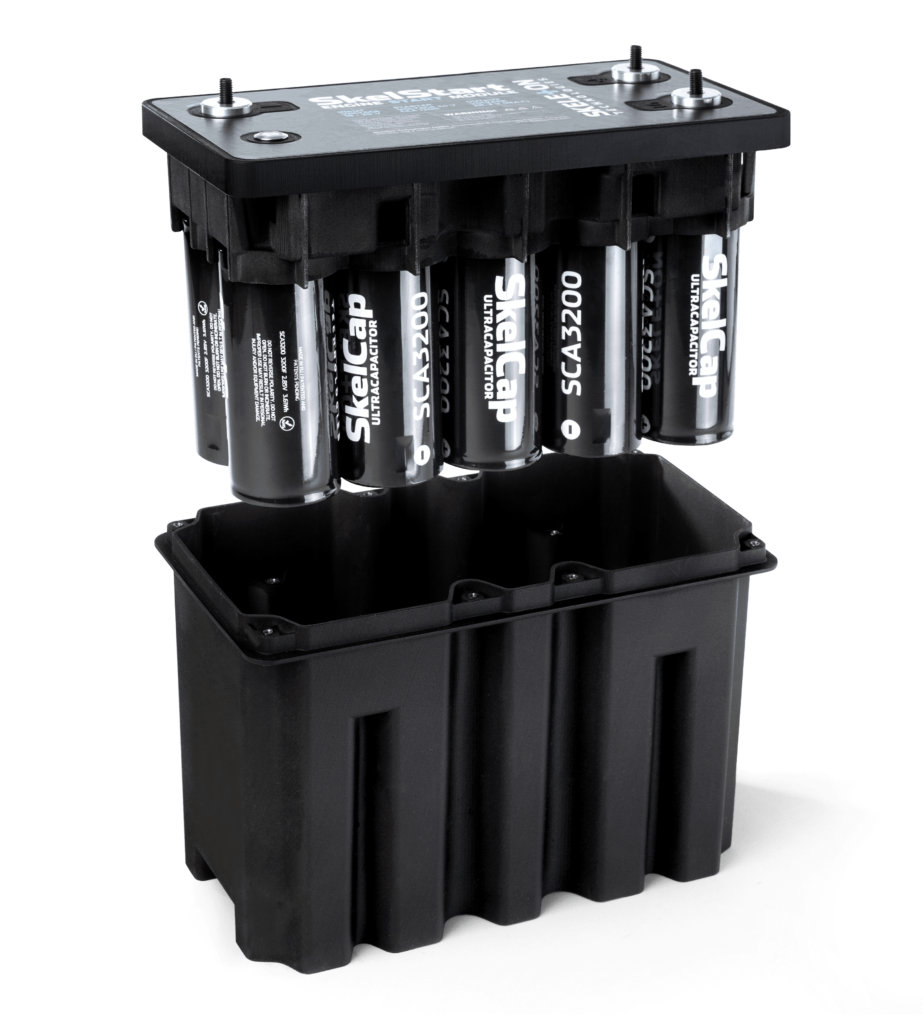
(Courtesy of Skeleton Technologies)
Hall concurs, but adds that by incorporating a ‘sailing’ mode, in which the motor/engine is switched off while coasting and by capturing brake energy, long-haul vehicles also would see a significant increase in both miles per charge and battery life.
“The best on-road fit are large trucks and construction equipment,” says McMillen. “Large vehicles use huge amounts of energy to get moving.”
Dr Pohlmann emphasises the value of integrating supercapacitors directly into the powertrain of performance and sports vehicles in particular, as well as motorsport machinery, where the company is working with push-to-pass and kinetic energy recuperation systems. Luxury vehicles also benefit, he adds, where much of the value is in providing braking energy recuperation and improved acceleration.
“For integration into 12 V and other low-voltage board nets, the application is less niche,” he says. “We are sure there will be plenty of supercapacitors on the road by 2030.”
Integration issues
One of the main obstacles to supercapacitor integration into EV powertrains, where substantial amounts of energy are required, comes from their principal disadvantage of low energy density in Wh/litre. This makes them relatively large, so finding the physical space to add enough of them to make a meaningful difference to the performance of the energy storage system can be difficult, says Sleppy.
However, technological progress is easing this problem, Hall notes, citing power electronics that have become smaller and cheaper, allowing DC-DC converters to transmit more power.
“Due to its much lower resistance, the power will come from the ultracapacitor before the battery when power demand is high,” he says. “But good power electronics are needed to manage the power and energy for long life, and safe, reliable operations of both the battery and capacitor.”
To achieve its promise, McMillen says, supercapacitors need separate control and switching in the circuit so that they can provide the power to overcome inertia to get a heavy vehicle moving, and to get the battery to jump back in for the sustained loads.
“The main challenge is to find out if the EV can actually benefit from supercapacitors, followed by convincing the OEMs to integrate not one but two novel technologies in their vehicles,” Dr Pohlmann notes.
“This is connected to the willingness of any OEM to share vehicle performance data. As only specific combinations of supercapacitors and batteries bring strong benefits – as in smaller batteries combined with high-power powertrains – the application needs to be carefully evaluated before reaching a decision.”
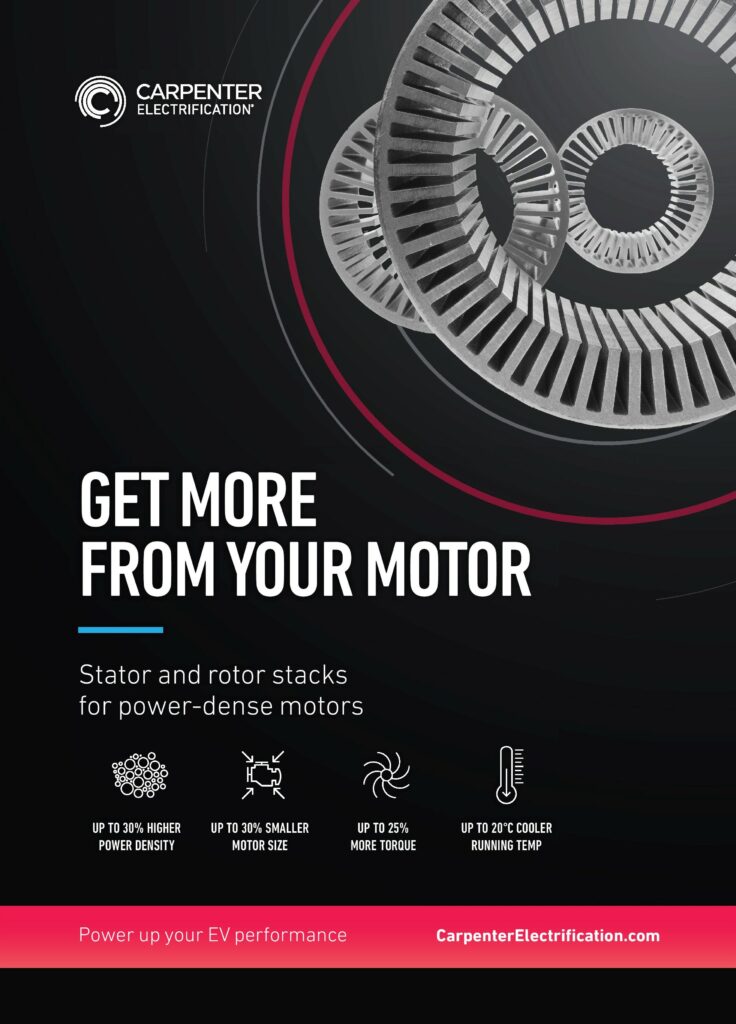
Also, supercapacitor technology is still somewhat unfamiliar to the automotive industry, leading to higher integration thresholds. “Here, only constant interaction can improve the situation,” Dr Pohlmann adds.
Graphene potential
As in many areas of technology, the use of graphene is expected to bring major performance benefits to supercapacitors. “Graphene is a class of material with very high electrical conductivity and a lot of surface area,” says Capacitech’s CTO Dr Isaiah Oladeji. “Successful adoption will lead to lower internal resistance and high capacitance.”
Graphene is already part of the recipe in many supercapacitor products, remarks McMillen, but he cautions that much more research is needed into its use in higher concentrations.
Graphene’s structure is inherently two-dimensional, which prevents it from holding on to ions to store energy, Hall points out. That is because graphene sheets tend to stick together face to face.
A lot of r&d effort is therefore going into making graphene sheets curve, to prevent that from happening and allowing the formation of ‘mesopores’ (pores larger than 2 nm across) that can be wetted by environmentally benign ionic liquids. One group of Chinese researchers, for example, achieves this by introducing oxygen atoms through synthesis of graphene oxide.
Skeleton Technologies uses a type of curved graphene in its supercapacitors and hybrid SuperBatteries, as noted above. “The main impact is higher energy density, so less space is needed for energy storage – lower volume and weight while maintaining the same performance,” says Dr Pohlmann.
“What we have seen during testing is the ability of graphene to help reduce the ESR of a supercapacitor,” adds Hall. “The challenge, of course, is finding a balance for a volume application that needs higher power than a commercial supercapacitor can provide while incorporating the high cost of the graphene. Many applications developers say they need higher power or energy, but most are not willing to pay much more for incorporating exotic materials.”
Structural supercapacitors
As with other low energy density power systems, such as photovoltaic solar panels, finding space for enough supercapacitors in a vehicle is difficult, so integrating them into structural components is an attractive option. Structural supercapacitors are therefore a growing area of academic research, Sleppy says, as these multi-purpose materials offer structural integrity and energy storage capabilities simultaneously.
However, their development poses a number of challenges. As Dr Oladeji points out, “Due to high electrode resistance and low ionic conductivity of the non-liquid electrolyte currently in use, structural supercapacitors need years more of development.”
Hall is sceptical about the practicality of the technology. “While the idea is great, to bring the cost down you need to be able to manufacture a product at volume for a wide range of applications, but creating a special product for a single application runs counter to those ideas,” he says.
There are also efficiency losses when the structure of the product is changed, he adds. Cylindrical cells are wound on machines with carefully controlled tension that is needed to minimise resistance while enabling the roll to enter the casing easily, while avoiding short-circuits and breaking. Similarly, prismatic cells need external pressure to achieve their design cycle life.
“While that could be built into a structural product, it isn’t very cost-effective. Using the cells inside an existing structure, for example on a door post or in a frame, could work, but access for maintenance would be the issue.”
He also points out that there are regulations, in the EU for example, that effectively rule out the structure from being used for energy storage, stipulating that body panels that could come into contact with pedestrians must not be energised.
“At Ioxus, we have explored the idea of using capacitors for storage inside body panels and wheel wells, but to date we have not had any real commercial interest in these products.”
Dr Pohlmann notes that structural supercapacitors are at a low technology readiness level, and they are being built on a small scale in laboratories. The main problem to solve, he explains, is the need for liquid electrolytes.
“Having a liquid component always adds a layer of complexity as well as safety considerations,” he says. “It’s possible to use water as the electrolyte, but that reduces the performance significantly, although it would also reduce the cost.
“The question is, do structural supercapacitors make sense? It might be more cost-efficient to just add a larger battery pack or a supercapacitor pack in a vehicle, assuming that the space is available.”
In conclusion, a thorough understanding of all the duty cycles of all the systems in a vehicle is crucial in assessing where best to use supercapacitors, and in sizing and matching them to each application. Equally important is a thorough understanding of battery technology to identify the gaps in battery performance that ultracapacitors can fill.
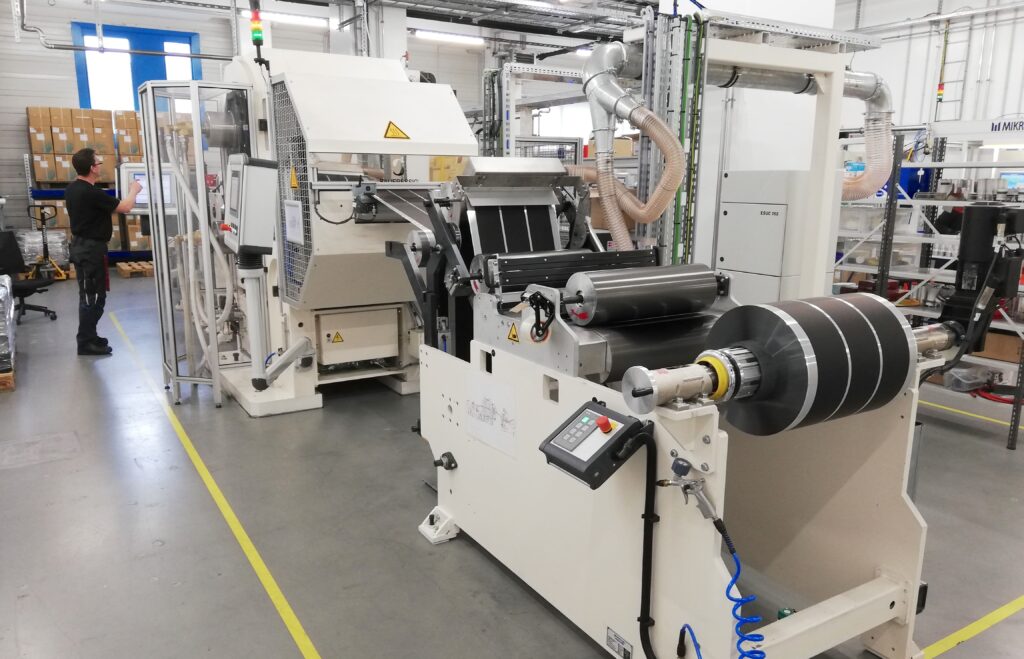
(Courtesy of Skeleton Technologies)
ONLINE PARTNERS
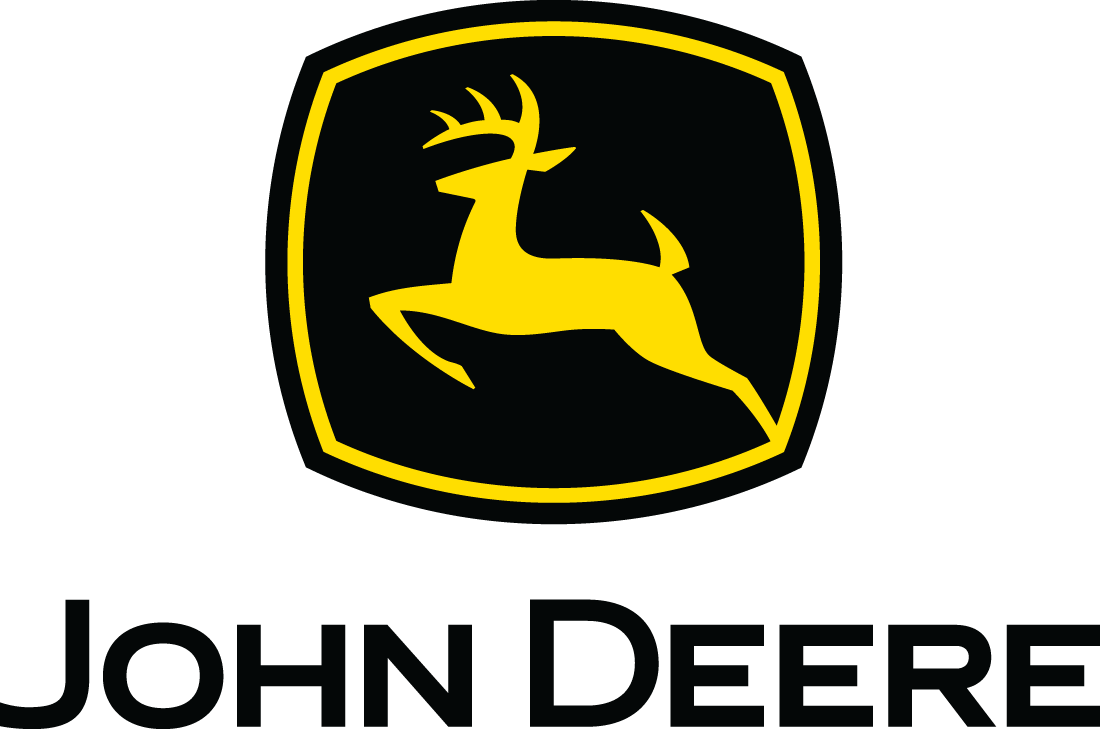
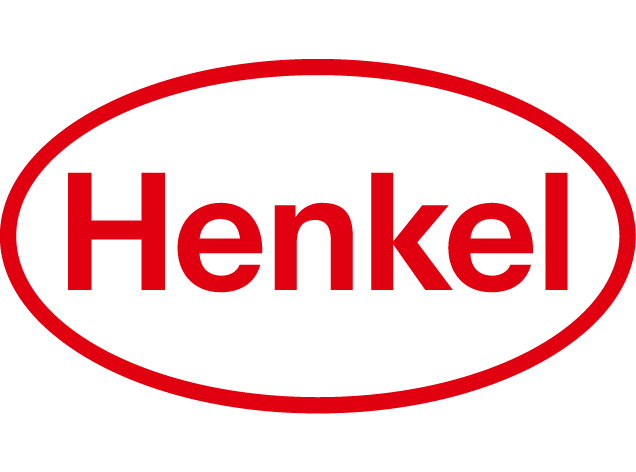
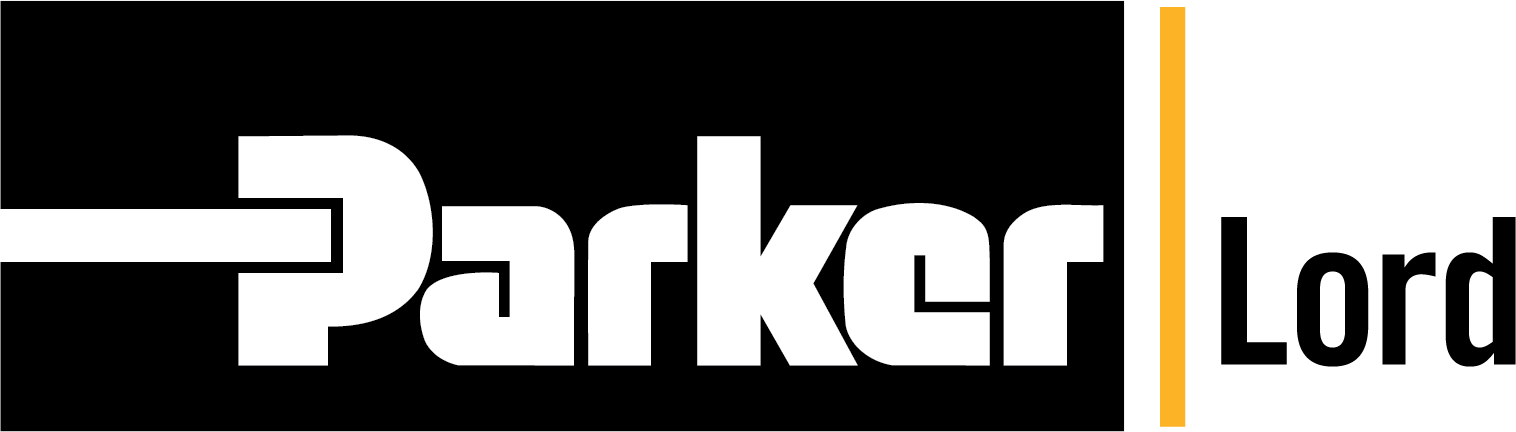
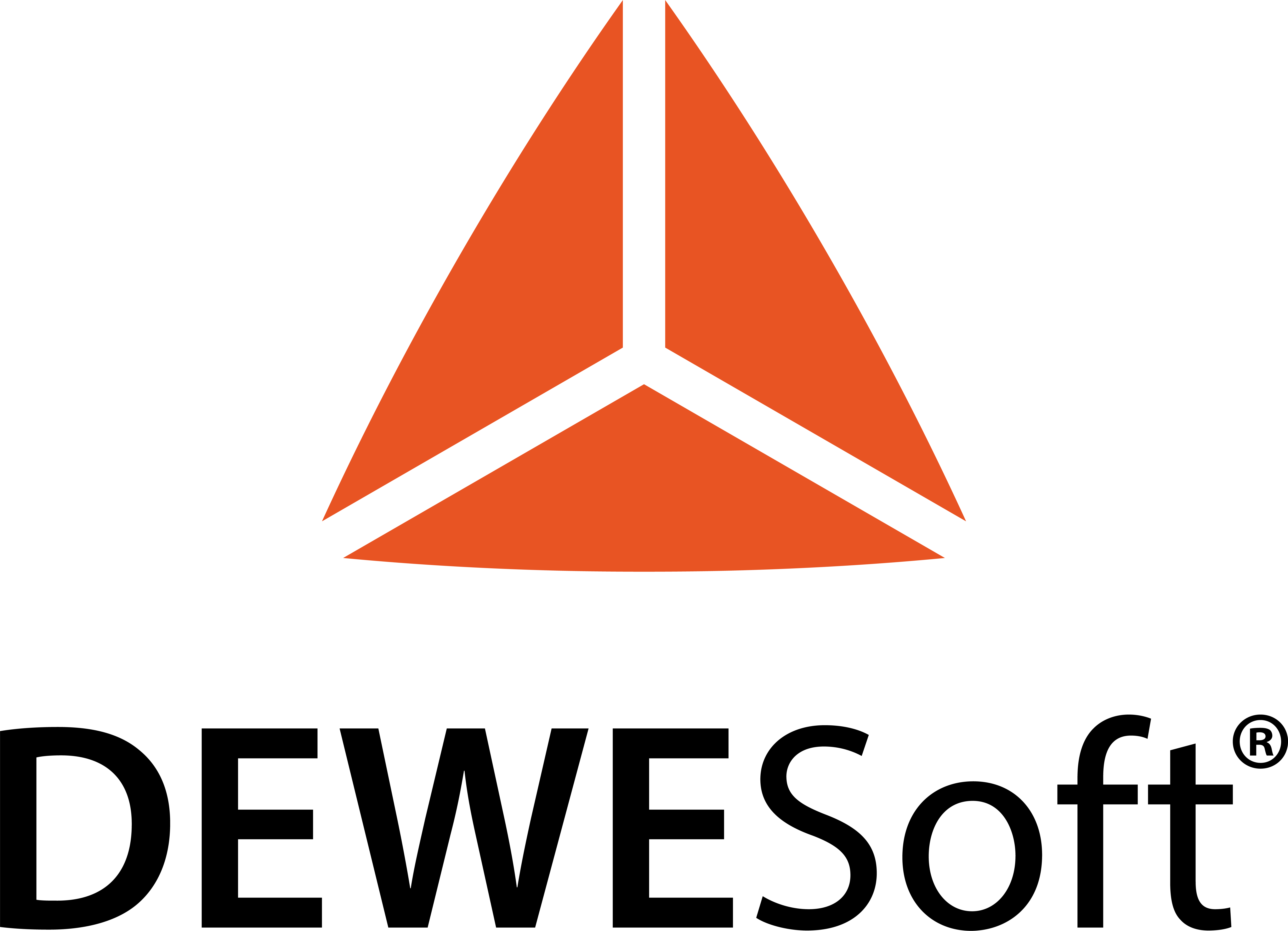
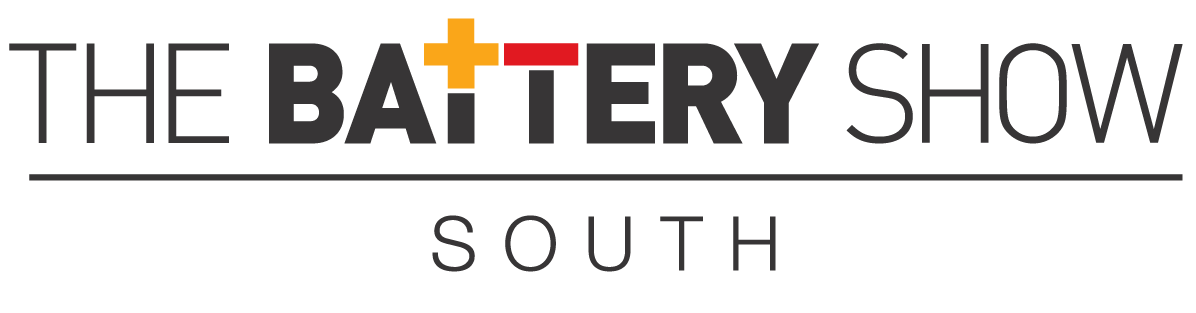
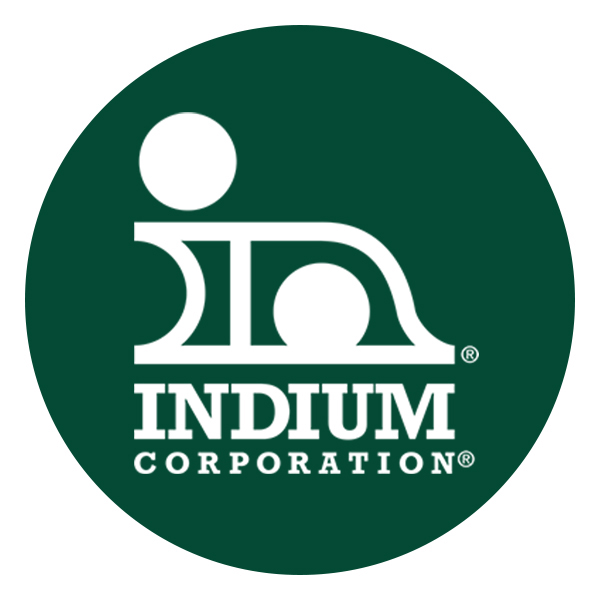
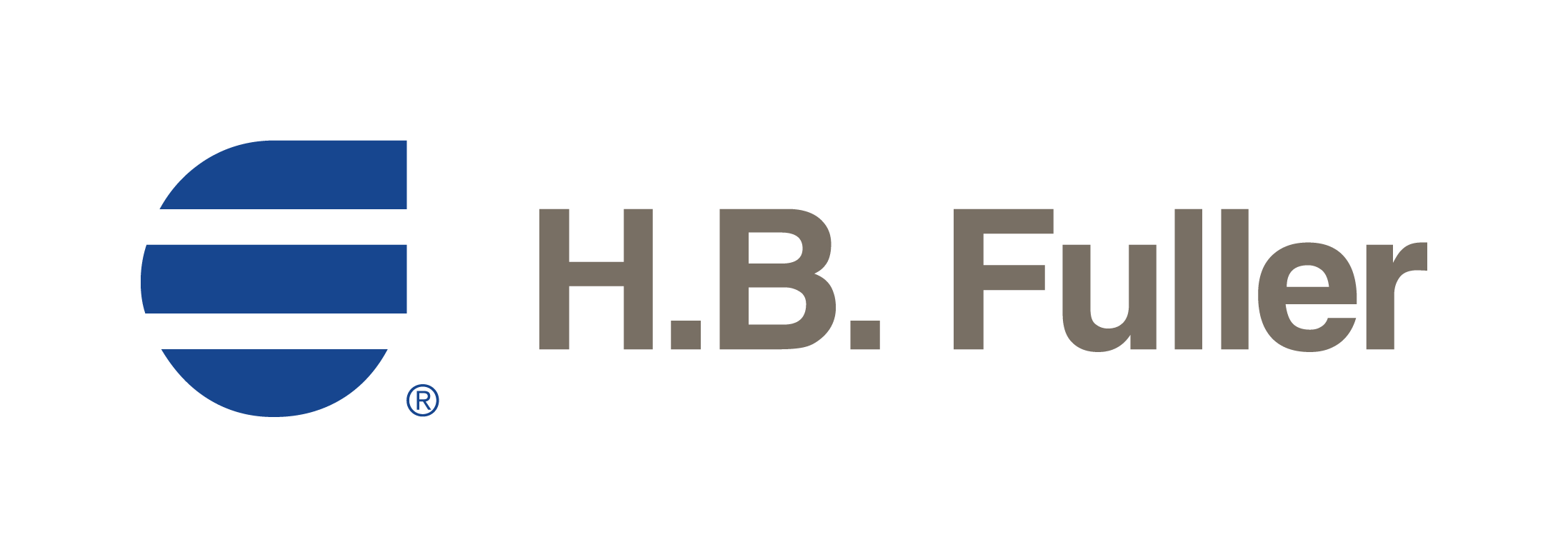