Sono Motors sets sights on whole-vehicle PV panels
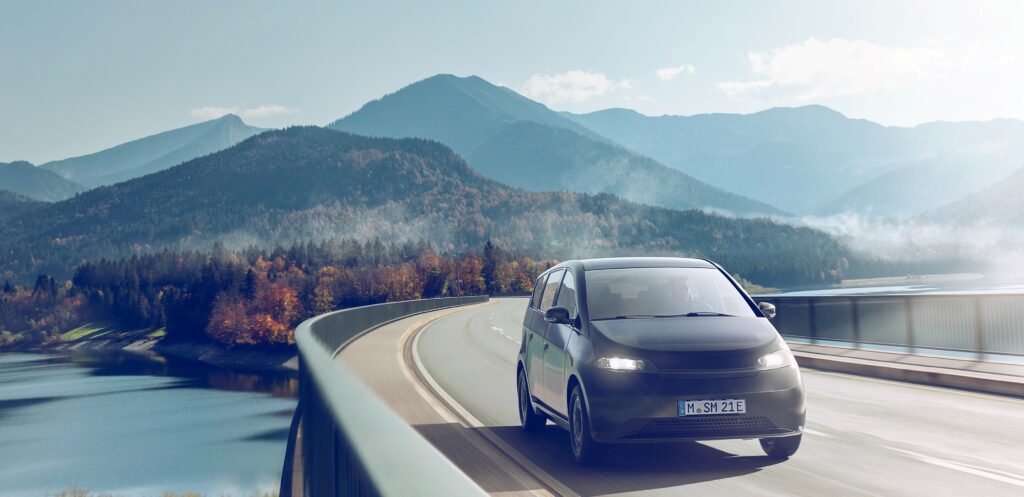
(Courtesy of Sono Motors)
Sono Motors, developer of the Sion solar-powered car, is working on integrating solar cells into all of its five-door, five-seat family hatchback’s outer body panels (writes Peter Donaldson).
The Sion is a BEV with a 54 kWh battery that the company expects to provide a range of 305 km on a full charge, with the solar panels adding an average of 112 km of range per week (245 km maximum) by charging the battery, including while the vehicle is moving.
Founded in 2016 by three friends in a garage in Munich, these days the Nasdaq-listed company employs more than 260 people. In pursuit of its goal of putting ‘solar on every vehicle’, Sono Motors has signed more than 17 commercial contracts with companies including MAN Truck and Bus, autonomous shuttle bus developer EasyMile and light EV developer ARI Motors.
“We are working with them on prototypes and projects for solar integration on trucks, trailers, campers, vans and even boats,” says Omar Stern, the company’s senior project manager for vehicle-integrated photovoltaics.
“The price of batteries as well as solar cells has been falling significantly for years now, while at the same time the efficiency of solar cells has constantly improved. As a result, using PV technology for mobility and transportation makes increasing sense.”
The solar cells that the company integrates into the Sion’s body panels are of the monocrystalline silicon type, with an efficiency of about 22%, and Stern emphasises the importance of selecting the right supporting laminate material.
“Usually, solar cells are laminated onto glass that’s 2-5 mm thick,” Stern says. “However, glass has a comparatively high weight and low fracture resistance. We therefore use a polymer as a substrate material. It is light, resistant and far more fracture-proof than glass.”
Sono Motors also developed its own multi-channel Maximum Power Point Tracking (MPPT) control unit that plays a central part in maximising energy efficiency and power output, he says.
MPPT is solar PV technology’s response to the fact that electrical power depends on voltage and current in the relationship encapsulated in the basic equation P = V x I. When graphed, the relationship follows a curve that runs between the physical limits set by the short-circuit current and the open-circuit voltage. The point at which the maximum power current (Imp) and the maximum power voltage (Vmp) intersect the curve is the maximum power point.
The shape of the curve changes with the intensity of the light falling onto the solar panel, introducing some complexity to the situation, so MPPT controllers regulate the panel’s output current and voltage to maximise the power delivered to the battery while minimising losses in the form of heat.
“Even with uneven sun exposure or shading, the maximum solar power is collected by each solar body panel,” Stern notes.
“Using the whole body of the Sion gives you more surface and therefore more possible solar yield than with add-on solar panels, and from a design perspective we can perform a much more seamless integration this way.”
While vehicle-integrated photovoltaics is a relatively young field, and challenges remain in merging automotive knowhow with solar PV expertise and applying them to the mass production of solar body panels, the company’s solar modules are durable and damage-resistant, Stern says.
The company expects the panels to generate useful power for the lifetime of the Sion, and Stern notes that the polymer layer provides the solar cells underneath with protection from small impacts and scratches.
“Replacement is only necessary if the cells are damaged,” he says. “In the case of a severe accident, after which you have to change a door for example, we expect our components to be no more expensive than a traditional painted door.”
ONLINE PARTNERS
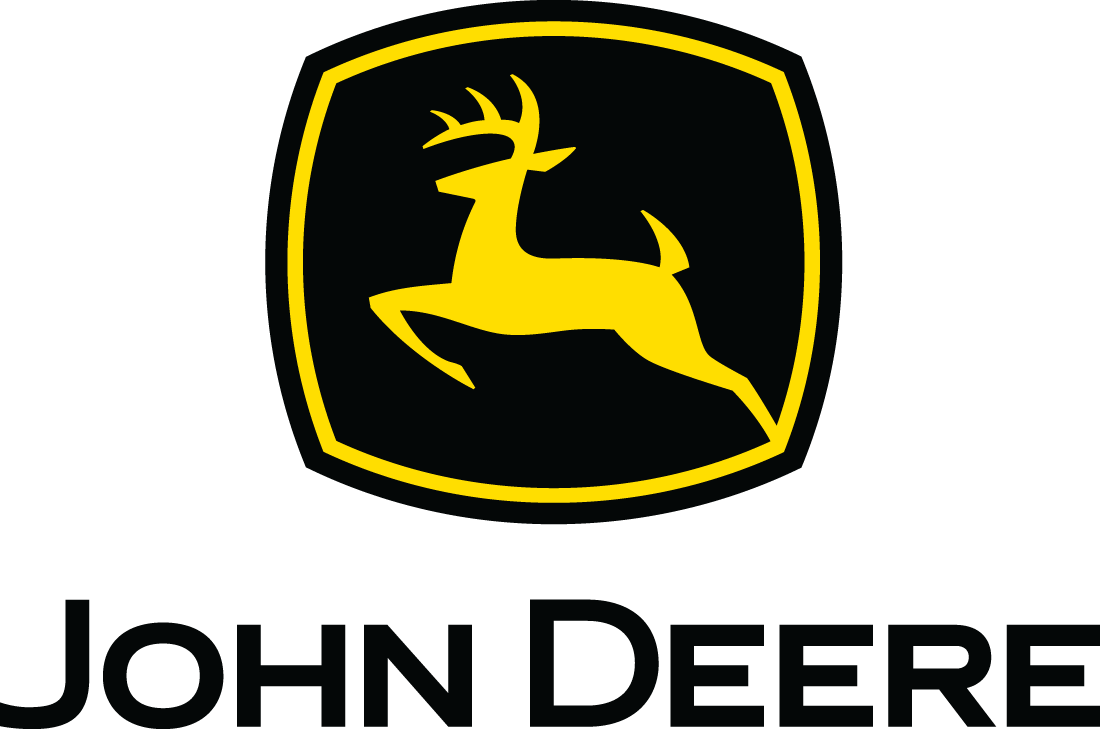
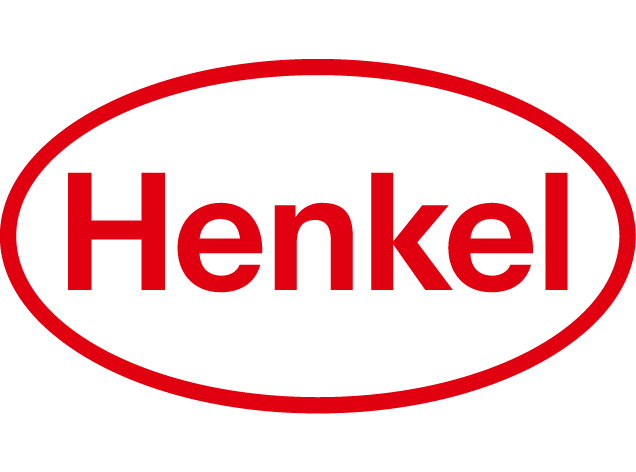
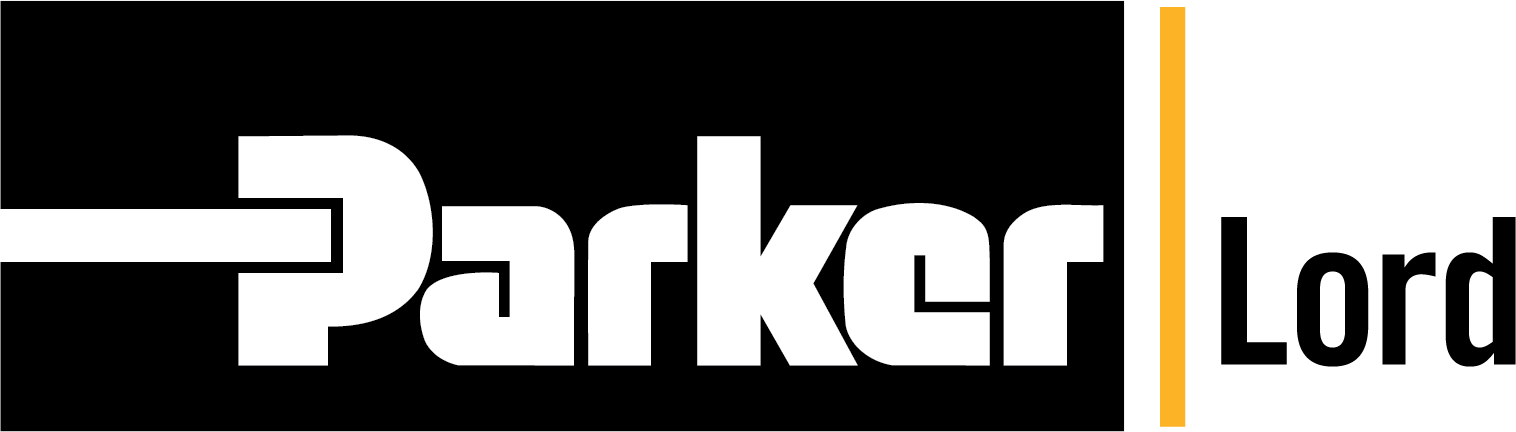
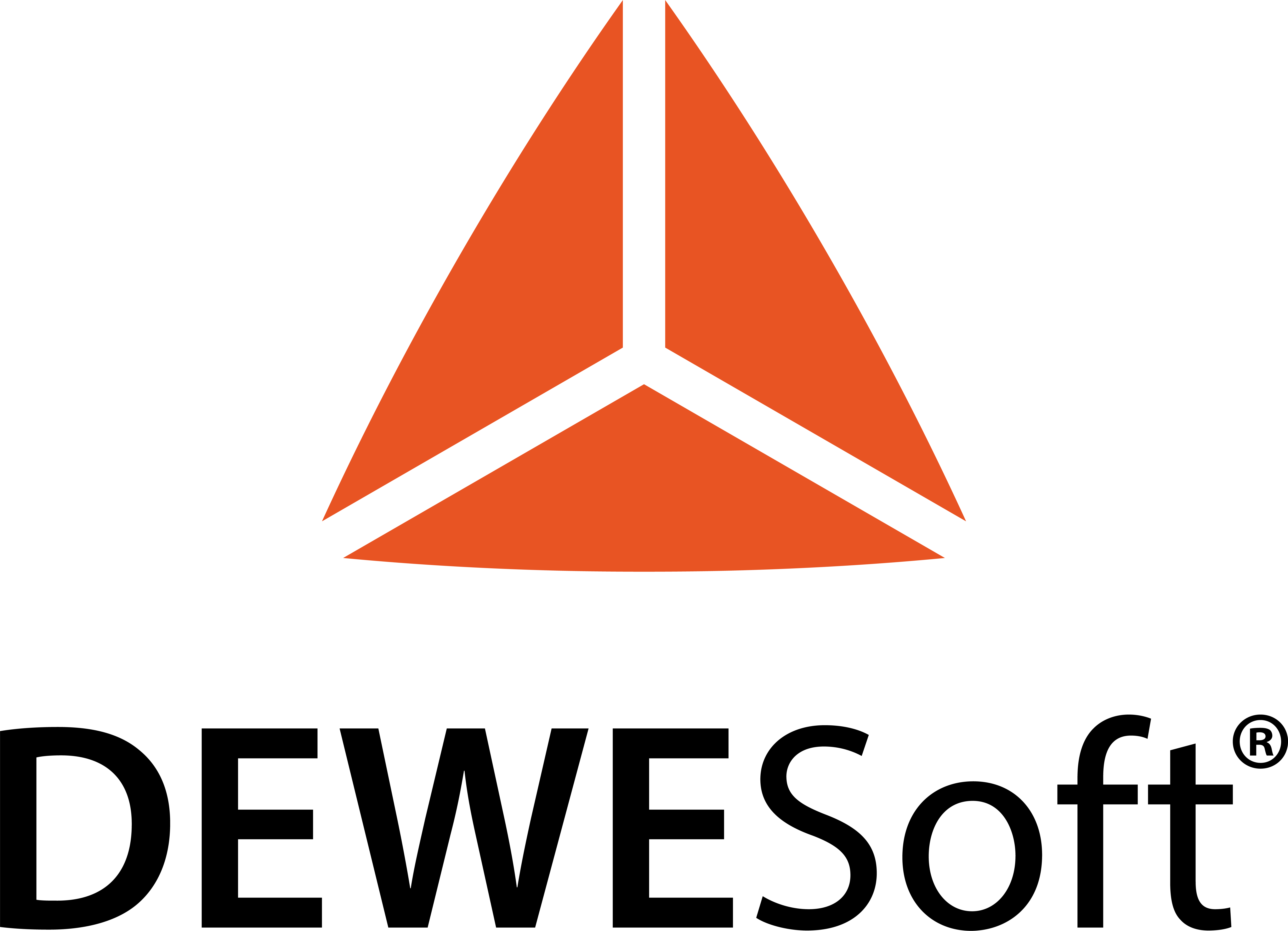
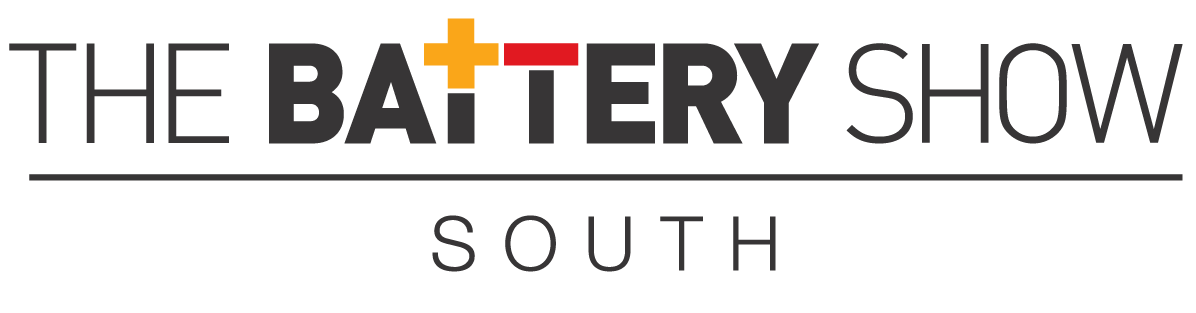
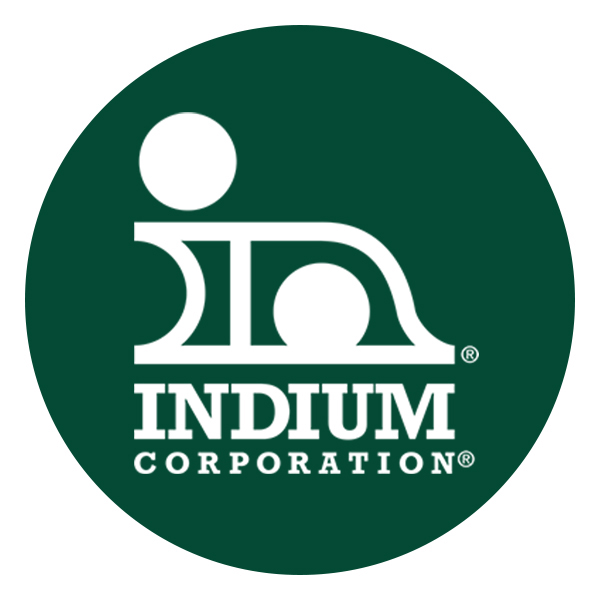
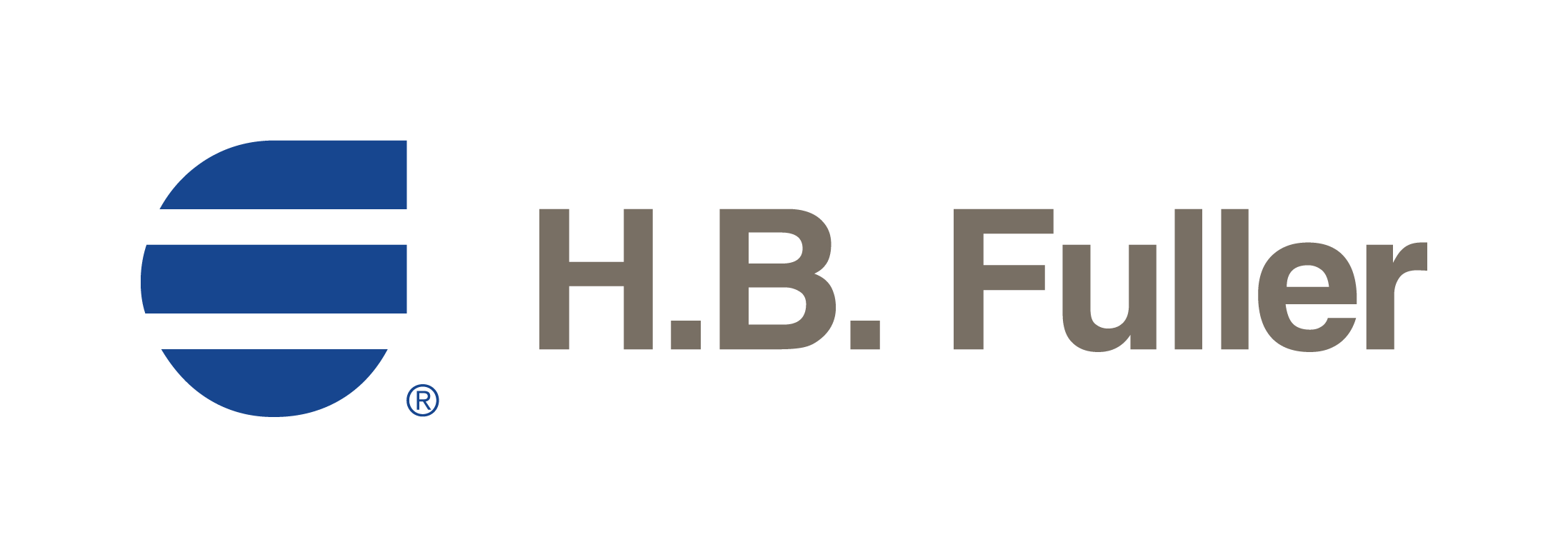