Solid-state batteries
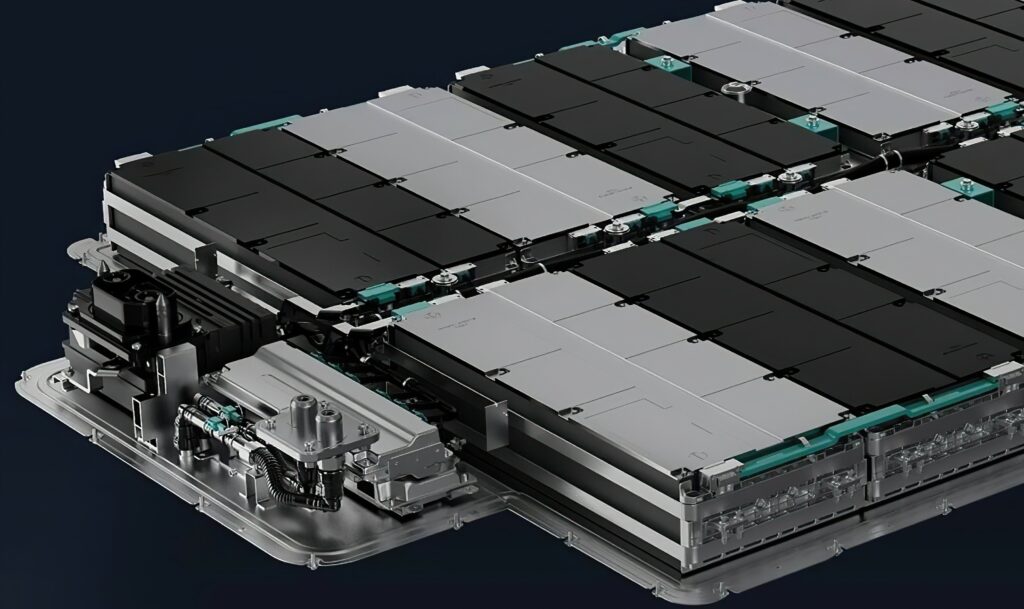
(Courtesy of NIO)
Liquid displacement
As batteries that use solid instead of liquid electrolytes begin to appear, Nick Flaherty cautions that challenges remain in bringing them to market
Solid-state batteries (SSBs) are seen in some areas as a key way forward for e-mobility applications. For one thing, replacing the liquid electrolyte in lithium-ion cells can help to reduce the growth of lithium dendrites that cause short-circuits that, in the worst case, lead to vehicle fires.
Another reason is that moving to SSBs also opens up the use of other materials that are not practical in liquid-based cells, particularly lithium metal as the anode. This can potentially provide a higher energy density than lithium-ion cells, and cells with an energy density of 1514 Wh/litre have already been demonstrated in the laboratory.
That lighter weight and higher energy density is also of interest for electric aircraft designs.
However, the development of SSBs is a challenge, and many observers do not see them being in mass production until 2030, for a number of reasons. One challenge is that a solid electrolyte limits the ability of the charge to move through the material, and, critically, across the interfaces of the different materials.
That can reduce the amount of power the cell provides, the specific energy measured in Wh/kg, as the voltage has to work harder to force the current through the cell. It also reduces the number of charging cycles, as the higher voltages can degrade the solid electrolyte faster than a liquid one.
Other challenges include the manufacturing process for high-volume EV designs, and the rise of alternative, safer liquid aqueous electrolytes that can be used with existing cell manufacturing lines and enable safer cells. As a result, many of the current research projects into new materials and structures for SSBs also include their manufacturability.
So finding the right combination of materials for high-performance SSBs for e-mobility is a major area of research, and there are currently three main contenders for the solid electrolyte at the heart of the cell. These are oxides and sulphides, which can be created as ceramic materials, and polymers which infuse a ceramic scaffold to carry the current instead.
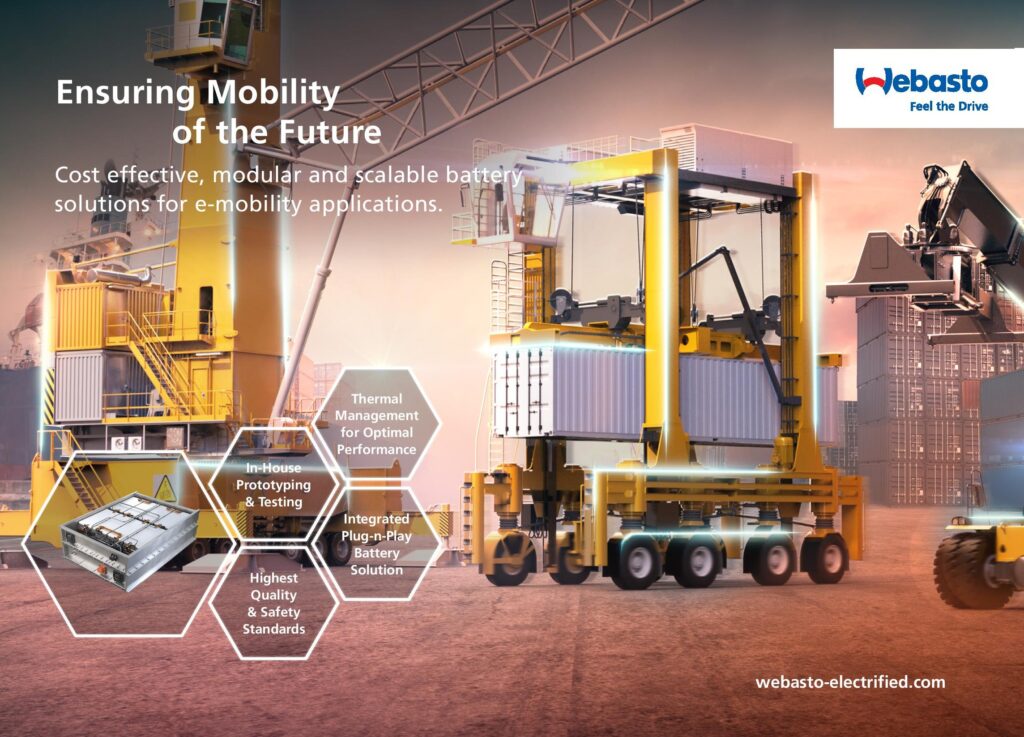
One difference between the development of SSBs and existing lithium-ion cells is the balance of specific energy in Wh/kg and energy density in Wh/litre.
The move to fully SSBs allows cells with much higher energy density, which means the cell is smaller and lighter for a given energy. That in turn means a battery pack can provide either more range in the same size, or a lighter, smaller, cheaper pack with the same range.
That often comes with a penalty in the specific energy, or the amount of power the cell can provide. This is more of an issue for heavy-duty electric platforms such as trucks and buses, so there are different trade-offs in the choice of materials for an SSB for different applications. Electric aircraft of course need both.
Using smaller, lighter cells leads to a fundamental redesign of the battery packs, with less need for physical protection and cooling, so lighter materials can be used. That is a dramatic step for an e-mobility platform and takes time to enter mass production, even when the cells are themselves in mass production. This is why most cell developers see 2030 as the key date for SSB technology. They have been working on the technology for many years, moving from A samples to B samples, increasing the capacity from 5 Ah to 20 Ah, for testing by car makers for early prototypes.
Several SSB cell developers are now building pilot lines for small-scale production in 2022 and 2023, and for volume production in 2024 and 2025. The cells from these lines can then be used in vehicles in series production in 2028 to 2030, which is why there is the focus on that timescale.
The move to full SSBs also has an impact on the choice of form factor. The most popular solid electrolytes are built from ceramic materials that do not bend, which rules out the use of cylindrical cells. This is seen as a problem, as cylindrical cells are the most cost-effective to make: they can be produced in high volume on an automated, roll-to-roll process.
Finding the most cost-effective method of mass production for SSBs from pouch cells then is a key area of development. The higher energy density might compensate partly for the more complex manufacturing process, by saving costs on cooling in other parts of the vehicle, but that is why other, non-standard techniques such as plasma processes and 3D printing are being explored.
How solid-state cells fit with existing manufacturing processes is also critical. Some are modifying existing lithium-ion lines, using polymer-based ‘semi-solid’ electrolyte and electrode materials but with standard materials for the rest of the cell. That will be enough to enable production in high-end, limited-run vehicles later this year.
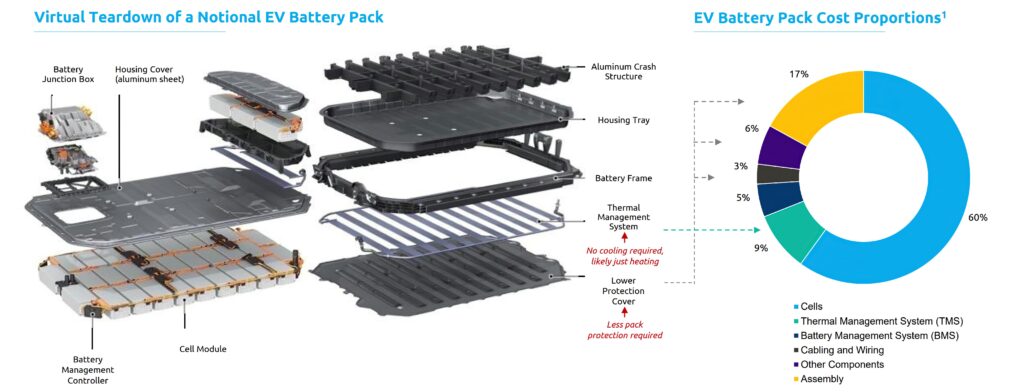
(Courtesy of SolidPower)
Semi-solid electrodes
Semi-solid electrodes use no binder, they mix electrolyte with active materials to form a clay-like slurry. The slurry allows thicker electrodes with less mass and cost while enabling a simpler manufacturing process. This is flexible enough to be used with a wide range of different materials, including silicon.
One project is looking to combine a lithium metal anode and a semi-solid cathode for electric aviation applications. The project also includes the development of a commercial, modular, pilot line that can scale up to volume production.
Another interim approach is using silicon anode technology already proven in cells being commercialised now. The 450 Wh/kg, 20 Ah cells are now in production, with 800 Wh/kg versions heading that way as well.
The challenge with silicon is that the anode can swell by a factor of three when charging, causing the cell to crack and leak. While considerable work has been done on minimising this issue, using a solid electrolyte avoids this problem
Other techniques used to boost the capacity of existing cells, such as using 3D structures in the copper or aluminium foils used for the cathode, can also be applied to SSBs.
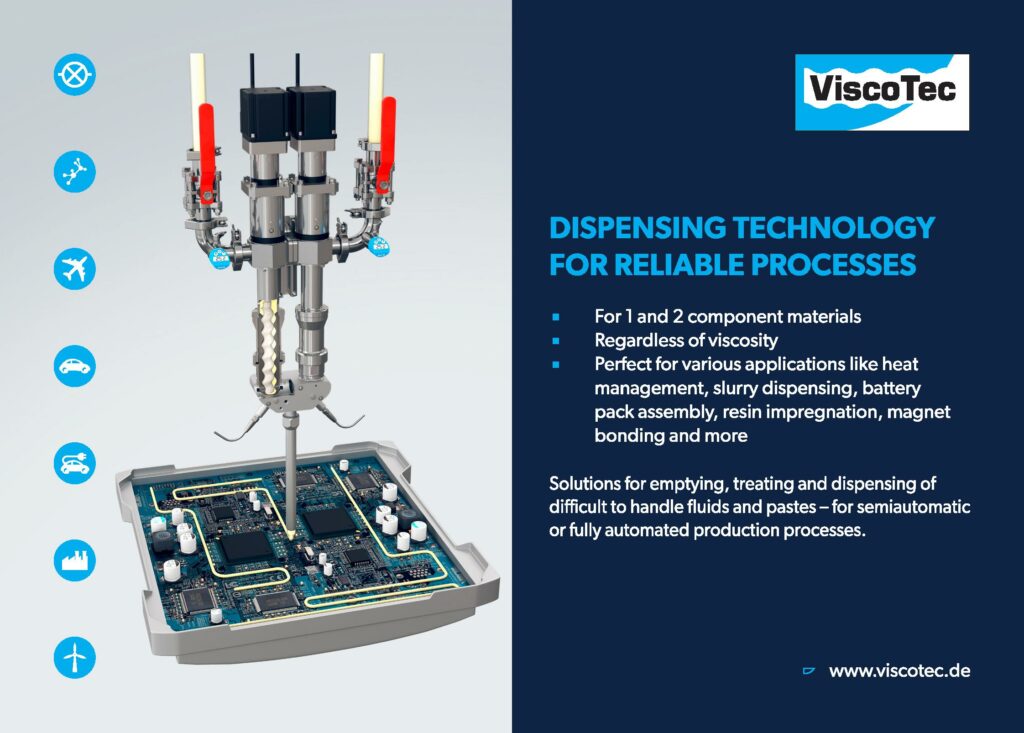
Polymer electrolytes
Semi-solid electrodes with a high nickel content and a polymer electrolyte are also being used for a 150 kWh battery pack for Chinese electric car maker NIO for the ET7. This is expected to be in production by the end of 2022.
The SSB uses interface engineering to achieve stable cycling of a lithium polyethylene oxide polymer electrolyte using a cathode with 50% nickel, 20% cobalt and 30% manganese for a cell that produces 4.2 V with a carbon-silicon anode that also contains lithium.
The cell has an energy density of 360 Wh/kg and would allow a range of more than 1000 km, along with supporting fast charging.
Material interface
The material interface is a key area of research in SSBs. The interface between the anode and a solid electrolyte shows a large electrical resistance whose origin is not well-understood.
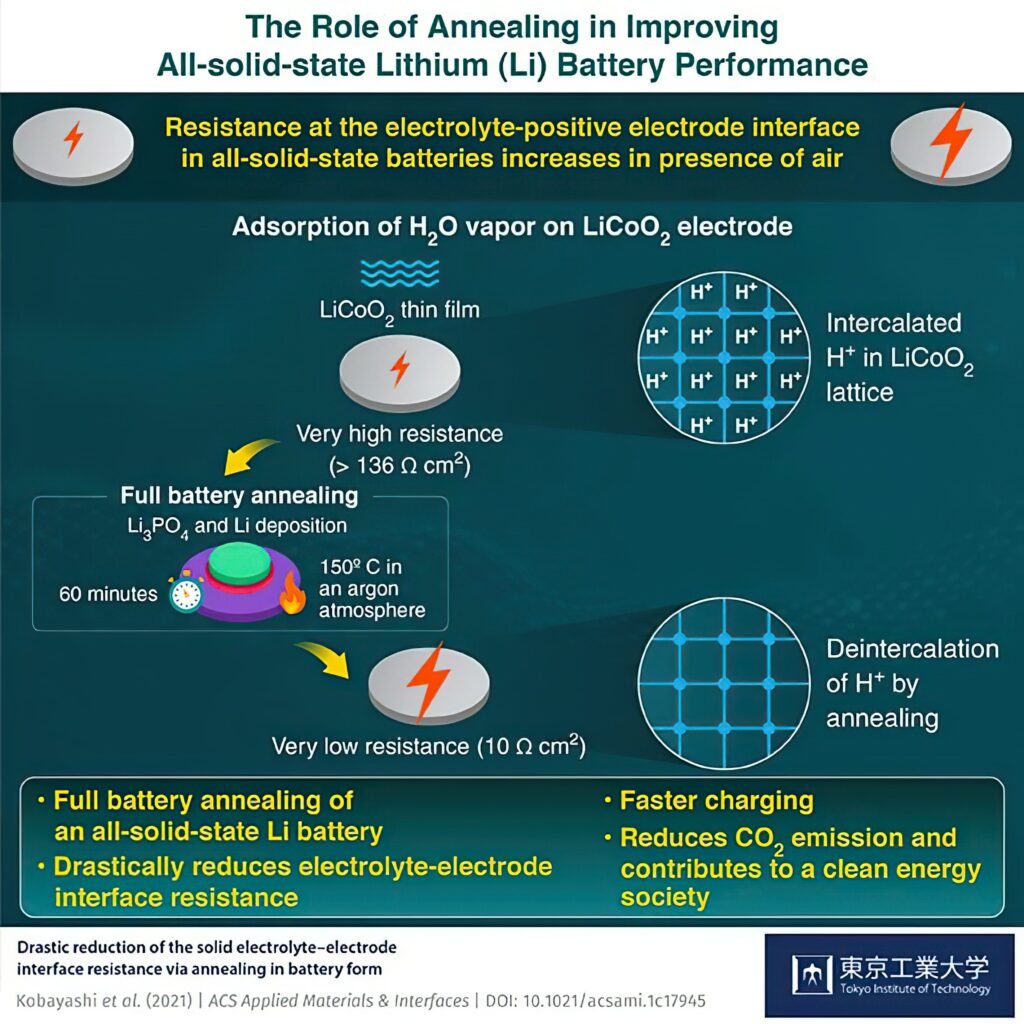
(Courtesy of Tokyo Institute of Technology)
This resistance increases when the electrode surface is exposed to air, degrading the battery’s capacity and performance. While several attempts have been made to lower the resistance, none have managed to bring it down to 10 Ω cm2, the same as when not exposed to air.
Tests on thin-film batteries consisting of a lithium cathode, LiCoO2 anode and a Li3PO4 solid electrolyte show that it is the water content in the air, rather than the oxygen or nitrogen, that degrades the battery’s performance, and by a factor of 10. Using an annealing heat treatment at 150 C for an hour reduced the resistance to 10.3 Ωcm2, comparable to that of the unexposed battery
Simulations and measurements show that this reduction could be attributed to the spontaneous removal of protons from within the LiCoO2 structure during annealing.
The importance of the interface has also been demonstrated in a new lithium metal pouch cell design by a major battery manufacturer.
This uses a silver-carbon (Ag-C ) nanocomposite layer over the lithium metal anode to stop the growth of the dendrites and provide larger capacity, longer cycle life and improved safety. It has been combined with a high-nickel layered aluminium oxide cathode and an argyrodite-type solid-state sulphide electrolyte, but the key was the combination process .
A warm isostatic pressing technique was used to improve the contact between the electrode and the electrolyte. This involves placing the metal particles in a flexible mould and then applying high pressure from a fluid rather than using direct pressure applied by a die press. The resulting electrodes are then sintered in a furnace, increasing the strength of the part by bonding the metal particles before coating.
The 5 µm Ag-C layer allowed the team to reduce the anode’s thickness and increase the energy to 900 Wh/litre and so make the cell half the size of a lithium-ion cell. This design also supports a lifetime of over 1000 charging cycles.
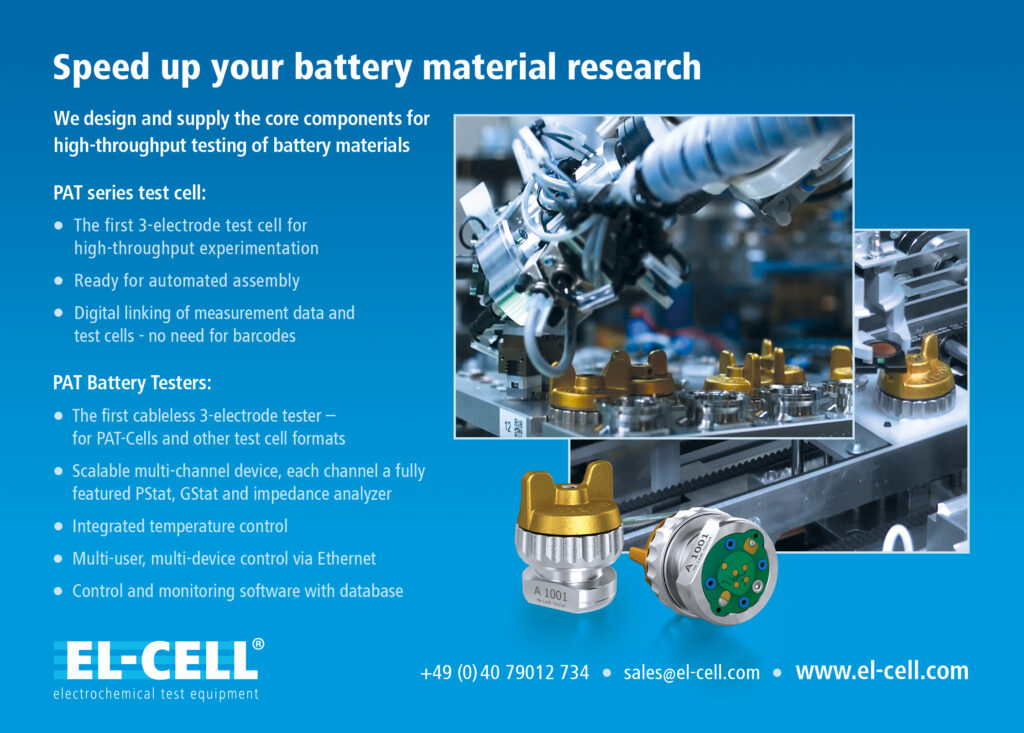
SCiB
One SSB technology already in production is called SCiB, and is used for 48 V hybrid vehicles. The latest design uses lithium titanium oxide (LTO) in its anode to achieve excellent characteristics, including safety, long life, low-temperature performance, rapid charging, high input/output power and large effective capacity.
The 20 Ah-HP SSB cell is designed for heavy-load applications where high power input and output are essential, and for situations where battery cells must suppress heat and operate continuously, such as rapid charging of commercial vehicles and ferries, and regenerative power systems for rolling stock. The cell is the same size as the current 20 Ah product, allowing designers to upgrade to the improved input and output power with the same module pack.
The cell has an energy density of 84 Wh/kg, so it’s still a long way off from the performance of lithium-ion cells. However, it allows an input power that is 1.7 times higher than the previous generation at 1900 W to reach 50% charge in 10 seconds, with an output power that is 1.6 times higher, again at 1900 W.
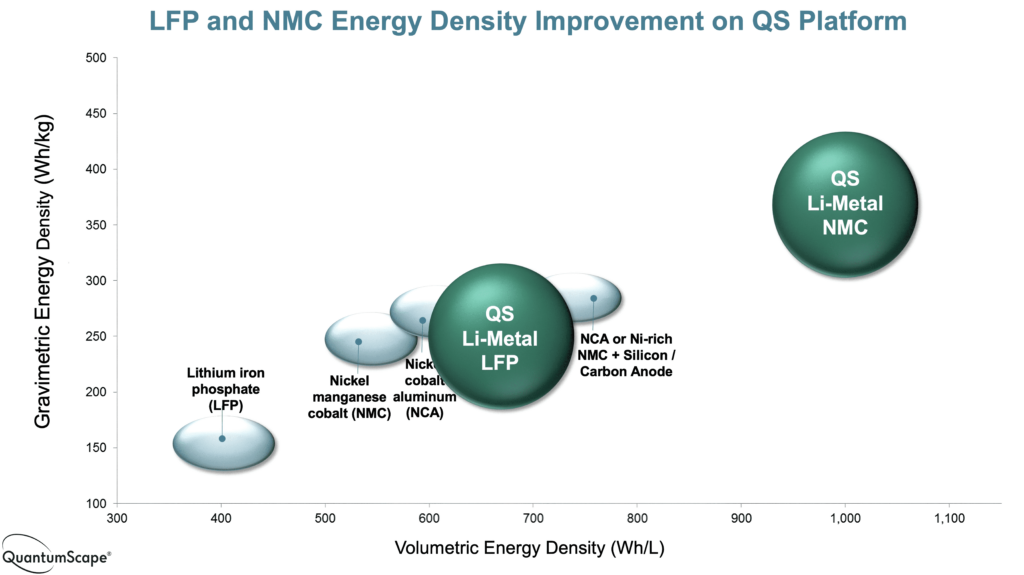
(Courtesy of QuantumScape)
This was achieved with a 40% reduction in cell resistance, which suppresses heat generation when a large current is applied. This comes from using a technique called electrospinning to produce a ‘skin-coated electrode’, where the surface of the electrode is coated with a nano-fibre membrane.
Electrospinning applies a high voltage to a polymer solution to spin yarn [zzz for the membrane ?]. The technology is suitable for the formation of an insulating layer for batteries, as it allows ions to move smoothly in an electrolyte solution while maintaining the inherent properties of the material, such as heat resistance and electrical insulation.
The ultra-thin insulating membrane reduces the distance between the cathode and anode, and its higher porosity and the ion conductivity reduces the internal electrical resistance. Reducing the thickness of the insulating layer also helps increase the battery capacity and improves both input/output power and capacity.
The reduced resistance allows water-cooling systems to be replaced by forced-air cooling, and for forced air cooling to be simplified to natural cooling. The lower resistance also reduces overvoltage, allowing the cell to function in a wider range of states of charge.
The 20 Ah-HP cell also achieves a longer life than the current 20 Ah cell by suppressing heat during continuous charging and discharging, owing to its lower internal resistance. Under test conditions, the cell maintained almost 100% capacity after 8000 charge-discharge cycles, while the capacity of the current 20 Ah cell fell by about 10%, even though it has a lifetime of 20,000 cycles. This compares to 500 cycles for silicon lithium cells, or 2000 cycles for more rugged lithium iron phosphate (LFP) cells.
Anodeless SSBs
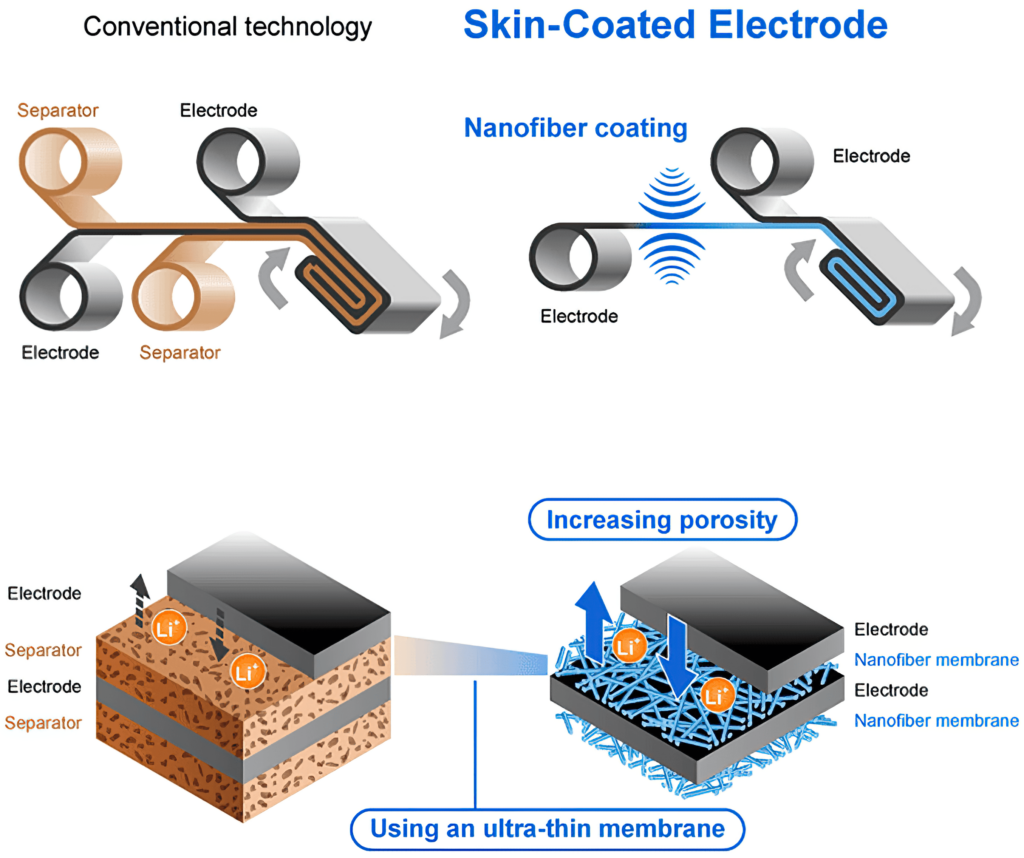
(Courtesy of Toshiba)
Another approach reaching production this year uses an ‘anodeless’ architecture and a proprietary solid ceramic separator that replaces the polymer separator used in conventional lithium-ion batteries. Replacing the separator enables the carbon or silicon anode used in lithium-ion batteries to be replaced with a lithium metal anode, which is more energy-dense than conventional anodes.
Some solid-state designs use excess lithium to form the anode, but in the ‘anode-free’ architecture the battery is manufactured anode-free in a discharged state, and the anode forms in situ on the first charge. This simplifies the manufacturing process, reducing cost, and allows for safer shipping as there is no charge in the cell.
The separator material has to have high conductivity, stability with the lithium metal, resistance to dendrite formation, and low interfacial impedance. The ceramic itself is non-combustible, making it safer than conventional polymer separators, which are hydrocarbons and so can burn. The structure of the ceramic separator is mostly proprietary, but avoiding rare earth elements and supporting a continuous-flow manufacturing process helps to keep manufacturing costs down.
This aims to provide an energy density of 1000 Wh/litre and a specific energy of 400 Wh/kg, which would boost the range of a vehicle by 50-90% with higher energy in a smaller battery pack.
Sulphide electrolytes
Using a sulphide-based solid electrolyte coupled with a silicon anode and a traditional NMC cathode means only one element needs to be changed in existing cell manufacturing. This has produced large-format 100 Ah pouch cells that will be in production in 2024, aiming for volume production of 800,000 cells a year by 2028.
Early versions of these cells, with a capacity of 2 Ah, have passed the standard nail penetration safety tests, and survive external short-circuits at 100% charge as well as overcharging to 200% of capacity, both of which cause traditional lithium-ion cells to fail.
The cells have a specific energy of 390 Wh/kg and an energy density of 930 Wh/litre with a silicon anode, rising to 440 Wh/kg at the same energy density with a lithium metal anode in cells in 2024. A third generation of cell is aiming for a specific energy of 560 Wh/kg for higher power performance in a larger cell at 785 Wh/litre with a new cathode material that doesn’t use nickel or cobalt, and will cost under $3/kWh, about 90% less than cathodes typically used in long-range vehicle battery packs now.
Another solid electrolyte material entering production is the Factorial Electrolyte System Technology. This has been used in a prototype 40 Ah cell that works at room temperature and can be a drop-in replacement for the liquid electrolyte in lithium-ion pouch cells to provide a boost in range of 20-50%.
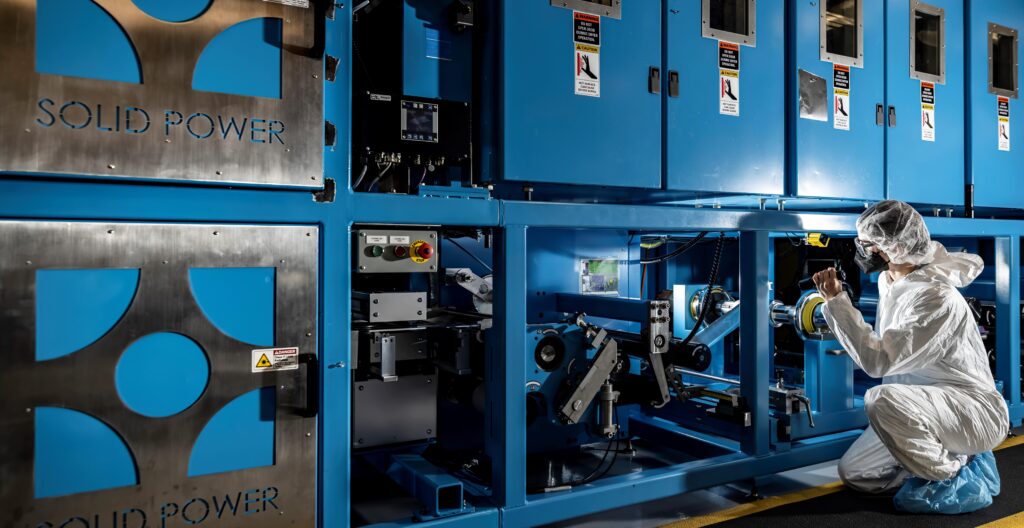
(Courtesy of SolidPower)
3D printing
Using a ceramic material for the electrolyte also opens up the use of additive manufacturing (AM) to produce-solid state batteries.
A microwave-controlled plasma production system called UniMelt is an AM process for high-volume production. Using temperatures of up to 6000 K, it can generate materials in as little as 2 seconds versus 2-3 days. It displaces costly and wasteful legacy manufacturing approaches with a less expensive production technology and a smaller footprint.
It can be used to create materials with a tight particle size distribution (PSD) for maximum energy density and engineered porosity for the electrolyte, as well as surface coatings for interfacial modification and passivation. The technique can be used for cathodes and anodes, including all NMC variants from 111 to 811 and beyond, NCA, LMO, high-voltage spinel, LTO, silicon anodes and other unique chemistries.
It is being used to develop products across NMC cathode, LFP, silicon-dominant anode, lithium, solid-state ceramic electrolytes and recycled cathode materials. One of these materials is lithium lanthanum zirconium oxide, which is under investigation for solid-state electrolytes.
The plasma approach has significant advantages. For instance, if a conventional 16 GWh battery cathode production plant was converted to the UniMelt platform, it would reduce CO2 emissions by 70%, lower water consumption by 90% from 6.3 million barrels a year and cut wastewater production of 7 million barrels a year entirely while requiring a factory that is half the size of existing facilities.
3D-printing machines have also been developed to print layers of different materials for solid-state batteries. This can use half the amount of materials, doubling the energy density of a cell, and allows the cells to be produced close to where the vehicles are being built, rather than in distant gigafactories
However, that has required the development of both new solid-state battery materials and the equipment for the AM process. The process is a combination of powder bed and jetted material deposition, and uses materials such as ceramic electrolyte and metal electrodes with a proprietary support material called PoraLyte. It avoids the limitations of overhanging parts of different layers and enables faster creation of devices with internal channels and cavities, and can even include active components such as sensors inside the battery.
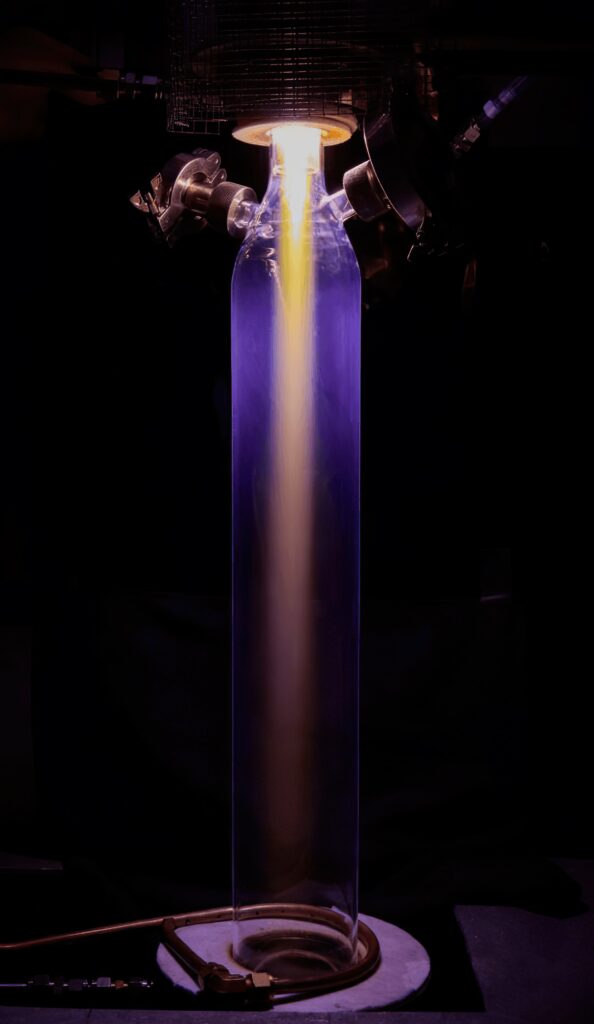
(Courtesy of 6K)
Using a powder process also makes it easier to recycle the ceramics and metals by conventional methods.
There are two generations of solid-state batteries using this production technique. The first is similar to today’s pouch cells that use the materials in existing plants, and will enable cells with a capacity of 600 Wh/litre with 400 charging cycles. This comes from using 30 layers in the cell to boost the capacity from 2.3 mAh to 3 Ah. This compares to 5 Ah for the solid-state SCIB cells in production and 20 Ah now starting to ship.
The first-generation batteries are being used initially for two -and three-seater EVs. A pilot plant with a capacity of 2.5 MWh a year is due to start production by the end of this year.
The second generation is built using the AM process. It will have an energy density of 1200 Wh/litre and a life cycle of several thousand cycles with 100% depth of discharge, rather than having to remain between 80% and 20% charge which is necessary for current cells. This will add 40% to the range of a battery pack.
The second generation requires specialist 3D printers and some other ancillary equipment, but the big advantage is it needs 30-40% less capital equipment and fewer processing steps than existing processes.
A single AM machine can produce the equivalent of 180,000 1860 cells per month, so 30 to 40 machines would be the equivalent of a factory producing 1 GWh of cells a year.
Using 3D printing also allows solid-state batteries to be produced in different, conformal shapes that are part of a vehicle’s structure. The cells do not need a mechanical casing and can be sealed with a 50-micron layer of electrolyte around the outside, giving the cell a much higher ratio of active material than other approaches, again boosting the capacity.
A third generation is being developed with a high-voltage cathode at 9 V rather than 4.2 V. This would give four times the energy density, potentially 2400 Wh/litre. It will be sampling by the end of 2023, with production due in 2024.
Aqueous electrolytes
Traditional lithium-ion technologies are still developing, and could well impact on advances in SSBs. One particular development is aqueous electrolytes, which boost the energy density of lithium-ion cells without needing to use nickel or cobalt in their electrodes.
As these electrolytes are water-based, they reduce the risk of fire in the event of a short-circuit, and can operate at temperatures below -50 C – a key advantage over existing lithium-ion packs.
One aqueous electrolyte is being combined with other advances in cathode design to give 60% more performance, and with a silicon anode to increase that further. However, this also faces the same challenges as SSBs in fitting into the production process for volume e-mobility applications.
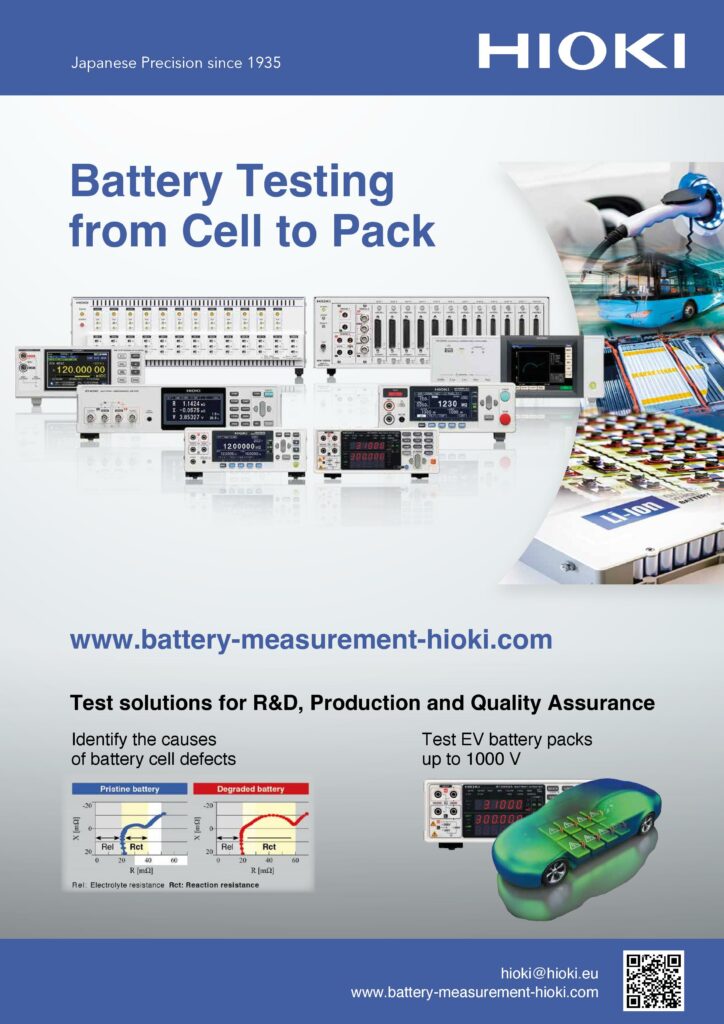
Conclusion
SSBs are driving a huge amount of innovation in e-mobility. New materials, new structures and new processes are all emerging that can deliver dramatically higher levels of energy density and power while being much safer than lithium-ion cells. The challenges of bringing these technologies to market for engineers to use though are also significant.
The interim step of ‘semi-solid’ electrolytes that can be added to existing manufacturing lines will boost the performance of battery packs by 10-20% for the next generation of high-end vehicles. It is however the prospect of new, more efficient manufacturing techniques enabled by the new materials that could prompt a dramatic change in the way battery packs are designed and manufactured. This will have a knock-on effect on the overall design of electric platforms on the ground as well as in the air.
Acknowledgements
The author would like to thank Dr Scott Brown at Nexeon, Moshiel Biton at Addionics, Professor Taro Hitosugi at the Tokyo Institute of Technology and Nad Karim at Sakuu for their help with researching this article.
Battery design tool
A new software tool can speed up the design of energy-dense solid-state batteries (SSBs) that use lithium metal anodes.
The Solid-State Battery Performance Analyser and Calculator (SolidPAC) takes a user input to analyse factors such as materials chemistry, thickness and electron flows, feeding back design specifications and an energy density estimate
The tool is based on the LabVIew software from NI but has been released as a standalone application compatible with a Windows platform
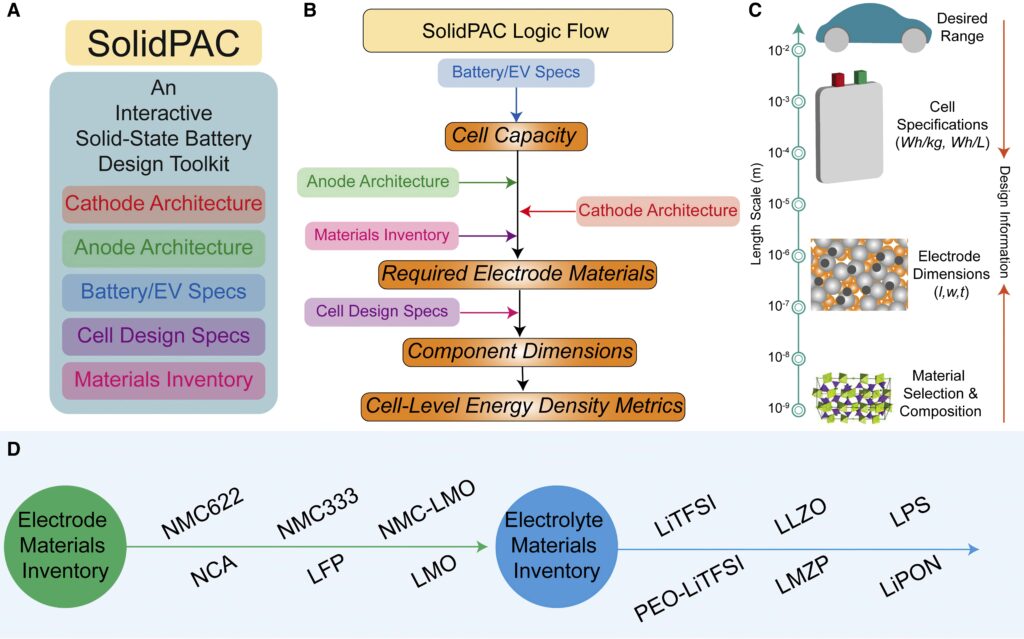
(Courtesy of Oak Ridge National Laboratory)
Key technological improvements rely on the integration of high-voltage and high-capacity cathodes, solid electrolytes and metallic lithium.
Current research on SSBs is focused primarily on understanding and evaluating cell chemistries. However, it is extremely important to appraise the overall impact of materials selection, electrode balances and the processing and integration practices used on the cell’s energy density.
SolidPAC provides estimates of cell-level energy densities based on chemical composition, component configuration and processing parameter inputs by users. It also provides an avenue to carry out ‘inverse design’ to engineer electrode thicknesses and loadings to meet energy density goals.
Cell-level capacity is estimated from the user inputs for pack range/energy/power and pack/module/cell configurations. These calculations are carried forward from the analogous BatPac developed for conventional lithium-ion batteries.
Combining cell-level capacity with anode and cathode architecture information provided by the user, along with material information made available in the inventory, are used to estimate the materials required to fabricate the cells. The component dimensions and the cell-level energy density calculations are then performed using the input cell design parameters.
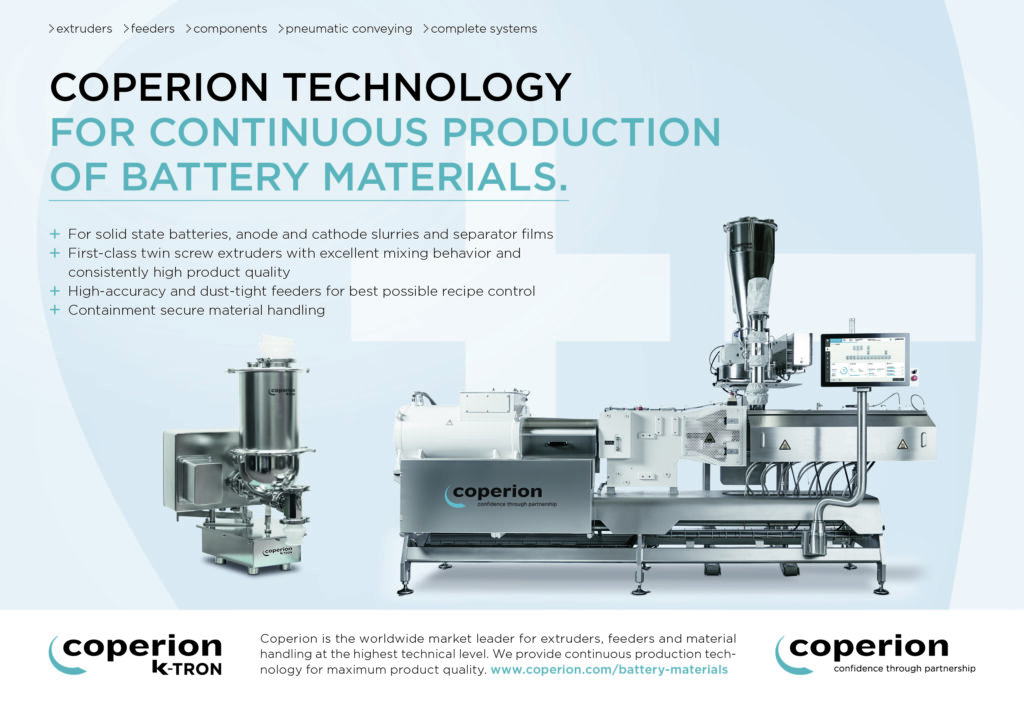
Some suppliers of solid-state batteries
China
BYD +86 755 8988 8888 www.byd.com
CATL +86 593 258 3668 www.catl.com
WeLion +86 108 032 6626 www.solidstatelion.com
Israel
Addionics – www.addionics.com
StoreDot +972 3 509 7710 www.storedot.com
Japan
EnVision AESC – www.envision-aesc.com
GS Yuasa International +81 3 5402 5717 www.gs-yuasa.com
Hitachi Chemical +81 3 5381 2370 hitachi-chem.lookchem.com
Panasonic +81 6 6908 1121 www.panasonic.com
Toshiba +81 3 3457 4511 www.global.toshiba
Korea
LG Chem +82 2 3773 1114 www.lgchem.com
Samsung SDI +82 3 1800 63098 www.samsungsdi.com
SK Innovation +82 2 2121 5114 eng.skinnovation.com
Switzerland
Blackstone Resources +41 41 449 61 63 www.blackstoneresources.ch
Taiwan
Prologium Technology – www.prologium.com
UK
Ilika +44 23 8011 1400 www.ilia.com
Johnson Matthey +44 20 7957 4120 www.matthey.com
LiNa Energy +44 1524 748099 www.lina.energy
Nexeon +44 1235 436320 www.nexeon.co.uk
USA
6K + 1 978 258 1645 www.6kinc.com
24M Technologies +1 617 553 1012 www.24-m.com
Factorial Energy +1 617 315 9733 www.factorialenergy.com
Prieto Battery +1 970 492 4195 www.prietobattery.com
Quantumscape +1 408 452 2000 www.quantumscape.com
Sakuu +1 888 376 5387 www.sakuu.com
SolidPower Battery +1 720 300 8167 www.solidpowerbattery.com
ONLINE PARTNERS
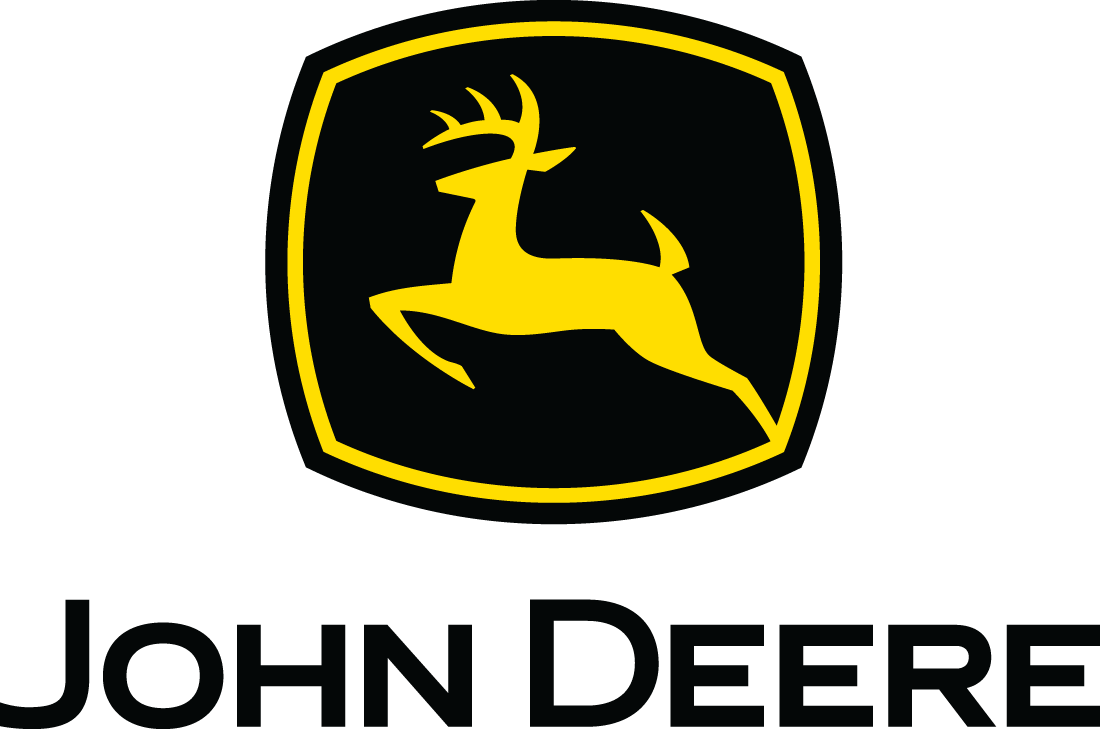
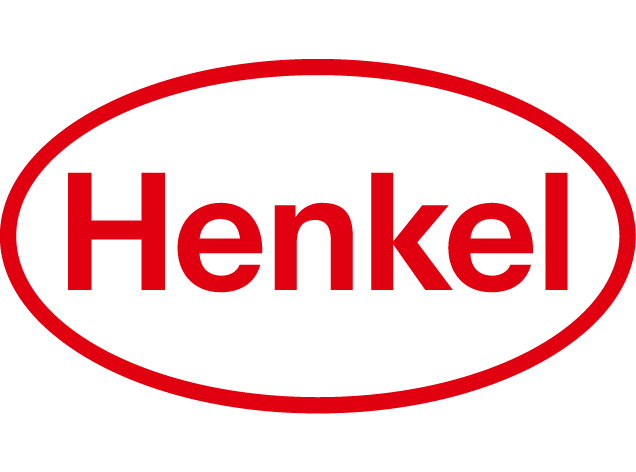
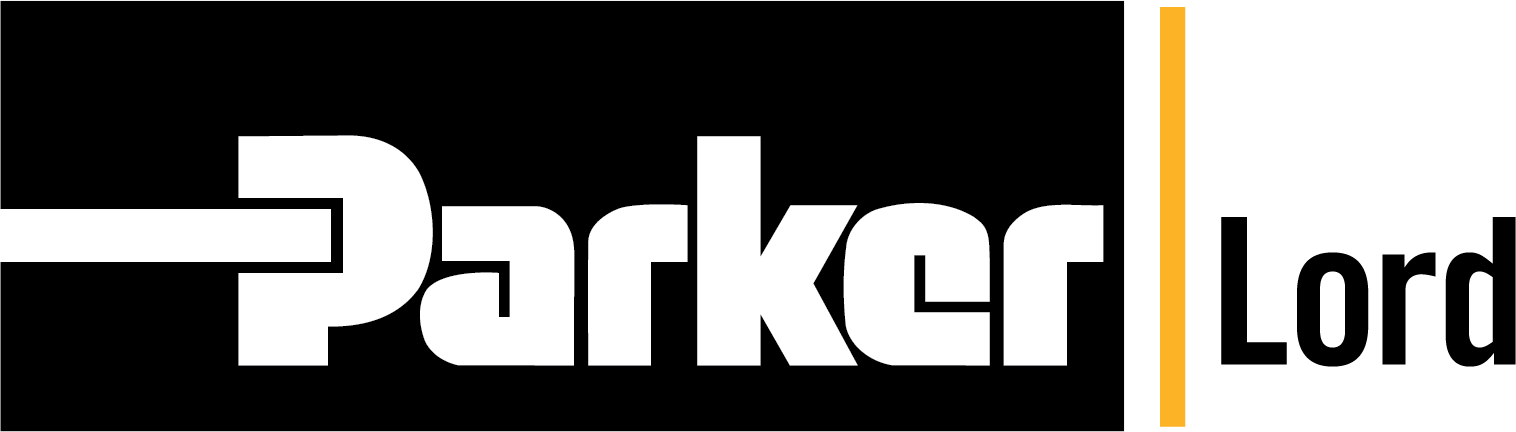
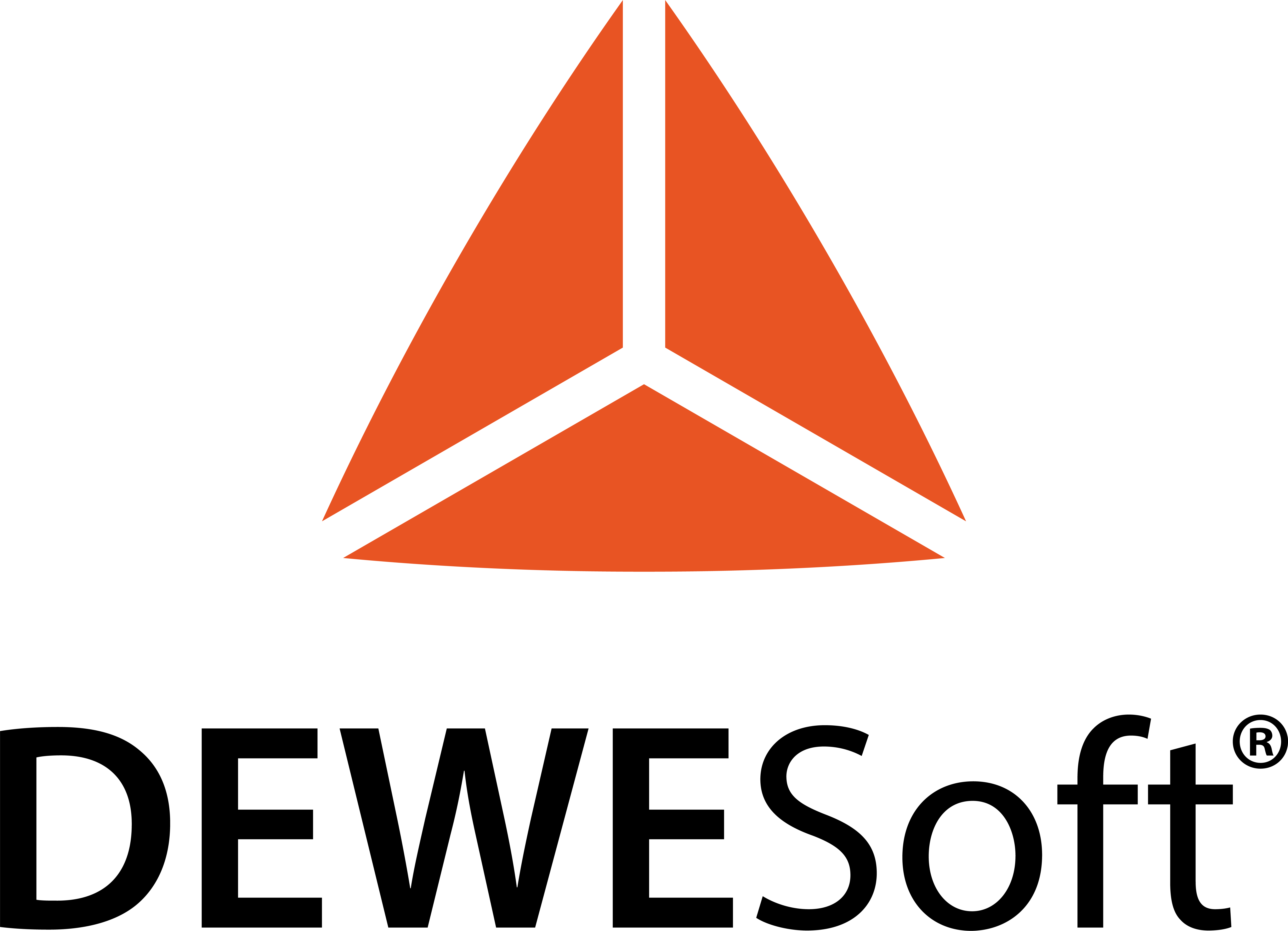
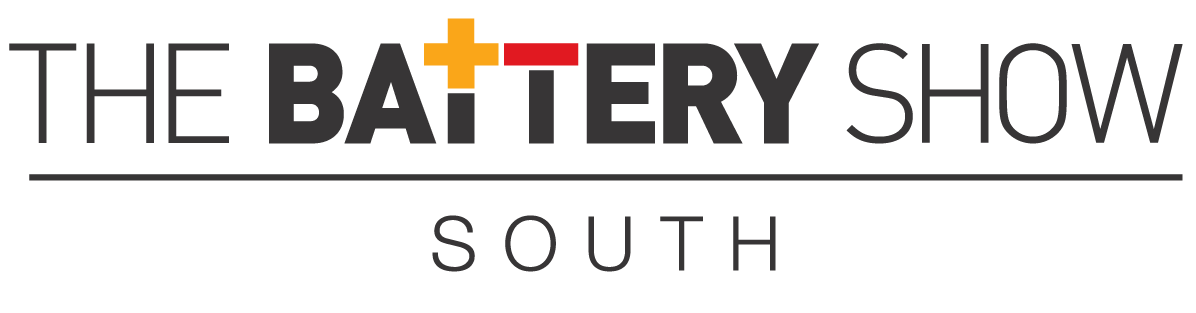
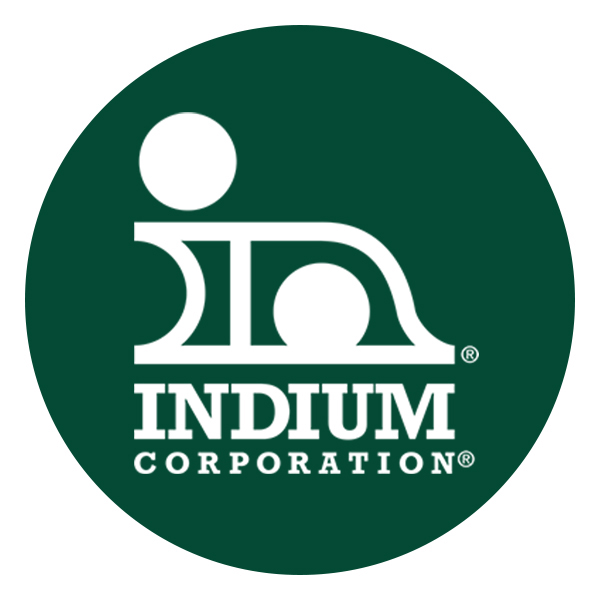
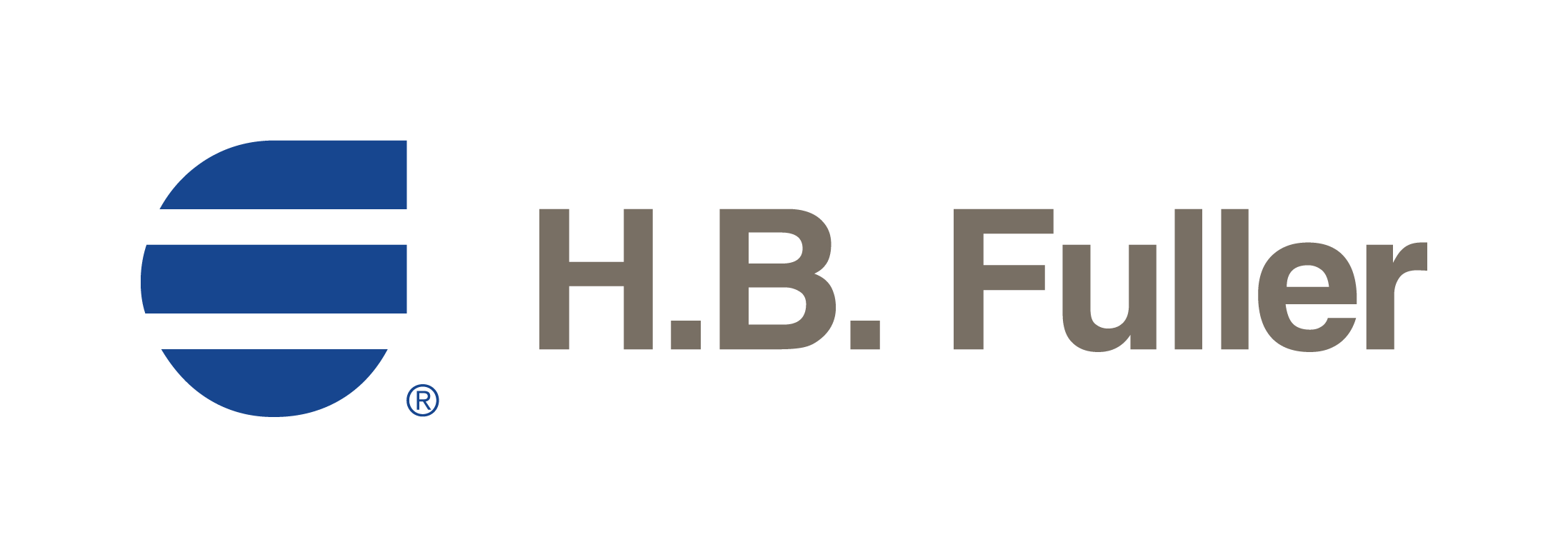