Solar power
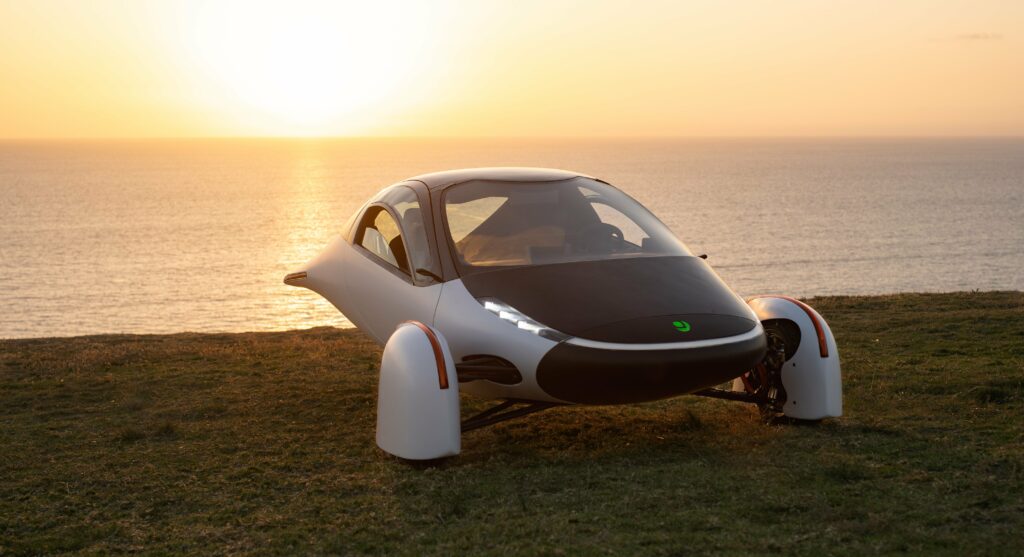
(Courtesy of Aptera Motors)
Light at the end of the tunnel
Solar cell technology is near the point of becoming mainstream in EVs, but some obstacles to their use still need to be overcome. Peter Donaldson reports
According to the NASA Earth Observatory, an average of 340 W/m2 of solar power reaches the Earth. Over an hour that would be 340 Wh/m2 in energy terms, although it varies significantly throughout the day, with latitude and with the seasons. Until fairly recently, tapping into this abundant source of clean energy to provide motive power for vehicles has seemed far removed from anything mainstream. That is no longer the case though, thanks to improvements in photovoltaic (PV) cell technology in areas including energy conversion efficiency, cost, lifespan and ease of integration into vehicle structures.
So significant has the progress in vehicle-integrated PV (VIPV) technology been that leading technology analysis and forecasting organisation IDTechEx announced at the end of 2019 that solar-powered vehicles had reached a tipping point.
The primary indication of this tipping point is the availability of single-crystal silicon photovoltaic cells that provide 50% more power per unit area than older technology, and at a cost low enough to make them viable even on the sides of vehicles. Another indication is the emergence of vehicles being offered to the public that can rely on sunlight as their primary source of energy for short journeys.
The start-up manufacturer of one such vehicle, who helped with the research for this article, emphasises the importance of efficient vehicle design. The company is developing a two-seat, three-wheeled solar car that might never need to visit a charging station, depending on the amount of sunlight available and the daily mileage requirement.
With a combination of a drag coefficient of only 0.13, a claimed weight of 65% less than typical contemporary EVs and minimal rolling resistance thanks to its three-wheeled configuration, the car offers a range of 40 miles a day on only the 700 W of power available from its solar panels. With a fully charged battery, the vehicle has a claimed range of 1000 miles.
We also consulted a major Korean vehicle manufacturer and a solar power technology specialist to gauge the state of the art in solar EVs and the engineering challenges still facing the industry.
Solar principles
PV cells are made from semiconducting materials that absorb photons and in the process raise the energy state of the material’s electrons so that they can flow as an electric current when connected in a circuit. This is the photovoltaic effect. The usefulness of any semiconductor as a PV device is strongly affected by three fundamental characteristics – quantum efficiency, spectral response and band gap.
Quantum efficiency is expressed as the ratio between the number of electrons the cell puts out as current and the number of photons that strike the surface of the device. This is usually qualified by specifying the wavelengths of the incident light.
Spectral response is a closely related measure expressed as the ratio of the current generated by the solar cell to the power of the light that falls on the solar cell. In spectral response diagrams, the number in Amps per Watt is plotted against the wavelength of the light, as different materials are sensitive to different wavelengths.
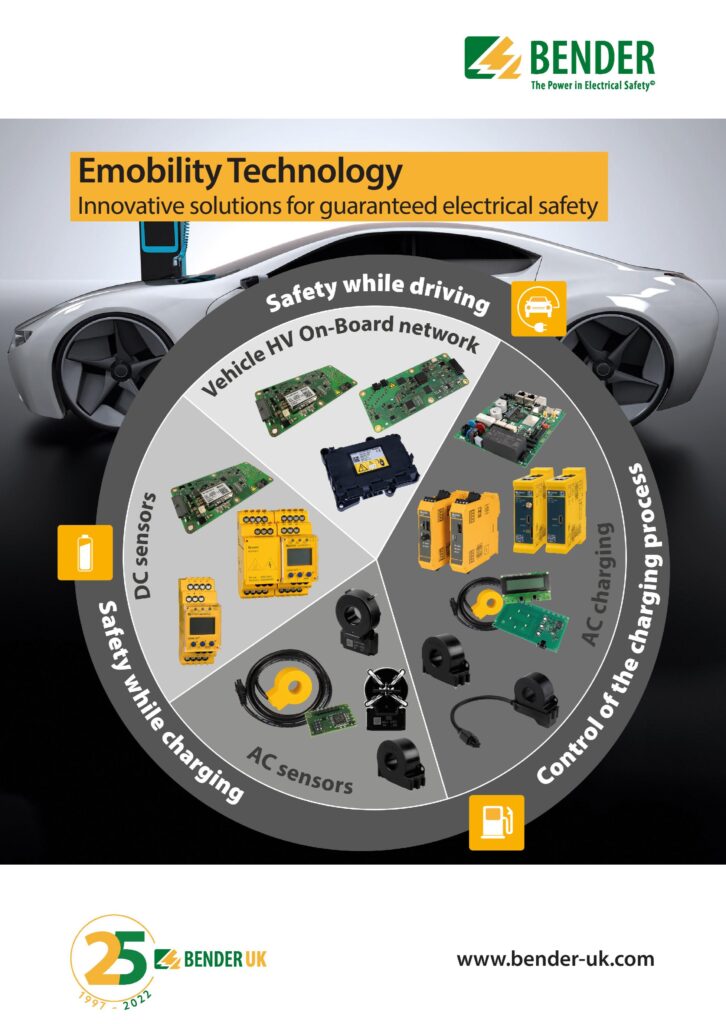
Every semiconductor has a band gap, which is the difference in energy (expressed in electron-volts) between the top of the valence band, in which an atom’s electrons take part in chemical reactions with other atoms, and the bottom of the conduction band, in which electrons have enough energy to move freely through the bulk material. Photons with energies lower than the band gap are not absorbed.
A typical PV cell is a multi-layered sandwich consisting of a negative front contact, a light-sensitive n-type semiconductor layer with an excess of negative charges (electrons), a p-n junction region, a p-type semiconductor with an excess of positive charges (‘holes’), and a positive back-contact. There are many variations on this generic scheme.
Most PV cells are made from relatively inexpensive, moderately performing polycrystalline silicon. Its performance is limited by boundaries between the crystals that constitute flaws in the surface of the cell, which reduce its efficiency.
Single-crystal silicon performs better but costs more because of the slower manufacturing process needed to create the ordered crystal structure in which each silicon atom is bonded to four neighbouring atoms, which enables predictable and uniform behaviour. Some single-crystal silicon PV cells can be formed into flexible panels.
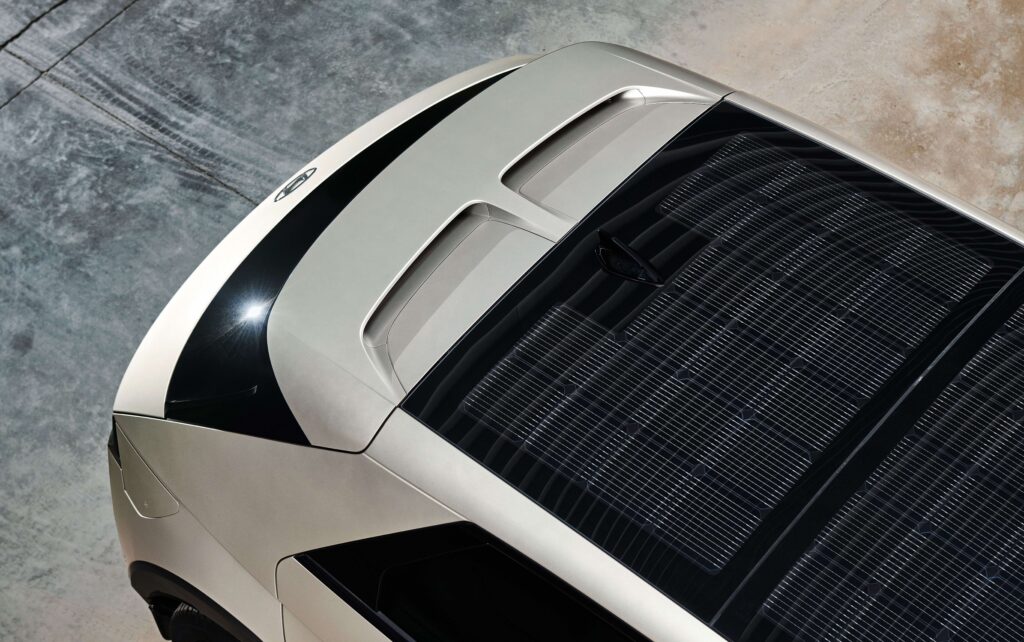
(Courtesy of Hyundai)
Promising perovskites
Solar cells based on perovskite materials have demonstrated even higher efficiencies than single-crystal silicon cells, and have low production costs, but at the moment they suffer from problems including a relatively short life.
Perovskite is the mineral compound calcium titanate (CaTiO3), which has a specific crystal structure, while perovskites are a family of materials named after it because they have the same type of crystal structure. That structure can hold a wide variety of positively charged cations of different elements, allowing the development of engineered materials that can be tuned to respond to different wavelengths of light.
This makes them suitable for use in tandem device architectures. Perovskite on silicon, for example, is attracting a lot of interest thanks to overall conversion efficiencies of around 30% demonstrated so far.
CIGS and organics
Other options include cells based on copper indium gallium di-selenide (CIGS), which is already in use on building facades and roofs, particularly in Japan. Barriers to its use in vehicles though include its relatively fragility, the small amounts of toxic cadmium in most formulations and the use of a heavy stainless steel substrate, the elimination of which are subjects of ongoing r&d.
Organic photovoltaics represent another option, and are based on conductive polymers and small organic molecules that contain carbon-hydrogen bonds. As they can be processed as solutions, they are relatively inexpensive, although their efficiencies of up to 18% or so are relatively low. However, their improving durability and flexibility allows them to be tightly rolled, a quality that makes them attractive for deployable solar covers that can charge a vehicle while parked, for example.
Trickle-down from satellites
The final group of PV materials of potential importance to EVs are based on semiconductor compounds made from elements from groups III and V of the Periodic Table (according to the old IUPAC grouping), including gallium, indium (group III), arsenic and antimony (group V). These are high-performance, high-cost materials used mostly in satellite solar panels and a divided into two broad groups based on the number of p-n junctions in a cell.
For example, III-V single-junction cells made from gallium arsenide are improving to the point at which their conversion efficiency is getting to within a few percentage points of the Shockley-Queisser theoretical limit for a single-junction solar cell of 33.7%, and they can be made in flexible form. GaAs solar cells have come down in price to the point where they are reportedly taking over from single-crystal silicon in large, high-altitude unmanned airships used as pseudo-satellites intended to remain aloft for 5 years or more.
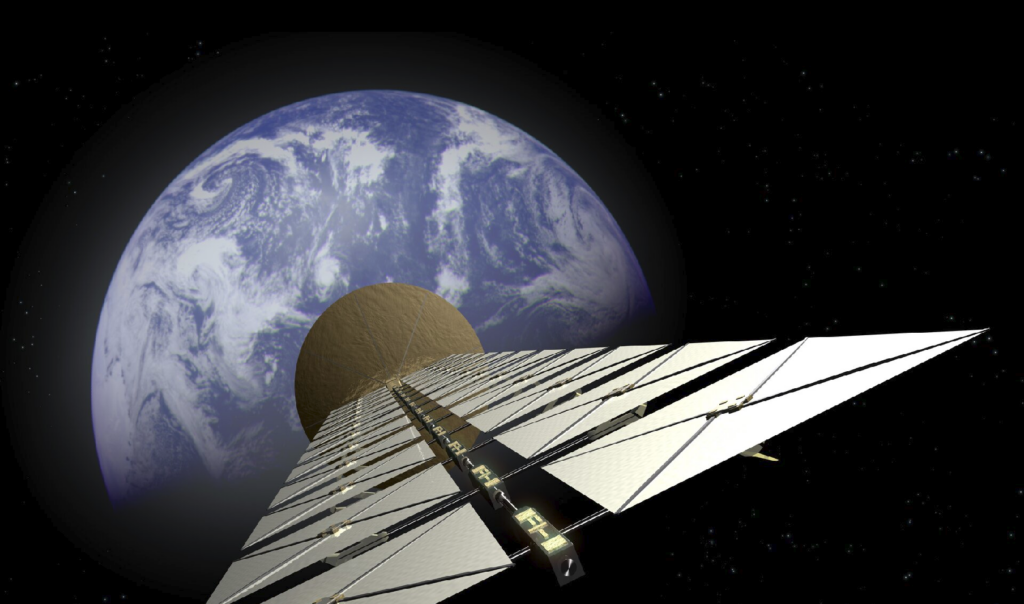
(Courtesy of ESA)
Even higher performance is achieved by III-V multi-junction cells, which make more use of the solar spectrum because they are formed from multiple optically and electrically coupled sub-cells with different energy band gaps. Their efficiency is reportedly improving by around 1% in absolute terms a year, and is approaching its own theoretical limit of 50%.
The IDTechEx report, entitled “Solar Vehicles 2021-2041 Second Edition”, says both III-V technologies would have to come down in cost by 90 to 99% before their use in EVs can be justified. Nonetheless, a major Japanese manufacturer has been testing an experimental triple-junction compound solar cell module rated at 860 W and around 34% efficiency on a battery EV demonstrator.
Remaining hurdles
Despite recent advances, there are still barriers to be overcome before solar photovoltaics will be standard equipment on most or all EVs, cars in particular.
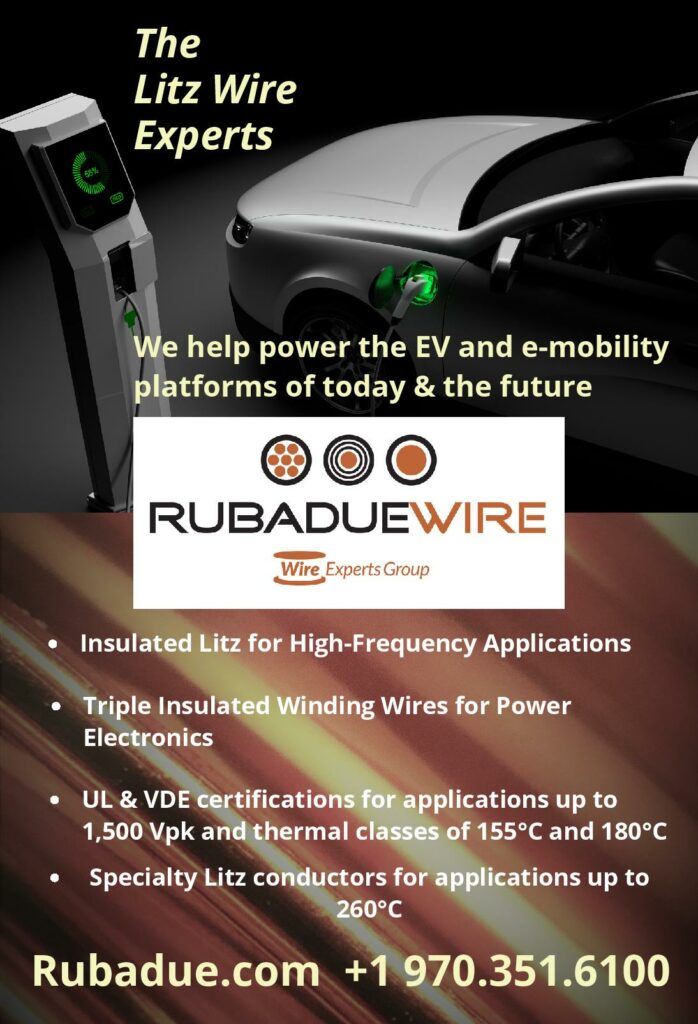
Probably the biggest technical challenge will be in manufacturing, according to one solar PV technology company we consulted in connection with this article. Moulding or integrating the PV laminate into the bodywork, which is often curved or sculpted in a form in a way that allows for customised mass production, will be difficult. There will be other challenges in aesthetics, particularly in balancing colour with power output requirements, the company says.
The engineer who leads the European advanced electrification team for a major Korean vehicle manufacturer, which offers a solar roof as an option on its latest fully electric mid-size crossover utility vehicle (CUV), believes solar power will be mandatory for road vehicles in future. The automotive industry is facing increasingly stringent CO2 regulations, with which vehicle OEMs find it tough to comply.
“We see two ways to meet them,” he says. “The first is to save energy with very efficient electrification, the second is to generate energy in the vehicle itself. Our vision is to develop solar systems for all our road vehicles in the future.”
He emphasises that solar PV panels allow for a significant reduction in the battery EV’s reliance on the charging infrastructure, which will also help popularise the technology. “If we can reduce the number of visits to charging station from one a week to one every 4 weeks, that would be a major benefit.”
He points out that most solar panels made these days are used on buildings or powerplants, and are flat and rectangular. “That’s great for maximising surface area, but it isn’t what’s needed in vehicles, so there are two main considerations,” he says. “The first is packaging; we need curvature in the panels themselves, even multi-directional curvature. They must be laminated on the outside of vehicles, and they are not easy shapes.
“The second consideration is the need to increase efficiency at a lower cost. We have a very small surface on the vehicles, so we need very efficient solar cells.”
The CUV’s solar roof uses state-of-the-art solar cells from an external supplier that have an efficiency of greater than 24%. “That’s a good value for the moment, and we are quite happy with it, but for the future we are considering developing our own solar cell technology.”
PV materials for the road
For road vehicles, high-efficiency crystalline silicon VIPV is showing real promise in passenger cars in particular, while flexible crystalline silicon or thin-film PV is better suited to the surfaces of trucks or vans, the solar technology expert adds. Similarly, crystalline silicon VIPV works well on off-highway vehicles with curved, irregular surfaces.
For ships and boats, flexible PV panels are increasingly applied to decks and cabin roofs, with semi-transparent PV materials on windows, and bi-facial panels on railings and balconies, while crystalline silicon integrated photovoltaics are well-suited to aircraft use.
While polycrystalline silicon photovoltaic materials have dominated the solar market for many years, they are rapidly being phased out and are therefore not likely to be significant for use in EVs in future. Their place is being taken by single-crystal silicon because of its high power density, the expert notes.
Our automotive electrification engineer concurs, emphasising its conversion efficiency of 24% along with its affordability as the factors that make it the most immediately promising technology for vehicles, and this is the technology it has integrated into the CUV’s roof.
The dedicated solar vehicle has body panels incorporating more than 180 single-crystal silicon cells, its manufacturer says. “We’ve chosen powder crystalline cells instead of flake cells, as that allows us to mould them to the organic compound curving surfaces of our vehicle. It also gives our cells greater resistance to impact and cracking.” A compound curved surface is one that curves in two or more opposing directions, so it cannot be opened out flat.
“We hope to upgrade our solar technology to more than 30% efficiency, from 24% at the moment, in the next few years.”
Of the other major PV technologies that could be considered for EV applications, some are very promising but require further development to be practical, and some are in service in applications with greater tolerance of high costs than the automotive industry.
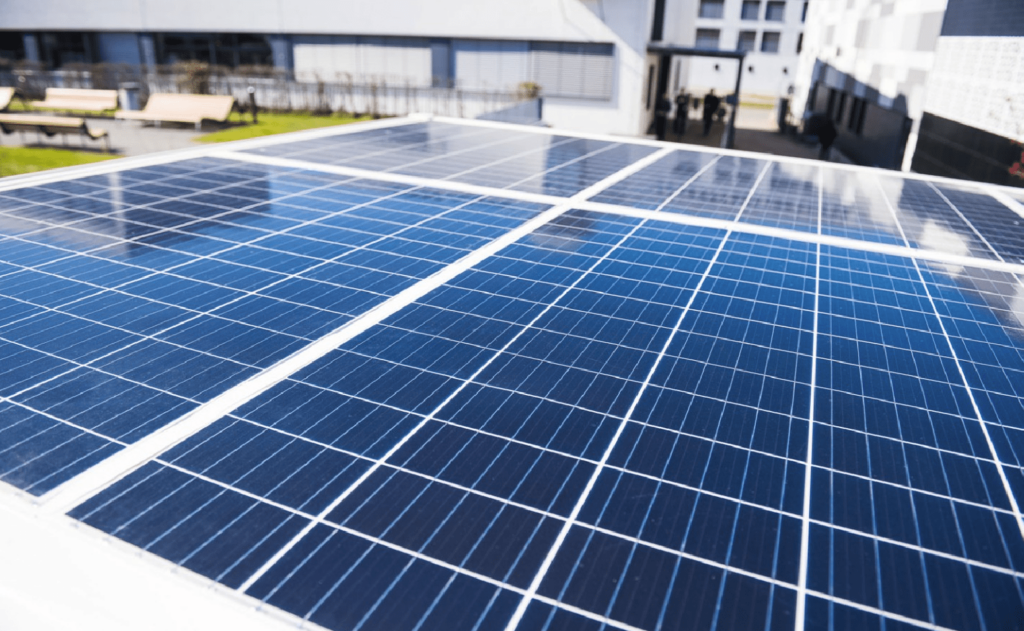
(Courtesy of Fraunhofer Institute)
Tandem attractions
Perovskites, for example, are not yet mature and need to overcome problems with efficiency and durability, although their use in combination with silicon in perovskite-on-silicon tandem configurations is anticipated as the next generation to replace single-crystal silicon, our solar technology expert says.
The electrification engineer agrees, noting that the OEM is considering using them in the near future, partly because improvements in the efficiency of single-crystal silicon cells have slowed down. “We used to see increases of 0.6% a year, but now we see saturation on the horizon and we think efficiency will max out at 29%.
“We think perovskite on silicon is currently the most promising replacement, and many solar cell suppliers are already working on the technology, which could eventually get us to more than 30% efficiency.”
“Other combinations are also possible, but they fail from the cost perspective,” he says. “The perovskite-on-silicon tandem is different because both the materials are inexpensive, and because of the intensive r&d on them we expect to see them in the field within 3 to 5 years.”
III-V sooner than expected
However, Germany’s prestigious Fraunhofer Institute is using III-V semiconductor technology in VIPV applications it is developing that can be moulded into complex curves for passenger cars. These cells, says the organisation, achieve efficiencies of over 35 %.
The panels are formed from cells that overlap at their edges, in the same way as roof shingles. The shingles can be configured flexibly with filigree metallisation and cell interconnections.
Connections between the shingles can be achieved with electrically conductive adhesives (ECAs), which connect the rear busbar of one cell to the front busbar of its neighbour. Shingling improves power density by increasing the active cell area in the module and by reducing losses from shading and resistance in conventional electrical interconnections. In turn, this enables the creation of PV modules with the highest efficiency levels, curved surfaces and nearly invisible circuitry, says the institute.
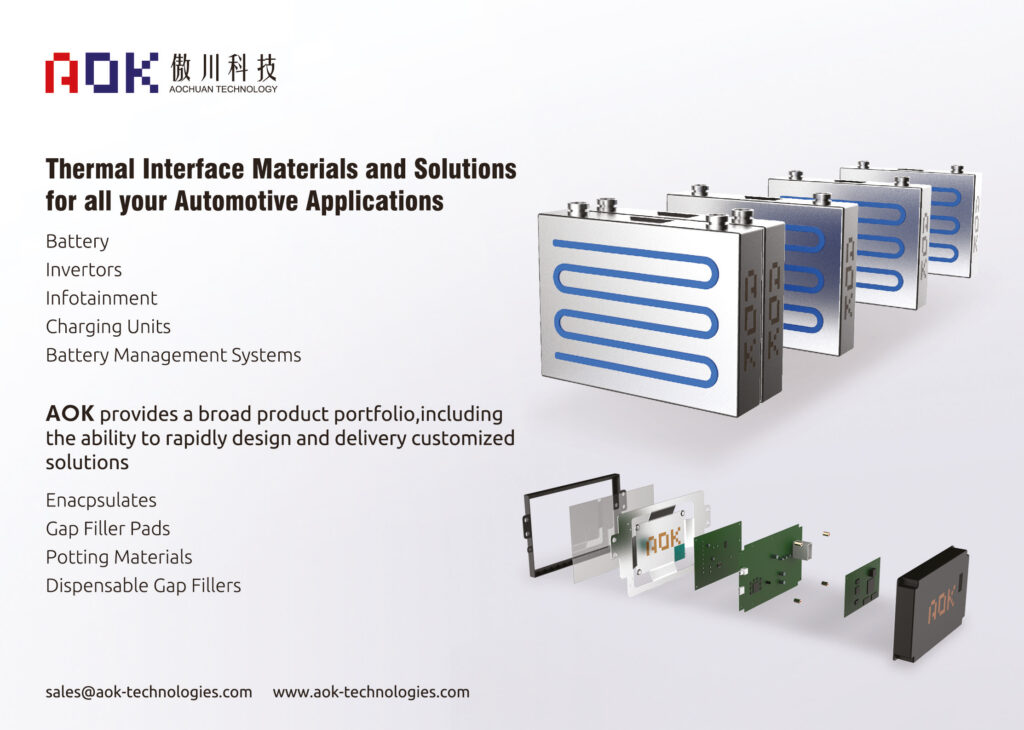
Interconnections using an ECA need joints from each aluminium finger contact to the silver busbar, to the ECA, to the busbar of the next cell and then to its corresponding silver finger, so the complete interconnection consists of multiple layers. Fraunhofer has therefore come up with a simpler, more efficient and potentially cheaper cell interconnect method with lower resistance based on laser-welded aluminium foil.
Range contribution
While there are several ways to gauge the contribution that solar power will make to EVs, additional range is a natural one given the industry’s focus on reducing range anxiety among potential customers for passenger cars in particular. Our solar power systems expert reckons that current solar PV technology can extend a typical car’s range by 15-20 km per day or 5000-7000 km a year, and for lighter vehicles the increase could be up to 50 km per day under ideal conditions.
With the expected improvements to photovoltaics’ efficiency in converting sunlight to electrical power, along with weight reduction and further efficiency increases from EV powertrains, our expert believes a bold estimate for the mid to long term is that integrated photovoltaics can be expected to cover about 20% of a typical EV’s energy consumption.
Our vehicle maker’s solar roof produces a peak power of 205 W and serves as a good measure of what can be expected from solar power on a representative mainstream EV. Depending on where in Europe it is operating, the engineer says, it can be expected to provide enough energy to drive maximum distances between 1500 and 2100 km per year. He says the average customer in Europe covers around 15,000 km annually, so energy from the roof could cover 10-14% of that now.
“We think we can increase this to 4000 km in the near future, which will then be about 25% of the total annual range for the average customer,” he says. “Further in the future, I think even 10,000 km a year is possible with the new technologies.”
The ‘never charge’ technology built into the solar vehicle’s composite structure is designed to harvest enough sunlight to travel about 11,000 miles (more than 17,700 km) a year in sunny climates, which is more than most of its drivers would need, says the manufacturer.
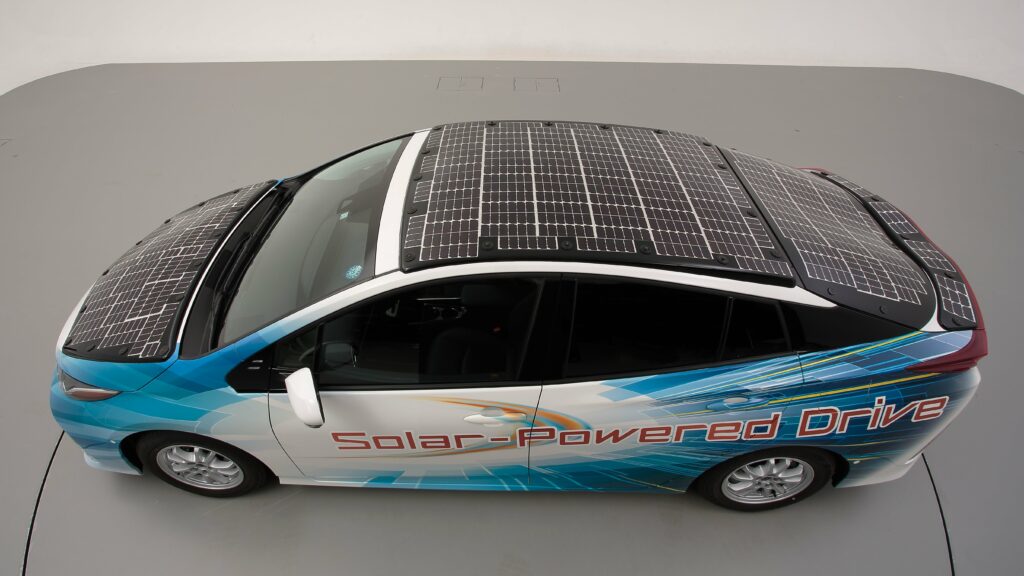
(Courtesy of Toyota)
Solar from the start
EVs that have been designed as EVs from scratch work much better, other things being equal, than those that are essentially modified IC engine vehicles or have been designed to share a platform with one in a mixed range, and the same is true of solar power, our expert says.
“The power generation functionality of the bodywork has an impact on many aspects of the car, its weight, design, cost, battery capacity and so on,” he says. “So, to gain maximum leverage from the photovoltaics’ contribution, it should be incorporated into the design process from the beginning.”
The developer of the dedicated solar three-wheeler agrees, emphasising that tit is building custom panels shaped to meet the vehicle’s aerodynamic requirements. “It is necessary to create the body and its solar integration together so as not to add drag and increase battery drain,” it says.
“The solar roof is only the beginning of this technology, and is only an option at the moment in our vehicle,” the electrification engineer says. “As more solar is integrated into the design, we can get much more from the system. For example, we can enlarge the areas where the light comes in perpendicular to the surface to generate more power. We can also tailor the battery and the conversion system, because solar panels can generate power all the time, not just when the car is being driven.”
Integrating panels
VIPV panels naturally have to meet more than just electrical power needs, even if they are optional. The Korean vehicle OEM’s solar roof is an example of this, as it carries structural loads in addition to generating power and is therefore a safety-critical component that presented challenges in terms of safety, durability, weight and weight distribution, our electrification engineer notes.
In the realm of safety, the vehicle had to pass a rollover test with the electric roof. That was a tall order, but the solution was to mount the solar panels within an internal steel frame, which provided the required protection for occupants and even allowed the panel itself to survive functionally intact.
One price paid for this is in extra mass, as the solar roof adds 20 kg to the vehicle, and adds it at the highest point in the structure, which is never favourable for mass and weight distribution. However, the battery pack in the floor is the heaviest component, so the roof does not affect the overall mass distribution very much. At 30 kg in total, the solar roof weighs no more than a panoramic sunroof.
Durability is another issue on which the company had to place a lot of attention, as the semiconductors used in solar panels are very brittle. “Vehicle vibration caused a lot of microcracking during testing, but we solved that using our own specially designed structures,” he says.
The option of simply adding a solar panel to an existing roof was not considered for the CUV. The engineer notes that while such an option would have the advantage of being quick to market, it would not fit the vehicle as well, as each different vehicle design would require its own add-on panel. “More important, an add-on panel can charge the auxiliary battery but not the main battery to increase range, because a dedicated control system is needed to do so and it is only possible in an integrated solution.”
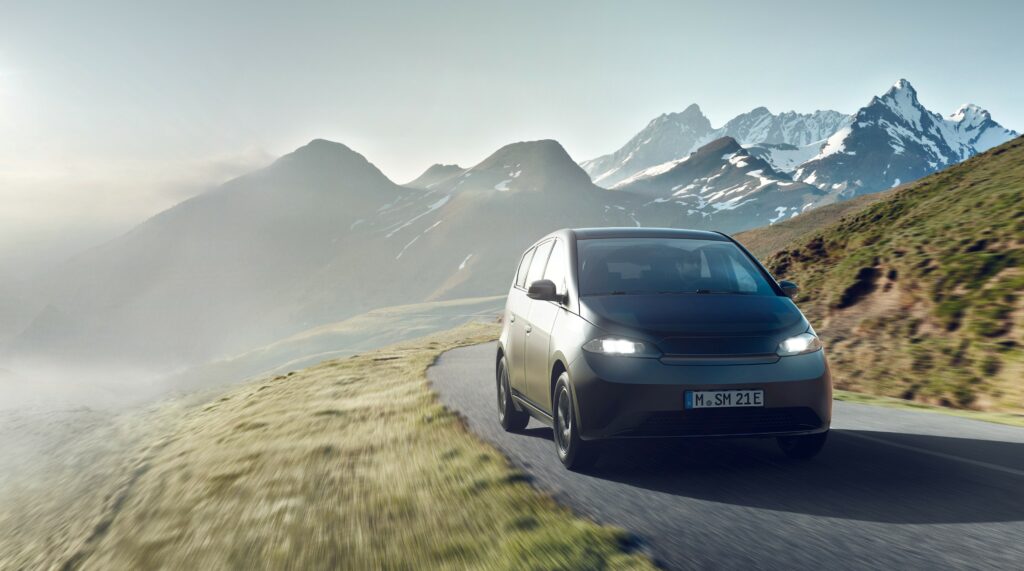
(Courtesy of Sono Motors)
Compared with add-on panels, VIPV will provide larger surface coverage, allow better aerodynamics and, subjectively speaking, have superior aesthetics, he adds. However, VIPV bodywork will come at a higher cost, primarily because of the need for custom photovoltaic elements; it is also less suited to retrofitting and more expensive to replace in the event of damage.
The integration task itself presents a number of challenges, according to our expert, including fulfilling the structural, aesthetic and light-gathering requirements of the panel at the same time along with safety, power optimisation and electrical design – all in a product that can be manufactured economically at scale.
The complexity of that task makes it tough to arrive at an acceptable cost per unit area for what (compared with normal PV production standards) are relatively small numbers of highly customised products formed into complex shapes. Here, the use of new materials that can conform to bodywork contours easily is expected to bring production costs down, and our expert’s company offers back-contact technology with a conductive back-sheet.
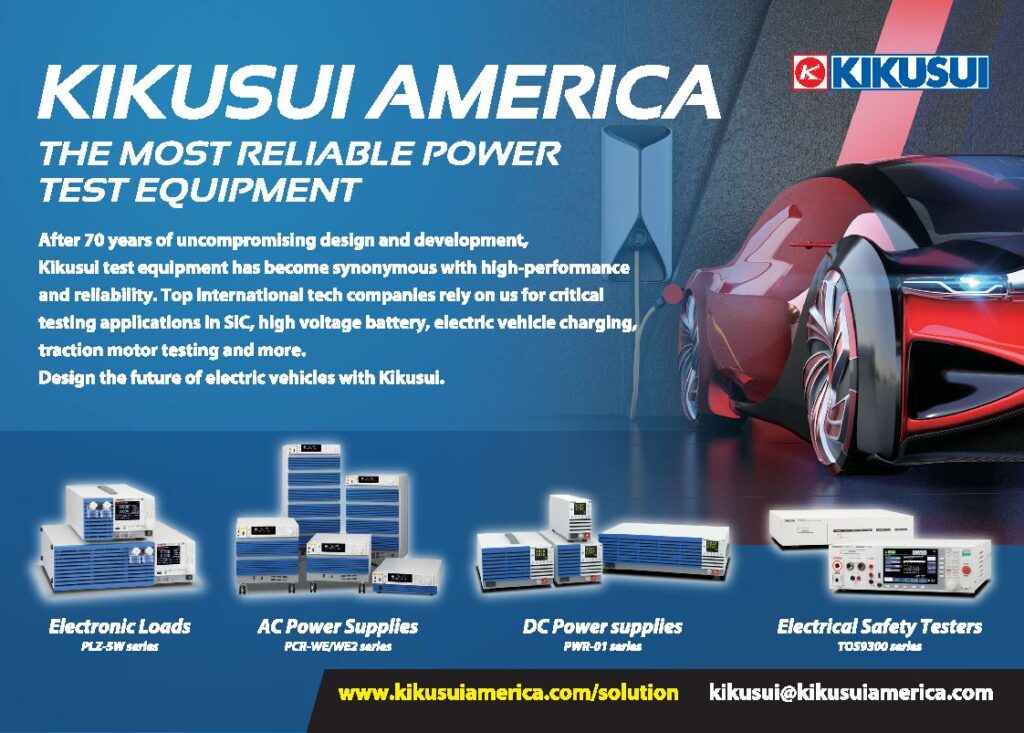
Back-contact technology
Conventional solar technology places the contacts and busbars in front of the PV cells, an arrangement that inevitably blocks some of the incident light and reduces their overall efficiency.
As the name suggests, back-contact technology puts all the electrical contacts on the back of the solar cells, on the opposite side to that exposed to sunlight. For this purpose, either intrinsically back-contacted cells, called interdigitated back-contact (IBC) cells, can be used or conventional cells are ‘tuned’ in a way that the front contact is brought to the back. These are called metal wrap-through (MWT) cells.
Our solar power specialist’s conductive back-sheet is used to interconnect the IBC or MWT cells. Using an automated pick-and-place process, the cells are positioned on top of the back-sheet, which basically acts as a huge flexible printed circuit board, eliminating the need for individual wiring. A perforated insulator sheet between the cells and the back-sheet guides the individual contact points and electrically insulates the circuit of cells.
This back-contact technology has been developed to provide high design flexibility in terms of the shape and size of the PV laminate as well as a highly automated manufacturing process. “Furthermore, residual stresses on cells after interconnection are much lower than with traditional tabbing and stringing,” the specialist says. “That reduces the risk of cell cracking while the PV laminate is being moulded into curved shapes, as well as during the vehicle’s life when the panels are subjected to dynamic mechanical loading.”
Durability and repair issues
VIPV solar bodywork is a new technology, and products that use it are still very much in the early stages of their lifecycle, making it difficult to predict rates of performance degradation. The panels are designed to pass VIPV acceptance testing, which includes accelerated ageing tests, but actual degradation rates in service remain unknown, particularly when it comes to the impact of dynamic mechanical loads, or expert points out.
“Also, the acceptable lower limit will most likely vary by application,” he says. “Regular PV installations can easily reach 25 to 30 years of economic lifetime, even under harshest climatic conditions.”
Our electrification engineer is similarly confident. “We don’t think lifespan will be a problem. “From our testing, we calculate that the solar roof’s power output will degrade by 15% over 20 years, and the customer will hardly notice. We think that is acceptable now, and it will improve with the next generation of systems.”
In designing for durability as well as efficiency, the three-wheeler’s engineers took numerous factors into consideration, including thermal gradients, solar insolation (a measure of the total amount of the Sun’s energy reaching the panels) and efficient wiring pathways, with the claimed result that the solar bodywork should have a service life of at least 10 years.

(Courtesy of Endurans)
Its panels have undergone testing for hail impact, durability and electroluminescence, the company reports. The latter is a quality control test that relies on the fact that solar cells emit light when current passes through them, and it can reveal defects including cracks, microcracks, scratches, failed diodes and bad solder joints.
Repairability is another issue that requires thinking through. With VIPV, body panels are no longer relatively simple sheets of metal, plastic or composite; they are complex integrated systems in their own right. Our expert notes that even for ordinary PV panels, repairing a damaged cover sheet or internal failures such as breakage of cell interconnections is hard, if not impossible, and integrating the panels into the bodywork can only make repair harder still.
“The focus should therefore be on disassembling the PV layer from the bodywork and re-applying a new one. If that is not possible or too expensive, the complete body part needs to be replaced,” he cautions.
While it is not possible to repair broken parts of the CUV’s solar roof because the photovoltaic elements are laminated into the glass, the company has come up with a practical way to mitigate the problem. “We made the panel in two sections, so that if one gets damaged you can change it, reducing the cost by about half. Using more modules that can be replaced individually is under consideration for the future,” the electrification engineer says.
Panels on the dedicated solar vehicle are designed for graceful degradation, in that the system will continue to generate power even if several cells are broken. They can also be replaced individually, allowing for repair and upgrade. “Owners will have the option to upgrade their solar modules to get increased range even as their vehicles age,” says the company.
As far as EVs are concerned, it looks as though solar power’s time will be coming soon.
Acknowledgements
The author would like to thank Carsten Loevenich at Hyundai Motor Europe, Imco Goudswaard at Endurans Solar, and Chris Anthony at Aptera Motors for their help with researching this article.
Some suppliers of solar power technologies
China
JA Solar +86 10 6361 1888 www.jasolar.com
Jinko Solar +86 21 51808777 www.jinkosolar.com
Longi Solar +86-21 6057 8585 www.longi-solar.com
Germany
Fraunhofer Institute +49 761 4588 0 www.ise.fraunhofer.de
Japan
Sharp +81 72 282 1221 www.global.sharp
Korea
LGChem +82 2 3773 1114 www.lg.com
Netherlands
Endurans Solar +31 6 537 08168 www.endurans-solar.com
UK
Oxford PV +44 1865 309618 www.oxfordpv.com
ONLINE PARTNERS
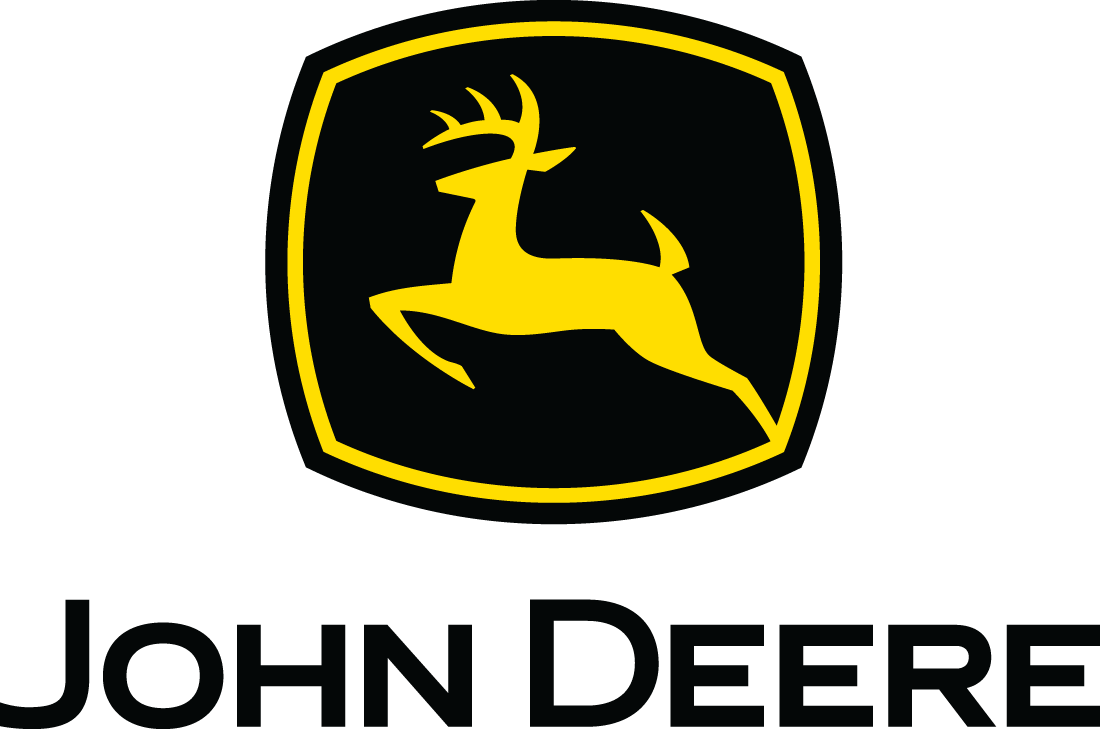
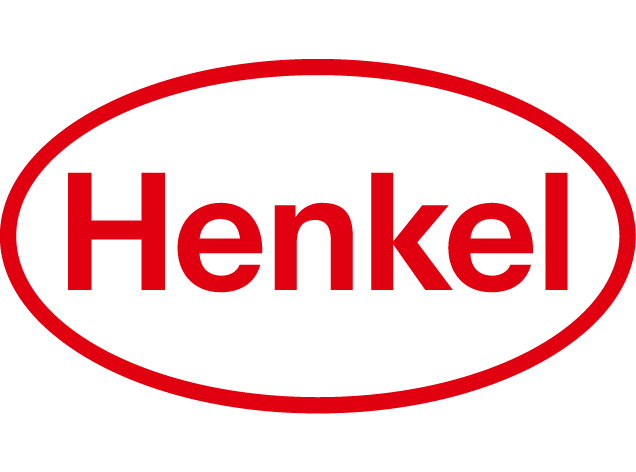
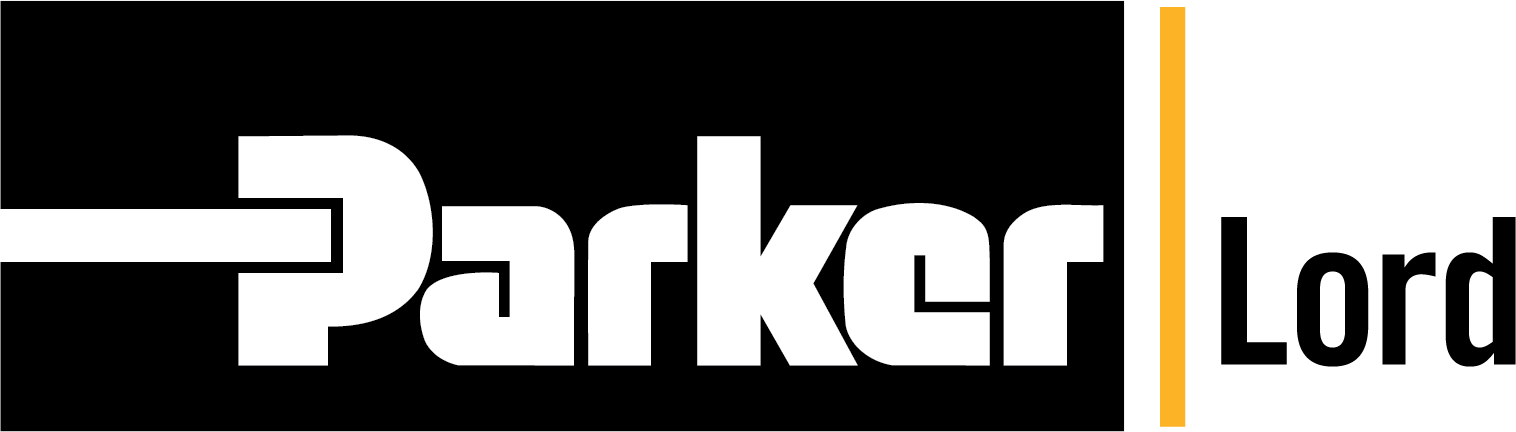
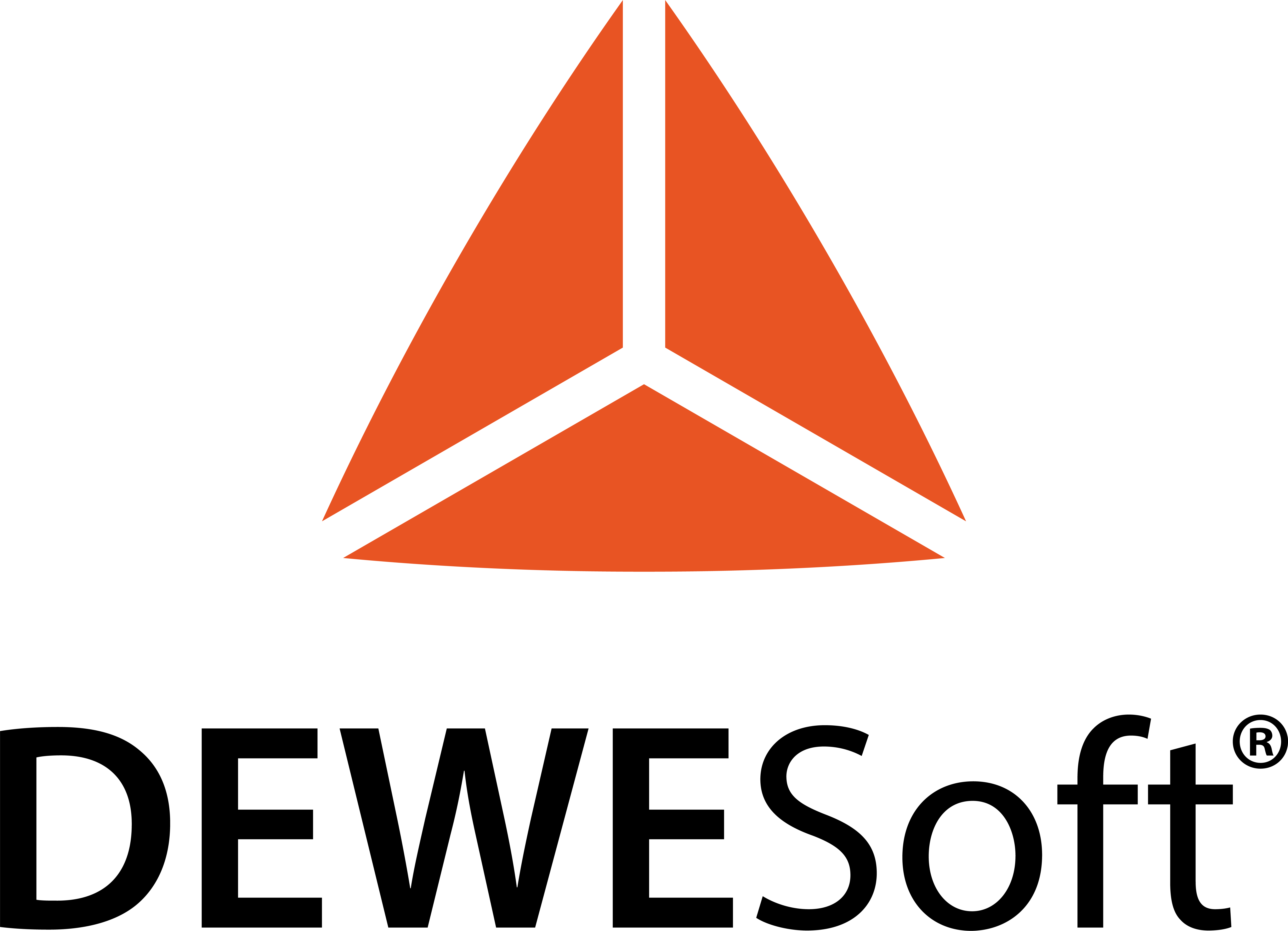
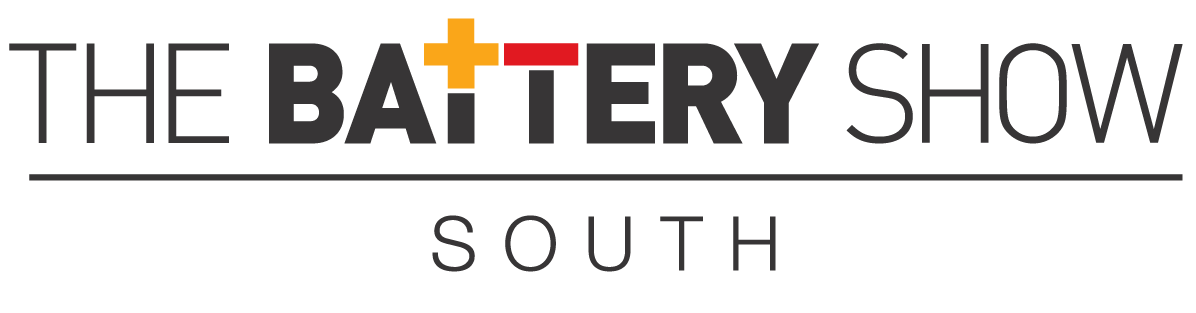
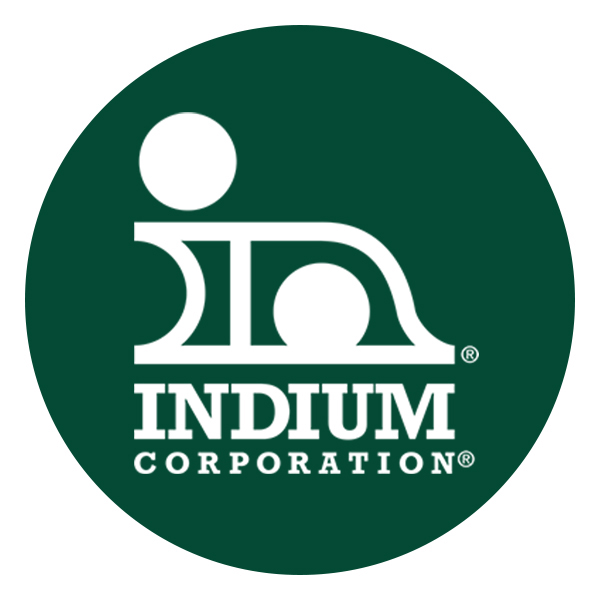
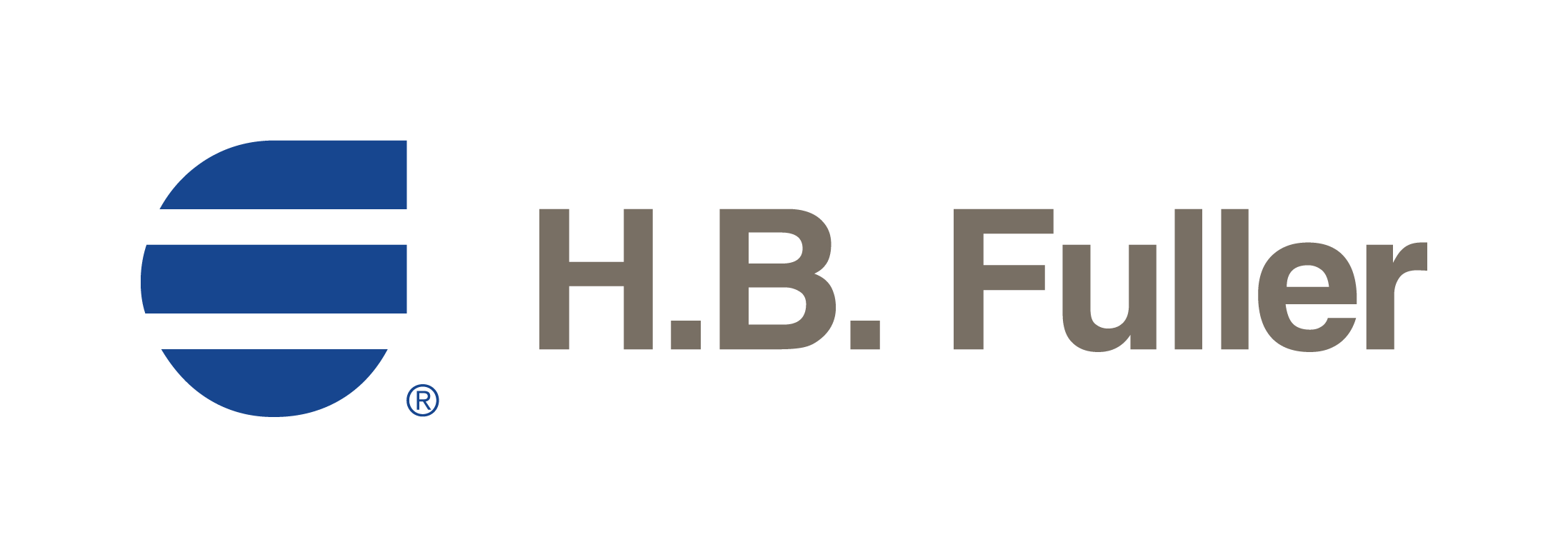