Snow problem for torque software
Porsche Engineering has developed a torque control system for EVs that provides stability in environments such as snow without the need for additional sensors (writes Nick Flaherty).
An electric all-wheel-drive vehicle with multiple motors has a key advantage in allowing variable distribution of the drive power every millisecond. This compares to a conventional all-wheel-drive vehicle, where the power is distributed to the axles through a central differential.
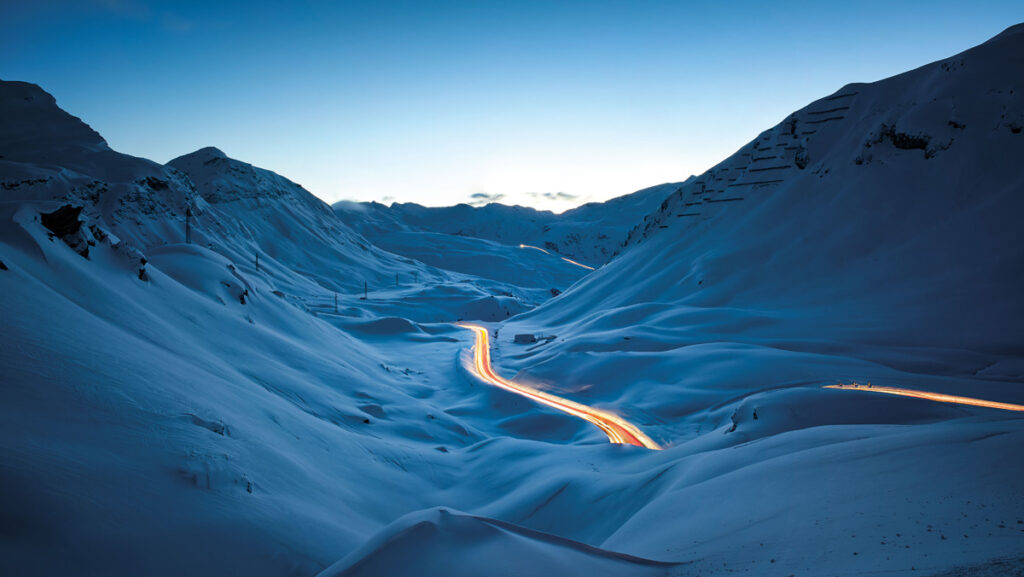
Porsche’s new algorithm for controlling the electric motors in vehicles provides stability in winter conditions
As a rule, the torque ratio is fixed: onethird at the front and two-thirds at the back, for instance. In theory the ratio can be changed, but additional components such as a multi-plate friction clutch are needed.
The software is being used initially in an electric all-wheel-drive SUV, but it also supports different motor configurations for other vehicle types. “We had to develop a lot of it from the ground up,” said Dr Martin Rezac, team leader for function development at Porsche Engineering.
The software starts with the base distribution, controlling how much power is transmitted to the front and rear axles. For straight-line driving and balancedweight scenario, for example, this is a 50/50 distribution. When the driver accelerates, the software switches to full rear-wheel drive – or all front-wheel-drive around a sharp bend. “This makes the vehicle noticeably more stable, even for passengers,” said Rezac.
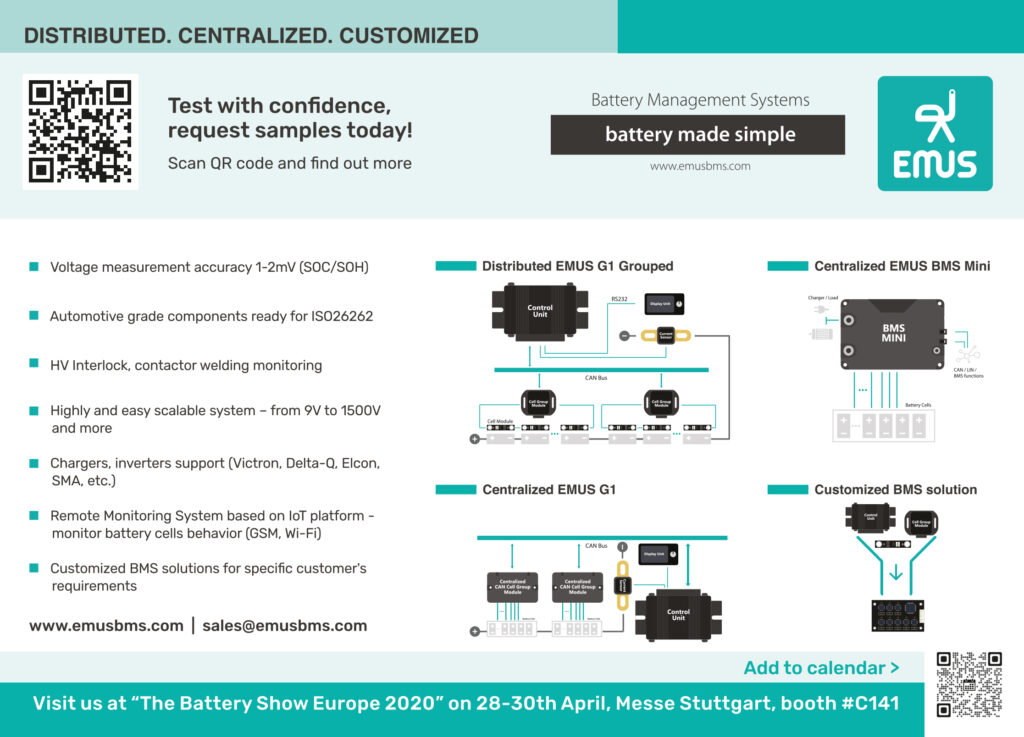
The second task is to adjust the torque to the wheel speed, ensuring that all the wheels are supposed to spin at the same speed. That’s easy on a motorway but harder on a snowy mountain pass. The control system detects any problems such as a wheel spinning on an icy patch of road and directs the torque to the wheels that are turning more slowly but still have grip within fractions of a second.
These two features lead to the third and most important function, the control of lateral movement. In a left-hand turn, the controller brakes the rear left wheel and accelerates the right one until a neutral driving situation is restored. The system takes similar measures when oversteer occurs.
This is achieved with a software module called the driving state observer. It continuously monitors a variety of factors: how forcefully the steering wheel is turned, how much the driver is accelerating, and how much the vehicle is turning around its vertical axis.
The data is provided by a yaw sensor. This actual status is compared with a dynamic model of the vehicle that represents the target state under normal conditions. If the observer module detects deviations from the model, for instance due to oversteer or understeer, the software intervenes. If the vehicle is not turning into a corner as quickly as would be expected from the current steering wheel position and speed, individual wheels are selectively braked until the direction is restored.
The software provides more than a conventional electronic stability control system. The individual wheels can be accelerated to ‘pull’ the vehicle back onto the right track without losing speed.
“The development of the vehicle observer was the biggest challenge, as the observer has to estimate the vehicle’s important parameters,” said Rezac. There is little original data available – it has to be derived from existing devices such as a sensor that detects the inclination of the car, for example, which is usually used for automatically adjusting the headlights.
The software was tested and calibrated over two winters in a wide range of real-world situations. If the sensor reports faulty data, for example, the torque control has to decide if it is still allowed to function even without the data source or should be switched off.
ONLINE PARTNERS
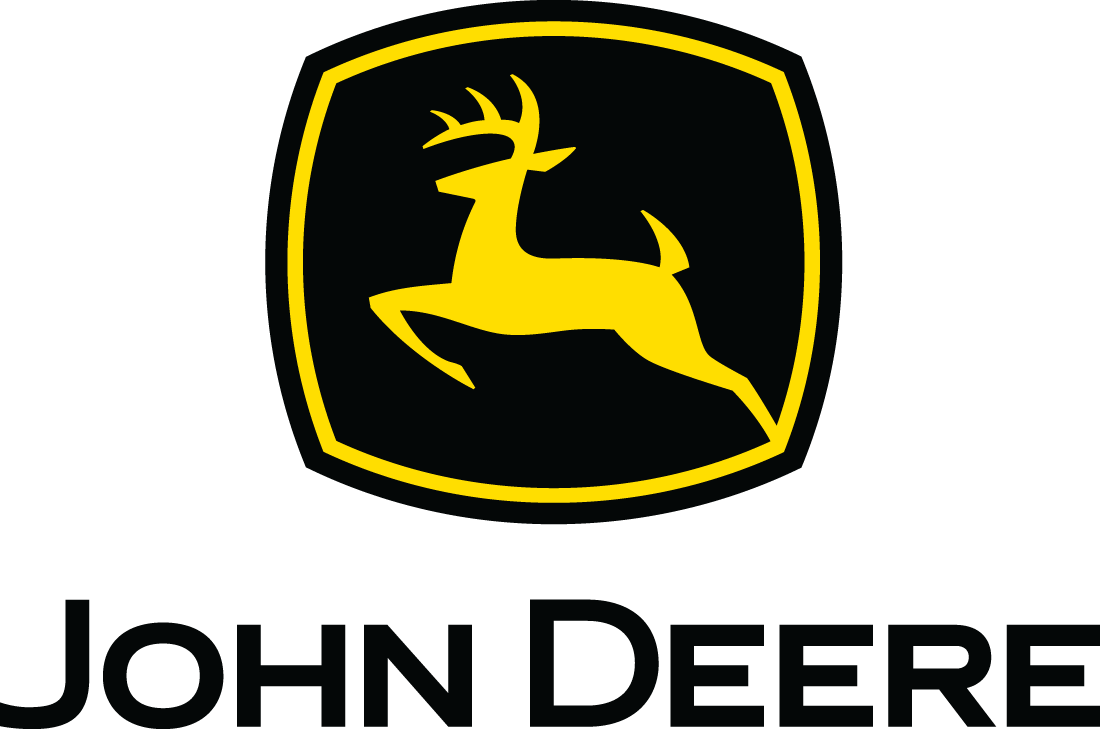
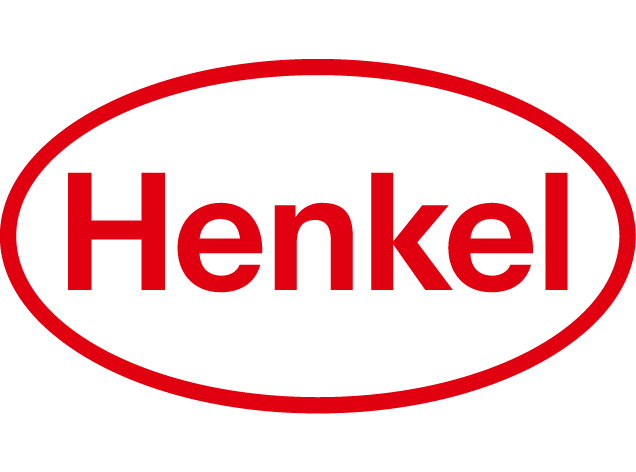
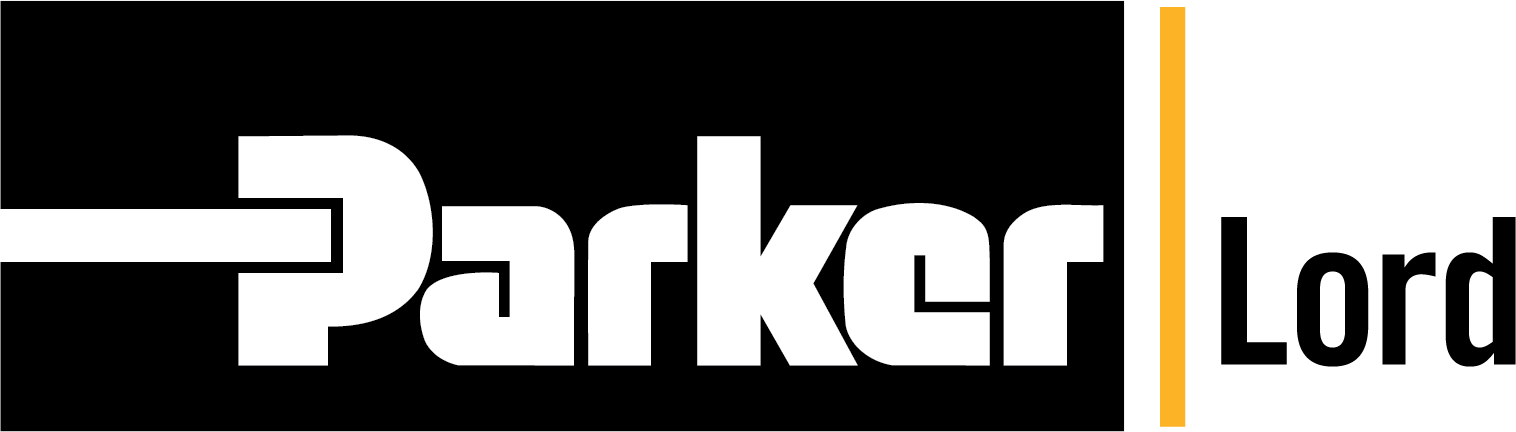
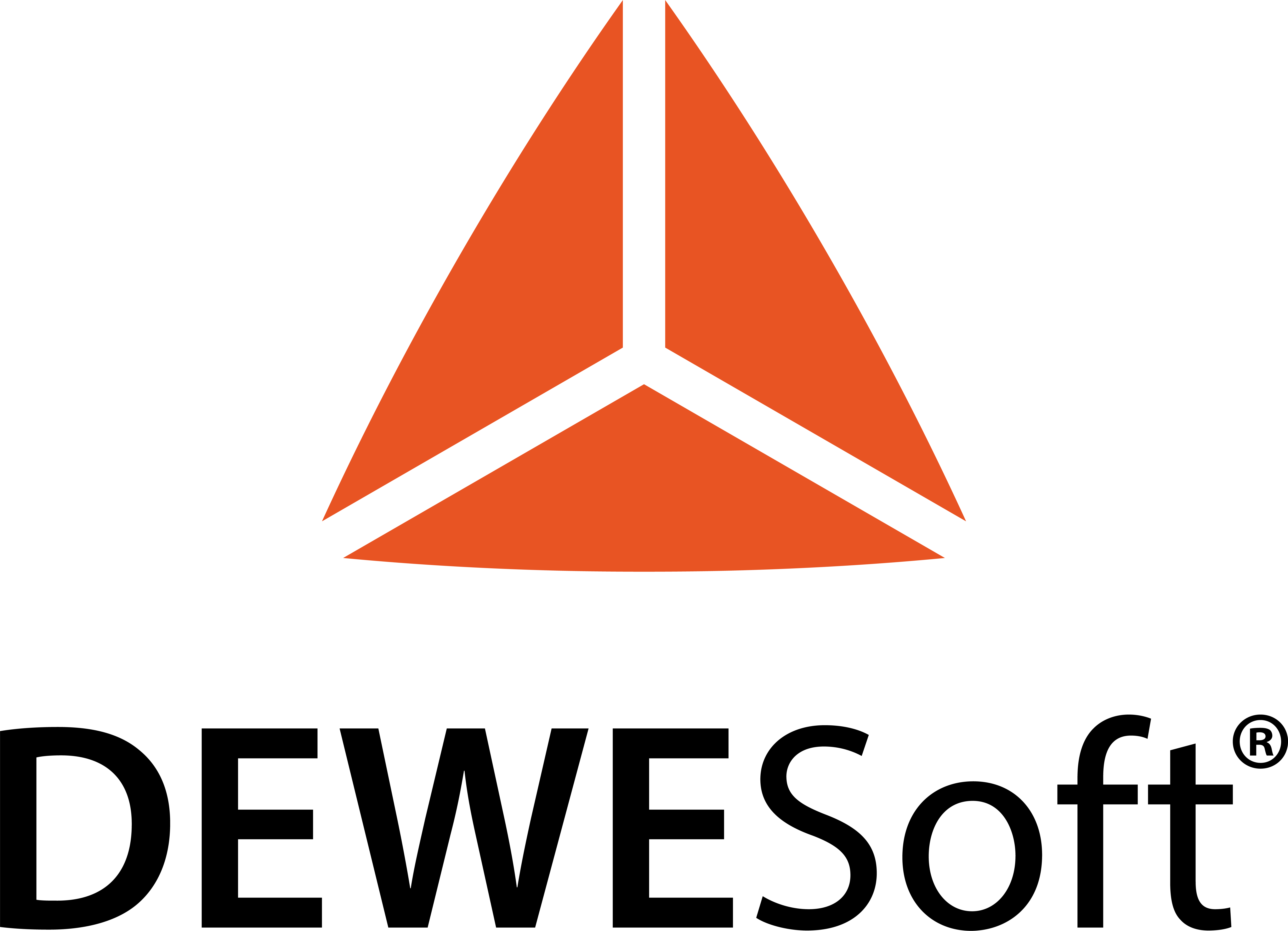
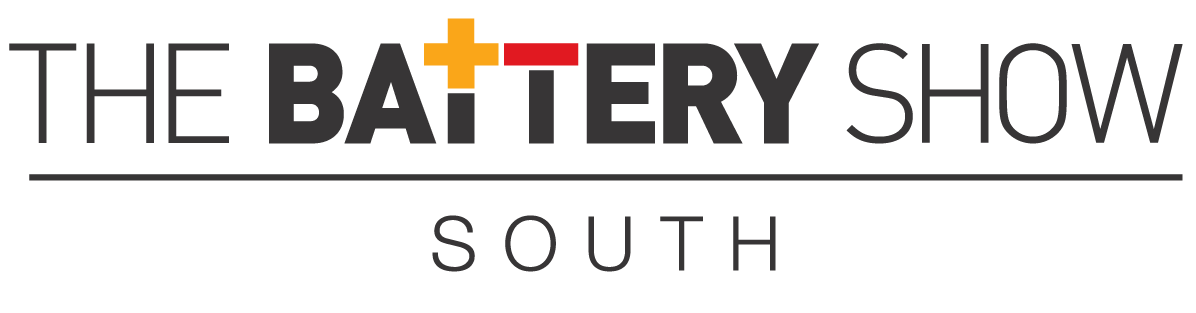
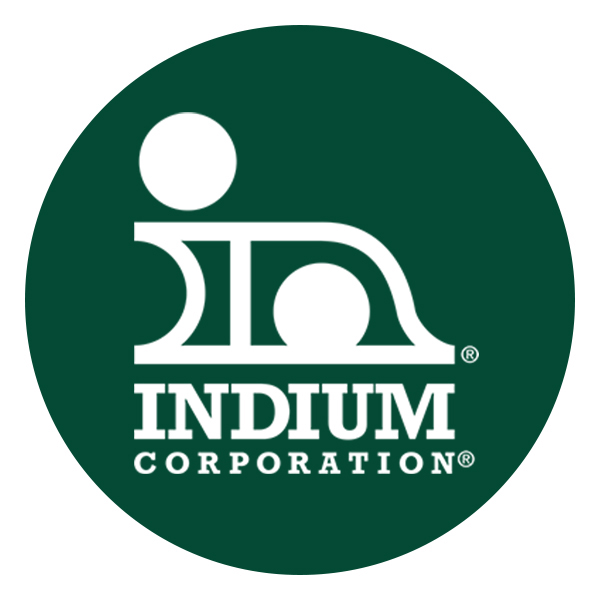
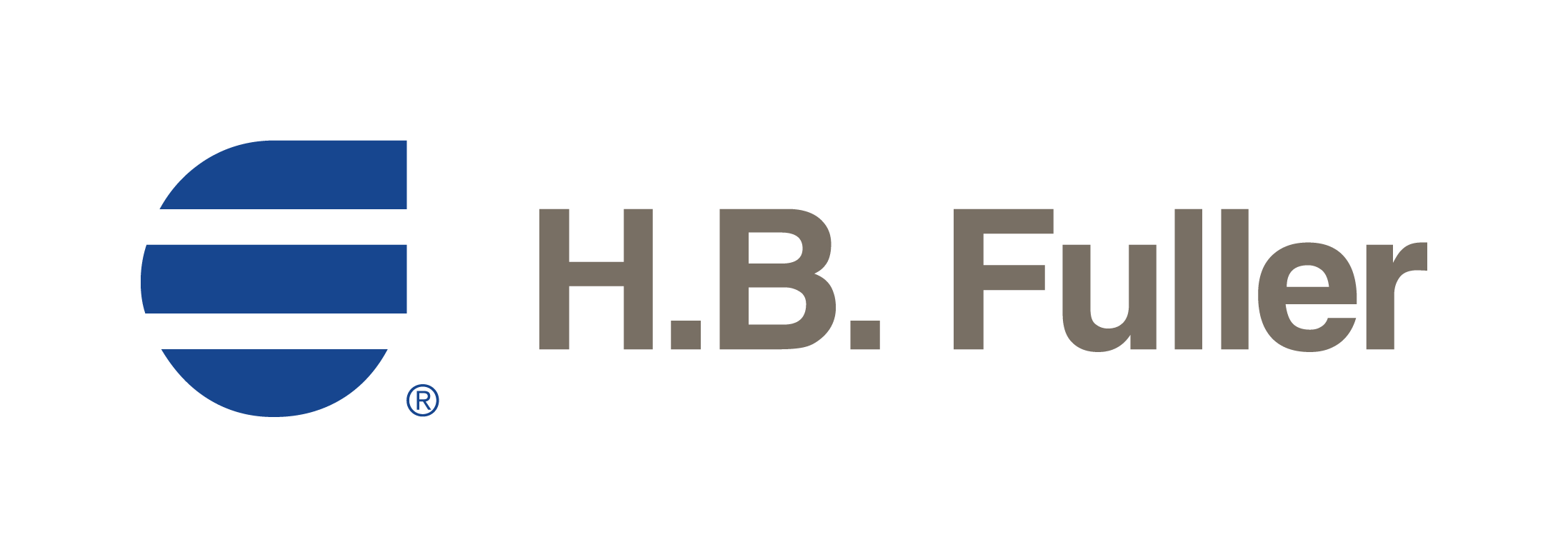