Electric & Hybrid Marine World Expo 2018
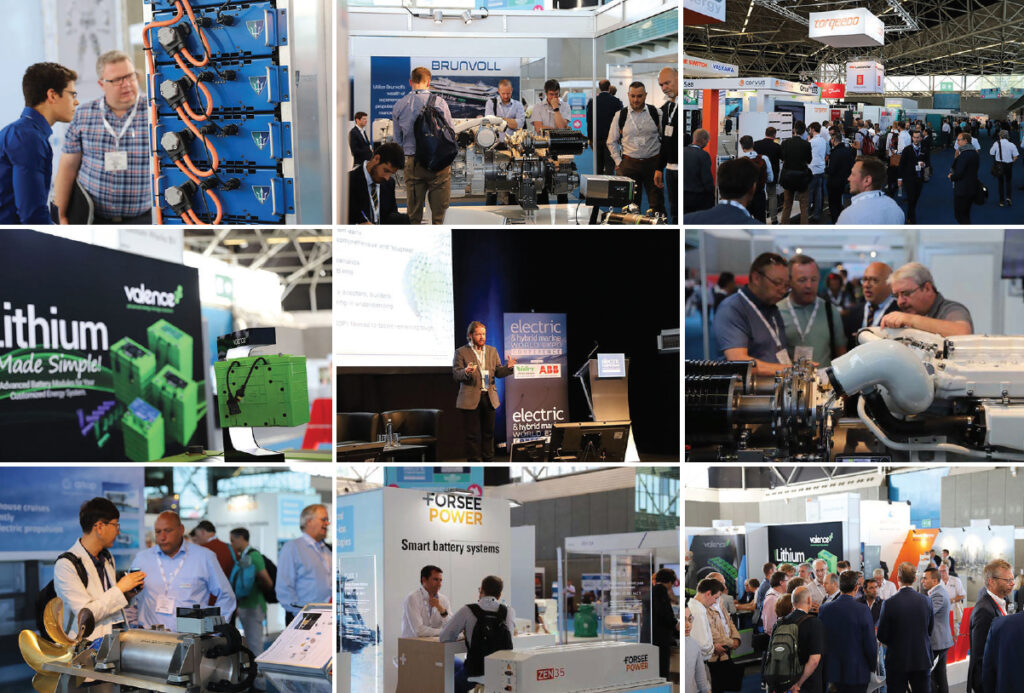
Sea change
Rory Jackson reports on some of the latest developments in maritime propulsion technology that were on show at this pre-eminent exhibition.
Taking place in the RAI Amsterdam Convention Centre, the Electric & Hybrid Marine World Expo is the largest aquatic propulsion trade show in the world. This year’s event was the biggest yet, with more than 130 exhibitors from across the globe showcasing their solutions for electrifying marine vessel powertrains to more than 4500 attendees.
Leonardo DRS had its PA44-625 electric motor on display at the expo. It is a permanent magnet AC motor with an axial flux configuration, and measures 647.7 mm in diameter and 252.3 mm in length.
“The US Coast Guard is building a new offshore patrol cutter, and the PA44 has been selected for the hybrid-electric drive [HED],” commented Greg Reed. “The HED will propel the ship at low speeds, as there is a concern that diesels, at low speeds and when they’re lightly loaded, experience coking or a build-up of carbon deposits, which is a significant maintenance problem.”
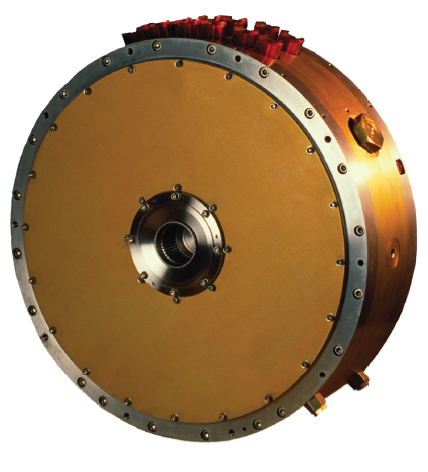
The PA44-625 was developed with power density as a key performance specification. It is rated at 625 hp (466 kW) and a torque of 1491 Nm (1100 lb-ft), while weighing only 195 kg.
“Permanent magnet motors incorporate a lot less back iron than induction machines or wound-rotor synchronous motors, which helps make them much lighter,” Reed said. “The PA44 also uses an aluminium casing and is liquid-cooled for thermal management.”
The machine uses a water/glycol mixture as its coolant, which flows at 3.5 gallons per minute to each of the two stators. One stator sits on each side of the rotor, with a variable-frequency drive being used to control the rotational speed. The permanent magnets in the PA44’s rotor are made from neodymium.
Its maximum motor speed is rated at 3600 rpm, while the standard operating speed is rated at 3000 rpm (at an efficiency of 95%).
Echandia Marine came from Sweden to showcase and discuss its successes with electric vessel designs, the most recent being the BB Green ferry, a result of the EU-funded BB Green research project.
The project to develop the ferry began in 2011 and ended in 2015. Its main deliverable was to build a full-size demonstrator, to verify and document the proof of concept for a high-speed, plug-in battery electric passenger ferry.
As Magnus Eriksson told us, “We’re now in the final phase of another EU project [Green Fast Ferries – Horizon 2020] involving the BB Green vessel, giving priority to demonstrations and finalising the preparations and certifications for serial production of the vessel.”
“We say the BB Green is the fastest and most energy-efficient battery-driven ferry in the world of its size, having a top speed of 30 knots,” Eriksson said.
“Power consumption is reduced by 30-40% relative to that of a conventional fuel-powered vessel of comparable size, passenger capacity and speed. Naval architects are generally happy to see a 1 or 2% improvement in energy efficiency.”
The key design innovation that enables the BB Green’s efficiency is its configuration as an air-supported vessel. For a 20 m air-supported vessel, up to 15 m3 of pressurised air is pumped into a cavity under the hull below the waterline by means of an electric lift fan system with air intakes in the bow of the vessel.
About 70-80% of the vessel’s displacement is supported on a cushion of air, in a similar way to a hovercraft but without the need for any soft and vulnerable skirts. The air-supported vessel concept reduces the frictional and wave-making resistances of the vessel, and enables the use of batteries and a drivetrain that are heavier (and therefore more powerful) than in a conventional, non-air-supported set-up. That could mean more speed, endurance or powered facilities for passengers.
The BB Green’s hull is fabricated using a vacuum-infused carbon composite with vinylester resin and a Divinycell core. Its propulsion uses a Volvo Penta integrated propulsion system thruster, with two counter-rotating 280 kW propeller drives, adapted for the vessel’s electric power plant. The vessel’s power source consists of 427 kW of lithium titanate oxide (LTO) battery packs, enabling a range of 12-14 nautical miles between recharging.
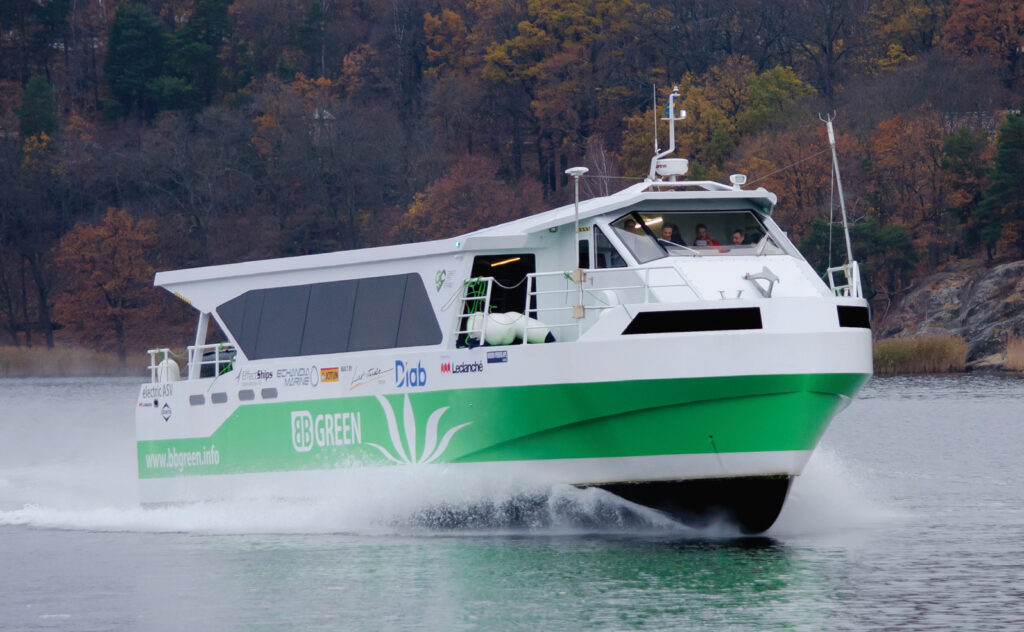
A hybrid HB Green is also in development. This will use two 440 kW diesel generators and a 70 kWh LTO battery. A hydrogen fuel cell FC Green vessel for longer voyages is planned as well.
Also on show at the Echandia Marine pavilion was the Toshiba SCiB battery module, which Toshiba supplies to Echandia.
“The module consists of 24 cells in pairs of two,” said Torkel Mallmin. “You can cycle them for up to 20,000 cycles, and even if it goes down to less than 40% depth of discharge, that doesn’t degrade its lifespan or expected number of cycles.”
The SCiB uses LTO chemistry, which makes such cells slightly heavier and more expensive than the lithium nickel manganese cobalt oxide cells in common use in the marine market. However, with LTO there is no crystalline build-up on the anode, which can cause internal short-circuits, triggering fires and explosions.
Engiro showed its range of permanent magnet inrunner (internal rotor) motors at the expo. They come in different shapes and sizes for varying torque and power requirements, from 3 to 200 kW.
“Marine users of electric motors tend to prefer direct-driveshaft solutions, in which the propeller shaft is directly mounted to the motor. That differs greatly from the needs of our electric truck customers, who always have a differential gear in between and a much wider speed range,” Jan Werner said.
All the motors use permanent magnets made from neodymium, for its greater magnetic strength over other magnetic materials. “In addition to its strength, we always try to reduce the amount of magnets embedded inside our motors – neodymium is expensive,” Werner noted.
The company’s largest motor, the 370W-27012-SER, has 10 permanent magnets and weighs 250 kg. It delivers 205 kW of continuous power or 235 kW of maximum power, and can use inputs from 550 to 750 V DC. Torque of 1110 Nm is generated at continuous power, up to a maximum of 2030 Nm.
The ‘370W’ in the product name serves to indicate the 370 mm diameter of the stator, and that it is a water/glycol-cooled system. The ‘27012’ corresponds to an internal code for the coil winding configuration, and the ‘SER’ refers to the flange, shaft and encoder type.
Werner said, “One difference between electric boat and electric truck powertrains is that marine applications need a higher continuous torque, so we are planning to offer our 370W-27012-SER in a special marine version.”
This is slated to incorporate a different electromagnetic design. That will lead to significant torque increases: nominal torque at continuous power is expected to be 2000 Nm (or potentially higher, up to a maximum of 2650 Nm), with peak torque expected to be 3800 Nm.
Baknor Engineering attended the expo to display its range of thermal management solutions, including its approach to liquid cooling for battery packs.
“Liquid cooling for electric and hybrid marine vehicles has been around for a while, and is used in multiple applications with specific battery pack designs,” said Michael Ruscigno. “We’ve been able to cool the individual cells in the battery pack, which results in far better temperature control for the overall battery module.”
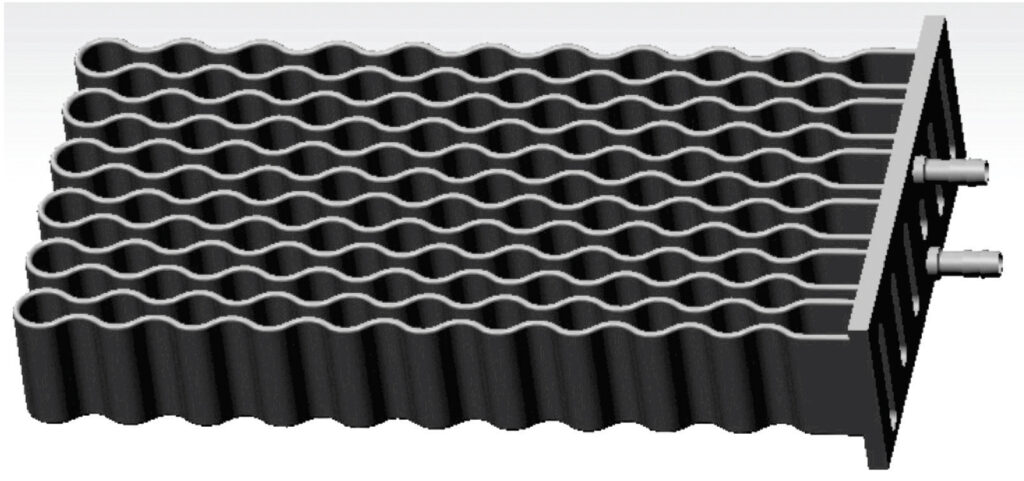
Extruded plates are formed around each individual cell, which results in more surface area per cell. The greater the surface area, the more heat that can be dissipated.
The ability to control heat at the cell level improves the performance of the battery pack/module and increases its lifespan. The technology can be scaled to work with batteries of different sizes.
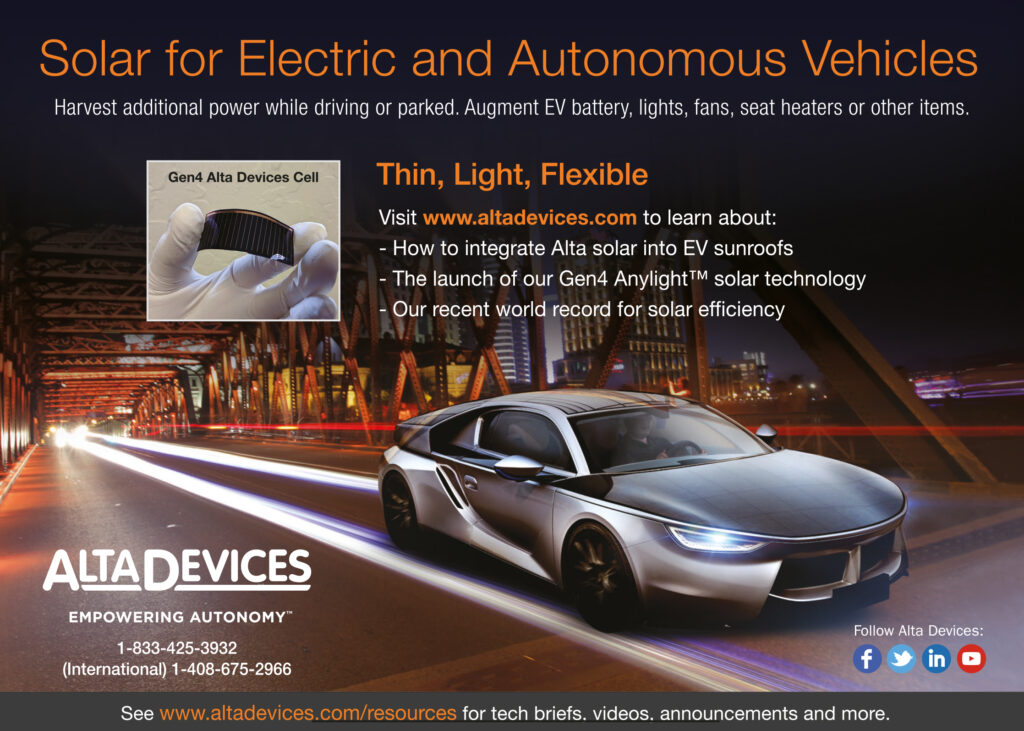
Mersen, a manufacturer of fuses and other electrical power components, is developing a new type of overcurrent protection device (OCPD) that is designed as a hybrid solution between carrying an operating current and interrupting an abnormally high overload current.
Fuses are generally the first choice for system protection in electrical and power electronics applications. They are cost-effective and passive components, can withstand operating currents and interrupt very high fault currents.
In some cases, however, where the triggering time for current interruption or discriminating between acting and not acting are key for an electric or hybrid vehicle, fuses can be combined with a faster system to take charge of the interrupt process.
“We’ve divided the two functions across two actuators, housed in a single box,” said Franck Charlier. “The key to optimising it is having a complete list of input specifications for the powertrain in question, so that we can select the right actuators for the voltage and current ratings that the end-user’s hybrid OCPD will be dealing with.”
That means knowing the correct maximum voltage and operating voltage, as well as the expected load current on the OCPD, which must encompass both the typical operating current rating and any current levels which are abnormal but not an overload risk.
Ratings relating to fault current conditions must also be specified, not just the highest level of short-circuit in kA but the complete prospective scope from minimum to maximum faults to be cleared.
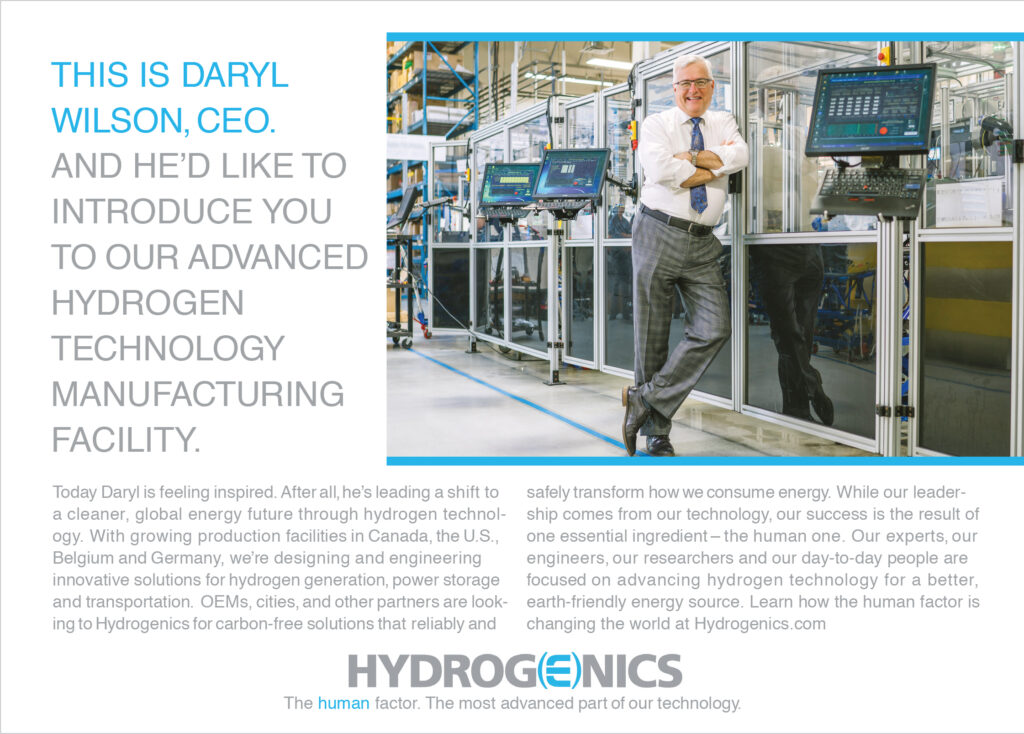
The system could be installed in any branch of an electric vessel’s powertrain that contains a significant consumer or producer of energy. That can mean connecting it to a DC output, an AC rectifier or a DC-fed inverter motor drive.
Although the hybrid OCPD comes as more of a semi-custom solution rather than a range of products, given its requirements for exact power system specifications before being built, Mersen hopes to target vessel grids operating at 500-1000 V DC.
“With our first pre-series prototypes, we are already covering 0-500 A or so,” Charlier said. “But we also expect to scale up, and probably reach 1200-1500 V, or higher than 1000 A in terms of current, some time in 2019.”
A safe and stable battery management system (BMS) that can control up to 65 modules, with different BMS units for different voltage ranges, was displayed by energy management and battery manufacturing company Lithium Werks.
The Valence BMS uses an IP56-rated enclosure for resisting water and dust, and enduring storage temperatures from -40 to +50 C. One Valence controls up to 65 of the company’s U-Charge XP series of lithium-ion magnesium phosphate modules, which come in power packs with voltages from 12 to 48 V. The modules can be connected in series to achieve voltages of up to 1000 V DC and in parallel to any capacity.
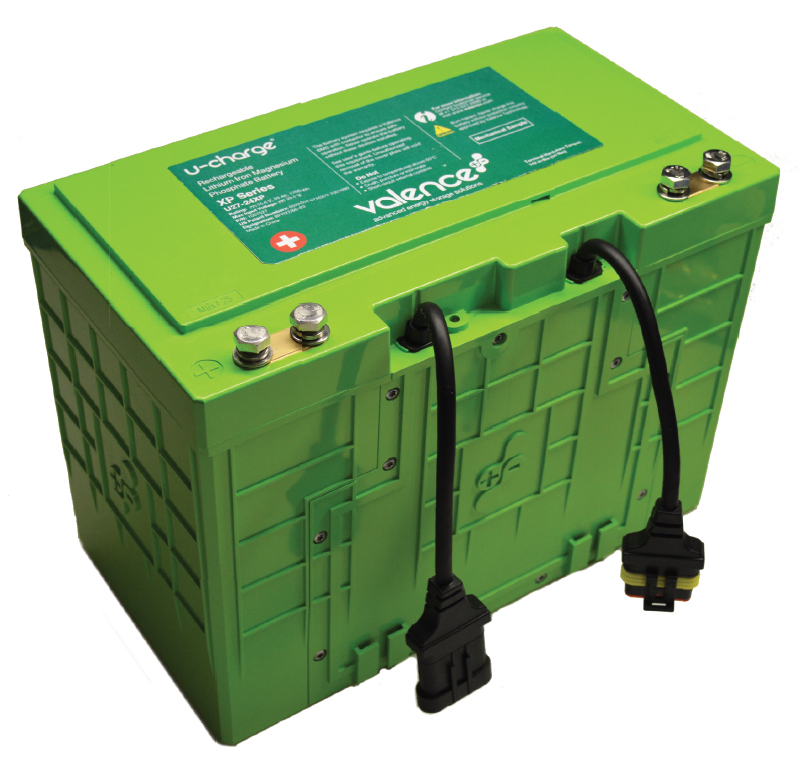
Lithium Werks said that this makes the XP series suitable for applications including electric marine vessels, port tractors, delivery trucks and buses. In addition, these energy storage and battery management systems are currently installed in applications such as materials handling and mining.
“If you need more than 65 modules, using multiple BMS units, the system will require our Master Battery Server [MBS],” said Stuart Douglas.
“With the MBS you can communicate with any sort of protocol, including CANopen, Profinet or Modbus. Communications from the BMS units to the battery modules use an RS-485 serial interface.”
For redundancy, if a power module or a string of them in a multi-BMS architecture has an issue, the section in question is safely disconnected by the MBS and the rest of the modules can continue to provide power safely and without interruption, Douglas explained.
The chemistry for the core of the U-Charge technology was selected for its high resistance to the liberation of oxygen, to ensure no significant exothermic event occurs upon heating.
AAA Propulsion showcased its new V-Pod electric underwater azimuth thruster design. It uses an integrated permanent magnet motor, with a relatively long ‘flexible’ shaft running through the hollow rotor shaft to the propeller and coupled at the back using a planetary gearbox.
“The advantage of the gearbox is that we can run at higher rpm with the electric motor, which means a smaller pod diameter and higher power than our previous systems,” said Dick-Jan de Blaeij.
“The smaller products in the series run from 1500-1800 rpm, as changes in propeller size affect changes in optimal speed, except when going above 1 MW when they will run between 1100 and 1350 rpm.”
The V-Pod was designed using CAD software, with CFD analysis and FEA carried out to optimise the structure. The design of the system’s strut was an especially crucial gain from the design phase as it also acts as rudder for the module.
That can be challenging to achieve for azimuth thrusters in general, owing to the round shapes that comprise the system. The strut provided enough lift for an extra 3% energy efficiency to the finished design when used as a pulling propeller.
Marine drive manufacturer Torqeedo displayed its Deep Blue lithium-ion battery series for maritime electric and hybrid drive systems.
The series consists of two prismatic cell battery models of different sizes. The larger model, the BMW i3 (originally supplied by the German car maker), weighs 256 kg and supplies 30.5 kWh at a nominal voltage of 360 V, while measuring 1660 x 964 x 174 mm.
The smaller battery, the BMW i8, is smaller but less ‘flat’, measuring roughly 1460 x 305 x 330 mm while also weighing just 98 kg. The i8 also provides up to 9.1 kWh over a 355 V supply.
“They both come from the BMW cars, directly supplied by our partners at the company,” explained Jamie Marley. “The i3 batteries are more economical in terms of energy density, and in terms of the Deep Blue batteries’ cost-to-power ratios and weights.”
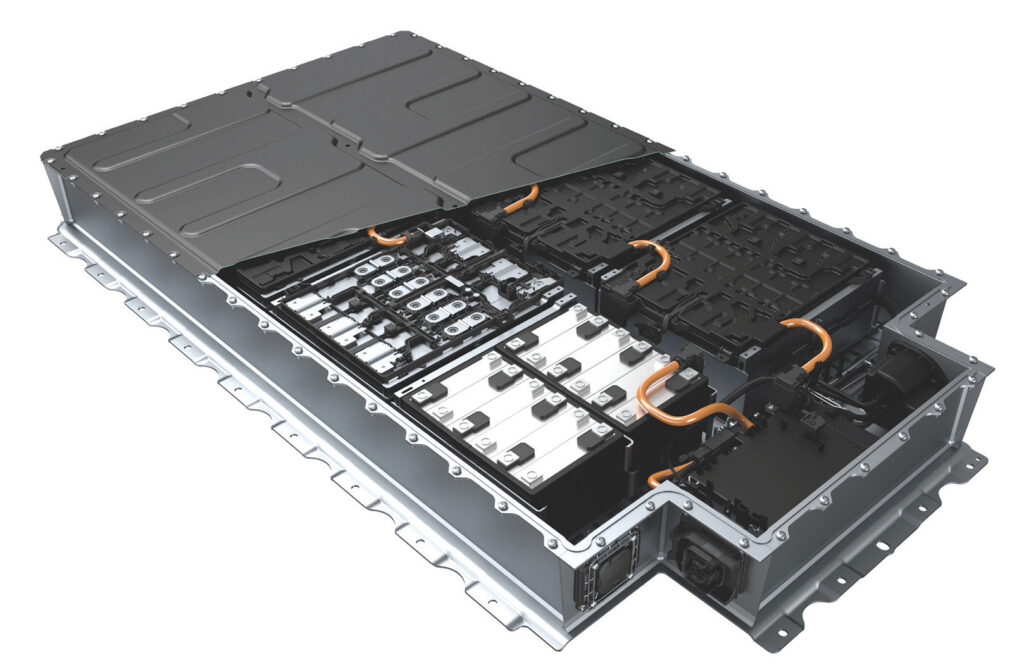
The batteries are housed in IP67 waterproof aluminium enclosures, which can be opened to replace individual parts, something that was not an option for the company’s previous battery offerings and could be necessary in the future as the batteries age.
If excess pressure should develop – owing to, for example, excessive overcharging, which can cause the battery cathode material to become unstable and produce carbon dioxide – the Deep Blue cells can dissipate pressure, temperature and gas through a pressure valve, which is not usually an option with foil-welded or pouch-type lithium-polymer cells.
Amphenol Industrial recently upgraded its HVSL connector interface to handle larger cables, and attended the show to discuss its useability in marine applications such as electric vessel energy storage systems.
“The connector comes in either IP67 or IP69 enclosures, depending on your exact protection needs against water immersion, high-temperature steam or high-pressure water,” Mathias Lundstedt said.
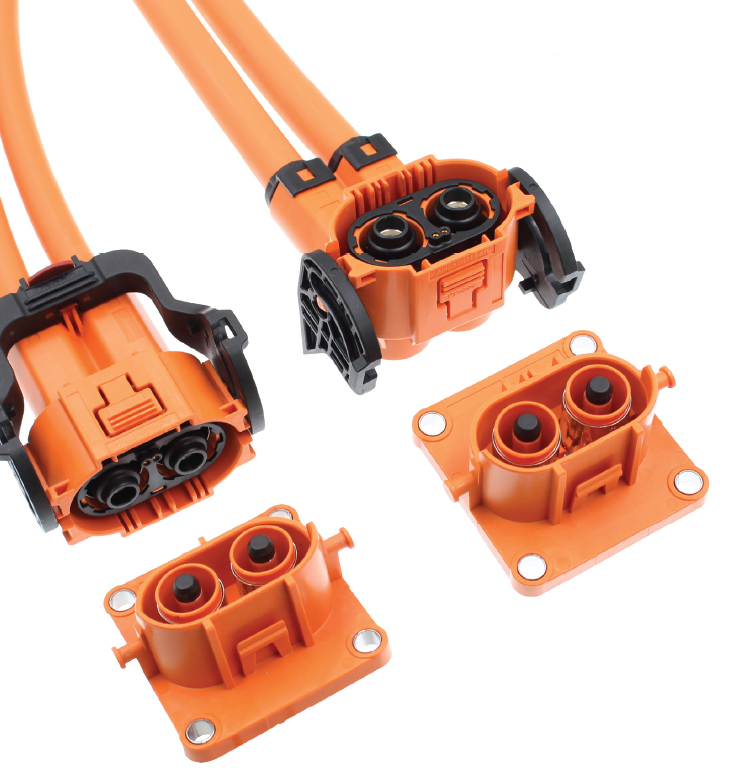
He added that the upgrades to the HSVL’s cable handling were achieved by integrating the company’s Radsok radial twist-type connectors and contacts of 5.7 mm in diameter. The Radsock configuration is manufactured by taking a stamped flat grid and twisting it into a hyperbolic geometry, resulting in a higher density of contacts to the mating pin. That avoids having to rely on beam elements or spring contacts, which could weaken over time.
ONLINE PARTNERS
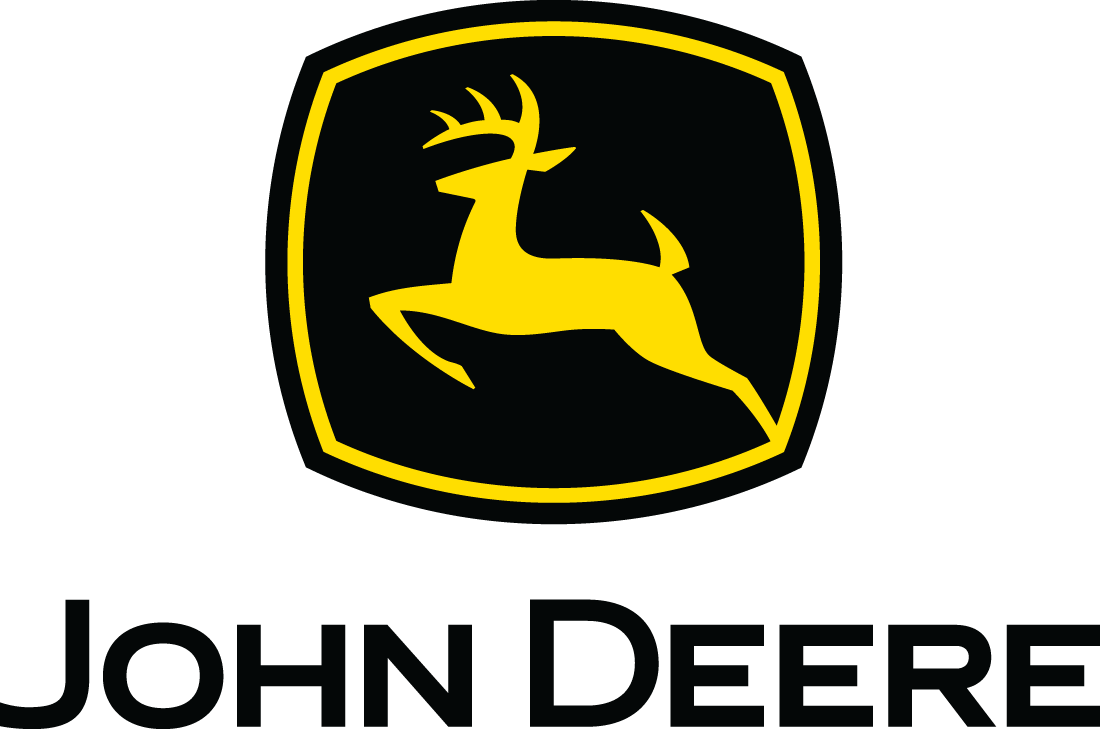
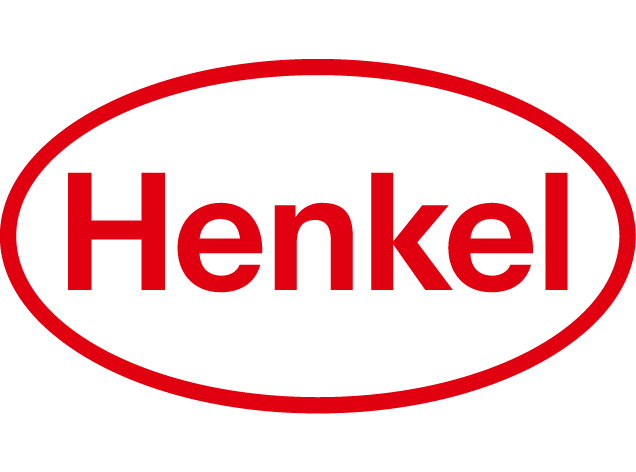
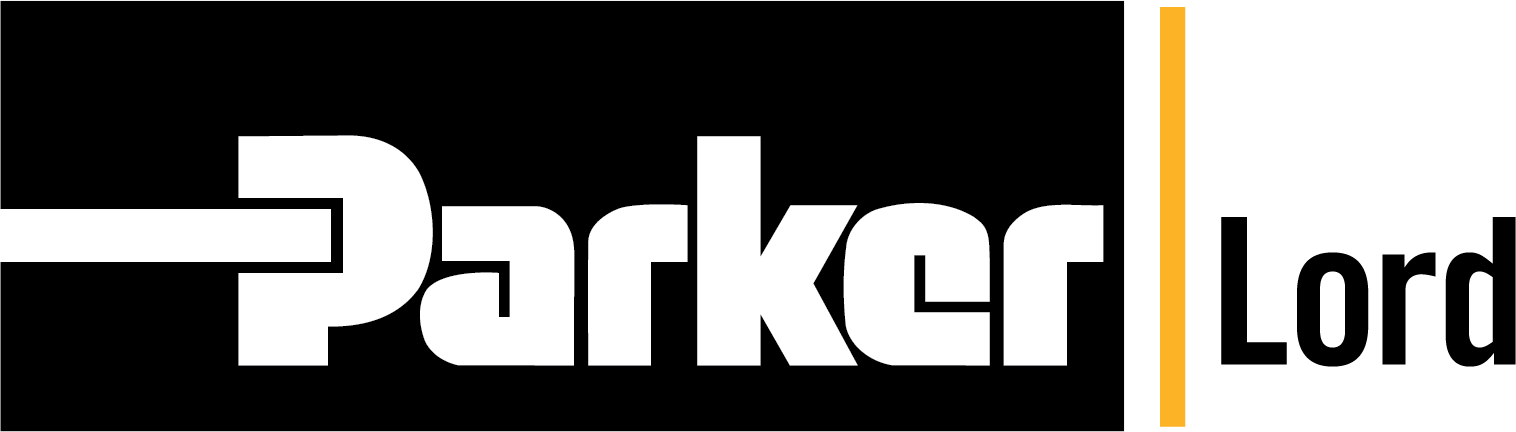
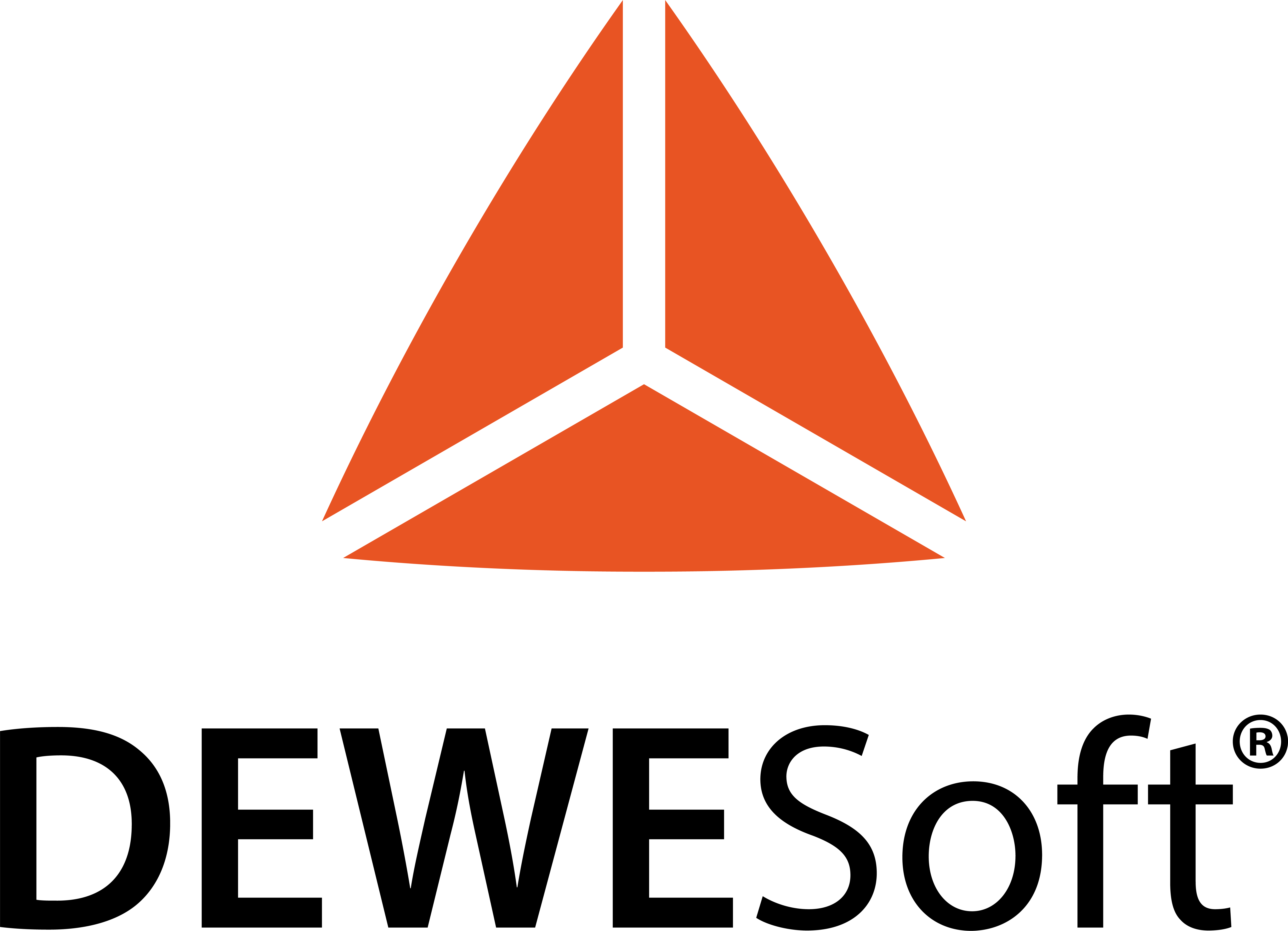
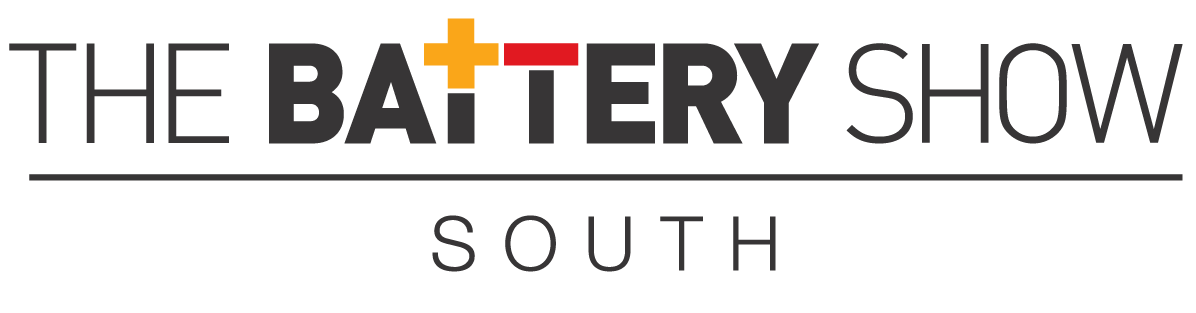
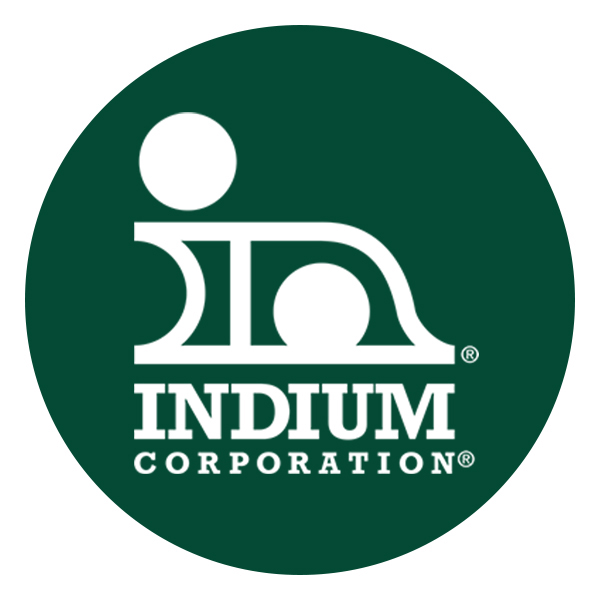
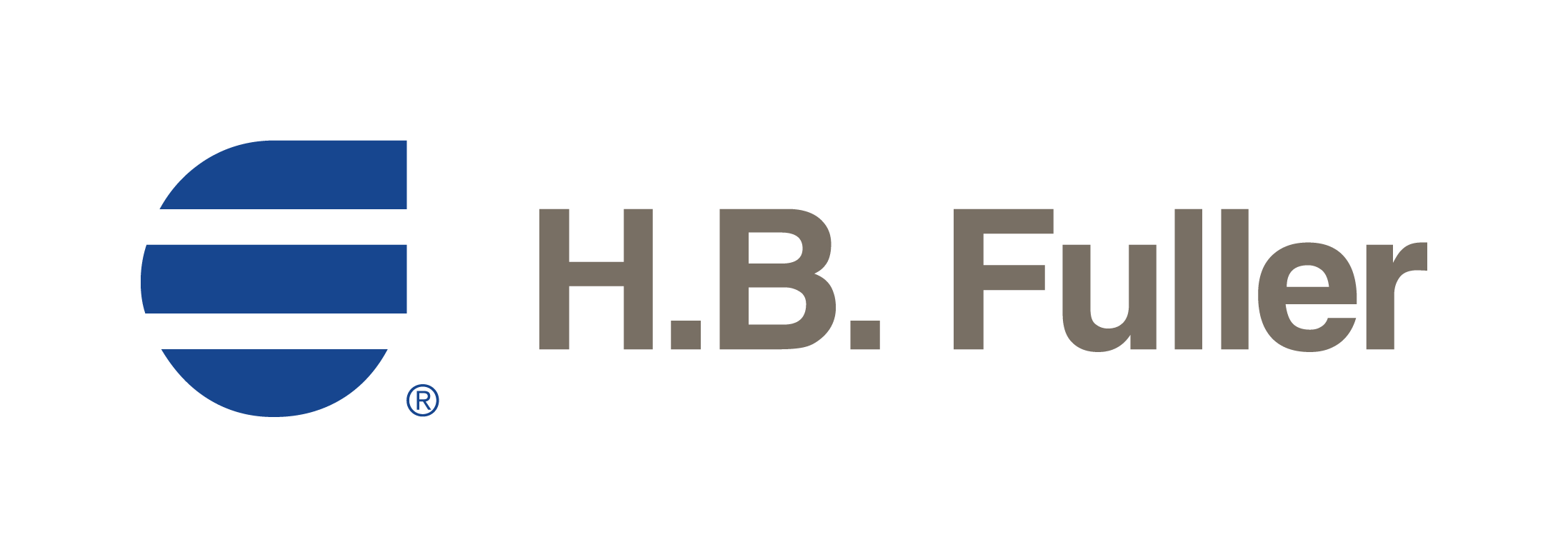