Safe AI for batteries
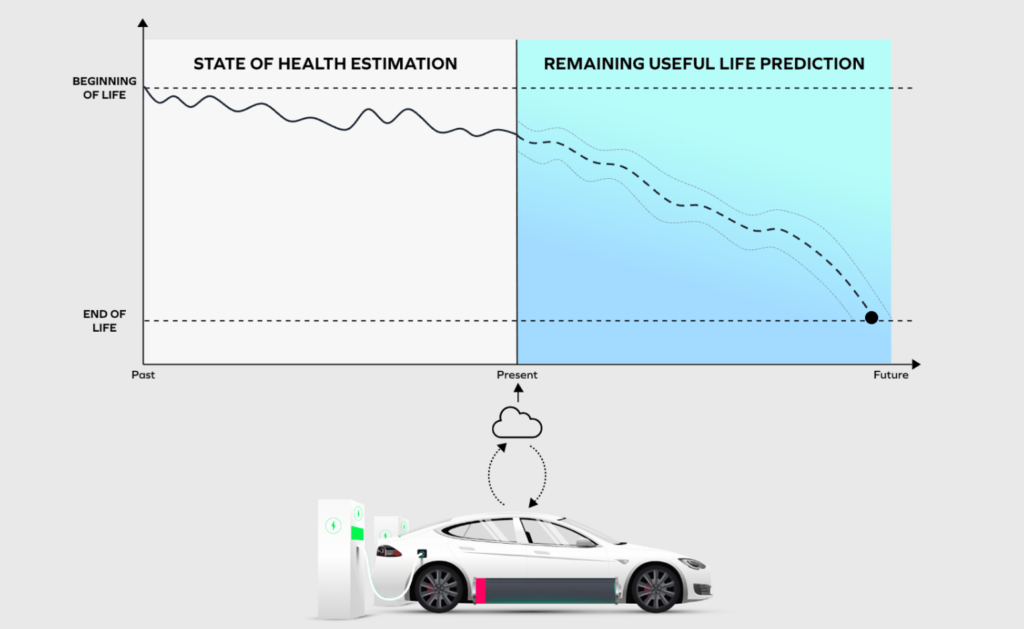
(Courtesy of Eatron)
While we are growing used to artificially intelligent software in smartphones, for example, if AI and machine learning are to benefit EV applications such as controlling batteries, inverters and motors, the software must meet all the safety, security and quality standards that apply to serial production vehicles in the automotive industry. This is the mission of Eatron Technologies, a UK company based in Warwick that is focused on intelligent management of EV batteries with its own hardware, embedded software and cloud-based AI, writes Peter Donaldson.
“If you want sustainable battery economics you have to have intelligent connected battery management platform as part of the pack, and batteries that are managed seamlessly through first, second and third life applications ,” according to CEO Dr Umut Genc. “We are all increasingly aware of the negative impacts of battery manufacturing from lithium and cobalt mining etc, and with our software we try to help some of those pain points by improving efficiency and sustainability.”
Essentially, Eatron begins by testing a battery cell to find out how it performs and works out how to control it intelligently. “We have a software platform that allows the integration of advanced control algorithms into the BMS, and a cloud layer where we combine these algorithms with digital models that learn continuously while the batteries are in the field,” he explains.
A connected vehicle sends data to Eatron’s cloud, enabling them to develop a usage profile from battery charge and discharge data, he adds. “When we understand that better, we can update certain parameters in the BMS over the air to increase the battery’s performance, minimise warranty claims, and maintain its health as far as possible to increase the pack’s useful life.
“With the help of digital models in the cloud, we learn and adapt, and we do that within the life of the individual battery. This way we can improve its efficiency and its lifetime by 10% to 15%, and if you think of the 100 million batteries deployed over the next five years an improvement of a few percent has a huge impact on sustainability and the environment.”
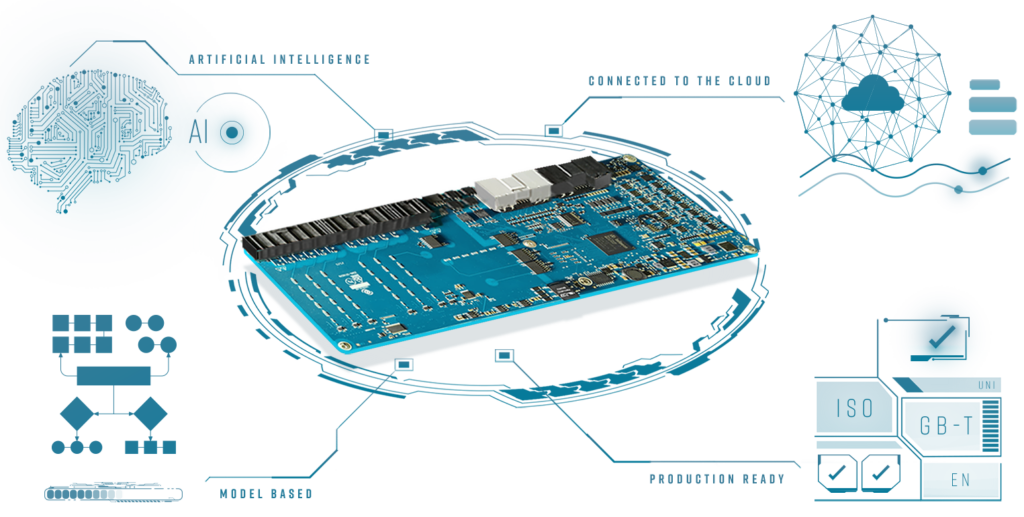
BMSTAR, Eatron’s AI-based battery management product, performs two key functions: predictive cell diagnosis and remaining useful life (RUL) estimation using both local and cloud-based processing.
Although the company focused purely on software at first, interaction with customers showed that there was also a need for bespoke electronic hardware, Genc notes. “EV batteries being a new industry, there’s not enough automotive grade, safe battery management hardware around, so we now develop our own for different applications that go with our software stack.”
This includes BMS hardware for 12V and 48V lithium-ion batteries as well as the higher voltage types. Typically, the boards are divided into a 5V side that looks after the sensing and computing functions, including running the AI and the battery models, and a high voltage side. The latter handles up to 1,000V and contains all the high voltage measurements, diagnostics and isolation monitoring for safety devices. It also has even an integrated emergency pyrotechnic driver, that ensure that, if necessary, the pack can be safely turned off and isolated from the rest of the vehicle, he explains.
“With high and low voltage management on one board, it is designed to automotive functional safety and cyber security standards, all of which require compliant system design, meaning the software, the hardware and their integration have to satisfy all those standards.”
This board is the brain of the main battery control unit and supervises other boards mounted closer to the battery modules that collect and pass on sensor data. Eatron measures the voltage of every cell and the temperature of three or four cells in every module, with a pack typically having 10 to 15 of these smaller boards that, together with the main control unit that handles the heavy computation, make up the full solution.
For battery manufactures and vehicle OEMs that make their own BMS, the company offers licences for specific software functions, such as state of health and state of charge, for integration into their systems, he emphasises.
Since its foundation in 2018, Eatron has grown to 90 people, opened a software house in Istanbul plus sales operations in China, India and Japan, and booked US $3 million in sales last year, says Genc.
ONLINE PARTNERS
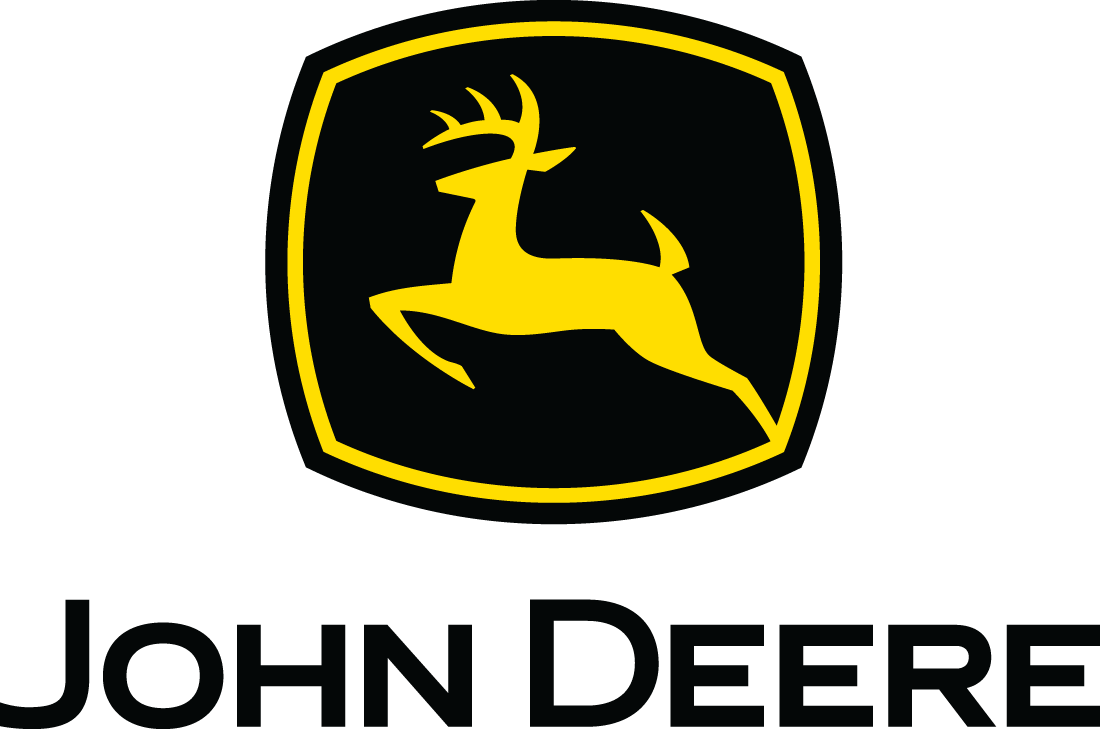
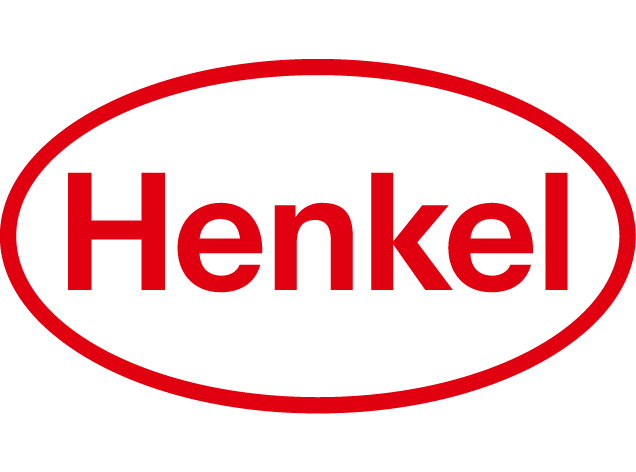
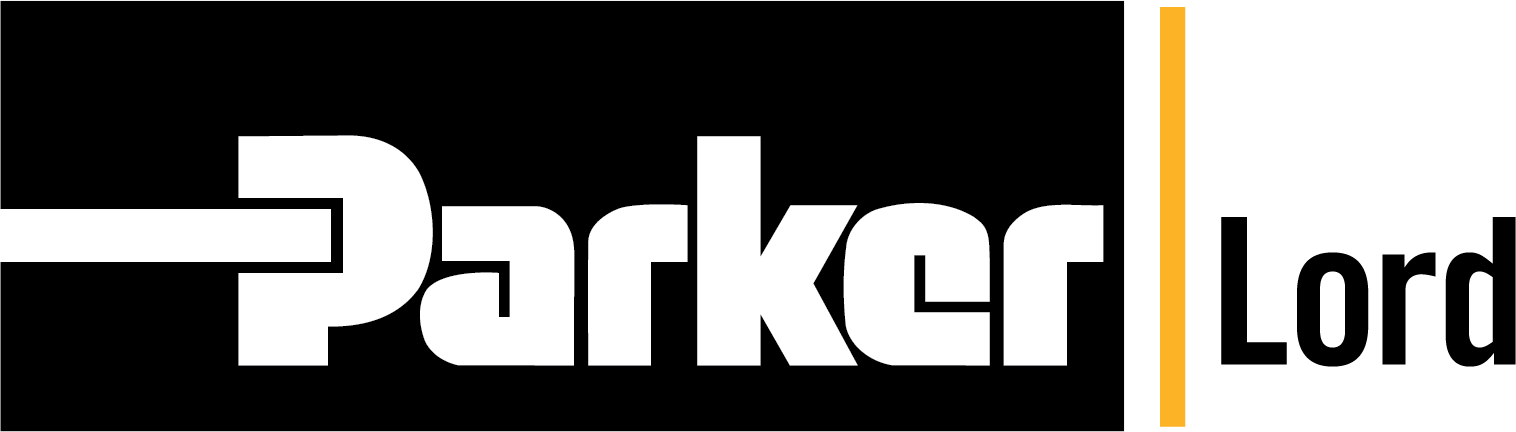
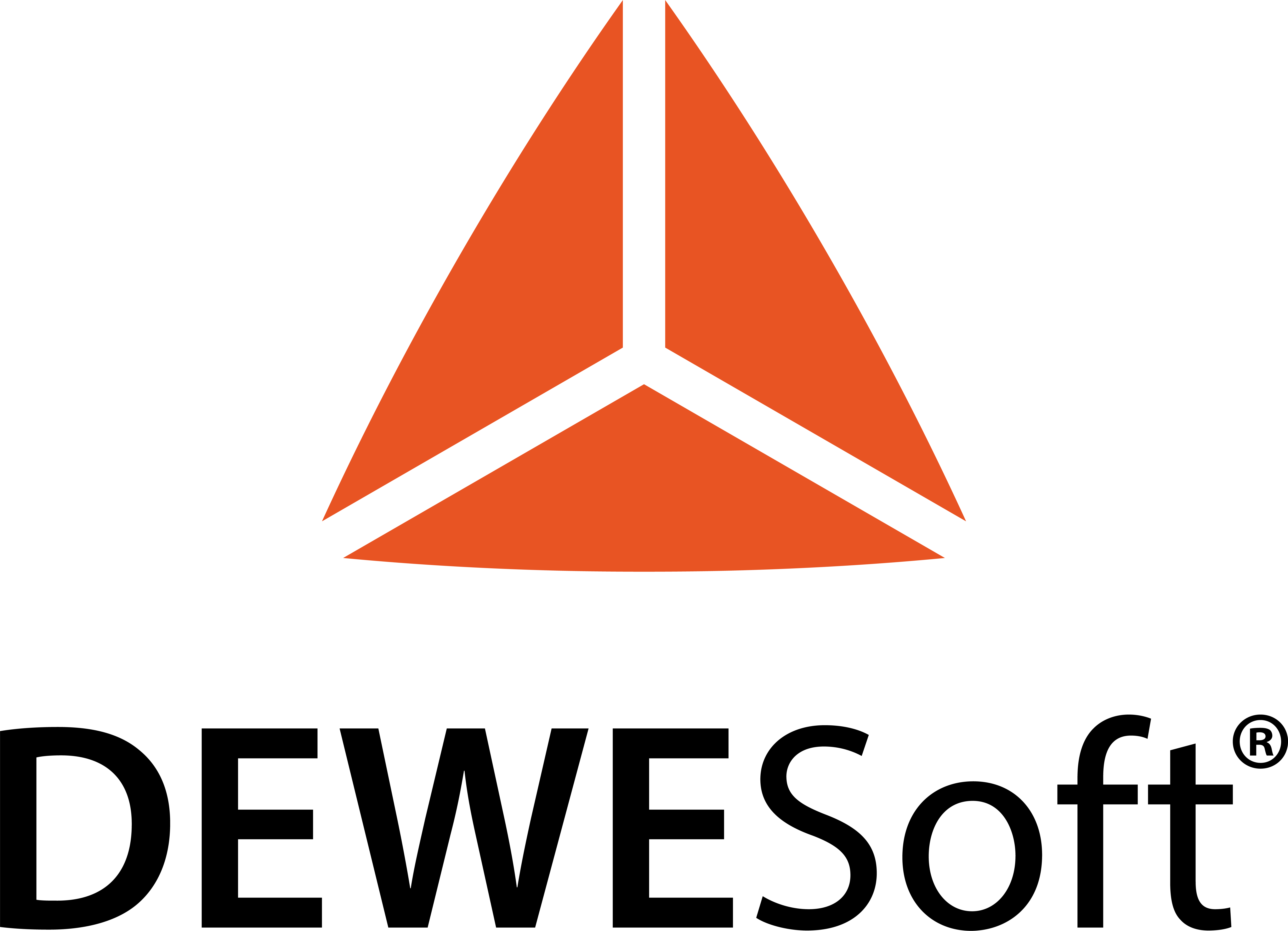
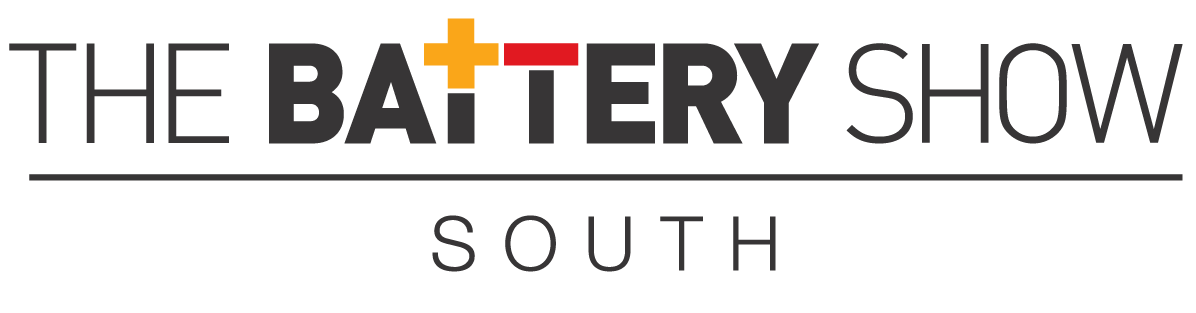
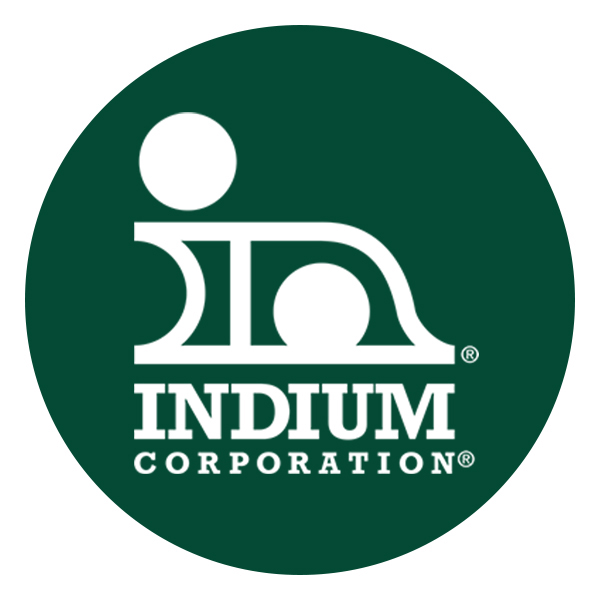
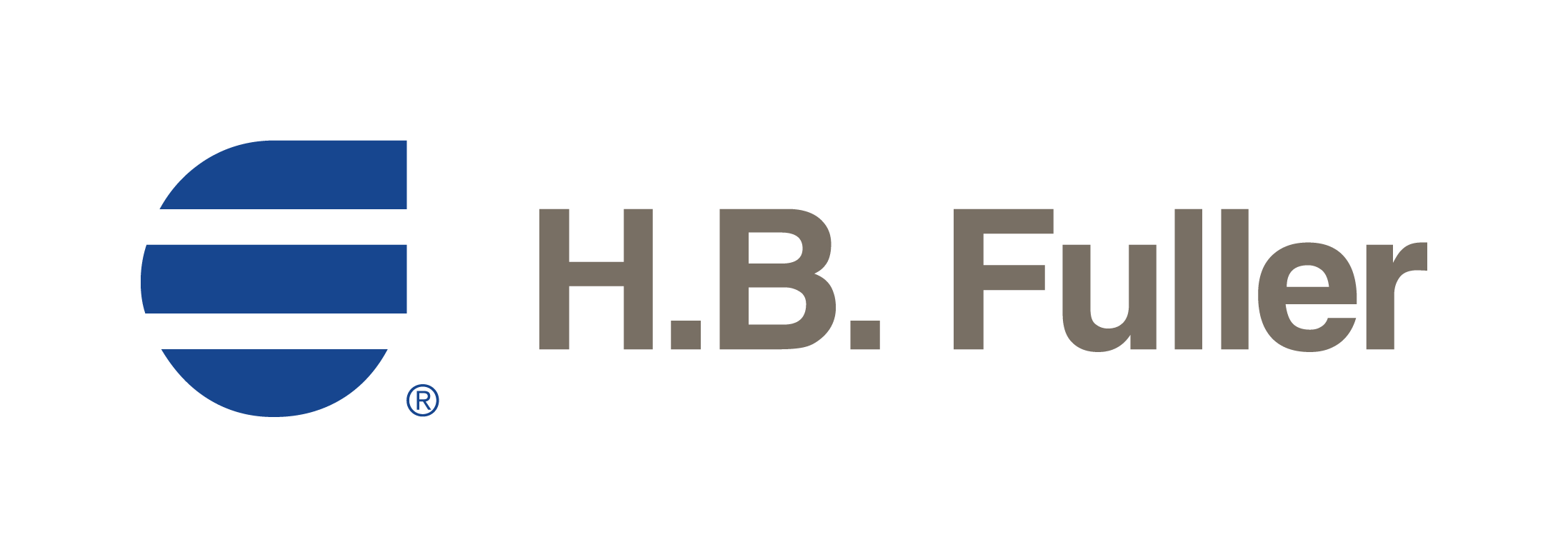