Ricardo’s fuel cell bus takes shape
On 17 August, Ricardo announced that it had received UK Government funding to convert a bus to hydrogen fuel cell power as a technology demonstrator. The vehicle, an Alexander Dennis Enviro400, will be operated by Stagecoach as part of the Tees Valley Hydrogen Hub initiative from February next year. Ricardo’s chief engineer for the conversion, Eric White, discusses the project exclusively with Peter Donaldson.
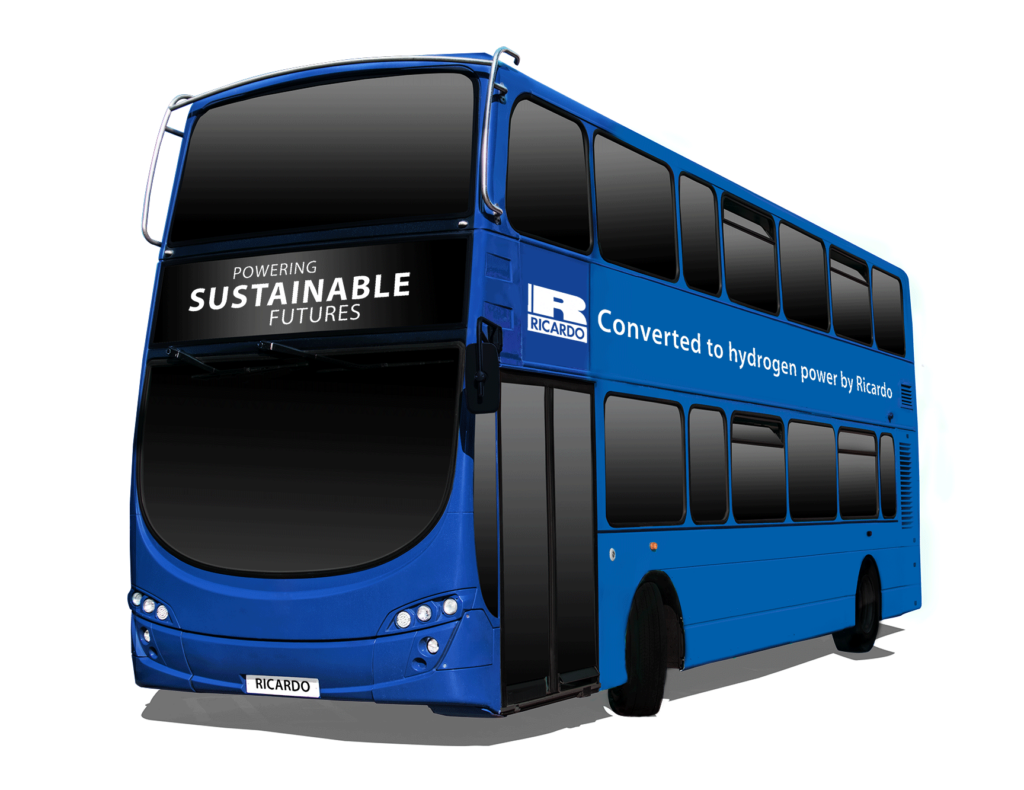
(Courtesy of Ricardo)
As it is a retrofit programme, packaging is one of the major challenges, and the bus has limited space for parts that are quite different in shape from the original powertrain and have different mounting requirements. Also, a fuel cell powertrain is larger than its diesel equivalent. The system is intended to be applicable to a range of buses and so is designed to it into the smallest of them, adding to the challenge, White explains.
“The components that take up the most space are the cylindrical fuel tanks, which weigh 100 kg each and occupy almost the full width of the bus,” he says. “We have designed a modular framework to house these cylinders safely at the back of the bus inside the existing structures, but it means that the back row of seats have had to be sacrificed, although we’ve lost only four passenger seats from the upper deck.”
The number of seats that have to be sacrificed depends on the required range. In this case, that is 300 miles, which demands up to seven tanks depending on the duty cycle. The system also includes a power-buffer battery, which is kept charged by the fuel cell, and regenerative braking so that it does not need external charging.
Constant use and frequent stop-start operations amount to severe duty cycles for bus powertrains, and this application places heavy demands on the small buffer battery to provide instant launch power and to recover energy from braking. Despite the demands placed on it though, White notes, simulations have shown that the required battery capacity is relatively small, at around 30 kWh.
“The whole system also has to be extremely robust, so we are using systems specifically designed for bus applications” White says.
“A hydrogen storage and fuel cell solution these days is considerably lighter and smaller to package than a battery electric solution of equal performance. The sheer size of the batteries in a BEV bus needed to meet the range requirements mean it would not be possible to package as a retrofit without losing a lot more passenger seats,” he adds. “Also, we can fully refuel the bus for a 300-mile range in about 6 minutes.”
The tanks store hydrogen gas at 350 bar. Ricardo has also been researching the use of metal hydrides as a hydrogen storage medium for transport use, but White explains that they chose tank storage for gaseous hydrogen for its availability, maturity, safety, cost-effectiveness and the fact that the system is certified for road use.
“This will be a direct replacement for the mechanical axle,” White says. “As there is no separate motor or driveshafts taking up room, it enables us to package the rest of the powertrain – including the fuel cell, battery and electrified ancillaries – in the engine bay.”
Ricardo has chosen all the major systems, and is now placing orders and doing the detailed design work for packaging solutions for modular retrofits generally and for the Tees Valley Enviro400 in particular. “We are very much looking forward to the demonstration sessions at the end of February 2022,” White says.
ONLINE PARTNERS
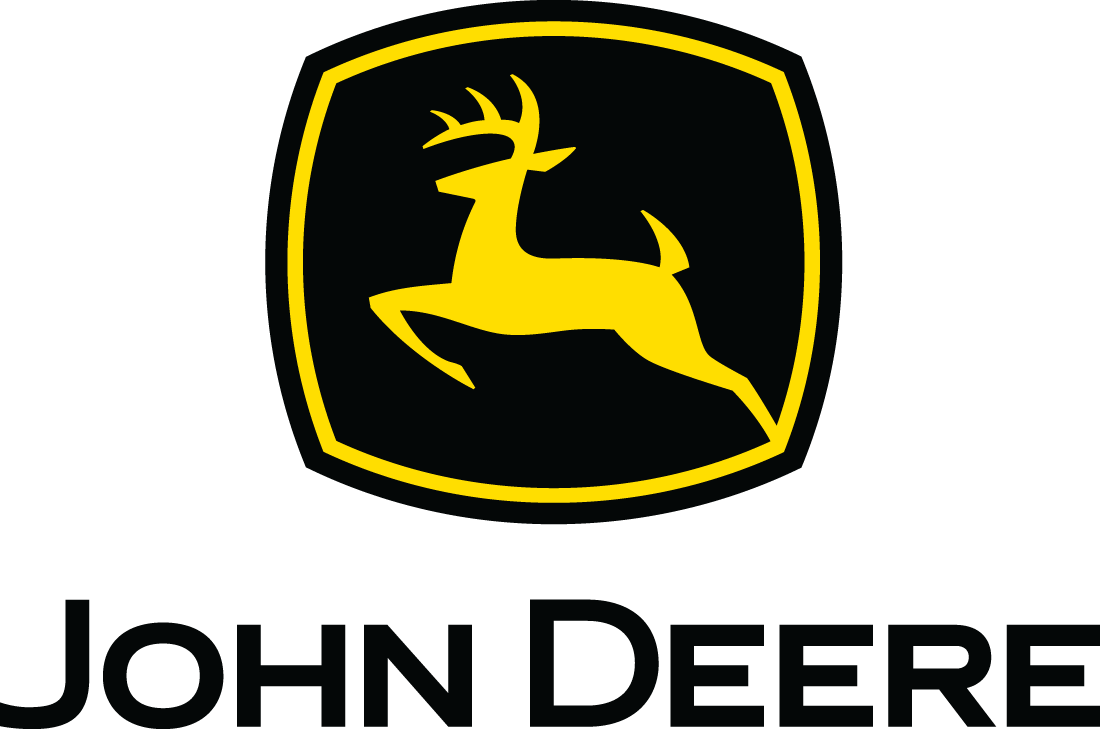
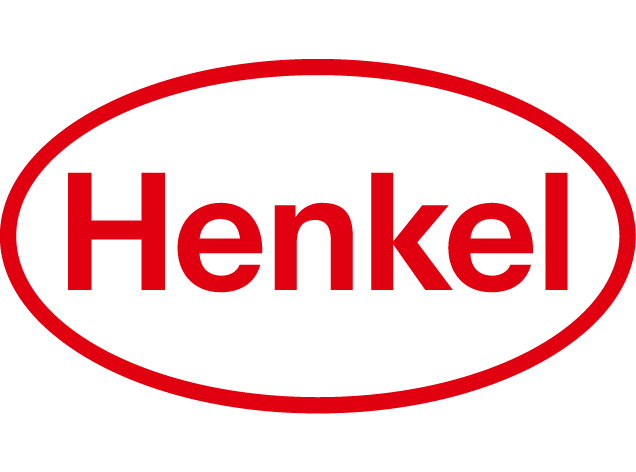
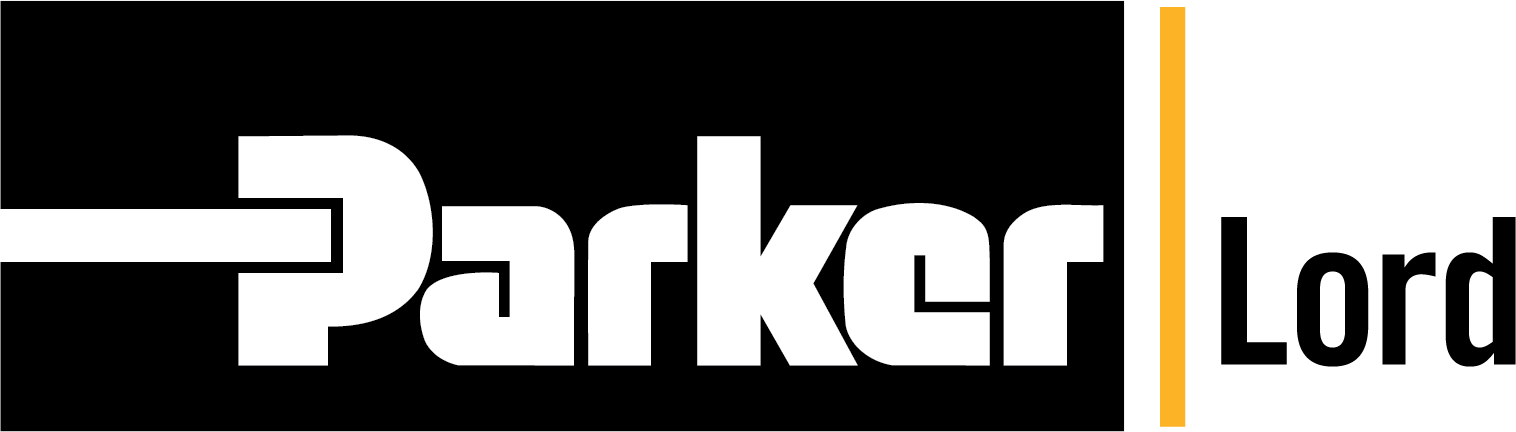
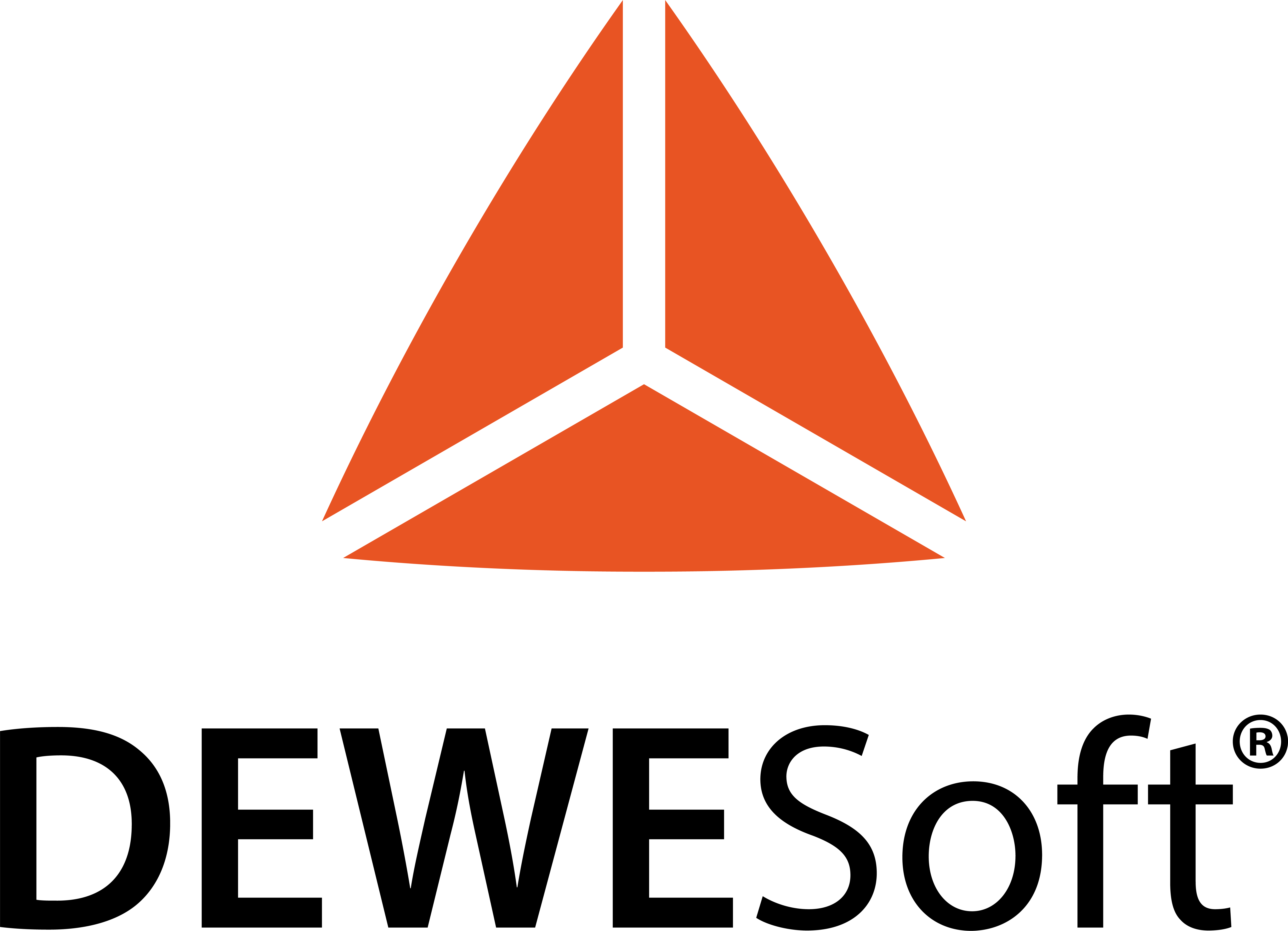
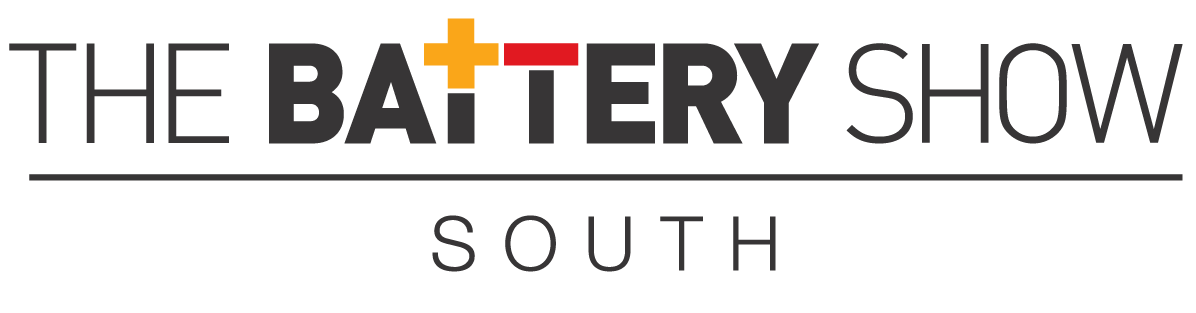
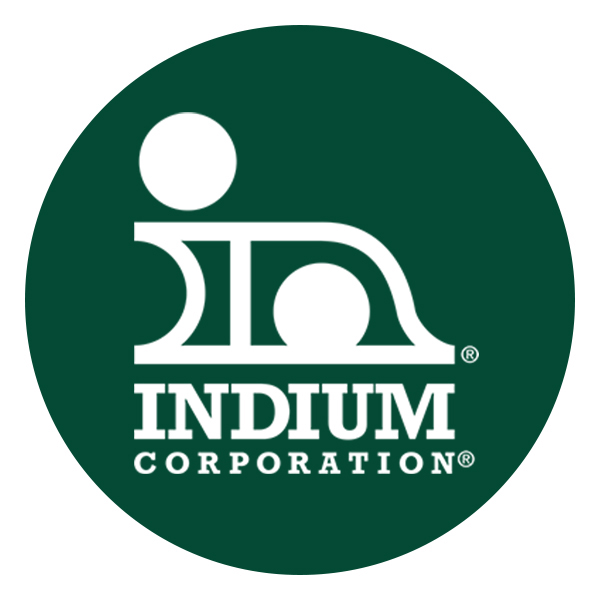

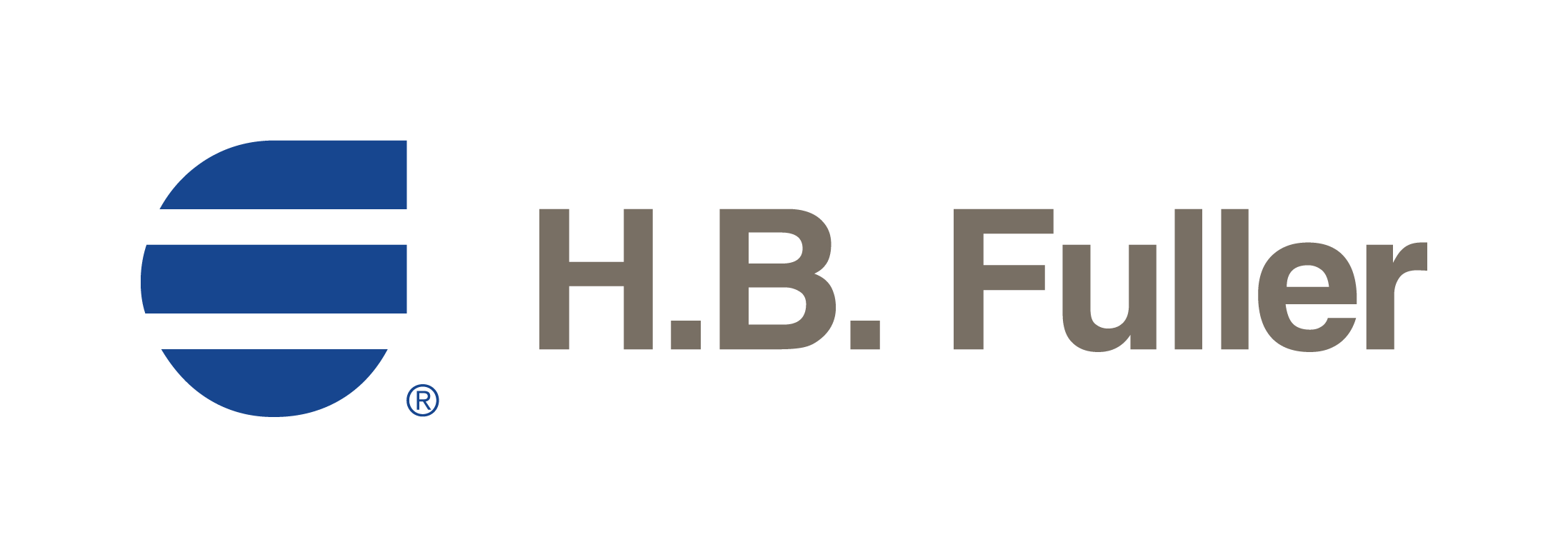
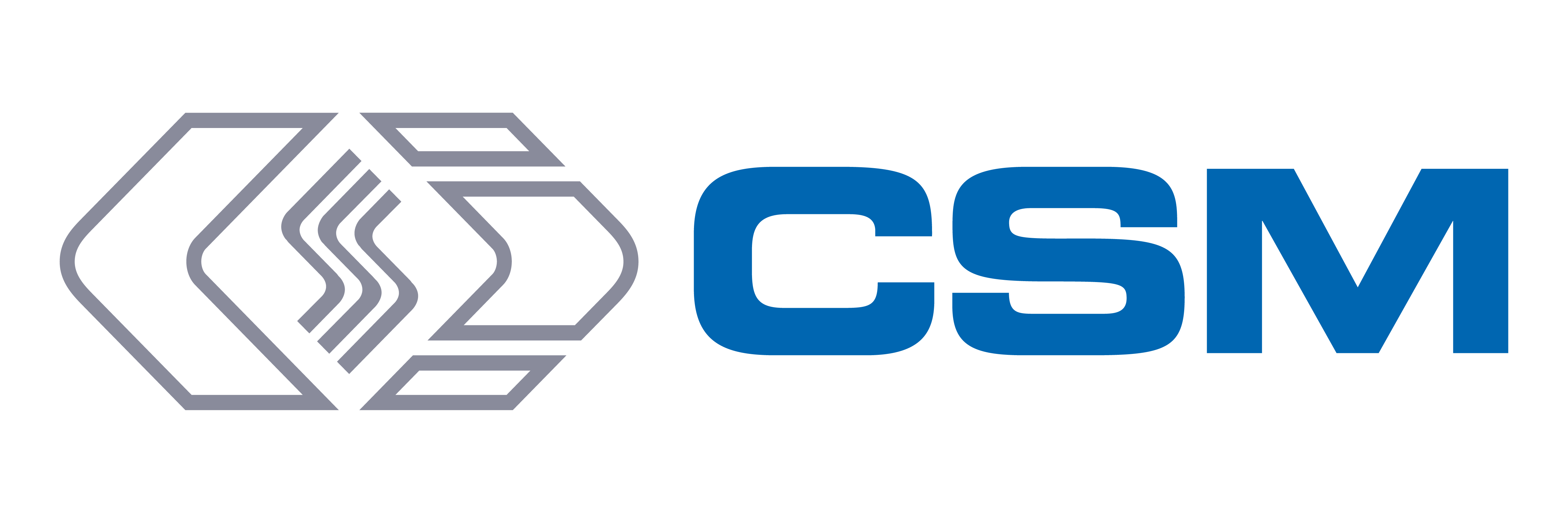
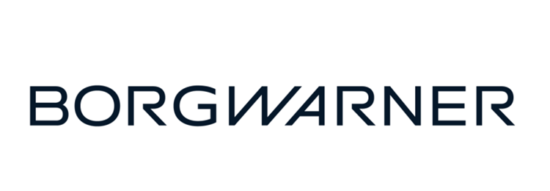