Ricardo Tees Valley hydrogen bus

(Images courtesy of Ricardo)
Route march
With this this hydrogen-electric bus set for its first demonstration run, Rory Jackson talks to its developers about the thinking that went into it
When discussing clean energy technologies, debates can arise over which ones are the most cost-effective, efficient or realistic in terms of how they can be used to help create a better, more renewable future for us all.
Disagreements over each technology’s usefulness can hinder progress towards our shared goal of an efficient, sustainable global economy, something Ricardo knows well. For decades, this global engineering group has honed its engineering proficiencies across gasoline, diesel, hybrid and fully electric powertrains. It has also continually invested in cutting-edge capabilities across CFD, digital twinning, test systems, automated manufacturing and more throughout the wider world of mobility.
Now the company is applying its capabilities to hydrogen-electric power. In August 2021 it announced that it had received UK government funding to retrofit a double-decker bus as a demonstrator for Britain’s first hydrogen transport hub, to be based in the Tees Valley in north-east England. The demonstrator platform is an Alexander Dennis Enviro400 bus, a diesel vehicle that is being converted to run on electricity from a hydrogen fuel cell, and stocked with enough hydrogen gas to cover 300 miles (482.8 km) between refuelling stops.
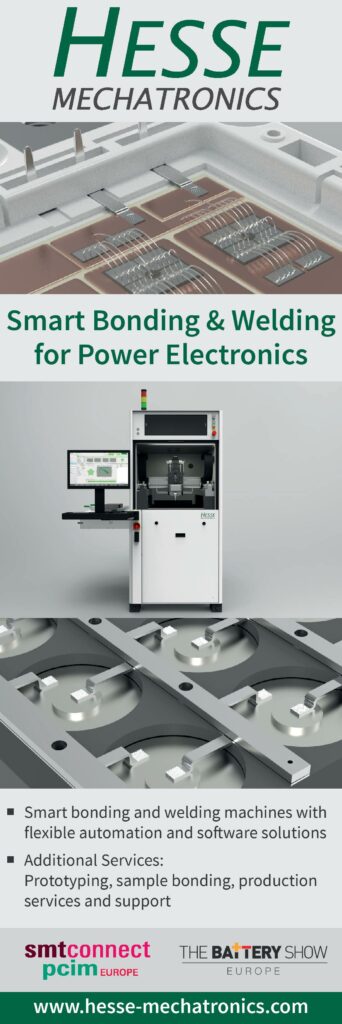
“We very much consider ourselves technology-agnostic,” says Andy Ennever, service leader of hydrogen fuel cell systems at Ricardo. “When it comes to devising the best solution for a mobility problem, we will go with whatever kind of energy medium, componentry and architecture is most appropriate.
“Make no mistake, we absolutely believe battery-electric powertrains have their place, but whether you’re dealing with hydrogen tanks, IC engine-based range extenders or just battery packs alone, the ‘best’ option will always be application-specific. We’ve seen for instance the rollout of battery-electric buses in London, which we expect to continue there, and we think that’s absolutely fine for the capital.”
Where the weather tends to be colder though, battery EVs start to struggle, as the ramp-up in heating requirements essentially causes parasitic losses in the battery’s energy efficiency. Hydrogen tanks by comparison suffer no such loss in the energy density or specific energy actually delivered to the motor-inverter over the course of an EV’s operations.
“The power density of battery EVs really drops in cold weather and becomes dire relative to the amount of energy you can store in hydrogen tanks, and in addition to the more assured range of hydrogen-electric power, there’s the recharging comparison,” Ennever says. “It takes less than 10 minutes to refuel a large hydrogen bus from empty, but it takes hours and hours to replenish the copious batteries needed for moving a heavy vehicle such as a bus for 300 miles.
“So if fleet operators in cold weather are asked to switch entirely to battery EV buses, they’ll be forced to decide between significantly increasing their fleet sizes to offset how many will need to be charging around the clock, or pouring money into some kind of pantograph solution to try to charge them during their operations to keep from operating fewer routes for less hours per day.
“And on the topic of grid infrastructure, charging a bunch of buses all at the same time, even at night when there’s less energy being consumed nationwide, is going to be a huge drain on the grid. In rural locations it’ll be even more of a challenge.”
With these problems in mind, Ricardo has developed its hydrogen-electric powertrain, with the principal intention of developing its fuel cell power unit as a turnkey solution for single- and double-decker buses, and as a drop-in replacement for various existing diesel IC engines. The fruits of its r&d are slated for a first run of the Enviro400 demonstrator this spring.
Development history
The first discussions to produce this kind of vehicle and powertrain began in 2020, and were initiated by the operator Brighton & Hove Buses in the south of England, itself a notable advocate of hydrogen-electric transport.
“They asked if it would be possible in physical and mechanical terms to retrofit some of their buses to run on hydrogen,” Ennever recounts. “That got us to investigate the market, and we discovered that most of Britain’s 38,000 buses run on diesel and last for 15 years or so. With zero-emissions targets coming into force in many areas in 2030, we surmised that there’s a huge business case there, so we started some internal r&d.”
He adds that Ricardo had been investing in hydrogen research for some time, including a £2 million-plus dedicated test facility (to be commissioned shortly) and collaborations such as Cranfield Aerospace Solutions’ Project Fresson, which aims to develop a commercially viable hydrogen-electric powertrain for a Britten-Norman Islander light utility aircraft. Alongside such ventures, developing a hydrogen bus was judged as a strategically suitable goal to pursue.
The team at Ricardo soon engaged with the UK government’s Department for Transport’s Tees Valley Hydrogen Transport Hub competition, and in June 2020 put in a joint submission with the Scottish transport group Stagecoach for a hydrogen retrofit bus, which won funding to produce a demonstrator.
Initial feasibility studies began in July 2020 and ramped up through the August, with rigorous emphasis on system-through-subsystem definition and component selection, as a working prototype was needed within the 6-7 months following the granting of funding in September 2020.
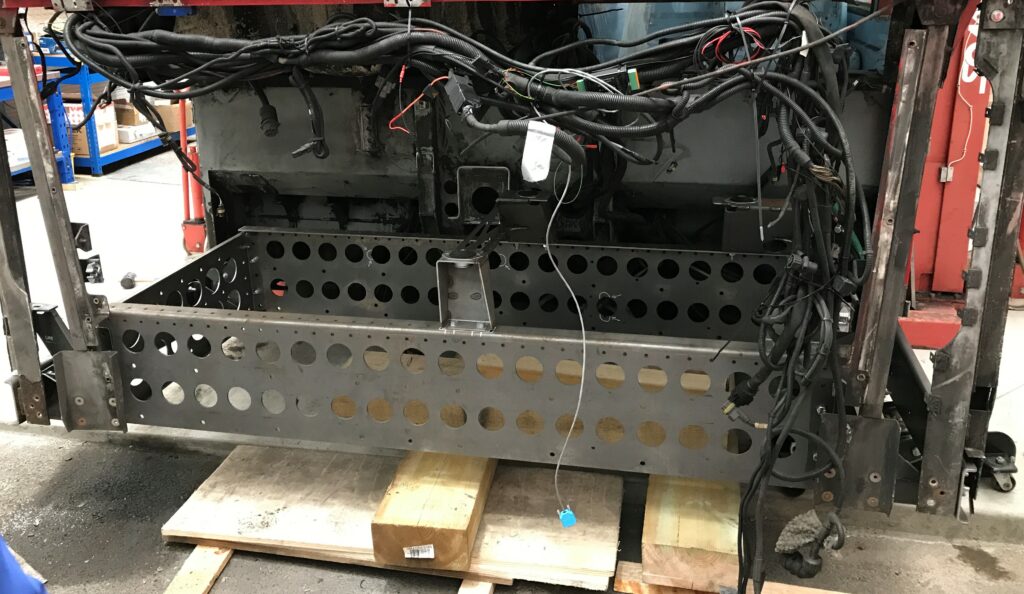
“Then we rapidly moved through the design processes, including defining the powertrain’s mechanical design, control requirements, software programming, thermal management configuration, and a huge amount of packaging exercises, because of course we have to work within a clearly defined set of spaces,” Ennever says.
“When it came to individual componentry, we focused first on defining the long-lead items so we could procure them as soon as possible. Eric White, the chief engineer for the project, oversaw completion of the powertrain design, and our technicians carried out the installation.”
System modelling and architecture
On the design optimisation, White comments, “We developed a vehicle-based simulation to model the behaviour of the bus over a number of drive cycles, and we specifically selected drive cycles that were real, and measured recordings of bus routes to ensure we were using a high-quality digital environment to formulate an accurate digital bus model.
“Then we used Design of Experiments methodology to undertake a lot of simulations and compile them into a database we could then interrogate, to find the optimum fuel cell power, hybrid battery size and other parameters.
“It also allowed us to analyse and understand how things like battery ageing and fuel cell ageing would progress over cycles, as well as investigating the implications for maintenance and total cost of ownership, which are fundamental to the business case for commercial e-mobility engineering.”
Ricardo has therefore opted not to choose components with absolute peak performance metrics, in favour of selecting a blend of components that work together to achieve system-level targets for efficiency, performance, and cost-optimisation.
The Alexander Dennis Enviro400 was chosen as the demonstrator for several reasons. First, it happens to have the smallest, tightest engine bay of most buses. As Ricardo sought to make a turnkey fuel cell powertrain, it followed that if the resulting module could fit the Enviro400, it would fit almost any other bus, with minimised engineering effort to make it do so.
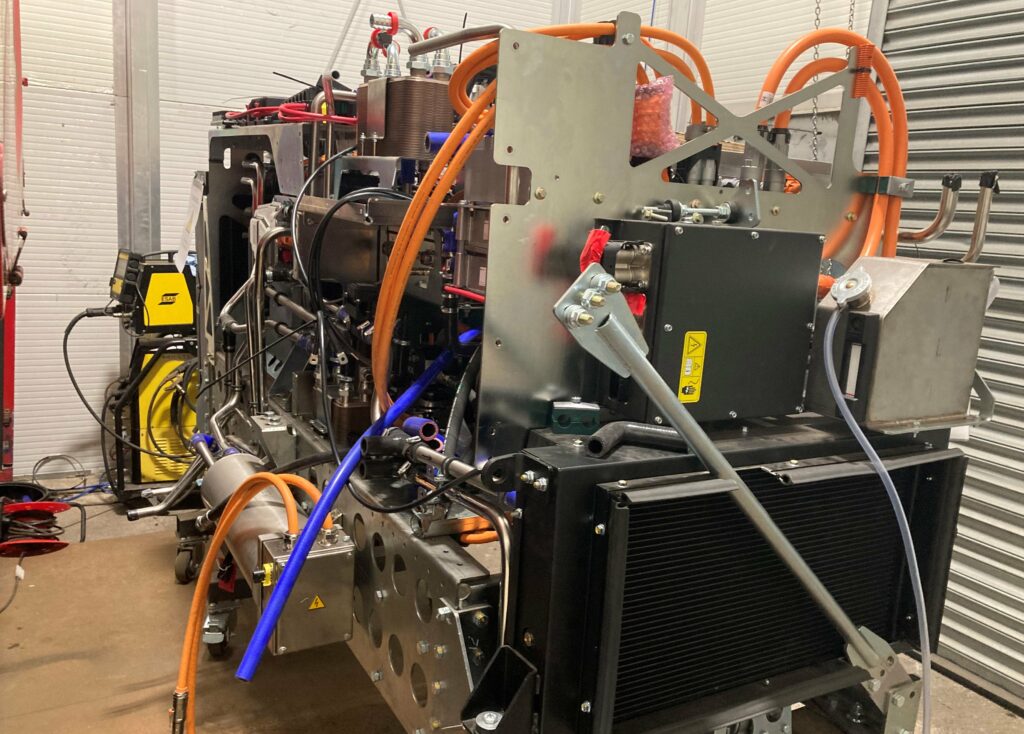
“The idea is that you take out the existing powertrain on any bus, and you can replace it with our fuel cell module and hydrogen tanks as required,” White explains.
The hydrogen tanks are installed at the back of the bus (with five seats on the lower deck removed to make space), and the fuel cell power module is underneath them in place of the Cummins IC engine. Alongside this are ancillary components for electrifying the power steering pump and the pneumatic system for the brakes, suspension and sliding doors. Lastly, an e-axle is installed in place of the mechanical axle.
“We went with an e-axle because there’s no space for a central drive,” White says. “Fitting a separate e-machine coupled with a propshaft going to a separate mechanical axle would have been unfeasible in this bus.”
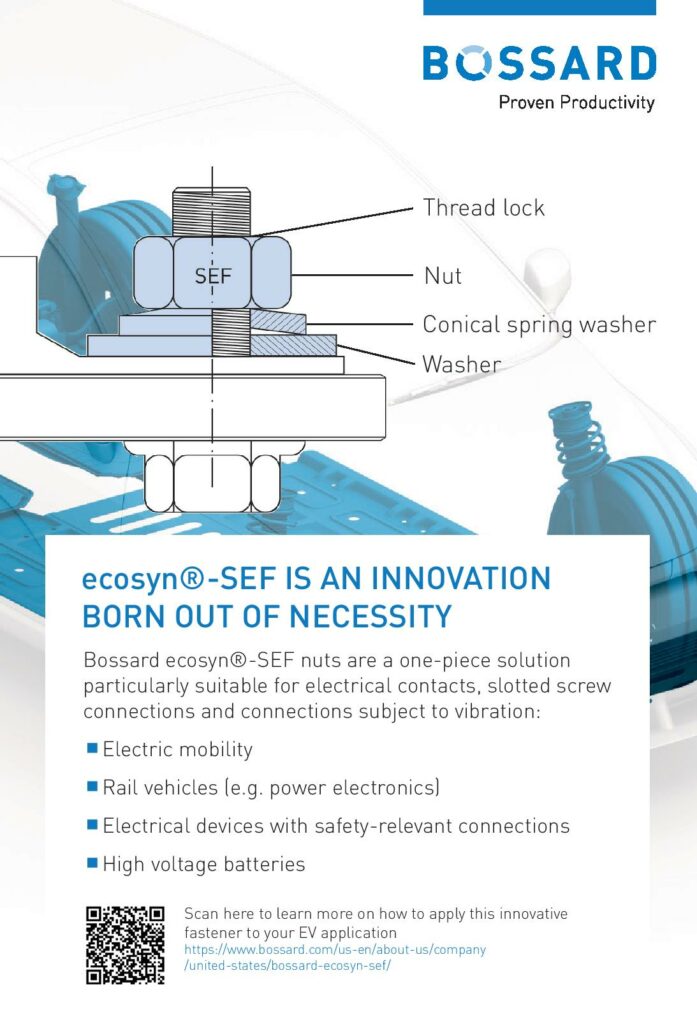
Propulsion
As a result, the e-axle selected is one that was designed as a direct mechanical swap for the previous axle. That made the integration process a simple matter of removing the original axle, taking off the air spring brackets and anti-roll bars, and installing and fastening the new axle.
“The e-axle is designed to run without gearboxes – its e-motors are permanent magnet AC machines designed for direct drive, making the traction system very efficient,” White adds. “And it has built-in inverters to minimise packaging issues, so further integration was a simple case of connecting an HV cable, coolant hoses, and some comms lines from our power distribution unit.
“Each motor is rated to 200 kW maximum for a cumulative 400 kW peak traction output, 20,000 Nm peak torque at start-up, and up to 250 kW and 7800 Nm continuously. Perfectly adequate for a city bus.”
Ennever adds, “Omitting gearboxes isn’t just advantageous for power efficiency, it also makes the ride a lot smoother for passengers, and in the long run makes for fewer points of failure, lower lubrication costs, smaller inventory requirements and other maintenance advantages.”
Power delivery
As with the vast majority of hydrogen-electric vehicles, energy is fed to the motor-inverter via a battery, which in turn receives current output by a PEM fuel cell.
The fuel cell is from an undisclosed supplier as a complete unit, with the balance of plant (BoP) already integrated, onto which Ricardo installs a liquid-cooling system. It was selected from a range of models and suppliers, which were weighed against each other for power, stability, cost, IP rating and other parameters.
“When we go to production for this powertrain, we anticipate having a lot more empirical data and experience informing what we want in our fuel cell, and we will continue to review the latest fuel cell breakthroughs and components for the performance they could give us, so it might very well change to a very different model by that time,” Ennever explains.
“Packaging, efficiency and power density are all important metrics for that, and we’re watching advances closely for anything that will significantly boost those. Something like, say, ramp rate or response rate isn’t as important because the energy output is stabilised via a battery.”
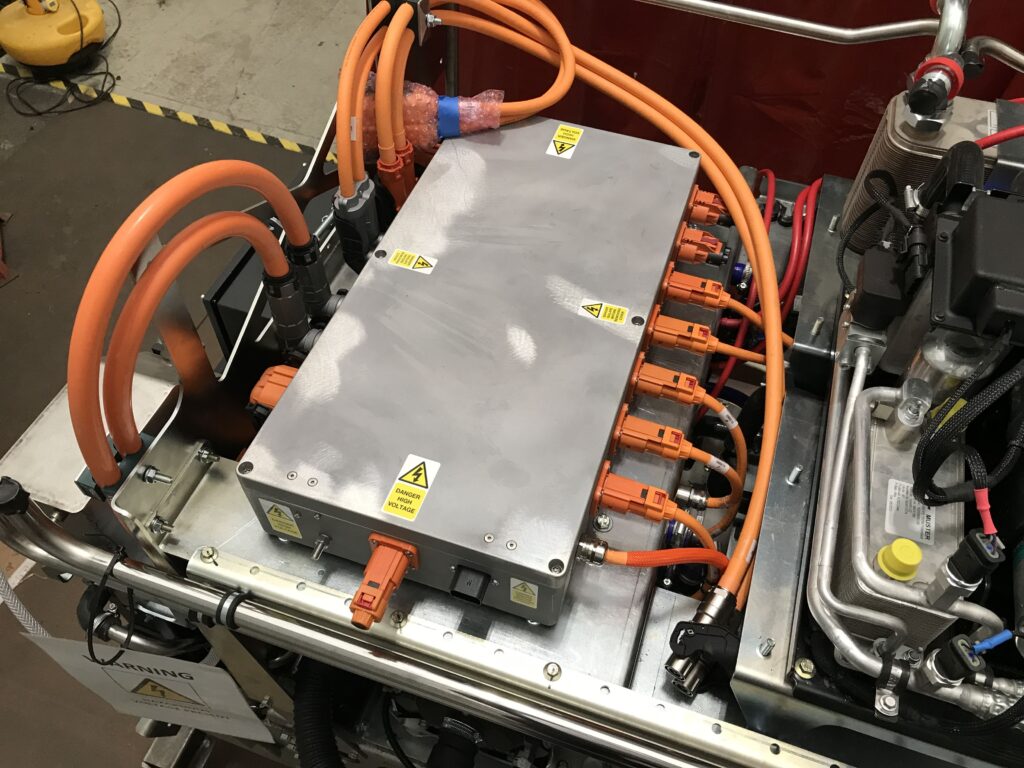
At the time of writing, two 655 V NMC battery packs had been installed, each sized for 33 kWh of energy capacity and 150 kW peak power output, hence a total of 66 kWh of energy storage (on top of that stored in the hydrogen tanks) and 300 kW (407 bhp) total peak powertrain output, with 100 kW continuous output collectively.
Theoretically, the capacity and power output of the batteries could have been smaller, as batteries sit in hydrogen-electric powertrains primarily to store energy regenerated during braking. They can also ensure a stable voltage input for the propulsion systems, although a DC-DC converter covers that in the Ricardo bus.
The team notes however that the battery being oversized for the bus’ performance requirements enables the battery to be exercised’ over a wider range of calibrations with the fuel cell, enabling more rigorous r&d and a larger body of testing data to be gathered for informing future powertrain configurations (which after all is one of the key purposes of a prototype).
“We were keen to have one that was road-certified to ECE R100, as that gives you much more confidence when it comes to making your EV and powertrain road-legal,” White adds.
“Where we most wanted to focus our engineering was in maximising the range gained from our fuel source. So we try to operate the fuel cell in its area of best efficiency. That is likely to be between 30 and 50 kW, or around half its peak power output of roughly 80 kW, and the battery fills in the peaks and troughs.”
The powertrain in the bus (and future iterations of it) is anticipated to be flexible depending on the application. For instance, the size of the fuel cell, including its number of cell layers or quantity of platinum, could be increased and the battery decreased for a longer range or busier route where higher constant power is needed.
In line with that flexibility, a large bespoke HV fuse box has been developed that serves as the power distribution unit. It connects to both batteries and the fuel cell, and supplies 655 V to the various points of consumption on board. These include the pneumatics for the doors, brakes and suspension, the hydraulics for the assisted power steering, a heat pump (to keep the battery and power electronics at their comfortable temperatures), and the inverter for the e-axle.
“And a DC-DC converter brings the HV from the fuse box down to 24 V for the control systems,” White adds.
Control systems
Ricardo has installed two main CAN buses: one for integrating e-mobility components with the rest of the vehicle’s systems, the other one local to the fuel cell module, which itself has 17 low-level control units for the cells, current output, and BoP.
The fuel cell comes with its own ECU for managing these controls, which along with the battery’s BMS and several low-level ECUs for thermal management, power distribution and so on are managed by a single, high-level VCU designed by Ricardo for managing system-wide data and power.
“There are seven other CAN buses which are used for specific, localised control comms in various areas of the fuel cell module,” White adds. “The VCU was created using our VICS [Vehicle Integrated Control & Simulation] development tool, a software system for quickly developing control solutions.
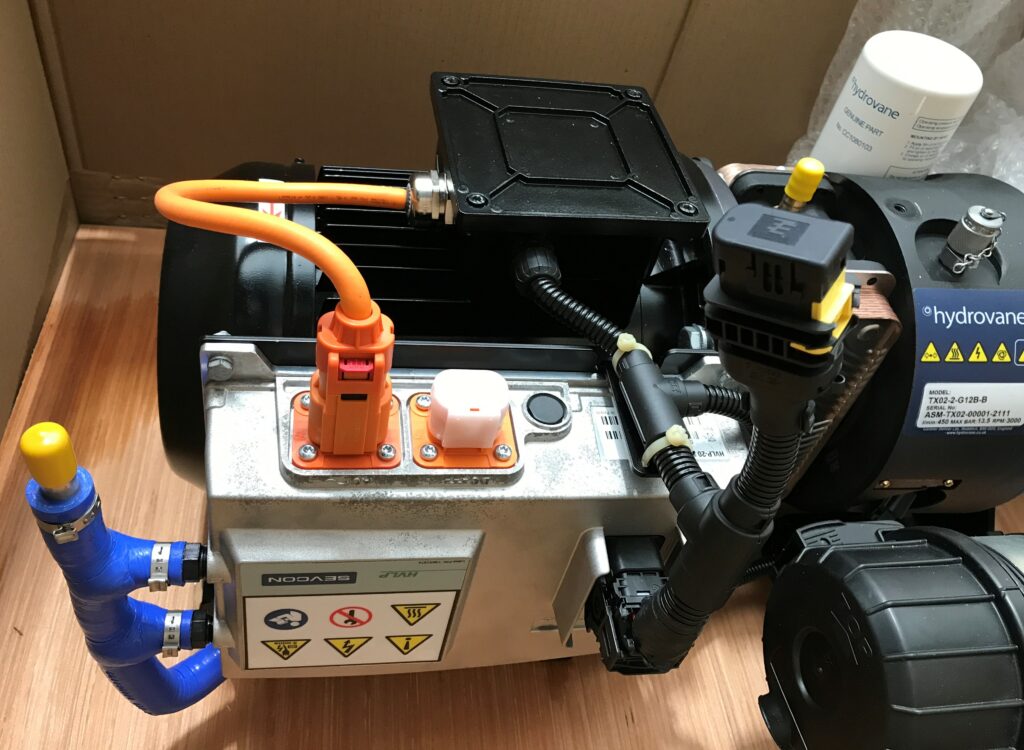
“It isn’t just for making control systems but also model-in-the-loop development to de-risk new software architectures, by gauging whether the control system actually has full control with correct functionality over subsystems, before moving to hardware in the loop.
“That’s great for simulating individual component additions or swaps, such as putting in a new accelerator pedal or cooling fan, to see early on if your VCU will accurately control those things without any malfunctions. It makes project development very efficient, and minimises how much work you need to do to get a robust, working EV with minimal downtime.”
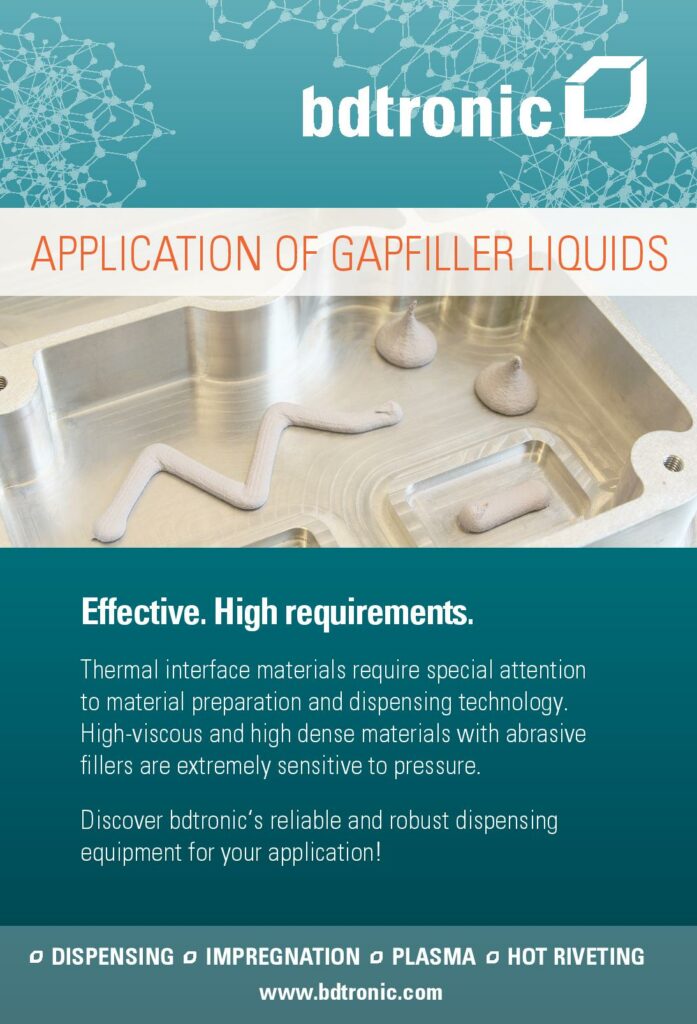
It was also through this tool that the team determined how best to integrate the VCU with the ECUs for all the other onboard systems. That includes the ECUs for the e-axle, fuel cell, the BMSs, a multi-string manager ECU (which serves to manage the interactions and behaviours of the two packs and BMSs), the brake resistor, the thermal management system’s various fans, pumps and actuators, the ABS and the various pneumatic and hydraulic ancillaries.
Information collected on these can be monitored by the driver through a new display installed separately from the existing dashboard, with live data including the amount of hydrogen fuel left and the state of health of different subsystems. Alerts will sound and actions recommended if any health discrepancies are detected.
The VICS software is now in its production stages for use in other future applications, having been taken from a base tool to an adapted, specialised program for this project.
Energy storage and infrastructure
“Each tank can be fitted either alongside each other, on top of each other, or in other arrangements in an array of, say, five to seven tanks,” White says. “You can tune that to the amount of space you have and the range you’re trying to achieve, but the tanks take up a fair bit of space, so different integrators will need to decide for themselves if they want to remove some seats to fit even more tanks.”
A total of five tanks sit in Ricardo’s demonstrator, equating to a total of 25 kg of hydrogen gas. They are supplied by Luxfer Cylinders, with each tank weighing about 100 kg empty and measuring roughly 200 cm long and 40 cm in diameter. They are Type III tanks, meaning they are made from carbon fibre with a metal liner.
These are designed for hydrogen gas pressurised to 350 bar; though some companies such as Toyota are pursuing 700 bar (and Luxfer do offer 700 bar hydrogen tanks), 350 bar remains the most common pressure level chosen and hence the easiest to find certifiable components for.
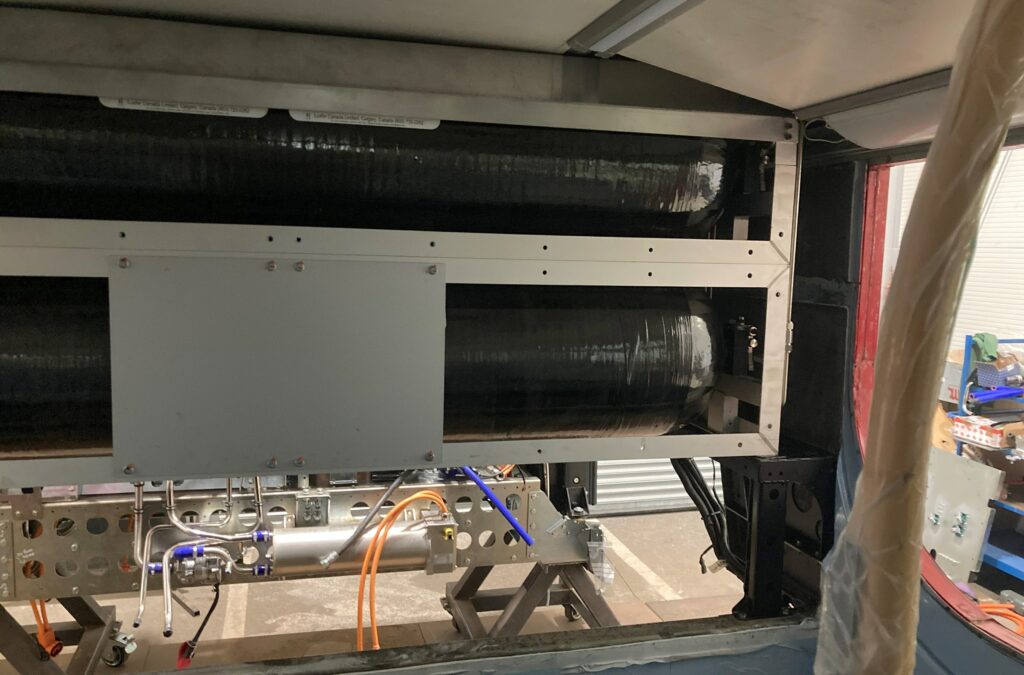
Ennever adds, “For a mid-size car like the Mirai, there’s sense in going to 700 bar, because you don’t have a lot of space on board for a great big 350 bar tank; you need to cram as much gas into as small a space as possible. But for buses, it comes down to a cost-trade-off. If prices for 700 bar cylinders and fittings drop close to those of 350 bar parts, it’ll make more sense to switch because you can reduce packaging volumes, intrude less into the bus and maybe get more passengers on board, making it financially worthwhile.”
Lastly, a fuel plate sits below the tanks for refilling them, positioned at a similar height to where the diesel fuel input had been.
Future plans
With the powertrain defined and engineered, the team is now working to validate the system and ensure it is ready for its demonstration run. Once that is done, Ricardo’s focus will be on final confirmations of the business case for the project before it decides to move towards productionising the powertrain – and Ennever and White are confident that this will go forward.
“When you look at the deployments of battery EV buses that operators across most of Britain are buying, they are specifically running them on their lighter duty cycle routes,” Ennever notes. “Given the limitations of that strategy and of battery technology, I think we’re all going to see a lot more hydrogen buses start to appear on the road in the years ahead.”
Specifications
Ricardo hydrogen-electric bus powertrain
Platform: Alexander Dennis Enviro400
PEM fuel cell
Peak power output: 400 kW
Maximum continuous power output: 100 kW (from battery; fuel cell is about 80 kW)
Operating power output: 30-50 kW
Onboard energy storage: 832.5 kWh (898.5 kWh including battery packs)
Hydrogen storage pressure: 350 bar
Hydrogen fuel storage: 25 kg
Some key suppliers
Hydrogen tanks: Luxfer Cylinders
DC-DC converters: InMotion
Batteries: AKASOL
Heat pump: Webasto
Electric heaters: Webasto
E-axle: Saietta
ONLINE PARTNERS
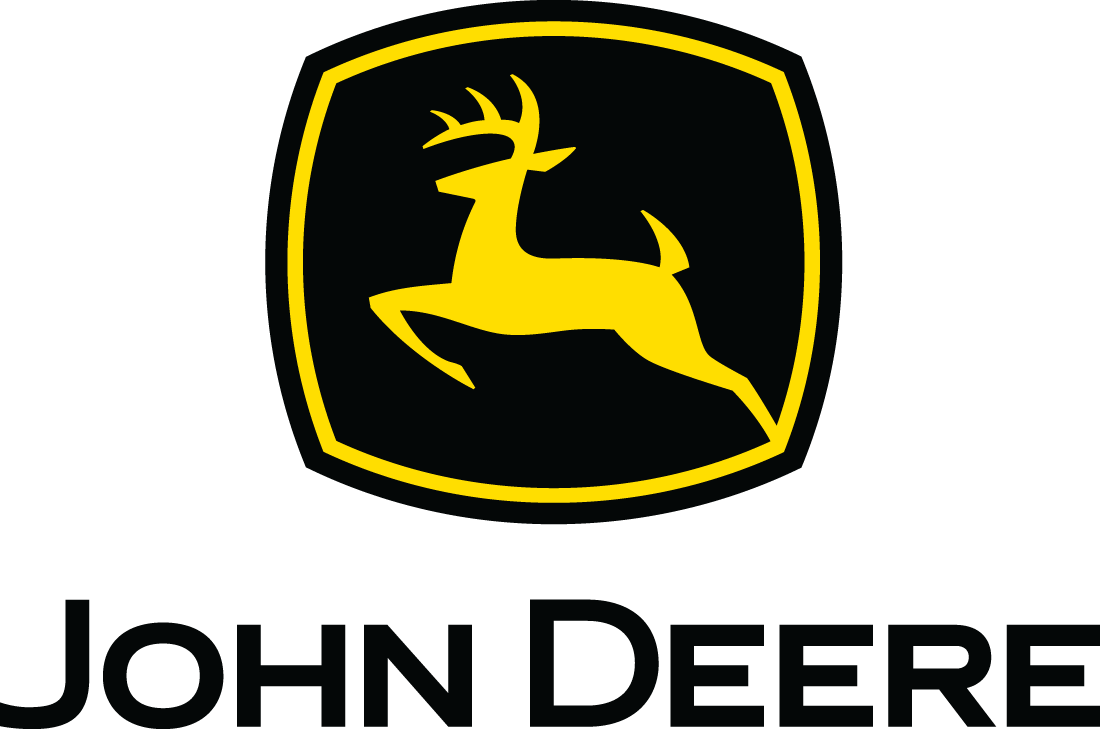
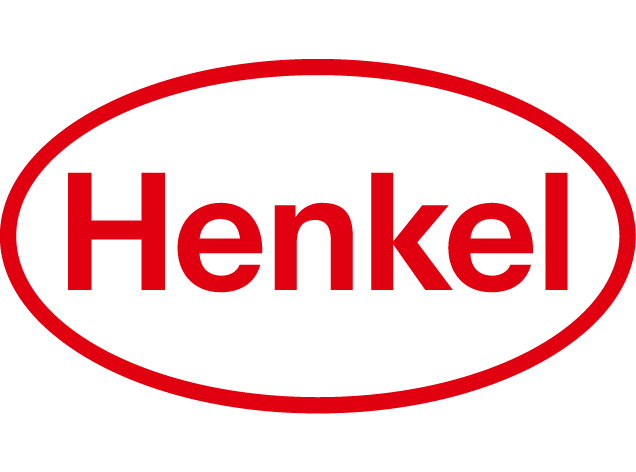
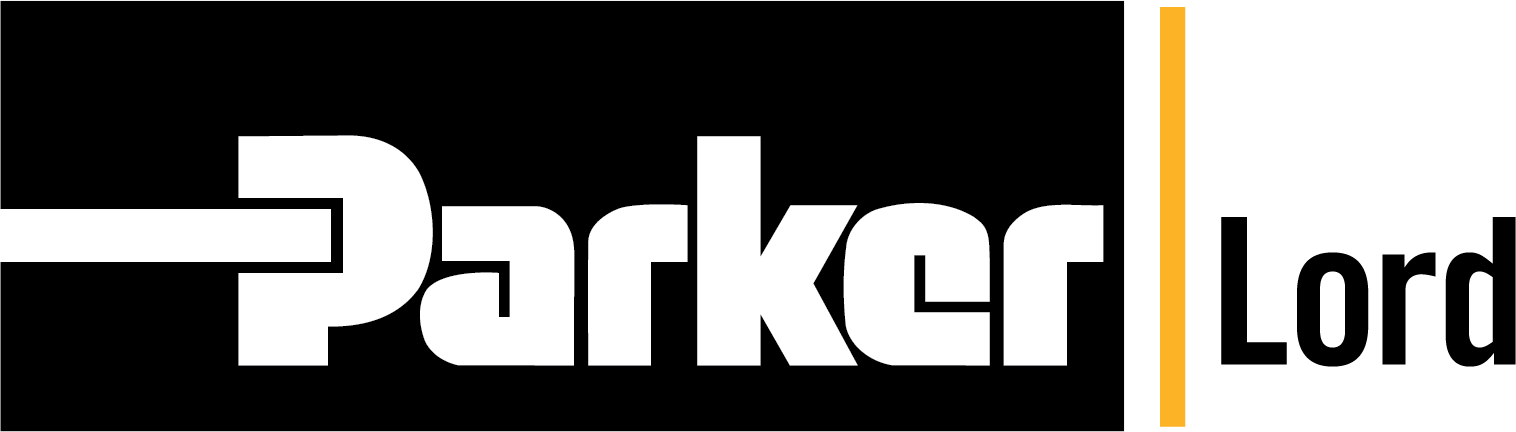
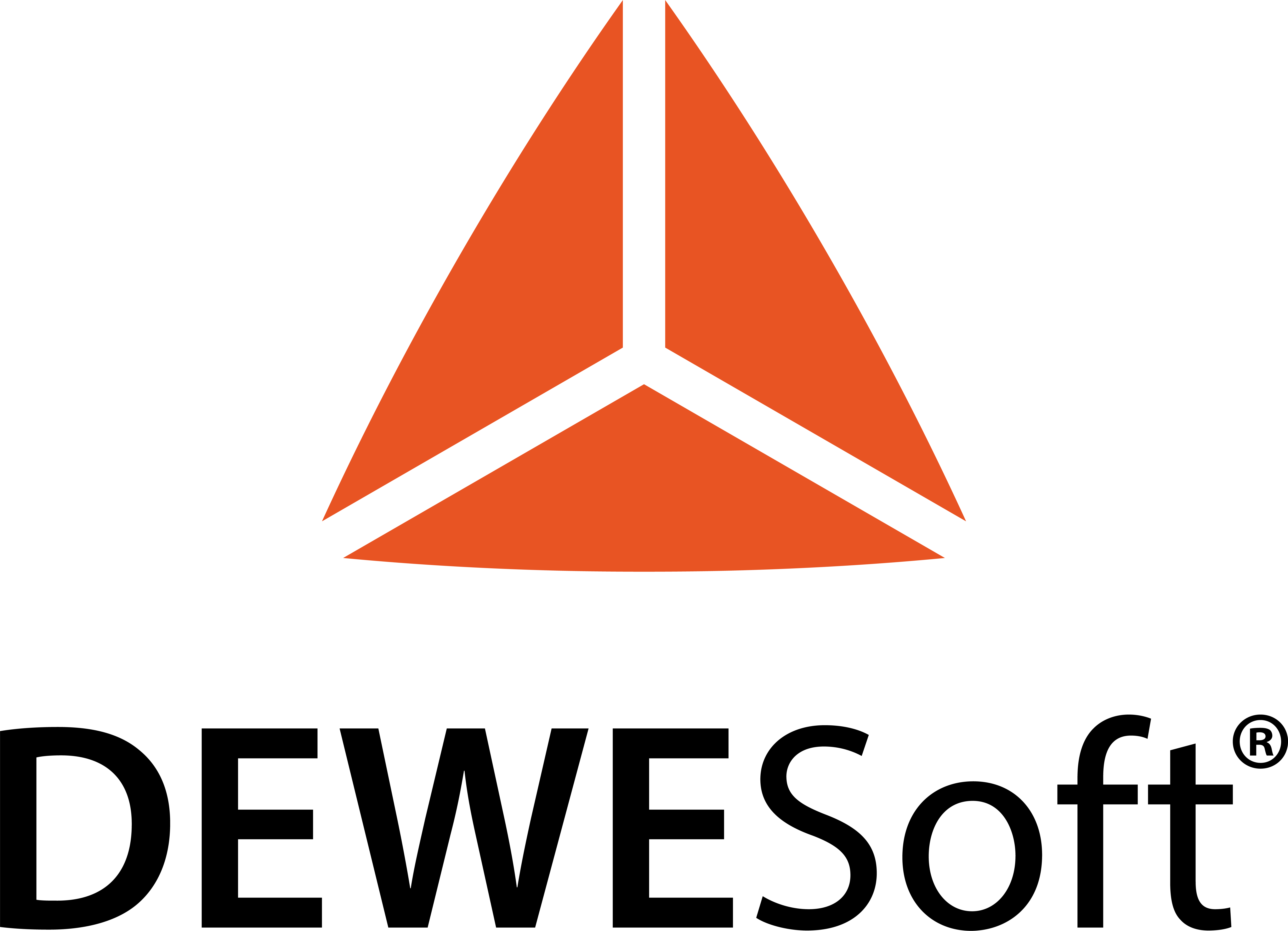
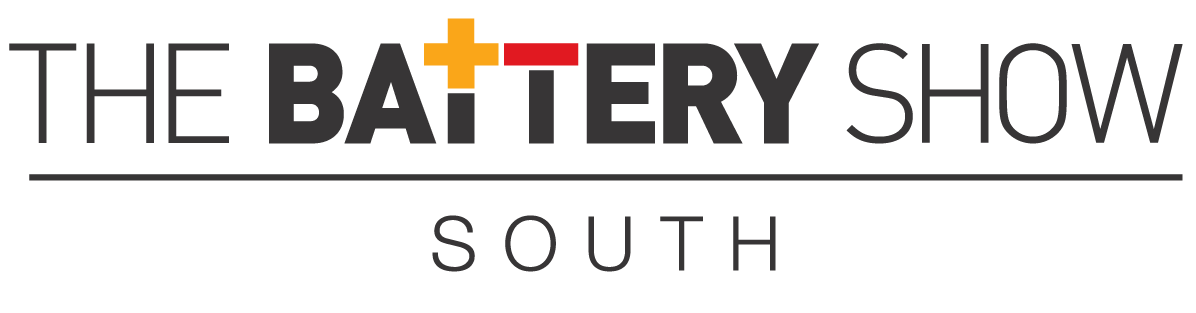
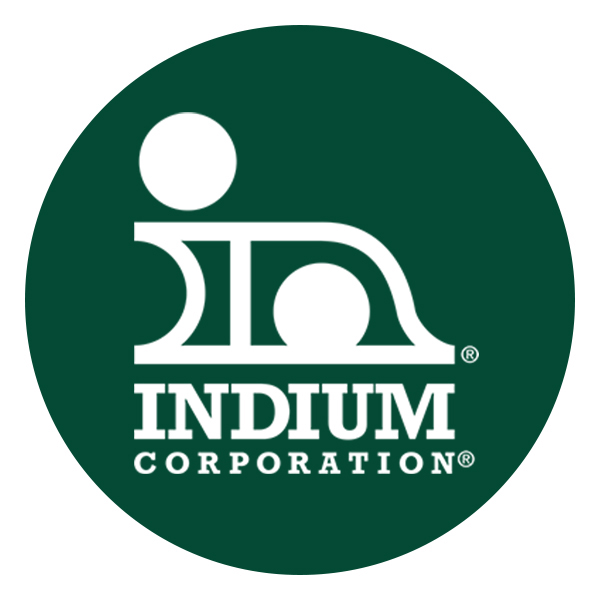
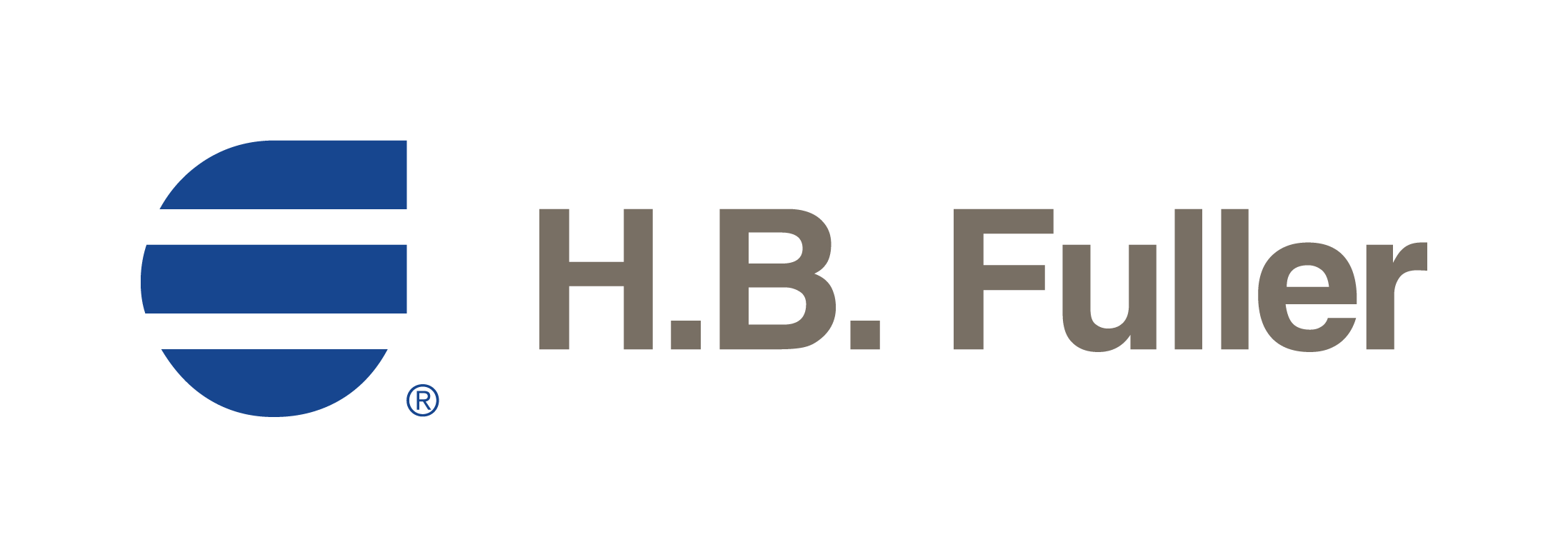