Superconducting aircraft motors
Power density and power-toweight ratio have always been very near the top of the list of essential attributes for aircraft propulsion systems, particularly in those elements that work at the sharp end of converting stored chemical energy into thrust (writes Peter Donaldson).
Rockets aside, the gas turbine engine has yet to be beaten in this respect. In the electrified commercial airliners of the future therefore, the electric motors that are expected to spin their fans and propellers will have to step up to the gas turbine’s level if the aircraft are to match the speed, range and payload capabilities achieved today while bettering their efficiency and carbon dioxide footprint.
The Advanced Superconducting Motor Experimental Demonstrator (ASuMED) project is on the cusp of testing what it describes as the first fully superconducting motor prototype designed to achieve the power densities and efficiencies needed for hybrid-electric distributed propulsion (HEDP) in large civil aircraft of the future. The demonstrator is to be rated at 1 MW at 6000 rpm with a power-toweight ratio of 20 kW/kg, 99.9% motor efficiency and better than 99% system efficiency, with a view to scaling it up to 10 MW or more.
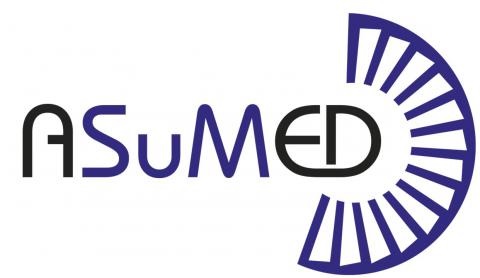
Funded by the European Commission, an industrial and academic consortium of 10 members is developing an innovative motor topology and key subsystems including a stator and rotor, a magnetisation system and a light, highly efficient cryostat to surround the motor.
The consortium consists of RollsRoyce, Oswald Elektromotoren (leading the motor development), Cambridge University, Karlsruhe Institute of Technology, the University of Applied Sciences Aschaffenburg, the Institute of Electrical Engineering in the Slovak Academy of Sciences, Demaco Holland, SuperOx, Air Liquide and K&S Project Management.
The term ‘fully superconductive’ here refers to the chosen synchronous, radial flux motor topology in which both the stator and rotor are superconductive. Tapes made from the high-temperature superconductive (HTS) compound yttrium barium copper oxide (YBCO) seem the most likely choice to form the windings for the stator and the stacks (sometimes called bulks) that create the rotor magnets.
These superconducting magnets can take advantage of the YBCO tape’s ability to sustain persistent currents that correspond to trapped magnetic fields. One of the fieldtrapping technologies under investigation is field cooling, in which steady and strong magnetic fields are applied using superconducting coils to magnetise the stacks.
These can be the stator coils or separate dedicated ones. A magnetic field that is ‘trapped’ remains in the magnet stacks even after the applied field is removed.
The extreme current density in the stator coils, combined with the flux density trapped by the superconductive magnets, will result in the highest power density of all the options explored, according to the ASuMED team.
HTS materials such as YBCO have critical temperatures below 93 K (-180.15 C), so the motor has to be housed in an enclosure – the cryostat – to keep its temperature stable and below critical. Dropping the temperature as far below critical as is practical maximises the current density that the tapes can hold, increasing the motor’s power and efficiency.
After a complex process to choose the cryostat type, the team opted to use separate ones for the stator and the rotor, with the latter housed inside the former – reflecting the topology of the motor. The two cryostats also use separate cooling circuits and different cooling media, requiring highperformance seals and bearings. The stator cryostat uses liquid hydrogen that moves through the cooling passages by capillary action, while the rotor uses gaseous helium in a forced convection process.
Ground tests by Oswald Elektromotoren are due soon, and should provide the first hard indications of whether airliners with HEDP are a truly practical proposition.
ONLINE PARTNERS
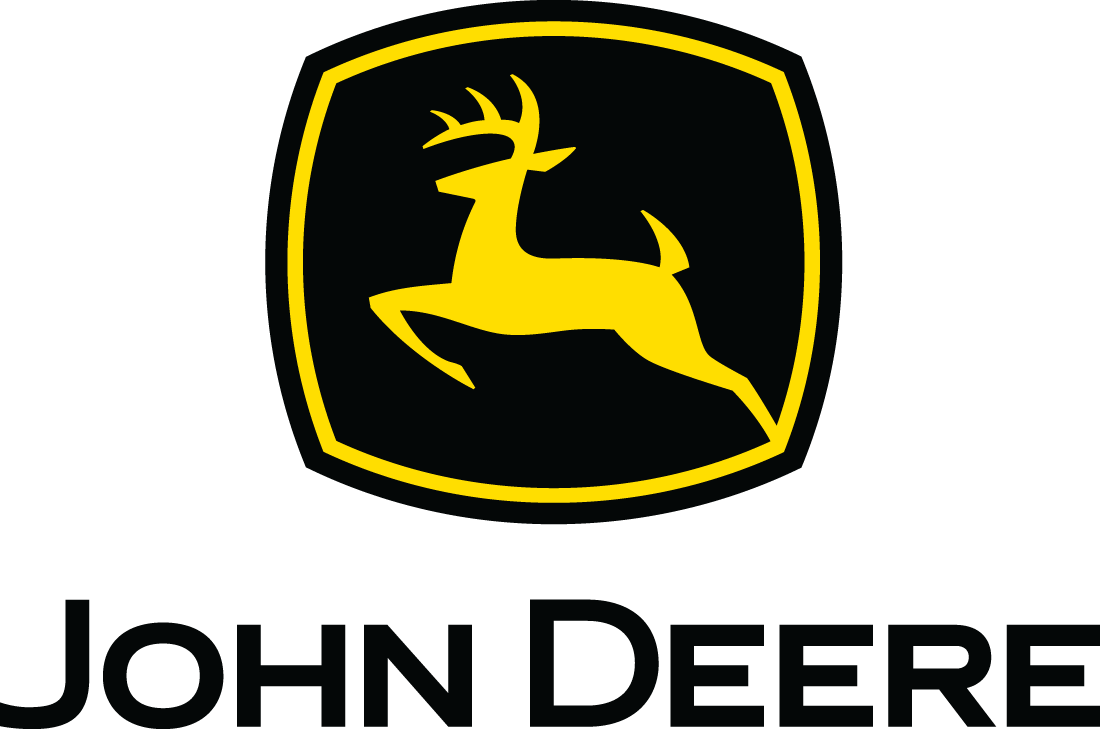
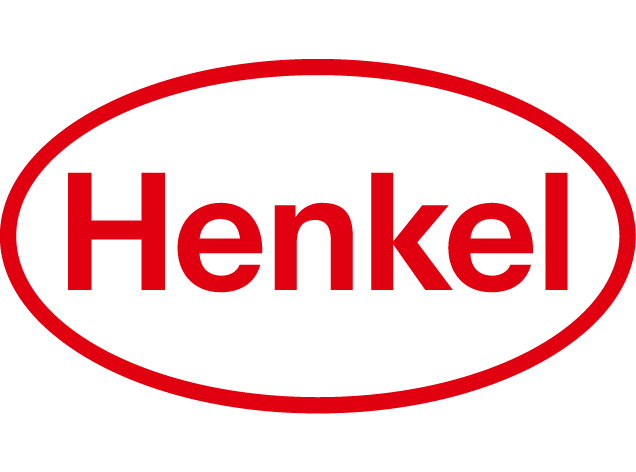
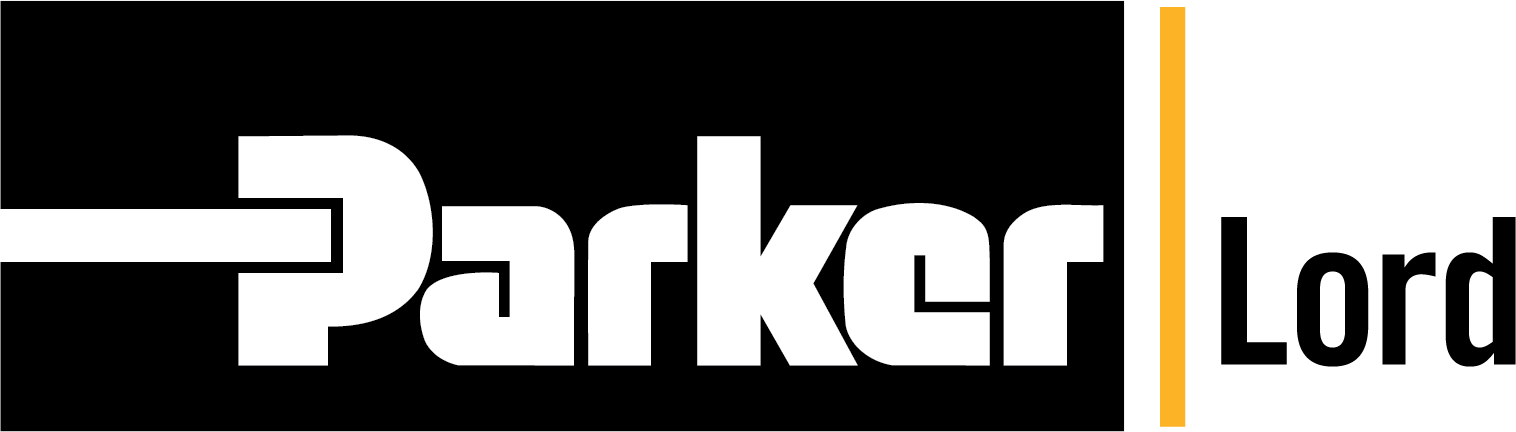
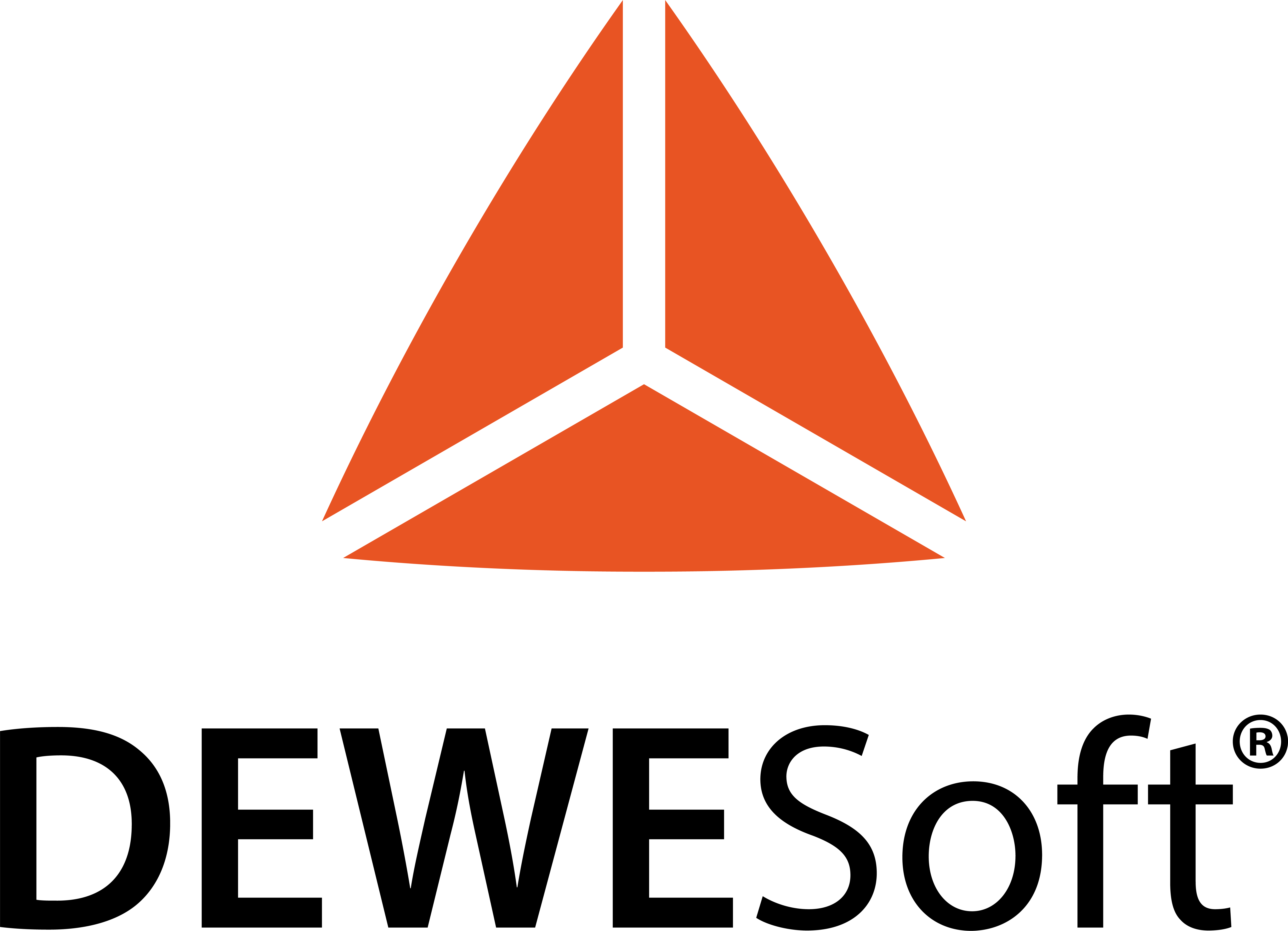
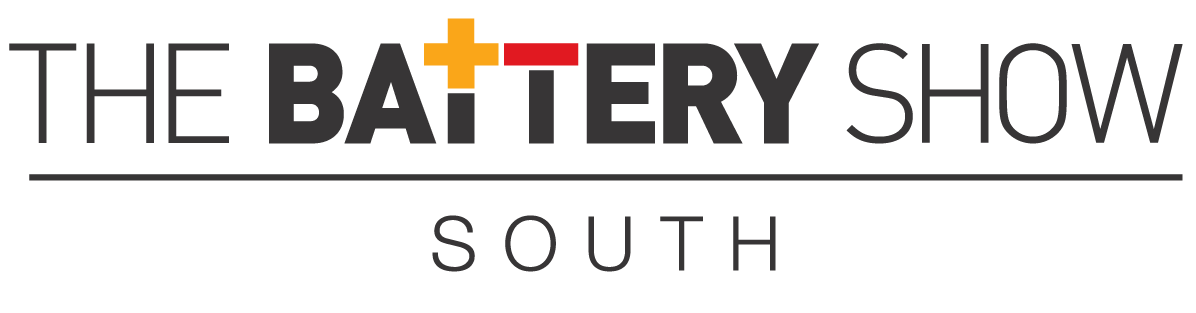
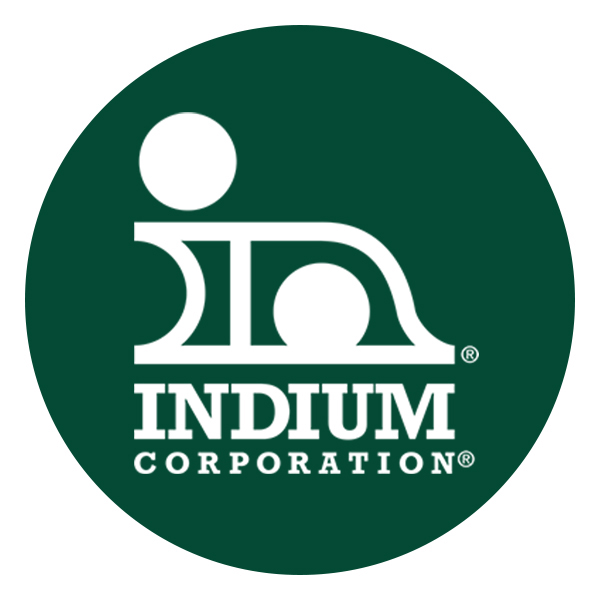

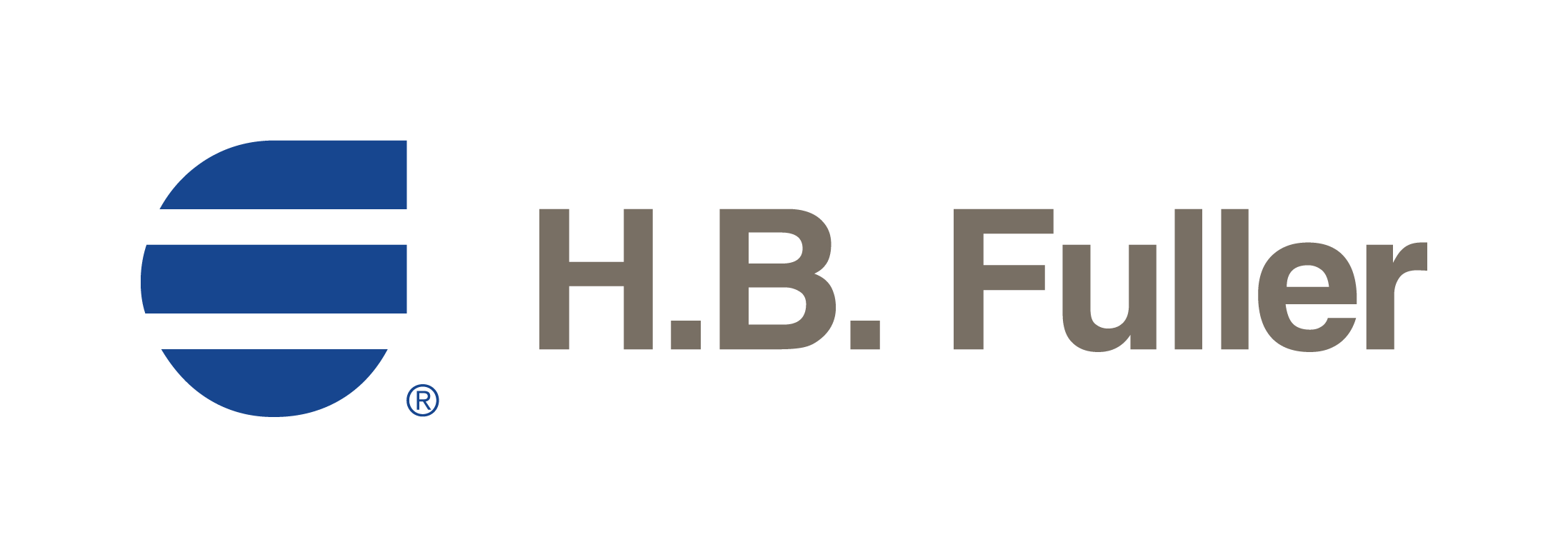
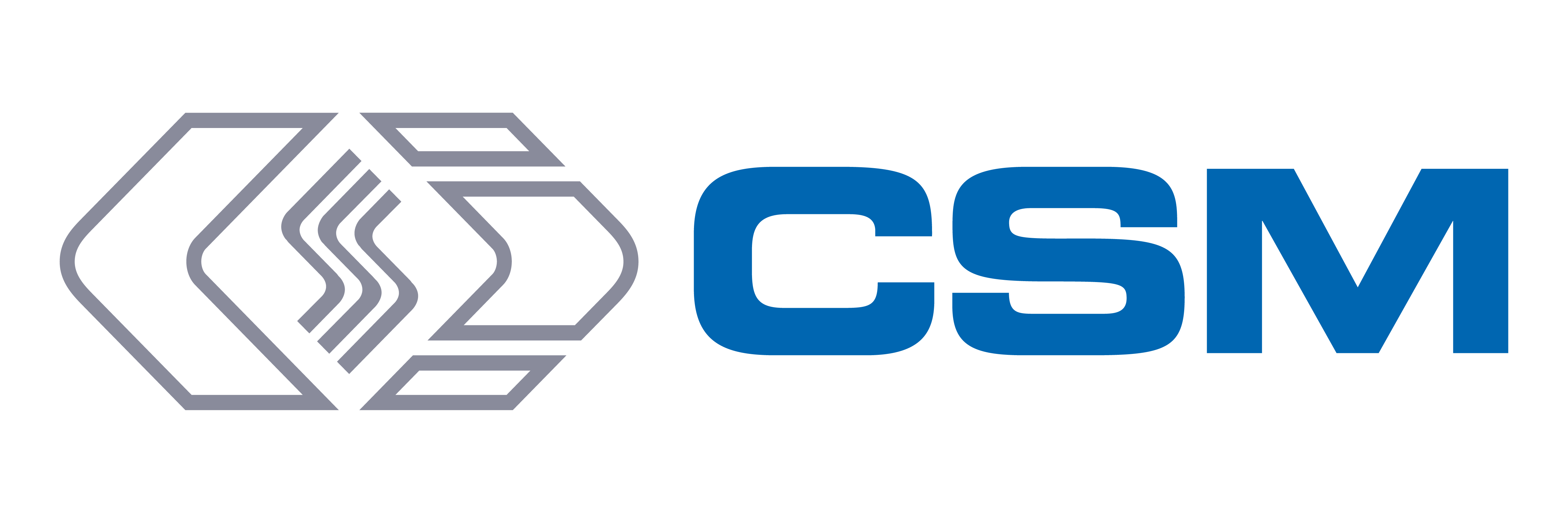
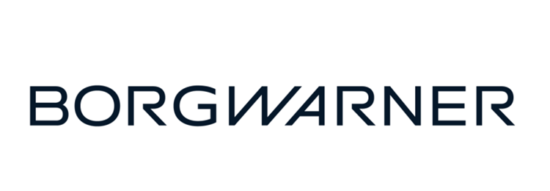