Powertrain testing
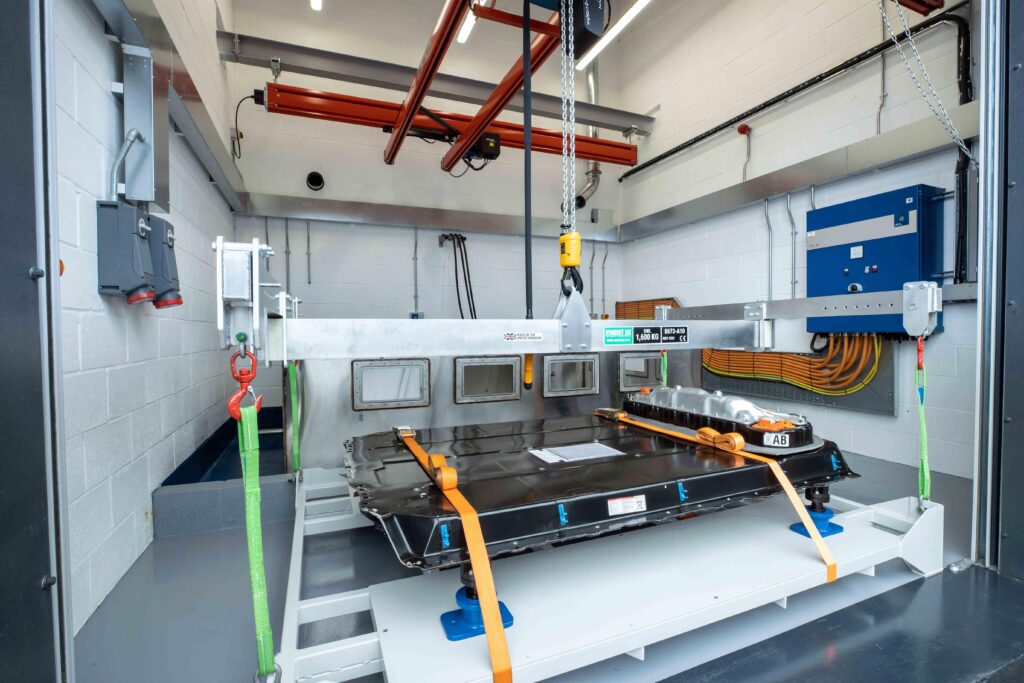
(Courtesy of Mahle)
Check it out
The growing shift towards electric and other forms of powertrains is being mirrored by changes in the services from test providers. Peter Donaldson reports
The state of the market for EV powertrain testing could be seen as buoyant at the moment, as the automotive industry transitions from IC engine test capabilities to those that support new and future propulsion systems centred on electrification and other alternatives to fossil fuels, such as hydrogen. The EU’s ban on the sale of new petrol and diesel cars from 2035 is giving a transformation already under way further impetus and urgency.
Vehicle and equipment manufacturers are developing the required test methodologies and capabilities, while service providers are transforming their offerings to support the needs of the new powertrain technologies. One provider of test services for rotating machinery reports that its teams is working almost entirely on fully electric vehicles and “not even on hybrids any more”.
Except for specific industries such as off-highway vehicles, marine and other big transportation vehicles where combustion powertrains remain important, electrification is the preferred method, its expert says.
In another shift, a large portion of the market is now moving from r&d-related testing to end-of-line testing, as most of the major car manufacturers gear up for large-scale EV production, a provider of variable-speed drives and controls systems for testing EV propulsion says. For the commercial vehicle and off-highway market, they are still investigating the best technologies to take them forward, according to an expert from the company.
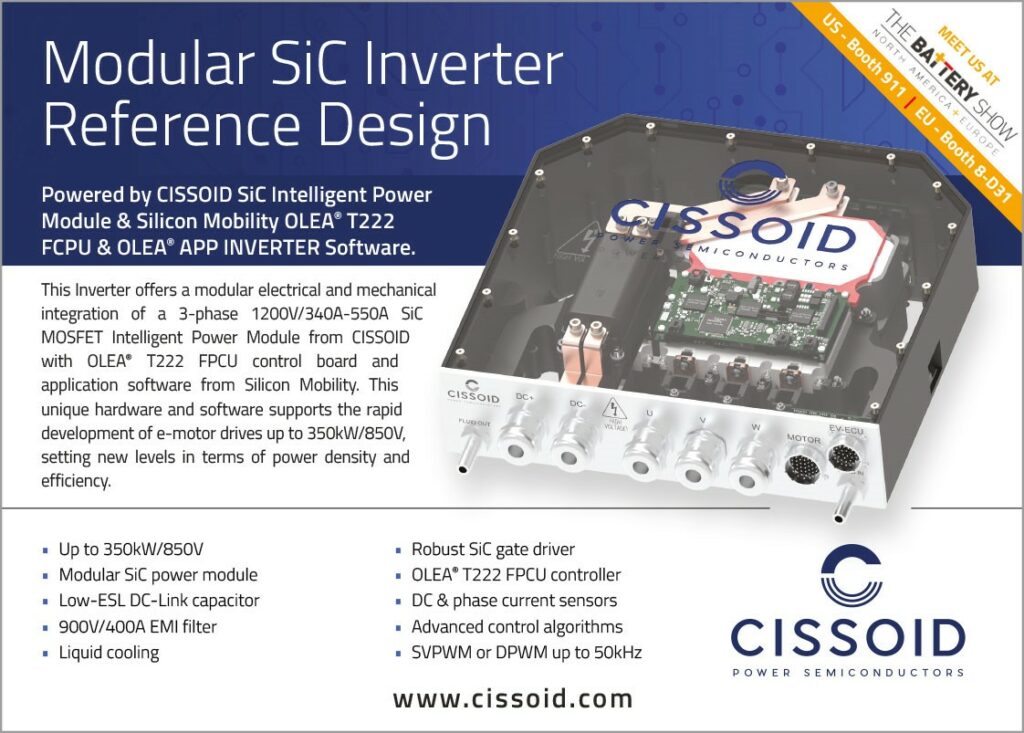
While the high-level goals of establishing whether components, subsystems and complete powertrains meet their torque and power, efficiency and durability targets are as relevant as ever, NVH measurement requirements are now much more demanding because of the need to identify and characterise multiple sources that are no longer masked by an IC engine, such as road noises, wind and components such as the steering and battery cooling system, for example.
The rotating machinery testing expert says testing these new-generation powertrains means measuring and evaluating new types of metric. New noise sources must be dealt with, he says, as must different frequency range and annoyance metrics, with a strong focus on tonal analysis. These metrics include the tonality hearing model, prominence ratio, sharpness and loudness.
“This completely reshapes what we used to know as a brand sound signature,” he says. “The growl of a V8 for example, or the smooth feeling of an inline 6 are no longer markers of specific categories of vehicles.
“Designing the internal and external sound of EV powertrains is very important. Electric car users want to feel comfortable, safe, and to experience a driving feel that corresponds to the type of car they are in.”
That means testing providers and automotive OEMs have had to broaden their scope to look at every noise source from the powertrain and body as an interacting system.
The expert emphasises that while automotive OEMs have built up a strong knowledge of the integration of powertrains into vehicle bodies, EV powertrains present new challenges because the sizes of components and the loads they generate are very different. High torque from low rpm requires a different body structure to handle it, and the ability to identify the loads and their proper paths through the body is key, he says.
Integrating the battery is also a challenge owing to the size and weight of a modern pack. That has major implications for weight distribution, overall body stiffness and the balance between vehicle performance and comfort, he adds.
Energy management is also very different, he says, as testing has to assess the efficiency of the flow of DC from the battery, through the inverter and the electric driveline to the wheels, rather than from burning a mixture of fuel and air through an entirely mechanical driveline to the wheels. “This requires new methods and materials,” the expert says.
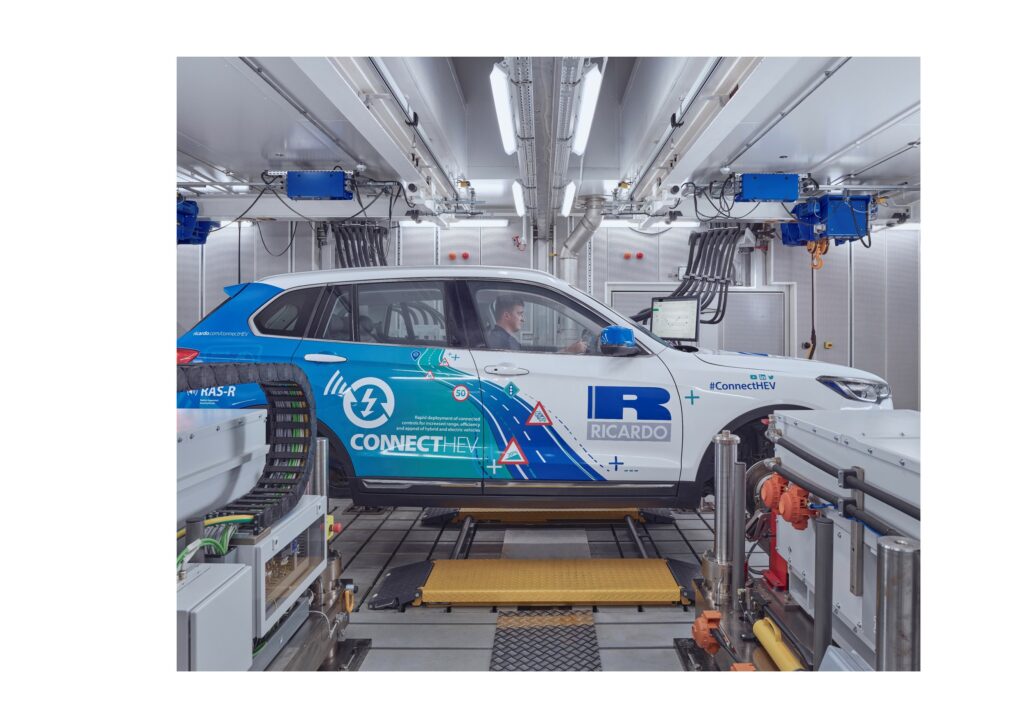
(Courtesy of Ricardo)
Testing essentials
EV powertrains are characterised by high-speed, high power-density input machines, with integrated gearbox systems that deliver high wheel torque from zero speed, explains a global engineering consultancy and services provider, which offers EV powertrain system design, development, integration, testing and validation of components as well as complete vehicles.
The company can test e-machines on single-axis test rigs, gearbox systems on input-output rigs and electric drive units (EDUs) on 2WD and 4WD powertrain rigs, an expert from the company explains. For complete vehicles, the company offers climatic test chambers for performance and efficiency development, along with range testing to EU and US standards.
The expert says test systems must be able to match the high performance of modern EV powertrains while being durable enough to deliver repeated test campaigns. He says, “Performance and efficiency are important factors for EV powertrain, requiring highly accurate torque measurement and power analysis systems that look at both the DC and AC systems.”
A basic test system consists of a high-speed dynamometer or a pair of wheel-speed dynos integrated with a battery simulator, says the variable-speed drives and controls systems provider. The simulator is needed because EV powertrains are normally tested without their batteries.
The company makes drive systems for the test stand industry. These differ from those primarily for industrial applications, for example by using output devices such as inverters and converters that provide higher switching frequencies with lower losses, and through the use of multiple processors along with software developed for test stand applications and internal clocks that can be configured to prioritise different parts of the system.
Typical systems tend to be more elaborate than the system described above, however. According to engineers from a vehicle test and validation services provider, they include rigs for testing the performance and durability of EDUs consisting of multiple AC dynos in a mix of high-torque and high-speed machines, battery simulators, coolant and oil conditioning systems and power analysers, along with environmental conditioning.
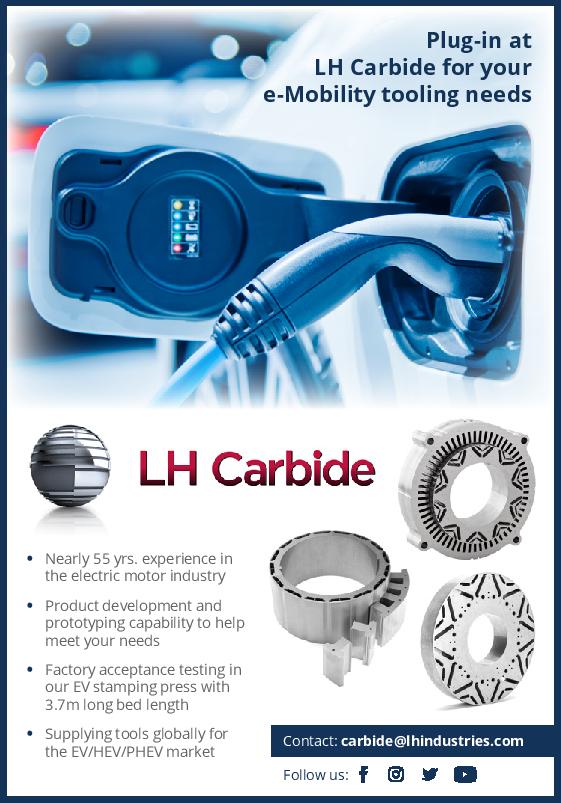
The company says it offers a full complement of testing services at the component, subsystem and system levels, including homologation support, and has recently focused its investment on electrified driveline and battery testing capabilities.
Battery testing systems generally focus on endurance and performance, and include environmental chambers, battery cyclers as well as coolant conditioning systems, the company’s engineers say. Naturally, both require control and data acquisition systems.
“Also testing systems – for batteries as well as EDUs – tend to have an environmental test focus,” they say. “Test systems include electromechanical shakers for impact and vibration testing, coolant and air-to-air thermal shock rigs, dust and water ingress as well as salt spray.”
The rotating machinery testing provider says it is important for data acquisition systems to be able to handle parameters including current, voltage, temperature, pressure, vibration and torque. Measuring very high torque at low rpm can be difficult because, for example, vehicle driveshafts can deform plastically, while typical torque measurement systems based on strain sensors assume that shaft deformation will remain in the material’s elastic zone, the company’s expert says, so there is a need to adapt the instrumentation.
“Analysis systems should also have enough flexibility to handle multi-attribute balancing,” he adds. “Noise and vibration analysis is completely redefined with electric powertrains, so advanced sound quality analysis tools with interactive audio analysis, jury testing and a sound designer to craft a unique sound signature for the brand are required.
Issues surrounding the integration of the powertrain and the battery pack are also critical, both from a durability and NVH perspective, he stresses, so accurate modal analysis and noise/vibration prediction starting early in the design stage is essential. The ability to interface a typical NVH system with power analyser data is becoming increasingly important for studying the impact of EDU control strategies on the occupants’ perception of comfort, he adds.
He says test benches need to adapt to modern EVs in a number of ways, including mechanically. “Typical sedan [saloon] cars these days are heavier than in the past, and have the same torque levels as trucks from not so long ago, and this from the lowest rpm,” he says.
“Test systems should not be seen as standalone entities, but should be closely interfaced with simulation systems. We should be able to test physical prototypes of subsystems in combination with multiple virtual vehicles, and by doing so avoid late surprises on the final vehicle prototype. This requires dedicated innovative test benches that combine test and simulation technologies.”
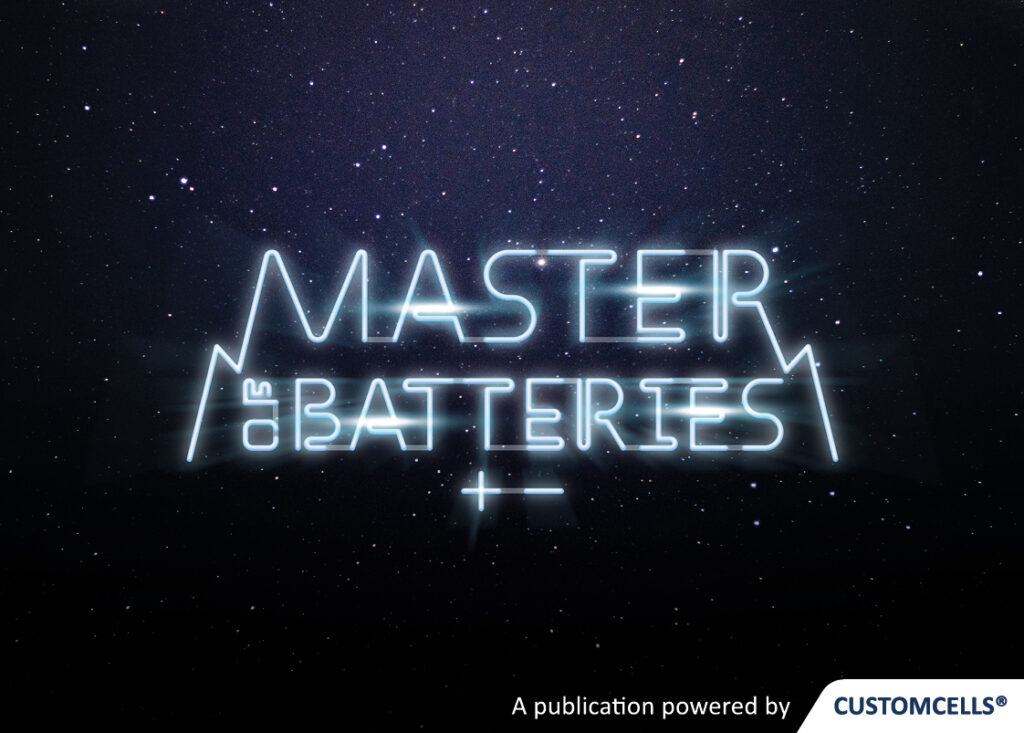
For the safety of those working on the test bench, he adds, proper cabling, sensors and operator training are essential.
The company uses simulation to optimise system performance from the early design stage, applying 3D simulation to predict mechanical performance across disciplines including noise and vibration analysis and acoustics, along with fatigue analysis, multi-body dynamics and crash safety.
Assessing the thermal behaviour of electric powertrains is crucial, the expert says, so the company uses CFD to analyse highly complex behaviours in liquids and gases, and has comparable capabilities in electromagnetic simulation to analyse the performance of electromechanical systems.
The company brings the test and simulation worlds together, he says, in a model-based testing capability that includes model-based virtual sensors and system in-the-loop testing.
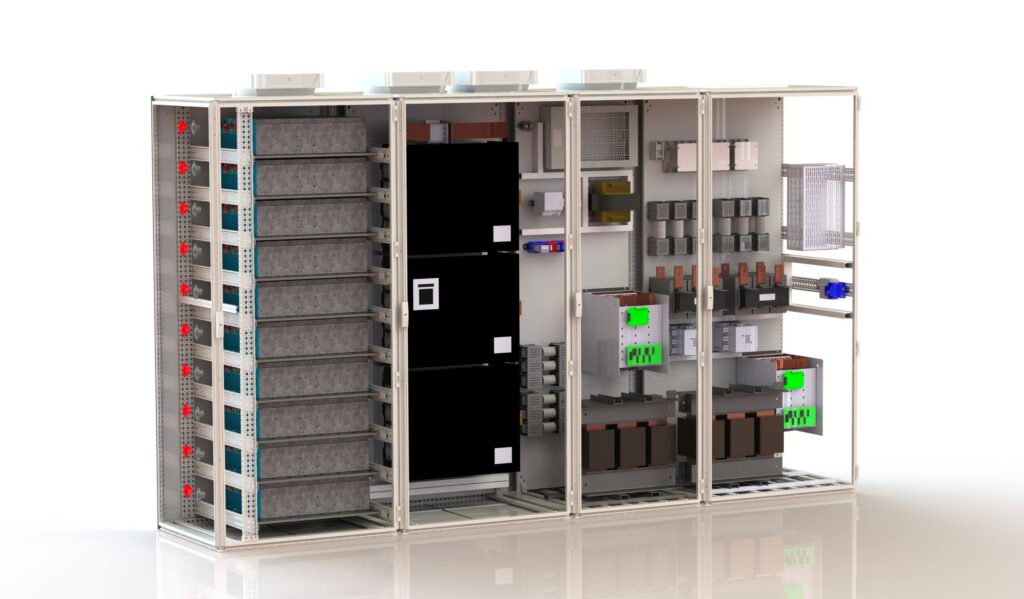
(Courtesy of Unico)
Need to know
When EV developers approach testing organisations, they can have one or several of a variety of goals in mind – performance mapping, efficiency characterisation, durability and responses to environmental stressors for example. However, battery and motor efficiency seems to be the top priority, closely followed by performance, durability and NVH.
The same rigs might be used to test for these attributes can also be used for validation and/or certification, according to the consultancy and services provider. The different test system architectures available allow customers to benchmark against competitors and develop improved EDUs for future products, its expert says.
The rotating machinery testing provider notes that its customers’ requests focus on two main subjects: multi-attribute balancing in an NVH context and energy flow analysis.
In the first, they are looking for help with identifying noise sources and analysis of the contribution of each source, and the company provides either the required tool or a complete set of analysis services. Problems addressed range from the mechanical, such as structural integration issues, to sound quality engineering including jury testing and sound design, the expert says, with detailed work extending up to complete wind noise analysis of the vehicle.
For energy flow analysis, the service centres on the use of a test cell dedicated to vehicle energy management. The cell features ambient temperature control from -10 to 45 ºC, and houses a spindle direct drive dyno that can run AWD vehicles, a rig that has recently been upgraded with a 300 kW EV supercharger, enabling the efficiency of energy transfer from the grid to the battery to be calculated, for example.
Here, the questions customers want answered are not so different from those that have long occupied IC powertrain developers, the expert says. They want to know how efficient their drivelines are, which component is generating the most losses, and what the effects of different control settings are on driveline efficiency.
“Now, a typical issue would be degradation of e-motor control during cold starts to increase heat generation, and the effect that has on driving range,” he says. “There is a balance between the requests for pure development/validation of customers’ own systems and benchmarking.”
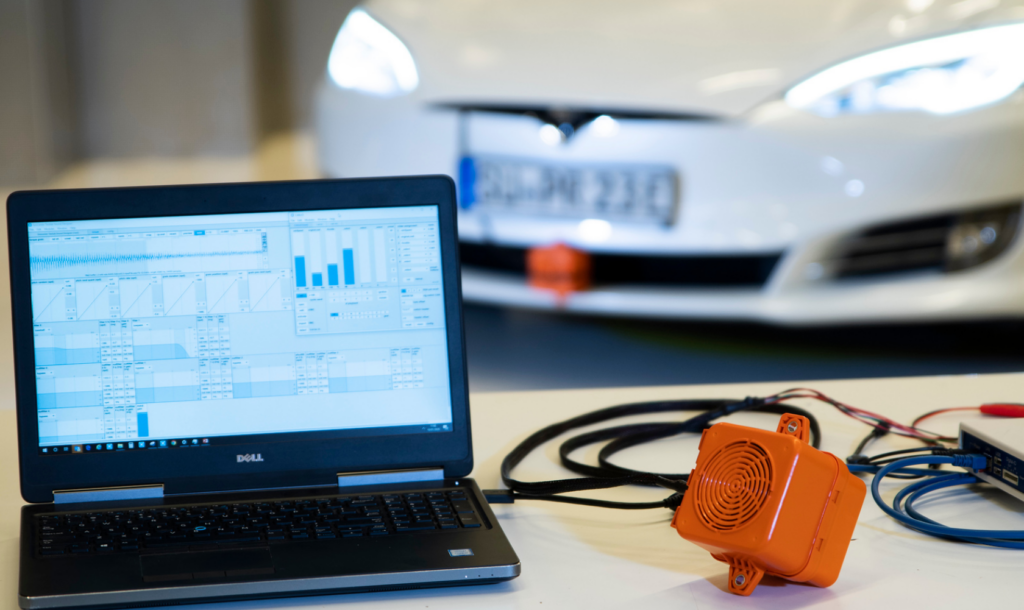
(Courtesy of Siemens)
Challenges drive change
In terms of the unique challenges that EV powertrains present to testing organisations, the engineering consultancy and services provider cites the range of needs discussed above, along with more specific issues such as electromagnetic compatibility (EMC), mechanical resilience and high voltage safety.
“Safety when dealing with HV systems is paramount, as they present a high level of risk,” its expert says. “When directly coupling to high-speed e-machines, driveline systems must be able to run at very high speeds.”
Test systems therefore need to be modified to ensure safe and accurate testing, he continues. This might mean changes to start-up and shutdown procedures, and precautions against EMI using sensors or isolating HV systems. While heat rejection from EV systems is generally lower than from IC engines, testing is generally conducted across a wider climatic range.
“We can test e-machines up to 30,000 rpm and EDUs to 4000 rpm wheel speed,” he says. “We have single and multi-axis rigs up to 4000 Nm and power ratings of 500 kW for single-axis, and 1 MW for multi-axis. Our facilities are designed to test a range of passenger vehicle systems, although, we also test smaller heavy-duty marine and aerospace systems.”
In the case of the primary powerplant, the speed range is much wider in EVs, the variable-speed drives and controls systems provider says. Typical roadcar engine dynos are rated up to 8000 rpm, while motorsport equivalents go up to 16,000, but EV motors almost universally spin at up to 20,000 rpm. Subsystems such as electrically assisted turbochargers in competition and high-performance hybrid powerplants spin faster still.
“IC engine powertrains can be tested against water brakes or eddy current dynos, but given the regenerative capabilities of an EV powertrain, the only logical choice of dyno is a full electrical system.”
That opens the way to energy savings, the expert adds, as the company operates test systems that integrate the battery simulator onto the same DC link as the dynamometer. “In this way, energy harvested by the dyno is used to power the battery simulator, so the only power required from the grid is for covering the electrical and mechanical losses. Without this technology, test houses would require far more power to cover EV testing.”
He says that has driven a big move away from older testing technologies, towards systems with lower inertia and consequently greater use of permanent magnet dynamometers. The company offers dynamometers and battery simulators with ratings up to several megawatts, and systems that support machinery that spins at up to 120,000 rpm.
Also, test data sampling rates tend to be much higher than they are in IC engine testing, engineers from the vehicle test and validation services provider point out. Tests such as power analysis require data to be measured at millions of samples per second.
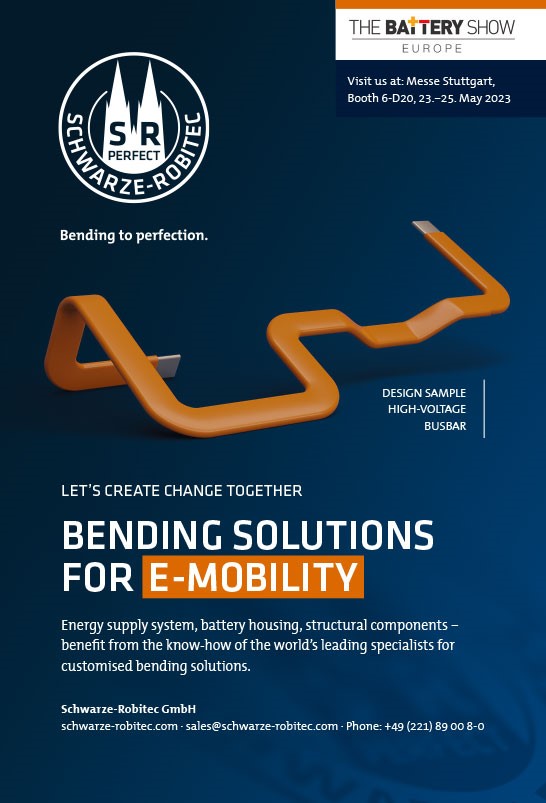
The engineering consultancy and services provider says measurements with such high sampling rates require highly accurate current and voltage sensors. Testing high-speed electrical machines also brings specific considerations to mechanical set-ups, requiring the use of balanced shafts and adapters, and requiring very high accuracy in alignment, for example.
The vehicle test and validation services provider has EV powertrain testing facilities in the US, UK and Germany, with battery simulators capable of delivering up to 1000 V, 1000 A and up to 1 MW, along with multiple AC dynos covering a broad range of torque and speed values.
At the low-speed, high-torque end are machines that can handle up to 5000 Nm continuously, while the high end includes machines that run at up to 20,000 rpm. Also, multiple accessory gearboxes allow commercial vehicle and off-highway powertrains to be tested.
From a design perspective, new EV powertrains also come in a wide range of system layouts, the rotating machinery testing provider points out. This encompasses a range of motor technologies and system architectures, including single and dual motors per axle, wheel motors, and inverters that are either separated from or closely integrated into the e-motor system.
Each one creates different design and measurement challenges for test systems, the company’s expert says. “Doing a benchmark measurement on a wheel motor is very difficult, for example, owing to problems with access to the components.”
There are also several mechanical aspects to consider, he says. For example, e-motors are attached to the vehicle body with much stiffer mounts than IC engines, which creates different NVH characteristics, and the high levels of torque from low rpm feed very large loads into the body, affecting durability as well as vibration and noise transfer.
When characterising noise and vibration using frequency response functions, for example, testing is always important for identifying the most important modes, he adds. “Certainly, at the level of the e-drive itself, performing an experimental modal analysis remains essential, because laminated stator housings with windings are very non-linear in their responses, and are difficult to model without test-based correlation.
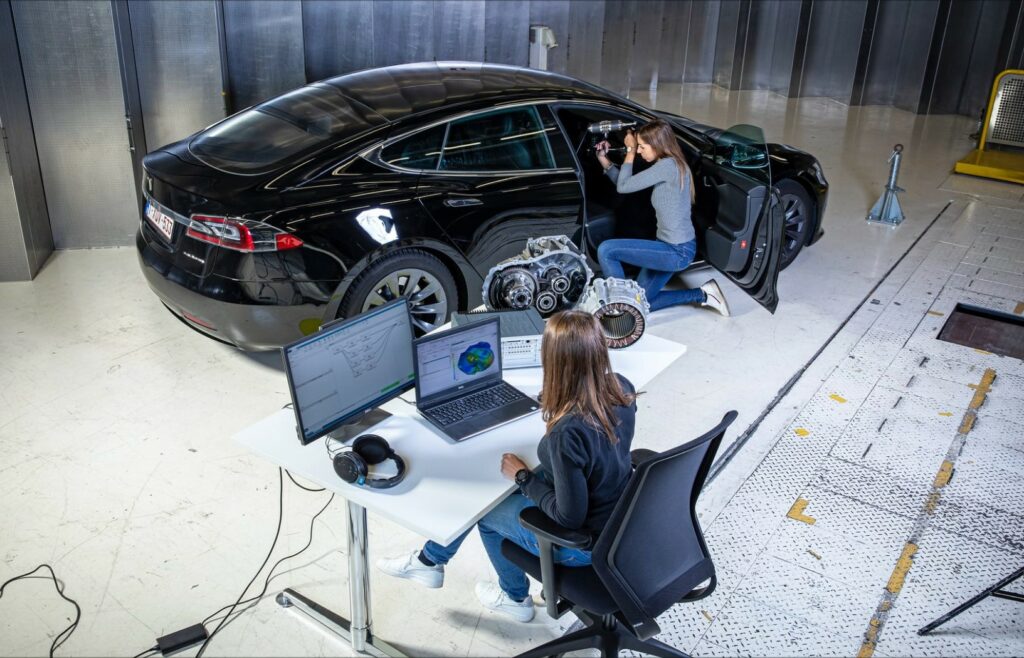
(Courtesy of Siemens)
Shaping test plans
Powertrain testing is complex, and typically follows the V model, in which the ‘V’ stands for verification and validation while also evoking the shape of the letter as an aid to visualising the flow of a development process and the relationship between the engineering and testing phases.
The engineering phases run down the left side of the V from top to bottom, progressing from user requirements engineering through system requirements engineering and architecture engineering and design down to fabrication of hardware and coding of software. On the right, the testing phases flow from bottom to top, from unit testing through subsystem integration testing then system integration testing, then system testing and finally acceptance testing.
Each testing phase verifies and validates the work done in the corresponding engineering phase on the opposite stroke of the V.
“EV powertrain plans cover performance and efficiency, durability, EMC, mechanical and environmental as well as abuse testing,” says the engineering consultancy and services provider. “There is some regulatory testing such as Regulation 85 for measurement of power but in general, EV powertrains follow multi-phase V model for development, which is comparable to their IC engine counterparts.”
Regulation 85 (R85) is a set of provisions for the approval of IC engine and electric drivetrains set out by the United Nations Economic Commission for Europe, and cover the measurement of net power for both and 30-minute maximum power for electric drivetrains, which are defined as the controller and motors.
Here, ‘net power’ means the power measured on a test bench at the crankshaft or its equivalent at a specified rpm, under reference atmospheric conditions, and with specified auxiliary devices attached. The ‘30-minute maximum power’ for an electric drivetrain means the net maximum power it can deliver at a specified DC voltage over a period of 30 minutes as an average. In hybrids, the IC engine and the electric drive are tested separately under R85.
Before they reach the approval testing stage, EDUs are typically split into their two constituent sub-systems, the high-speed e-machine and the transmission assembly, the vehicle test and validation services provider explains. These are initially tested and developed in isolation from one another, particularly during the early phases of development.
“One of the benefits of separating these two subsystems is it enables accelerated testing to be carried out, for example to prove the durability of the transmission geartrain in isolation from the rest of the system,” the expert from the engineering consultancy and services provider says. “The battery would also initially be tested separately, for safety, performance and durability.”
The expert adds that a chassis dyno would then be used to test the complete system, before moving to a track for vehicle-level testing.
It is once that durability is proven that the drivetrain is put through regulatory testing such as R85, with lithium-ion batteries going through R38.3 to ensure they and their and cells are safe for transport, and R100 covering safety in their intended use in vehicles.
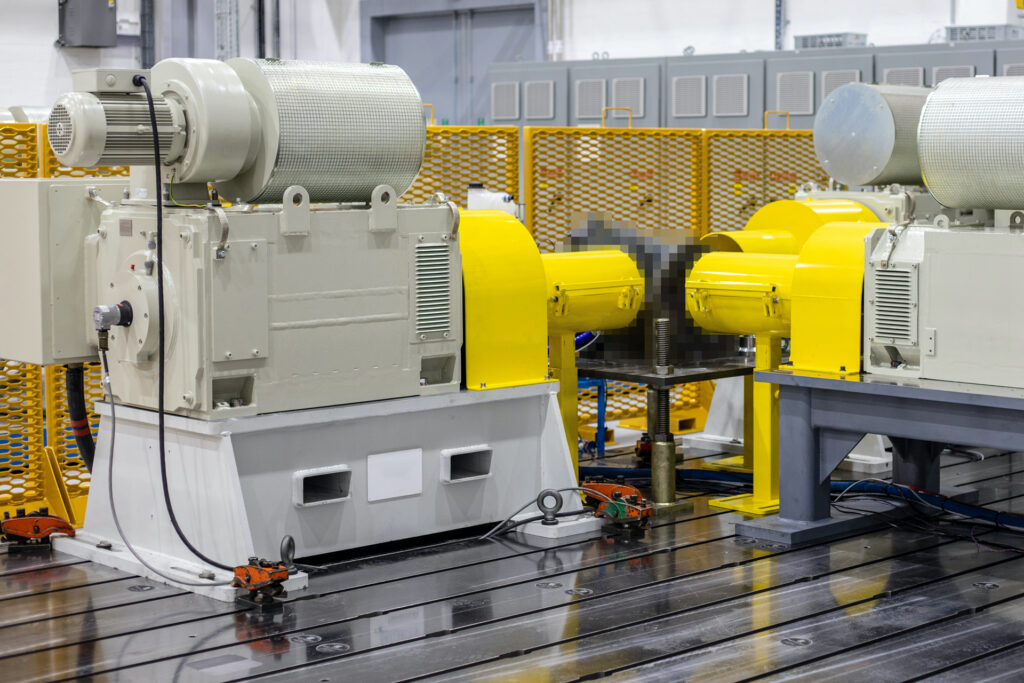
(Courtesy of UTAC)
Integrating HiL simulation
Hardware-in-the-loop (HiL) simulation is now an essential element of modern test facilities, facilities that increasingly use state-of-the-art digital engineering techniques and tools. These help to save time and money by linking physical and virtual development, particularly for software, which is now a critical element of the development path for complex electrified systems, according to the engineering consultancy and services provider.
“Advanced data management pipelines enable co-simulation of digital models with physical components, allowing for accurate and comprehensive validation of complex systems,” its expert explains. “This is particularly crucial in the development of electrified systems, where the integration of software-driven components has increased the need for rigorous testing.”
He explains that HiL simulations accelerate product development and reduce risk by replicating real-world conditions in a controlled environment. With the use of physical as well as digital components it is possible to validate performance under a wide range of scenarios. Also, virtual validation speeds up innovation for vehicle developers who need to bring their vehicles to market as quickly as possible without compromising quality, he adds.
Electric drives include control electronics that help optimise the vehicle’s performance and, by shaping responses to driver inputs for example, also help refine its brand character, the rotating machinery testing provider says.
Model-based testing enables integrated test and simulation in a single validation environment, increasing productivity and providing extra insight into the systems under test, as well as reducing cost and risk. It also maximises the consistency of the tools and methods while providing a highly agile system engineering environment.
Further, it enables attribute-specific evaluation using virtual models, combined virtual-physical models and physical prototypes, the expert notes. “For example, it is possible to test a single physical e-drive system in combination with multiple virtual vehicles in different driving scenarios.”
The real and the virtual come together in a piece of equipment the company calls an executable digital twin bench, which the expert describes as a real-time simulation rig. It uses closed-loop automation that relies on physical sensor measurements from the system under test (SUT) and variables from the real-time simulation environment. The rig control loop includes a real-time platform that replicates the physical boundaries of the SUT using software models of the rest of the vehicle.
The company’s engineers develop high-fidelity variants of these models to operate the SUT in all possible environments, he says. “This rig enables our customers to accelerate the development of their subsystems and control logics, and supports adaptive retrofit studies.”
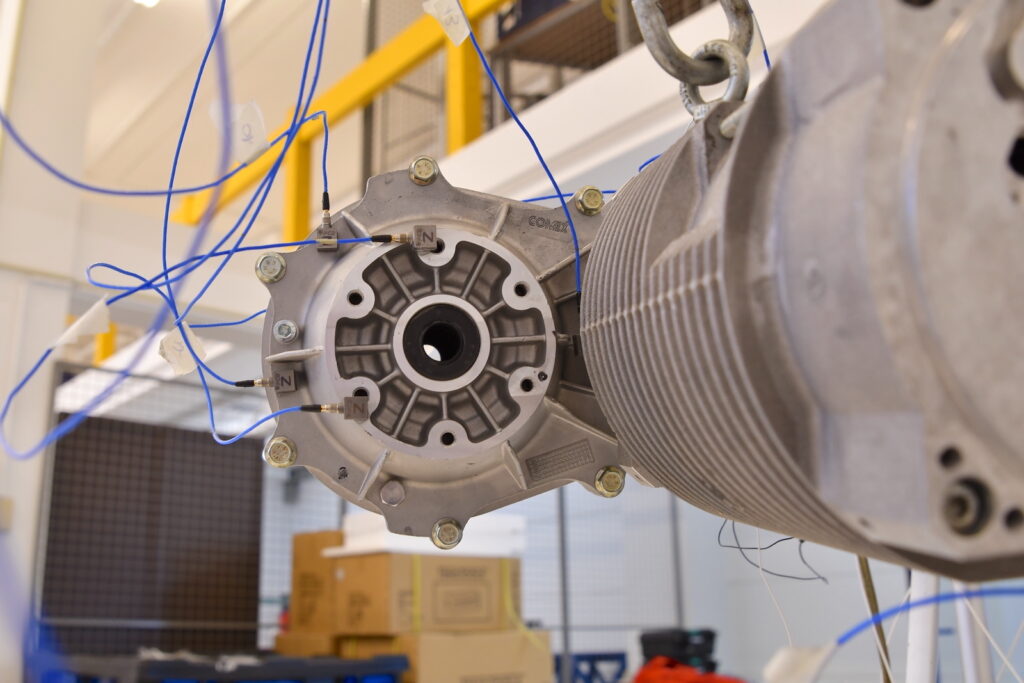
(Courtesy of Siemens)
Preparing for test
Given the complexity of the testing, it might be assumed that vehicle developers have to make elaborate preparations for any test campaign, but that is not necessarily the case. For example, the engineering consultancy and services provider prepares one-off prototypes for initial r&d as well as testing production-level drive units, the company’s expert says.
The vehicle test and validation services provider emphasises the importance of flexibility in this respect, because different customers often wish to engage with them in different ways. Some, he says, like to supply all the fixturing along with the system they want tested, while others want to deliver the SUT only, relying on the testing provider to design and make all the fixturing.
“We will typically look to the customer to supply a CAN database file along with their hardware, the expert says. “Other than that, no special preparation is needed to test at our facilities.”
Voltage trends
Looking to the future, an increase in both current and voltage is expected in EV powertrain systems, the engineering consultancy and services provider notes. It explains that although the passenger car market seems to have settled on 400 or 800 V systems at the moment, that is likely to change as much higher voltages are already in use by other industries, such as rail.
This view of voltage trends is not universal, however. The variable-speed drives and controls manufacturer for example does not expect voltages to go much above 800 for passenger vehicles. The vehicle test and validation services provider agrees, adding that the 350-450 V DC systems common a few years ago are being superseded by 700-850 VDC systems, largely to meet needs for faster charging.
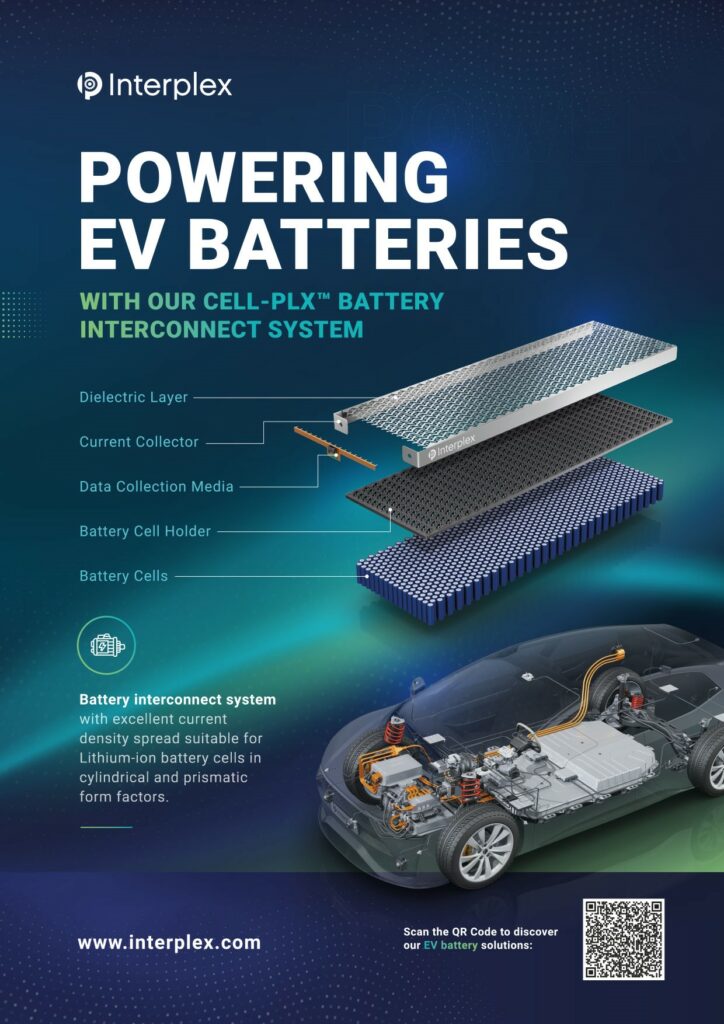
“We expect this voltage level will remain the ceiling for the mainstream automotive market for a reasonable period of time; however, motorsport and special off-road applications will continue to push the boundaries,” the expert at the test and validation services provider says.
Beyond system voltage, the expert does not expect further major changes in powertrain technologies in the short term, as the industry is in an era of rapidly increasing production volumes. He anticipates incremental improvements in batteries, electric machines and inverters, such as the shift to SiC devices, but does not expect them to drive significant changes in the testing required.
The engineering consultancy and services provider points to the growing importance of fuel cells in EV powertrains as the economy for future fuels such as hydrogen develops, leading to a greater need for testing fuel cells integrated into powertrains. “We have invested in fuel cell test systems and are focusing future facilities to allow testing of integrated hydrogen and EV systems,” it says.
The rotating machinery testing regards the development of autonomous driving as the big challenge ahead, to which testing organisations will have to rise. “This represents a big game-changer in the way we use our cars and the driving sensations we expect,” says the company’s expert.
“Comfort, quietness and driving dynamics will be perceived in a completely different way. This will require a new way of thinking about the e-motor integration and the global sense of being driven rather than driving a vehicle.”
Acknowledgements
The author would like to thank Tim Bassett at Ricardo, Andy Gardner at Unico (UK), and Brian Donohoe, Phil Robertson, and Peter Miller at UTAC for their help with researching this article.
China
EOL Expertise
+86 138 2522 4911
www.eolexpertise.com
Germany
Atesteo
FEV
HBM
IABG
Siemens
Teamtechnik
+49 2404 9870 0
+ 49 241 56890
+49 6151 803 0
+49 89 6088 0
+49 800 509 0100
+49 71 41 7003 0
India
Slovenia
Sweden
Switzerland
UK
Drive System Design
Integral Powertrain Testing
Intertek
Ricardo
UTAC
+44 1926 678 310
+44 1908 972 550
+44 116 236 1620
+44 1273 455 611
+44 117 403 0640
USA
ONLINE PARTNERS
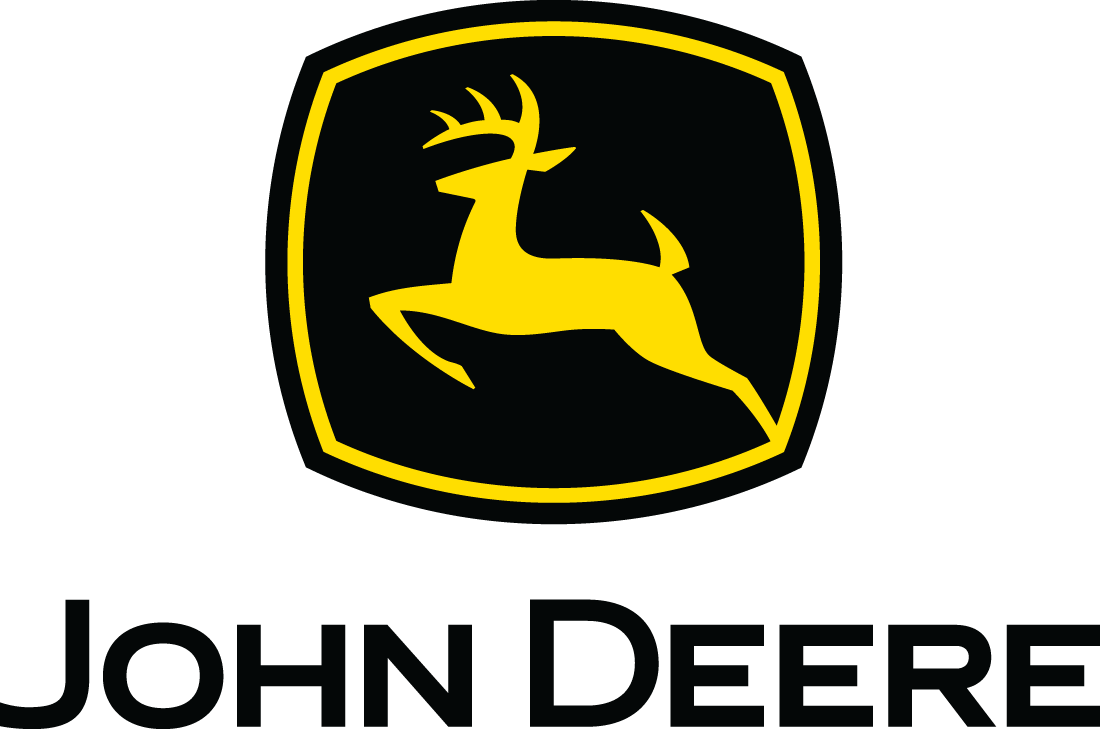
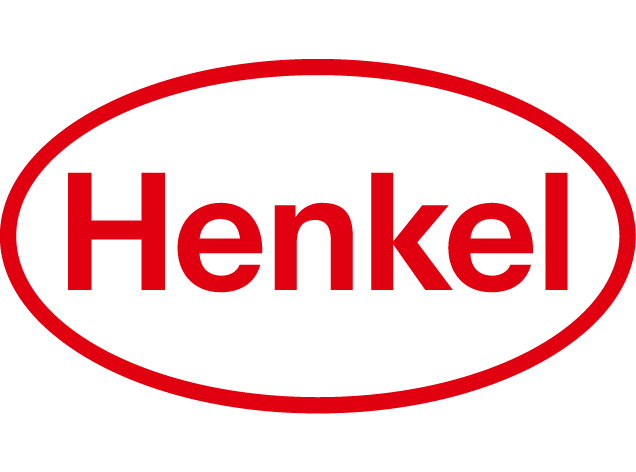
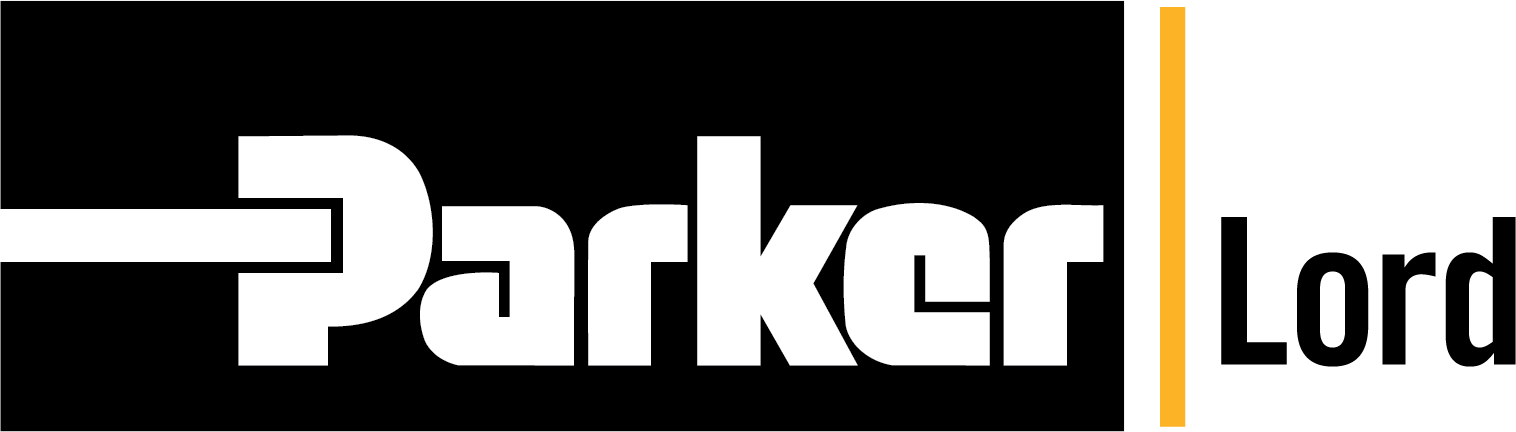
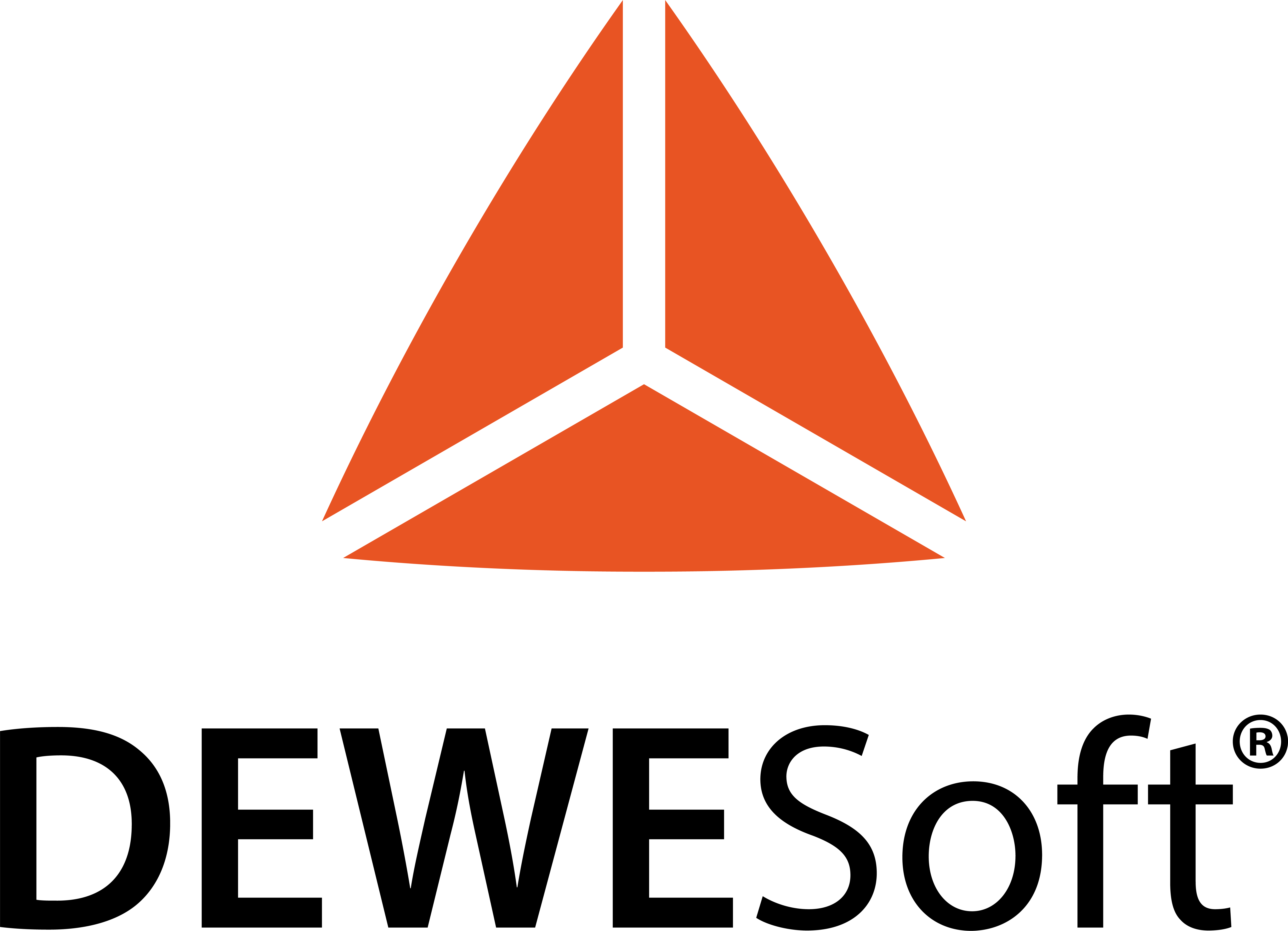
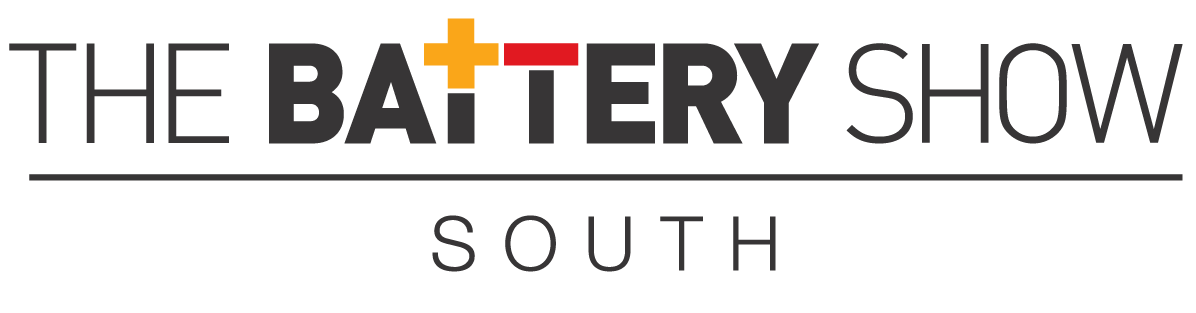
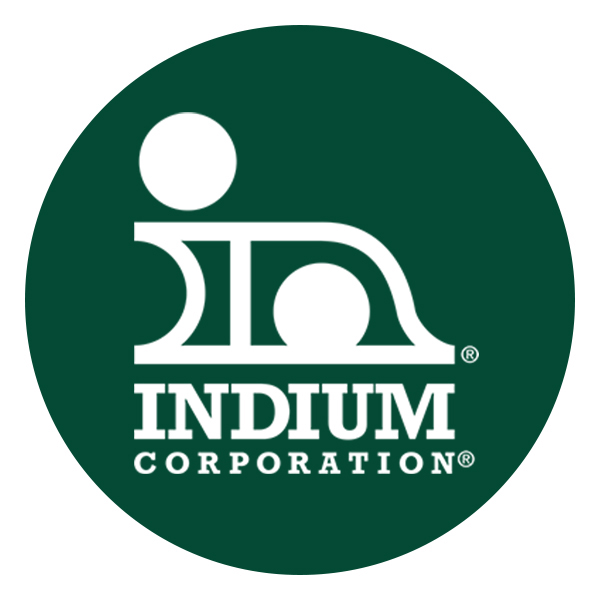
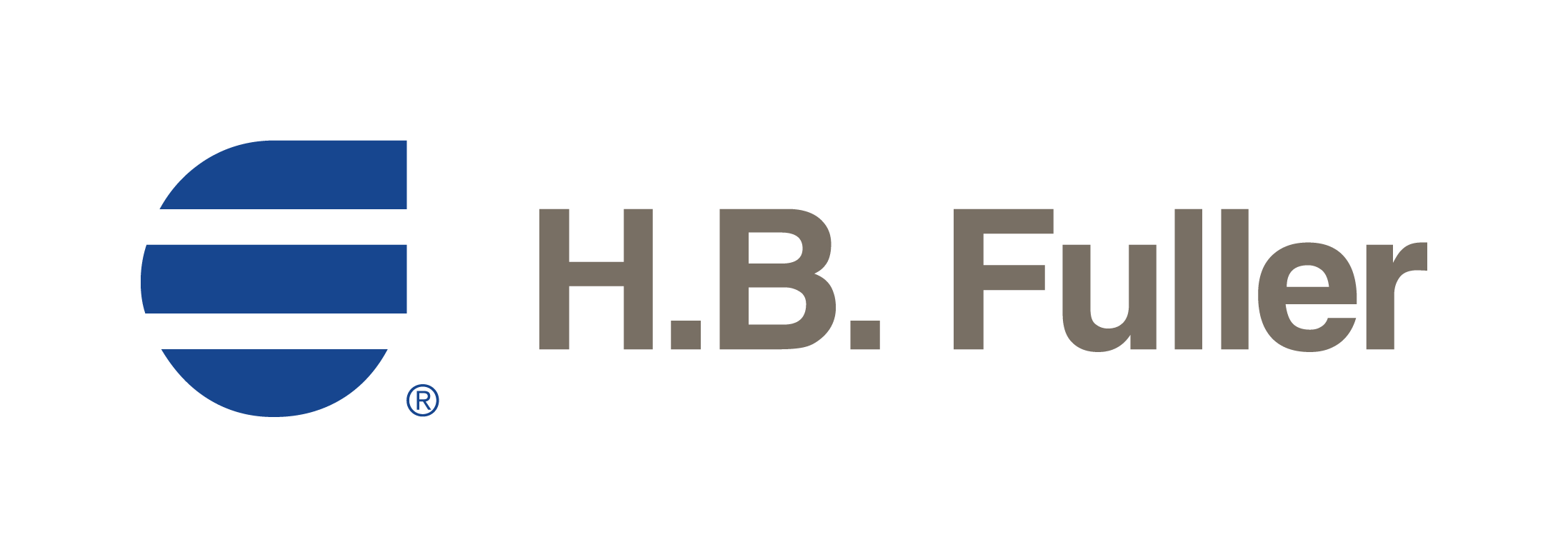