Testing facility for e-motors
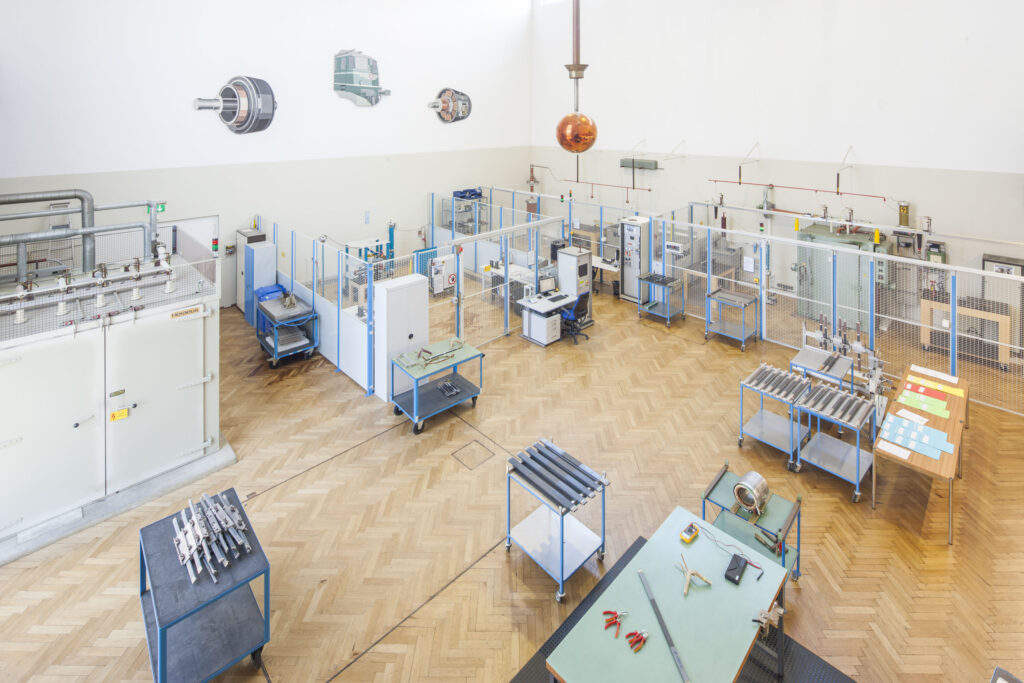
New testing laboratory for E-mobility drives The Von Roll institute in Breitenbach, Switzerland, recently expanded the capabilities of its already comprehensive test facilities with the addition of a new lab, dedicated to the testing of e-motors specifically for mobility applications.
Von Roll’s speciality is insulation material and as such, the new lab is geared towards characterising and testing all elements of insulation within motor systems. “Electric mobility is on the advance worldwide. The trend in the drives of electric vehicles is increasingly towards high voltage with 800 volts and higher,” says Christoph Herold, Director and Head of the Von Roll Institute. One significant result of this move to higher voltages being that insulation materials are pushed harder, being exposed to higher temperatures and stresses.
The range of testing that can be undertaken at the institute is extensive, starting with basic UL1446 standards tests to ascertain the fundamental compatibility and thermal resistance of components. In addition to basic resistance checking, it is also necessary to ensure that different insulation materials used in a system are chemically compatible with each other, to prevent unwanted reactions between various insulation types.
A host of other equipment is at the disposal of the institute for testing e-motor insulation materials. For example, environmental test chambers allow for the simulation of specifi c climactic conditions, with maximum temperatures of up to 340 Celsius, a minimum of -45 Celsius, and up to 100% humidity. The effects of thermal ageing can also be simulated using one of 15 furnaces, capable of accepting parts up to 750mm long and weighing 30kg.
The institute has also developed a system specifically for performing voltage endurance tests on the insulation for traction motors that run at high switching frequencies. This high-frequency sine-wave voltage supply, with a maximum test frequency of 1000Hz and up to 7kV RMS value can also detect partial discharge problems and show the resistance against them.
These latter tests are particularly useful when it comes to e-motors – specifically the latest generation of 800V systems – for the analysis and prevention of corona discharge, which is a common source of failure in high-voltage motors. Until recently, traction motors did not run at sufficiently high voltages to produce ozone. This ionized oxygen chemically reacts with many insulation materials and over a long period of time is corrosive to the insulation, causing premature failure in the winding insulation system.
ONLINE PARTNERS
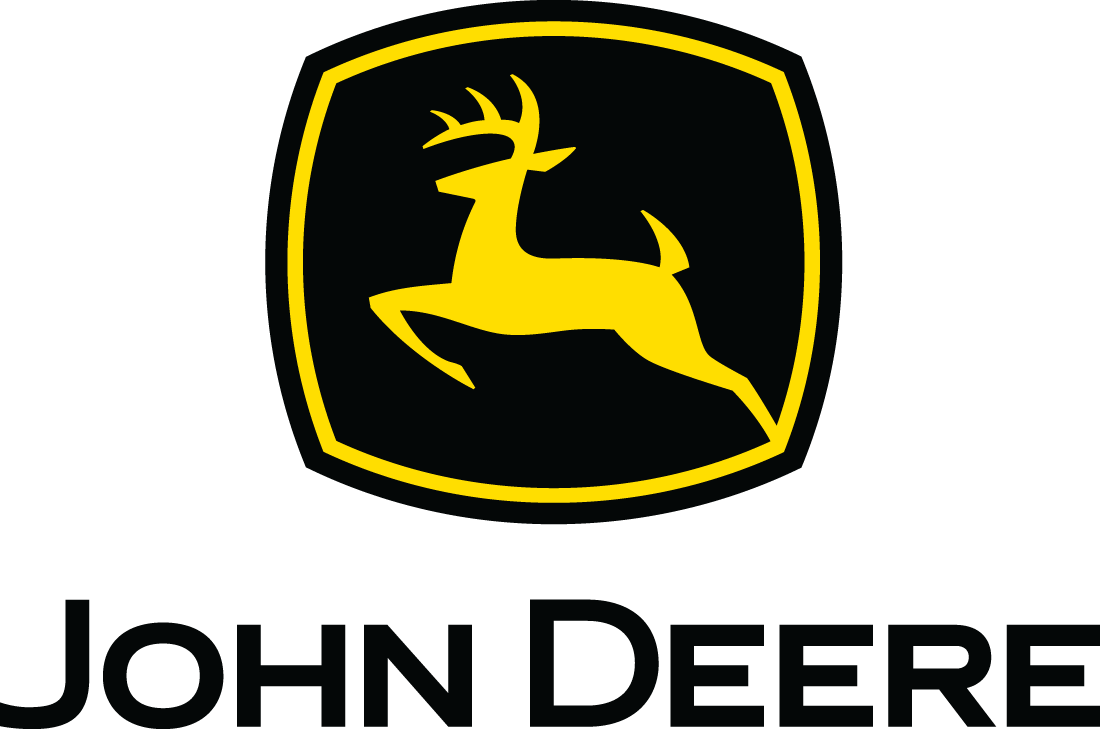
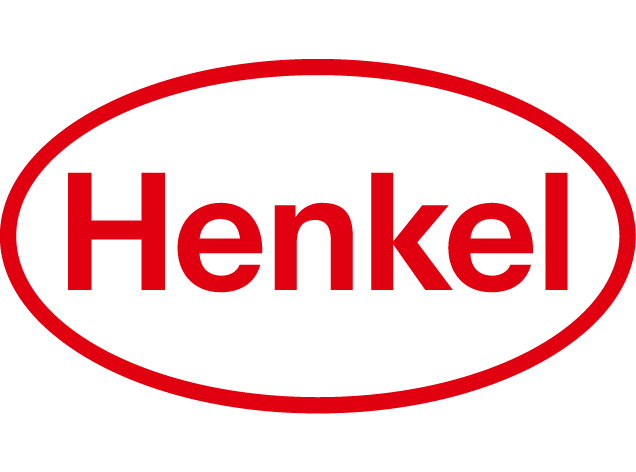
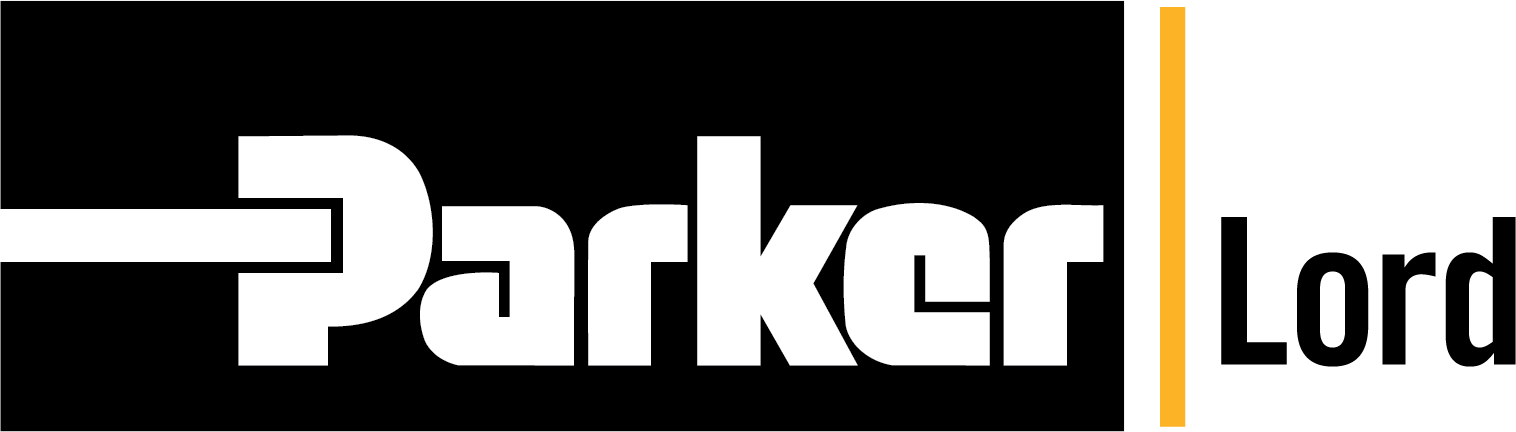
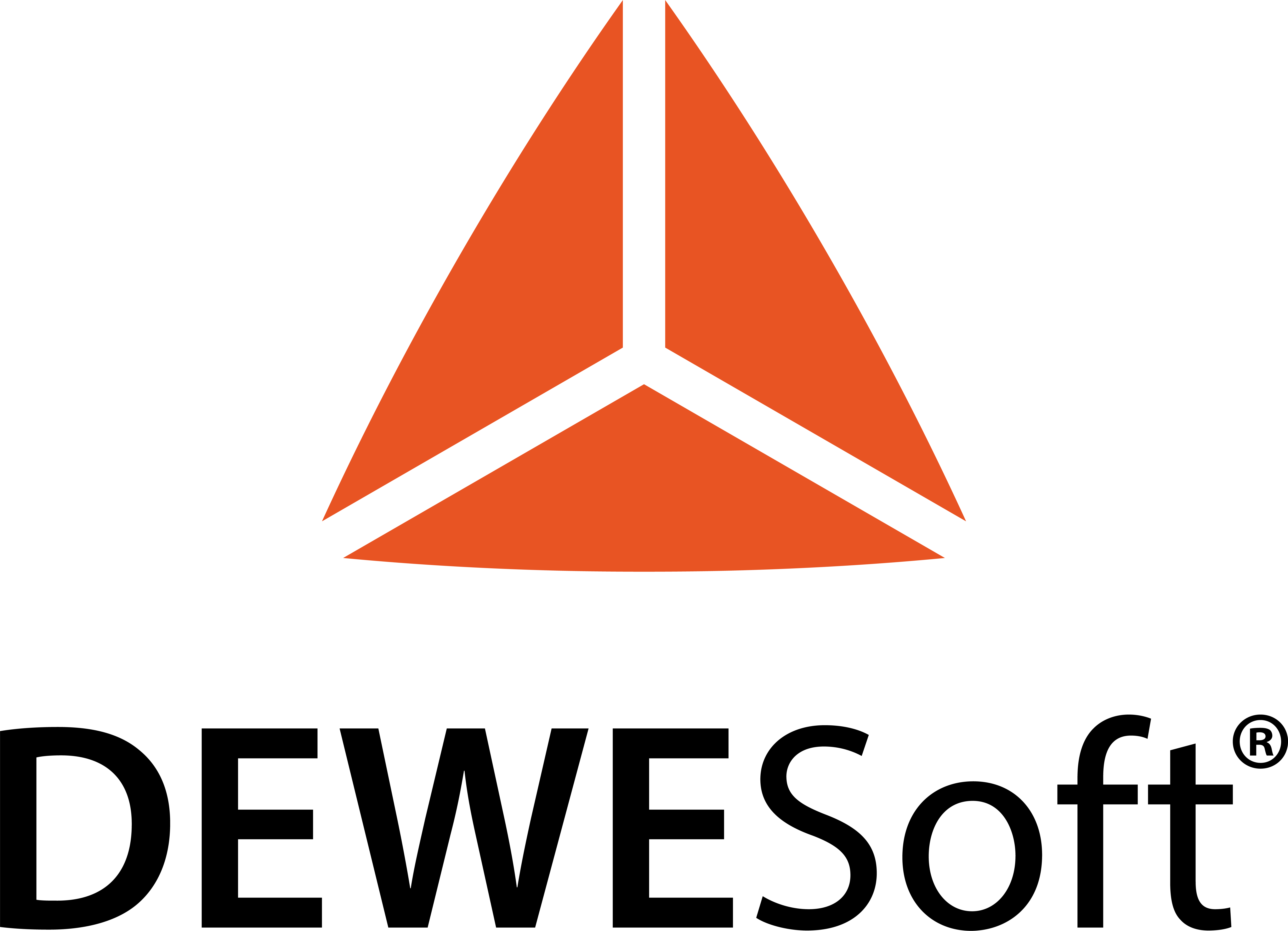
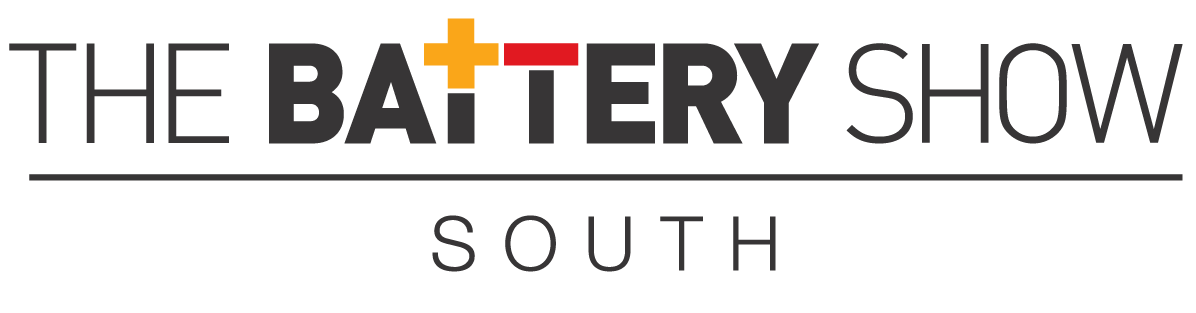
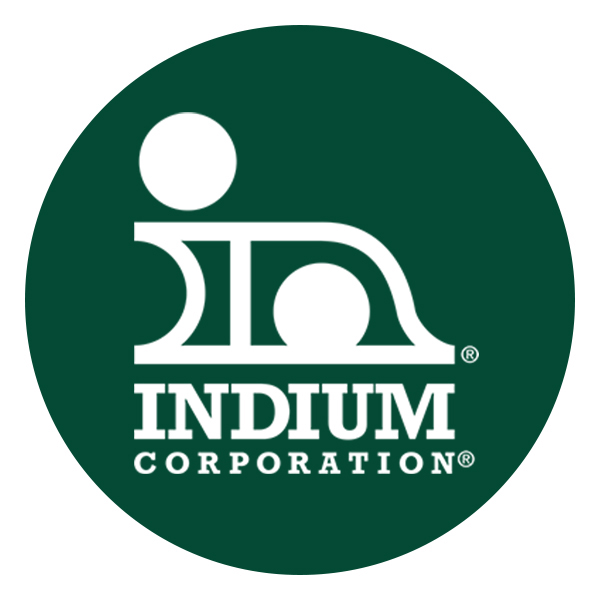
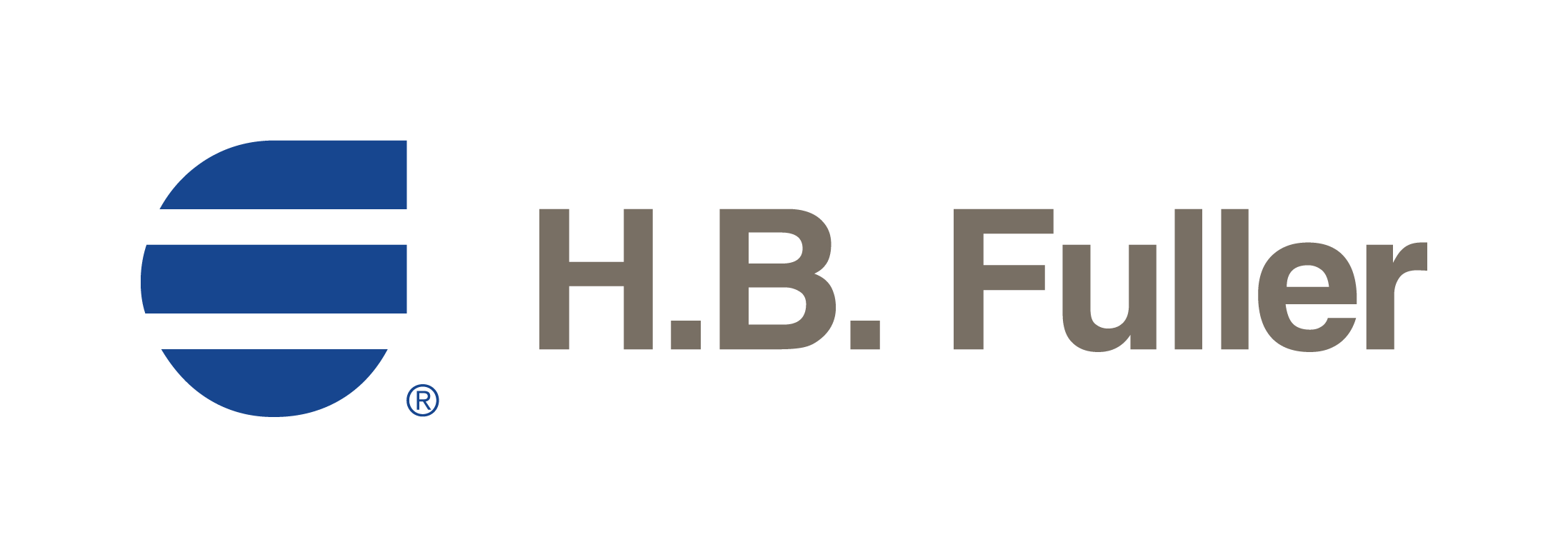