New-gen composites on show
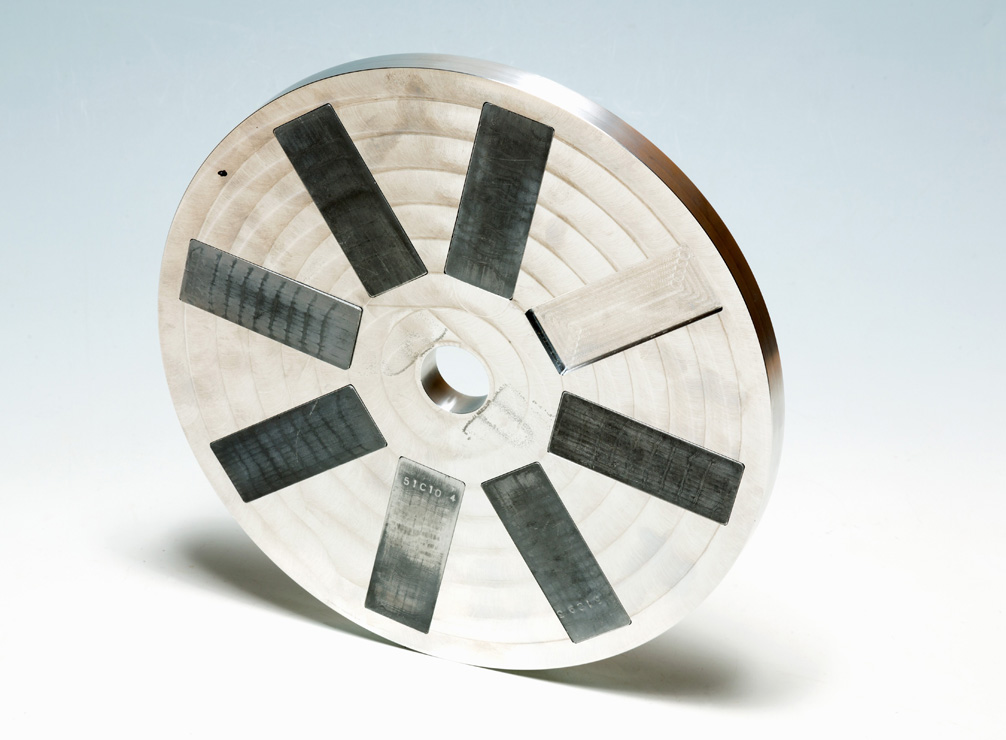
(Courtesy of Alvant)
Lightweight materials are a key element of the integrated engineering approach needed for EV vehicle development, as engineers strive to reduce vehicle weight in order to increase the effectiveness of the battery energy available (writes Lawrence Butcher).
A new generation of materials developed by UK-based Alvant provide an interesting option for engineers engaged in such projects. Alvant specialises in aluminium matrix composite (AMC) materials and, importantly, in developing methods to allow their practical use in manufacturing.
“In essence, we take aluminium and combine it with a secondary high-performance reinforcement material, either in the form of particles or fibres,” explained Richard Thompson, commercial director at Alvant.
“That allows us to create materials with superior performance to traditional metallic materials such as aluminium alloys, high-strength steels and titanium alloys.” Alvant’s tag line is ‘the strength of steel with the weight of aluminium’.
Components made with Alvant’s materials are created using a proprietary process called advanced liquid pressure forming. This process is flexible and can create net-shape parts or billets, depending on the specification, the aim being for it to be as close to the finished dimensions as possible, in order to reduce follow-on machining operations.
That is quite different from the way metal matrix composites (MMCs) have been used in the past, where the starting point was a billet of material that was machined to shape, resulting in a high degree of (expensive) material wastage.
The specific application dictates the reinforcement type used and the distribution of reinforcement within a part. For example, for structural parts such as suspension members or other highly loaded parts, continuous fibres are used. “That gives you very high specific strength with directional control over the fibres as well,” said Thompson.
Particle reinforcement is used for complex shapes, allowing more complex geometries to be formed.
One interesting string to Alvant’s bow is its syntactic foam product, which is an ultra-lightweight aluminium, full of tiny spherical voids within the aluminium. It can be used in a similar way to honeycomb core material in carbon fibre composites, providing internal structure to a part without increasing mass to the same degree as a solid filler material.
Sandwich materials are not a new idea, but generally they are assembled, whereas Alvant’s CorXal material – the brand name for its composite of syntactic foam and fibre-reinforced aluminium combination – is a homogenous structure that is produced in a single process.
“The density we can achieve with it is around 1.5 g/cm3, similar to some carbon composites but with greatly improved stiffness and strength over unreinforced aluminium,” Thompson said. “The skin portion of the material
features a continuous fibre, while the core is made from the syntactic foam, which greatly reduces the density.”
Of particular interest to the EV industry is a project Alvant recently completed with a customer – producing a motor rotor using its materials. “We targeted the rotor and, using selective reinforcement of the rotor with an MMC, we were able to reduce its weight by 40% while retaining the required stiffness,” said Thompson.
Stiffness is naturally an important design constraint to ensure a consistent airgap is maintained. Efficiency savings were twofold – overall package weight was reduced, as were the inertia and thus parasitic losses.
Another attractive property of the Alvant materials is their coefficient of thermal expansion, which is lower than that of aluminium. This could be a significant benefit in motor applications as well as areas such as battery structures. The low thermal expansion is due to the reinforcing fibres, which constrain the growth of the material.
The light weight and temperature resistance of the materials make them a viable replacement for composites, providing much of the weight saving without any reduction in mechanical properties at temperatures above carbon composite thresholds. The fact that the materials’ matrix is aluminium, rather than a resin, also means it retains high thermal conductivity – an important aspect in applications such as motors or batteries, where directly cooling parts can be a challenge.
ONLINE PARTNERS
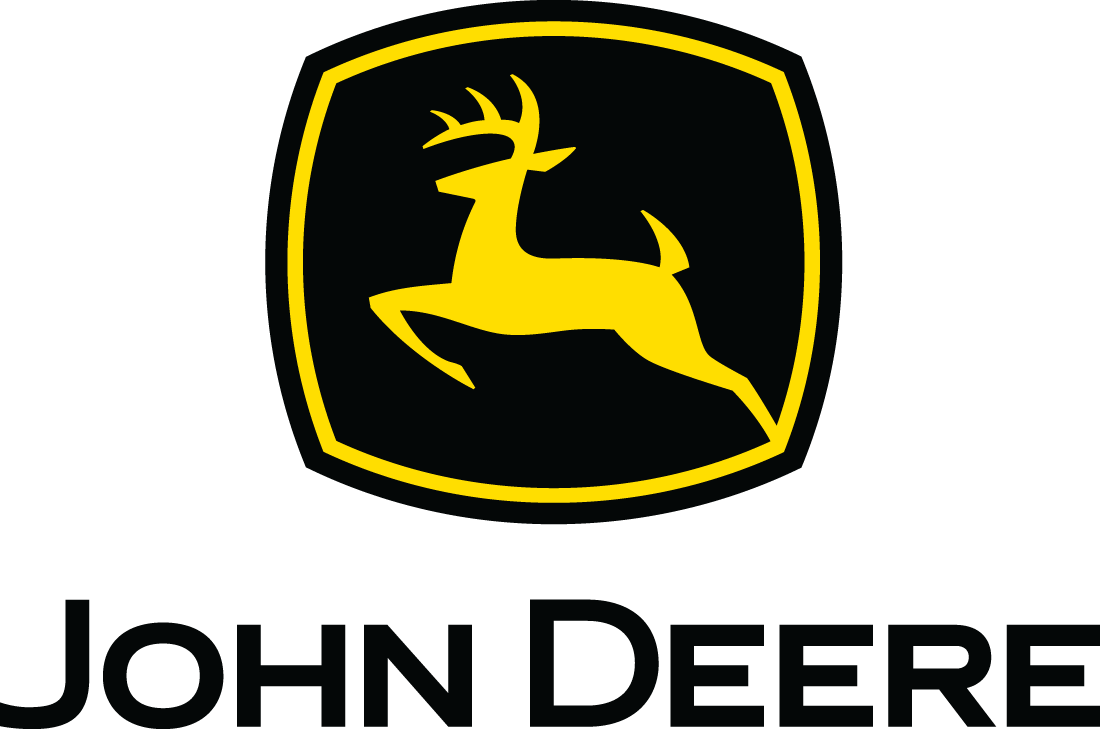
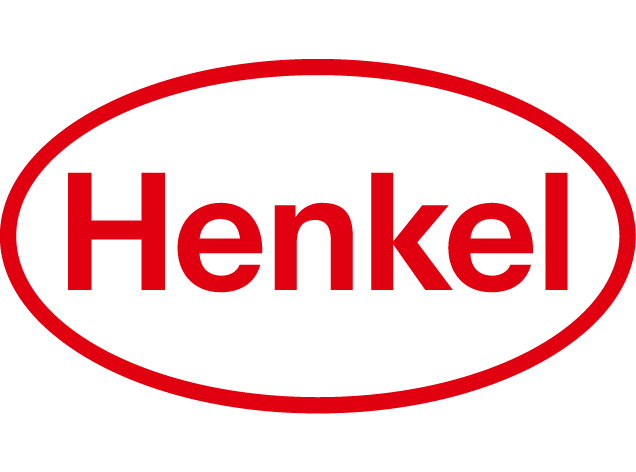
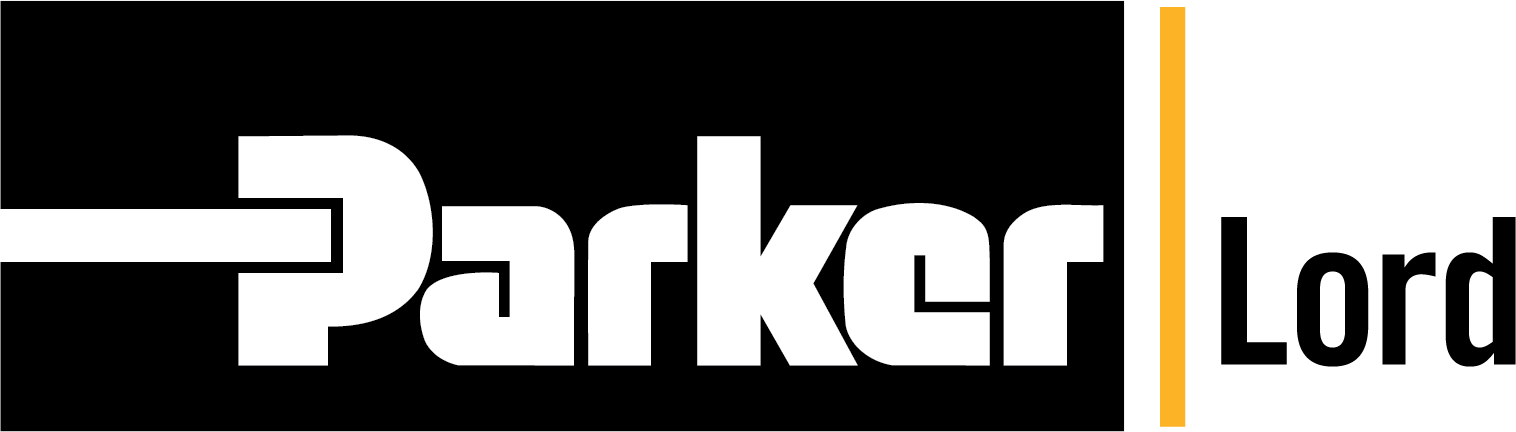
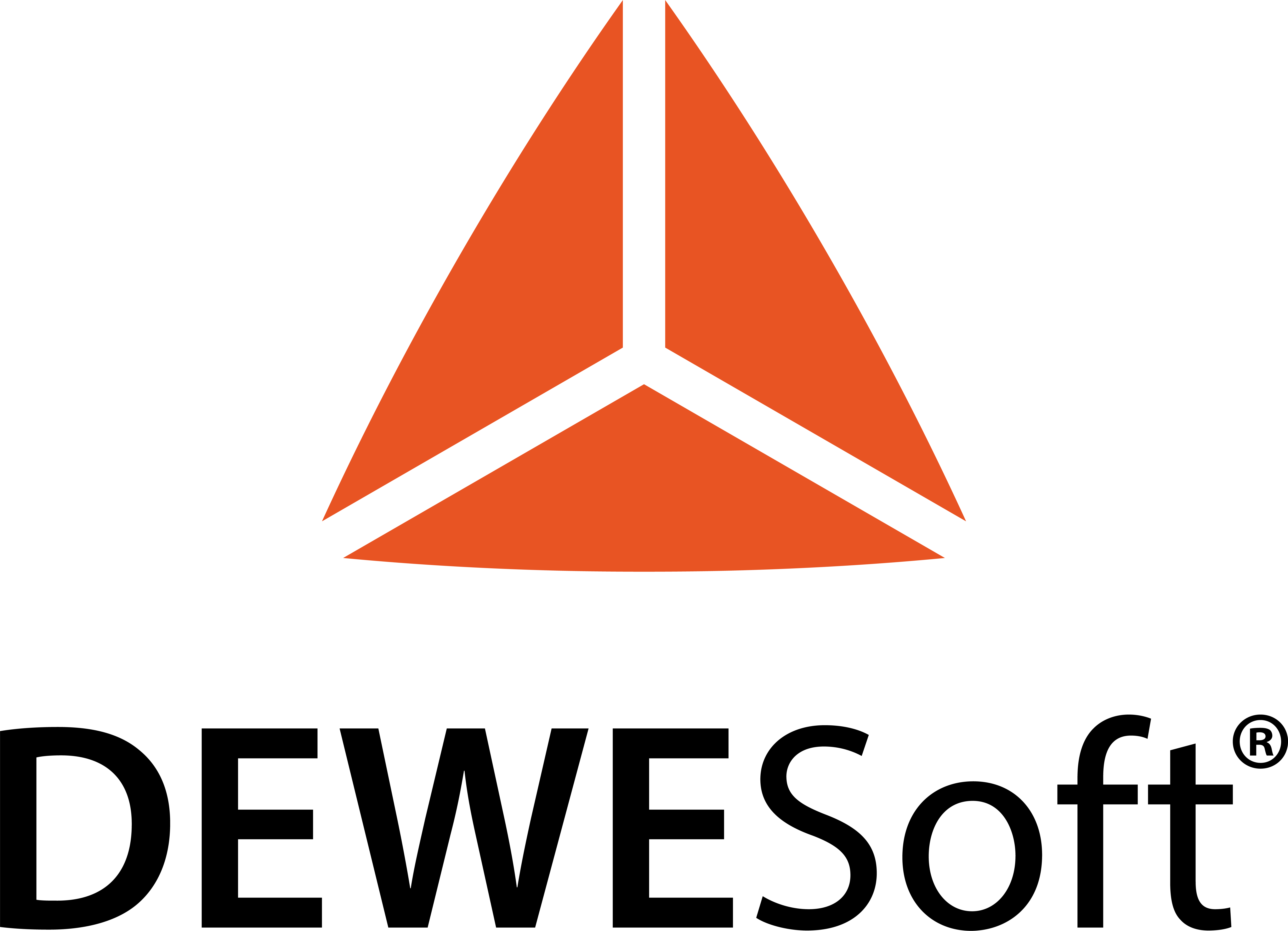
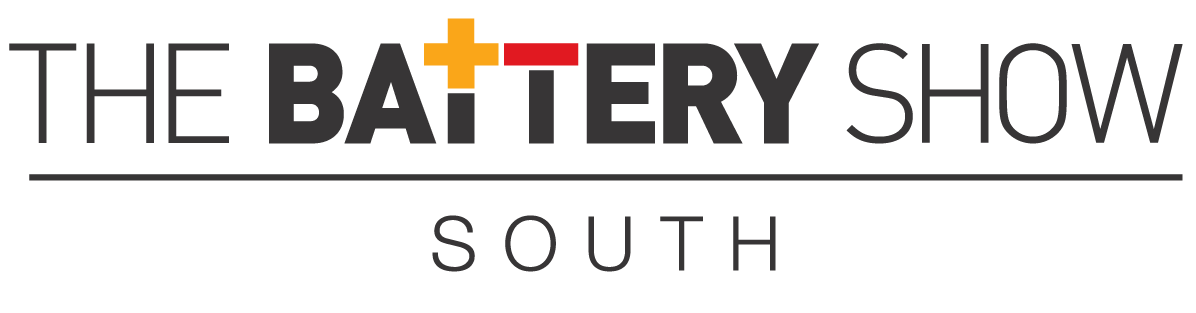
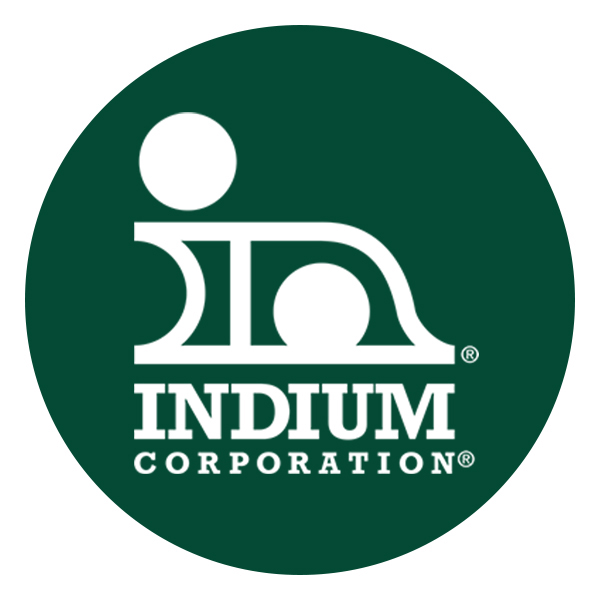
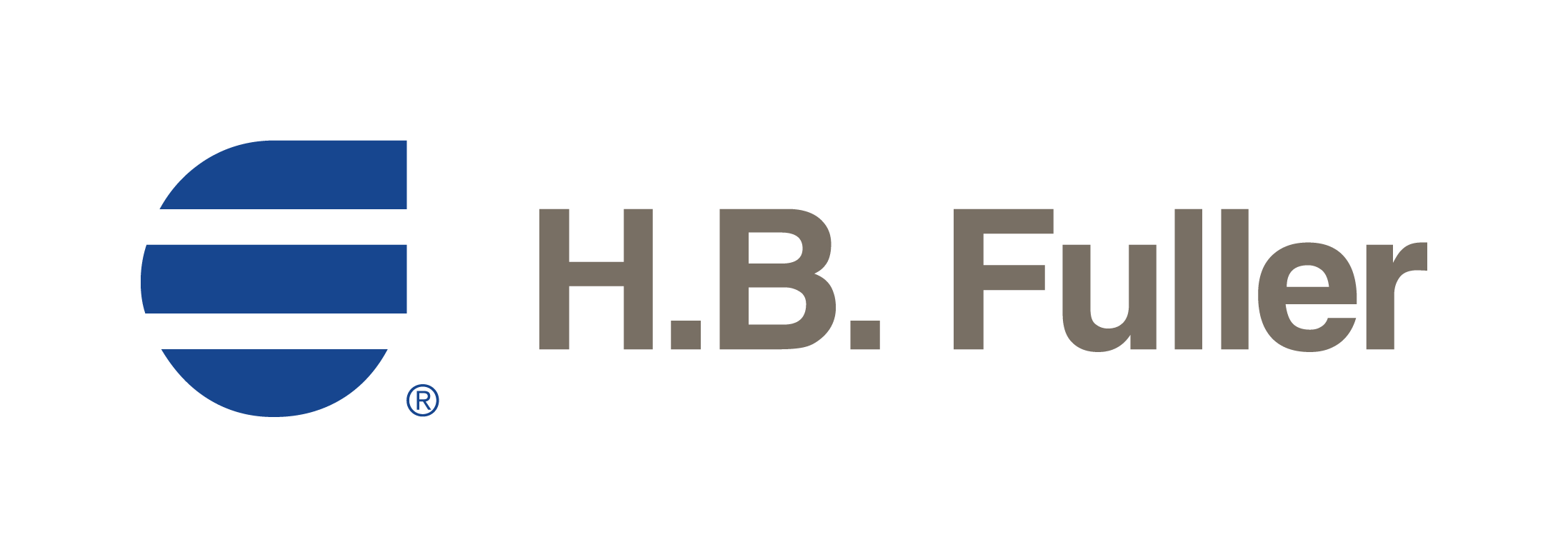