Tesla Octovalve analysis
It’s not often that we get the opportunity to dig into the details of an important EV subsystem from the point of view of an independent engineering team, but that is what Cory Steuben of Munro & Associates provided at the recent Battery Show and EV Tech online event (writes Peter Donaldson).
The subsystem was the Tesla Model Y’s heat pump, in particular the ‘Octovalve’ at the heart of it that controls the flow of working fluid to everything that needs cooling or heating.
Munro & Associates is focused on promoting lean design across multiple industries. One of its key activities is ‘teardown benchmarking’, in which it buys vehicles of interest, dismantles them to evaluate every aspect of their design and then sells in-depth reports about its findings.
Tesla’s Model Y is the latest in a series of BEVs and hybrids subjected to this process. The Octovalve and its relationship with the rest of the thermal management system represents the latest Tesla thinking on the subject to reach the market.
Mounted ahead of the SUV’s front firewall, the core of the heat pump consists of two manifolds, one made of polymer for water-glycol coolant and the other (the ‘super-manifold’) of aluminium alloy for R1234YF refrigerant, as well as a compressor, a chiller (where heat is exchanged between coolant and refrigerant) and the Octovalve.
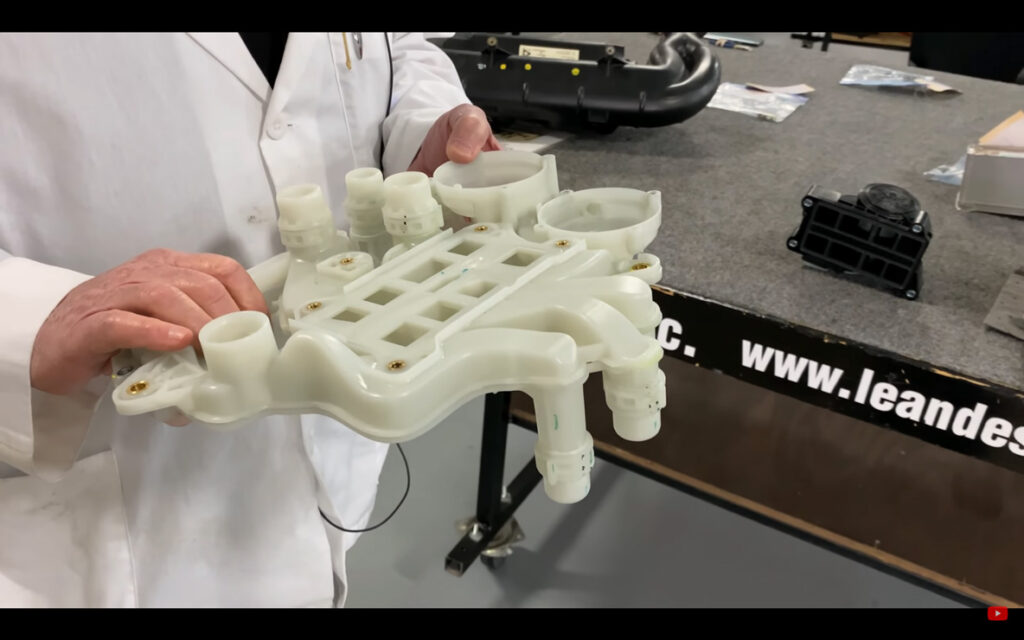
All these components are packaged into a volume about the size of a large briefcase. The two manifolds bolt together, one on top of the other, with the Octovalve attached to the waterglycol manifold.
The rest of the heat pump system’s components are elsewhere. They include a condenser and an evaporator for the cabin, both located (with a fan) in the cabin HVAC case, a low voltage electric heater for the cabin, a liquid-cooled condenser for the powertrain, a refrigerant accumulator and a set of expansion valves in the refrigerant loop. A coolant radiator and a refrigerant condenser are in the conventional location at the front of the vehicle and reject heat to the atmosphere when the whole system is at high temperature.
The other main components include the battery, the front and rear drive units with integral power electronics, and the control electronics with their own coolant loops. Cooling priority is given to the ADAS computer, whose powerful processors receive coolant at its lowest temperature immediately downstream of the chiller.
Water-glycol coolant flow to and from all these components is controlled by the Octovalve, which Steuben describes as a small, unassuming part that looks like a cylinder lying horizontally on its base.
It is a rotary valve, with eight ports that mate to matching ones on the water-glycol manifold; it has five internal valve positions to direct flow through all the coolant loops. It achieves these different positions by being driven through about 270º in one direction and then the other by a motor with an integral reduction gearbox.
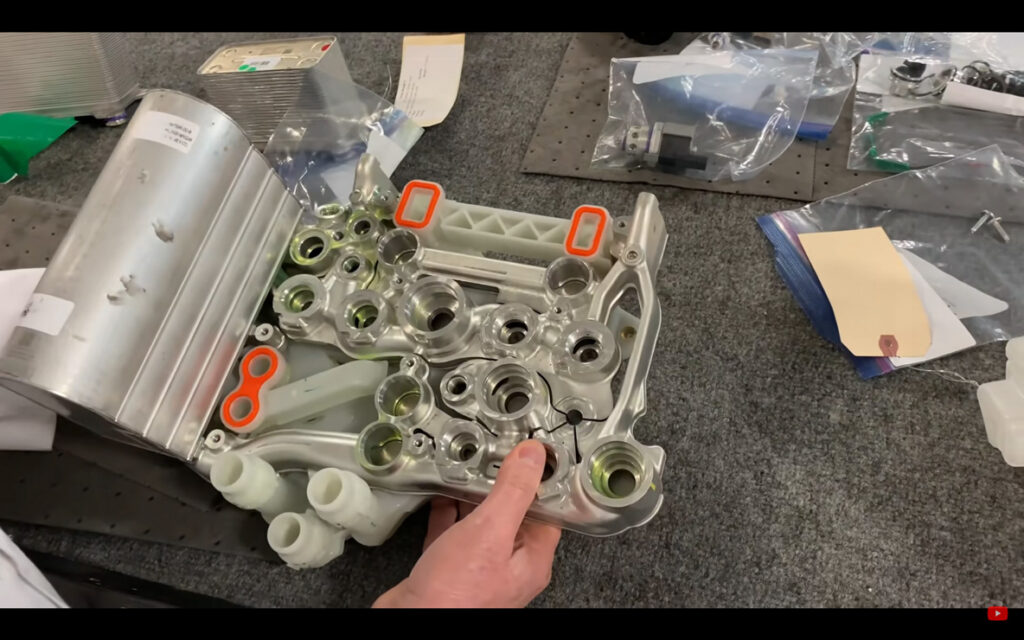
To work this out, instead of dismantling or carrying out any kind of destructive examination of the Octovalve, Munro used CAT scanning to reveal the internal mechanism in all its positions in full cross-section and show how the moving parts interface with the static seals.
Steuben’s assessment was that the Octovalve and the two manifolds make for a very reliable design, because of the large number of separate components, pipes and connections they eliminate. A lower parts count also enables more control of the manufacturing processes, he said.
The refrigerant super-manifold, for example, consists of a plate brazed to a forging and an extrusion (the chiller). That is three main parts instead of the hundreds – including hoses, fasteners, clips and interfaces – in conventional systems such as those Munro found in the Chevrolet Bolt, Nissan Leaf, Jaguar iPace and Audi e-Tron it previously analysed.
ONLINE PARTNERS
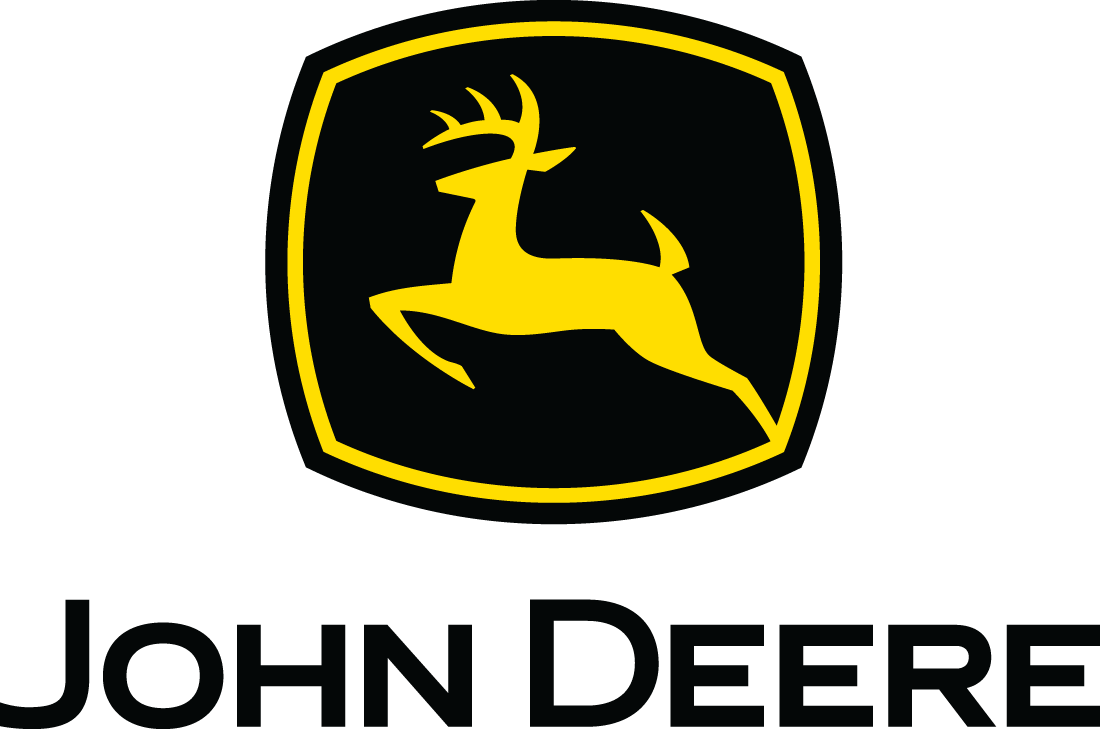
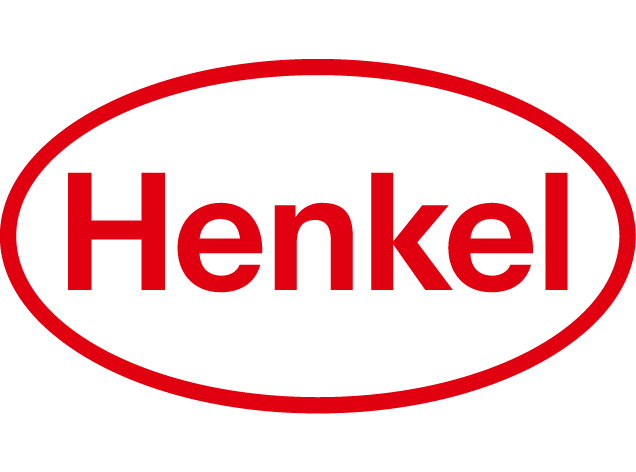
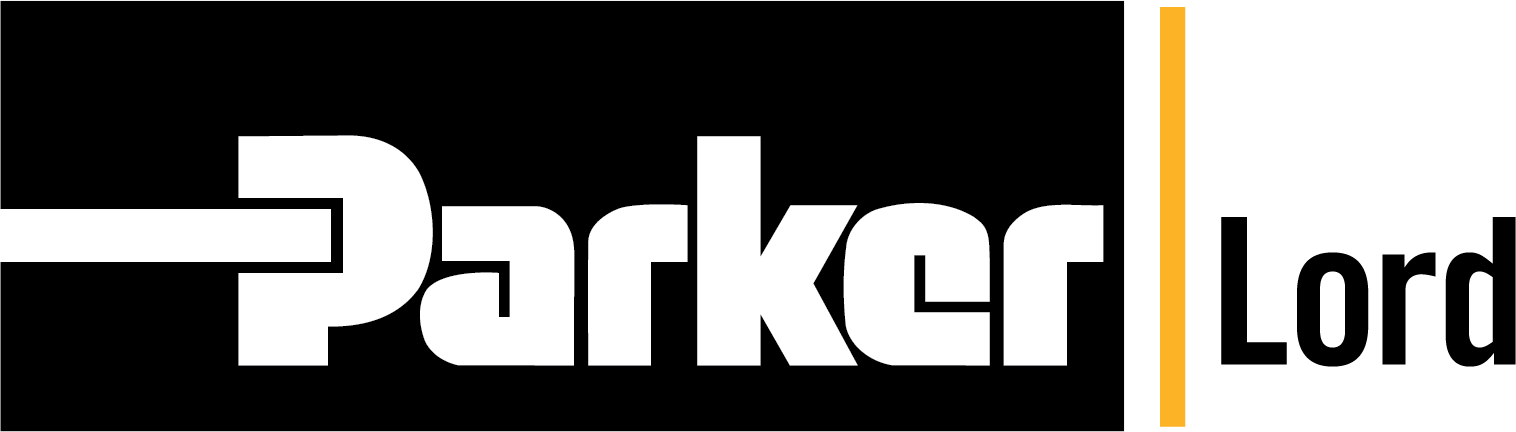
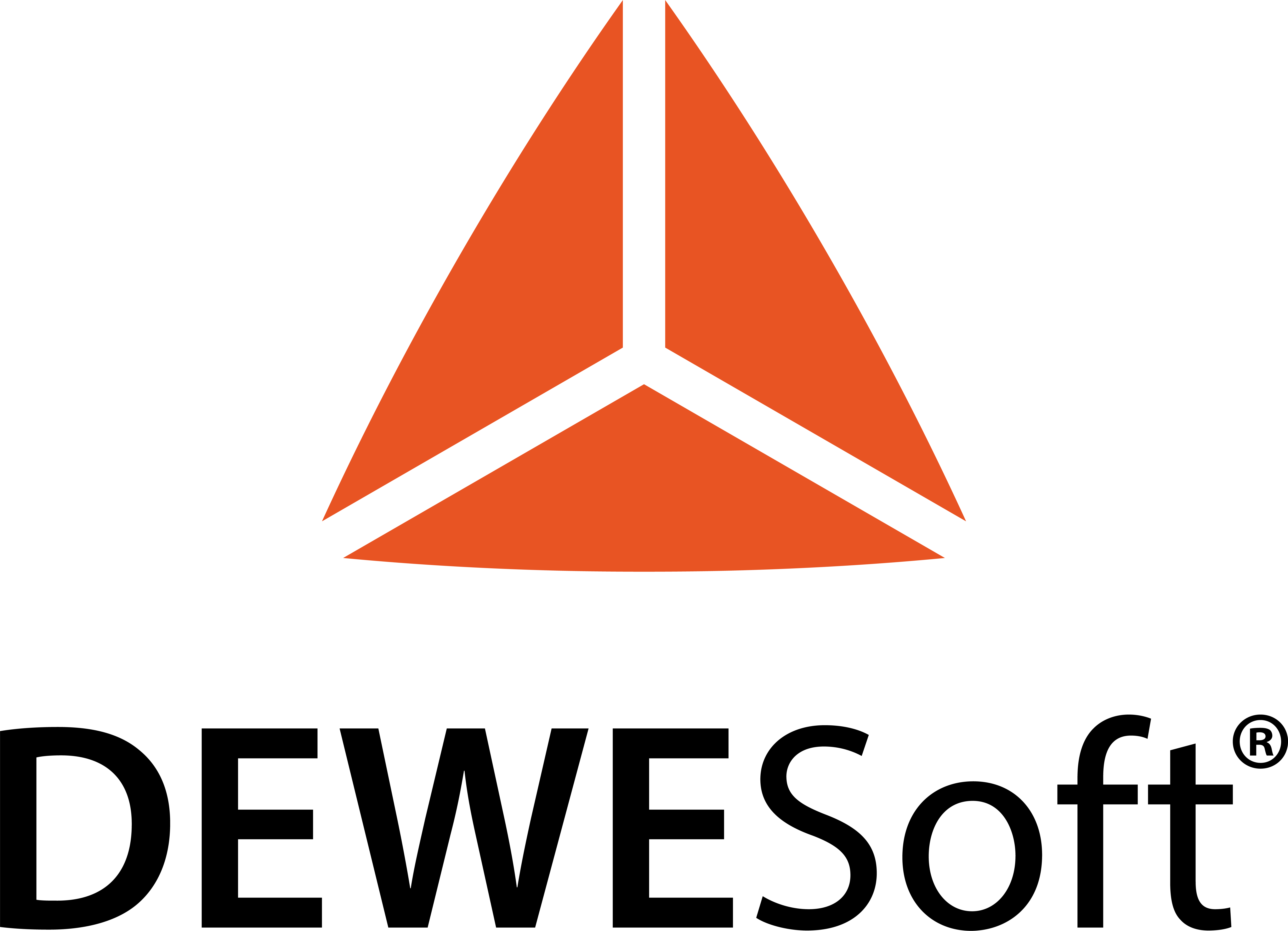
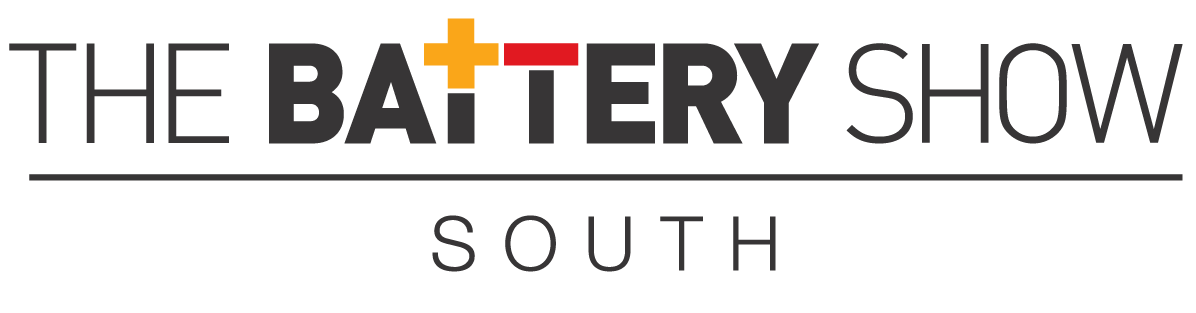
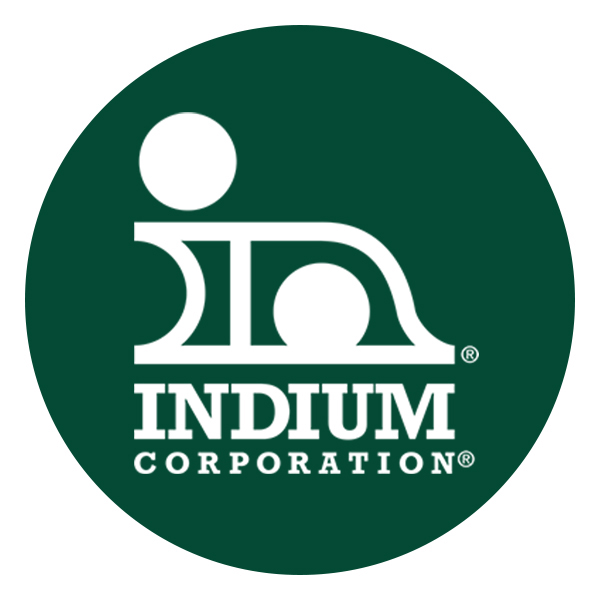
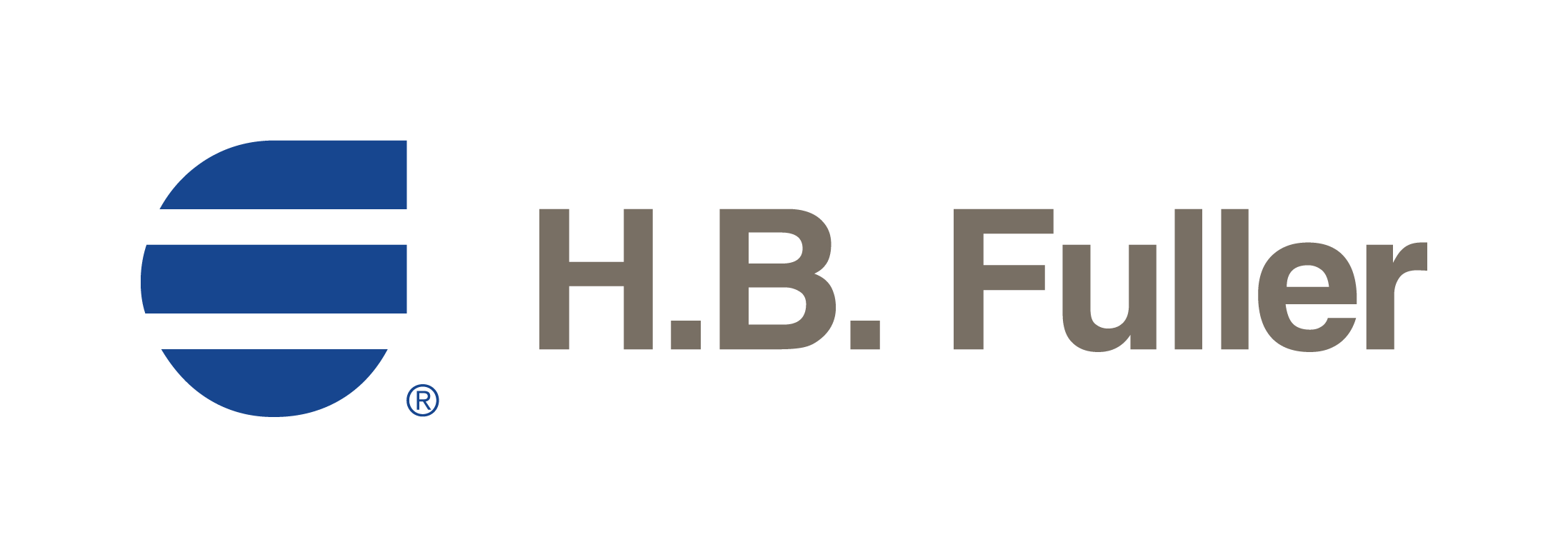