VIA Motors CHEMA skateboard
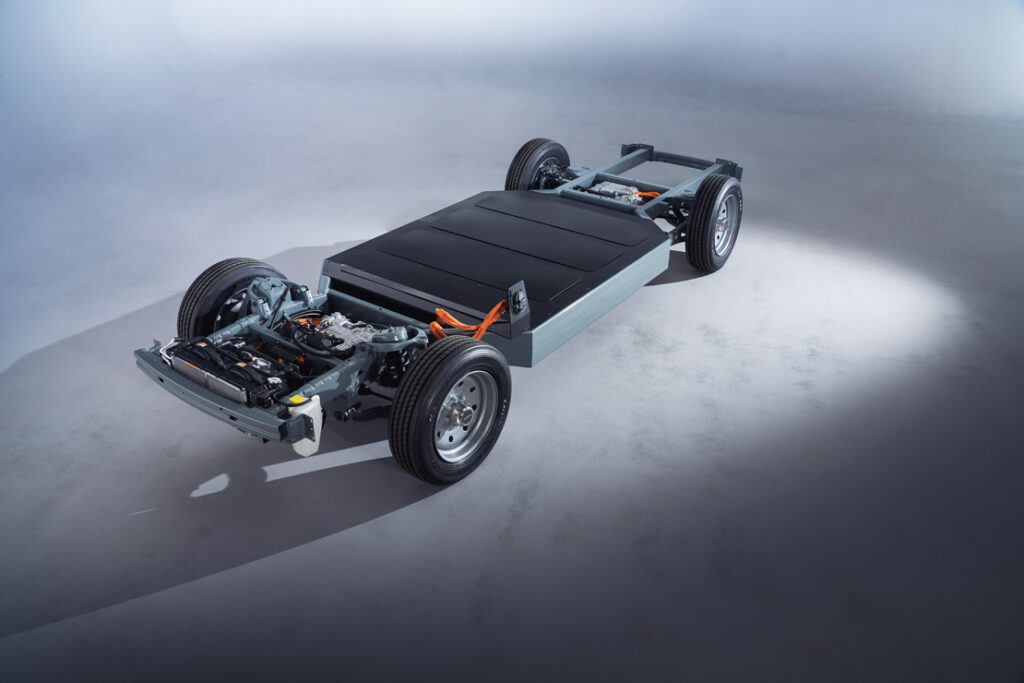
(Image courtesy of VIA Motors)
This hardware system puts modularity at the heart of commercial EV designs. Rory Jackson describes how it was designed and developed.
Flexible working
For more than 10 years, Utah based VIA Motors has strived to develop technologies and system architectures for EVs to bring to fruition its vision for the next generation of electric commercial vehicles.
As previously discussed in this publication (EME 8, Winter 2020), VIA’s solutions for simulating EV performance, integrating components and writing effective algorithms for managing electric powertrains have spurred the creation of electric conversion systems for several popular commercial fleet vehicles in the US.
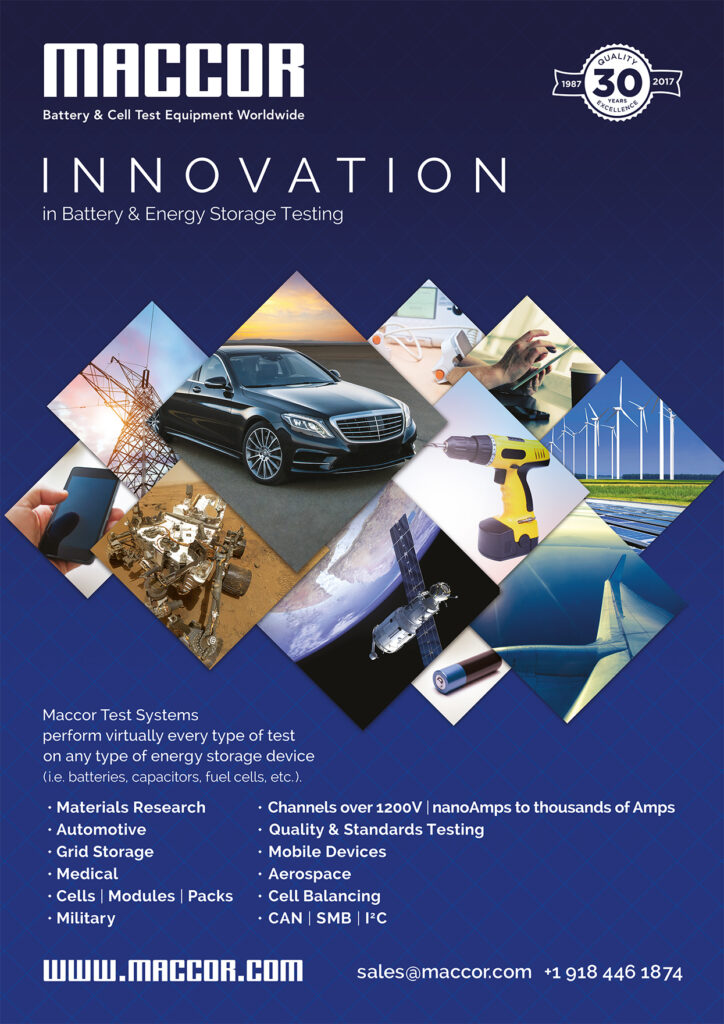
These include PHEV conversions for GM’s Silverado pick-up trucks and Express vans, as well as EV conversions for other Class 2 light-duty trucks, medium-duty vans, 9 m passenger buses and more.
The company’s latest project focus, however, marks a departure from this long-running work, as it transitions into the architectural model most frequently used in the latest generation of blanksheet EVs: the skateboard.
“It’s as much a change of vision as it is a change of engineering approach,” explains VIA Motors’ CTO, Thierry Caussat.
“We’ve long taken a modular, flexible approach in our software, which has been key to rapidly adopting and integrating new, high-quality electric components into our powertrains as they came onto the market, but now we’re doing this on the hardware side too, resulting in our new skateboard platform.”
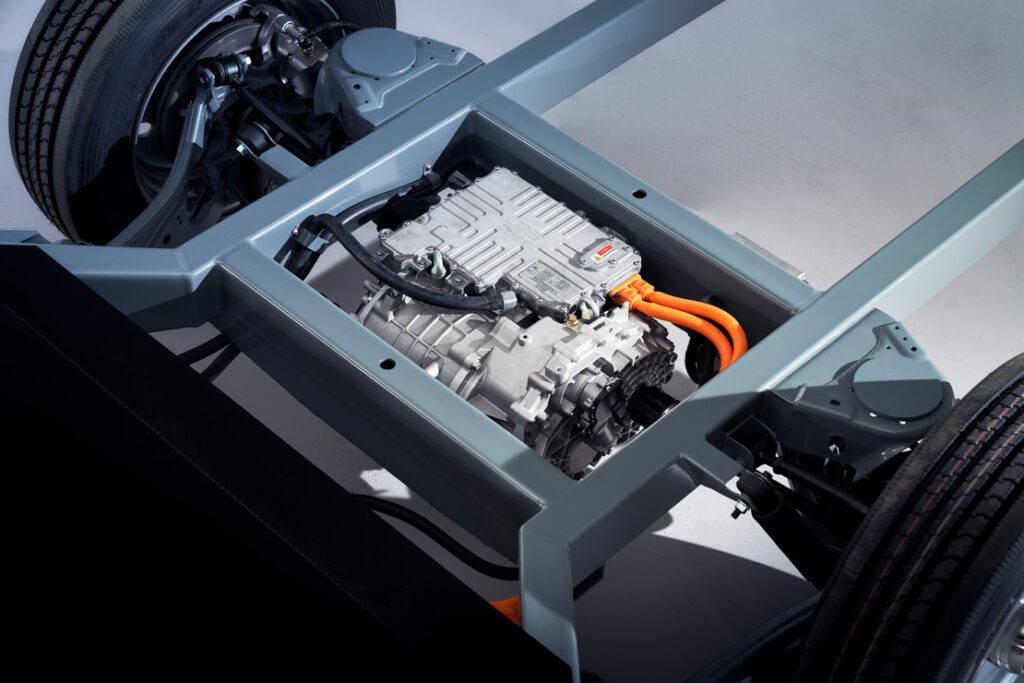
The skateboard represents one of the simplest shapes possible in vehicle engineering. It is a flat board that is easily accessible by technicians from any angle, and is well-suited to linear arrangements of battery packs, with a wheel on each of its four corners, so it is ideal for automotive OEMs prioritising modularity in designs. VIA’s skateboard platform marks one of the first being developed for strictly commercial markets – with a strong emphasis on last-mile delivery services – having these design advantages in mind.
Also, by having a platform that they can design and manufacture from the ground up, and with an open frame for quickly swapping new components in and out for rapid static testing and trial drives, VIA anticipates being able to tune each skateboard project quickly and precisely to the right-size and ideal solution for each customer’s need.
The skateboards are being designed for Class 2, 3, 4 and 5 trucks. These are 5.5-6 m long, have a total payload range (including both cab and carried freight) of between 2200 and 11,000 lb (1000-4989 kg) and a cargo capacity of up to 1280 cu ft. The wheelbase can be adjusted from 2.74 to 5.08 m, and the maximum range of the system is calculated as 124 miles (200 km), using the US Department of Energy’s NREL parcel delivery cycle.
At the time of writing, the initial prototype of the first generation of VIA’s skateboard was beginning full system proof-of-concept trials, and it will be commercially available from June.
“Following development cycles on the road to full production, the first mass-production skateboard specified for payloads up to 2 imperial tons will start mass production around late 2022, early 2023,” Caussat says.
After that, production of skateboard derived Class 4 and 5 vans with the maximum 11,000 lb payload limit is scheduled for 2024.
Platform configuration
To create the base skateboard platform upon which each vehicular solution can be drawn out, simulated and built, VIA first recognised and defined three aspects of EVs – the body, the chassis and the electric powertrain.
“The body marks the final part of any custom project, be it a van or truck, to go on top of the skateboard platform. That base platform consists of the chassis and the electric powertrain,” Caussat says.
The chassis is divided further, into the frame, wheels and suspension, and the braking and steering systems. The powertrain can also be divided into front, middle and rear compartments.
The first and last of these principally provide spaces for traction systems, cooling systems and control systems, whereas the long, flat middle section provides a battery bed, as is standard for skateboard architectures.
Naturally, to supply each customer with a tailored EV without having to start from a blank sheet every time, the company looked for common parameters between commercial fleet EVs that the base skateboard platform could be designed around, so that it could serve as a versatile one-size-fitsall basis for making different trucks and vans.
As Richard Fabini, systems engineering manager at VIA, explains, “With a good understanding of the range of masses and body/cab styles, we performed full vehicle mass studies to ensure our skateboard would accommodate the required axle loads under expected cargo distributions while delivering the necessary traction forces to propel the vehicle.”
These studies were combined with, and trialled in, VIA’s VDrive IDE (Integrated Development Environment).
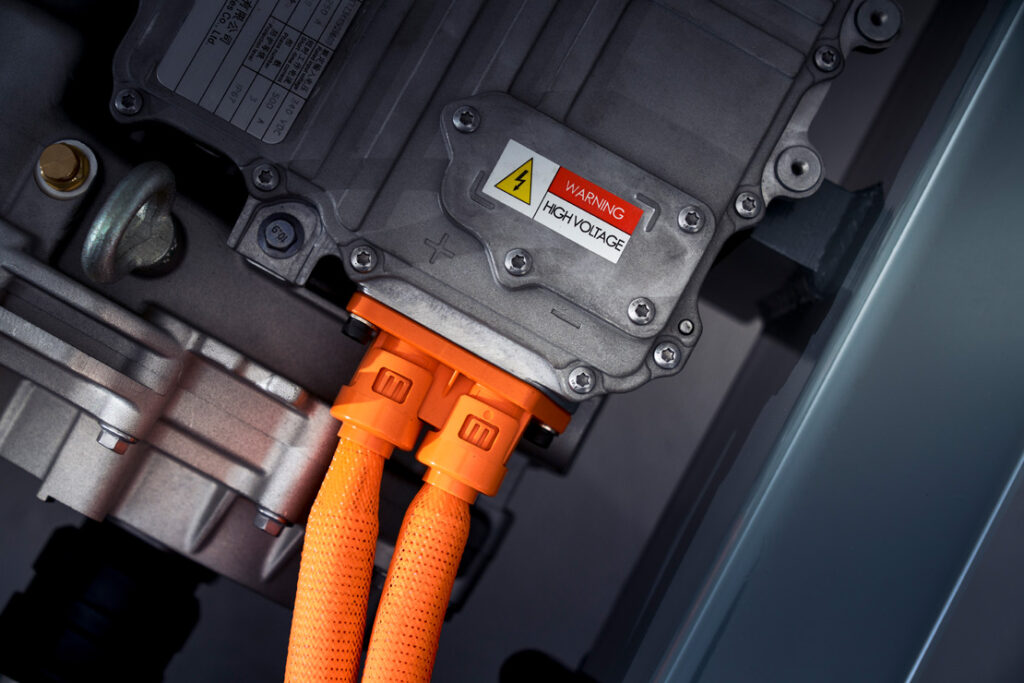
This is an in-house software tool that, among other things, simulates how digital twins of the company’s newest EV design concepts will perform across a wide range of virtual environments and routes.
As well as being critical for defining the skateboard’s optimal battery, powertrain, auxiliary component sizes and other key physical parameters, the software also tests VIA’s control algorithms and CAN communications to verify the component integration and command functions in every vehicle.
The work in VDrive IDE is refined during the development cycle, and becomes the source of auto-generated control firmware that is installed in the vehicle.
The routes encompass a range of urban and inter-city roads, given that VIA targets last-mile delivery companies as its main customer focus. This is expected to serve both the surge in home deliveries spurred by the pandemic as well as the demand for large fleets of vehicles to enable such organisations to move goods from distribution centres to residences.
“The first skateboard-based vehicle we’re making with these characteristics is primarily a front-wheel platform, with an optional all-wheel drive that will incorporate a motor into the rear axle,” Fabini says.
“It’s critical that sufficient traction can always be achieved with the axle drive arrangement, regardless of how the user might alter the weight distribution of their cargo. Combining studies of mass, powertrain capabilities and traction constraints determined how to produce the most useful vehicle and cargo area.”
Manufacturing and autonomy
Costs are the biggest concern for commercial EV fleet managers, and it is well-established that this market’s shift from IC-engined vehicles to EVs and HEVs is motivated mostly by the latters’ lower operating costs, largely in terms of maintenance, repairs and overhauls.
With this motivation, and to ensure high rates of manufacturability and easy mechanical adjustments, VIA’s skateboard platform has been built using as many standard metal parts as possible, which are fabricated in bulk, available in great capacity, and offered by a wide range of suppliers.
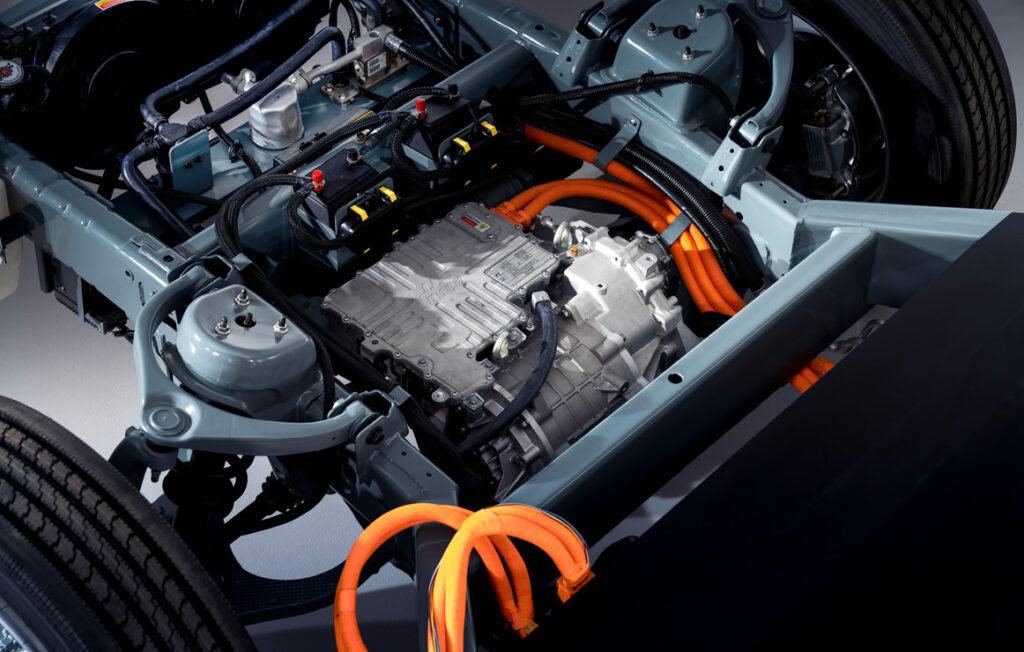
That allows the base parts of each skateboard to be purchased and assembled cost-effectively, using repeatable, industrialised techniques instead of needing any expensive investments in new tooling, such as customised dies, forming equipment or specialised joining techniques.
“By keeping prices low on both our vehicles and the parts needed for future structural repairs or replacements, we lower fleet managers’ upfront and operating costs,” Fabini says.
“With that in mind, our skateboard platform is made largely from standard steel material grades and sections, all of which are being manufactured constantly, so we never need to request a batch of anything specific, they’re just always available.”
Aluminium was also considered early on, especially for its mass advantage over steel, but the high prices of aluminium components and their lower structural rigidity made them unsuitable. Steel, on the other hand, supported the team’s performance goals and cost targets, proving to be the right match for the application.
Fabini says, “If some areas need greater strength to prevent intrusions into the battery packs, we can have individual parts made from high-strength steel. Coupled with FEA crash modelling tools, our VDrive software can evaluate the trade-offs between mass in different structural implementations, as well as thermal and electrical components across the vehicle, to quantify the benefits of different parts or materials.”
As well as VIA using its own software, engineering firm Ricardo has provided extensive engineering consultation and r&d collaboration to VIA, particularly on the frame-wide and subsystem-level analysis and simulations that have led to the skateboard platform in its current form.
Caussat adds, “With a fixed cost point in mind for the skateboard, we can be flexible with almost every other component. We can vary the sizes of battery packs, the size and type of motor – asynchronous or permanent magnet – and the computer hardware and amounts of cabling used for all other functions.”
On the topic of functions, the CTO notes that at the other end of the cost considerations for fleet operators is autonomy, given that self-driving EVs could result in more battery-efficient driving behaviours, fewer accidents and other cost-saving benefits.
Incorporating autonomous capabilities into the skateboard platform would increase complexity, owing to integrations of drive-by-wire actuators for steering and braking, with perception-layer sensors such as Lidar, ultrasonic and vision systems. These would naturally increase the upfront price, Caussat notes, but it remains a perennial point of interest among commercial delivery firms.
“The essential interfaces needed for connecting autonomy components to our ECUs and microcontrollers are all present in our skateboard platform,” he adds. “We have a partner we’re working with to develop our autonomy system architectures, and we have laid out plans with them to work on the current and the next generations of our skateboards, which will scale up in weight capacities, so we want to be sure that every customer has the option of autonomy.”
For initial production for customers in Mexico and South America, VIA has contracted AT Motors (which is in Mexico). It has a large network of dealers, service centres and parts warehouses throughout the country, which will provide a hub for assembly, repairs and final checks of VIA’s skateboard-based vehicles.
Traction compartments
As mentioned, the front and rear sections of VIA’s skateboard platform can integrate motors and transmission across electric, hybrid, and fuel configurations, although initial versions will be produced for a front-wheel drive with a transverse electric propulsion system, and the option of all-wheel drive.
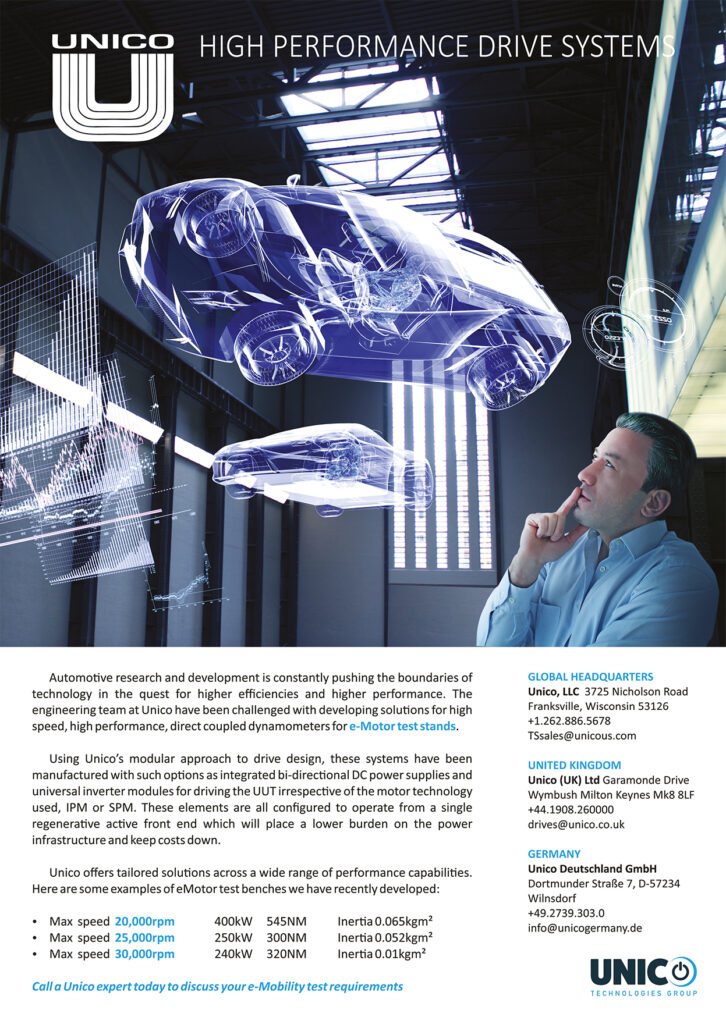
The front traction compartment of the skateboard is 500 mm long and 680 mm wide, while the rear traction compartment is 640 mm long and 780 mm wide.
Also, the front crush zone compartment is 475 mm long and 820 mm wide, while the rear crush zone compartment is 625 mm long and 950 mm wide. This ample spacing facilitates the easy placement of the skateboard’s components.
VIA has worked with numerous partners to simulate and determine which of its propulsion systems could be integrated and used on board the skateboard.
“The traction solution we’ve opted for is styled as a ‘three-in-one’ design, in that the three major traction components are integrated inside a single housing,” Caussat explains. “That’s the motor itself, the inverter and the transaxle gearbox, which is a single speed transmission for the sake of simplicity and longevity.”
By integrating these components, the modules can share a common cooling system, HV and LV cabling to the rest of the EV (with no significant interconnections needed between the three constituent machines), along with mounting points for further ease of integration on vehicles.
“This kind of motor-inverter-gearbox greatly reduces copper quantities, number of cooling pipes and connectors, the isolation and number of silicone jackets. It creates so much simplicity, which is not only helpful but resonates so well with what we’re trying to achieve in our development cycles with our skateboard,” Caussat comments.
VIA is in talks with a partner that supplies just such a three-in-one module, although details about it have yet to be announced.
The front section of VIA’s skateboard platform will also integrate other key components in line with classic automotive designs. Primarily this will mean a heat pump, radiators, fans and other heat exchange devices for thermal management, given the frontal airflow.
“We’re also going to place some key low-voltage components in the front as well, including the fuse box, water pumps and so on, in a sub subcompartment forward of the traction compartment,” Caussat adds.
Fabini continues, “We have flexibility in what can go where forward and rearward of the traction system, but we do need to maintain the position of the steering rack, so there are some constraints.
“We’ve also identified a dozen different suppliers of good, tightly packaged traction solutions, with a variety of performances and cost levels. None of them will be too difficult to integrate, given the size of the front and rear compartments, it’s just that the selected electric transaxle makes a lot of sense for cost, packaging and other considerations.”
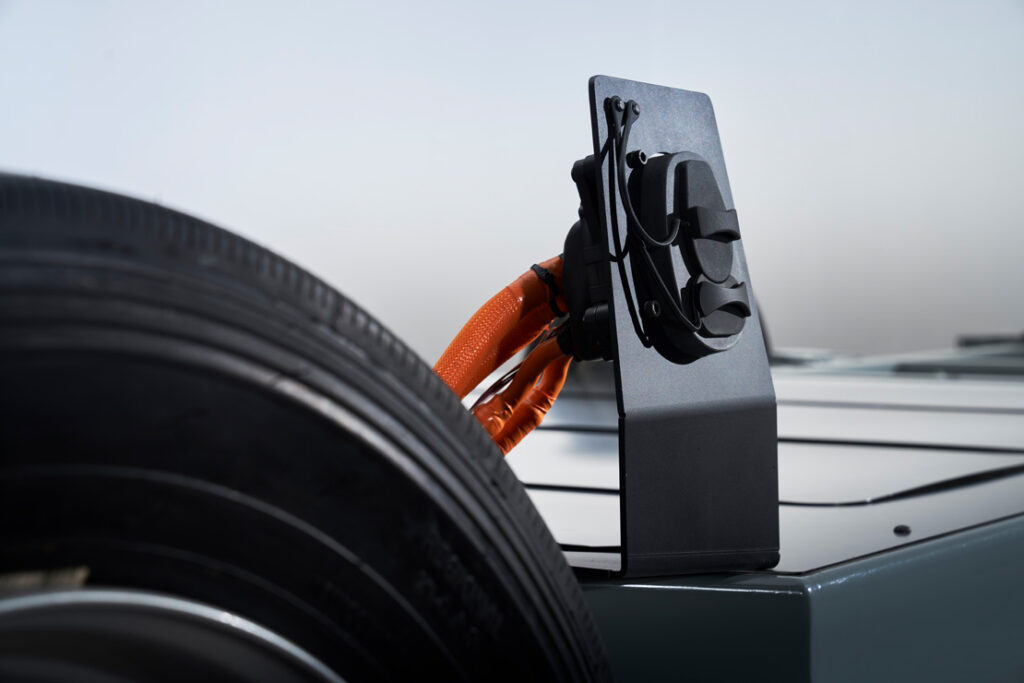
The flexible architecture also means power distribution or charging systems can be moved to the back if that’s more convenient for a customer’s charging station arrangement.
Series-hybrid powertrains can also be installed, for example with an IC engine and generator in the front to charge batteries on lengthy highway journeys while keeping the traction motor in the rear.
“We also have the flexibility to use inwheel motors,” Fabini notes. “We’re not targeting that initially, but they could be integrated, we’d just need to investigate the impacts on the suspension and frame loads since we’d be moving a lot of mass to the corners. But we’re definitely proponents of the technology, and we’re sure all that could be managed easily enough.”
Midsection
As mentioned, the middle of the vehicle is used mainly for energy storage, although in addition to battery packs, equipment for key functions such as charging and power distribution will typically be mounted in the middle. The skateboard’s battery zone is 2130 mm long and 1600 mm wide.
“We’re very flexible regarding the kinds of chargers we can integrate – from Level 2 AC charging at 6 or 7 kW all the way up to 15 kW, but we can also just put in DC fast charging, which can range up to 150 kW,” Caussat explains.
“While DC fast-charging infrastructure is widely available in the 50 kW range, modern DC fast-charging standards support up to 350 kW. Fleets have a variety of needs, and VIA’s skateboard will offer solutions that achieve those, from overnight charging to high-power charging during load/unload.”
Taking all that into consideration, VIA selected an onboard charger that would best suit the needs of customers, with the current onboard charger able to charge at 32 A and 6.6 kW at 220 VAC, with a 95% efficiency rating. However, owing to the flexibility of VIA’s skateboard platform, the company can easily incorporate a different charger for specific use-cases.
In a similar way to its motor considerations, VIA is looking into a range of partners and products for batteries, to identify any advantages in specific energy, energy density, cost per kWh and other key parameters.
The integrated design approach also incorporates the battery’s contribution to the overall frame structure for bending, beaming and crash deformation, to improve safety and reduce the skateboard’s cost and mass.
“While we have a lot of in-house knowledge of batteries, we have started working closely with a battery r&d and production company, who have been helping us to define the best way to configure batteries across the different users and applications,” Caussat says.
“We provide them with high-level requirements, and they study those and the available technologies, to discuss with us what kinds of anode and cathode chemistries and other parts we could use to optimise cost, production volumes and performance according to our constraints.”
Although requirements can vary from customer to customer, the platform does have a few maximum specifications for the battery, including 100 kWh of maximum realistic energy, 650 kg of maximum realistic mass, and 680 litres of maximum realistic volume. Also, a 200 km range has a base requirement of an 85 kWh battery.
In addition, the company’s work with Ricardo has covered extensive structural analysis of the frame, including a number of virtual crash tests designed to investigate the potential for intrusions into the battery compartment.
While the chassis, body and supplementary restraint system work in conjunction to protect the occupants in event of a crash, a primary responsibility of the frame is to prevent intrusion into the battery compartment. Even in the worst frontal/rear offset and sidepole impacts, battery integrity must be maintained, to prevent cell deformation, short-circuits and fluid leaks.
“The physics of how metals crumple and deform are well-understood, and by keeping everything in our skateboard beneath the cabin floor – including batteries, electric powertrain and auxiliaries – they won’t ever intrude into the occupant compartment,” Fabini says. “This is easily achieved and marks a significant advantage of EVs, whereas a lot of work has to be done to keep taller engines and transmissions away from the occupants in IC-engined vehicles.
“Today’s virtual tools lend themselves well to simulating all aspects of the vehicle and confirming the levels of performance and functionality, while identifying how to improve the cost, serviceability and other parameters.”
Future plans
With the goal of transforming commercial fleets and last-mile deliveries, VIA is continuing its studies into how full-vehicle designs based on VIA’s skateboard platform can be optimised, with the next stages of research being to characterise how the dynamics and materials of different bodies interact with the chassis and powertrains.
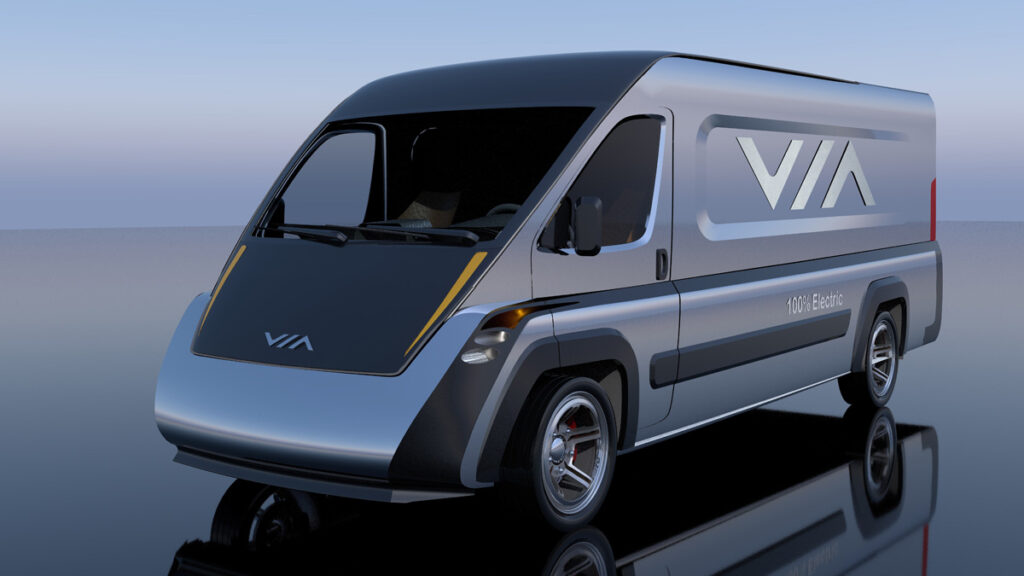
Further research will study how different bodies will interact with VIA’s skateboards, with class 4 and 5 vans carrying up to 11,000 lb scheduled for production in 2024As Caussat says, “At the end of the day, the skateboard must be truly modular – and that means being able to pair it with any reasonable kind of body that will be compatible with the cost, chassis, route and range required by every customer.”
Specifications
VIA modular skateboard platform
Length: 5.5-6 m
Wheelbase: 2.74-5.08 m
Payload capacity: 4989 kg
Maximum range: 200 km (at 85 kWh)
Maximum energy storage: 100 kWh
Maximum cargo volume: 1280 cu ft
ONLINE PARTNERS
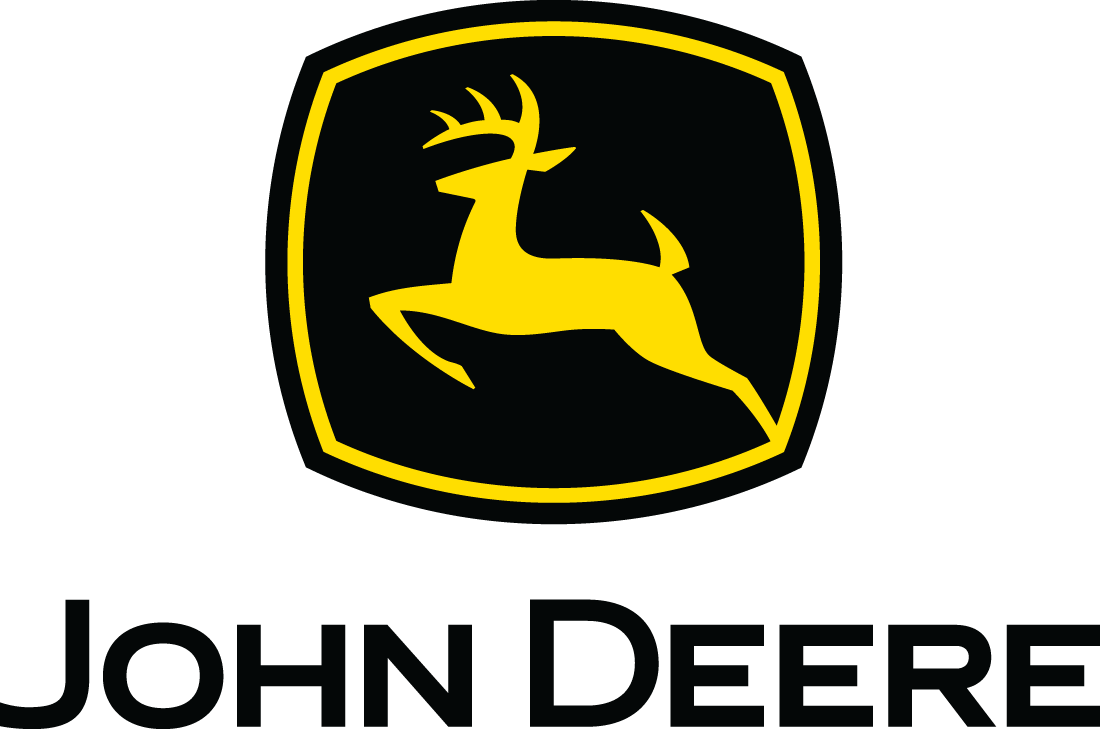
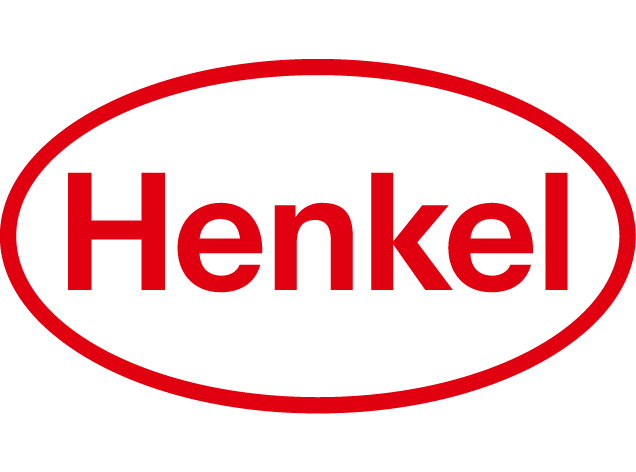
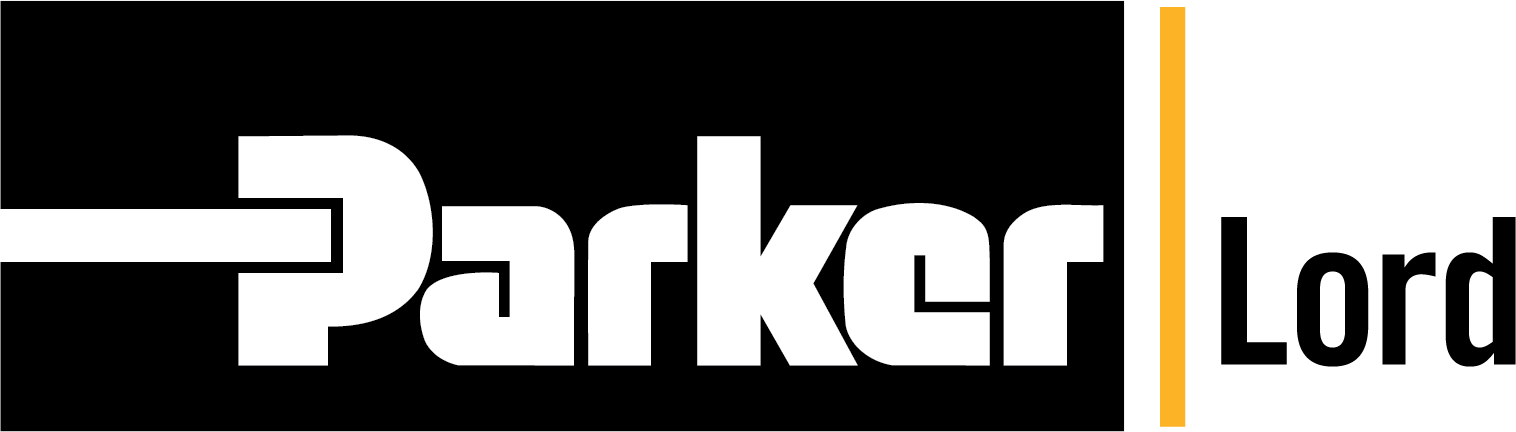
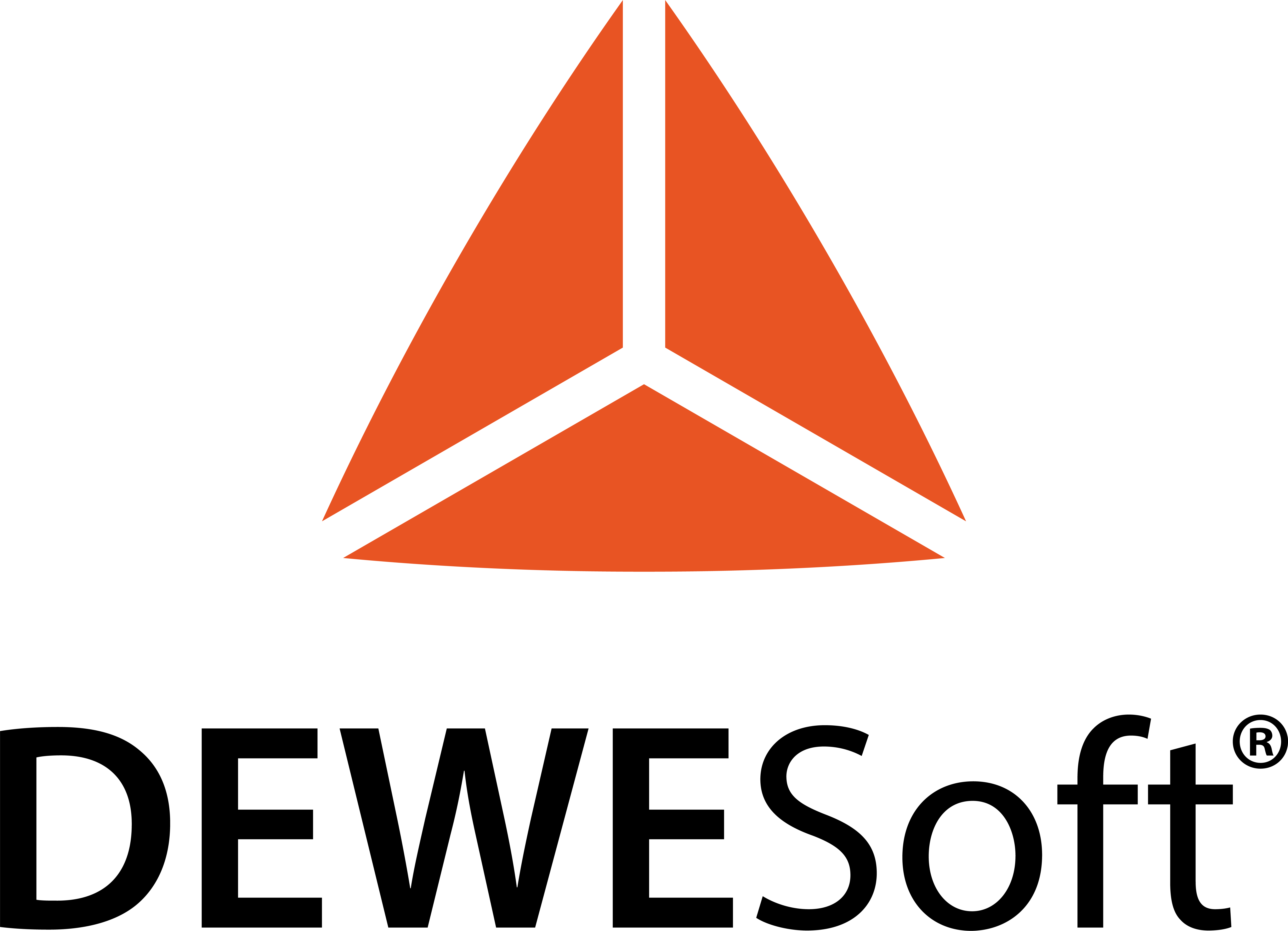
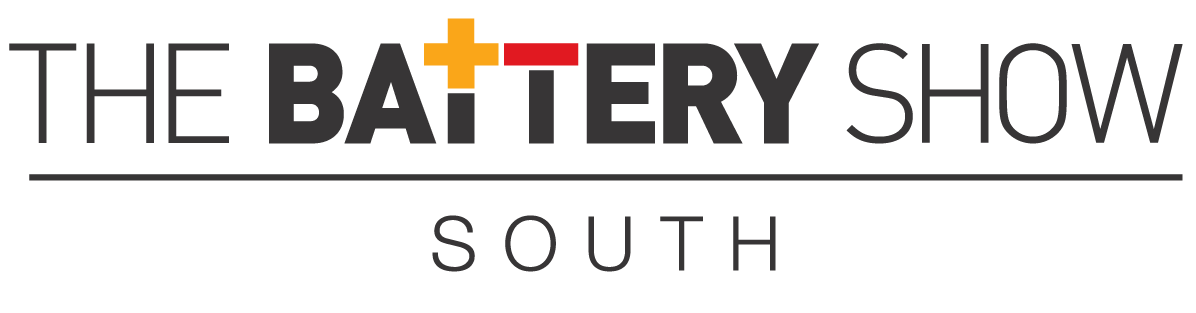
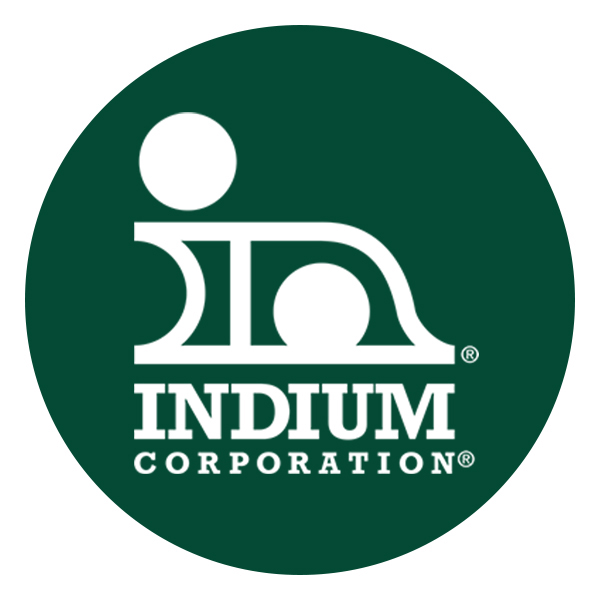
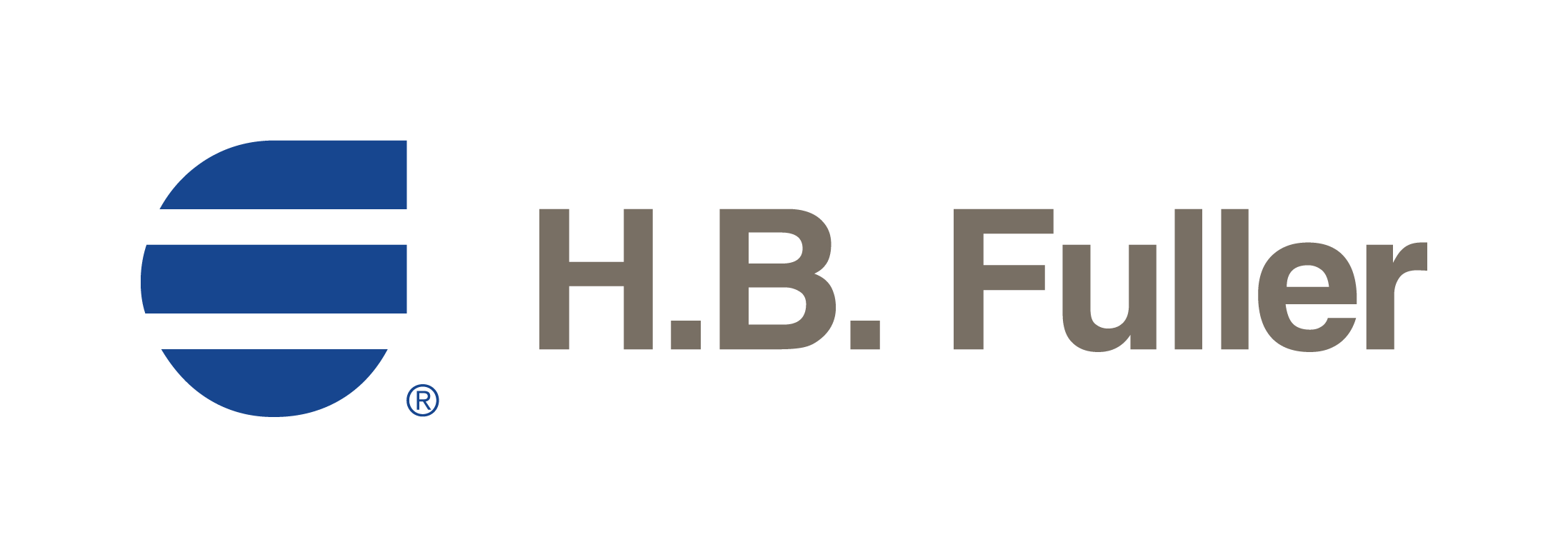