Hydrogen
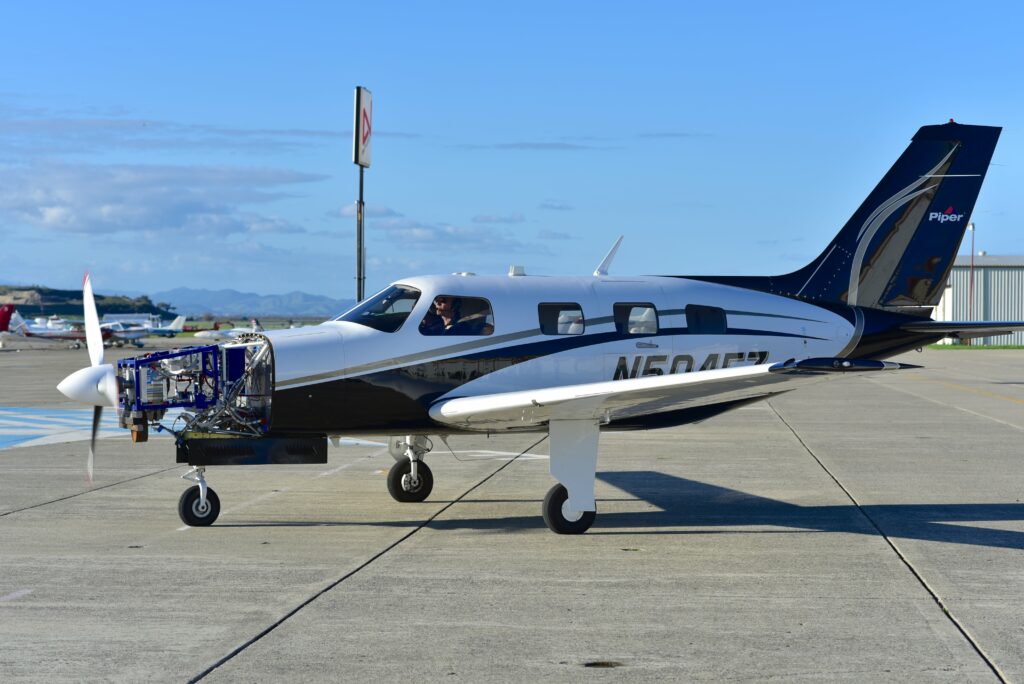
(Courtesy of ZeroAvia)
It’s all taking off
Nick Flaherty highlights some of the inroads developers are making into rolling out a range of hydrogen-powered vehicles.
Many of the engineering challenges with converting hydrogen to electricity to drive a motor in a vehicle have been addressed over the past decade through the development of fuel cells with hydrogen-powered cars and buses on the road. The proton exchange membrane (PEM) stack technology has proved to be an effective catalyst for combining hydrogen with oxygen to produce electricity, and the storage and management of hydrogen at pressures of 300 and 700 bar is now well-established.
There have remained significant engineering challenges though to the mass production of hydrogen-powered vehicles.
One of those is safety. With hydrogen under a pressure of 700 bar in a passenger car, the certification of the vehicle as safe even in a crash has been a key barrier. Now though, the Euro NCAP safety organisation has certified its first hydrogen-powered family car, Hyundai’s Nexo, at a safety level of five stars.
The Nexo follows Honda’s hydrogen-powered Clarity, which has been available for the past 10 years in the US and Japan, and Toyota’s Mirai that has been on the market for four years. Certifying more hydrogen-electric passenger vehicles helps to spur the volume production of components and drive down the cost of key parts such as the PEM stack and compressor for other transport sectors.
However, the supporting infrastructure has been slow to roll out to support volume production of vehicles. The infrastructure is a complex mix of supplying hydrogen via cylinders or a gas pipe network, or producing the hydrogen on-site using an electrolyser driven by the electricity grid or a renewable energy source.
Bus and truck applications are increasingly using hydrogen to produce electricity, and for a number of reasons. The first is to provide more range than is currently available with batteries, as hydrogen fuel tanks can be filled quicker than recharging a battery pack, although there are issues with the different pressures used as this can determine how quickly a fuel tank can be filled.
Bus depots and distribution centres have the space for an electrolyser, which is usually housed in a shipping container. The containers were previously connected to the local electricity grid, but they can now be connected to renewable energy sources such as wind, hydroelectric or solar power.
This is also an advantage for the hydrogen-powered aircraft being developed. For example, a 20-seat, midrange electric aircraft with a range of 500 miles is being developed by ZeroAvia that would be able to use 500 airports across the US. This is achievable for a network of electrolysers using renewable energy.
Fuel cells
Fuel cells based around a PEM stack for heavy-duty bus, truck and now marine systems are a major focus for the longer journey times where battery packs are too large and too heavy.
These are now achieving economies of scale by using a common PEM design. Ballard, which sold its car fuel cell business to Daimler in 2005, has developed an 85 kW fuel cell module that has been integrated into buses for ADL, Wrightbus, Solaris and a Chinese OEM. It has been designed with a focus on operational maintenance and replacement, rather than the initial cost of the stack.
Having low-cost replacements of the stack and hydrogen pumps has become the key engineering design challenge. For example, a key requirement is that the fuel cell can start operation at temperatures down to -25 C without having to plug the vehicle into an external energy source. This is achieved by using lubricants for the hydrogen pump with a lower freezing point; they are more expensive than other lubricants but reduce the overall cost of operation.
Another engineering approach has been to make the design of the PEM stack modular and scalable, so Ballard has a 70 kW version for smaller urban transit buses, and a 100 kW version for longer ranges. This modularity comes mainly from increasing the number of modules in the stack, as well as increasing the pressure of the hydrogen passing through them. However, higher pressures increase the cost of the ancillary components and create more issues with reliability and lifetime.
A 30 kW version from Ballard can also be used as a range extender with a smaller tank of hydrogen to boost the performance of an electric bus and reduce the need for recharging. The cell can also be used for 7-8 tonne delivery trucks, and there are now 600 of these on the road in China using this technology.
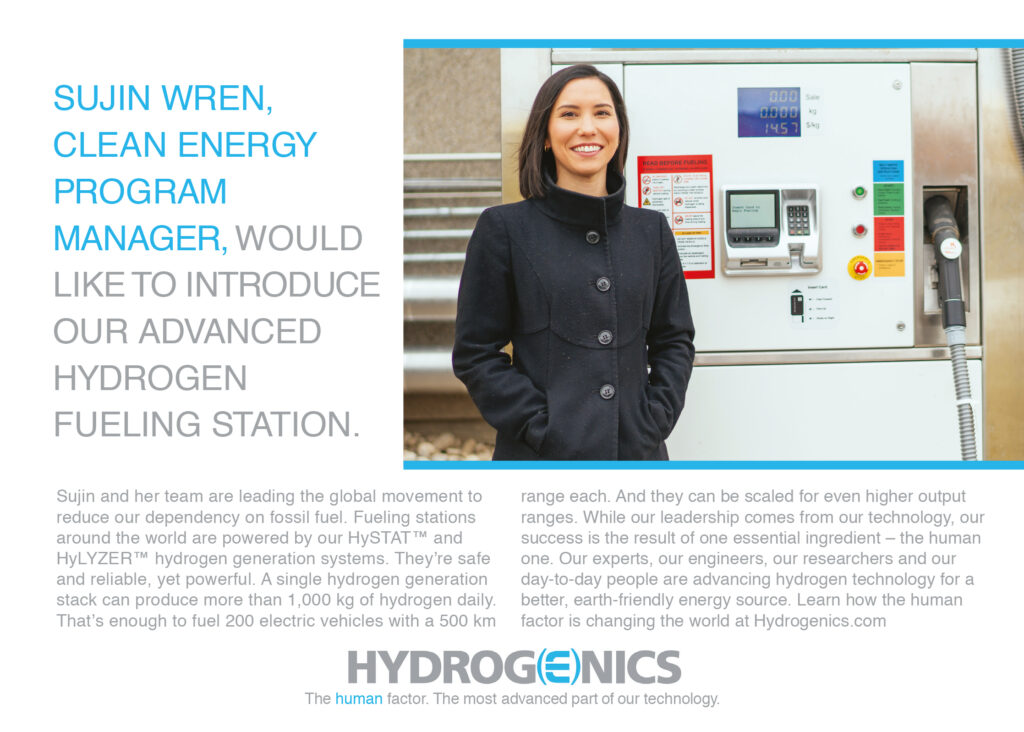
A hydrogen train would use a power level of 200 kW with two of the 100 kW fuel cells, while a ship might have four or five of the 200 kW fuel cells to produce 800 kW to 1 MW.
Improvements in battery technology have also helped with the adoption of fuel cells. With no battery, the fuel cell has to be large, from 300 to 500 kW, to accommodate all the acceleration of the vehicle. Now the peak power can be delivered by a battery pack that is a fraction of the size of the one in a battery-electric vehicle, and recharged by the fuel cell and any regenerative energy captured from the braking system. This also avoids putting too much stress on the battery pack, extending its lifetime.
All of this means that fuel cell technology has reached the optimum point where the cost has fallen from tens of dollars per kW to $1/kW for the entire system at volume production.
As much as 70% of the cost of a battery is the raw materials, such as lithium, nickel and cobalt, which makes it hard to achieve further cost reductions. In contrast, all the cost of the fuel cell is in the manufacturing, so there is potential for designs to reduce the costs. Automated volume production by companies such as Bosch in Germany, Cummings in the US and suppliers in China are replacing the current hand-assembled modules.
A bus is typically on the road for 12 to 14 years, and the fuel cell supplier needs to make sure the cost of the cell is lower than a diesel engine over that time. This is especially so in the truck market, which unlike the bus market is not subsidised. That has implications for the design of the compressors and filters, for example how often the filters have to be changed.
Previously, the stack in the fuel cell was the most expensive element, but as the cost of the stack falls the overall cost is a balance of components such as the pumps and compressors. The key is to work with the supply chain for the plumbing of the fuel cell, the pumps and compressors, pipes and valves to reduce the price. This is where the growing number of automotive OEMs developing these components is positive for the bus and truck markets.
However, the heavy-duty stack needed for bus and truck applications needs to have a working life of 20,000-30,000 h. For example, the fleet of 10 hydrogen-powered buses in London are now being refurbished, after the fuel cells reached more than 30,000 h.
The fuel cell maker refurbishes the fuel cell, removing the carbon-plated stack and the membrane electrode assembly (MEA), recycling the platinum catalyst in the membrane and 96% of the metal. The carbon plates are washed, the MEA in the stack is reconditioned, plated with a new layer of platinum and re-installed.
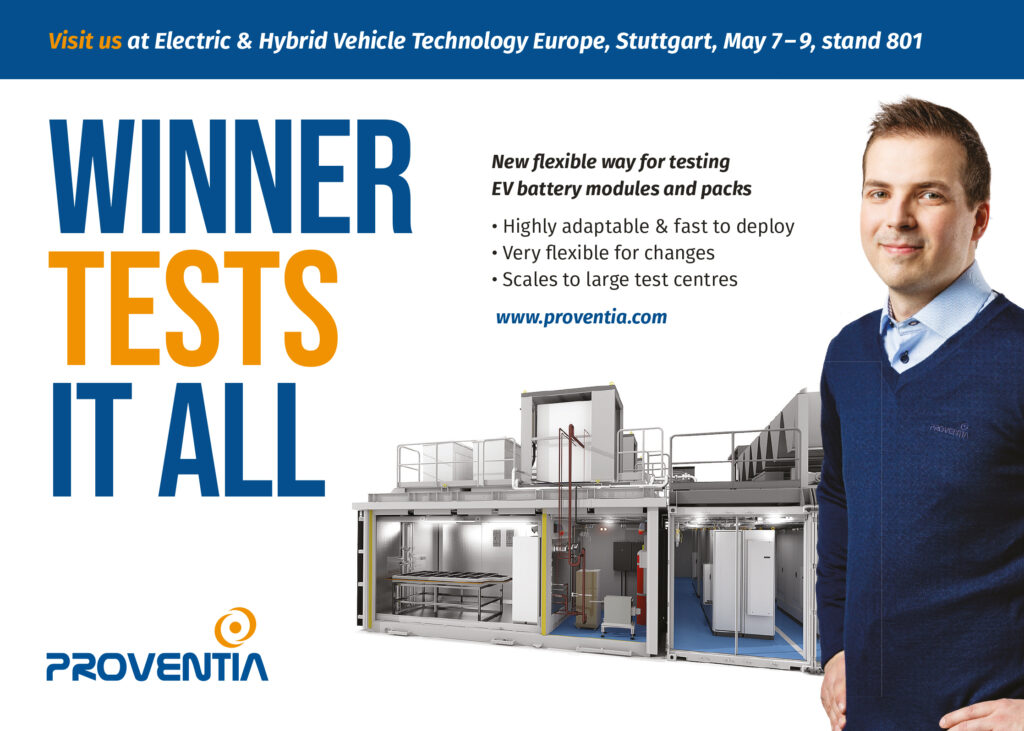
This raises the question of whether a fuel cell with a lifetime of more than 40,000 hours is needed to extend the life of a bus or truck. This kind of stack would need a lot of extra platinum, so one alternative is to have a less expensive fuel cell with a 20,000 h lifetime that can be replaced quickly and easily.
Currently the cost of changing and refurbishing the stack is lower than that of the long-life fuel cell, especially considering that a diesel engine in a bus is rebuilt in midlife. Ballard is not looking at a 40,000 h stack though, as the 25,000 h lifetime is the design point. Now the focus is on reducing the cost of the cell.
Another way to make the fuel cell more cost-effective is to reduce the amount of platinum needed. To that end, researchers at the Technical University of Munich, in Germany, have found a way to make platinum twice as effective as a catalyst.
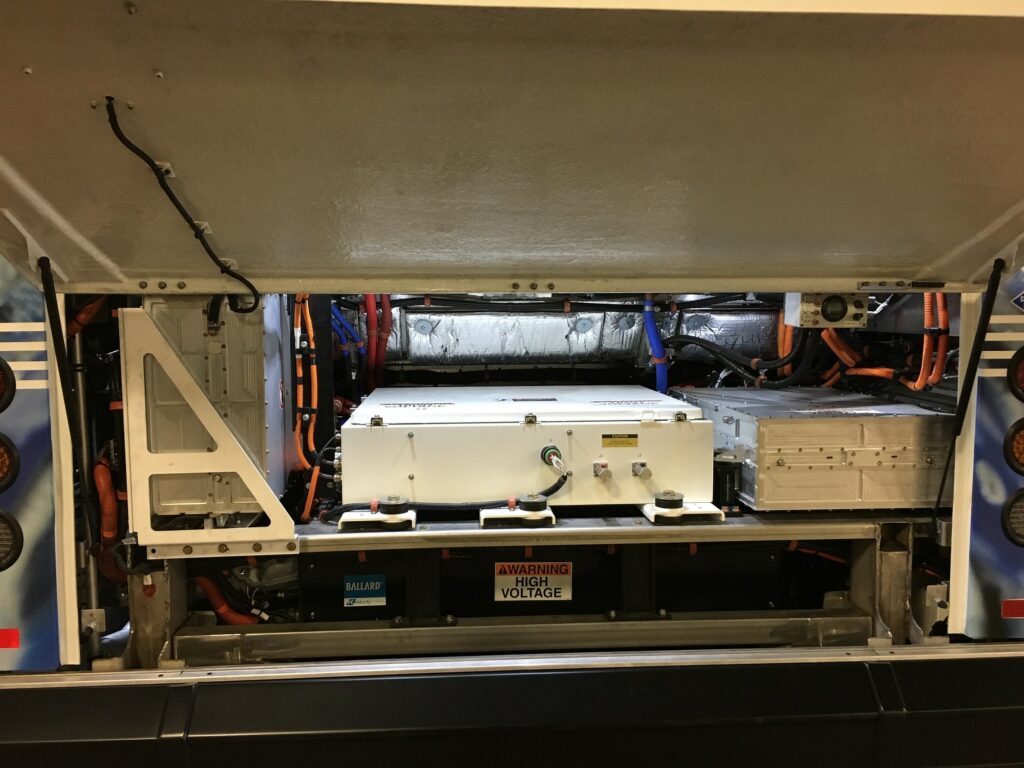
(Courtesy of Ballard)
The team created a computer model of the complete fuel cell stack, looking at how small a cluster of platinum atoms can be and still have a highly active catalytic effect. This modelling showed that particles measuring about 1 nm and containing about 40 platinum atoms in a sphere are ideal.
Experiments showed that this catalyst is twice as effective as the best conventional catalyst on the market, although it is still not adequate for commercial applications, as the production process has not been proven.
Aircraft
Improving the efficiency of fuel cells and reducing the weight of the ancillary components is also enabling the use of hydrogen in passenger aircraft.
ZeroAvia for example is testing a prototype hydrogen powertrain for a 10-seat passenger aircraft with a range of up to 500 miles. For aviation though, the stack needs to be able to operate at higher altitudes than air taxis, and at lower temperatures. This requires a change in cell composition to cope with a different range of humidities and temperatures of the incoming air.
A demonstration powertrain with a peak power of 260 kW has been fitted to a six-seat Piper aircraft. The power is delivered through two sub-units with dual redundancy: two inverters, two motors, and two stacks with 150 kW each side. A 300-mile flight in the aircraft uses 15-17 kg of hydrogen, about three times that used by a hydrogen-powered car such as the Mirai or Clarity.
The company aims to have dual redundancy in all its power units, says Valery Miftakhov, founder and CEO of ZeroAvia. The commercial version of the powertrain will have a rating of 600-800 kW, with dual redundancy through two 300 kW units. This will be used for larger aircraft carrying up to 20 passengers, and the technology is due to be supplied to airframe makers in 2022.
“Beyond that, it’s an interesting question whether to use four units for 40 seats, or we increase the size of the power units,” says Miftakhov. “It might be simpler to increase the number of units but we haven’t got that far.”
The 20-seater traditional fixed-wing design uses 70-90 kg of hydrogen at 350 bar. There is a trade-off between the size of the fuel tank, weight and aerodynamic impact, because the 700 bar tanks are heavier as a percentage of the hydrogen’s weight.
“The US has 500 key fuelling locations – 97% of commercial activity operates in 150 airports, and adding smaller airports brings that number up to 500,” says Miftakhov.
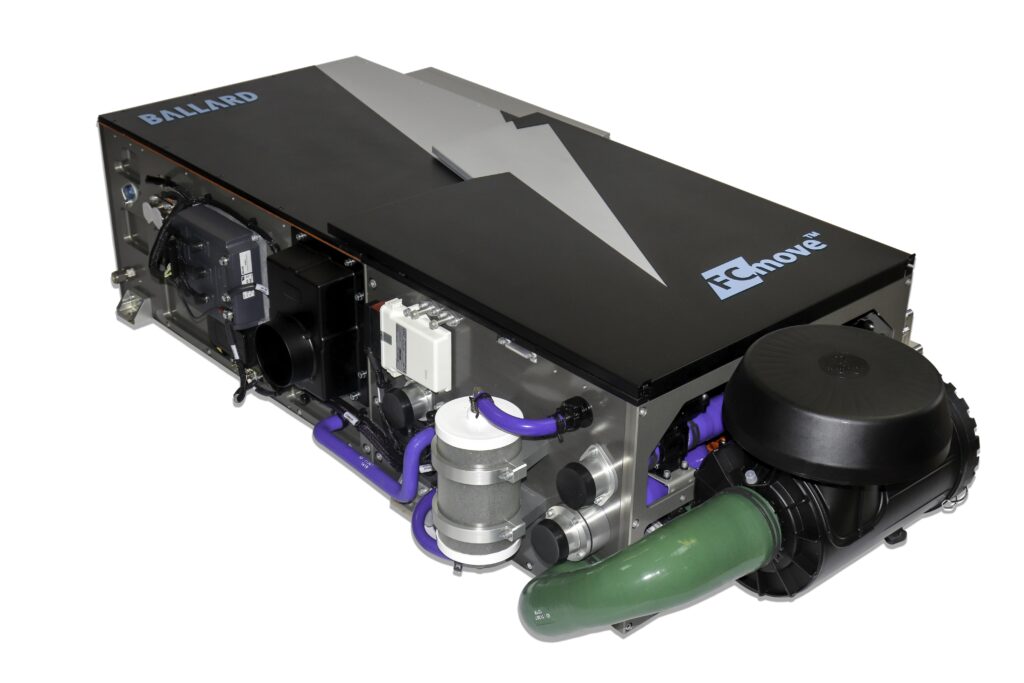
(Courtesy of Ballard)
The economics of a limited number of sites mean electrolysis is more cost-effective. Not having to ship hydrogen cylinders to airports cuts the cost by half, he says.
Another hydrogen-powered aircraft is the Skai, which is being developed by Alaka’i Technologies. It is an air taxi capable of vertical take-off and with a range of 400 miles, and was designed by BMW’s DesignWorks subsidiary. It seats up to five passengers and uses six electric motors with redundancy and, for added safety, an airframe parachute. The company has applied for a licence to test the technology.
Shipping
Shipping is another area where hydrogen-electric power has a potential advantage over battery power.
For example, Siemens is working with Swedish stack supplier PowerCell on a fuel cell system for shipping. Siemens will supply its Siship BlueDrive battery-electric propulsion system, into which PowerCell will install its fuel cell modules for ferries, yachts, cruise ships and research vessels.
Auriga Energy is also developing a fuel cell for shipping, as part of the European Hylantic research project. Auriga developed the UK’s first hydrogen-powered ferry, the 12-seat Hydrogenesis, which is currently in its seventh year of operation.
The Hylantic project is due to deliver a modular marine fuel cell by October next year. This initial development, based around a 12 kW stack from Ballard, will be a 10 kW unit measuring 1 m x 800 mm x 300 mm. The project will then develop a 50 kW cell built from the 10 kW base unit with a structure that allows multiples of 10, 20 or 50 kW.
Again the supply of hydrogen is a key issue, so the project is looking at applications with local shipping where the ports of departure and arrival are either the same or can easily have electrolysers installed.
Forklift trucks
Forklift trucks are another area where hydrogen is a potential power source, given that warehouses usually have the space to store hydrogen cylinders or electrolysers to supply hydrogen on-site.
As well as developing marine systems, Auriga Energy has also been working with Bristol Forklifts on a hydrogen-powered electric forklift. This uses a Ballard fuel cell stack with a control system, compressor and cooling, with two hydrogen cylinders driving a 2 kW electric motor and battery.
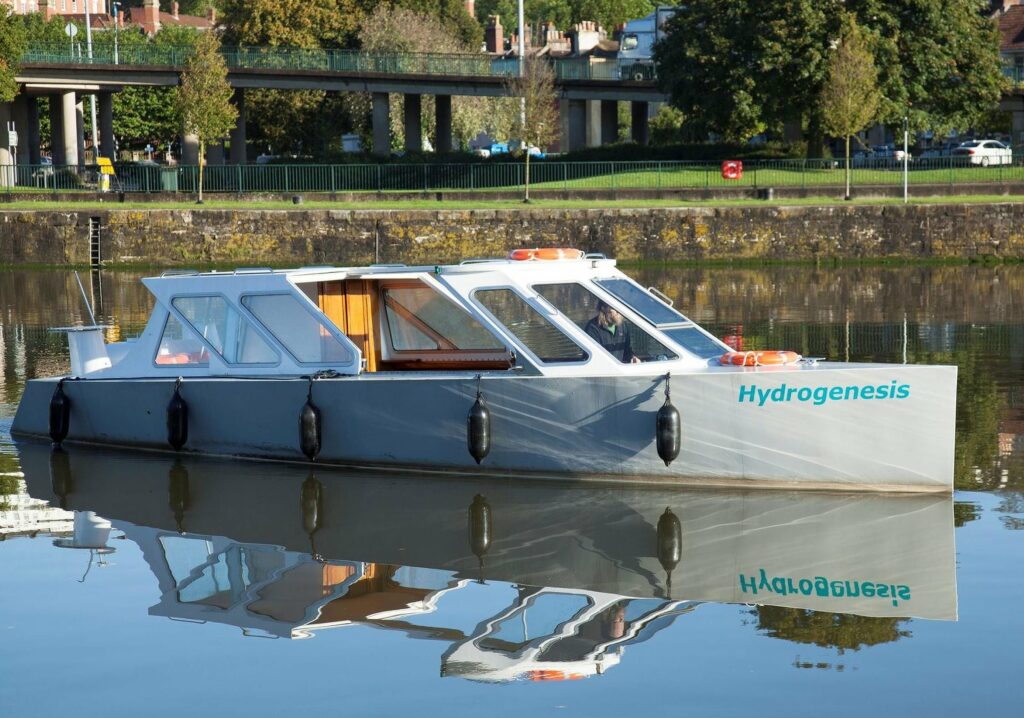
(Courtesy of Auriga Energy)
“We were making this for the Type 3 battery-powered forklifts that operate in warehouses, as there are tens of thousands of them,” says Jas Singh, Auriga’s managing director. “We use two small gas cylinders, the idea being that the cylinders can be replaced or refilled to 172 bar pressure.”
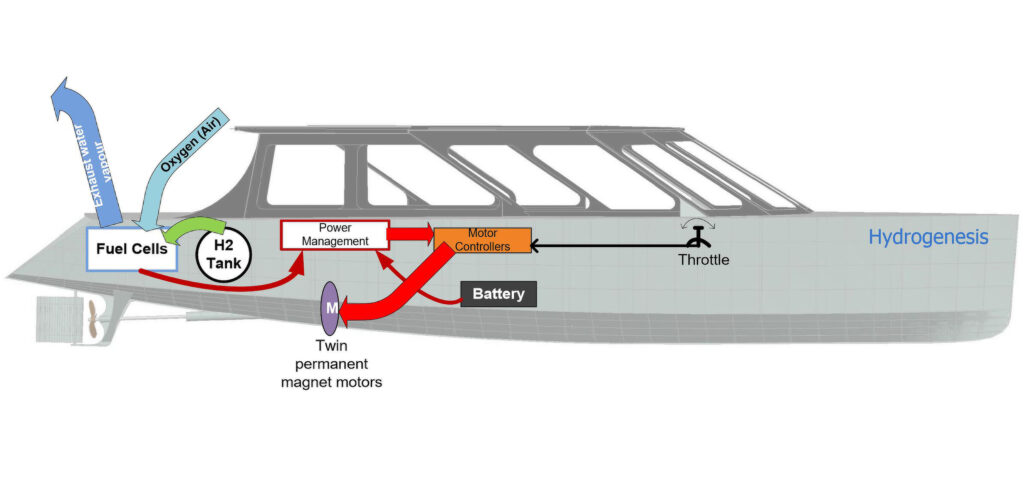
Two cylinders give a full shift of operation. “Both cylinders are used at the same time, as it is too complicated otherwise,” he says. “We have our own regulator from 172 to 0.5 bar; each PEM is like a head gasket, with air on one side at ambient pressure and hydrogen at pressure on the other side. The battery is there to take out the spikes – you also need a battery for start-up, as the fuel cell takes a few seconds to warm up.”
A warehouse belonging to retailer Colruyt, in Belgium, is also using hydrogen-powered forklifts. These use a 100 kW fuel cell with a 50 kg tank at 350 bar pressure. The hydrogen is provided by a combination of an alkaline electrolyser producing 30 m³/h at 1 bar and a 30 m³/h PEM electrolyser.
Infrastructure
Electrolysers are key to providing the hydrogen needed for the fuel cells, so one company, ITM Power, is rolling out a network of 10 hydrogen refuelling stations across the UK, four of which are available to the public.
Each station produces hydrogen on-site using a ‘rapid response’ electrolyser. The rapid response element is key, as most electrolysers take time to produce the hydrogen. For example, a 1.5 MW electrolyser will produce 30 kg of hydrogen in an hour, enough for 10 cars. Typical electrolysers range from 250 kW to 1 MW.
The ITM system however can refuel a fuel cell electric car in 3 minutes, providing 300 to 420 miles of driving. The company has 17 supply deals with companies such as Honda, Hyundai and Toyota, as well as materials supplier Johnson Matthey, and JCB and Anglo American to refuel construction equipment.
Hydrogenics, which is now a joint venture between powertrain maker Cummins and speciality chemicals supplier Air Liquide, is also supplying a large-scale fuel cell electrolysis system for a fuelling station in Germany. It is working with compressor maker Maximator on a 1 MW plant in Wuppertal to produce hydrogen for 10 fuel cell buses. Surplus energy generated by a local waste incinerator will power the electrolyser, generating more than 400 kg of hydrogen per day.
Conclusion
The development of hydrogen-powered electric mobility systems is a complex evolution of fuel cell and electrolyser technology. The move to volume production of passenger cars using fuel cells is driving down the cost of ancillary compressor and cooling components. This is also reducing the cost of electrolysers, allowing the generation of hydrogen locally rather than shipping hydrogen cylinders. This combination of technologies is accelerating the adoption of hydrogen-electric powertrains In a wider range of applications.
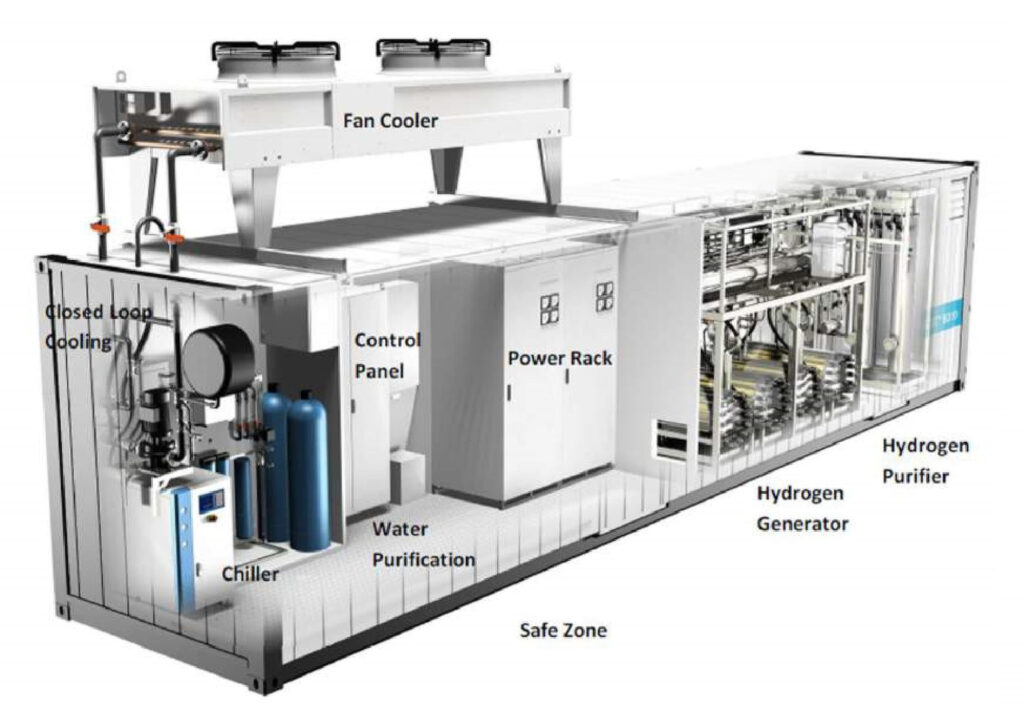
(Courtesy of Hydrogenics)
Types of electrolyser
There are two types of electrolyser. An alkaline system uses a porous membrane that allows OH- ions to go from one side of it to the other. This needs a liquid electrolyte to stimulate the electrolysis, usually 30% potassium hydroxide in water.
With a proton exchange membrane (PEM) system, only protons are allowed through. This uses a solid electrolyte coated on the membrane electrode assembly.
In terms of looks the two are quite different, says Denis Thomas at Hydrogenics – an alkaline electrolyser is cylindrical; a PEM system is a cube. This is important, as the footprint of the electrolyser is one of the key considerations for installation.
A PEM system is more compact than an alkaline one, and is more efficient. For example, an alkaline system in a 40 ft container uses 500 kW of power and produces 100 m3 (10 kg) of hydrogen per hour. A PEM system in the same-size container uses 1.5 MW of power and produces 300 m3 (30 kg) per hour and can be scaled from 80 kW, producing 1 kg/h, up to 25 MW.
After it’s been generated, the hydrogen is purified to remove water, producing 99.99% pure gas that then has to be compressed and cooled. Usually the hydrogen is produced at a pressure of between 10 and 30 bar. Alkaline systems produce hydrogen at 10 bar, while PEM versions deliver 30 bar without a compressor. In both systems the gas then needs to be compressed to 700 bar for passenger vehicles, and 300-350 bar for trucks and buses.
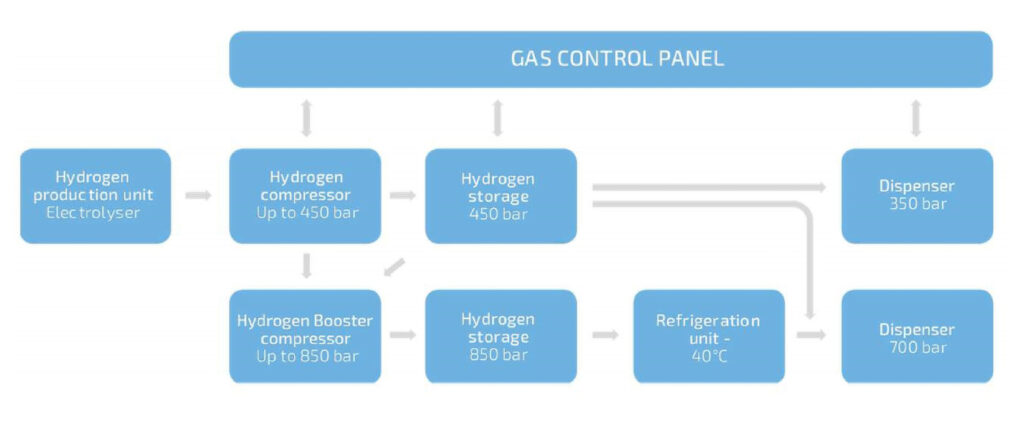
(Courtesy of Hydrogenics)
There are many different elements required for the electrolyser core. Most of the time the compressors are the bottleneck and require careful maintenance, and in case of failure they can present a technical risk by reducing the purity of the fuel.
Also, refuelling a vehicle quickly requires the hydrogen to be under a high pressure. However, when filling the fuel tank the hydrogen goes from high pressure to low and this heats up the gas. In order to refuel a car in 3 minutes, similar to filling up on gasoline, the hydrogen needs to be cooled to -40 C before refuelling to avoid it reaching 70-80 C in the vehicle tank – that’s a specific requirement for filling stations, says Thomas.
ONLINE PARTNERS
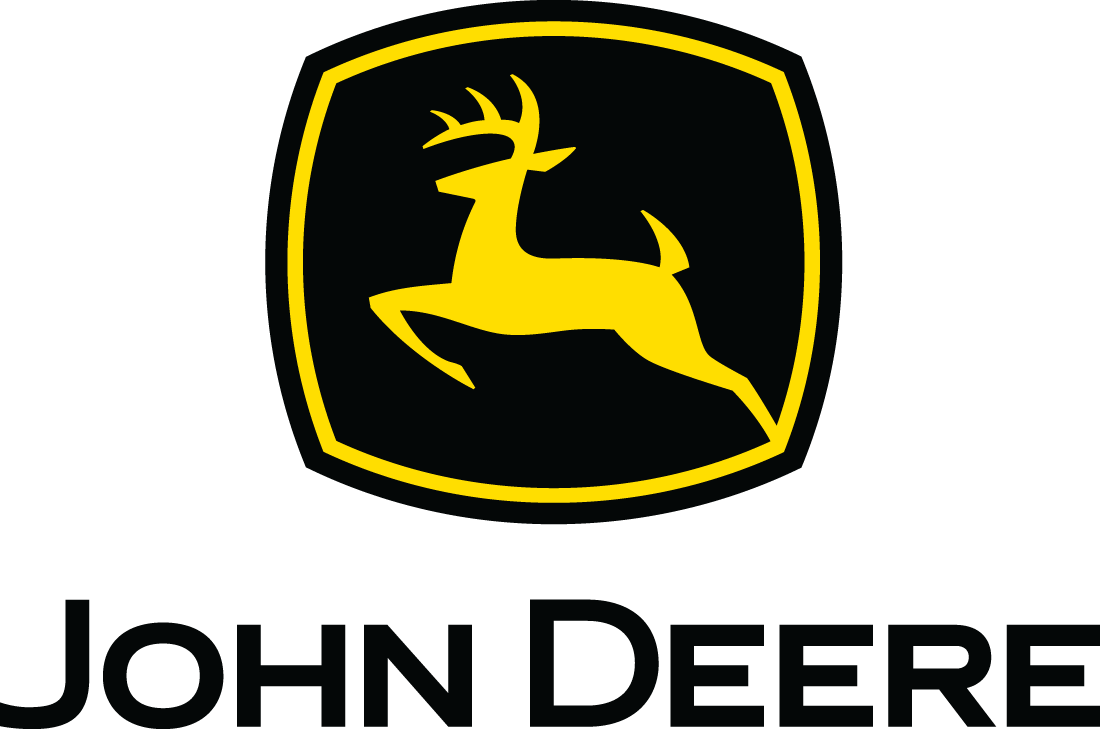
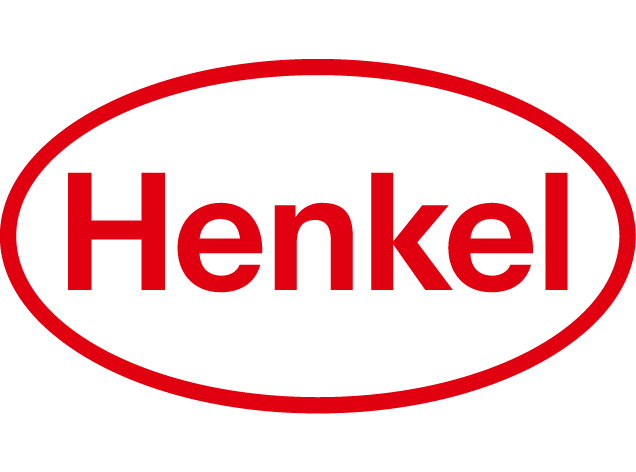
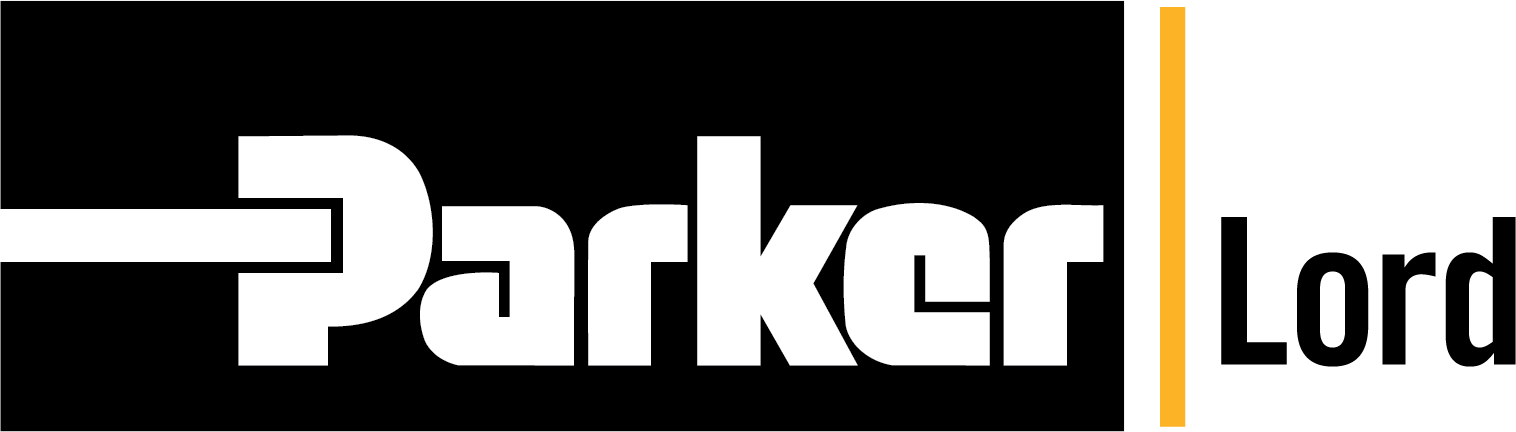
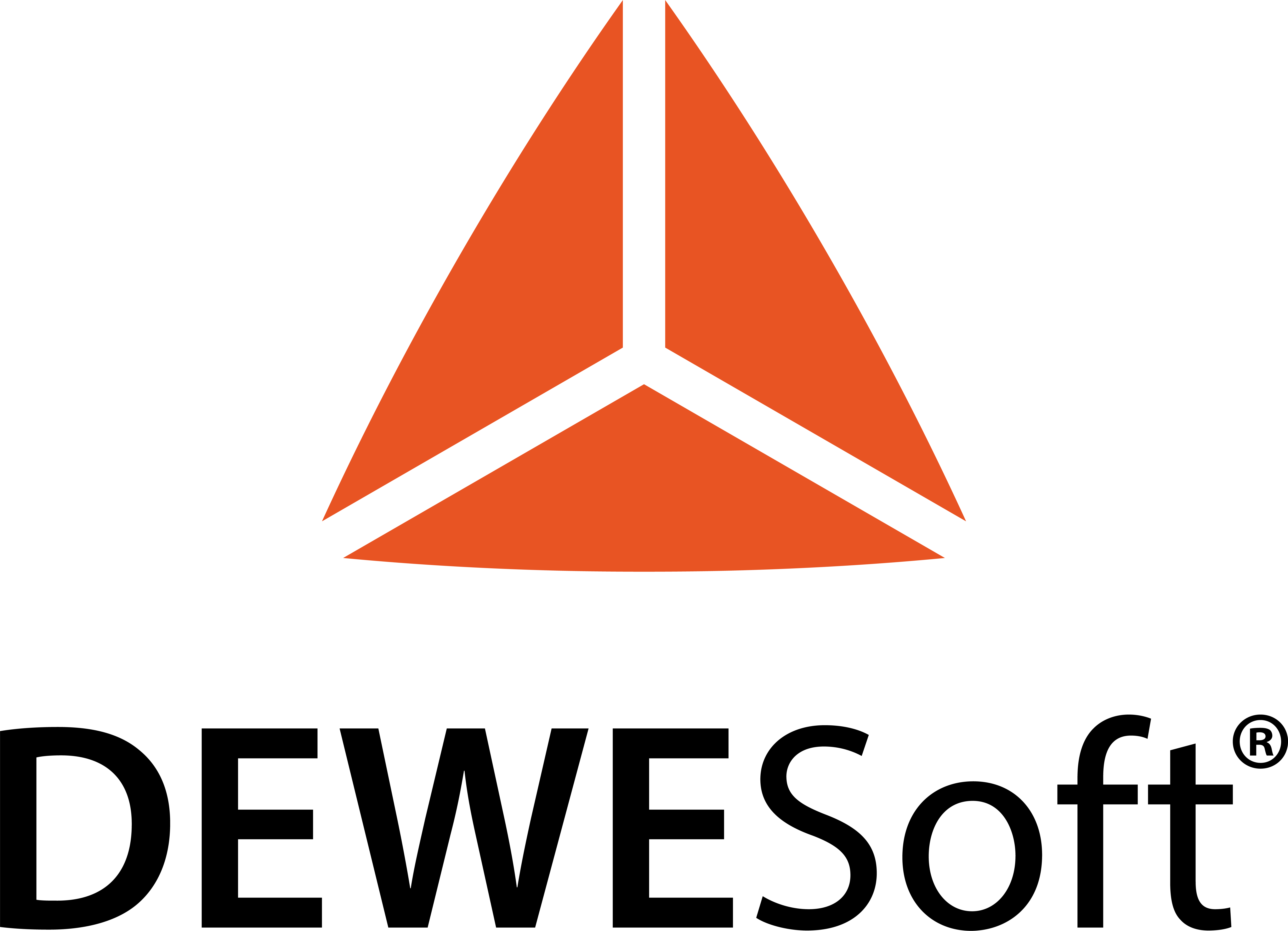
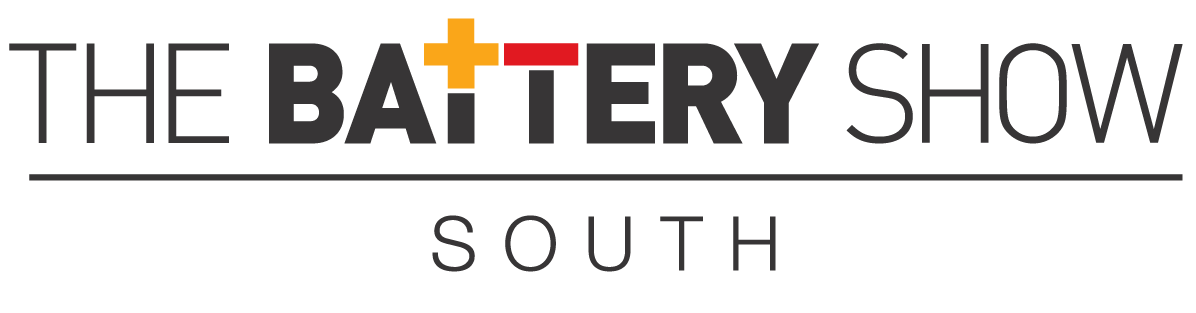
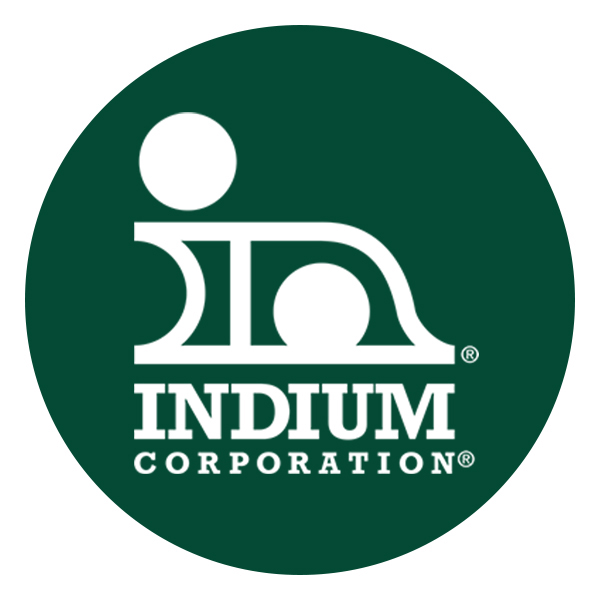
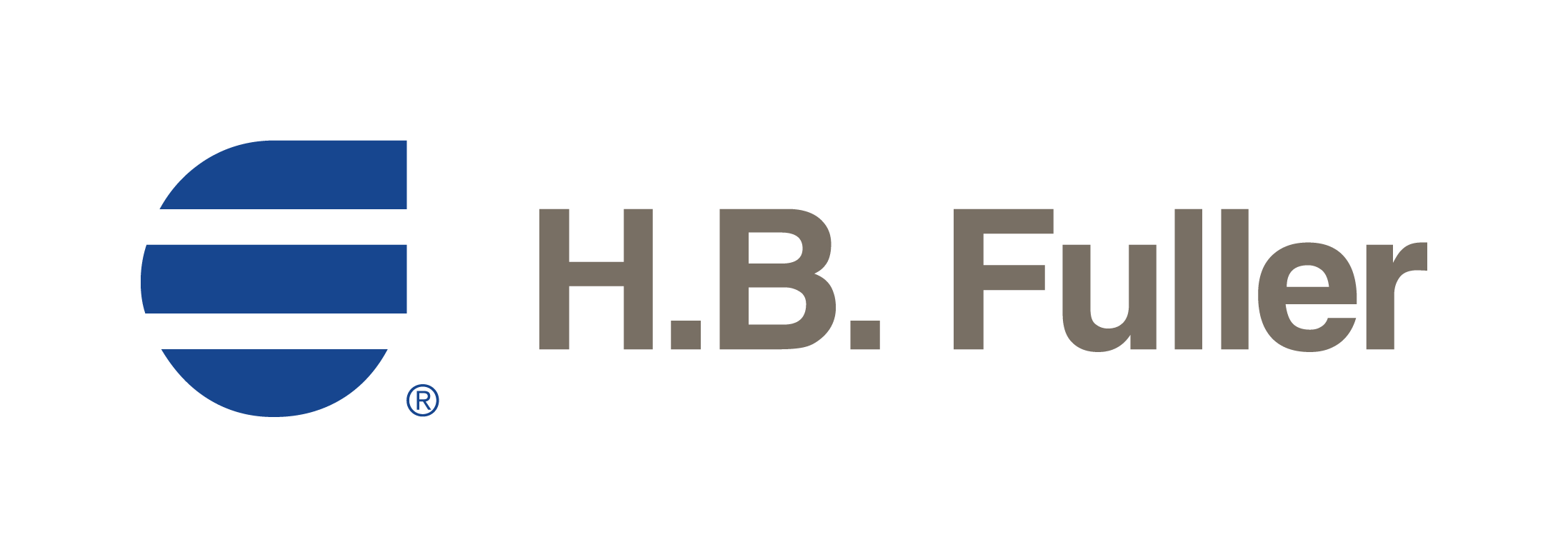