Advanced two-component thermal gap filler targets battery cooling in electric vehicles
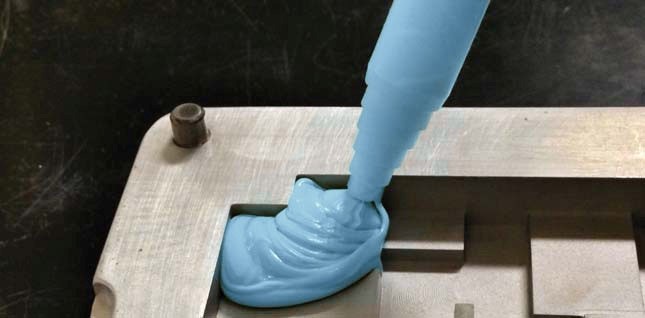
(Image courtesy of Parker Chomerics)
Parker Chomerics’ dispensable cure-in-place material targets multi-height component cooling in battery systems and power electronics
Thermal management in battery systems and power electronics requires solutions that accommodate complex PCB geometries with varying component heights. Parker Chomerics’ THERM-A-GAP CIP 35E provides 3.5 W/m-K thermal conductivity through a two-component dispensable system that cures in place.
The material delivers 3.5 W/m-K thermal conductivity with 50 Shore 00 hardness after curing. Electrical properties include 8 kVac/mm dielectric strength (ASTM D149), 10¹³ Ωcm volume resistivity, and 8.0 dielectric constant at 1,000 kHz. These specifications support applications requiring thermal coupling with electrical isolation. The 1:1 mix ratio enables dispensing through static mixing tips on manual or automated equipment. No pre-mixing, weighing, or degassing is required. High flow rate supports industrial-scale dispensing requirements.
Multi-height components in battery management systems create thermal interface challenges that traditional gap pads cannot address efficiently. The cure-in-place approach fills irregular geometries around components without requiring custom pad cutting or multiple thickness inventories. The 50 Shore 00 hardness provides thermal contact without transmitting compressive forces to solder joints or component interconnections. This characteristic is critical in battery applications where thermal cycling can stress electronic assemblies.
Power modules with varying component heights benefit from the conformable nature of the cured material. The dispensable format eliminates pre-cutting requirements while providing consistent thermal paths across complex surface topographies. Vibration damping properties contribute to system reliability in automotive applications where mechanical stress affects electronic assembly longevity.
Packaging options range from 45cc cartridges to 10,452cc containers, supporting prototype through production volume requirements. RoHS compliance meets automotive electronics manufacturing standards. The cure-in-place process enables automated application in high-volume production environments. Material waste is minimized compared to pre-cut pad solutions, particularly for custom geometries.
The material enables new approaches to thermal management in space-constrained applications. Complex three-dimensional thermal paths can be created without tooling requirements for molded solutions. For battery pack designs where component placement is driven by space optimization, the ability to create custom thermal interfaces improves overall system thermal performance while reducing material and manufacturing costs.
Click here to read the latest issue of E-Mobility Engineering.
ONLINE PARTNERS
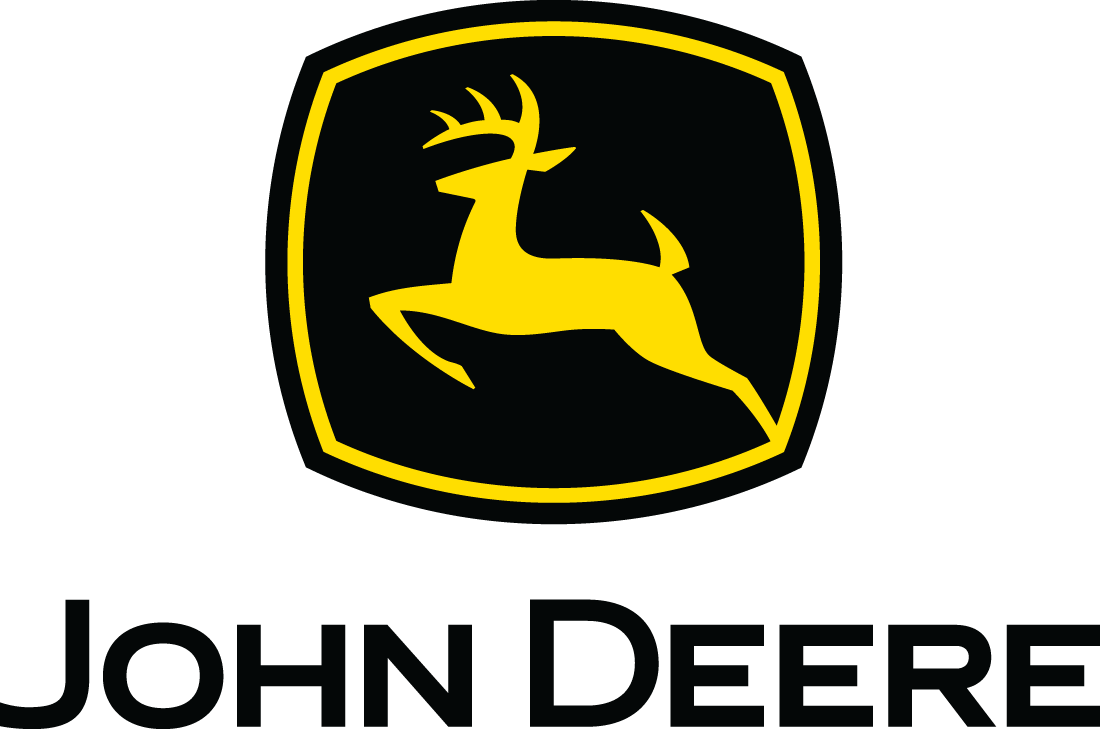
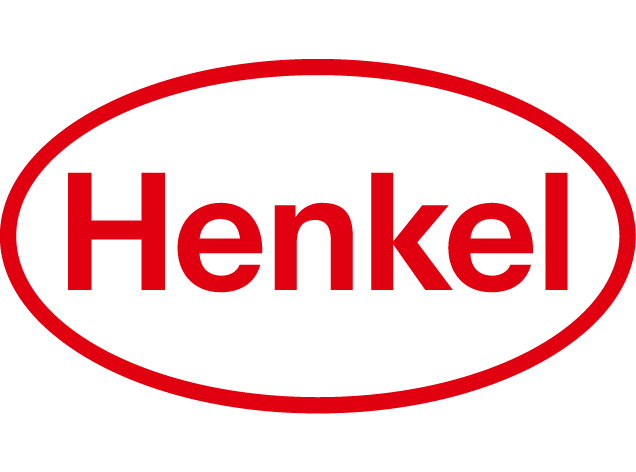
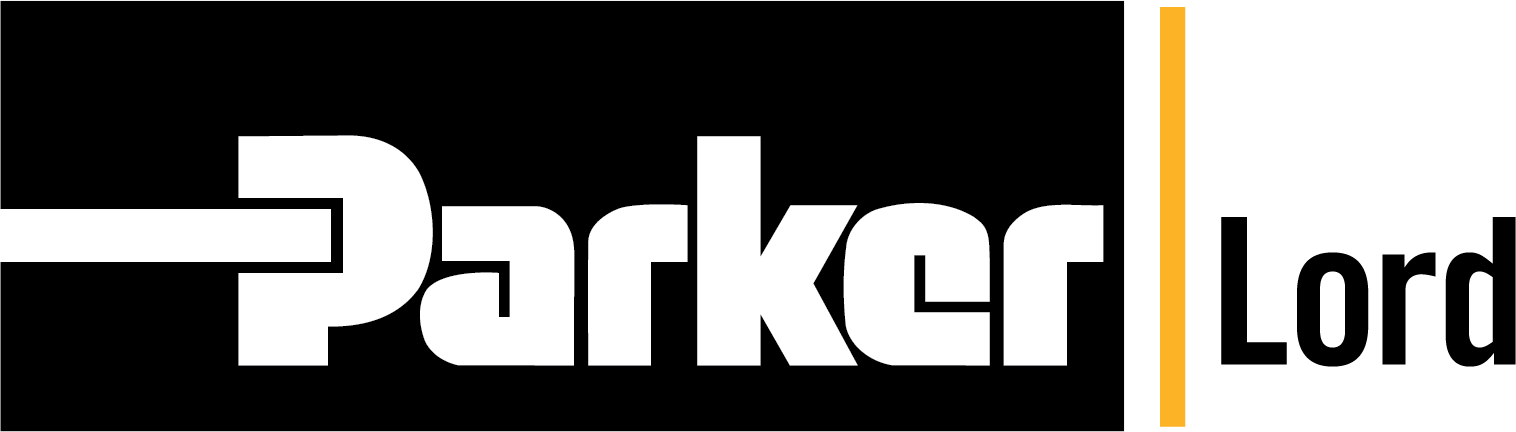
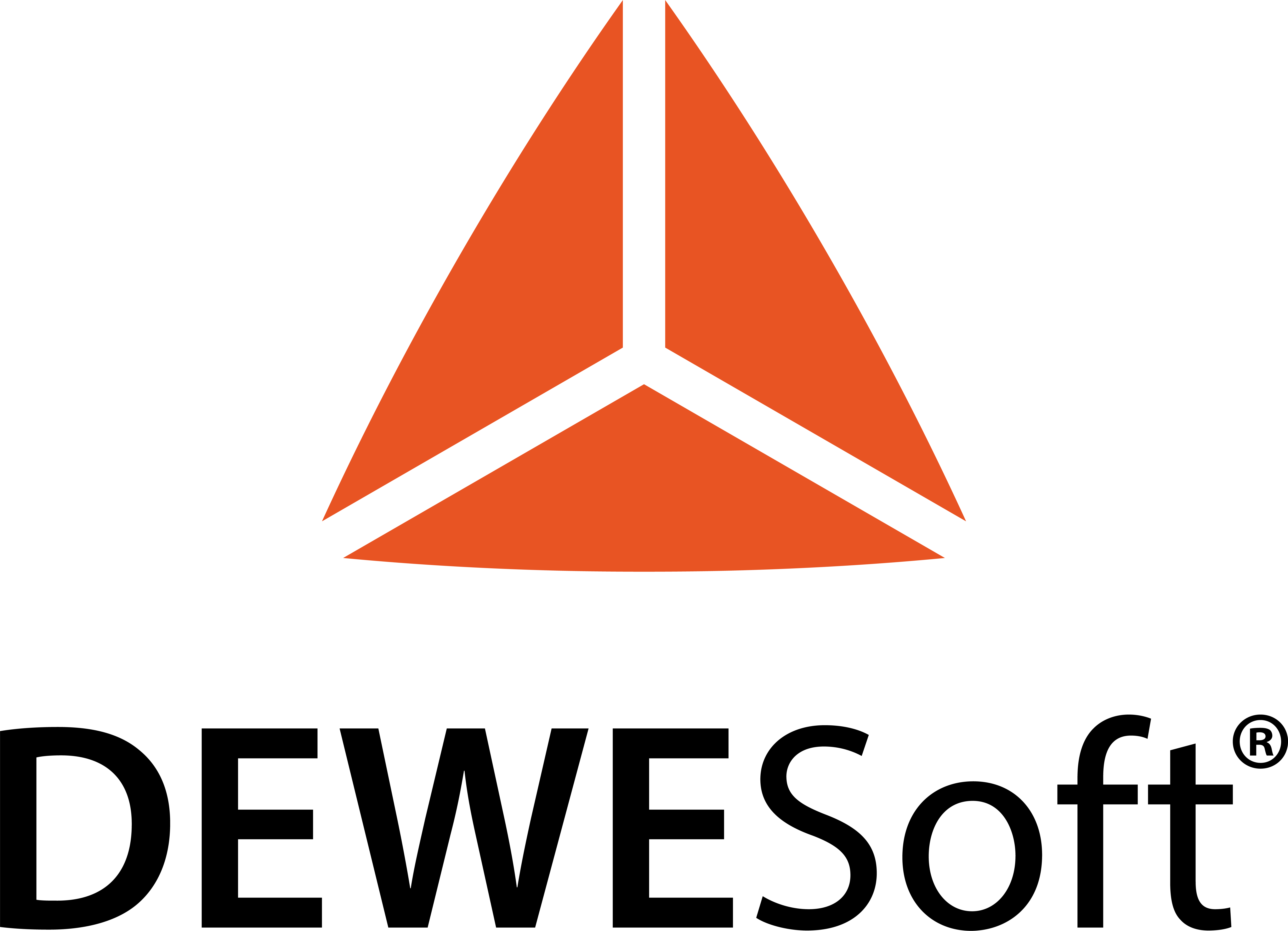
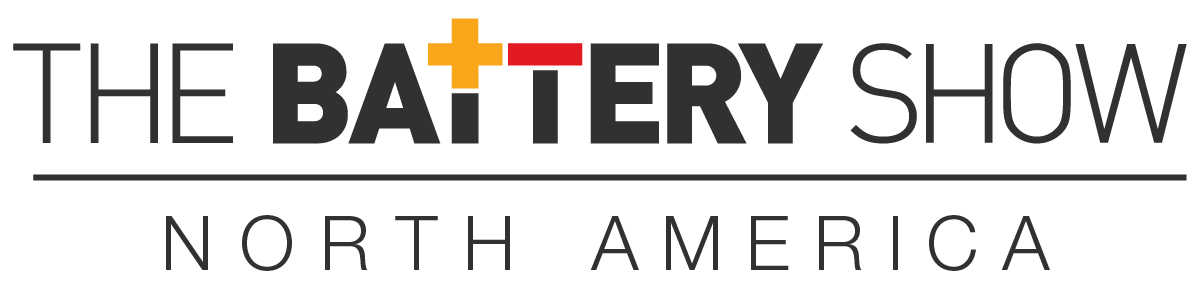
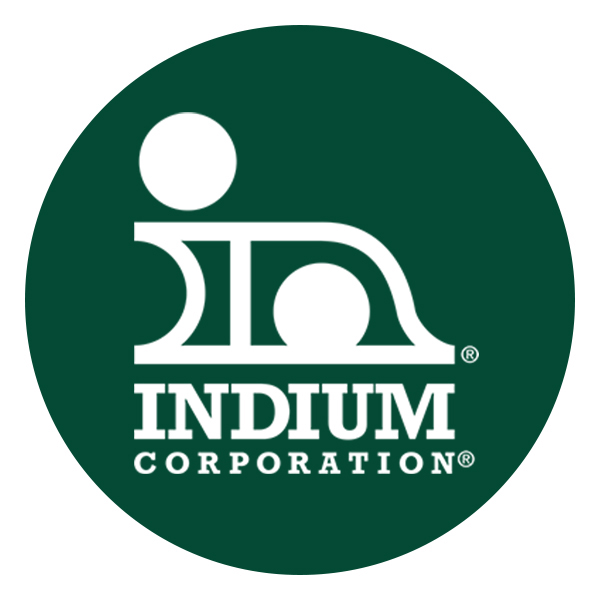
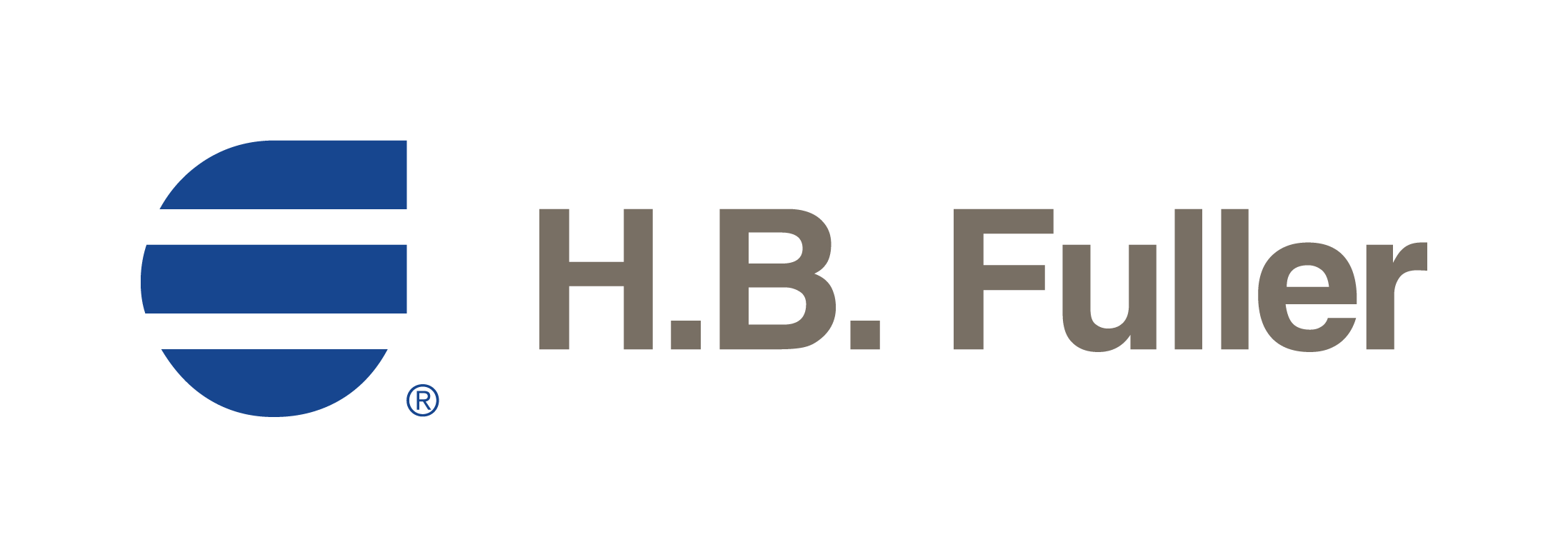
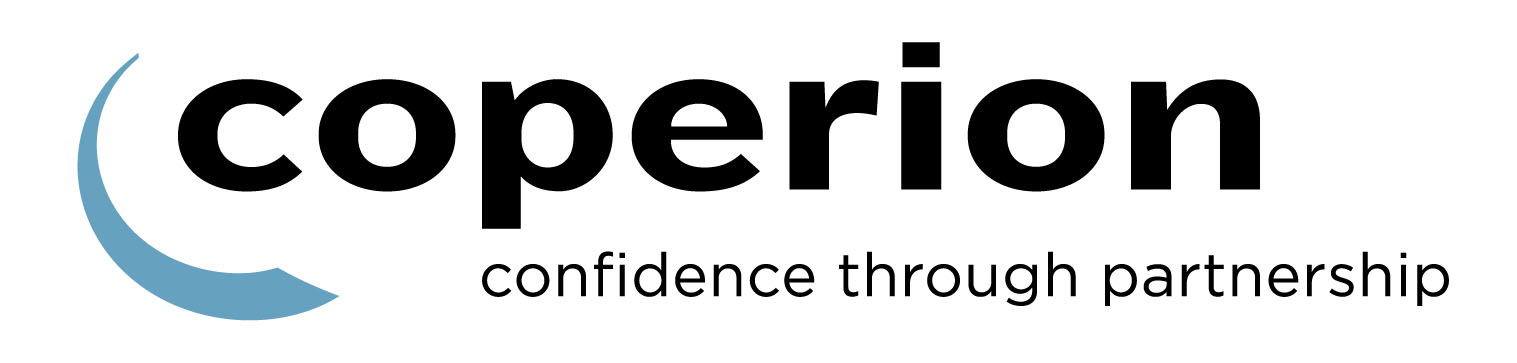
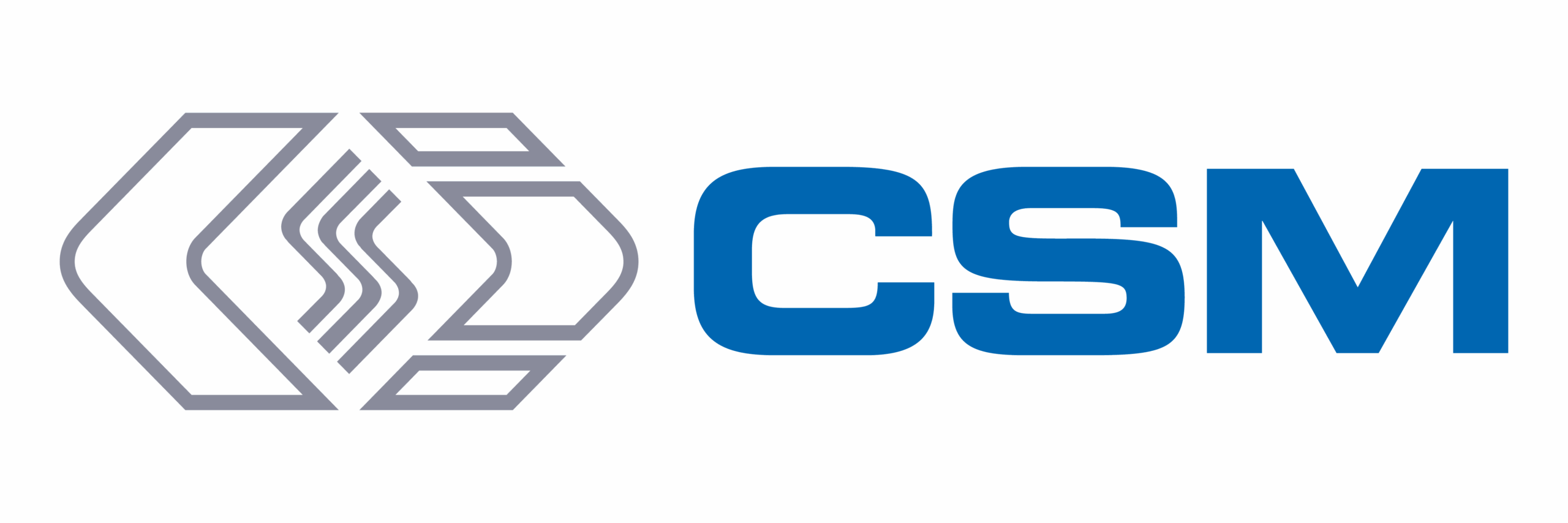