Fast-cure thermal adhesive revolutionizes EV battery pack design
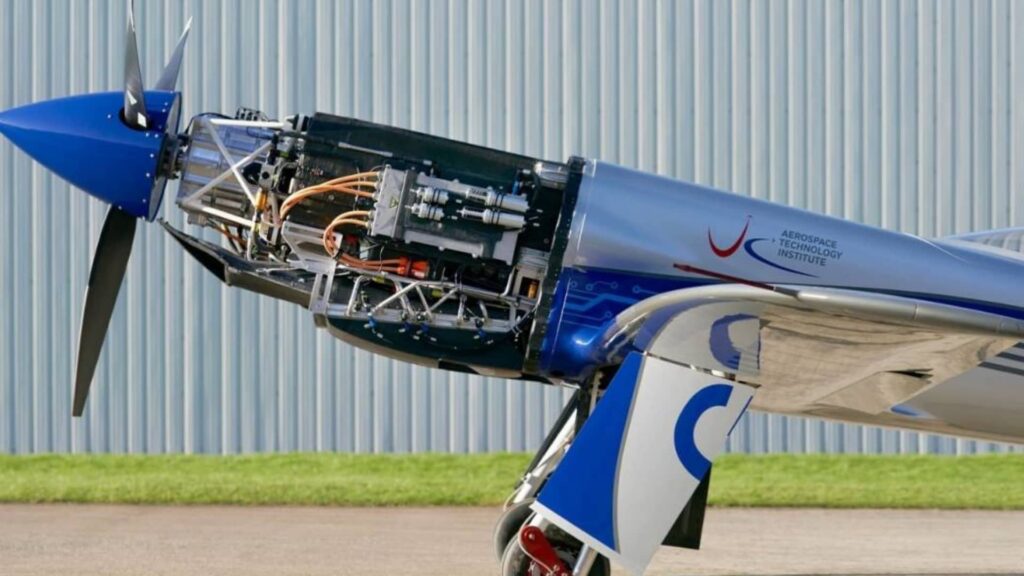
(Image courtesy of Electroflight)
As EV manufacturers push the boundaries of efficiency, safety, and performance, innovations in thermal management and structural bonding have become increasingly important. Parker’s CoolTherm TC-2002 thermally conductive adhesive addresses a critical need in battery pack design, offering both mechanical stability and efficient heat dissipation, writes Peter Donaldson.
CoolTherm TC-2002 was developed to meet a previously unaddressed demand for a fast-curing, thermally conductive metal bonding adhesive. “There was an unmet need for a fast room-temperature curing metal bonding adhesive with 1 W/mK thermal conductivity,” says Eric Wyman, global business development manager at Parker Hannifin. “This material enables novel battery pack designs; mechanical fixturing of cells can be reduced or eliminated, and efficient thermal transfer can be achieved without a separate material,” he emphasises.
One of the most significant applications of TC-2002 is in the bonding of cylindrical lithium-ion cells to cooling plates, ribbons, or housings. With its high thermal conductivity and bond strength, CoolTherm TC-2002 allows for more compact, thermally efficient battery designs.
CoolTherm TC-2002 is a two-component adhesive system based on an acrylic polymer, filled with non-electrically conductive ceramics. In addition to its high thermal conductivity, it also has a broad operating temperature range, maintaining stability across temperatures from -65°C to +100°C. Its low coefficient of thermal expansion (CTE) reduces the risk of bond failure due to thermal cycling, while UL 94 V-0 certification ensures excellent fire resistance, and its dielectric properties prevent current leakage and corrosion-related issues.
CoolTherm TC-2002 is designed for ease of use in both small- and large-scale production environments. It can be applied using manual, pneumatic, or electric dispensing guns for smaller applications, while larger-scale operations benefit from compatibility with meter mix dispensing systems available in 5-gallon pails or 55-gallon drums.
For optimal performance, CoolTherm TC-2002 is mixed at a 10:1 ratio of resin to curative using a static mixing tip. The working life at room temperature is approximately 7-8 minutes, with handling strength achieved within 20-25 minutes and full cure in 2-3 hours. The adhesive also contains glass beads to maintain a consistent bondline thickness of 100 µm.
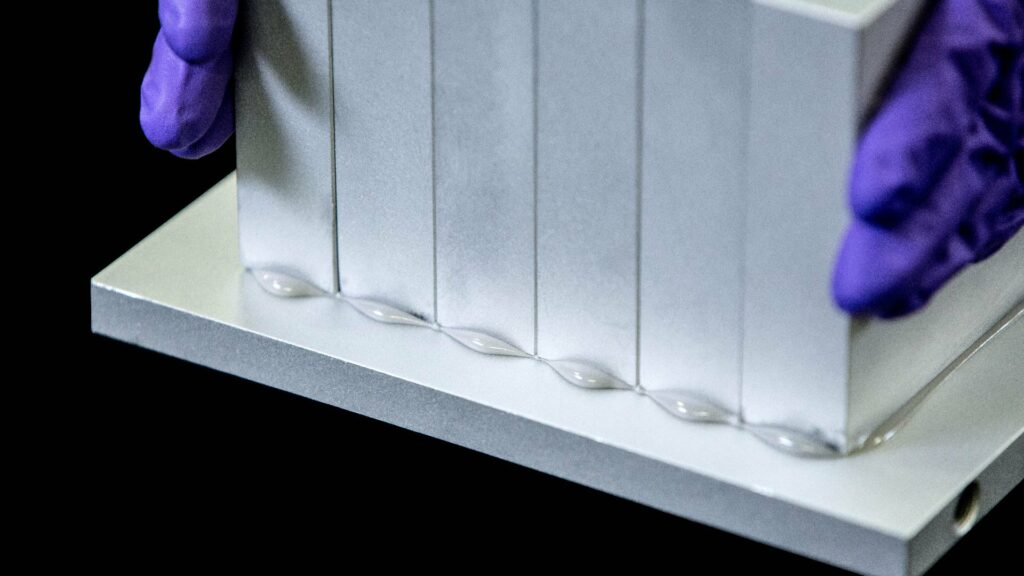
(Image courtesy of Parker Hannifin)
The development of this product presented several challenges, particularly in balancing flow and dispensing characteristics with the increased filler loading required for thermal conductivity. Shelf-life variability due to raw material inconsistencies was another hurdle. “Manufacturing this new type of adhesive came with several issues that had to be overcome,” Wyman explains. Parker Hannifin addressed them through established procedures including design of experiments (DOEs), design failure mode effect and analysis (DFMEA), and process failure mode effect and analysis (PFMEA), he adds.
CoolTherm TC-2002 has been successfully deployed in the EV industry for nearly a decade, proving its reliability in real-world applications. TC-2002 is still in use at the original customer for close to a decade,” Wyman confirms, highlighting its long-term stability and effectiveness.
Click here to read the latest issue of E-Mobility Engineering.
ONLINE PARTNERS
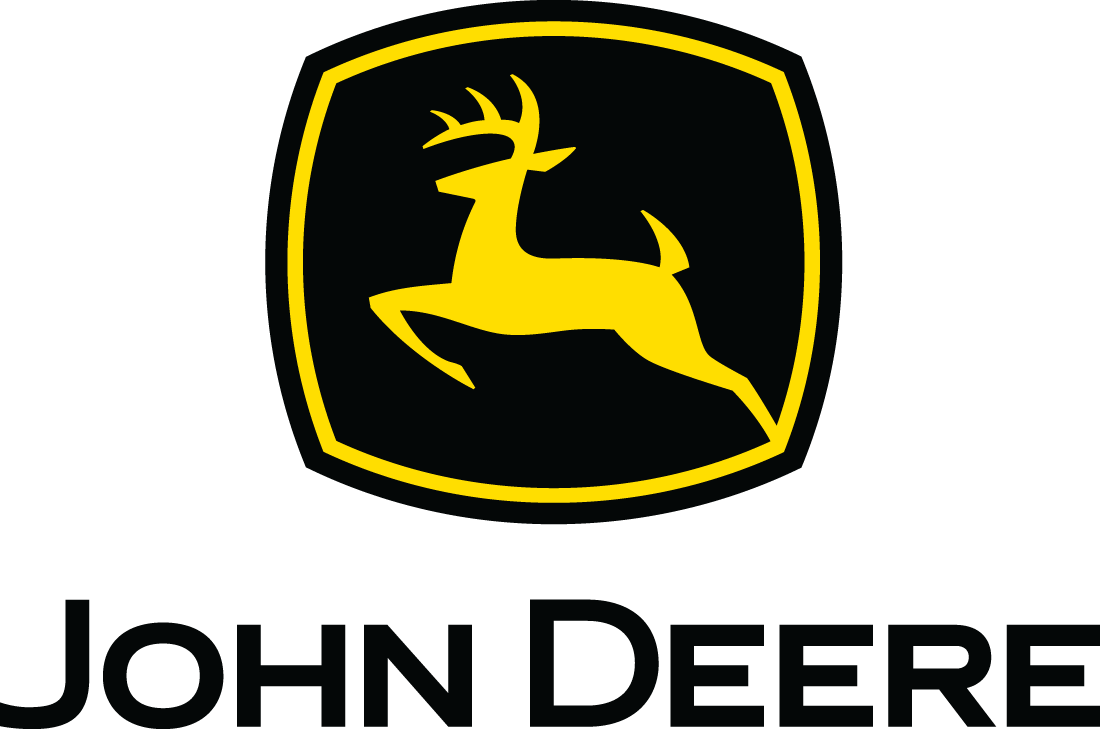
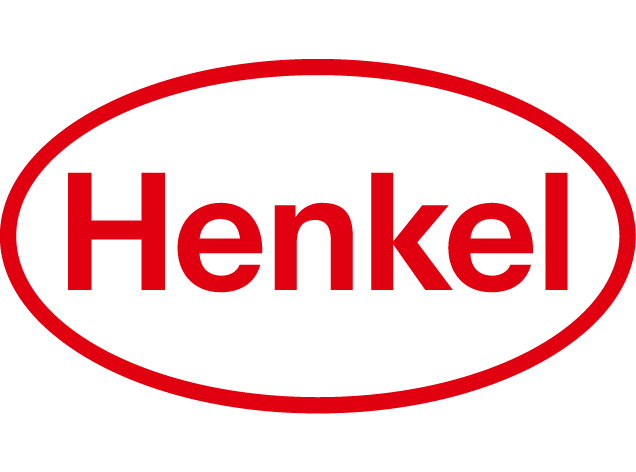
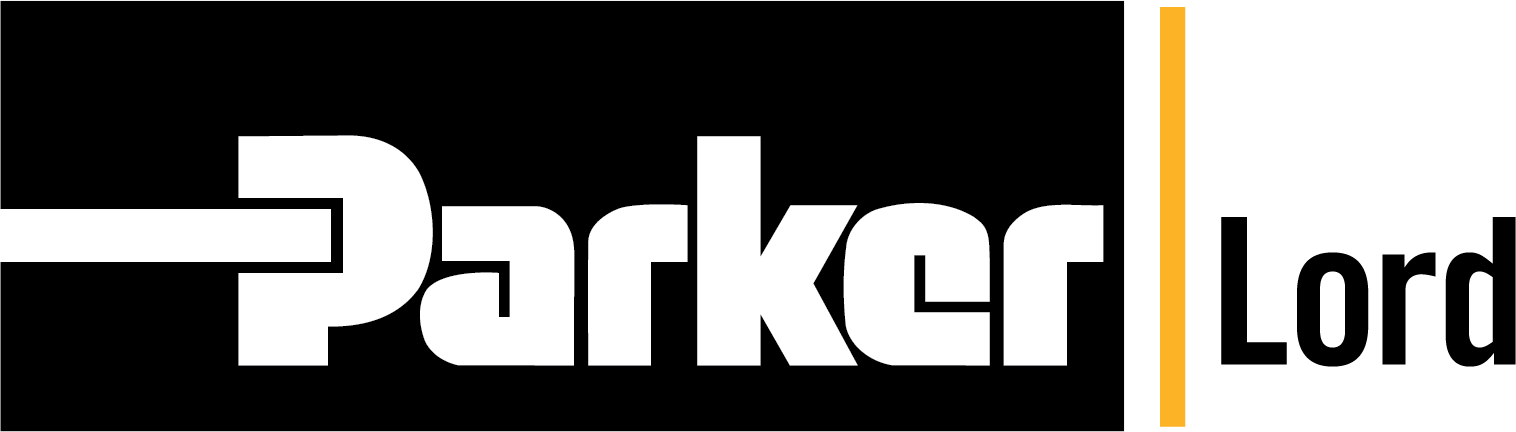
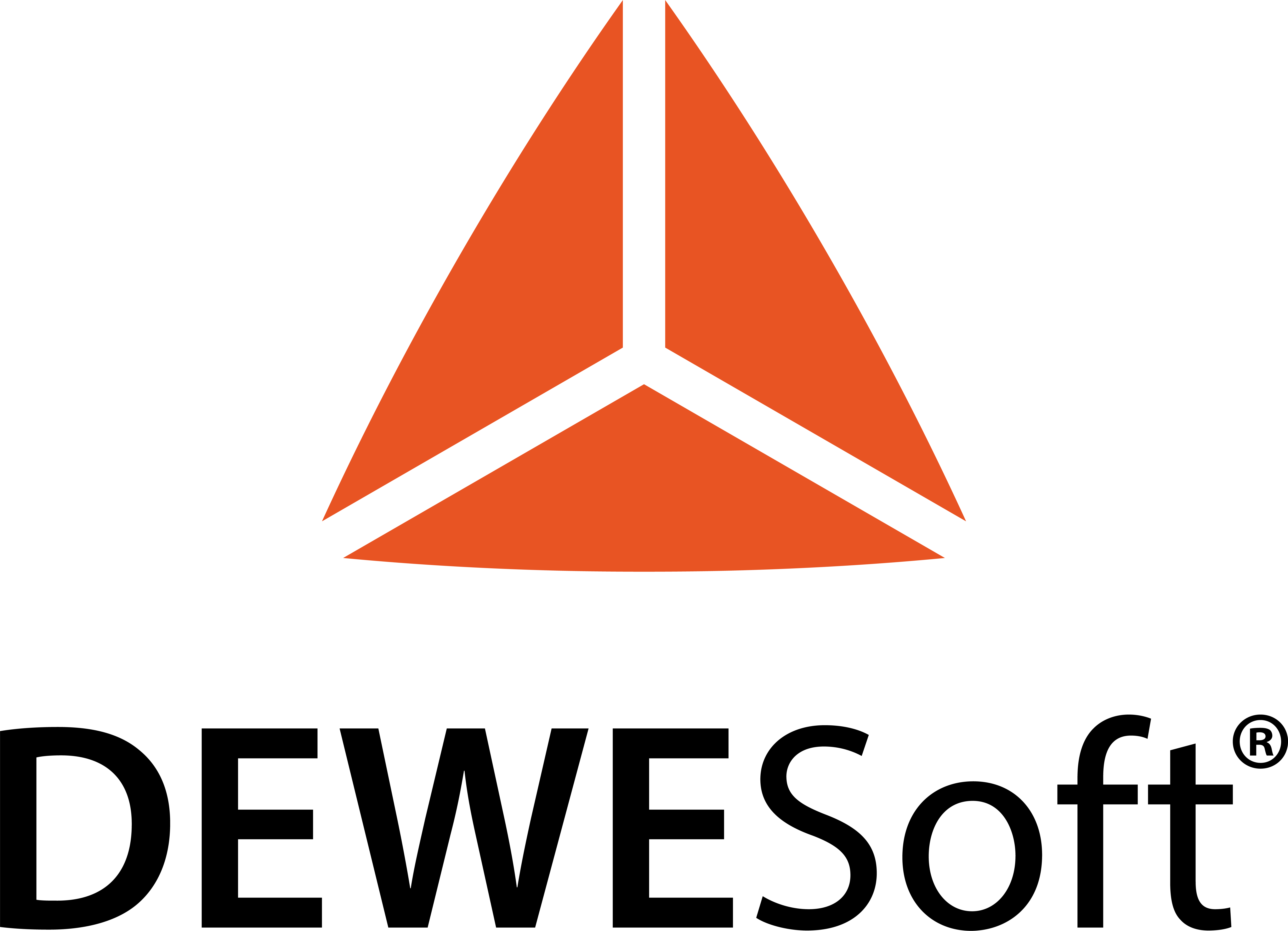
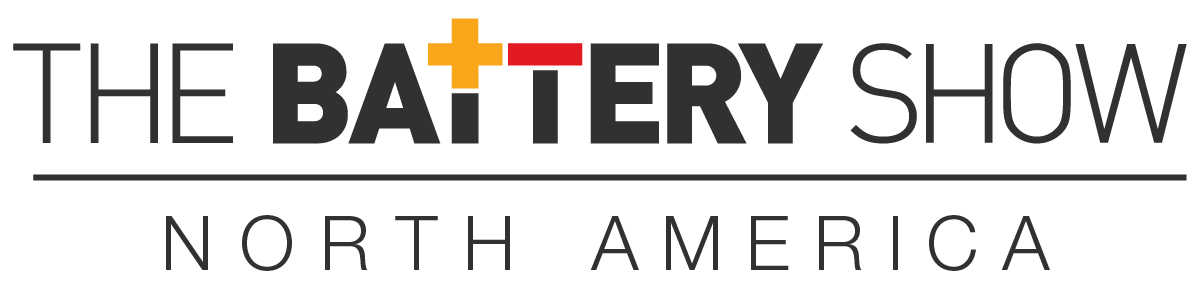
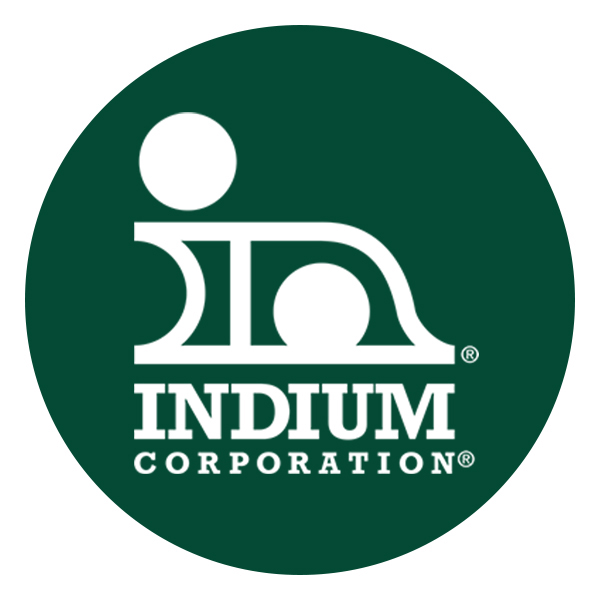
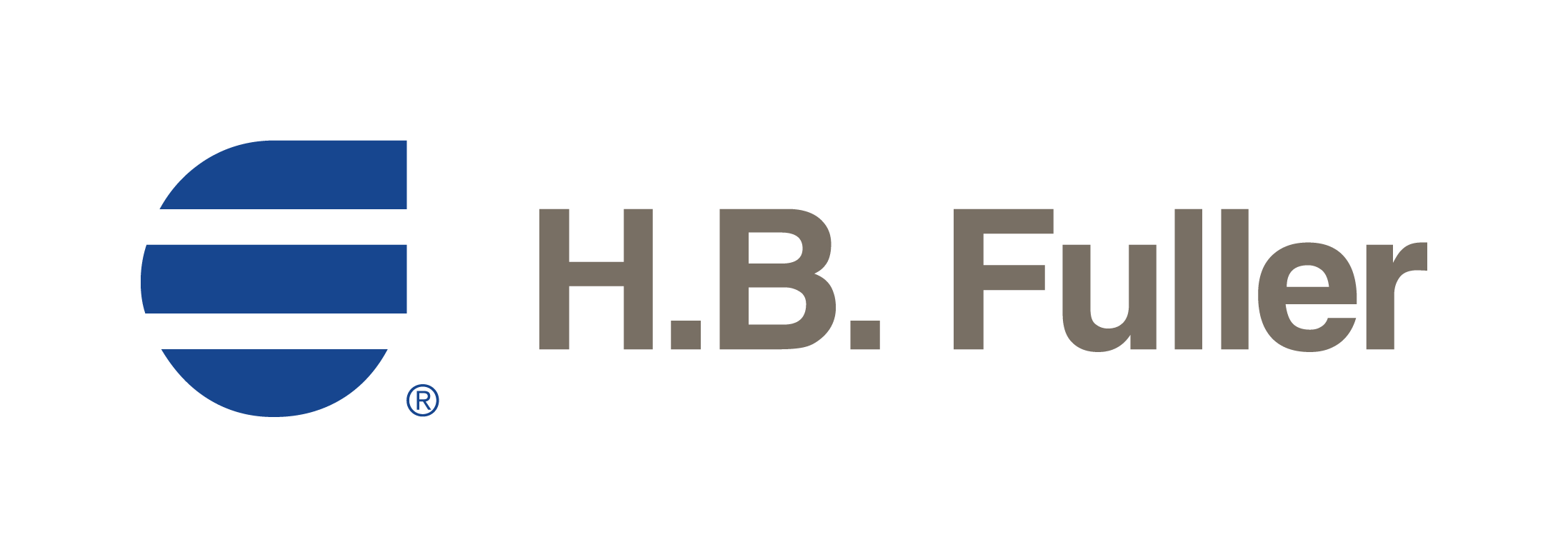
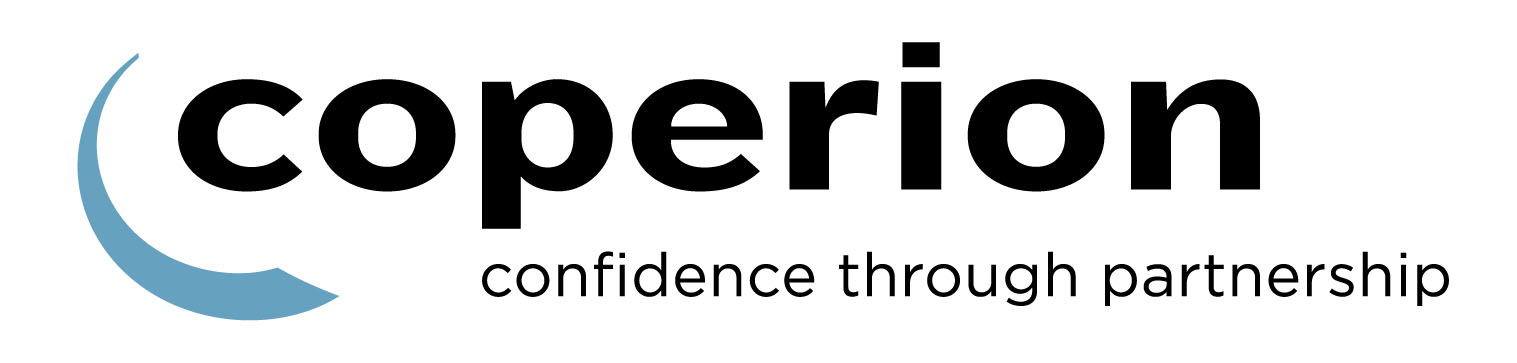