NXP intelligent gate drivers for traction inverters
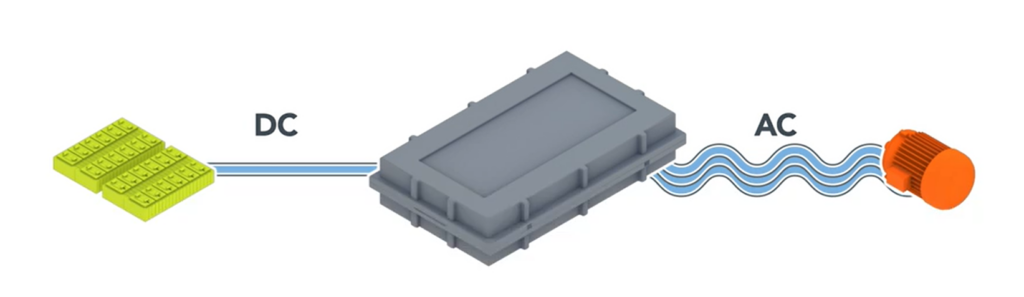
(Images courtesy of NXP)
Long-established IC-engined vehicle OEMs and new EV specialists are competing to get EVs to market rapidly while being faced with rising costs and the desire to maintain control of the intellectual property embodied in their vehicles (writes Peter Donaldson).
Under this pressure, many are responding by building up their abilities to design, develop and manufacture core powertrain subsystems, while Tier 1 suppliers are keen to maintain their relevance to OEMs by integrating multiple components including inverters, motors and transmissions.
At the same time, both OEMs and Tier 1s are working to improve performance and efficiency, and to comply with stringent functional safety requirements. To meet these complex challenges, they are turning increasingly to semiconductor suppliers for help.
Namrata Pandya and Vince McNeil at NXP Semiconductors explain the growing importance of a new generation of high-current intelligent gate drivers.
In a typical modern EV powertrain, the inverter that takes DC from the battery and turns it into AC for the traction motor is under the command of a microcontroller, but the microprocessor at the heart of the controller cannot generate gate signals with currents large enough to switch on the high-power electronics in the inverter, whether those are IGBTs or SiC MOSFETs. The gate driver turns the microcontroller’s instructions into switching signals with currents large enough to control the switches in the inverter, up to 15 A in the case of NXP’s GD3100 and GD3160.
Also, the gate drivers integrate many supporting functions that protect the high-power devices they control from harsh operating conditions, and increase system efficiency while reducing fault detection and response times. This kind of functionality requires external devices and circuitry in competitors’ solutions, but it is integrated into the same piece of silicon in NXP’s new gate drivers.
These functions are also intelligent and programmable for different applications, Pandya says. “We are one of the industry leaders as far as short-circuit protection is concerned,” she says. “From the fault taking place to its detection and the system taking its protective actions is less than a microsecond.”
All power electronic devices can withstand short-circuits for a short time, McNeil says. For IGBTs this is about 10 µs, but with SiC it more like 2 or 3 µs. “We are far below the minimum time in which to react and protect the device,” he says.
Fault verification also takes place within that cycle, McNeil adds, which requires programmability to adapt it to different inverters. “When you detect a fault, you want to make sure it is real and not just a glitch,” he says. “So the leading-edge blanking time is one of the programmable features that allows us to look at the event and decide whether it is a real one.”
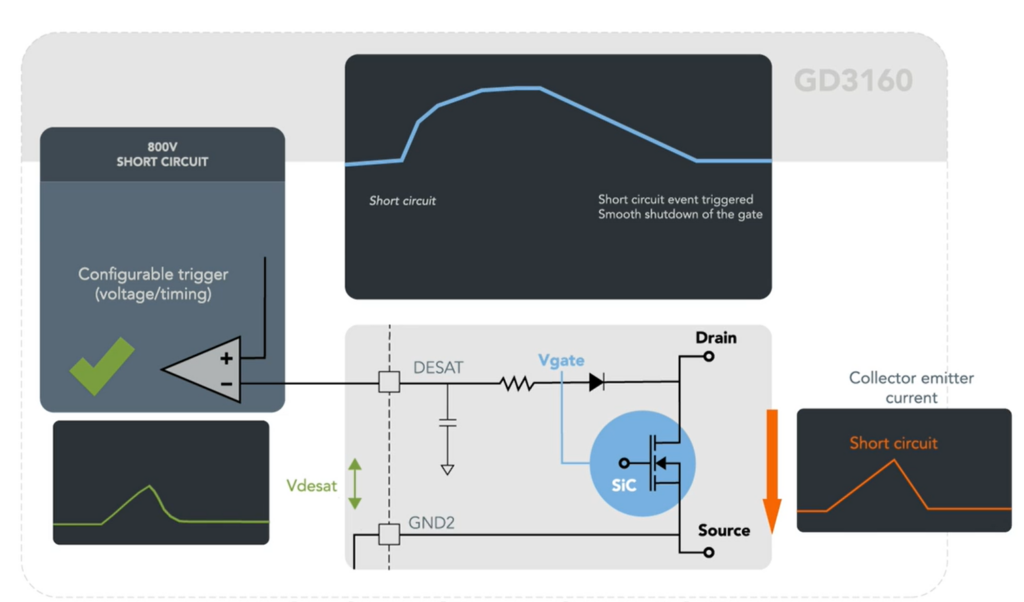
With that decision made, the protection circuit has to power down the IGBT or SiC MOSFET quickly enough to protect it from damage, but gently enough to avoid other unwanted effects. “The soft shutdown is a mechanism used to pull current out of the device to shut it down, but in a controlled manner so that you don’t have a rebound effect,” McNeil says.
The protection logic also incorporates temperature sensing, which again is critical for SiC power electronics because they are built on dies that are physically smaller than those of IGBTs, so the same energy input leads to more rapid heating and higher temperatures, McNeil explains.
To improve efficiency, Pandya adds, NXP has also integrated a segmented drive capability into its gate drivers. By minimising voltage overshoots, this capability reduces switching losses in charging and discharging the high-power devices’ gate electrodes. This effectively tailors the drive power to the power the inverter is required to deliver.
“With the segmented drive feature, we are able to improve efficiency by 5%,” Pandya says. Integrating these capabilities onto the gate driver silicon also reduces the bill of materials by as much as 20 to 25 US cents per driver, she adds.
ONLINE PARTNERS
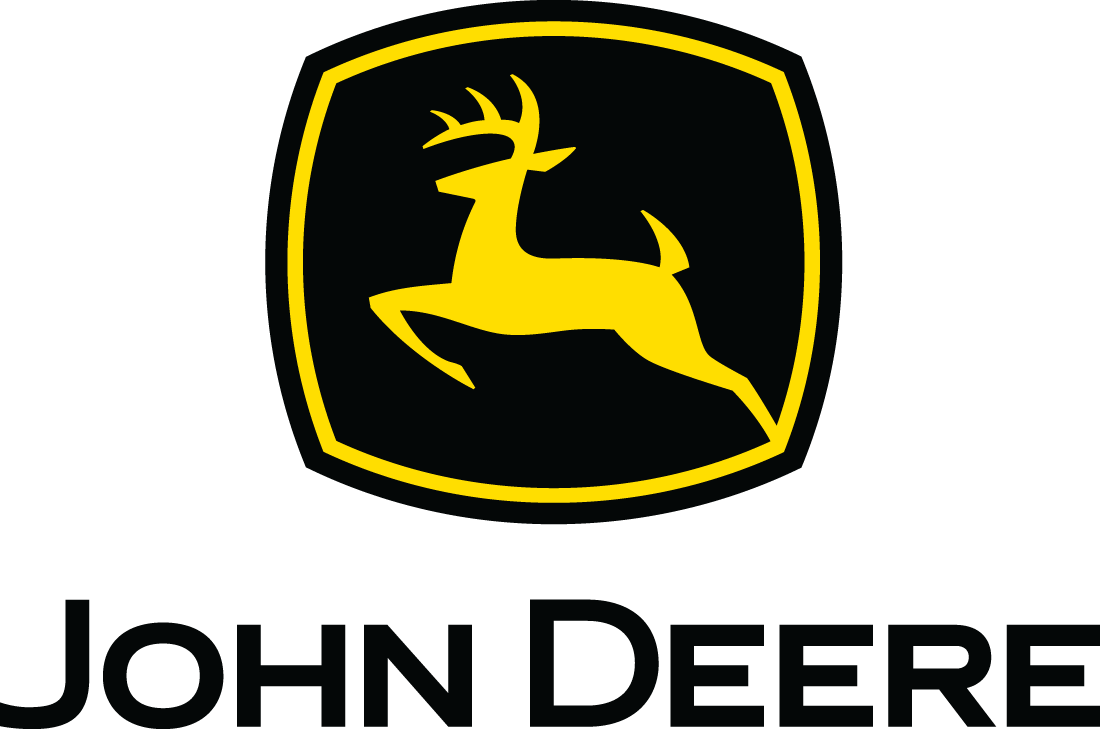
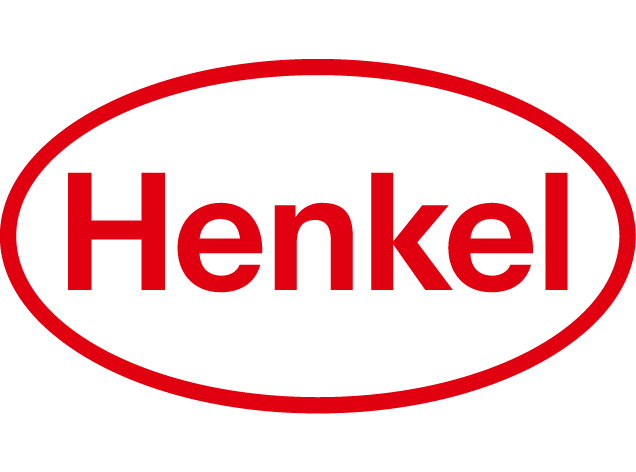
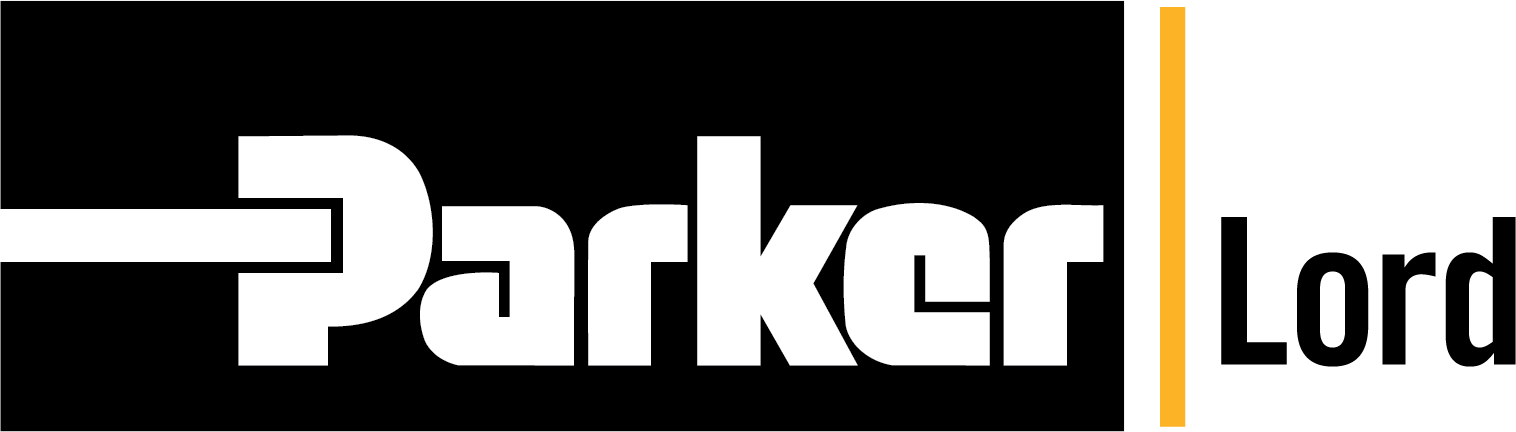
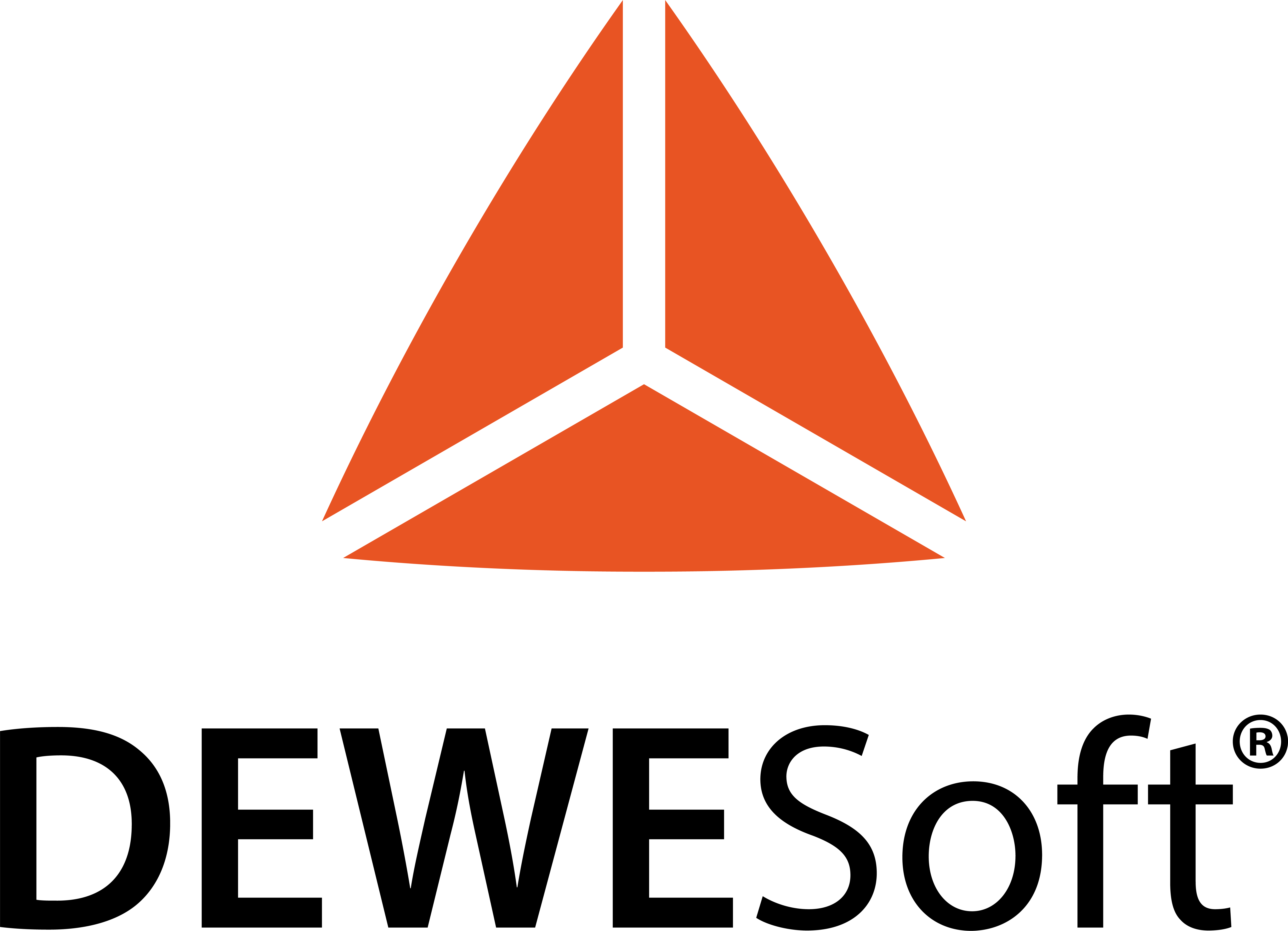
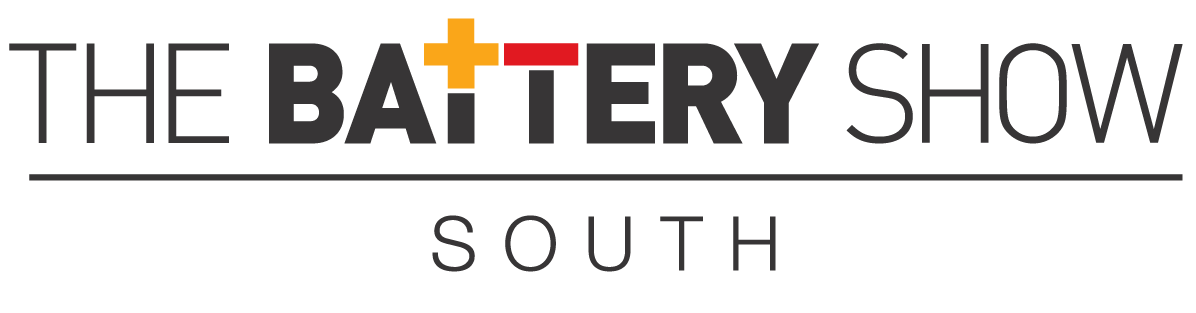
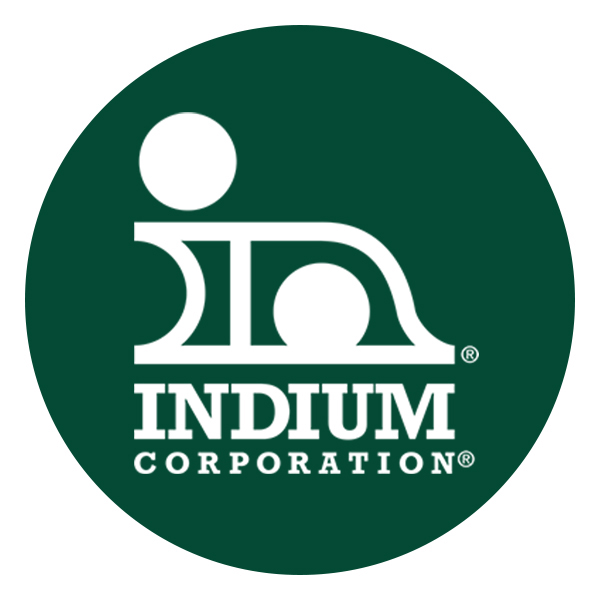
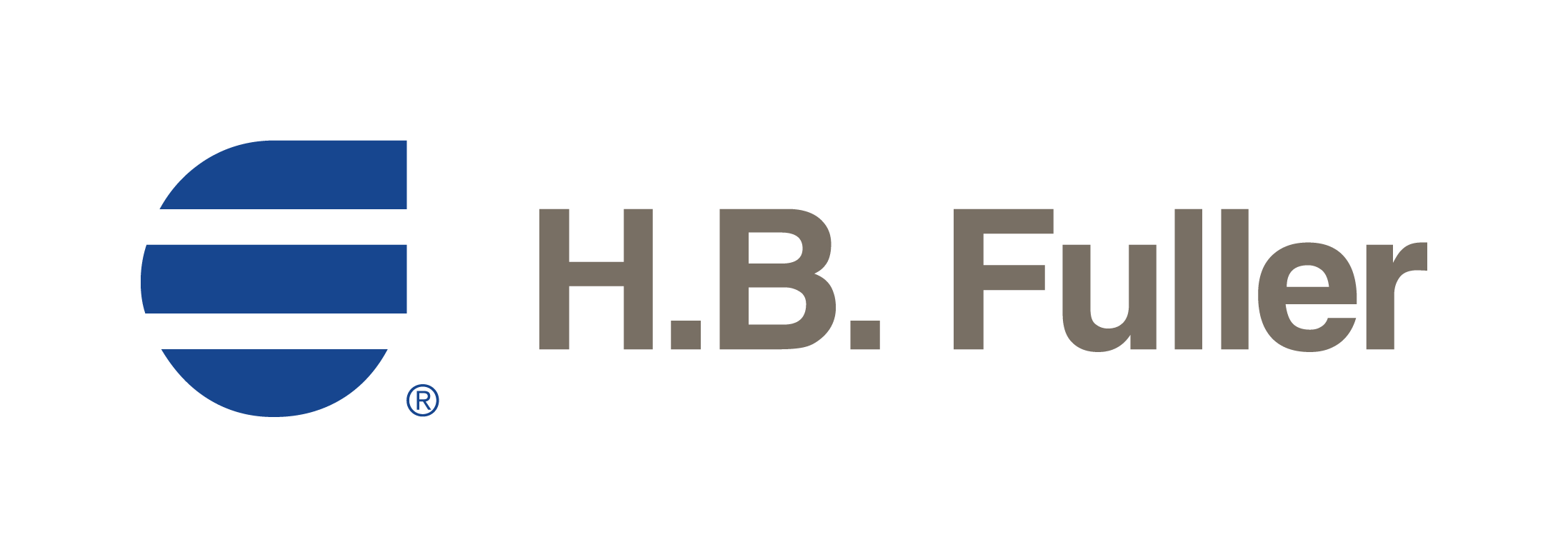