AI for battery material discovery
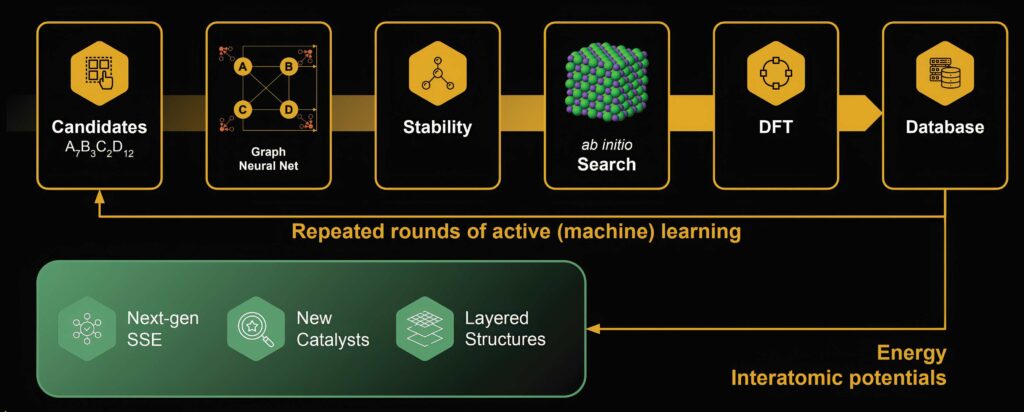
(Image courtesy of SandboxAQ)
SandboxAQ has developed a new approach to using artificial intelligence (AI) for the discovery of new battery materials, writes Nick Flaherty.
The company has combined a chemical simulation platform with the transformer AI frameworks in large language models to create what it calls a ‘large quantitative model,’ or LQM.
“I am thinking about the current way of battery material development, which is very traditional; a trial-and-error process, starting with a hypothesis, synthesis and analytical methods to test the results for the next round of the cycle,” says Ang Xiao, technical lead for materials science at SandboxAQ.
“We want to use AI and physical models to revolutionise these cycles with a large quantitative model with numerical equations. We start with chemical structure generation and use AI to predict the performance and properties as well as the cost because this is critical,” he continues.
“The two challenges we are facing in materials science are data and model architecture. For the data, we know there is massive amounts of data from the materials database at UC Berkeley, which has a library of 240,000 materials. That’s a great idea but only covers small areas,” says Xiao. “For the universal chemical space for solid state materials, a back of the envelope calculation says there are 10177 solid state materials; but AI is only as good as the training data.”
“We can significantly shorten the discovery phase from years to just a few months to get to five years for mass production, down from 10 years. Our LQM is not just reducing the cost and the time, but the most important thing is to identify materials that have never been thought of, revolutionising the discovery of totally new materials.”
Therefore, the company uses the simulation models to generate the data to train the AI model.
“It’s a smart way to generate the data because we use AI to guide the generation of the data, so we balance exploration and exploitation. We are screening millions of compounds.”
This produces suitable materials that are then tested in simulations, and can then be licensed to partners for testing in terms of suitability for battery production.
“Our business model is to work with customers to develop milestone projects,” says Xiao. “For example, we work with Dow to discover new materials using our LQM, for them to develop the IP of the materials and we share the IP. We focus on the modelling part and license the resulting materials to our partners.
“We use quantum mechanical simulation to check the results for intermolecular potentials and after that, we will validate those properties. After we have internal validation, we sample the materials to our partners who will test them and give us feedback to refine our searches to find the best candidate.
The first stage is to specify the material for the electrolyte, but the interface is also critical for the cathode. Therefore, the next phase of the collaboration will look at the reactions on the surface of the electrolyte.
“We have a very clear roadmap with two steps, starting with the battery cycle predictions this year and next year, continuing with the AQvote tool using morphology and electrochemical data to accurately identify factors such as the knee point in the discharge curve.”
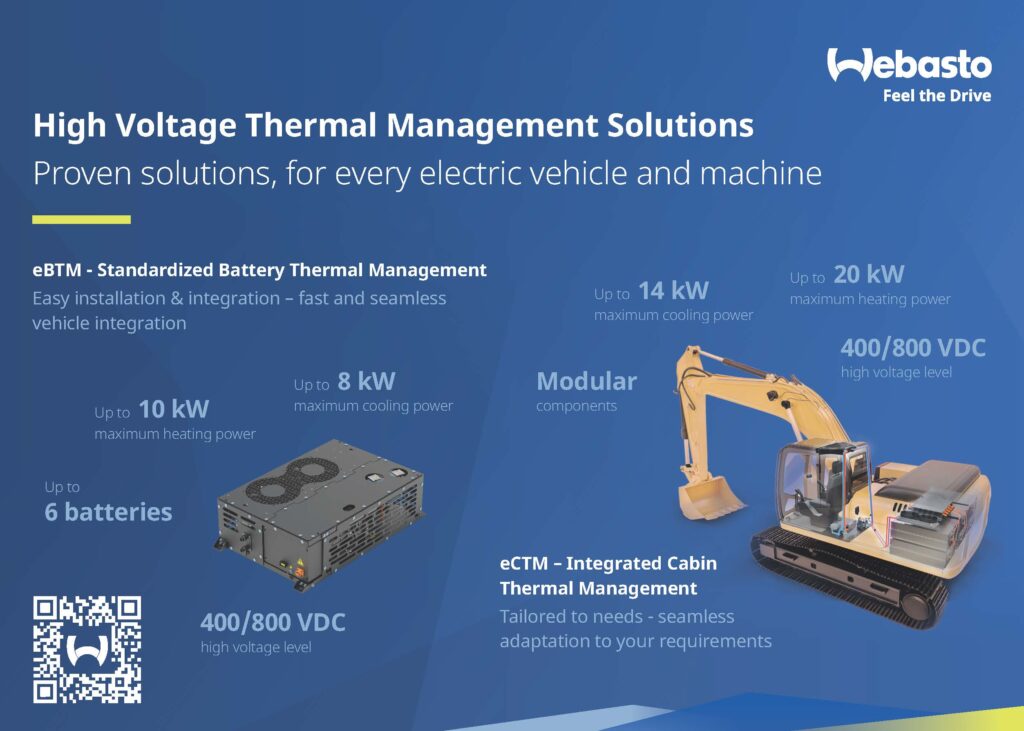
Click here to read the latest issue of E-Mobility Engineering.
ONLINE PARTNERS
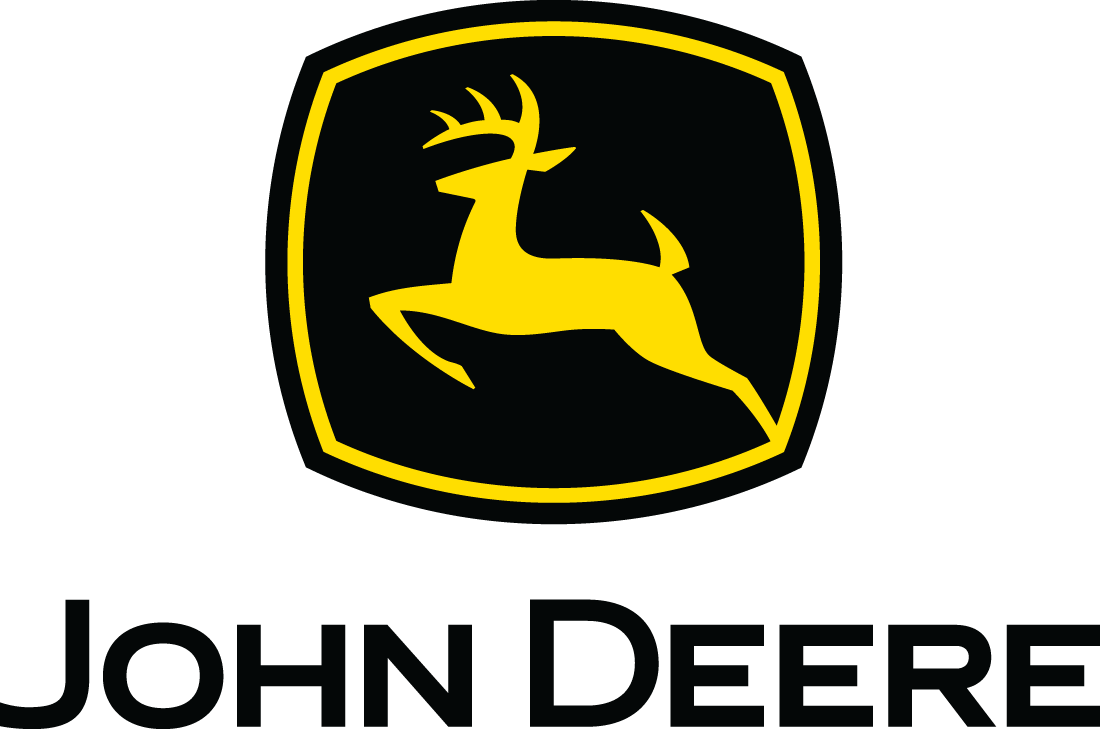
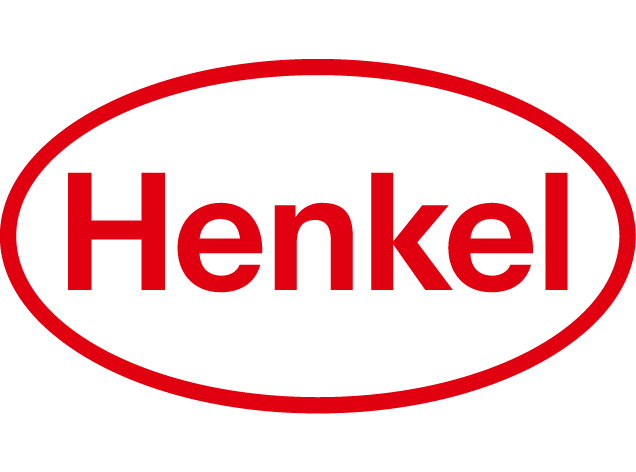
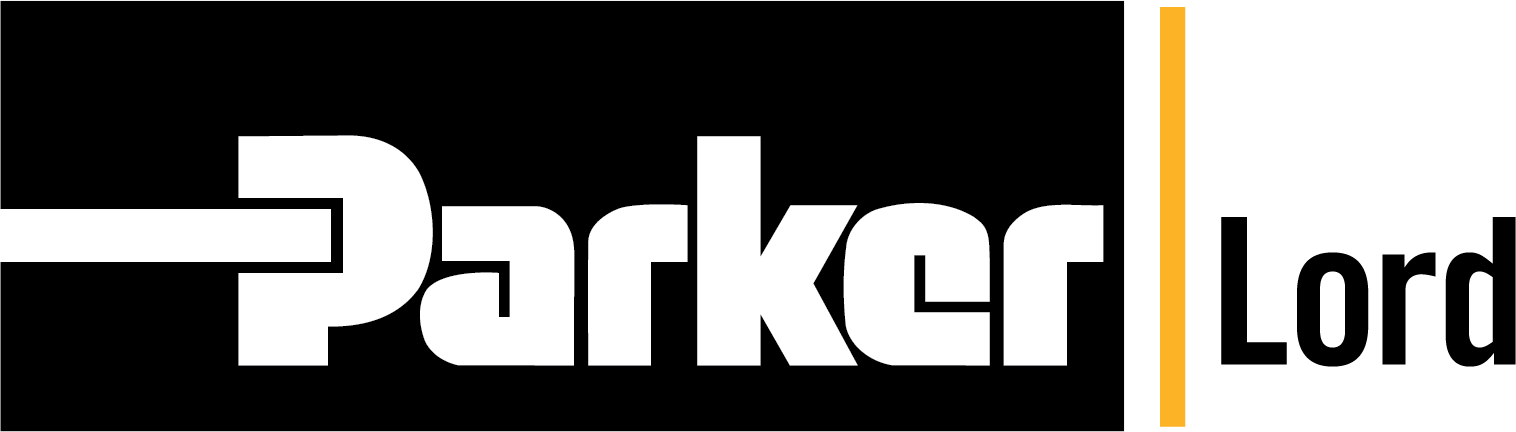
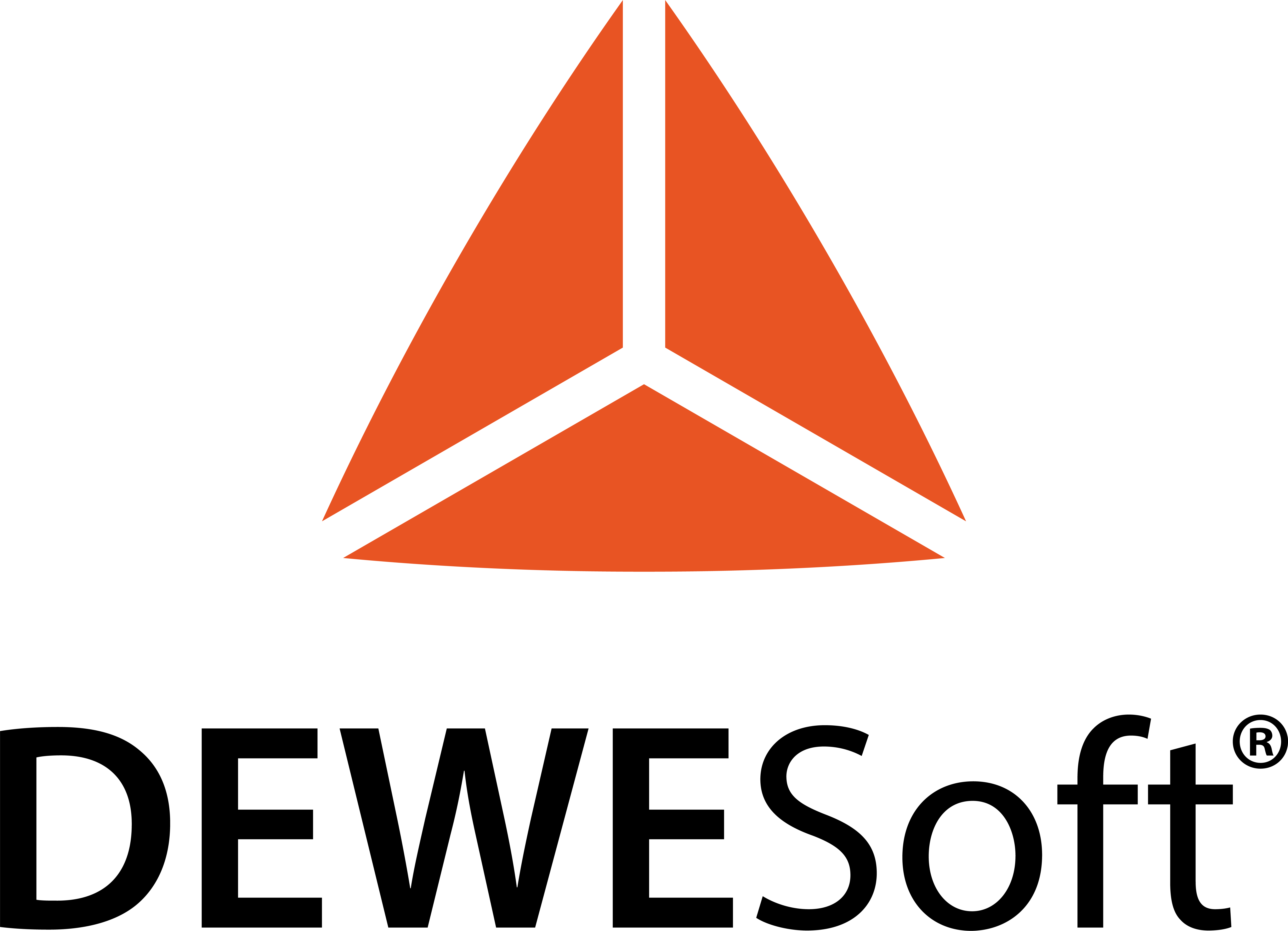
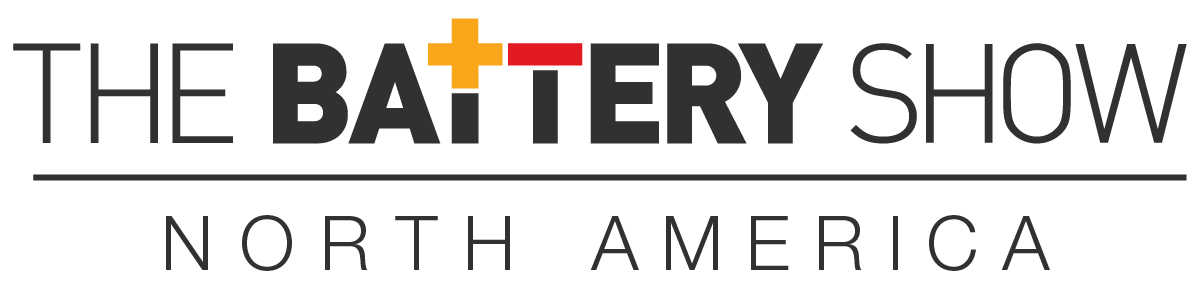
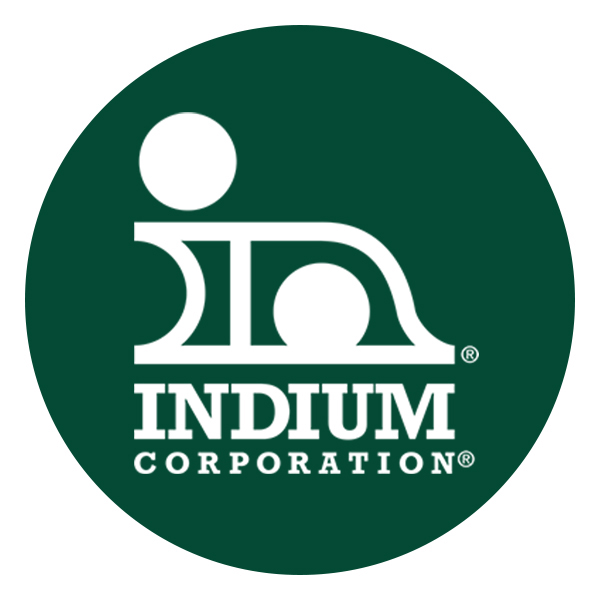
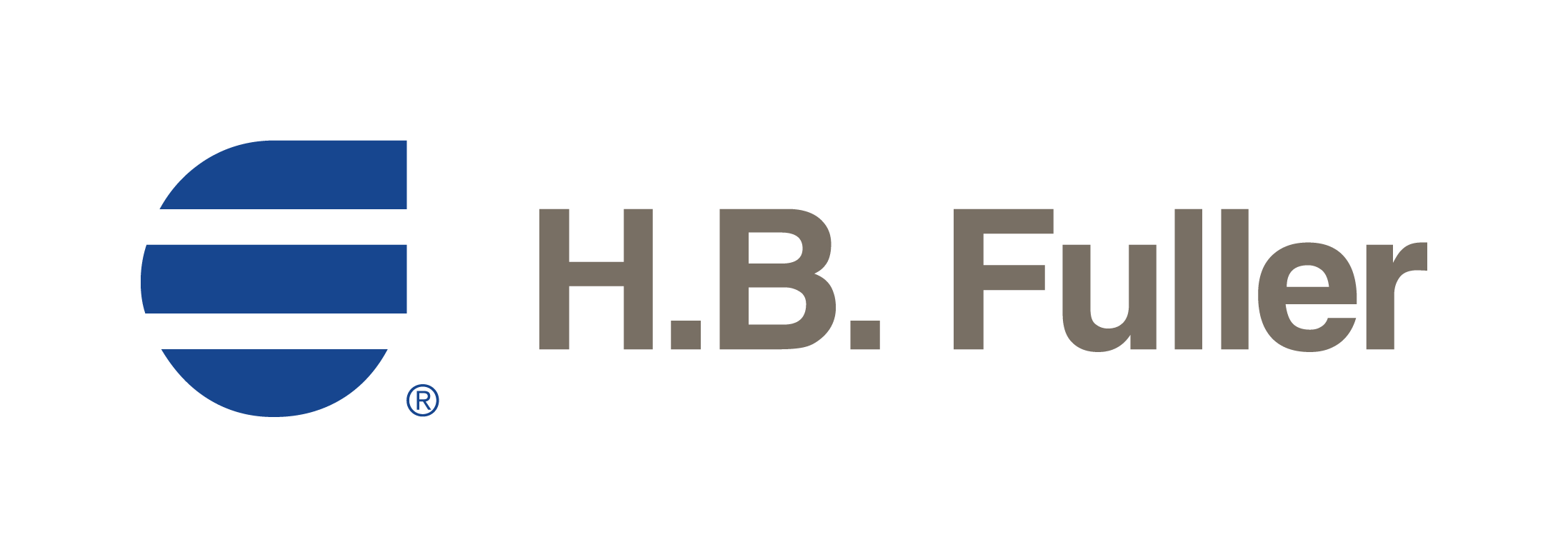
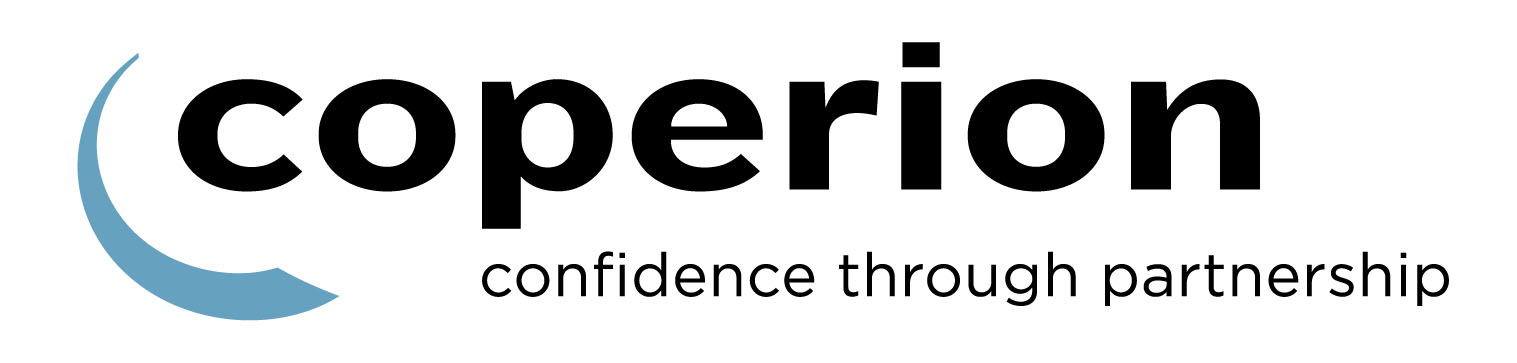