Nestech takes rapid prototyping of motor cores to a new level
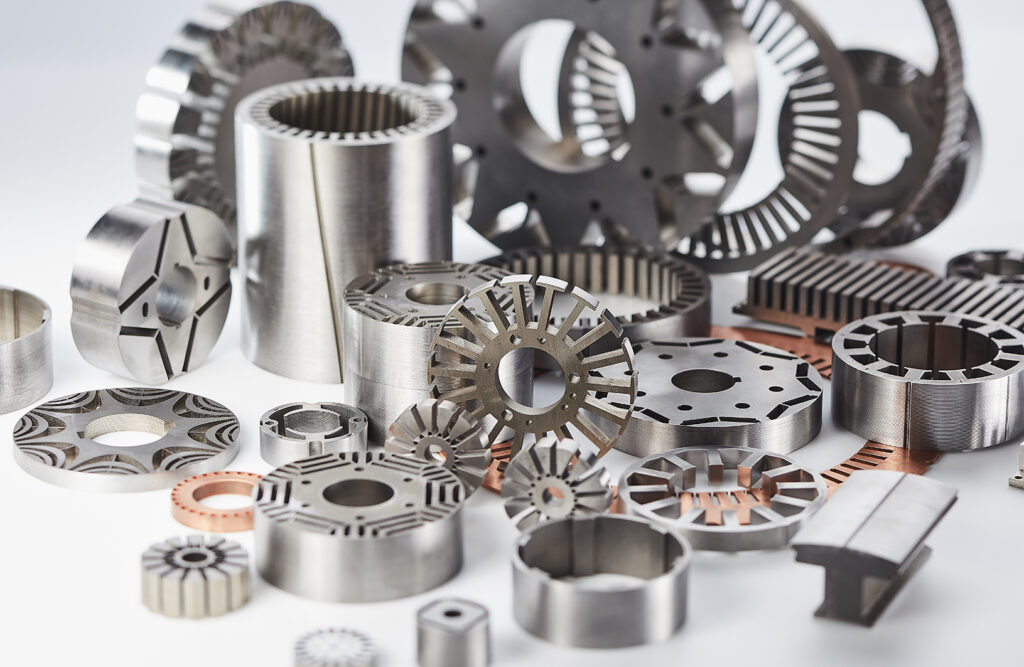
(Image courtesy of Nestech)
As electrical machine manufacturers strive to squeeze ever more efficiency out of motors and generators, there is a growing need for rapid prototyping to support tests of new core geometries in hardware form to confirm they perform in the way simulations say they should, writes Peter Donaldson.
This has created demand for individual laminations, and complete rotor and stator core stacks in small numbers, but in a wide variety of shapes and sizes – a demand that rapid prototyping specialist Nestech serves from its facility in the town of Valdastico in north-eastern Italy.
“The customer may need to freeze a new design, but before doing that, they need to test it, and this is where we can support them,” says Nestech sales manager Roberto Movio. “We can make laminations, but, most importantly, we can support the building of complete core stacks. Making laminations is a simple cutting process, but if you are to supply a core stack you have to manufacture a special tool that works as an aligning, stacking and pressing template.”
All these tools must accommodate the new and increasingly complex geometries of the laminations that make up the stacks. In stators, Movio says there are changes in the number and geometry of the winding slots, and the type and thickness of the electrical steels used, but there are more new designs in the rotors.
“We see most of the innovations in the rotor geometries, which be of permanent magnet or reluctance types, or combine reluctance and permanent magnets. Engineers constantly create new geometries with different quantities and positions of magnets, and so on. Every day we see new designs in this direction,” he says.
Movio adds that new designs are moving towards very thin, low-Gauss materials such as N010, N020 and N027, rather than traditional materials of 0.35 mm or 0.5 mm thicknesses, with the thinner lamination helping to reduce eddy currents and their associated losses.
The material is often treated with backlack, a self-bonding coating of electrically insulating material that is increasingly used to hold laminations together, as an alternative to mechanical interlocking or welding, because it eliminates points of metal-to-metal contact that creates efficiency-sapping short circuits.
Using CAD files provided by the customer, Nestech cuts the laminations to shape with a laser. “Laser cutting is a thermal process, so it always causes some heating of the steel and the insulation, so it is very important to keep the power as low as possible to minimise the impact on the physical structure of the electrical steel and any burning of the insulation on the cut edges,” says Movio.
To cut the steel, a low-power beam has to be concentrated on a very small area, and Nestech uses a 2 kW fibre laser with a beam of just 50 microns in diameter at the nozzle.
The company recently performed a study comparing lamination samples shaped by three methods: stamping; cutting with a standard, 8 kW CO2laser; and its own fibre laser, which it had examined by an independent specialist laboratory.
The laboratory commented that the magnetic properties of the stamped and fibre laser-cut laminations were comparable, with the stampings performing better in electromagnetic fields of lower strength and the fibre laser-cut samples doing better in stronger fields. Those cut with the high-power, CO2 laser did significantly worse.
The more powerful laser removed twice as much insulating material as the low-power one, and also caused a ‘heeling’ effect that created some irregularity in the laminations.
As well as its custom lamination cutting and stacking capabilities, Nestech can supply the windings for the motors.
“We provide the requested wire type, wire section, number of phases, and so on, following instructions from the customer,” Movio says. “We also have a small test station where we test the performance of everything we make.
“If you go for laser cutting and our prototyping system, we are talking about weeks – not months – to get the first prototypes.”
In addition to the rapid creation of initial ‘Proto A’ prototypes, Nestech can support the ‘Proto B’ stage, building small numbers of stacks incorporating the changes found necessary in Proto A testing. This especially applies when volumes do not justify investment in stamping, Movio says: “Switching from laser to stamping technology can be postponed or even avoided.”
Click here to read the latest issue of E-Mobility Engineering.
ONLINE PARTNERS
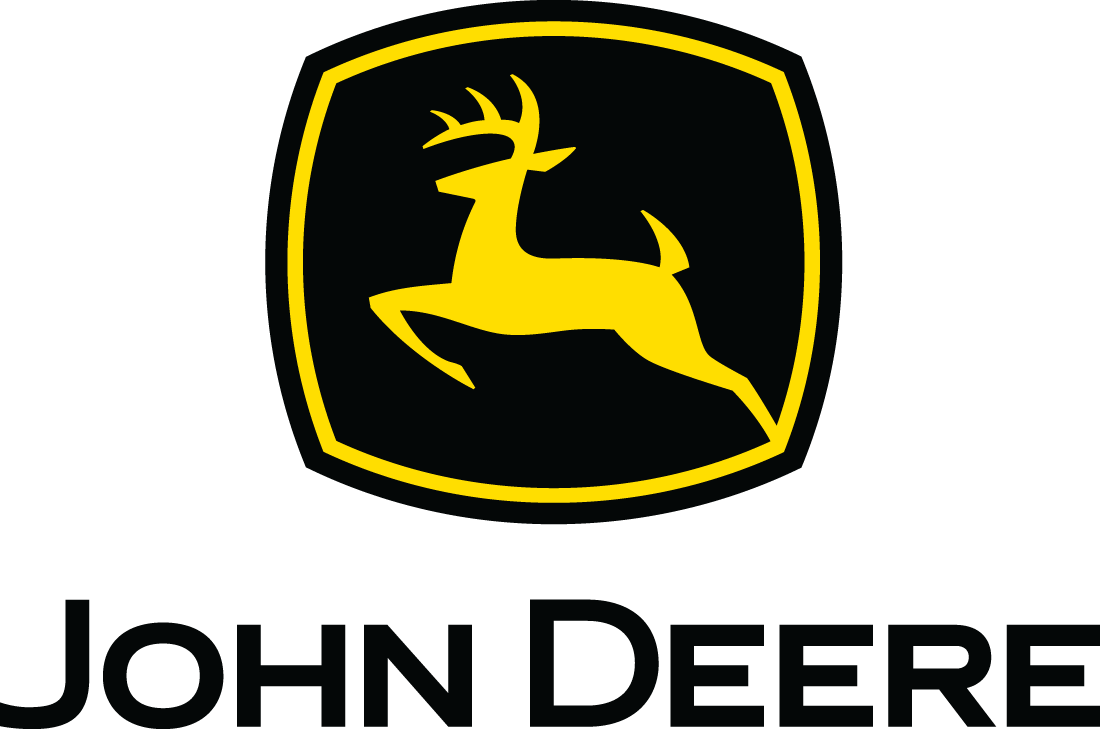
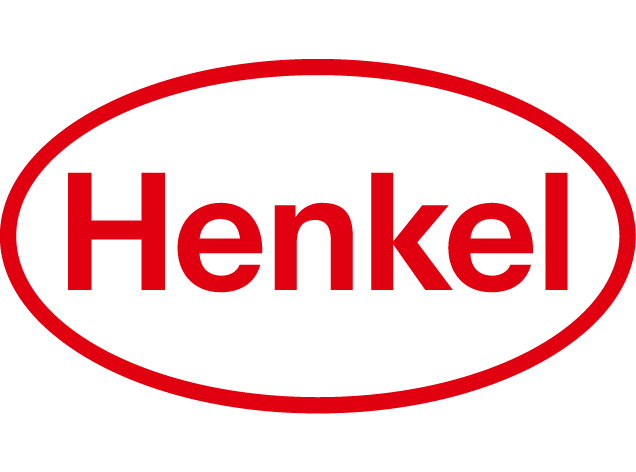
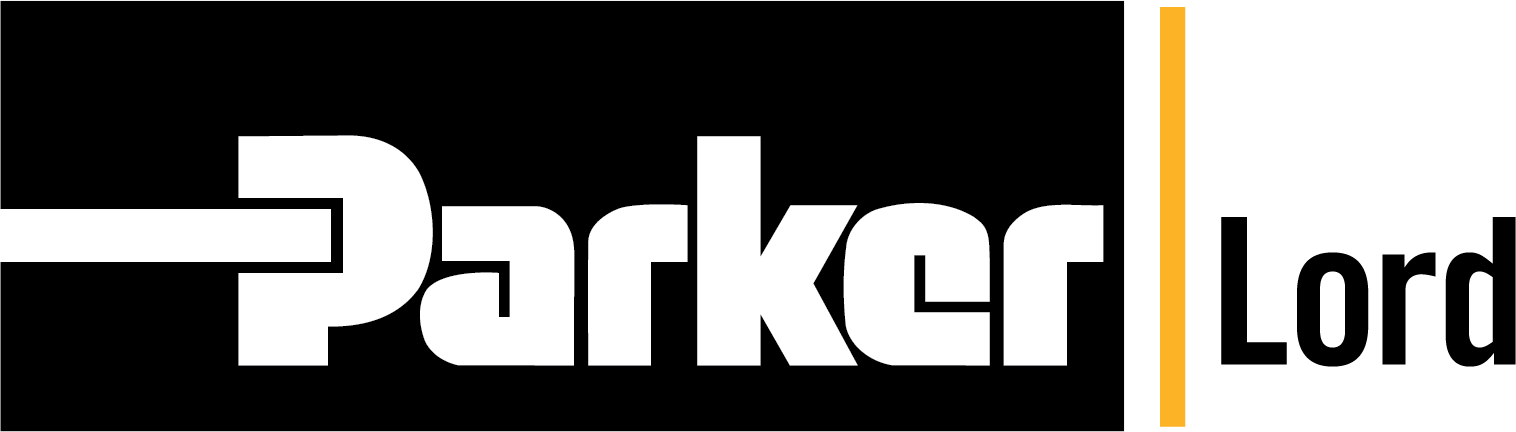
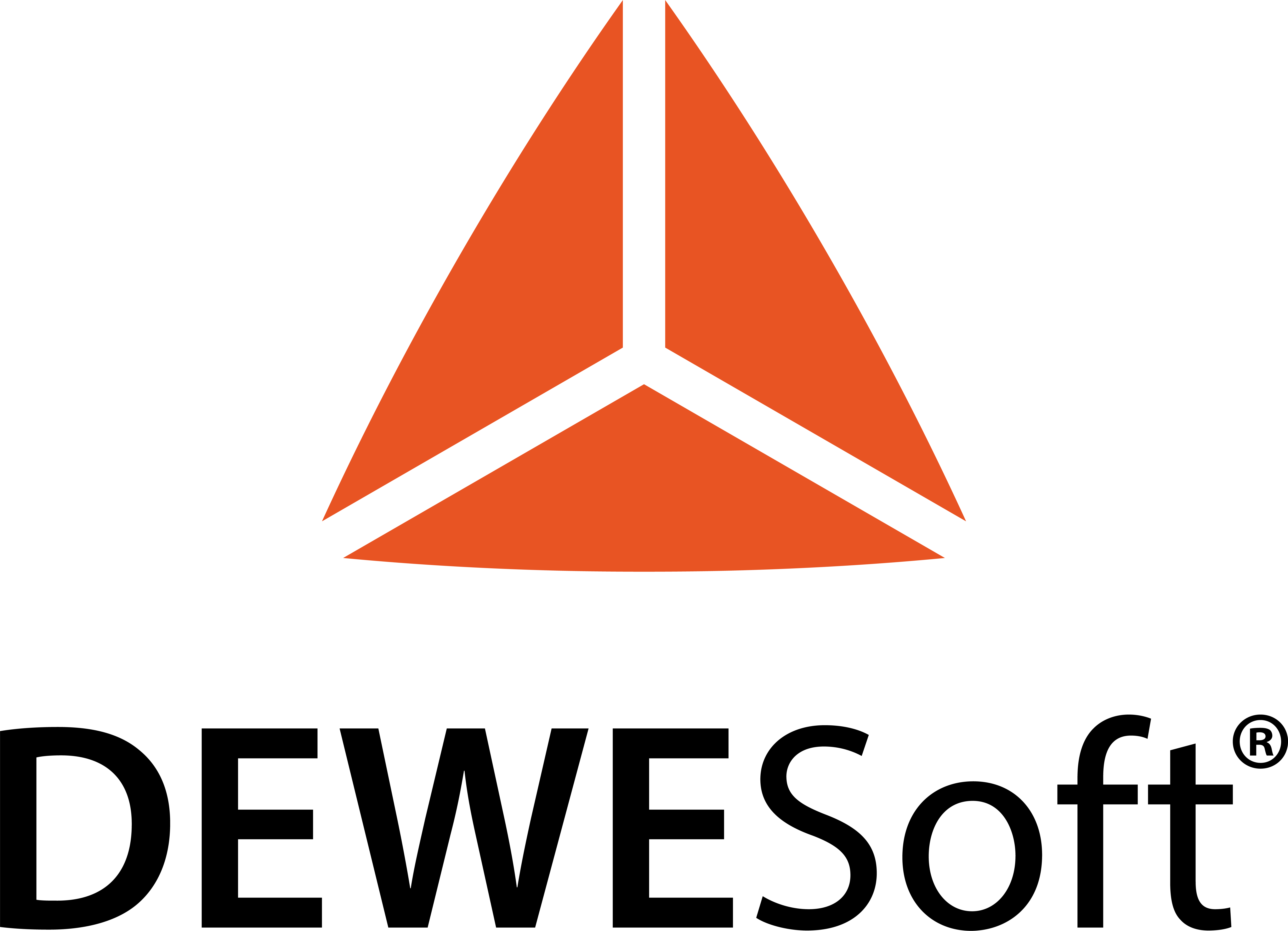
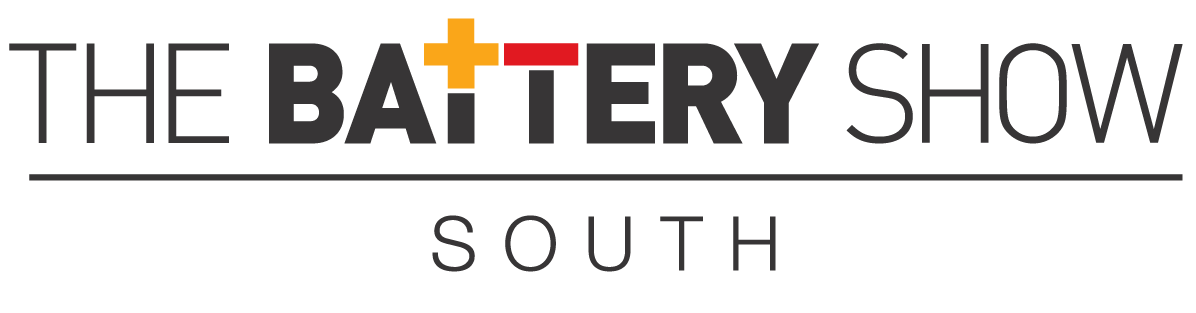
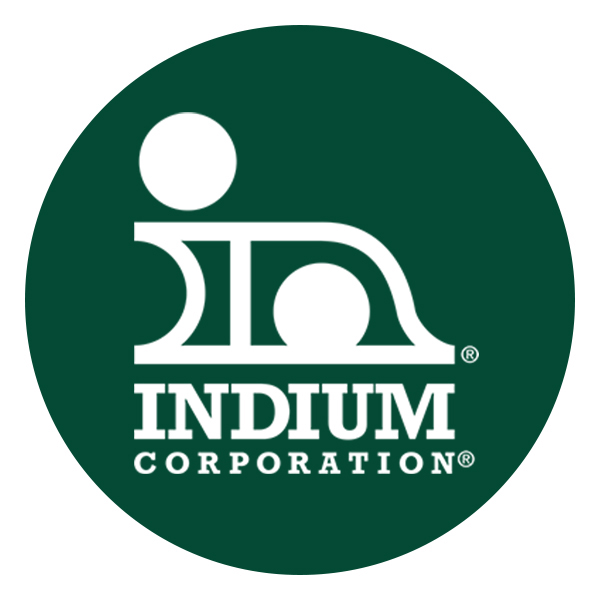
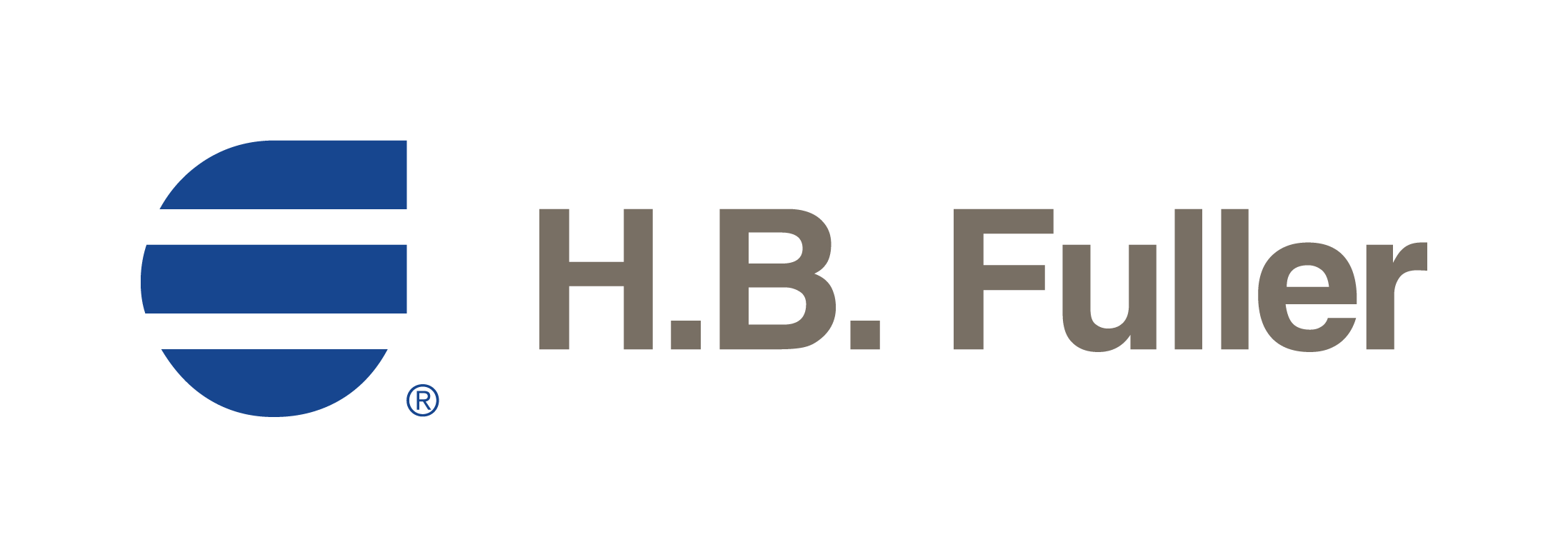