NASA tech lands for brake systems
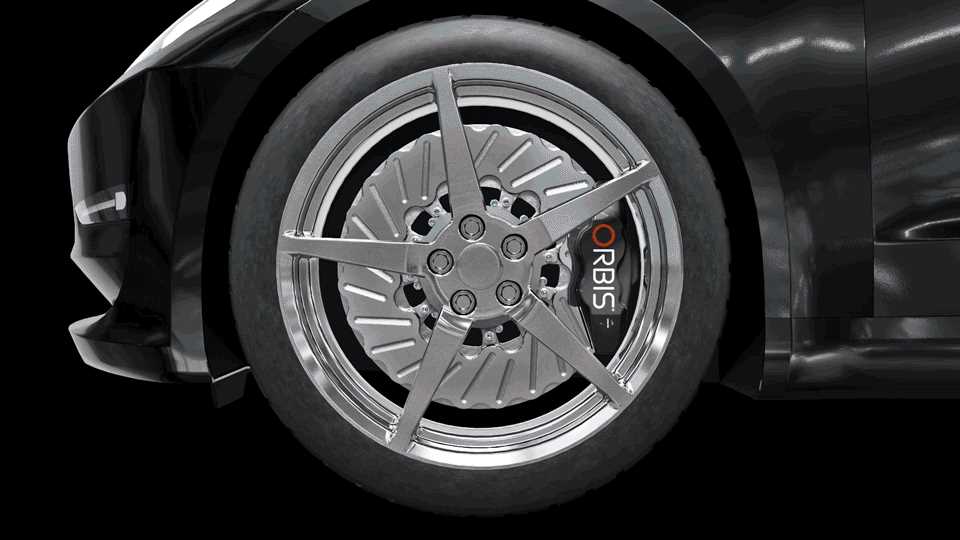
(Image courtesy of Orbis)
Orbis Brakes in the US has licensed a NASA-patented technology for lightweight braking systems in electric vehicles, writes Nick Flaherty.
The revolutionary brake disc design is at least 42% lighter than conventional cast-iron rotors, with performance comparable to much more expensive carbon-ceramic models.
Reducing the mass of wheels means a vehicle will use less energy to brake and accelerate. Conventional brake discs are heavy because they consist of two metal plates, cooled by air circulating between them. The design is inefficient because it’s the outside surfaces that are heated by friction with the brake pads, whereas the air cooling takes place on the inside surfaces, where the plates face each other.
The new technology was developed by Jonathan Lee, a structural materials engineer at NASA’s Marshall Space Flight Centre in Huntsville, Alabama, who was working on the Space Launch System.
The design started with a single disc with a series of small fins around the central hub. As they spin, these draw in air and push it across the surface of the disc, where the brake pads make contact, cooling the rotor, as well as the pads and calipers. Several long depressions around the braking surfaces, radiating from the centre, create the regular pattern.
The spinning fins and centrifugal force of the wheel push air into the depressions, causing a turbulent airflow that draws away heat. “When the air flings out, it goes across the brake caliper and cools it – no conventional rotor is capable of doing that,” said Lee.
Trenches in the braking surfaces increase the available surface for air cooling by over 30% and reduce the disc weight while boosting friction.
The troughs draw away more than just heat. Water and road debris getting between the pad and rotor are equally problematic, so the trenches provide a place for the air vortex to push any substance out of the way. Unwanted material can escape through a small hole at the end of each one.
A second, periodic wave is cut along the disc’s outer edge. By replacing the conventional, circular design with an undulating pattern, the rotor has more surface area that will come into contact with the cool air flowing over it. This extra heat dissipation will occur no matter which periodic wave pattern is used.
A thin layer of black coating applied to surfaces that don’t come into contact with the brake pads can help the rotor radiate extra heat. This three-part cooling system – convection powered by airflow, conduction of heat across the metal rotor, and radiation from dark-coated surfaces – has never been used effectively on any conventional disc brake rotor before, said Lee.
The new design can dramatically improve reliability and reduce particulate emissions. “When brake pads exceed a certain critical temperature, depending on their materials, they can emit a 10,000-fold increase in toxic nanoparticulates,” said Marcus Hays, co-CEO of Orbis Brakes.
Orbis is currently testing its EcoWave brake design to ensure it will not create that kind of emission. The initial NextWave brakes are being offered as aftermarket replacements for Tesla vehicles, enabling faster stops and better directional changes.
The company is developing two more lines: LightWave will combine the NextWave rotor with a lightweight caliper, while CarbonWave will be exclusively for EVs.
Click here to read the latest issue of E-Mobility Engineering.
ONLINE PARTNERS
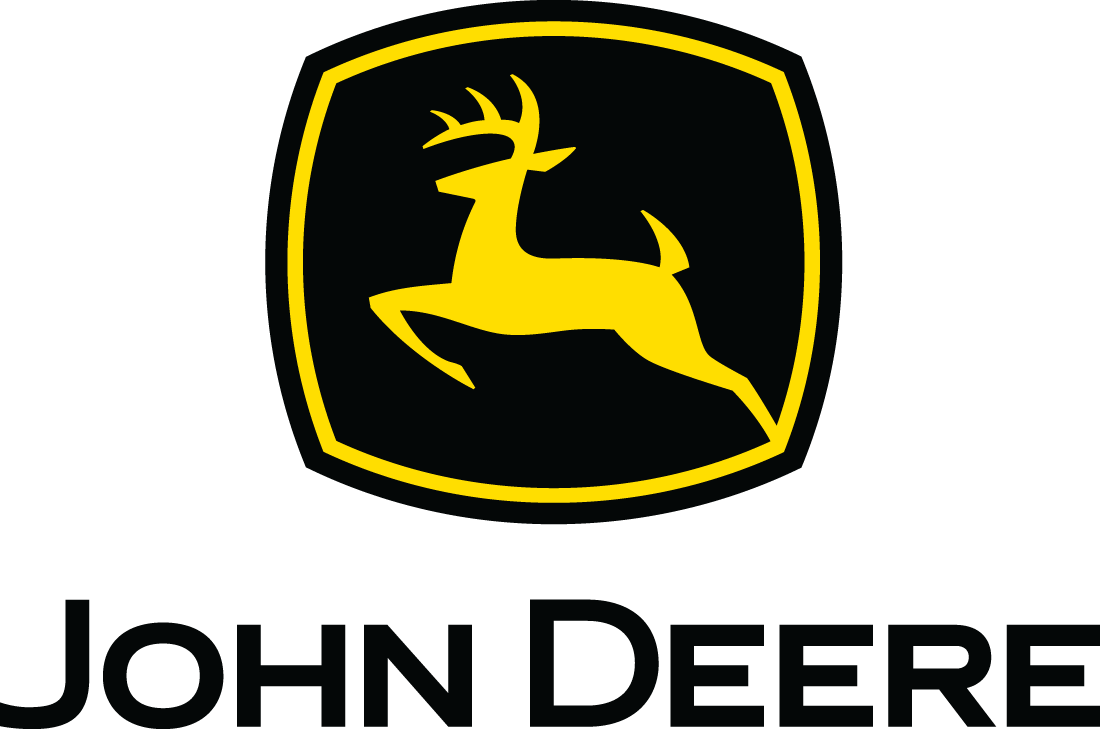
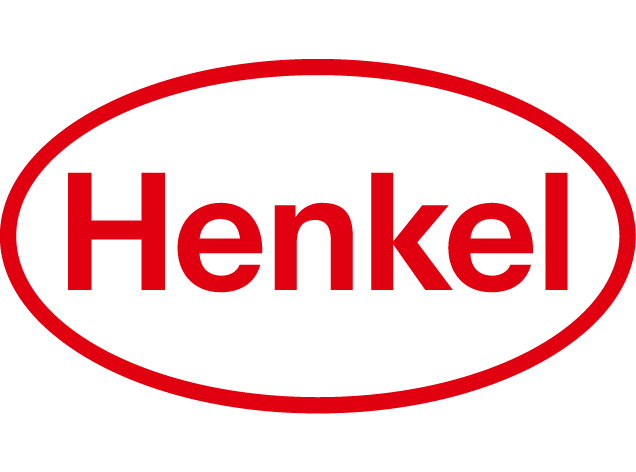
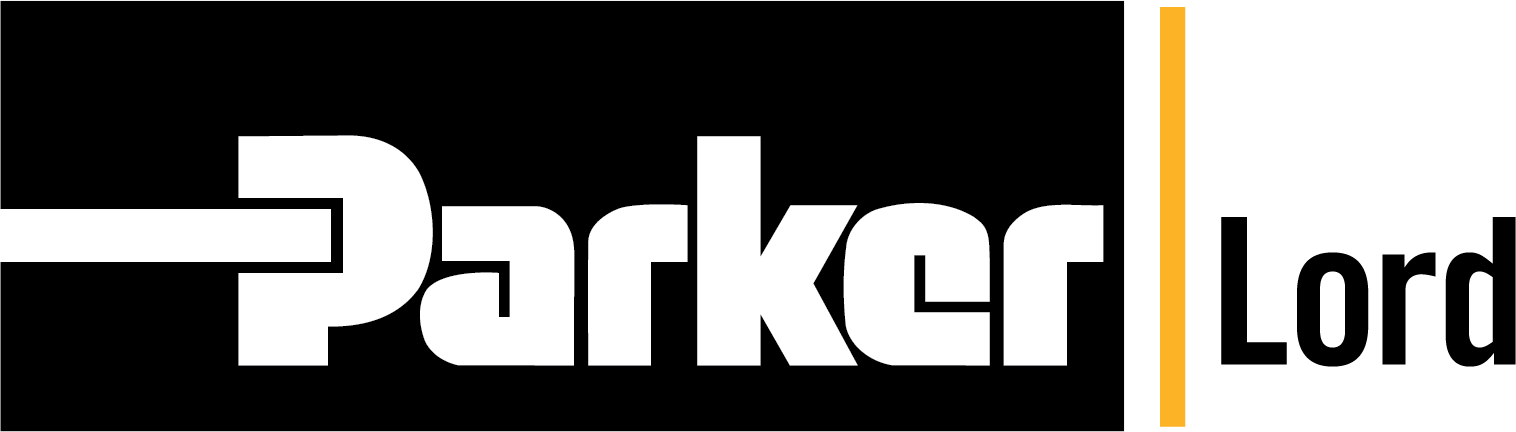
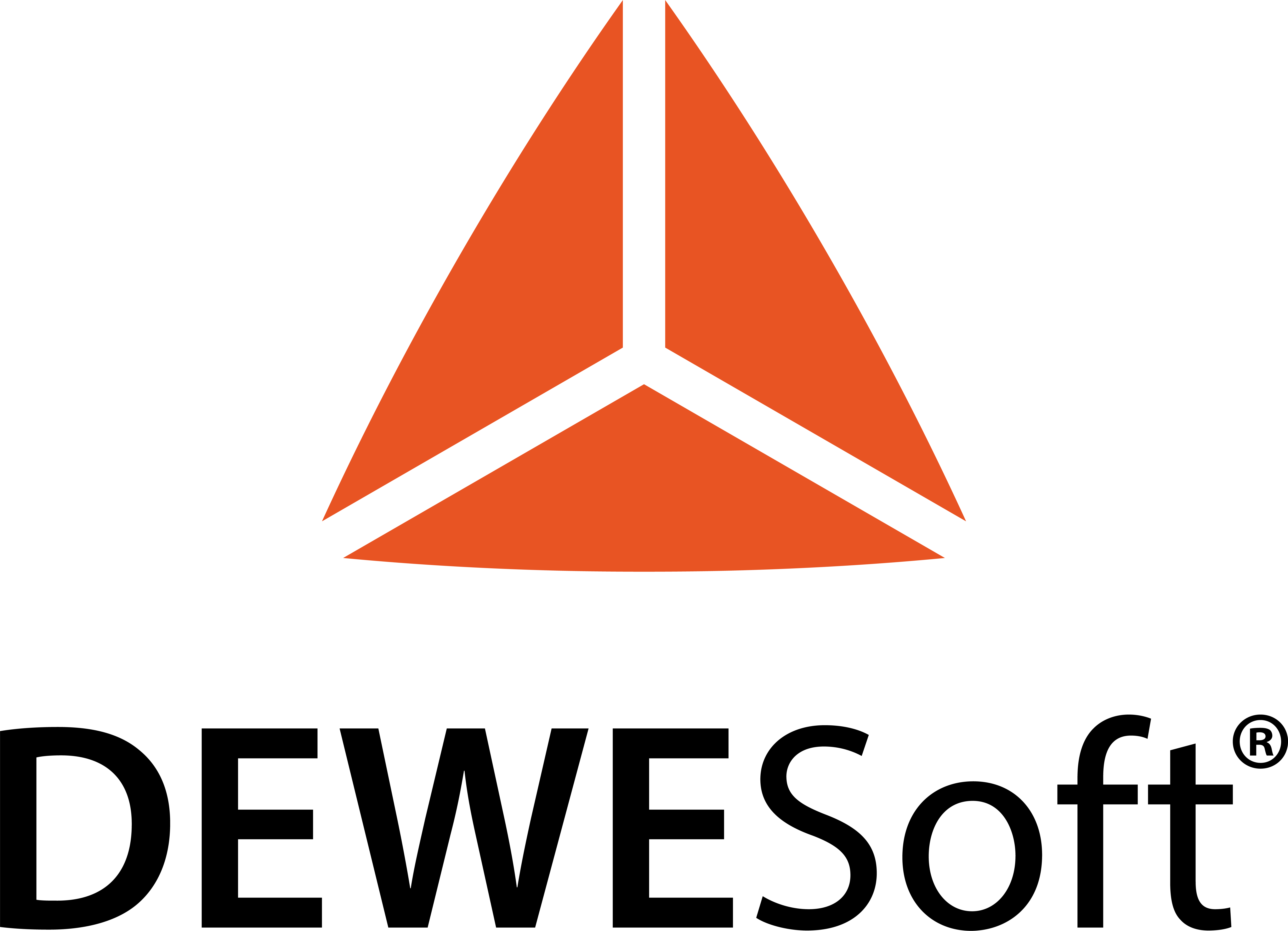
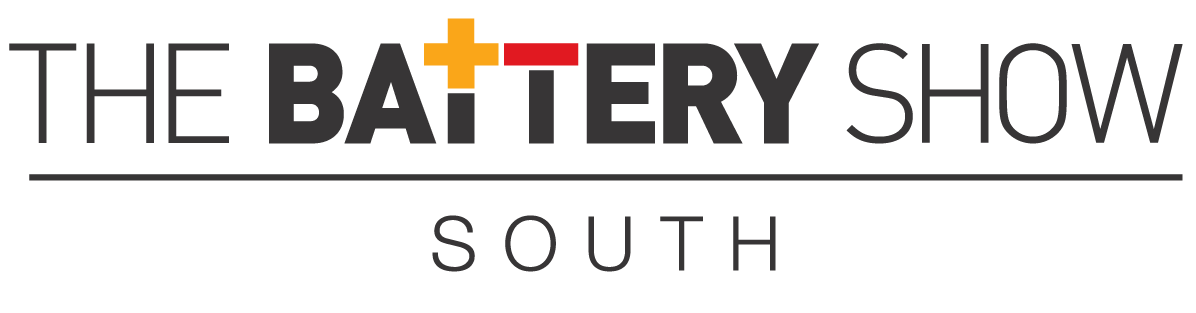
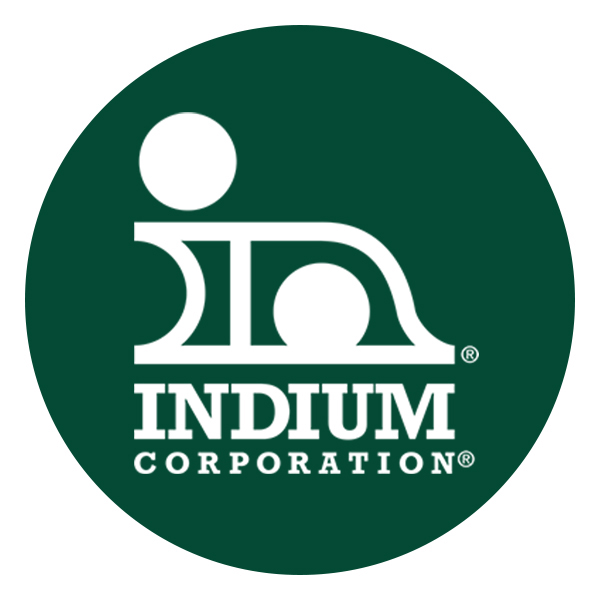
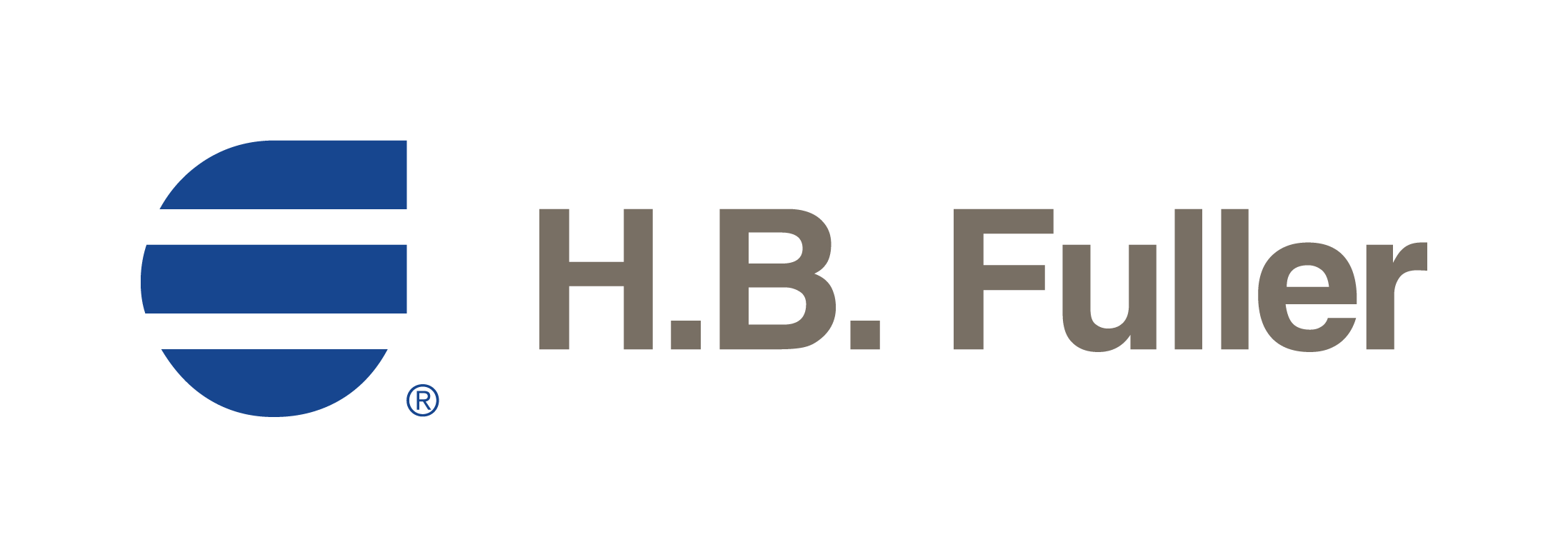