Motor materials
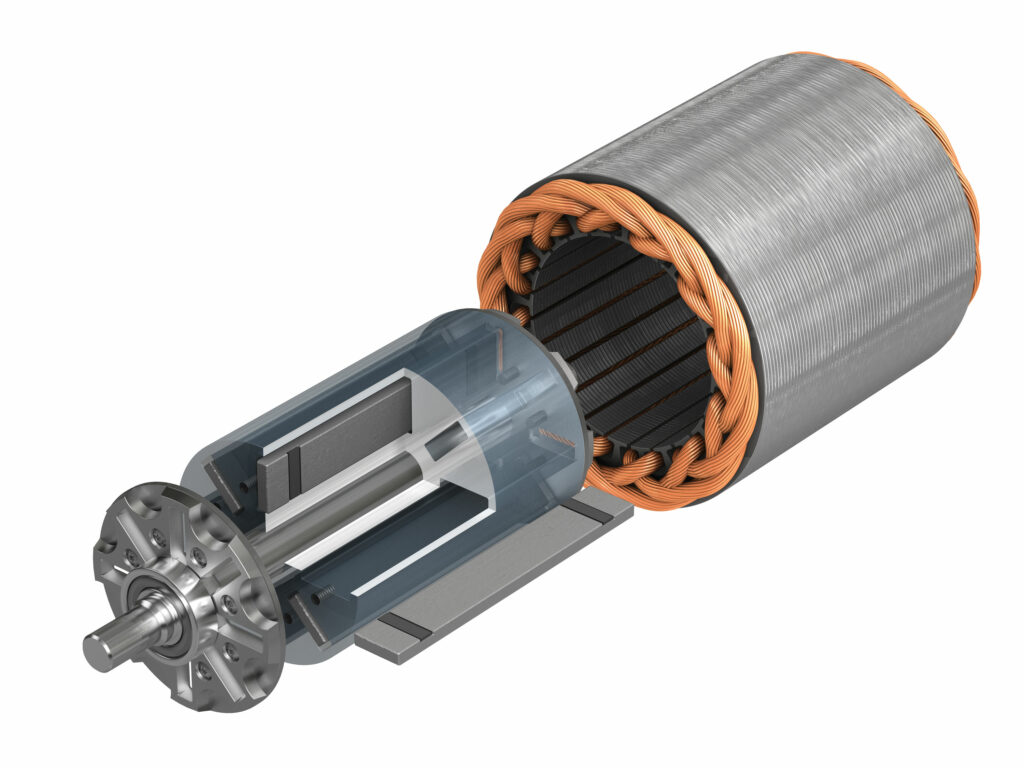
(Image courtesy of Henkel)
Making a material difference
Peter Donaldson parses the wisdom of industry experts in motor materials
Materials are as fundamental to e-motors as they are to every other engineered artifact, and selecting the right material for each application is crucial in any motor development project. Powering a broad range of vehicles with diverse duty cycles and operating environments, presents multifaceted challenges and material trade-offs.
Prominent among those challenges are the needs for high power density and high specific power to enable high performance without adding too much weight or bulk. Simultaneously, efficiency is pursued to maximise vehicle range/endurance and minimise energy consumption. These core performance requirements mandate careful consideration of the materials employed throughout the motor.
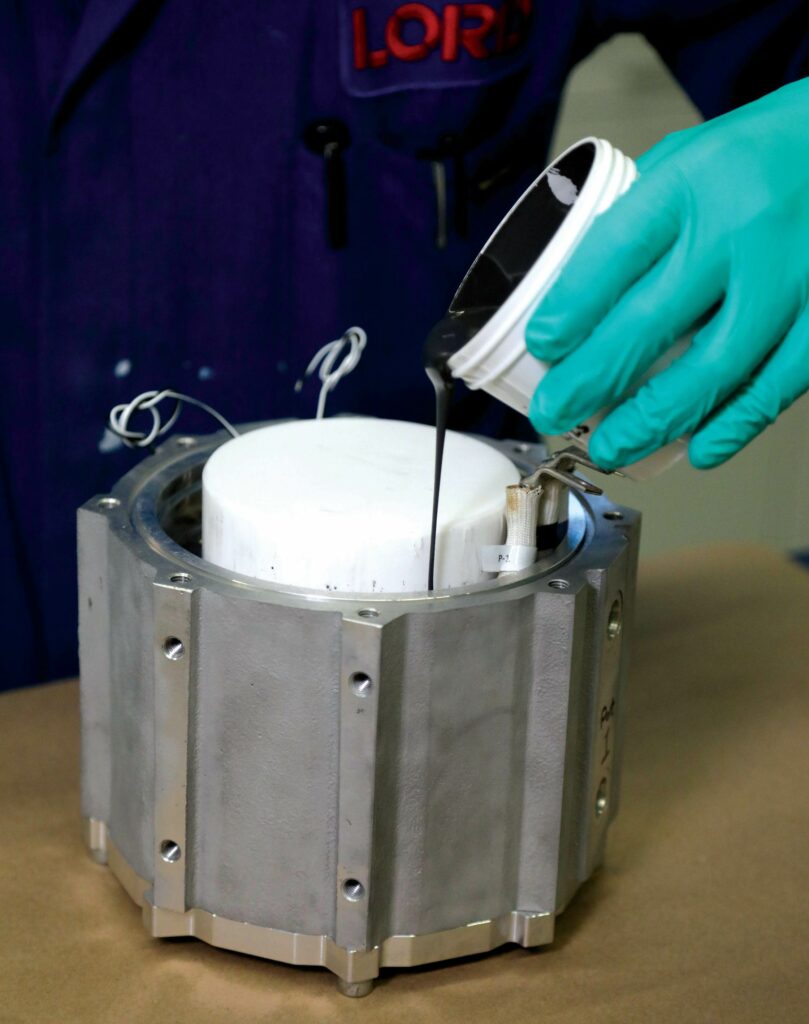
(Image courtesy of Parker Lord)
Harsh work
E-motors must withstand harsh operating conditions, including extreme temperatures, vibrations and environmental stressors such as corrosion-promoting salty/humid conditions. Coatings and surface treatments can improve corrosion resistance, for example, but they add cost and complexity associated with the extra steps required in the manufacturing process. Temperature stability is also critical, and materials must maintain their properties over a wide temperature range, which can be a particular challenge with respect to magnets and insulation materials. Vibration induces high-frequency stress reversals that can cause cracking in many materials. Therefore, robust mechanical design and resilient materials are equally crucial, and work must be done to improve the reliability and durability of insulation materials.
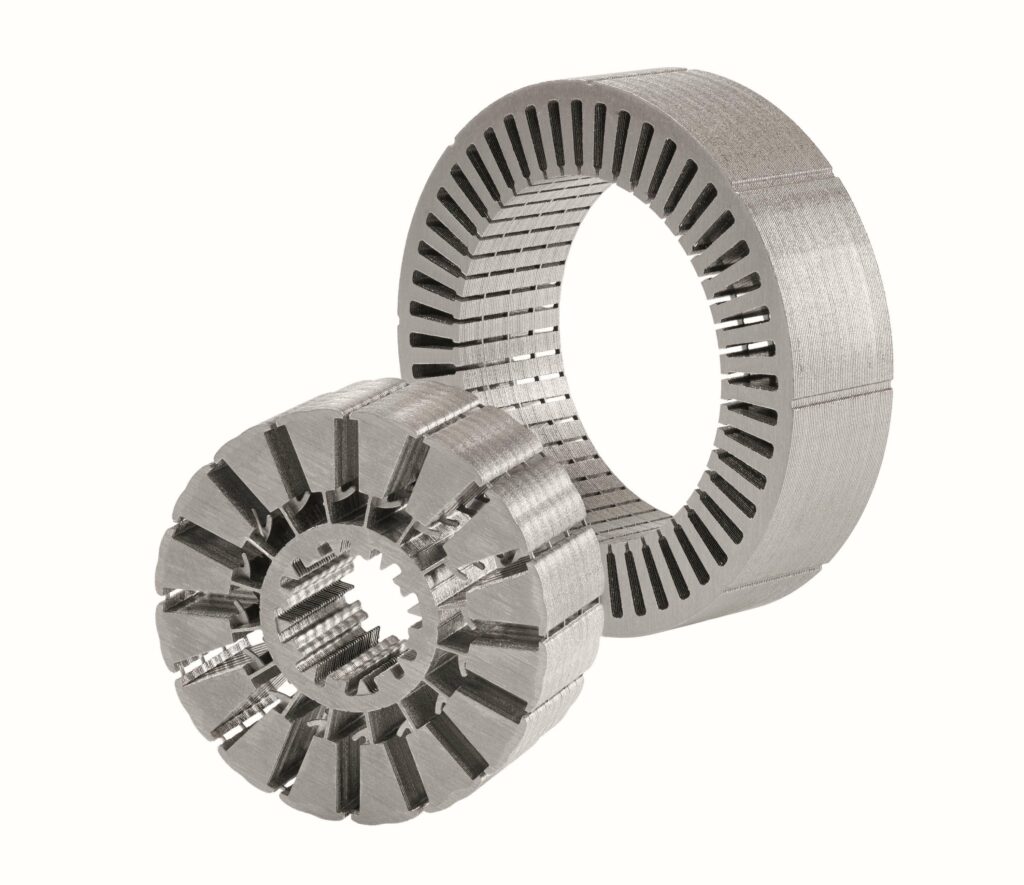
(Image courtesy of Voestalpine)
High rpm and centrifugal force
Power is a product of torque and rotational speed, and high power output often means a motor spinning very fast, which generates large centrifugal forces that, in turn, necessitate high-strength alloys that can withstand such forces without deformation or failure, although these might add weight. Lamination stacks can also be subjected to large stresses at high rotational speeds, meaning that strong bonding techniques and high-quality insulation materials are essential.
Rotational speed also affects the selection of bearing materials because increased outward force can affect bearing lifespan and efficiency; thus, bearing materials must minimise friction and consequent wear. Advanced ceramic bearings, for example, offer low friction and high durability, but are more expensive than traditional steel bearings, more on which later.
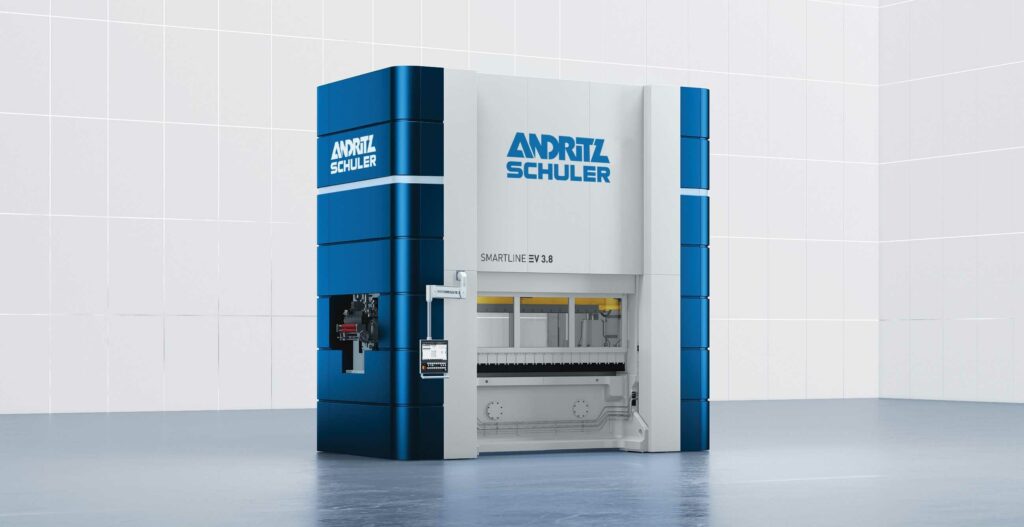
(Image courtesy of Andritz Schuler)
Taking the heat
Motors with higher power density inevitably generate more heat, meaning that the tasks of cooling and, more broadly, thermal management become increasingly important. Engineers, therefore, are faced with selecting materials for heat sinks, cooling channels and thermal interfaces that require thermal conductivity to be balanced against weight and cost. Effective thermal design, such as employing thermally conductive potting compounds or implementing actively cooled stators, can help mitigate the peak temperatures experienced by motor components, thereby preserving efficiency and extending lifespan. The higher thermal conductivities of self-bonding varnishes (Backlack for example) on electrical steel, compared with that of air, also contribute to more effective heat dissipation from the motor core. (For more on cooling, see the feature starting on page 42.)
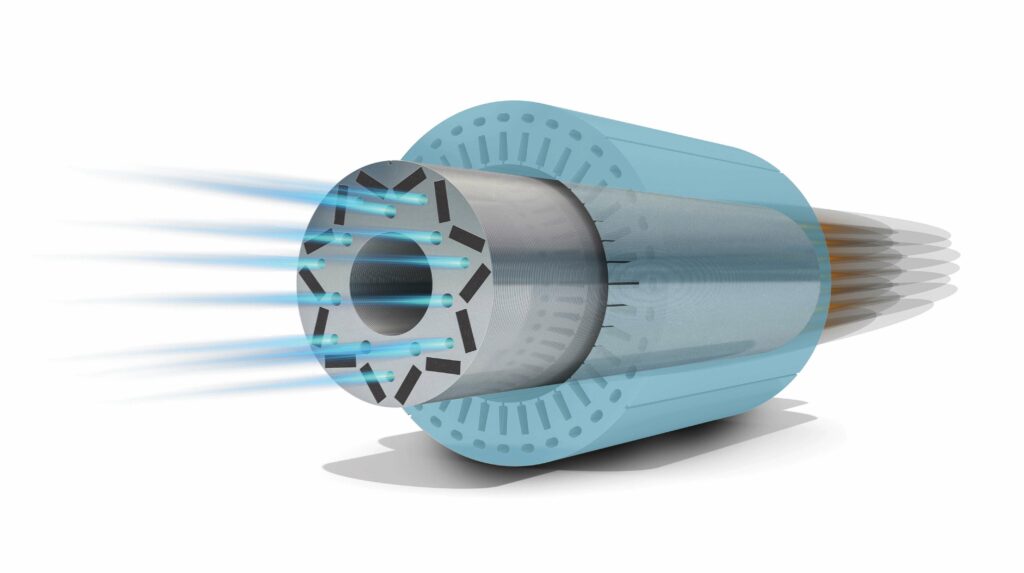
(Image courtesy of Voestalpine)
Chasing efficiency
The pursuit of higher motor efficiency is constrained by several limitations imposed by available materials. A primary challenge lies in maximising the packaging density of the motor’s core components, namely the laminated rotor and stator stacks, as well as the copper windings in the stator. Existing insulation coatings on electrical steel sheets, sometimes made as adhesive layers used to bond these sheets together, introduce a physical barrier that limits how tightly the laminations can be packed. Similarly, the insulation around copper wiring and the required spacing between windings impact the achievable density in the stator. Ongoing research is focused on developing adhesive systems capable of achieving ultra-thin bond-line thicknesses while maintaining high bond strength and exhibiting rapid curing times.
Beyond packaging density, the temperature stability of permanent magnetic materials at elevated operating temperatures presents a substantial hurdle. As motors become more power-dense, their magnets are subjected to substantial heat. Maintaining magnetic performance at such temperatures is crucial for sustained efficiency and reliability. Furthermore, the formation of eddy currents within the electrical steel contributes to energy losses, necessitating use of materials with inherently lower eddy current susceptibility.
One of the most significant material limitations hindering higher-efficiency motors designed for e-mobility is electrical insulation. Traditional slot liner materials such as aramid paper and wire coating materials like enamels have not evolved at the same pace as e-motor design. Thermoplastic solutions for both slot and wire insulation are being developed to address this mismatch, experimentally demonstrating efficiency increases of 1–2 percentage points owing to the thinner insulation leading to an increased fill factor and lower thermal resistance. This impacts motor design, the battery pack and the entire system, enabling more compact, lighter, cost-effective and sustainable designs with potential for downsized batteries for equal range.
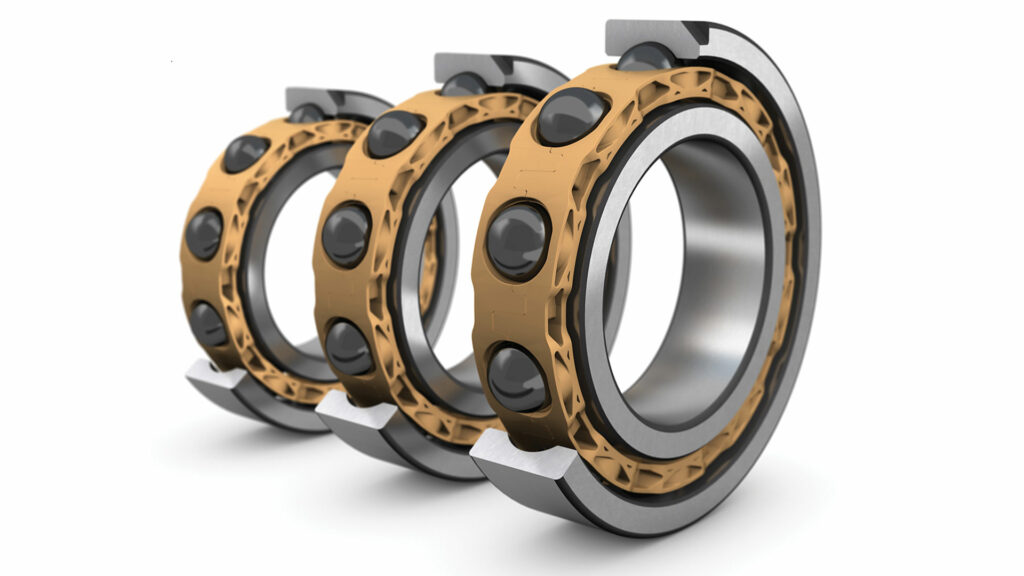
(Image courtesy of SKF)
Imperatives of mass production
As production volumes rise, scalability and cost-effectiveness become critical, bringing their own set of material trade-offs. Rare earth magnets, high-grade electrical steel and advanced alloys, for example, can all be expensive, making material substitution and recycling attractive options where available. Volume production focuses attention on design for manufacturability and automation, often penalising complex motor designs and the use of highly specialised materials. At the same time, diversifying material sources and developing recycling infrastructure become increasingly vital to supply chain security and sustainability.
Supply chain security
With increasing geopolitical uncertainty, the supply chain security of critical raw materials, particularly those used in high-performance permanent magnets, is a growing concern. Heavy reliance on imports of these materials or their precursors poses a potential threat to the future development of high-efficiency motors, especially in regions with limited domestic resources. To mitigate this risk, significant efforts are being directed toward establishing local capabilities for recycling and processing end-of-life magnetic materials. The goal is to create a circular economy for these critical components, ensuring a more stable and sustainable supply. Finding suitable alternatives to rare earth magnets that offer comparable performance is a major challenge, as is the development of cost-effective and environmentally friendly processes for their recycling. Furthermore, improving the temperature stability of magnetic materials for high-temperature applications is also exercising the ingenuity of materials scientists and engineers.
Magnetic attraction
Rare earth permanent magnets create strong magnetic fields that are crucial for achieving high power density and efficiency. These strong magnetic fields contribute to lower conductive (‘copper’) losses by reducing the current needed to generate a specified amount of torque. In particular, neodymium-iron-boron (NdFeB) magnets exhibit high magnetic remanence and coercivity that reduce electrical losses in the stator and enable motors to operate more efficiently, even at partial loads. While alternatives to rare earth magnets, such as ferrite magnets, are cheaper and offer better intrinsic temperature stability and corrosion resistance, they typically exhibit lower magnetic performance and lack the high remanence or energy production crucial for efficient e-motors.
Today, sintered NdFeB magnets are the standard used in e-motor development. The temperature stability they need to withstand high operating temperatures comes from the use of heavy rare earth elements such as dysprosium and terbium. Whilst first-generation high-temperature sintered NdFeB magnets had a heavy rare earth content of between 8% and 10% by weight, the latest grain boundary diffusion treated magnets contain much less, typically between 2% and 3%.
Hot-deformed NdFeB magnets provide an alternative without requiring heavy rare earths, achieving temperature stability equal to that of most sintered magnet grades but with better corrosion resistance. Production of hot-deformed magnets is simpler than that of sintered magnets formed from highly pyrophoric (igniting spontaneously in air) powders, and recycled powders are being developed for hot-deformed magnet production.
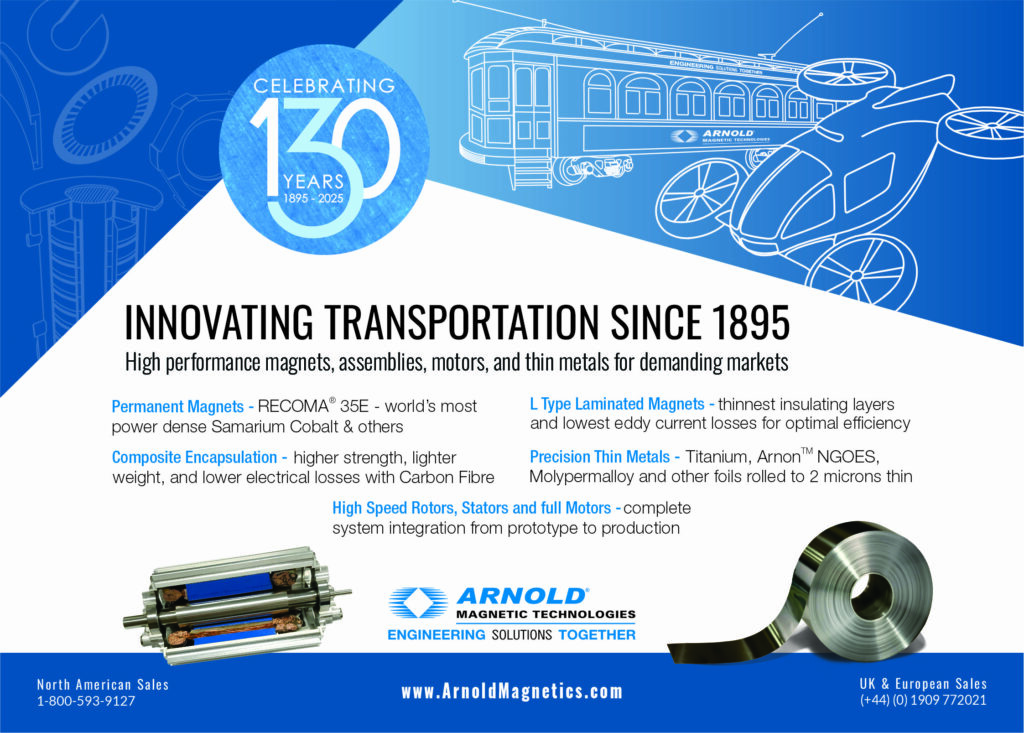
Grains, crystals and orientation
Besides permanent magnets, motors also rely on electromagnets, formed by current flowing through conductors wound around cores of electrical steel. Electrical steel is a crystalline material composed of grains, which are regions where the iron atoms are arranged with a consistent structure. The interfaces between these grains are known as grain boundaries. Certain grain orientations offer lower resistance to changes in the direction of magnetisation (magnetically favourable textures), while others are less conducive (magnetically unfavourable textures). Grain boundaries themselves act as obstacles to the movement of magnetic domains, which are regions within the material where the magnetic moments of the atoms are aligned. A smaller number of grain boundaries generally makes reversal of magnetic polarity easier, leading to reduced core losses. This is why electrical steel undergoes high-temperature processing to promote grain growth, resulting in larger grains. However, in very high-frequency applications, excessively large grains can lead to increased eddy current losses.
One important distinction is between electrical steels that are grain-oriented and those that are not. Grain-oriented electrical steel exhibits superior magnetic properties, specifically in the rolling direction, owing to its specially aligned crystallographic texture, but exhibits poor properties perpendicular to the rolling direction. This brings advantages for use in segmented stator stacks where this directional property can be used effectively. However, processing grain-oriented steel into such segmented stacks is more complex and, importantly, it is unsuitable for use in the rotor.
Non-grain-oriented electrical steel, on the other hand, possesses good magnetic properties both longitudinally and transversely to the rolling direction. This isotropic behaviour makes it more universally applicable for various motor components, including the stator in non-segmented designs and the rotor, because rotors are not normally segmented.
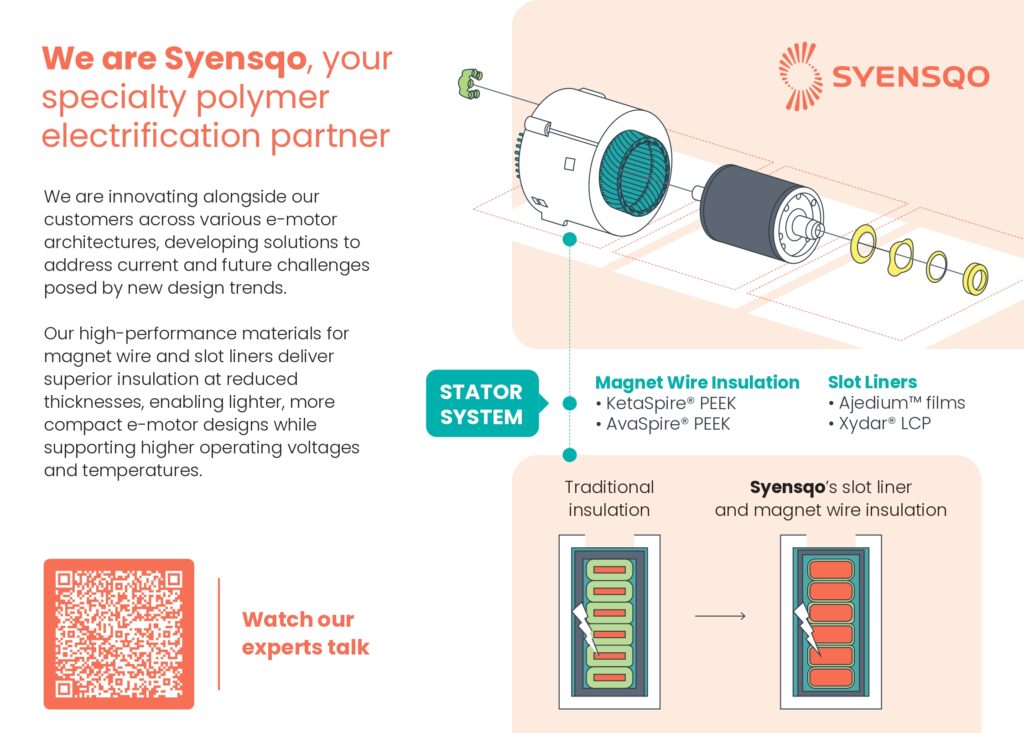
Extra ingredients
Alloying elements such as silicon (Si), aluminium (Al), manganese (Mn) and phosphorus (P) are added to electrical steel to modify its properties; specifically, to increase its electrical resistivity. This is crucial for reducing eddy current losses, which become particularly dominant in high-speed machines and at higher operating frequencies. Consequently, electrical steel grades used in e-mobility applications typically have higher alloy content.
However, these alloying elements tend to diminish the polarisation and saturation magnetisation of the steel, which can reduce the motor’s torque density, but increasing the alloy content often leads to increases in the mechanical strength of the steel.
Minimising core losses
Efforts to improve electrical steels are focused on reducing core losses at high switching frequencies, increasing permeability, developing cost-effective manufacturing processes for thin laminations and improving mechanical strength. High permeability is a measure of its ability to conduct magnetic flux. The higher the permeability, the higher the torque and power of a motor.
Core losses affect the energy consumption of a motor, and the aim is to minimise losses caused by electrical eddy currents and hysteresis. Hysteresis is the phenomenon of the magnetic flux density in a motor’s iron core (stator and rotor) lagging behind the cyclic magnetising force produced by the current in the windings. This ‘magnetic lag’ results in energy loss. Together, hysteresis losses and eddy current losses are known as iron losses.
Achieving optimal performance at the high switching frequencies used to drive motors by inverters based on silicon carbide (SiC) transistors requires thin laminations with insulating coatings, which increase manufacturing complexity and cost. The thickness of the electrical steel laminations also has an impact on motor efficiency, with thinner laminations increasing resistance to the flow of eddy currents in motor cores. The general trend in motor core production underscores the importance of steel laminations that typically range in thickness from 0.20 to 0.25 mm; however, even thinner laminations (<0.2 mm) are good for reducing eddy current losses at higher switching frequencies. Also, alloying elements such as Si, Al, Mn and P reduce electrical conductivity and, consequently, eddy current losses.
The production and subsequent processing of very thin and highly alloyed steel sheets and lamination stacks present significant manufacturing challenges in terms of both time and complexity. For example, the stamping and joining of such thin materials represent major hurdles because such processes push traditional mechanical interlocking methods to their technical limits.
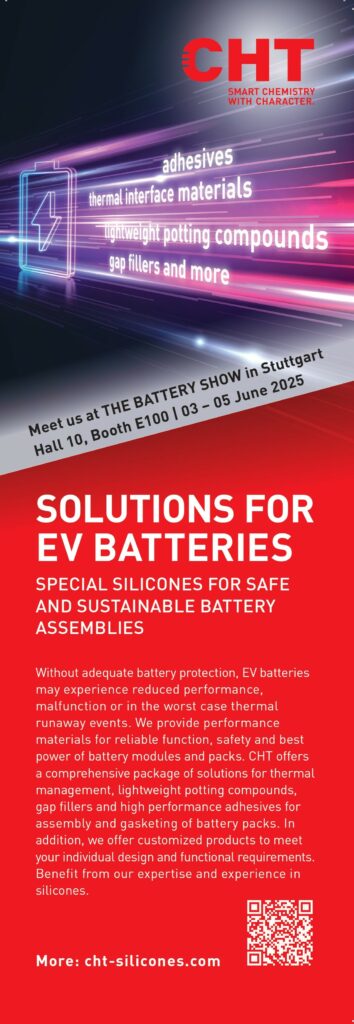
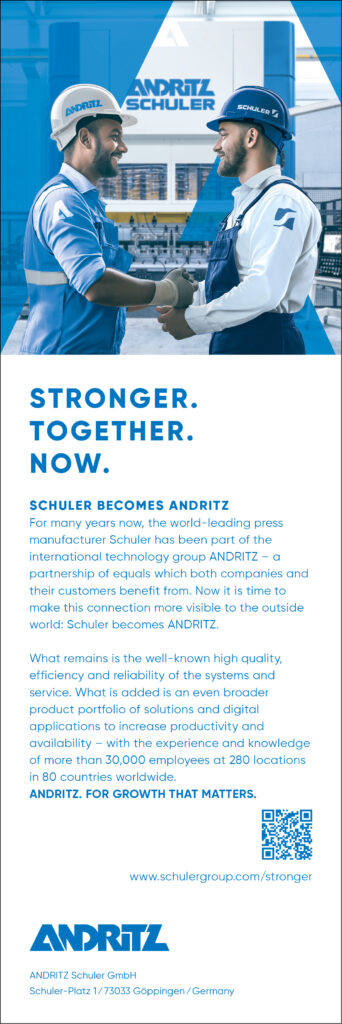
Advanced lamination and coatings
Interlocking electrical steel sheets by means of clinching can impair the magnetic properties of the motor by damaging the insulation between the sheets and the electrical steel itself. As an alternative, adhesive can be applied to the raw material before punching. The lamination stacks are then created by pressing the electrical sheets together, leaving the insulation undamaged. However, applying adhesive inside the punching tool can lead to a lower output rate and might be effective only in certain areas.
Insulation coatings applied to electrical steel laminations play a crucial role in reducing eddy current losses and improving overall motor efficiency. By electrically isolating the individual laminations, these coatings prevent the flow of large inter-laminar eddy currents within the steel core.
Focusing on thermoplastic insulation, a key area for efficiency gains, current manufacturing equipment is compatible with thermoplastic films for slot liners and wire coatings, despite their lower thicknesses, which eases adoption because no major investment is required.
Beyond eddy current reduction, certain coatings, particularly self-bonding varnishes (face-bonding), offer additional benefits such as improved acoustic performance through vibration damping, enhanced stack stability by bonding the laminations together and the elimination of point contacts that could lead to short circuits. Furthermore, media-tight stacks achieved through adhesive bonding can facilitate more efficient cooling by preventing the escape of cooling media. The higher thermal conductivity of some bonding varnishes also contributes to heat dissipation.
The self-bonding process (Backlack), for example, offers a comprehensive solution. In application of this technique, the electrical sheets are joined together to form a stack under pressure and temperature in a baking station. This creates face bonding, which not only enhances the structural integrity of the stack, thereby reducing vibrations and noise during motor operation, but also results in denser layering of the sheets. Furthermore, because the thermal conductivity of bonding varnish is higher than that of air, it is easier for heat to be removed from the motor core.
Two-layer stamping represents another emerging technology aimed at addressing the challenges of joining thin laminations. Instead of stamping a single layer of the lamination with all its features (such as the outer shape, slots and holes) in one process through a series of dye stations, two-layer stamping involves simultaneously processing two layers of the electrical steel sheet in certain stages of the progressive dye. Likely advantages of this process include higher production efficiency and throughput, unit cost reduction, and (potentially) better stacking accuracy and material savings.
Other manufacturing innovations are also crucial for effective application of advanced materials. One of these is the drive toward reducing overall material usage, which inherently shortens cycle times by minimising the number of processing steps. For stator windings, the integration of meter mix dispensing and curing systems for end winding potting offers a streamlined approach, particularly when considered early in the design phase, and it can enhance thermal management and electrical insulation.
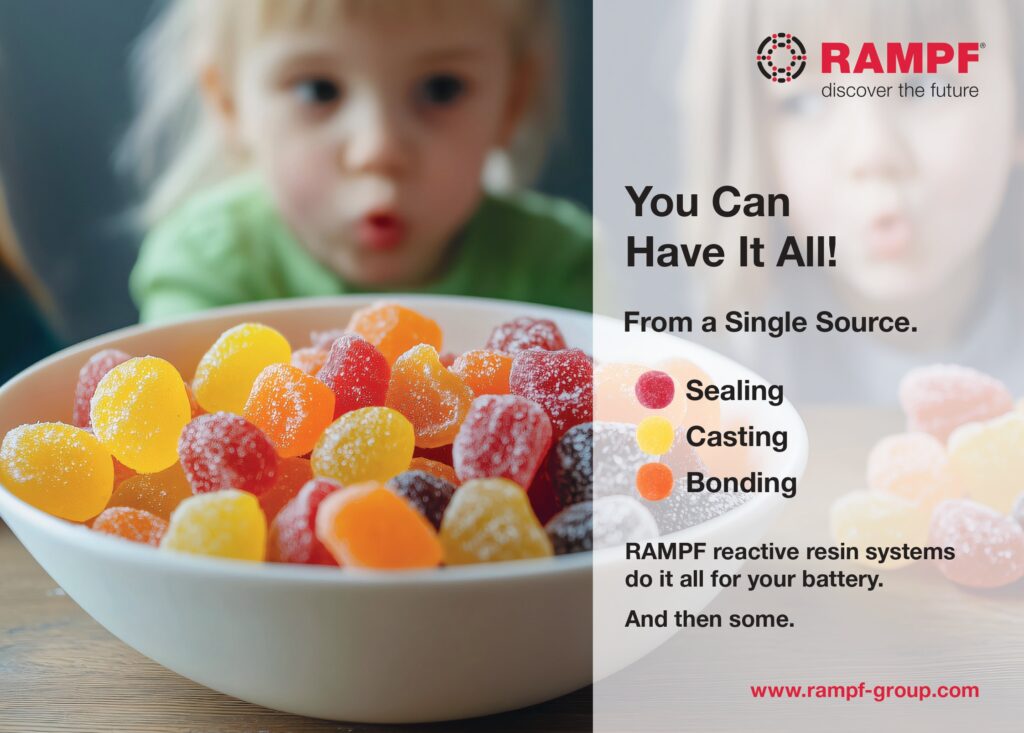
Winding materials
For windings, copper provides better conductivity than alternatives such as aluminium, but it is both heavier and more expensive. Because aluminium conductors have to be larger in cross section than copper ones sized to carry the same maximum current, copper conductors tend to be more compact for a given performance. Development effort is going into increasing the conductivity of aluminium alloys to make them better substitutes for copper. While superconductors offer even higher conductivity, they must be maintained at very low temperatures, which is impractical for most e-mobility applications in the near term.
Where weight and cost are high priorities in motor design, aluminium alloys with high conductivity are increasingly attractive. Examples include the high-purity 1xxx series materials such as 1050 and 1350, which have an aluminium content of 99% or more. In addition to conductivity that is typically 61% of the International Annealed Copper Standard (IACS), they also offer good corrosion resistance and high ductility, but relatively low mechanical strength.
The aluminium-magnesium-silicon alloys of the 6xxx series, such as 6101 and 6061, offer moderate conductivity of 40% to 50% of the IACS plus good mechanical strength through heat treatment and good resistance to corrosion. The more diverse 8xxx series includes some alloys tailored specifically for electrical conductivity, such as 8006 and 8011. While the conductivity is lower than that of the 1xxx alloys, they offer a useful combination of formability and strength.
Beyond these alloys, ongoing r&d efforts are exploring advanced techniques to improve the conductivity of aluminium alloys, more of which later.
Insulation materials for windings are another key area for r&d, with advanced thermoplastics providing alternatives to enamels, for example. Enhancements to wire enamels show marginal impact on insulation thickness compared with thermoplastic extruded solutions, which offer around 20% thickness reduction while maintaining superior properties after ageing (such as partial discharge inception voltage; PDIV). While polyimide, polyester-imide, and polyurethane-based wire enamels differ, all tend to lose thickness during ageing, degrading both the PDIV and the overall performance. Conversely, thermoplastic solutions demonstrate minimal performance drop, as highlighted in IEC 6000-34-21/41.
Nanotechnology-based coatings and fillers in wire enamels show improved partial discharge resistance but still fall significantly short of automotive industry corona resistance requirements, which currently favour PD-free designs. These fillers can also introduce unacceptable brittleness.
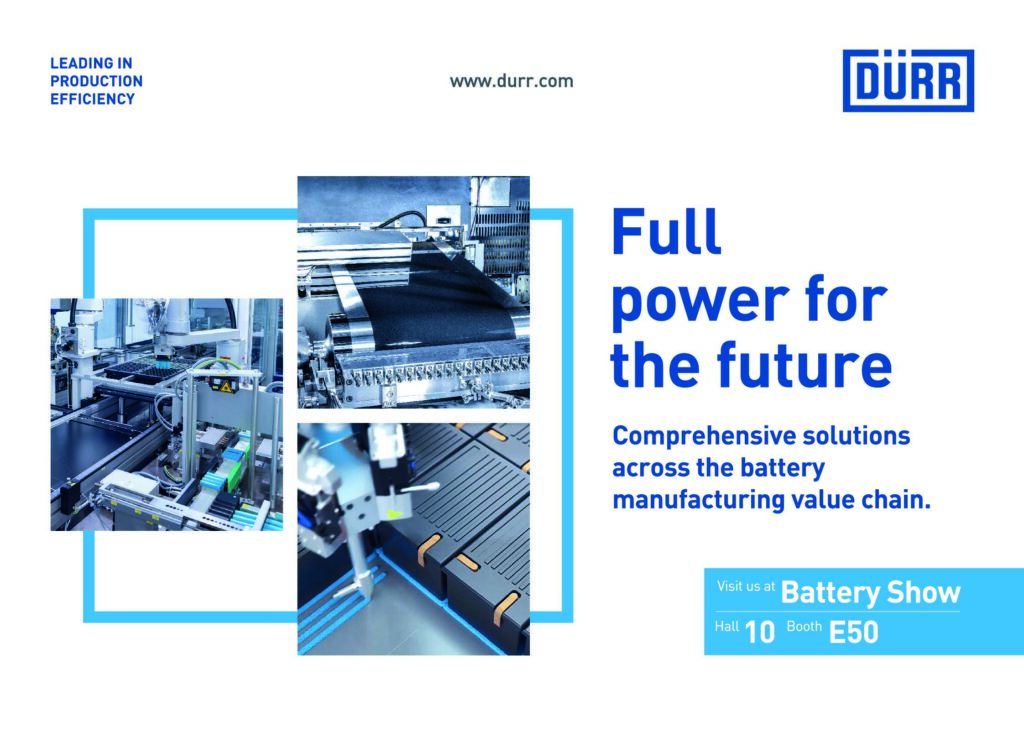
Ceramic bearings
Despite their extra cost, ceramic bearings are attractive for premium and high-performance EVs, for example, where every fraction of a percent in terms of efficiency and reduction in parasitic losses contributes to extended range and overall driving experience. Here, ceramic bearings are used in traction motors, where their lower friction reduces energy consumption and heat generation, while their ability to withstand higher speeds supports high power outputs.
Motors used in electric racing and high-performance road-going motorcycles often run at extremely high rotational speeds, evidencing how the enhanced stiffness of ceramic bearings enables more precise rotor dynamics.
The reduced friction and increased durability of ceramic bearings can also benefit high-end e-bikes with powerful mid-drive motors, particularly in demanding off-road or high-speed applications.
Additionally, the characteristics of low weight and high-temperature capability make ceramic bearings very attractive for eVTOL and electric fixed-wing aircraft, which are particularly sensitive to both weight and heat.
Finally, EVs of many kinds often have auxiliary motors for various functions such as cooling pumps, compressors for air conditioning and power steering. In applications where these auxiliary motors operate at high speeds for extended periods, ceramic bearings can improve their efficiency and lifespan.
Bearing material options
Several types of ceramics are employed in bearings, each offering a specific set of properties. Silicon nitride (Si₃N₄), which is the ceramic used most commonly for high-performance bearings, combines high hardness, a high strength-to-weight ratio, good wear resistance, a low coefficient of friction, stability at high temperatures, and good resistance to corrosion and other types of chemical attack. Silicon nitride bearings can operate with minimal or no lubrication in certain applications.
Zirconia (ZrO₂) is endowed with high strength and toughness, together with robust resistance to wear. While generally not as hard as silicon nitride, it is better at resisting crack propagation. Zirconia bearings tend to be chosen for applications in which high load-carrying capacity and resistance to impact are important characteristics. Partially stabilised zirconia (PSZ) is a variant in common use.
Alumina (Al₂O₃), which is significantly less expensive than either silicon nitride or zirconia, offers good hardness and wear resistance but lower strength and fracture toughness. Alumina bearings are typically used in less demanding applications where cost is a primary concern and extreme speeds or loads are not encountered.
The fourth key ceramic material for e-motor bearings is SiC, which boasts exceptional hardness, high-temperature strength, and excellent wear and corrosion resistance. However, it is generally more brittle and more difficult to manufacture into complex shapes compared with silicon nitride.
Another option is hybrid bearings, which consist of ceramic rolling elements (balls or rollers) running in steel races. This combination takes advantage of the low friction and wear resistance of the ceramic elements while potentially reducing the overall cost compared with all-ceramic bearings. In hybrid bearings, it is crucial that the steel races be of high quality and appropriately hardened to match the performance characteristics of the balls or rollers.
Working with meramics
Implementation of ceramic materials presents several unique design, integration and manufacturing challenges. Their hardness makes them difficult to machine to the extremely tight tolerances required for high-precision bearings. Thus, specialised grinding and lapping processes are necessary, which can be time-consuming and costly procedures.
Ceramics are generally more brittle than steel and they can be susceptible to damage from sudden impacts or excessive loads. Therefore, motor designers must carefully consider potential shock loads on the bearings and implement mitigating measures such as flexible couplings or vibration damping elements.
The interface between ceramic bearings and the shaft and housing also requires careful design. Differences in thermal expansion coefficients between the ceramic and metallic parts must be considered to prevent excessive stresses or loosening at different operating temperatures. Consequently, specialised mounting techniques and interference fits might be necessary.
Although some ceramic bearings can operate with minimal or even no lubrication, others might still require specialised lubricants, particularly for operation at very high speeds or under high loads, and those lubricants must be compatible with both the ceramic material and the operating environment.
Producing high volumes of ceramic bearings with consistent quality and tight tolerances can be challenging. Scaling up manufacturing processes requires significant investment in specialised equipment and expertise.
Ensuring the quality and integrity of ceramic bearings requires sophisticated inspection techniques to detect microscopic flaws or cracks that could lead to premature failure, for which non-destructive testing methods such as ultrasonic testing or dye penetrant inspection may be employed.
Despite these challenges, the performance advantages offered by ceramic bearings in specific e-mobility applications continue to drive research and development in this area. Advances in ceramic material science, manufacturing techniques, and cost reduction strategies are likely to expand their adoption in the near future.
Emerging materials
Several materials and technologies that hold significant promise are emerging for future e-motor development. In the realm of adhesives, advances in materials for stack lamination, magnet bonding, thermally conductive potting compounds and easy-to-reopen liquid gasketing materials are crucial for improving motor performance, durability and ease of service.
Clearly, rare earth permanent magnets are likely to remain central to achieving high-efficiency motors in the short-to-medium term, and ongoing research continues to focus on reducing the reliance on heavy rare earth elements like dysprosium and terbium, which are essential for high-temperature stability. Grain boundary diffusion treated magnets represent a significant step in this direction, achieving comparable temperature stability with significantly lower heavy rare earth content.
In the domain of electrical steel, post-annealable grades of steel offer the advantage of high strength in the as-delivered condition while achieving excellent magnetic properties after a final annealing step performed by the customer. Furthermore, stress-relief annealing techniques are vital for mitigating material damage induced by punching or cutting processes, thereby preserving the magnetic performance of the laminations.
Advanced techniques under investigation to increase aluminium’s conductivity include those characterised as severe plastic deformation. Methods such as equal channel angular pressing and high-pressure torsion can refine the metal’s grain size down to the nanometre scale, creating a nano-crystalline grain structure that facilitates easier current flow.
Research suggests that adding small amounts of elements such as cerium and lanthanum can improve the conductivity of aluminium by modifying its electron band structure and reducing impurities. Another approach, involving the incorporation of carbon nanotubes into aluminium, results in a composite material containing highly conductive pathways, significantly increasing overall conductivity and strength. Finally, studies are exploring specific low-alloy compositions (such as Al-Fe-Si, Al-Mg-Si, Al-Fe-Cu with boron treatment and grain refinement) that show promising improvements in terms of electrical conductivity, approaching or even exceeding 60% of the IACS while maintaining reasonable mechanical properties.
Even with these advanced materials, the trade-offs between conductivity, mechanical strength, thermal properties, and cost will continue to shape the adoption of aluminium in motor windings for e-mobility applications.
Thermally conductive potting for end windings is another promising technology. By effectively dissipating heat from the motor windings, it enables the design of smaller motors with higher power output and improved durability.
The development of bonding varnishes and Backlack coatings with enhanced thermal conductivity also contributes significantly to improved thermal management within the motor core. In the longer term, superconducting materials developed to work at higher temperatures could be practical for e-mobility applications, offering significantly reduced resistive losses in windings.
The constant push toward higher efficiencies to achieve cheaper, more sustainable vehicles with longer range (or the same range with smaller batteries) is an overriding industry trend. The shift toward 800 V and SiC technologies has increased interest in thermoplastic materials with higher PDIV and breakdown voltage per thickness. However, the benefits of thinner, mechanically robust thermoplastic films are also evident in 400 V systems, allowing for miniaturisation and reduced material usage.
One of the most critical aspects for sustainability is reducing raw material use while maintaining performance. More efficient designs, enabled by materials like thinner, high-performing insulation, allow for miniaturisation, leading to a lower carbon footprint for both the e-motor (potentially a 10% reduction) and the battery pack (1–2% reduction).
Balancing cost, performance and sustainability
Increasingly, engineers must consider the environmental impact of their material choices throughout the motor’s life cycle from extraction to disposal. Of the materials used in motors, rare earth magnets are arguably the most problematic in this respect because of the impacts associated with their mining and processing. Sustainable sourcing, recycling and, where practical, material substitution come to the fore here. This also affects design as much as material selection priorities because motors must be easy to disassemble for recycling.
The selection of materials for e-motors in the coming 5–10 years will be increasingly influenced by the evolving interplay between performance, cost and sustainability. In many cases, these goals are mutually reinforcing.
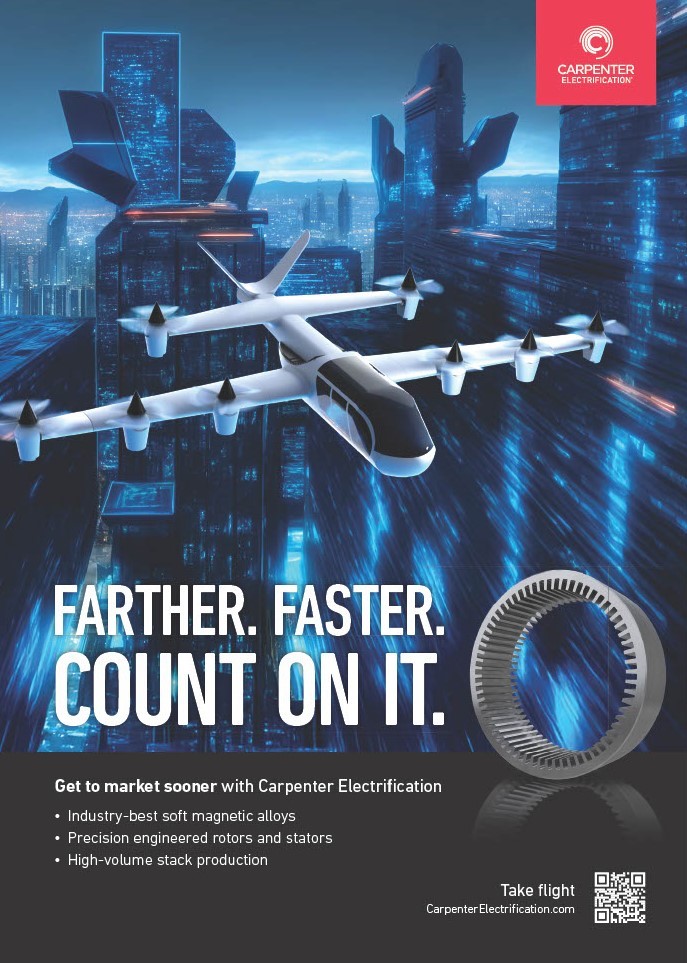
Acknowledgements
The author would like to thank the following for their help with this article: Wolfgang Schumann, e-mobility product manager at ANDRITZ Schuler; Matthias Brachmann, e-mobility business development manager at Henkel; Alexander Buckow, co-head Heraeus Remloy; Eric Wyman, business development manager, and Dan Barber, application engineer, at Parker Lord; Luigi Marino, global marketing manager at Syensqo; and Roman Sonnleitner. product manager at Voestalpine.
Some suppliers of motor materials
Andritz Schuler
Arnold Magnetics
Aurubis
Axalta
Carpenter Technologies
Electron Energy Corporation
Henkel
Heraeus Remloy
Nippon Steel
O‘Keefe Ceramics
Parker Lord
Syensqo
Vacuumschmelze
Voestalpine
Click here to read the latest issue of E-Mobility Engineering.
ONLINE PARTNERS
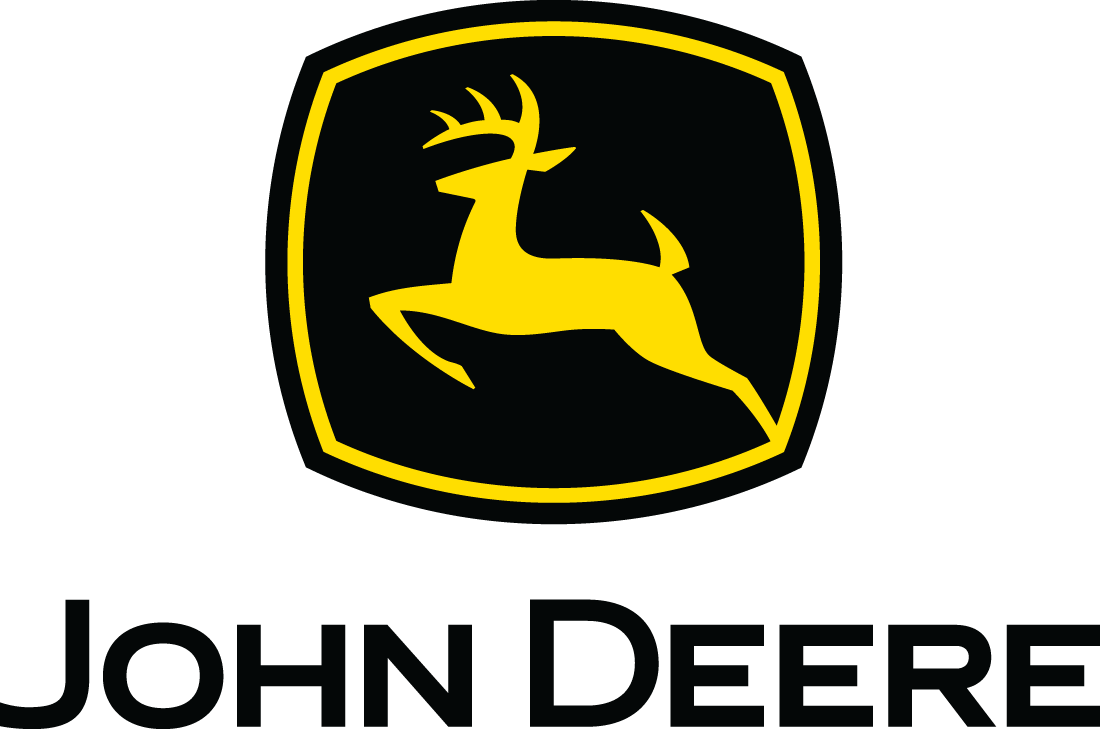
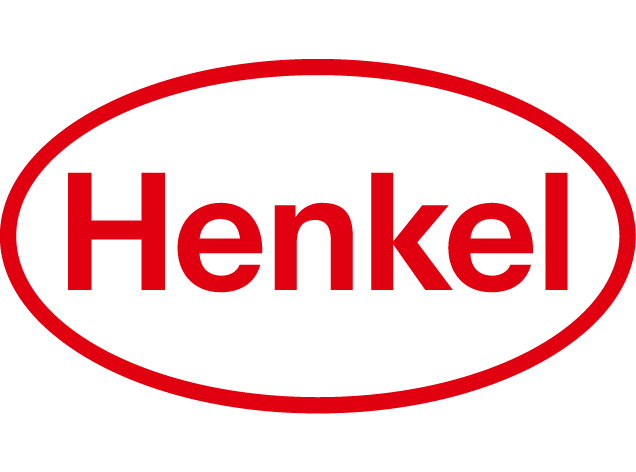
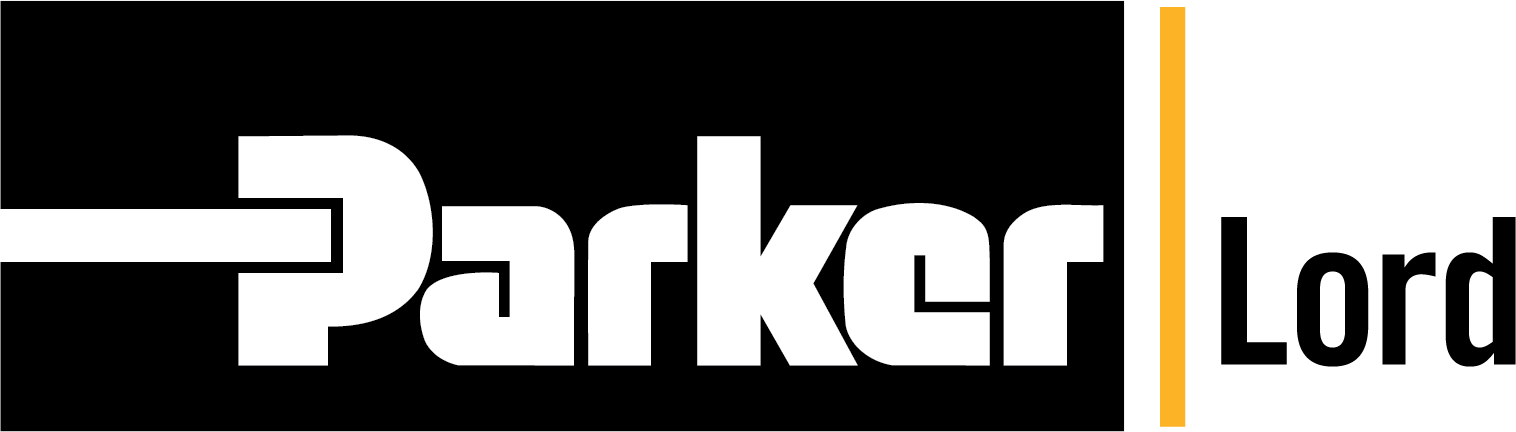
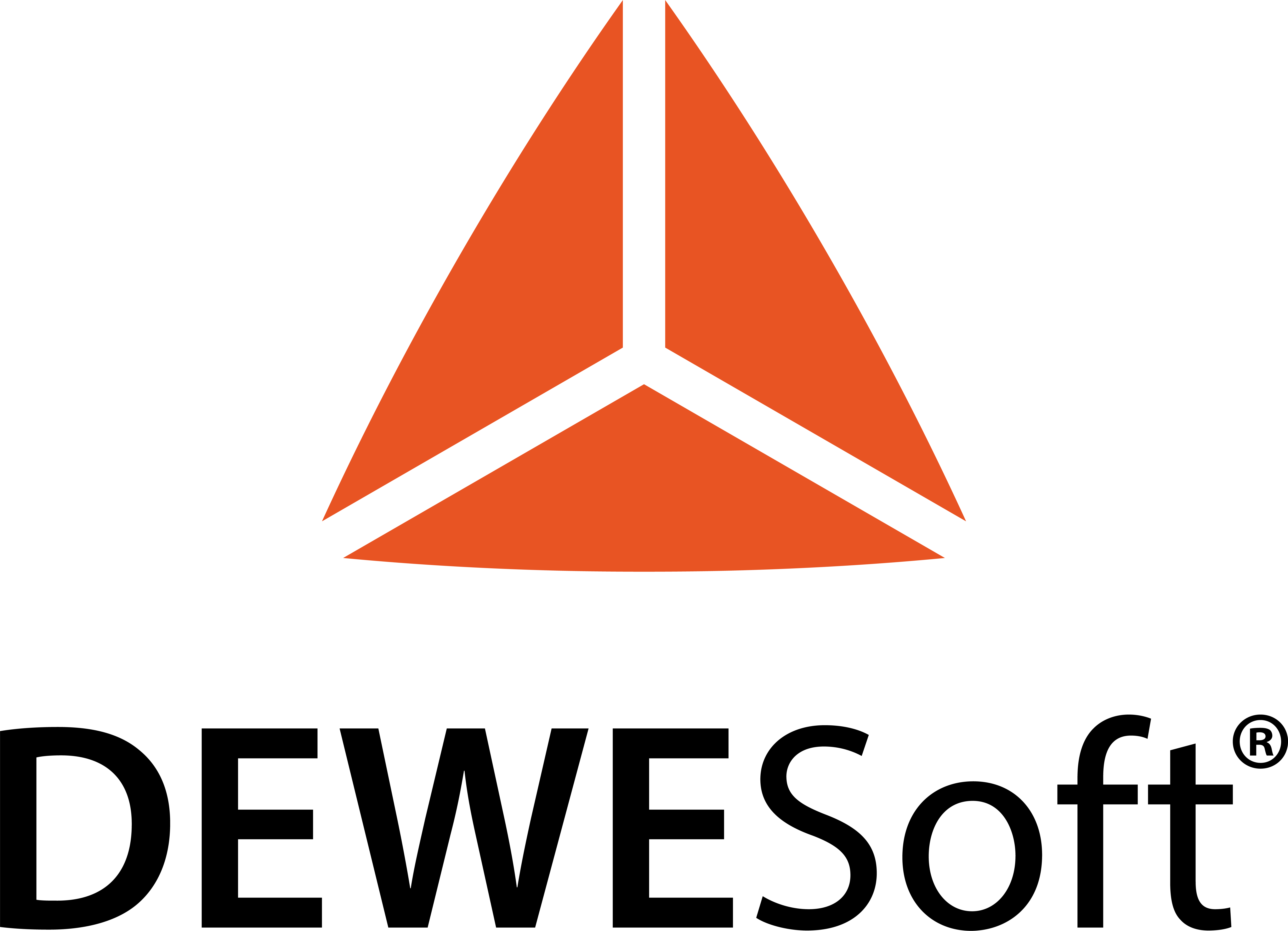
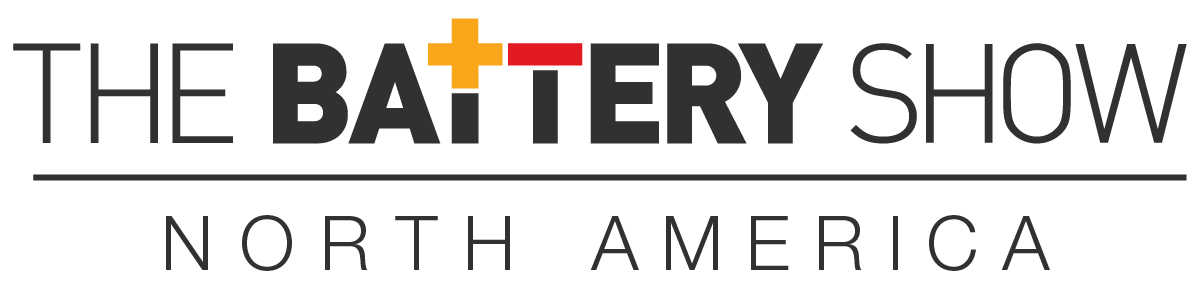
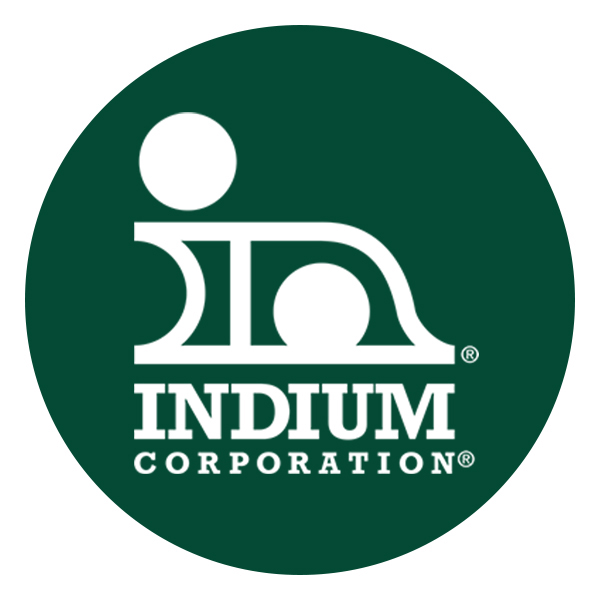
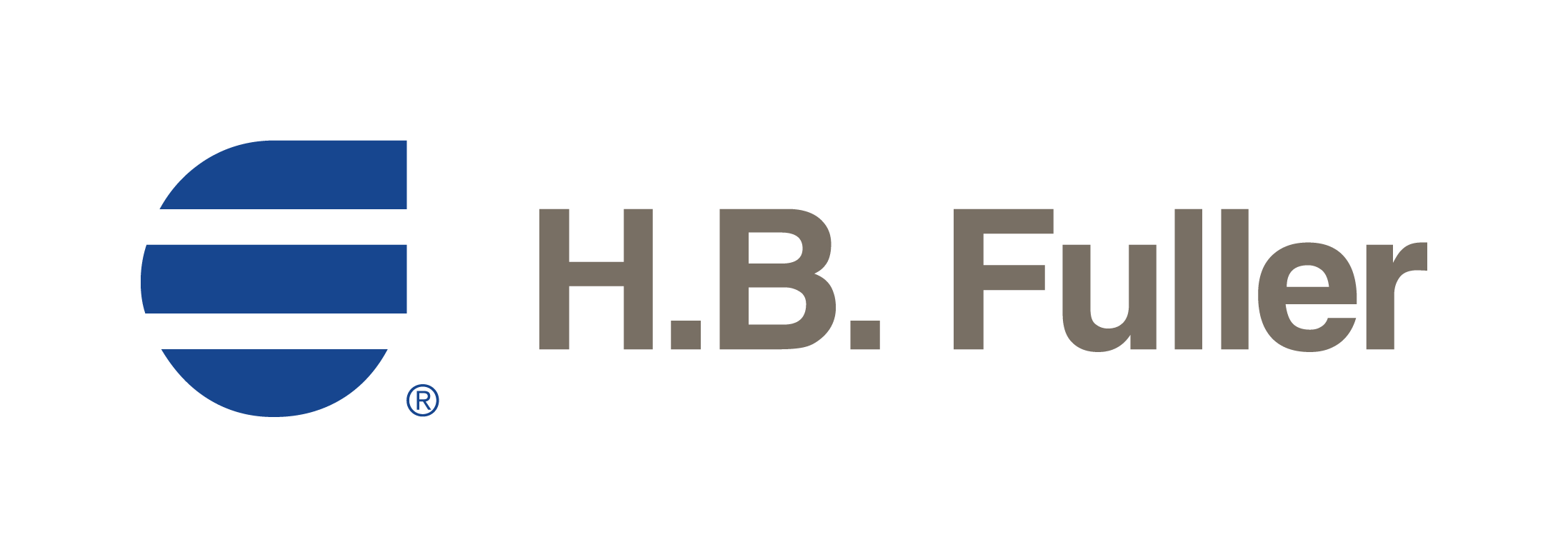
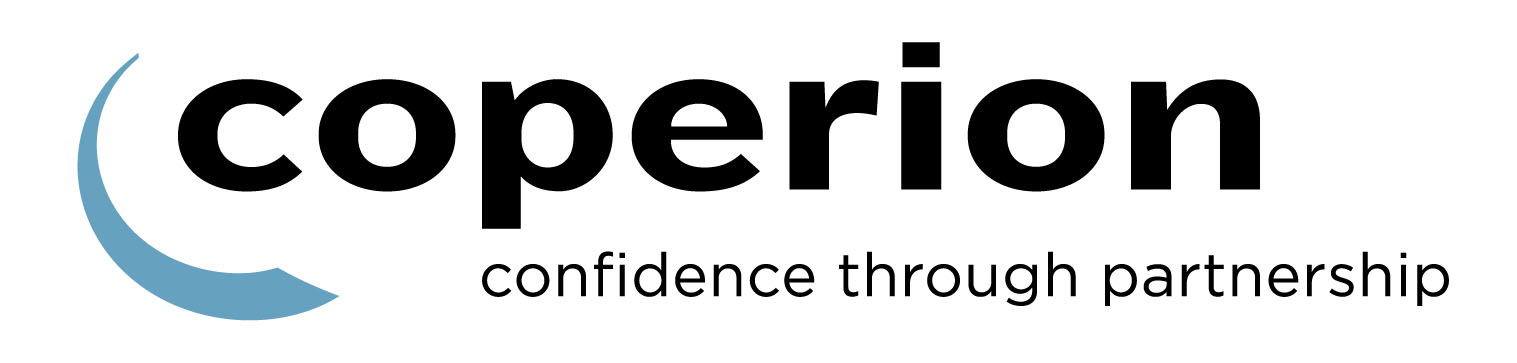