In conversation: Michael Fischer
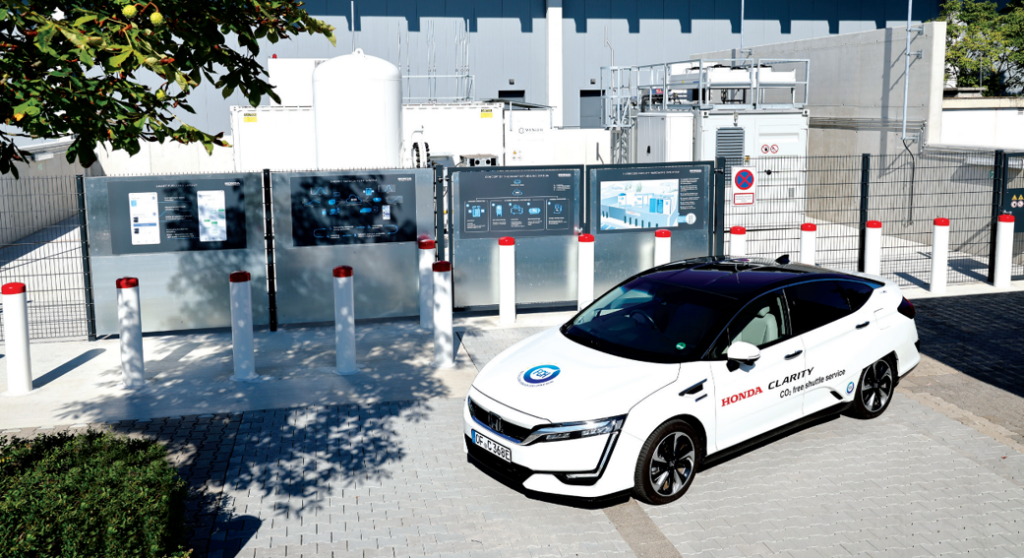
infrastructure, all aimed at making EVs more sustainable and useful for consumers
(All images courtesy of Honda R&D Europe)
Recharging communities
Honda R&D Europe’s deputy GM talks with Rory Jackson about changing where EVs stand relative to the environment, the grid and the home
A drive to understand how complex machines work can spur one towards a life of engineering and research across a diverse field of sciences, as Michael Fischer, deputy GM of Honda R&D Europe, has experienced.
Today, he directs a team of predominantly e-mobility engineers at the Honda R&D facility in Offenbach, Germany, but his teenage years were taken up by a love of internal combustion engines, and the sophisticated mechanics by which they transformed chemical energy into shaft horsepower for cars and motorbikes.
“Not long before I had to choose a university, and a degree discipline that my career and life path would follow, someone stole my motorbike,” Fischer recounts. “The police found it crashed into a small river, and in a really bad condition; the engine and electrics just didn’t work anymore. But I wanted to keep the bike, so that became my first big engineering project – disassembling the old powertrain, and then specifying and building a new one into the bike.”
After half a year or so, the bike was running again, and it had become clear to the young Fischer that mechanical engineering was his calling. He soon enrolled at the Technical University (TU) of Darmstadt, beginning with fundamental mathematics and physics, and soon moving onto applied projects involving thermodynamics, mechanics and other specialist subjects.
“A position soon opened at Honda R&D Europe, and because they work from a small but innovative research centre, with a very wide and open remit for developing new technologies, it was exactly what I’d been hoping for,” Fischer recounts.
The position in question was as a research engineer for automotive powertrains, including more of the Diesel aftertreatment r&d that had captured Fischer’s interest at TU Darmstadt, but also Honda’s work in battery- and hybrid-electric powertrains, which by 2006 was already well under way.
“By then, I had a dream target that I called ‘air in, air out’,” he muses. “I wanted what came out of cars’ tailpipes to have as little harmful emissions as the stuff going in. Literal zero-emission is challenging, but some use the term ‘zero-impact emissions’, meaning a powertrain that does no harm to the environment.”
This led to a range of research directions, including particle filters for gasoline engines, or new, selective catalytic reduction (SCR) and lean NOx catalyst (LNC) solutions, aimed at NOx aftertreatments for both gasoline and diesel engines.
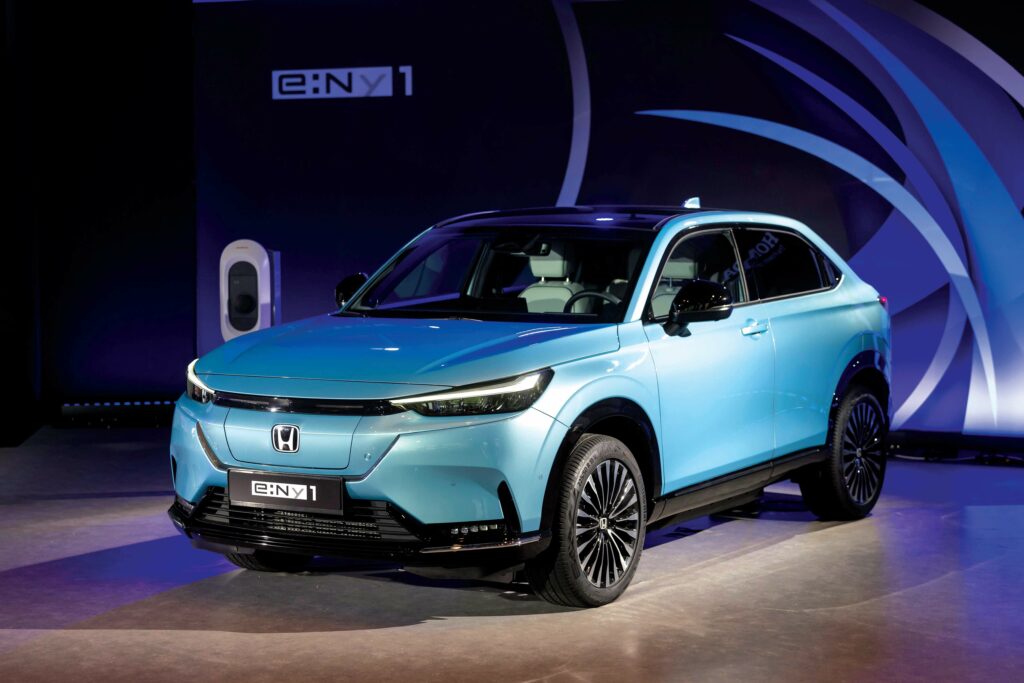
enable smart home energy allocation or P2P energy trading
AI for cleaner powertrains
Before long, Fischer’s scope expanded to include new forms of software-defined solutions for directly reducing emissions during the combustion process.
“For instance, I soon took on some projects evaluating the use of artificial neural networks for engine control, as well as aftertreatment control. Some key objectives were to intelligently estimate NOx emissions being produced by engines, and to control the exhaust gas-recirculation rate and NOx aftertreatment systems to reduce them most effectively,” he recounts.
“Those projects have been highly scientific, and that’s why I decided to do my PhD thesis on neural networks for transient NOx estimation, all outside of work hours, but using project results from my research at Honda.”
In that PhD, Fischer used a self-organising map – a type of artificial neural network (ANN) trained using unsupervised learning – to produce virtual sensors capable of closely estimating transient NOx emissions, based on sensor signals commonly available in mass-production engines (specifically engine speed, injected fuel mass, Lambda, mass air flow, boost pressure and exhaust-gas temperature).
Estimations were performed using local linear functions, and their quality showed they could replace an engine-out NOx sensor, making for potentially significant cost advantages to powertrains incorporating such technology into their control software.
“We developed advanced control strategies, and elaborated on how those could be applied in hybrid cars, especially in optimising fuel consumption as engines could be run independently of traction requirements – for me, that was the big leap into e-mobility. Honda already had great experience in hybrid powertrains and then it accelerated for everyone following the ‘Dieselgate’ emissions scandal a couple of years later.”
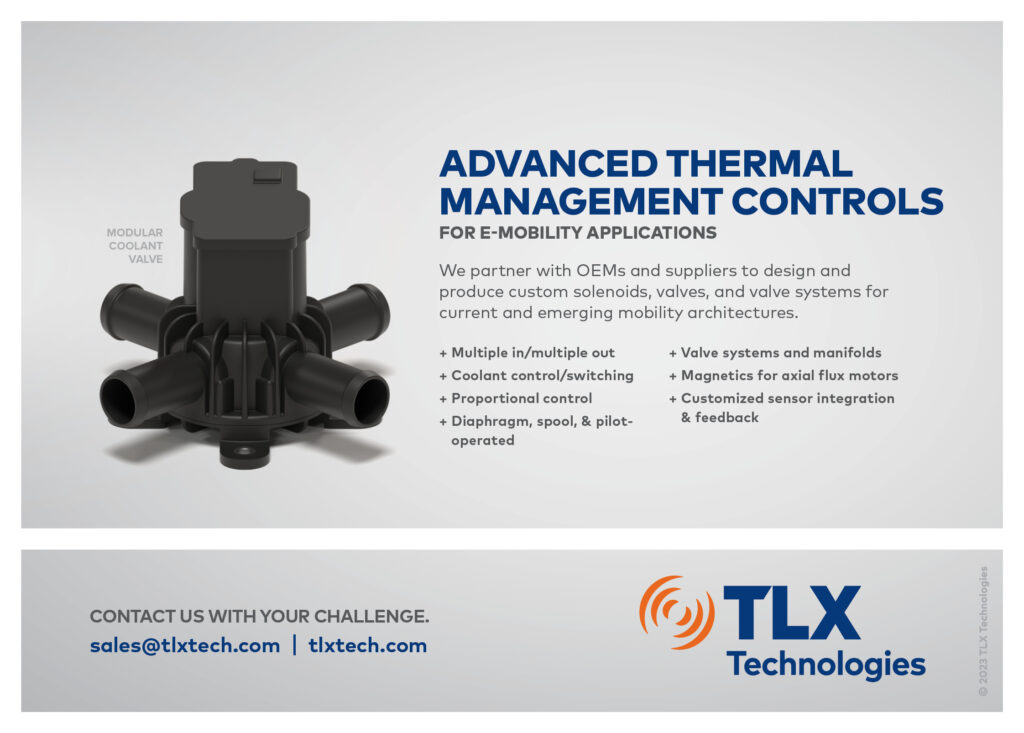
Circularity with three points
Through such experiences, Fischer now steers Honda R&D Europe’s Energy & Automobile division with a three-pronged approach to sustainability targets, combining mechanical engineering, materials science and digitalisation.
“Digitalisation in particular is a huge buzzword, but we really do try and keep track of how software can help us make mobility a more sustainable world,” he says. “Take, for example, the target of resource circulation. One primarily views this as a material challenge: what kinds of materials are you using in, say, batteries, where are you extracting them from, how can you avoid materials that are environmentally harmful or difficult to harvest?
“But there’s also a strong digital component: through software databases, we can track each of those parameters at each stage of a product’s lifecycle. We can track and verify that the companies in charge of material extraction are doing so through sustainable and humane practices.”
Additionally, Honda R&D aims to make sure such data cannot be defrauded or cheated, to ensure components that are developed for production are genuinely sustainable from life to end-of-life, and not mere greenwashing.
This has spurred considerable focus by Fischer and his team into blockchain. As blockchain-powered ledgers cannot be modified, and are inherently cyber secure, blockchain or similar approaches show immense potential for digital solutions on the traceability of goods and energy.
EVs as home devices
As EVs become increasingly software-defined, there are growing suggestions that cars will one day be used as devices in a similar way to smartphones. Fischer cautions, however, against certain impracticalities of such statements.
“An excess of infotainment and personal information devices inside EV cabins can be a huge and unsafe distraction for drivers, certainly as long as we’re the ones doing the driving and not some self-driving autopilot system,” he says.
However, there is growing interest in many markets that there should be ways of using EVs and their great energy storing and charging capabilities to advantage in both mobility and home applications, particularly to minimise the amount of energy taken from the grid. To that end, Honda places a lot of focus on energy and charging intelligence, which Fischer points to as being one of the most undervalued and underrepresented topics in discussions about e-mobility engineering.
“On the one hand, I think EVs are always going to be more expensive than combustion cars of a similar size. That’s almost guaranteed by function of putting a large battery pack into a car, but smartphones cost far more than house phones, and everyone still owns one, because they enable you to do much more than you could do before,” he notes.
“Imagine if EVs could be engineered with capabilities not only for driving but as a huge home energy storage system. They could soon form an integral part of how homeowners track and optimise their day-to-day energy usage.
“In the UK, for instance, we already have our e:PROGRESS solution – a time-of-use tariff to help customers recharge their EVs specifically when electricity is cheap. If the EV is then leveraged to charge devices all over their homes, you’ve made the EV a part of their life, 24 hours a day, just like their smartphone,” Fischer adds.
Such a concept could be extended to create ‘energy communities’ in the future, and Fischer gives the example of a homeowner with a PV roof. If such an individual is not at home to charge their own EV, and the PV roof stands to generate an electricity surplus that might otherwise go to waste, they could leverage a blockchain solution to engage in energy trading with their neighbour – essentially selling electricity to their neighbour’s EV in a P2P charging arrangement.
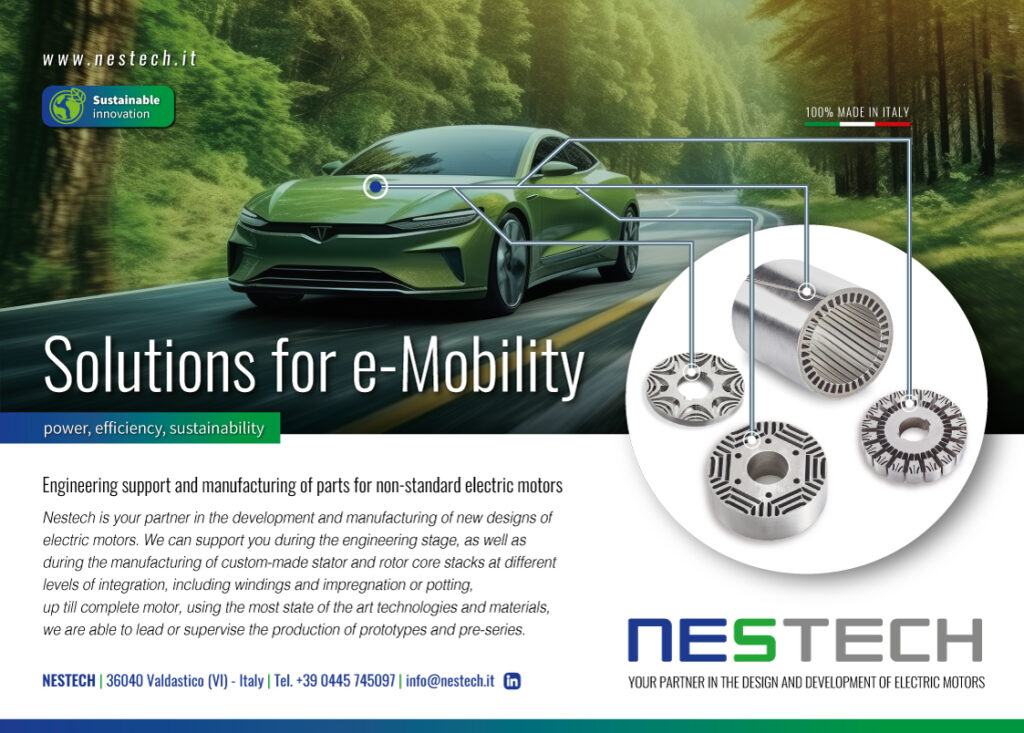
Charging forwards
With the creation of such communities in mind, V2G and bidirectional charging take up much of Honda’s European research within its focus on energy management and intelligent charging. This began in earnest in 2016, when Fischer and his team started installing a fast-charging system at their facility, using the Honda R&D Europe base as a testbed for how the energy flows from EV charger to building could be optimised.
These included installing 750 kW (peak) of rooftop solar cells, some Honda-designed bidirectional chargers, and a plethora of voltage and current sensors throughout the building to closely study energy flows.
The bidirectional charger is referred to in-house as Honda R&D’s ‘Power Manager’, and is a 10 kW DC system, developed based on ISO 15118-20 (the standard for EV-to-EVSE comms, although it had not been officially published at that time).
“We developed our charging manager – a hardware and software solution hidden behind the metre system – which controls the rates at which EVs charge, based on forecasts of weather and electricity consumption, as well as real-time measurements of energy flows across our facility. Key factors in its intelligence are parameters entered into the chargers by its users, including our own researchers, such as their target time for when they will leave, and how much SoC [state of charge] they want to have by that time,” Fischer says.
“The charging manager computer optimises all the EVs’ chargings, such that everyone gets their desired SoC on time, and prioritises the rooftop PV cells over the grid as the preferred energy source, while also minimising peak load in the system. Widespread deployments of such smart charging infrastructure will be critical in the future; national grids cannot presently withstand every road user charging an EV at once.”
Most work on developing the charging manager was software-related, falling into two categories: one was writing the algorithms necessary for intelligent control of charging loads and power draws; the other was optimising the communications links throughout the facility, between chargers, vehicles and other devices.
“The problem with ISO 15118-20 and other charging comms standards today is that their interpretation is often left up to individual engineers. Hence, industry often holds ‘plugfests’, which are great opportunities for charger manufacturers and automotive engineers to test and improve their systems’ interoperability, and to improve how standards are written to better guide network and comms engineers towards a clearly defined way of writing charging comms,” Fischer notes.
Through this EV charging system, Honda R&D Europe has qualified with its Honda e-fleet and bi-directional chargers to operate the frequency control reserve, a rapid and automatic response mechanism used by transmission-system operators to stabilise frequencies against sudden changes in electricity supply or demand, principally to keep grids stable.
Stress and power density
However, optimisation of EV charging raises questions over the increased degradation and stress that batteries suffer from repeated charging and discharging. “There is no ‘yes’ or ‘no’ answer to this question; it only depends on what you’re doing with the battery,” says Fischer. “Obviously, if you run it from 0% to 100% SoC and back over and over again each day, you’ll induce lithium dendrite build-ups and reduce your pack’s lifespan quite a bit.”
“With our frequency control reserve, we can control for very small SoC swings, even keeping packs in the sweet spot of 40-60%, which can have a positive effect on battery lifespans. But then most of your electronic components could be working 24/7 and suffering lifespan drops of their own because you’re managing the SoC too persistently. We’re accounting for that when researching new power electronics, ECUs and so on.”
For Fischer, the path forward certainly includes shifting r&d from focusing only on battery energy density and rerouting it towards power density, such that gradual improvements in charging infrastructure will make recharging passenger EVs as simple and time-efficient as refilling at petrol stations.
Further enablers for a smarter energy future will include the ability to make batteries from sustainable materials, improved thermal management strategies for mitigating cell temperature increases during charging, and advancements in battery engineering.
Here, Fischer cites cell-to-pack architectures as an efficient means of maximising energy density, but he cautions that recycling such packs could be extremely difficult without a straightforward disassembly method.
Zero-impact, infinite possibility
Fischer believes big challenges remain before battery recycling becomes a reality. Material selection is among the largest and makes for a significant source of trade-off. The more that rare materials such as nickel or manganese are used in cells, the more of a business case there is to recover and reuse such materials.
But their rare nature also drives the creation of batteries from more abundant, low-value materials, for which recycling and circularity would be far less easy to achieve via a profit motive.
“Batteries with only cheap and abundant materials – for example, sodium-based ones – could be a great path towards more sustainable and affordable packs one day, but regulations would be needed to make recycling of them mandatory and not lead to scrap hills of depleted packs,” he says.
Honda R&D Europe has recently extended its energy testbed with a 225 kW electrolyser and extensive hydrogen-storage infrastructure.
“We think hydrogen will play a huge role in future energy and mobility, even if hydrogen isn’t always necessary for passenger cars as batteries can satisfy most of their range requirements. There are so many vehicles and industries where hydrogen is important for decarbonisation that we shouldn’t view electric and hydrogen systems as separate. It is more correct to take a holistic view, optimising total energy efficiency and storage with whatever is the smartest solution,” Fischer says.
“For instance, on really sunny days, our PV cells will generate 750 kW, and the energy from that can’t all be stored in batteries alone. It makes much more sense to store it as hydrogen, which can be used to refuel FCEVs [fuel-cell EVs], H2 engine-powered vehicles or combined heat-and-power systems. And while those might be three different ways of applying hydrogen, again, we don’t view them too separately here at Honda when it comes to our research.
“There’s a reason we seat our virtual-simulation engineers next to our bench-testing engineers. Each can directly learn ways to improve their own software and tools from the other so long as they communicate well – much as is the case with our different hydrogen research teams, and of both hydrogen and battery EV developers.”
Michael Fischer
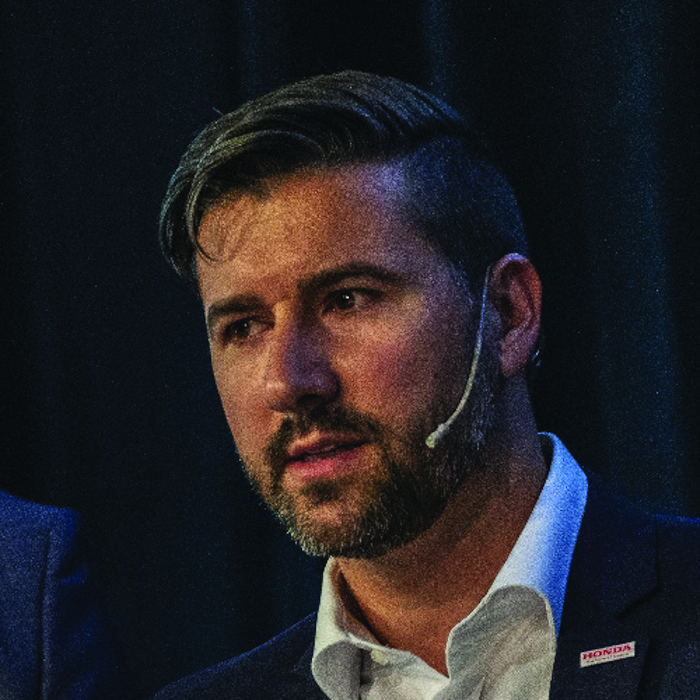
Michael Fischer was born and raised near Darmstadt in Hesse, Germany. After graduating secondary school in 1999, he performed one year of civil service before beginning a degree programme at the Technical University of Darmstadt in 2000.
He achieved a master’s diploma in engineering in 2006, and wrote his thesis (as part of a collaboration between Honda and TU Darmstadt) on how advanced NOx aftertreatment techniques could be applied to diesel passenger cars to effectively reduce harmful emissions.
That year, Fischer started working as a project leader (powertrain) at Honda R&D Europe, becoming section leader for powertrain technology in 2011, and achieving his doctorate in 2013.
Over the subsequent 10 years, he advanced through a number of managing roles across automotive engineering, materials research and digital solutions, directing growing teams of specialist researchers at the Honda R&D Europe facility in Hesse.
In April 2021, Fischer became deputy general manager for Honda R&D Europe’s Energy & Automobile division, a position he continues to hold to this day.
Honda R&D Europe’s facilities feature extensive smart charging, hydrogen and other infrastructure, all aimed at making EVs more sustainable and useful for consumers (All images courtesy of Honda R&D Europe)
Honda was already producing HEV cars and powertrains when Fischer started working at Honda R&D Europe in 2006
Through technology such as bidirectional charging, V2G and blockchain, future EVs (such as Honda’s new e/NY1) could enable smart home energy allocation or P2P energy trading.
Click here to read the latest issue of E-Mobility Engineering.
ONLINE PARTNERS
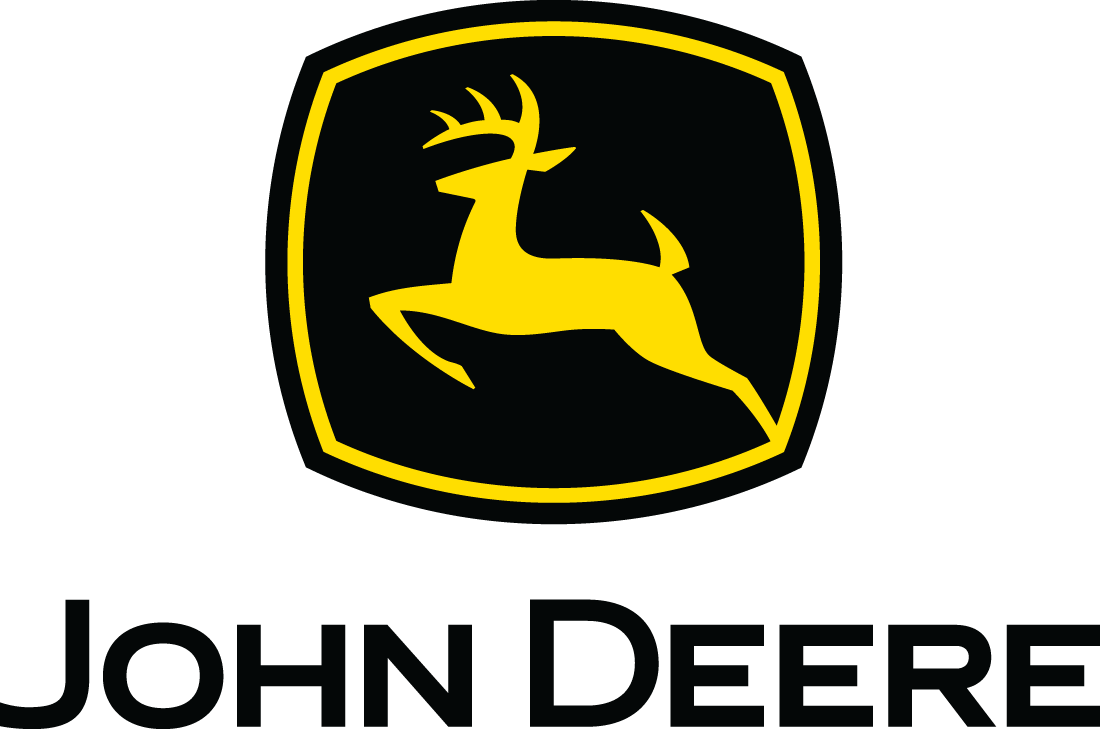
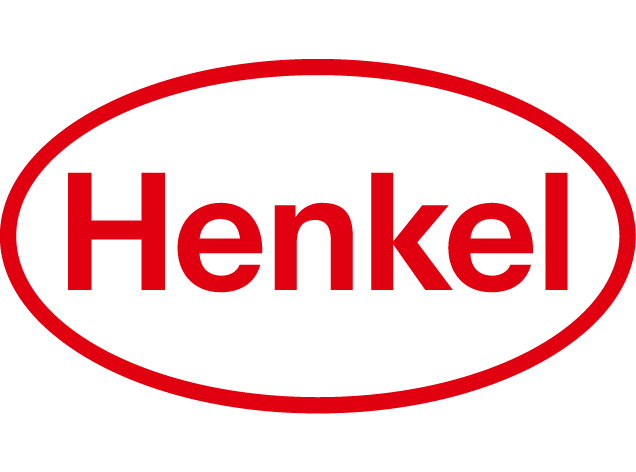
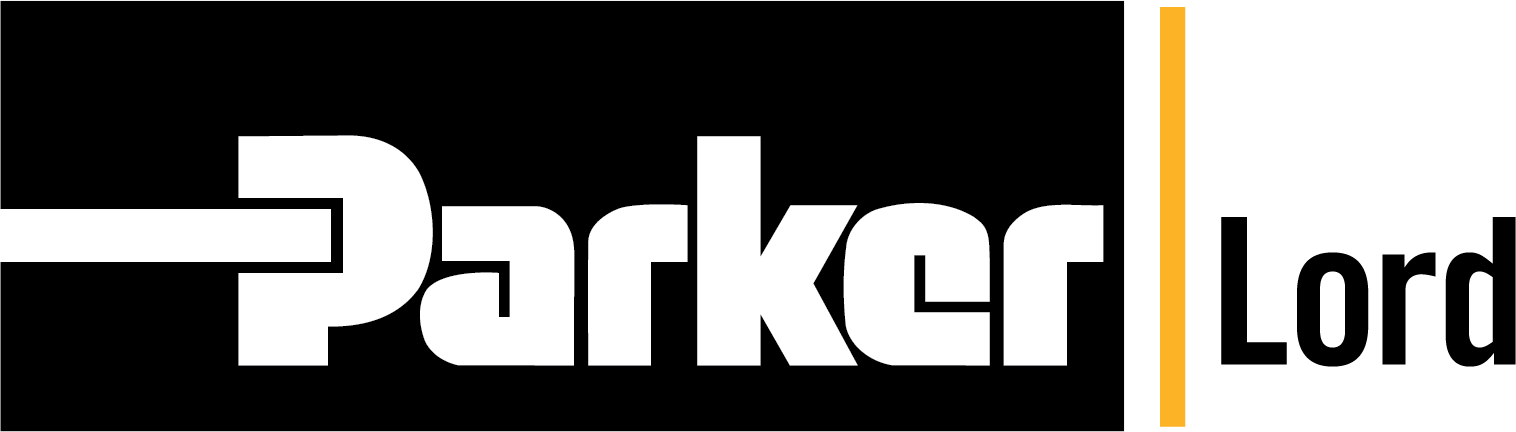
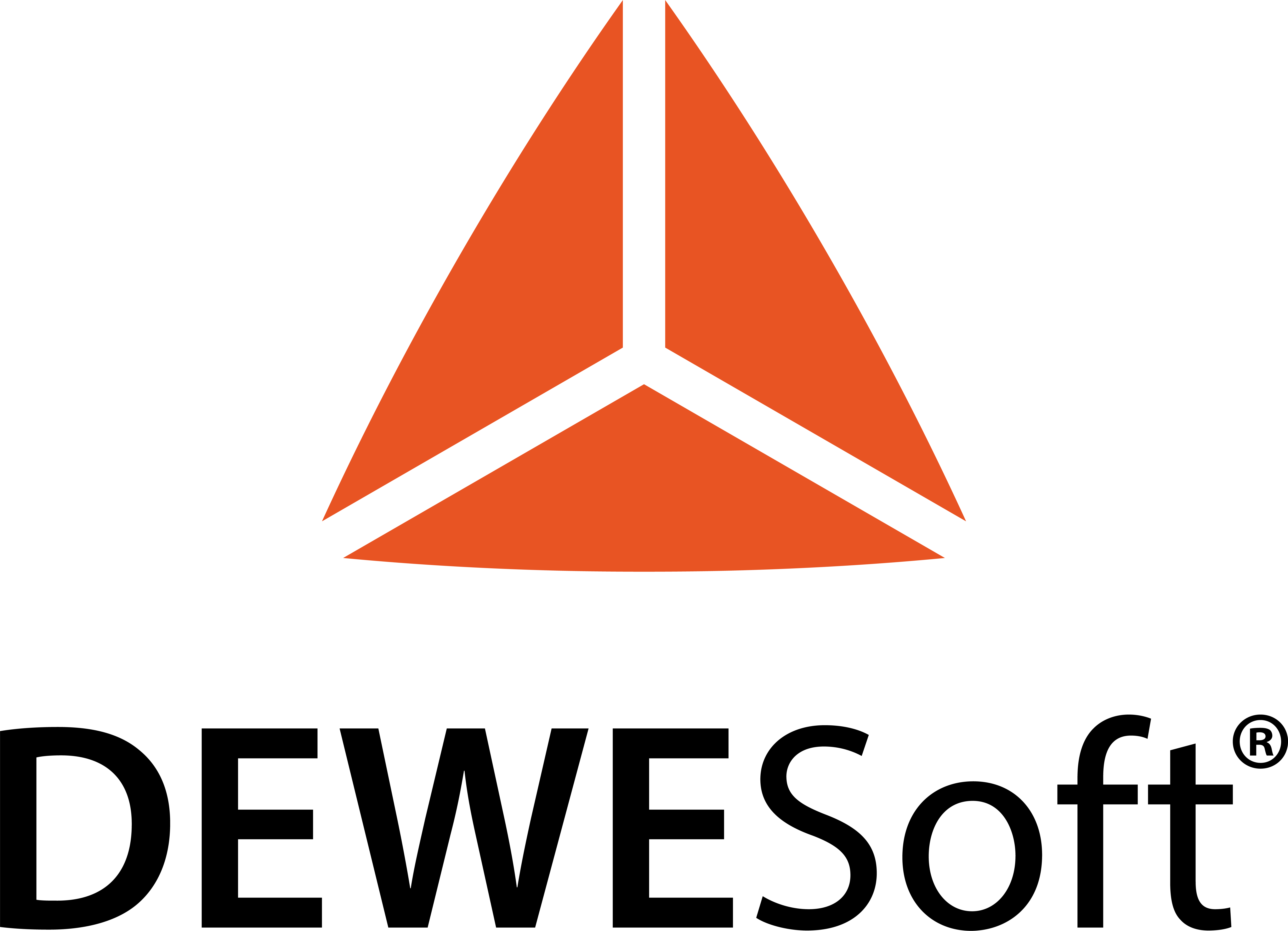
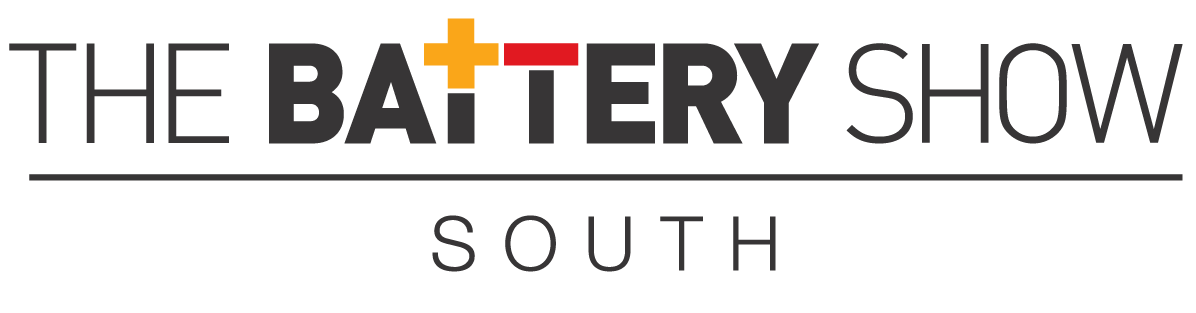
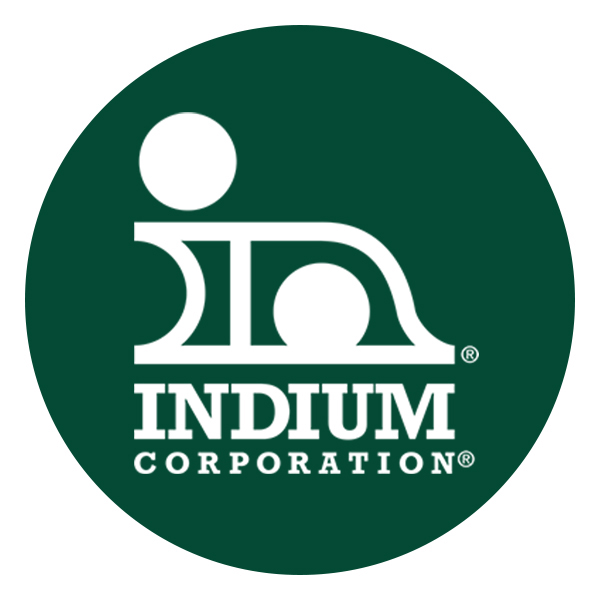
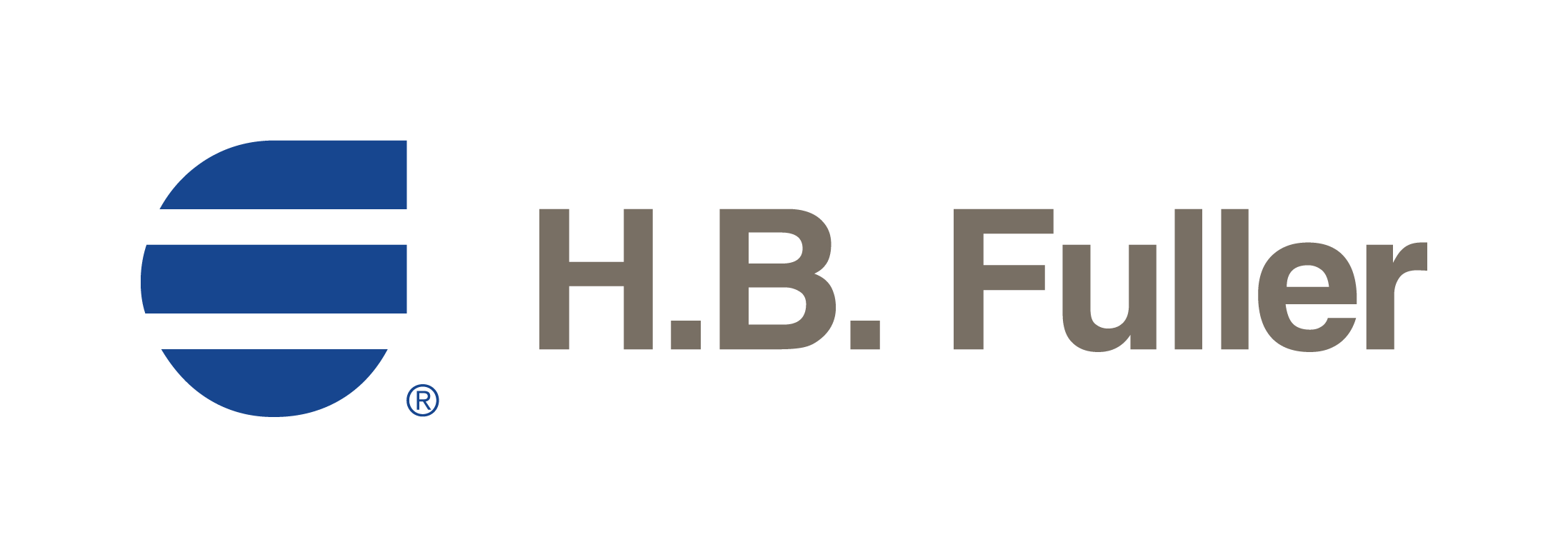