magniX magni350, 650 and magniDrive 100

Pilot programmes
Rory Jackson looks at how these electric powertrains and their inverter have been designed for crewed aircraft integrators
In every part of aerospace engineering, a race is on to break new ground and claim headline-grabbing milestones in sustainable aviation. While it might seem to some that commercial airliners are moving at a sluggish pace compared with the automotive world in reducing their harmful emissions, it is not out of a lack of interest in decarbonisation. Regulatory bodies need to scrutinise the safety of new technologies intensely before allowing their use for transporting hundreds of millions of passengers a year.
This need for safety means their approval of the use of biofuels and e-fuels for example in passenger jet powertrains has been glacially slow, compared with the rapid pace of innovation being achieved by new air-going e-mobility groups. Of those, and not counting the spate of (crewed as well as uncrewed) eVTOL aircraft manufacturers that have emerged in the past 5 years, very few (if any) of them are aiming at the mass international transport of people that generates so much of the world’s CO2 output.
Instead, a handful of SMEs are pioneering the case for eSTOL airliners that will one day become part of day-to-day life for anyone involved in commercial aviation, from private jets to large people carriers, and the industry’s attention has recently been drawn towards two successful test flights.
One is the first flight of Eviation’s all-electric Alice airplane; in addition to its 19.2 m wingspan and nine-passenger capacity, it is also notable for it being a clean-sheet design and battery-powered. The other is the first flight of Universal Hydrogen’s fuel cell-powered DHC8-Q300 aircraft, which with a 50-56 seating capacity typically and a 27.4 m wingspan, was the largest electrified aircraft to have flown at the time of writing.
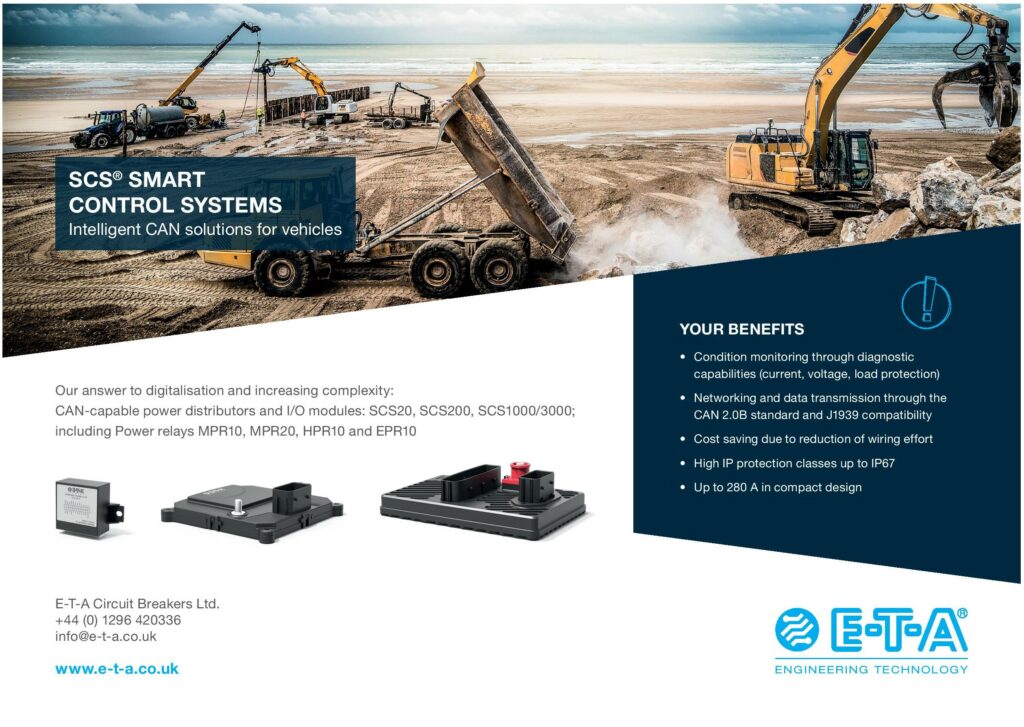
These two cases represent fundamentally different approaches in terms of energy technologies, but they share a common approach in power output. Both have chosen their electric motor and inverters from the same supplier, US-based magniX, one of the few companies manufacturing electric powertrains specifically for crewed aircraft integrators.
Its current offerings are the magni350 and magni650 EPUs (electric propulsion units). Each consists primarily of a permanent magnet synchronous AC motor and a set of motor inverters, as well as a constant-speed propeller mounted on the front of the motor and directly driven by the motor shaft, as well as an accessory gearbox for powering ancillary aircraft systems from the shaft.
The EPUs both operate on an 800 V AC supply from their inverters. The magni350 has a mass of 128 kg with all inverters and HV cables, and can output power continuously up to 350 kW, while the magni650 weighs 206 kg with cables and inverters and produces up to 700 kW.
For comparison, and for anyone seeking a benchmark against conventional aerospace powertrains, the standard-issue engine for the DHC8-Q300 is a Pratt & Whitney turboprop, either the PW123B or PW123E. The former has a dry weight of 450 kg and a maximum power of 1865 kW, while the latter weighs the same and produces up to 1775 kW.
That gives the PW turboprops a very slight advantage in power-to-weight ratio, one unlikely to be retained in the future, given the anticipated maturation of electric motor technologies. Meanwhile, the magni650 has an advantage in volumetric power density over the other three systems: the PW123B and PW123E both measure about 0.73 m3, compared to 0.2 m3 for the magni350 and 0.26 m3 for the magni650.
However, if decarbonisation and energy efficiency in aviation are the ultimate goals, then the EPUs win out by some measure. In battery and hydrogen-electric aircraft, they will generate no carbon emissions and consume no jet fuel, with any specific fuel consumption being limited to hybrid configurations and the IC engine being used as a range extender.
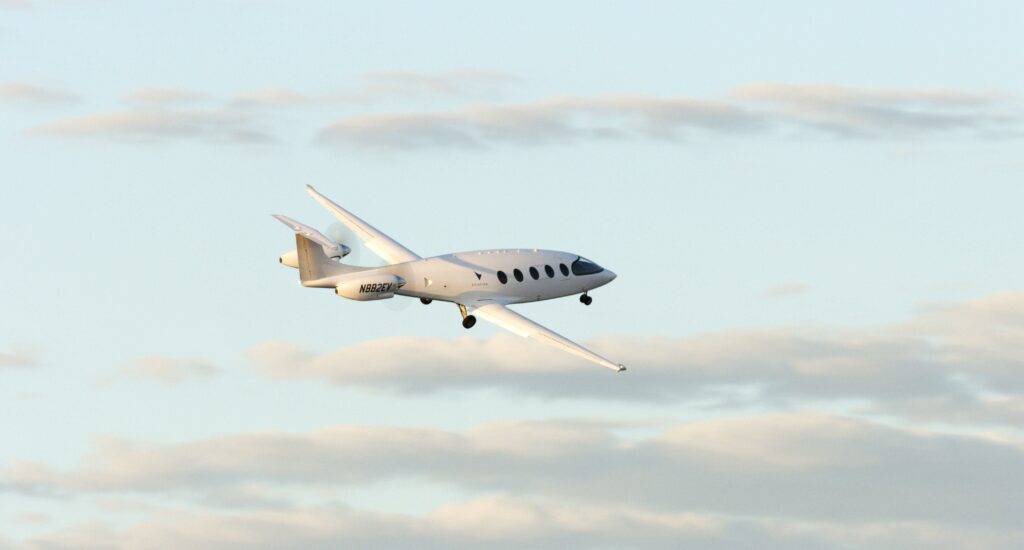
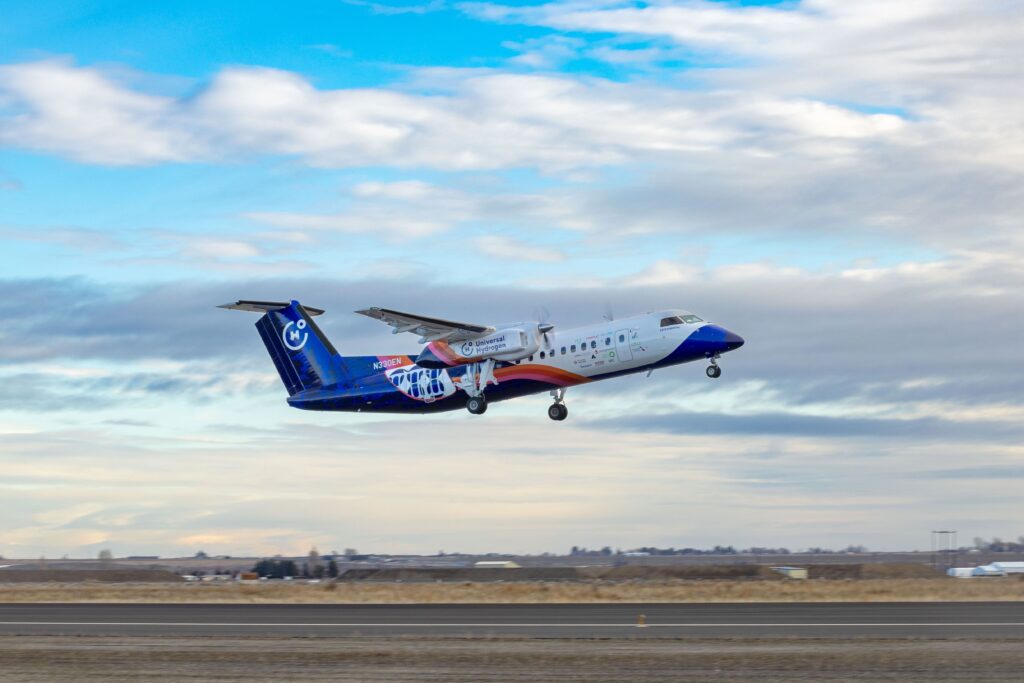
EPU development history
As a company, magniX traces its origins back to 2005, when it was founded as Guina Energy on the Gold Coast of Australia, to pursue the founder Tony Guina’s passion for (and fundamental research into) electromagnetics across propulsion motors, generators and other applications. That led to some successes in developing superconducting technologies, and accumulating a knowledge of magnetic field optimisation and shielding, for example.
As David Sercombe, VP of the magni350/650 programme, recounts, “It was after 2015 that we decided we wanted to apply all that knowledge to the duty cycles and power demands in aviation, which are such that when you take off, you’re running at 100% power for a lot of time before you pull back to cruise.
“That’s true whether the aircraft is powered by IC engines or electric propulsion, but our technological development had specifically targeted efficiency at high continuous power outputs, rather than say peak transients or thermal mass. Our motors have been designed to operate at high power and stay at a reasonably consistent temperature, from 5 minutes into 2 or 4 hours out.”
That led to the development and testing of the company’s first EPU prototype, the magni5, in 2017. That was also the year it was rebranded as magniX, having been acquired by the Clermont Group in 2016, which had previously funded Guina Energy (and is also the majority shareholder of Eviation).
“The magni5 was the first permanent magnet machine we’d built which was targeting a direct-drive aerospace application, and proved that the core electromagnetic and mechanical design could achieve high power density and torque density,” Sercombe says. “Satisfied that the concept worked, we then started looking into what it would take to build a product capable of generating efficient, robust propulsion for an aircraft.
“That direct-drive capability is key as well. Driving a propeller or fan is quite different from driving a wheel, and the ability to work without a gearbox – as you have in conventional aerospace powerplants – means we have a less complex and heavy system than you might ordinarily get. In that sense, the electric future potentially offers higher performance and greater simplicity than the fuel-powered past.”
This development resulted in the unveiling of the company’s next generation of products, the magni250 and magni500 which, like magniX’s present-day (and higher power) flagship products, also brought with them the first generation of inverter controller, built and optimised around the required input and frequency of AC power needed by the 250 and 500 kW motors.
In addition to being tested on magniX’s own aircraft, these were the first e-motors to be tested on other organisations’ aircraft. Riona Armesmith, CTO of magniX, recounts, “The first of those was the eBeaver, in 2019, an electrified DHC-2 Beaver seaplane flown in partnership with Harbour Air, a carbon-neutral and all-seaplane airline in British Columbia. It drew particular attention for being a battery-electric craft taking off from water in the Canadian winter. In that trial, it flew 74 km in 24 minutes.
“The second was the eCaravan, in 2020, which was a modified Cessna Caravan, a widely used 12-seater capable of higher altitudes and longer distances than the eBeaver. The eBeaver continues to fly and accumulate useful data, with over 80 test flights at this point.” That aircraft also had a range of 160 km.
Both were powered by a single magni500 EPU, which weighs 185 kg with inverters and produces up to 560 kW. By comparison, the Pratt & Whitney R-985 Wasp Junior SB engine replaced in the eBeaver weighed 290 kg (not including oil) and produced just 300 kW.
“At the time, the narrative around electrification of propulsion systems in aviation was becoming very strong,” Sercombe notes. “Aerospace propulsion therefore seemed to be the right niche for which we had a product offering in our portfolio of electric motors, in terms of its performance and mechanics.
“The motors have been refined since then, with a strong emphasis on how to integrate them into different airframe systems, how best to productionise them and how to eventually certify them, and those lessons have been fed directly into how the magni350 and magni650 were optimised before their official launch in 2021.
“That took a lot of testing, analysis and iteration for knowing how to get the ancillaries right for the different aircraft we’ll integrate into – a motor isn’t an isolated system, it’s a key structural element. It’s reacting to forces from the propeller, it’s interacting with the propeller control system and the drive accessories.
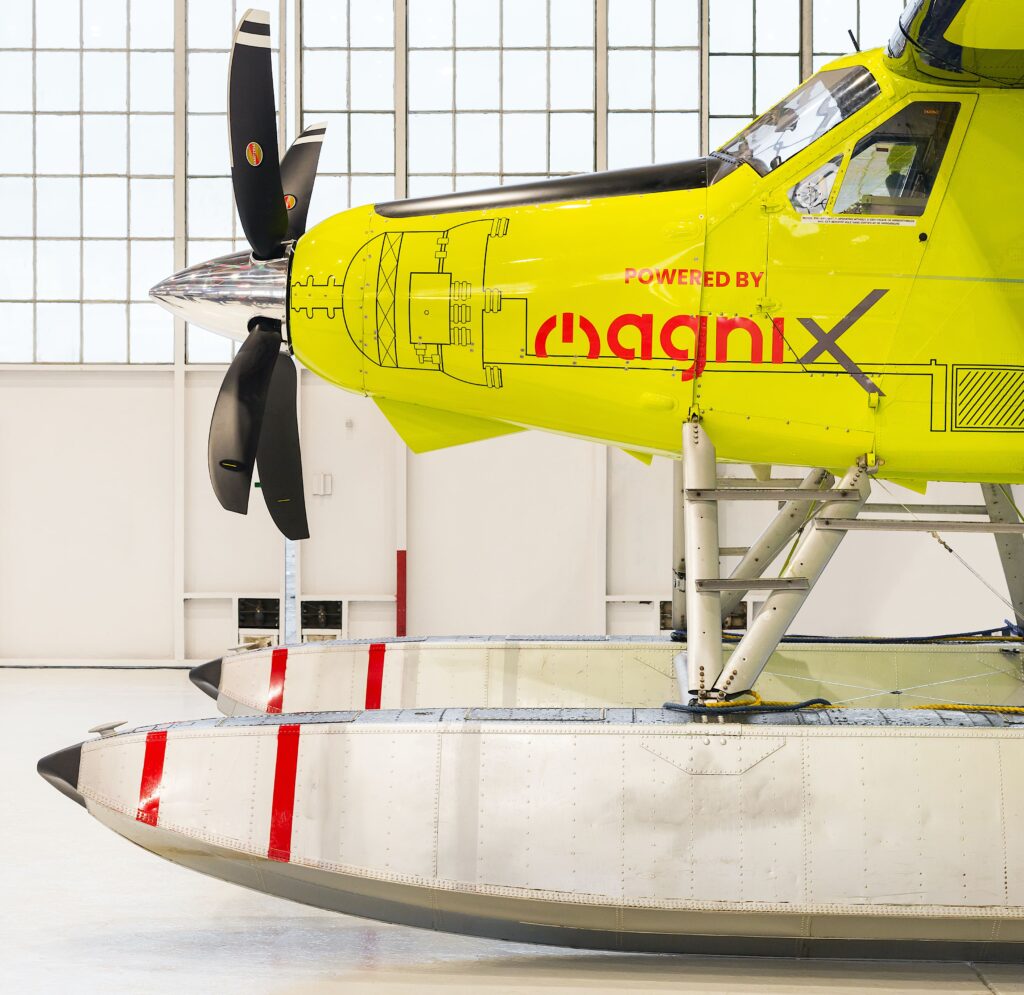
“With the 250 and 500, there were a lot of ancillary components to support the EPUs that the customers would have to specify, buy and package. We would help them with that, but now everything’s well-integrated into a single package.”
A magni250 went on to be used in June 2022 to power a Robinson 44, the first all-electric helicopter magniX worked on, in its first flight at Seal Beach, California. The flight was in partnership with Tier 1 Engineering to provide customer Lung Biotechnology PBC with a zero-carbon means of transporting life-saving organs. The helicopter seats four (including one or two crew members), and measures 11.66 m long and 3.28 m tall; a range of further test flights have been conducted since, including cross-country fights.
Miguel Marmol, VP of engineering at magniX, notes, “Aviation as a market has a lot of barriers to entry, as defined by regulations, but the 350 and 650 have what you might call a pedigree for certification. We’ve been working closely with the regulatory authorities to inform datasets on how electric aircraft are going to be certified, because if you look at the regulations, they’re written for piston and turbine engines; there’s no mention of electric in them.
“We’ve also worked with the FAA to get what are called FAA CFR33 special conditions from them – we’re the only company that has these – about how the aerospace rules that currently exist can be feasibly applied to test flights of our products, along with whatever additional rules are needed to account for the differences between the EPUs and conventional aircraft powertrains. That’s informed materials choices, manufacturing processes, supply chains, quality control systems and more.”
As alluded to earlier, the Eviation Alice has flown with magniX power units – specifically, two magni650s mounted on its aft fuselage, through which it achieved a first successful test flight of 8 minutes in September 2022. Universal Hydrogen’s De Havilland Canada DHC8-Q300 replaced one of its two turboprop engines with a magni650, and flew for 15 minutes in March this year.
That makes a total of five aircraft that have flown using magniX’s EPUs, although the company notes that other, unnamed groups have taken delivery of its powertrains, and are using them to build and develop electric aircraft concepts around them.
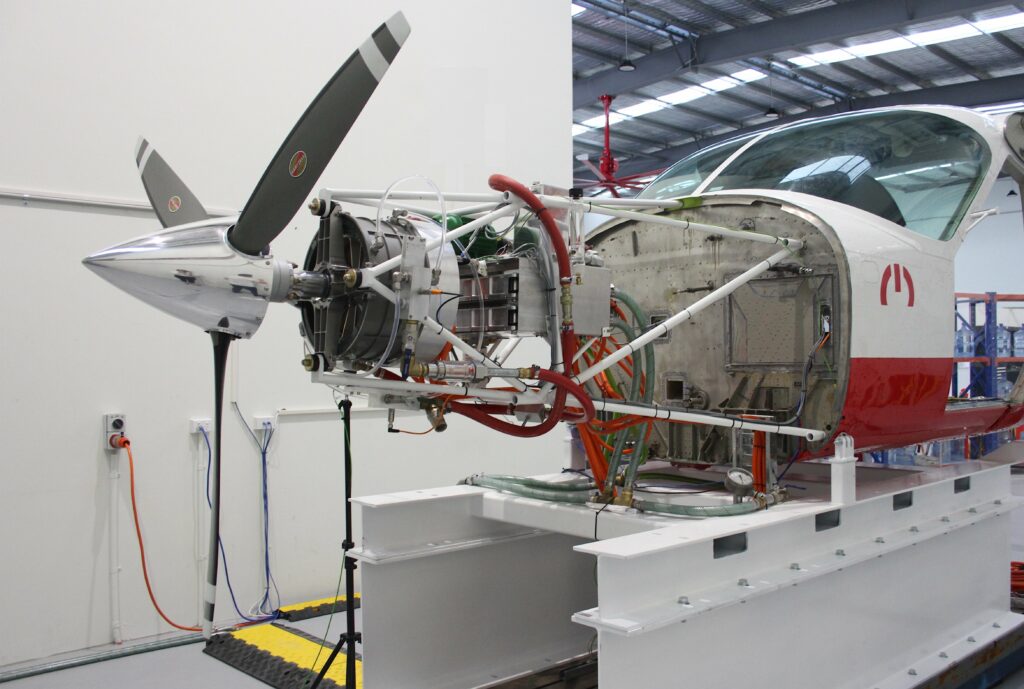
Powertrain anatomy
MagniX does not currently manufacture its own energy storage systems, but the end-user’s battery pack (whether standalone or replenished by an IC engine or fuel cell) is connected to the magniX inverters, with typically a single HV DC bus going into each. Four inverters feed AC power into each magni650, with two inverters for each magni350.
“They’re combined DC-AC inverters and motor controllers, and they’re designed with aviation in mind, specifically to mitigate the effects of altitude on voltage, and with safety evaluations having determined the system architecture and software development,” Sercombe says.
Each inverter is a model known as the magniDrive 100, which measures about 361 mm wide, 352 mm long and 80 mm tall, and produces up to 400 A. As well as the housing featuring the standard trio of U-V-W three-phase cable connectors for power output to the motor, it also has connectors for a LV DC power supply for local controller, processor and sensor systems, and ports for the entry and exit of liquid coolant.
That coolant is provided by an integrated oil system that also cools the motor and lubricates its bearing. The motors meanwhile have a 250 mm radius, 675 mm at their widest diameter, and 550 mm in length for the magni350, or 715 mm for the magni650. In diagrams and images, each motor sits forwards of its inverters, but technically the inverters can be mounted anywhere on the aircraft for ease of integration and maintenance.
Both motors consist (from input to output end) of a cylindrical drum-like housing with the permanent magnet AC machine inside, a cone-shaped housing for the accessory gearbox on the front (which at a minimum drives the oil pump for the cooling and lubricant system), and forward of that is the propeller governor, on which is mounted an industry-standard, hydraulically-actuated constant speed propeller.
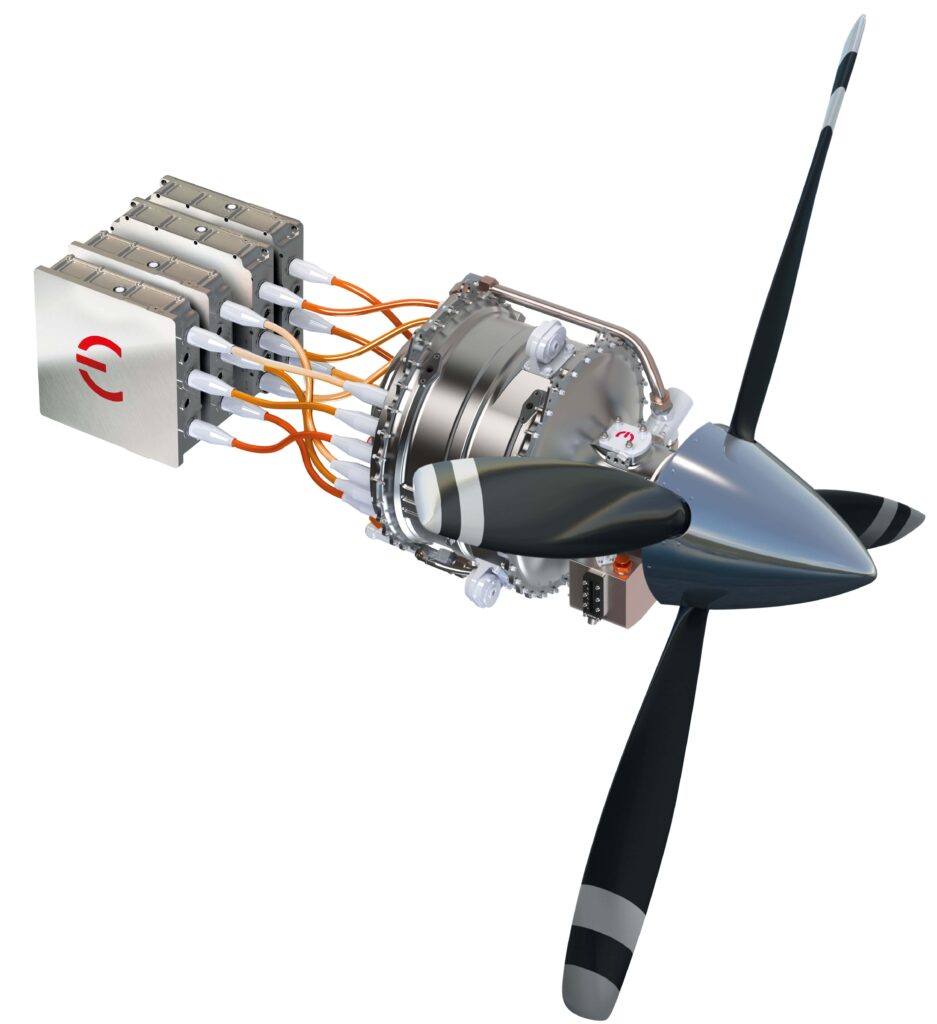
For both the magni350 and 650, the accessory gearbox sits forward of the motor and provides power to the oil pump, with a pad for aircraft accessories such as vacuum pumps, and another for a propeller governor which regulates the speed of the propeller.
Included in the motor housing are mounts that are designed to transmit and spread loads from the propeller safely through to the airframe. As the plane flies, manoeuvres or suffers turbulence, the brunt of the forces tend to be imparted on the front of the powertrain, so rugged and certified propeller cones are part of magniX’s selections with each new project.
“The reason we have four inverters for the magni650 and two for the magni350 is not just because each magniDrive 100 is rated to a finite amount of power,” Sercombe notes.
“Each inverter effectively powers a different quadrant or half of the stator, which is great for fault tolerance because if something does go wrong with one magniDrive, we don’t get a total loss of power, as you would if you’d just gone with one big 700 kW inverter. The fault area can be isolated and the remaining inverters can keep on driving the motor.
“And by keeping them packaged separately, the inverters become what’s known in aerospace as LRUs: line replaceable units. If one needs service or checking, you take it out while you’re on the ground, replace it with a new one, and continue operating.”
At the time of writing, magniX was capable of small-scale manufacturing and selling its EPUs for testing and research purposes, although it will not be allowed to sell them for commercial flights until certification is achieved.
“We’ve avoided reinventing the wheel wherever we can, by using things like bearings, pumps, or sensors that are already commonly used in certified aircraft powertrains,” Armesmith says. “It’s fair to say that a lot of new entrants into electrified aviation, particularly in the eVTOL space, are so hell-bent on innovating on everything that frankly they risk running out of money before they achieve certification to sell to commercial airliners.”
Marmol adds, “A good example of that is our ability to customise and provide an accessory gearbox in whatever form different customers need; each certified aircraft flying today can have a different combination of things like hydraulic pumps, electric generators, air conditioners or bleed air pumps that need to be driven off of an engine, so we need to be able to fit our solution to each of those.”
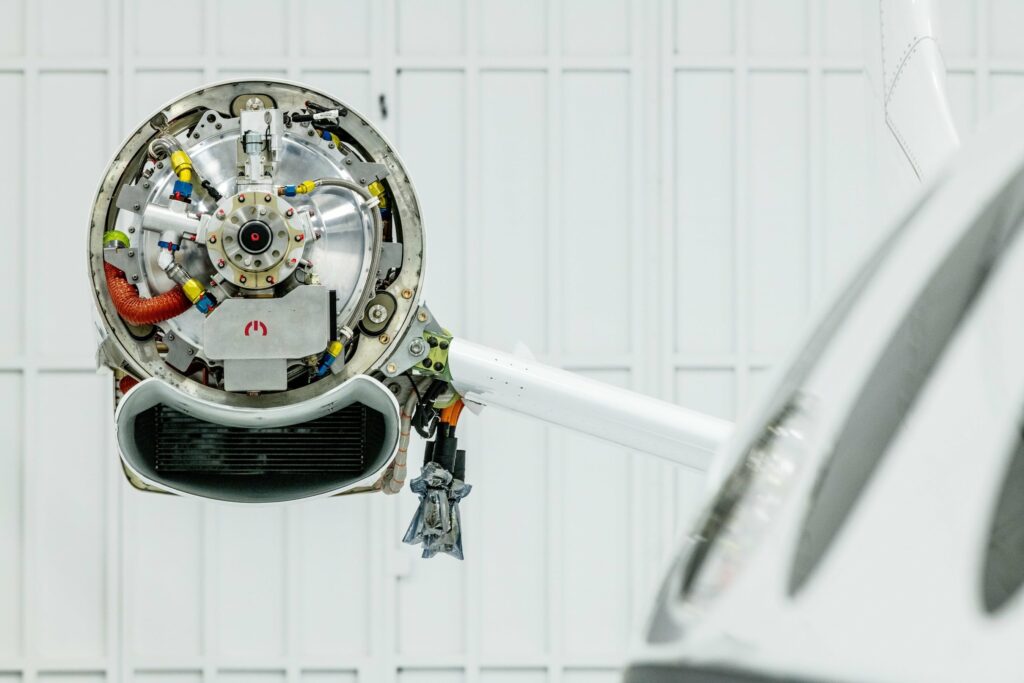
Multi-purpose oil system
As mentioned, a single common oil cooling loop handles both the active thermal management and the lubrication of the magni350 and magni650 EPUs’ bearings; another oil system is used for the hydraulic actuation of the constant speed propeller. Although all aircraft integrating the powertrains will doubtless fly through extremely cold airspace, air cooling – be it from the surrounding atmosphere or the backwash of the propellers across the motor or nacelle housings – would have fallen considerably short of requirements.
“The application space is not always cold; with aerospace, you need to be prepared for -20 to +70 ºC,” Armesmith explains. “In commercial aviation, planes spend a lot of time sat on the runway, where it can be baking hot. Then when it’s time to take off, they go from sitting still to pushing their motors to maximum power. Eventually that will mean there is some ambient cooling, but not before there is an even larger build-up of heat in the windings and magnets.
“On top of that, you’re putting a great deal of work into the air. Whether you’re cutting through the air with a propeller or fan, the energy imparted means the air isn’t as cold as you might think. Air isn’t the heat sink you might think it is, especially as at our high torque densities we need very strong cooling in order to hit the required current densities consistently and without huge efficiency losses.”
Also, air cooling implies friction between the air and hotspots across the powertrain. Effectively that means, for a fixed-wing aircraft, air cooling requires deliberately adding drag – and the larger the motor, the more drag this implies – making it counterproductive to the improved aerodynamics desirable for helping an electric aircraft further on a finite energy store.
“That’s why in this industry you don’t typically see electric motors or generators above 30-40 kW that are air-cooled. There’s a bit of a break point there, where it’s acceptable so long as your electric machine is small, or if it’s something like a starter/generator that you see on a fair number of aircraft these days.”
Sercombe adds, “At a certain point along a powertrain, all liquid-cooled systems have to dissipate their heat, often through a radiator or similarly conventional kind of heat exchanger, and it’s those kinds of well-known systems already used on aircraft that we also use as our points of interface.
“That way, OEMs can install the heat exchangers where it makes sense from the point of view of aerodynamics, thermal and centre of gravity, with hoses running to and from our EPUs, and those and the pumps will be sized to meet the flow rate and pressure needed for full power.”
In addition to the mechanical simplicity gained by using only oil for thermal management as well as cooling – and the hydraulics also use pumps and valves optimised for oil, simplifying part counts – the company notes that using the traditional water-glycol coolants familiar to many in automotive would have been unfeasible in aerospace.
For one thing, handling the temperature differential would be challenging with water-glycol; second, it can also freeze, and expands as it approaches freezing, so cold storage is key in order to continue operating safely at extreme temperature lows.
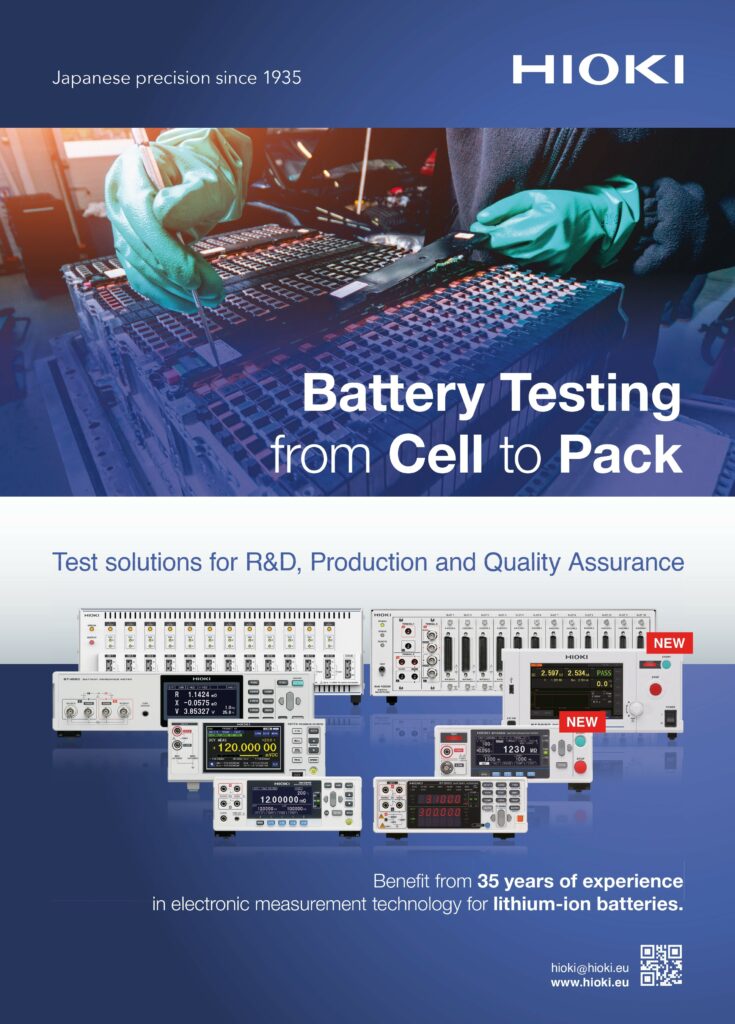
Lastly the use of water-glycol can mandate the integration of an electro-deionisation system to maintain the coolant’s purity and hence its chemical and thermal performance. Such a system could take up significant space, power and weight though.
“Overall, it’s important to remember that while EV drivers won’t have their pedal to the floor all the time, aircraft pilots in a sense do,” Sercombe adds. “An aircraft’s electric motor will run at 100% power for a considerable length of time during take-off, and then still at a significant power level for the rest of it.
“So while hotspots will still occur in essentially the same locations as in an automotive e-powertrain, that higher performance throughout the duty cycle drives how we need to model, design and engineer for thermal cycling, thermal stresses and the degradation of different powertrain elements under thermal conditions.
“That’s maybe not revolutionary thinking. For decades, people have encountered analogous differences, particularly regarding around duty cycles, when trying to take an automotive piston engine and run a plane or helicopter on it; and although the world has seen electric aircraft powertrains across, say, the UAV world for some years now, passenger airliners run far higher power outputs, and that’s where the technology changes quite a bit.”
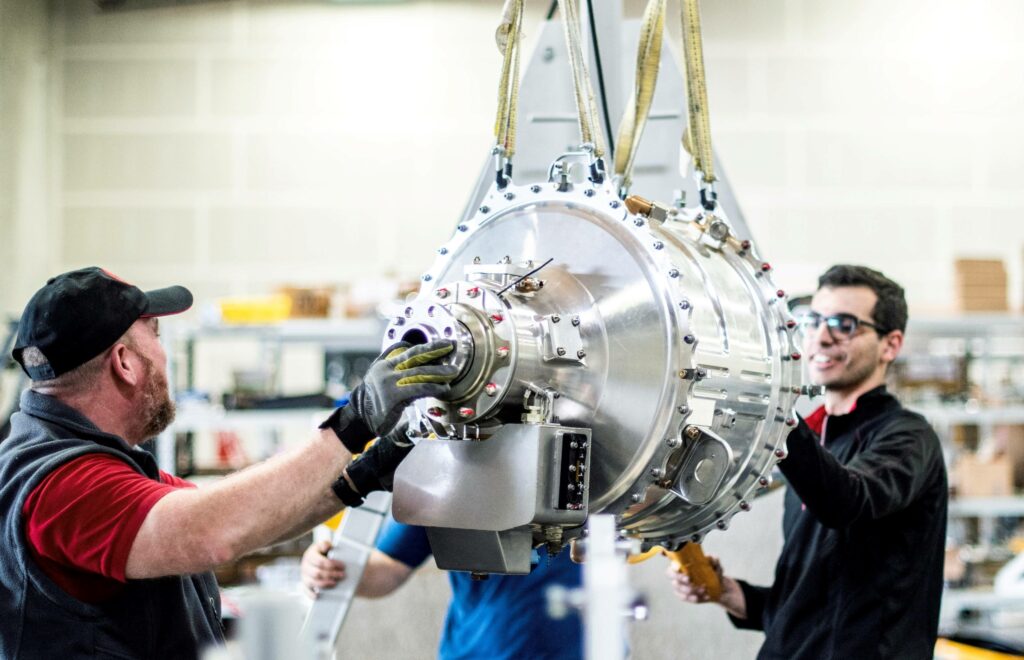
Motor design
As discussed, the magni350 and magni650 motors are permanent magnet AC synchronous machines, each with a stator constructed external to a rotor. In addition to the aforementioned power outputs, the smaller motor produces up to 1608 Nm of torque, while the magni650 is capable of up to 3216 Nm. Both motors have a top shaft speed of just 2300 rpm, thereby prioritising torque over speed in how it produces power.
“There’s a lot of focus purely on power density in electric motors, which is a sticking point for me because power doesn’t size your motors, torque does, and torque is what you really need in traction motors, whether you’re driving a wheel or a propeller,” Armesmith observes.
“That is especially true for direct-drive applications, so a lot of integrators can be led astray by these great big power numbers from motor manufacturers, which omit the fact that you need a big, heavy and inefficient gearbox at the front to get any meaningful driving torque out of it.”
Also, going with an asynchronous motor configuration would probably have incurred penalties in terms of weight and power efficiency, and in turn torque density, particularly when designing such a system for directly driving a propeller.
Considerable r&d has gone into the magnetics, flux, windings and other internal parts and parameters in order to create an electric motor capable of the low speed and high torque that are ideal for driving propellers on large aircraft.
Naturally, this included considerable thermal modelling and iteration, as high torque in electric motors also requires high current – as noted earlier, each magniDrive inverter can deliver up to 400 A to its respective stator quadrant – which poses a clear risk of heat build-up and losses without a high-duty cooling system such as the oil coolant circuit.
In addition, insulating the stator windings, and indeed the entire powertrain, was deemed a critical focus of engineering, given that at altitude, the naturally insulating effect of air diminishes as air density drops. This, and phenomena such as corona effects stemming from ionised air, meant factors such as careful spacing of conductors and minimum creepages and clearances had to be considered throughout the motor and electronics, particularly given that at 800 V the magniX powertrains have effectively the highest voltage ever flown.
“Right now, there’s something of a convergence in automotive e-motors,” Sercombe says. “We’re seeing a lot of focus on hairpin stators and IPM rotors, and there’s some research into different cooling schemes. Other than that though, the EV industry has reached a kind of equilibrium, largely motivated by what’s cost-effective and mass-manufacturable, and also to reduce dependence on things like rare earths, which are getting harder to source.
“But none of that translates to the duty cycles needed for an aerospace product. Peaks of 18-30 seconds are one thing, but our peaks can last at least 5-10 minutes.
Weight is at a massive premium too – and worse, as we minimise mass, we reduce the size of our physical sink for hiding thermal transients. That means we have a very different toolset to that in automotive, including viable materials choices, inverter and motor topologies.”
Armesmith adds, “We operate at higher nominal [power] frequencies than those in automotive, and that drives you to look for materials that allow you to do that. While we can’t discuss the exact path we took, we’re not using silicon iron or anything straightforward like that, and we’ve also had to keep weight and reliability in mind.”
Critically, one area the company worked hard on reducing was regeneration. At no point during flight, as well as descent, can the plane simply carry on under its own momentum while air drives the propellers to generate current. That would create a large amount of drag, and the plane would start to fall rapidly.
“Maybe a glider or UAV could do that, but not a passenger aircraft,” Armesmith says. “There are rules against it in aerospace, so we have to actively stop regeneration from being possible, it’s a fault we have to arrest,” Armesmith says.
“So, if we’ve either lost power or had to turn the motor off for any reason, the propeller needs to be able to windmill freely. We can’t have any electromagnetic resistance to the propeller free-turning owing to regeneration back into the DC bus.”
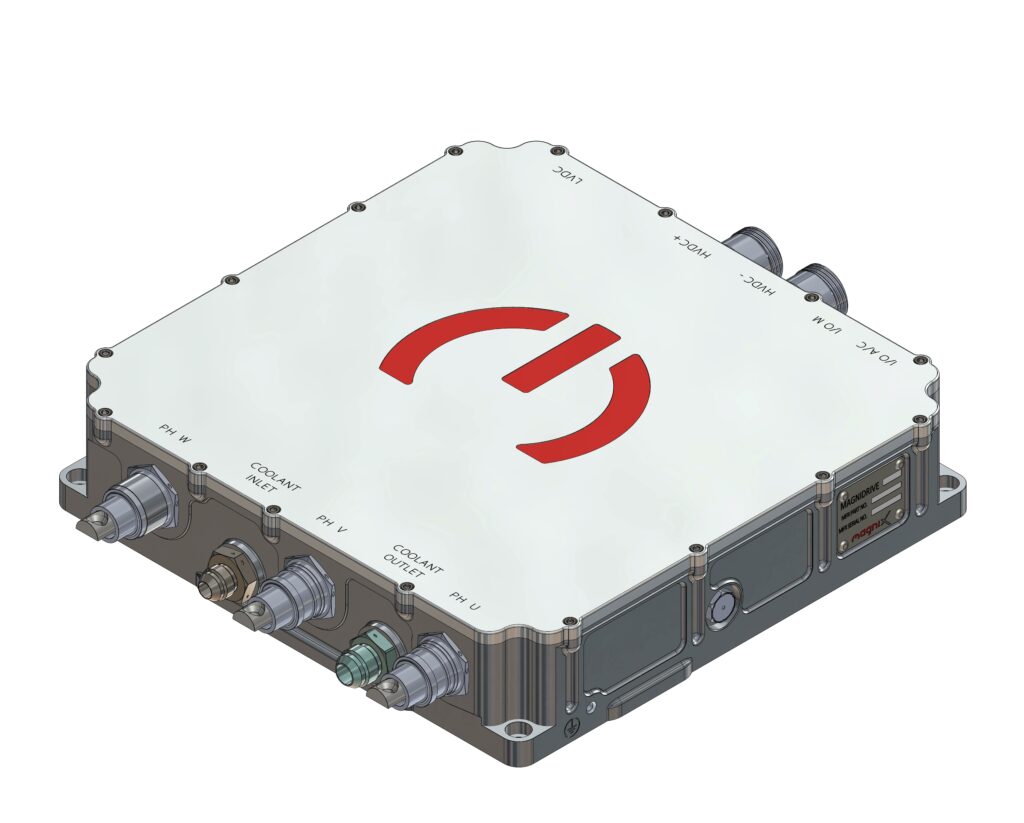
Bearings
In our past features on in-wheel motors (such as Protean’s PD-18, EME 3, Summer 2019, or Elaphe’s L1500, EME 7, Autumn 2020), we have seen that the bearing forms a critical point at which fatigue and radial impacts must be absorbed, damped or transmitted safely through to the rest of the motor and wheel, such that they do not cause cracks in (or movements in the air gap between) the rotor and stator, or a puncture in a wheel.
Sercombe says choosing bearings for the magni350 and magni650 had a similar importance to those for road vehicles. “I think the art of effective application design comes down to picking your bearings and connectors, then designing everything else to fit between those two,” he says.
“For integration into aircraft, you first need to consider what’s happening at the front. You have a large spinning multi-blade propeller producing thrust, and every time you bank or turn you have an additional set of forces from gyroscopic procession and other aerodynamic forces that are acting on the front and then being loaded through the bearing.
“In fact, any time the aircraft is subjected to inertial loads, some of those are essentially going through the bearings, so they have to be sized appropriately for the rotor and stator. If you’re integrating more than one on the motor shaft then it has to be the right combination of bearings for the kinds of loads they’ll endure – it’s foolish to try to combine loads or elements within individual bearings – and of course, bearings push constraints into the system from assembly and longevity points of view.”
These considerations also affect bearing selections to an extent in traditional aerospace turbine engines; unique to the EV aircraft space though are assessments of how their integration within an inverter-fed electric motor can be executed safely. Insulating bearing supports, grounding electrical connections, and careful use of shielding are key to ensuring the bearings cannot be damaged.
Another perennial concern is maintenance, particularly the ability to inspect the condition of the bearings in the EPUs, and thereby gauge the time until replacement becomes vital.
“Fortunately, we’re using oil-fed bearings, which allows us to inspect the condition of the oil as it leaves the bearing to gauge the bearing’s health,” Armesmith notes. “So we have sensors that measure the oil temperature for signs of excess heat or friction, as well as the presence of particles in the oil that would indicate bearing wear.
“We can monitor the particle content using magnetic chip detectors and similar devices, which are standard in aerospace for airplanes and helicopters. It makes sense to use those as tried-and-tested solutions rather than reinventing the wheel.
“Similarly, we anticipate that the existing worldwide infrastructure of aircraft MRO providers will be suitable for repairing our motors and replacing things like bearings. Aircraft turbine engine parts already fit together with clearances tight enough to be analogous to electric motor parts, like the sub-1 mm air gap typical between rotors and stators.
“There’ll be a few added complications for them though, like the fact that there’s stator winding insulation and permanent magnets that risk being damaged during reassembly, but it won’t change the fact that jobs like replacing bearings isn’t terribly complicated, whether the engine is IC or electric.”
Similarly to bearings, connectors form vital interface points where shock and vibration loads tend to be concentrated throughout flight. Although various aerospace-grade connectors are available from suppliers around the world, the unique situation of an 800 V electric aircraft powertrain motivated magniX to engage in a connector development programme with its (unnamed) supplier, which helped in defining the necessary insulation, mechanical and safety requirements across the 800 V system.
“These connectors are optimised for high-voltage operation at altitude and the environmental demands at altitude,” Sercombe adds.
The inverter
The magniDrive 100 is rated to 170 kW of maximum continuous power as it rectifies DC current into an AC supplier for the motor segments; each unit weighs about 12 kg.
As mentioned, the magni350 is powered and controlled by two magniDrives, while the magni650 uses four. The inverters are not integrated into the same housing as the motors; instead they are installed on the airframe as deemed sensible by the aircraft’s engineers or operators. Three-phase HV cabling and coolant hose are similarly connected and run as makes sense for the integrator.
“Each magniDrive is responsible for its segment of the stator, not just in delivering AC power but also in terms of control, monitoring and fault handling. Each also communicates a stream of performance and usage information back to the airframe,” Sercombe says.
“Installation on the airframe is fairly straightforward. We provide an installation manual, but beyond that we’ve seen a number of different configurations and orientations in where systems integrators have chosen to mount the inverters relative to the motors – each aircraft has a very different use case.
“And it’s important to remember that there’s more than just volume or weight considerations that motivate placing an inverter further from its motor – placing it closer to the energy source upstream can be useful from an engineering point of view. Batteries and fuel cells can exhibit different dynamic electromagnetic behaviours, on top of very different ramp rates and other power characteristics, so integrating tightly with them, with a minimal length of cabling between, can be desirable.”
Two objectives were paramount in the engineering of the magniDrives. The first was power density, particularly to match as much as possible the inverters’ outputs with the motors’ required inputs across the operational profile of each aircraft.
A primary driver of power density was the selection of power transistors, although that in turn brings a balancing act between performance and availability, and to date magniX has tested a range of solutions, each over hundreds of hours, in its efforts to search for an optimal transistor. The tests investigate other vital parameters such as insulation quality, and performance over time and at peak voltage, as well as extreme tests of up to 2.5 times their rated voltages, to gauge the reliability over their lifetime.
The second objective was to design the system for everything required for safety compliance in aerospace, which revolved mostly around control and protecting against faults. That meant for instance a focus on packing in as many health monitoring sensors, comms channels, and EMI and ESD protection systems as possible.
“On the software side, it meant we had to really refine and iterate well on things like voting logic in the embedded software, for when there are multiple instances of data or conflicting information coming in from redundant sensor groups,” Armesmith says.
“We spent a lot of time early on working on control, but control engineering techniques are well-established, and aerospace is something like 10% controls, 90% protections. So since then we’ve focused much more on protection, particularly the software’s ability to predict a fault, to react quickly in preventing a failure, and in keeping a failure from propagating.
“Probably the most important regulation for meeting airworthiness requirements was DO-160G, which also comprises a long list of guidelines on mechanical design, environmental protections against threats like humidity, salt, fungus, vibration, and changes in temperature and air pressure as you change altitude. It gets you to think deeply about how to design high-voltage systems to physically withstand the environment of an aircraft.”
The inverter’s thermal management requirements are a major reason why magniX has not attempted an air-cooled version of its powertrains. As the magniDrive must receive and deliver up to 170 kW during take-off, and a quantity of power not far below that throughout cruise, even a very efficient inverter would still lose and emit at least 2-3 kW in heat.
Couple that with the fact that the inverter is packaged separately from the motor, and one soon realises that air cannot even reach the inverters or their heat sinks, let alone dissipate the generated heat sufficiently.
Aviation standards also dictated the control system architecture, with all the programming inside the magniDrive having run in line with FAA guidance on software development lifecycles.
“That informs what your development environment looks like, how you develop software, who does it, where independent evaluation is required, and how the control hardware you’re going to use must be engineered,” Sercombe says.
“That last one especially raises questions over how long your chosen computer processors have been used, and whether they’re tried and tested enough. Going down a development path on hardware that lacks pedigree in aerospace can be challenging compared to staying in the space of technology that’s been proven in aviation but perhaps has more constraints in terms of speed and processing power.”
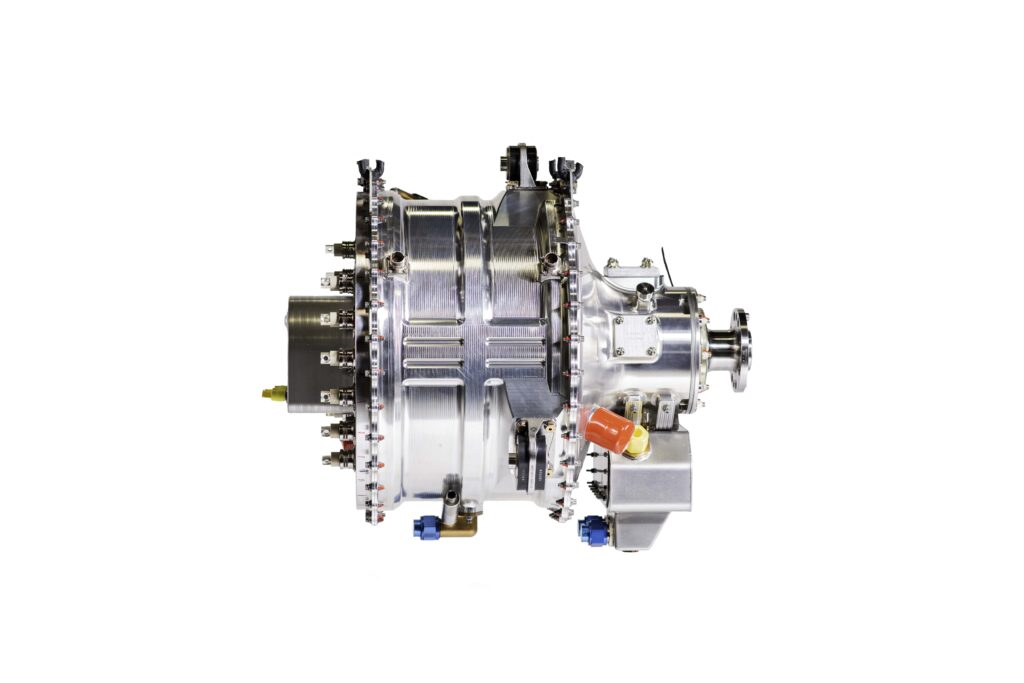
Hybrid and hydrogen power
Although it has achieved considerable success with its electric propulsion systems so far, magniX also plans to diversify and expand its offerings to include ‘upstream’ subsystems in power generation – specifically, hybrid ICE-electric systems and hydrogen fuel cells.
“That move is somewhat out of necessity,” Armesmith comments. “We’ve proven our ability to understand and develop systems for aerospace, including back-and-forths with regulators to determine new rules and standards around electrified aircraft systems, starting with the motors and then adding the magniDrives, before fleshing-out the airplane integration side. Given that journey and that basis, moving towards power generation and energy storage is the next logical step.
“We’ve worked on a number of programmes now where, although we didn’t start as the integrator, we’ve been closely involved in ensuring the system works holistically, especially regarding inter-component functions like pre-charge or protections, and that integration understanding has accumulated to the point that going into hybrid and hydrogen energy systems is just an extension of what we already know how to do. Engineering end-to-end aircraft power systems, potentially even as self-contained, turnkey solutions, will help form future standards on green aviation.”
Hydrogen fuel cells in particular are viewed by the company as potentially crucial to long, zero-carbon flights without excessive weight owing to the batteries’ gravimetric energy density. It is also key to making larger, more powerful motors viable, as they are technically constrained in how big and heavy magniX can make them before they crowd out the available weight that battery packs can take up.
The company adds that until a battery is designed that can achieve at least 1 kWh/kg, without major drawbacks in other vital parameters such as its C-rate or lifespan, hydrogen will have too significant an advantage in specific energy to ignore.
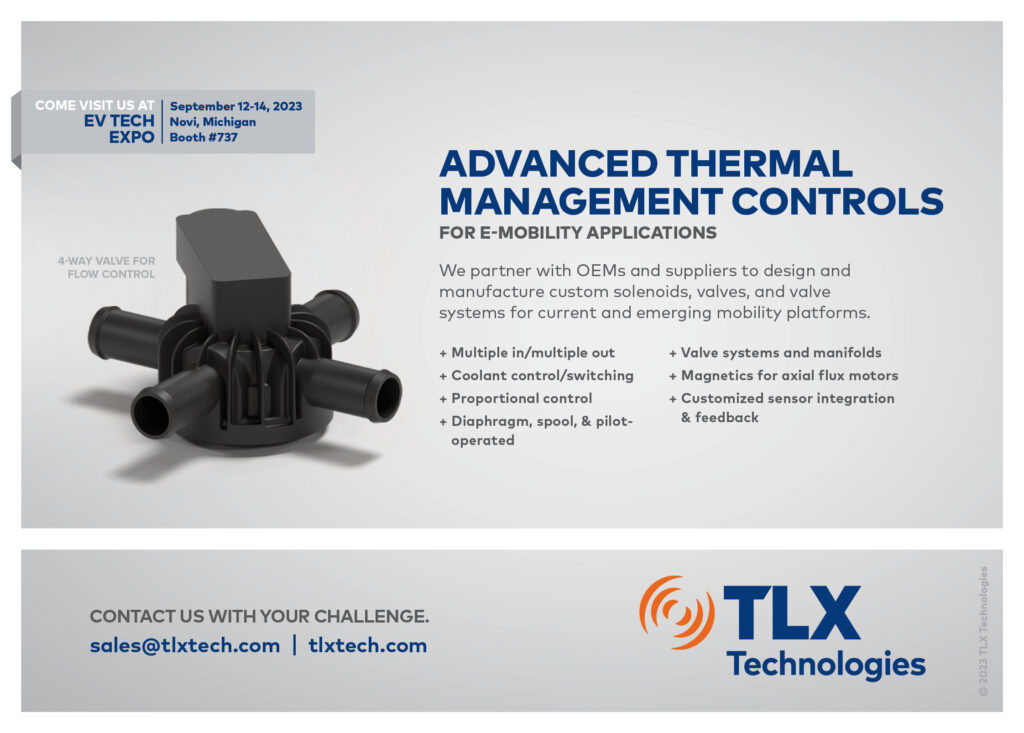
“We also have designs for hybrid systems , but we acknowledge that batteries might continue advancing to the point that by the time we get an end-to-end hybrid solution to market, hydrocarbon fuels no longer have a big enough specific energy advantage over batteries to make them particularly worth it, in a similar way to what we’re seeing in the automotive market at the moment,” Armesmith adds.
“A big part of that comes from hybrid powertrains being mechanically much more complex to package, integrate, maintain and certify than all-battery solutions. That’s because you have all these engine regulations and then you’re adding to that a bunch of old and new electrical regulations, probably with some further regulations on having both HV and kerosene in the same space. And certification takes a long time, so we’ve yet to go ahead with making a hybrid powertrain, because batteries could well be a more convenient offering by the time we’re cleared to sell hybrids to commercial airliners.”
Future plans
MagniX is continuing to work with a range of partners on integrating and using its electric propulsion systems. Notably, its announced projects include work on NASA’s Electrified Powertrain Flight Demonstration programme.
Test flights for that are set for 2025, and are expected to include combinations of the pre-existing onboard gas turbines with the EPUs. The turbines can be used for propulsion, or simply for electric power output, burning fuel to generate electricity and charging batteries for powering magniX’s motors.
Different configurations will be explored, and the hybridisation will be based on the existing architectures in the certified regional aircraft models. “That’s going to be a really interesting proving case for hybrid aviation technology, where there’ll be not only two separate, segregated power systems but also a unique way they’ll integrate and work together,” Sercombe says.
“There are a lot of companies looking into larger aircraft, the kinds certified under FAR Part 25, and many of those are thinking that a multi-powertrain system might be the optimal approach to electrifying those airframes. The NASA trials will put hard numbers to parameters like fuel savings, emissions, how pilots interact with the system, and a gamut of other areas.”
Specifications
magni350 EPU
Permanent magnet synchronous AC motor
Inrunner
Oil-cooled
Operating voltage: 500-800 V DC
Take-off rpm range: 1900-2300 rpm
Dimensions (including gear cone): 550 mm length, 250 mm radius, 675 mm at widest diameter
Total EPU weight (dry, including all magniDrives and HV DC cables): 128 kg
Maximum power output: 350 kW (at 2300 rpm)
Peak torque: 1608 Nm
EPU total system efficiency (including motor, inverters, AC cables, pump and governor) at cruise torque: 93.5%
magni650 EPU
Permanent magnet synchronous AC motor
Inrunner
Oil-cooled
Operating voltage: 500-800 V DC
Take-off rpm range: 1900-2300 rpm
Dimensions (including gear cone): 715 mm length, 250 mm approximate radius, 675 mm at widest diameter
Total EPU weight (dry, including all magnidrives and HV DC cables): 206 kg
Maximum power output: 700 kW (at 2300 rpm)
Peak torque: 3216 Nm
EPU total system efficiency (including motor, inverters, AC cables, pump and governor) at cruise torque: 93.5%
magniDrive 100 inverter
Inverter
Dimensions: 361 x 352 mm
Weight: 12 kg
Power: 170 kW
Current: 400 A
Peak power density: 14.17 kW/kg
ONLINE PARTNERS
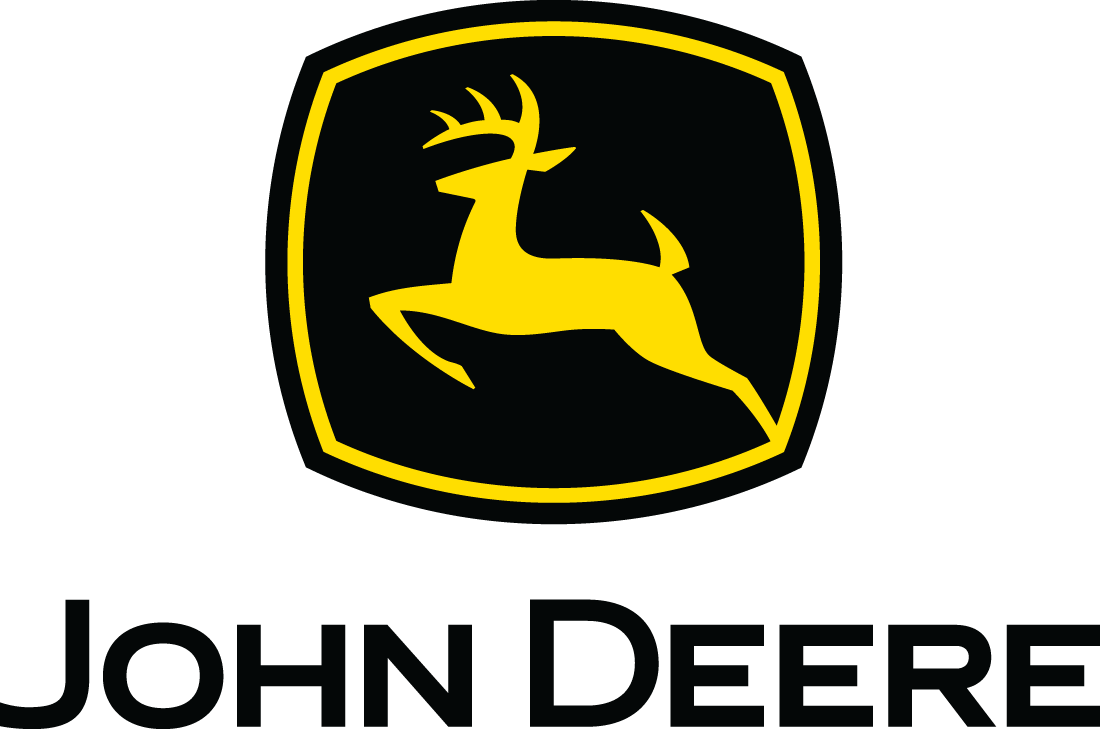
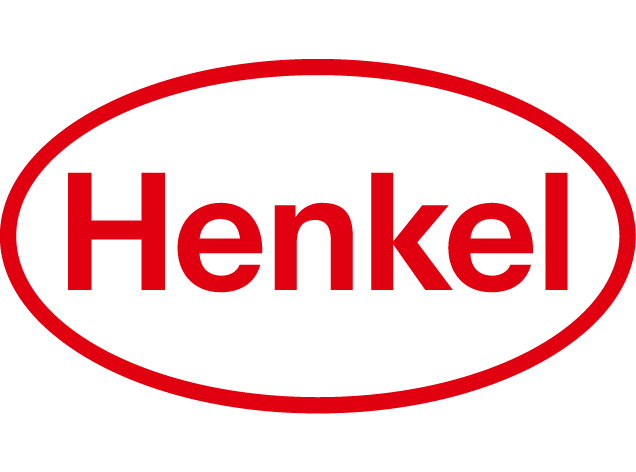
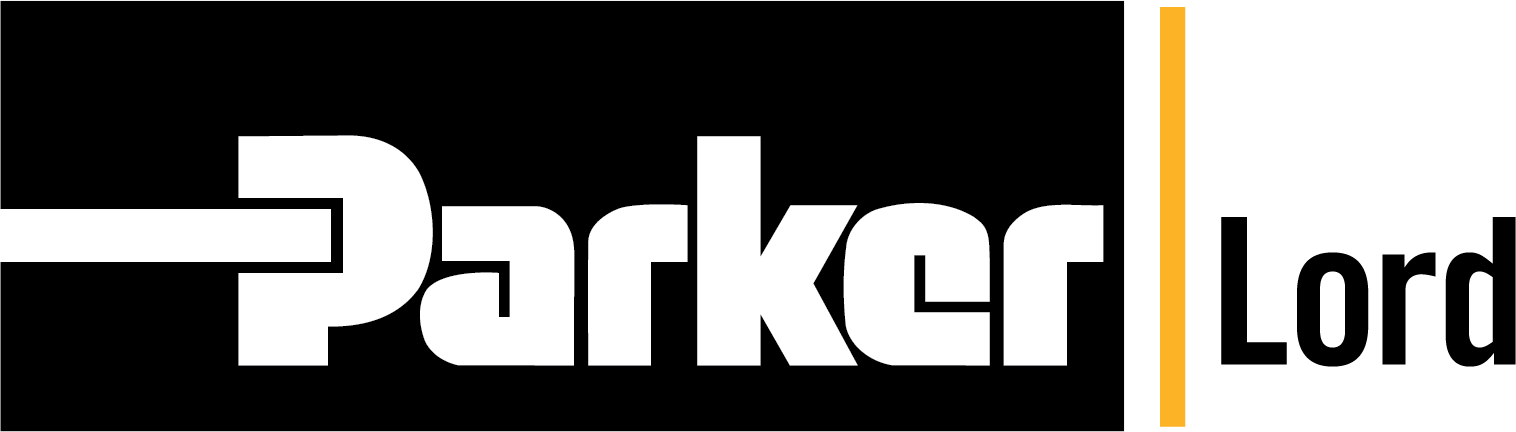
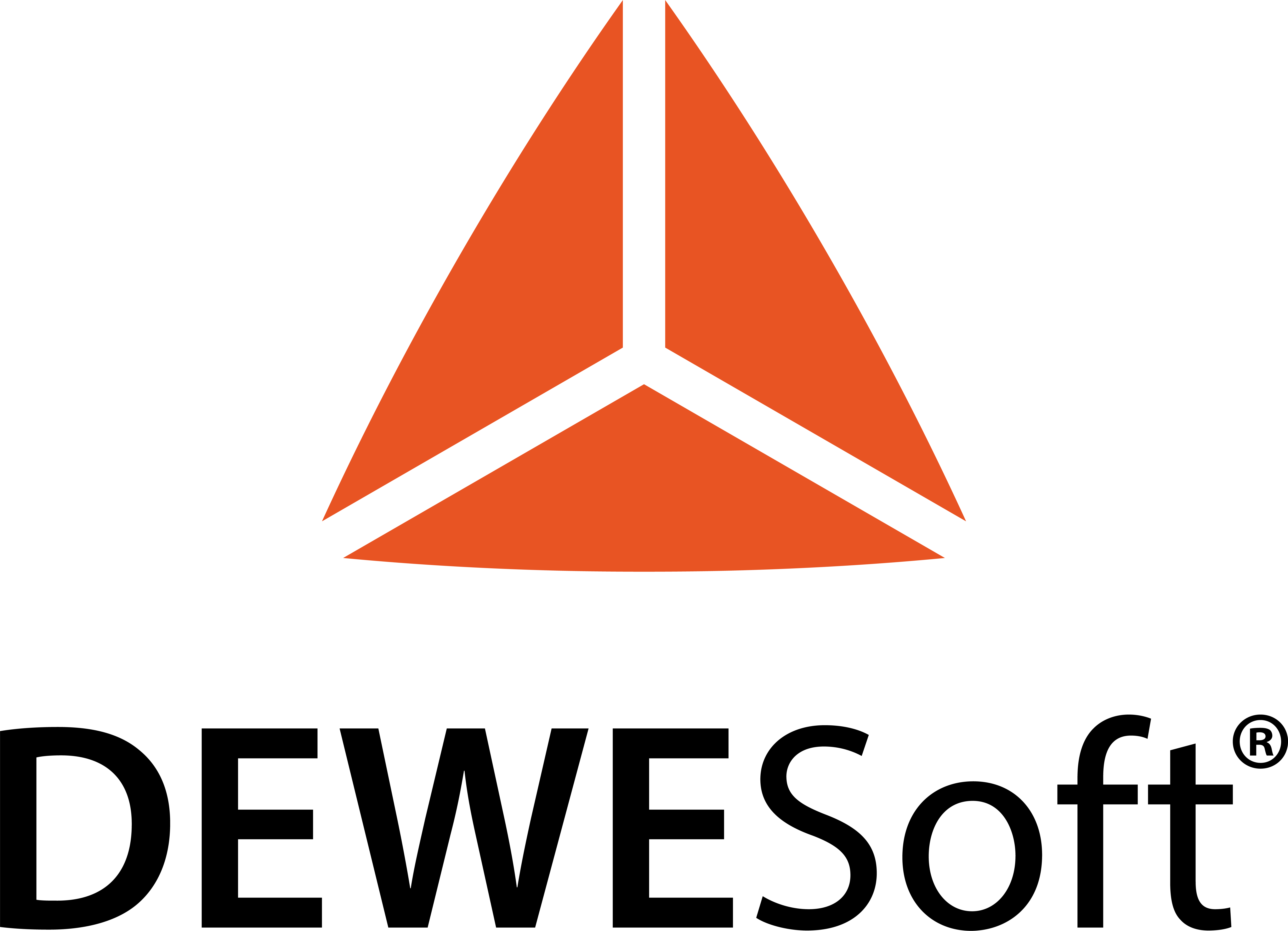
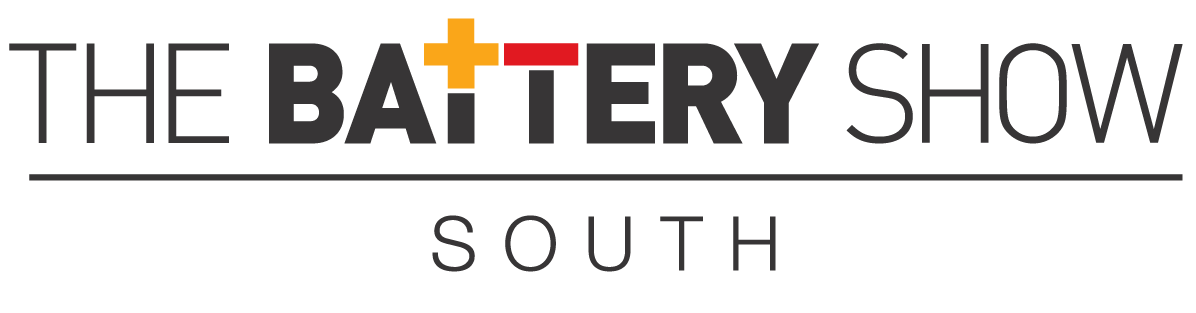
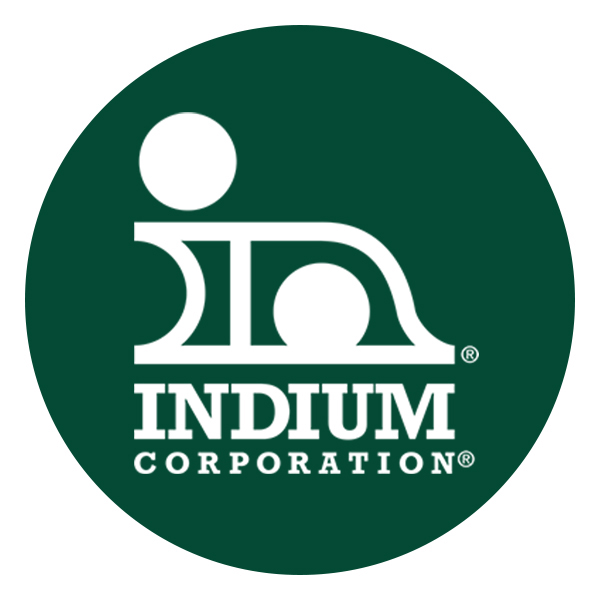
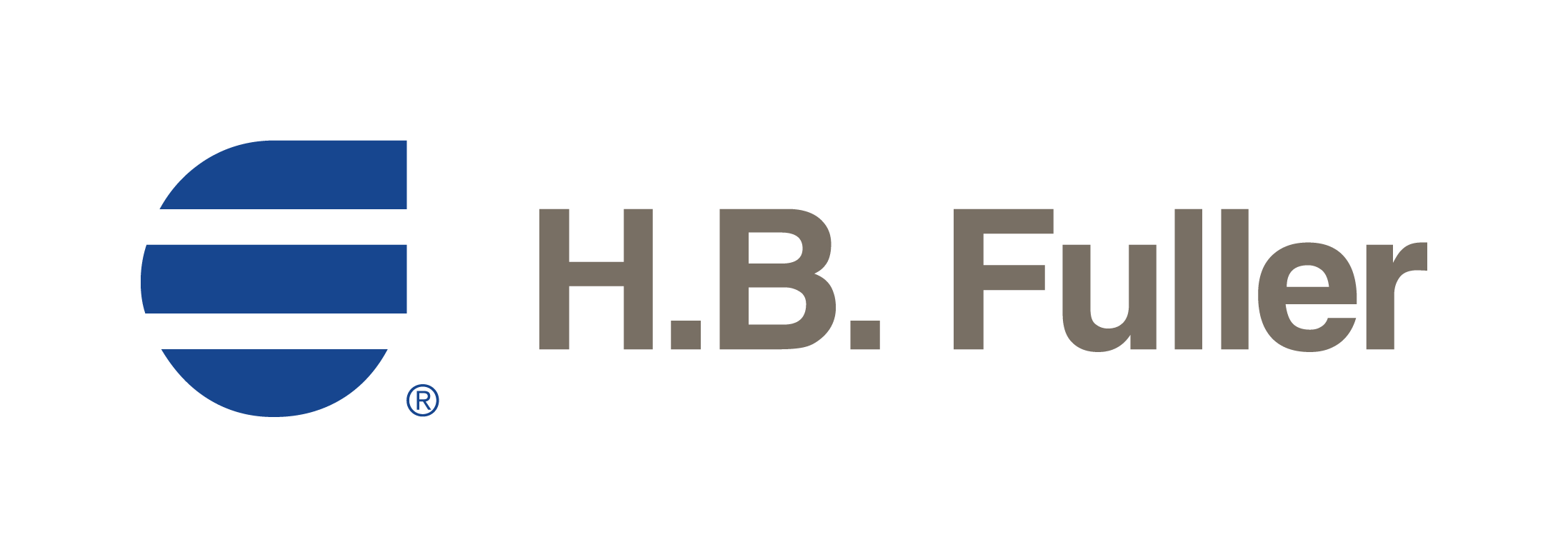