Lotus gives update on LEVA platform
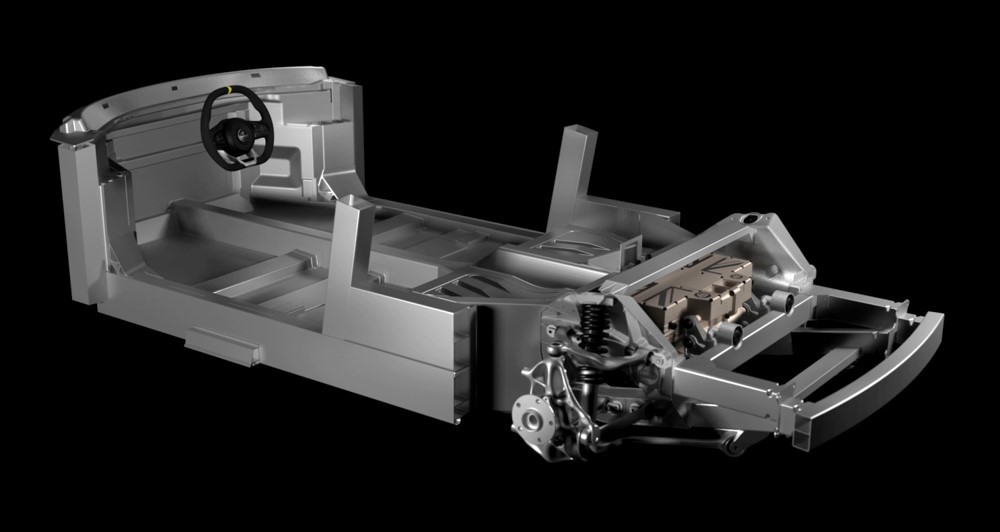
(Courtesy of Lotus)
Lotus has openly said that its latest sportscar, the Emira, will be its last mainstream model with an IC engine (writes Peter Donaldson).
Its next-generation two-seater will be based on the Lightweight Electric Vehicle Architecture (LEVA), on which Lotus is working with initial funding from industry body the Advanced Propulsion Centre, in partnership with casting specialist Sarginsons and Bristol University. The European Battery Show and Electric & Hybrid Vehicle Technology Expo in Stuttgart at the end of June provided an opportunity for a progress update from Lee Jeffcoat, head of business development at Lotus Engineering.
“With the LEVA platform, we’ve been looking to optimise the structure so that the overall vehicle weight is no more than the current IC-engined alternative,” he says. “Obviously, with the batteries, weight is a major challenge, but we have managed to make the structure 37% lighter than the Emira’s by optimising existing technologies.”
On display at the show was a structurally representative mock-up of the rear chassis and powertrain of the developmental Type 135 – the codename of the next-generation two-seater. It’s configured as a mid-engined sportscar with a ‘chest’ battery and twin, mirror-image inverters and motors set up to turn conventional drive shafts and wheel hubs. The inverters and motors together form the electric drive unit (EDU).
“In optimising the rear section, we have introduced aluminium die castings,” Jeffcoat says. “We have also removed the need for a separate subframe, because the EDU is much lighter than an IC engine, and the mounting can be optimised for the higher frequencies.”
Lotus has looked carefully at the role the battery plays in the structure to minimise combined mass. “We have looked at integrating the battery fully within the structure, which brings potential benefits but adds the risk of significant complexity,” Jeffcoat explains.
The challenge is to create a pioneering semi-structural solution. “At this point we are looking at the battery pack being a stressed member of the chassis, but making it a removable one to cater for servicing requirements and so on,” Jeffcoat says.
A lot of attention has also been paid to lightening the suspension and its supporting structure, he adds. “We have a die-cast mounting for all the suspension components, in place of extruded aluminium in earlier designs. We can create structurally very strong, very light mounting points that also support the EDU and the crash structure behind.”
The EDU itself is mounted directly to the primary structure through mounts with rubber inserts. The motors are positioned directly underneath the inverters, and the aluminium structure around it is made up of the die-cast suspension mountings and the extrusions of the crash structure.
The twin motors are from a manufacturer in the UK, while the inverters are off-the-shelf units that have been integrated with a single-speed transmission to create an optimised EDU, Jeffcoat notes.
Whether the production vehicle will use exactly this configuration for the EDU has yet to be decided, he says, as Lotus is still looking at the performance attributes it wants, as well as the cost and availability of components and optimising the whole package for its intended markets around the world.
It is a similar story with the battery, even as the company looks for production solutions. Although Lotus is working with a number of cell suppliers, it has not yet selected one because it is keeping its technology options open.
“We will need to decide this fairly quickly, as we will have prototype vehicles running by the end of 2023 and we want to start production in 2026,” Jeffcoat says.
ONLINE PARTNERS
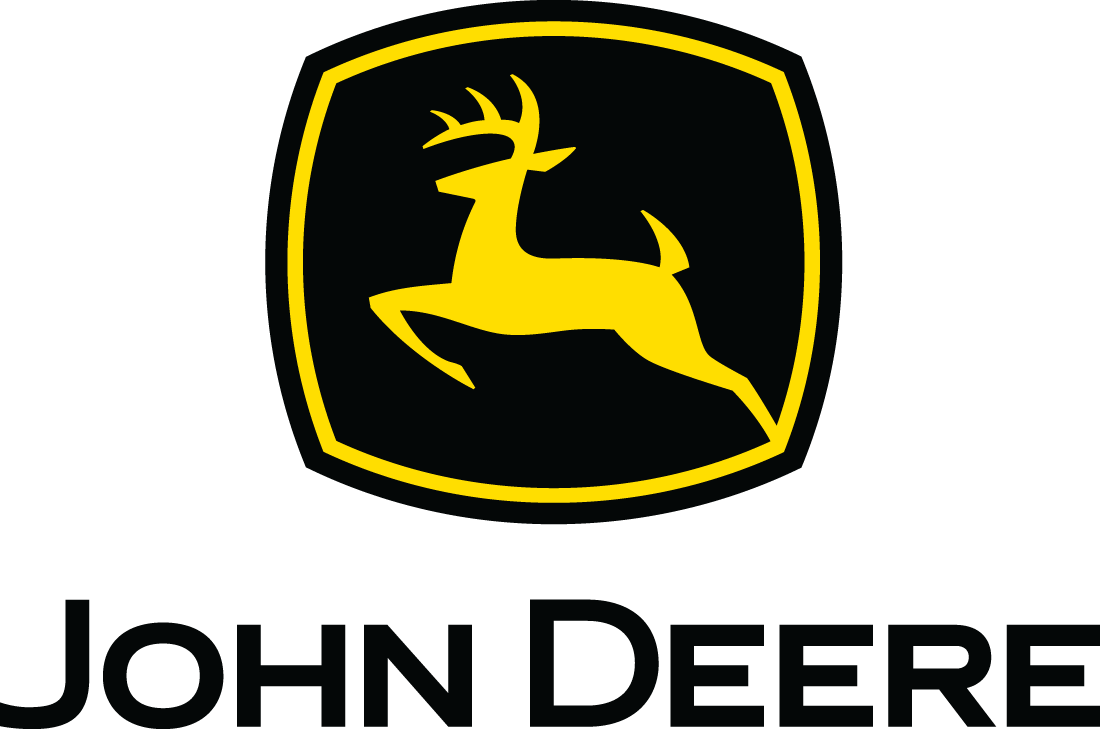
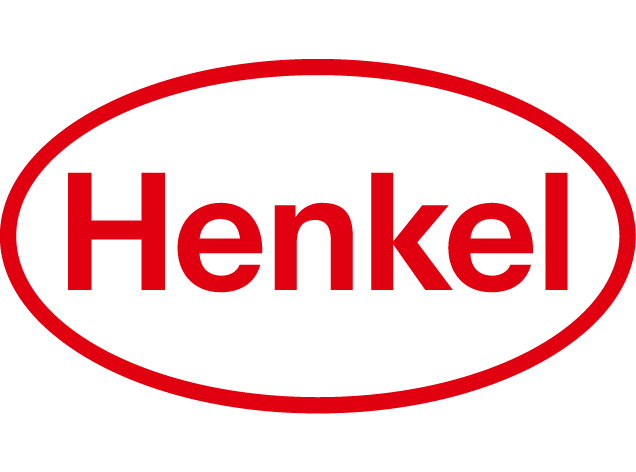
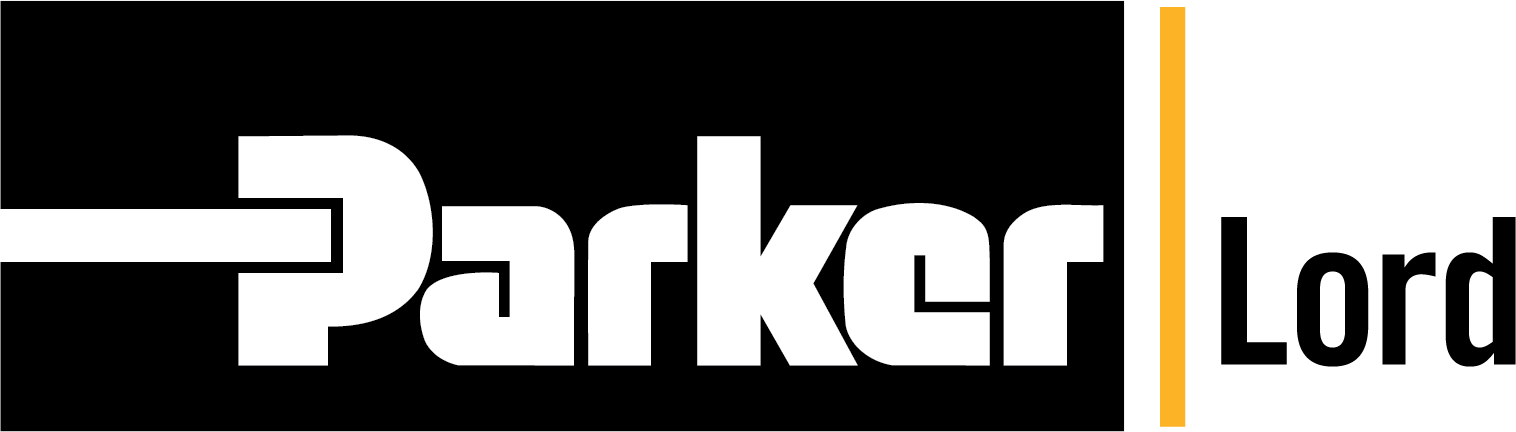
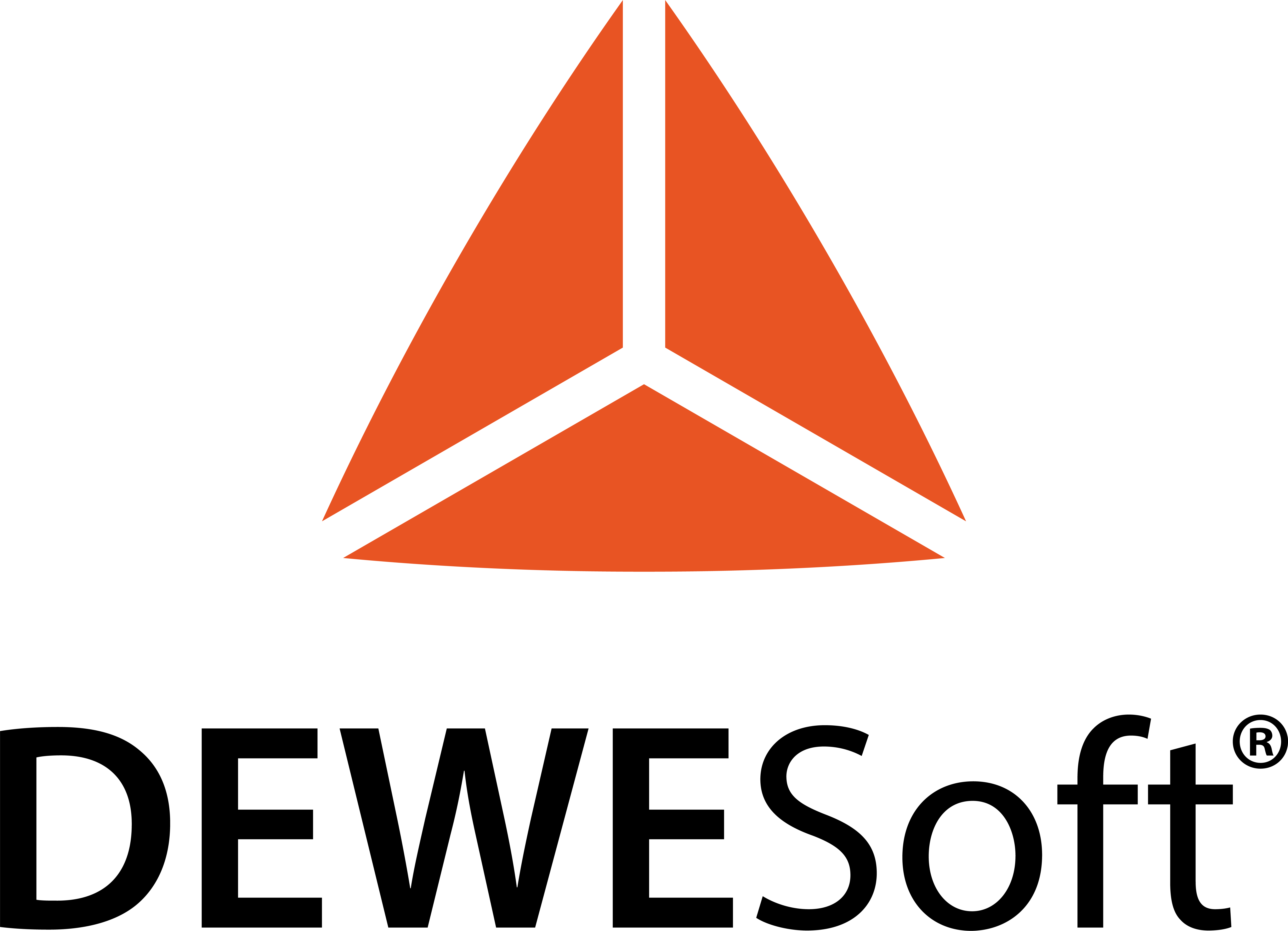
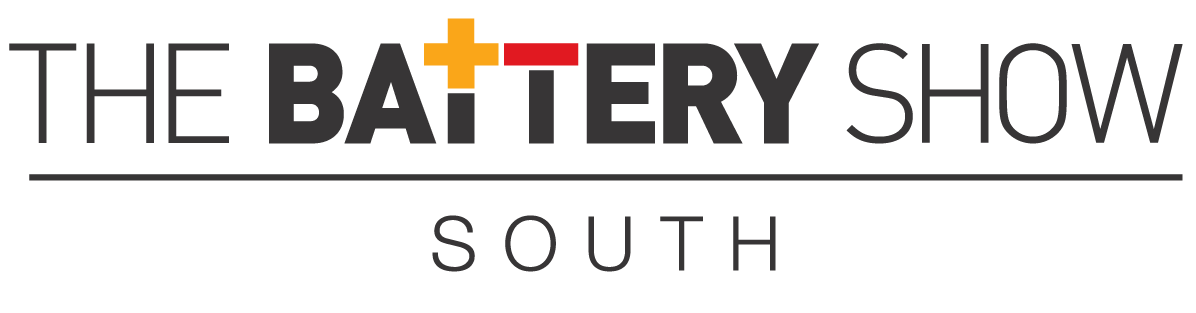
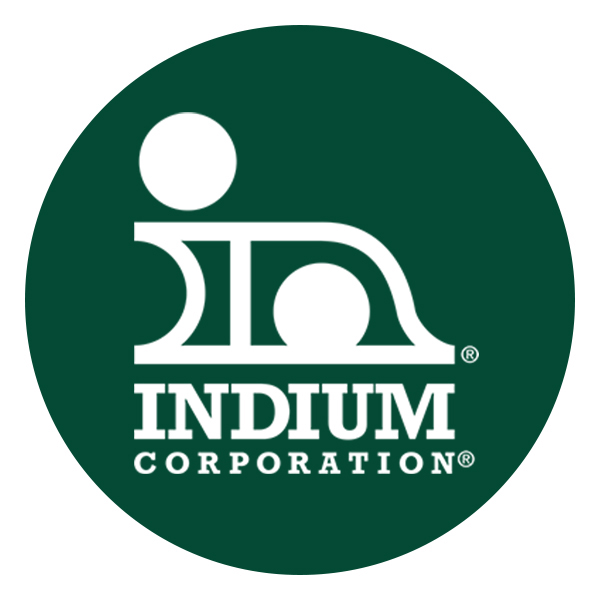
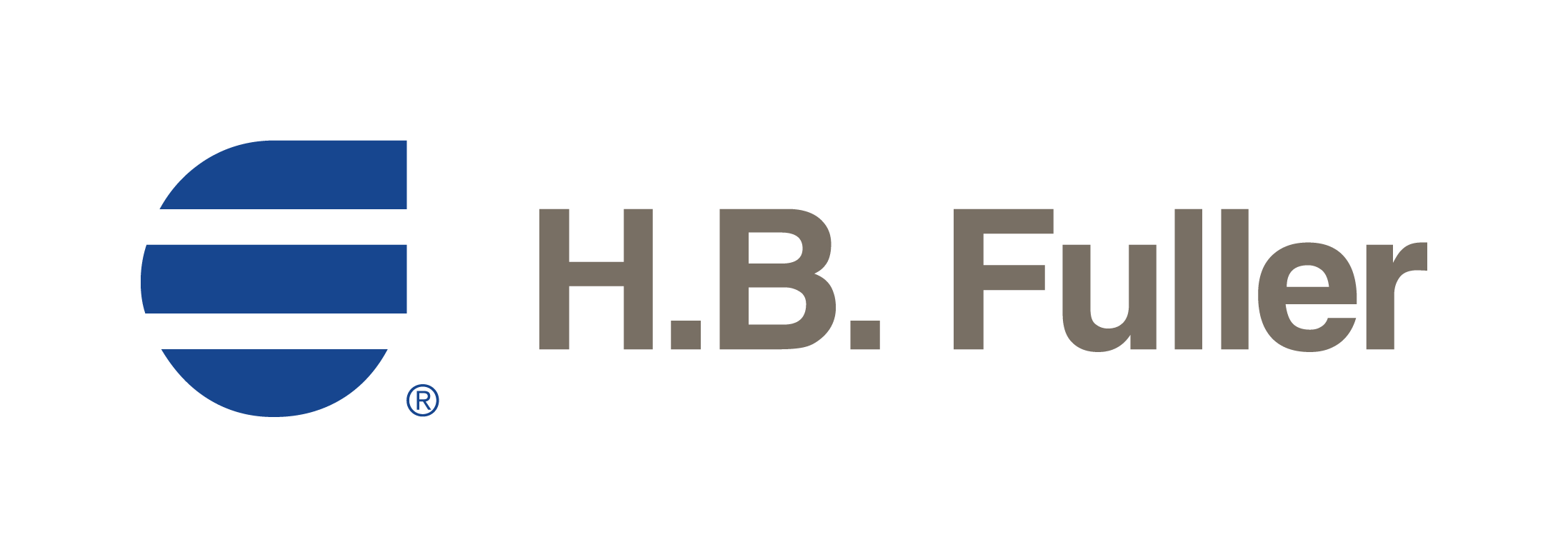