Lofstom Loop
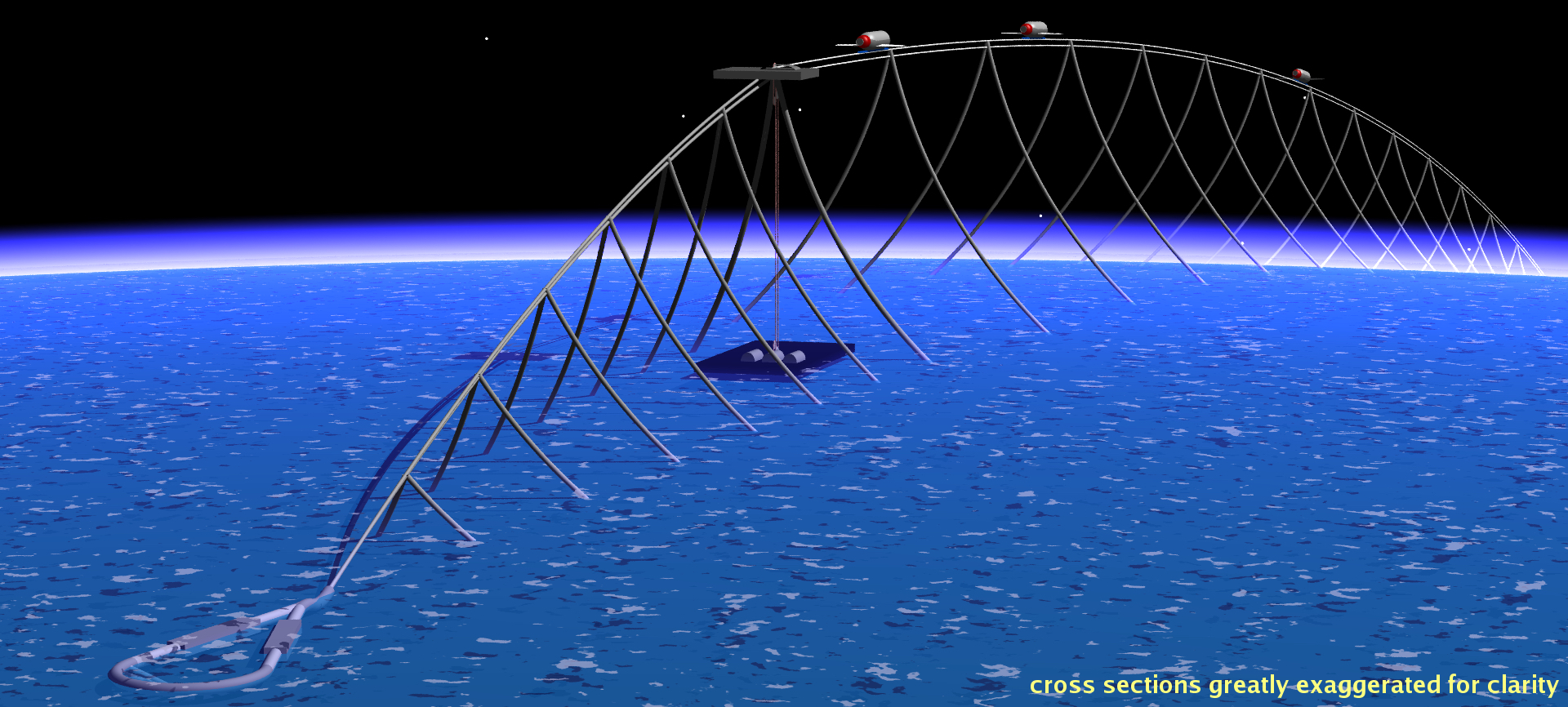
Several electric revolutions have shaped society down the years, from the construction of national grid systems and electric train, trams and trolley buses to the ongoing hybrid and BEV revolution (writes Peter Donaldson).
Even beyond Earth, electric propulsion is a reality for many satellites and planetary probes, although their extremely efficient ion thrusters and so on are all low-power devices incapable of developing the thrust needed to lift a spacecraft out of a gravity well.
Nonetheless, futurists have proposed several ways of using electric power to do just that, all of which involve some combination of linear motors and active megastructures. One of these is the Lofstrom loop, a spindly runway 80 km high and about 2000 km long that promises to launch payloads into Low Earth Orbit (LEO) for a few dollars per kilo – three orders of magnitude less than the $1500/kg or so of today’s cheapest rocket, the SpaceX Falcon Heavy.
Active structures require constant motion and therefore power input to remain stable. Perhaps the most familiar example would be a stream of water from a hose held at an upward angle and bouncing off a plate to keep it off the ground. As long as enough water keeps flowing fast enough, the plate stays aloft. That takes a lot of energy to run, but the benefit is that it enables the creation of structures far larger than any that have only passive support provided by the strength of their materials.
First described in principle by Keith H Lofstrom in a 1985 paper for the American Institute of Aeronautics & Astronautics, the Lofstrom loop is based on this principle, but replaces the stream of water with a flexible segmented tubular iron rotor 5 cm in diameter that is driven by linear motors to support a looped and evacuated tube from the inside, where a magnetic field prevents contact between the rotor and the tube. Given that the rotor reaches a velocity of 14 km/s, any contact with the outer tube would be disastrous.
The tightest curves in the loop’s 5600 km total length are at the two opposite ends on the ground (or under the ocean) where magnets deflect the rotor around a 14 km radius. The linear motors are installed close to where the rotor enters and leaves these deflectors.
Magnets support the launch vehicle above the runway, and the eddy currents that these magnets generate in the rotor create the drag that pulls the vehicle along. The runway’s length was chosen based on the velocity required to get into orbit and the acceleration that human passengers can comfortably withstand for minutes at a time.
For example, to achieve a 300 km LEO altitude requires acceleration at 1.41 g for 8 minutes, 57 seconds, imparting a launch velocity of 7451 m/s; the vehicle still needs a small rocket motor to circularise its orbit. The loop’s height puts it above most of the atmosphere to minimise drag while leaving enough above it to provide protection from most meteorites and space debris. It is powered and deployed from the ground, it can be built with available engineering materials and it can launch thousands of tons per day to high orbit.
In 2009, Lofstrom calculated that at 85% usage, a 4 GW loop could launch 750,000 tons a year for a gross cost per kilo of $3, assuming $9 billion in capital costs amortised over 5 years and 1.3 cents per kWh for energy. One suggested use of such a loop is to help construct an even larger space-access active megastructure known as an orbital ring connected to the ground by an electric railway.
ONLINE PARTNERS
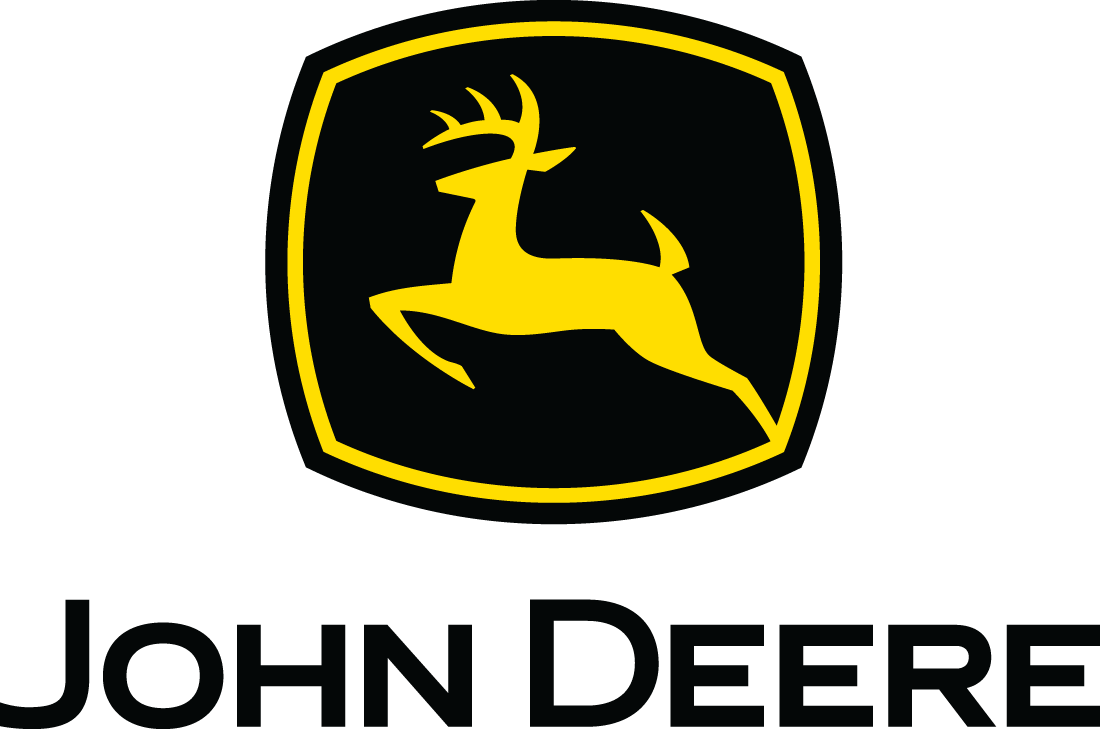
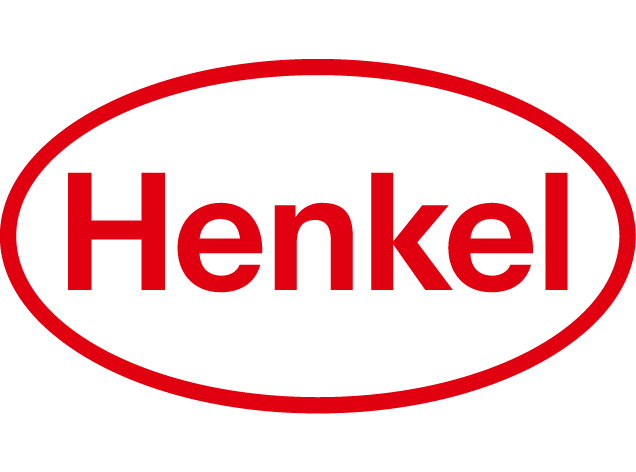
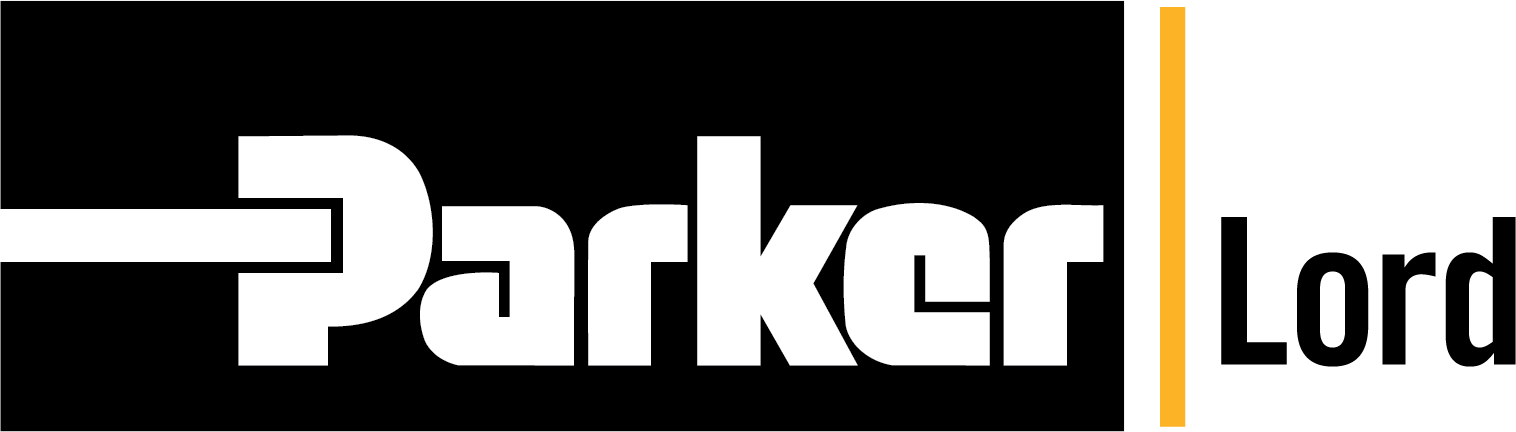
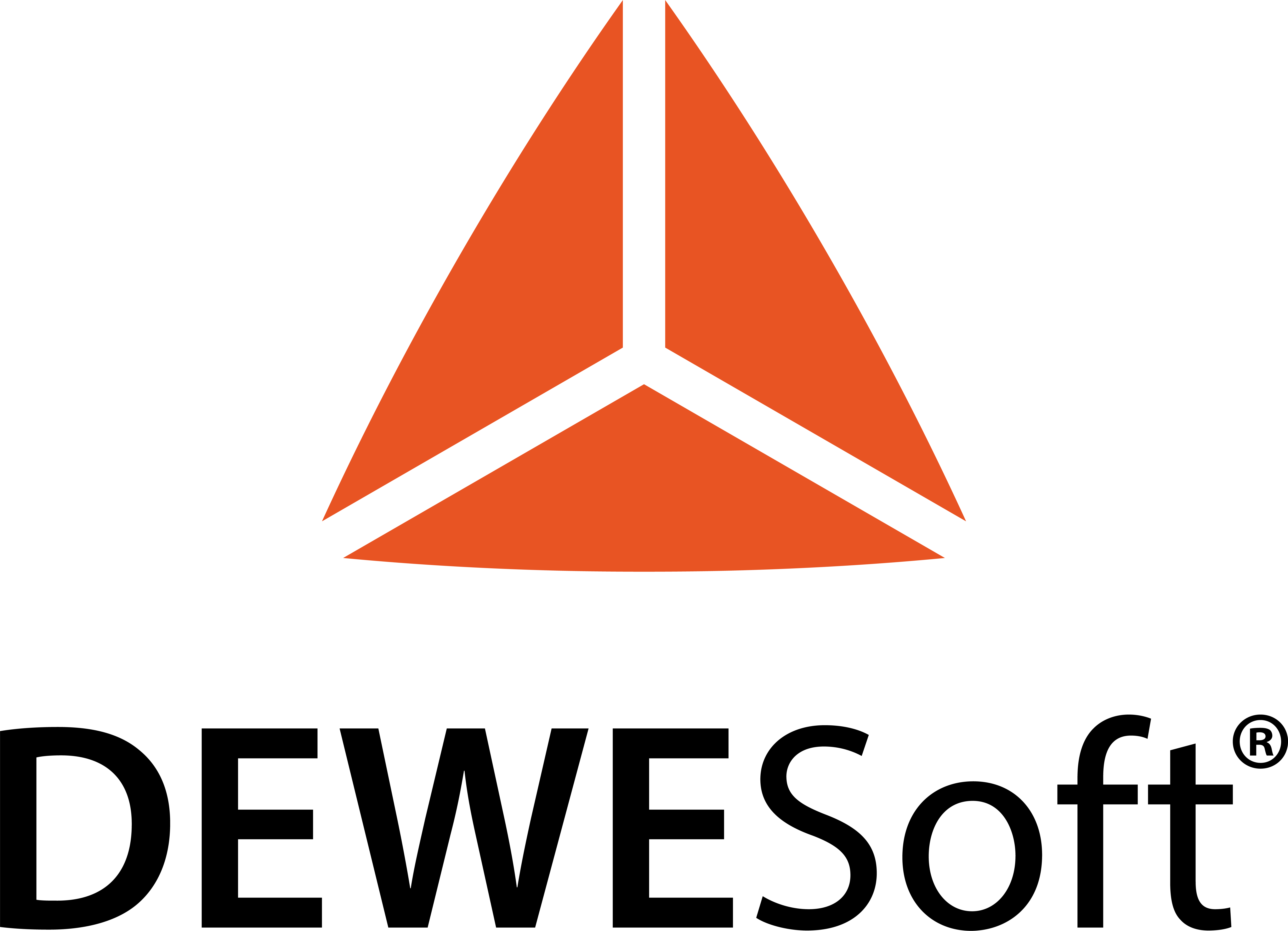
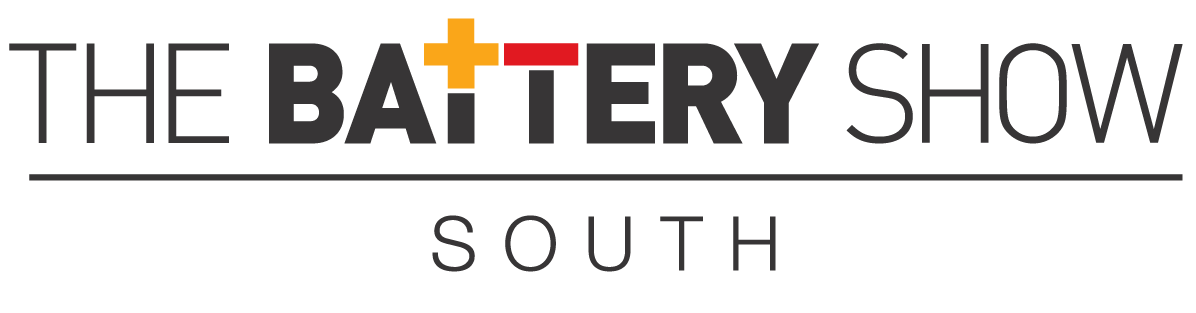
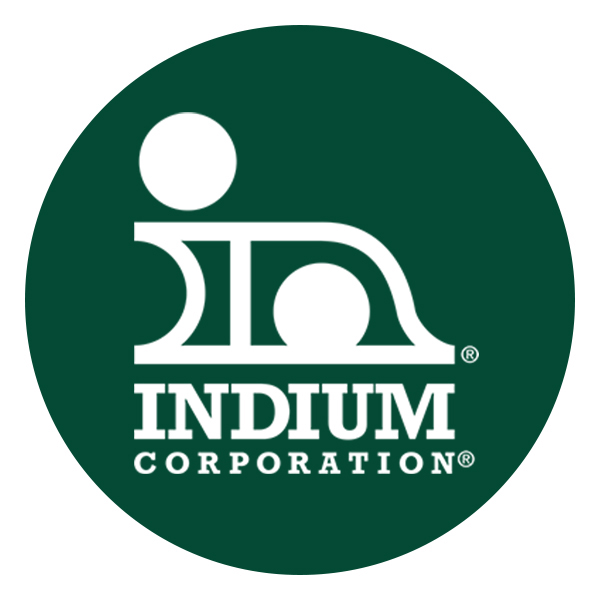
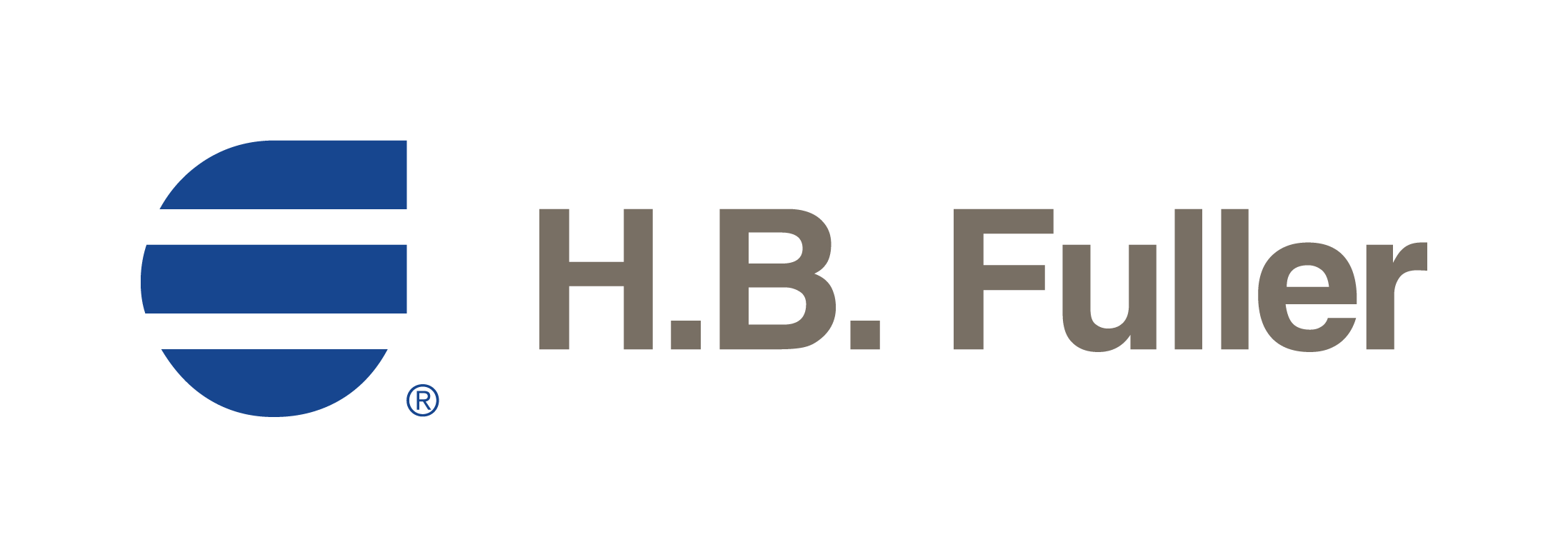