Lithium iron phosphate batteries
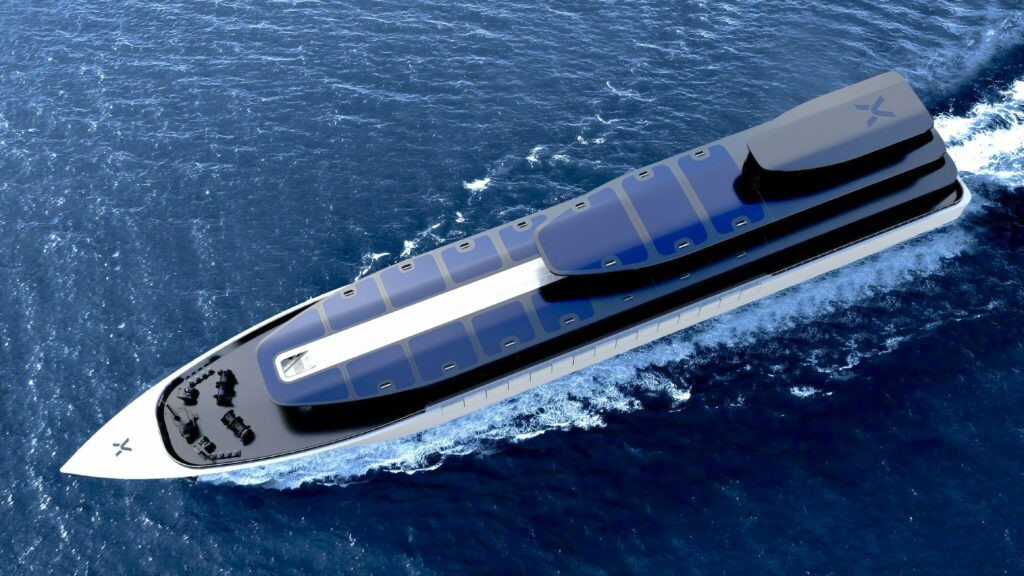
(Courtesy of PowerX)
New kit on the block
Developments in LFP technology are making it a serious rival to lithium-ion for e-mobility, as Nick Flaherty explains
Lithium-ion batteries have some disadvantages for e-mobility that cannot be ignored, such as lower safety and higher cost than other chemistries. At the same time, improvements in battery pack technology in recent years have seen the energy density of lithium iron phosphate (LFP) packs increase to the point where they have become viable for all kinds of e-mobility applications from vehicles to new types of shipping such as so-called battery tankers.
LFP was developed at the University of Texas in the 1990s, using triphylite, a natural mineral of the olivine family. The first cells were built in 1996, with LiFePO4 cathodes, a graphite carbon electrode and a metallic backing as the anode.
The cells have a lower energy density than NMC and NCA lithium-ion cells, typically 125 Wh/kg increasing to 160 Wh/kg with improved packing technology, which has limited their use in e-mobility.
As the technology improves, however, the low-temperature operation of LFP cells, their fast charging and long cycle life are making them more appealing for a range of applications. They are now being used for electric cars as well as electric shipping called battery tankers that can transport power from island to island.
There are several challenges with LFP for high-power applications though, owing to the unique crystal structure of LFP. First, its FeO6 octahedra shares edges with two LiO6 octahedra and one PO4 tetrahedra, resulting in low electronic conductivity.
Second, lithium-ion diffusion in LFP is through a 1D diffusion channel, which is low in diffusivity and easily affected by the Li/Fe mixing. To overcome the low ionic and electronic conductivity issues, approaches have therefore been adopted in the material design, such as reducing particle size or directional crystal growth, conductive layer coatings and element doping.
Nanosized particles can also reduce the diffusion length for the lithium ions, improving the rate capability, while carbon coating is an effective way to improve material electronic conductivity from 10– 9 S/cm to 10 – 2 S/cm. Element doping helps to improve the electronic conductivity and thermal stability as well.
Comparing LFP and NMC 811 shows that both types of cathode active material shine in different key characteristics. The higher cell voltage, powder density and specific capacity give NMC a clear advantage in terms of volumetric energy density for long driving ranges.
By contrast, LFP has a longer cycle life, better rate capability and safety. The risk of thermal runaway after a mechanical damage to a cell is also much lower, which has made LFP especially popular for commercial vehicles that have frequent access to charging, such as buses, forklifts and scooters, says Dr Stepan Schwarz of IBU-tec advanced materials in Germany.
The cells can also be safely charged to 100% in each cycle, rather than having to stop at 80% to avoid overcharging, as in NMC cells. This can simplify the battery management algorithms but there are other complexities for BMS systems in managing LFP cells.
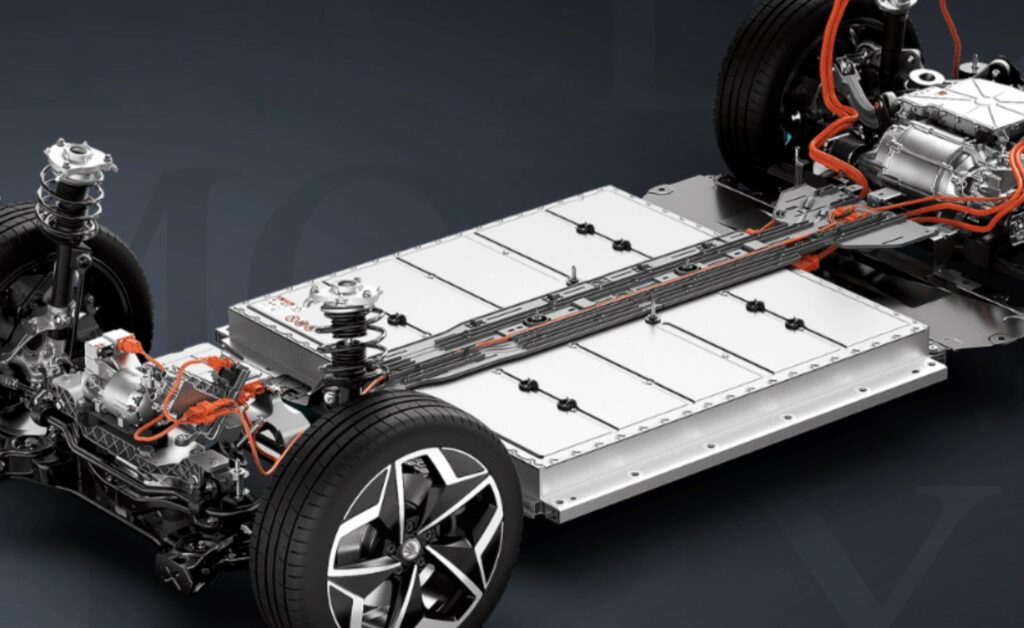
(Courtesy of LG Energy Solutions)
Although LFP has a major advantage in terms of thermal stability and cost, the hysteresis characteristics in the state of charge-open circuit voltage (SoC-OCV) curve and the difficulty and accuracy of estimating the SoC affect the BMS development. Typically, the ampere-hour integration algorithm is used to estimate the SoC of LFP batteries but it fails to meet the accuracy requirements owing to cumulative long-term errors.
The fact that the anodes in an LFP cell do not use cobalt and nickel is also a key advantage for car makers, as there are fears that these will be more difficult to source in the coming years. Although mining of both commodities is projected to double by 2030, it is not expected to meet the increase in demand.
This is making LFP increasingly interesting for a range of e-mobility applications. Cells are being developed with a range of materials and in new hybrid battery pack architectures. Tesla for example is using LFP for standard-range vehicles, while Volkswagen and Mercedes-Benz are planning to adopt LFP technology in their future cars.
The cells also have a much longer cycle life than NMC. That means they are suitable for second-life applications such as stationary storage on solar or wind farms when the e-mobility capacity drops below 80%.
One power-grade material for LFP cells is IBUvolt LFP400, which was developed for passenger vehicles and maritime environments. Compared with other LFP grades on the market, IBUvolt LFP400 has a much higher carbon content says Dr Schwarz, which leads to a much better conductivity and, as a result, to a low DC resistance, addressing two of the key challenges.
“At 5C charging rate an SoC of more than 80% can be achieved,” he says. “This positions LFP well for fast-charging applications, especially for vehicle batteries relying on it for economic reasons, where fast charging can compensate for the lower range that comes from using LFP when compared to batteries with higher energy density, such as NMC.”
Improvements to the LFP chemistry include adding manganese to create LMFP (lithium manganese iron phosphate) cells. These have higher volumetric energy densities to further establish these materials in the price-sensitive high-volume designs.
LFP is also a promising candidate for solid-state cells. For example, Freyr Battery in Norway is building LFP cells using ‘semi-solid’ gel electrolytes developed by 24M, a spin-out from the Massachusetts Institute of Technology.
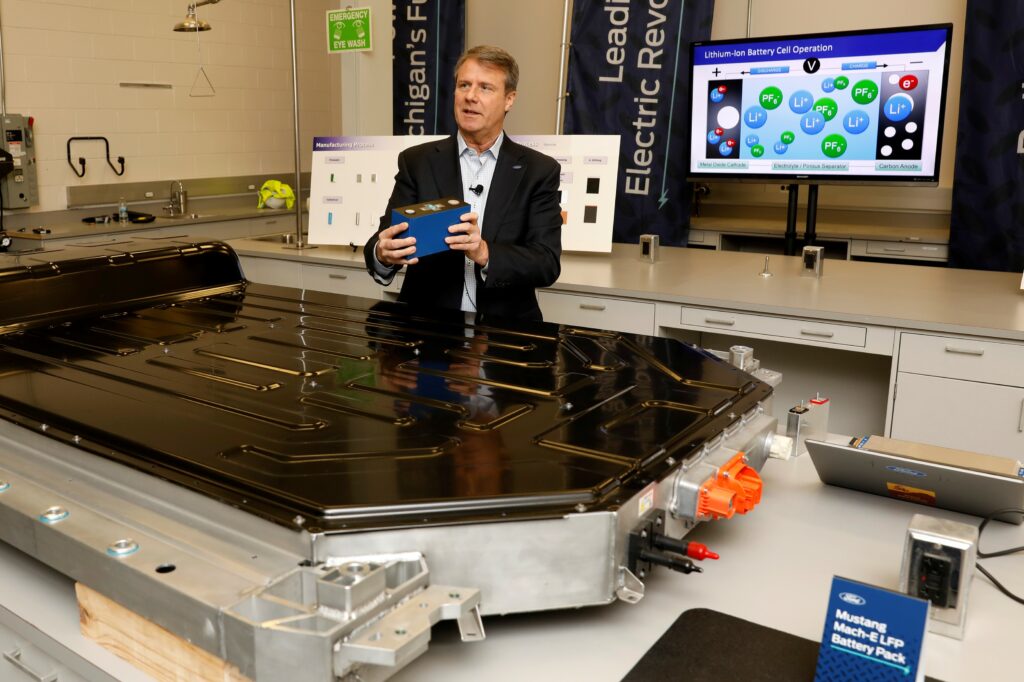
(Courtesy of Ford)
Battery management
Because of the wide range of driving conditions and variations in cells, it is difficult to accurately determine battery pack capacities in EVs by using predictive models or even direct measurement. That makes precise pack capacity estimation in EVs by the BMS a challenge.
Researchers have therefore turned to a wide range of techniques, from stochastic fuzzy neural networks and adaptive neuro-fuzzy inference systems to neural networks such as recurrent neural networks and fed-forward neural networks. More recently, deep learning techniques have also been considered during the SoC estimation, learning from test data. This can make the BMS algorithms independent of the type of chemistry and so support LFP.
Also, an adaptive extended Kalman filter (EKF) can be used to estimate model parameters including OCV, combining the updated OCV with an EKF to estimate the SoC. Reconstructing the SoC-OCV curve based on historical experimental data and incorporating a parameter backtracking strategy can reduce parameter jitter.
The OCV curve can be updated with temperature changes and battery ageing, and finally the SoC estimation is based on the updated OCV curve combined with an EKF. However, this is not accurate enough for LFP with periods of voltage plateau and hysteresis.
In one study, researchers in China have been looking into the charging cell voltage curves for estimating LiFePO4 battery pack capacities in EVs, and have developed a generic algorithm to find the optimum transformation parameter for overlapping voltage cell voltage curves.
A small battery pack with four LiFePO4 cells in series is used to verify the method, and the result shows that the estimation errors of the pack and cell capacities are less than 1%. This allows the LFP battery pack capacity to be precisely estimated to more accurately predict the available range or operating time and
Capacity variations of series-connected cells directly influence the pack capacity, so estimating the precise pack capacity has to consider variations in cell capacity. The initial pack capacity can be calculated using data from standard tests, but the pack capacity changes as cell capacities fade, rendering the measured initial pack capacity meaningless.
Materials challenges
Many cell makers want to produce their own LFP materials. This can require a complex thermal process with rotary kilns and pulsation reactors, as well as ancillary equipment for pre- and post-processing.
To address that, researchers in Russia, at Skoltech, have studied the hydroxyl (OH) defects in LiFePO4, to help improve its manufacturing process.
“It is well-known that LiFePO4 materials usually have a considerable amount of Li/Fe anti-site defects,” says Senior Research Scientist at Skoltech, Dmitry Aksyonov. “This is a type of point defect when lithium and iron atoms exchange their positions in the crystal lattice. However, before our work, nobody had assumed that the PO4 part can also be an active defect mechanism in this material.
“We discovered that in some cases the PO4 anion can be substituted by four or five OH groups, which has a negative effect on electrochemical performance of LiFePO4-based batteries. Such defects are called OH defects, or more specifically hydrogarnet-type hydroxyl defects.”
The Skoltech team used a combination of computational modelling and experiments to combine the density functional theory and neutron diffraction to study OH defects in LiFePO4. They were also able to confirm their results experimentally in an LiFePO4 sample.
“Hydrogarnet OH defects are well-known in geology, but not so much in materials science,” Aksyonov says. “The presence of OH defects in LiFePO4 could have been envisaged much earlier by drawing parallels with its structural analogues in the olivine mineral group. Therefore, the biggest takeaway from our work is probably that researchers should seek knowledge not only in their home field but in others as well.”
Since OH defects are not easy to detect, commercially produced LiFePO4 materials can have them as well, he notes, and it is important to have these deteriorating effects under control.
LFP vehicles
LFP is a more recent choice for battery cell technology, but car makers are developing platforms with a programmable battery management systems that can use LFP or NMC.
Xpeng in China for example has used LFP for its mainstream EV with a 60 kWh battery pack and a range of 480 km; This compares to 70 kWh for the version with an NMC pack, which has a range of 586 km. The DC fast-charging time is similar, at around 30 minutes, but the AC charging for the LFP pack is slightly longer, an extra 40 minutes in 5 hours. The EV with the LFP pack is also 50 kg heavier.
Separately, XPeng launched a version of its G3 460c car with an LFP battery pack that has the same driving range of 460 km as the original NMC-powered version. Xpeng is also using the technology for a third vehicle range, an SUV, that adds bidirectional charging.
This SERES 5 SUV has options of an 80 kWh LFP pack or a 90 kWh semi-solid state high-performance NMC pack, giving it a range of 500 km with both options. The packs are compatible with 95% of the charging systems in Europe, and support a smart fast-charging system with a quick recharge to shorten the waiting time.
A bidirectional function Xpeng calls “vehicle-to-load” can provide power to travel appliances such as induction cookers and coffee makers, while a vehicle-to-vehicle function can also help charge other people’s EVs in an emergency. To do these is far safer using LFP cells, as the power requirements are different from driving.
Ford is also adopting LFP technology, from CATL in China, building NMC as well as LFP batteries in the US. LFP will be used first in the Mustang Mach-E, then in the F-150 Lightning truck in 2024 to increase LFP production capacity to supply the rest of Ford’s EV range. Ford sees LFP batteries as being less expensive to produce than NCM ones, while providing more frequent and faster charging and using fewer high-demand, high-cost materials.
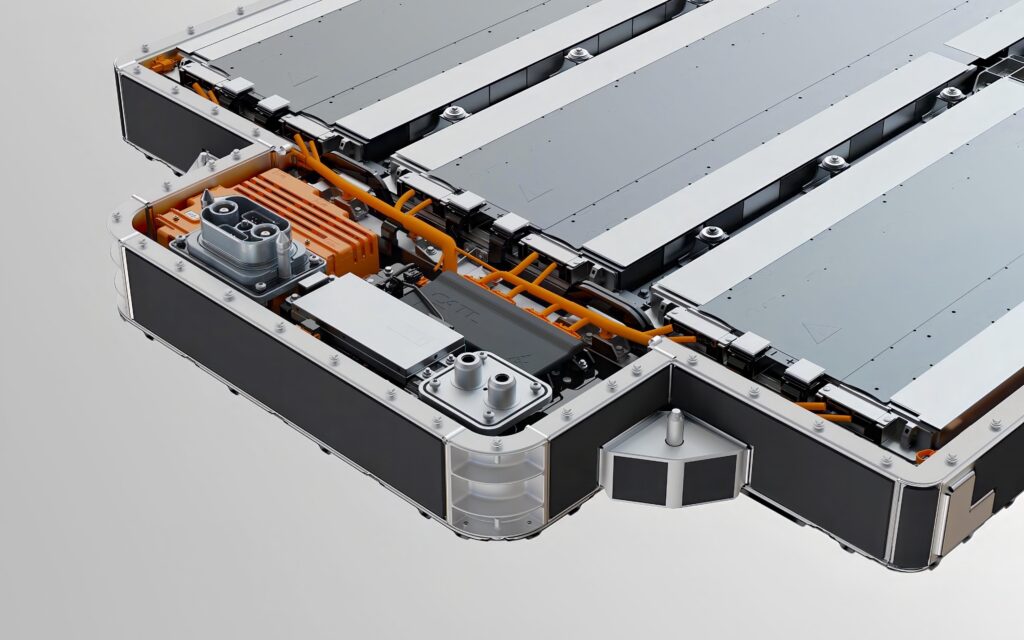
(Courtesy of NIO)
Hybrid packs
Another Chinese car maker, NIO, has launched a range with a 75 kWh hybrid battery pack consisting of LFP and NMC cells. They are due to ship in November this year.
The pack uses NIO’s patented CTP technology, which integrates the cells directly into the floor of the vehicle rather than using modules. This eliminates the side and end plates as well as the supporting structures that were used to support the modules. This simplifies manufacturing and assembly by 10%, increases volume use by 5%, and increases energy density by 14% to 142 Wh/kg, says NIO.
Using LFP gives extended range in cold weather, and more accurate SoC estimates from the BMS give a battery performance at the same level as NMC, says NIO.
NIO has also designed a complete thermal management software and hardware system for the standard-range battery, using the energy from the LFP pack to warm up the NMC batteries. This reduces the loss of range in low temperatures by 25% compared to a pure LFP counterpart.
The thermal management system, which NIO calls an environment shielder, uses low thermal conductivity materials and the structural design of the pack to channel heat from the LFP cells in extremely cold environments to the NMCs, improving the passive thermal insulation performance.
The intelligent thermal system dynamically adjusts the amount of heat travelling to the NMC cells to avoid overheating and balance the responsiveness of the cells with the energy consumption. A radiant thermal compensation heater heats the battery cells uniformly to maintain the battery’s working temperature while taking into account its energy consumption.
A dual-chemistry algorithm controls the performance of the NMC and LFP cells in low temperatures to improve the energy efficiency of the whole battery system. This includes a hybrid cell battery SoC estimation system developed by NIO that reduces the estimation error to less than 3%, reaching the same level of accuracy as a standard BMS for an NMC pack.
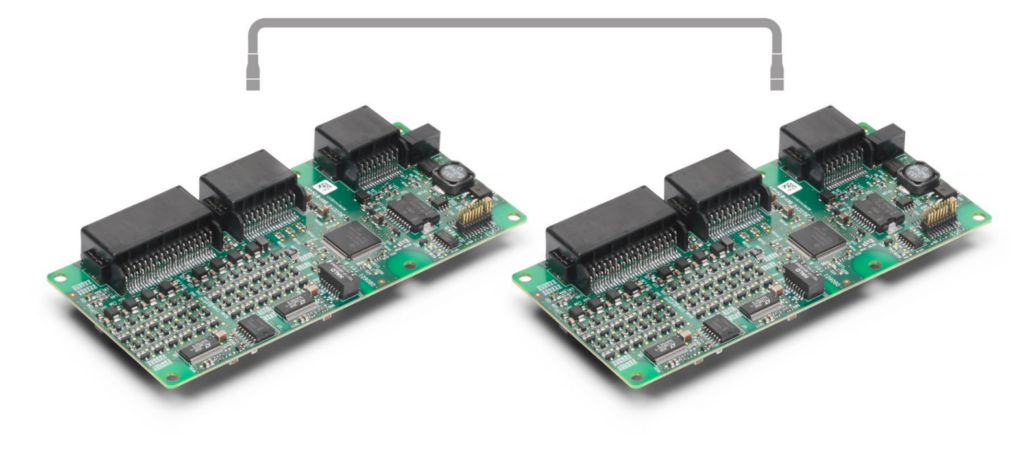
(Courtesy of Sensata Technologies)
Hybrid BMS
However, developing a BMS for a hybrid pack is not simple, as the electrochemical properties of the two batteries are very different. This is a particular challenge for estimating the SoH of each cell.
To address that, researchers in the College of Mechanical Engineering at the University of Shanghai have used fuzzy logic with a “difference state observer (DSO)” and continuous feedback correction to monitor an LFP cell in comparison to the NMC cells in the pack. Results from experiments with an LFP connected to a 200 Ω resistor to simulate the self-discharge difference, along with sensor errors, showed the algorithm can control the LFP’s SoC estimation error to about 1%.
The underlying algorithm is also robust, achieving an SoC estimation error of within 2% when there are both current and voltage sensor errors.
First, a conventional algorithm is used to achieve an accurate SoC estimate for the NMC cells, and the LFP’s SoC is directly mapped according to the principle of series cell electricity equivalence as its short-term SoC estimation result.
Self-correction of the SoC of the LFP cells is then performed at full charge as well as the calculation of the state discrepancy amount. The continuous feedback correction of the LFP uses the difference state observer with fuzzy logic and is combined in a capacity scatter diagram. This enables accurate SoC estimation from the cell level to the hybrid pack level.
Sensata Technologies has also developed a BMS that supports up to 24 cells in series and 2000 A for scooters, three-wheelers and electric forklifts.
A single c-BMS24X BMS can be used with up to 10 battery packs in parallel, and has an automatic contactor control to avoid high inrush current. It is designed to enable quick and easy exchange of depleted batteries with fully charged ones in parallel battery packs.
Proprietary ‘SoX’ algorithms measure and predict the SoC, SoH, state of power and state of energy of the battery with a high degree of accuracy and provide higher levels of fault tolerance and robustness than the previous BMS systems. They are designed to balance cell chemistries such as LFP and hybrid applications, where determining the balancing requirement is difficult and would normally be less precise the longer the battery has not been through a full charge-discharge cycle.
It also includes support for battery heater management and an automatic sleep mode for low power consumption in idle state.
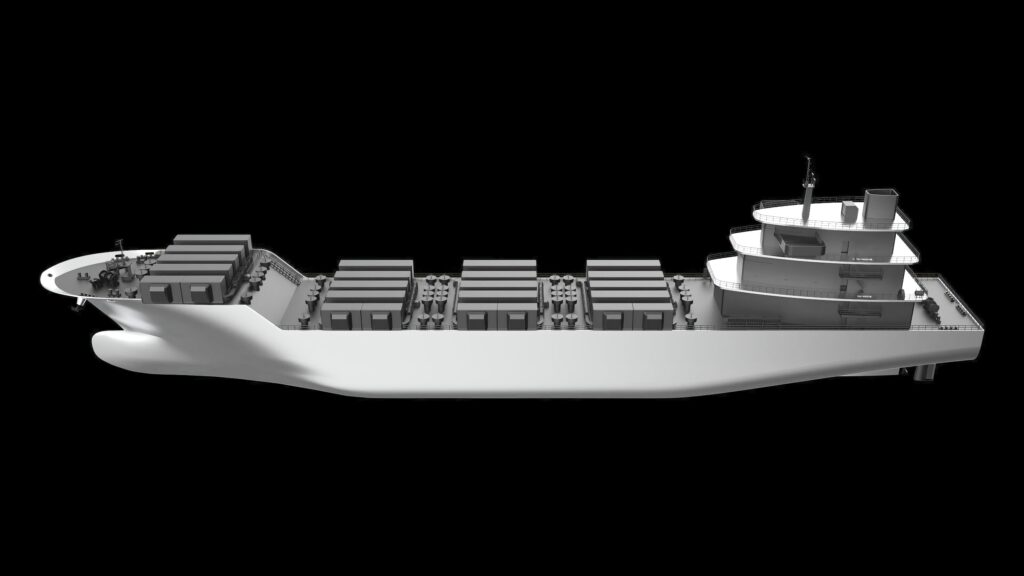
(Courtesy of PowerX)
Marine
LFP really comes into its own however in colder environments and for shipping.
In one study, researchers at the Pacific North West National Laboratory (PNNL) in the US compared the most commonly used lithium-based battery types – NCM, NCA and LFP – in laboratory conditions. The experiments emulated a battery enclosure thermally coupled to freezing seawater using an industrial battery performance tester in PNNL’s Arctic simulation lab. The battery strings were repeatedly cycled to determine the usable capacity.
Both NCM and NCA strings exhibited degradation after cycling, while the LFP string maintained stable operation for more than 700 complete cycles. Although the initial capacity of the LFP cells is lower, this stability is key for LFP in low-temperature marine applications.
Each battery string was cycled through 10 runs of a baseline protocol at room temperature to verify performance under standard operating conditions. When charged at 0.5C and then discharged at 2C, the reversible discharge capacity was identical to that at 0.1C rate.
The only difference observed was on the charge-discharge plateaus, where higher charging and lower discharging voltage curves were observed at elevated C-rates. This is a normal phenomenon for batteries, and is ascribed to the increase in electrochemical polarisation at elevated current densities.
At room temperature, the LFP string showed very stable cycling stability without seeing any decay of capacity or voltage plateau. Very similar behaviours were observed for the NCA and NCM cell strings, with almost identical discharge capacities at low and high C rates, as well as stable cycling.
The difference is stark at lower temperatures though. One interesting observation by PNNL is that when operated at high currents – that is, 2C discharge rate – the LFP cell string has a much higher reversible capacity (about 1.05 Ah) compared to low-speed charging at 0.1C. This is due to the heat generation and propagation at high current densities.
The LFP string showed exceptional cycling stability at a temperature of 2.4 ºC, even showing a slight increase in capacity as the heat generation at high C-rate helps to warm up the cells and enhances capacity release. For cycling stability, the NCA string showed inferior performance in terms of discharge capacity and voltage, degrading after 200 cycles to a capacity retention of 72%.
Along with the fading capacity, the NCA cell voltage also showed a gradual decay trend, indicating slow active material degradation or gradual growth of solid electrolyte interface (SEI) on the graphite anode at these low temperatures.
The NCM string’s performance was even worse. The capacity started to decay from the 20th cycle and was completely degraded by the 46th. The string still had a capacity comparable to the original value but lost the ability to deliver current at the 2C discharge rate.
This is usually caused by lithium plating on the graphite anode as a result of reduced lithium diffusion in the graphite anode or across the SEI. The deposited lithium metal reacts readily with liquid electrolyte, leading to cell capacity decay and voltage increase. Cell damage caused by SEI formation is irreversible and progressive, and can cause long-term damage leading to a catastrophic thermal event or loss of battery function.
Shipping
Japanese battery start-up PowerX has shown the detailed design of the first-ever ‘battery tanker’.
The vessel is 140 m long and will be equipped with 96 containerised marine batteries, providing a total capacity of 241 MWh. The onboard battery systems allow it to store and transport surplus electricity generated from renewable sources to other areas where power is needed.
Decommissioned or idle thermal power plants located near ports can be converted into charge/discharge points for the tankers, where the power is transmitted to users over grid connections on the land. For instance, in Japan, a battery tanker could carry power from regions with high renewable energy supply potential, such as Kyushu and Hokkaido, to high-demand areas of Honshu or for inter-island power transmission.
The battery system is based on the PowerX proprietary module design using LFP cells with a lifespan of over 6000 cycles. The design is scalable, allowing additional batteries to be installed to create larger vessels or larger sizes to meet specific mission requirements.
The system includes dedicated gas emission controls and fire suppression mechanisms along with real-time monitoring of the battery system, charging controllers and power conversion systems.
Using a ship avoids issues with malfunctioning or damaged underwater power cables, which are costly to repair, and the costs of ultra-high voltage connections and substations, says PowerX.
The company plans to build the vessel by 2025, and test it in Japan and internationally in 2026.
Conclusion
Developments in LFP cells are making them more compelling to adopt. Avoiding scarcity issues with cobalt and nickel is of course an important issue, but the performance of LFP materials has increased. Coupled with more fast-charging infrastructure being available makes the technology suitable for mainstream consumer vehicles.
Challenges in the development of BMS technology have been addressed, providing acceptable range and fast charging. The BMS algorithms can be updated over the air to bring regular improvements to managing the battery pack.
Low-temperature operation comes into its own in several ways. It opens up new applications in ships at sea and for off-road vehicles in locations where temperature is an issue. It also opens up the development of hybrid packs that combine LFP and NMC cells.
With the advances in hybrid BMS algorithms, this gives vehicle designers the best of both worlds, with low-temperature operation and fast charging as well as the energy to heat up NMC cells for optimum performance.
ONLINE PARTNERS
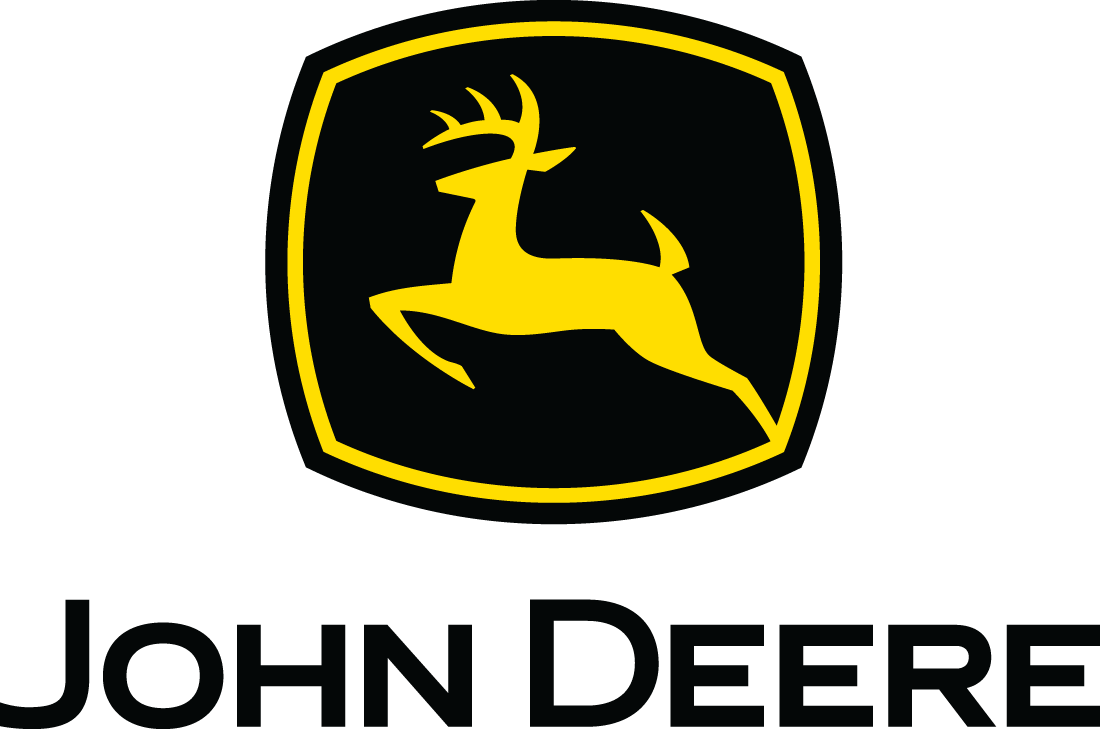
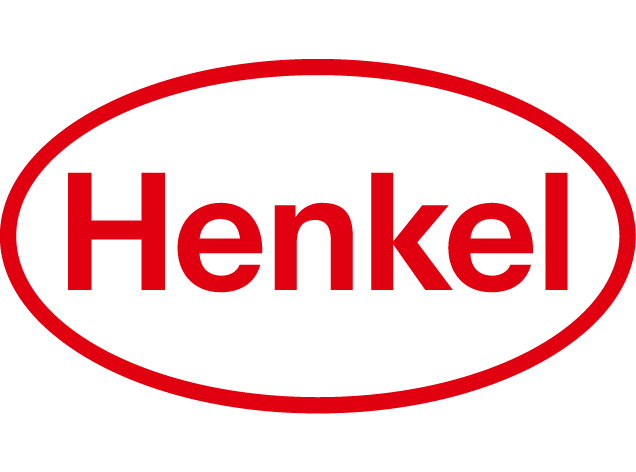
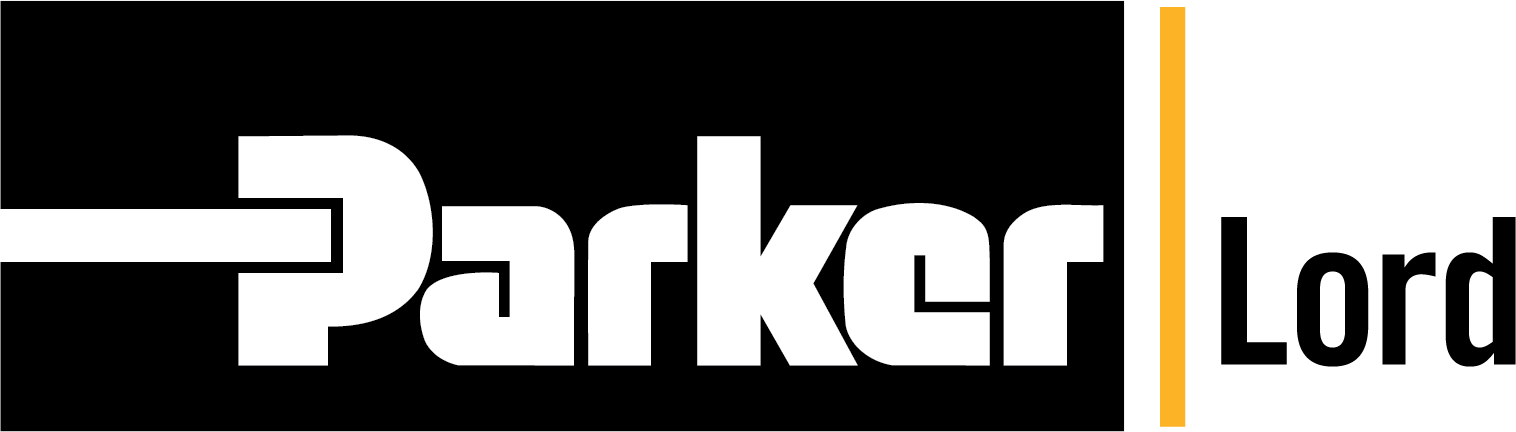
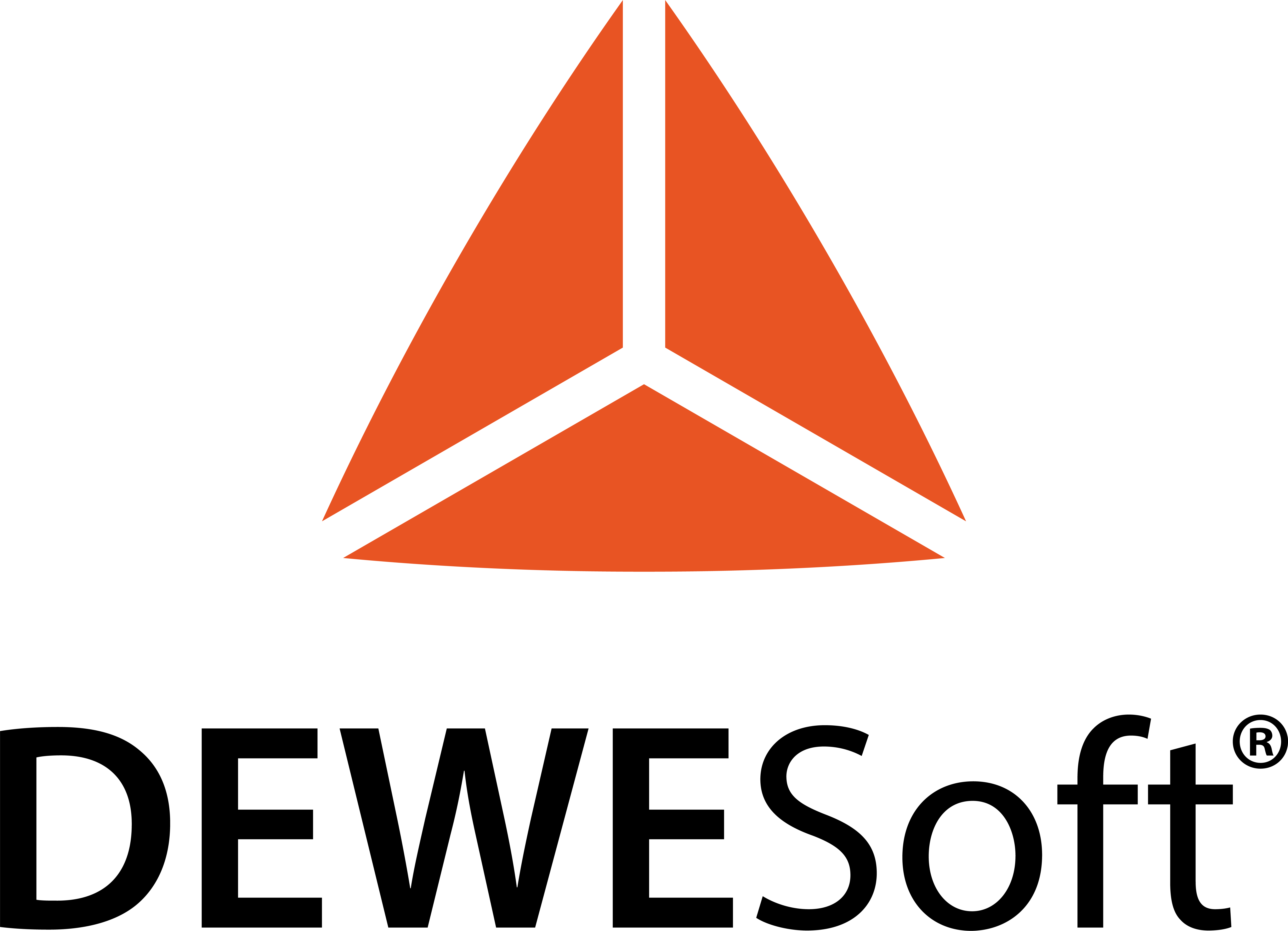
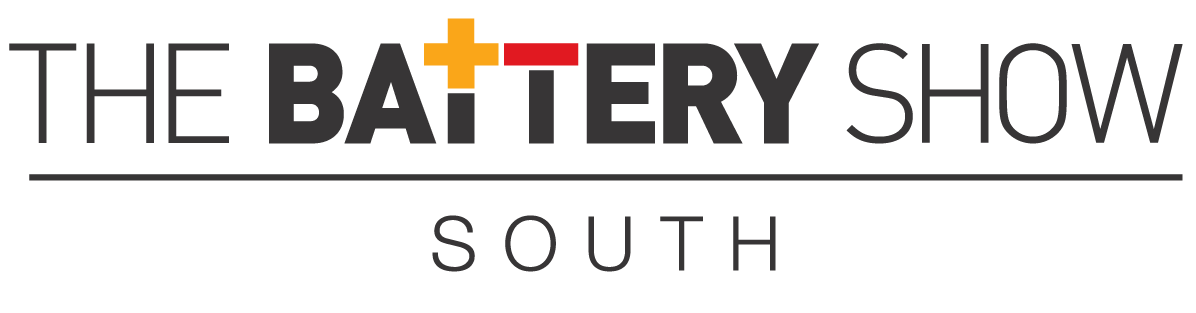
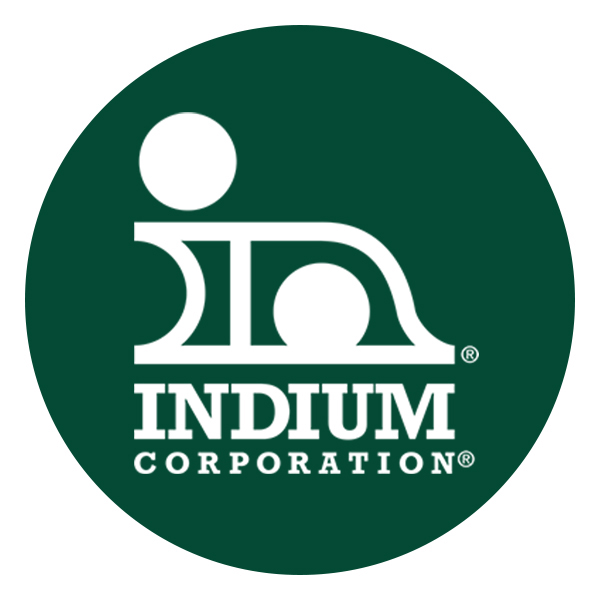
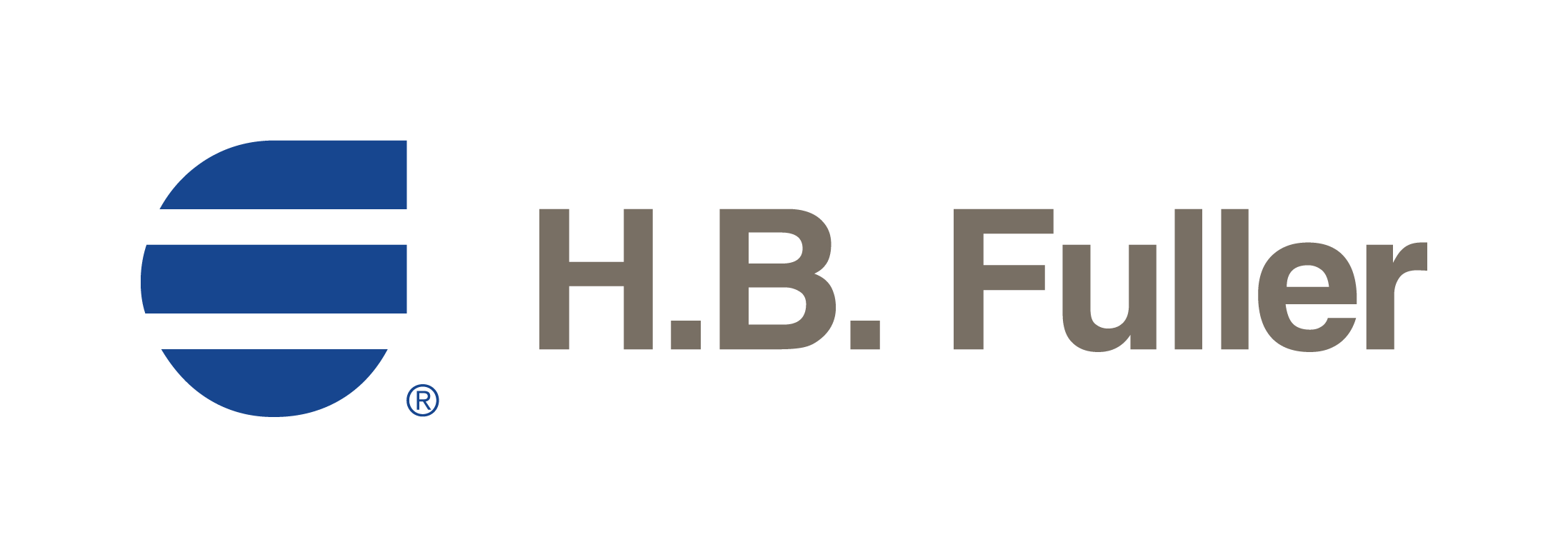