Lithium-air pack beats lithium-ion
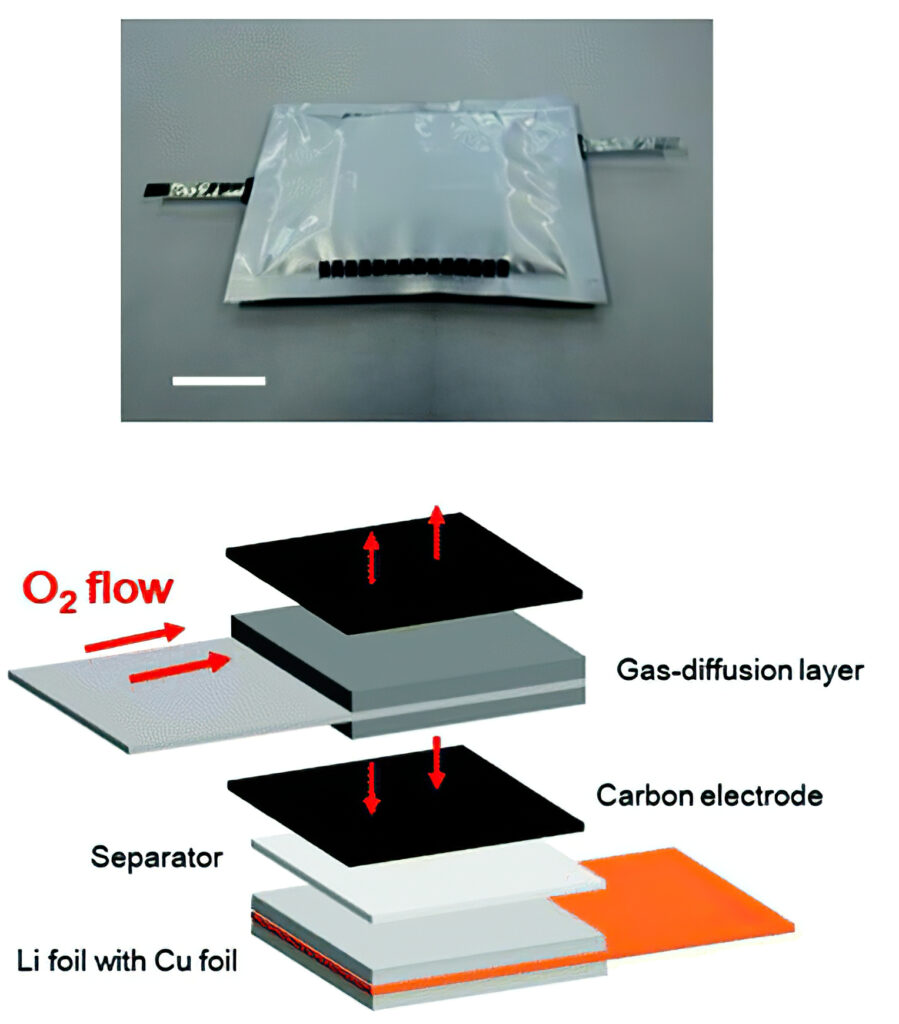
Researchers in Japan have developed a lithium-air battery that has a far higher energy density than current lithium-ion batteries (writes Nick Flaherty).
Lithium-air batteries have the potential to be the ultimate rechargeable packs, as they are lightweight and have high capacity, with theoretical energy densities of 3150 Wh/kg – several times that of the lithium-ion or even solid-state batteries currently available (see page 32 of issue 13).
However, despite the very high theoretical energy densities, only a small number of lithium-air batteries with high energy densities have actually been fabricated and evaluated. This limited success is attributed to the fact that a large proportion by weight of them contains heavy inactive components such as separators and electrolytes that do not directly participate in actual battery reactions.
The National Institute for Materials Science in Japan has been carrying out basic research on lithium-air batteries, and has developed one with an energy density of more than 500 Wh/kg, 10 times higher than other lithium-air systems.
The lithium-air battery works by combining lithium ions with oxygen from the air to form lithium oxide at the anode during discharge.
This makes the development of a stacked cell very different from other batteries that use an electrolyte. In a stacked cell, oxygen needs to be transported in the horizontal direction in the gas diffusion layer. The oxygen then needs to be further transported in the vertical direction to go through the whole part of the positive electrode. That means the development of a gas diffusion layer is highly important for practical implementation as well as cell configuration.
The researchers built a single-layered cell with a 2 x 2 cm electrode as a possible candidate for standard lithium-air cells, in which the oxygen can be transported through the gas diffusion layer in only the vertical direction. By restraining the top and bottom of the cell with a rigid substrate and a spring, the confining pressure of the oxygen inside the cell can be quantitatively controlled.
The key is that the design of this cell can be easily extended to a large stacked type cell configuration by enlarging the electrode size (2 x 2 cm to 4 x 5 cm to 10 x 10 cm) and increasing the number of stacking layers, from a single cell to a two-layer stacked cell to a 10-layer stacked cell.
The team is currently developing higher-performance battery materials, and plans to integrate them into the battery with the aim of greatly increasing the battery’s cycle life. The team then plans to test it in a practical application.
ONLINE PARTNERS
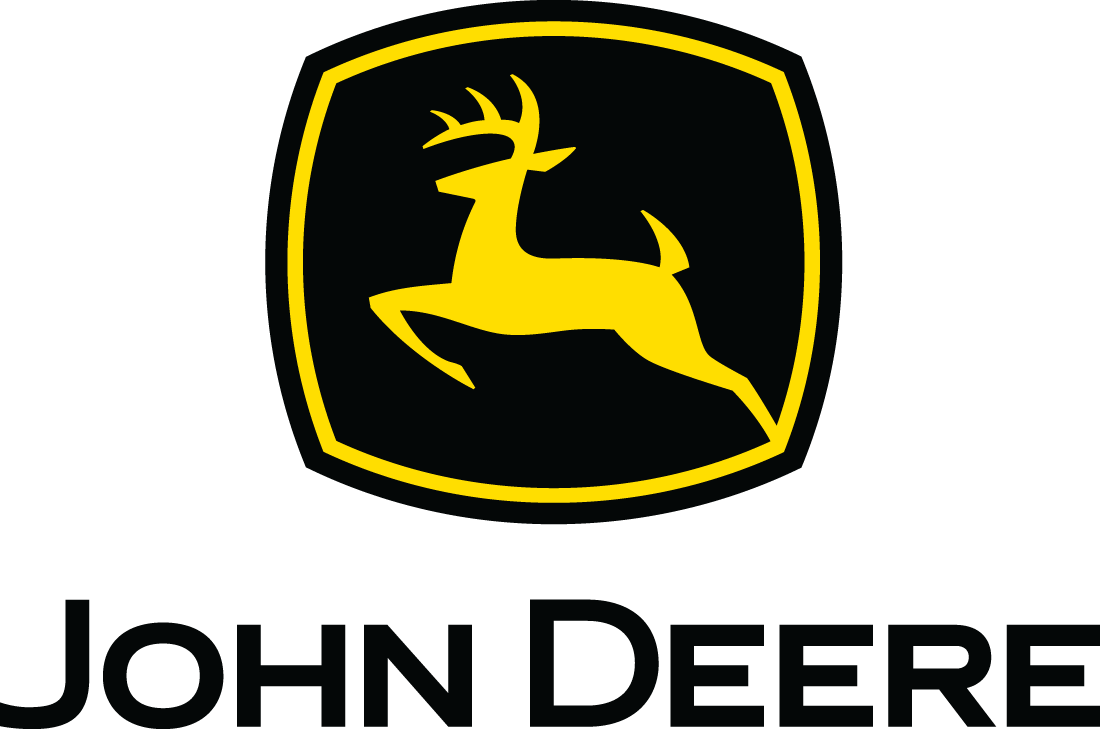
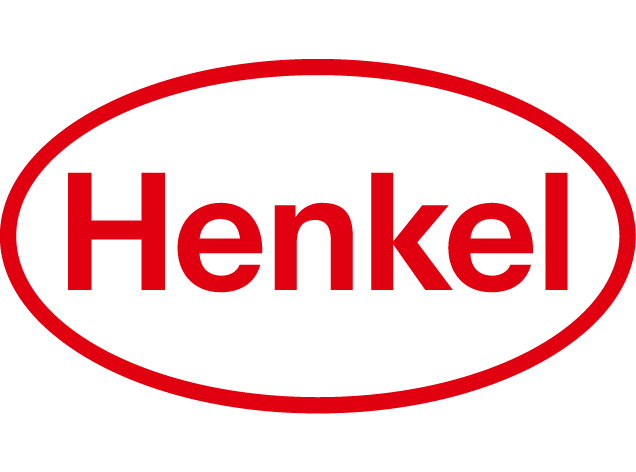
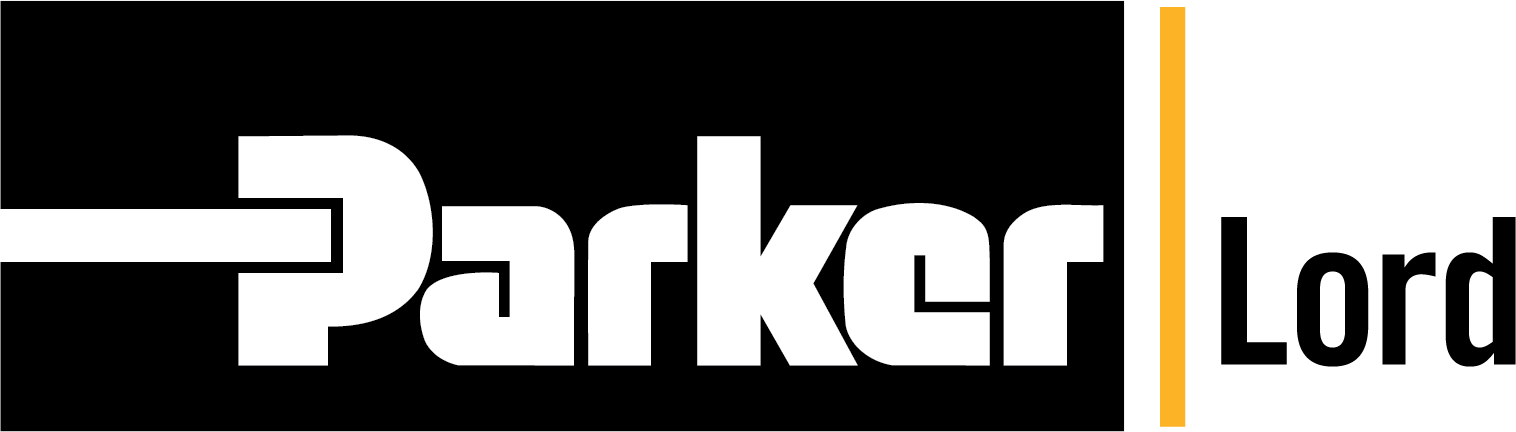
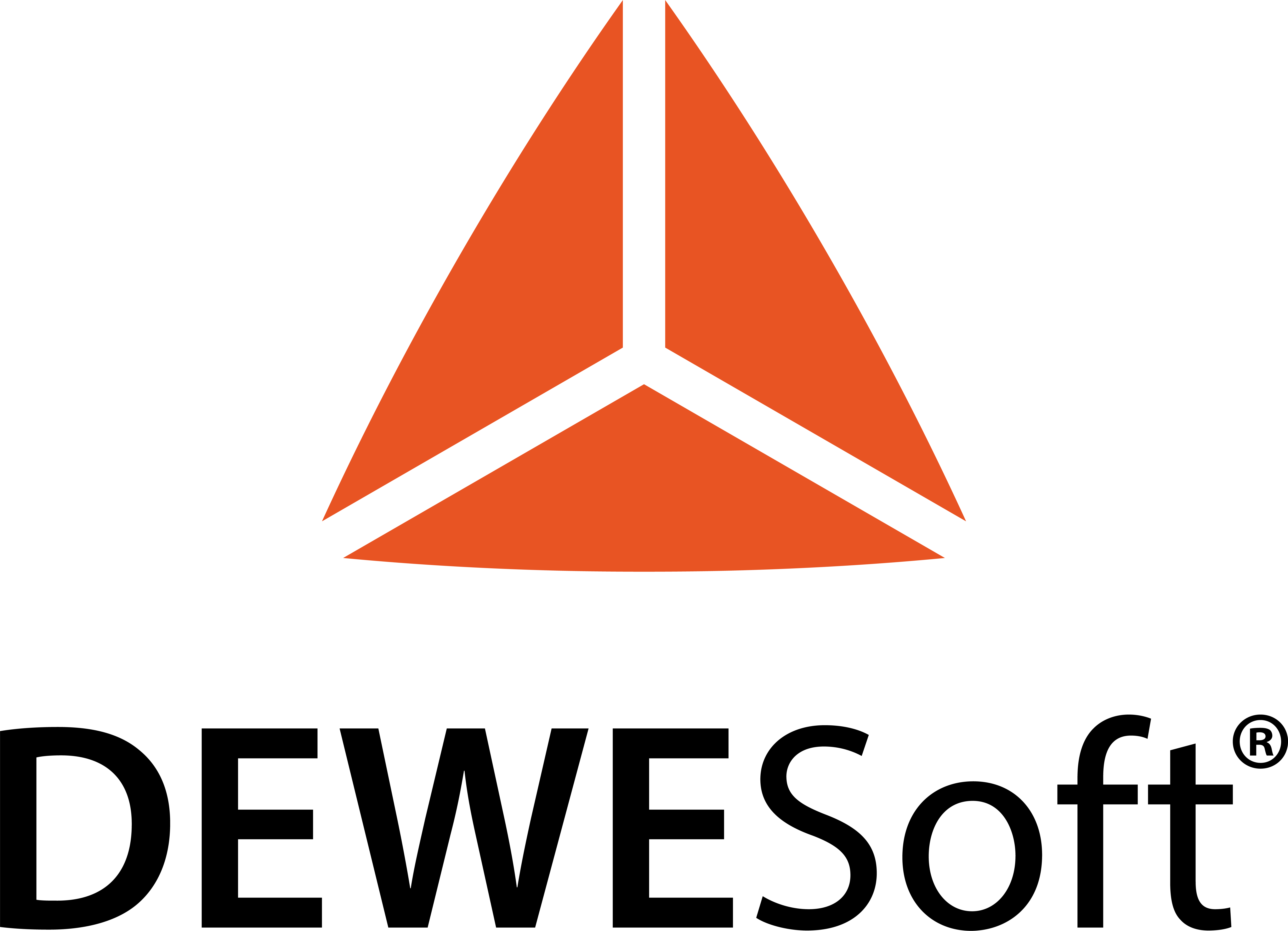
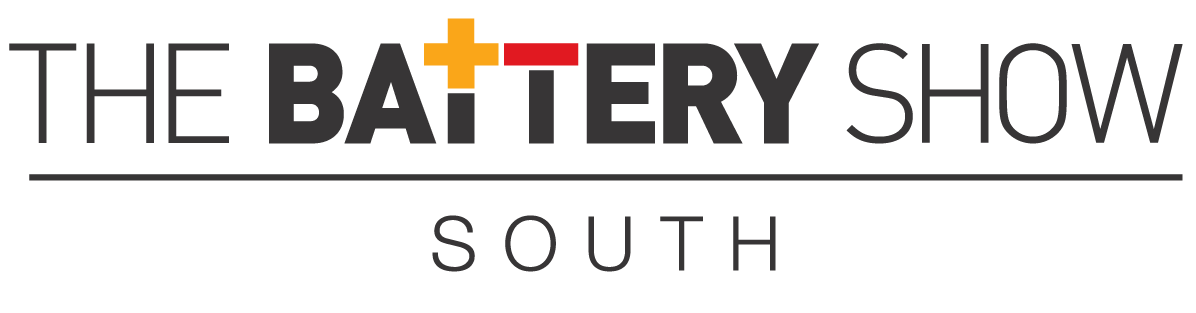
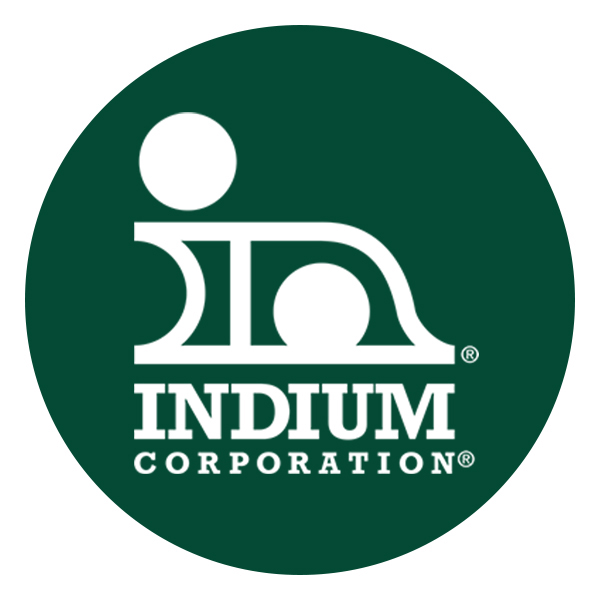
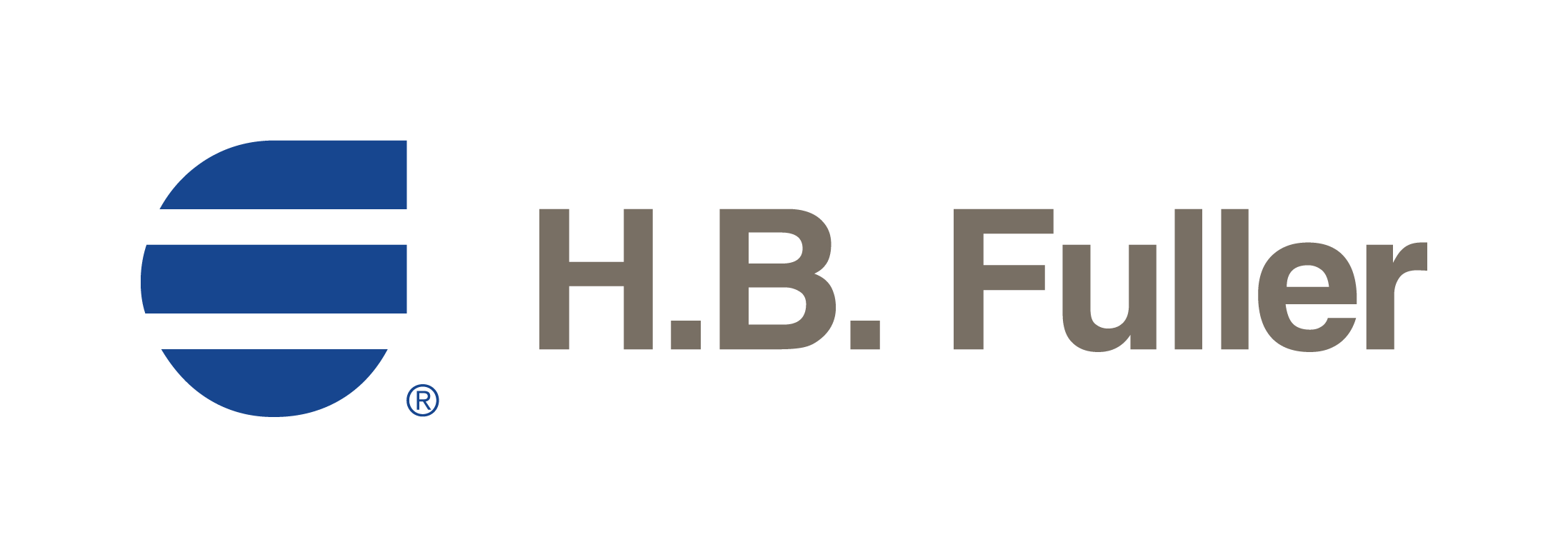