Lightyear One
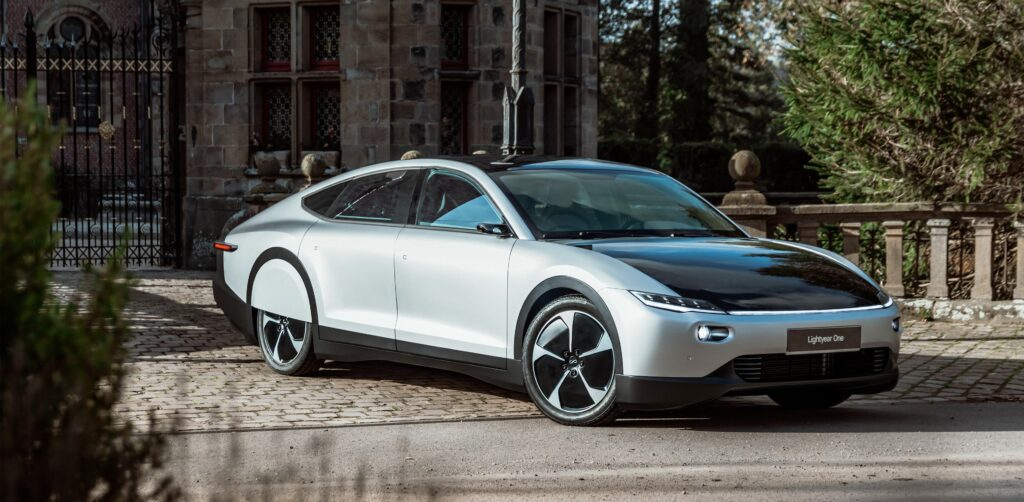
(Images courtesy of Lightyear except where stated otherwise)
Ray of sunshine
Rory Jackson explains how this aerodynamic five-seater has been designed for daily trips purely on solar power
While EV technology has come a long way over the past decade, the main concerns being raised by engineers, advocates and prospective customers of battery EVs remain the same. Range anxiety broadly encapsulates these problems, and boils down to a few key points – battery energy capacities are insufficient, charging points are too few and far between, and poor vehicle efficiencies mean batteries will either be drained before drivers reach their destinations or they have to stop along the way for a few hours to recharge them.
If these drawbacks stand in the way of more people switching to electric mobility then the case for a well-engineered solar EV becomes clear. A vehicle with its own solar panels can recharge itself independently of grid infrastructure, and it can replenish its battery while the driver is commuting, stuck in traffic, shopping and so on.
Extending range using solar power means the need for massive investments in charging points could become a thing of the past, as could conventional IC engine-based range extenders and the emissions they produce.
Of course, the potential drawbacks should be obvious. Solar panels need sunlight to work, and even then the practical energy they provide could be extremely limited if the EV platform is not highly optimised around its use. And if it is optimised, will the resulting EV look, feel and perform like something that anyone would actually want to drive?
Netherlands-based Lightyear has answered this with a resounding ‘Yes’. Since 2016, it has worked to achieve its vision of a highly efficient solar EV it says will do much to ease range anxiety.
That EV is the Lightyear One, which is set to enter series production later this year. This five-seater car’s roof and hood are covered in photovoltaic (PV) cells that sit atop a body and chassis designed around optimising aerodynamics and weight. It also contains a list of parts balanced around maximising energy efficiency, so that the PVs provide the kinds of ranges and speeds consumers expect from 21st century technology.
As a result, Lightyear’s launch car has a maximum range of 725 km between charges and an optimal energy consumption rate of 83 Wh/km, as measured in the WLPT (Worldwide Harmonised Light Vehicles Test Procedure). Its solar panels recharge the battery packs at a rate that gives on average 0.7 kph (although a charger input is installed at the rear, which charges at 570 kph with a 60 kW supply), and the car features four in-wheel motors independently controlled via SiC inverters that allow it to accelerate from 0 to 100 kph in just under 10 seconds, up to a speed cap that is currently fixed at 160 kph.
Its efficiency is such that it has reached distances of 710 km in tests at Aldenhoven, Germany, on just a single charge of its 60 kWh pack and at an average speed of 85 kph (over 9 hours) in typical weather conditions for the region. It has also managed just over 400 km in winter tests (10 C and cloudy conditions) at Bridgestone’s track in Aprilia, Italy, while maintaining 130 kph.
In the latter trial, it maintained an energy consumption rate of 141 Wh/km, a figure the company cites as two-thirds of the consumption of comparable EVs under similar test conditions. It also claims that other such EVs would only achieve about only 265 km range on a 60 kWh battery pack.
Solar challenge
Although it is now a company of 350 people, Lightyear was founded in 2016 with just five individuals, some of who now serve on its chief management team, including CEO Lex Hoefsloot, chief strategy officer Martijn Lammers, chief design officer Koen van Ham, and CTO Arjo van der Ham.
Before Lightyear, Hoefsloot recruited van der Ham and several others in 2012 to form a team representing the Eindhoven University of Technology (where they all studied) in the annual Bridgestone World Solar Challenge (WSC) in Australia. This 3000 km solar-powered endurance race had already seen successes by Dutch teams from Delft and Twente universities; these, along with Eindhoven’s own reputation as an automotive research institute, motivated Hoefsloot to compete.
This led to the Stella, the world’s first solar-powered family car and Eindhoven’s contender in the 2013 WSC’s first-ever Cruiser class, aimed at encouraging marketable multi-person solar car designs. It and its successors have won that class every year since.
After graduating in 2016, the team members came together to form a company. After researching trends, challenges and consumer concerns of the time, they decided to apply their collective knowledge towards electrification in the hope of helping to tackle climate change.
“We actually first looked into electrifying container ships, as they were the biggest polluters in the Netherlands, but the quantity of batteries needed to power them was 10% of the volume of the ship, which took 100% of the loading capacity,” van der Ham recalls. “To recharge them in the 3 days they typically take to unload, a power input of 1500 MW – equivalent to the largest coal plant in the Netherlands – would be needed for each ship.”
Eventually they arrived back at solar cars, after seeing that energy remained a serious point of concern for many regarding trends in electrification, connectivity, shared mobility and even autonomy.
That meant not merely the energy density of batteries, but the implicit burden on national grids and the scale of construction works and costs (in terms of new charging stations and related infrastructure) that a sudden worldwide adoption of EVs would entail.
“If a car can replenish its own energy by sunlight alone, it doesn’t need to be a burden on the grid, and drivers could do all their day-to-day shopping and commutes without ever plugging in. That’s hugely convenient for the 80% of car owners who don’t have a driveway or garage for home charging, and street parking will never work for charging EVs unless you install a 22 kW AC connector on literally every parking space,” van der Ham says.
“That’s how we wound up back where we’d begun, at solar car design, and we set a goal of achieving a lightyear’s worth of sustainable, solar-powered kilometres [9.5 trillion km] with all our cars by 2035.”
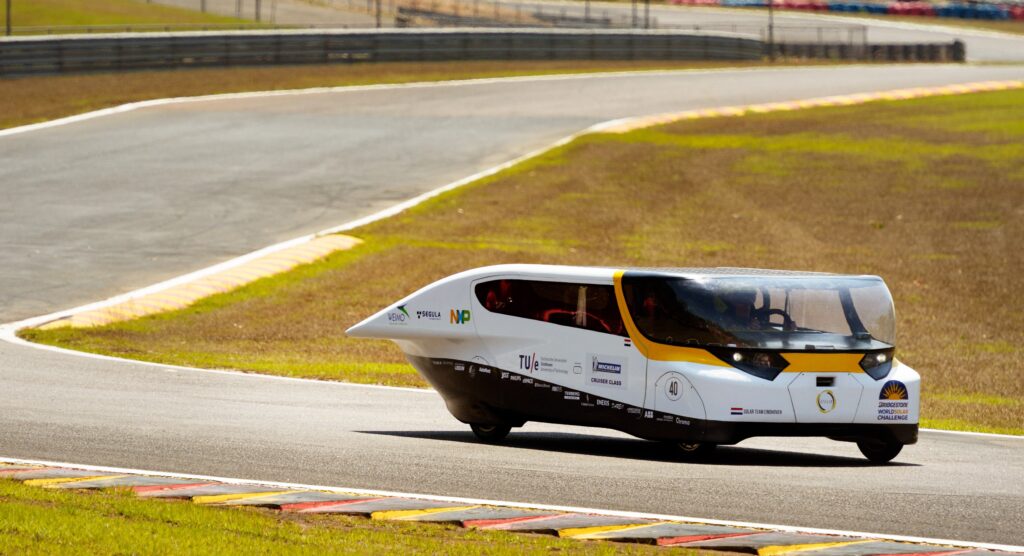
(Courtesy of Solar Team Eindhoven)
Lightyear’s timeline
While that may seem a staggering target, van der Ham points out that roughly all the cars in the world today collectively drive about one lightyear of distance annually. After raising capital (much of which came from the various parties from their WSC days and subsequent showcases of the Stella) Lightyear established its offices in Helmond, near Eindhoven.
Concept development of the company’s first car started in 2017, with these early stages dominated by spreadsheets of energy consumption, solar yield and other metrics, as well as some concept design sketches. This gradually progressed towards 3D models indicating how trade-offs between aerodynamics and solar panel area might affect the final look of the car.
“These were the models we used for the public launch of the car and the first unit reservations in June that year,” van der Ham says. “It actually looked very similar to what we have now, but of course everything underneath changed. We only had 20 people back then so the technical content wasn’t anywhere near as developed or mature as it is now.”
From 2018 to ’19, the engineering team worked on efficiency calculations to determine the powertrain’s layout, aerodynamics, solar architecture and ergonomics, along with other packaging concerns. These have been vital to the vehicle’s performance capabilities, and led to the unveiling of the prototype in June 2019.
The aerodynamics have remained much the same, with most r&d thereafter concentrating on maturing the motors, solar panels, inverters and related electronics.
In June 2021, the performance was extensively validated using single Lightyear One prototypes across standardised trials, which established its 700-plus km range capability using less than 60 kWh at 85 kph.
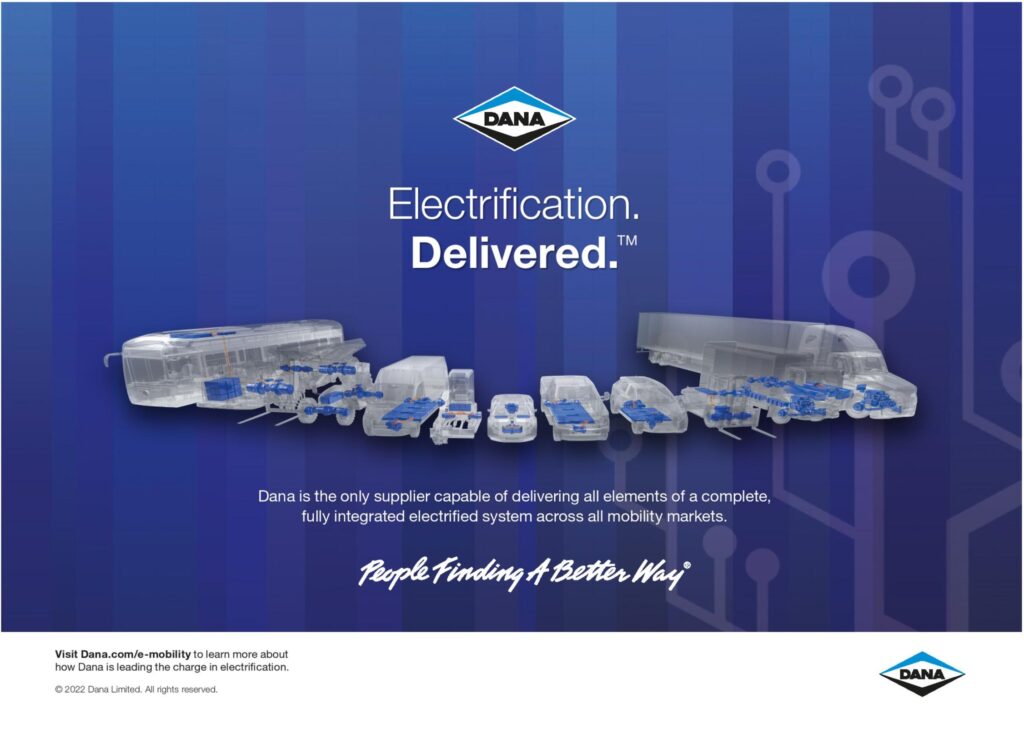
Production plans
The company is now focused on the release of the Lightyear One, with low-volume series production imminent. A maximum of 946 of the model (priced at €150,000) are expected to be manufactured (as per its upcoming homologation under the EU’s Small Series Type Approval), to start around the end of this summer.
“The decision to go with a low-volume, limited edition, high-price car initially was for several reasons,” van der Ham says. “First, we’re putting a lot of very new technology into this car – obviously we’re testing it not only to homologation requirements but in much more exhaustive safety trials too. But we want to grow our brand and company at a steady state, and establish firmly how robust and valuable our tech is before we scale up to high-volume series production.”
Lightyear aims to start high-volume production of its next model, the Lightyear Two, around late 2024 to early 2025. It is anticipated to cost €30,000 per unit, with much of the same technology and efficiency as the One, with most of the price drop coming from no longer having to cover the r&d costs of all-new IP and from being designed for mass manufacturability.
The building of the cars has been contracted to Valmet Automotive, in Finland, whose plant currently produces Mercedes-Benz’s third- and fourth-generation A-Class vehicles, as well as its GLC-Class. It has also manufactured numerous models from Porsche, Saab and other OEMs.
“And next year Valmet will be completely climate-neutral in their production methods, so it’s really exciting knowing that our cars will be totally green both before and during their lives,” van der Ham adds.
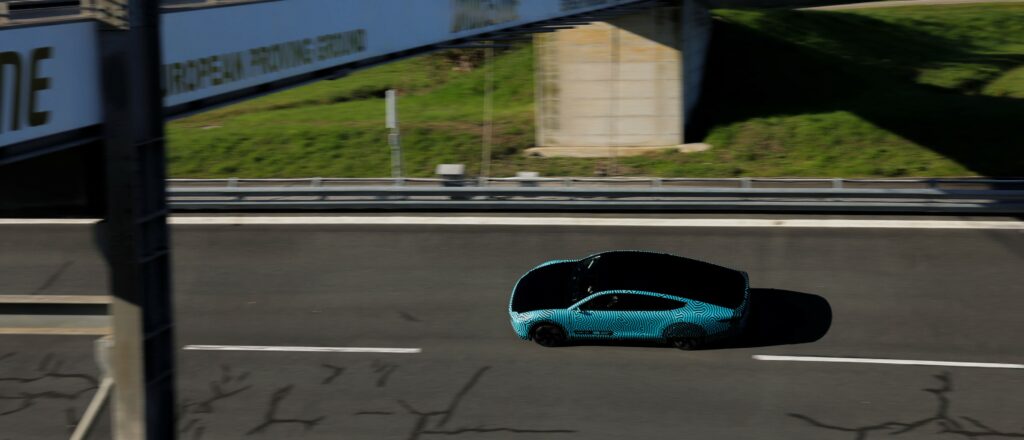
Solar-kilometres
As mentioned, many efficiency trade-offs had to be calculated to package the Lightyear One’s componentry in a way that would keep its performance consistently optimised.
“We view systems-level engineering, not technology, as the key to performance. You have to integrate, connect and balance everything perfectly,” van der Ham comments.
“It isn’t about the performance of the individual parts. You can find EV companies with more powerful and efficient motors than ours, as well as denser batteries, and other claims here and there, but what you absolutely will not find anywhere else is a more efficient five-seat production car.”
First, acceleration, range, and many other values were weighed against each other, not in hypothetical terms but with precise numbers and graphs to accurately prioritise between them.
“Once we’d defined those numbers and the relationships between them, we made a scoring formula that described our ideal car, which meant we could really treat e-mobility engineering as just a series of mathematical problems,” van der Ham says.
“It was very different to what we’d learned about traditional automotive OEM practices. And initially it was just a formula for the number of kilometres we could drive each year running entirely on sunlight.
“We gradually expanded it with loads of constraints, including having to carry a human comfortably, fitting a tonne of homologation requirements, noise caps and many others. But the key target to optimise – the number of kilometres we could drive each year on sunlight – remained.”
Every design decision and concept trade-off was filtered through to the resulting number of ‘solar-kilometres’. As a key example of this, Ham points to the Lightyear One’s tyres.
Tyres are one of the first things chosen in a new car model, as they determine a lot in terms of performance, packaging, handling and safety. The present choice is the Turanza Eco tyre developed in collaboration with Bridgestone, which has very low rolling resistance. Bridgestone’s i3 tyre was also an option, but its rolling resistance is not as low.
“There was another brand that had a 6-7% lower rolling resistance coefficient than even the Turanza Ecos, but when we looked at the overall integral trade-off, those other tyres didn’t work because they were wider,” van der Ham says. “The greater frontal area of the car meant we lost more energy through increased drag resistance than we gained from reduced roll resistance.
“Every decision had to be analysed at the vehicle output level. If we’d sliced our engineering teams into separate silos for choosing different components, we’d have made the wrong choices.”
Each component was developed and modelled by a system architect, who then delivered their model to a holistic integrated simulation of the Lightyear One called the Vehicle Performance Model (VPM). The VPM was produced through Matlab Simulink primarily to analyse energy consumption and evaluate which subsystems would maximise solar-kilometres. It also allowed ad hoc tweaks to weight, aerodynamics, auxiliary power consumption and other parameters to model the systemic knock-on effects.
“Thanks to the VPM approach, every Lightyear engineer knows by heart that to lower energy consumption by 1 Wh/km according to the WLPT cycle, we need to remove 43 kg of weight, or 43 W of auxiliary power consumption,” van der Ham explains. “That’s incredibly useful for questions like, ‘Do I add X kg of insulation to save Y amount of energy consumed by the heating system?’ Our engineers can answer almost immediately with a yes or no.”
This mathematical approach led Lightyear to a clear list of subsystems, configurations and arrangements of them for maximising the One’s solar-kilometres. Wherever possible, the company has sought to use COTS parts, although some IP had to be developed in-house, such as the designs for the solar panels, inverter and motors.
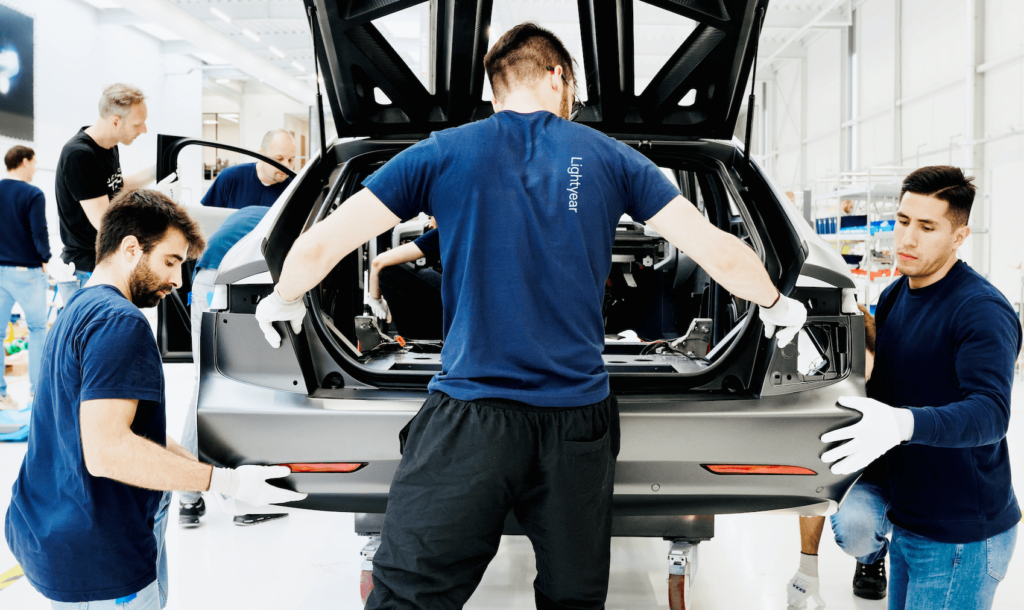
Architectural optimisations
The Lightyear One’s chassis is made mostly from sheet aluminium, which is folded before being riveted and bonded together. This is to minimise weight and maximise the speed and flexibility of design iterations.
“It’s a similar construction approach to the Alpine A110, for example,” van der Ham comments. “We came very close to using carbon fibre, which would have cut maybe 10% of the weight but it would also have driven up material costs by a factor of 10 or so, making aluminium the more sensible choice.”
The structure also includes an aluminium roll cage on top, which consists mainly of standard extruded profiles but with some casted joints. The exterior also features some fibreglass composite panels on the sides for aesthetics and to save weight, while insulation is largely provided through standard EPP foam, although that might be replaced or enhanced in the future if other materials are found to be more optimal.
With four in-wheel motors, it might be assumed that the chassis is a standard skateboard configuration; however, the batteries do not sit under the feet of the passengers but under the seats and in the rear.
“If you want to sit comfortably, you need enough height between your ankles and hips,” van der Ham points out. “So if you seat your passengers atop your batteries, you’re raising the height of the vehicle by the height of the batteries, about 12-15 cm. That’s about a 12-15% increase in the car’s frontal area and aerodynamic drag that you can’t get back.
“We’ve really sought to maximise our efficiency from battery to wheel. It seems crazy to us that some automotive engineers quibble over 1-2% increases in inverter or motor efficiencies while failing to remove comparatively staggering losses in aerodynamics and packaging that have far bigger impacts on how much energy it takes to move their EVs.”
The battery packs connect to two HV power distribution boxes, one at the front and one to the rear, each of which sends power to two inverters, making four inverters for four motors. Most of the thermal management systems sit under the hood to save interior space.
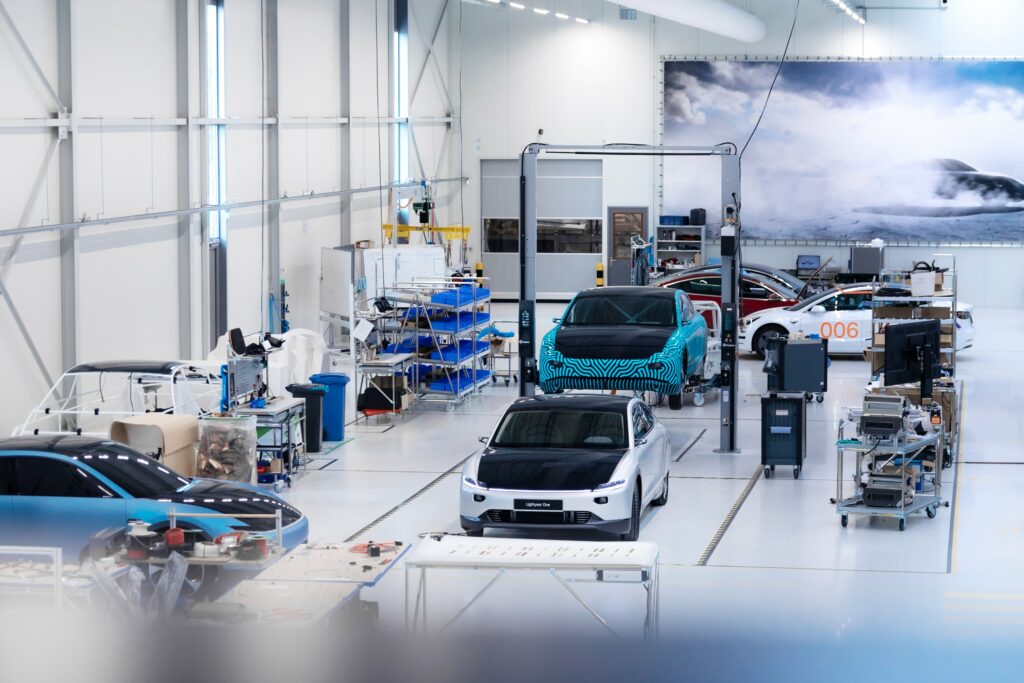
“That spares plenty of room for the cabin interior, and the rear seats can fold forward to create a huge amount of storage in the back for say, surfboards, furniture or a mattress for example,” van der Ham says.
“We’ve also raised the trunk somewhat to match the height of the rear seats when they’re folded. That has created extra room below, half of which we use for a lot of our LV components, including our DC-DC converter, onboard charger and a connector box for the batteries. The other half is open space, so the floor of the trunk swings open to reveal bonus storage equivalent to, say, two crates of beer.
“Having a large vehicle with no driveshafts or transmission helps hugely when it comes to storage and packaging.”
Computer-aided style
The space freed up by not using such drivetrain parts was also key to optimising the underbody’s aerodynamics. In addition to the holistic VPM simulation, the aero across the entire exterior was first modelled using CAD diagrams in Dassault’s CATIA v6 (its cloud-based platform that allows engineers to collaborate simultaneously).
“The CAS [computer-aided style] models, which ensured the aerodynamics are married to the aesthetics, were delivered by Granstudio, in Turin,” van der Ham adds. “It’s run by Lowie Vermeersch, who was the design director at Pininfarina before leaving to found Granstudio.”
During the years in which Vermeersch headed Pininfarina, the studio produced the designs for such models as the 2007 Maserati GranTurismo, the 2009 Ferrari 458 Italia and the 2010 Maserati GranCabrio.
“We had a very good back-and-forth with Granstudio,” van der Ham explains. “They would draw a new CAS model, send it to us, and we’d mesh it and simulate the aerodynamics, mostly in an ecosystem based around openFOAM that we developed ourselves. Sometimes though we’ll validate the simulations using an additional package, usually Ansys.
“And we’ve recently switched from running our openFOAM ecosystem on an internal cluster to running it on AWS, which has brought our iteration times down from a day to about 2 hours, enabling multiple and really great feedback loops daily. We can run aero simulations, analyse the results, send the feedback to Granstudio, and repeat it and fix it over and over before close of business.”
Further validation is derived every now and then from wind tunnel tests, which serve as strong ‘recalibrators’ once a present model has deviated enough from how it looked in a previous test. It was through wind tunnel testing that Lightyear’s engineers have proven that the One maintains a drag coefficient of less than 0.2 in normal driving conditions.
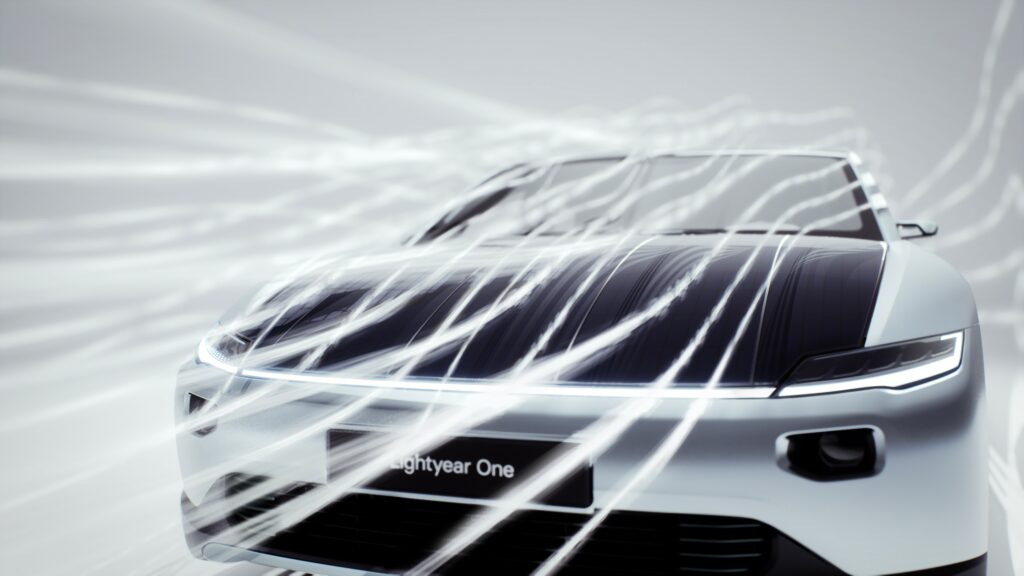
Thermal management
The Lightyear One’s thermal management system consists broadly of a refrigerant circuit and a coolant circuit; the former can also work in reverse, to work as a heater in cold weather. A heat exchanger is installed between the two circuits, and the refrigerant circuit can run through it or not, depending on the mode selected.
“That means we can actively heat or cool the water-glycol medium in the refrigerant system,” van der Ham says. “We can direct the refrigerant circuit to take heat from the battery or motors to heat up the cabin for example, including our heated seats. That makes a lot of sense since people generally like to be about the same temperature as batteries, around 20-25 C.”
He adds that the coolant circuit splits into two loops: one for the forward motors and one for the rears. Each of these splits off into an additional loop for other components – one for the onboard charger and the HV-to-LV DC-DC converter, the other for the battery packs, which can be toggled to work in series (as a single loop) or in parallel (single input and output but with multiple channels between) with the rear motor cooling loop.
“The main reason for that is because, upon starting the vehicle, you might want to cool both, for which series and parallel are both fine,” van der Ham says. “But if you need to extract heat from the motors and use it to cool the batteries, a series loop works best, and if you want the refrigerant loop heated via the heat exchanger then we use the parallel mode.
“Eventually, once the battery is at operating temperature, you might start pushing it and start generating surplus heat, but the coolant circuits pass through a radiator as standard, so if more cooling is needed we can send excess heat into the refrigerant loop through the heat exchanger.
“It’s an effective but very complex system; we’ll probably simplify the thermal management in future models.”
Solar on top
Lightyear uses monocrystalline silicon (mono-Si) cells, partly because it found a secure supplier in Maxeon Solar Technologies. They were also chosen because Maxeon cells are rated at a solar conversion energy efficiency of 25.1%, which was deemed the best in terms of cost versus performance.
“If you really want to max-out the efficiency on your solar recharging, you need to go to something akin to the triple-junction, GaAs-based panels used in satellites and high-altitude solar drones, which would make our cars not affordable for anyone,” van der Ham says. “Even single-junction GaAs cells would have cost €150,000 by themselves, just for one car’s roof. That’s simply not worth it, not even for the 27-28% solar-to-electricity conversion efficiency they’d bring.
“Maxeon have made the most efficient mono-Si cells for years. That said, we do quite a bit with the cells before we actually put them on the car.
Once received by the Lightyear One’s engineers, the square-shaped cells are cut into smaller sizes to make them fit the 2D dimensions and 3D curvature of the roof and hood without cracking. While flexible, the crystalline structure of each Maxeon panel is such that it will only bend along one axis at a time (like card or paper), so the pure product cannot simply be bent and bonded onto the car if its aerodynamics are to be preserved.
“We buy small cells, as they are easier to shape to our geometric tolerances, and we also buy glass and lamination materials selected to minimise reflections as well as damage from hail, gravel and scratches from other sources,” van der Ham says. “We’ll continue producing our own modules in series production as well though.”
In addition to construction methods, solar electrical engineering has been a major focal point for Lightyear. A typical solar cell will output around 0.5 V and 2 A; this low-voltage, high-current supply contrasts with feeding battery cells, as they tend to be high-voltage and low-current by comparison.
“If you want a really efficient solar-to-battery energy supply, you need to put your voltage up,” van der Ham explains. “Typically, that’s done by connecting a couple of hundred cells in series. That gives you 50-100 V, which can be efficiently stepped up to maybe 400 V for the battery.
“The problem with that though is that a string of series-connected cells needs the current running through to be equal all the way, and the current in a solar cell is determined by the amount of sunlight it receives. With a curved roof, you’ll never have all the cells getting equal sunlight: each sunrise, the cells facing the west will limit the current generated in the cells facing east.
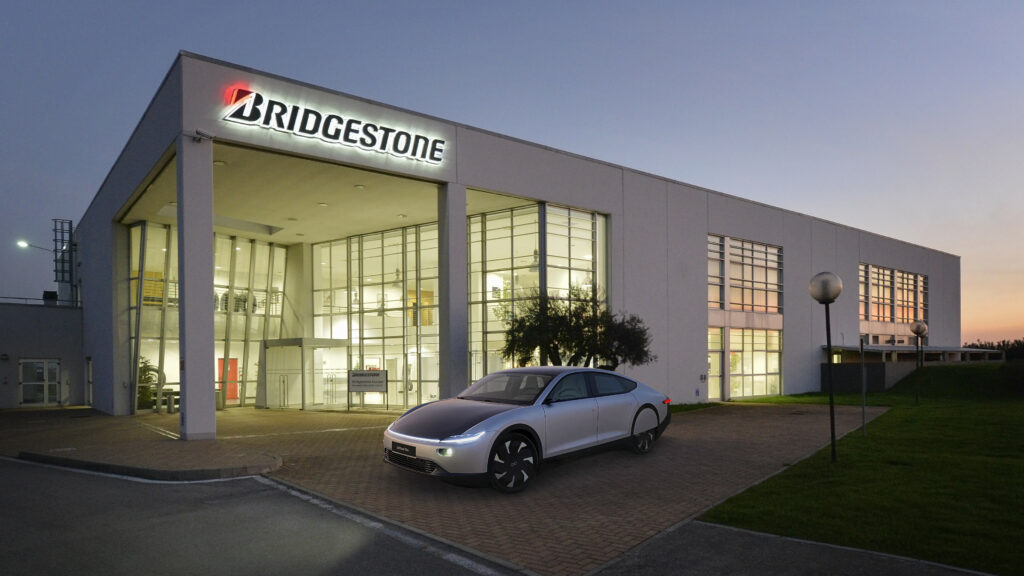
“As a benchmark, we calculated that if a VW Beetle – possibly the most curved production car there is – was made solar-electric, it would lose 25% of its optimal solar efficiency because of how its shape would lose out on direct solar contact, and shadows would lead to further current mismatches within the long strings.”
Lightyear solves this by using 28 shorter strings (instead of one large one) in the standard Lightyear One, resulting in just 1% of solar efficiency being lost to such effects. Each string also connects to its own tracker and power converter module to monitor efficiency in real time (these tracker-converters are interleaved to minimise EMI and the need for filter capacitors).
“We also had to ensure the solar hood complies with safety regulations in case of impacts with pedestrians,” van der Ham says. “Cars normally use thin aluminium hoods that crumple to absorb impact energy and minimise harm to humans, so a lot of r&d went into ensuring our hood’s solar glass has similar energy absorption characteristics.”
The glass itself is a combination of the types used in solar power stations and those in the automotive industry. A lengthy design and validation plan was devised in-house to prove the resulting panels to the same extent as conventional automotive hoods and roofs as well as PV panels. For example, normal PV panels are temperature-tested to 85 C, but Lightyear tests its panels to higher temperatures to prove their reliability and durability to regulators.
Underneath the solar panels are conductive back-sheets from Endurans, which are key to their aesthetic finish, structural reinforcement and electrical connectivity and output; Endurans estimates a 3% increase in power output from using its back-sheets. The back sheets are also recyclable and are made from a non-hazardous polyolefin.
Notably, the solar panels can deliver their energy to the car’s HV or LV networks, with the tracker-converters and the BMS collectively managing which is powered at a given moment.
That is partly because keeping the HV converter active requires more energy than the LV converter, owing to the added burden on the BMS as well as the relevant relays, junctions, and other electrical parts, so minimising that energy requirement occasionally can be useful. This is also true for the HV-LV conversion, so it makes sense from an efficiency standpoint to include an LV-LV connection from the solar system to the cabin and driver systems (a small, dedicated LV battery is integrated for regulating this input).
“That lets us do some smart things with excess solar power,” van der Ham says. “For instance, if all batteries are full and you’re in a hot climate, we can use it to work the cooling pumps harder and intensify the cooling of the batteries and cabin, or heat the batteries if you’re somewhere cold.
“Efficiency is really what makes solar useful. Once you have a really efficient car and you sit 5 m2 of solar panels on it, you can recharge enough energy for the average commute in most of the world. In the US, that’s about 20 miles a day; in the Netherlands it’s about 20 km. So even without any sunlight at all, our maximum range gives 2 weeks of commuting before having to plug in.”
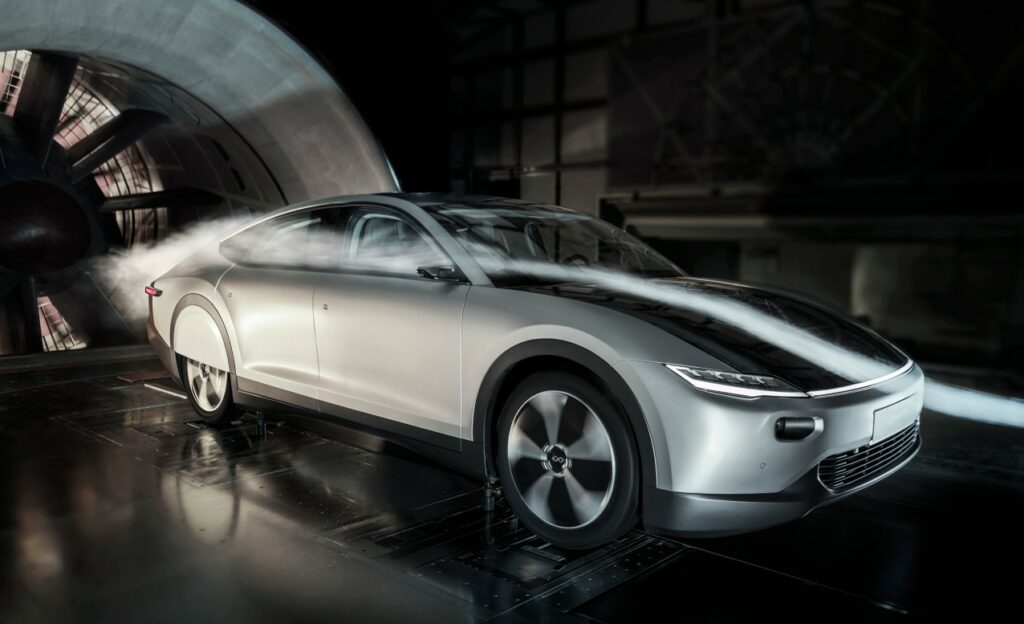
Batteries
Priorities for the packs’ designs were to minimise height (as per the aforementioned passenger seating concern) while keeping enough internal space for venting if a thermal runaway occurs. Interconnections were largely achieved through traditional spot-welding, with monitoring boards welded directly onto the interconnection tabs of their respective modules for reliable connections (van der Ham emphasises his team’s distaste for using wires).
The monitoring boards connect to a central BMS board at the back of the batteries, which manages the contactors, disconnection functions, and sensors for current, temperature as well as many other parameters. The BMS is a COTS component chosen largely for its safe ASIL-C rating, and for added safety the packs feature penetration plates on their undersides to protect against road debris.
Lightyear’s packs use NMC 21700 cells designed for energy density over high power. These ensure sufficient energy for long ranges in a smaller package than those found in other five-seater EVs, as well as low C-rates (usually around 0.1 C discharged) during normal driving, with a peak discharge rate of just over 1 C and a peak charge rate of just under 1 C.
“Those rates also make it very easy for our packs to reach 10 years or more of lifetime, and drastically reduce the cooling requirements,” van der Ham says. “We know some drivers really want to be able to go from 0 to 100 kph in 3 seconds, but allowing that has a huge impact on the returns from purchasing our EVs.”
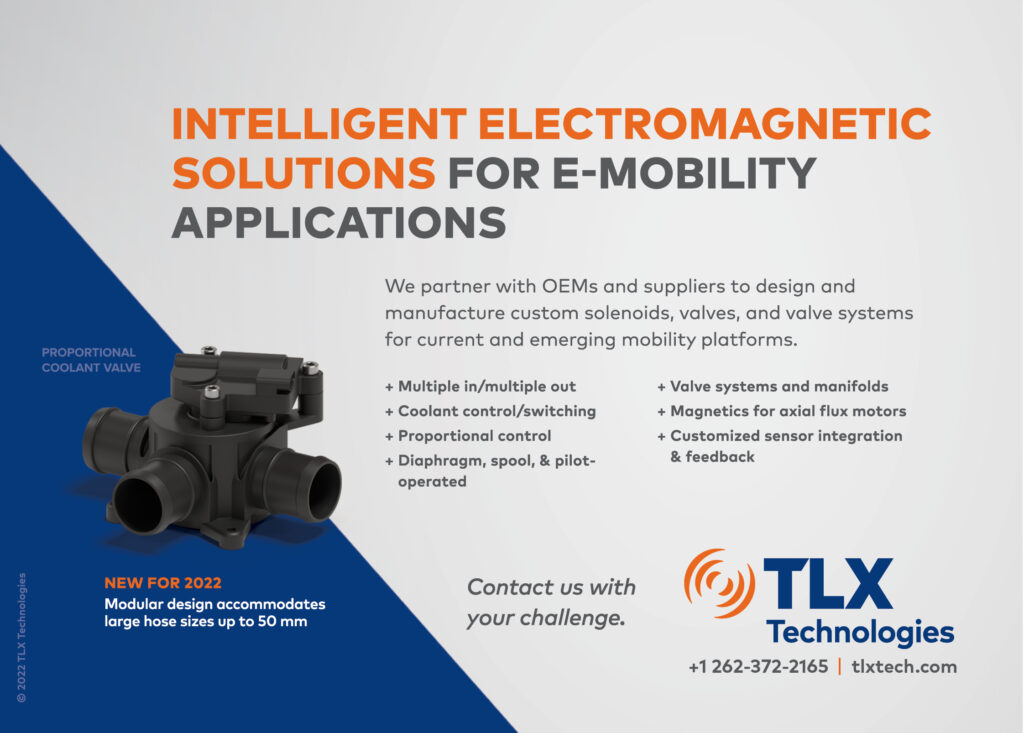
He adds that their cell type is common in newer laptops, e-bikes and other high-energy, low-power, high-volume consumer goods, meaning Lightyear is less prone to supply chain disruptions than EV OEMs that opt for high-power automotive cells. They are also very cost-effective in what is already a lower-energy and hence lower-cost pack than most on the market.
“The battery makes up one-third of the bill of materials in most EVs, and most OEMs trying to maximise their range will go the way of a pack with 140 kWh or even more,” he says. “There’s no way you’re optimising on price if you try to hit range targets just by buying and adding more battery cells, even with the most optimistic price forecasts for 2025.
“We are confident that 60 kWh is the most cost-effective compromise between range and price, not just for our Lightyear One but in the Two model as well. Both will be efficient enough to hit 400 miles on that kind of pack, while still being affordable enough for the kinds of vehicles they are.”
The company has also found that using this comparably small pack has enabled the use of smaller components throughout the rest of the powertrain than in other EVs, as having fewer energy modules means less weight to shift and less power needed, echoing the experiences of Workhorse in the US (EME 8, Winter 2020) and Riversimple in the UK (EME 10, Summer 2021) among others.
“There was a study by Aachen University and Volkswagen where they experimented mathematically with how they could change a VW Golf 7 if 100 kg was magically removed,” van der Ham recounts. “They redesigned every part with the new load-cases and found a further 30 kg could be cut out.
“Then they repeated the process with that 30 kg gone, and extracted another 15 kg. It was a great showcase of how important weight efficiency should be as a core tenet of automotive design, and the effect with batteries is even stronger because of the specific energy differences.”
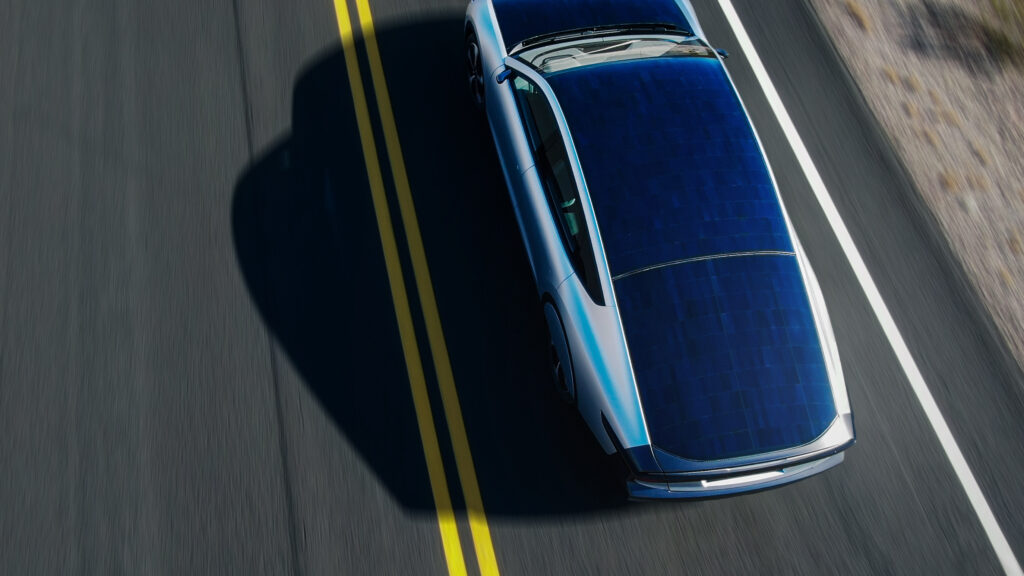
In-wheel motors
Each of the four motors is a radial flux, permanent magnet AC machine with distributed windings. The concept design was produced internally before an (undisclosed) external supplier was contracted for more detailed design and manufacturing.
“We did look at axial-flux motors for some time, and we’re just on the edge of where it might make sense to do so, in terms of diameter versus axial length, as well as torque density,” van der Ham comments. “But in the end we went with radial flux because it makes air gap control easier.
“We tried it with axial flux, we built a prototype, and found it so much more difficult for in-wheel motors. If you hit a kerb or just corner hard, your sub-1 mm air gap is gone and your motor is ruined.”
The motors also use bearings that are chosen for their extremely low roll resistance. Physics dictates that the bearing (mainly its robust environmental protection seal) still causes one-third of the motor’s efficiency loss, despite being the best Lightyear could find. As a result, the motors reach a peak efficiency of 97% in tests and an average of 93% over cycles, with an average efficiency across the drivetrain (battery to wheel) of around 91%.
“The motors are actually over-designed for what they need to deliver, just so that they run more efficiently at the points we’re actually using them for,” van der Ham says. “We’re getting 20 kW out of them but on the dyno you can pull 40 kW from them easily, albeit with heavier cooling.
“We don’t need to; we just put more copper into them to make sure they run efficiently at the low power levels needed for gentle commuting. Most other motors lose a ton of efficiency at low revs.”
He adds that the choice of in-wheel motors (rather than e-axles or a central drive) wins out in Lightyear’s view on mechanical efficiency grounds too. As noted, even high-quality bearings cause one-third of efficiency losses – every additional bearing, belt, differential and so on will cause further losses, he says, making it (in his view) impossible to reach 91% efficiency across a whole drivetrain with e-axles or central drives.
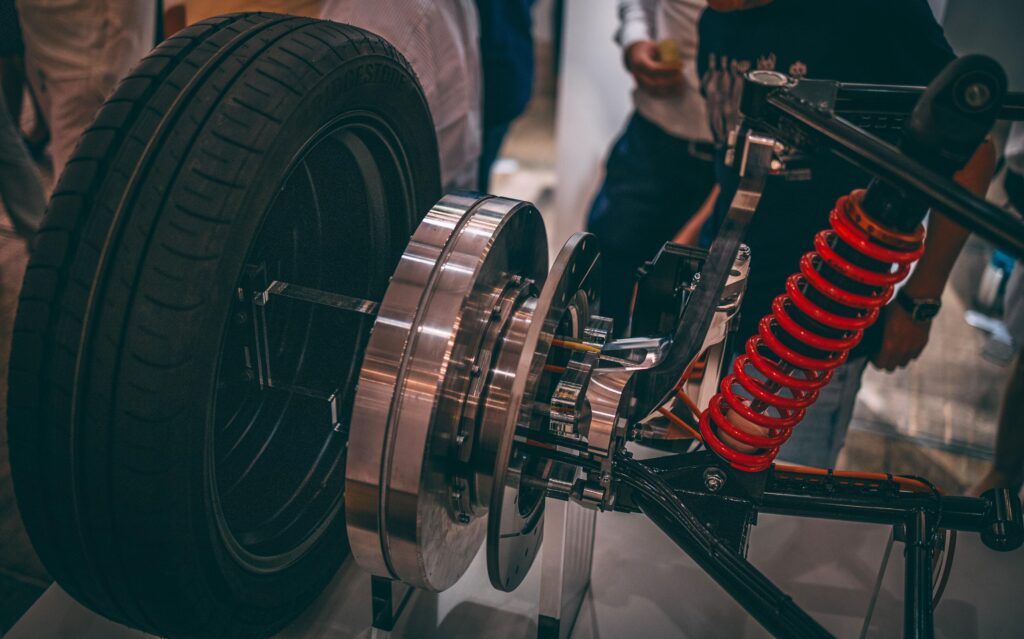
(Photo: Mark Vletter)
“The industry is flooded with companies shouting about how their EV has a 95% efficient motor, but then they never include the gearboxes, the shafts, the bearings from the motor to inside the wheels, because if you did, their battery-to-wheel efficiency would typically be 70-85%,” van der Ham comments.
Much of Lightyear’s motor r&d went into optimising the placements of magnets, minimising end-windings and reducing eddy current losses in the back-iron by using appropriately thin stator laminations. The design features 30 pole pairs, a high number chosen to ensure the electrical frequency (32 kHz) can easily match the mechanical frequency, as discrepancies here would cause losses.
“Being 0.5º off is enough to cause losses, so we use an observer in the inverter to measure the waveforms in real time against an embedded model of one phase,” van der Ham explains. “That gives us the position of the motor and allows us to really maximise the accuracy and timing of the commutation.
“There are some other tricks in the inverter to help with that, such as very accurate delay compensation, a reliability signal for the observer, and the wheel encoders serve as back-ups when the reliability signal calls for them.”
Silicon carbide inverters
Each motor has its own SiC inverter mounted nearby on the chassis, connected via cables running over the suspension assemblies. As mentioned, the inverter was designed entirely in-house, as after a year of searching Lightyear could not find a COTS inverter that matched its efficiency and packaging requirements.
“We’re not using SiC for extremely high power switching, as most others are,” van der Ham explains. “For us, the real benefit is that it allows us to simplify our thermal management massively. By making the inverters really efficient, we almost never have to cool them, except for the bare minimum just to keep their temperature a bit consistent, for reliability’s sake, but it really reduces the power drawn by our cooling system.
“We could even run them air-cooled. We’ve tested them enough to see that airflow would be sufficient, but again that’s something that would take away from our aerodynamics, so liquid was the best option.”
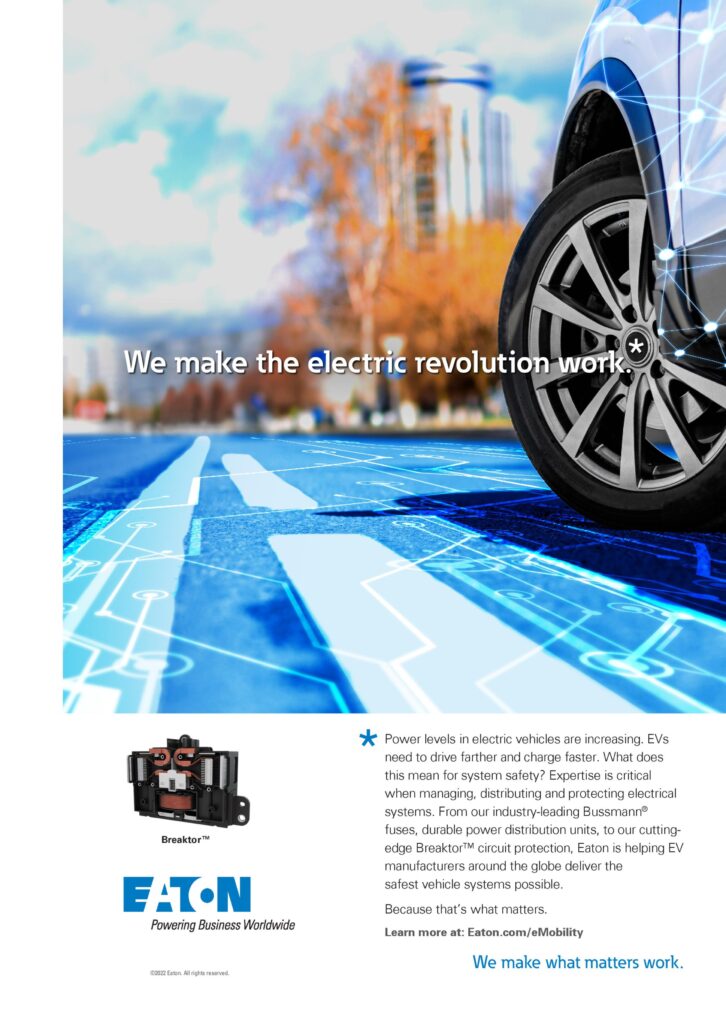
In electrical terms, the architecture of Lightyear’s SiC inverter is generally similar to those found among most silicon MOSFET- and IGBT-based inverters, albeit with some minor differences in the drive circuits.
Where it differs most is in its packaging. The SiC transistors are arranged as SMT devices, soldered onto a PCB, something that is deceptively simple at first glance but with some proprietary design innovations, largely around ways of conducting heat through the PCB to its underside. The engineers therefore decided against complex approaches such as sintering their transistors directly to a cooling block (as in the Tesla Model 3) or buying integrated modules, as most do.
“By dividing total power and torque over four motors, each inverter delivers 20 kW at peak and around 10 kW continuous most of the time,” van der Ham says. “Meanwhile, other manufacturers are racking their brains trying to build a 250-300 kW inverter, which is a really hard engineering challenge.”
Other factors came into play when choosing this traction approach. For example, instead of concentrating purely on enhancing the drive circuits and thermal management, as many OEMs do, Lightyear’s inverter architects placed a lot of r&d emphasis on the energy consumed by its sensing elements, drive circuits and controller FPGA. These static components were identified as disproportionately influential, not only on overall energy efficiency but also EMI, and thus became major points of focus.
“We are switching at a variable frequency, but around 32 kHz, quite a bit faster than typical,” van der Ham says. “That creates EMI challenges but helps a lot with efficiency, not necessarily in the inverters but very much in the motors, by creating much lower harmonic distortion in the amplitude waveforms and hence electromotive force. And you save considerably on iron and copper losses in the motor.”
As a final query, we asked van der Ham if he and his team were ever tempted to package the inverters inside the hub-wheel motors. “Not right now, but we are re-evaluating that design choice for our next generation EVs,” he says.
“We are almost at the limit of the cable lengths we can run between the motors and inverters. If we want to switch even faster, we’re going to need shorter cables, and if we can integrate the inverters in the motors then there’s that problem decidedly solved. We’ll have to look at the trade-off with reliability and thermal management.
“Motor torque can be limited by cooling, so maybe putting the inverter there isn’t the wisest thing. But our drive components are nowhere near their thermal limits so it wouldn’t be an issue.”
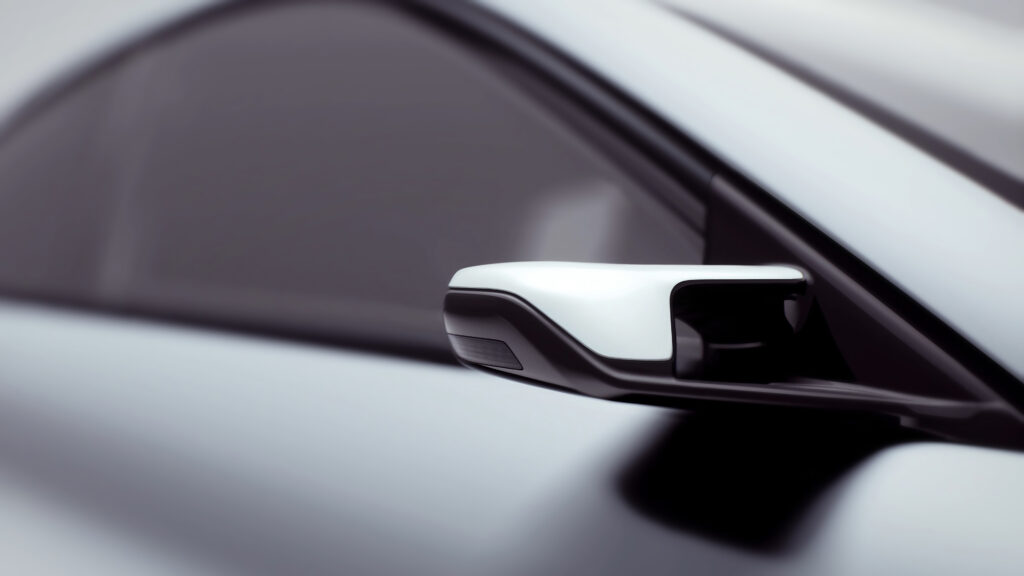
Control systems
There are essentially two high-level ECUs responsible for governing the Lightyear One’s operations: a VCU and a safety supervisor. The former oversees and controls almost all functions including thermal management, torque-focused commands to the inverter, steering and braking systems, while also running energy optimisations across the whole vehicle, from the PVs to the inverters.
The latter receives all the same data inputs as the former, and analyses for safety indicators. If something is found that indicates a component failure or unsafe conditions, the safety supervisor can trigger safe states in one or more subsystems.
“That centralised safety check allows us to simplify a lot of the control architecture in terms of functional safety, and achieve the ASIL certifications for most systems without having to heavily customise each individual part to ASIL standards,” van der Ham explains. “We can just design the functionality of each one with a QM rating.”
There are two more high-level control units that are more relevant to drivers and mechanics. One monitors and adjusts the power for cabin systems such as the driver instrument cluster which displays information on speed, solar energy, the weather and navigation among other data. It also governs the passenger infotainment systems, which include monitors for Apple CarPlay and Android Auto, as well as a wireless device charging pad and cellular receivers for over-the-air software updates. Lastly, a telematics unit is responsible for all external connections between charging, diagnostics and other systems with the car.
Most of the comms in the vehicle are CAN-based, with a main powertrain CAN and a safety CAN that each run from the powertrain components to the VCU and safety supervisor respectively. There are a few additional low-level CAN buses for auxiliary systems, and some LIN buses for peripheral items such as door locks and window buttons.
Lightyear has also partnered with Sibros, which optimised its systems for over-the-air firmware updates and debugging, as well as cybersecurity.
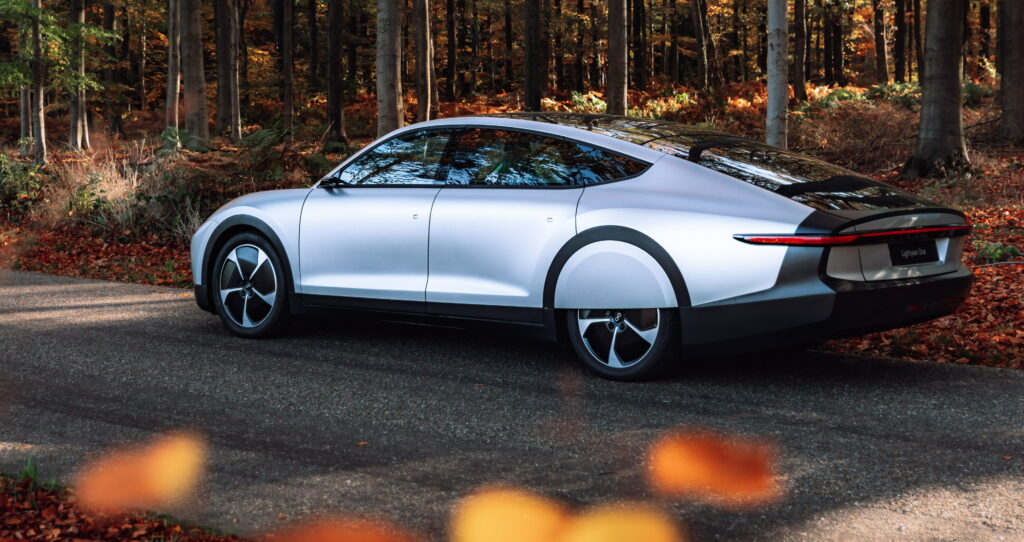
Future plans
In addition to the upcoming production of the Lightyear One, and of the high-volume Lightyear Two design, the company plans to develop autonomous robotaxis. Its engineers see such vehicles as the best way to achieve its core goal of clean mobility for all, and they anticipate that they could tackle autonomy with a similar speed and effectiveness with which they have approached electrification.
It is worth noting that this has been made possible through Lightyear deliberately breaking the mould early on in their approach to automotive design. Van der Ham notes that most new car models are conceived with an array of core components – engines, transmissions, suspensions and so on – that a chassis and body are designed around.
Since the 1950s, the traditional model of engine in the front, driveshafts to the sides, steel stand monocoques and so on has been held sacred. Yet reversing the conventional order has enabled Lightyear to reach new heights in efficiency, and position itself as the Tesla of solar e-mobility.
“No dominant model of design flows or even vehicle architectures has emerged in EVs, but we’re ahead of everyone else in terms of our car’s efficiency and practicality, especially when it comes to making something that consumers can use for all their daily routines without having to stop and charge,” van der Ham says.
“If you look at the current offerings from Tesla, Hyundai, Ioniq and others, we are almost twice as efficient. We also have all the resources we need to keep our r&d moving faster than theirs, so we’ll stay ahead with each new model we put out.”
Specifications
Lightyear One
Five-door liftback
5057 x 1898 x 1426 mm
Solar-electric
In-wheel motors
Maximum battery capacity: 60 kWh
Maximum range between charges: 725 km
Optimal energy use: 83 Wh/km (141 Wh/km in winter conditions)
Maximum continuous speed (capped): 160 kph
Maximum power output (capped): 80 kW
Acceleration: 0-100 kph in just under 10 seconds
Some key suppliers
Vehicle manufacturing: Valmet Automotive
Semiconductors: NXP
Controllers: OpenECU
Recycled CFRP: undisclosed
Solar cells: Maxeon Solar Technologies
Solar back-contact modules: Endurans
Battery pack: undisclosed
In-wheel motors: undisclosed
Bearings: undisclosed
Tyres: Bridgestone
Seats: Recaro
Simulation software: Mathworks
Simulation software: Dassault
Simulation software: CFD Direct
Simulation software: Ansys
Cybersecurity and over-air firmware: Sibros
Automotive design services: Granstudio
Structural engineering consultation: CSi
Additional engineering consultation: FEV
ONLINE PARTNERS
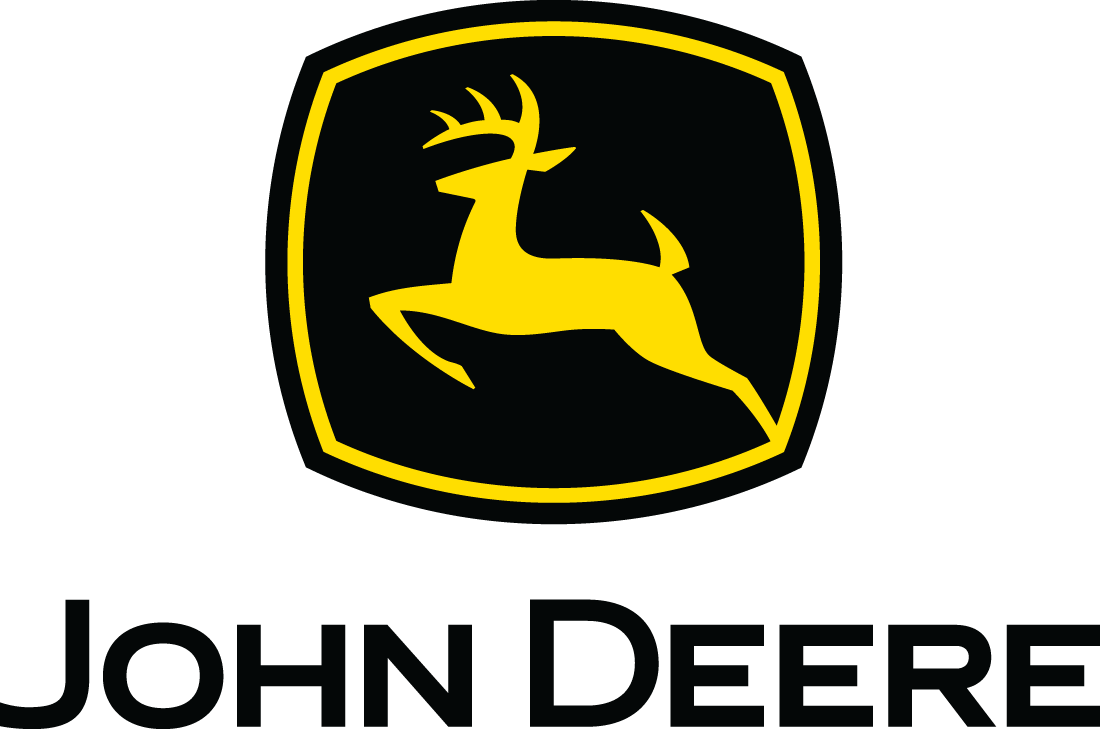
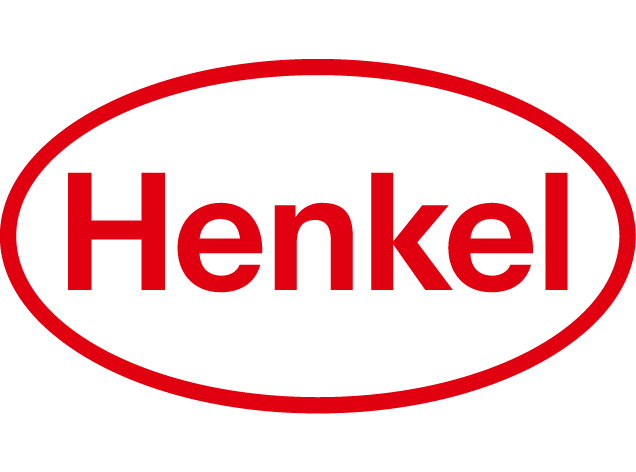
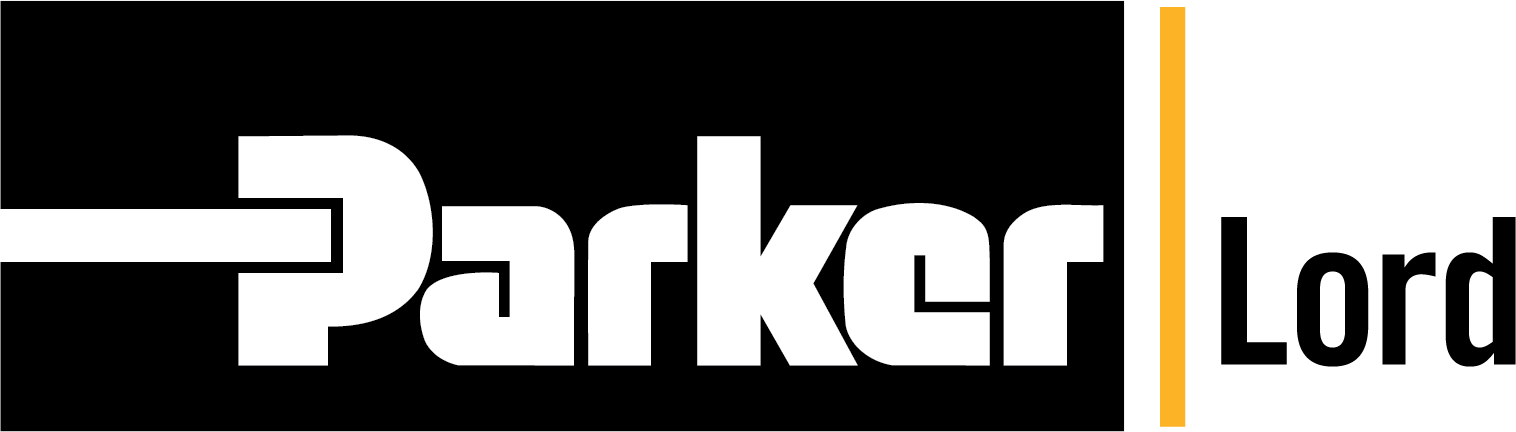
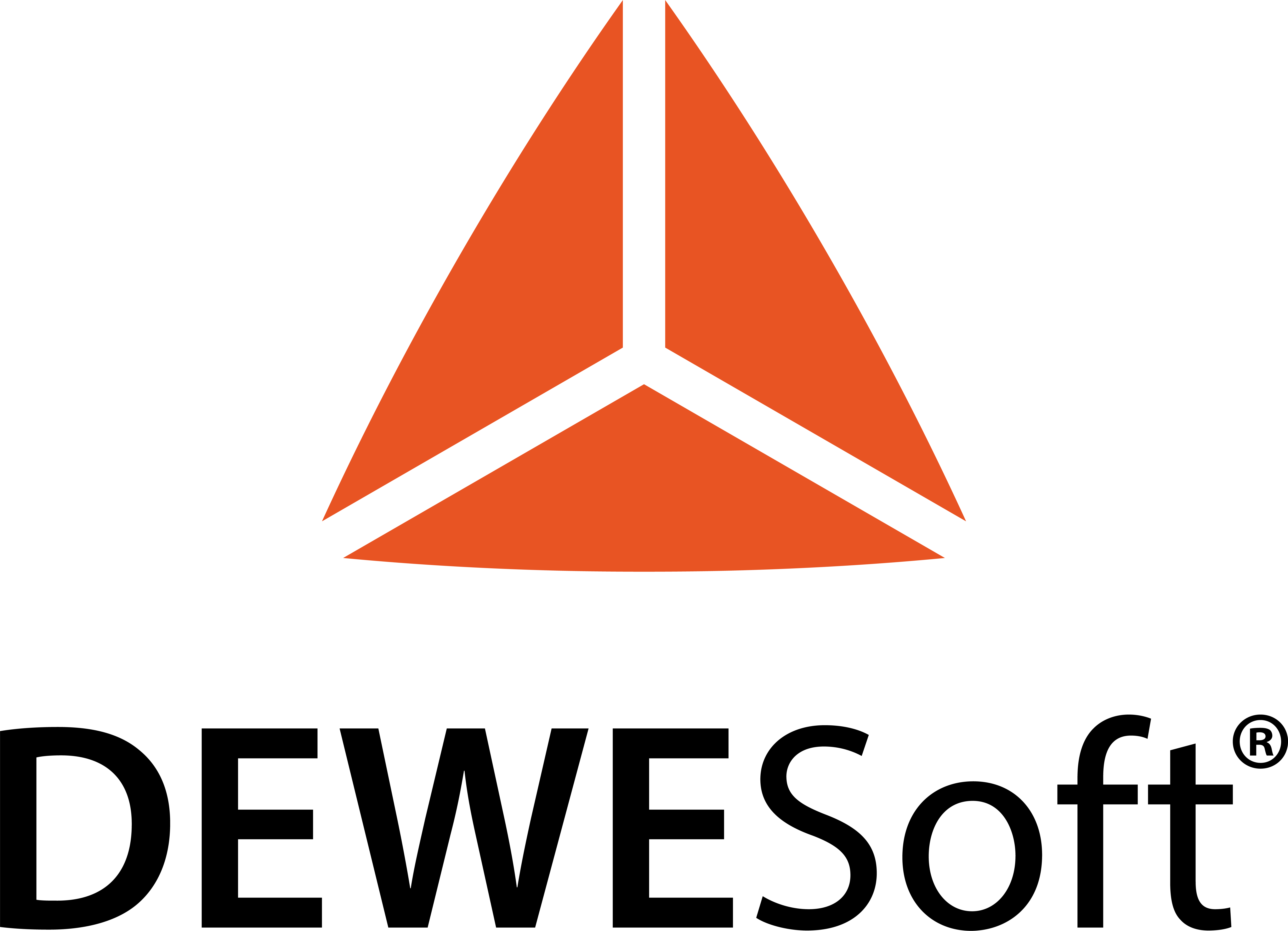
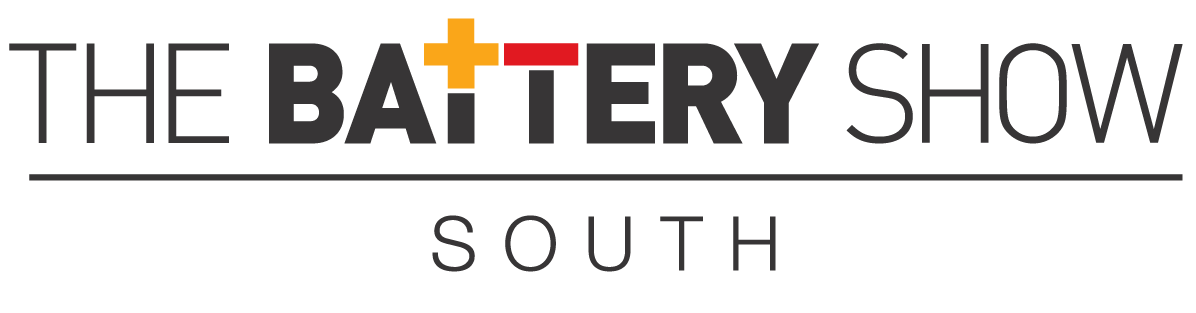
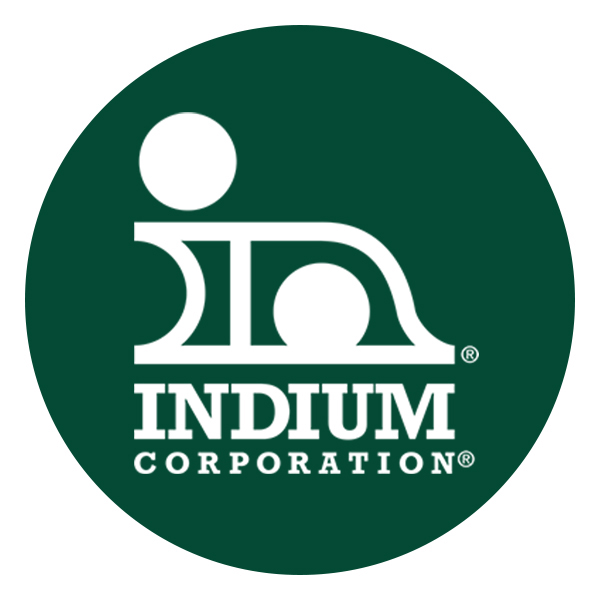
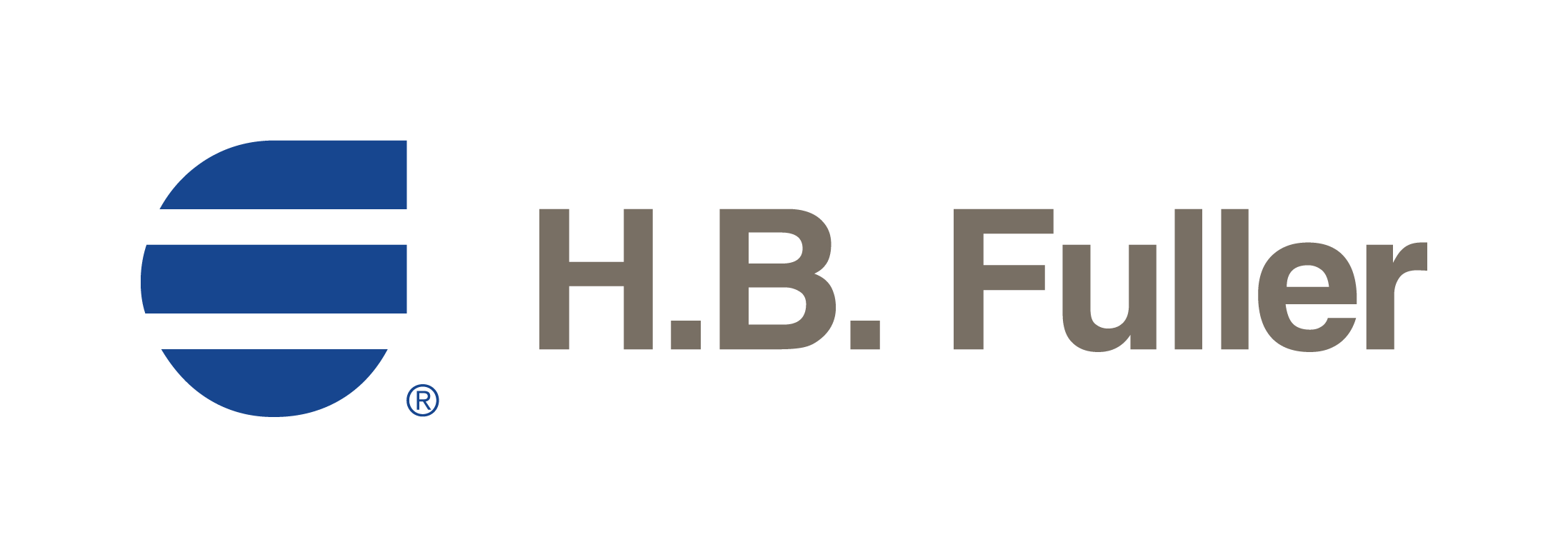