Lightning Strike electric motorcycle
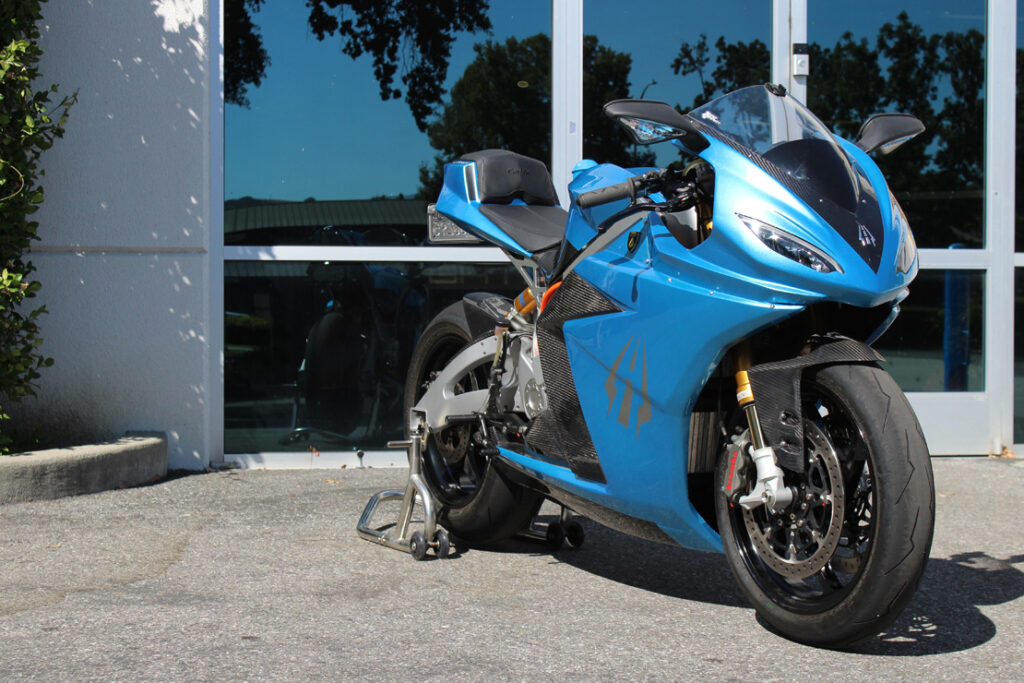
(Photos: Stewart Mitchell)
Road runner
Stewart Mitchell explains how this road-going machine was developed to take on the ICE competition – at a competitive price.
Lightning Motorcycles is an all-electric motorcycle manufacturer that produces the LS-218 ‘superbike’ and the more affordable Strike, which is pitched head-on against gasoline-powered alternatives. Founder of the San Jose, California company Richard Hatfield says, “The 218 was designed to survive extreme conditions such as racing flat-out around a track, and it was way over-engineered for what is typically needed for a production motorcycle; that is reflected in the $70,000 price tag for the top-performing R model. We needed something more accessible to take the fight to ICE-powered road machines.”
Describing the concept for the Strike, he says, “At a given performance level, the reliability inherent in the simplicity of an electric powertrain, as well as its quietness along with significantly reduced running costs, make it a very attractive prospect. However, electric motorcycles are not without their challenges – the biggest one being packaging. The e-drive system, the energy store and the control systems must suit the shape of a human rider, and they must be able to operate all the controls safely and comfortably.
“Although the frontal area of a motorcycle is relatively small compared to a car, the aerodynamic drag per unit of area is significantly more, and the aerodynamic efficiency of a vehicle heavily influences its range. For that reason, the Strike is a sports bike with a full aerodynamic fairing.
“We wanted the Strike to have a performance level similar to a 600-750 cc ICE motorcycle. It needed to be something that riders with varying levels of experience could find entertaining. That gave us a window of between 67 and 90 kW [90-120 bhp] peak output and a 10-20 kWh battery pack to provide reasonable range. That would position the Strike as a mid-range performance street machine, whereas the LS-218 is our all-out superbike.”
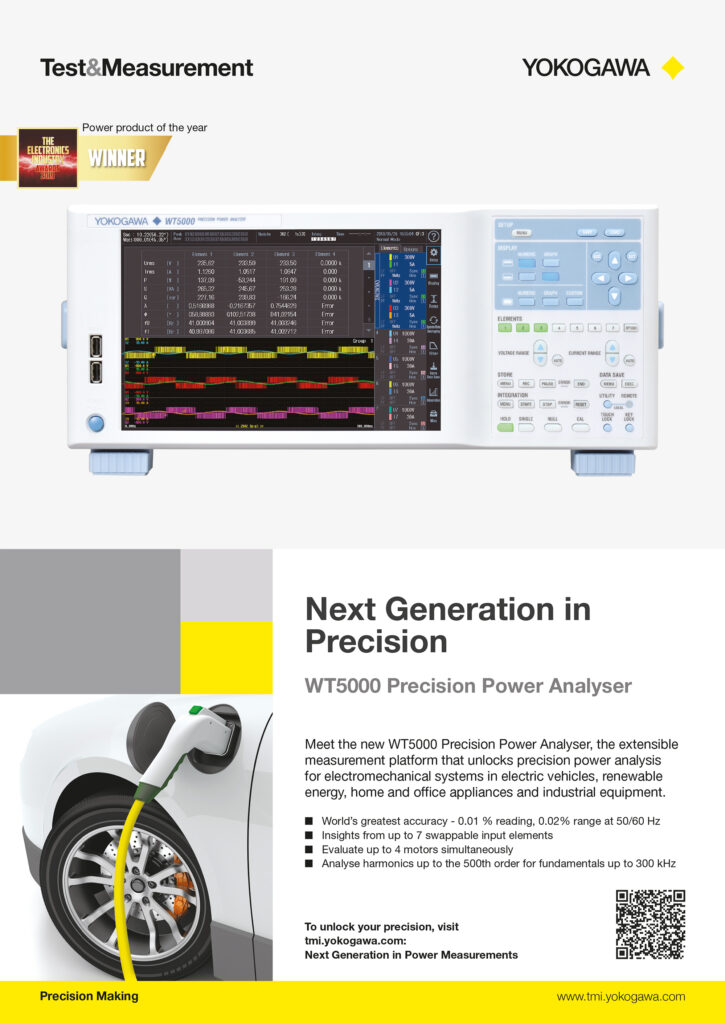
Even at this decidedly more modest performance level though, most riders wouldn’t use all of the Strike’s potential, but, as Hatfield says, “It’s much more fun to have performance that you don’t use than want to have some performance you don’t have.”
The Strike is targeted to be profitable at less than $13,000 for a base model, with a fully optioned version available for under $20,000. The concept for a cost-conscious, road-focused midrange sports motorcycle came about in 2017, and the production version was launched this year.
Strike overview
Hatfield says, “We decided to produce three models of the Strike, each with a different cell technology and price – a 10 kWh with up to 100 miles of range, a 15 kWh with up to 150 miles of range and a 20 kWh version with up to 200 miles of range.
“They all have a similar powertrain design, but the 20 kWh version uses a cell technology with an energy density of around 300 kWh/kg, whereas the 10 and 15 kWh machines use cells with much less energy density, albeit ones that cost less.”
Hatfield notes that nevertheless the 10 kWh version has a far higher C-rate than the 20 kWh version. As such, although the range of the bike is less, the cells can accept current more quickly and therefore charging time is shorter.
He says, “The cell technology in the 10 kWh pack isn’t leading edge in energy density, but it is an excellent, stable high C-rate, affordable workhorse of a cell.”
The 10 and 15 kWh versions produce 90 bhp, while the 20 kWh version produces 120 bhp, in each case from 300 V (DC). Each model has the same horizontally stacked pouch cell design. Hatfield notes, “The format of the cell doesn’t restrict us in this situation; however, the packaging envelope is the critical factor.”
The 10 kWh Strike weighs 455 lb, the 15 kWh 465 lb and the 20 kWh 485 lb. Every element of each version is a stressed member. The swing arm mounts directly off the back of the motor, the battery pack mounts off the front of the motor, and the forks mount off the front of the battery pack.
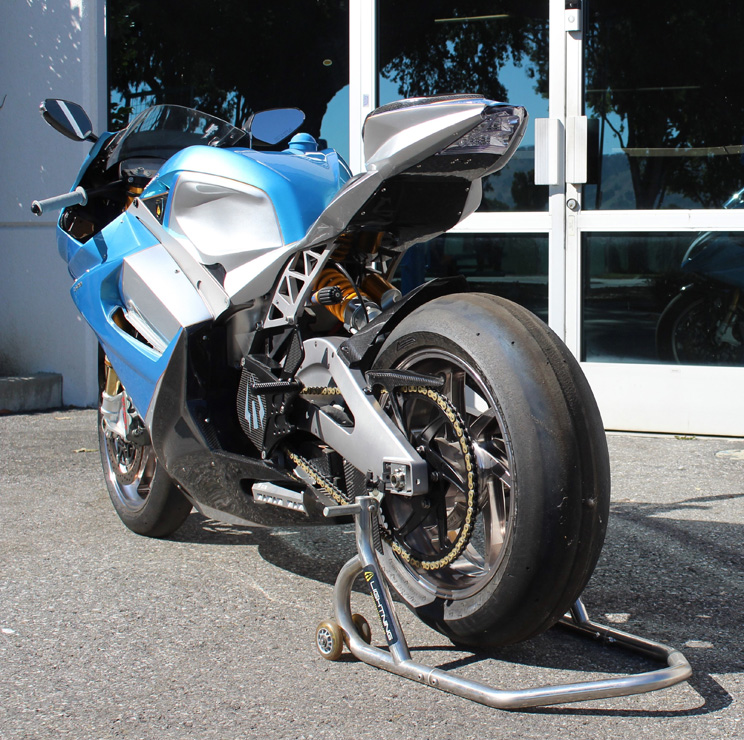
“Everything is performing multiple functions, and that was intentional to get the weight down,” notes Hatfield. He adds that a lot of CAD modelling and then physical testing went into ensuring all the components could work well from a primary function perspective, and have the right amount of compliance and flexibility to make the desired chassis stiffness. “That was a very challenging task,” he says.
E-drive
The Strike uses a three-phase highperformance copper core radial flux induction motor. Hatfield explains, “Radial flux motors derive their power from their length, which meant we could use a motor with a small diameter for the power target, which suited the geometry for the Strike well.
“However, there is a trade-off with the radial flux motors because they are high-speed machines, meaning there is a gearing requirement to bring the output speed down to wheel speed. Our philosophy was to avoid building a complicated gearbox, because that would add weight and cost. We also had to consider the reliability of things such as gears, bearings and shifter mechanisms.
“Given that the performance output of the Strike motor is substantial, we were able to implement a direct drive with a reduction gear to the output sprocket that drives the rear wheel via a belt.
“Radial flux motors tend to require higher rpm to make equal power compared to axial flux. However, axial flux systems offer better torque at lower rpm but run out of peak power lower in the rpm range than a radial flux. Axial flux motors tend not to be as power-dense as radial flux ones, and we wanted to be able to take power as high as we reasonably could and push peak torque to the redline.”
When it comes to temperature tolerance and manufacturing costs, Hatfield notes, that’s where radial flux induction motors have advantages. “There’s a slight difference in efficiency by a few per cent at certain speeds and in certain load cases, but that is where the trade-offs come in,” he says. “We felt that a minor percentage of efficiency was worth sacrificing to maintain the product’s price point.
“For the Strike motor, we found something of a sweet spot for price, reliability and performance. Reliability was critical because you can get a bad reputation quickly if your products are unreliable. We knew we would have lower failure rates using an [asynchronous] induction-type motor solution than we would with a synchronous permanent magnet machine, as you can’t demagnetise an induction motor.”
An induction motor is cost-effective to manufacture, and since it doesn’t have a permanent magnet array the cost is lower and more predictable than for a synchronous machine.
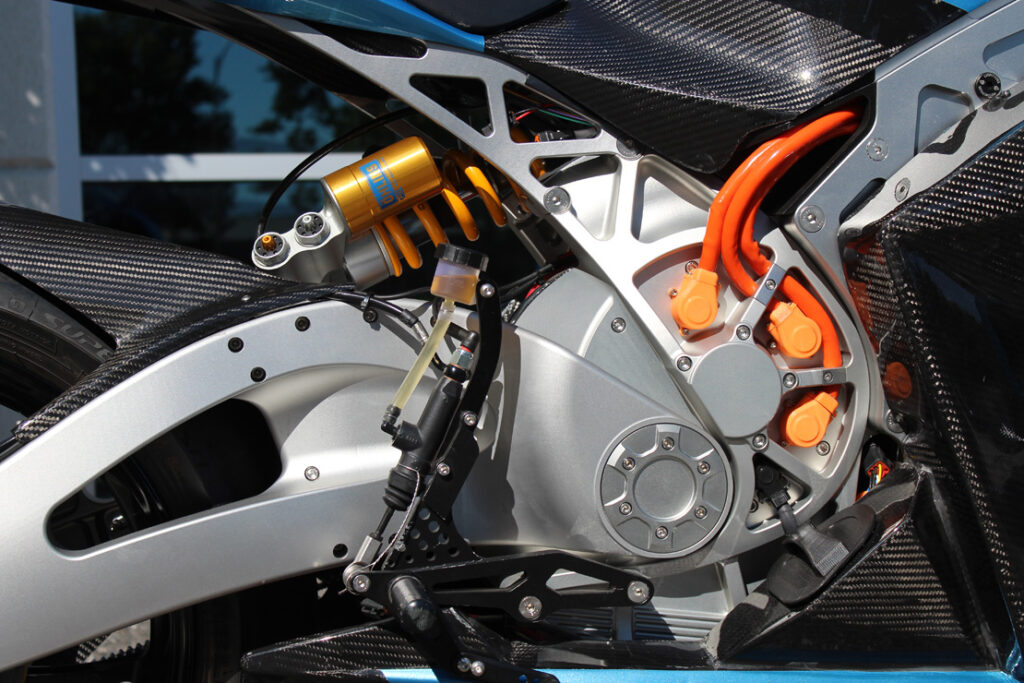
Hatfield notes, “There are also some ways that induction motors can be safer than permanent magnet motors. For example, if you lose one phase in your inverter with a permanent magnet motor, it can often lock the drive wheel(s), but induction motors won’t do that.”
The core of the Strike motor consists of heavy copper bars connected at both ends by conductive rings that electrically short the bars together. The stator is built from stacks of electrical steel laminations.
The motor was designed and is manufactured in-house. The stator and the rotor were developed in partnership with subcontractors.
The more current that is added to an induction motor, the more torque that is produced. However, efficiency falls as current rises.
That wasn’t an issue, according to Hatfield. “Although we lose a bit of efficiency at full load, the induction-type motor behaves much better in a broader range of operating conditions than the alternatives,” he says.
“Also, this is a technology that has been proven in automotive use. We have a slightly different set of conditions on two wheels. Typically, the power-to-weight ratio is much higher, so typical use is at a relatively low percentage of peak performance. Given that, the induction-type radial flux design with a 90-120 bhp output was the best target.”
As for reliability, he says, “One of the standard failure modes in induction motors is bearing failure. You can end up with premature bearing failure due to the bearing creating an alternative circuit running through its parts, grounding the charge. That can cause the material to break down and damage the bearing’s internals.
“Another failure mode is the rotor position sensor, which is quite sensitive to heat. If you run it too aggressively on the temperature, you tend to fail it. Most motors have a Hall effect sensor, an encoder coupled with an encoder bearing or a resolver from a driveline speed sensor.
“You have to determine what percentage of the motor’s costs you want to spend on position sensing. We have chosen a very robust (undisclosed) solution.”
As for the weight, Hatfield says, “We didn’t set a benchmark on the weight; we just looked for the best set of compromises we could achieve between adequate power, cooling and reliability. There were some trade-offs if we went for a smaller package as far as cooling is concerned because there needed to be a certain amount of fluid flowing over the hot parts of the motor package, and if it is too densely packaged the cooling becomes much more challenging.
“If we’d gone for a smaller motor, it would have been shorter, not smaller in diameter. It would have had to run at a higher percentage of its peak power for the same performance level, and even just a couple of percent of extra load can have a major impact on reliability. The higher the percentage of peak power operation, the more you get into greater current losses and heat generation that leads to flux losses and inefficiencies.
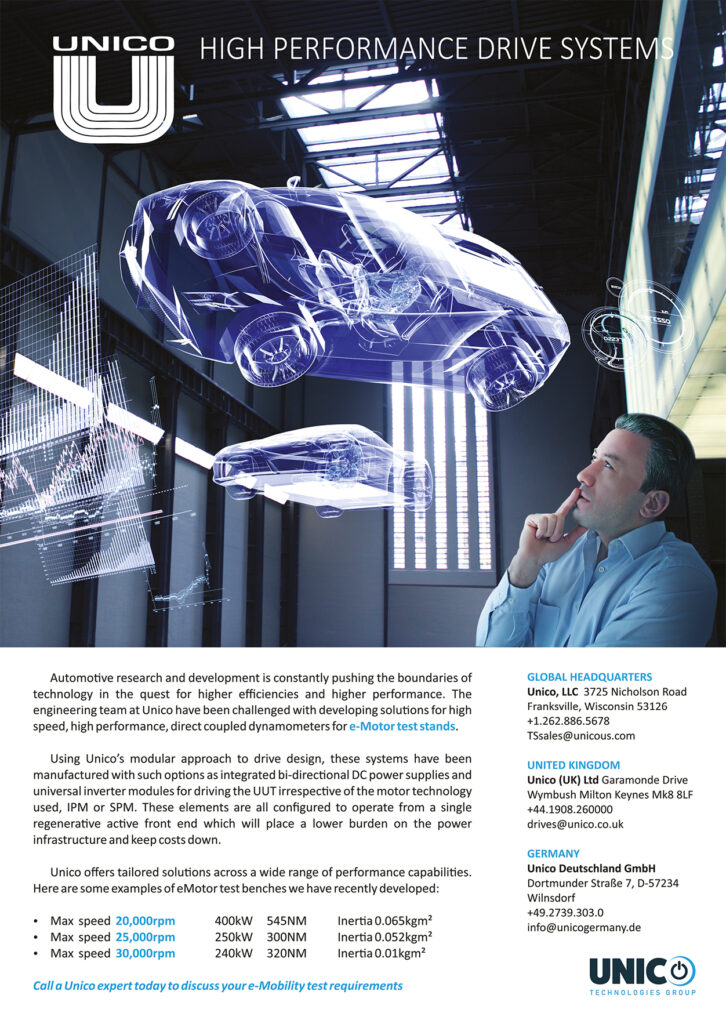
“Then you have the negative spiral of trying to push more power through less copper, and getting more heat and less power out of it. That trajectory continues even in steady-state demand, so the problem just gets worse and worse. In fact, we overengineered some of the elements of the Strike to make sure they could take some punishment and that we wouldn’t be close to the limits on the powertrain.”
The Strike’s induction motor is a four-pole design, which Hatfield says was chosen because that allows operation at a reasonably low switching frequency while maintaining high efficiency and high rpm potential. “You sacrifice a bit of motor acceleration compared to a motor with a higher number of poles, but this technology fits the targets of the motorcycle in terms of cost, reliability and performance,” he says.
The rotor design has four magnetic poles, with the two pole pairs opposing each other around the rotational axis. Hatfield explains, “Splitting the poles gave us more choices with the inverter and operating voltage. We can’t go as high in rpm as some of the radial flux induction motors out there, but again this is a cost-effective machine.”
To get to its 15,000 rpm redline, the motor runs at 500 Hz AC. As for the inverter technology, Hatfield says, “Mechanically, we kept all the IGBTs equal in length and as short as possible to maintain high-performance switchgear. The number of poles we have and the maximum rpm, owing to the maximum speed at which the polarity of the electromagnetic field can be switched, were all considered at every phase of the powertrain’s design. “We didn’t want to go any higher than 500 Hz because the more often the polarity of the field has to be switched per rotation of the rotor, the more expensive the switchgear.
“The efficiency is very high relative to the best induction motors on the EV market today. We tried to minimise the slip as much as possible, because slip in an induction motor has a significant impact on efficiency. We designed the motor to be optimally efficient at the speed range of 50-80 mph at very low throttle opening, because that’s where you’re going to spend most of your time if you are cruising on a long journey.
“We only traded away a bit of efficiency at rapid acceleration from standstill and for cruise speed efficiency, because this bike is really for transient-throttle riding and fast changes of direction – although we did want reasonable range for cruising because that’s what people want when they compare this to gasoline bikes.”
The stator of the Strike motor is built from high-silicon magnetic steel laminations, which Hatfield says is for maximum power density. “Our lamination design has a major impact on reducing the heat generated and increasing the efficiency,” he says.
“We use one specification of electrical steel that’s very high quality. It’s being used in all sorts of magnetic applications because it increases magnetic density. It also has excellent mechanical properties, and there is good data that suggests we can use it in other components to make them less prone to cracking and lighter than they are now.”
Battery
The Strike’s battery pack was designed in-house, and uses cells from another manufacturer. Hatfield says, “We see ourselves as beneficiaries of the battery wars, not as participants. We want the opportunity to work with every improving technology when it is made available to us.”
The battery pack measures 12 in wide, 24 in high and 10 in deep. The width exploits the maximum real estate within the body of the motorcycle, and the height is as much as the team could stack into the main body above the narrowing area at the base of the motorcycle, which is necessary so it can lean over. The charger module is located at the bottom of the pack in that narrow section of the bodywork.
All commercially available cell types, chemistries and energy densities were investigated during the Strike’s design. Hatfield says, “These were critical for the Strike because the charge-discharge rate we were targeting affected some of the cells’ rated capacity over time and in certain regions of SoC [state of charge], and therefore the energy density of the pack.
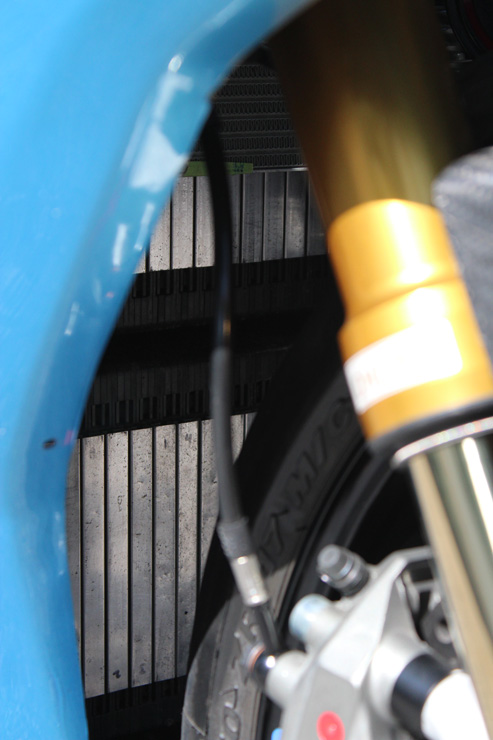
“Because we wanted the battery to be able to handle quite aggressive charging and discharging, we had to overrate on the capacity of the battery pack. The amount of energy that can be extracted from the battery is reduced over time owing to cyclic loading if there is no headroom in the capacity and if the cell chemistry can’t take the prolonged exposure to that condition.”
The Strike uses lithium NMC (nickel manganese cobalt oxide) pouch-type cells. Hatfield says, “The energy density and characteristics required of electric performance motorcycles make NMC an ideal solution here, more so than some other chemistries that we looked at, such as LFP [lithium iron phosphate]. One reason is that the LFP cells are nominally 3.2 V, whereas the NMC cells are 3.6 V nominally, and NMC operates at a higher charge range and voltage.
“As with everything though, it was a trade-off, because LFP performs well with low resistance thanks to its phosphate cathode material. You can run them with high current and long cycle life, and they have decent thermal stability, and a reasonable tolerance of high cycle abuse.
“LFPs also tolerate 100% SoC and are less stressed than other lithium-iron energy storage systems by undervoltage for prolonged periods. In general, though, despite the pros of the LFP cells, we needed higher energy density, which made NMC cell technology much more suitable.
“Everyone we’re working with is developing NMC cells, but we’ve used quite a few different manufacturers, and the technology keeps getting better. There are a bunch of commercial considerations too, as a given battery manufacturer might only want to work with one OEM, or maybe have to provide exclusivity to a certain OEM group. We use NMC cell technology in all our Strike models, although we have different suppliers for each model spec, with differing energy densities and costs.”
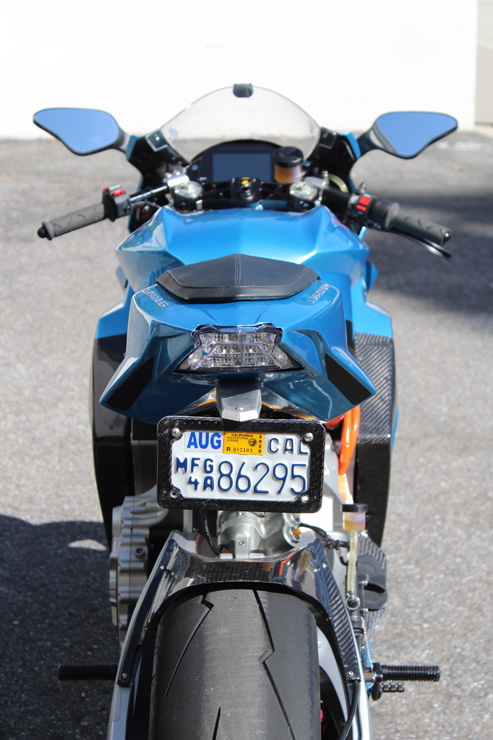
The company uses an automotive pouch-type NMC cell with an energy density of about 300 kWh/kg. Hatfield says, “The energy density was a bit better in the pouch cell than in the cylindrical ones, but there are some trade-offs. In most cases, we are interested in a certain performance level of the battery pack, although because our motorcycles are for the street, we had to consider the range as well.
“You have to find the trade-off between weight, capacity, C-rate and so on. The advantage of a cylindrical cell is that it’s spiral wound, and when the materials inside expand and contract, it usually remains in its containment. With pouch cells though, you have to allow for outgassing and expansion and contraction, but it is a lot easier to get heat out of a pouch cell.
“With the pack configuration for the Strike, we have a sandwich plate construction where a pouch cell is flanked by an expansion material, then a heat rejection plate alongside that in turn is alongside an air channel between each cell.
“Also, from a cooling perspective, our investigations found that getting the heat out of the centre of a spiral-wound cylindrical cell was much harder than a flat pouch cell, because the core of the heat-generating elements are in the centre of the coil. You can direct air or coolant around the outside, but the centre – where all that heat is generated – is very challenging to cool.”
The NMC pouch cells chosen by Lightning Motorcycles have the anode and cathode separated by a composite material, and the cell is filled with an electrolyte fluid. The electrode carries current, and the active material stores the energy. The high energy capacity of these cells comes from the relatively small metal electrode – most of the cell is made up of the active material.
Each cell measures 205 x 157 x 7 mm, and each outer is made from soft aluminium sheet with thermal conducting tabs at either end to draw out heat from the centre. Aluminium plates connected to the tabs at either end are a tall U-shape for maximum surface area to allow the heat to dissipate as efficiently as the packaging constraints allow.
The Strike’s battery pack is a 72S 2P (a total of 72 cells split into two modules in parallel) configuration; all versions of the bike follow this standard. Each cell is 3.6 V nominal. Hatfield says, “There’s a bit of headroom, so 4.15 V is the highest we go on the voltage of the cells during charge/high load. 4.1 V is conservative at full voltage for these cells, and discharge stops at around 3.0 V.”
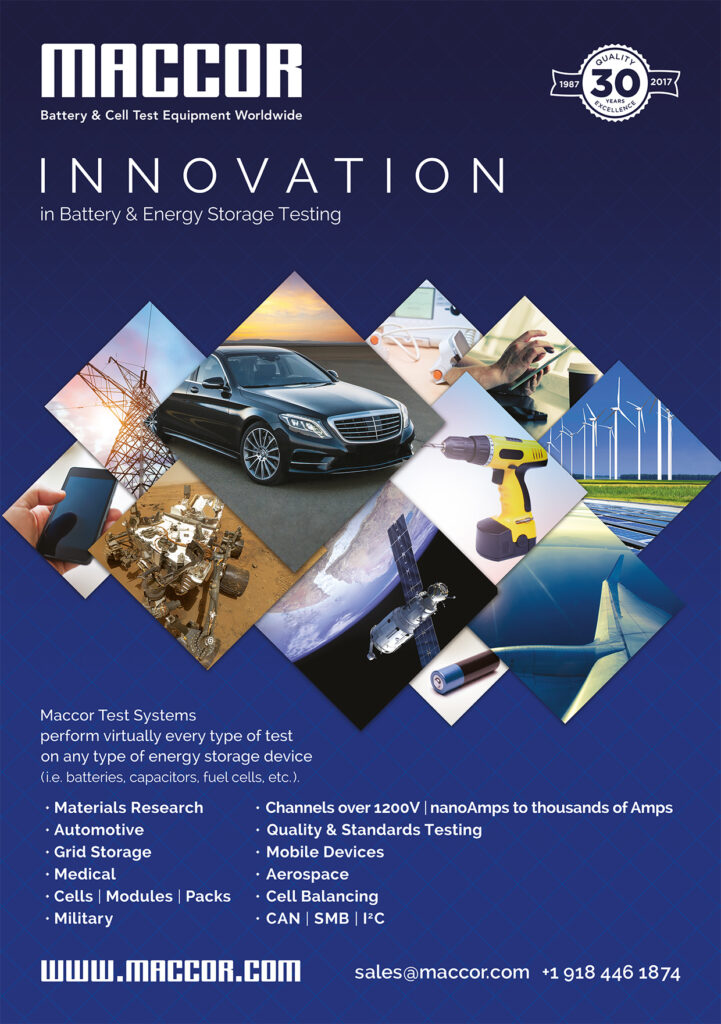
Regarding the targets for the module configuration, Hatfield says, “A lot of it is mechanical considerations and packaging. If you use one module or cell array above another, it’s much easier to jump from module to module without running too much cabling around the bike. That is what we have done with the two series arrays we have in the Strike.”
Charge and discharge
The main property of a battery – its capacity – is not fixed but varies with temperature, discharge current and other factors.
“The battery management system [BMS] has three essential functions to control this,” notes Hatfield. “One is to make sure all the cells are at the same level of SoC, ensuring that you’re not allowing any cell or module’s SoC to be too high or low. The second is to keep the cells in balance, ensuring that all the cells and modules have the same SoC. The third is temperature management.
“When the battery is charging, the BMS monitors the shift in energy from cell to cell, to ensure they are all even and that their temperatures are within design parameters. If the battery’s healthy and it’s performing linearly, the BMS doesn’t have much to do.
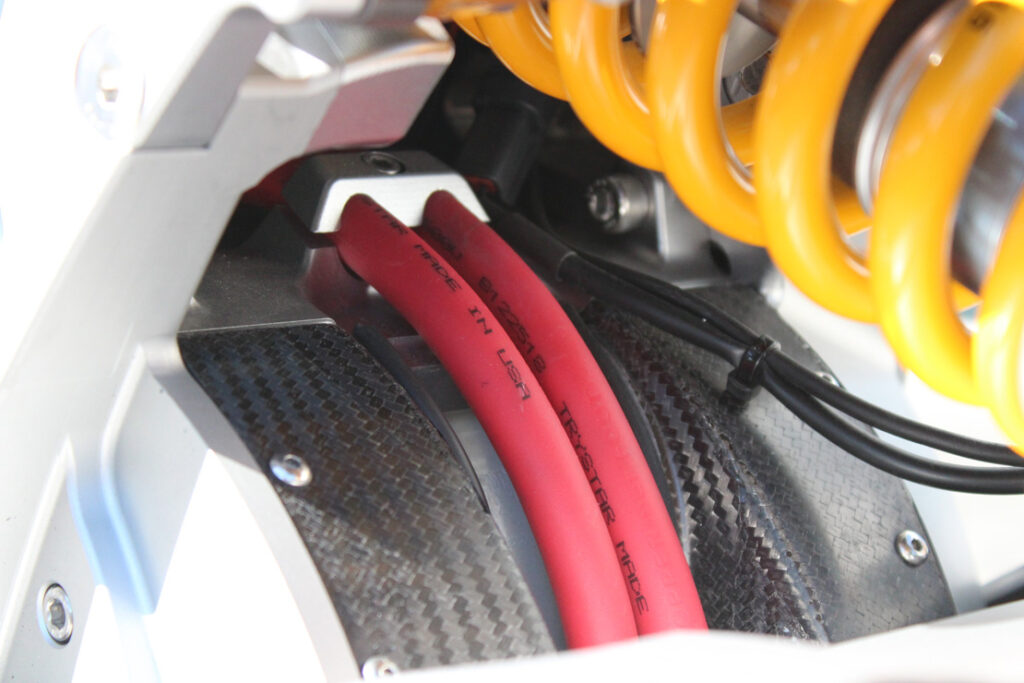
“The BMS reads all the cells many times a second doing that analysis of temperature, SoC and current. We have been developing it for many years, and we use the same basic BMS topology on all our products. The system is very reliable and can measure a very fine point of voltage on each cell.
“The battery often performs better with higher temperatures as far as the chemical reaction is concerned, but the heat does have an impact on the life of the battery, and in extreme cases can cause thermal runaway. Typically our BMS begins to take corrective actions when the battery temperature approaches 130 F [54 C].
“For the longevity of the cells, the battery is better off left at 40-60% SoC if it’s really hot. As for when it starts getting cold, full load at below 40 F can cause some degradation of the cells, and the colder you get after that, the more it falls off.
“The good thing about the motorcycle applications is that, in general, if it’s comfortable for you to ride the motorcycle then the batteries are comfortable to run. If you’re uncomfortable then the chances are the battery is uncomfortable as well, although the battery is probably slightly more tolerant than you are.
“The battery is heavy and dense, and has a lot of thermal mass. That is used in its favour to maintain temperature for a certain amount of time post-charge, to ensure the cells don’t get shocked by the change of temperature when the battery is taken off charge.
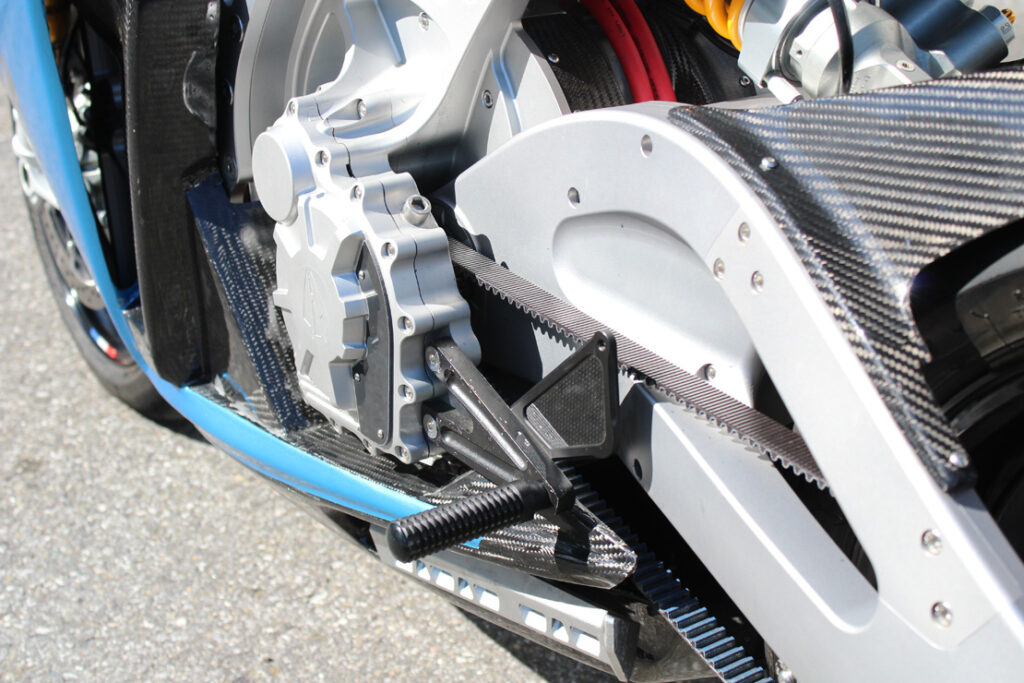
“As you’re riding the motorcycle, the BMS will let the battery generate some temperature within the cells to maintain the ideal temperature window; that is between 60 and 100 F. We don’t want to get the battery too hot because the electrolyte can evaporate, which can lead to damage or failure of the cell, and even thermal runaway.”
The Strike’s battery is air-cooled. Hatfield says, “A motorcycle with an open front potentially has a lot of airflow going through it. We worked with battery companies who helped with the development of a pack shape, size and frontal area to generate the right cooling system for the battery pack. It uses aluminium sheets within the sandwich of cells to wick the heat out to air channels where heat can be carried away. The aluminium sheets are located between each cell in series.”
One unique feature of the cells is the location of the cooling tabs, on opposing ends of each cell rather than alongside each other on one end. “We have found that having tabs at opposing ends of the cell means we have a more uniform temperature distribution across the cell, as opposed to a heat pattern where there are hot and cool spots throughout,” says Hatfield.
“You’re not concentrating the heat in the same place. Also, we always stack them sideways, because the cells reject heat out of the sides as well as at the ends where the tabs are. Stacking them parallel to the floor can trap the heat and put lot more pressure on the central and lower cells. For that reason, we run them perpendicular to the ground, across the width of the motorcycle.”
The Strike uses a combined charging system that covers every type of public electric charging connector for EVs. The BMS monitors the temperature of the cells, and when the cells reach a certain threshold, it will reduce the charging current.
“Like most people in the EV business, we leave some headroom regarding the minimum and maximum SoC,” notes Hatfield. “That is because over- or under-charging can make the cells very susceptible to thermal runaway.
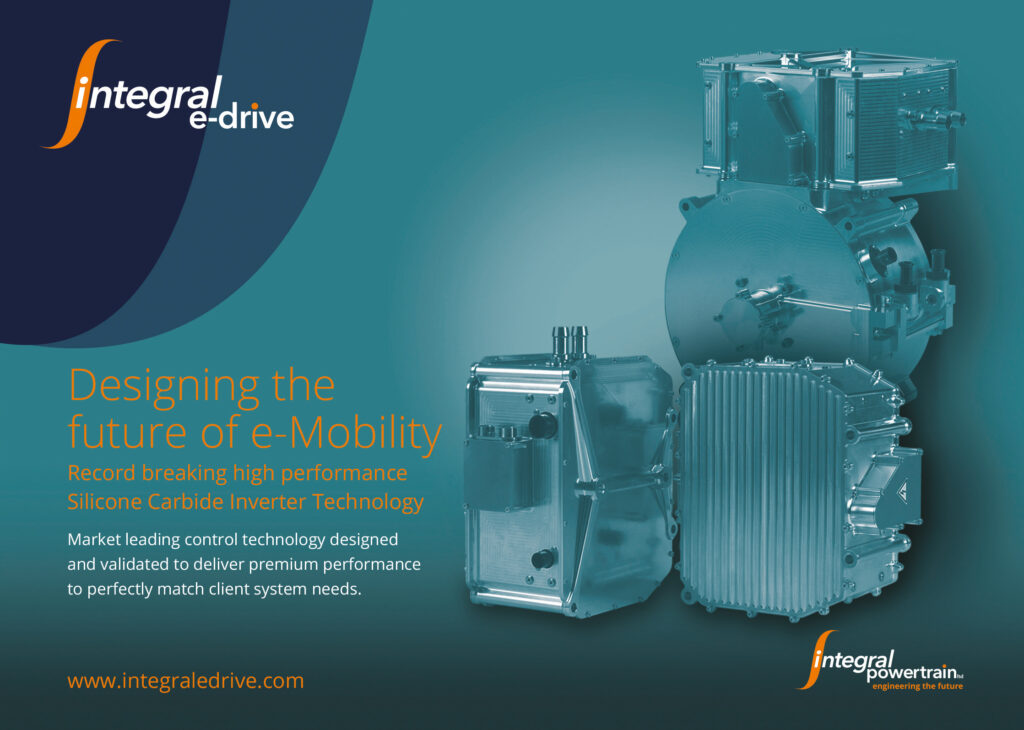
“However, it is critical to have that headroom in place because no-one wants to jump on a motorcycle that’s reading 80 or 90% charge – they want to read 100% after every charge. As such, in terms of the running of the motorcycle, between 20 and 80% SoC is pretty typical.”
Regeneration
All Strike models have regenerative braking capabilities and this, Hatfield says, can give the Strike different personalities.
He notes, “Over a regular ride on the street, it is not likely that there will be much more than 10% energy recovered, and even 10% would be a very heavy regen-bias drive cycle. We couldn’t make the battery pack 10% smaller because we would then be relying on the rider getting that amount of regen.”
The rider can operate the regen within preprogrammed limits as they desire. It is speed-dependent, such that the initial deceleration is more aggressive at closed throttle over a certain speed, and it tapers off as the motorcycle’s speed falls. That, Hatfield says, was to ensure easy slow-speed control and to provide an ‘engine braking’ sensation similar to that which many long-term motorcycle riders are accustomed to.
He says, “I found for myself, and for many people who have ridden the Strike, that the longer we ride electric motorcycles, the more regen we want. I have it set up such that during typical street riding I only use the brakes to hold me at a hill on a stop, and I have enough regen during normal riding that I don’t have to use the brakes at all.
“Tailoring the regen for individual rider preferences is managed within the vehicle control unit [VCU], and is adjusted through the rider interface. However, if the SoC is close to 100% we limit regen so as not to overcharge the cells, because the current that is pushed into the battery under full regen can damage the cells.”
Control
The inverter is managed by the VCU, which receives inputs from motor speed sensors, current draw sensors from the motor, the BMS, temperature sensors throughout the driveline and the throttle for both deployment and regen. The inverter determines the correct current required from the motor as a function of the torque demand as applied by the throttle.
The data from the BMS is prioritised over throttle inputs, because the battery charging and discharging requires the most monitoring. The inverter uses IGBT semiconductor technology, which allows for a maximum current of 700 A. It is in the IGBTs where most of the heat in the inverter is generated.
The decision to use IGBT semiconductor technology, Hatfield says, was because of the target efficiency at the 300 V running power of the Strike. “We run what is considered high current at 300 V,” he adds. “That automatically favours IGBTs over MOSFETs.
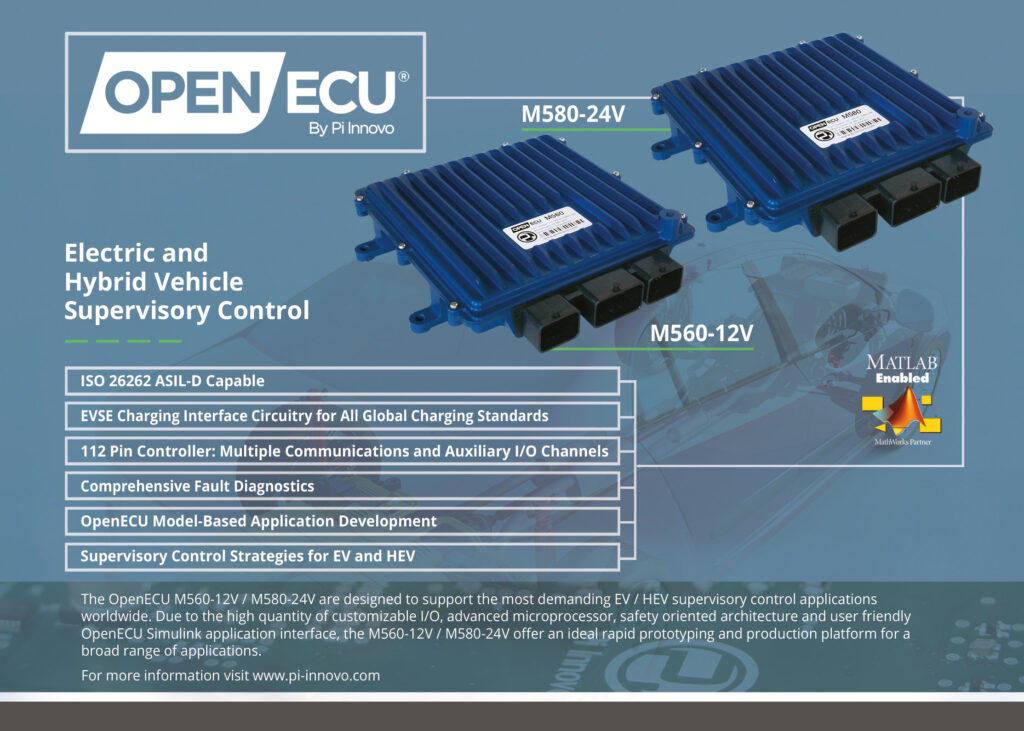
“The choice of semiconductors was carefully considered, because if they cannot manage the system correctly, they can cause major issues with electrical power dissipation. It’s almost like electrical friction, which can give us more energy to power the motorcycle if we minimise it.
“However, because cost and reliability were a consideration here – and in the knowledge that traditional silicon switch technology has the maturity to give us the reliability we wanted – we stuck with it for our motorcycles.”
The power management system consists of chipsets in modules of 12 series connections. As such, there are six of these modules connected to the 76 cells in the battery pack.
The capacitor design in the inverter was another element of the control technology that was heavily investigated. “If you go for a large capacitor, you can get more instantaneous power, but of course you’ve got space and temperature considerations,” Hatfield says. “As with everything else, there is a trade-off.
“The biggest challenge with the highly power-dense motorcycle application is EMI. When you’re in a high electrical power environment in a confined space with all these electronics on a motorcycle, electrical noise management becomes a big deal.
“We’ve gone a long way to try to reduce this where possible. We use twisted pairs for communication lines, a series of different types of capacitors to filter out noise, we place electrical boxes that could interfere with each other as far away as possible and use a series of different shielding techniques between physical parts.”
Thermal management
One advantage of induction motors over many other traction technologies on the market is heat tolerance, although for the high-performance, high cyclic loading behaviour of the Strike, Lightning Motorcycles designed a bespoke liquid cooling system for the motor and inverter.
The air-to-liquid heat exchanger sits in the conventional radiator position on a motorcycle, in the body behind the front wheel, as it allows for maximum airflow for rejecting heat. The inverter and motor are cooled on the same circuit using a water-glycol solution running through isolated channels.
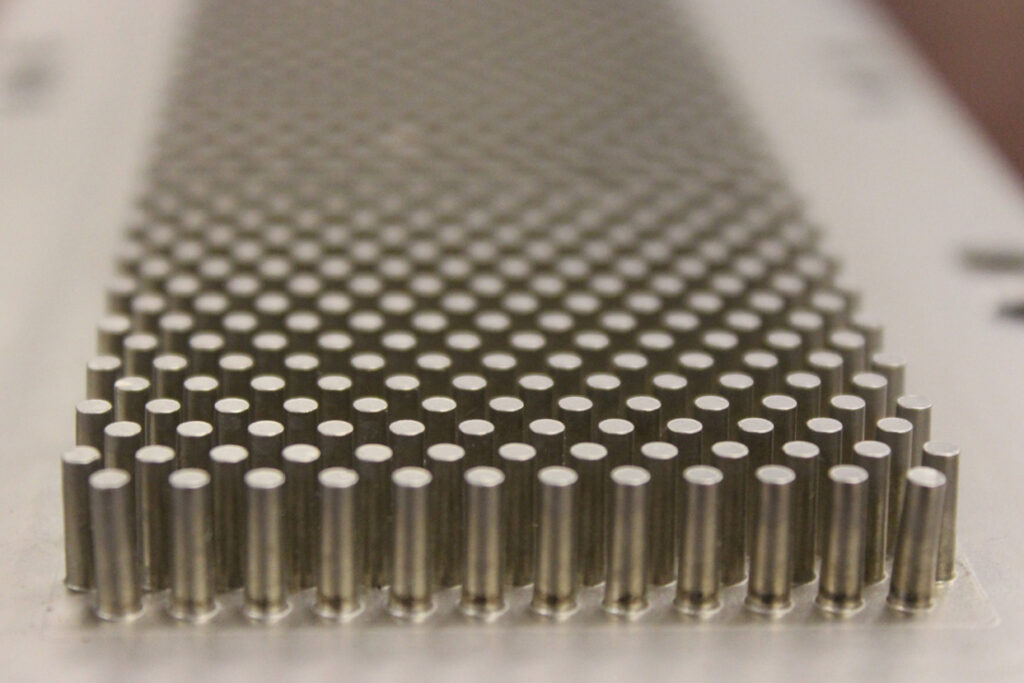
Hatfield says, “The cooling system had been a particular consideration throughout the entire design process of both the inverter and motor. It was critical to fashion the IGBTs and the rest of the power electronics in such a way to accept the cooling, as well as function as effectively as switchgear.
“The challenges with the indirect (water jacket or water channel) approach are to do with the isolation of the water and the parts it is meant to be cooling, and keeping the temperature the same throughout the component(s). You can’t easily avoid the components close to the pump outlet being at a lower temperature than the heat exchanger inlet side. The thermal delta across the motor can change its electrical resistance, so an efficient and uniform cooling solution is critical.
“We found that as far as overall efficiency is concerned, the heat exchange process using the water-glycol system through sleeves is more efficient than direct dielectric fluid cooling. However, you can’t get water-glycol into the same places as dielectric fluid, so some complex analysis was done to position the jacket as close to the heat sources as possible.
“During that analysis, we also discovered that thanks to the better thermal capacity of water-glycol, and its density and viscosity, we could run the cooling circuit pressure at a level where the pumping losses are very low compared to that required of a direct fluid cooling solution. We run the cooling system on the Strike at similar pressure levels to those of an ICE system.
“You’re looking at a factor of five times lower than the direct fluid cooling system. It’s not five times more efficient overall though, because of the pressure delta, as the water-glycol cooling system is less focused in terms of where it’s drawing heat from than the direct fluid system, but overall it is a more efficient system.”
The cooling jacket fully surrounds the motor. There are no gaps in the stator for cooling tabs or such like material to help pull heat to the jacket, it’s simply full contact around the outside. However, the paths the heat takes from the core of the heat-generating sections to the cooled housing have been carefully considered. The housing is made from a 7075 T6 alloy, which as well as being load-bearing is thermally conductive.
The same cooling circuit for the motor cools the inverter. The inverter is fed first from the pump outlet, then coolant flows to the motor, the heat exchanger and then back to the pump. Unlike the motor, there are specific thermal paths that run from the core of the heat-generating elements of the inverter to the cooling plate that carries the heat to the water channel. The power electronics, including the capacitors, DC-DC converters and switchgear are mounted on the same plate.
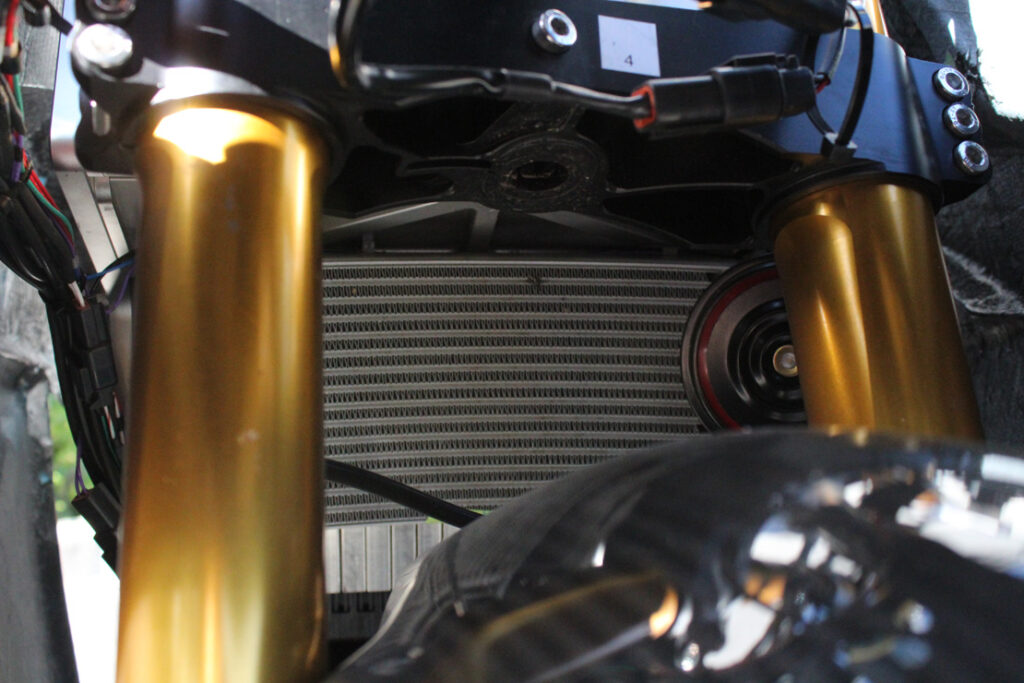
The coolant channel is located on one side of the inverter, and the outside of the cooling plate (inside the cooling channel) has an array of extruded pins to increase the cooling plate’s thermal capacity and surface area. The higher surface area on the inside of the cooling plate also regulates the pressure as the volume increases through the cooling housing on the side of the inverter.
Hatfield says, “This cooling package increases the longevity in the IGBTs, keeping them within a narrow thermal range. There are very disparate materials inside the IGBTs, and when you start heat-cycling them, they can start to fail.
“The IGBTs’ coefficient of thermal expansion is fundamental to the packaging, as the more they expand, the less space there is around them for the temperature to be rejected. The most fundamental thing we do is use an adequately sized liquid-to-air heat exchanger and have adequate flow.”
The cooling plate is fastened by an O-ring directly to the cooling channel. There is just one cooling plate on the inverter unit, providing the sole area for active cooling. The chassis of the inverter is machined from the same material as the motor housing, so some heat is rejected through that as well.
Lightning Motorcycles opted for a mechanical pump for the cooling system. Hatfield says, “When an electric pumps fails, particularly for high power-dense e-drive cooling system applications, you run the risk of not knowing about it, and you have to take steps to protect the motor. With a mechanical system, while the motor’s turning so is the pump.”
Driveability
The nature of an electric drivetrain allows it to be accurately tailored for a desired response and driveability. The Strike has several driving modes that offer different throttle responses, maximum power and regeneration.
Hatfield explains, “The whole characteristics of the bike can be tuned with the mode that the motorcycle is being ridden in. In the standard set-up, the first 60% of the throttle movement is 30% of the torque command, and then the last 40% is 60%, so it is very progressive.
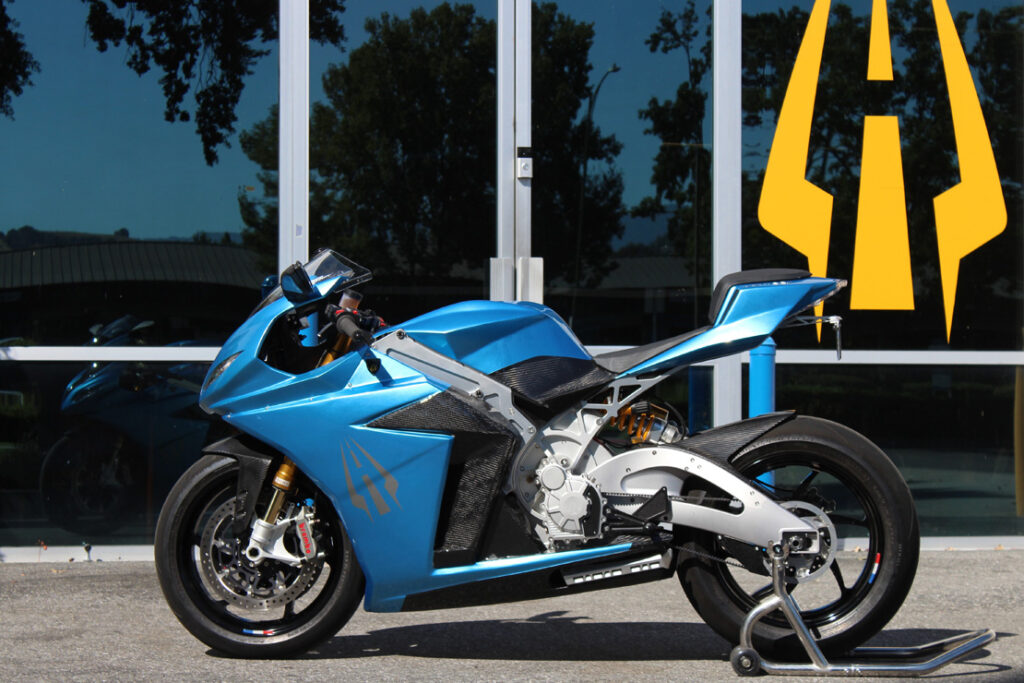
“That distribution is adjusted to be more or less reactive in different driving modes. The most sporting is tailored for excellent power and fast drive off a corner while providing good feedback, so the torque delivery is high but progressive and predictable. At lower speeds and torque settings, the output is much reduced so that the motor output doesn’t overpower the rear tyre.
“As is the nature of e-drives, we can manipulate the characteristics of the torque delivery for almost any amount we want under peak torque. That means, if requested, there is scope to tailor the torque delivery to a customer’s preference.”
The future
As to future machines from Lightning Motorcycles, Hatfield says, “We are always looking to stay up to date with the latest in e-mobility technology, notably cell technology heading towards the 400 kWh/kg mark. Although we are a little way off that at the moment, I think that level of technology will be revolutionary for the e-mobility market.”
Datasheet
Lightning Motorcycles Strike
(Carbon edition)
Vehicle Type: electric motorcycle, road
applications
Motor: Lightning FluxVector 300 V,
three-phase AC induction motor.
Maximum rpm, 15,000
Motor cooling: indirect water-glycol
liquid
Output: 90 kW, maximum power,
245 Nm torque
Inverter: silicon IGBT
Inverter cooling: indirect water-glycol
Battery pack: 20 kWh, 72S 2P
configuration, NMC pouch cell
Battery cooling: air-cooled.
Charger: 6.6 kW onboard charger
Transmission: clutchless direct
single-speed drive
Final drive: belt
Weight: 219 kg
Front suspension: 43 mm forks
Rear suspension: aluminium swingarm
with cantilever monoshock
Front brakes: twin steel discs with fourpiston
caliper
Rear brakes: steel disc with twin-piston
calliper/optional regenerative braking
Some key suppliers
Motor: in-house
Brakes: Brembo
Suspension: Ohlins
Display: AIM
Tyres: Pirelli
Fluid lines: Earls
AM machinery: Lulzbot
ONLINE PARTNERS
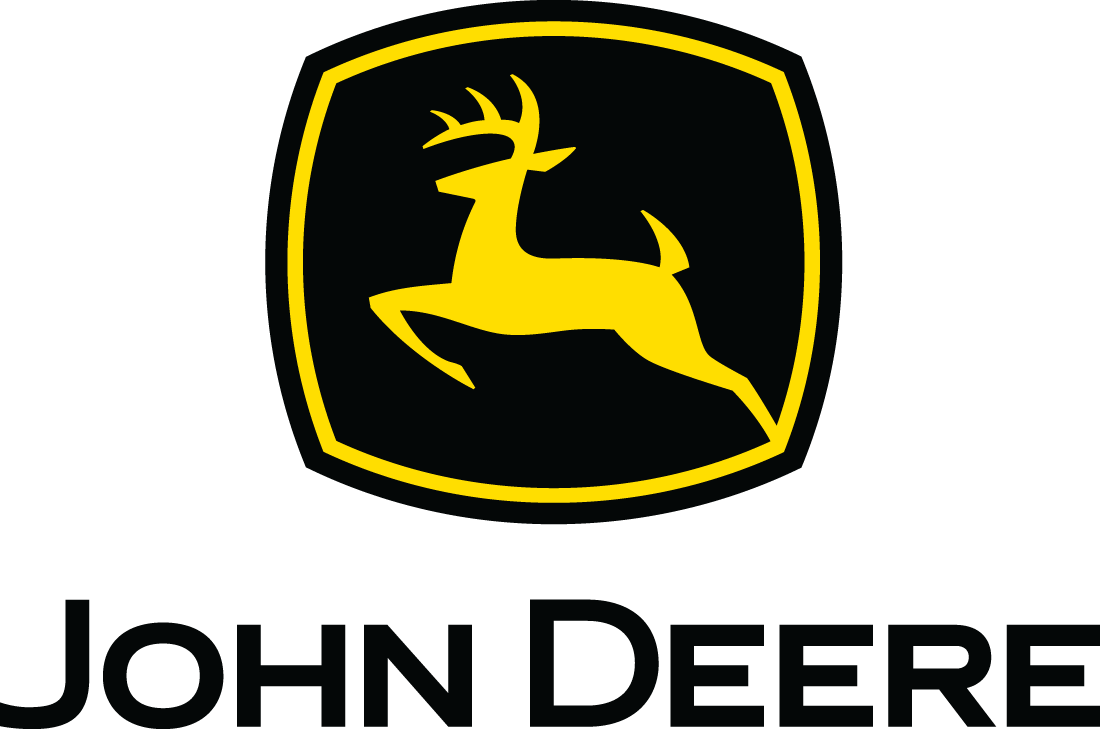
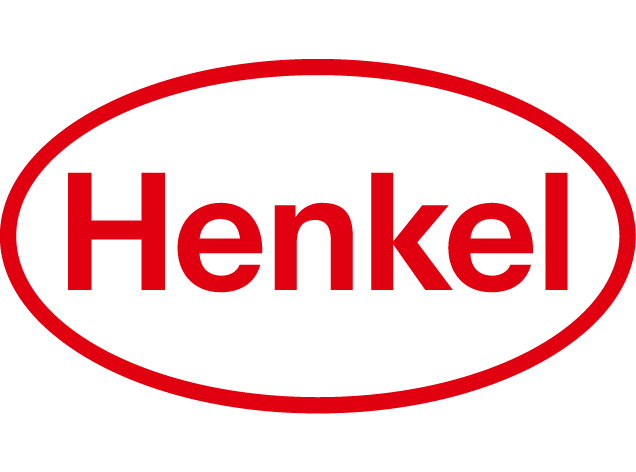
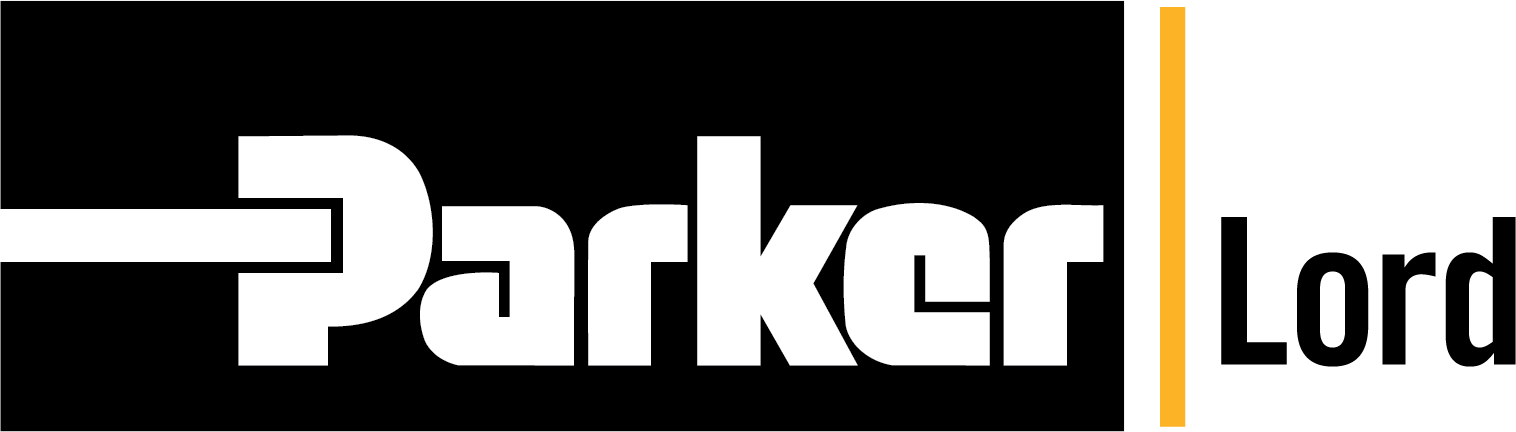
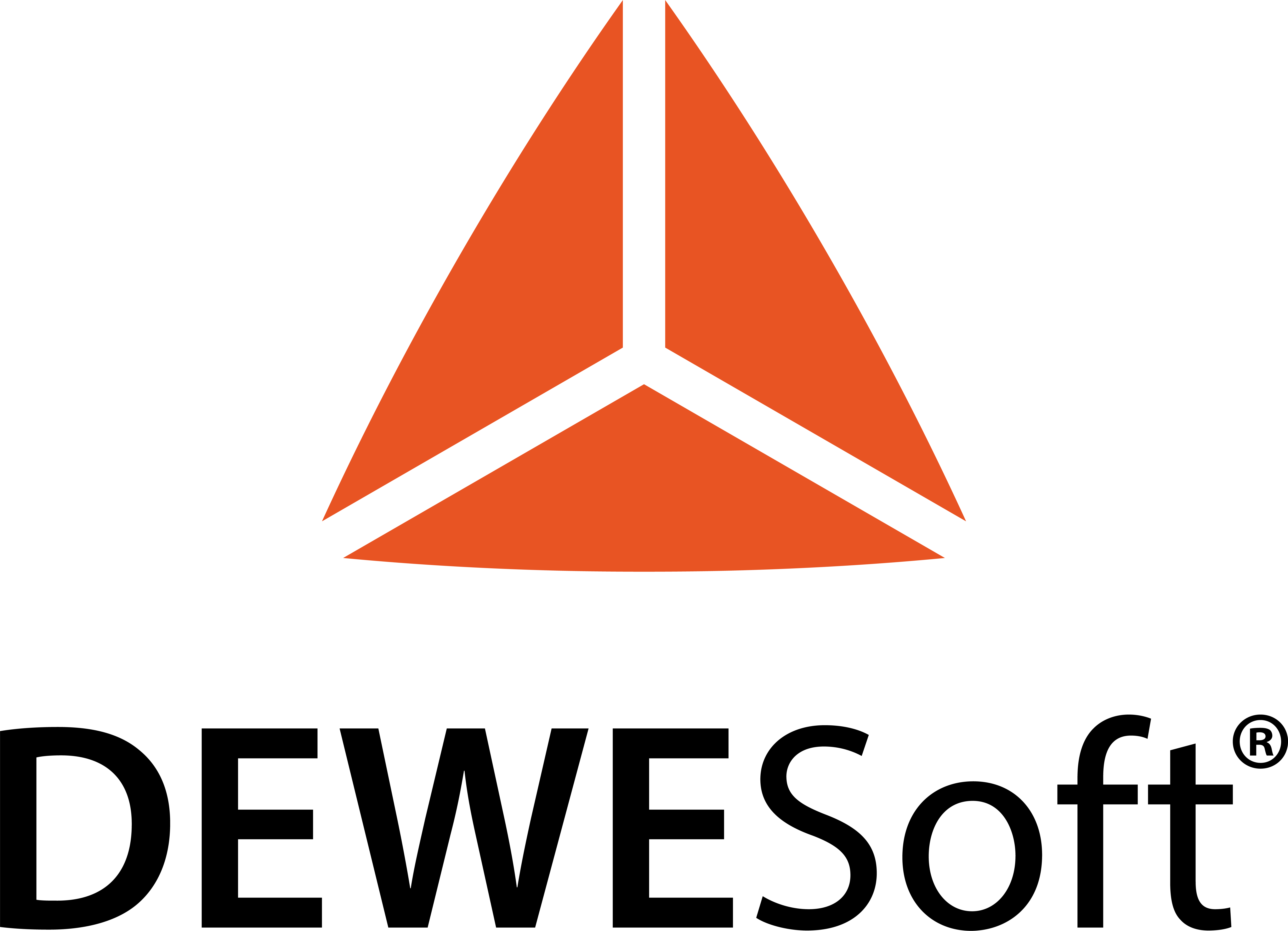
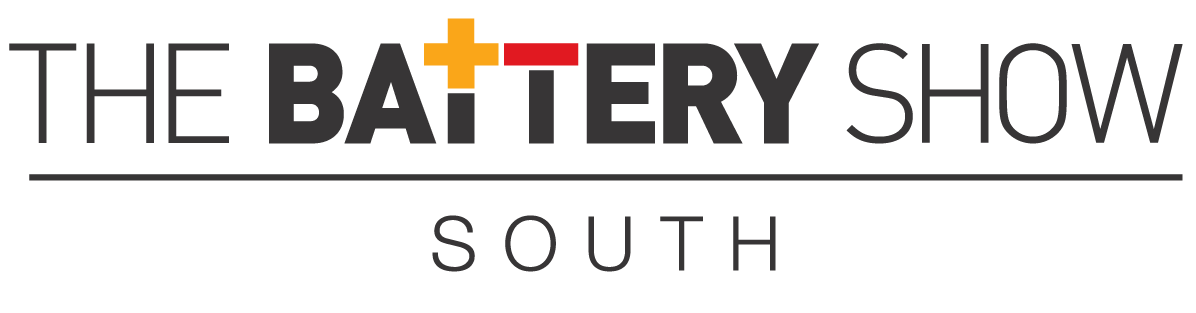
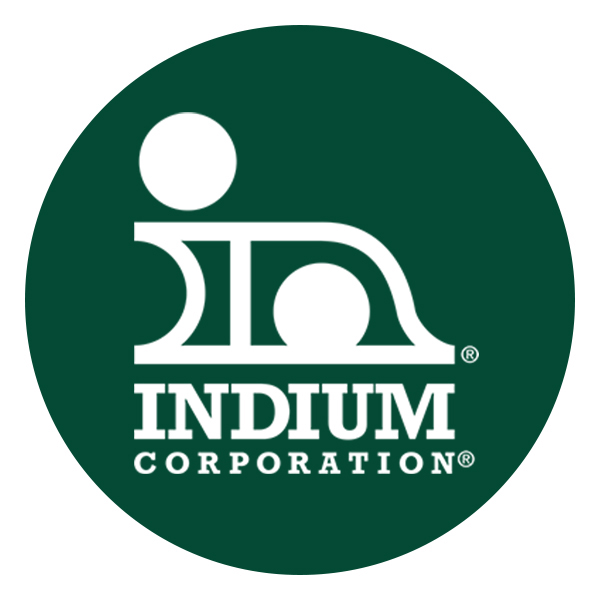
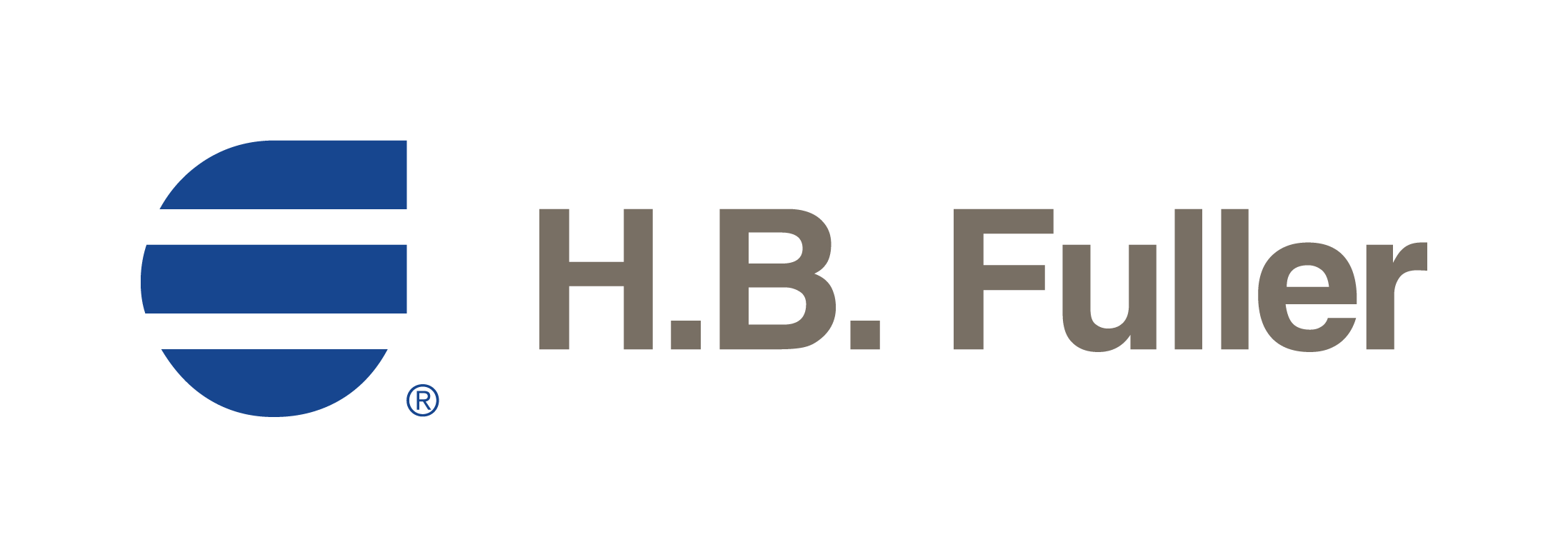