Kennemetal’s additively-manufactured boring tool
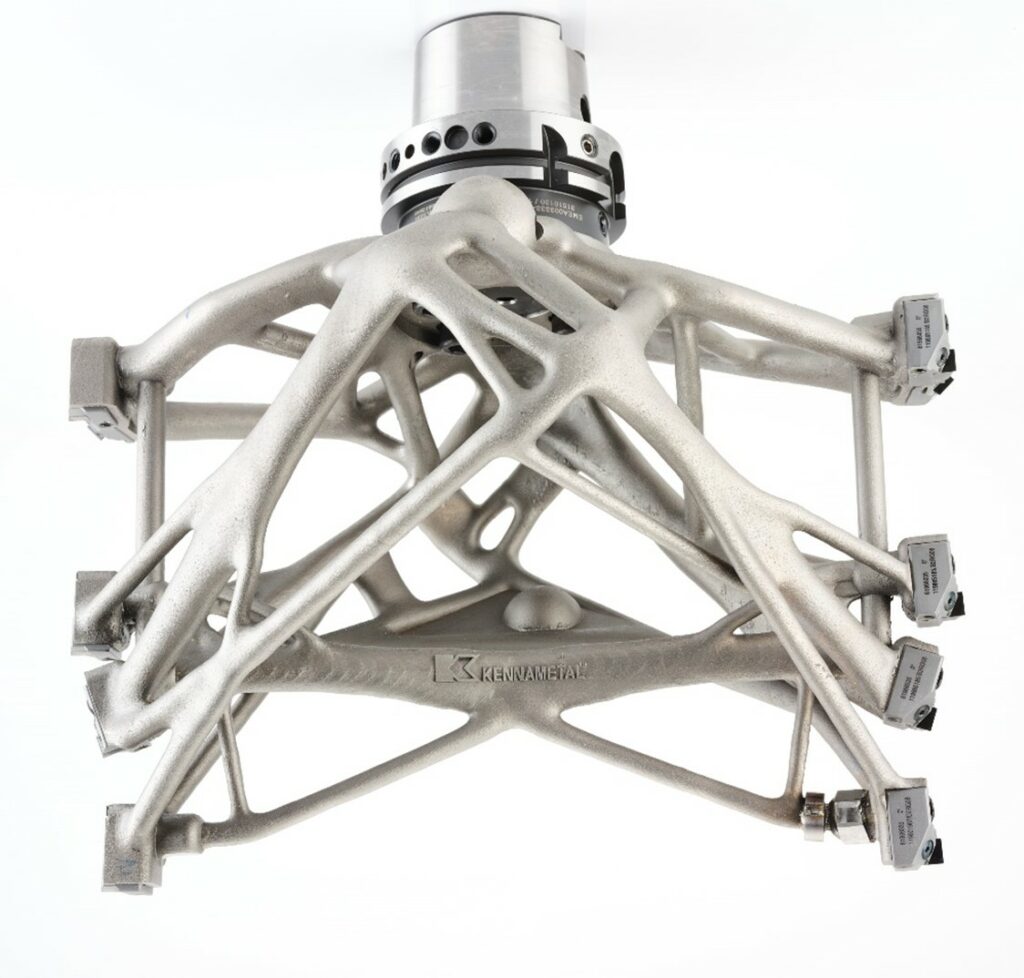
(Image courtesy of Kennemetal)
Kennametal has created a new machining tool leveraging its “KENionic” technology, which is aimed at tackling industry requirements on the precision production of motor and transmission housings. KENionic leverages additive manufacturing (AM) to design and make systems on average 50% lighter than conventional tooling, and capable of performing machining tasks in approximately 50% of the time that conventional tooling would take.
“KENionic technology is used in a customer application-specific insert tool holder, and is principally a large boring solution: it provides a high precision bore finishing required to form engine and transmission housings for transportation systems,” Dr. Carlonda Reilly, vice president and chief technology officer of Kennametal told EME.
“Depending on the user’s configuration it can be up to 60% lighter than standard boring tool designs, and that weight reduction also enables it to be more rapidly accelerated and decelerated. Additionally, the shape we’ve created using KENionic through AM integrates the functionality of multiple tools into one, providing easier and fewer tooling changes, making for either fewer interruptions to – or entirely uninterrupted – production cycles. A housing that might usually take three or more separate operations to complete can therefore be done with just one operation.”
A variety of advanced numerical modelling methods including FEM and simulation software tools were used to optimise the design of the tool for boring operations around target parameters for strength, stiffness, cutting force, and performance. Dr. Reilly notes here that the design resulting from modelling and simulation mimics organic shape adaptations found in nature, hence the solution’s name (being a portmanteau of Kennametal and “bionic”).
Having arrived at a design suited to these qualities, the company turned to AM to utilise KENionic technology and make its complex and unusual shape a reality. That shape can be scaled up and down – the primary constraint being the size of the additive printer needed – to meet the boring diameters and form factors of different customers’ housing units, including cases where existing boring tools for ICE powertrain housings (for instance in range extenders, parallel hybrids, or systems running on e-fuels).
“The system achieves its cutting power through our proprietary insert technology: the tool is designed with pockets formed for holding Kennametal’s proprietary inserts, for secure mounting and ease of replacement between operations giving high overall bore precision and productivity,” Dr. Reilly adds.
The tool-holder forming the bulk of mass and weight in KENionic technology is a steel construct and was additively manufactured via laser powder bed fusion. The inserts meanwhile can range from tungsten carbide to polycrystalline diamond and other materials suited to cutting metal, with a wide range of proprietary designs for those inserts depending on the nature of the job. Kennametal has the capability to additively manufacture carbides as well using metal binder jet capabilities for those materials.
“Going forward, we will continue to work directly with customers to understand their technical challenges, and leverage our resources in materials science, modelling, simulation, additive manufacturing, and our proprietary inserts and other technologies, including KENionic technology, to provide them with the optimal solutions for boring and related processes,” Dr. Reilly concludes.
Click here to read the latest issue of E-Mobility Engineering.
ONLINE PARTNERS
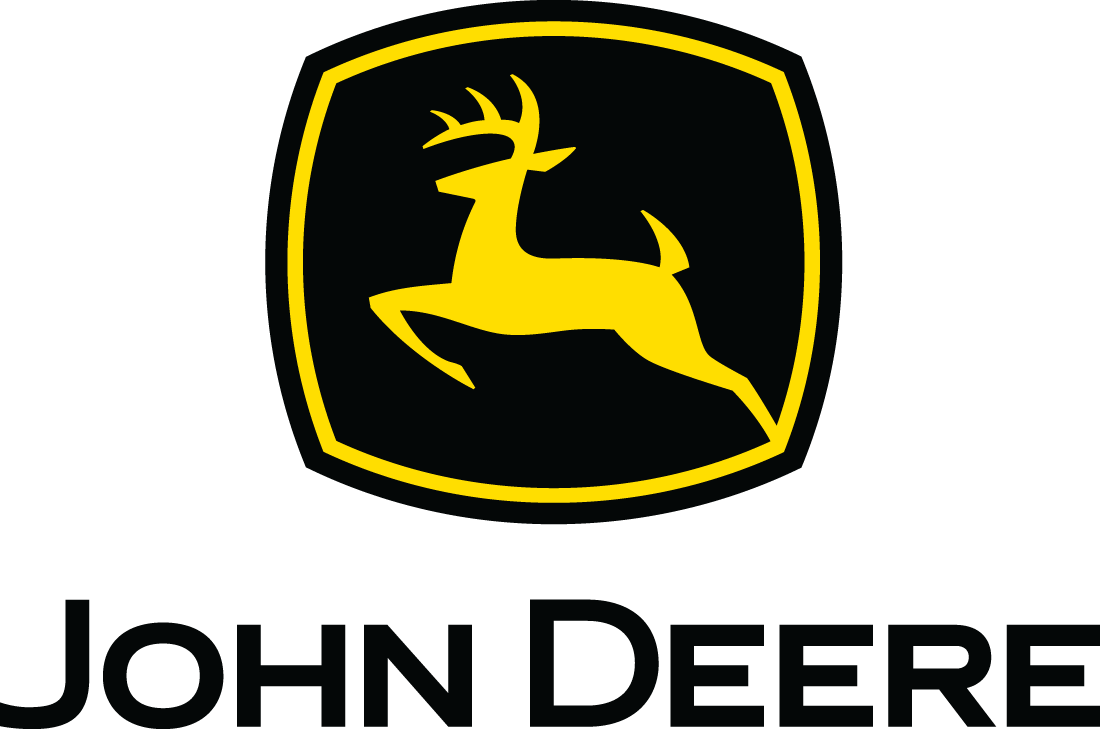
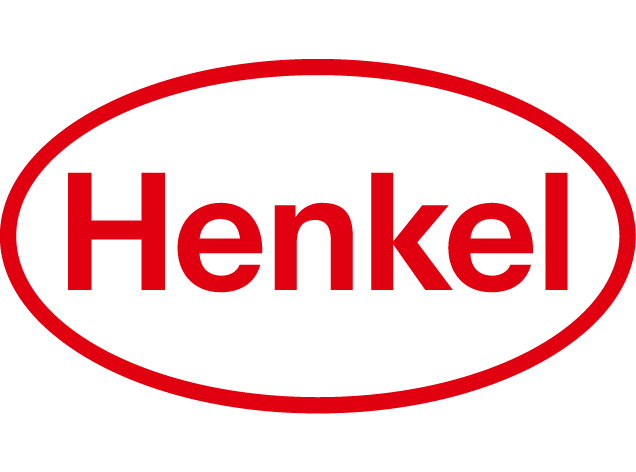
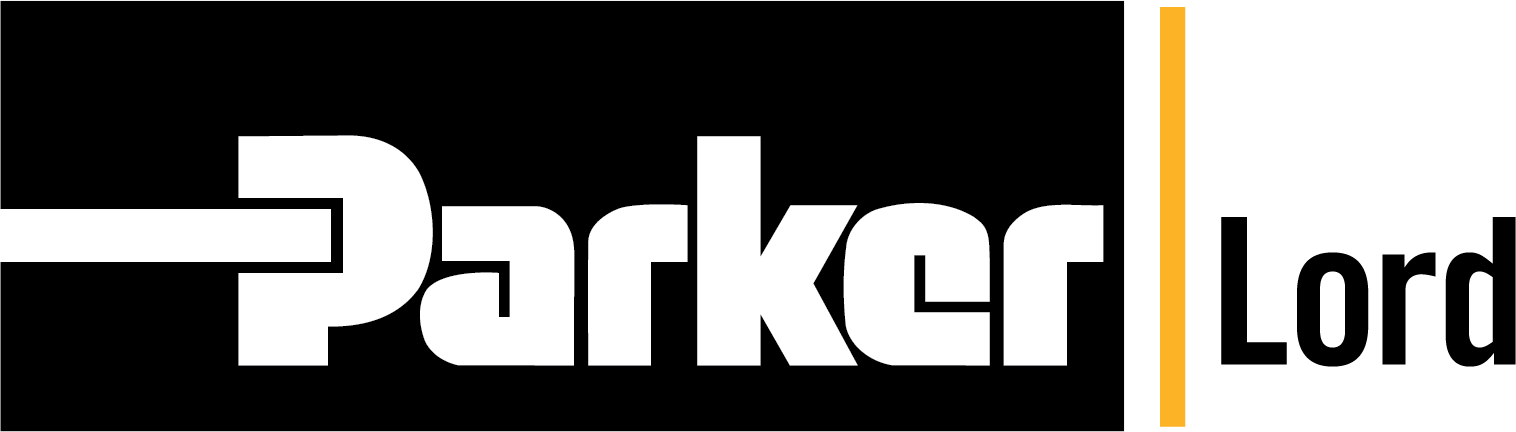
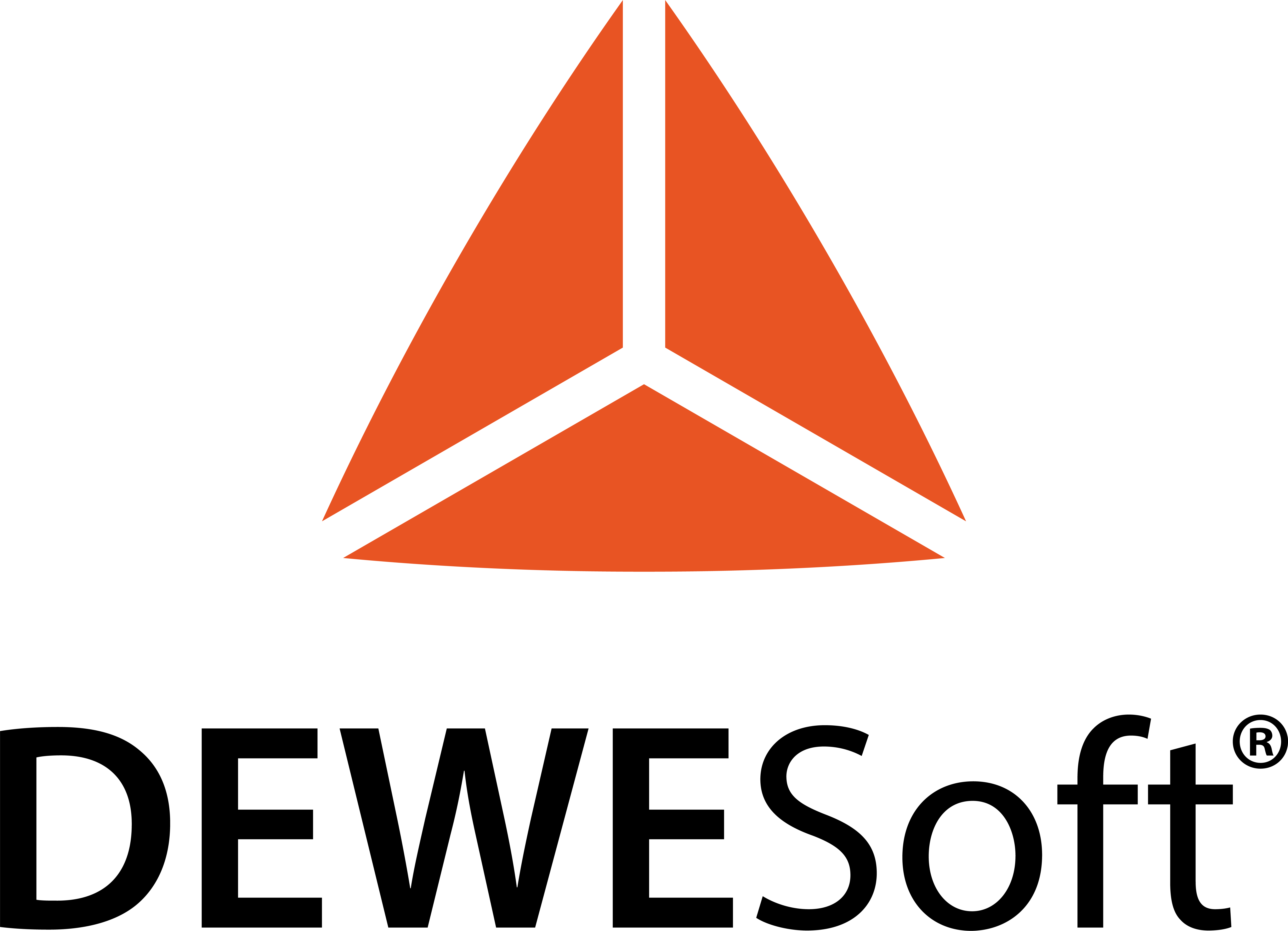
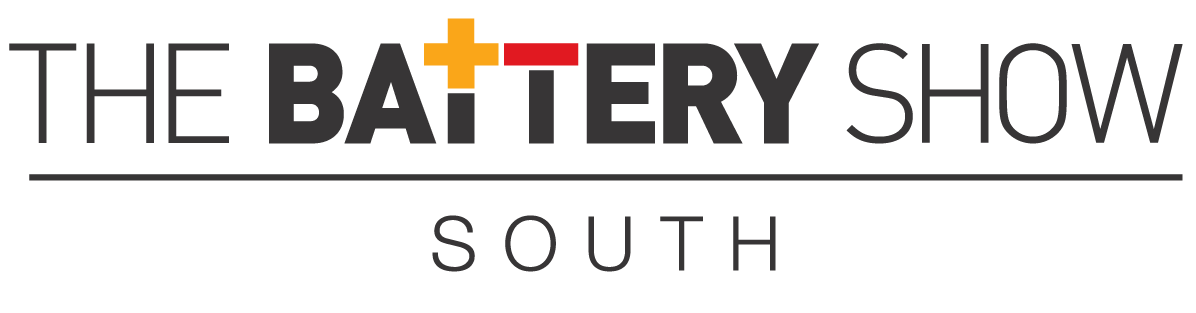
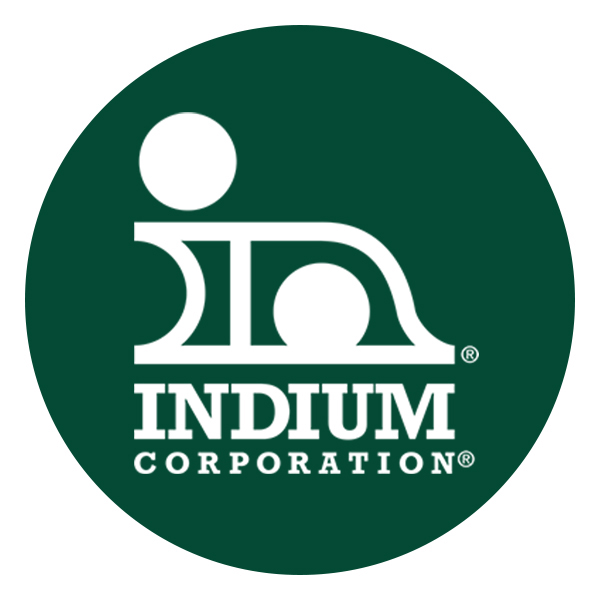
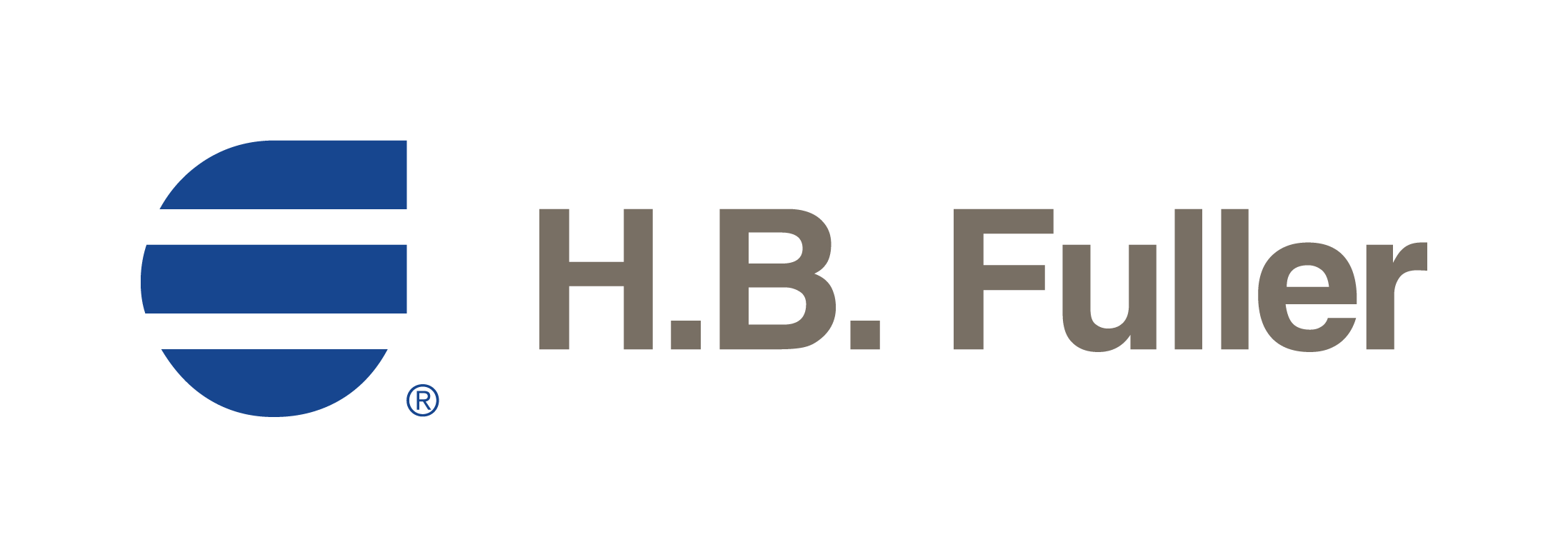