Supercapacitors
Nick Flaherty looks at the latest developments in supercapacitor technology for e-mobility systems.
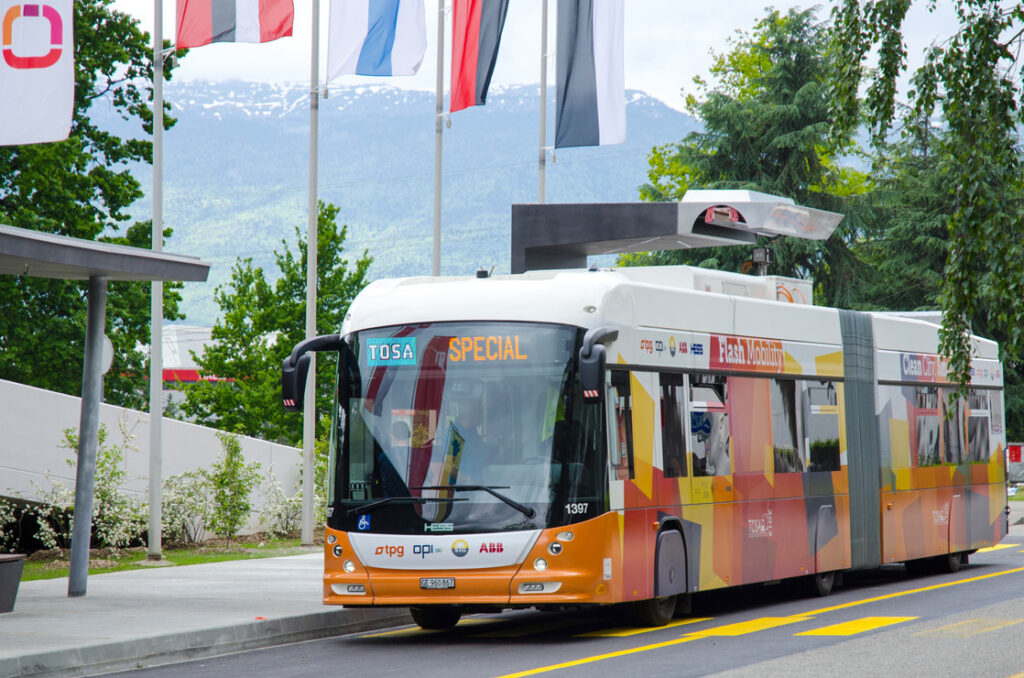
(Courtesy of ABB)
Putting the super into supercapacitors
Batteries are the go-to technology for powering electric vehicles of all kinds, but supercapacitors (also known as ultracapacitors) are increasing in capacity and performance to become a viable alternative in some applications.
Supercapacitor technology is already well-established in stop-start and mild hybrid architectures. Unlike batteries, which use an electrochemical process, supercapacitors are based around electrostatic techniques.
This provides fast charging and millions of discharge cycles that batteries cannot deliver. However, they cannot hold the charge for very long, so are an ideal companion to batteries in many e-mobility designs.
In stop-start and hybrid topologies, supercapacitors are used to provide power to the powertrain quickly and easily without putting a strain on the battery pack. With kinetic energy recovery systems, the energy recovered from the braking or suspension system can be captured and reused easily without having to access the battery pack. This also reduces losses, and over time improves the efficiency of the overall system and so extends the range.
The materials used for supercapacitors are also improving, with new approaches such as curved graphene or glass polymer mats, boosting the energy density. This is creating a class of device some like to call an supercapacitor, although the terms are interchangeable.
Carbon
The performance and properties of supercapacitors are determined to a great extent by the electrode material used. Swiss supplier SECH for example uses activated carbon powder. A patented process increases the pore size of the carbon and provides the largest possible accessible surface.
Also, the best possible match between the pore size and the ions used in the chosen electrolyte is selected, so that the electrode material has a high capacity and a low internal resistance with electrochemical stability.
The electrode material is processed on an automated production line with a separator in the capacitor winding which is built into a hermetically sealed housing and impregnated with an electrolyte. The capacitors are characterised by laser-welded internal connections to seal the cell, the use of pure aluminium for housings and electrical contacts as well as a patented housing design.
This provides a single-cell voltage of 3.0 V with integrated terminals for more compact modules and packs. The internal connections provide a low internal resistance and a path to remove the heat from the supercapacitor.
Graphene
Graphene, the 2D version of carbon, has been used to boost the energy capacity of supercapacitors.
“Current supercapacitors have an energy density of 7 Wh/kg, as opposed to our curved graphene supercapacitors that offer around 20 Wh/kg,” says Taavi Madiberk, CEO of supercapacitor maker Skeleton Technologies, in Estonia. “We have a roadmap to 60 Wh/kg while retaining charging times measured in seconds and a cost point lower than high-power batteries.”
Reaching that 60 Wh/kg is key for the wider adoption of supercapacitors in e-mobility systems.
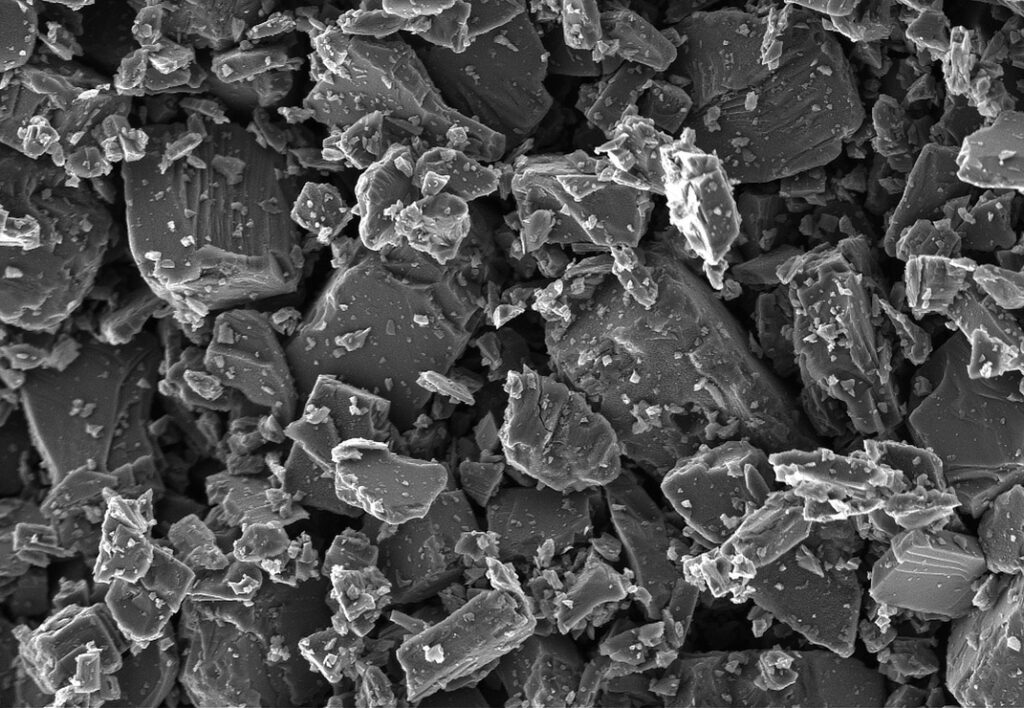
(Courtesy of Skeleton Technologies)
“Right now, with the current generation that we produce and on the market, you can service niche applications such as active suspension or hybrids,” says Sebastian Pohlmann, head of cell development at Skeleton.
“In order to get to the next step, the energy density has to double at least. That doubling then services 48 V hybrids and the high-power peaks that would otherwise damage or degrade the batteries,” he says.
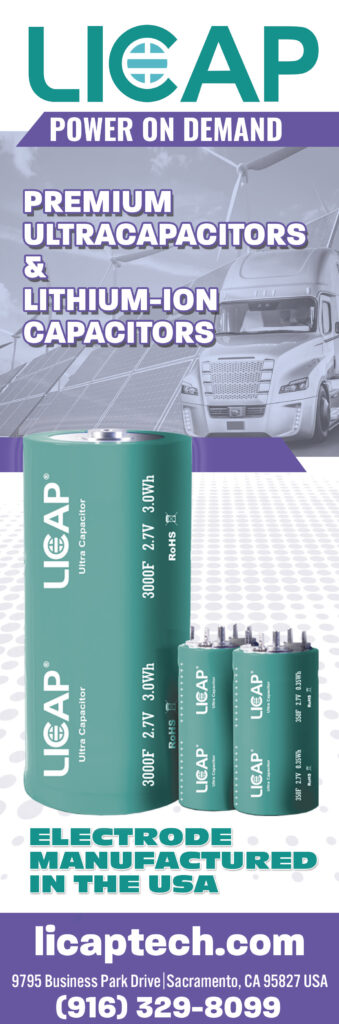
Over the past decade the focus has been on increasing the voltage and cell capacity, and progress has been made at the cell construction level rather than in the materials, increasing the amount of active material in the cell. The move to new materials is key, giving a 60% increase in energy density just by changing the material.
“If you increase the voltage you also increase the energy density by a factor of squared, so we plan to move from 2.85 V to 3.4 V; we have prototypes with that voltage, so we know it can be done. Combining that with the electrode material gives us the next generation,” he says.
“The magic threshold for cell voltage in a 48 V system is 3.2 V. It means a battery pack can consist of 15 rather than 17 cells, reducing weight and cost.”
“We know from the basic electrochemistry that it should be possible. In theory you can go higher, but 3.4 V has proven to be a realistic target.
“You can charge a cell to a higher voltage, but the lifetime will decrease quickly – 10 times faster – as the electrolyte is unstable at these voltages, so it decomposes, creating gas and clogging the surface area of the electrode. That leaves less of the energy storage material accessible, so the key point is to find an electrolyte that withstands the voltage without degrading,” he says.
The electrolyte for a supercapacitor is also very different from the electrolyte in a battery. The former has essentially two components, while for batteries the electrolyte has evolved with up to seven different ones.
“We have learned the lessons from the lithium-ion battery industry, and engineered an electrolyte that deals with all the degradation mechanisms,” says Pohlmann.
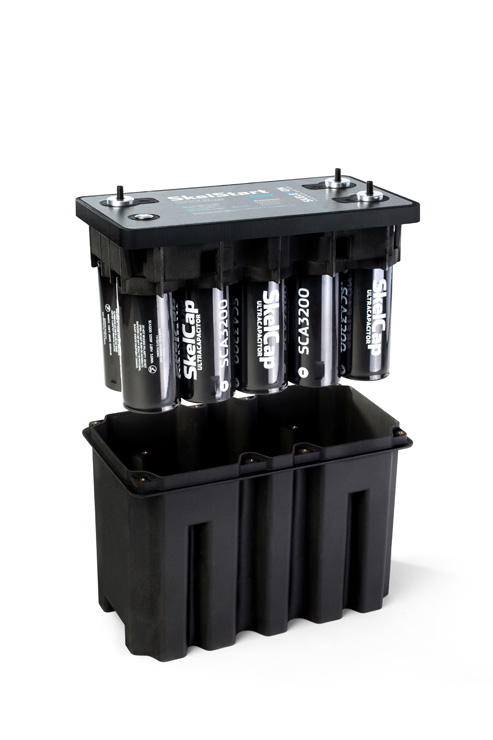
(Courtesy of Skeleton Technologies)
A key point is to have control over the formulation of the electrolyte to balance the performance of the electrode materials. “As we are not relying on someone else selling their electrode active material we can tailor the material to fit with an electrolyte that works well – that’s a unique approach,” he says.
“We are already working with Tier 1 suppliers and OEMs with the present generation of devices. There are a lot of lessons to be learned from these devices to build the knowledge base for the industry, and there’s a lot of trust that needs to be built up through testing,” he says. “We are working at the prototype phase for them to give their feedback, eliminating the weaknesses they saw before.”
Skeleton is now shipping cell-level prototypes to selected automotive companies and Tier 1 suppliers, and in 2020 plans to do the same with modules and welded packs. Beyond 2020, the company aims to provide production samples of the technology ahead of the launch in 2021, alongside the ability to test it in a production line.
This staggered development is determined partly by the application, as that determines the pack size. A 48 V hybrid powertrain for example uses a larger cell size than a pure electric vehicle.
Another driver for the staggered release is cost reduction. The cost of the supercapacitors is currently $45005000/kWh, but the new cells will bring that down to less than $1000/kWh.
Dry electrode
An alternative material technology for supercapacitors is the dry electrode – that is, one that does not use a wet electrolyte. This is a well-known process, patented by Maxwell Technologies, which is now part of electric car maker Tesla, and avoids toxic solvents.
However, these supercapacitors can have problems with quality, particularly with the thicknesses of coatings. As the supercapacitor is electrostatic, small differences in thickness of the coatings can make a big difference in energy capacity and reliability.
The potential for dry-electrode technology is significant though. The Tesla Model 3 currently has an energy density (at cell level) of 210 Wh/kg, and 275 Wh/litre at the battery pack level. A dry electrode supercapacitor can store 300 Wh/kg, with the potential for more than 500 Wh/kg. That would boost the car’s present range of 220 miles to around 375 miles.
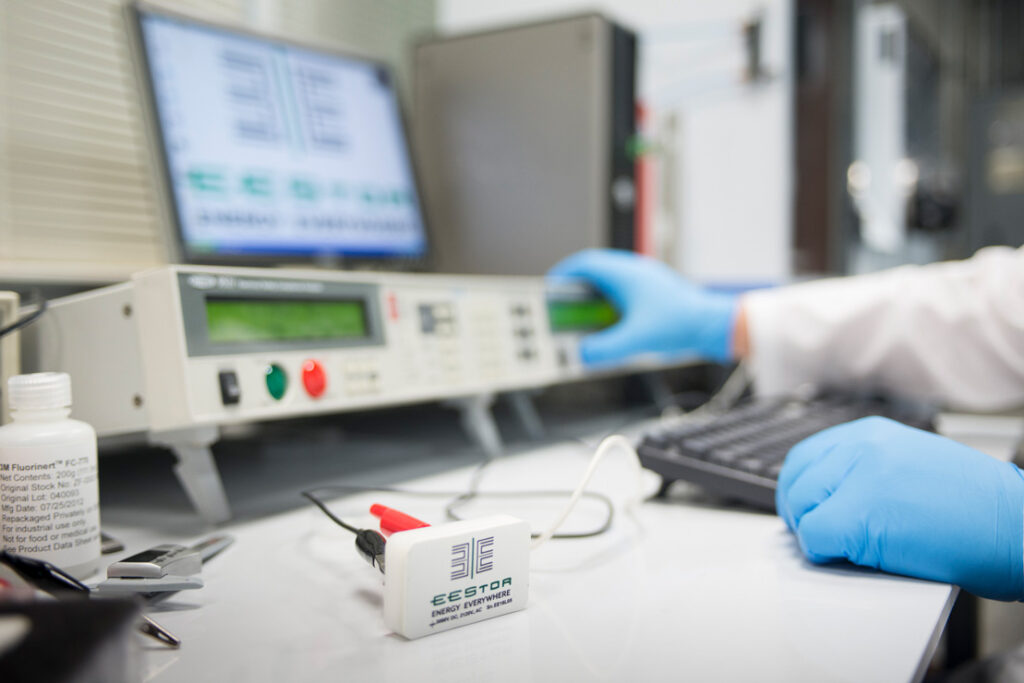
(Courtesy of EEStor)
The technology will be used in North America and Europe in five mild hybrid and plug-in hybrid vehicles from Geely, the owner of Volvo and Lotus. Production for these vehicles is set to begin later this year.
Ceramic supercapacitors
Another material technology being developed for supercapacitors actually comes from the electric car industry. Ceramic technology developed by EEStor, in Canada, is based on a composition-modified barium titanate (CMBT) material that can handle higher voltages.
In 2006, EEStor was working with an electric car maker called Zenn Motors on a pilot programme of production. “Zenn [Zero emission, no noise] sold around 1000 vehicles in the US, and it has been proven that the reason we don’t all drive electric cars is because the batteries suck, so we had to choose between developing low-speed electric vehicles or energy storage, which we did in 2012 and collapsed the companies into each other to focus on the electric vehicle technology,” says Ian Clifford, CEO of EEStor.
Clifford recognised early on that testing is essential for the credibility of the material. “Early on we started working with Intertek, who have a lot of experience with capacitor-type devices, and we are now completing testing on our ninth-generation material with them, expanding it to include two other organisations that specialise in highvoltage capacitors to make sure we have a credible, repeatable process for the test data,” he says.
“CMBT mixed with glass can maintain a higher dielectric constant at voltage than other dielectrics. A lead-free relaxer with low residual polarisation – which is unique and means you get more energy out during discharge,” says Bryan Kelly, vice–president of production at EEStor.
Adding the glass changes the capacitor’s thermal response, allows a higher voltage and lowers the sintering temperature, so instead of using precious metals for the electrodes, supercapacitor makers can use base metals.
Doubling the relative permittivity from the eighth-generation samples to the ninth generation today cuts the size and cost of a supercapacitor in half, without increasing the current leakage. It also holds charge for longer than the previous material, up from 848 s to 1265 s, or 20 minutes.
This opens up new applications, such as supercapacitors in an electric bus to replace batteries. As a bus would stop every 10-15 minutes, it could be quickly recharged at each stop.
But there is still a lot of testing to do. Slight differences in the types of glass, their content, coatings and/or other additions to it can result in drastic changes to the thermal coefficient of capacitance (TCC) and to the DC bias voltage saturation characteristics of CMBT-glass hybrid dielectrics.
The TCC and DC bias voltage saturation are measurements of how the performance of the dielectric varies with temperature and high voltages. The lowest possible variation in performance with temperature is essential for automotive applications.
A last key development of the material is that the thermal performance has also improved. Samples experience less than 15% variation in performance over a temperature range of -30 to +150 C, up from -30 to +85 C in the previous generation.
The next challenge is to produce the packs. These will vary from simple stopstart packs to full electric power packs.
Skeleton has developed hybrid supercapacitor battery packs that can extend the battery life by 50-100%, and extend the range by 20-40%, by taking energy back from the braking system. This also allows the battery element of the pack to be smaller.
Buses
Supercapacitors have been used in buses, allowing times of 10-15 s to fully recharge the bus during a stop. But that needs to be combined with a highvoltage DC charging system.
Automation company ABB has developed a high-capacity flashcharging electric bus system. A 135-seater bus called TOSA (Trolleybus Optimisation Systeme Alimentation) is charged directly at selected stops with a 15 s energy boost while passengers enter or leave the bus.
“Through flash-charging, we are able to pilot a new generation of electric buses for urban mass transport that no longer relies on overhead lines,” says Claes Rytoft, an independent consultant. “This project will pave the way for switching to more flexible, cost-effective public transport infrastructure while reducing pollution and noise.”
The 400 kW charging system uses a laser-controlled moving arm that connects to an overhead receptacle for charging at bus shelters, instead of the usual trolley poles to overhead lines. At the end of the bus route a 3-4 minute boost enables a full recharge of the supercapacitors.
While several different supercapacitorpowered buses have been shown as prototypes, none have yet seen largescale adoption. This is largely down to the need for an extensive charging infrastructure.
“I don’t think it’s fully viable with the cost of the charging stations and the currents that have to flow – it’s a big market for supercapacitors along with batteries for a fully electric bus,” says Pohlmann at Skeleton.
Skeleton is working with Wrightbus in the UK to add supercapacitors to a diesel hybrid double-decker bus. It is supplying the supercapacitors for energy recovery, which gives a 36% fuel saving compared to a UK-based EuroVI diesel bus, and also adds at least another three passengers to the carrying capacity compared to a lithium battery-based hybrid equivalent.
While lithium battery systems might last around 4-5 years, the 1 million cycles of the supercapacitors will provide an estimated lifetime of 1215 years. “Supercapacitors provide a major fuel saving, and their long lifetime will reduce maintenance,” says Mark Nodder, CEO of Wrights Group, which owns Wrightbus.
Stop start
The early use for the technology has been in start-stop systems. Supercapacitor supplier Ioxus for example has developed a 24 V battery support system for heavy equipment. It is a drop-in replacement for a lead-acid battery, with one 24 V uStart supercapacitor in parallel with 31 batteries in series.
It supports engine capacities of up to 50 litres in off-road equipment to provide the vehicle with a start, no matter the condition of the existing batteries or external temperature. It also continuously monitors the voltage to inject power when needed to maintain a smooth system voltage.
A smartphone Bluetooth app allows users to look at the voltage of the batteries, the charge level of the uStart, to initiate a jump-start without connecting any wires, or put the unit into maintenance mode for safe removal or repair.
If the batteries run too low owing to loads from accessories, or are too old, the uStart collects energy from the batteries, concentrating it to get the vehicle’s bus voltage up to 24 V, then provides the power to crank the engine and start. This eliminates jump-starts in remote locations, which can be costly, so saving thousands of dollars over the life of the vehicle.
Taking to the air

(Courtesy of Flying Whales)
Supercapacitors are also at the heart of the development of a hybrid airship. The LCA60T from French firm Flying Whales will be able to carry a cargo of up to 60 tonnes such as timber in its 75 m-long hold or underslung, at speeds of 100 kph, with a range of several thousand kilometres per day.
Engineers from Skeleton are helping to develop the 1.5 MW propulsion system for the helium-filled, rigidstructure airship, using supercapacitors to provide an extra 2 MW for hovering, lifting and stabilisation.
“The airship programme is focused initially on addressing the specific industrial requirements for the timber industry in France, but it also has the potential to connect landlocked regions across the world to the global economy,” says Madiberk at Skeleton.
ONLINE PARTNERS
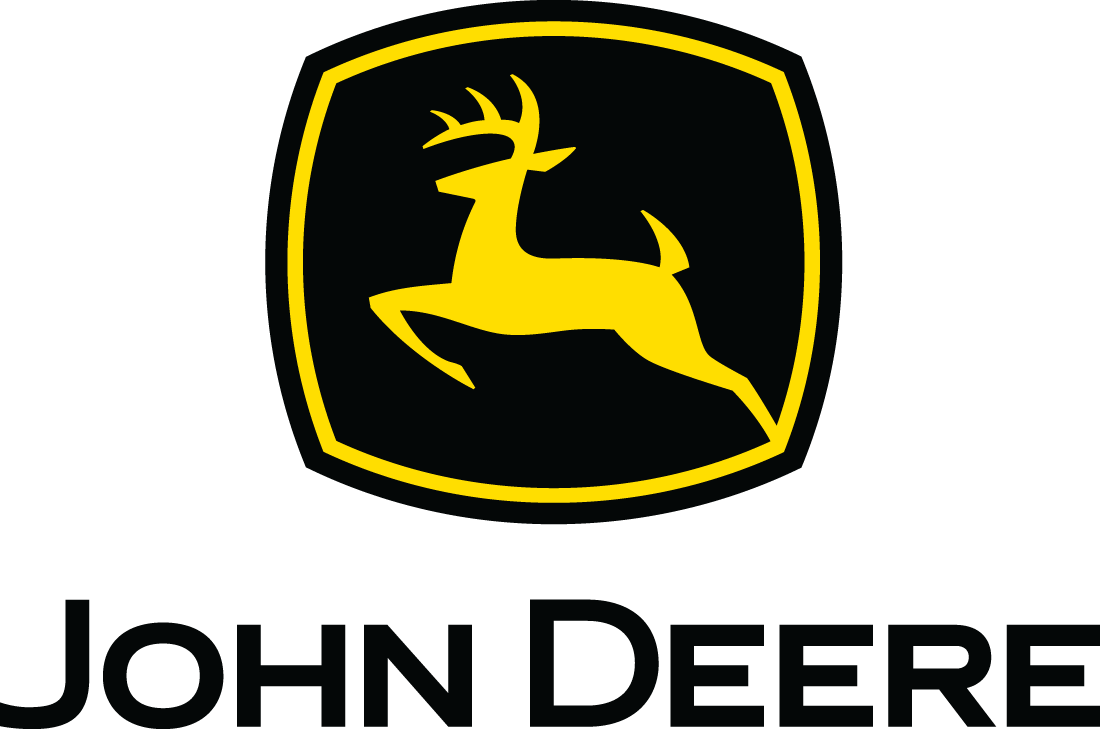
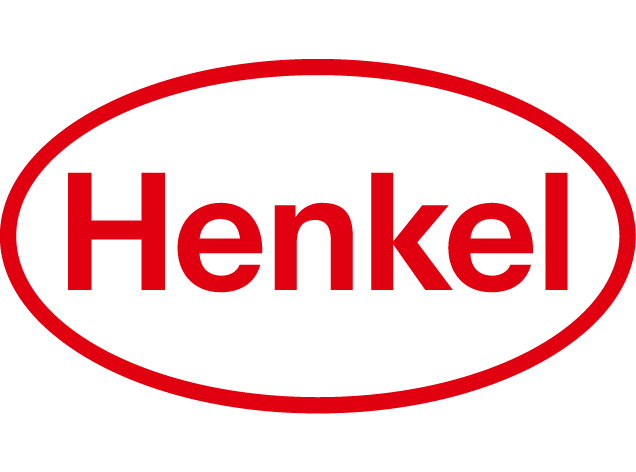
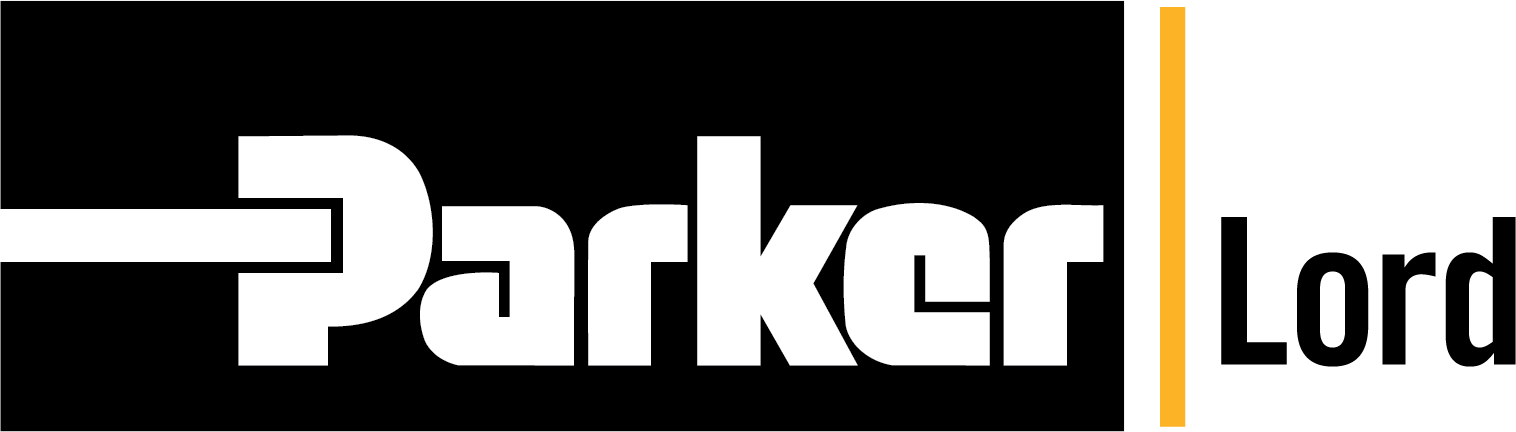
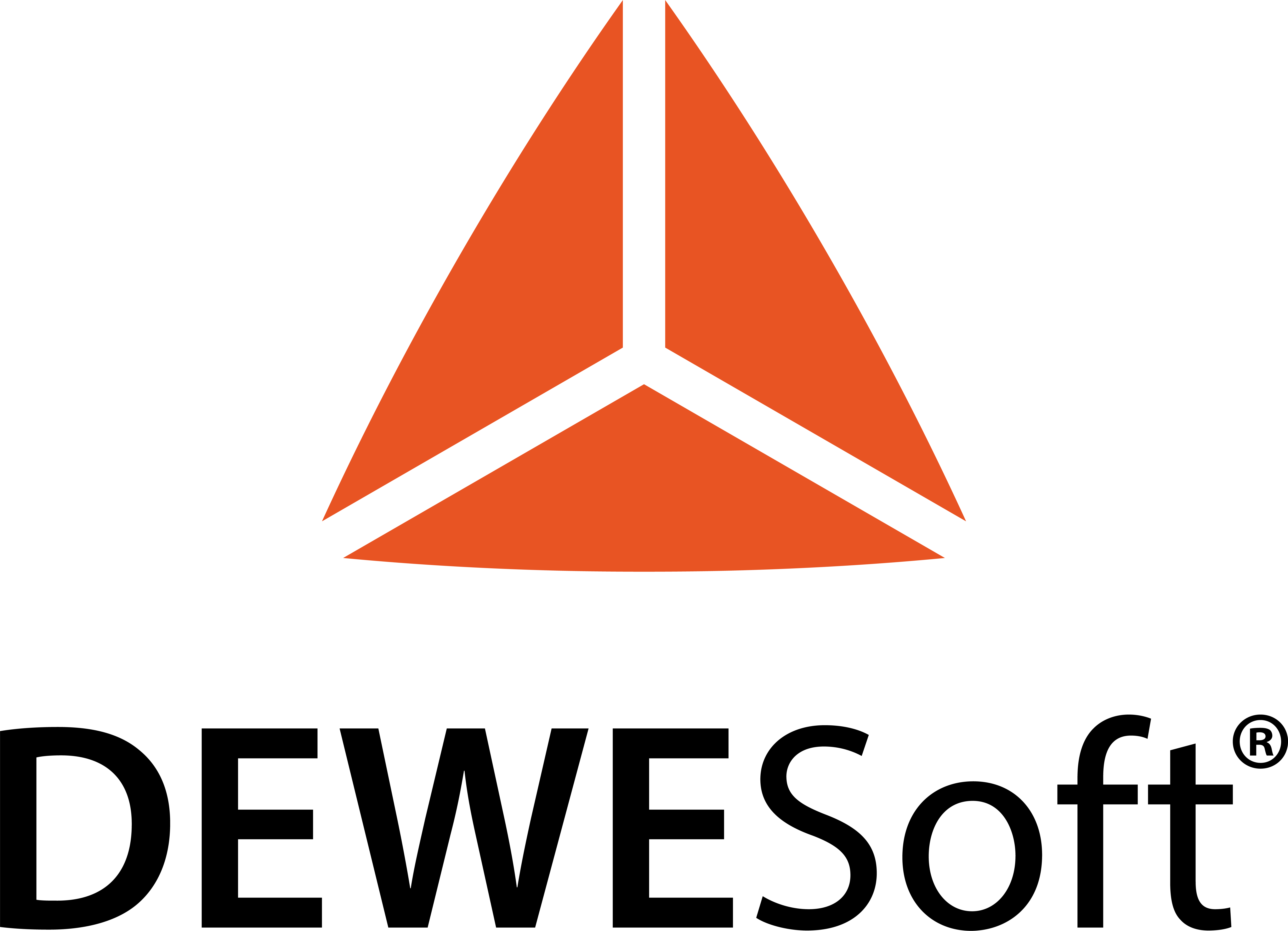
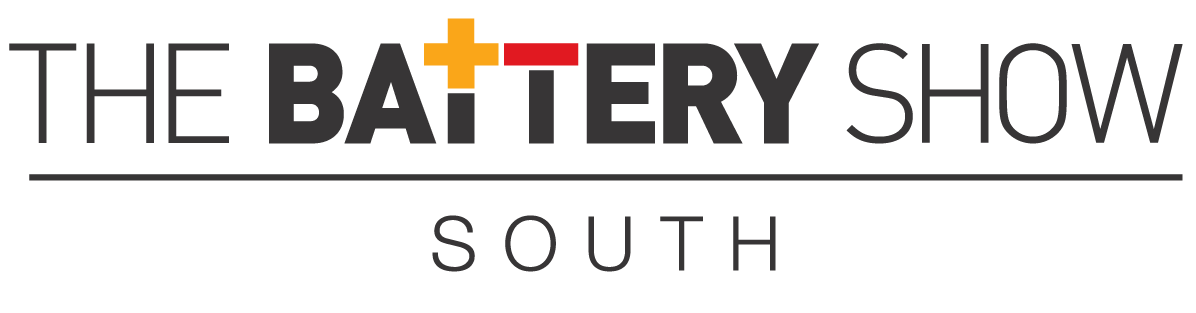
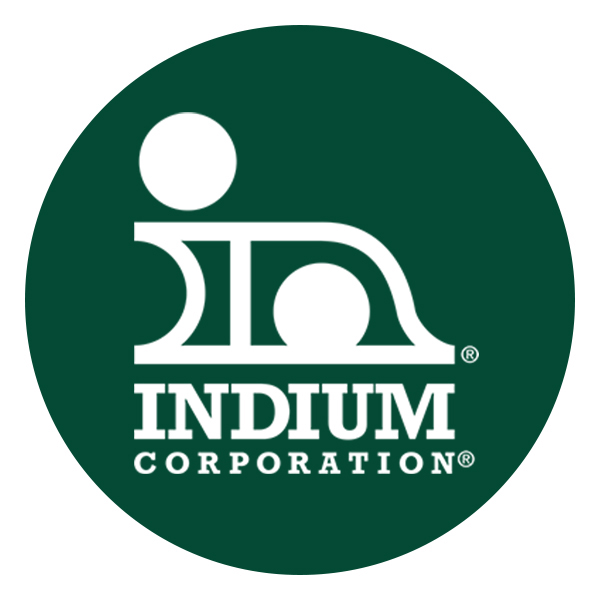
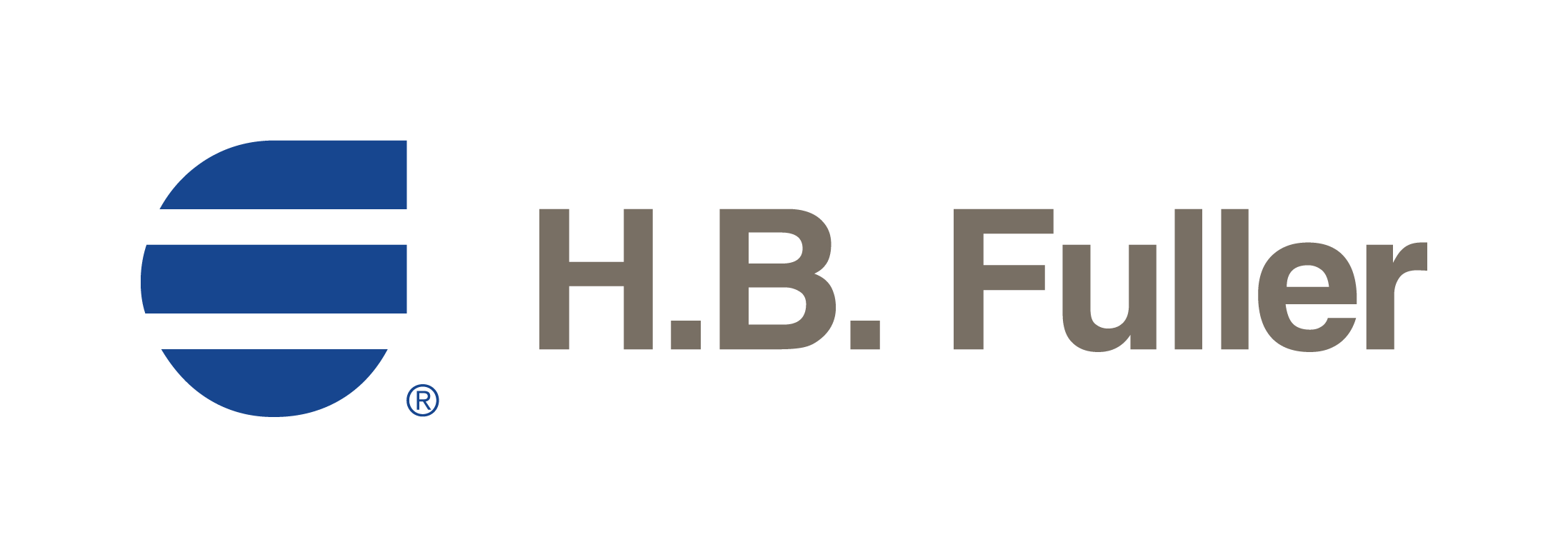