InoBat Auto
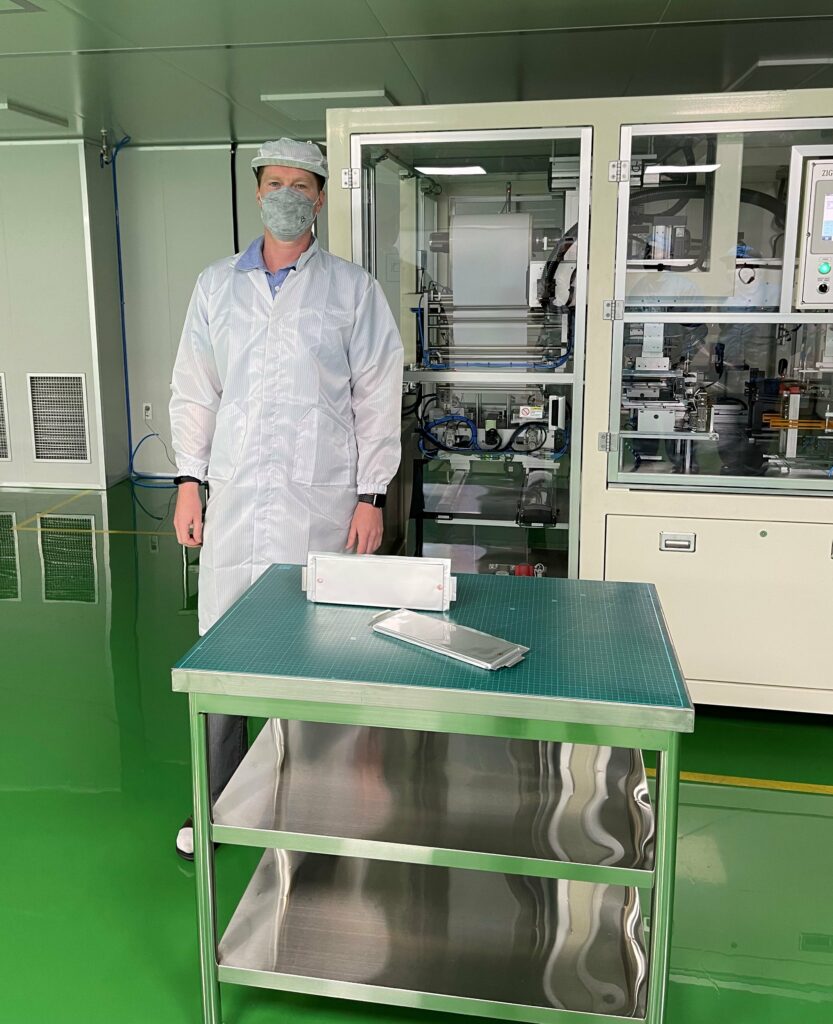
(Photos courtesy of Inobat Auto)
Quick to market
Peter Donaldson reports on how this company aims to slash the time needed to introduce new batteries to the EVs industry
Rapid development of innovative new cell technologies and a focus on tailoring chemistries to maximise the effectiveness of individual applications are at the heart of InoBat Auto’s approach to EV battery development.
Now delivering its first lithium-ion cells based on NMC cathode chemistries in NMC 622 and 811 formulations, the start-up company plans to offer cells for a very broad range of EV requirements in terms of performance and cost. Cells are already being supplied by a contract manufacturer in Asia, while the first of two new plants for in-house development and production is under construction near the Slovakian capital Bratislava.
The company was founded to address the issue of the available cells not being optimised for specific applications, says its CTO Doug MacAndrew, and development was slow. “The founders created relationships with a number of development partners. The aim was to change the way battery chemistry is optimised and to shorten the timeline to product introduction from the horrendous 10-year gestation period typical of incumbent manufacturers to something closer to 12 to 18 months.”
He argues that this drawn-out cell development cycle is a consequence of the industry not having been pressured into change, combined with an evolutionary approach that is also characterised by research and development divided into silos. “Businesses might have 2000 or 3000 scientists narrowly focused on different types of development opportunities, and bringing these together when faced with those silos is quite a challenge,” he says.
“We cut across those silos, and don’t try to pick winners among materials before we start the development process. We bring many different material inputs into the optimisation process, and compare all to all, not one to all or one to a few.”
He emphasises that this approach has proved effective in the pharmaceuticals industry, where it has long been used in the drug discovery process. “In methodological terms, there’s nothing stopping you doing electrochemical optimisation in the same way,” he says. “You just change the drivers and the way in which the data is reviewed, but ultimately it is the same mechanism.”
Automated analysis
“We can do it more quickly because we can automate our analysis and experimentation, and we can keep open the options presented by different materials during the evaluation and assessment phases,” he adds.
“One cycle of assessment produces many results – not just one – so we get design-for-power, design-for-energy and design-for-life outputs from a single cycle. We have carried out almost three cycles already and built up a knowledge database associated with the results. That gives us a great insight into what is possible across many different materials providers, for example in characterising loading factors and design conditions within the cell.
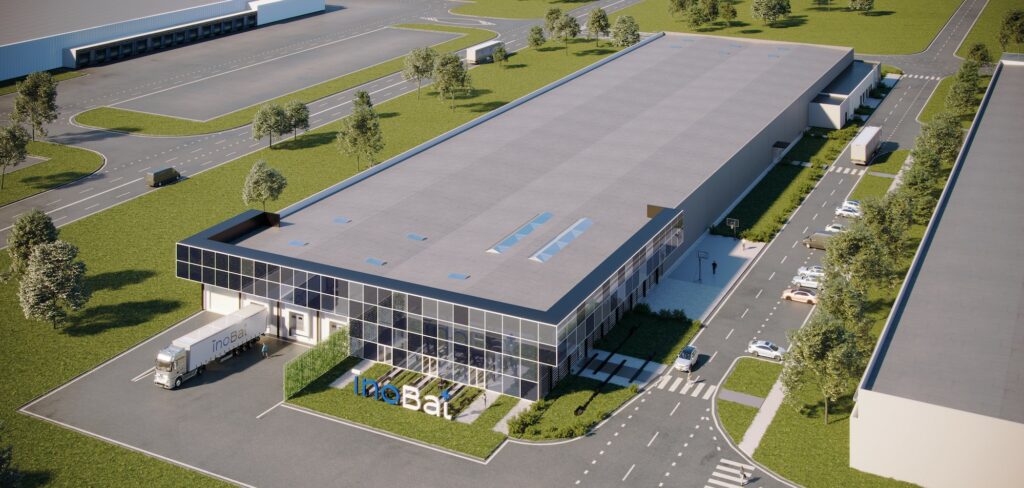
“We have an in-house team of scientists who drive evaluation and experimentation, and also provide guidance to the automated processes.
“Looking back at why InoBat Auto was started, one of the frustrations I’ve seen over the past 5 years is that battery pack designers and vehicle designers who are not aligned to one of the big cell suppliers are very much at the mercy of what is on the market,” adds the company’s COO Iain Wight.
He emphasises that there are many developers of high-performance vehicles, buses, trucks, aircraft other types of vehicle that are heavily underserved in this respect.
“From my own experience, you can select a cell and design a battery to go into a vehicle, but you have no real control over that core component. So, once you have designed, validated and tested the battery you are probably 18 months or 2 years into the process, and you can suddenly find that your chosen cell is no longer in production, sending you back to the beginning,” he says.
“Using the tools Doug mentioned, we aim to provide a long-term solution to some of those underserved markets and companies who want a level of continuity.
“As methodology and batteries improve over time, we can maintain the same form factor while bringing in chemical improvements, increasing power, energy capacity and longevity throughout the vehicle’s production and service life,” he says.
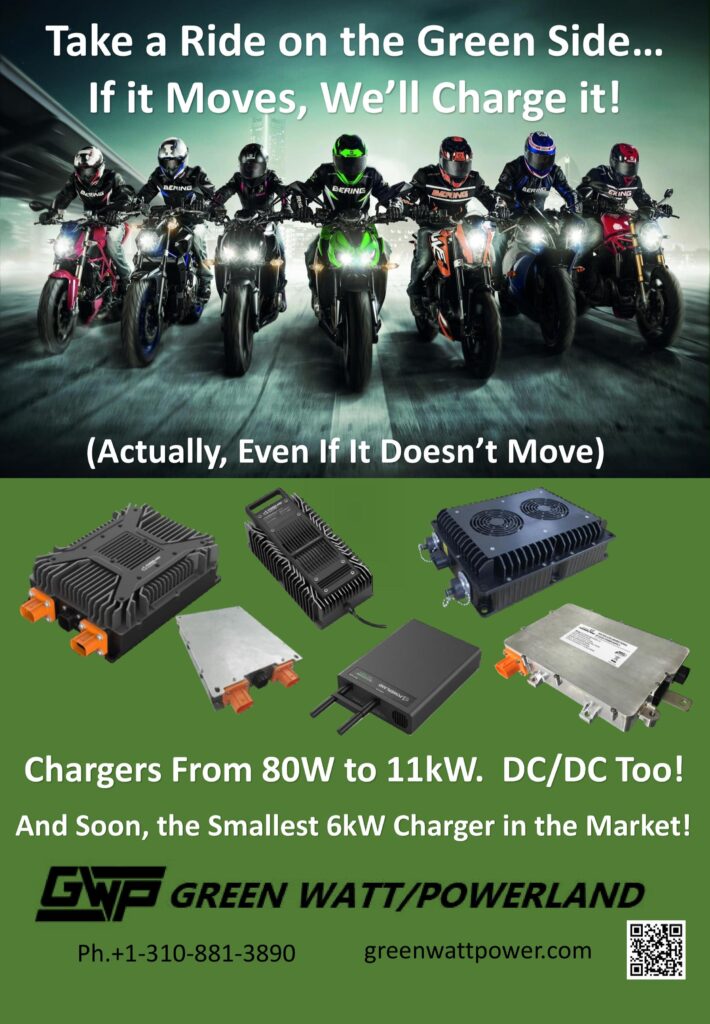
“From day one the take-it-or-leave-it approach has compromised many vehicle designs, to the point where they become uncompetitive and are not taken up,” MacAndrew adds. “We want to provide the opportunity for our customers to define and manage their brands at an electrochemical level.
“We see that the battery will be the differentiator of the future. Clearly, electrical machines will be scaled appropriately, but the battery and the way it operates could, for example, be the enabler for performance versions in vehicle ranges. The battery is going to be that differentiator.”
Wight concurs, adding that such differentiation will be a big challenge with EVs. “Everybody knows how to tune an IC engine: basically you put more air through it by whatever means you can,” he says. “It’s very different with battery EVs though, because they are not as flexible unless you start off with a higher spec battery and then derate it throughout the range, but that is very wasteful.”
InoBat Auto has identified four market segments it considers underserved as routes to market for its cells, and offers customised chemistries in a range of form factors. Those segments are premium and performance automotive, aviation, commercial vehicles and off-highway machinery.
While that might seem ambitiously broad at this stage, Wight argues that there are commonalities among these segments that enable them to be addressed initially by two types of chemistry.
Automotive and aerospace
“If you look at aerospace requirements, especially for VTOL aircraft, they need very high power on take-off and landing,” Wight says. “But landing is more critical for the battery because at that point you have a very low state of charge but still need maximum power.
“That’s not so different from the needs of a performance car. If the battery is derated when its charge gets low so that full power is not available, the driver will be pretty disappointed.”
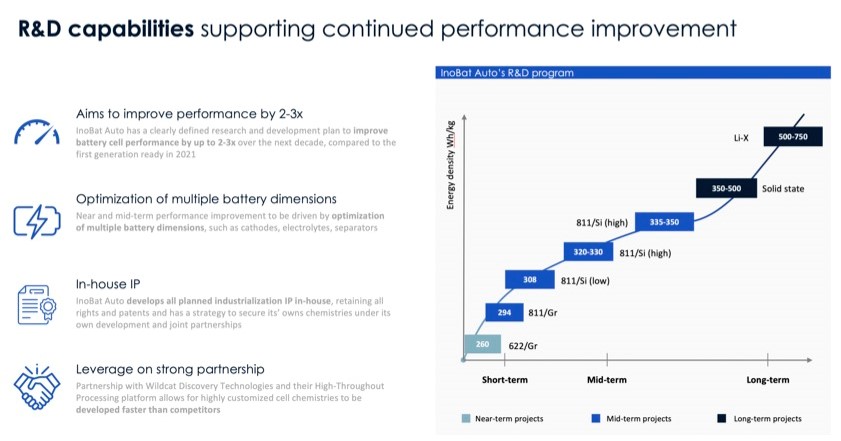
Wight argues that high-performance automotive, motorsport and aviation have several other similarities in what they need and can tolerate from their cells. While high power and “reasonable” energy density are a must, he says, moderate service life compared with commercial vehicle batteries is tolerable, and the prices that the vehicles command allow them to live with relatively expensive cells.
In contrast, commercial vehicles tend to have set duty cycles, and need good energy density for range coupled with long service lives, and they are more cost-sensitive, he says. They therefore need chemistries that are different from those that are best suited to the high-performance automotive and aviation sectors.
“Between those two extremes you can cover quite a number of underserved segments of the market,” Wight says.
MacAndrew adds, “For commercial vehicles, we anticipate applying a chemistry that offers extended service life, but that characteristic conflicts with chemistries optimised to deliver high power. So there are chemistries and form factors we believe will suit each of those.”
The industry is coming out of a period in which vehicle designers took whatever cells they could get in volume, MacAndrew says, reporting that different segments are reconsidering their integration approaches and their expectations of cells.
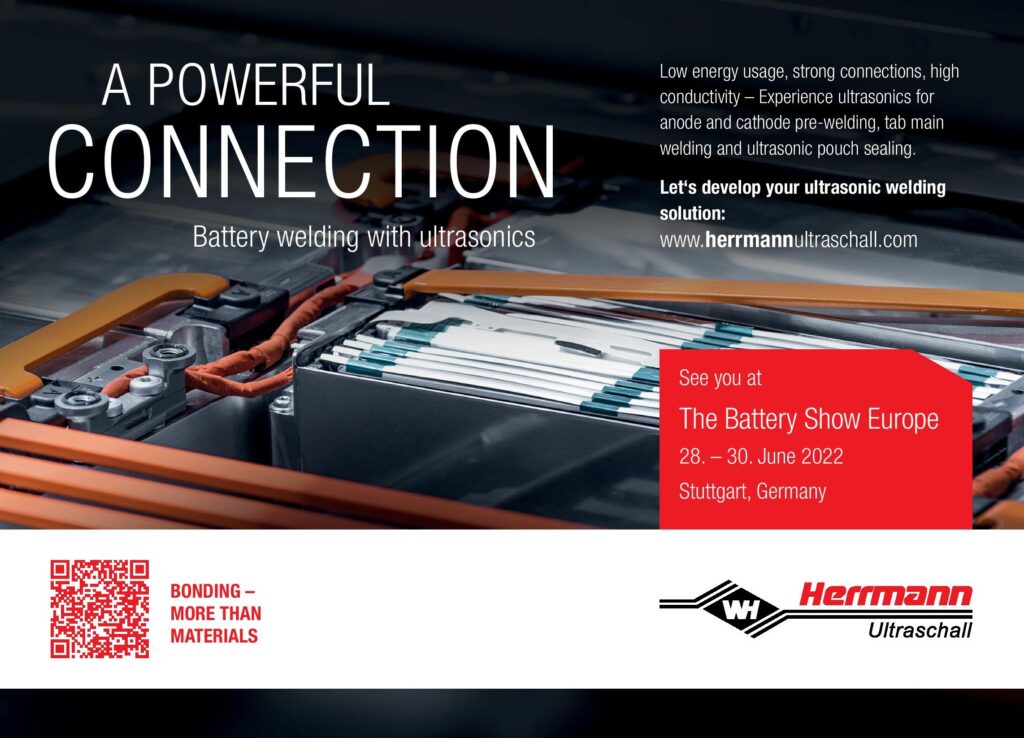
Each of the four target segments is considering different form factors and different chemistries, he adds. For high-performance automotive and aviation, the latter is highly weight-sensitive, while the commercial and off-highway segments are showing interest in large-format cylindrical and prismatic cells.
“Some of the segments we are looking at want to go and explore, and they can now do that because we are willing to talk to them,” MacAndrew says.
There is also growing interest in cells suited to cell-to-pack and cell-to-chassis battery construction, he notes.
“This has driven some really detailed analysis to assess not only how the cell cost plays out, but also how the cost and efficiency of integration can be optimised for them,” he explains. “We see a trend towards looking at large-format cylindrical cells with both terminals one end of the cell or with terminals spaced far enough apart to get high power out of them, and the pack assembly process is somewhat simpler.”
At the same time, he adds, prismatic form factors have been shown to allow for cell-to-chassis construction, while pouch cells need more mechanical support. “There is a trend towards looking at how the pouch can be supported, how it can be mounted and maintained, and how all of that can be simplified,” he says.
“We see large form factor pouch cells being considered to reduce the number of components in an installation, which provides the opportunity to optimise cost. How that thinking will translate into final decisions about the sizes and types of cells to adopt remains to be seen, but we are in discussion with a number of OEMs who are looking at it.”

NMC 622 and 811
InoBat Auto selected NMC chemistries for their energy density-, service life- and power density-focused products, NMC 622 and NMC 811. While the numbers refer to the proportions between the named elements in the cathode mix – six parts nickel to two parts manganese and two parts cobalt, for example – they are not exact, as both NMC 622 and 811 are labels that refer to families of chemistries. “A 622 could be 65% nickel and still be called a 622,” MacAndrew explains.
“We talked with most if not all of the materials providers to give us the chance to assess the efficacy of all their elements and to decide how each of them is best applied as part of our combinatorial approach to developing solutions,” he says.
“A 622 would have been considered an exotic NMC a few years ago, when 111 would have been the typical cell chemistry implemented initially,” he notes. “Each material provider is optimising and creating its own families of formulae, 622 being a family that we have been evaluating for cathode use.”
He says InoBat Auto has evaluated most of the 622s available at both industrialisation and pre-industrialisation levels, and reports good results. Measured against cells considered the best in class at the time, these chemistries proved to be just as good as the comparison cells in most parameters, such as gravimetric energy density, while improving on them in key target parameters including lower internal resistance and higher volumetric energy density.
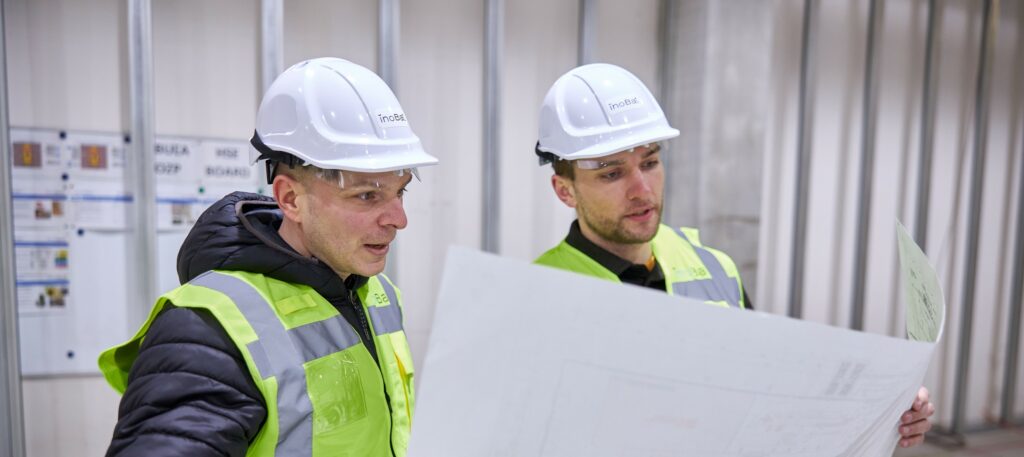
InoBat Auto has also continued to evaluate 811 chemistries for cathode use, MacAndrew says, in an effort to improve stability, capability and in particular the life of cells with 811-based cathodes. As with 622 chemistries, 811 formulae are not all the same; a formula with 85-86% nickel would still be called an 811 even with just 0.5% by weight each of manganese and cobalt, he adds.
Cell energy density can also be greatly improved by preloading (pre-lithiating) the graphite anode with silicon. “We have been screening silicon materials for some time that will go into cells that already contain our graphite elements – we have anodes with 622 graphite and 811 graphite base chemistries,” MacAndrew says.
He classes the 622 and 811 cells with graphite-based anodes as InoBat Auto’s first- and second-generation technologies, while those under development with silicon-based anodes as generations three and four.
“We have produced experimental cells with increasing levels of silicon on the anode that deliver energy capacities of around 350 Wh/kg, which we see as a break-over point for automotive, and pushing towards 400 Wh/kg, which we think is the equivalent break-over for an aviation steady-state application,” he says.
He explains that the silicon allows more of the active elements to be deposited on the anode in the formation process during cell manufacture when it receives its first charge under carefully controlled conditions, becoming lithiated. “That is the potential energy that is being created, and then the ion exchange is what delivers the electrical performance,” he says. “Silicon allows for an increase in that activity to take place.”
He emphasises that the 622 and 811 chemistries have different pros and cons, with 622 better for stability and service life and 811 for power density. Cells with 622 chemistry are lasting beyond 3000 cycles, whereas the capacity of cells with 811 chemistry fade on a steeper gradient. He adds that 811 cells are still good for 1500 cycles, but for vehicles where total cost of ownership is more important than ultimate performance, 622 is better.
Wight emphasises the importance of the end-use requirement for the cell in the battery pack and the vehicle-to-chemistry selection, stressing that understanding the duty cycle is critical. “In the IC world you wouldn’t put an engine with a 12,000 rpm limit but only a 1500 rpm useable range in a commercial vehicle or family car, because it would be horrible to drive. Similarly, with batteries, it is important to make sure they are fit for the vehicle’s purpose.”
Optimising chemistries
Optimising chemistries for different applications involves extensive testing using small form-factor coin cells to evaluate multiple combinations of materials against a number of performance parameters under various conditions, such as temperature extremes.
“We look carefully at an electrochemical level, which allows us to target our questions and to make sure we are down-selecting based not just on the headline performance parameter, but also on secondary and tertiary parameters that are not immediately obvious but are necessary to optimise for,” MacAndrew says.
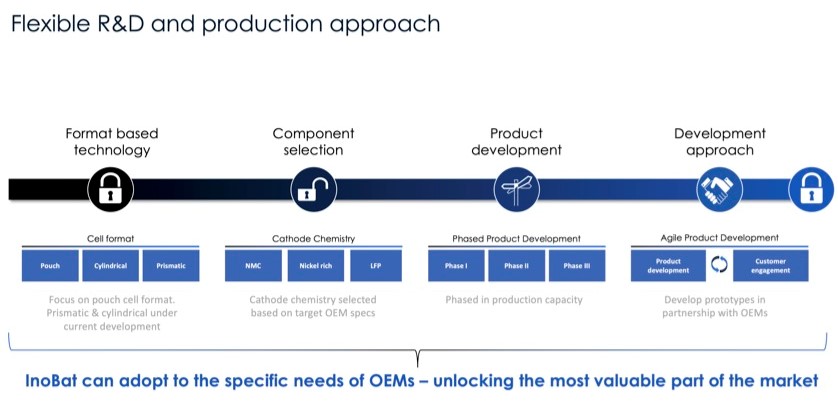
“The data that comes out is so detailed that we spend many hours looking at one set of results. Their interactions are quite extensive, and the complexity of that data means it still has to be interpreted even though it has gone through a powerful computer using AI to pick out the information we need to see.”
The process also helps in designing cells for safety, particularly with regard to finding electrode chemistries that are resistant to thermal runaway while also achieving the required performance in combination with the other components of the cell, MacAndrew explains.
“We work with separator technology that can help reduce energy release under certain abuse conditions, we optimise electrolytes so they can mitigate for abusive situations or faults, and we implement quality processes to ensure we don’t induce conditions under which resistances can build,” he says.
“Then we define how cells need to be operated at a system level to provide a sustainable performance without risking any of the severe reactions that can take place if you charge any cell too much, or if you completely discharge a cell then recharge it. Cells can’t compensate for that level of abuse.
“What we define is a safe operating window and safe characterisation of the cell,” he adds. “Then we work with integrators and OEMs who know the importance of the part they play in vehicle safety.”
Contrasting safety cases
MacAndrew emphasises that the safety cases in aviation and automotive are different. “I would hesitate to say aviation is at a higher level, but it has a different focus because of the nature of the operation,” he says.
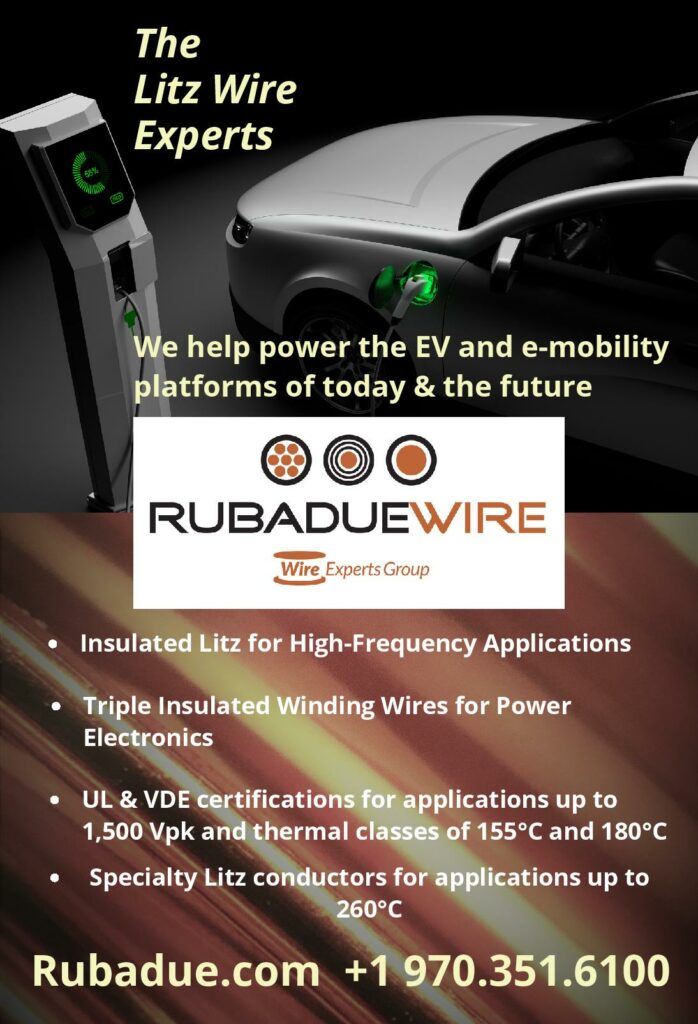
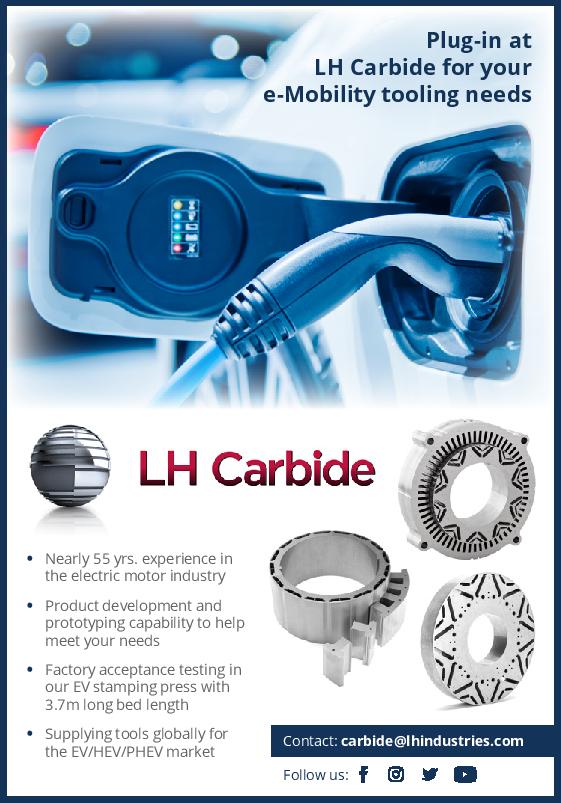
“Continued safe flight, for example, is an EASA requirement stipulating that an aircraft must not be sensitive to a fault to the point where it can’t continue its journey and land safely. That’s different from the safety case for automotive, where maybe the powertrain can be powered down substantially or completely if the battery suffers a fault, as the vehicle will be able to get to the side of the road safely. In aviation there is no side of the road.
“We need to help aviation businesses design robust, rugged systems that can react to any potential fault and to still remain safe in flight. We carry out cycle testing to make sure the cells operate in normal conditions as well as under abusive conditions and with faults, which we simulate to make sure the system can provide the necessary power, even if part of it has been taken offline.”
The rules stipulate that if the aircraft develops a fault during the approach to landing, for example, it must be able to complete a go-around or an aborted landing and be able to divert, he adds.
As with conventional aviation, the power system is designed with enough margin so that it can deliver the power needed to achieve the required performance, even with a fault or under abusive conditions. “So you have got an extra 20%, or whatever the number has to be, and the system’s ability to deliver it comes from the design of the cell all the way through to the complete installation.”
BMS involvement
While InoBat Auto’s core business is the development and manufacture of cells, which are only part of a battery’s architecture, the company works with battery OEMs to help ensure that their battery management systems (BMSs) are defined robustly enough to operate the battery safely.
Wight emphasises the importance of focusing on cell development and avoiding competition with integrators and battery pack designers, and how InoBat Auto will help them develop modules if asked, principally by providing advice on the best approach for their applications.
MacAndrew adds that Inobat Auto defines the operating regimes for the cells, and then provides those characterisations to the BMS developers.
In some instances, the parameters are relatively simple, such as temperature limits, but the nature of the characterisation goes much deeper and involves the creation of look-up tables (‘maps’) for the BMS.
“We also provide specific conditions of operation for specific states of charge at specific temperatures,” MacAndrew says. “There is a map that the BMS uses to understand what the allowable charge and discharge rates are at all states of charge at those temperatures. That map table allows the BMS to maintain safe and secure use of that chemistry.
“Similarly, we also provide a voltage operating window where the maximum and minimum voltages are set out, and another look-up table that the BMS uses to assess what the maximum charge and discharge voltages are at different temperatures.
“Each of those tables are a part of what we provide to the integrator to allows them to create a BMS that will make informed decisions about how hard the battery can be operated and how quickly it can be charged.”
Ideally, each cell would maintain as near as possible the same state of charge as all the others under all conditions, so that their performance is uniform. That is not always possible when the cells are integrated into a pack, MacAndrew explains, as some cells will be in locations that will be hotter or cooler than others, so an important part of the BMS’ job is balancing the cells. It does so by stopping, slowing or accelerating the charging of individual cells using dedicated resistors, and with active charging moving charge between cells to equalise them.
“We can help by making our cells as accurate and repeatable as possible to minimise balancing time,” he says.
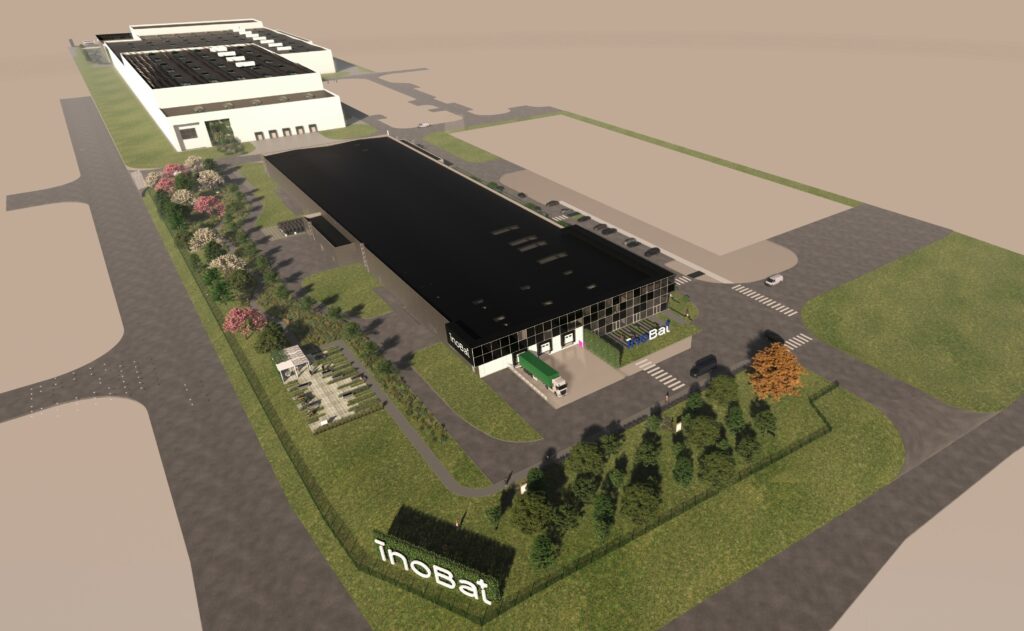
Cooling advice
Thermal management is another pack-level task which is generally the responsibility of the battery integrator or the vehicle OEM, with which InoBat Auto, as the cell supplier, can offer help and advice.
“Obviously there is an operating window for the cells and, as you increase power and draw high currents, internal resistance will generate heat, and at some point the battery will have to be actively cooled,” MacAndrew notes. “Our approach is to make sure the cell surface can be accessed so that heat can be extracted and dissipated to a cooling system.”
While InoBat Auto provides cells that operate safely over a well-defined temperature range, which is communicated clearly to the vehicle OEM, he says, the OEM is faced with the challenge of managing the weight budget and complexity involved in delivering a stable system, part of which involves choosing between air and liquid for the cooling medium.
That is a likely point of divergence between the key markets for InoBat Auto’s cells of high-performance automotive and aerospace applications, as the former is increasingly adopting liquid cooling – with immersion cooling using dielectric fluids on the horizon – while most electric aircraft developers are keen to avoid it because of the extra weight and complexity involved.
Duty cycles
Wight argues that a deep understanding of the duty cycle ought to play a central role in making such choices. “If you can achieve the duty cycle with air cooling, you take quite a lot of weight and complexity out of the system, and that has obvious benefits in a lot of areas,” he says.
He cites a motorsport application involving very high temperatures and aggressive g-forces as an example. “The solution for that was to allow the thermal mass of the battery to control its temperature through a well-known duty cycle, then use forced air cooling between events,” he says.
“It was a great solution for that environment. Reliability was key and, as ever, if you have a very harsh environment, the more parts you put into it, the greater the likelihood you’ll have a failure.”
Future developments
Beyond generations one through four, InoBat Auto has a roadmap for further electrochemical development. “That includes more exotic materials for the cathode,” MacAndrew says. “We are also evaluating how we can further optimise the performance of the anode, and we are ultimately looking at combining the functions of the separator and the electrolyte.”
The central aim of these efforts is to maximise the gravimetric and volumetric energy densities, which depends to a large extent on how many lithium ions can be packed onto the electrodes.
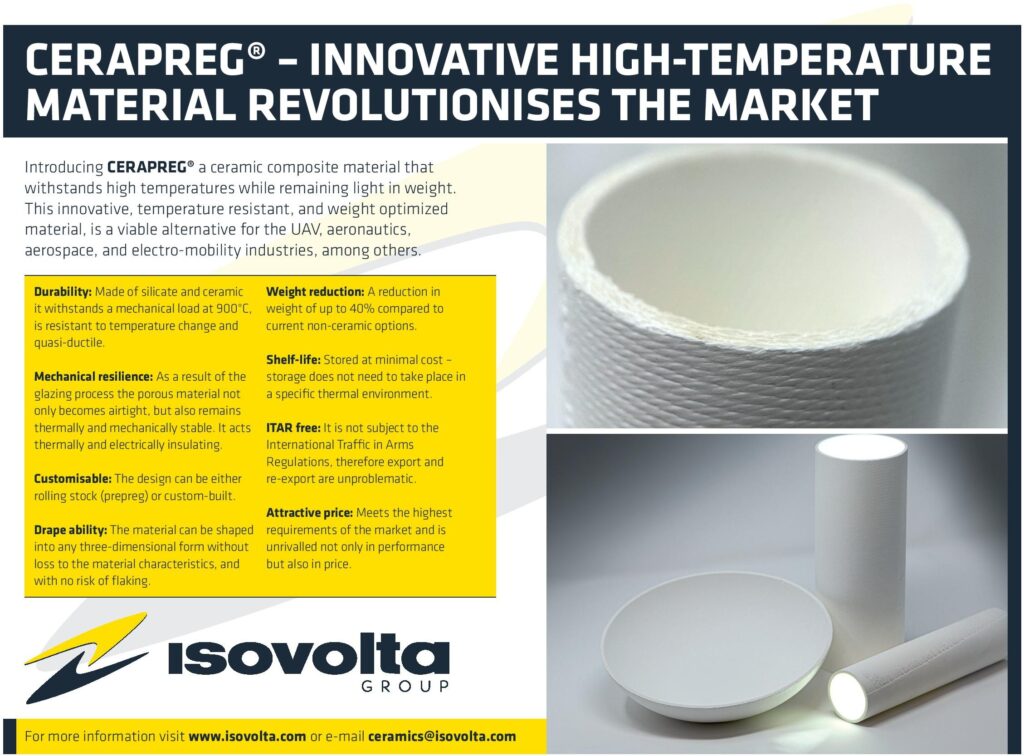
“There is a theoretical maximum for both electrodes that is not possible to achieve, but which we use when we assess how much energy per gram, per square centimetre, that we can get into the designs we are developing,” he says.
While pre-lithiation of the anode is one way of increasing the number of ions it can hold, using lithium metal for the anode comes as close to the maximum that can be achieved, he explains. In parallel, the company is working on solid-state cell technology, with a focus on safety in general and optimising the separator in particular.
“We are carrying this out independently of other activities at this point to assess the functionality we are trying to achieve,” MacAndrew says. “Ultimately, that will allow us to offer solid-state solutions as well, and they might be paired with our lithium anode.”
From r&d to gigafactories
All of the above relies on the company’s r&d, prototyping, sampling and volume production capabilities that at the moment rely on partners in the Asia-Pacific region but will transfer to Europe over the next 2 years, with director for strategy execution and programme management Pavol Krokos steering the process.
Construction is under way on the first facility in Slovakia, with a second, much larger one nearby at the planning stage. In the meantime, sample batteries are already being delivered, Krokos says.
“Working closely with our technology partners and contract manufacturing partners, we provide all the knowhow and audit the suppliers,” he adds. “We provide the chemistry and the recipes, we have all the processes documented, we own all the intellectual property and the production protocols, all the way from slurry to coating and formation, and we control the steps and the quality of the samples.”
He emphasises though that InoBat Auto expects to continue technological collaboration with its Asian partners, even after the facilities in Slovakia to make cells in different sizes and formats are up and running.
Phased development
Development of the facilities near Bratislava is planned in three phases. The first is focused on building the r&d centre with its laboratories and a semi-automated pilot production line.
Called Volta 1, this facility is due to be commissioned by the end of this year, with trial production of sample pouch cells set to begin in January 2023. The cells it produces will support customers’ battery development programmes, Krokos says. The laboratories will be commissioned and in operation this September.
In the second phase, the company plans to build a new plant next door to serve as a ‘pilot gigafactory’ that will be commissioned in 2024. Known as Volta 2, it will have a maximum capacity of 2 GWh, and is intended to supply customers with low production volumes.
Volta 2 will also serve as a stepping stone to larger gigafactories in that the same processes and equipment will be used to scale up production for these new facilities. The company is currently going through a detailed site selection procedure to choose between candidate sites in eastern and western Europe for its third plant, whose capacity could be up to 32 GWh.
The semi-automatic pilot line in Volta 1 is to be installed as a turnkey solution supplied by partner Wuxi Lead. It is semi-automatic, in that all the cell production steps from slurry mixing to coating and formation are carried out automatically, but between each step and the next the partial cells are transferred between machines manually by technicians.
“That way we ensure that quality is very high,” Krokos says. “When we provide samples to customers, the first cell and the 1000th cell are exactly the same with automated manufacturing.”
In addition to sample small pouch cells, Volta 1 is intended to be able to produce sample cells in different sizes and formats, and space has been set aside for another assembly line for them. Production capacity will be between 15 and 20 MWh per shift, which translates to between 50,000 and 70,000 cells a year when running one shift in the 9000 m2 facility, Krokos says.
“We can increase production according to demand, but these numbers will be sufficient to support various customer development programmes through one year.”
With a starting capacity of 1 GWh, Volta 2 will be a 40,000 m2 facility, so it will have space to double its capacity, producing both pouch and prismatic cells. The pouch line will be able to produce cells of different sizes, MacAndrew notes, but the situation with prismatic cells is more complicated. “It’s not that easy to produce different cell sizes unless you have different assembly lines,” he says.
“Our r&d labs are next door to Volta 1, so the engineers are right beside the production line,” Wight adds. “The small-scale line allows us to prototype cells so that we can iron any problems out before we take them into the gigafactories, which will aid efficiency in time.”
InoBat Auto chose to go with a single supplier of a turnkey solution for Volta 1 as a risk reduction measure, he says; one of the risks it eliminates is mixing pieces of equipment from different suppliers. “That ensures control of and clear responsibility for everything that goes through that line.”
Standards
InoBat Auto intends its cells to meet both aviation and automotive standards, so quality control will have to be very tight. Krokos notes that the company has already received ISO 9001 certification for its management and processes, and is working on the segment of the standard that covers manufacturing operations, and anticipates receiving the ticket when the facility is commissioned.
MacAndrew says ISO 9001 is the broad engineering standard for manufacturing and control, and adds that InoBat Auto is applying the EN 9100 aviation standard as well. “EN 9100 takes the objectives of ISO 9001 and adds to them to satisfy aviation requirements in the same way that IATF 16949 does for automotive, and we are also working towards that standard.”
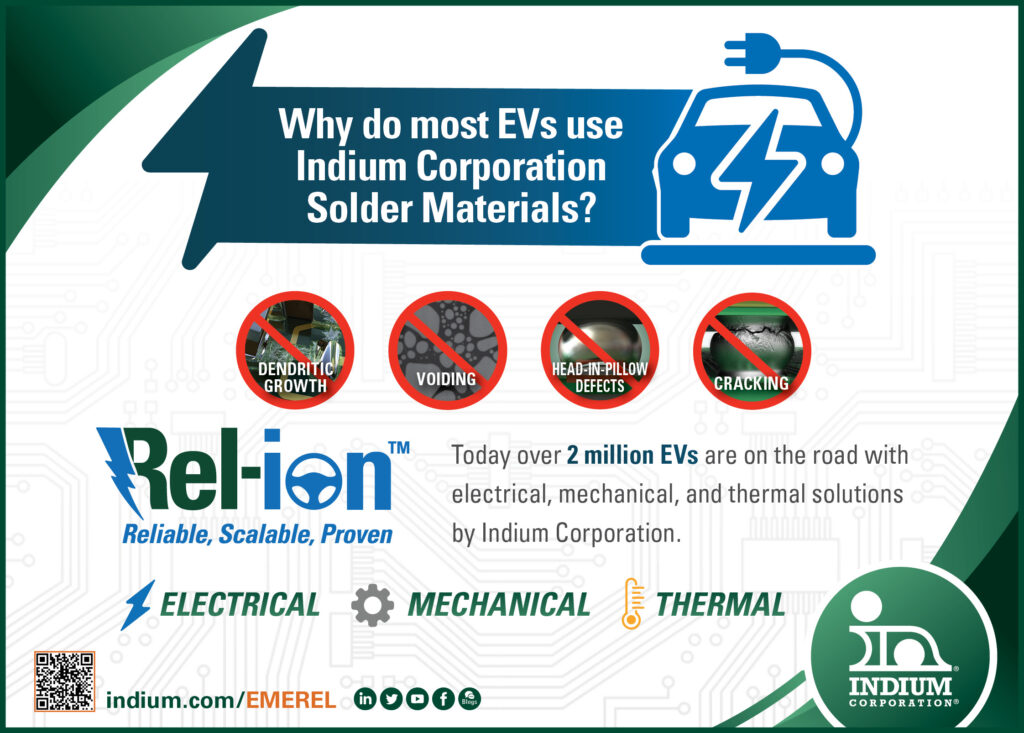
Sustainable future
InoBat Auto is also determined to minimise the environmental impact of its entire operation, so Krokos says the company has contracted for green electricity supplies. Slovakia has a mix of hydroelectric and nuclear plants, and the Volta 2 gigafactory will have solar panels over its entire roof, and all the plants will recycle their process water.
“We are considering the circular economy at the start, looking at everything from the mine to the battery’s second life and ultimate recovery of materials,” MacAndrew says.
Traceability will be key to providing good quality cells for second-life applications such as storage for renewable energy sources, as well as being essential for aviation applications, he says. Schemes such as battery passports and technologies that link BMS to the cloud will be integral to the process.
“The health and usage of these cells are going to be measurable and reportable during manufacture and operation,” he says. “We are looking at a data system that allows us to keep track of how our cells are being used.”
He emphasises that the end of a cell’s life is not the end of the electrochemical life of its active materials. “We are studying how we can recover 90-95% of those materials for reprocessing into virgin material for new batteries,” he says.
A company in the InoBat Auto group is planning to build a recycling facility within 1 km of the factory complex, according to Krokos. “The first process will shred batteries down to black mass, then hydrometallurgy will refine the active materials from the black mass,” he says.
“We are already applying for permits, and plan to develop the project in the next 2 years. It won’t be entirely dedicated to Volta 1 and Volta 2, as we will need to collect batteries from elsewhere to feed the beast.”
“For each stage that we are assessing we have a set of steps to follow. We can show that material recovered from a used battery has been through cell analysis and development, and we can demonstrate good performance in cells based on recycled material,” says MacAndrew. “We are also looking at using materials that are complementary to recycling, and avoiding materials in cells that will contaminate those we want to reuse.”
Short supply lines also reduce an industry’s carbon footprint, and in line with developing European policy, InoBat Auto is working to ensure it can deliver a percentage of each of its cells with both local and recycled content.
“We are seeing a lot of interest and government support, not only for gigafactories but also for the manufacture of cell materials in the region,” MacAndrew says. “Security and sustainability of supply go hand in hand with local manufacture.”
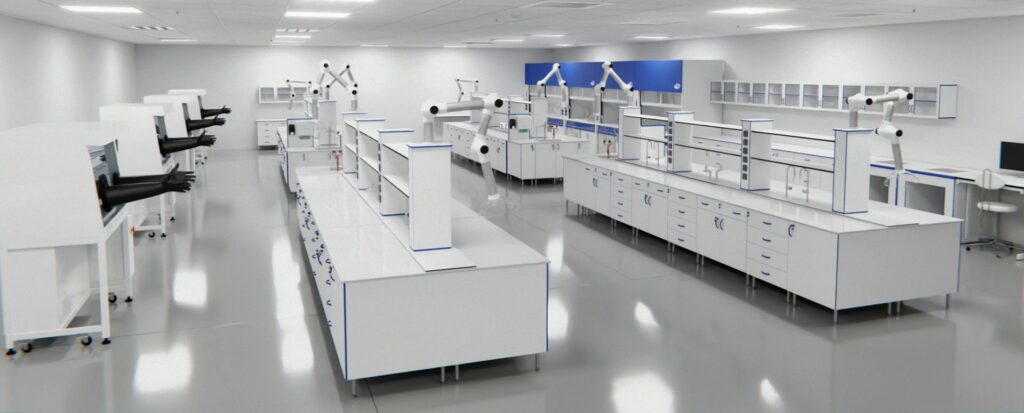
The InoBat Auto team
Although a young company, InoBat Auto has built an expert C-level team with extensive experience in breadth and depth in automotive, aerospace and electrical engineering as well as advanced manufacturing.
With more than 28 years in the automotive industry, Doug MacAndrew began his career with Rover Group, then spent 8 years at McLaren, developing and delivering the SLR hypercar and its derivatives for Mercedes, followed by the MP4/12 family of supercars.
He has been involved in EVs for 14 years, a period in which he served as CTO at Smith Electric Vehicles, a start-up truck electrification business in the north of England that produced around 1000 certified EVs plus a similar number of prototype and development vehicles.
For the past 7 years he has worked in Slovakia on EVs and electric aircraft, including eVTOL machines. He joined InoBat Auto two-and-a-half years ago to focus on industrialisation, technical development and building the company’s engineering team.
An electronics engineer by training, Iain Wight worked on the development of military aircraft navigation systems before moving into the automotive sector with Bosch for 6 years in the early 1990s at the advent of full electronic management systems in vehicles.
Participation in club racing led to a move to Pi Research, which became Cosworth Electronics, where he spent 8 years working on data and control systems in multiple formulae at the highest levels of motorsport.
In 2003, he began a 14-year stint at Ricardo, joining as business development director and finishing as director of transmissions for the company’s performance products group. During that time, the group developed transmissions for Bugatti’s Veyron and Chiron hypercars as well as most of Porsche’s motorsport transmissions in addition to systems for Le Mans, World Rally Championship and Formula One cars.
Ricardo’s development of the transmission for Jaguar’s CX75 hybrid supercar brought Wight into contact with Williams Advanced Engineering (WAE), to which he moved as business development director 5 years ago. At WAE he focused on electrification and battery development, working on systems for e-bikes, a 2 MW hypercar and much in between, he says.
He joined InoBat Auto in early 2022 at the invitation of CFO Paul Hancock, with whom he had worked at Ricardo.
“One of the biggest challenges we faced at Williams was supplying the right cells, and it is going to be a massive challenge in the future,” Wight says. “By joining InoBat Auto, I knew I could play an interesting role doing something about it.”
Pavol Krokos has extensive experience in construction and finance. Before joining InoBat Auto, he ran several modular building projects in Germany, Austria and the Czech Republic. He managed multi-million Euro projects for major customers, taking responsibility for their finances and working directly with investors and banks.
ONLINE PARTNERS
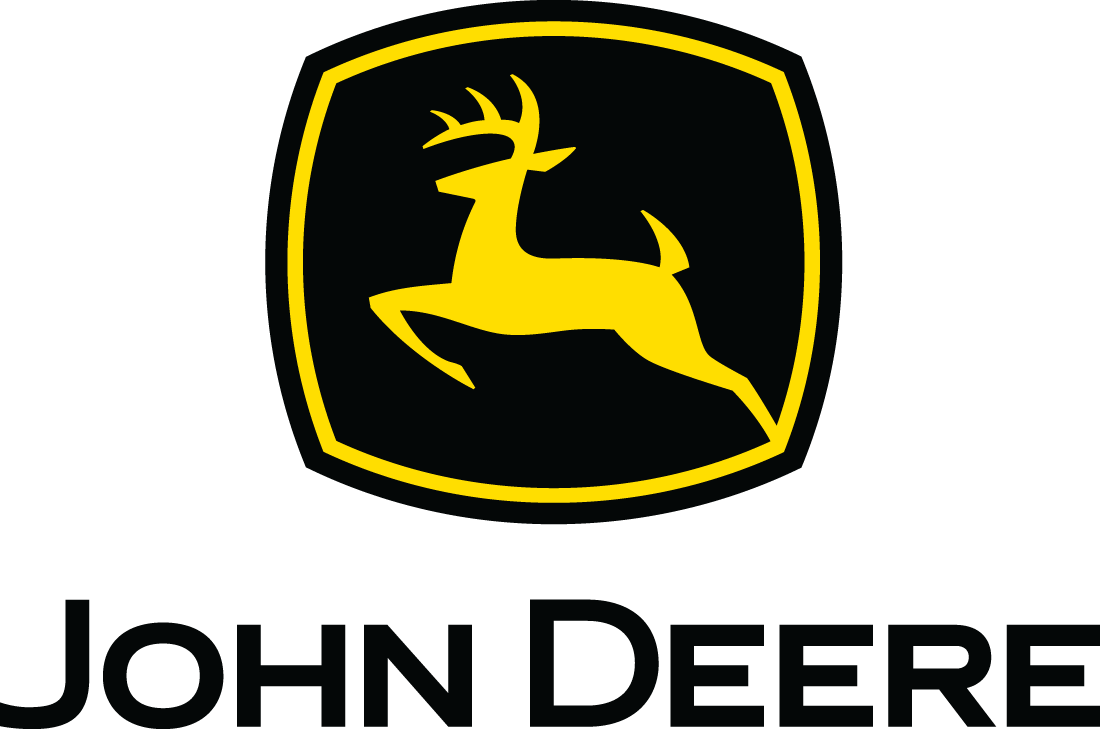
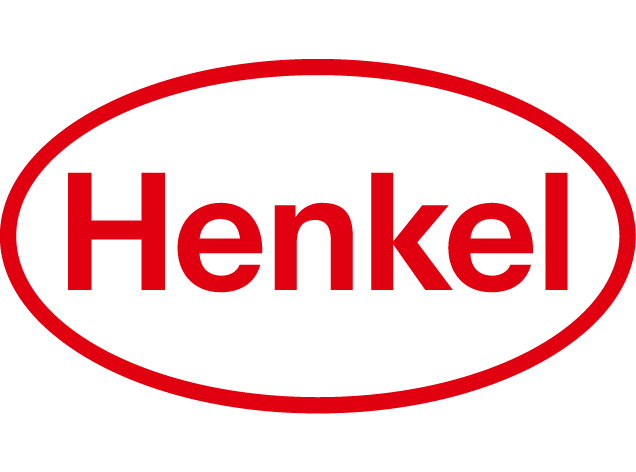
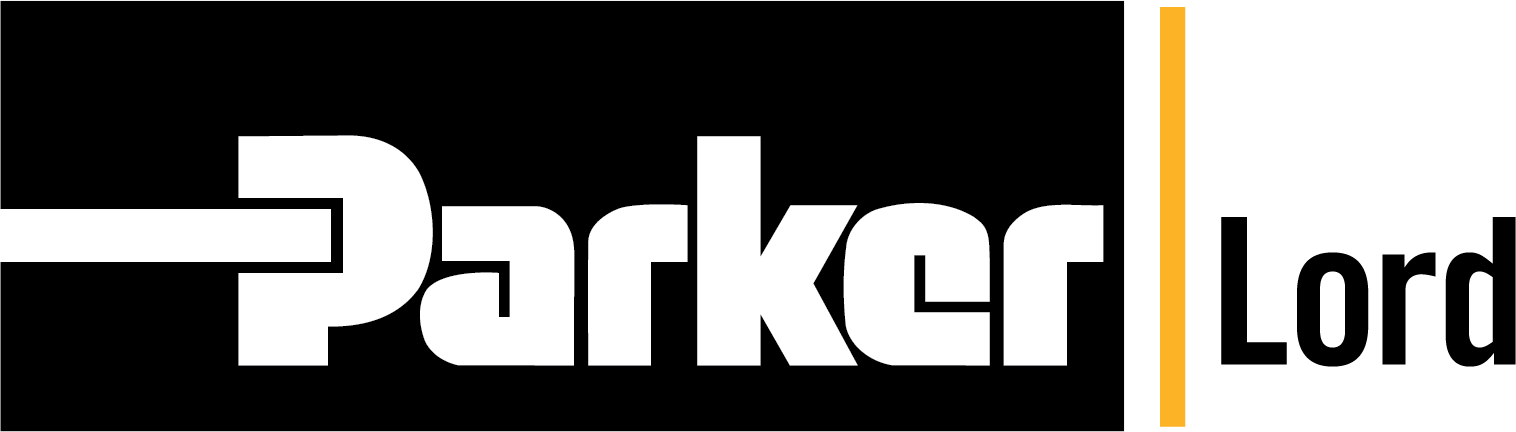
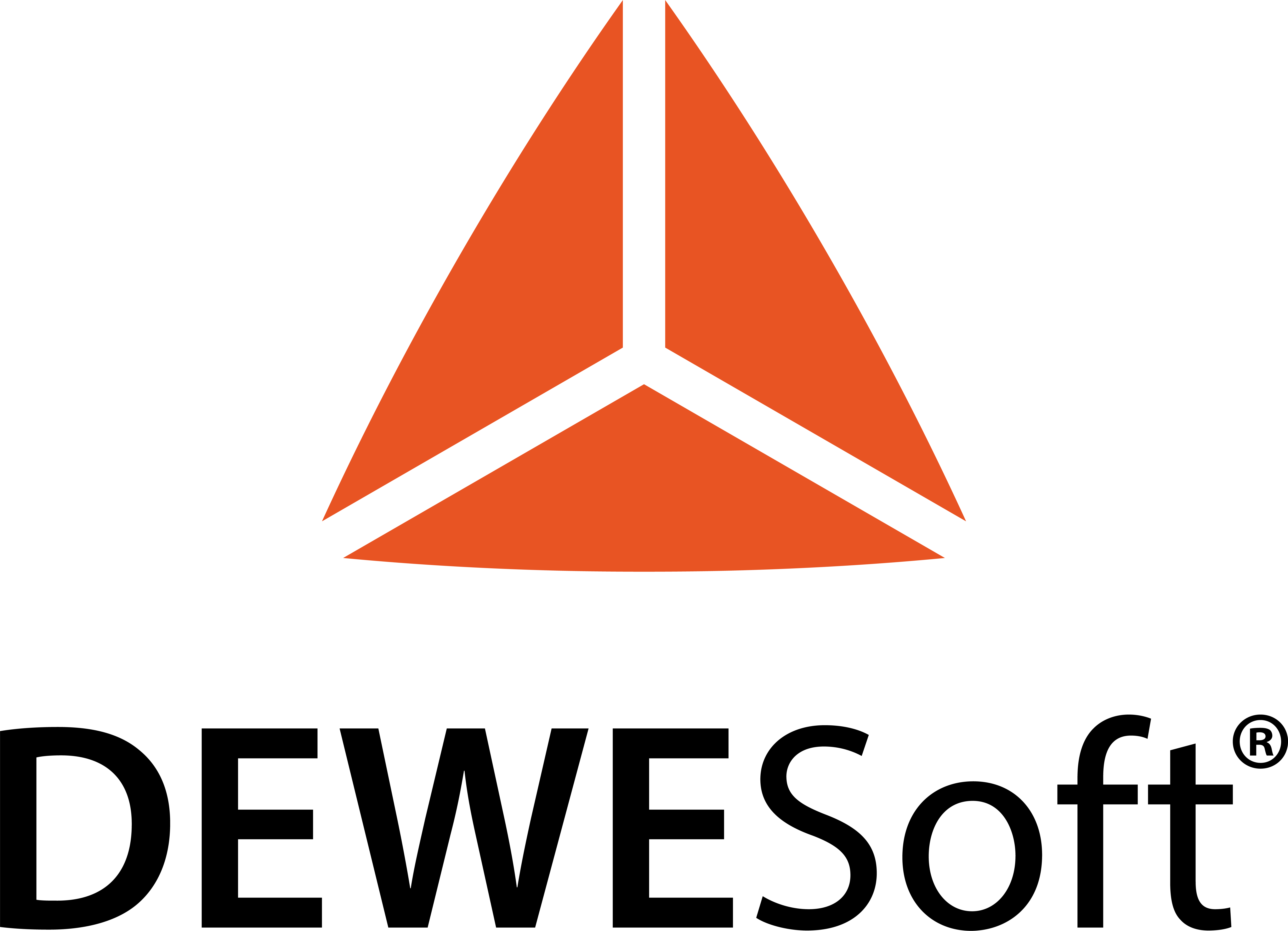
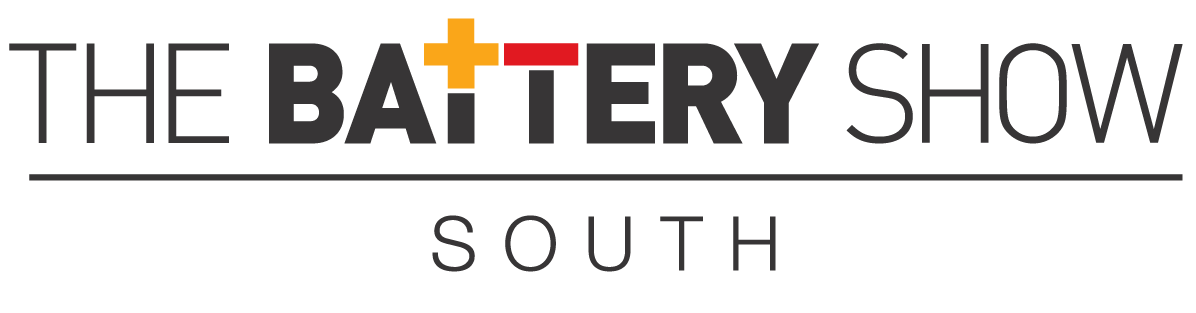
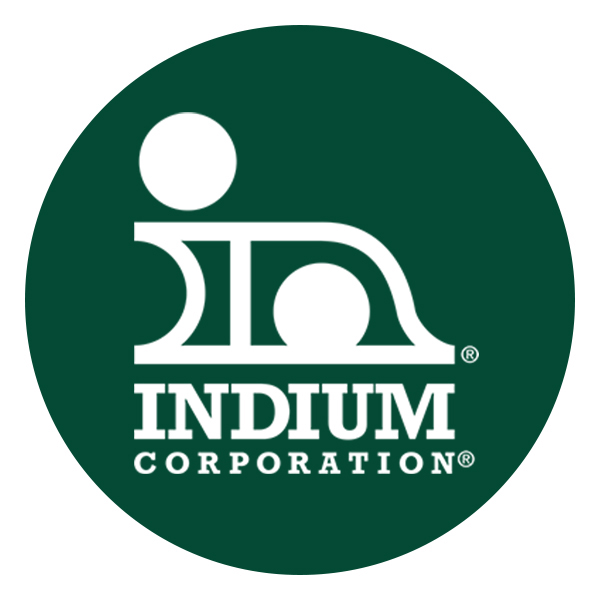
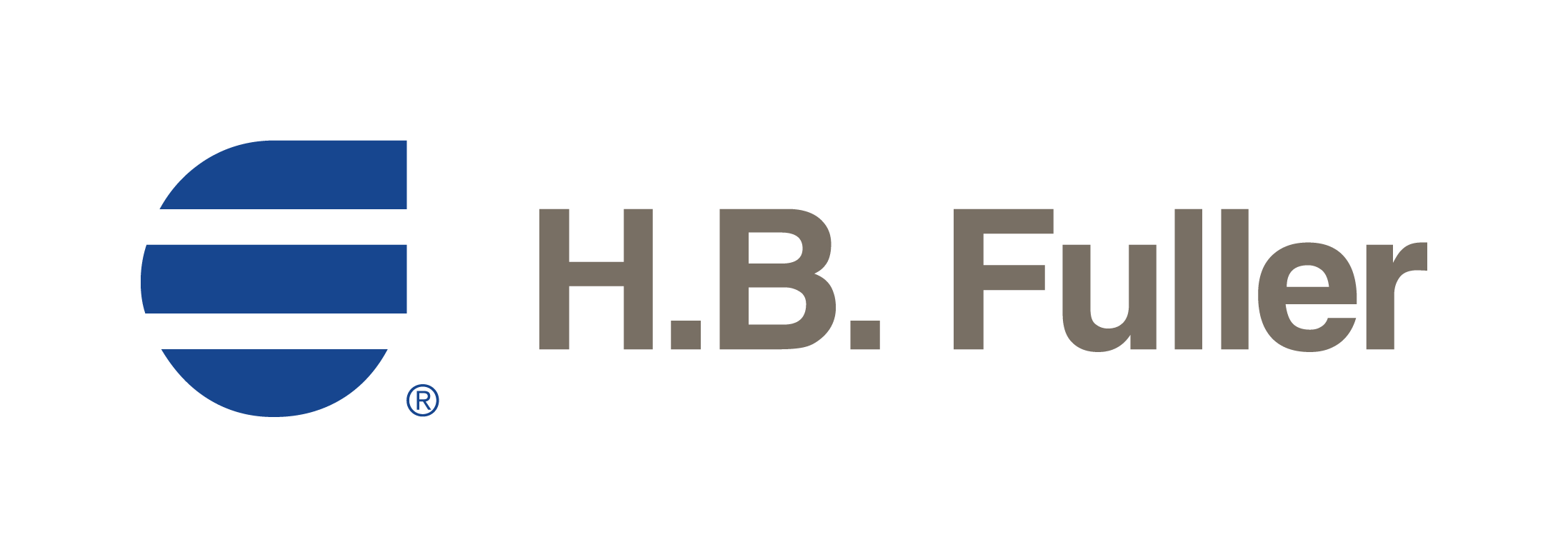