Electrolyte detection outs cell leaks
Cell leakage in lithium ion batteries is bad news, so battery makers want to find any that happen during manufacture or assembly so their quality control teams can prevent early failures and minimise warranty costs, while drivers need confidence, safety and low servicing costs. Sandra Seitz from vacuum analysis and test instrument specialists Inficon explained that the company has developed a direct electrolyte detection method and a range of vacuum machines to test different types of cells.
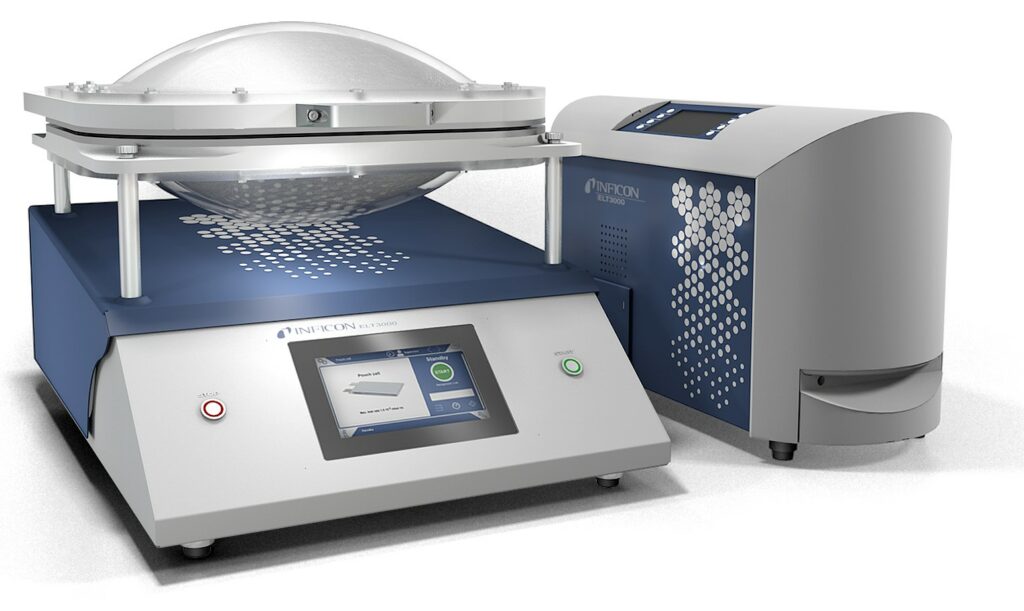
The pressure in most battery cells, and particularly in pouch cells that rely on outside pressure to push the anode and cathode together, is below atmospheric, she said. Therefore a small leak will tend to draw in air along with moisture that will react with the electrolyte to form sulphuric acid, worsening the leak, so leaks tend to grow. With holes of up to 56 microns in size, the pressure differential tending to push the electrolyte out are balanced by forces including surface tension that make it cling to the walls of the leak path, so no electrolyte gets out. A hole any larger than that will result in a leak rate of at least 10-6 mbar l/sec. (The millibar-litre per second is the standard measure of leakage rate that takes air pressure into account). Inficon’s detection method targets leaks of this size or larger.
The method works by reversing the normal pressure conditions in the cell using a vacuum chamber into which the cell is placed, Seitz explained. “You are actually pulling electrolyte out of the cell, which then can evaporate on the surface of the leak opening, and a mass-spectrometer-based sensor detects the solvent vapour.”
The system stores all test data ready for export, includes a USB port for bar code scanners and other means of identifying test items and features Fieldbus interfaces to link it to factory automation systems including ProfiNet, ProfiBus, and DeviceNet plus an Ethernet IP interface.
The core of the system is the ELT3000, consisting of a gas detection unit with the sensor, and a gas control unit that controls the pump down and sends the gas to the sensor. A set of different vacuum chambers of different sizes can be connected to it, including the flexible FTC3000 that can cope with unusual cell shapes by holding them between a membrane in the lid and one in the base that form a seal around the cell as vacuum is pulled. Calibration is provided by the E-Check test leak that provides a constant signal of electrolyte solvent, Seitz said.
ONLINE PARTNERS
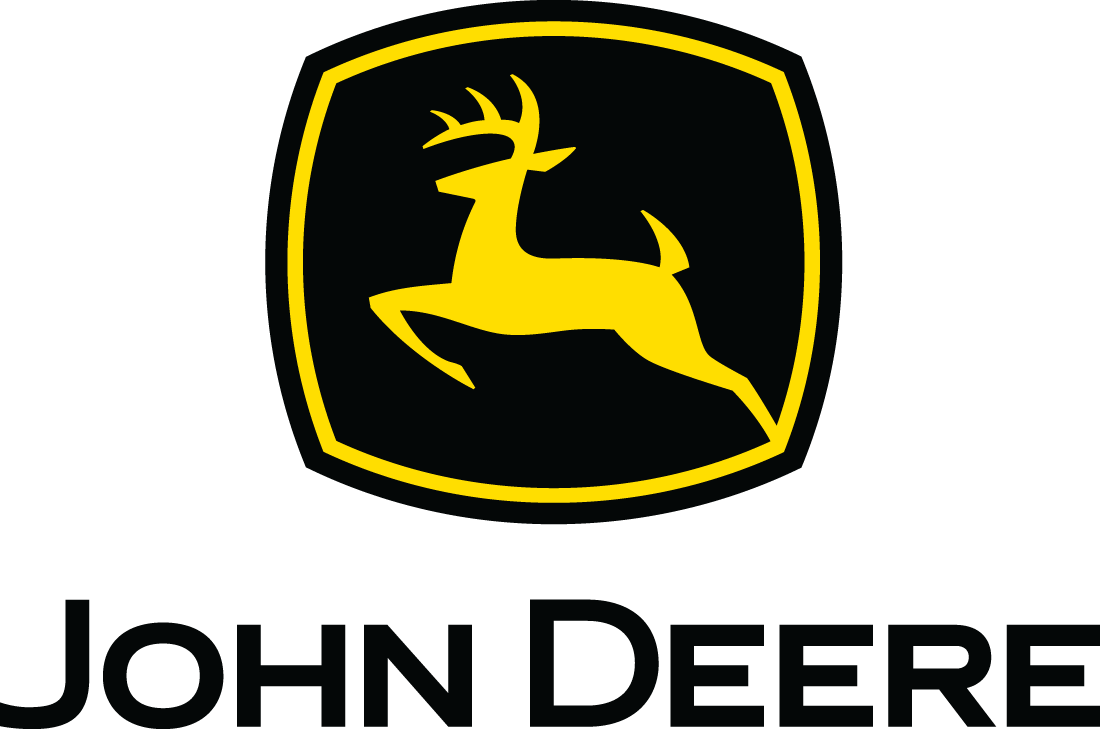
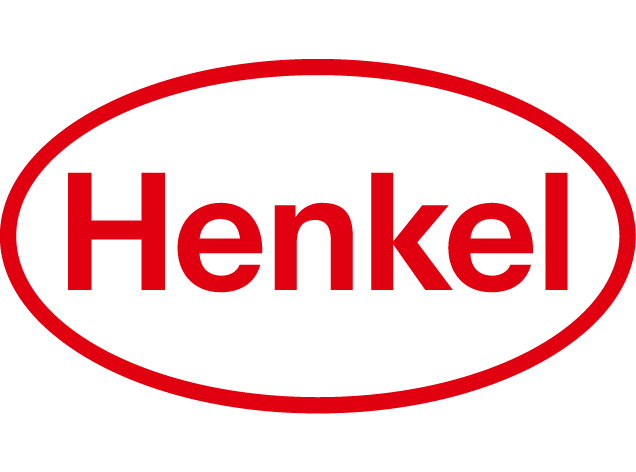
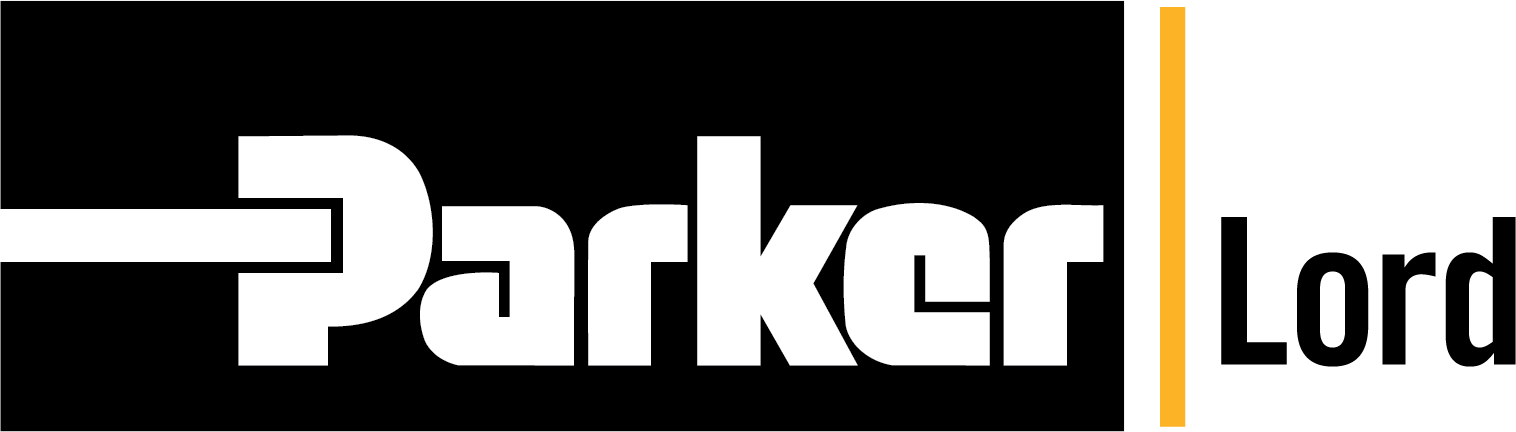
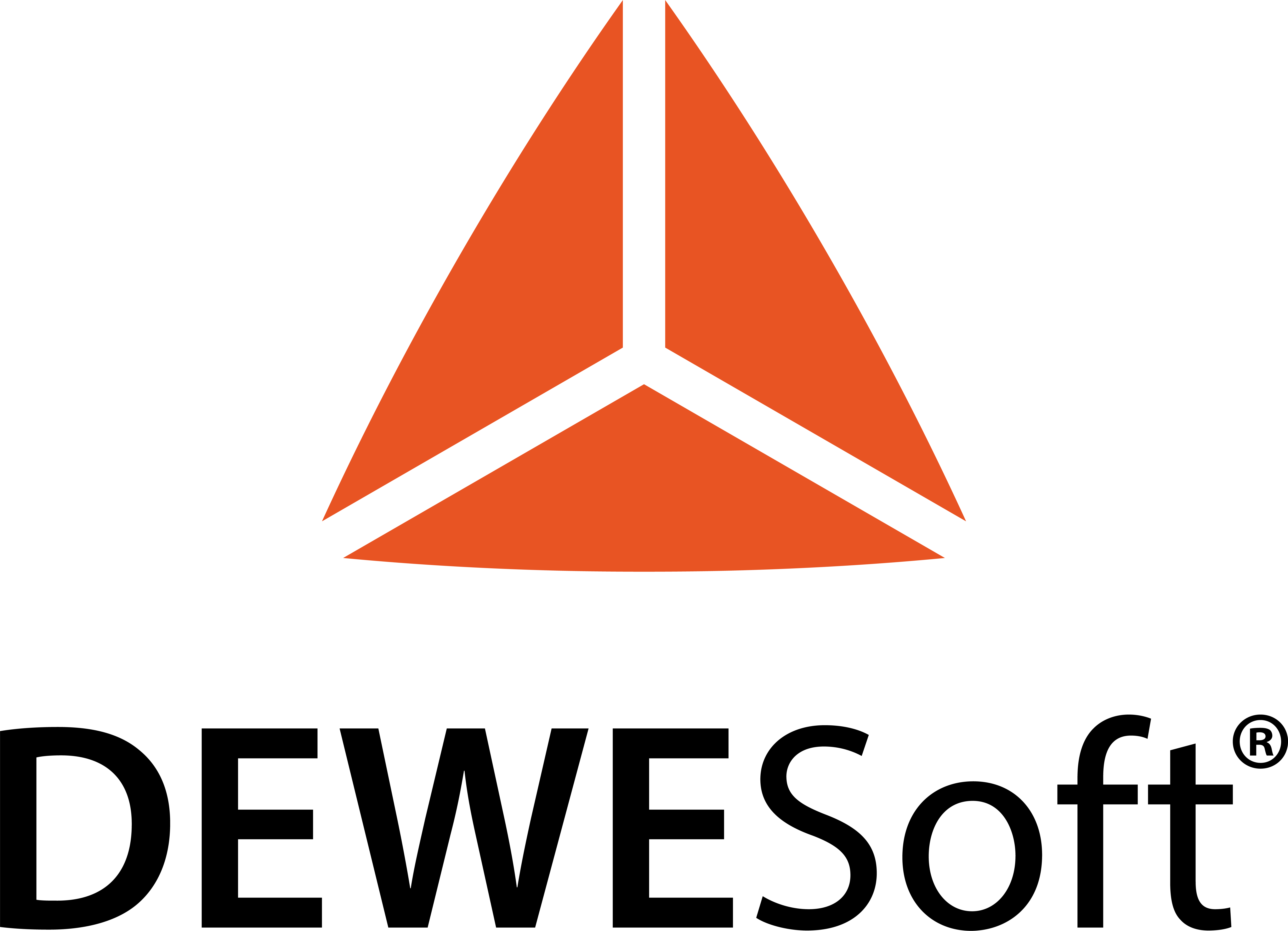
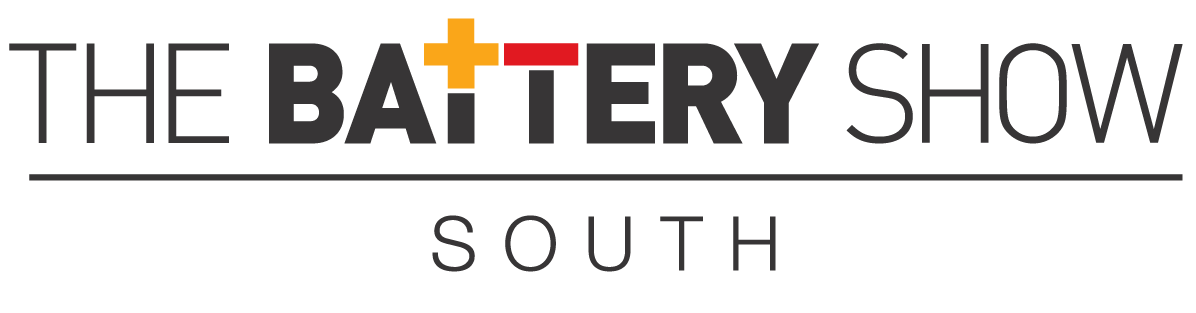
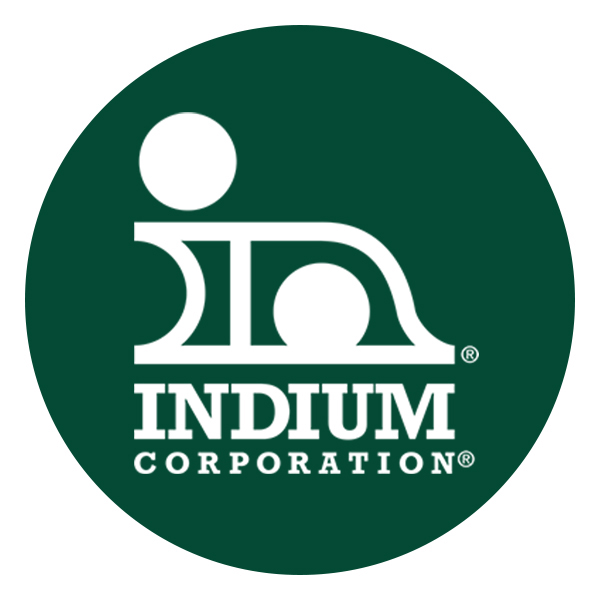

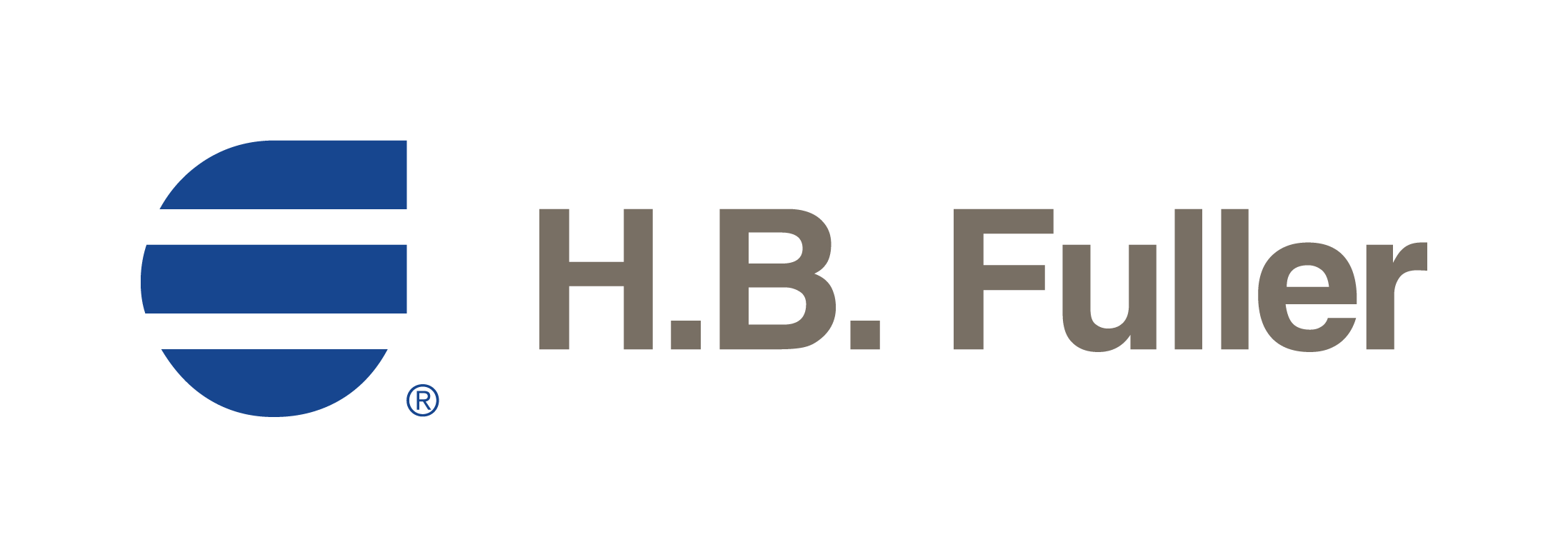
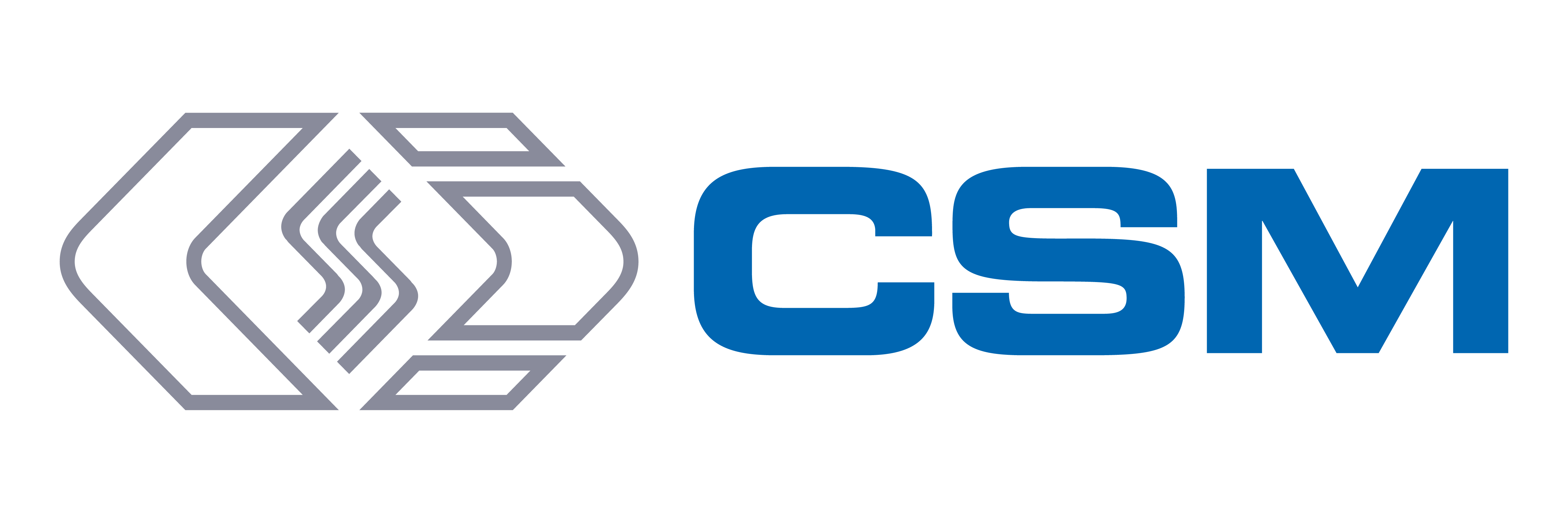
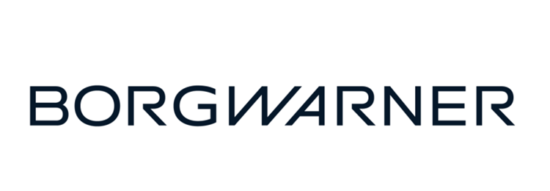