Individual wheel control
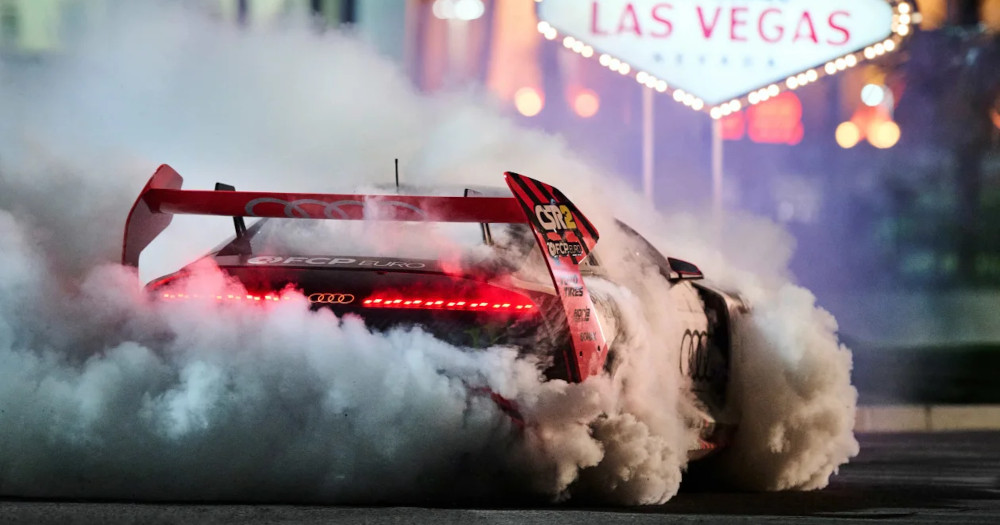
It’s worth taking 9 minutes and 36 seconds out of your day to watch professional rally driver Ken Block’s Electrikhana on YouTube (writes Peter Donaldson). I don’t know whether he is a mathematician, but Block is clearly running some very advanced software somewhere in his central nervous system. His latest instrument is the Audi S1 Hoonitron, a bi-motor, 800 V, all-wheel-drive battery-electric monster styled with a respectful nod to the 1985 Sport Quattro S1 rally car.
In its drifting romp around the streets of Las Vegas in the video, Hoonitron appears to spin its wheels almost continuously, whether tracking in a straight line with its fore-and-aft axis in line with its direction of travel, executing a series of 360º spins along its line of advance, or entering a hairpin bend backwards then shooting out of it forwards, describing a narrow vee in the process. Through the whole automotive ballet, whenever the car isn’t followed by a constantly replenished plume of tyre smoke it is enveloped in one.
Audi has revealed very little about whatever advanced control software (if any) helps Block maintain control of the Hoonitron so far beyond the normal limits of grip and stability, but the basic architecture of the drivetrain enables a degree of individual wheel control, which is increasingly important in EVs, particularly all-wheel-drive machines, for stability management.
There are many ways of providing drive to all the wheels of an EV. Most conventionally, a conversion of an IC-engined off-road vehicle might use a single motor driving the wheels though a transfer case, front and rear propshafts, differentials and half shafts. A second option is for one motor per axle to drive a pair of wheels through a differential, while a third is to give each wheel its own motor that turns it with a driveshaft, and a fourth is to integrate a motor into every wheel.
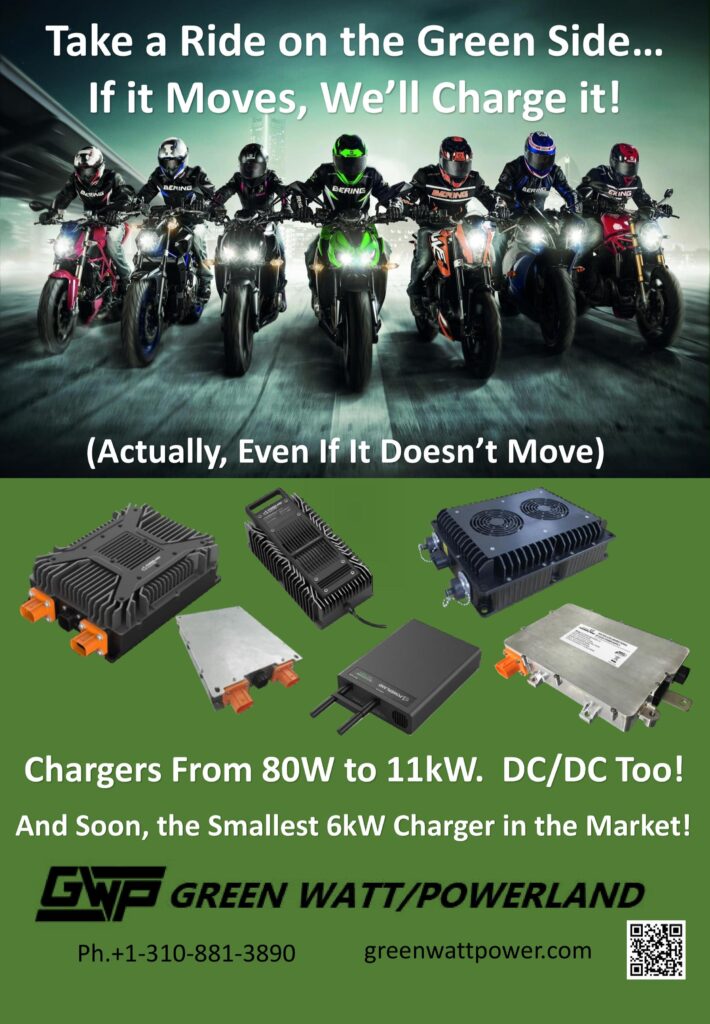
In all cases, the motor can drive the wheel directly or through a reduction gearbox.
Audi went for the second option with the Hoonitron, its pair of Formula E-spec motors driving a differential through a reduction gearbox. Block is provided with a ‘handbrake’ with which to initiate slides and spins, which works by shutting off power to the rear motor.
In the more mundane world of roadcars, individual wheel control (IWC) is more commonly used to enhance safety by preventing slides and spins, using various techniques implemented through software.
With the ability to apply driving torque, no torque or braking torque to each wheel individually, along with friction braking and steering inputs, IWC can implement schemes such as direct yaw control by differentially braking the wheels to generate a yaw moment, and sliding mode control (SMC) to maintain stability and control in cornering at the limits of adhesion.
Although the term is used in the context of incipiently sliding vehicles, ‘sliding’ is a mathematical term, as SMC is described as a non-linear control method that alters the dynamics of a non-linear system (such as a cornering vehicle) by applying a discontinuous control signal that forces it to ‘slide’ along a cross-section of the system’s normal behaviour.
In future, IWC is likely to extend into other areas of vehicle stability management, including active suspension, as researchers look into the best ways to combine wheel motor torque reaction and suspension geometry, for example, to provide very precise control of wheel vertical movement and thus vehicle weight and grip distribution.
However many or few of these techniques might be embodied in the Hoonitron, it is a rolling, sliding, pirouetting advertisement for the fine control potentially available to all-wheel-drive EVs.
ONLINE PARTNERS
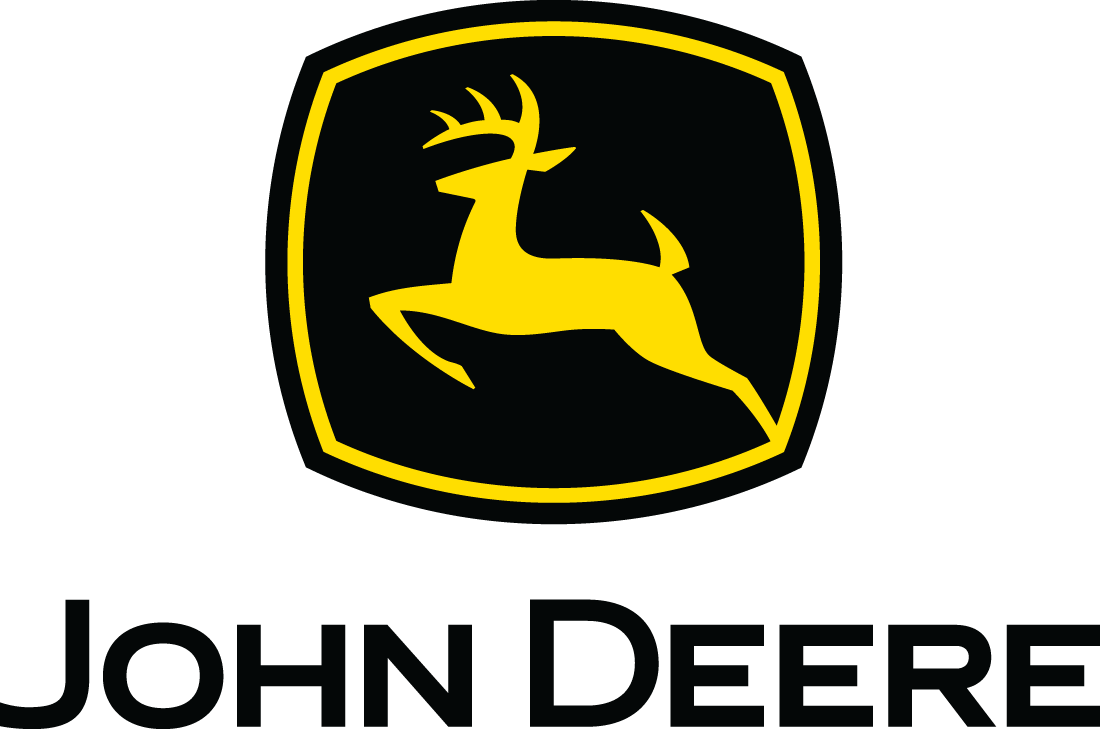
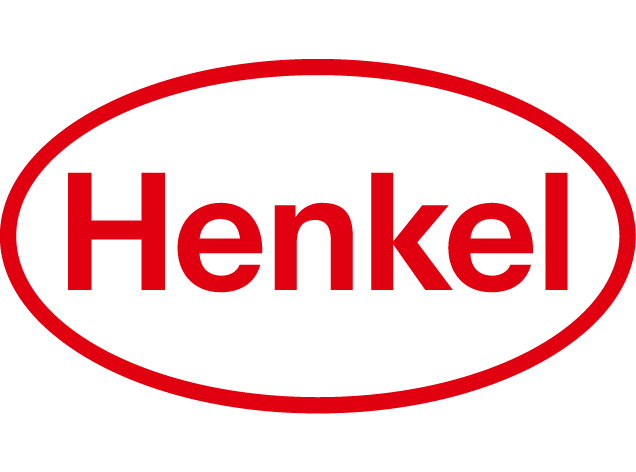
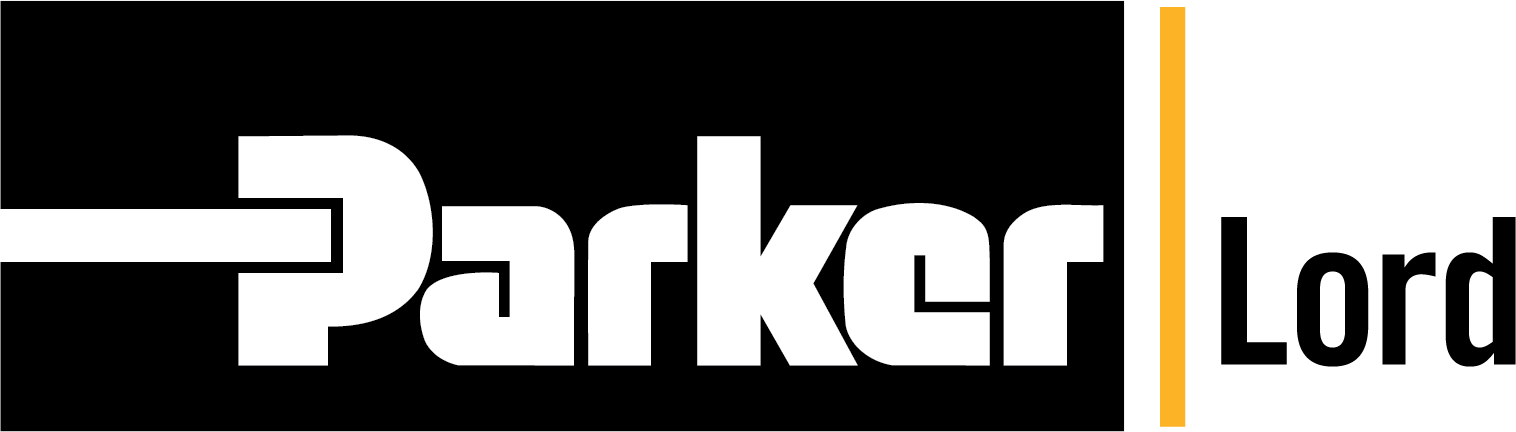
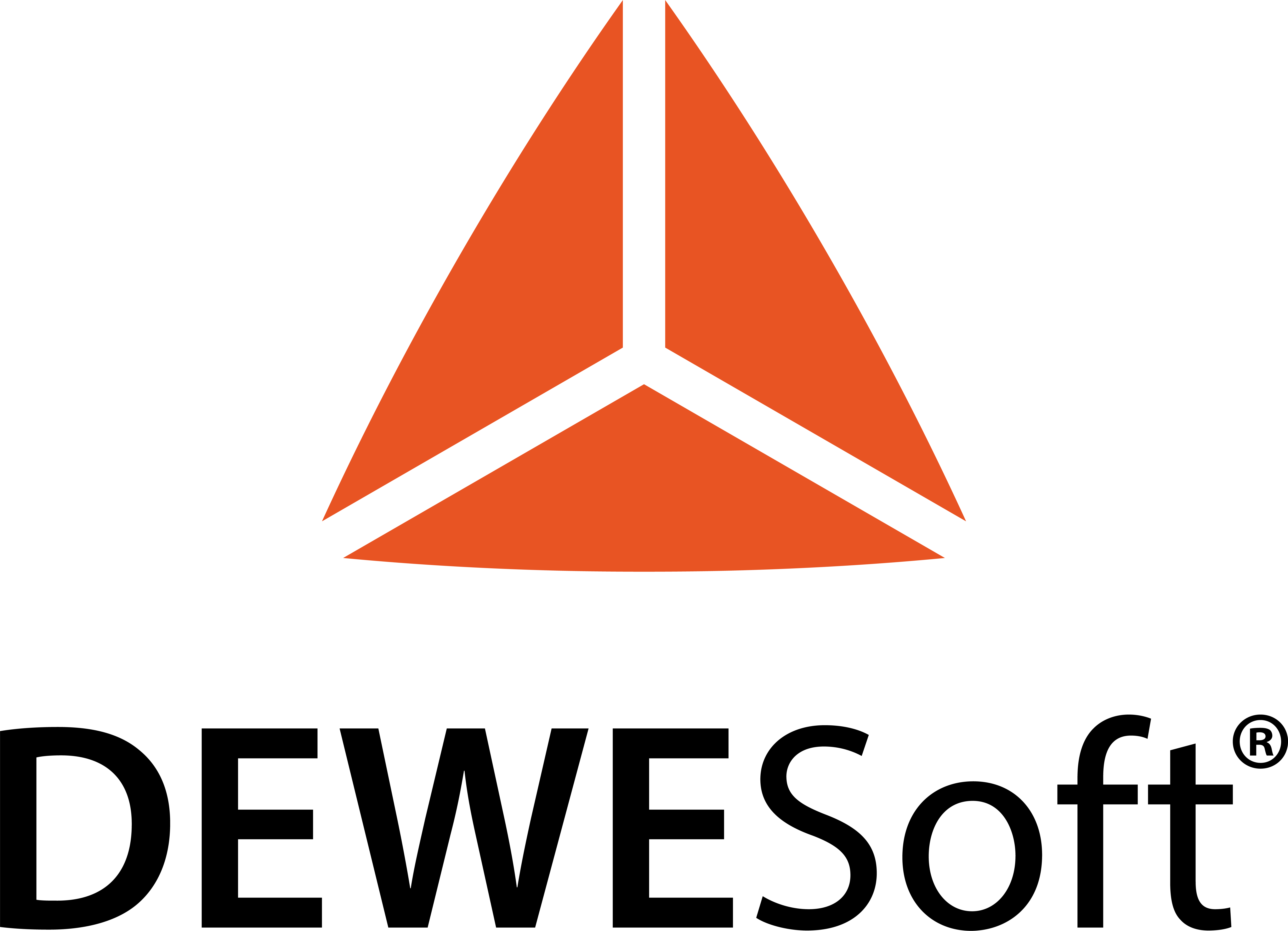
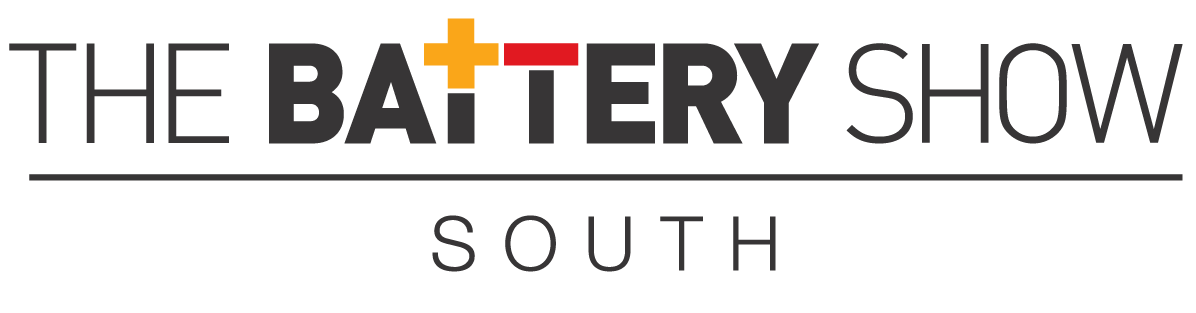
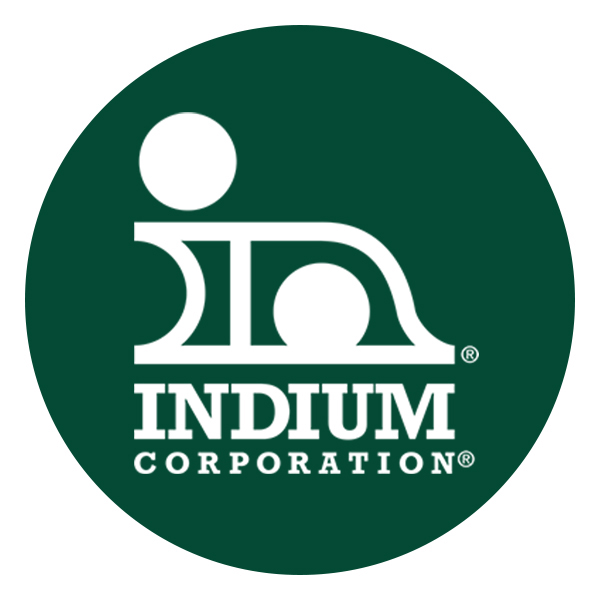
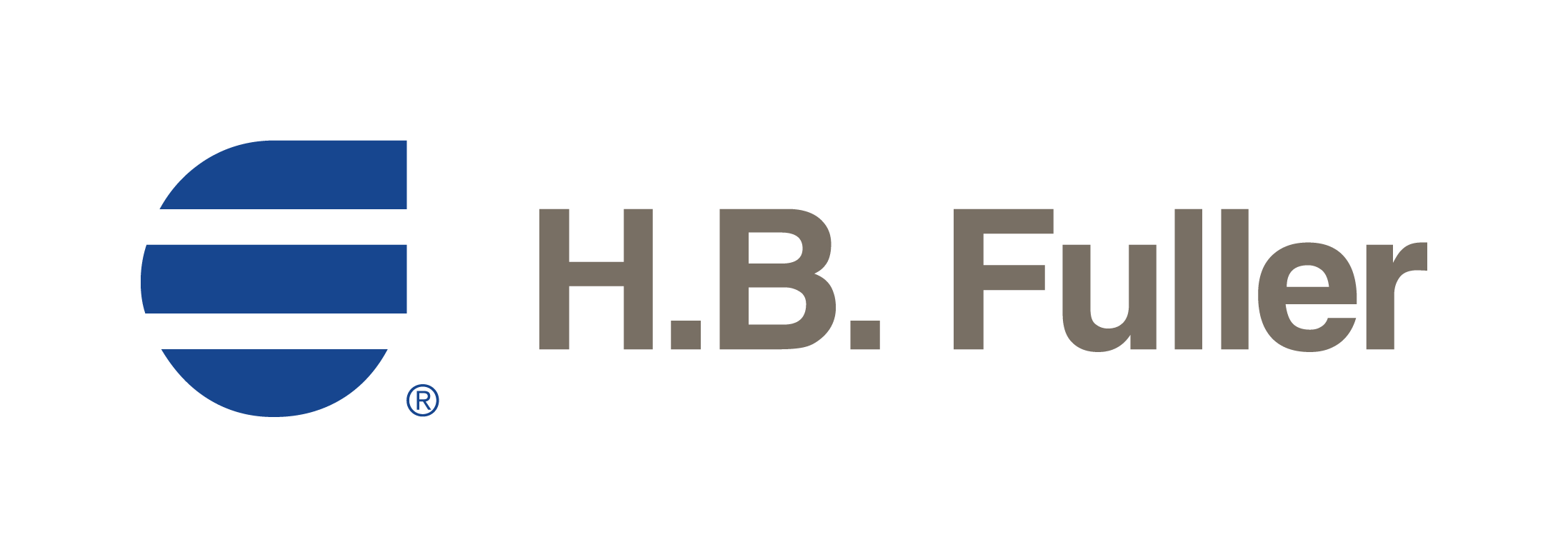