Holding electronics together under high voltages and temperatures
While EVs may have much in common with consumer electronics, the combination of high voltages and powers, and the safety-critical nature of many of their systems, is providing some major headaches for printed circuit board assembly (PCBA) contractors and electronics manufacturing services (EMS) providers – headaches that vehicle OEMs won’t be able to cure with over-the-air software updates (writes Peter Donaldson).
Despite what Terry Gou, founder and former chair of smartphone manufacturing giant Foxconn, has said, an EV is not an iPhone with four wheels. “A lot of people are finding that out real fast,” says Brian O’Leary, global head of e-mobility and infrastructure at Indium Corporation, which specialises in advanced materials – particularly solders – and solutions for assembling electronic systems.
More than 2 million EVs now contain Indium’s materials, O’Leary says, giving the company valuable insights into some of the knotty problems facing what is still a young industry.
He emphasises that legacy automakers as well as start-ups entering the e-mobility sector face intense pressure and focus on time to market, with the interval between design and production at scale shrinking from years to months. That is partly because EVs consist largely of electronics, with just a small fraction of the moving parts of an IC engine.
That has allowed the OEMs to contract directly with the PCBA contractors or EMS providers, instead of through Tier 1 suppliers – a disruptive change that has lowered the barriers to entry for such providers. Further, many engineers in EV start-ups have a consumer electronics background.
“Couple that with several EMSs that have limited automotive experience, and you find a steep learning curve for both OEM and supplier when it comes to building for reliability,” O’Leary says.
“In EVs as well as some of the DC fast-charging and energy storage systems, the ever-increasing voltages, longer mission profiles or duty cycles and increased density of components on a PCBA are putting tremendous pressure on designers to build products that have to run harder, longer and hotter. Standards that meet these new challenges either do not exist or are incomplete.”
He notes for example that a surface insulation resistance standard such as IPC J-STD-004B is often applied to PCBAs used in systems like advanced infotainment and autonomy. These use components such as chip-scale packages with a 0.3 mm pitch, which are common in mobile phones.
“The current standard will test for a relatively short duration of time, with larger spacing between components at lower voltage,” O’Leary says. “We have seen catastrophic failure in the field due to resulting shorts since the testing did not meet reality.”
Implicated in the creation of such shorts is the formation of dendrites: branching metallic structures that grow and connect components that shouldn’t be connected.
O’Leary gives an example in which Indium was called in by a customer to mitigate a problem with component warpage on a PCBA.
He says the customer’s set-up was still trying to solve the issue by using a lower oven temperature to reduce the thermal load on the board and a thicker stencil with larger apertures to deposit more solder paste to fill the warpage gaps. The paste was new and designed to run at a higher reflow temperature, and did not need excess material to fill the gap; instead it had the elasticity to continue to bond with a warping component during reflow.
“When they switched to the new solder, they wound up using too much of it, and with the lower oven temperature it did not fully cure, resulting in a gooey residue under the component,” he explains. “That didn’t immediately cause a defect, but once the board had a lot of voltage running through it dendrites started to form and cause shorts.
“That literally shut down dozens of EVs right in the middle of a highway. A single dendrite can kill a car, and it’s something that no over-the-air update can patch.”
He emphasises that this was not a problem with the materials but one of process set-up and miscommunication under pressure to get the product out of the door, to which the industry is becoming more vulnerable.
“Dendrites are a very real concern with EVs, because the boards are getting much more densely populated as they are expected to do more, so component pitches are becoming even less forgiving,” O’Leary says.
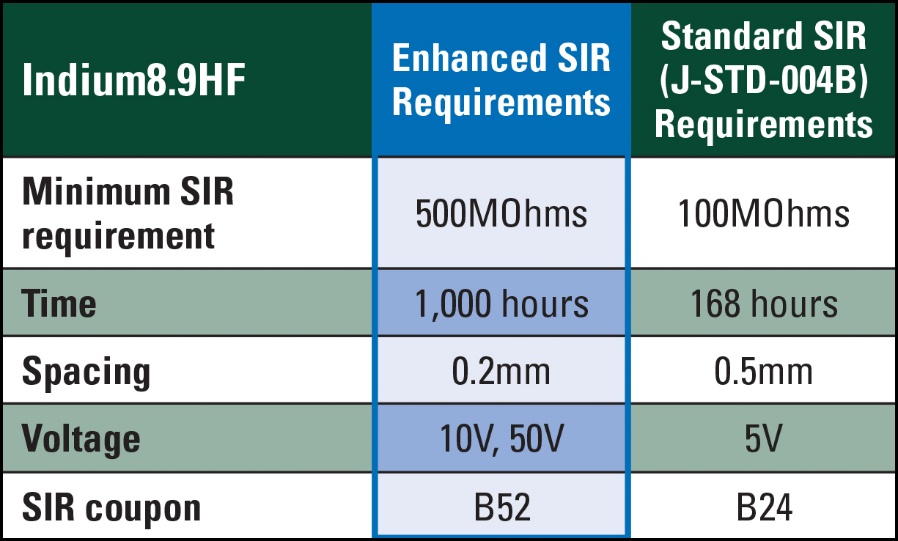
(Courtesy of Indium Corporation)
ONLINE PARTNERS
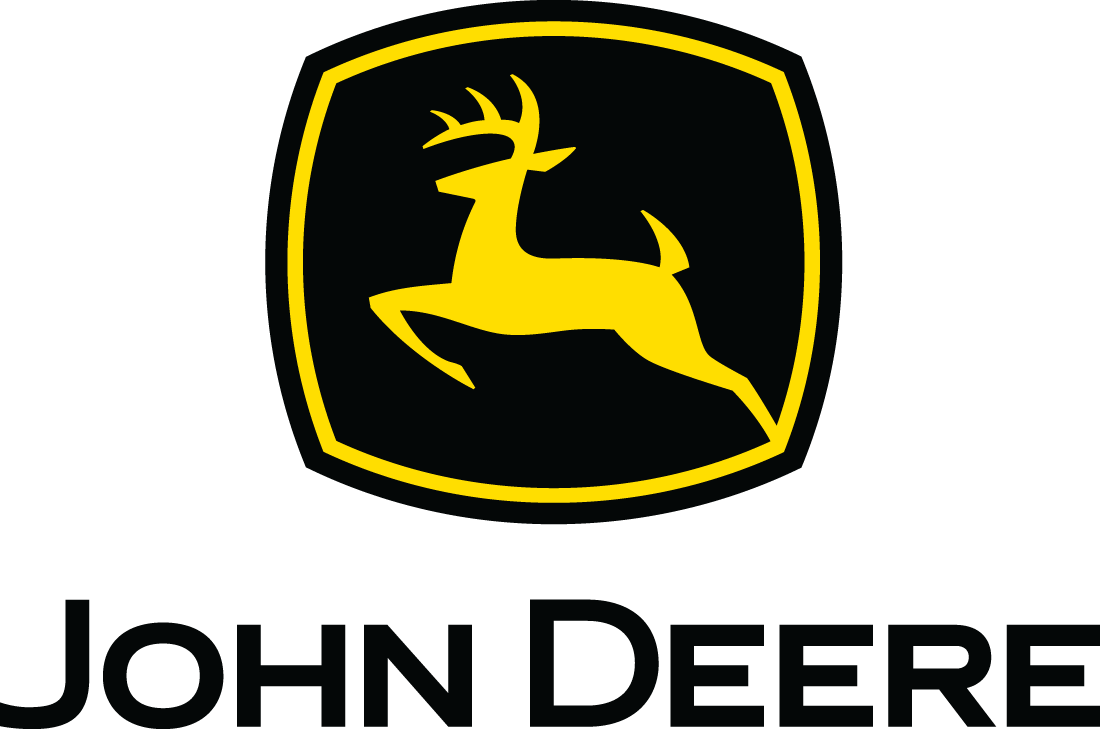
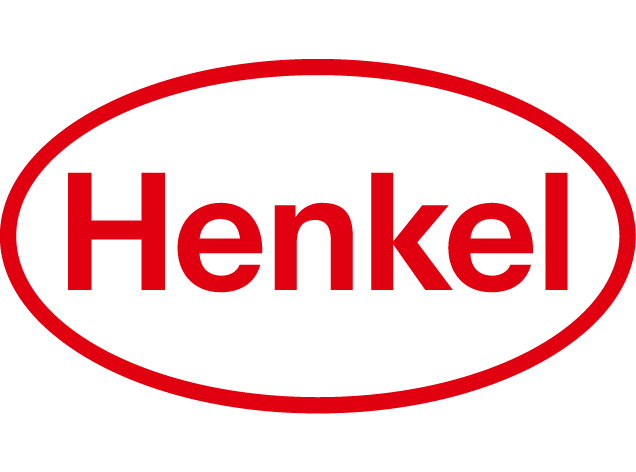
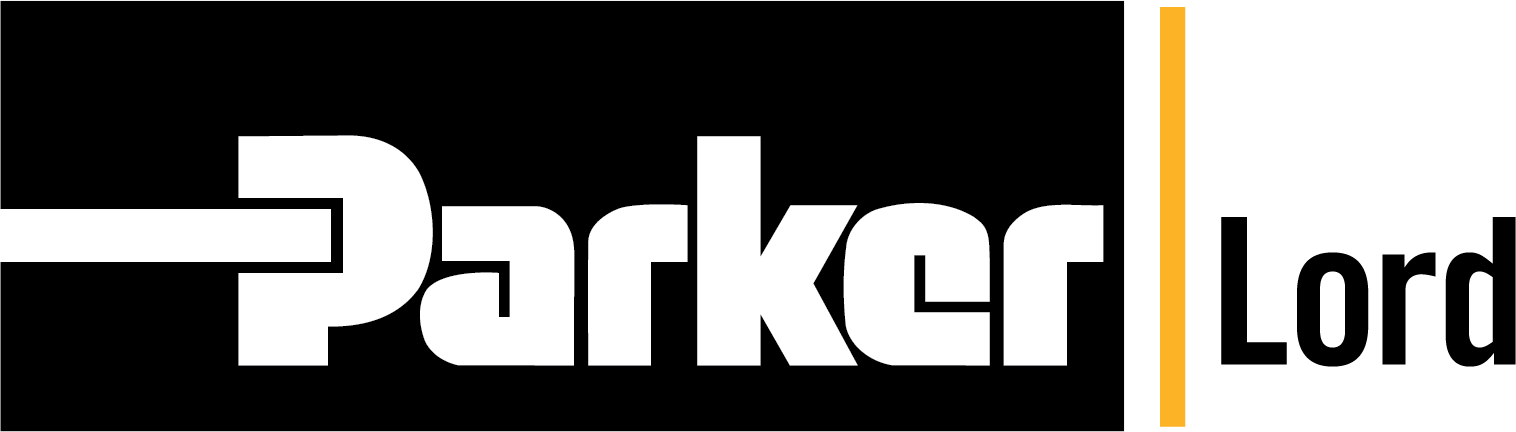
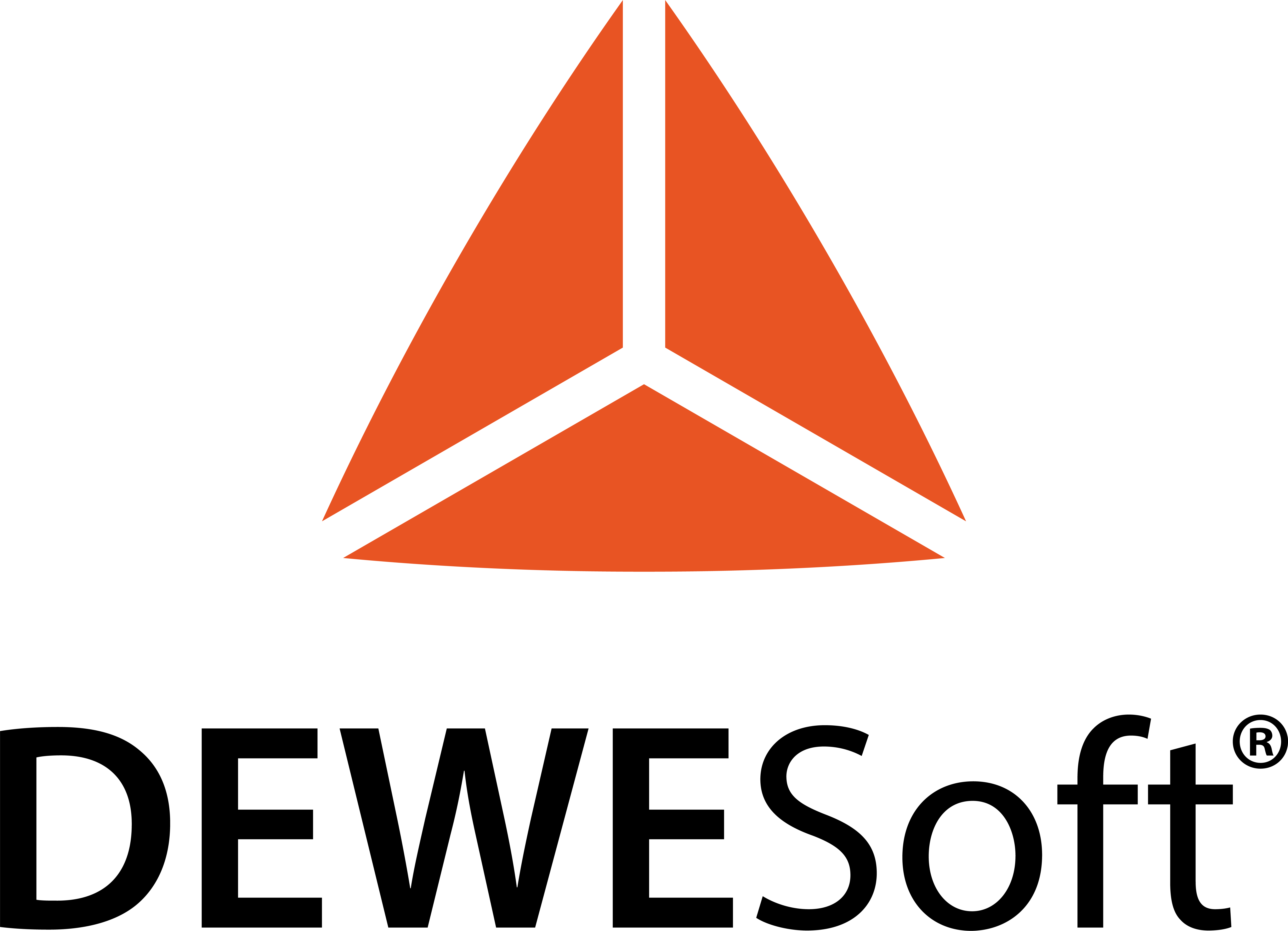
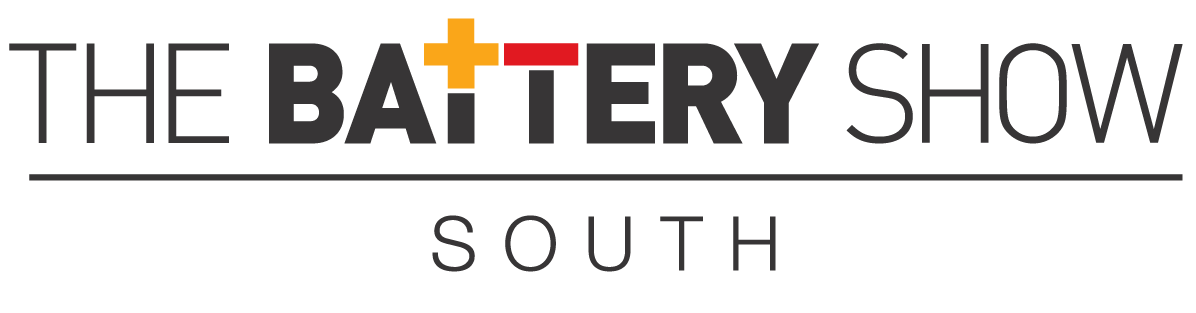
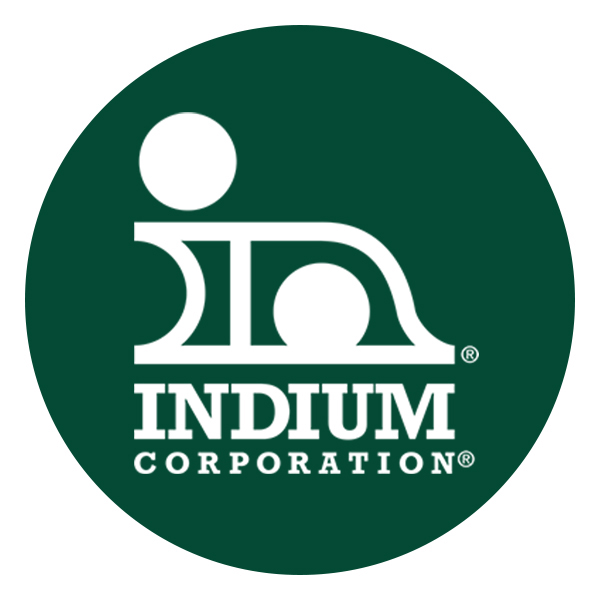
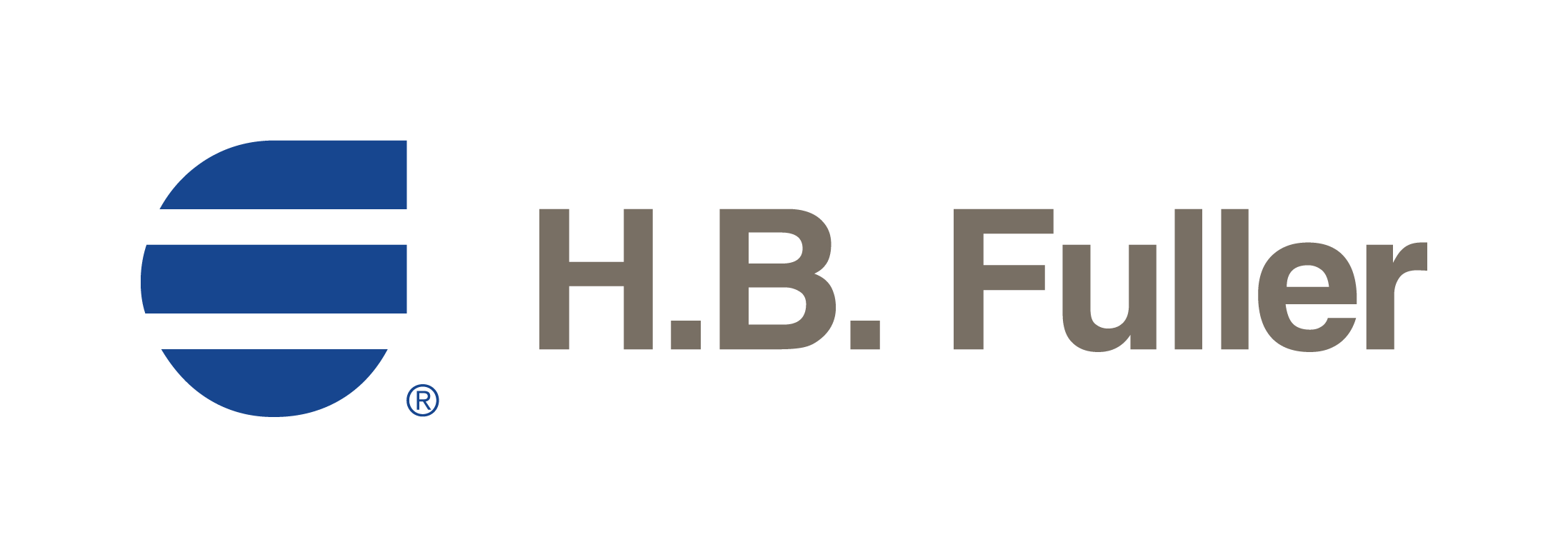