E-Kotug tugboat
A desire to cut maintenance costs prompted the development of this hybrid version of an existing tugboat. Rory Jackson reports.
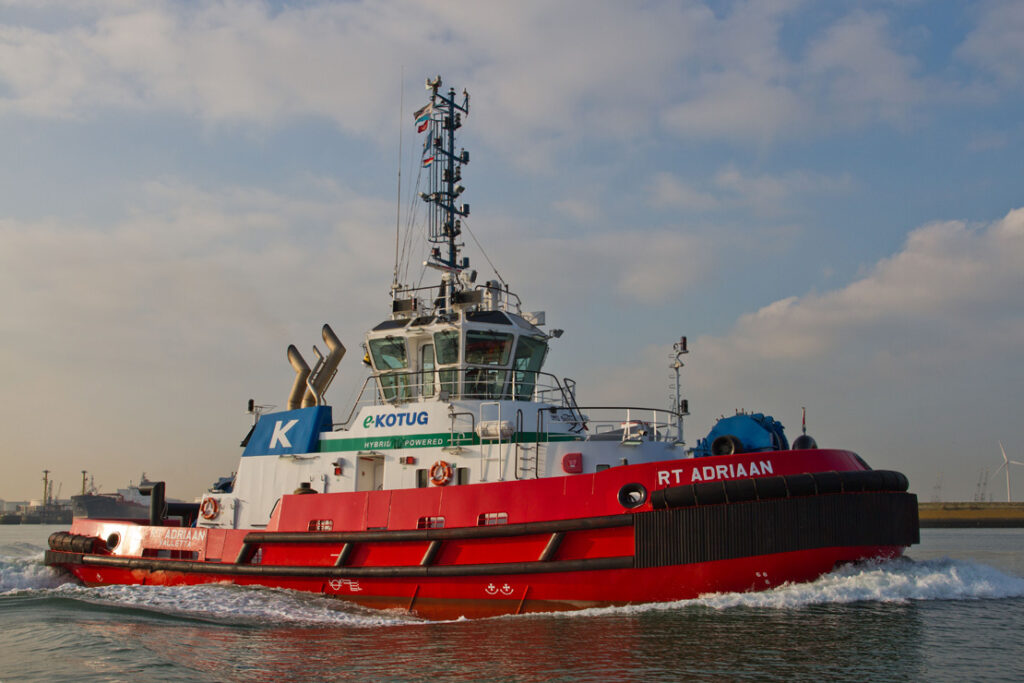
Pulling together
The E-Kotug is a diesel-electric tugboat owned and operated by international towage services provider Kotug Smit Towage. It is a hybrid-powered version of the Dutch company’s dieselpowered Rotortug design, which features three 360° azimuthal rotating thruster-propeller units. These enable the tug to manoeuvre and maintain its station with a greater degree of control than using conventional rear-facing thrusters.
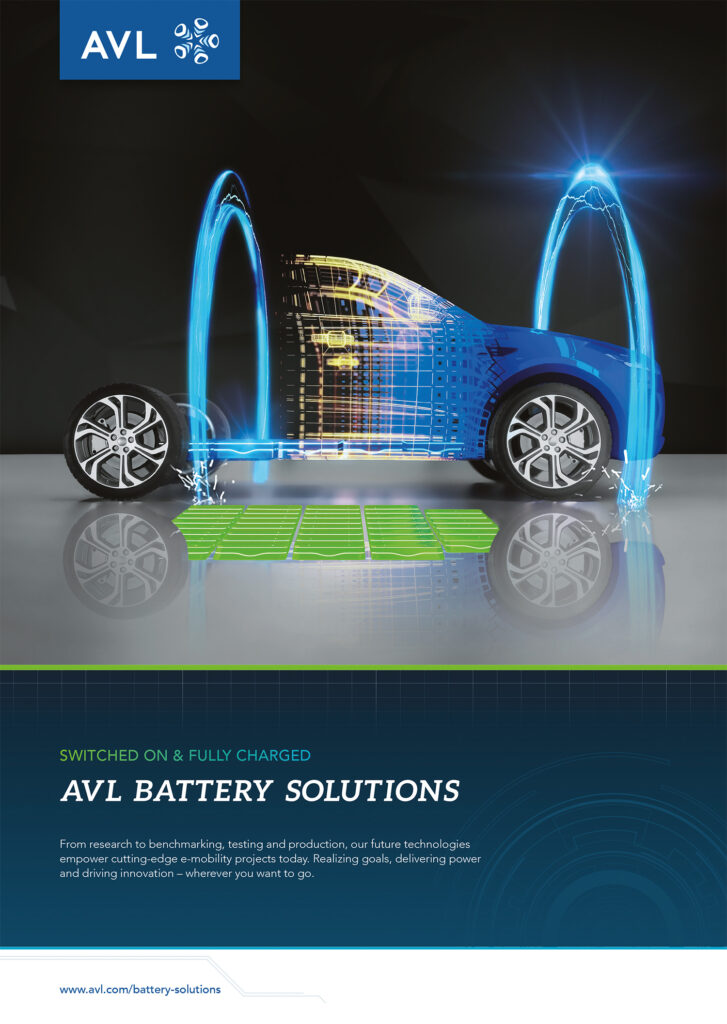
While controllability and safety are useful for any vehicle, tugboats are also at frequent risk of collision with the large, heavy ships they tow. That poses a tangible safety hazard to the onboard crew.
Kotug has therefore kept the thruster-propeller units as it has sought to electrify the Rotortug powertrain. Now the three examples of the E-Kotug are currently part of the fleet of Kotug Smit Towage, with two operating in Rotterdam and one in the German port of Bremerhaven.
The E-Kotug powertrain
The conventional Rotortug is driven by three Caterpillar 3512C-HD engines, and these V12 four-strokes are still used in the E-Kotug to maintain some component uniformity between the two types of tug.
The motivation to electrify the powertrain came when the company’s engineers saw the potential to significantly reduce long-term maintenance costs by dividing the propulsion work between fuel and battery power.
“The Caterpillar engine is designed to be used at 80-100% power, but the long distances and waiting times meant the Rotortugs spent maybe 5% of operations using that engine load,” says Koos Smoor, manager of fleet performance and innovation at Kotug.
“While the slow transit speeds across ports are fuel-economic, they still generate severe emissions because the engine wasn’t designed to be used at 25-60% of its power envelope. But we didn’t want to go fully dieselelectric because the degree of power conversion needed for high loads during towing operation would mean efficiency losses, equivalent to 5-10% of power.”
To have the best of both worlds, the E-Kotug tows using diesel power directly from the engines, and transits and manoeuvres through harbours and marine traffic using battery power. “That is mainly why we decided to go with a hybrid, to avoid idling on engine power and to cut maintenance costs, because the engines’ running hours are roughly halved, from 2000 hours per year to 1000,” Smoor adds.
“With this reduced engine use, overhauls can go from once every five years to every 10 years, and the oil can be changed every two years rather than annually.”
Motor/generators are integrated on each of the three Caterpillar engines’ output shafts, and each engine has a power take-off gearbox to connect and drive the thrusters in the event of a battery failure. Should that happen, AC power from the generators is used for steering and winch operations.
The vessel’s battery power comes from a pack made up of 18 cells connected in series. Each cell stores 6.5 kWh of energy, for a total capacity of 117 kWh.
The cell used is Corvus’ air-cooled AT6500-250-48, a lithium nickel manganese cobalt oxide cell with a rated lifetime energy storage of 32,500 kWh and a lifespan of at least 5000 cycles. Each one has a 150 Ah capacity, while weighing 70 kg and measuring about 59 x 38 x 33 cm. As well as its 48 V operating voltage, each cell gives a maximum voltage of 50.4 V, a minimum voltage of 38.4 V and a continuous current of 450 A.
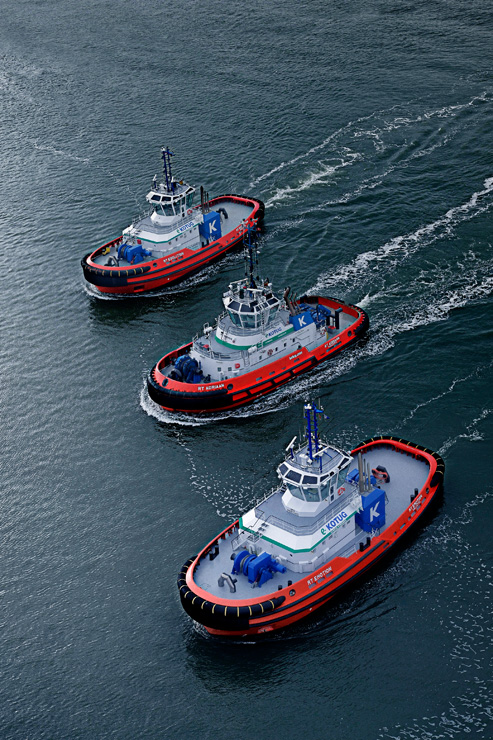
Curiously, while the power and energy capacities of the batteries were important, the key reason behind Kotug’s selection of these batteries came down to Corvus giving the Dutch company a 10-year warranty and providing technical and engineering support.
Smoor explains, “Investing in a hybrid powertrain can be costly, and we plan to see a return after about 10 years, particularly via reduced maintenance. Most battery companies typically offer two years of support, but that’s just not long enough when it comes to making a vehicle like this viable – if you have to buy a new battery every two years, the business case for using a hybrid tug goes out of the window.
“So we built the powertrain to spec for the project location and time span, and we’ve aimed to manage the temperature and usage of the batteries very carefully at each mission stage.”
Were this tug to be used in a port other than Rotterdam or Bremerhaven, a different battery or generator might be needed to account for the distance it might have to travel along the harbour’s length, or the distance between the harbour and the breakwater. The rest of the powertrain might then need new cables, power converters, thermal management and so on.
“That’s why there aren’t too many hybrid tugboats in service – you have to understand the sailing profile, then you need the right components to go with it,” Smoor says.
“The hybrids in the port of Rotterdam work well there, but if you used the same hybrid configuration in Singapore or Shanghai, for example, you would need more power to cover the larger port areas.”
The battery pack is air-cooled and kept in its own air conditioned chamber – as is typical for electric and hybrid-powered vessels – with the battery management system (BMS) optimising the air conditioning to maintain a constant temperature across the cells.
That maximises the lifetime of the battery by focusing the cooling on the cells in the middle of the pack, as these tend to run hotter than those at the corners.
“The batteries are constantly monitored by the BMS, and if an issue is detected then it will shut down the batteries, and an alarm will sound,” Smoor explains. “There are two types of alarm: a low level, non-essential one that can be reset, and a high-level one that can’t.”
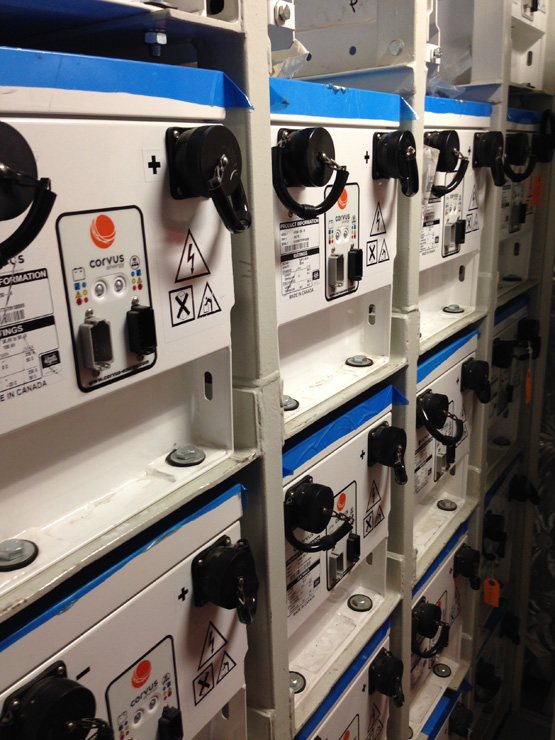
A low-level alarm could be triggered by something such as a minor voltage difference between the cells. While the battery voltage does not need to be balanced across the cells for normal operations, and the operator might therefore choose to ignore such an alarm during transit, balancing is healthier for the battery’s lifespan. That said, the operator can still acknowledge the alarm, reset it and continue operating the tug as normal.
However, if a high-level alarm sounds, potentially meaning the loss of a critical system, the operator cannot reset it. The BMS will automatically disconnect the batteries, and the operations computer will contact an on-call Corvus engineer to reset the E-Kotug’s battery pack.
“Corvus is remotely connected with these batteries, so they can see what the nature of the alarm is, 24/7,” notes Smoor. “They can then send a checklist of tasks to be carried out – safety diagnostics, fixes and so on.
“An engineer on board the tugboat goes through that list, and once they’ve confirmed that everything’s back to normal, the Corvus engineer sends the E-Kotug engineer a password to get the battery back online.
“In the first E-Kotug operations, we had a few high-level alarms just because we were going through a normal early learning process, but nowadays they don’t happen.”
Cameras are also installed in the battery room so that engineers can remotely view what is happening inside, and the air conditioning is monitored to ensure it is cooling the battery pack correctly. The battery room is equipped with canisters of fire-extinguishing gas that can be released to put out the flames of a thermal runaway.
Before a mission
The E-Kotug’s control system has five distinct operational ‘modes’ for each stage of a typical towing mission, which have been designed and written into the operating system by Aspin Kemp & Associates.
At the start of a mission, the tug will most often be moored at the harbour in Stop mode. In this mode, the onboard energy storage system supplies power to the main switchboard at 400 V, and to the various transformers at 30 V and 50 Hz.
Even in this mode, the batteries might run close to empty, simply by keeping the onboard electronics powered. At this point, one of the onboard generators can be powered by one of the engines, and it will start to charge the battery pack, taking up to 40 minutes for a full charge. After that, the generator will probably be inactive for six or seven hours if the E-Kotug remains in Stop mode.
Smoor notes, “We can fully charge the batteries at a faster rate, but then their lifetime will be reduced. We could also do it slower, but then the running hours of each generator might be too high, hence we fine-tune this to roughly 40 minutes’ total charging time when in Stop mode.”
As an alternative to using the generator for moored charging, the tugboat’s battery can be drip-charged from an onshore AC power source. That can take 12-24 hours, however, so advance notice is required that the E-Kotug will not be needed for that period of time.

Should the tugboat’s captain receive a call notifying of a new job, for example one that requires a 45-minute journey to where the towing operation will begin, the Transit 1 mode can be activated.
At Transit 1, the batteries deliver 120 kW to each of the E-Kotug’s thrusters for an operating speed of 6 knots. Again, as the batteries run low on charge (which may be after about 30 minutes at 6 knots), one of the engines can drive a generator to charge the battery pack, essentially serving as a range extender.
During this mode, the generator takes 45 minutes to charge the battery pack. Each of the three main generators is a 500 kW, six-pole, 480 V three-phase induction unit from TECO-Westinghouse.
Transit 1 is the most commonly used transit mode for E-Kotug users, but it is inadequate for the busier days at the ports across Northern Europe in which the vehicle currently operates.
On days when the crew is called on to carry out a relatively high number of towing jobs, the captain can switch to the faster Transit 2 mode, which typically provides a speed of between 8 and 9 knots.
In Transit 2, the tug’s main aft engine powers the aft thruster at around 80% load (1412 kW), giving that thruster a rotating speed of 1500 rpm, while the battery pack drives the two forward propellers at 1000 rpm.
“The forward propellers don’t add any thrust in this mode; we just power them to keep the propeller blades rotating at a speed to match the water flowing through them so that we don’t get any excess drag,” Smoor explains.
Towing operations
Once the E-Kotug has reached the designated position for a towing job, some time may need to pass before the towline can be connected. For example, the crew on board the ship to be towed might be finishing some other operation, or the linesmen might need more time to connect the towline between the tug and the ship.
In cases such as these, the captain can switch the tugboat to Idle mode. Here, all the thrusters are again powered by the batteries rather than a mix of the batteries and the Caterpillar engines.
The captain has full control over the thrusters, but as a default they are set to a full stop, to enable the E-Kotug to be manoeuvred alongside the ship (or at the bow or stern, if that is where it is needed initially).
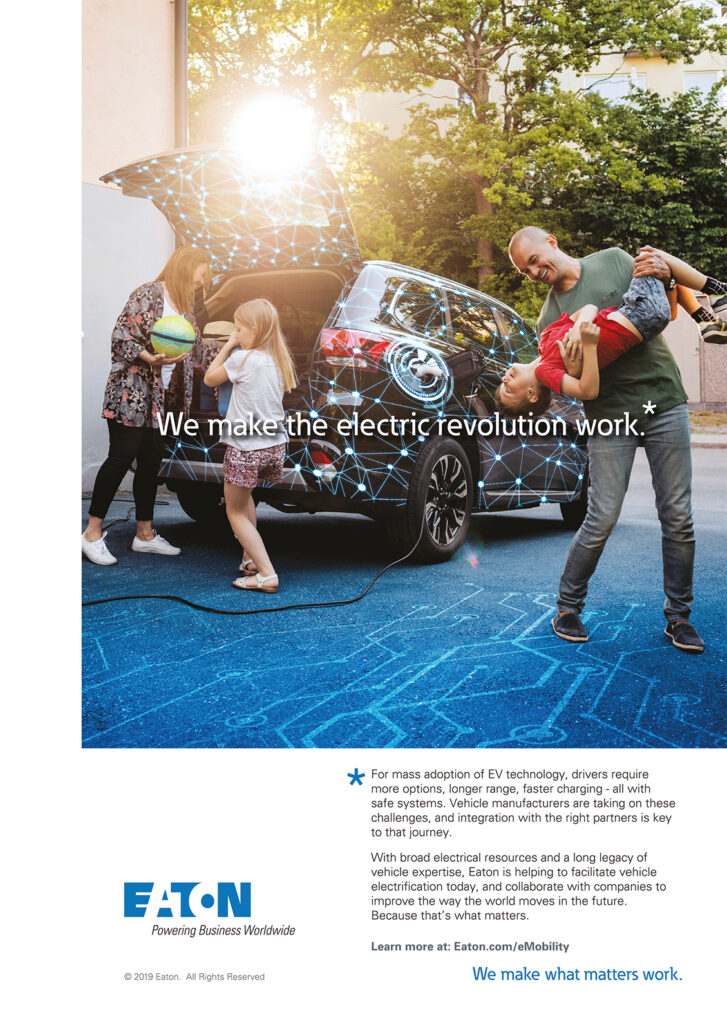
The battery power combined with the azimuthing thrusters also enables the captain to adjust the tugboat’s position to compensate for waves (without being locked into either of the fixedspeed profiles of Transit 1 or 2), and avoid any possible impacts between the tug and the ship.
The Idle mode is designed to enable the E-Kotug to use as little power as possible while waiting for the towline to be connected. When the ship is ready, its pilot will send the order to the tugboat, and the tug’s captain can then manoeuvre the E-Kotug to whichever part of the ship at his chosen speed to attach the towing line to the mooring line.
Once the line is secured to the ship, towing can begin, and the tug is set to Assist mode.
Pulling the ship to or from the quayside typically takes about 30 minutes, but the batteries can’t provide the power required for this level of work. Therefore, in Assist mode, all three main engines are started, and they drive the propellers at their full 1765 kW power capacity in order to provide the necessary bollard pulling force, which can go up to 84 tonnes with the E-Kotug.
The towline is held on the tugboat by a motor/generator-operated winch. This is powered by the battery, but like the steering it can use the TECO-Westinghouse motor/generators for back-up power if the battery is disconnected, such as if a high-level alarm occurred earlier in the operation. And when the towline is taut and being pulled away by the ship, the freewheeling of the winch motor recharges the battery.
In operations where the tugboat is pulling a ship away from the quayside towards the breakwater, the ship can use its own propellers after clearing the busier part of the harbour. At that time, the tug’s diesel engines are no longer required at full load, and are typically run at between 50% and 80% power.
“Also, towards the end of the towing operation, as the ship reaches its cruising speed using its own propellers, the batteries can be recharged with the excess power that the tugboat’s engines are not using,” says Smoor. “So the tug’s three main generators are activated, and the engines provide 250 kW for each of them, to replenish the power used in the Transit and Idle modes for the return to port.”
Over the course of the operation – which typically takes 90-120 minutes, evenly divided between transit, idling and towing – one of the aforementioned alarms might sound as the captain switches from one operating mode to the next.
If a high-level alarm rings, signifying a critical failure in a key electrical component such as a battery cell or DC-DC converter, the captain has to choose between calling onshore operators to dispatch another tug to finish the job, or switch to the vessel’s onboard back-up power.
This switch activates a bypass to control the thrusters entirely by the main engines (with steering coming from the generators), much like on a conventional fuel-powered tugboat.
“At this point, the motor/generators will mostly be freewheeling on the engines’ output shafts, with minor AC power going to the steering, but the tug can still at least carry out its job – just without the hybrid benefits,” Smoor notes.
Return to harbour
The 30-45 minutes back to the mooring station are typically in Transit 1 mode, on battery power, with the generators working to charge the batteries fully by the time the E-Kotug is moored and waiting for the next job.
A few post-mission checks and tasks might follow. For instance, if the captain knows that the next job will not be for another 12 hours or more, he can connect the shore power cable to maintain full battery charge until then.
Between towing jobs, the captain needs to check that the steering and winches are operating correctly. Voltage checks can be carried out to ensure that the thrusters can be steered (and that the winches can be operated) on both DC power from the battery pack and AC power from the generators, to confirm that the redundant steering power is working before the next mission starts.
The tug captain also typically turns the thrusters 40-50° port and starboard after a mission, to make sure they are still in normal working order. He can also check that the battery cell voltages are balanced; if not, the BMS can be told to do so. At that point, the tug will remain stationary until the cell voltages are the same.
The future
Future iterations of the E-Kotug are expected to integrate roughly the same powertrain but to adopt batteries with greater energy capacities, to more easily achieve the 10-year lifespan required by the project’s cost projections.
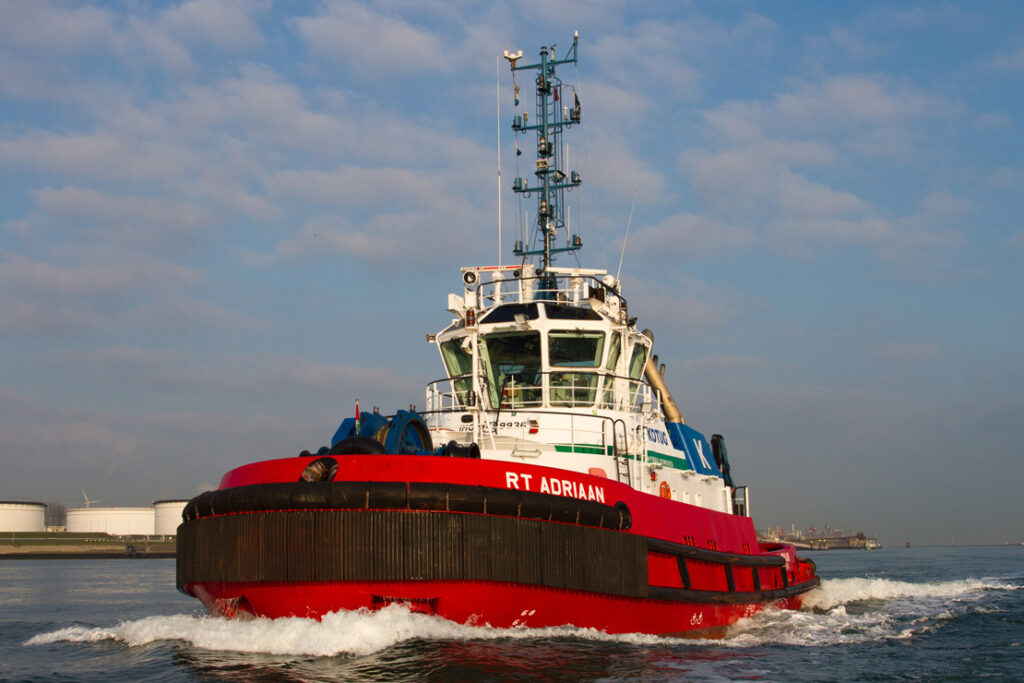
E-Kotug specifications
Length: 31.95 m
Draft: 6.25 m
Beam: 12.60 m
Displacement: 598 tonnes
Maximum forward speed: 12.5 knots
Maximum bollard pull: 84 tonnes
Operating bollard pull: 80 tonnes
Some key suppliers
Powertrain integration: Aspin Kemp & Associates
Operating system: Aspin Kemp & Associates
Engines: Caterpillar
Batteries: Corvus Energy
Motor/generators: TECO-Westinghouse
Thrusters: SchottelSwitchboards: Aspin Kemp & Associates
DC-DC converters: ZekatexAC-DC inverters: Vacon
ONLINE PARTNERS
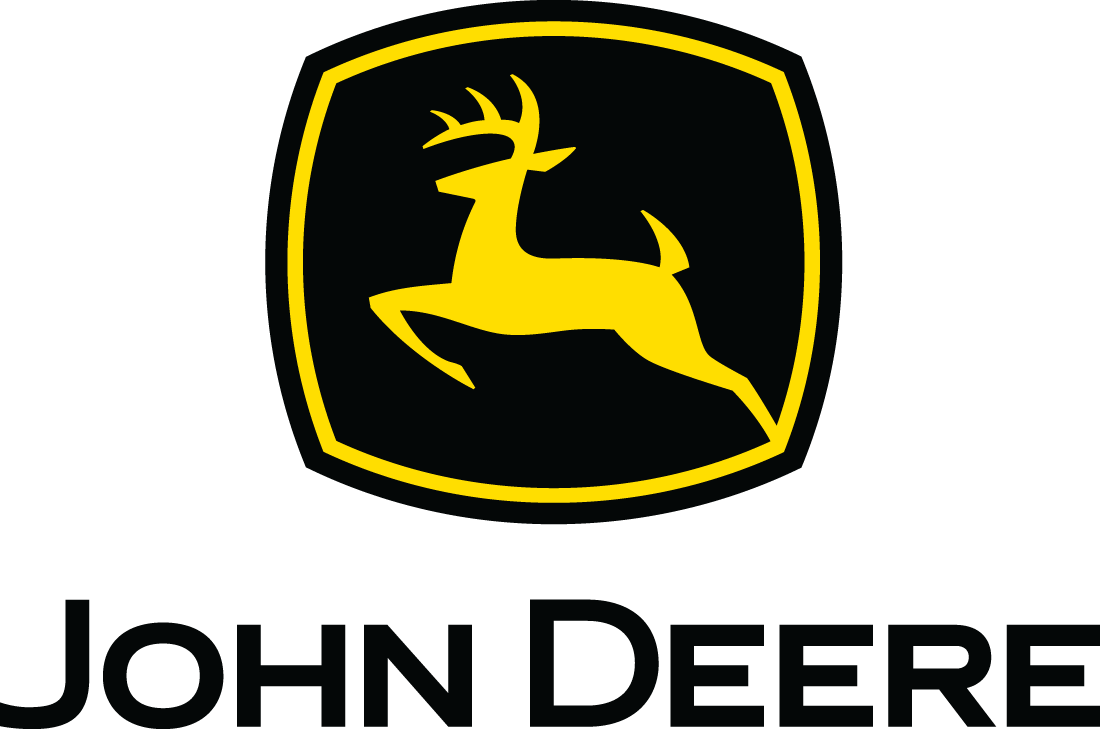
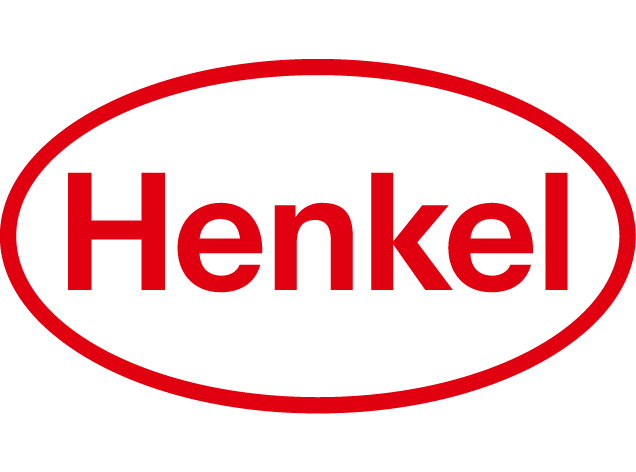
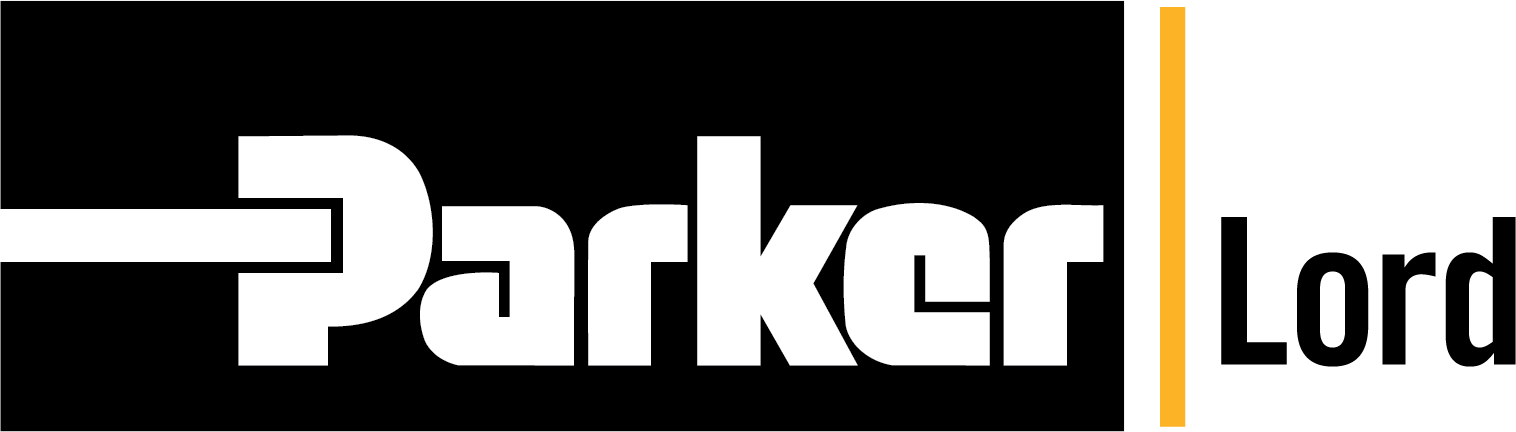
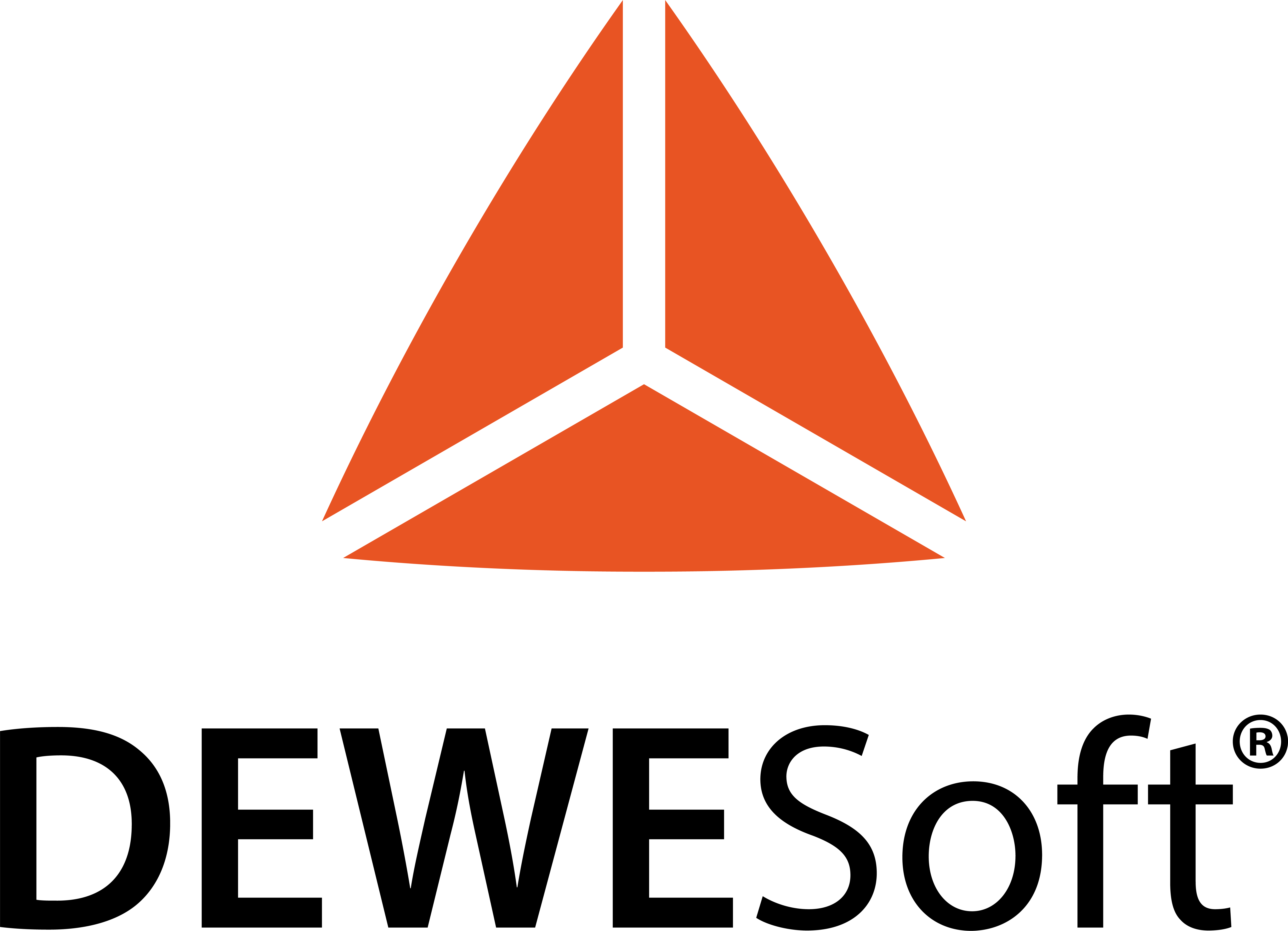
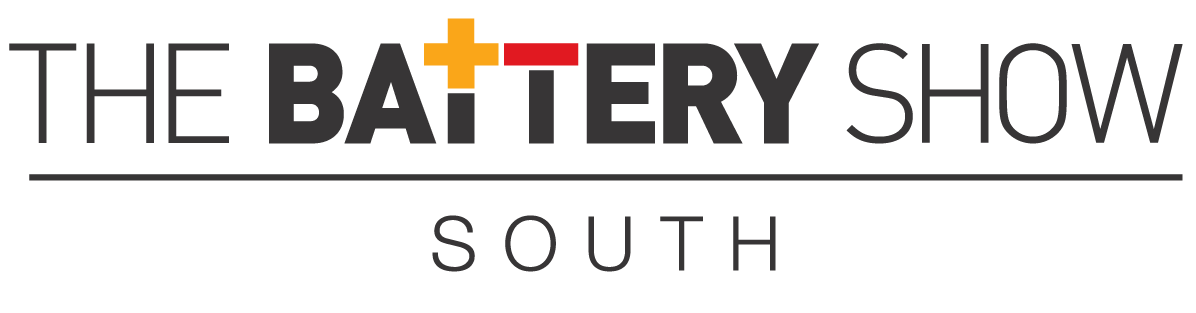
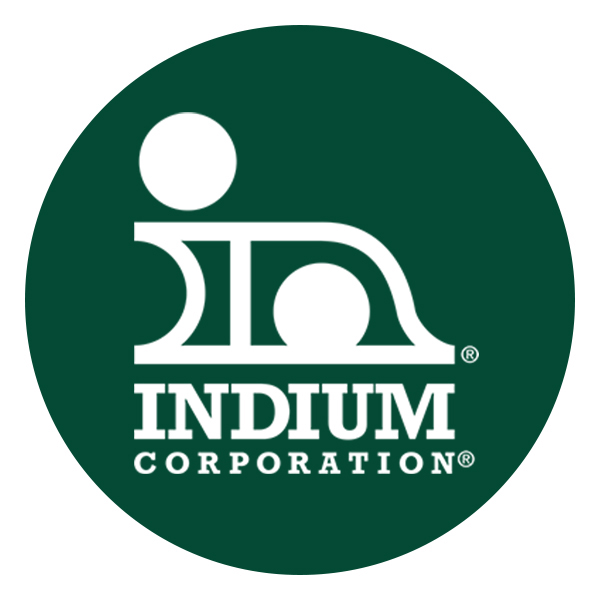

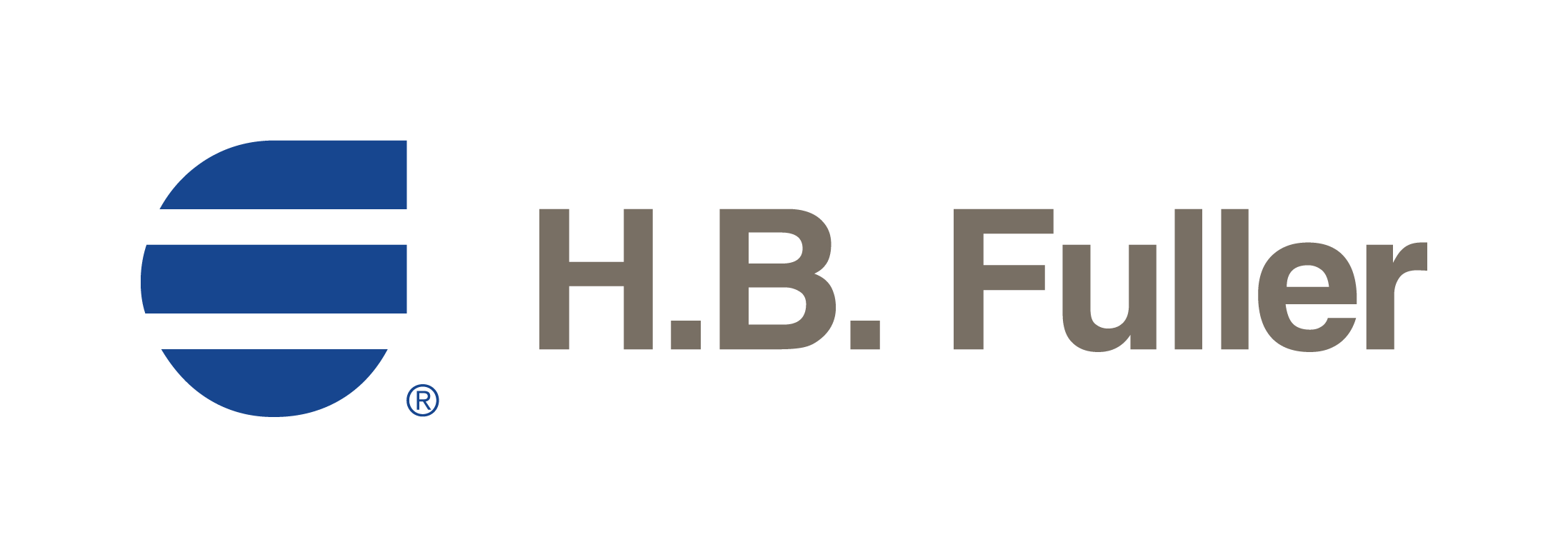
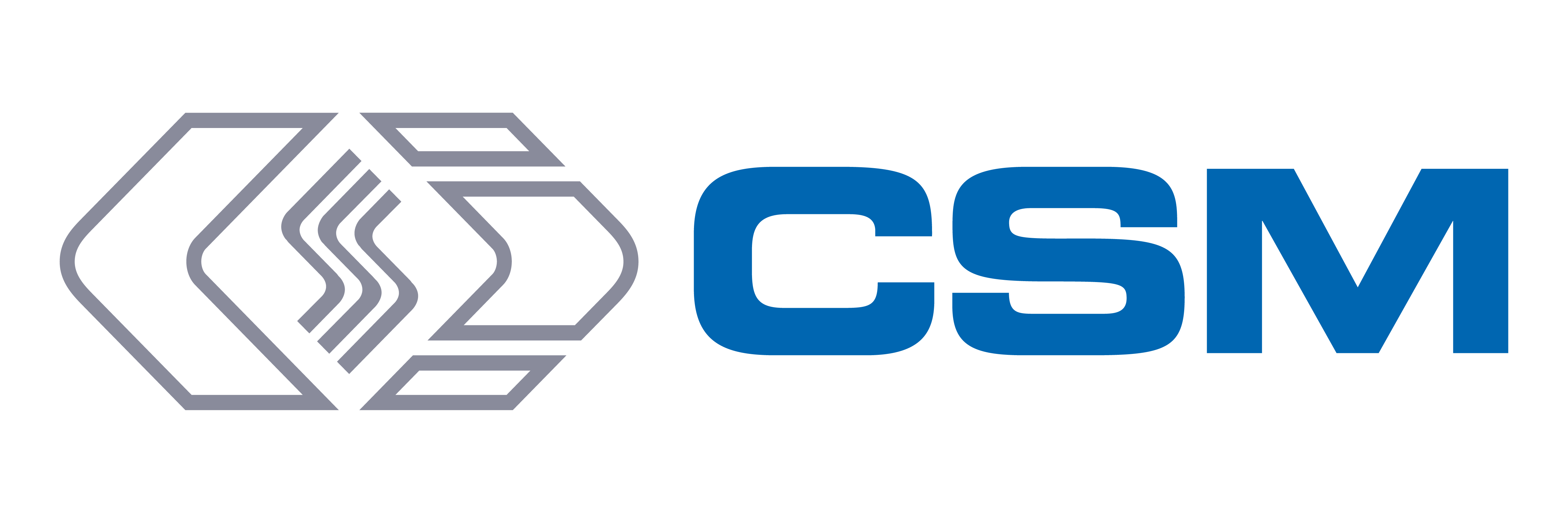
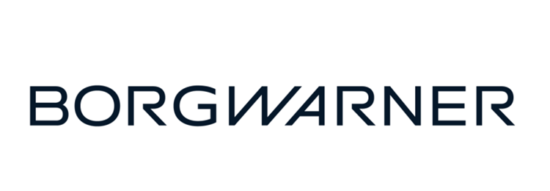